Cut Costs with Laser Metal Cutting Machine China (2025)
Introduction: Navigating the Global Market for laser metal cutting machine china
In the rapidly evolving landscape of industrial manufacturing, sourcing a laser metal cutting machine from China poses a significant challenge for international B2B buyers. With a myriad of options available, businesses often struggle to identify reliable suppliers, assess machine capabilities, and ensure competitive pricing. This guide serves as a crucial resource, offering comprehensive insights into the types of laser cutting machines, their diverse applications across various industries, and essential strategies for vetting suppliers.
Buyers from Africa, South America, the Middle East, and Europe, particularly in countries like Italy and Spain, will benefit from an in-depth exploration of the laser cutting technology landscape. Understanding the differences between fiber and CO2 lasers, as well as their specific advantages for metal processing, is vital for making informed purchasing decisions. Furthermore, this guide will provide actionable insights into cost considerations, maintenance requirements, and technological advancements, empowering buyers to navigate the complexities of the global market confidently.
By equipping decision-makers with the knowledge necessary to evaluate their options, this guide aims to facilitate seamless sourcing experiences. Whether you are a small business looking to upgrade your manufacturing capabilities or a large corporation aiming to optimize production efficiency, the insights provided here will help you make strategic, informed choices that align with your operational goals.
Understanding laser metal cutting machine china Types and Variations
Type Name | Key Distinguishing Features | Primary B2B Applications | Brief Pros & Cons for Buyers |
---|---|---|---|
CO2 Laser Cutting Machine | Utilizes CO2 gas for high precision cutting. | Aerospace, automotive, and signage industries. | Pros: Excellent for non-metal materials; high cutting speed. Cons: Higher operational costs due to gas consumption. |
Fiber Laser Cutting Machine | Employs fiber optics for efficient energy transfer. | Metal fabrication, electronics, and medical devices. | Pros: Low maintenance; high energy efficiency. Cons: Limited to metal cutting; initial investment can be high. |
YAG Laser Cutting Machine | Uses Yttrium Aluminum Garnet crystals for cutting. | Jewelry making, electronics, and precision parts. | Pros: High precision and excellent beam quality. Cons: Slower cutting speed compared to CO2 and fiber lasers. |
Plasma Laser Cutting Machine | Combines plasma technology with laser for thicker materials. | Heavy industries, shipbuilding, and construction. | Pros: Effective for thick materials; versatile. Cons: Lower precision than other types; more post-processing required. |
Hybrid Laser Cutting Machine | Integrates multiple laser technologies for versatility. | Aerospace, automotive, and sheet metal industries. | Pros: Combines strengths of different lasers; adaptable to various materials. Cons: Complexity can lead to higher maintenance needs. |
What are the Characteristics of CO2 Laser Cutting Machines?
CO2 laser cutting machines are renowned for their high precision and versatility, particularly in cutting non-metal materials such as wood, plastics, and textiles. They are widely used in industries like aerospace, automotive, and signage, where detailed designs and intricate patterns are essential. When considering a CO2 machine, B2B buyers should evaluate the cost of gas and operational efficiency, as these can impact long-term expenses.
How Do Fiber Laser Cutting Machines Stand Out?
Fiber laser cutting machines leverage fiber optics to deliver high-intensity laser beams, making them highly efficient for metal cutting applications. They are particularly favored in metal fabrication, electronics, and medical device manufacturing due to their speed and low maintenance requirements. Buyers should consider the types of metals they plan to cut, as fiber lasers excel with thin to medium thicknesses but may have limitations with thicker materials.
What Makes YAG Laser Cutting Machines Suitable for Precision Work?
YAG (Yttrium Aluminum Garnet) laser cutting machines are distinguished by their ability to produce high-quality beams, ideal for precision applications like jewelry making and electronics. They offer excellent cutting capabilities for small, intricate parts. However, their cutting speed is generally slower compared to CO2 and fiber lasers. Buyers should assess their specific needs for precision versus speed when considering YAG machines.
In What Situations Should Plasma Laser Cutting Machines Be Used?
Plasma laser cutting machines are ideal for heavy industries that require cutting thicker materials, such as shipbuilding and construction. They combine plasma technology with laser cutting, providing versatility in handling various materials. While they are effective for thick cuts, B2B buyers should note that plasma machines may require more post-processing due to lower precision compared to other laser types.
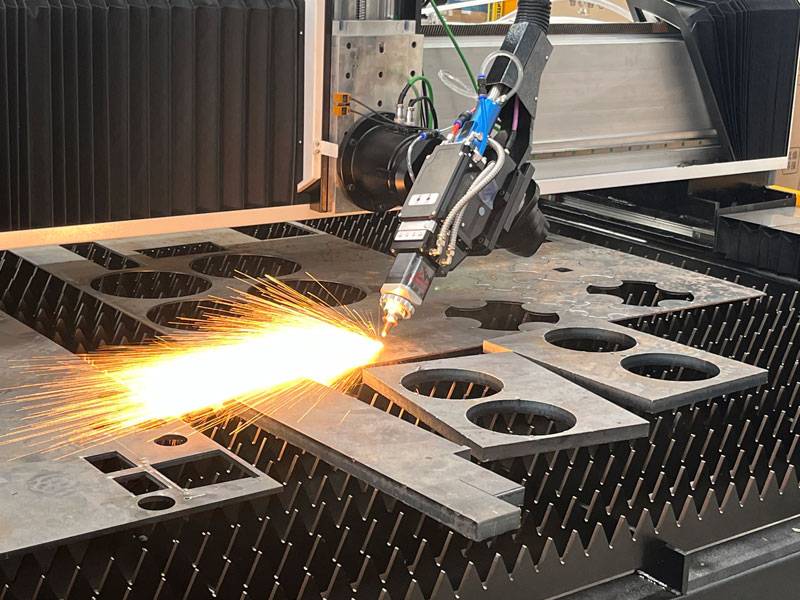
A stock image related to laser metal cutting machine china.
Why Consider Hybrid Laser Cutting Machines for Diverse Applications?
