The Ultimate Guide to Electrical Harness Manufacturers (2025)
Introduction: Navigating the Global Market for Electrical Harness Manufacturers
Navigating the complex landscape of electrical harness manufacturers can be a daunting task for international B2B buyers, especially those operating in emerging markets across Africa, South America, the Middle East, and Europe. The need for reliable and high-quality electrical harnesses is crucial, as these components are integral to a wide range of applications, from automotive to industrial machinery. However, the challenge lies in sourcing the right suppliers who can meet specific technical requirements while also offering competitive pricing.
This comprehensive guide aims to empower B2B buyers by providing valuable insights into the electrical harness manufacturing sector. It covers essential topics such as the different types of electrical harnesses, their applications across various industries, and the critical factors to consider when vetting suppliers. Additionally, we delve into cost considerations, allowing buyers to make informed financial decisions.
By equipping buyers with the knowledge to navigate supplier options effectively, this guide facilitates better purchasing decisions that align with their operational needs and budget constraints. For businesses in regions like Poland and South Africa, understanding these dynamics is vital for maintaining a competitive edge in an increasingly globalized market. Whether you are looking for innovative solutions or cost-effective sourcing strategies, this guide serves as an essential tool for enhancing your procurement process in the electrical harness sector.
Understanding Electrical Harness Manufacturers Types and Variations
Type Name | Key Distinguishing Features | Primary B2B Applications | Brief Pros & Cons for Buyers |
---|---|---|---|
Automotive Harnesses | Designed for vehicles; includes connectors, terminals. | Automotive manufacturing, repair | Pros: High durability, compliance with safety standards. Cons: Complexity in customization. |
Industrial Harnesses | Heavy-duty materials; designed for harsh environments. | Machinery, manufacturing equipment | Pros: High resistance to wear and tear. Cons: Higher initial costs. |
Aerospace Harnesses | Lightweight, high-performance materials; stringent regulations. | Aircraft, spacecraft systems | Pros: Enhanced safety and performance. Cons: Long lead times for production. |
Medical Device Harnesses | Biocompatible materials; focus on precision and safety. | Medical equipment, diagnostics | Pros: High reliability and safety standards. Cons: Limited suppliers and higher costs. |
Consumer Electronics Harnesses | Compact design; integrates with various electronic devices. | Electronics manufacturing, repairs | Pros: Versatile applications, cost-effective. Cons: May require frequent updates to meet technology changes. |
What Are the Characteristics of Automotive Harnesses?
Automotive harnesses are specialized wiring systems designed for vehicles, featuring connectors and terminals that facilitate electrical connections across various components. These harnesses are engineered to endure vibrations, extreme temperatures, and exposure to chemicals. When purchasing, B2B buyers should consider the manufacturer’s compliance with automotive safety standards, the availability of custom solutions, and the harness’s compatibility with specific vehicle models.
How Do Industrial Harnesses Differ in Their Applications?
Industrial harnesses are built to withstand harsh conditions, making them ideal for machinery and manufacturing equipment. They are constructed from heavy-duty materials that resist abrasion and corrosion. Buyers looking for industrial harnesses should evaluate the supplier’s experience in their specific industry, the harness’s resistance to environmental factors, and the total cost of ownership, including installation and maintenance.
What Makes Aerospace Harnesses Unique?
Aerospace harnesses utilize lightweight, high-performance materials to meet stringent regulatory requirements in the aviation industry. These harnesses ensure safety and reliability in critical systems such as navigation and communication. B2B buyers must consider the supplier’s certifications, the lead times for production, and the harness’s ability to meet rigorous testing standards when making purchasing decisions.
Why Are Medical Device Harnesses Important?
Medical device harnesses are crafted from biocompatible materials, focusing on precision and safety for sensitive medical applications. These harnesses are crucial in ensuring the reliability of medical equipment and diagnostics. Buyers should prioritize suppliers with a strong reputation in the medical field, adherence to regulatory standards, and the ability to provide traceability for materials used in production.
How Do Consumer Electronics Harnesses Adapt to Market Needs?
Consumer electronics harnesses are designed for compactness and versatility, integrating with various electronic devices. They are often produced in high volumes, making them cost-effective for manufacturers. B2B buyers should assess the supplier’s capability to adapt to rapid technological changes, the quality of materials used, and the potential for future upgrades or modifications in design.
Related Video: Nangudi Wire Harness And Cable Assemblies Manufacturer Production Process
Key Industrial Applications of Electrical Harness Manufacturers
Industry/Sector | Specific Application of Electrical Harness Manufacturers | Value/Benefit for the Business | Key Sourcing Considerations for this Application |
---|---|---|---|
Automotive | Wiring harnesses for electric vehicles | Enhanced vehicle performance and safety features | Compliance with international safety standards, durability under extreme conditions |
Aerospace | Electrical systems in aircraft | Improved reliability and reduced weight | Certifications for aerospace applications, resistance to high altitudes and temperatures |
Industrial Automation | Control systems in manufacturing equipment | Increased efficiency and reduced downtime | Customization options, integration with existing systems, scalability |
Renewable Energy | Solar panel connectivity and wind turbine wiring | Maximized energy transfer and system longevity | Environmental resistance, compatibility with various energy systems, cost-effectiveness |
Telecommunications | Cable assemblies for communication systems | High-speed data transfer and reliability | Compliance with telecom standards, flexibility in design, and lead time for delivery |
How Are Electrical Harness Manufacturers Applied in the Automotive Sector?
In the automotive industry, electrical harness manufacturers provide wiring harnesses crucial for electric vehicles (EVs). These harnesses connect various components, including batteries, motors, and control systems, ensuring efficient power distribution. This application addresses the growing demand for EVs and the need for enhanced performance and safety features. Buyers must consider compliance with international safety standards and durability under extreme conditions, especially in regions with varying climates like Africa and South America.
