Discover Top Welding Machine Manufacturers: Save Costs Today (2025)
Introduction: Navigating the Global Market for Welding Machine Manufacturers
In the competitive landscape of industrial manufacturing, sourcing welding machines can pose significant challenges for international B2B buyers. Whether you’re based in Africa, South America, the Middle East, or Europe, the quest for reliable and efficient welding equipment requires a thorough understanding of various types, applications, and supplier capabilities. This guide serves as a comprehensive resource for navigating the global market for welding machine manufacturers, addressing the complexities of the procurement process.
We delve into the diverse types of welding processes, including MIG, TIG, and plasma arc welding, to help you identify the best fit for your specific applications. Additionally, we cover critical considerations such as supplier vetting, quality assurance, and cost factors, empowering you to make informed purchasing decisions. Understanding these elements is essential for optimizing your operations and ensuring that your welding projects meet the highest standards of quality and efficiency.
This guide is tailored to assist international B2B buyers by providing actionable insights and practical strategies. By focusing on the unique needs of markets in regions like Egypt and Italy, we aim to bridge the gap between manufacturers and buyers, facilitating successful partnerships that drive innovation and growth in the welding industry.
Understanding Welding Machine Manufacturers Types and Variations
Type Name | Key Distinguishing Features | Primary B2B Applications | Brief Pros & Cons for Buyers |
---|---|---|---|
MIG Welding Machines | Uses a continuously fed wire as an electrode, ideal for thin materials. | Automotive manufacturing, light fabrication. | Pros: Fast and efficient; easy to learn. Cons: Limited to thinner materials; requires external gas. |
TIG Welding Machines | Utilizes a non-consumable tungsten electrode; offers high precision. | Aerospace, medical devices, high-end fabrication. | Pros: High-quality welds; versatile with various metals. Cons: Slower process; requires skilled operators. |
Stick Welding Machines | Employs a consumable electrode coated in flux; versatile and portable. | Construction, repair work, and maintenance. | Pros: Great for outdoor work; minimal equipment required. Cons: Produces slag; not suitable for thin materials. |
Flux-Cored Arc Welding Machines | Similar to MIG but uses a tubular wire filled with flux; effective without external gas. | Heavy equipment repair, shipbuilding. | Pros: High deposition rates; effective in windy conditions. Cons: More expensive wire; requires cleanup of slag. |
Plasma Arc Welding Machines | Generates a high-energy arc for precision welding; can cut materials as well. | Aerospace, automotive, and high-tech industries. | Pros: Very precise; suitable for thick materials. Cons: Higher initial investment; requires skilled operators. |
What Are the Characteristics of MIG Welding Machines?
MIG welding machines, also known as Gas Metal Arc Welding (GMAW) machines, are characterized by their use of a continuously fed wire electrode. This method is particularly suitable for joining thin materials, making it a popular choice in automotive manufacturing and light fabrication. When purchasing MIG welding equipment, B2B buyers should consider the machine’s duty cycle, ease of use, and compatibility with various gas types, as these factors influence operational efficiency and cost-effectiveness.
Why Choose TIG Welding Machines for Precision Work?
TIG welding machines, or Gas Tungsten Arc Welding (GTAW) machines, are distinguished by their use of a non-consumable tungsten electrode, allowing for high precision and control. This makes them ideal for applications in aerospace and medical device manufacturing, where weld integrity is paramount. Buyers should evaluate the machine’s power settings, portability, and the availability of compatible filler materials to ensure it meets their specific welding requirements.
How Do Stick Welding Machines Offer Versatility?
Stick welding machines, or Shielded Metal Arc Welding (SMAW) machines, are favored for their versatility and portability. They use a consumable electrode coated in flux, making them suitable for outdoor applications and on-site repairs. When selecting a stick welding machine, B2B buyers should consider the electrode size compatibility, ease of maintenance, and the machine’s performance in various environmental conditions, as these factors can significantly impact productivity.
What Makes Flux-Cored Arc Welding Machines Effective?
Flux-cored arc welding machines are similar to MIG machines but utilize a tubular wire filled with flux, allowing for effective welding without the need for external shielding gas. This feature makes them particularly advantageous for heavy equipment repair and shipbuilding, especially in windy conditions. Buyers should assess the machine’s wire feed speed, voltage control, and the cost of consumables, as these will affect the overall operational costs and efficiency.
Why Opt for Plasma Arc Welding Machines in High-Tech Industries?
Plasma arc welding machines are recognized for their ability to generate a high-energy arc, making them suitable for precision welding and cutting. They are commonly used in aerospace and automotive sectors where high-quality welds are essential. When considering a plasma welding machine, B2B buyers should focus on the machine’s power output, cooling system, and the required skill level for operation, as these factors will influence both the quality of the welds and the cost of training operators.
Related Video: 4 Types of Welding Explained: MIG vs TIG vs Stick vs Flux Core
Key Industrial Applications of Welding Machine Manufacturers
Industry/Sector | Specific Application of Welding Machine Manufacturers | Value/Benefit for the Business | Key Sourcing Considerations for this Application |
---|---|---|---|
Automotive Manufacturing | Assembly of vehicle frames and components using MIG and TIG welding processes | Increased production efficiency and durability of vehicles | Supplier reliability, technology compatibility, and after-sales support |
Construction and Infrastructure | Joining structural steel beams and reinforcement bars via Shielded Metal Arc Welding (SMAW) | Enhanced structural integrity and safety in buildings | Compliance with local regulations, material specifications, and warranty terms |
Oil and Gas | Pipeline construction and maintenance with Flux Cored Arc Welding (FCAW) | Reduced downtime and operational costs | Availability of specialized equipment, skilled labor, and safety certifications |
Shipbuilding | Fabrication of hulls and decks using Plasma Arc Welding | Improved weld quality and reduced labor costs | Precision in equipment specifications, training for operators, and service agreements |
Aerospace | Assembly of aircraft components using Electron Beam Welding | Lightweight structures with high strength-to-weight ratios | Advanced technology requirements, certification standards, and long-term support |
How is Welding Applied in Automotive Manufacturing?