Hybrid laser cutting machines offer a unique solution by integrating multiple laser technologies, allowing them to adapt to various materials and thicknesses. They are particularly beneficial in industries like aerospace and automotive, where versatility is crucial. However, the complexity of hybrid systems can lead to increased maintenance requirements. Buyers should weigh the benefits of adaptability against the potential for higher upkeep costs.
Related Video: [LaserMen] 1500w handheld fiber metal welding and cutting laser machine laser welders
Key Industrial Applications of laser metal cutting machine china
Industry/Sector | Specific Application of laser metal cutting machine china | Value/Benefit for the Business | Key Sourcing Considerations for this Application |
---|---|---|---|
Automotive Manufacturing | Cutting intricate metal parts for vehicle assembly | Enhanced precision leads to improved product quality and reduced waste | Consider machine speed, precision, and compatibility with various metals |
Aerospace Engineering | Fabrication of lightweight structural components | Reduces overall weight, improving fuel efficiency and performance | Look for certifications and compliance with industry standards |
Electronics Production | Manufacturing of circuit boards and electronic housings | Increases production speed and reduces labor costs | Evaluate the machine’s ability to handle thin materials and small tolerances |
Construction and Architecture | Custom metalwork for building structures | Offers design flexibility and faster construction timelines | Assess the machine’s capability for large sheets and complex designs |
Metal Fabrication Services | Custom cutting for various metal products | Provides versatility in service offerings and meets diverse client needs | Check for after-sales support and availability of replacement parts |
How is Laser Metal Cutting Used in Automotive Manufacturing?
In the automotive manufacturing sector, laser metal cutting machines from China are crucial for producing intricate metal parts that are essential for vehicle assembly. These machines offer high precision, which significantly reduces material waste and enhances the overall quality of automotive components. For international buyers, especially those in Africa and South America, it’s essential to consider the machine’s speed and compatibility with various metals to ensure efficient production lines.
What Role Does Laser Cutting Play in Aerospace Engineering?
Laser cutting technology is a game-changer in aerospace engineering, allowing for the fabrication of lightweight structural components. These components are vital for reducing the overall weight of aircraft, thereby improving fuel efficiency and performance. Buyers from Europe, particularly Italy and Spain, should prioritize sourcing machines that comply with stringent aerospace industry standards and certifications to ensure safety and reliability in their applications.
How is Laser Metal Cutting Beneficial for Electronics Production?
In the electronics production industry, laser metal cutting machines are employed to manufacture circuit boards and electronic housings. This technology accelerates production speed while minimizing labor costs, which is crucial for staying competitive in a fast-paced market. Buyers should focus on machines that can handle thin materials and achieve small tolerances to meet the precise specifications required in electronics manufacturing.
What Advantages Does Laser Cutting Offer in Construction and Architecture?
Laser cutting technology is widely used in construction and architecture for custom metalwork, enabling architects and builders to create intricate designs. This capability not only provides design flexibility but also speeds up construction timelines, leading to cost savings. Buyers should evaluate machines based on their ability to handle large sheets and complex designs, ensuring they can meet the diverse demands of modern architecture.
Why Choose Laser Cutting for Metal Fabrication Services?
For metal fabrication services, laser cutting machines offer the versatility needed to produce a wide range of custom metal products. This flexibility allows service providers to meet diverse client needs effectively. International buyers should consider after-sales support and the availability of replacement parts when sourcing these machines to maintain operational efficiency and minimize downtime.
Related Video: Metal laser cutting machine LS7 | BLM GROUP
3 Common User Pain Points for ‘laser metal cutting machine china’ & Their Solutions
Scenario 1: Navigating Quality Concerns with Chinese Laser Metal Cutting Machines
The Problem: Many B2B buyers, especially those from Africa and South America, often encounter quality assurance issues when sourcing laser metal cutting machines from China. They may receive equipment that does not meet their specified requirements or industry standards, leading to operational inefficiencies and potential financial losses. The lack of reliable product information and the challenge of verifying manufacturers can create significant apprehension in decision-making.
The Solution: To mitigate quality concerns, buyers should conduct thorough due diligence before finalizing any purchase. Start by sourcing machines from established manufacturers with a proven track record. Look for suppliers who provide detailed specifications and certifications for their machines, such as ISO 9001 or CE markings. Engaging third-party inspection services prior to shipment can also ensure that the machines meet the required quality standards. Additionally, consider visiting the manufacturing site or attending trade shows in China to establish direct relationships with suppliers. This can help in assessing the manufacturing processes and product quality firsthand.
Scenario 2: Understanding Technical Specifications and Applications
The Problem: International buyers, particularly from the Middle East and Europe, frequently struggle with the technical specifications of laser metal cutting machines. The terminology and technology can be overwhelming, making it difficult to determine which machine will best fit their specific cutting needs. This confusion can lead to purchasing a machine that is either underperforming or over-specified for their operations, resulting in wasted resources.
The Solution: Buyers should invest time in understanding the fundamental specifications that impact performance, such as cutting speed, laser type (e.g., fiber vs. CO2), and material compatibility. Engaging with technical experts or consultants who specialize in laser cutting technology can provide valuable insights tailored to specific applications. Additionally, requesting demonstrations or trial periods from suppliers can help buyers evaluate the machine’s performance in real-world conditions. It’s also beneficial to join industry forums or groups where peers share their experiences and recommendations regarding different laser cutting machines.
Scenario 3: Managing After-Sales Support and Spare Parts Availability
The Problem: A common pain point for B2B buyers is the lack of reliable after-sales support and spare parts availability for laser metal cutting machines sourced from China. Once the machine is installed, companies may face delays in obtaining necessary maintenance or repairs, which can lead to significant downtimes and productivity losses.
The Solution: To address this issue, buyers should prioritize suppliers who offer robust after-sales services, including installation support, training, and timely access to spare parts. When negotiating contracts, ensure that the supplier commits to specific response times for service requests and part replacements. It’s also advisable to inquire about the availability of spare parts and whether the supplier maintains a stock in regional warehouses to expedite shipping. Forming partnerships with local service providers who are familiar with the machines can also enhance maintenance efficiency. Lastly, developing a preventive maintenance schedule can help in anticipating and minimizing potential downtime, ensuring continuous operations.