What Role Do Electrical Harness Manufacturers Play in Aerospace Applications?
In aerospace, electrical harness manufacturers supply electrical systems that are integral to aircraft functionality. These harnesses are designed to withstand harsh environmental conditions, ensuring reliability and safety during flight operations. The need for lightweight yet durable materials is paramount in this sector, as it directly impacts fuel efficiency. International B2B buyers should focus on manufacturers with the necessary certifications for aerospace applications and those that demonstrate resistance to high altitudes and temperatures, particularly in Europe and the Middle East.
How Are Electrical Harness Manufacturers Enhancing Industrial Automation?
Electrical harness manufacturers are pivotal in the industrial automation sector, providing control systems for manufacturing equipment. These harnesses facilitate seamless communication between machines, enhancing efficiency and reducing downtime. The integration of advanced technologies necessitates customization options from manufacturers to meet specific operational requirements. Buyers in Africa and South America should prioritize sourcing from manufacturers that offer tailored solutions and scalability to accommodate future growth.
In What Ways Do Electrical Harness Manufacturers Support Renewable Energy?
In the renewable energy sector, electrical harness manufacturers create wiring systems for solar panels and wind turbines. These harnesses ensure optimal energy transfer and contribute to the longevity of renewable energy systems. As global energy demands shift towards sustainability, the reliability of these harnesses becomes critical. Buyers need to consider environmental resistance and compatibility with various energy systems, particularly in developing regions where renewable energy adoption is accelerating.
How Are Telecommunications Enhanced by Electrical Harness Manufacturers?
Electrical harness manufacturers play a vital role in telecommunications by providing cable assemblies for communication systems. These harnesses are designed for high-speed data transfer, ensuring reliability in connectivity. With the increasing demand for robust communication networks, buyers should seek manufacturers that comply with telecom standards and offer flexible designs. Lead time for delivery is also a crucial consideration, especially for international buyers looking to meet tight project timelines in Europe and the Middle East.
Related Video: Catia V5 Electrical Harness Design – Automotive Harness Design Tutorial
3 Common User Pain Points for ‘Electrical Harness Manufacturers’ & Their Solutions
Scenario 1: Difficulty in Customizing Electrical Harness Solutions for Unique Applications
The Problem: B2B buyers often face the challenge of sourcing electrical harnesses that meet specific application requirements. This is particularly true for industries like automotive, aerospace, and industrial machinery, where unique designs and specifications are critical. Many manufacturers offer standard solutions that do not accommodate the unique dimensions, materials, or environmental conditions required for specialized projects. Buyers may find themselves in a position where off-the-shelf products either underperform or lead to costly modifications later.
The Solution: To effectively overcome this challenge, buyers should prioritize collaboration with electrical harness manufacturers that specialize in custom solutions. Begin by conducting thorough market research to identify manufacturers that have a proven track record in your specific industry. During initial discussions, clearly communicate your project requirements, including dimensions, materials, and environmental factors. Request samples or prototypes to assess the quality and fit of the harnesses. Additionally, consider manufacturers that utilize advanced technologies such as CAD and simulation software to design and test harnesses before production. This proactive approach not only ensures a better fit but also reduces lead times and costs associated with revisions.
Scenario 2: Quality Assurance and Compliance Challenges in Electrical Harness Manufacturing
The Problem: Ensuring that electrical harnesses comply with industry standards and regulations is a significant concern for B2B buyers, especially in regions with stringent quality control measures, like Europe. Non-compliance can lead to severe repercussions, including product recalls, legal penalties, and damage to brand reputation. Buyers may struggle to verify whether manufacturers consistently meet quality benchmarks and regulatory standards, particularly when dealing with overseas suppliers.
The Solution: To mitigate these risks, buyers should adopt a comprehensive supplier evaluation process. This includes requesting certifications such as ISO 9001 or IPC/WHMA-A-620, which demonstrate adherence to international quality management standards and cable assembly criteria. Additionally, conduct on-site audits of potential suppliers to assess their manufacturing processes and quality control measures firsthand. Establish clear communication about your compliance requirements and ask for documentation that proves adherence to relevant standards. By fostering a strong partnership built on transparency and accountability, you can ensure that the electrical harnesses you source meet all necessary compliance and quality standards.
Scenario 3: Navigating Supply Chain Disruptions in Electrical Harness Procurement
The Problem: B2B buyers frequently encounter supply chain disruptions that affect the timely delivery of electrical harnesses. Factors such as geopolitical issues, raw material shortages, and logistical challenges can lead to unexpected delays, impacting project timelines and budgets. Buyers in regions like Africa and South America may find themselves particularly vulnerable to these disruptions due to less developed supply chains.
The Solution: To navigate these challenges, buyers should diversify their supplier base and not rely solely on a single source. Establish relationships with multiple manufacturers across different regions to mitigate the risks associated with localized disruptions. Additionally, consider implementing a just-in-time (JIT) inventory strategy that allows for more flexibility in procurement while reducing holding costs. Regularly communicate with suppliers about their production capabilities and lead times, and develop contingency plans that outline alternative sourcing strategies should disruptions occur. By proactively managing your supply chain and fostering strong relationships with multiple suppliers, you can better withstand disruptions and maintain project momentum.
Strategic Material Selection Guide for Electrical Harness Manufacturers
When selecting materials for electrical harness manufacturing, it’s crucial for international B2B buyers to understand the properties, advantages, and limitations of common materials. This guide analyzes four prevalent materials: PVC, XLPE, Teflon, and Thermoplastic Elastomers (TPE), focusing on their applications, benefits, and considerations for buyers from diverse regions such as Africa, South America, the Middle East, and Europe.
