Discover Top Assembly Cable Manufacturers: Your Essential Guide (2025)
Introduction: Navigating the Global Market for assembly cable manufacturers,assembly cable
In today’s interconnected world, sourcing high-quality assembly cables can be a daunting task for international B2B buyers, particularly those operating from regions like Africa, South America, the Middle East, and Europe. The challenge lies not only in identifying reliable assembly cable manufacturers but also in understanding the diverse applications and specifications that these cables must meet to ensure optimal performance in various industries. This guide aims to demystify the process, providing a comprehensive overview of assembly cables, including their types, applications, and critical factors for supplier vetting.
Navigating the global market requires informed purchasing decisions, especially when dealing with the nuances of different regions and their specific needs. This guide equips buyers with essential insights into evaluating potential suppliers, understanding cost implications, and recognizing quality standards that align with their operational requirements. Whether you are a procurement manager in Colombia seeking sustainable solutions or a technical director in Nigeria looking for advanced cable technologies, this resource will empower you to make strategic choices that enhance your supply chain efficiency.
By addressing key challenges and offering actionable recommendations, this guide serves as an indispensable tool for international B2B buyers. It will help streamline the sourcing process, ultimately leading to better procurement outcomes and improved operational efficiency in your projects.
Understanding assembly cable manufacturers,assembly cable Types and Variations
Type Name | Key Distinguishing Features | Primary B2B Applications | Brief Pros & Cons for Buyers |
---|---|---|---|
Custom Assembly Cables | Tailored to specific requirements; varied lengths and connectors | Aerospace, Automotive, Industrial | Pros: High adaptability, precise fit. Cons: Longer lead times, potentially higher costs. |
Standard Assembly Cables | Pre-manufactured, widely available; less customization | Consumer Electronics, IT, Telecommunications | Pros: Cost-effective, quick delivery. Cons: Limited customization, may not meet specific needs. |
Industrial Assembly Cables | Durable materials; resistance to harsh environments | Manufacturing, Robotics, Heavy Equipment | Pros: High durability, reliability. Cons: May be over-engineered for lighter applications. |
High-Performance Assembly Cables | Enhanced conductivity; specialized insulation | Medical Devices, Telecommunications, Aerospace | Pros: Superior performance, reduced signal loss. Cons: Higher cost, may require specialized installation. |
Multi-Purpose Assembly Cables | Versatile designs for various applications | General Manufacturing, Construction, HVAC | Pros: Flexibility, broad application range. Cons: May compromise on performance for specific tasks. |
What Are the Characteristics of Custom Assembly Cables?
Custom assembly cables are specifically designed to meet unique specifications of various industries, including aerospace and automotive. They can be tailored in terms of length, gauge, and connector types, making them ideal for applications requiring a precise fit. When purchasing custom cables, B2B buyers should consider lead times and potential costs, as these can be higher than standard options. Additionally, ensuring that the manufacturer has a robust quality assurance process is vital to avoid performance issues.
How Do Standard Assembly Cables Compare?
Standard assembly cables are mass-produced and readily available, making them a popular choice for consumer electronics and IT applications. Their key features include cost-effectiveness and quick delivery, allowing businesses to maintain inventory without significant investment. However, buyers should be cautious about the limitations in customization, as standard cables may not fulfill specific operational requirements. Evaluating compatibility with existing systems is crucial to ensure seamless integration.
What Makes Industrial Assembly Cables Suitable for Harsh Environments?
Industrial assembly cables are constructed from robust materials designed to withstand harsh conditions, such as extreme temperatures and exposure to chemicals. They are commonly used in manufacturing and robotics, where durability and reliability are paramount. Buyers should assess the environment in which the cables will be used to ensure they select the right type. While industrial cables offer exceptional resilience, they may be over-engineered for lighter applications, leading to unnecessary expenses.
Why Choose High-Performance Assembly Cables?
High-performance assembly cables are engineered for optimal conductivity and reduced signal loss, making them suitable for sensitive applications like medical devices and telecommunications. These cables often feature specialized insulation to enhance performance. When considering high-performance options, buyers should weigh the benefits against the higher costs and ensure that their installation teams are equipped to handle any specialized requirements. The investment can lead to improved efficiency and reliability in critical applications.
What Are the Advantages of Multi-Purpose Assembly Cables?
Multi-purpose assembly cables are designed for versatility, allowing them to be used across various applications, including general manufacturing and HVAC systems. Their flexible design makes them a practical choice for businesses looking to simplify inventory management. However, buyers should be aware that while these cables offer a broad range of uses, they may not perform as well in specialized applications. Evaluating the specific needs of each application is essential to ensure optimal performance without compromising on quality.
Related Video: Types of Cables || Types of USB 🤓💯 #pctips #computerparts #computerknowledge #cable #usb #ytshorts
Key Industrial Applications of assembly cable manufacturers,assembly cable
Industry/Sector | Specific Application of assembly cable manufacturers,assembly cable | Value/Benefit for the Business | Key Sourcing Considerations for this Application |
---|---|---|---|
Automotive | Wiring harnesses for vehicle assembly | Enhances vehicle safety and reliability, reduces assembly time | Compliance with international automotive standards and certifications |
Industrial Automation | Control systems for machinery | Increases operational efficiency and reduces downtime | Need for high durability and resistance to environmental factors |
Telecommunications | Data transmission cables for telecom infrastructure | Supports high-speed communication and connectivity | Ensure compatibility with existing systems and scalability |
Renewable Energy | Cables for solar and wind energy installations | Facilitates sustainable energy solutions and reduces energy costs | Focus on flexibility and resistance to outdoor conditions |
Construction and Infrastructure | Power and data cables for smart buildings | Integrates advanced technology for energy management and security | Consider local regulations and standards for building materials |
How Are Assembly Cables Used in the Automotive Industry?