Strategic Material Selection Guide for laser metal cutting machine china
What Are the Key Materials for Laser Metal Cutting Machines from China?
When selecting materials for laser metal cutting machines, international B2B buyers must consider several factors that impact performance, cost, and application suitability. Below are analyses of four common materials used in laser cutting, focusing on their properties, advantages, disadvantages, and specific considerations for buyers from Africa, South America, the Middle East, and Europe.
How Does Steel Perform in Laser Metal Cutting Applications?
Key Properties: Steel, particularly carbon and stainless steel, is known for its strength and durability. It has a high melting point (around 1370°C for carbon steel) and excellent tensile strength, making it suitable for high-pressure applications. Stainless steel offers additional corrosion resistance due to its chromium content.
Pros & Cons: The durability of steel makes it ideal for heavy-duty applications, but it can be more expensive than other materials, particularly stainless steel. Manufacturing complexity varies; while carbon steel is easier to cut, stainless steel may require more advanced laser settings to achieve clean cuts.
Impact on Application: Steel is widely used in construction, automotive, and aerospace industries. Its compatibility with various media makes it a versatile choice for different applications.
Considerations for International Buyers: Compliance with standards such as ASTM A36 for carbon steel or ASTM A240 for stainless steel is crucial. Buyers should also consider local availability and import tariffs that might affect overall costs.
What Are the Advantages of Aluminum in Laser Cutting?
Key Properties: Aluminum is lightweight and has excellent thermal conductivity. It melts at a lower temperature (around 660°C) compared to steel, which can lead to faster cutting speeds.
Pros & Cons: The lightweight nature of aluminum makes it suitable for applications where weight reduction is essential, such as in the aerospace industry. However, it is less durable than steel and can be more expensive due to its processing requirements.
Impact on Application: Aluminum is often used in automotive parts, consumer electronics, and architectural applications. Its compatibility with various finishes allows for aesthetic versatility.
Considerations for International Buyers: Buyers should ensure compliance with standards like ASTM B221 for aluminum extrusions. Additionally, they should consider the availability of specific aluminum alloys that meet their application needs.
Why Choose Copper for Laser Metal Cutting?
Key Properties: Copper is known for its excellent electrical and thermal conductivity, making it ideal for electrical applications. It has a relatively low melting point (around 1085°C) and is highly ductile.
Pros & Cons: The high conductivity of copper makes it a preferred choice for electrical components. However, it is more expensive than steel and can be challenging to cut due to its reflective surface, which may require specialized laser settings.
Impact on Application: Copper is commonly used in electrical wiring, circuit boards, and heat exchangers. Its unique properties make it suitable for specific applications that require high conductivity.
Considerations for International Buyers: Compliance with standards such as ASTM B170 for copper and its alloys is essential. Buyers should also consider the environmental impact of copper mining and processing, especially in regions with strict environmental regulations.
What About Plastic Materials in Laser Cutting?
Key Properties: While not a metal, plastics such as acrylic and polycarbonate are increasingly used in laser cutting. They are lightweight, have good chemical resistance, and can be cut at lower temperatures.
Pros & Cons: Plastics offer design flexibility and can be produced at a lower cost than metals. However, they are not suitable for high-temperature applications and may not provide the same level of durability as metals.
Impact on Application: Plastics are often used in signage, displays, and various consumer products. Their versatility makes them suitable for a wide range of applications.
Considerations for International Buyers: Compliance with standards like ASTM D638 for plastics is crucial. Buyers should also consider the recycling and disposal regulations in their regions.
Summary Table of Material Selection for Laser Metal Cutting Machines
Material | Typical Use Case for laser metal cutting machine china | Key Advantage | Key Disadvantage/Limitation | Relative Cost (Low/Med/High) |
---|---|---|---|---|
Steel | Automotive, construction, aerospace | High durability and strength | Higher cost for stainless steel | Medium |
Aluminum | Aerospace, automotive parts, electronics | Lightweight and good thermal conductivity | Less durable than steel | High |
Copper | Electrical wiring, circuit boards | Excellent conductivity | Expensive and challenging to cut | High |
Plastic | Signage, displays, consumer products | Design flexibility and low cost | Not suitable for high-temperature applications | Low |
This guide provides essential insights for international B2B buyers looking to make informed decisions regarding material selection for laser metal cutting machines sourced from China. Understanding the properties, advantages, and limitations of each material will facilitate better purchasing strategies tailored to specific industry needs.
In-depth Look: Manufacturing Processes and Quality Assurance for laser metal cutting machine china
What Are the Main Stages of Manufacturing Laser Metal Cutting Machines in China?
The manufacturing process of laser metal cutting machines in China involves several critical stages, ensuring the machines are of high quality and capable of meeting international standards. Understanding these stages can help B2B buyers from Africa, South America, the Middle East, and Europe make informed purchasing decisions.
1. Material Preparation
The first stage in the manufacturing process is material preparation. High-quality raw materials, such as steel, aluminum, and other alloys, are sourced based on the specifications of the laser cutting machine. Material thickness and type are crucial for the machine’s performance. Suppliers often use advanced software to calculate the optimal material requirements, ensuring minimal waste and maximizing efficiency.
2. Forming Techniques
After material preparation, forming techniques are employed to shape the components of the laser cutting machine. Common forming methods include laser cutting, bending, and punching. Laser cutting is particularly important as it allows for precise shapes and sizes, which are essential for the machine’s assembly. The use of CNC (Computer Numerical Control) machines ensures high accuracy during this stage, which is vital for the overall performance of the final product.
3. Assembly Process
The assembly process is where all the pre-formed components come together. Skilled technicians or robotic systems perform this stage, ensuring that each part fits perfectly and functions as intended. Assembly includes integrating the laser source, optics, and control systems, which must be aligned precisely to achieve optimal cutting performance. Quality assurance checkpoints are often established during assembly to detect any issues early on.
