The Ultimate Guide to Centrifugal Pump Manufacturers (2025)
Introduction: Navigating the Global Market for Centrifugal Pump Manufacturers
In the quest for sourcing reliable centrifugal pumps, international B2B buyers face a myriad of challenges, from understanding diverse market offerings to ensuring quality and compliance with local standards. This guide aims to demystify the global market for centrifugal pump manufacturers, providing an in-depth analysis of various types, applications, and the critical factors to consider when selecting suppliers. Whether you are operating in sectors like water treatment, oil and gas, or food processing, knowing how to navigate the complexities of centrifugal pump sourcing is essential for making informed purchasing decisions.
This comprehensive resource will cover essential topics, including the different types of centrifugal pumps, their specific applications across various industries, and strategies for effectively vetting suppliers. Additionally, we will explore cost factors and provide insights into potential pitfalls to avoid during the procurement process. With a particular focus on the needs of buyers from Africa, South America, the Middle East, and Europe, this guide empowers you to make strategic purchasing choices that align with your operational requirements and budget constraints.
By equipping you with actionable insights and a clear understanding of the centrifugal pump landscape, this guide serves as a crucial tool in optimizing your procurement strategy and enhancing your supply chain resilience.
Understanding Centrifugal Pump Manufacturers Types and Variations
Type Name | Key Distinguishing Features | Primary B2B Applications | Brief Pros & Cons for Buyers |
---|---|---|---|
Single Stage Centrifugal Pump | Simple design, low initial cost, efficient for low head applications | Water supply, irrigation | Pros: Cost-effective, easy maintenance. Cons: Limited to low head applications. |
Multi-Stage Centrifugal Pump | Multiple impellers for high pressure and flow | Oil and gas, power generation | Pros: High efficiency, suitable for high pressure. Cons: Higher initial cost, complex maintenance. |
Submersible Centrifugal Pump | Designed to operate underwater, compact design | Wastewater treatment, dewatering | Pros: Space-saving, effective in high water levels. Cons: Limited accessibility for repairs. |
Magnetic Drive Centrifugal Pump | Sealed design, no mechanical seals, low maintenance | Chemical processing, pharmaceuticals | Pros: Leak-free operation, reduced maintenance. Cons: Higher cost, limited flow rates. |
ANSI Centrifugal Pump | Standardized design, interchangeable parts | Industrial processes, HVAC systems | Pros: Easy to replace parts, widely available. Cons: May not suit specialized applications. |
What Are the Key Characteristics of Single Stage Centrifugal Pumps?
Single stage centrifugal pumps feature a straightforward design that includes a single impeller. They are primarily utilized in applications requiring low head and moderate flow rates, such as water supply and irrigation. For B2B buyers, the simplicity of design translates to lower initial costs and easier maintenance. However, their performance is limited when it comes to high head applications, making them less suitable for industries with demanding pressure requirements.
How Do Multi-Stage Centrifugal Pumps Differ in Functionality?
Multi-stage centrifugal pumps incorporate multiple impellers to generate higher pressures and flow rates, making them ideal for applications in oil and gas or power generation. These pumps excel in high-pressure environments, offering enhanced efficiency. B2B buyers should consider the higher initial investment and more complex maintenance routines, which may require specialized training or expertise. However, the long-term operational efficiency can justify these costs in demanding applications.
What Makes Submersible Centrifugal Pumps Unique?
Submersible centrifugal pumps are specifically designed to operate underwater, featuring a compact design that allows them to function in tight spaces. They are widely used in wastewater treatment and dewatering applications, where high water levels are prevalent. For international B2B buyers, the space-saving benefits are appealing, but accessibility for repairs can be a challenge. It’s essential to evaluate the operational environment and maintenance capabilities before purchasing.
Why Choose Magnetic Drive Centrifugal Pumps?
Magnetic drive centrifugal pumps are characterized by their sealed design, which eliminates the need for mechanical seals. This feature makes them particularly suitable for chemical processing and pharmaceutical applications, where leak prevention is critical. B2B buyers benefit from reduced maintenance needs, although the higher upfront cost and limited flow rates may be drawbacks. When considering these pumps, it’s crucial to weigh the operational environment against the cost-effectiveness over time.
What Are the Advantages of ANSI Centrifugal Pumps?