In the automotive sector, assembly cables are primarily utilized in wiring harnesses that connect various electronic components within vehicles. These cables ensure the efficient transmission of power and data, which is crucial for vehicle safety systems, entertainment features, and engine management. For international buyers, especially from regions like Africa and South America, it is essential to consider suppliers who comply with international automotive standards to ensure reliability and safety. Additionally, sourcing from manufacturers who can provide custom solutions tailored to specific vehicle models can significantly enhance production efficiency.
What Role Do Assembly Cables Play in Industrial Automation?
Assembly cables are integral to control systems in industrial automation, where they connect sensors, actuators, and controllers within machinery. These cables facilitate communication and power distribution, leading to increased operational efficiency and minimized downtime. For buyers in the Middle East and Europe, it is vital to source cables that meet high durability standards, especially in environments subject to vibrations and temperature fluctuations. Additionally, understanding the specific requirements for cable shielding and insulation can help mitigate electromagnetic interference, further enhancing system performance.
How Are Assembly Cables Essential in Telecommunications?
In telecommunications, assembly cables are crucial for establishing data transmission pathways in telecom infrastructure. They support high-speed internet and mobile connectivity, which are essential for modern communication systems. International buyers, particularly from South America and Africa, should focus on sourcing cables that offer high bandwidth capabilities and are compliant with local and international standards. Ensuring compatibility with existing networks and future scalability is key to optimizing investments in telecommunications infrastructure.
What Benefits Do Assembly Cables Provide in Renewable Energy?
Assembly cables are vital in renewable energy applications, particularly in solar and wind energy installations. They connect various components such as inverters, batteries, and energy storage systems, facilitating efficient energy transfer. For buyers in regions like Europe, where renewable energy is a growing sector, sourcing cables that are flexible and resistant to harsh outdoor conditions is critical. This not only ensures longevity but also enhances the overall efficiency of energy systems, contributing to reduced operational costs.
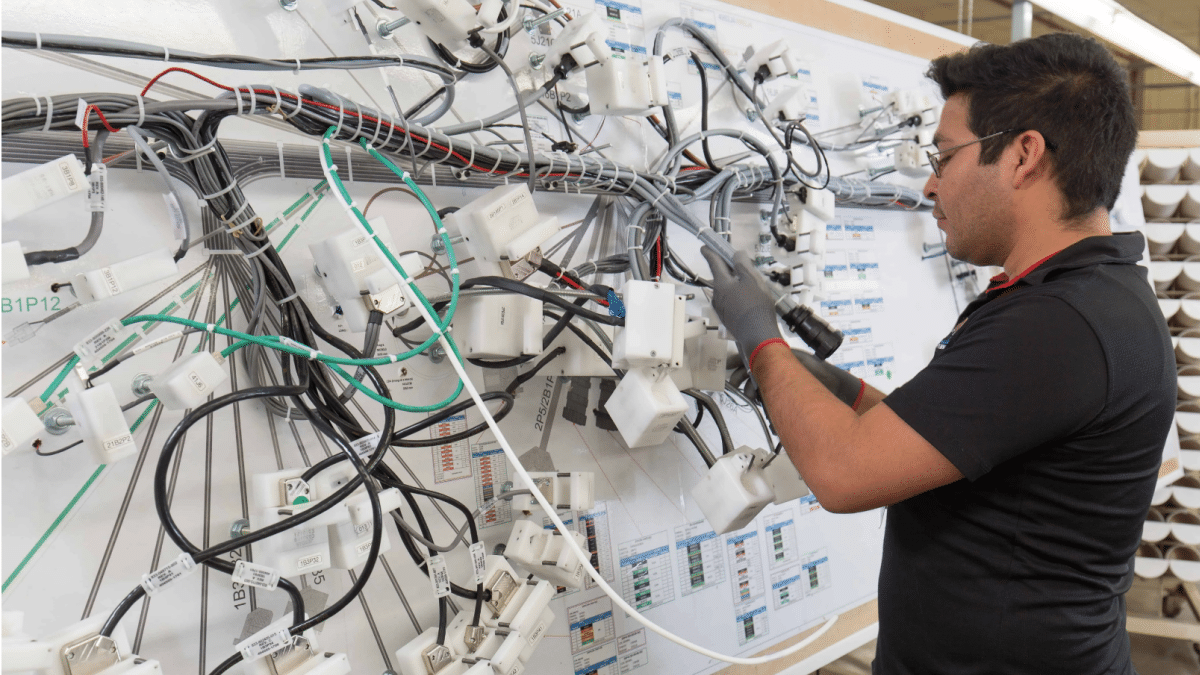
A stock image related to assembly cable manufacturers,assembly cable.
Why Are Assembly Cables Important in Construction and Infrastructure?
In the construction and infrastructure sector, assembly cables are used for powering and data transmission in smart buildings. These cables enable the integration of advanced technologies for energy management, security systems, and communication networks. Buyers in Africa and the Middle East should consider local regulations and standards when sourcing these cables to ensure compliance and safety. Additionally, opting for cables that can withstand environmental challenges common in construction sites can lead to reduced maintenance costs and increased operational efficiency.
3 Common User Pain Points for ‘assembly cable manufacturers,assembly cable’ & Their Solutions
Scenario 1: Inconsistent Quality in Assembly Cables
The Problem:
One of the most prevalent issues faced by B2B buyers in industries such as automotive or electronics is the inconsistency in the quality of assembly cables. Buyers often receive products that do not meet the required specifications, leading to production delays and increased costs. This inconsistency can arise from variations in manufacturing processes, inadequate quality control measures, or differences in raw materials used by assembly cable manufacturers. For international buyers, especially those in regions like Africa and South America, where local suppliers may not have stringent quality assurance protocols, this problem can be even more pronounced.
The Solution:
To mitigate the risks associated with quality inconsistencies, B2B buyers should establish clear quality standards and specifications before engaging with manufacturers. It’s crucial to request samples and conduct thorough inspections before committing to larger orders. Implementing a supplier evaluation process that includes audits of manufacturing practices can also help ensure that the assembly cable manufacturer adheres to the necessary quality standards. Additionally, consider partnering with manufacturers that possess international certifications (such as ISO 9001) to enhance trust in their quality assurance processes.