What are the Key Properties of PVC in Electrical Harnesses?
Polyvinyl Chloride (PVC) is a widely used thermoplastic material in electrical harnesses due to its excellent electrical insulation properties. It is capable of withstanding temperatures up to 105°C and has good resistance to chemicals and moisture. PVC is also flame-retardant, making it suitable for various applications.
Pros & Cons: PVC is cost-effective and easy to manufacture, which makes it a popular choice for many manufacturers. However, it has limitations in high-temperature applications and can become brittle over time, especially under UV exposure.
Impact on Application: PVC is compatible with a wide range of media, including water and oils, but it may not perform well in extreme environments or with certain solvents.
Considerations for International Buyers: Compliance with standards such as ASTM D3032 and UL 83 is essential. Buyers should also consider the environmental regulations surrounding PVC, particularly in Europe, where restrictions on certain phthalates are in place.
How Does XLPE Compare for Electrical Harness Applications?
Cross-Linked Polyethylene (XLPE) is another popular material, known for its superior thermal and chemical resistance compared to PVC. It can handle temperatures up to 90°C continuously and has excellent mechanical properties.
Pros & Cons: XLPE offers high durability and is resistant to moisture and chemicals, making it suitable for harsh environments. However, it tends to be more expensive than PVC and may require more complex manufacturing processes.
Impact on Application: XLPE is ideal for applications that involve exposure to oils, solvents, and high temperatures, making it a preferred choice in automotive and industrial settings.
Considerations for International Buyers: Buyers should ensure compliance with international standards such as DIN 53372 and JIS K 6768. The higher cost may be justified in applications requiring enhanced performance.
What Advantages Does Teflon Provide in Electrical Harnesses?
Teflon (PTFE) is renowned for its exceptional chemical resistance and high-temperature stability, withstanding temperatures up to 260°C. It is often used in environments where extreme conditions are a factor.
Pros & Cons: The primary advantage of Teflon is its ability to resist nearly all chemicals, making it ideal for specialized applications. However, it is significantly more expensive than other materials and can be challenging to process.
Impact on Application: Teflon is suitable for applications involving corrosive substances, making it a go-to material in the chemical and pharmaceutical industries.
Considerations for International Buyers: Buyers should be aware of the high costs and the need for specialized manufacturing techniques. Compliance with standards such as ASTM D3308 is crucial for quality assurance.
Why Choose Thermoplastic Elastomers (TPE) for Electrical Harnesses?
Thermoplastic Elastomers (TPE) combine the properties of rubber and plastic, offering flexibility, durability, and excellent weather resistance. TPE can operate effectively at temperatures ranging from -40°C to 125°C.
Pros & Cons: TPEs are versatile and can be processed like plastics, allowing for easier manufacturing. However, they may not be as resistant to certain chemicals as PVC or XLPE.
Impact on Application: TPE is suitable for applications that require flexibility and resilience, such as automotive wiring and consumer electronics.
Considerations for International Buyers: Buyers should check for compliance with standards such as ISO 9001 and UL 94. The adaptability of TPEs makes them an attractive option for various markets, including Europe and South America.
Summary Table of Material Selection for Electrical Harness Manufacturers
Material | Typical Use Case for Electrical Harness Manufacturers | Key Advantage | Key Disadvantage/Limitation | Relative Cost (Low/Med/High) |
---|---|---|---|---|
PVC | General electrical insulation | Cost-effective and easy to manufacture | Limited high-temperature performance | Low |
XLPE | Automotive and industrial applications | High durability and chemical resistance | Higher cost and complexity | Medium |
Teflon | Chemical and pharmaceutical applications | Exceptional chemical resistance | Expensive and challenging to process | High |
Thermoplastic Elastomers (TPE) | Automotive wiring and consumer electronics | Flexibility and weather resistance | Lower chemical resistance than others | Medium |
This strategic material selection guide provides valuable insights for international B2B buyers, ensuring informed decisions that align with regional standards and application requirements.
In-depth Look: Manufacturing Processes and Quality Assurance for Electrical Harness Manufacturers
What Are the Key Stages in the Manufacturing Process of Electrical Harnesses?
The manufacturing process of electrical harnesses consists of several critical stages that ensure quality and functionality. Here’s a breakdown of each stage:
-
Material Preparation: This initial phase involves sourcing high-quality raw materials such as wires, connectors, and insulation materials. The selection of materials is crucial as it affects the durability and performance of the harness. For international buyers, verifying material certifications (e.g., RoHS, REACH compliance) is essential to ensure they meet regional standards.
-
Forming: During this stage, the raw materials are cut to specific lengths and shaped according to the design specifications. Techniques such as crimping and soldering are employed to attach connectors to wires. Advanced manufacturers utilize automated machinery to enhance precision and efficiency, which can significantly reduce human error and production time.
-
Assembly: In the assembly phase, the formed components are integrated into a complete harness. This includes organizing the wiring, attaching connectors, and ensuring proper routing to avoid interference with other components. Manufacturers often employ specialized tools and fixtures to ensure consistent assembly quality.
-
Finishing: The final stage involves insulating, labeling, and packaging the harnesses. Insulation is critical to prevent short circuits and ensure safety. Quality labeling helps in identifying the harnesses during installation and maintenance. This stage may also include visual inspections and final adjustments before the product is packed for shipment.
How Is Quality Assurance Implemented in Electrical Harness Manufacturing?
