Improve Quality: The Complete Guide to Gasket Manufacturers (2025)
Introduction: Navigating the Global Market for Gasket Manufacturers
Navigating the global market for gasket manufacturers presents a significant challenge for international B2B buyers, especially those in regions like Africa, South America, the Middle East, and Europe. With the increasing demand for reliable sealing solutions across various industries, understanding how to source high-quality gaskets that meet specific operational needs is crucial. This guide provides a comprehensive overview of gasket types, applications, and the nuances of supplier vetting, ensuring that buyers can make informed decisions that enhance their operational efficiency.
In today’s competitive landscape, the ability to identify reputable gasket manufacturers is paramount. This guide empowers B2B buyers by outlining essential factors to consider, including material specifications, application suitability, and cost implications. It also delves into the importance of establishing strong supplier relationships, thereby facilitating smoother procurement processes and reducing the risk of operational disruptions.
Whether you are in the automotive, aerospace, or industrial sector, the insights provided in this guide will help you navigate the complexities of sourcing gaskets effectively. By understanding the market dynamics and evaluating potential suppliers with a strategic approach, buyers can enhance their procurement strategies and ensure they are equipped with the best sealing solutions available.
Understanding Gasket Manufacturers Types and Variations
Type Name | Key Distinguishing Features | Primary B2B Applications | Brief Pros & Cons for Buyers |
---|---|---|---|
Rubber Gaskets | Flexible, excellent sealing properties, resistant to various chemicals | Automotive, HVAC, plumbing | Pros: Cost-effective, easy to install. Cons: Limited temperature range. |
Metal Gaskets | High strength, durability, suitable for high-pressure applications | Oil & gas, power generation | Pros: Long-lasting, can withstand extreme conditions. Cons: More expensive, requires precision fitting. |
Spiral Wound Gaskets | Composed of alternating layers of metal and filler material | Chemical processing, marine | Pros: Versatile, good for high-temperature applications. Cons: Can be complex to install. |
PTFE Gaskets | Chemically resistant, non-stick properties, high thermal stability | Pharmaceutical, food processing | Pros: Excellent chemical resistance, low friction. Cons: More costly, less compressible than rubber. |
Cork Gaskets | Made from natural cork, compressible and resilient | Electrical, automotive | Pros: Eco-friendly, good sealing performance. Cons: Limited lifespan, can degrade in high temperatures. |
What Are the Characteristics and Suitability of Rubber Gaskets for B2B Buyers?
Rubber gaskets are known for their flexibility and excellent sealing capabilities, making them ideal for applications in automotive, HVAC, and plumbing sectors. They can resist various chemicals, though their temperature range is limited compared to other materials. B2B buyers should consider the specific environmental conditions where these gaskets will be used, as well as the cost-effectiveness of rubber options in large-scale applications.
How Do Metal Gaskets Stand Out in High-Pressure Applications?
Metal gaskets are distinguished by their high strength and durability, making them suitable for demanding environments such as oil and gas or power generation. They can withstand extreme pressures and temperatures, but this comes at a higher cost. B2B buyers should assess the precision required for installation, as improper fitting can lead to leaks and system failures.
What Makes Spiral Wound Gaskets a Versatile Choice?
Spiral wound gaskets consist of alternating layers of metal and filler material, providing versatility for various applications, particularly in chemical processing and marine industries. They are effective in high-temperature scenarios but can be complex to install due to their design. Buyers should evaluate their installation capabilities and the specific applications to leverage the benefits of spiral wound gaskets effectively.
Why Are PTFE Gaskets Preferred in Sensitive Environments?
PTFE gaskets are renowned for their chemical resistance and non-stick properties, making them ideal for pharmaceutical and food processing applications. They can withstand high thermal conditions but are generally more expensive than rubber alternatives. B2B buyers must consider the specific chemical exposure and the need for low friction in their processes when opting for PTFE gaskets.
How Do Cork Gaskets Provide Eco-Friendly Solutions?
Cork gaskets are made from natural materials, offering a compressible and resilient sealing option suitable for electrical and automotive applications. They are eco-friendly but have a limited lifespan and can degrade under high temperatures. Buyers interested in sustainability should weigh the environmental benefits against the potential for shorter service life in demanding conditions.
Related Video: Gasket Maker Overview – Permatex Tech Tip Series
Key Industrial Applications of Gasket Manufacturers
Industry/Sector | Specific Application of Gasket Manufacturers | Value/Benefit for the Business | Key Sourcing Considerations for this Application |
---|---|---|---|
Oil and Gas | Sealing in pipelines and drilling equipment | Prevents leaks, ensuring safety and compliance | Material compatibility, temperature resistance, certifications |
Automotive | Engine and transmission gaskets | Enhances performance, reduces emissions | OEM specifications, durability, and cost-efficiency |
Chemical Processing | Sealing in reactors and storage tanks | Maintains pressure and prevents contamination | Chemical resistance, size specifications, and certification |
HVAC Systems | Gaskets for air handling units | Improves energy efficiency and reduces noise | Material selection, temperature tolerance, and compliance standards |
Food and Beverage | Sealing in processing and packaging equipment | Ensures hygiene and prevents contamination | FDA compliance, material safety, and customization options |
What are the key applications of gaskets in the oil and gas industry?
In the oil and gas sector, gaskets play a critical role in sealing pipelines and drilling equipment. They are designed to withstand extreme pressures and temperatures, preventing leaks that could lead to environmental disasters or safety hazards. For international buyers in regions like Africa and the Middle East, sourcing gaskets that meet local regulations and material standards is essential. Ensuring that gaskets are made from materials compatible with the specific fluids being transported is crucial for operational safety and efficiency.
How do automotive gaskets enhance vehicle performance?