ANSI centrifugal pumps are designed to meet standardized specifications, allowing for easy interchangeability of parts. They are commonly used in industrial processes and HVAC systems, making them a reliable choice for many B2B applications. The ease of sourcing replacement parts and widespread availability are significant advantages for buyers. However, ANSI pumps may not be suited for specialized applications, and buyers should assess whether their specific needs align with these standard designs.
Related Video: API 610 Pump Types and Classification – 18 types of API 610 Centrifugal Pumps
Key Industrial Applications of Centrifugal Pump Manufacturers
Industry/Sector | Specific Application of Centrifugal Pump Manufacturers | Value/Benefit for the Business | Key Sourcing Considerations for this Application |
---|---|---|---|
Water Treatment | Pumping and distributing treated water | Ensures efficient water supply and distribution | Reliability, energy efficiency, and maintenance support |
Oil and Gas | Transporting crude oil and refined products | Enhances operational efficiency and reduces downtime | Material compatibility, pressure ratings, and certifications |
Chemical Processing | Moving corrosive and viscous fluids | Maintains process integrity and safety | Chemical resistance, durability, and compliance with regulations |
Agriculture | Irrigation systems for crop production | Increases crop yield and optimizes water usage | Flow rate, energy consumption, and adaptability to local conditions |
Mining and Minerals | Slurry transport in mineral processing | Improves recovery rates and reduces operational costs | Wear resistance, pump design, and ease of installation |
How Are Centrifugal Pumps Used in Water Treatment?
Centrifugal pumps play a crucial role in water treatment facilities by efficiently pumping and distributing treated water to various consumers. These pumps are designed to handle large volumes of water, ensuring a consistent supply that meets regulatory standards. For international buyers, especially in regions like Africa and South America, sourcing pumps that are energy-efficient and require minimal maintenance is essential to reduce operational costs and enhance service reliability.
What Role Do Centrifugal Pumps Play in the Oil and Gas Industry?
In the oil and gas sector, centrifugal pumps are integral for transporting crude oil and refined products through pipelines. They ensure smooth and continuous flow, which is vital for minimizing downtime and maximizing production efficiency. Buyers from the Middle East and Europe must consider factors like material compatibility with hydrocarbons, pressure ratings, and certifications to ensure compliance with industry standards and enhance operational safety.
How Are Centrifugal Pumps Essential in Chemical Processing?
Centrifugal pumps are widely used in chemical processing to move corrosive and viscous fluids safely and efficiently. Their ability to maintain process integrity while handling harsh chemicals is critical for safety and compliance. For B2B buyers in regions with stringent regulatory environments, such as Europe, sourcing pumps that offer chemical resistance and durability is paramount to avoid costly downtimes and ensure operational efficiency.
What Benefits Do Centrifugal Pumps Offer in Agriculture?
In agriculture, centrifugal pumps are pivotal for irrigation systems, facilitating the movement of water for crop production. By optimizing water usage, these pumps help increase crop yields and ensure sustainable farming practices. Buyers from regions like Africa and South America should focus on selecting pumps that offer high flow rates and low energy consumption to maximize productivity while minimizing costs.
How Do Centrifugal Pumps Enhance Mining and Minerals Processing?
Centrifugal pumps are essential in mining operations for transporting slurries during mineral processing. They improve recovery rates and reduce operational costs by providing efficient slurry movement. For B2B buyers in the mining sector, particularly in resource-rich regions, it’s important to consider the wear resistance and specific pump design suited for abrasive materials to ensure longevity and reliability in harsh environments.
Related Video: Centrifugal Pump Basics – How centrifugal pumps work working principle hvacr
3 Common User Pain Points for ‘Centrifugal Pump Manufacturers’ & Their Solutions
Scenario 1: Navigating Energy Efficiency Regulations in Pump Selection
The Problem: Many B2B buyers, particularly those in regions like Africa and South America, face increasing pressure to comply with local energy efficiency regulations. Centrifugal pumps are often significant energy consumers, and selecting a model that meets these regulations without sacrificing performance can be daunting. Buyers may struggle to understand which certifications and efficiency ratings are necessary for their specific applications, leading to potential fines or operational inefficiencies.