Scenario 2: Long Lead Times Affecting Production Schedules
The Problem:
Another significant challenge for B2B buyers is managing long lead times for assembly cable deliveries. In sectors like telecommunications and automotive, timely access to components is critical. Buyers may experience delays due to manufacturers’ production schedules, shipping logistics, or unexpected demand spikes. Such delays can disrupt entire production lines, leading to financial losses and damaged relationships with end customers.
The Solution:
To address lead time issues, B2B buyers should develop a robust forecasting system that accurately predicts demand based on historical data and market trends. Engaging with assembly cable manufacturers who offer flexible production capabilities can also be beneficial. Consider establishing a just-in-time (JIT) inventory system to minimize the impact of lead times on operations. Regular communication with suppliers regarding inventory levels and production timelines can foster better relationships and prompt updates, allowing buyers to adjust their production schedules accordingly.
Scenario 3: Limited Customization Options for Specific Applications
The Problem:
B2B buyers often encounter challenges when seeking assembly cables that meet specific application requirements. Standardized products may not suit unique applications in industries such as renewable energy or medical devices, leading to compromised performance or safety issues. Buyers, especially those from diverse regions like the Middle East and Europe, may find that local suppliers lack the capability to provide customized solutions that align with their needs.
The Solution:
To overcome the limitations of standard offerings, B2B buyers should proactively communicate their specific requirements to assembly cable manufacturers. This includes detailing the technical specifications, environmental conditions, and compliance standards relevant to their applications. Engaging with manufacturers that have a proven track record of customization can lead to more tailored solutions. Additionally, leveraging technology such as CAD (Computer-Aided Design) can facilitate better collaboration between buyers and manufacturers, ensuring that the final product aligns with the exact specifications needed for optimal performance.
By addressing these common pain points with actionable strategies, international B2B buyers can significantly enhance their procurement processes and build stronger relationships with assembly cable manufacturers.
Strategic Material Selection Guide for assembly cable manufacturers,assembly cable
What Are the Key Materials for Assembly Cable Manufacturers?
When selecting materials for assembly cables, manufacturers must consider various factors such as performance properties, cost, and application suitability. Here, we analyze four common materials used in assembly cable manufacturing: copper, aluminum, polyvinyl chloride (PVC), and thermoplastic elastomers (TPE). Each material has unique properties that can significantly impact the end product’s performance and suitability for specific applications.
How Does Copper Perform in Assembly Cable Applications?
Copper is one of the most widely used materials in electrical assembly cables due to its excellent electrical conductivity and thermal properties. It typically has a temperature rating of up to 200°C and can withstand high pressures.
Pros: Copper cables are known for their durability and reliability, making them suitable for high-performance applications. They also exhibit good corrosion resistance, especially when coated or alloyed.
Cons: The primary drawback of copper is its cost, which can be significantly higher than alternatives like aluminum. Additionally, copper is heavier, which may not be suitable for applications requiring lightweight materials.
Impact on Application: Copper’s superior conductivity makes it ideal for applications in telecommunications and power distribution, where efficiency is paramount.
Considerations for International Buyers: Buyers from regions such as Africa and South America should ensure compliance with local electrical standards, such as IEC or ANSI, which often specify copper for high-performance applications.
What Are the Advantages of Aluminum in Assembly Cables?
Aluminum is another popular choice for assembly cables, particularly in large-scale applications like overhead power lines.
Pros: Aluminum is lightweight and cost-effective, offering a good balance of conductivity and mechanical strength. Its corrosion resistance is also notable, especially in outdoor applications.
Cons: While aluminum is less expensive, it has lower conductivity than copper, which may require larger wire sizes to achieve the same performance levels. This can complicate manufacturing and installation.
Impact on Application: Aluminum is commonly used in power transmission and distribution systems where weight and cost are critical factors.
Considerations for International Buyers: Buyers in regions like the Middle East should be aware of local standards such as ASTM and JIS that may influence material selection based on environmental conditions.
How Does PVC Contribute to Cable Assembly Performance?
Polyvinyl chloride (PVC) is a versatile thermoplastic widely used in insulation and jacketing for assembly cables.
Pros: PVC is cost-effective, offers good mechanical strength, and is resistant to many chemicals. It also provides excellent insulation properties, making it suitable for various electrical applications.
Cons: While PVC is durable, it has a limited temperature range (typically up to 70°C) and can become brittle over time, especially when exposed to UV light.
Impact on Application: PVC is ideal for indoor applications, including residential wiring and low-voltage cables.
Considerations for International Buyers: Compliance with local safety standards is crucial, as certain regions may have restrictions on the use of PVC due to environmental concerns.
What Role Do Thermoplastic Elastomers (TPE) Play in Cable Manufacturing?
Thermoplastic elastomers (TPE) are increasingly being used in assembly cables due to their flexibility and durability.
Pros: TPEs offer excellent elasticity and can withstand a wide temperature range (from -40°C to 120°C). They also provide good chemical resistance and are less prone to cracking.
Cons: The main limitation of TPE is its higher cost compared to PVC and other materials. Additionally, TPEs may not be suitable for high-temperature applications.
Impact on Application: TPE is often used in automotive and industrial applications where flexibility and resistance to harsh environments are essential.
Considerations for International Buyers: Buyers from Europe and Africa should consider the specific requirements of their applications, ensuring that TPEs meet relevant standards for safety and performance.
Summary Table of Material Selection for Assembly Cables
Material | Typical Use Case for assembly cable manufacturers,assembly cable | Key Advantage | Key Disadvantage/Limitation | Relative Cost (Low/Med/High) |
---|---|---|---|---|
Copper | Telecommunications, power distribution | Excellent conductivity and durability | High cost and weight | High |
Aluminum | Overhead power lines, large-scale applications | Lightweight and cost-effective | Lower conductivity requiring larger sizes | Medium |
Polyvinyl Chloride (PVC) | Indoor wiring, low-voltage applications | Cost-effective with good insulation properties | Limited temperature range and UV sensitivity | Low |
Thermoplastic Elastomers (TPE) | Automotive, industrial applications | Flexibility and wide temperature range | Higher cost and limited high-temperature suitability | Medium |
This strategic material selection guide provides international B2B buyers with essential insights to make informed decisions when sourcing assembly cables. Understanding the properties, advantages, and limitations of each material will help ensure optimal performance and compliance with regional standards.