4. Finishing Touches
Finishing involves surface treatments, painting, and final inspections. Surface treatments, such as powder coating, enhance durability and aesthetics. The finishing stage is crucial, as it affects both the machine’s lifespan and its operational efficiency. Final inspections are conducted to ensure that all components meet the required specifications before the product is packaged and shipped.
How Is Quality Assurance Implemented in Laser Metal Cutting Machine Manufacturing?
Quality assurance (QA) is integral to the manufacturing of laser metal cutting machines, ensuring that they meet both international and industry-specific standards. B2B buyers should be familiar with these QA processes to ensure they are sourcing from reliable manufacturers.
International Standards: What Should Buyers Look For?
Many manufacturers in China adhere to international quality standards, such as ISO 9001, which provides a framework for quality management systems. Compliance with ISO 9001 indicates that a manufacturer has established processes for continuous improvement and customer satisfaction.
Additionally, industry-specific certifications such as CE (Conformité Européenne) for European markets and API (American Petroleum Institute) for oil and gas applications are crucial. These certifications ensure that the machines meet safety and performance regulations in their respective markets.
What Are the Key Quality Control Checkpoints?
Quality control (QC) involves several checkpoints throughout the manufacturing process. Here are the primary checkpoints that B2B buyers should be aware of:
1. Incoming Quality Control (IQC)
IQC is the first checkpoint, where raw materials are inspected upon arrival. This step ensures that the materials meet the specified standards before they enter the manufacturing process. Buyers should inquire about the supplier’s IQC procedures to ensure that high-quality materials are being used.
2. In-Process Quality Control (IPQC)
During the manufacturing process, IPQC checks are conducted to monitor the quality of work-in-progress items. This involves regular inspections and measurements to ensure that components are being manufactured within specified tolerances. A robust IPQC system helps catch defects early, minimizing costly rework.
3. Final Quality Control (FQC)
FQC occurs at the end of the manufacturing process, where the completed laser cutting machine undergoes a thorough inspection. This includes functional tests to assess cutting accuracy and overall performance. Buyers should request detailed FQC reports, as these documents provide insights into the machine’s quality before shipment.
How Can B2B Buyers Verify Supplier Quality Control?
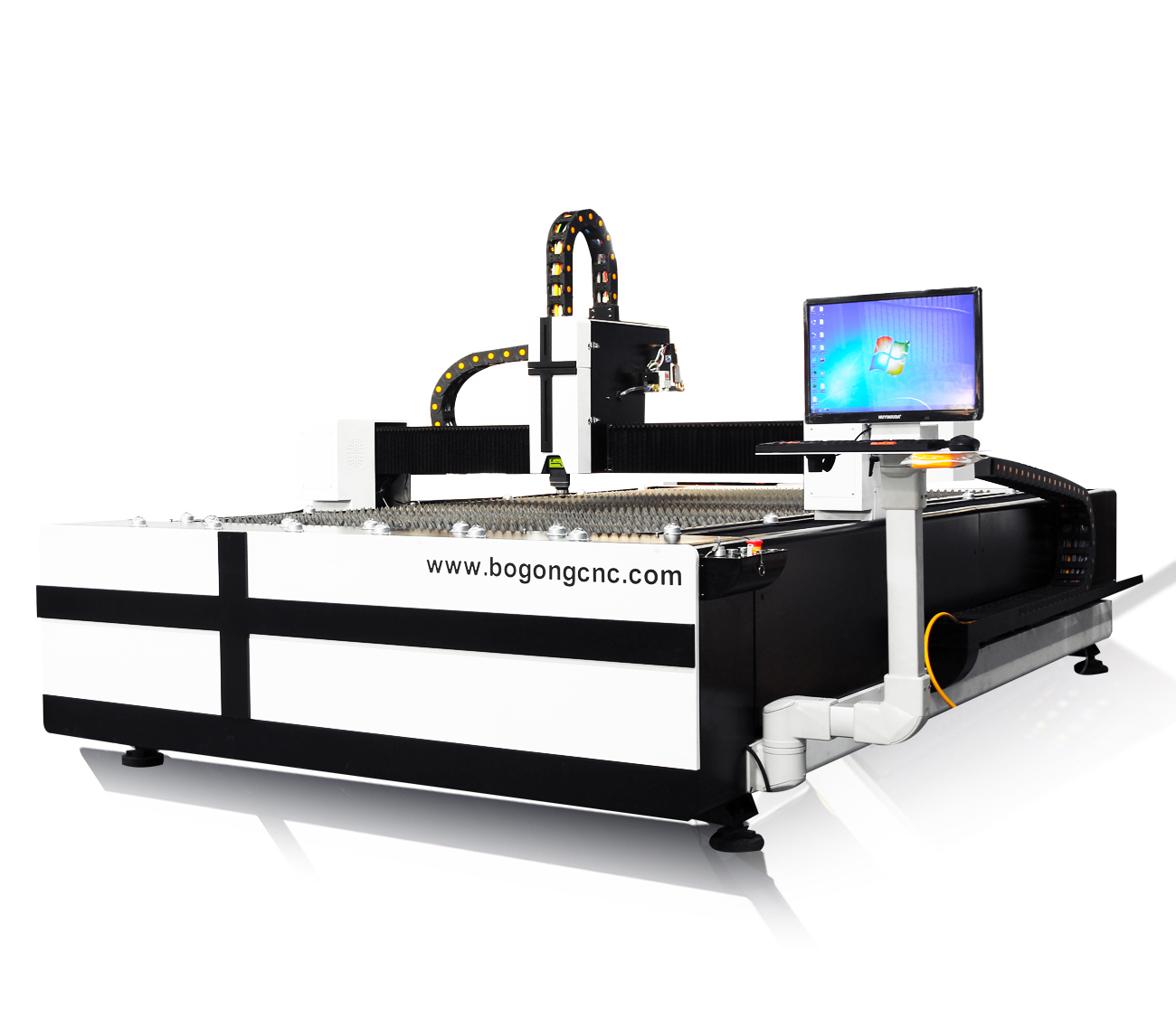
A stock image related to laser metal cutting machine china.