In the automotive sector, welding machine manufacturers provide essential equipment for assembling vehicle frames and components. Processes like MIG and TIG welding are favored for their speed and strength, ensuring that vehicles can withstand rigorous use. B2B buyers in this industry must consider the compatibility of welding machines with existing manufacturing lines, the reliability of suppliers, and the availability of spare parts and technical support to minimize production downtime.
What are the Welding Applications in Construction and Infrastructure?
Welding plays a critical role in the construction and infrastructure sector, particularly in the joining of structural steel beams and reinforcement bars. Shielded Metal Arc Welding (SMAW) is commonly used due to its versatility and effectiveness in various positions. Buyers should focus on sourcing machines that comply with local building codes and safety regulations, as well as those that offer robust warranty terms and after-sales service, ensuring that their projects maintain structural integrity and safety.
How is Welding Used in Oil and Gas Industries?
In the oil and gas industry, welding machines are crucial for pipeline construction and maintenance. Flux Cored Arc Welding (FCAW) is often employed due to its efficiency in high-demand environments. International B2B buyers must prioritize suppliers that can provide specialized equipment, ensure skilled labor is available for operation, and maintain safety certifications to comply with industry standards, thereby reducing potential operational costs and downtime.
What are the Key Applications of Welding in Shipbuilding?
Shipbuilding heavily relies on welding technologies, particularly Plasma Arc Welding, for fabricating hulls and decks. This method enhances weld quality and reduces labor costs, making it ideal for large-scale ship construction. Buyers in this sector should evaluate the precision of equipment specifications and the training provided for operators, as well as ensure service agreements are in place to support ongoing maintenance and operational efficiency.
How is Welding Applied in Aerospace Manufacturing?
In the aerospace industry, welding is essential for assembling aircraft components, where Electron Beam Welding is often utilized due to its ability to create lightweight yet strong structures. This is vital for enhancing fuel efficiency and performance. B2B buyers must be aware of the advanced technology requirements and stringent certification standards that govern this sector, ensuring that their welding equipment meets these demands while also securing long-term support from manufacturers to maintain operational standards.
Related Video: What is MIG Welding? (GMAW)
3 Common User Pain Points for ‘Welding Machine Manufacturers’ & Their Solutions
Scenario 1: Navigating High Equipment Costs in Welding
The Problem:
International B2B buyers, particularly in emerging markets like Africa and South America, often face the challenge of high upfront costs associated with purchasing welding machines. These machines are essential for various industries, from construction to automotive. However, the initial investment can be prohibitive, especially when businesses are also managing tight budgets and fluctuating currency exchange rates. This can lead to hesitation in acquiring the necessary equipment, ultimately hindering productivity and growth.
The Solution:
To mitigate these costs, buyers should consider sourcing welding machines from manufacturers that offer flexible financing options, such as leasing or installment payments. Additionally, engaging with manufacturers that have a local presence can help in reducing shipping and import costs. It’s also beneficial to research and negotiate bulk purchase agreements, which can provide significant discounts. Furthermore, investing in used or refurbished equipment can yield substantial savings while still meeting operational needs. Buyers should also assess the total cost of ownership, including maintenance, energy consumption, and productivity gains, to make informed decisions.
Scenario 2: Difficulty in Understanding Welding Machine Specifications
The Problem:
B2B buyers often struggle to decipher the technical specifications of welding machines. With various types of welding processes like MIG, TIG, and Stick welding, understanding which machine is appropriate for specific applications can be overwhelming. This lack of clarity can lead to purchasing equipment that does not meet the operational requirements, resulting in inefficiencies and wasted investment.
The Solution:
To tackle this issue, buyers should prioritize engaging with knowledgeable welding machine manufacturers who provide comprehensive technical support and consultation services. Before making a purchase, it’s advisable to clearly define the specific welding applications, materials, and production volumes required. Participating in webinars or training sessions offered by manufacturers can also enhance understanding of different welding processes and machine capabilities. Additionally, requesting detailed product comparisons and case studies from manufacturers can help buyers make more informed decisions that align with their operational needs.
Scenario 3: Ensuring Consistent After-Sales Support and Training
The Problem:
Once a welding machine is acquired, B2B buyers often find themselves facing challenges related to after-sales support and training. In regions like the Middle East and parts of Europe, where technical expertise may vary, inadequate training can lead to improper machine usage, increased downtime, and safety hazards. This can significantly impact productivity and project timelines, creating frustration for both buyers and their teams.
The Solution:
Buyers should seek out welding machine manufacturers that emphasize robust after-sales support and offer comprehensive training programs. It’s crucial to verify that the manufacturer provides on-site training sessions for operators and maintenance personnel, tailored to the specific machines purchased. Establishing a long-term relationship with the supplier can also ensure ongoing support and access to updated training resources as technology evolves. Buyers should also consider manufacturers who offer remote support options, such as virtual troubleshooting and maintenance assistance, to resolve issues quickly and minimize downtime. By prioritizing manufacturers with strong service commitments, buyers can enhance operational efficiency and ensure a safer working environment.
Strategic Material Selection Guide for Welding Machine Manufacturers
When selecting materials for welding machines, manufacturers must consider various factors that impact performance, durability, and cost-effectiveness. Below, we analyze four common materials used in welding machine manufacturing, focusing on their properties, advantages, disadvantages, and implications for international buyers.