The Solution: To effectively navigate energy efficiency regulations, buyers should prioritize sourcing centrifugal pumps that are certified to meet local standards, such as ISO 9001 for quality management and ISO 14001 for environmental management. Engaging directly with manufacturers who provide transparent documentation about their products’ energy consumption and efficiency ratings can streamline this process. Additionally, buyers can utilize software tools or consult with industry experts who can analyze their specific operational requirements and recommend suitable pump models that not only comply with regulations but also optimize energy usage. Building a relationship with a manufacturer that offers ongoing support and updates on regulatory changes can further enhance compliance and operational efficiency.
Scenario 2: Addressing Pump Maintenance and Downtime Challenges
The Problem: Buyers often encounter significant challenges related to the maintenance and reliability of centrifugal pumps, which can lead to unexpected downtime and lost revenue. In sectors like agriculture and manufacturing, the failure of a pump can halt operations, causing financial strain and affecting supply chain commitments. Many buyers may not have adequate knowledge of maintenance protocols or the right resources to ensure their pumps remain operational.
The Solution: A proactive approach to maintenance is essential for minimizing downtime. Buyers should prioritize manufacturers that offer comprehensive service agreements, including routine inspections, preventive maintenance schedules, and training for in-house staff. Additionally, implementing a predictive maintenance program using IoT sensors can provide real-time monitoring of pump performance and alert users to potential issues before they escalate. Investing in training workshops offered by manufacturers can empower staff with the necessary skills to carry out basic maintenance, ensuring that pumps operate at peak efficiency and reducing the likelihood of costly breakdowns.
Scenario 3: Ensuring Compatibility with Existing Systems
The Problem: Another common pain point for B2B buyers is the challenge of ensuring that new centrifugal pumps are compatible with existing systems. Whether in water treatment facilities in the Middle East or in manufacturing plants across Europe, integrating new pumps can require significant modifications to pipelines, control systems, and other equipment. Buyers may face costly delays and increased project budgets if compatibility issues are not addressed early in the purchasing process.
The Solution: To mitigate compatibility issues, buyers should conduct a thorough assessment of their current systems before selecting a centrifugal pump. This involves documenting existing specifications, including flow rates, pressure requirements, and pipe sizes. Collaborating with manufacturers during the selection process can provide insights into which models can seamlessly integrate with current infrastructure. Buyers should also consider modular pump designs that allow for easier integration and future scalability. Additionally, investing in simulation software can help visualize how the new pump will interact with existing systems, allowing for informed decision-making and reducing the risk of costly modifications after installation.
Strategic Material Selection Guide for Centrifugal Pump Manufacturers
When selecting materials for centrifugal pumps, manufacturers must consider various factors that directly impact performance, durability, and cost-effectiveness. Below is an analysis of four common materials used in centrifugal pump manufacturing, tailored for international B2B buyers, especially those from Africa, South America, the Middle East, and Europe.
What Are the Key Properties of Cast Iron in Centrifugal Pumps?
Cast Iron is one of the most widely used materials in centrifugal pump construction due to its excellent mechanical properties and cost-effectiveness. It typically has a temperature rating up to 200°C (392°F) and can handle pressures around 10 bar (145 psi). Its inherent corrosion resistance is moderate, making it suitable for various applications, particularly in water and wastewater management.
Pros: Cast iron is durable and can withstand significant wear and tear, making it ideal for heavy-duty applications. It is also relatively inexpensive compared to other materials, which can significantly reduce manufacturing costs.
Cons: The primary limitation of cast iron is its susceptibility to corrosion in aggressive environments, such as those involving acidic or saline fluids. Additionally, it is heavier than alternative materials, which may impact installation and maintenance.
Impact on Application: Cast iron is well-suited for handling water and non-corrosive fluids. However, for applications involving corrosive or abrasive media, alternative materials may be required.
Considerations for International Buyers: Buyers should ensure compliance with local standards such as ASTM or DIN for cast iron specifications. In regions like Africa and South America, where infrastructure may vary, understanding the local availability of cast iron components can be crucial.
How Does Stainless Steel Enhance Pump Performance?
Stainless Steel is favored for its high corrosion resistance and strength, making it suitable for various applications, including food processing and chemical handling. It typically supports higher temperature ratings (up to 300°C or 572°F) and pressures (up to 20 bar or 290 psi).