Automotive gaskets are vital components in engines and transmission systems. They help to create tight seals that prevent oil and coolant leaks, which is essential for maintaining engine performance and efficiency. For B2B buyers in Europe and South America, understanding OEM specifications is key when sourcing these gaskets. Durability and cost-effectiveness are also significant considerations, as higher-quality gaskets can lead to lower maintenance costs and improved vehicle reliability.
In what ways do gaskets support chemical processing operations?
In chemical processing, gaskets are used in reactors, storage tanks, and piping systems to maintain pressure and prevent contamination. The right gasket materials must be selected based on the chemicals being processed to avoid degradation and ensure safety. International buyers, particularly from regions with stringent safety regulations, should prioritize sourcing gaskets that offer chemical resistance and meet industry certifications. This attention to detail helps in preventing costly shutdowns and maintaining product integrity.
Why are gaskets important in HVAC systems?
Gaskets in HVAC systems are crucial for sealing air handling units and ductwork. They help improve energy efficiency by preventing air leaks and reducing noise levels, which is especially important in commercial buildings. For B2B buyers in Europe, sourcing gaskets that comply with energy efficiency standards can provide a competitive edge. Material selection, especially for high-temperature applications, is critical for ensuring long-lasting performance and compliance with local regulations.
How do gaskets ensure safety in food and beverage processing?
In the food and beverage industry, gaskets are essential for sealing processing and packaging equipment. They help maintain hygiene and prevent contamination, which is vital for consumer safety and regulatory compliance. For international buyers, especially in regions like South America and Africa, sourcing FDA-compliant gaskets made from safe materials is paramount. Customization options may also be necessary to meet specific equipment designs and operational needs.
3 Common User Pain Points for ‘Gasket Manufacturers’ & Their Solutions
Scenario 1: Inconsistent Quality of Gasket Products
The Problem:
B2B buyers often face challenges related to the inconsistency in the quality of gaskets supplied by manufacturers. This issue can lead to unexpected failures in sealing applications, resulting in costly downtime, increased maintenance expenses, and compromised product integrity. Buyers may discover that gaskets supplied in bulk vary in thickness, material composition, or elasticity, which can affect their performance under pressure or temperature changes. This inconsistency not only impacts the immediate project but can also damage long-term supplier relationships and harm the buyer’s reputation.
The Solution:
To mitigate quality inconsistency, buyers should implement a robust supplier evaluation process before entering into contracts. This includes requesting samples and conducting rigorous testing under operational conditions to verify performance metrics such as tensile strength, compression set, and resistance to chemicals. Establishing clear specifications and tolerances for gaskets can help ensure that manufacturers understand the quality standards required. Additionally, consider developing partnerships with manufacturers that employ ISO 9001 or similar quality management systems, as these certifications indicate a commitment to maintaining high standards in production. Regular audits and quality checks should also be part of the ongoing relationship to ensure compliance and address any deviations promptly.
Scenario 2: Difficulty in Sourcing Custom Gaskets for Unique Applications
The Problem:
Many B2B buyers encounter difficulties when trying to source custom gaskets tailored to specific applications. Industries such as aerospace, automotive, and energy often require gaskets that meet unique specifications regarding size, shape, and material to handle extreme environments or specific chemicals. This can lead to delays in production schedules and additional costs if standard gaskets do not meet the necessary requirements, resulting in project delays and missed deadlines.
The Solution:
To effectively source custom gaskets, buyers should engage in thorough communication with potential gasket manufacturers early in the design process. Providing detailed drawings, specifications, and any relevant test data can help manufacturers understand the specific needs. It may also be beneficial to work with manufacturers that offer prototyping services, allowing for the creation of initial samples to test in real-world conditions. Additionally, consider leveraging local manufacturers who might be more responsive to custom requests and have shorter lead times compared to overseas suppliers. Establishing a collaborative relationship with the manufacturer will facilitate adjustments during the design phase, ensuring that the final product is precisely what is needed without compromising on quality or increasing costs.
Scenario 3: Managing Long Lead Times and Delivery Delays
The Problem:
International B2B buyers, particularly those in Africa and South America, often struggle with long lead times and delivery delays when ordering gaskets from manufacturers. These delays can significantly disrupt supply chains and project timelines, as gaskets are critical components in various applications, from machinery to automotive systems. When buyers are unable to receive gaskets on time, it can lead to halted production lines, increased labor costs, and strained customer relationships.
The Solution:
To manage lead times effectively, buyers should prioritize building strong relationships with multiple gasket manufacturers to diversify sourcing options. This not only ensures a backup supplier in case of delays but also creates competitive pressure that can lead to improved service levels. Furthermore, buyers should negotiate clear delivery schedules and penalties for late shipments in their contracts to encourage accountability. Utilizing Just-In-Time (JIT) inventory practices can also help alleviate some pressures; by ordering gaskets closer to the time they are needed, buyers can reduce the impact of delays. Additionally, employing logistics management software can provide real-time updates on shipment status, allowing for proactive measures to be taken should any delays arise.
Strategic Material Selection Guide for Gasket Manufacturers
When selecting materials for gaskets, manufacturers must consider various factors that influence performance, durability, and suitability for specific applications. Below, we analyze four common gasket materials, detailing their properties, pros and cons, impact on applications, and specific considerations for international B2B buyers, particularly from regions like Africa, South America, the Middle East, and Europe.
What Are the Key Properties of Rubber Gaskets?
Rubber gaskets are widely used due to their flexibility and ability to form a seal under compression. Key properties include:
- Temperature/Pressure Rating: Typically ranges from -40°F to 250°F (-40°C to 121°C) and can withstand moderate pressure.
- Corrosion Resistance: Generally resistant to water and some chemicals, but can degrade in the presence of oils and solvents.
Pros: Rubber gaskets are cost-effective, easy to manufacture, and provide excellent sealing capabilities for a variety of applications.
Cons: They may not be suitable for high-temperature or high-pressure environments, and their lifespan can be limited in harsh chemical conditions.