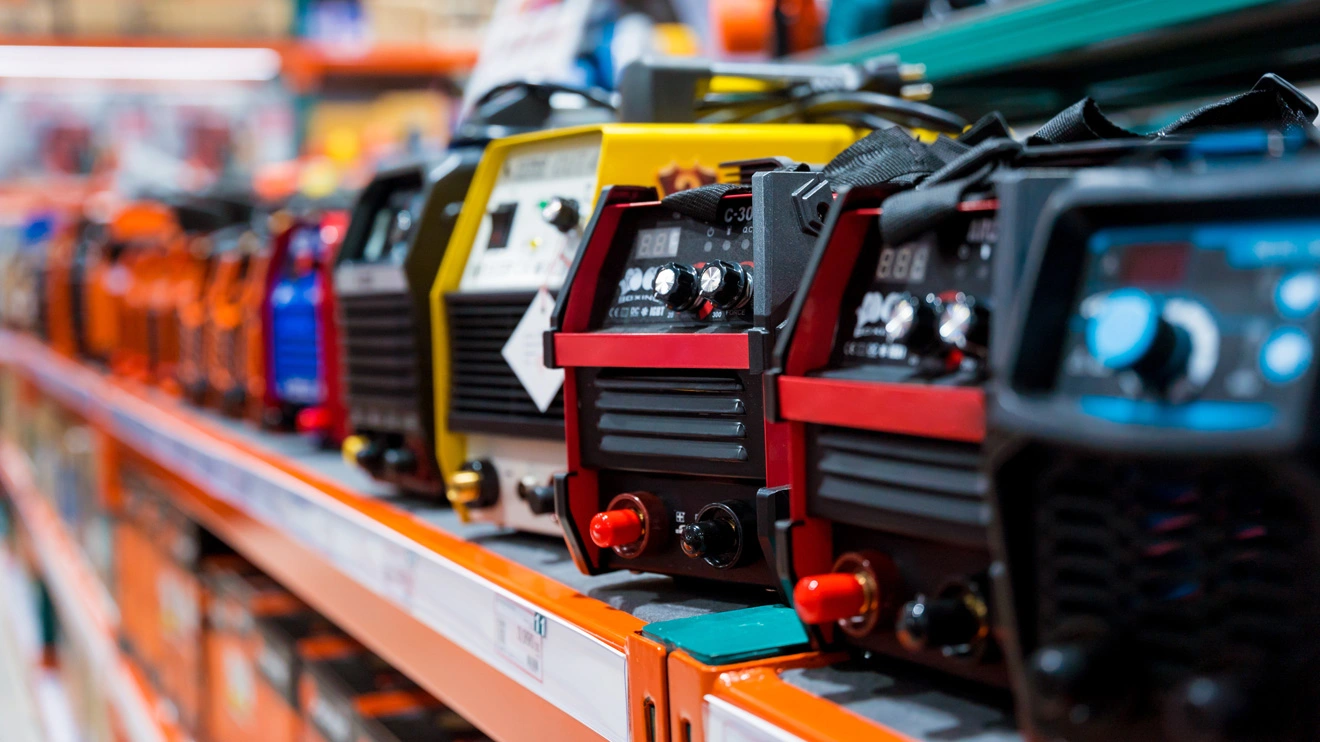
A stock image related to Welding Machine Manufacturers.
What Are the Key Properties of Steel in Welding Machines?
Steel is one of the most widely used materials in welding machines due to its excellent mechanical properties. It typically boasts high tensile strength, good ductility, and resistance to deformation under load. Steel can withstand high temperatures, making it suitable for various welding applications. However, its susceptibility to corrosion can be a concern, particularly in humid environments.
Pros & Cons:
– Pros: Durable, cost-effective, and widely available. Steel components can be easily machined and welded.
– Cons: Prone to rust if not properly coated or treated, which may lead to increased maintenance costs.
Impact on Application:
Steel’s strength and heat resistance make it ideal for heavy-duty welding applications. However, its corrosion susceptibility necessitates protective coatings, especially in regions with high humidity, such as parts of Africa and South America.
Considerations for International Buyers:
Buyers from regions like Egypt and Italy should ensure compliance with local standards (e.g., ASTM A36) and consider the availability of corrosion-resistant coatings.
How Does Aluminum Compare as a Material for Welding Machines?
Aluminum is increasingly popular in welding machine manufacturing due to its lightweight nature and excellent corrosion resistance. It has a lower melting point than steel, which can be advantageous for specific welding processes. However, aluminum’s lower tensile strength compared to steel can limit its use in high-load applications.
Pros & Cons:
– Pros: Lightweight, excellent corrosion resistance, and good thermal conductivity.
– Cons: Higher cost than steel and lower strength, which may not be suitable for all applications.
Impact on Application:
Aluminum is particularly useful in applications where weight is a critical factor, such as in portable welding machines. Its corrosion resistance makes it suitable for marine and outdoor applications.
Considerations for International Buyers:
Buyers should look for compliance with standards such as ASTM B221 for aluminum products. In Europe, EN standards may apply, influencing material selection based on regional preferences.
What Are the Benefits of Using Copper in Welding Equipment?
Copper is known for its exceptional electrical conductivity, making it an ideal choice for components that require efficient heat transfer, such as welding electrodes and cables. It is also resistant to corrosion, especially in marine environments.
Pros & Cons:
– Pros: High electrical conductivity, excellent thermal properties, and good corrosion resistance.
– Cons: Higher cost and weight compared to aluminum and steel, which can affect overall machine portability.
Impact on Application:
Copper’s properties make it essential for high-performance welding machines that require efficient heat management. However, its weight can be a drawback in portable applications.
Considerations for International Buyers:
Compliance with industry standards like ASTM B170 is vital. Buyers in the Middle East, where high temperatures can affect performance, should prioritize copper’s thermal properties.