In-depth Look: Manufacturing Processes and Quality Assurance for assembly cable manufacturers,assembly cable
What Are the Main Stages in the Manufacturing Process of Assembly Cables?
The manufacturing process for assembly cables involves several critical stages, each contributing to the final product’s quality and reliability. Understanding these stages can help international B2B buyers make informed decisions when selecting suppliers.
-
Material Preparation: This initial stage involves sourcing high-quality raw materials, including copper or aluminum conductors, insulation materials, and protective sheathing. Suppliers should demonstrate transparency in their sourcing practices, ideally utilizing materials that meet international standards to ensure durability and performance.
-
Forming: In this phase, the raw materials are shaped into the desired configurations. Techniques such as extrusion for insulation and molding for connectors are commonly employed. Buyers should inquire about the machinery used and the technological capabilities of the manufacturer, as advanced equipment often results in better precision and efficiency.
-
Assembly: The assembly process integrates all components into a cohesive unit. This step may involve soldering, crimping, or using advanced connection technologies. It is vital for buyers to verify that the manufacturer employs skilled labor and utilizes automated processes where applicable to minimize human error.
-
Finishing: The final stage includes testing, labeling, and packaging the assembly cables. Finishing processes may also involve applying coatings or treatments to enhance durability. Buyers should ensure that manufacturers have robust finishing processes that comply with relevant safety and quality standards.
How Is Quality Assurance Implemented in Assembly Cable Manufacturing?
Quality assurance (QA) is critical in the manufacturing of assembly cables, as it directly impacts product performance and safety. Here are key aspects of QA that B2B buyers should consider:
-
International Standards Compliance: Manufacturers should adhere to recognized international quality standards such as ISO 9001, which outlines requirements for a quality management system. Additionally, compliance with industry-specific standards, such as CE marking for European markets and API standards for oil and gas applications, can further assure buyers of product quality.
-
Quality Control Checkpoints: Effective quality control (QC) involves several checkpoints throughout the manufacturing process:
– Incoming Quality Control (IQC): This initial inspection assesses the quality of raw materials before they enter production.
– In-Process Quality Control (IPQC): Ongoing checks during the manufacturing process help identify and rectify issues in real-time.
– Final Quality Control (FQC): A comprehensive inspection of the final product ensures that it meets all specifications before shipping. -
Common Testing Methods: Manufacturers employ various testing methods to validate the performance and safety of assembly cables. These may include:
– Electrical Testing: Verifying conductivity and insulation resistance.
– Mechanical Testing: Assessing tensile strength and flexibility.
– Environmental Testing: Evaluating performance under extreme conditions (temperature, humidity, etc.).
How Can B2B Buyers Verify Supplier Quality Control Practices?
Ensuring that a supplier maintains high-quality standards is crucial for B2B buyers. Here are actionable steps to verify QC practices:
-
Supplier Audits: Conducting on-site audits allows buyers to assess the manufacturing processes, equipment, and QC protocols firsthand. This step is particularly important for buyers in Africa, South America, the Middle East, and Europe, where varying quality standards may exist.
-
Review of Quality Reports: Requesting detailed quality assurance reports can provide insights into the manufacturer’s QC history. These reports should include data on defect rates, inspection results, and compliance with standards.
-
Third-Party Inspections: Engaging independent inspection agencies can provide an unbiased evaluation of the supplier’s operations and quality practices. This is especially valuable for buyers unfamiliar with local manufacturing norms.
What Are the Quality Control and Certification Nuances for International B2B Buyers?
International buyers must navigate specific nuances in quality control and certification processes, which can vary significantly by region. Here are some considerations:
-
Regional Compliance Standards: Familiarize yourself with the specific compliance requirements in your target market. For instance, cables sold in Europe must meet stringent CE standards, while products for the Middle East may require different certifications.
-
Understanding Certification Processes: Some manufacturers may hold certifications that are not universally recognized. Buyers should verify that certifications are relevant to their market and that they can be independently verified.
-
Cultural and Regulatory Differences: Buyers from diverse regions like Africa and South America may encounter different expectations regarding quality and reliability. It’s essential to establish clear communication with suppliers to ensure mutual understanding of quality standards.
Conclusion: How Can International Buyers Enhance Their Supplier Selection Process?
By understanding the manufacturing processes and quality assurance protocols of assembly cable manufacturers, international B2B buyers can make more informed decisions. Prioritize suppliers who demonstrate commitment to quality through certifications, transparent practices, and robust QC checkpoints. Engaging in thorough supplier evaluations, including audits and third-party inspections, can further mitigate risks and ensure that the products meet the necessary performance and safety standards. This proactive approach is essential for fostering successful long-term partnerships in the assembly cable industry.
Practical Sourcing Guide: A Step-by-Step Checklist for ‘assembly cable manufacturers,assembly cable’
In the competitive world of assembly cable manufacturing, international B2B buyers must navigate a complex landscape to ensure they procure high-quality products that meet their specific needs. This guide provides a practical step-by-step checklist to streamline your sourcing process, especially for buyers from Africa, South America, the Middle East, and Europe.
Step 1: Define Your Technical Specifications
Before reaching out to potential suppliers, it’s crucial to clearly define your technical requirements for assembly cables. This includes understanding the type of cables you need, their specifications (e.g., length, gauge, insulation type), and any industry standards they must meet. A well-defined specification not only aids in accurate quotes but also helps in comparing products from different suppliers effectively.