Pros: The primary advantage of stainless steel is its excellent resistance to corrosion and staining, which extends the lifespan of pumps in harsh environments. It is also lightweight compared to cast iron, facilitating easier installation.
Cons: The main drawback is the higher cost associated with stainless steel, which can impact overall project budgets. Additionally, the manufacturing process can be more complex, requiring specialized equipment and techniques.
Impact on Application: Stainless steel is ideal for applications involving aggressive chemicals or high-purity requirements, such as in pharmaceuticals or food and beverage industries.
Considerations for International Buyers: Buyers should verify compliance with international standards like JIS for stainless steel grades. In regions like the Middle East, where corrosion from saltwater is a concern, selecting the right grade of stainless steel is critical.
What Are the Advantages of Plastic Composites in Pump Manufacturing?
Plastic Composites, such as polypropylene and PVC, are increasingly used in centrifugal pumps due to their lightweight and corrosion-resistant properties. They can typically handle temperatures up to 80°C (176°F) and pressures around 6 bar (87 psi).
Pros: The primary advantage of plastic composites is their excellent chemical resistance, making them suitable for a wide range of corrosive fluids. They are also significantly lighter than metals, reducing transportation and installation costs.
Cons: However, plastic composites often have lower mechanical strength compared to metals, which can limit their use in high-pressure applications. They may also be more prone to wear over time, especially in abrasive environments.
Impact on Application: These materials are particularly effective in handling corrosive chemicals in industries like agriculture and wastewater treatment.
Considerations for International Buyers: Buyers should ensure that the selected plastic composites meet relevant standards, such as ASTM for chemical resistance. In regions like Africa, where temperature fluctuations can be extreme, understanding the thermal properties of these materials is essential.
How Do Bronze Alloys Contribute to Pump Efficiency?
Bronze Alloys are often used in centrifugal pumps for their excellent wear resistance and strength. They can typically handle temperatures up to 250°C (482°F) and pressures around 15 bar (217 psi).
Pros: The wear resistance of bronze alloys makes them ideal for applications involving abrasive materials. They also possess good corrosion resistance, particularly in marine environments.
Cons: The main disadvantage is the higher cost compared to cast iron and plastic composites. Additionally, bronze can be more challenging to machine, which may complicate manufacturing processes.
Impact on Application: Bronze alloys are particularly effective in marine and industrial applications where durability is critical.
Considerations for International Buyers: Buyers should check compliance with relevant standards such as ASTM for bronze specifications. In Europe, understanding the local supply chain for bronze components can be beneficial for timely project execution.
Summary Table of Material Selection for Centrifugal Pumps
Material | Typical Use Case for Centrifugal Pump Manufacturers | Key Advantage | Key Disadvantage/Limitation | Relative Cost (Low/Med/High) |
---|---|---|---|---|
Cast Iron | Water and wastewater management | Durable and cost-effective | Moderate corrosion resistance | Low |
Stainless Steel | Food processing, chemical handling | Excellent corrosion resistance | Higher cost and complex manufacturing | High |
Plastic Composites | Handling corrosive chemicals | Lightweight and chemically resistant | Lower mechanical strength | Medium |
Bronze Alloys | Marine and industrial applications | Excellent wear resistance | Higher cost and machining challenges | High |
This strategic material selection guide provides essential insights for international B2B buyers in selecting the appropriate materials for centrifugal pumps, ensuring optimal performance, compliance, and cost-effectiveness.
In-depth Look: Manufacturing Processes and Quality Assurance for Centrifugal Pump Manufacturers
What Are the Key Stages in the Manufacturing Process of Centrifugal Pumps?
The manufacturing of centrifugal pumps involves several critical stages that ensure the final product meets industry standards and customer specifications. Understanding these stages can help international B2B buyers identify reliable suppliers and ensure they receive high-quality products.
Material Preparation: What Materials Are Commonly Used?
The first step in the manufacturing process is the preparation of materials. Common materials for centrifugal pumps include:
- Cast Iron: Known for its strength and wear resistance, often used for standard pumps.
- Stainless Steel: Ideal for corrosive environments, ensuring durability and longevity.
- Bronze and Composite Materials: Used for specific applications where corrosion resistance and lightweight properties are essential.