How Does Plastic Reinforce Welding Machine Components?
Plastics, particularly engineering-grade polymers, are increasingly used in welding machines for non-structural components. They offer excellent insulation properties and are resistant to corrosion and chemicals.
Pros & Cons:
– Pros: Lightweight, corrosion-resistant, and cost-effective for non-load-bearing applications.
– Cons: Limited heat resistance and structural integrity compared to metals.
Impact on Application:
Plastics are ideal for housing and insulation components in welding machines, reducing overall weight and improving portability.
Considerations for International Buyers:
Buyers should ensure that the selected plastic materials comply with relevant standards, such as ASTM D638 for tensile properties.
Summary Table of Material Selection for Welding Machine Manufacturers
Material | Typical Use Case for Welding Machine Manufacturers | Key Advantage | Key Disadvantage/Limitation | Relative Cost (Low/Med/High) |
---|---|---|---|---|
Steel | Structural components and frames | Durable and cost-effective | Prone to corrosion without treatment | Medium |
Aluminum | Lightweight portable welding machines | Excellent corrosion resistance | Higher cost and lower strength | High |
Copper | Electrodes and heat transfer components | High electrical and thermal conductivity | Expensive and heavy | High |
Plastic | Insulation and non-structural components | Lightweight and corrosion-resistant | Limited heat resistance | Low |
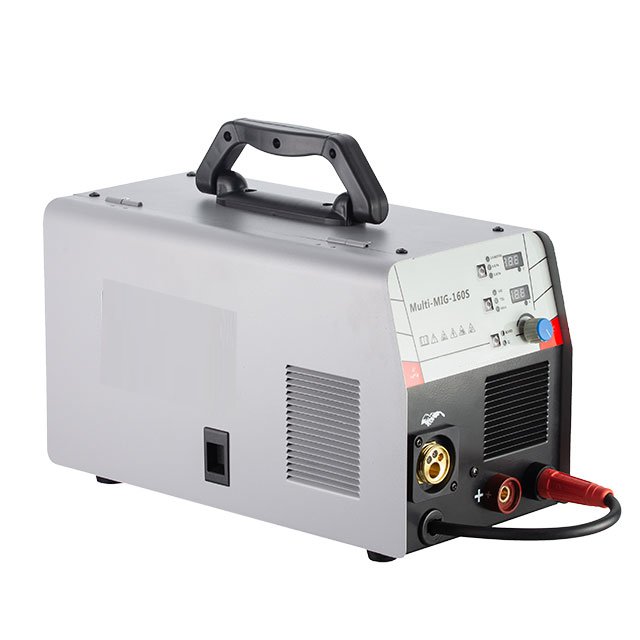
A stock image related to Welding Machine Manufacturers.
This guide provides a comprehensive overview of material selection for welding machine manufacturers, emphasizing the importance of understanding material properties and regional considerations for international buyers.
In-depth Look: Manufacturing Processes and Quality Assurance for Welding Machine Manufacturers
What Are the Main Stages in the Manufacturing Process of Welding Machines?
The manufacturing process for welding machines consists of several critical stages: material preparation, forming, assembly, and finishing. Each stage is crucial for ensuring the quality and reliability of the final product.
Material Preparation
The first step involves sourcing high-quality raw materials. Common materials used in welding machines include steel, aluminum, and various alloys. The preparation phase also includes cutting, machining, and treating these materials to meet specific mechanical and thermal properties. This stage is vital, as the integrity of the materials directly impacts the performance and durability of the welding machine.
What Techniques Are Used for Forming Welding Machines?
Forming processes can include stamping, bending, and welding of subcomponents. In this phase, manufacturers often employ techniques such as CNC machining for precise component fabrication. The use of automated processes enhances efficiency and accuracy, minimizing human error. Advanced forming techniques, including hydroforming and laser cutting, can also be utilized to create complex geometries required in modern welding machines.
How Is the Assembly of Welding Machines Conducted?
The assembly stage involves putting together the various components, including the power supply, control systems, and welding torches. Manufacturers often utilize modular designs, allowing for easier assembly and maintenance. This stage may involve both manual and automated assembly techniques, ensuring that each component is correctly integrated. Quality checks are frequently performed at this stage to catch any potential issues before moving on to the finishing phase.
What Finishing Processes Are Essential for Welding Machines?
Finishing processes are crucial for ensuring that the welding machines are not only functional but also aesthetically pleasing and resistant to environmental factors. Common finishing techniques include painting, powder coating, and surface treatment to prevent corrosion. These processes enhance the machine’s longevity and usability in different environments, which is particularly important for international buyers operating in diverse climatic conditions.
How Is Quality Assurance Implemented in Welding Machine Manufacturing?
Quality assurance (QA) is a fundamental aspect of the manufacturing process, ensuring that welding machines meet international standards and customer specifications.
What International Standards Should B2B Buyers Be Aware Of?
International standards such as ISO 9001 are vital for establishing a quality management system (QMS) within manufacturing organizations. ISO 9001 focuses on meeting customer requirements and ensuring continuous improvement. Additionally, industry-specific certifications like CE (Conformité Européenne) for European markets and API (American Petroleum Institute) standards for oil and gas applications are critical. These certifications assure buyers of compliance with safety, health, and environmental regulations.
What Are the Key Quality Control Checkpoints During Manufacturing?
Quality control (QC) checkpoints are essential throughout the manufacturing process. Common checkpoints include:
- Incoming Quality Control (IQC): This involves inspecting raw materials and components upon arrival to ensure they meet specified standards.
- In-Process Quality Control (IPQC): This occurs during the manufacturing process, where various parameters are monitored to detect any deviations from quality standards.
- Final Quality Control (FQC): Conducted after assembly, FQC involves comprehensive testing of the finished product to ensure it functions correctly and meets all specifications.