Step 2: Research Potential Suppliers
Conduct thorough research to identify reputable assembly cable manufacturers. Look for suppliers with a proven track record in your region or industry, and utilize platforms like LinkedIn, trade directories, and industry-specific forums. Focus on suppliers that have experience working with international clients, as this can ease the logistical challenges associated with cross-border transactions.
Step 3: Evaluate Supplier Certifications and Compliance
Ensure that potential suppliers hold relevant certifications and comply with international standards, such as ISO 9001 for quality management or UL certification for safety. These certifications indicate that the manufacturer adheres to recognized quality and safety standards, providing you with assurance regarding the reliability of their products.
- Check for compliance with local regulations: Depending on your region, ensure that the cables meet specific regulatory requirements.
Step 4: Request Samples and Specifications
Before making a large purchase, request samples of the assembly cables you are considering. Testing these samples will help you evaluate their quality and suitability for your applications. Pay close attention to the materials used, the construction quality, and the overall performance under expected conditions.
Step 5: Assess Pricing and Payment Terms
Once you have shortlisted potential suppliers, compare their pricing structures and payment terms. While cost is an important factor, it should not be the sole criterion for selection. Look for transparency in pricing, including any additional costs such as shipping or import duties, and ensure that payment terms align with your financial capabilities.
Step 6: Check References and Customer Reviews
Before finalizing your supplier, ask for references from previous clients and look for customer reviews or testimonials. This step will provide insights into the supplier’s reliability, delivery times, and customer service. Engaging with past customers can also help you gauge how well the supplier addresses issues and supports their clients.
Step 7: Negotiate Contracts and Terms of Service
Once you have selected a supplier, negotiate the terms of the contract thoroughly. This includes delivery schedules, warranty conditions, and after-sales support. A well-negotiated contract protects your interests and ensures that both parties have a clear understanding of their obligations.
By following this checklist, B2B buyers can enhance their sourcing process for assembly cables, ensuring they partner with reliable manufacturers that meet their specific requirements.
Comprehensive Cost and Pricing Analysis for assembly cable manufacturers,assembly cable Sourcing
What Are the Key Cost Components in Assembly Cable Manufacturing?
When analyzing the cost structure of assembly cable manufacturers, several key components should be considered:
-
Materials: The choice of materials directly impacts the cost. High-quality materials such as copper or specialized polymers will increase the price but may enhance performance and durability. Buyers should evaluate the material specifications required for their applications to ensure they are not overspending on unnecessary features.
-
Labor Costs: Labor costs can vary significantly based on the region of manufacturing. In countries with lower labor costs, such as Nigeria or Colombia, manufacturers may offer competitive pricing. However, the skill level of the workforce also plays a critical role in production efficiency and quality.
-
Manufacturing Overhead: This includes expenses related to facilities, utilities, and equipment maintenance. Efficient production processes can help minimize overhead costs. Buyers should inquire about the manufacturer’s operational efficiencies to assess potential savings.
-
Tooling: Custom tooling can be a significant upfront cost, especially for specialized cable designs. However, this cost is often amortized over the production run. It’s crucial for buyers to understand the tooling costs associated with their specific requirements and how they influence the overall price.
-
Quality Control (QC): A robust QC process ensures the product meets specifications and reduces the risk of defects. While implementing stringent QC measures adds to costs, it can save money in the long run by preventing returns and enhancing customer satisfaction.
-
Logistics: Shipping and handling costs can vary widely based on the destination and Incoterms agreed upon. Buyers should factor in logistics when calculating total costs, especially for international shipments.
-
Margin: Manufacturers typically include a profit margin in their pricing. This margin can vary based on competition, market demand, and the perceived value of the product.
How Do Price Influencers Affect Assembly Cable Costs?
Several factors can influence the pricing of assembly cables:
-
Volume/MOQ: Minimum order quantities (MOQ) can significantly affect pricing. Larger orders often lead to bulk discounts, so buyers should consider their purchasing strategy to optimize costs.
-
Specifications and Customization: Custom specifications can lead to higher prices due to the additional engineering and production costs involved. Buyers should balance their needs for customization with budget constraints.
-
Material Quality and Certifications: Higher-quality materials and certifications (e.g., ISO, RoHS compliance) can increase costs but may be necessary for specific applications. Buyers should weigh the benefits of certifications against the additional costs.
-
Supplier Factors: The reputation and reliability of suppliers can impact pricing. Established suppliers may charge more for their proven track record, while emerging suppliers may offer lower prices to gain market share.
-
Incoterms: The choice of Incoterms affects shipping costs and responsibilities. Understanding the implications of terms like FOB (Free on Board) or CIF (Cost, Insurance, and Freight) can help buyers manage their logistics expenses more effectively.
What Buyer Tips Can Help Optimize Costs in Assembly Cable Sourcing?
International B2B buyers can implement several strategies to optimize costs when sourcing assembly cables:
-
Negotiate Effectively: Always negotiate terms, including pricing, delivery schedules, and payment terms. Establishing a good relationship with suppliers can lead to better pricing and terms.
-
Focus on Total Cost of Ownership (TCO): Consider not just the purchase price but also maintenance, durability, and potential failure costs. This holistic view can lead to better long-term investment decisions.
-
Understand Pricing Nuances for International Markets: Different regions may have varying pricing structures due to labor, materials, and overhead costs. Buyers from Africa, South America, the Middle East, and Europe should understand these regional dynamics to make informed decisions.
-
Request Multiple Quotes: Gathering quotes from various suppliers allows for better comparison and understanding of the market rates. This practice can also provide leverage during negotiations.
-
Stay Informed on Market Trends: Keeping abreast of industry trends and fluctuations in raw material prices can help buyers make timely purchasing decisions.
Disclaimer on Indicative Prices
Prices for assembly cables can fluctuate based on market conditions, demand, and other economic factors. It is advisable for buyers to seek updated quotes and engage directly with suppliers to obtain the most accurate pricing information tailored to their specific requirements.