B2B buyers must take proactive steps to verify the quality control practices of their suppliers. Here are effective strategies to ensure that you are partnering with a reputable manufacturer:
1. Conducting Supplier Audits
Performing on-site audits of the manufacturing facility can provide valuable insights into the supplier’s quality control processes. During an audit, buyers can assess the adherence to international standards and the effectiveness of quality checkpoints.
2. Requesting Quality Reports
Buyers should request quality control reports, including IQC, IPQC, and FQC documents. These reports provide critical information about the manufacturing processes and highlight any issues that may have arisen during production.
3. Utilizing Third-Party Inspection Services
Engaging third-party inspection services can help verify the quality of the laser cutting machines before they are shipped. These services can conduct independent inspections and provide objective assessments of the product’s quality.
What Are the Specific Quality Control Nuances for International B2B Buyers?
For B2B buyers from regions like Africa, South America, the Middle East, and Europe, understanding the nuances of quality control is essential for successful procurement. Here are some considerations:
-
Cultural Differences: Different regions may have varying expectations regarding quality and service. It is important to communicate clearly and establish mutual understanding with suppliers.
-
Regulatory Compliance: Ensure that the products meet the regulatory requirements specific to your region. This may include additional certifications or compliance documentation that manufacturers must provide.
- Logistical Challenges: Be aware of potential logistical challenges that could impact the quality of the product upon arrival. Proper packaging and handling during shipping are crucial to maintain the machine’s integrity.
By understanding the manufacturing processes and quality assurance practices of laser metal cutting machines produced in China, international B2B buyers can make informed decisions that align with their operational needs and standards.
Practical Sourcing Guide: A Step-by-Step Checklist for ‘laser metal cutting machine china’
In today’s competitive manufacturing landscape, sourcing a laser metal cutting machine from China can be a strategic move for businesses in Africa, South America, the Middle East, and Europe. This guide provides a structured checklist to ensure a successful procurement process, enabling you to make informed decisions and maximize your investment.
Step 1: Define Your Technical Specifications
Clearly outline your operational needs, including the type of materials you will cut, thickness ranges, and desired precision. This step is critical as it directly impacts the machine’s capability and suitability for your production line. Consider factors such as:
– Power Output: Machines typically range from 500W to 6000W; higher power allows for cutting thicker materials.
– Cutting Speed: Understand the speed requirements to meet your production goals.
Step 2: Research Market Trends and Technologies
Stay updated on the latest advancements in laser cutting technology. This knowledge will help you identify machines that offer the best value and efficiency. Look for:
– Innovative Features: Such as automatic focusing, integrated software for design, and energy-efficient models.
– Industry Feedback: Consult industry reports or forums to gauge what features are becoming standard.
Step 3: Evaluate Potential Suppliers
Thoroughly vet potential suppliers to ensure credibility and reliability. Request detailed company profiles and case studies that highlight their experience in the laser cutting sector. Key aspects to consider include:
– Certifications: Verify that the supplier holds relevant certifications, such as ISO 9001, which indicates quality management standards.
– Customer References: Reach out to existing customers for insights on machine performance and supplier support.
Step 4: Request and Compare Quotes
Once you’ve shortlisted suppliers, request detailed quotations that include pricing, delivery timelines, and after-sales support. Comparing quotes is essential to ensure you receive a competitive offer. Focus on:
– Total Cost of Ownership: Consider not just the initial purchase price but also maintenance costs, energy consumption, and potential downtime.
– Warranty and Support: Understand the warranty terms and the availability of spare parts and technical support.
Step 5: Negotiate Terms and Conditions
Engage in negotiations to finalize the price and terms of purchase. This step is crucial to protect your interests and ensure a favorable deal. Pay attention to:
– Payment Terms: Discuss options such as deposits, payment schedules, and any financing options available.
– Delivery Terms: Clarify shipping responsibilities, customs clearance, and timelines to avoid delays.
Step 6: Conduct a Pre-Shipment Inspection
Before finalizing the purchase, arrange for a pre-shipment inspection to verify that the machine meets your specifications. This step helps to mitigate risks associated with receiving subpar equipment. Ensure that:
– Performance Testing: The machine is tested for operational efficiency and quality.
– Documentation: All necessary documentation, including manuals and compliance certificates, is provided.
Step 7: Plan for Installation and Training
Post-purchase, ensure a smooth transition by planning for installation and operator training. This is vital to maximize the machine’s potential and minimize operational hiccups. Consider:
– Professional Installation: Engage the supplier for installation to ensure compliance with safety standards.
– Training Programs: Arrange for training sessions for your operators to familiarize them with the machine’s features and maintenance requirements.
By following these steps, B2B buyers can strategically navigate the procurement process for laser metal cutting machines from China, ensuring they make informed decisions that align with their operational needs and business goals.
Comprehensive Cost and Pricing Analysis for laser metal cutting machine china Sourcing
What are the Key Cost Components of Laser Metal Cutting Machines from China?
When sourcing laser metal cutting machines from China, understanding the cost structure is crucial. The primary components influencing the cost include:
-
Materials: The quality and type of materials used for the machine significantly affect the overall cost. High-grade steel and advanced optics can elevate the price but ensure better durability and performance.
-
Labor: Labor costs in China can vary depending on the region and skill level required. Skilled labor for assembly and quality control can add to the expense, impacting the machine’s final price.
-
Manufacturing Overhead: This includes costs associated with factory operations, utilities, and equipment maintenance. Efficient production processes can help minimize these costs, thus affecting pricing.
-
Tooling: Custom tooling for specific applications can increase upfront costs but may lead to better precision and efficiency in the long run.
-
Quality Control (QC): Investing in quality control processes ensures that machines meet international standards, which may add to the cost but is essential for reliability and performance.
-
Logistics: Shipping costs, including freight charges and customs duties, can significantly impact the total cost, especially for international buyers. Understanding the best shipping methods and routes can help manage these expenses.