What Common Testing Methods Are Used to Ensure Quality?
Testing methods for welding machines can vary based on the type and application of the machine. Common testing methods include:
- Functional Testing: Verifying that the machine operates as intended under various conditions.
- Electrical Testing: Ensuring that electrical components meet safety and performance standards.
- Durability Testing: Assessing the machine’s ability to withstand prolonged use and environmental conditions.
How Can B2B Buyers Verify Supplier Quality Control?
B2B buyers should conduct thorough due diligence when selecting a welding machine manufacturer. This can include:
- Audits: Performing on-site audits of the manufacturing facility to assess their quality control processes.
- Reports: Requesting quality control reports and certifications to verify compliance with international standards.
- Third-Party Inspections: Engaging third-party inspection agencies to conduct independent assessments of the manufacturing processes and final products.
What Are the Quality Control Nuances for International B2B Buyers?
International buyers, particularly from regions such as Africa, South America, the Middle East, and Europe, should be aware of specific nuances in quality control. Different markets may have varying standards and regulatory requirements. For instance, buyers in Europe must ensure compliance with CE marking, while those in the Middle East may need to consider local standards like GSO (Gulf Standards Organization). Understanding these requirements is essential for avoiding potential compliance issues and ensuring the seamless importation of welding machines.
Conclusion
In summary, the manufacturing processes and quality assurance practices for welding machines are intricate and multifaceted. By understanding the main stages of manufacturing and the critical role of quality assurance, international B2B buyers can make informed decisions when sourcing welding machines. Emphasizing compliance with international standards and conducting thorough supplier evaluations can significantly mitigate risks and enhance the procurement experience.
Practical Sourcing Guide: A Step-by-Step Checklist for ‘Welding Machine Manufacturers’
In the competitive landscape of welding machine procurement, it is essential for B2B buyers to have a structured approach to sourcing reliable manufacturers. This guide provides a practical checklist that will help you navigate the complexities of selecting the right welding machine manufacturer for your needs. By following these steps, you can ensure a successful procurement process that meets your technical and operational requirements.
Step 1: Define Your Technical Specifications
Before initiating the sourcing process, clearly outline your technical requirements. This includes the type of welding processes you will utilize (e.g., MIG, TIG, or Stick welding) and the materials you will work with.
– Considerations:
– What is the maximum thickness of the materials?
– Are there specific features or technologies you need, such as inverter technology or multi-process capabilities?
Step 2: Research Potential Suppliers
Conduct thorough research to identify potential welding machine manufacturers. Use online directories, industry trade shows, and referrals from industry peers to compile a list of candidates.
– Key Resources:
– Industry-specific websites and forums
– Trade associations and their member directories
– Reviews and testimonials from previous clients
Step 3: Evaluate Supplier Certifications
Verify that potential suppliers possess the necessary certifications and compliance with international standards. This is crucial for ensuring product quality and safety.
– Look for:
– ISO 9001 certification for quality management
– CE marking for compliance with European standards
– Any relevant industry-specific certifications
Step 4: Request Detailed Quotations
Once you have shortlisted suppliers, request detailed quotations that include pricing, delivery times, and terms of service. A comprehensive quote allows for better comparison among suppliers.
– Focus on:
– Breakdown of costs (equipment, shipping, installation)
– Payment terms and warranties offered
– Lead times for production and delivery
Step 5: Assess After-Sales Support and Service
Evaluate the after-sales support provided by the manufacturers. Reliable after-sales service is essential for minimizing downtime and ensuring long-term performance.
– Inquire about:
– Availability of spare parts and service technicians
– Training programs for your operators
– Support for troubleshooting and maintenance
Step 6: Conduct Factory Visits (if possible)
If feasible, arrange factory visits to assess the manufacturing processes and quality control measures in place. This step can provide invaluable insights into the supplier’s capabilities.
– What to observe:
– Production efficiency and equipment used
– Quality assurance processes
– Safety standards and worker conditions
Step 7: Review Contracts Thoroughly
Before finalizing any agreements, ensure you review the contracts carefully. Pay attention to terms regarding delivery, warranty, and liability.
– Key points to check:
– Clauses for breach of contract and dispute resolution
– Conditions for warranty claims and returns
– Flexibility in case of changes in order quantity or specifications
By following these steps, B2B buyers from Africa, South America, the Middle East, and Europe can make informed decisions when sourcing welding machine manufacturers, ensuring that they choose a partner who meets their operational needs and standards.
Comprehensive Cost and Pricing Analysis for Welding Machine Manufacturers Sourcing
What Are the Key Cost Components in Welding Machine Manufacturing?
When sourcing welding machines, understanding the cost structure is essential for making informed purchasing decisions. The primary cost components that manufacturers face include:
-
Materials: The cost of raw materials such as steel, aluminum, and electrical components can vary significantly based on market conditions and sourcing strategies. High-quality materials often come at a premium but can enhance the machine’s performance and longevity.
-
Labor: Skilled labor is crucial in the manufacturing process. Labor costs can differ based on the region, expertise required, and the complexity of the machine being produced. In regions with a high demand for skilled welders, labor costs may be higher, impacting the overall pricing.
-
Manufacturing Overhead: This includes indirect costs associated with production, such as utilities, rent, and equipment maintenance. Efficient manufacturing processes can help minimize these overhead costs, allowing for more competitive pricing.
-
Tooling: The initial setup of tools and molds for production can be a significant upfront investment. Custom tooling for specialized welding machines can further increase costs, but it may also enhance product precision and quality.
-
Quality Control (QC): Ensuring that machines meet industry standards and certifications incurs additional costs. Comprehensive QC processes are critical to avoid costly recalls or warranty claims later.