Impact on Application: Rubber gaskets are ideal for applications involving water, air, and some mild chemicals. However, they may fail in applications involving aggressive chemicals or extreme temperatures.
Considerations for International Buyers: Buyers should ensure compliance with local standards such as ASTM or DIN. In regions like Europe, the preference for eco-friendly materials is increasing, which can influence material choices.
How Do Metal Gaskets Perform in High-Pressure Applications?
Metal gaskets are designed for high-pressure and high-temperature environments, making them suitable for demanding applications. Their key properties include:
- Temperature/Pressure Rating: Can withstand temperatures up to 1,200°F (650°C) and pressures exceeding 5,000 psi.
- Corrosion Resistance: Varies by metal type; stainless steel offers good resistance, while carbon steel may corrode quickly.
Pros: Metal gaskets are durable and can handle extreme conditions, making them suitable for critical applications in industries like oil and gas.
Cons: They can be more expensive and complex to manufacture. Installation requires careful handling to avoid damage.
Impact on Application: Metal gaskets are commonly used in high-performance engines, pressure vessels, and heat exchangers where reliability is paramount.
Considerations for International Buyers: Compliance with industry standards is crucial. Buyers in the Middle East and Africa should be aware of the specific environmental conditions that may affect metal performance, such as humidity and temperature fluctuations.
What Advantages Do Composite Gaskets Offer?
Composite gaskets combine materials like rubber and metal to leverage the benefits of both. Their properties include:
- Temperature/Pressure Rating: Generally rated for moderate temperatures and pressures, typically up to 400°F (204°C) and 1,500 psi.
- Corrosion Resistance: Excellent resistance to a wide range of chemicals, depending on the composite materials used.
Pros: They provide a good balance of flexibility and strength, making them versatile for various applications.
Cons: Composite gaskets can be more expensive than rubber gaskets and may require more complex manufacturing processes.
Impact on Application: Ideal for applications where both flexibility and strength are required, such as in automotive and industrial machinery.
Considerations for International Buyers: Buyers should check for certifications that verify the performance of composite materials, especially in regions with strict compliance regulations like Europe.
Why Are PTFE Gaskets Preferred for Chemical Applications?
Polytetrafluoroethylene (PTFE) gaskets are known for their exceptional chemical resistance. Key properties include:
- Temperature/Pressure Rating: Can withstand temperatures up to 500°F (260°C) and pressures up to 3,000 psi.
- Corrosion Resistance: Highly resistant to almost all chemicals, making them ideal for aggressive environments.
Pros: PTFE gaskets are non-reactive and provide excellent sealing capabilities, making them suitable for a wide range of applications.
Cons: They can be more expensive and may require specialized manufacturing techniques.
Impact on Application: PTFE gaskets are commonly used in the pharmaceutical, food processing, and chemical industries where contamination is a concern.
Considerations for International Buyers: Buyers should ensure that PTFE gaskets meet relevant food safety and chemical compliance standards, particularly in Europe and North America.
Summary Table of Gasket Materials
Material | Typical Use Case for Gasket Manufacturers | Key Advantage | Key Disadvantage/Limitation | Relative Cost (Low/Med/High) |
---|---|---|---|---|
Rubber | Water and air sealing applications | Cost-effective and easy to manufacture | Limited lifespan in harsh conditions | Low |
Metal | High-pressure and high-temperature setups | Extremely durable and reliable | Higher cost and complex installation | High |
Composite | Automotive and industrial machinery | Balance of flexibility and strength | More expensive and complex to manufacture | Medium |
PTFE | Chemical processing and food industries | Excellent chemical resistance | Higher cost and specialized manufacturing | High |
This guide provides a comprehensive overview of the most common gasket materials, helping international B2B buyers make informed decisions based on their specific needs and regional compliance requirements.
In-depth Look: Manufacturing Processes and Quality Assurance for Gasket Manufacturers
What Are the Typical Manufacturing Processes for Gasket Manufacturers?
The manufacturing of gaskets involves a series of well-defined stages, each critical to ensuring the final product meets industry standards and customer specifications. The main stages include material preparation, forming, assembly, and finishing.
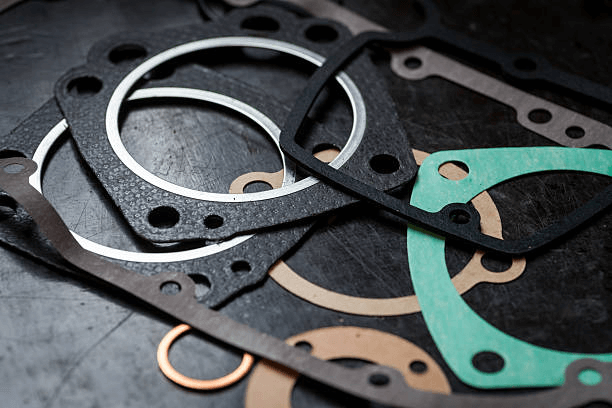
A stock image related to Gasket Manufacturers.
How is Material Prepared in Gasket Manufacturing?
The first step in gasket manufacturing is material preparation. This involves selecting the appropriate raw materials, which can range from rubber, silicone, and metal to composite materials. Gasket manufacturers must consider factors such as temperature resistance, pressure tolerance, and chemical compatibility when choosing materials.
Once the materials are selected, they undergo processes like cutting, shredding, or grinding to achieve the desired size and texture. This preparation is essential for ensuring that the materials can be easily shaped and bonded during the forming stage.
What Forming Techniques Are Commonly Used in Gasket Production?
Forming is a critical stage where the prepared materials are transformed into gasket shapes. Common techniques include:
-
Die Cutting: This method uses a die to cut gaskets from sheets of material. It’s ideal for high-volume production and allows for precise shapes and sizes.