Quality assurance (QA) is integral to the manufacturing process, ensuring that each harness meets established standards. Here are some key QA practices:
-
International Standards and Certifications: Compliance with international quality standards such as ISO 9001 is crucial. This certification indicates that the manufacturer has a quality management system in place, ensuring consistent product quality. Industry-specific certifications like CE (Conformité Européenne) for European markets or API (American Petroleum Institute) for oil and gas applications are also important for international buyers to consider.
-
Quality Control Checkpoints: Effective QA involves multiple checkpoints throughout the manufacturing process:
– Incoming Quality Control (IQC): This step ensures that all raw materials meet predefined quality standards before they enter production.
– In-Process Quality Control (IPQC): Regular inspections during the manufacturing process help identify issues early, allowing for immediate corrective actions.
– Final Quality Control (FQC): This comprehensive evaluation occurs before shipment, ensuring that the final product adheres to all specifications and quality standards. -
Common Testing Methods: Electrical harnesses undergo various testing methods to ensure reliability and safety. These may include:
– Continuity Testing: Verifies that electrical pathways are intact.
– Insulation Resistance Testing: Ensures that the insulation is effective, preventing electrical leakage.
– Mechanical Stress Testing: Assesses the harness’s ability to withstand physical stress and strain during use.
How Can B2B Buyers Verify Supplier Quality Control Practices?
For B2B buyers, particularly those from regions like Africa, South America, the Middle East, and Europe, verifying a supplier’s quality control practices is essential. Here are actionable steps:
-
Supplier Audits: Conducting on-site audits allows buyers to assess the manufacturer’s facilities, processes, and quality management systems firsthand. This helps verify compliance with international standards and the effectiveness of their QA practices.
-
Requesting Quality Reports: Buyers should request detailed quality reports that outline testing results, compliance certifications, and any corrective actions taken during production. This transparency is vital for establishing trust and confidence in the supplier.
-
Third-Party Inspections: Engaging third-party inspection agencies to evaluate the manufacturing process can provide an unbiased assessment of the supplier’s quality standards. This is especially relevant for international buyers who may not have local resources to conduct thorough evaluations.
What Are the Nuances of Quality Control for International B2B Buyers?
International B2B buyers must navigate various challenges when ensuring quality control in electrical harness manufacturing:
-
Understanding Regional Standards: Different regions may have varying quality and safety standards. Buyers must familiarize themselves with these regulations to ensure compliance. For example, European buyers must ensure that products meet CE marking requirements, while those in the Middle East may need to consider Gulf Cooperation Council (GCC) standards.
-
Supply Chain Transparency: Ensuring transparency in the supply chain is crucial for quality assurance. Buyers should seek suppliers who provide detailed information about their sourcing practices and the origin of materials used in manufacturing.
-
Cultural and Communication Barriers: Language and cultural differences can impact quality assurance processes. Buyers should establish clear communication channels and potentially consider local representatives or consultants who can facilitate understanding and compliance.
Conclusion: Ensuring Quality in Electrical Harness Manufacturing
For international B2B buyers, understanding the manufacturing processes and quality assurance practices of electrical harness manufacturers is critical. By focusing on material preparation, forming, assembly, and finishing stages, along with robust QA protocols, buyers can ensure they partner with reliable suppliers. Verifying quality through audits, reports, and third-party inspections will further safeguard investments and ensure compliance with regional standards, ultimately leading to successful business outcomes.
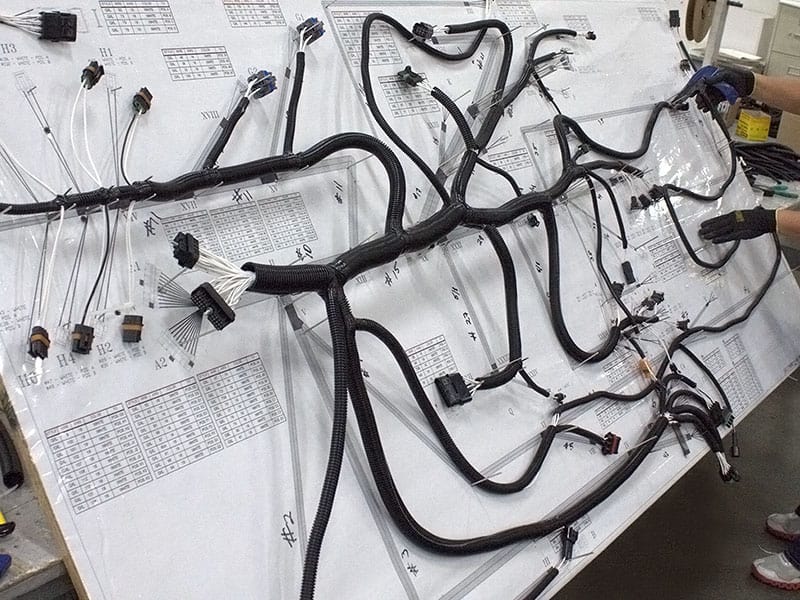
A stock image related to Electrical Harness Manufacturers.
Practical Sourcing Guide: A Step-by-Step Checklist for ‘Electrical Harness Manufacturers’
When sourcing electrical harness manufacturers, it is essential to follow a structured approach to ensure quality, compliance, and alignment with your project requirements. This checklist serves as a practical guide for international B2B buyers, especially those from Africa, South America, the Middle East, and Europe, to effectively navigate the procurement process.
Step 1: Define Your Technical Specifications
Before reaching out to manufacturers, clearly outline the technical specifications required for your electrical harnesses. This includes factors such as wire gauge, insulation material, connector types, and operational voltage. Having detailed specifications helps manufacturers understand your needs and ensures that you receive accurate quotes.
- Considerations:
- What industry standards must be met (e.g., ISO, UL)?
- Are there specific environmental conditions the harness must withstand?