-
Logistics: Shipping and handling costs can vary based on the destination and the mode of transport. International buyers should consider these costs in their total procurement budget.
-
Margin: Manufacturers typically add a profit margin on top of production costs. This margin can vary based on market competition, demand, and the perceived value of the machine.
How Do Price Influencers Affect Welding Machine Costs?
Several factors influence the pricing of welding machines, which international buyers should consider:
-
Volume and Minimum Order Quantity (MOQ): Larger orders may qualify for bulk discounts, significantly reducing the per-unit cost. Understanding the MOQ policies of suppliers can help buyers plan their purchases effectively.
-
Specifications and Customization: Custom-built machines with specific features or capabilities usually come at a higher price. Buyers should evaluate whether standard models can meet their needs to optimize costs.
-
Materials and Quality Certifications: Machines made from higher-grade materials or those that meet stringent quality certifications often cost more. Buyers should weigh the long-term benefits of investing in quality against initial costs.
-
Supplier Factors: The reputation and reliability of the supplier can affect pricing. Established manufacturers may charge more due to their proven track record, but they often provide better warranties and support.
-
Incoterms: The chosen Incoterms (International Commercial Terms) influence the total cost, including shipping responsibilities and risk transfer. Buyers should negotiate favorable terms to minimize unexpected costs.
What Are Effective Buyer Tips for Sourcing Welding Machines?
International buyers, especially those from Africa, South America, the Middle East, and Europe, should employ several strategies to enhance cost-efficiency:
-
Negotiate Pricing: Engage suppliers in discussions to negotiate prices, especially for larger orders. Highlighting potential long-term relationships can lead to better terms.
-
Consider Total Cost of Ownership (TCO): Evaluate not just the purchase price but also the operational costs, maintenance, and potential downtime associated with the machine. This holistic view can lead to smarter purchasing decisions.
-
Be Aware of Pricing Nuances: Understand the regional market dynamics affecting pricing. For instance, tariffs, import duties, and currency fluctuations can impact the final cost of machines sourced from abroad.
- Research Suppliers Thoroughly: Ensure that the suppliers have good reviews and a reputation for delivering quality machines. Verifying certifications and compliance with local standards can prevent future issues.
Disclaimer on Indicative Prices
Pricing for welding machines can fluctuate based on various factors, including market demand and supply chain conditions. Therefore, buyers should approach indicative prices with caution and conduct thorough market research to obtain accurate quotes before making purchasing decisions.
Alternatives Analysis: Comparing Welding Machine Manufacturers With Other Solutions
Understanding Alternatives to Welding Machine Manufacturers
In the landscape of industrial manufacturing, welding machines are pivotal for creating robust and durable metal structures. However, as global markets evolve, B2B buyers must consider various alternatives that can offer similar benefits while potentially addressing specific needs such as cost, maintenance, or application suitability. Below, we compare welding machine manufacturers with two viable alternatives: adhesive bonding and mechanical fastening.
Comparison Table of Welding Methods
Comparison Aspect | Welding Machine Manufacturers | Adhesive Bonding | Mechanical Fastening |
---|---|---|---|
Performance | High strength, permanent bonds | Good for non-structural applications; can be weaker than welds | Strong, removable joints; suitable for dynamic loads |
Cost | Higher initial investment | Generally lower cost | Moderate initial cost; cost-effective for large volumes |
Ease of Implementation | Requires skilled labor | Easier to apply; less training needed | Simple installation; tools are widely available |
Maintenance | Periodic maintenance required | Minimal maintenance needed | Low maintenance; easy to replace components |
Best Use Case | Heavy machinery, structural applications | Electronics, plastics, wood | Automotive, appliances, modular structures |
Detailed Breakdown of Alternatives
Adhesive Bonding: Is it a Viable Alternative to Welding Machines?
Adhesive bonding involves using chemical adhesives to join materials together. This method is particularly effective for joining dissimilar materials, such as metal to plastic or wood. The primary advantages of adhesive bonding include its ability to distribute stress across a wider area and its suitability for applications where traditional welding may not be feasible. However, the bond strength may not match that of welded joints, and curing times can delay production. Additionally, it may not be suitable for high-temperature applications.
Mechanical Fastening: When Should You Consider This Method?
Mechanical fastening utilizes screws, bolts, or rivets to create joints between materials. This method is often preferred for its simplicity and the ability to disassemble components easily for maintenance or repair. Mechanical fastening is cost-effective, especially for large production runs, as it requires minimal training and equipment. However, it may not provide the same level of structural integrity as welding, particularly in high-stress environments. Mechanical joints can also introduce potential points of failure if not properly installed.
Conclusion: How to Choose the Right Solution for Your Needs
When selecting between welding machine manufacturers and alternative methods such as adhesive bonding or mechanical fastening, B2B buyers should evaluate their specific application requirements, budget constraints, and the skill levels available within their workforce. For heavy-duty and structural applications, welding remains the gold standard, while adhesive bonding offers a unique solution for diverse materials and delicate assemblies. Mechanical fastening presents a versatile and cost-effective option, especially for modular designs. Ultimately, the right choice will depend on balancing performance, cost, and the long-term maintenance needs of the project.
Essential Technical Properties and Trade Terminology for Welding Machine Manufacturers
What Are the Key Technical Properties for Welding Machines?
When selecting a welding machine, international B2B buyers must understand several critical technical specifications that significantly impact performance and suitability for specific applications. Here are some essential properties to consider:
1. Material Grade
Material grade refers to the type of materials that a welding machine can effectively work with, including carbon steel, stainless steel, and aluminum. Different welding processes are suited for specific material grades, affecting strength and durability. Buyers should ensure that the chosen machine can accommodate the materials used in their projects to avoid costly errors.