During this stage, materials undergo quality inspections to verify their composition and integrity. Buyers should inquire about the suppliers’ sourcing practices and whether they conduct material certifications.
Forming: What Techniques Are Used in Pump Component Fabrication?
Once materials are prepared, the next stage is forming, which includes various manufacturing techniques such as:
- Casting: A primary method for creating pump casings and impellers. This process involves pouring molten metal into molds, which is then cooled to form solid components.
- Machining: Essential for creating precise dimensions on components like shafts and housings. Techniques such as turning, milling, and drilling are commonly employed.
- Forging: Sometimes used for critical components to enhance their mechanical properties through deformation under heat and pressure.
Buyers should assess the capabilities of potential suppliers in terms of equipment and technology, as advanced techniques can lead to better quality and performance.
Assembly: How Are Centrifugal Pumps Assembled?
The assembly stage is where all individual components come together to form the complete pump. This process typically includes:
- Fitting Components: Aligning and fitting the impeller, casing, and motor.
- Sealing: Applying seals and gaskets to prevent leaks and ensure optimal performance.
- Balancing: Ensuring that rotating parts are balanced to minimize vibrations during operation, which is crucial for longevity.
Buyers should look for suppliers that utilize skilled labor and automated systems for assembly, as this can significantly affect the quality of the final product.
Finishing: What Finishing Processes Are Commonly Applied?
The finishing stage enhances the pump’s performance and aesthetic appeal. Key processes include:
- Surface Treatment: Techniques such as shot blasting, powder coating, or anodizing improve corrosion resistance and surface finish.
- Quality Inspection: Final inspections are conducted to check for defects, alignment, and overall quality before shipping.
International buyers should request information on finishing processes, as these can impact the pump’s durability and performance in specific environments.
What Quality Assurance Standards Should B2B Buyers Consider?
Quality assurance is paramount in the manufacturing of centrifugal pumps, especially for international B2B buyers. Familiarity with relevant standards can help ensure product reliability and compliance.
Which International Standards Are Relevant for Centrifugal Pump Manufacturers?
Manufacturers often adhere to several international quality standards, including:
- ISO 9001: A widely recognized standard that ensures consistent quality management systems. It emphasizes continuous improvement and customer satisfaction.
- CE Marking: Required for products sold in the European Economic Area, indicating compliance with health, safety, and environmental protection standards.
- API Standards: The American Petroleum Institute provides guidelines specifically for pumps used in the oil and gas industry, ensuring safety and reliability.
Understanding these standards can help buyers make informed decisions about suppliers’ capabilities and product quality.
How Is Quality Control Implemented During Manufacturing?
Quality control (QC) involves systematic checks throughout the manufacturing process to ensure that products meet specified standards. Key checkpoints include:
- Incoming Quality Control (IQC): Inspects raw materials upon arrival to verify they meet quality specifications.
- In-Process Quality Control (IPQC): Ongoing inspections during production to catch defects early and ensure adherence to manufacturing standards.
- Final Quality Control (FQC): Comprehensive testing of finished products before shipment, including performance tests and visual inspections.
Buyers should inquire about the specific QC processes employed by potential suppliers, as robust quality control can significantly reduce the risk of receiving defective products.
What Testing Methods Are Commonly Used for Centrifugal Pumps?
Testing is a critical component of quality assurance. Common methods include:
- Hydraulic Testing: Assessing the pump’s performance under pressure to ensure it meets operational specifications.
- Vibration Testing: Evaluating the mechanical integrity and balance of rotating components.
- Non-Destructive Testing (NDT): Techniques like ultrasonic and magnetic particle testing are used to identify internal defects without damaging the components.
Buyers should request documentation of testing procedures and results to ensure that suppliers meet their quality expectations.
How Can B2B Buyers Verify Supplier Quality Control?
For international buyers, verifying a supplier’s quality control processes is crucial. Here are actionable steps to ensure due diligence:
- Supplier Audits: Conduct on-site audits to evaluate manufacturing practices, equipment, and quality control systems.
- Request Quality Reports: Ask for detailed QC reports, including the results of tests performed on the products.
- Third-Party Inspections: Consider hiring independent inspection agencies to evaluate suppliers’ facilities and processes.
Buyers from regions like Africa, South America, the Middle East, and Europe should be particularly diligent in this process, as it can prevent costly mistakes and ensure compliance with local regulations.