Alternatives Analysis: Comparing assembly cable manufacturers,assembly cable With Other Solutions
When considering assembly cable manufacturers and their products, it’s crucial for B2B buyers to explore viable alternatives that may fulfill their operational needs more effectively or economically. This analysis will compare assembly cables against two alternative solutions: wire harness assemblies and flexible printed circuit boards (FPCBs). Each option presents unique benefits and drawbacks that cater to different applications and industry demands.
Comparison Table
Comparison Aspect | Assembly Cable Manufacturers, Assembly Cable | Wire Harness Assemblies | Flexible Printed Circuit Boards (FPCBs) |
---|---|---|---|
Performance | High durability; suitable for heavy-duty use | Reliable connections; good for complex systems | Lightweight; high flexibility |
Cost | Moderate to high, depending on specifications | Generally lower; cost-effective for bulk | Higher initial costs; more complex design |
Ease of Implementation | Requires expertise for installation | Easier to integrate; less specialized skills needed | Requires specialized knowledge for assembly |
Maintenance | Low maintenance; long lifespan | Moderate; can be prone to wear | Low; typically more robust than traditional wiring |
Best Use Case | Industrial machinery, automotive, aerospace | Automotive, electronics, consumer appliances | Mobile devices, medical equipment, compact electronics |
What Are the Advantages and Disadvantages of Wire Harness Assemblies?
Pros:
Wire harness assemblies provide a streamlined solution for connecting multiple components within a system. They are particularly advantageous in applications where space and weight are constraints, such as in automotive or consumer electronics. Their modular nature allows for easier troubleshooting and replacement, which can reduce downtime.
Cons:
While cost-effective, wire harnesses can be less durable than assembly cables in extreme conditions. They may also require careful planning in design to ensure optimal performance and avoid interference among wires, which could complicate the initial setup.
What Are the Benefits and Drawbacks of Flexible Printed Circuit Boards (FPCBs)?
Pros:
FPCBs are designed for high flexibility and lightweight applications, making them ideal for portable devices and medical equipment. They can integrate multiple functions into a single board, reducing the need for additional components, which can simplify the design and assembly process.
Cons:
The complexity of designing FPCBs can lead to higher initial costs compared to traditional assembly cables. Additionally, FPCBs may not be suitable for high-current applications due to their limited power handling capabilities, which can restrict their use in certain industrial sectors.
How to Choose the Right Solution for Your Needs?
In selecting the best solution, B2B buyers should evaluate their specific operational requirements, including the environment in which the cables will be used, the complexity of the systems being designed, and budget constraints. Assembly cables are ideal for heavy-duty applications requiring durability, while wire harness assemblies offer a cost-effective and simpler alternative for less demanding environments. Conversely, if innovation and space-saving designs are priorities, FPCBs might be the best fit despite their higher costs.
Ultimately, understanding the strengths and weaknesses of each option will empower buyers from Africa, South America, the Middle East, and Europe to make informed decisions that align with their strategic goals and operational needs.
Essential Technical Properties and Trade Terminology for assembly cable manufacturers,assembly cable
What Are the Key Technical Properties of Assembly Cables?
Understanding the essential technical properties of assembly cables is crucial for B2B buyers, especially when sourcing from international manufacturers. Here are some critical specifications to consider:
1. Material Grade
The material grade of assembly cables typically refers to the type of conductor and insulation used. Common materials include copper and aluminum for conductors, while PVC, Teflon, or rubber may serve as insulation. The choice of material affects conductivity, flexibility, and resistance to environmental factors. For buyers, selecting the right material grade ensures optimal performance for specific applications and compliance with industry standards.
2. Voltage Rating
The voltage rating indicates the maximum voltage that the cable can handle without degrading or posing a safety hazard. It is vital for buyers to match the voltage rating with their application requirements to prevent failure or hazards. Understanding voltage ratings helps in selecting cables suitable for industrial, commercial, or residential use, particularly when sourcing from regions with varying electrical standards.
3. Temperature Rating
Temperature ratings specify the range of temperatures within which the cable can operate safely and effectively. Buyers must consider the operating environment—whether it’s high heat or extreme cold—when selecting cables. This specification is crucial to prevent insulation breakdown and ensure longevity, especially in harsh climates prevalent in regions like Africa and the Middle East.
4. Tolerance
Tolerance refers to the permissible deviation in dimensions and properties of the cables. It is important for ensuring compatibility with connectors and other components in the assembly process. Buyers should ensure that the manufacturer meets the required tolerances to avoid issues in assembly and installation, leading to operational inefficiencies.
5. Shielding
Shielding is a critical property that protects cables from electromagnetic interference (EMI). This is particularly important for applications involving sensitive data transmission. Buyers should assess the need for shielding based on their operational environment and the potential for interference, ensuring reliable performance in their electrical systems.
What Are Common Trade Terms in the Assembly Cable Industry?
Familiarity with industry terminology is essential for effective communication and negotiation between buyers and manufacturers. Here are some common terms to know:
1. OEM (Original Equipment Manufacturer)
An OEM is a company that produces parts or equipment that may be marketed by another manufacturer. Understanding the role of OEMs is crucial for buyers looking for custom assembly cables or components, as it influences the sourcing strategy and quality assurance processes.
2. MOQ (Minimum Order Quantity)
MOQ refers to the smallest number of units that a supplier is willing to sell. This term is important for buyers to understand the financial implications of their purchases. Knowing the MOQ helps in budgeting and assessing the feasibility of sourcing from different manufacturers, especially when considering export costs from regions like South America or Europe.
3. RFQ (Request for Quotation)
An RFQ is a document issued by a buyer to solicit price quotes from potential suppliers. This process is essential for comparing offers and negotiating terms. Buyers should ensure their RFQs are detailed, specifying technical requirements and delivery expectations to receive accurate quotes.
4. Incoterms (International Commercial Terms)
Incoterms define the responsibilities of buyers and sellers in international transactions, specifying who pays for shipping, insurance, and tariffs. Familiarity with these terms is crucial for B2B buyers to avoid unexpected costs and understand their obligations in the supply chain, particularly in cross-border transactions.