Step 2: Research Potential Suppliers
Conduct thorough research to identify potential electrical harness manufacturers. Utilize online directories, trade shows, and industry forums to compile a list of suppliers that specialize in your required product type.
- Tips:
- Look for manufacturers with a strong reputation in your target market (e.g., Europe or the Middle East).
- Check for reviews and testimonials from other B2B buyers.
Step 3: Verify Supplier Certifications
Ensure that the manufacturers you are considering hold relevant certifications, such as ISO 9001 for quality management systems or specific industry certifications. This step is crucial to guarantee that the supplier adheres to international quality standards.
- Key Certifications:
- ISO 9001
- ISO/TS 16949 (automotive industry)
- UL certification for safety compliance
Step 4: Evaluate Production Capabilities
Assess the production capabilities of each potential supplier to ensure they can meet your volume and quality requirements. Request information about their manufacturing processes, machinery, and workforce qualifications.
- Questions to Ask:
- What is the manufacturer’s maximum production capacity?
- Do they have experience with similar projects in your industry?
Step 5: Request Samples and Prototypes
Before finalizing your supplier, request samples or prototypes of the electrical harnesses. This allows you to evaluate the quality of materials and craftsmanship firsthand.
- What to Look For:
- Quality of connections and insulation
- Compliance with your specified technical requirements
Step 6: Discuss Terms and Conditions
Engage in discussions about pricing, payment terms, lead times, and shipping logistics. Understanding these factors upfront can help prevent misunderstandings later in the process.
- Considerations:
- Are there minimum order quantities?
- What are the warranty and return policies?
Step 7: Establish a Communication Plan
Finally, establish a clear communication plan with your chosen supplier. Regular updates and open lines of communication can prevent issues and ensure that both parties are aligned throughout the production process.
- Best Practices:
- Schedule regular check-ins via email or video calls.
- Use project management tools to track progress and address any concerns promptly.
By following these steps, international B2B buyers can navigate the procurement process of electrical harness manufacturers more effectively, ensuring high-quality products that meet their specific needs.
Comprehensive Cost and Pricing Analysis for Electrical Harness Manufacturers Sourcing
What Are the Key Cost Components in Electrical Harness Manufacturing?
Understanding the cost structure of electrical harness manufacturing is crucial for international B2B buyers. The primary cost components include:
-
Materials: The choice of materials significantly impacts the overall cost. Common materials such as copper wires, insulation, and connectors vary in price based on quality and availability. Buyers should consider sourcing materials from local suppliers to mitigate costs.
-
Labor: Labor costs can differ significantly between regions. For instance, labor in Africa or South America may be less expensive than in Europe, impacting the final price of the harness. It’s essential to evaluate the skill level required for assembly and the associated costs.
-
Manufacturing Overhead: This includes costs related to factory utilities, equipment maintenance, and indirect labor. Efficient manufacturing processes can reduce overhead costs, which is beneficial for both the manufacturer and the buyer.
-
Tooling: Tooling costs are incurred when creating custom molds and dies for production. These costs can be substantial, especially for complex designs. Buyers should inquire about tooling costs upfront to avoid unexpected expenses.
-
Quality Control (QC): Implementing stringent QC measures ensures that the products meet specified standards. While this can add to the cost, it ultimately reduces the risk of defects and returns, providing long-term savings.
-
Logistics: Shipping and handling costs are critical, especially for international transactions. Factors such as distance, shipping method, and customs duties can add significant expenses. Buyers should factor in these costs when evaluating suppliers.
-
Margin: Finally, manufacturers include their profit margins, which can vary based on market competition and negotiation outcomes. Understanding the market average can help buyers negotiate better terms.
How Do Price Influencers Affect Electrical Harness Sourcing?
Several factors influence pricing in the electrical harness industry:
-
Volume and Minimum Order Quantity (MOQ): Larger orders typically result in lower per-unit costs. Buyers should assess their demand to negotiate favorable terms based on volume.
-
Specifications and Customization: Customized harnesses often incur additional costs due to the complexity of design and production. Buyers should clearly define their requirements to avoid costly revisions.
-
Materials and Quality Certifications: High-quality materials and certifications (e.g., ISO, UL) can lead to higher prices. However, they ensure reliability and compliance, which can be crucial for certain applications.
-
Supplier Factors: Established suppliers may charge a premium for their experience and reliability. Evaluating multiple suppliers can help buyers find a balance between cost and quality.
-
Incoterms: Understanding Incoterms (International Commercial Terms) is vital for determining who bears shipping costs and risks. This knowledge can influence the total cost and negotiating strategy.
What Are Effective Buyer Tips for Cost-Efficient Sourcing?
To maximize cost-efficiency in sourcing electrical harnesses, buyers should consider the following strategies:
-
Negotiate Terms: Always negotiate pricing, payment terms, and delivery schedules. Many suppliers are open to discussions, especially for large orders.
-
Evaluate Total Cost of Ownership (TCO): Instead of focusing solely on the purchase price, consider the TCO, which includes maintenance, operational costs, and potential savings from higher-quality products.
-
Understand Pricing Nuances: Be aware that prices may fluctuate based on market conditions, currency exchange rates, and geopolitical factors, particularly for buyers in Africa and South America. Staying informed can help in timing purchases effectively.
-
Leverage Technology: Use digital platforms for supplier comparison and to gain insights into market trends. This can provide a competitive edge in negotiations.
-
Build Relationships: Establishing long-term relationships with suppliers can lead to better pricing and terms. Frequent communication and trust can encourage suppliers to prioritize your orders.
Disclaimer on Indicative Prices
Prices in the electrical harness manufacturing sector can vary widely based on multiple factors. The figures provided in this analysis are indicative and should be confirmed with suppliers for accuracy and relevance to specific sourcing needs. Buyers should conduct thorough market research and seek multiple quotes to ensure they receive the best value.