-
Compression Molding: Here, raw materials are placed into a heated mold, where they are compressed under pressure. This technique is particularly effective for rubber and silicone gaskets, providing consistent thickness and density.
-
Extrusion: This process involves forcing material through a shaped die to create continuous lengths of gasket material. It’s suitable for creating gaskets with complex profiles.
-
Waterjet Cutting: This technique uses high-pressure water to cut materials, allowing for intricate designs without affecting the material’s integrity. It is particularly useful for composite gaskets.
How is Assembly Conducted in Gasket Manufacturing?
After forming, gaskets often require assembly, particularly if they consist of multiple components or require additional features like adhesives or coatings. Assembly may involve the use of bonding agents or mechanical fasteners, depending on the design specifications. Ensuring that the assembly process is consistent is crucial for maintaining gasket integrity and performance.
What Finishing Processes Are Important for Gaskets?
Finishing processes enhance the functional and aesthetic qualities of gaskets. This stage may include:
-
Surface Treatment: Processes such as coating or texturing can improve adhesion and reduce wear.
-
Quality Inspection: This is a critical aspect of the finishing process, where gaskets are checked for defects and compliance with specifications.
-
Packaging: Proper packaging is essential for protecting gaskets during transportation and storage, preventing any damage that could compromise their performance.
What Quality Assurance Measures Are Critical for Gasket Manufacturers?
Quality assurance (QA) in gasket manufacturing is paramount to ensure that products meet international standards and customer requirements.
Which International Standards Should Gasket Manufacturers Adhere To?
Gasket manufacturers often comply with various international standards to assure quality and safety. Some key standards include:
-
ISO 9001: This is the most recognized quality management system standard. It ensures that organizations meet customer and regulatory requirements consistently.
-
CE Marking: This indicates compliance with European health, safety, and environmental protection standards, particularly important for buyers in Europe.
-
API Standards: The American Petroleum Institute (API) sets specific standards for gaskets used in the oil and gas industry, focusing on performance and reliability.
What Are the Key Quality Control Checkpoints?
Quality control (QC) involves several critical checkpoints throughout the manufacturing process:
-
Incoming Quality Control (IQC): This initial step involves inspecting raw materials for conformity to specifications before they enter production.
-
In-Process Quality Control (IPQC): During the manufacturing process, periodic checks are conducted to ensure that the production process adheres to quality standards.
-
Final Quality Control (FQC): After the gaskets are completed, they undergo final inspections and testing to verify their performance and compliance with specifications.
Which Testing Methods Are Commonly Used in Gasket Quality Assurance?
Common testing methods for gaskets include:
-
Compression Set Testing: This measures how much a gasket deforms under sustained compression, ensuring it can maintain its sealing properties over time.
-
Leak Testing: This involves subjecting gaskets to pressure or vacuum to detect any leaks, ensuring their reliability in applications.
-
Thermal and Chemical Resistance Testing: These tests evaluate how well gaskets can withstand extreme temperatures and exposure to various chemicals, which is vital for applications in industries such as automotive and oil and gas.
How Can B2B Buyers Verify Supplier Quality Control?
International B2B buyers must take proactive steps to verify the quality control processes of gasket manufacturers. Here are some actionable insights:
What Steps Should Buyers Take for Supplier Audits?
-
Conduct Audits: Regular audits of potential suppliers can provide firsthand insight into their manufacturing processes and quality control measures. This includes checking for certifications, equipment, and adherence to international standards.
-
Request Documentation: Buyers should request quality assurance documentation, including inspection reports, compliance certifications, and material safety data sheets. This information helps assess the reliability of the supplier.
-
Utilize Third-Party Inspections: Engaging third-party inspection services can provide an objective evaluation of the supplier’s quality control processes and product integrity.
What Are the Nuances of QC and Certification for International Buyers?
For buyers from Africa, South America, the Middle East, and Europe, understanding the nuances of quality control and certification is essential.
-
Regulatory Compliance: Buyers should be aware of the specific regulations and standards applicable in their region, such as the European Union’s REACH regulations or local industry standards.
-
Cultural Considerations: Different regions may have varying expectations regarding quality and certification processes. Understanding these cultural nuances can help buyers communicate effectively and establish strong supplier relationships.
-
Supply Chain Transparency: Buyers should prioritize suppliers who demonstrate transparency in their manufacturing and quality control processes. This includes clear communication about sourcing materials and compliance with environmental and social standards.
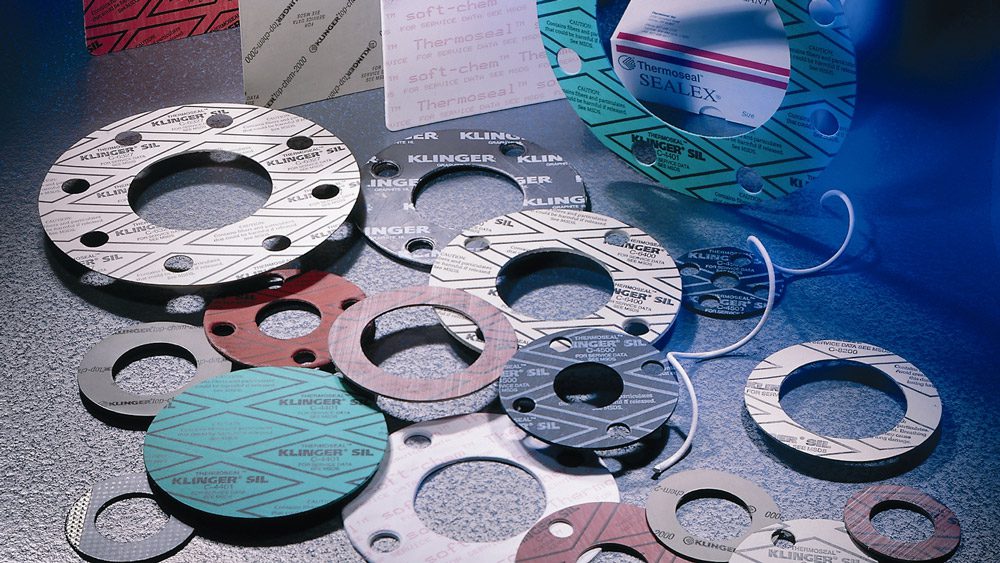
A stock image related to Gasket Manufacturers.