5. Lead Time
Lead time is the period between the initiation of an order and the delivery of the goods. Understanding lead times helps buyers plan their operations and manage inventory effectively. This is especially significant for international buyers who may face longer shipping times due to customs and logistics in different regions.
By grasping these essential technical properties and trade terms, international B2B buyers can make informed decisions when sourcing assembly cables, ensuring compliance with their specific needs and regional standards.
Navigating Market Dynamics and Sourcing Trends in the assembly cable manufacturers,assembly cable Sector
What Are the Current Market Trends in the Assembly Cable Sector for International Buyers?
The assembly cable sector is experiencing significant shifts driven by technological advancements and evolving customer demands. One of the primary global drivers is the increasing reliance on automation and smart technologies across industries such as automotive, telecommunications, and renewable energy. This transition is creating a surge in demand for high-performance assembly cables that can support complex applications and ensure reliable connectivity.
Emerging B2B technology trends include the adoption of Industry 4.0 practices, which emphasize interconnected systems and data-driven decision-making. This trend is prompting assembly cable manufacturers to innovate and offer solutions that integrate seamlessly with smart manufacturing processes. For international buyers, particularly from regions like Africa, South America, the Middle East, and Europe, there is a growing emphasis on sourcing cables that not only meet technical specifications but also enhance operational efficiency and safety.
Additionally, the increasing focus on supply chain resilience due to global disruptions has led buyers to seek suppliers who can provide flexible and responsive sourcing options. Buyers are encouraged to engage with manufacturers that offer customizable solutions, ensuring they can adapt to changing market dynamics and customer needs effectively.
How Is Sustainability Shaping the Sourcing Decisions in the Assembly Cable Industry?
Sustainability is becoming a critical factor in the sourcing decisions of international B2B buyers in the assembly cable sector. The environmental impact of production processes and the lifecycle of materials used in assembly cables is under scrutiny, prompting a shift towards more eco-friendly practices. Buyers are increasingly prioritizing manufacturers who implement sustainable production methods and use recyclable or biodegradable materials.
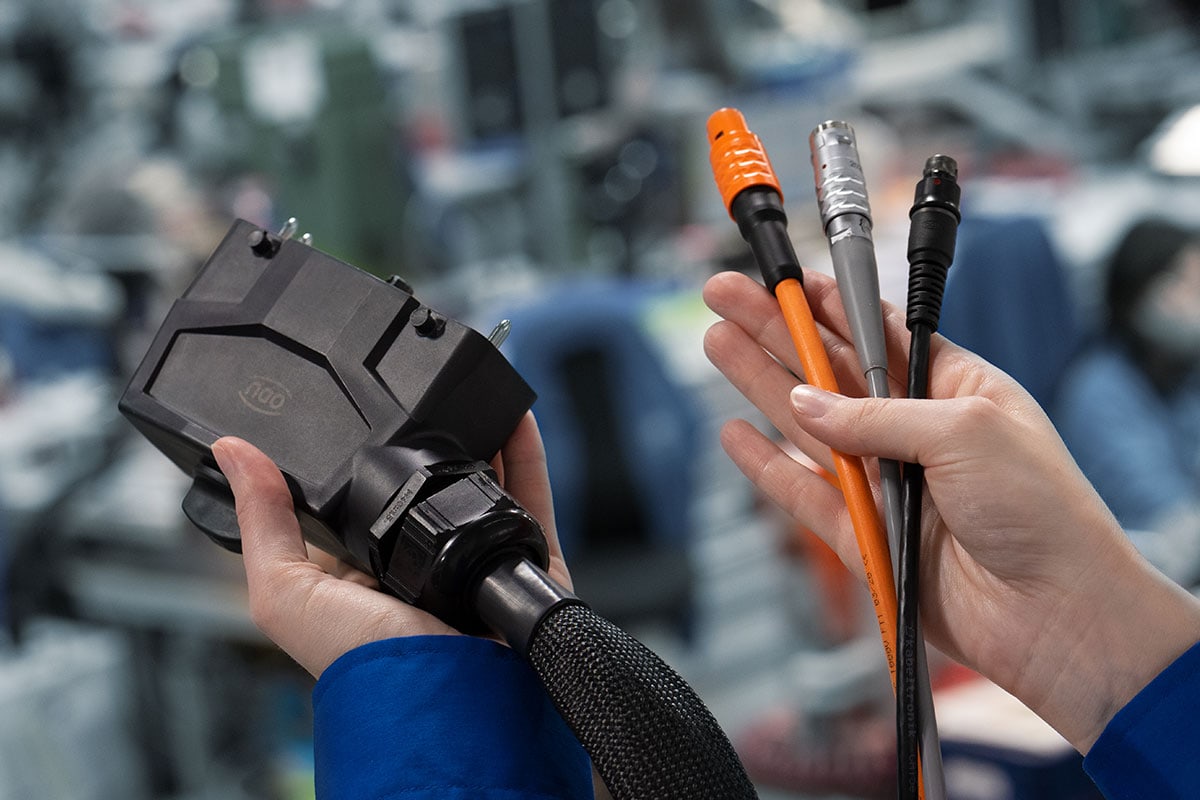
A stock image related to assembly cable manufacturers,assembly cable.
Ethical sourcing is another key consideration, as businesses aim to align with corporate social responsibility (CSR) initiatives. Buyers from Africa, South America, the Middle East, and Europe are particularly focused on ensuring their supply chains are transparent and ethical, avoiding suppliers linked to harmful labor practices or environmental degradation. This trend is driving demand for ‘green’ certifications, such as ISO 14001, which signify a manufacturer’s commitment to environmental management.
Furthermore, the use of innovative materials such as bio-based plastics and low-impact metals is gaining traction. Buyers should actively seek partnerships with manufacturers that not only comply with environmental regulations but also exceed them, providing a competitive edge in an increasingly eco-conscious market.
What Is the Historical Context of the Assembly Cable Sector and Its Evolution?