2. Welding Capacity (Amperage)
The welding capacity, measured in amperes (A), indicates the machine’s ability to generate sufficient heat for different thicknesses of metal. For example, machines with higher amperage ratings are ideal for thicker materials, while lower amperage machines are suitable for thinner metals. Selecting the appropriate amperage is crucial to ensure proper fusion and joint integrity.
3. Duty Cycle
The duty cycle represents the percentage of time a welding machine can operate continuously within a specific period, typically 10 minutes. For instance, a 60% duty cycle means the machine can operate for six minutes and must cool for four minutes. Understanding duty cycle ratings helps buyers choose machines that can handle their workload without overheating, which is especially important in high-demand environments.
4. Voltage Input
Different welding machines require varying voltage inputs, ranging from 110V to 480V. Buyers must consider the electrical infrastructure available at their facilities when selecting a machine. Machines that operate on higher voltage inputs tend to be more powerful and can handle more demanding applications, but they may require specialized electrical setups.
5. Control Type
Welding machines may feature manual, semi-automatic, or fully automatic controls. The type of control impacts ease of use and precision in welding operations. For example, fully automatic machines can enhance productivity in large-scale operations by minimizing human error. Buyers should assess their workforce’s skill level and the complexity of their projects when determining the appropriate control type.
What Are Common Trade Terms Used in the Welding Industry?
Understanding industry jargon is essential for international B2B buyers to navigate negotiations and contracts effectively. Here are some common terms that may arise in discussions with welding machine manufacturers:
1. OEM (Original Equipment Manufacturer)
An OEM is a company that produces parts and equipment that may be marketed by another manufacturer. In the welding industry, buyers often seek machines from reputable OEMs to ensure quality and reliability. This term is critical for buyers looking for trusted suppliers and understanding the provenance of their equipment.
2. MOQ (Minimum Order Quantity)
MOQ refers to the smallest quantity of a product that a supplier is willing to sell. This term is particularly important for B2B buyers, as it can affect inventory costs and the ability to meet project timelines. Understanding MOQ helps buyers negotiate better terms and plan their procurement strategies effectively.
3. RFQ (Request for Quotation)
An RFQ is a formal document sent to suppliers requesting pricing and other relevant information for specific products or services. For welding machine buyers, issuing an RFQ is a crucial step in the procurement process, enabling them to compare offers and make informed purchasing decisions.
4. Incoterms (International Commercial Terms)
Incoterms are a set of predefined commercial terms used in international trade. They clarify the responsibilities of buyers and sellers regarding shipping, insurance, and tariffs. Familiarity with Incoterms helps welding machine buyers understand their obligations and reduce risks associated with global procurement.
5. WPS (Welding Procedure Specification)
A WPS is a formal document that provides direction for making a weld. It outlines the welding process, materials, and parameters necessary for consistent quality. Buyers should ensure that their welding machines comply with relevant WPS standards to maintain quality assurance in their projects.
Understanding these technical properties and trade terms will empower international B2B buyers to make informed decisions when sourcing welding machines, ultimately enhancing their operational efficiency and project success.
Navigating Market Dynamics and Sourcing Trends in the Welding Machine Manufacturers Sector
What Are the Key Market Trends Impacting the Welding Machine Manufacturers Sector?
The welding machine manufacturing sector is experiencing significant growth driven by several global factors. One primary driver is the increasing demand for advanced manufacturing techniques across industries such as construction, automotive, and aerospace. In regions like Africa and South America, infrastructural development is on the rise, creating a robust demand for welding machines. Additionally, the ongoing industrialization in the Middle East is propelling the need for high-quality welding equipment, particularly for energy and construction projects.
Emerging technologies such as automation and digitalization are reshaping the landscape of the welding industry. B2B buyers are increasingly seeking machines equipped with smart technology for improved efficiency and precision. For instance, the integration of IoT (Internet of Things) in welding machines allows for real-time monitoring and predictive maintenance, which can significantly reduce downtime. Moreover, the trend towards hybrid welding techniques, combining traditional methods with advanced processes, is gaining traction, particularly in Europe, where manufacturers are focused on enhancing productivity while minimizing costs.
Another notable trend is the shift towards localized sourcing strategies. International buyers from Africa and the Middle East are prioritizing suppliers who can provide quick delivery and support services, reducing lead times and enhancing operational efficiency. As such, understanding local market dynamics and establishing strong relationships with local manufacturers is crucial for B2B buyers in these regions.
How Are Sustainability and Ethical Sourcing Influencing B2B Purchasing Decisions?
Sustainability has emerged as a critical factor in the decision-making process for B2B buyers in the welding machine sector. With increasing awareness of environmental impacts, buyers are now prioritizing manufacturers that adopt eco-friendly practices and materials. This includes the use of recyclable components and energy-efficient machines, which not only help reduce the carbon footprint but also comply with international environmental regulations.
Ethical sourcing is equally important, as buyers are becoming more conscious of the supply chain’s social implications. They are keen on partnering with manufacturers who uphold fair labor practices and contribute to local economies. Certifications such as ISO 14001 (Environmental Management) and ISO 45001 (Occupational Health and Safety) are becoming essential criteria for evaluating potential suppliers. Buyers from Europe, for instance, are particularly stringent about these certifications, as they align with the EU’s commitment to sustainability.
Moreover, the adoption of “green” materials in manufacturing processes is gaining momentum. Welding machines that utilize low-emission gases and environmentally friendly filler materials are now in high demand. By investing in sustainable and ethically sourced products, B2B buyers not only enhance their corporate social responsibility profile but also attract environmentally conscious clients.
How Has the Welding Machine Manufacturing Sector Evolved Over Time?