By understanding the manufacturing processes and quality assurance measures associated with gasket production, international B2B buyers can make informed decisions, ensuring they select suppliers that meet their quality expectations and regulatory requirements.
Practical Sourcing Guide: A Step-by-Step Checklist for ‘Gasket Manufacturers’
To successfully procure gaskets from manufacturers, international B2B buyers must navigate a series of essential steps. This guide outlines a practical checklist to ensure that buyers from Africa, South America, the Middle East, and Europe can make informed decisions that align with their specific requirements.
Step 1: Define Your Technical Specifications
Clearly outlining your technical requirements is the first step in sourcing gaskets. Consider factors such as material type, size, thickness, and specific applications (e.g., automotive, industrial machinery). Precise specifications help suppliers understand your needs, reducing the risk of receiving incorrect products.
- Material Considerations: Determine whether you need rubber, metal, or composite gaskets based on environmental conditions and application requirements.
- Performance Standards: Specify any industry standards or certifications required for compliance.
Step 2: Research and Shortlist Potential Manufacturers
Conduct thorough research to identify potential gasket manufacturers that meet your criteria. Utilize online directories, industry associations, and trade shows to compile a list of reputable suppliers.
- Global Reach: Consider manufacturers with experience in international shipping, particularly those familiar with customs regulations in your target markets.
- Customer Reviews: Look for testimonials and case studies from previous clients to gauge reliability and quality.
Step 3: Verify Supplier Certifications
Before proceeding, ensure that the manufacturers hold the necessary certifications relevant to your industry. This could include ISO certifications, quality management, and environmental standards.
- Quality Assurance: Certifications can indicate a commitment to quality and adherence to international standards, which is crucial for safety-critical applications.
- Sustainability Practices: Check if the supplier follows sustainable practices, which can be increasingly important in global supply chains.
Step 4: Request Samples for Evaluation
Once you have narrowed down your options, request samples from potential suppliers. This allows you to assess the quality and suitability of their gaskets before making a bulk order.
- Performance Testing: Evaluate the samples under actual working conditions to ensure they meet your performance standards.
- Compatibility Checks: Confirm that the samples fit seamlessly into your existing systems or components.
Step 5: Discuss Pricing and Payment Terms
Engage in discussions about pricing, payment options, and delivery timelines with shortlisted manufacturers. Transparency at this stage is essential to avoid misunderstandings later.
- Negotiation: Be prepared to negotiate terms that suit both parties, considering factors like order volume and long-term partnership potential.
- Payment Security: Discuss payment methods that offer security, such as letters of credit or escrow services, especially for larger transactions.
Step 6: Establish Communication Channels
Effective communication is key to a successful partnership. Establish clear lines of communication with the chosen manufacturer to facilitate ongoing discussions about production updates, delivery schedules, and any potential issues.
- Language Considerations: Ensure that language barriers are addressed to avoid miscommunication.
- Regular Updates: Set expectations for regular updates on production progress, especially for large or custom orders.
Step 7: Finalize the Agreement and Place Your Order
After all evaluations and negotiations are complete, finalize the contract with your chosen manufacturer. Ensure that all terms discussed are documented, including delivery timelines, warranty conditions, and after-sales support.
- Legal Review: Consider having a legal expert review the agreement to ensure it protects your interests.
- Order Confirmation: Confirm the order in writing, detailing quantities, specifications, and expected delivery dates.
By following this checklist, B2B buyers can streamline the sourcing process for gasket manufacturers, ensuring they select the right partners for their operational needs while minimizing risks associated with international procurement.
Comprehensive Cost and Pricing Analysis for Gasket Manufacturers Sourcing
What Are the Key Cost Components in Gasket Manufacturing?
When sourcing gaskets, international B2B buyers must understand the various cost components that contribute to the overall pricing. The primary cost elements include:
-
Materials: The choice of materials significantly impacts costs. Common materials for gaskets include rubber, silicone, and metal. High-performance materials or specialized composites may increase costs but offer better durability and performance.
-
Labor: Labor costs vary by region. In countries with lower labor costs, such as some in Africa and South America, manufacturers can provide competitive pricing. However, in regions like Europe, labor costs are typically higher, which can reflect in the final price.
-
Manufacturing Overhead: This includes the costs associated with running the facility, such as utilities, rent, and equipment maintenance. Efficient manufacturing processes can help reduce overhead and ultimately lower costs.
-
Tooling: Custom tooling for specific gasket designs can add to initial costs. Buyers should consider whether their designs require specialized tools, which could influence both the upfront investment and lead times.
-
Quality Control (QC): Ensuring quality through rigorous testing and inspection processes is essential in gasket manufacturing. Comprehensive QC processes may raise costs but are necessary for maintaining product reliability.
-
Logistics: Transportation costs can vary significantly based on the shipping method, distance, and logistics partners. Buyers should evaluate the total logistics cost, especially for international shipping.
-
Margin: Manufacturers will typically add a profit margin on top of the cumulative costs. This margin can vary based on the supplier’s market positioning and the competitive landscape.
How Do Price Influencers Affect Gasket Pricing?
Several factors influence the pricing of gaskets, and understanding these can aid in negotiating better deals:
-
Volume and Minimum Order Quantity (MOQ): Higher order volumes often lead to lower per-unit costs. Buyers should negotiate MOQs to maximize savings, especially when dealing with manufacturers in regions with lower production costs.