What Nuances Should International B2B Buyers Be Aware of in Quality Control?
Understanding the nuances of quality control in different regions can enhance procurement strategies. For instance:
- Cultural Differences: Different regions may have varying approaches to quality management. Buyers should be aware of these differences and adapt their communication accordingly.
- Regulatory Compliance: Ensure that suppliers comply with local and international regulations relevant to the buyer’s market, as non-compliance can lead to legal issues.
- Supply Chain Stability: Assess the supplier’s ability to maintain quality during periods of high demand or supply chain disruptions.
By considering these factors, B2B buyers can better navigate the complexities of sourcing centrifugal pumps from international manufacturers, ensuring they partner with reliable suppliers who prioritize quality and performance.
Practical Sourcing Guide: A Step-by-Step Checklist for ‘Centrifugal Pump Manufacturers’
To successfully navigate the procurement of centrifugal pumps, international B2B buyers must follow a structured approach. This checklist will help streamline the sourcing process, ensuring that you select the right manufacturer that meets your operational needs and compliance requirements.
Step 1: Define Your Technical Specifications
Clearly articulate the technical requirements for your centrifugal pumps. Consider factors such as flow rate, head pressure, fluid type, temperature, and application environment. This step is crucial as it helps narrow down suppliers who can meet your specific needs and ensures compatibility with your existing systems.
Step 2: Research Potential Suppliers
Conduct thorough research to identify potential centrifugal pump manufacturers. Look for companies with a solid track record in your industry and region. Utilize online platforms, industry directories, and trade shows to gather a list of candidates. Pay attention to their reputation, customer reviews, and case studies to gauge their reliability.
Step 3: Evaluate Supplier Certifications
✅ Verify supplier certifications and compliance with international standards. Certifications such as ISO 9001 or relevant industry-specific standards ensure that the manufacturer adheres to quality management practices. This not only protects your investment but also mitigates risks associated with substandard products.
Step 4: Request Prototypes or Samples
Before making a bulk order, request prototypes or samples of the centrifugal pumps. This step allows you to assess the product quality, performance, and suitability for your application. Pay close attention to the materials used, assembly quality, and operational efficiency during testing.
Step 5: Analyze Pricing and Payment Terms
Get detailed quotes from multiple suppliers and analyze the pricing structures. Understand the total cost of ownership, including shipping, customs, and installation fees. Additionally, discuss payment terms to ensure they align with your financial capabilities, especially if you are sourcing from international suppliers.
Step 6: Assess After-Sales Support and Warranty
Evaluate the after-sales support offered by the manufacturer. Reliable suppliers should provide comprehensive warranties and responsive customer service. Inquire about technical support, spare parts availability, and maintenance services to ensure long-term operational efficiency of the pumps.
Step 7: Build a Relationship with Your Supplier
Once you have chosen a supplier, invest time in building a strong relationship. Open communication can lead to better negotiations, customized solutions, and priority support in the future. Establishing a partnership can also provide insights into new technologies and innovations in centrifugal pump manufacturing.
By following this checklist, B2B buyers can streamline their sourcing process, ensuring that they select a centrifugal pump manufacturer that not only meets their specifications but also aligns with their operational goals.
Comprehensive Cost and Pricing Analysis for Centrifugal Pump Manufacturers Sourcing
What Are the Key Cost Components for Centrifugal Pump Manufacturers?
When sourcing centrifugal pumps, understanding the cost structure is essential for international B2B buyers. The primary cost components include:
-
Materials: The choice of materials significantly impacts the overall cost. Common materials include stainless steel, cast iron, and specialized alloys. Prices can vary based on market conditions and material availability.
-
Labor: Labor costs can differ widely depending on the geographical location of the manufacturer. Regions with lower labor costs may offer more competitive pricing but could also affect quality and lead times.
-
Manufacturing Overhead: This includes indirect costs related to production facilities, utilities, and administrative expenses. Efficient manufacturing processes can reduce overhead, impacting pricing positively.
-
Tooling: Initial tooling costs for custom designs can be substantial. Buyers should inquire about these costs upfront, as they may not be included in the quoted price.
-
Quality Control (QC): Implementing rigorous QC processes adds to production costs. However, it is crucial for ensuring product reliability and compliance with industry standards.