The assembly cable sector has evolved significantly over the past few decades, transitioning from basic cable manufacturing to a sophisticated industry characterized by advanced technologies and specialized applications. Initially, the focus was primarily on the production of standard cables for general use. However, as industries grew more complex and interconnected, the demand for customized and high-performance cables surged.
In the early 2000s, the introduction of new materials and manufacturing techniques, such as cross-linking and advanced insulation, revolutionized the sector. This allowed for the development of cables that could withstand extreme conditions and offer enhanced durability. As industries began embracing digitalization and automation, the assembly cable sector adapted by incorporating smart technologies, paving the way for innovative products that meet the needs of modern manufacturing.
Today, the assembly cable sector stands at a crossroads, driven by sustainability, technological advancements, and changing consumer expectations. For international B2B buyers, understanding this evolution is crucial in making informed sourcing decisions that align with both current market trends and future developments.
Frequently Asked Questions (FAQs) for B2B Buyers of assembly cable manufacturers,assembly cable
-
How do I choose the right assembly cable manufacturer for my needs?
Selecting the right assembly cable manufacturer involves assessing their industry experience, product quality, and customization capabilities. Start by reviewing their portfolio and client testimonials to gauge reliability. It’s also essential to inquire about their certifications, such as ISO standards, which indicate adherence to quality management systems. Additionally, consider their production capacity and lead times, especially if you are in a region like Africa or South America where logistical challenges may arise. -
What types of assembly cables are available for different applications?
Assembly cables come in various types, including power cables, data cables, and specialty cables for specific industries like automotive and telecommunications. For example, if your application requires high-speed data transfer, look for cables that meet the relevant standards such as CAT6 or CAT7. Understanding the specific requirements of your application will help you narrow down the options and select a manufacturer that specializes in the type of assembly cable you need. -
What are the minimum order quantities (MOQs) typically required by assembly cable manufacturers?
Minimum order quantities (MOQs) can vary significantly among assembly cable manufacturers, ranging from a few hundred meters to several kilometers, depending on the type of cable and customization required. When sourcing from manufacturers in regions like Europe or the Middle East, be sure to discuss MOQs upfront to avoid unexpected costs. Some manufacturers may offer flexible MOQs for first-time buyers or smaller businesses, so it’s advisable to negotiate based on your specific needs. -
How can I ensure quality assurance when sourcing assembly cables internationally?
To ensure quality assurance, request samples before placing a bulk order. Check if the manufacturer has quality control processes in place, such as inspections during production and final testing. Certifications like ISO 9001 can also indicate a commitment to maintaining high-quality standards. Furthermore, consider conducting audits or hiring third-party inspection services, especially when dealing with suppliers from regions that may have different regulatory standards. -
What payment terms should I expect when working with assembly cable manufacturers?
Payment terms can vary widely among assembly cable manufacturers. Common options include upfront payment, 30% deposit with the balance upon delivery, or letters of credit. It’s crucial to discuss payment terms early in the negotiation process to ensure they align with your cash flow needs. When dealing with international suppliers, consider the potential impact of currency fluctuations and international banking fees on your total cost. -
What logistics considerations should I keep in mind when sourcing assembly cables?
Logistics are a critical factor when sourcing assembly cables, especially if you are importing from overseas. Consider the shipping methods available, such as air freight for faster delivery or sea freight for cost-effectiveness. Additionally, be aware of customs regulations and import duties in your region, as these can significantly affect the total cost. Collaborating with a freight forwarder can simplify the process and help you navigate these complexities. -
Can assembly cables be customized for specific applications?
Yes, many assembly cable manufacturers offer customization options to meet specific application requirements. This can include modifications to cable length, gauge, insulation materials, and connector types. When discussing customization, be clear about your technical specifications and any industry standards that must be met. Custom solutions may involve longer lead times and potentially higher costs, so factor these into your planning. -
What are the common challenges faced when sourcing assembly cables from international suppliers?
Common challenges include communication barriers, differences in quality standards, and logistical issues such as shipping delays. To mitigate these challenges, establish clear communication channels and set expectations early in the relationship. It’s also beneficial to familiarize yourself with the supplier’s local regulations and industry practices. Building a strong partnership with your supplier can help navigate these challenges effectively, ensuring a smoother sourcing experience.
Important Disclaimer & Terms of Use
⚠️ Important Disclaimer
The information provided in this guide, including content regarding manufacturers, technical specifications, and market analysis, is for informational and educational purposes only. It does not constitute professional procurement advice, financial advice, or legal advice.
While we have made every effort to ensure the accuracy and timeliness of the information, we are not responsible for any errors, omissions, or outdated information. Market conditions, company details, and technical standards are subject to change.
B2B buyers must conduct their own independent and thorough due diligence before making any purchasing decisions. This includes contacting suppliers directly, verifying certifications, requesting samples, and seeking professional consultation. The risk of relying on any information in this guide is borne solely by the reader.
Strategic Sourcing Conclusion and Outlook for assembly cable manufacturers,assembly cable
In the ever-evolving landscape of assembly cable manufacturing, strategic sourcing remains a crucial component for international B2B buyers. By focusing on quality, reliability, and cost-effectiveness, businesses can not only enhance their supply chain resilience but also improve their competitive edge. Buyers from regions such as Africa, South America, the Middle East, and Europe should prioritize partnerships with manufacturers that demonstrate a commitment to sustainability and innovation.
What are the key benefits of strategic sourcing for assembly cables? It allows companies to leverage global market trends, access advanced technologies, and ensure compliance with international standards. These factors can significantly impact the overall performance and longevity of assembly cables, which are integral to various industries, including automotive, telecommunications, and consumer electronics.
Looking ahead, the demand for high-quality assembly cables is expected to grow, driven by technological advancements and increasing industrial applications. International B2B buyers are encouraged to engage with reputable suppliers who can provide tailored solutions that meet their specific needs. By doing so, businesses can not only secure their supply chains but also foster long-term growth in an increasingly competitive market.