-
Specifications and Customization: Customized gaskets tailored to specific applications generally cost more than standard products. Buyers should weigh the benefits of customization against the additional costs.
-
Material Selection: The choice of materials directly influences price. High-quality materials may incur higher initial costs but can lead to lower maintenance and replacement costs over time.
-
Quality and Certifications: Gaskets with industry-specific certifications or higher quality standards may command higher prices. However, investing in certified products can prevent costly failures in critical applications.
-
Supplier Factors: The reputation and experience of the supplier can also affect pricing. Established suppliers may charge a premium for their reliability and quality assurance.
-
Incoterms: Understanding the terms of trade can help buyers manage logistics costs effectively. Different Incoterms may shift responsibilities and costs between the buyer and seller, impacting the overall price.
What Are the Best Tips for Negotiating Gasket Prices?
For international B2B buyers, particularly from regions like Africa, South America, the Middle East, and Europe, negotiating effectively can lead to significant cost savings:
-
Understand Total Cost of Ownership (TCO): Beyond the initial price, consider the long-term costs associated with the gasket, including maintenance, installation, and potential downtime. A lower upfront cost may not always translate to better value.
-
Leverage Volume Discounts: If possible, consolidate orders to take advantage of bulk pricing. Discussing future orders can also create leverage during negotiations.
-
Conduct Market Research: Understanding market rates for similar gaskets can empower buyers during negotiations. Comparisons can help establish realistic pricing expectations.
-
Establish Long-Term Relationships: Building a rapport with suppliers can lead to better terms and pricing. Suppliers are often more willing to negotiate with buyers they trust.
-
Be Prepared to Walk Away: If negotiations stall, be prepared to seek alternatives. This can sometimes encourage suppliers to offer better pricing or terms.
Disclaimer on Pricing
Prices for gaskets can vary widely based on numerous factors, including the specifics of the order, supplier location, and current market conditions. Buyers should conduct thorough research and consult multiple suppliers to ensure they receive competitive and fair pricing.
Alternatives Analysis: Comparing Gasket Manufacturers With Other Solutions
When evaluating gasket solutions, it’s essential for B2B buyers to consider various alternatives that can meet their specific industrial requirements. Gaskets play a crucial role in preventing leaks and ensuring efficient operation in many applications. However, there are other technologies and methods that can serve similar purposes. This analysis will compare gasket manufacturers against two viable alternatives: sealing compounds and metal seals.
Comparison Aspect | Gasket Manufacturers | Sealing Compounds | Metal Seals |
---|---|---|---|
Performance | Reliable under various pressures and temperatures, good chemical resistance | Offers flexibility and can fill gaps; performance varies with application | High durability and strength; excellent for high-pressure applications |
Cost | Moderate to high initial costs depending on material | Generally low cost, but may require more frequent replacement | Higher initial cost, but long-term savings due to durability |
Ease of Implementation | Requires precise installation; potential for complexity in custom designs | Easy to apply, often requiring minimal tools | Installation can be straightforward but may require specialized knowledge |
Maintenance | Typically low maintenance; longevity varies with material | May require regular checks and reapplication | Low maintenance due to durability; infrequent replacement needed |
Best Use Case | Ideal for standard applications in automotive, industrial machinery | Best for irregular surfaces and temporary seals | Suitable for extreme conditions and high-pressure environments |
What Are the Benefits and Drawbacks of Sealing Compounds as an Alternative to Gaskets?
Sealing compounds, such as silicone or polyurethane, offer a flexible solution for sealing gaps. They can easily conform to irregular surfaces, making them ideal for applications where traditional gaskets may struggle. However, while they are generally lower in cost and easy to apply, their performance can be inconsistent, particularly in high-temperature or high-pressure environments. Frequent reapplication may also be required, which could add to overall operational costs.
How Do Metal Seals Compare to Gasket Solutions?
Metal seals, including O-rings and C-rings, provide excellent durability and are particularly effective in high-pressure and extreme temperature applications. Their strength ensures a reliable seal, making them suitable for critical applications in sectors such as aerospace and oil and gas. However, the initial costs can be higher, and specialized installation techniques may be required. While maintenance is low, metal seals can be less adaptable to irregular surfaces compared to gaskets or sealing compounds.
Conclusion: How Should B2B Buyers Choose the Right Sealing Solution?
When determining the best sealing solution, B2B buyers must consider their specific operational needs, including the nature of the application, environmental conditions, and budget constraints. Gasket manufacturers are ideal for standard applications where reliability and longevity are crucial. Sealing compounds provide flexibility for irregular surfaces but may require more frequent maintenance. Metal seals are suited for high-stress environments but come with higher initial costs. By evaluating these factors, international buyers can make informed decisions that align with their operational requirements and cost-effectiveness.
Essential Technical Properties and Trade Terminology for Gasket Manufacturers
What Are the Essential Technical Properties for Gasket Manufacturers?
In the gasket manufacturing industry, understanding specific technical properties is crucial for ensuring product performance and compliance with industry standards. Below are some critical specifications that B2B buyers should consider when sourcing gaskets.
1. Material Grade: What Should You Know?
Material grade defines the quality and suitability of the gasket for specific applications. Common materials include rubber, silicone, graphite, and metal. For example, silicone gaskets are excellent for high-temperature applications, while rubber gaskets provide good sealing for general use. Understanding material grade helps buyers select gaskets that meet environmental and operational requirements, thereby reducing the risk of failure and ensuring longevity.
2. Tolerance: How Does It Impact Performance?
Tolerance refers to the permissible limit of variation in a gasket’s dimensions. Gaskets must fit precisely within the mechanical assembly to ensure an effective seal. Tighter tolerances typically lead to better sealing performance but may increase manufacturing costs. Buyers should evaluate the tolerance levels required for their specific applications to balance performance with budget constraints.