The welding machine manufacturing sector has undergone substantial evolution since its inception in the early 20th century. Initially dominated by manual welding techniques, the industry has gradually transitioned to automated and semi-automated systems, significantly enhancing precision and productivity. The introduction of MIG (Metal Inert Gas) and TIG (Tungsten Inert Gas) welding processes revolutionized the sector by allowing for more versatile applications across various materials.
In recent decades, advancements in technology have further transformed the landscape. Digital control systems, robotics, and sophisticated software have become integral to modern welding machines, catering to the increasing complexity of manufacturing processes. Today, the sector is focused on developing smart welding solutions that not only improve operational efficiency but also provide real-time data analytics, paving the way for predictive maintenance and enhanced quality control.
As the market continues to evolve, welding machine manufacturers must stay attuned to technological advancements and shifting consumer demands to remain competitive in the global marketplace.
Frequently Asked Questions (FAQs) for B2B Buyers of Welding Machine Manufacturers
-
How do I choose the right welding machine for my business needs?
Choosing the right welding machine depends on several factors, including the type of materials you will be working with, the thickness of the materials, and the welding process you intend to use (MIG, TIG, Stick, etc.). Assess your specific applications and consider the machine’s features, such as portability, power output, and ease of use. Additionally, consult with manufacturers to understand which machines suit your operational requirements best and inquire about customization options to meet your unique needs. -
What is the best welding machine for heavy industrial applications?
For heavy industrial applications, machines like MIG welders with high amperage capabilities or TIG welders designed for thick materials are typically recommended. Flux-Cored Arc Welding (FCAW) machines are also effective for robust materials due to their high heat generation. Evaluate machines that offer durability, high duty cycles, and reliability under demanding conditions. Additionally, consider brands known for heavy-duty performance and inquire about after-sales support to ensure operational continuity. -
What factors should I consider when vetting welding machine manufacturers?
When vetting welding machine manufacturers, consider their industry experience, product certifications, and customer reviews. Look for manufacturers with a strong reputation in your region, especially those that comply with international quality standards. Additionally, assess their ability to provide technical support, spare parts availability, and warranty terms. Engaging with current users and seeking testimonials can provide insights into the reliability and performance of their machines. -
Are customization options available for welding machines?
Yes, many manufacturers offer customization options for welding machines to cater to specific applications or industry requirements. This may include adjustments to power settings, additional features such as multi-process capabilities, or tailored accessories. When discussing options with manufacturers, clearly outline your needs and ask for recommendations based on your operational goals. Custom machines may also lead to improved efficiency and better outcomes for specialized tasks. -
What is the minimum order quantity (MOQ) for welding machines?
The minimum order quantity (MOQ) for welding machines can vary significantly among manufacturers and is often influenced by production capacity, material costs, and shipping logistics. Some manufacturers may allow single-unit purchases, especially for standard models, while others might require bulk orders to optimize pricing. It’s advisable to discuss your needs directly with manufacturers to negotiate terms that align with your purchasing strategy, especially if you are entering new markets. -
What payment terms should I expect when purchasing welding machines internationally?
Payment terms for international purchases of welding machines can vary based on the manufacturer’s policies and the buyer’s negotiation power. Common terms include advance payments, letters of credit, or net payment terms (e.g., net 30 or net 60 days). Ensure to discuss payment methods that offer security, such as escrow services, and consider the currency exchange rates that may impact the overall cost. Always clarify any additional fees associated with payment processing. -
How can I ensure the quality of welding machines from international suppliers?
To ensure the quality of welding machines from international suppliers, request product certifications and compliance with industry standards (e.g., ISO, CE). Additionally, consider conducting factory audits or requesting samples for testing. Establishing a robust quality assurance process, including inspections during production and prior to shipment, can help mitigate risks. Building strong communication with suppliers and understanding their quality control measures is also essential for ensuring product reliability. -
What logistics considerations should I keep in mind when importing welding machines?
When importing welding machines, consider logistics factors such as shipping methods, customs regulations, and delivery timelines. Research the best shipping options based on cost and speed, and ensure compliance with import duties and taxes in your country. Engage with freight forwarders experienced in handling industrial equipment to streamline the process. Additionally, plan for potential delays by allowing sufficient lead time between ordering and receiving your machines.
Important Disclaimer & Terms of Use
⚠️ Important Disclaimer
The information provided in this guide, including content regarding manufacturers, technical specifications, and market analysis, is for informational and educational purposes only. It does not constitute professional procurement advice, financial advice, or legal advice.
While we have made every effort to ensure the accuracy and timeliness of the information, we are not responsible for any errors, omissions, or outdated information. Market conditions, company details, and technical standards are subject to change.
B2B buyers must conduct their own independent and thorough due diligence before making any purchasing decisions. This includes contacting suppliers directly, verifying certifications, requesting samples, and seeking professional consultation. The risk of relying on any information in this guide is borne solely by the reader.
Strategic Sourcing Conclusion and Outlook for Welding Machine Manufacturers
As the global demand for welding machines continues to rise, the significance of strategic sourcing cannot be overstated. International B2B buyers from Africa, South America, the Middle East, and Europe must prioritize understanding the various types of welding processes, such as MIG, TIG, and Flux-Cored Arc Welding, to select machines that align with their specific operational needs. Collaborating with reputable manufacturers ensures access to quality equipment, which not only enhances productivity but also drives cost efficiency.
Furthermore, leveraging local partnerships can facilitate smoother supply chain management and service support, particularly in regions like Egypt and Italy, where industrial growth is accelerating. Buyers should also remain informed about technological advancements in welding machinery to stay competitive in their respective markets.
Looking ahead, the welding industry is poised for innovation, with advancements in automation and digitalization paving the way for enhanced precision and efficiency. By adopting a proactive approach to sourcing and staying attuned to industry trends, international B2B buyers can secure a competitive edge. Now is the time to evaluate your sourcing strategies and explore partnerships that will propel your operations into the future.