Alternatives Analysis: Comparing Electrical Harness Manufacturers With Other Solutions
Exploring Alternatives to Electrical Harness Manufacturers
In the evolving landscape of electrical engineering and manufacturing, B2B buyers often seek various solutions that can meet their specific needs effectively. While electrical harness manufacturers offer a robust solution for connecting electrical systems, several alternative technologies and methods can also achieve similar outcomes. This section will compare electrical harness manufacturers with two viable alternatives: custom wiring solutions and printed circuit boards (PCBs).
Comparison Table
Comparison Aspect | Electrical Harness Manufacturers | Custom Wiring Solutions | Printed Circuit Boards (PCBs) |
---|---|---|---|
Performance | High durability and reliability | Varies based on materials | Excellent for complex circuits |
Cost | Moderate to high | Typically lower | Can be cost-effective at scale |
Ease of Implementation | Moderate complexity | High flexibility | Requires design expertise |
Maintenance | Low maintenance needs | Moderate, depends on installation | Low, but requires careful handling |
Best Use Case | Automotive, aerospace | Prototyping, repairs | Consumer electronics, automation |
What Are the Advantages and Disadvantages of Custom Wiring Solutions?
Custom wiring solutions involve creating tailored wiring systems based on specific project requirements.
Pros:
– Flexibility: Custom wiring can be designed to fit unique specifications, making it ideal for specialized applications or limited space environments.
– Cost-Effective for Prototypes: Often less expensive than off-the-shelf solutions, especially for small-scale or prototype projects.
Cons:
– Quality Variability: The performance of custom wiring can vary significantly depending on the materials and craftsmanship used, potentially leading to reliability issues.
– Complex Installation: Installation can be complicated and may require skilled technicians, increasing labor costs.
How Do Printed Circuit Boards (PCBs) Compare in Terms of Efficiency?
PCBs are a foundational technology in modern electronics, providing a compact and efficient method for circuit assembly.
Pros:
– High Efficiency: PCBs can support complex circuits in a compact design, improving performance and reducing the overall footprint of electrical systems.
– Scalability: Once designed, PCBs can be mass-produced at a lower cost, making them ideal for high-volume applications.
Cons:
– Initial Design Costs: The design process for PCBs can be expensive and time-consuming, particularly for intricate designs.
– Less Flexible for Modifications: Changes to the circuit design post-manufacturing can be difficult and costly.
How Can B2B Buyers Choose the Right Solution for Their Needs?
Choosing between electrical harness manufacturers and alternative solutions like custom wiring or PCBs depends on several factors, including the specific requirements of the project, budget constraints, and the desired performance characteristics. B2B buyers should evaluate their needs regarding durability, complexity, and cost-effectiveness. For applications requiring high reliability in harsh environments, electrical harnesses may be the best choice. Conversely, for rapid prototyping or less demanding applications, custom wiring or PCBs might be more suitable. Conducting thorough research and potentially consulting with industry experts can help ensure that the selected solution aligns well with the buyer’s operational goals and long-term strategy.
Essential Technical Properties and Trade Terminology for Electrical Harness Manufacturers
What Are the Essential Technical Properties for Electrical Harness Manufacturing?
When sourcing electrical harnesses, understanding the technical specifications is crucial for ensuring product quality and compatibility. Here are several key properties that B2B buyers should consider:
-
Material Grade
– The material used in electrical harnesses, such as copper or aluminum for conductors, and PVC or polyurethane for insulation, affects conductivity, durability, and flexibility. High-grade materials can ensure better performance and longevity, making them a smart investment. -
Tolerance
– Tolerance refers to the allowable deviation from specified dimensions. It’s critical in applications where precision is necessary, such as in automotive or aerospace industries. Tight tolerances can enhance the reliability of the electrical connections and overall system performance. -
Temperature Rating
– This indicates the maximum operating temperature of the harness. For instance, high-temperature applications, like those in automotive engines, require harnesses rated for elevated temperatures to prevent insulation degradation. Selecting the correct temperature rating can prevent failures and enhance safety. -
Voltage Rating
– Each harness must be rated for the maximum voltage it will encounter during operation. Choosing a harness with an insufficient voltage rating can lead to insulation breakdown and potential hazards. Understanding the operating environment is essential for making the right choice. -
Shielding
– Shielding is used to protect against electromagnetic interference (EMI), which can disrupt signal integrity in sensitive applications. Buyers should assess the need for shielding based on the operational environment and the sensitivity of the equipment being used.
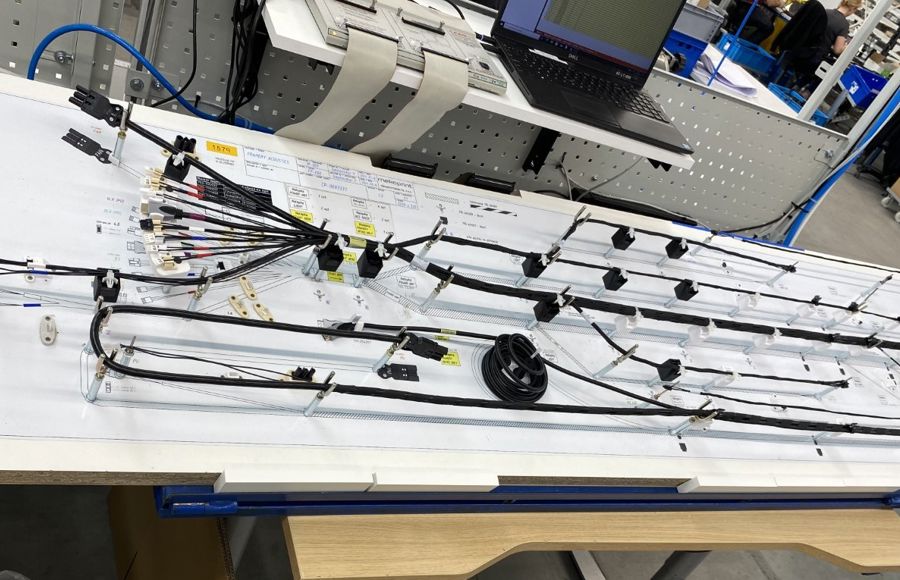
A stock image related to Electrical Harness Manufacturers.