-
Margin: Suppliers typically include a profit margin in their pricing. This margin can vary based on competition, demand, and the supplier’s business model.
What Influences the Pricing of Laser Metal Cutting Machines?
Several factors can influence the price of laser metal cutting machines sourced from China:
-
Volume and Minimum Order Quantity (MOQ): Bulk orders often attract discounts, making it beneficial for buyers who can commit to larger quantities.
-
Specifications and Customization: Customized machines tailored to specific applications can lead to higher prices. It’s essential to weigh the necessity of these custom features against your budget.
-
Materials and Quality Certifications: Machines made from superior materials and certified for quality (e.g., CE, ISO) generally command higher prices. Buyers should assess whether these certifications are necessary for their operations.
-
Supplier Factors: The reputation and reliability of the supplier can affect pricing. Established suppliers may charge more due to their experience and quality assurance processes.
-
Incoterms: Understanding the Incoterms used in the transaction can clarify who bears the costs and risks at various stages of shipping, impacting the total landed cost.
How Can Buyers Negotiate for Better Pricing on Laser Metal Cutting Machines?
Negotiation plays a pivotal role in securing favorable pricing. Here are some strategies for international B2B buyers:
-
Conduct Market Research: Knowing the market price range for similar machines can empower you during negotiations.
-
Build Relationships: Establishing a good rapport with suppliers can lead to better terms and pricing flexibility.
-
Leverage Volume Discounts: If possible, commit to larger orders to negotiate lower prices per unit.
-
Discuss Payment Terms: Flexible payment terms can sometimes reduce upfront costs, making the purchase more manageable.
-
Consider Total Cost of Ownership (TCO): Evaluate not just the initial purchase price but also the long-term costs associated with maintenance, energy consumption, and potential downtime.
What Pricing Nuances Should International Buyers Be Aware of?
International buyers, particularly from Africa, South America, the Middle East, and Europe, should consider the following nuances:
-
Exchange Rates: Fluctuating exchange rates can impact the final cost. It’s advisable to lock in rates where possible.
-
Import Duties and Taxes: Understanding the local regulations regarding import duties can help estimate the total landed cost more accurately.
-
Cultural Differences: Negotiation styles and business practices vary by region. Familiarizing yourself with these can enhance communication and lead to better outcomes.
Disclaimer on Indicative Prices
Prices for laser metal cutting machines can vary widely based on the factors outlined above. It is essential to obtain quotes from multiple suppliers and conduct thorough due diligence before making any purchasing decisions.
Alternatives Analysis: Comparing laser metal cutting machine china With Other Solutions
Understanding Alternative Solutions to Laser Metal Cutting Machines
In today’s competitive manufacturing landscape, B2B buyers must evaluate various cutting technologies to determine the best fit for their operational needs. While laser metal cutting machines from China are known for their precision and efficiency, alternative methods may offer distinct advantages depending on specific applications, budget constraints, and operational contexts. This section presents a comparative analysis of laser metal cutting machines against two viable alternatives: plasma cutting and water jet cutting.
Comparison Table of Cutting Technologies
Comparison Aspect | Laser Metal Cutting Machine China | Plasma Cutting | Water Jet Cutting |
---|---|---|---|
Performance | High precision, clean cuts | Moderate precision, rougher edges | High precision, no heat-affected zone |
Cost | Moderate initial investment, low operational costs | Lower initial investment, higher operational costs | High initial investment, moderate operational costs |
Ease of Implementation | Requires skilled technicians for setup | Easier to set up, less training needed | Complex setup, requires specialized training |
Maintenance | Low maintenance, regular checks needed | Moderate maintenance, consumables needed | High maintenance, frequent part replacements |
Best Use Case | Thin to medium metals, intricate designs | Thick materials, quick cuts | All materials, intricate shapes, no thermal distortion |
Detailed Breakdown of Alternatives
What are the Advantages and Disadvantages of Plasma Cutting?
Plasma cutting utilizes a high-velocity jet of ionized gas to cut through electrically conductive materials. Its primary advantage is the lower initial investment compared to laser cutting, making it an attractive option for startups or smaller operations. Plasma cutting is particularly effective for thick materials and can achieve rapid cuts, which enhances productivity.
However, plasma cutting does have drawbacks. The precision is generally lower than that of laser cutting, leading to rougher edges that may require additional finishing work. Additionally, plasma cutting can produce a heat-affected zone, which can compromise the integrity of the material being cut.
How Does Water Jet Cutting Compare to Laser Metal Cutting?
Water jet cutting employs a high-pressure jet of water, often mixed with abrasives, to cut through various materials. One of its most significant advantages is the ability to cut a wide range of materials, including metals, glass, and composites, without creating a heat-affected zone. This makes it ideal for applications where material integrity is critical, such as aerospace and automotive components.
On the downside, water jet cutting typically involves a higher initial investment and more complex machinery. The operational costs can also be moderate, as it requires regular maintenance and replacement of parts, especially the cutting nozzles. Additionally, the setup and operation of water jet cutting machinery may require specialized training, which could lead to longer lead times for new users.
How Can B2B Buyers Choose the Right Cutting Solution?
Choosing the right cutting technology requires a careful assessment of various factors, including the type of materials to be processed, budget constraints, and the desired level of precision. Buyers from Africa, South America, the Middle East, and Europe should consider their specific operational requirements and long-term goals.
For companies focusing on intricate designs and high precision with a willingness to invest more upfront, laser metal cutting machines from China may offer the best value. Conversely, businesses that prioritize quick cuts on thicker materials might find plasma cutting to be more economical. Water jet cutting is suitable for those needing versatility across different materials and applications, albeit at a higher cost.
Ultimately, the decision should align with both immediate needs and future scalability, ensuring that the chosen technology will support growth and efficiency in the long run.
Essential Technical Properties and Trade Terminology for laser metal cutting machine china
What Are the Essential Technical Properties of Laser Metal Cutting Machines?