3. Compression Set: Why Is It Important?
The compression set is a measure of a gasket’s ability to return to its original thickness after being compressed. A low compression set indicates that the gasket can maintain its sealing properties over time, even under pressure and temperature changes. Buyers must assess the compression set to ensure that the gasket will not lead to leaks or failures in critical applications.
4. Temperature Resistance: What Are the Limits?
Temperature resistance indicates the range of temperatures a gasket can withstand without degrading. This property is especially important in industries such as automotive and aerospace, where gaskets are subjected to extreme conditions. Buyers should verify that the gasket material can handle the operational temperatures to avoid premature failure and ensure safety.
5. Chemical Compatibility: What Should You Consider?
Chemical compatibility is the ability of a gasket material to resist degradation when exposed to various chemicals and fluids. Depending on the application, gaskets may come into contact with oils, solvents, or other corrosive substances. It is vital for buyers to consult compatibility charts to ensure that the chosen gasket material will not react adversely with the fluids it will encounter.
What Are Common Trade Terms in Gasket Manufacturing?
Understanding industry jargon is essential for navigating the procurement process effectively. Here are some common terms that B2B buyers should be familiar with.
1. OEM (Original Equipment Manufacturer): What Does It Mean?
OEM refers to companies that manufacture products that are marketed under another company’s brand. In the gasket industry, OEM suppliers produce gaskets specifically designed for use in original equipment. Buyers often seek OEM gaskets for their reliability and compatibility with their machinery.
2. MOQ (Minimum Order Quantity): Why Is It Relevant?
MOQ signifies the minimum quantity of gaskets that a manufacturer is willing to produce or sell. This term is crucial for B2B buyers, as it affects inventory management and cost. Understanding the MOQ helps buyers determine if a supplier’s offerings align with their production needs and budget.
3. RFQ (Request for Quotation): How Should You Use It?
An RFQ is a document issued by a buyer to solicit price quotes from suppliers for specific products or services. In gasket procurement, an RFQ can help clarify pricing, specifications, and delivery timelines, enabling buyers to make informed decisions.
4. Incoterms: What Are They and Why Do They Matter?
Incoterms, or International Commercial Terms, are standardized trade terms that define the responsibilities of buyers and sellers in international transactions. They clarify aspects such as shipping costs, insurance, and risk transfer. Understanding Incoterms is vital for B2B buyers engaged in international trade, as it helps mitigate misunderstandings and disputes.
5. Lead Time: How Does It Affect Your Procurement Process?
Lead time refers to the duration from placing an order to receiving the goods. In gasket manufacturing, lead times can vary based on material availability and production schedules. Buyers should consider lead times when planning their inventory to avoid disruptions in their operations.
By grasping these essential technical properties and trade terms, international B2B buyers can make informed decisions, ensuring they select the right gaskets for their specific needs while navigating the complexities of the supply chain effectively.
Navigating Market Dynamics and Sourcing Trends in the Gasket Manufacturers Sector
What Are the Current Market Dynamics for Gasket Manufacturers?
The gasket manufacturing sector is experiencing significant growth, driven by advancements in technology and increasing demand across various industries such as automotive, aerospace, and energy. As international B2B buyers from regions like Africa, South America, the Middle East, and Europe seek quality and reliable components, understanding these market dynamics becomes crucial. The global gasket market is projected to expand at a compound annual growth rate (CAGR) of over 5% through the next few years, fueled by the rise in infrastructure projects and a shift towards renewable energy sources.
Key trends influencing the market include the integration of digital technologies such as Industry 4.0, which enhances production efficiency and transparency. Smart manufacturing techniques and automation are being adopted to reduce lead times and improve quality control, making sourcing decisions more data-driven. Additionally, buyers are increasingly prioritizing suppliers that can offer flexible customization options to cater to specific application needs, particularly in regions with diverse industrial requirements like Egypt and Poland.
Furthermore, the geopolitical landscape is affecting sourcing strategies. Buyers are diversifying their supply chains to mitigate risks associated with single-source dependencies, especially in light of recent global disruptions. For B2B buyers, this means exploring partnerships with manufacturers that have robust logistic capabilities and a proven track record in international trade.
How Important Is Sustainability and Ethical Sourcing in the Gasket Industry?
Sustainability is becoming a pivotal concern in the gasket manufacturing sector, as environmental regulations tighten globally. Buyers are now more inclined to engage with suppliers who demonstrate a commitment to sustainable practices. This includes the utilization of eco-friendly materials, such as biodegradable elastomers and recyclable metals, which not only reduce environmental impact but also appeal to increasingly eco-conscious end consumers.
Ethical sourcing is equally critical, particularly in regions where labor practices may vary. B2B buyers are increasingly demanding transparency in the supply chain, looking for manufacturers that adhere to fair labor practices and possess relevant certifications such as ISO 14001 (Environmental Management) and ISO 45001 (Occupational Health and Safety). These certifications not only signify compliance with international standards but also enhance the credibility of suppliers in competitive markets.
Moreover, incorporating sustainability into sourcing strategies can yield significant long-term cost benefits. By opting for green materials and processes, companies can reduce waste and energy consumption, ultimately leading to lower operational costs and a stronger market position.
What Is the Historical Context of the Gasket Manufacturing Sector?
The gasket manufacturing industry has evolved considerably since its inception in the early 20th century, initially dominated by simple paper and rubber gaskets. With the advent of advanced materials such as PTFE and silicone, the industry has expanded to accommodate a variety of applications across sectors. The late 20th century saw a surge in automotive and aerospace industries, pushing manufacturers to innovate and improve gasket performance under extreme conditions.
Today, the focus is not only on material advancements but also on manufacturing processes. Techniques such as precision die-cutting and 3D printing are transforming how gaskets are produced, allowing for quicker turnaround times and greater customization. This historical evolution highlights the industry’s responsiveness to market demands, making it essential for B2B buyers to stay informed about both historical and emerging trends to make strategic sourcing decisions.