- Connector Types
– The type of connectors used in a harness significantly influences compatibility with other components. Standard connectors (e.g., Molex, JST) can simplify integration, while custom connectors might be necessary for specialized applications. Understanding connector types can aid in ensuring seamless assembly and functionality.
What Are Common Trade Terms Used in the Electrical Harness Industry?
Familiarizing yourself with industry jargon can facilitate smoother communication and negotiations. Here are some essential terms:
-
OEM (Original Equipment Manufacturer)
– An OEM is a company that produces parts or equipment that may be marketed by another manufacturer. Understanding OEM relationships is vital for sourcing components that meet specific quality and compatibility standards. -
MOQ (Minimum Order Quantity)
– This term refers to the smallest number of units a supplier is willing to sell. Knowing the MOQ is essential for budgeting and inventory management, especially for international buyers who may face higher shipping costs for small orders. -
RFQ (Request for Quotation)
– An RFQ is a document that solicits quotes from suppliers for specific products or services. For B2B buyers, issuing an RFQ can streamline the procurement process and ensure competitive pricing. -
Incoterms (International Commercial Terms)
– These are predefined commercial terms published by the International Chamber of Commerce (ICC) that clarify the responsibilities of buyers and sellers in international transactions. Familiarity with Incoterms is crucial for understanding shipping logistics and cost responsibilities. -
Lead Time
– Lead time refers to the time taken from placing an order to delivery. It is a critical factor in supply chain management, especially for projects with tight deadlines. Buyers should confirm lead times to avoid delays in production schedules. -
Testing Standards
– Refers to the regulatory benchmarks that harnesses must meet, such as ISO or IEC standards. Understanding these standards ensures compliance with safety and performance criteria, which is especially important for international markets.
By grasping these technical properties and trade terms, international B2B buyers can make informed decisions when sourcing electrical harnesses, optimizing both their purchasing processes and overall project success.
Navigating Market Dynamics and Sourcing Trends in the Electrical Harness Manufacturers Sector
What Are the Current Market Dynamics and Key Trends in Electrical Harness Manufacturing?
The electrical harness manufacturing sector is experiencing significant transformation, primarily driven by technological advancements and evolving market demands. Global drivers such as the increasing adoption of electric vehicles (EVs) and the growth of renewable energy sources are propelling the demand for high-quality electrical harnesses. For international B2B buyers from Africa, South America, the Middle East, and Europe, understanding these dynamics is crucial.
Emerging trends include the integration of smart manufacturing technologies like IoT (Internet of Things) and AI (Artificial Intelligence), which enhance production efficiency and quality control. Moreover, the rise of Industry 4.0 is pushing manufacturers to adopt advanced automation and robotics, resulting in faster turnaround times and reduced operational costs. For instance, manufacturers are increasingly utilizing automated assembly lines to streamline processes, which is particularly beneficial for buyers looking to minimize lead times.
Additionally, there’s a growing emphasis on customization, as businesses seek to meet specific client requirements. This trend is particularly relevant for buyers in diverse markets such as Poland and South Africa, where tailored solutions can provide a competitive edge. Understanding these market dynamics will enable buyers to make informed decisions and leverage opportunities within the electrical harness manufacturing sector.
How Is Sustainability and Ethical Sourcing Changing the Electrical Harness Manufacturing Landscape?
Sustainability and ethical sourcing are becoming increasingly vital for electrical harness manufacturers, with significant implications for B2B buyers. The environmental impact of manufacturing processes is under scrutiny, prompting companies to adopt greener practices. For buyers, partnering with manufacturers who prioritize sustainability not only enhances corporate social responsibility (CSR) but also aligns with global sustainability goals.
The importance of ethical supply chains cannot be overstated. Buyers are encouraged to seek manufacturers who comply with environmental regulations and utilize sustainable materials. For instance, the use of recyclable materials in electrical harness production is gaining traction, helping to reduce waste and energy consumption. Certifications such as ISO 14001 for environmental management systems and adherence to RoHS (Restriction of Hazardous Substances) directives are essential indicators of a manufacturer’s commitment to sustainability.
Moreover, transparency in sourcing practices is increasingly demanded by consumers and businesses alike. B2B buyers should ensure that their suppliers maintain ethical labor practices and have traceable supply chains, which can mitigate risks and enhance brand reputation. By prioritizing sustainability and ethical sourcing, buyers can foster long-term partnerships that contribute to a healthier planet and a responsible business image.
How Has the Electrical Harness Manufacturing Sector Evolved Over Time?
The evolution of the electrical harness manufacturing sector has been marked by technological advancements and changing consumer demands. Initially focused on basic electrical connections, the sector has transformed into a high-tech industry that integrates sophisticated design and engineering processes. The introduction of computer-aided design (CAD) and simulation software has revolutionized the way manufacturers develop harnesses, allowing for greater precision and efficiency.
Over the past few decades, the rise of the automotive and electronics industries has significantly influenced the sector, leading to increased demand for specialized harnesses that cater to complex systems in vehicles and consumer electronics. As electric and hybrid vehicles gain popularity, the need for advanced electrical harness solutions continues to grow, driving innovation and investment in the sector.