When considering the purchase of a laser metal cutting machine from China, understanding the essential technical specifications is crucial for making informed decisions. Here are some of the key properties to consider:
1. Material Grade Compatibility
Laser cutting machines are designed to work with specific grades of materials, such as stainless steel, aluminum, and carbon steel. The material grade affects the cutting speed, quality, and overall efficiency of the process. Buyers should ensure that the machine can handle the materials they plan to work with, as this will directly impact production capabilities and costs.
2. Cutting Thickness Capacity
The cutting thickness capacity indicates the maximum thickness of material that the machine can effectively cut. This specification is vital for B2B buyers as it determines the range of applications the machine can serve. A machine with a higher cutting thickness can handle more demanding projects, thereby expanding business opportunities.
3. Positioning Accuracy and Tolerance
Positioning accuracy refers to the machine’s ability to place the laser beam precisely where it is needed. Tolerance is the allowable deviation from a specified dimension. High accuracy and low tolerance are essential for industries requiring tight specifications, such as aerospace and automotive. Poor accuracy can lead to waste and increased costs, making this property a critical consideration for buyers.
4. Power Output and Laser Type
The power output, measured in watts, determines the cutting speed and the type of materials that can be processed. Common laser types include fiber, CO2, and solid-state lasers. Each type has its advantages depending on the application. For instance, fiber lasers are typically more efficient and better for metals, while CO2 lasers are preferred for non-metal materials. Buyers should match the power output and laser type with their production needs.
5. Control System and Software Compatibility
The control system governs the operation of the laser cutting machine. A user-friendly interface and compatibility with CAD/CAM software are essential for efficient operation. This impacts the ease of use and the learning curve for operators. Buyers should consider whether the system allows for seamless integration with existing production workflows.
What Trade Terminology Should B2B Buyers Know When Purchasing Laser Cutting Machines?
Understanding industry jargon is crucial for effective communication and negotiation in B2B transactions. Here are some common terms related to laser cutting machines:
1. OEM (Original Equipment Manufacturer)
An OEM is a company that produces parts or equipment that may be marketed by another manufacturer. When purchasing from China, buyers should know if they are dealing with an OEM or a reseller, as this impacts the quality assurance and warranty options.
2. MOQ (Minimum Order Quantity)
MOQ refers to the smallest quantity of goods that a supplier is willing to sell. This is particularly important for international buyers, as it can affect inventory costs and initial investment. Understanding MOQ can help in negotiating better terms and managing production schedules.
3. RFQ (Request for Quotation)
An RFQ is a document sent to suppliers to request pricing information for specific goods or services. For B2B buyers, submitting an RFQ can streamline the procurement process and ensure that they receive competitive pricing from multiple suppliers.
4. Incoterms (International Commercial Terms)
Incoterms are a set of international rules that define the responsibilities of buyers and sellers in international trade. Familiarity with these terms helps buyers understand shipping costs, insurance, and liability, which are critical for budgeting and logistics planning.
5. Lead Time
Lead time is the amount of time it takes from placing an order to receiving the goods. Understanding lead times is essential for planning production schedules and meeting customer demands. Long lead times can affect a buyer’s ability to respond to market changes quickly.
By grasping these technical properties and trade terms, B2B buyers can navigate the complexities of purchasing laser metal cutting machines from China, ultimately leading to more successful procurement and operational strategies.
Navigating Market Dynamics and Sourcing Trends in the laser metal cutting machine china Sector
What Are the Current Market Dynamics for Laser Metal Cutting Machines from China?
The laser metal cutting machine sector is experiencing rapid growth, driven by advancements in technology and increasing demand across various industries such as automotive, aerospace, and manufacturing. International B2B buyers, particularly from Africa, South America, the Middle East, and Europe, are increasingly sourcing from China due to its competitive pricing and technological innovations. The integration of Industry 4.0 concepts, such as automation and artificial intelligence, is reshaping the market, enabling enhanced precision and efficiency in manufacturing processes.
Emerging trends include the adoption of fiber laser technology, which offers superior cutting speeds and operational efficiency compared to traditional CO2 lasers. Furthermore, the rise of smart factories is prompting manufacturers to invest in high-performance laser cutting machines that can integrate seamlessly with existing production lines. As international buyers navigate these dynamics, understanding the specific needs of their industries will be crucial in selecting the right equipment.
Additionally, geopolitical factors and trade agreements are influencing sourcing strategies. For instance, buyers from Europe may benefit from favorable tariffs under certain trade agreements with China, while those in Africa and South America might explore partnerships that foster technology transfer. Staying informed about these market conditions can empower buyers to make strategic decisions that align with their operational goals.
How Is Sustainability Influencing the Sourcing of Laser Metal Cutting Machines?
Sustainability is becoming a pivotal factor in the sourcing of laser metal cutting machines. As global awareness of environmental issues increases, international buyers are under pressure to adopt practices that minimize ecological impact. This is especially relevant for industries in Europe, where regulatory frameworks are more stringent regarding emissions and waste management.
Buyers should prioritize suppliers who demonstrate a commitment to sustainability through certifications such as ISO 14001, which indicates effective environmental management systems. Additionally, sourcing machines that utilize ‘green’ materials and technologies can significantly reduce the carbon footprint of manufacturing processes. For example, fiber lasers are known for their energy efficiency, consuming less power than traditional laser cutting technologies, thereby aligning with sustainable practices.
Ethical sourcing is also gaining traction, with companies expected to maintain transparency in their supply chains. This includes ensuring that raw materials are sourced responsibly and that manufacturing processes adhere to ethical labor standards. By aligning with suppliers that prioritize sustainability and ethical practices, B2B buyers can enhance their brand reputation and meet the growing consumer demand for environmentally friendly products.
What Is the Evolution of Laser Metal Cutting Technology?
The evolution of laser metal cutting technology dates back to the late 1960s when the first laser was used for cutting applications. Over the decades, advancements in laser technology, including the development of high-powered CO2 and fiber lasers, have significantly improved cutting capabilities and efficiency. The introduction of computer numerical control (CNC) systems in the 1980s revolutionized the industry, allowing for precise and automated cutting processes.