By understanding these dynamics, international buyers can better navigate the complexities of sourcing gaskets, ensuring they partner with manufacturers who align with their operational goals and ethical standards.
Frequently Asked Questions (FAQs) for B2B Buyers of Gasket Manufacturers
-
How do I choose the right gasket manufacturer for my needs?
Choosing the right gasket manufacturer involves evaluating several key factors. Start by assessing the manufacturer’s experience and expertise in your specific industry. Look for certifications that indicate quality standards, such as ISO 9001. Additionally, consider their ability to customize products to meet your specifications. Review customer testimonials and case studies to gauge their reliability and service quality. Finally, check their production capacity to ensure they can meet your order volume and delivery timelines. -
What types of gaskets are most commonly used in industrial applications?
The most common types of gaskets used in industrial applications include rubber gaskets, metal gaskets, and composite gaskets. Rubber gaskets are versatile and suitable for a range of sealing applications, particularly in low-pressure environments. Metal gaskets, often made from materials like stainless steel, are used in high-temperature and high-pressure situations. Composite gaskets combine materials for enhanced performance and are ideal for demanding applications. Understanding the specific requirements of your application will help you select the appropriate gasket type. -
What should I consider when evaluating gasket manufacturers for international trade?
When evaluating gasket manufacturers for international trade, consider their compliance with international quality standards and regulations. Investigate their experience in exporting to your region, as this can affect logistics and delivery times. Assess their ability to communicate effectively in your preferred language, which is crucial for addressing any issues that may arise. Additionally, review their payment terms and shipping options to ensure they align with your budget and timeline. -
How can I ensure the quality of gaskets from international suppliers?
To ensure the quality of gaskets from international suppliers, request samples for testing before placing a larger order. Establish clear quality assurance protocols that the manufacturer must follow, including documentation of compliance with relevant industry standards. Regular audits and inspections during the production process can also help maintain quality. Consider working with third-party inspection services to verify that the gaskets meet your specifications and are free from defects.
-
What are the typical minimum order quantities (MOQs) for gasket manufacturers?
Minimum order quantities (MOQs) for gasket manufacturers can vary widely depending on the type of gasket, material, and complexity of the design. Generally, MOQs can range from a few hundred to several thousand units. It’s essential to discuss your needs with the manufacturer to determine if they can accommodate smaller orders, especially for custom gaskets. Some manufacturers may offer flexibility on MOQs for first-time buyers or trial orders. -
What payment terms should I expect when dealing with gasket manufacturers?
Payment terms when dealing with gasket manufacturers can vary, but common practices include upfront deposits of 30-50% before production, with the balance due upon completion or prior to shipment. Some manufacturers may offer net payment terms, allowing a certain period (e.g., 30 or 60 days) after delivery for payment. It’s crucial to establish clear payment terms in your contract to avoid misunderstandings. Always verify the manufacturer’s accepted payment methods, such as bank transfers, letters of credit, or online payment platforms. -
How can I communicate my customization needs effectively to gasket manufacturers?
Effective communication of your customization needs to gasket manufacturers starts with providing detailed specifications, including dimensions, materials, and performance requirements. Utilize technical drawings or CAD models to illustrate your requirements clearly. It’s also beneficial to discuss any specific applications or environments in which the gaskets will be used, as this can affect material choices and design features. Regular follow-ups and feedback during the design phase can help ensure that the final product meets your expectations. -
What logistics considerations should I keep in mind when sourcing gaskets internationally?
When sourcing gaskets internationally, consider logistics factors such as shipping methods, lead times, and customs regulations. Choose a shipping method that balances cost and delivery speed, such as air freight for urgent orders or sea freight for larger shipments. Familiarize yourself with customs requirements in your country to prevent delays at the border. Additionally, work with a reliable freight forwarder who can assist with documentation and ensure smooth transportation of your goods.
Important Disclaimer & Terms of Use
⚠️ Important Disclaimer
The information provided in this guide, including content regarding manufacturers, technical specifications, and market analysis, is for informational and educational purposes only. It does not constitute professional procurement advice, financial advice, or legal advice.
While we have made every effort to ensure the accuracy and timeliness of the information, we are not responsible for any errors, omissions, or outdated information. Market conditions, company details, and technical standards are subject to change.
B2B buyers must conduct their own independent and thorough due diligence before making any purchasing decisions. This includes contacting suppliers directly, verifying certifications, requesting samples, and seeking professional consultation. The risk of relying on any information in this guide is borne solely by the reader.
Strategic Sourcing Conclusion and Outlook for Gasket Manufacturers
What Are the Key Takeaways for Strategic Sourcing in Gasket Manufacturing?
In conclusion, effective strategic sourcing remains pivotal for B2B buyers in the gasket manufacturing sector. Understanding the nuances of gasket structures, such as the emerging Gasket design, can significantly enhance product performance and customer satisfaction. Buyers should prioritize suppliers that demonstrate a commitment to quality and innovation, as these factors directly influence the longevity and efficiency of gaskets in various applications.
How Can International Buyers Leverage Strategic Sourcing for Competitive Advantage?
International buyers, particularly from Africa, South America, the Middle East, and Europe, are encouraged to conduct thorough market research to identify suppliers that not only meet technical specifications but also align with sustainable practices. Engaging in partnerships that prioritize transparency and responsiveness will facilitate smoother transactions and foster long-term relationships.
What Is the Future Outlook for Gasket Manufacturers?
As the global demand for high-quality gaskets continues to rise, staying ahead of industry trends and technological advancements will be crucial. Embrace this opportunity to innovate your sourcing strategies, positioning your business for future success. Act now to secure partnerships that will drive growth and resilience in an increasingly competitive marketplace.