Today, electrical harness manufacturers are not only suppliers but also strategic partners in product development, contributing to enhanced functionality and safety in various applications. For B2B buyers, understanding this evolution is critical for identifying suppliers who can meet current and future needs effectively.
Frequently Asked Questions (FAQs) for B2B Buyers of Electrical Harness Manufacturers
-
How do I ensure quality when sourcing electrical harness manufacturers internationally?
To ensure quality when sourcing electrical harness manufacturers, begin by conducting thorough research into potential suppliers. Look for manufacturers with certifications such as ISO 9001, which indicates adherence to quality management standards. Request samples to evaluate their craftsmanship and materials used. Additionally, consider visiting the manufacturing facilities if possible, or utilize third-party inspection services to verify quality before placing larger orders. -
What are the best practices for vetting electrical harness suppliers?
Vetting electrical harness suppliers involves several key steps. Start with checking their industry reputation through online reviews and testimonials. Request references from previous clients to understand their experience. Verify the supplier’s certifications and compliance with international standards. Additionally, assess their financial stability and production capacity to ensure they can meet your demands. Engaging in initial smaller transactions can also help gauge reliability before committing to larger orders. -
What customization options should I expect from electrical harness manufacturers?
Most electrical harness manufacturers offer a range of customization options to meet specific requirements. These can include variations in wire gauges, insulation types, connectors, and overall harness configurations. Discuss your project needs in detail with potential suppliers to understand their capabilities. Consider providing design specifications or CAD files to facilitate accurate customization. It’s essential to ensure that the manufacturer can accommodate any unique requirements related to your application. -
What is the typical minimum order quantity (MOQ) for electrical harnesses?
Minimum order quantities (MOQs) for electrical harnesses can vary significantly based on the manufacturer and the complexity of the harness. Generally, MOQs can range from 100 to 1,000 units. However, some manufacturers may offer lower MOQs for custom designs, especially for prototyping. It’s advisable to discuss MOQs upfront and explore options for bulk orders or long-term partnerships to negotiate better terms. -
What payment terms are common when dealing with electrical harness manufacturers?
Payment terms can differ widely among electrical harness manufacturers, but common practices include a deposit (typically 30-50%) upfront, with the balance due upon completion of the order or prior to shipping. Some manufacturers may offer net terms (e.g., Net 30 or Net 60) for established clients. Always clarify payment terms and conditions before finalizing contracts, and consider using secure payment methods to mitigate risks. -
How can I manage logistics when importing electrical harnesses?
Managing logistics for importing electrical harnesses involves coordinating with suppliers, freight forwarders, and customs brokers. Start by determining the most efficient shipping method based on cost and delivery timelines. Ensure all documentation is in order to avoid customs delays, including invoices, packing lists, and certificates of origin. Working with an experienced logistics partner can streamline the process, helping you navigate international regulations and minimize potential issues. -
What quality assurance measures should I expect from electrical harness manufacturers?
Reputable electrical harness manufacturers typically implement stringent quality assurance measures. These may include in-process inspections, final product testing, and compliance checks with international standards. Ask potential suppliers about their QA processes, including the use of automated testing equipment and adherence to industry-specific regulations. Requesting quality certificates and test reports can provide further assurance of their commitment to quality. -
What are the common challenges faced when sourcing electrical harnesses from international suppliers?
Sourcing electrical harnesses from international suppliers can present challenges such as communication barriers, differing regulatory standards, and lead time discrepancies. Time zone differences can complicate timely responses, while variations in quality standards may lead to unexpected issues. To mitigate these challenges, establish clear communication channels, set realistic timelines, and ensure thorough documentation of all agreements. Building strong relationships with suppliers can also help address challenges more effectively.
Important Disclaimer & Terms of Use
⚠️ Important Disclaimer
The information provided in this guide, including content regarding manufacturers, technical specifications, and market analysis, is for informational and educational purposes only. It does not constitute professional procurement advice, financial advice, or legal advice.
While we have made every effort to ensure the accuracy and timeliness of the information, we are not responsible for any errors, omissions, or outdated information. Market conditions, company details, and technical standards are subject to change.
B2B buyers must conduct their own independent and thorough due diligence before making any purchasing decisions. This includes contacting suppliers directly, verifying certifications, requesting samples, and seeking professional consultation. The risk of relying on any information in this guide is borne solely by the reader.
Strategic Sourcing Conclusion and Outlook for Electrical Harness Manufacturers
The landscape of electrical harness manufacturing is evolving rapidly, driven by technological advancements and increasing global demand. For international B2B buyers, particularly from Africa, South America, the Middle East, and Europe, strategic sourcing has never been more crucial. By leveraging data-driven insights and fostering collaborative partnerships, buyers can optimize their supply chains, reduce costs, and enhance product quality.
What are the key takeaways for B2B buyers in sourcing electrical harnesses? First, prioritize suppliers who demonstrate a commitment to innovation and sustainability. Engaging with manufacturers that employ advanced materials and eco-friendly practices will not only align with global standards but also improve long-term profitability. Second, consider the geographical advantages of sourcing from regions with established electrical infrastructure and skilled labor, such as Eastern Europe or South Africa, which can mitigate risks and enhance responsiveness.
Looking ahead, the electrical harness market is poised for growth, fueled by emerging technologies such as electric vehicles and smart appliances. B2B buyers should act now to secure their supply chains and capitalize on these trends. By embracing strategic sourcing, companies can position themselves favorably for future opportunities. Engage with reliable manufacturers today to build a resilient, efficient, and innovative supply chain for tomorrow.