In recent years, the focus has shifted towards incorporating smart technologies and automation, marking a new era in laser cutting. Today’s machines are equipped with advanced software that enables real-time monitoring and predictive maintenance, ensuring optimal performance and reducing downtime. This evolution not only enhances productivity but also caters to the increasing demand for customization in manufacturing processes.
As international buyers continue to explore sourcing options, understanding the historical context of laser technology can provide valuable insights into the capabilities and innovations available in the market today. This knowledge empowers them to make informed decisions that align with their operational needs and future growth objectives.
Frequently Asked Questions (FAQs) for B2B Buyers of laser metal cutting machine china
-
How do I choose the right laser metal cutting machine for my business needs?
Selecting the right laser metal cutting machine involves assessing your specific production requirements, such as the types of materials you will be cutting (e.g., steel, aluminum), the thickness of those materials, and the desired cutting speed. Consider the machine’s power, precision, and available features like automation options. Additionally, review supplier specifications and customer testimonials to ensure the machine meets your quality and performance standards. Engaging with suppliers for demonstrations or detailed consultations can also provide valuable insights tailored to your business. -
What are the key specifications to look for in a laser metal cutting machine from China?
When evaluating a laser metal cutting machine, focus on specifications such as laser power (measured in watts), cutting speed, and accuracy. Other important factors include the size of the cutting bed, compatibility with various materials, and the type of laser technology used (e.g., fiber or CO2). Additionally, check for the availability of software for design and operation, ease of maintenance, and the machine’s energy efficiency. These specifications will significantly influence your production capabilities and overall operational costs. -
What customization options are available when sourcing laser metal cutting machines from China?
Many Chinese manufacturers offer customization options to meet specific operational needs. Buyers can request modifications related to machine size, cutting head types, and additional features like automated loading systems or advanced cooling mechanisms. It’s also possible to customize software to integrate with existing production systems. When discussing customization, ensure clear communication about your requirements and obtain detailed quotations to assess the impact on pricing and delivery timelines. -
What is the minimum order quantity (MOQ) for laser metal cutting machines from Chinese suppliers?
The MOQ for laser metal cutting machines can vary widely among suppliers, typically ranging from one unit for smaller manufacturers to several units for larger firms. When negotiating with suppliers, clarify your intended purchase volume and inquire about any flexibility in their MOQ. Some manufacturers may offer lower MOQs for first-time buyers or during promotional periods, so it’s beneficial to express your long-term purchasing intentions to foster a better relationship. -
What payment terms should I expect when purchasing a laser metal cutting machine from China?
Payment terms can differ between suppliers, but common practices include a 30% deposit upon order confirmation and the remaining 70% before shipment. Some suppliers might offer letters of credit or payment through secure platforms like Alibaba. It’s crucial to discuss and agree upon payment terms upfront to avoid misunderstandings. Additionally, consider the currency exchange rates and any potential transaction fees if paying in a foreign currency. -
How can I ensure quality assurance when sourcing laser cutting machines from China?
To ensure quality, request detailed product specifications and certifications (like ISO) from potential suppliers. Visiting the manufacturing facility, if possible, allows you to inspect the production process and quality control measures firsthand. Additionally, consider third-party inspection services to evaluate the machine before shipment. Establishing clear quality expectations and using contracts that include quality clauses can also help safeguard your investment. -
What logistics considerations should I keep in mind when importing laser metal cutting machines from China?
Logistics play a critical role in the importing process. Consider the shipping method (air freight for speed, sea freight for cost-effectiveness), customs duties, and local regulations in your country regarding machinery imports. Collaborate with freight forwarders experienced in international B2B shipping to streamline the process. Be aware of potential delays and plan for contingencies, especially if sourcing large or heavy machinery that may require special handling. -
How can I establish a reliable supplier relationship for long-term sourcing of laser cutting machines?
Building a reliable supplier relationship involves consistent communication, transparency about your business needs, and regular performance evaluations. Start with smaller orders to assess quality and service before scaling up. Engaging in regular feedback sessions can help align expectations and foster collaboration. Additionally, consider signing long-term contracts that benefit both parties, which can lead to better pricing, priority service, and improved product support in the future.
Important Disclaimer & Terms of Use
⚠️ Important Disclaimer
The information provided in this guide, including content regarding manufacturers, technical specifications, and market analysis, is for informational and educational purposes only. It does not constitute professional procurement advice, financial advice, or legal advice.
While we have made every effort to ensure the accuracy and timeliness of the information, we are not responsible for any errors, omissions, or outdated information. Market conditions, company details, and technical standards are subject to change.
B2B buyers must conduct their own independent and thorough due diligence before making any purchasing decisions. This includes contacting suppliers directly, verifying certifications, requesting samples, and seeking professional consultation. The risk of relying on any information in this guide is borne solely by the reader.
Strategic Sourcing Conclusion and Outlook for laser metal cutting machine china
In the competitive landscape of laser metal cutting machines, international B2B buyers must prioritize strategic sourcing to maximize value and efficiency. By understanding the unique offerings from Chinese manufacturers, businesses from Africa, South America, the Middle East, and Europe can leverage cost advantages while ensuring quality and technological innovation.
How Can Strategic Sourcing Enhance Your Purchasing Decisions?
Strategic sourcing empowers buyers to not only evaluate the financial implications of their purchases but also to assess supplier reliability, after-sales support, and long-term partnership potential. Engaging with reputable Chinese suppliers can lead to improved production capabilities, faster turnaround times, and access to cutting-edge technology that can significantly enhance operational efficiency.
What Lies Ahead for Buyers in the Laser Metal Cutting Industry?
Looking forward, the demand for laser metal cutting machines is expected to rise, driven by advancements in automation and material processing. Buyers should remain proactive in exploring partnerships that offer not just machinery, but also comprehensive support services and training to maximize their investment.
By aligning purchasing strategies with reliable suppliers, international B2B buyers can position themselves to thrive in an evolving market landscape. Take the next step in your sourcing journey by evaluating your options and establishing connections with trusted manufacturers in China today.