-
Logistics: Shipping and handling costs can greatly influence total expenses, especially for international shipments. Factors such as distance, mode of transport, and Incoterms play a vital role here.
-
Margin: Manufacturers typically build a profit margin into their pricing. Understanding the margin expectations can help buyers negotiate better deals.
How Do Price Influencers Affect Sourcing Decisions?
Several factors can influence the pricing of centrifugal pumps, which B2B buyers should consider:
-
Volume and Minimum Order Quantity (MOQ): Purchasing in bulk often leads to discounts. Be mindful of the MOQ as it can affect your overall cost per unit.
-
Specifications and Customization: Custom-designed pumps can incur additional costs due to unique specifications. Discussing your needs early in the process can help in obtaining accurate quotes.
-
Quality and Certifications: Higher quality and industry certifications (like ISO) often come at a premium. Assess the necessity of these certifications based on your application and regulatory requirements.
-
Supplier Factors: The reputation and reliability of suppliers can influence prices. Established suppliers with a track record of quality may charge more but can offer long-term reliability.
-
Incoterms: Understanding Incoterms is crucial for calculating total costs. Terms like FOB (Free on Board) or CIF (Cost, Insurance, and Freight) can shift costs and responsibilities between buyer and seller.
What Are the Best Negotiation Tips for International B2B Buyers?
Negotiating effectively can lead to significant cost savings. Here are some actionable tips:
-
Research and Benchmark: Gather market data to understand standard pricing and practices. This information can provide leverage during negotiations.
-
Build Relationships: Developing a good rapport with suppliers can lead to better pricing and terms. Long-term relationships often yield better service and flexibility.
-
Consider Total Cost of Ownership (TCO): Assess not just the initial purchase price but also maintenance, operational costs, and potential downtime. A lower upfront cost may not always equate to better value in the long run.
-
Be Transparent About Your Needs: Clearly communicate your requirements and constraints. This transparency can help suppliers tailor their offers more effectively.
-
Leverage Competition: Obtaining quotes from multiple suppliers can create competitive pressure, often resulting in better pricing.
What Pricing Nuances Should International Buyers Be Aware Of?
International buyers, particularly from regions like Africa, South America, the Middle East, and Europe, should be aware of specific pricing nuances:
-
Currency Fluctuations: Exchange rates can significantly impact costs. Consider negotiating in a stable currency to mitigate this risk.
-
Import Duties and Taxes: Be aware of any tariffs or taxes applicable to imported pumps. These can add to the overall cost and should be factored into your budget.
-
Cultural Factors: Different regions may have varying expectations regarding negotiation styles and payment terms. Understanding these cultural nuances can facilitate smoother transactions.
-
Lead Times: International shipping can introduce delays. Factor in lead times when planning your procurement to avoid operational disruptions.
Disclaimer on Indicative Prices
Prices for centrifugal pumps can vary widely based on the factors mentioned above. It is advisable to seek multiple quotes and conduct thorough due diligence to ensure a fair and competitive price. Always verify the details with suppliers to obtain the most accurate and up-to-date pricing information.
Alternatives Analysis: Comparing Centrifugal Pump Manufacturers With Other Solutions
In the realm of fluid transportation, centrifugal pumps are a popular choice among manufacturers for their efficiency and versatility. However, international B2B buyers should consider various alternative technologies that may better suit their specific operational needs. This analysis will compare centrifugal pump manufacturers with two notable alternatives: positive displacement pumps and peristaltic pumps.
Comparison Table of Centrifugal Pumps and Alternatives
Comparison Aspect | Centrifugal Pump Manufacturers | Positive Displacement Pumps | Peristaltic Pumps |
---|---|---|---|
Performance | High flow rates, suitable for low-viscosity fluids | Excellent for high-viscosity fluids; consistent flow | Gentle pumping action; ideal for shear-sensitive fluids |
Cost | Moderate initial investment; operational costs vary | Generally higher upfront costs; lower operational costs | Moderate costs; cost-effective for small-scale applications |
Ease of Implementation | Relatively straightforward installation and integration | May require specialized installation | Simple setup, especially for small systems |
Maintenance | Requires regular maintenance; susceptible to wear | Lower maintenance needs; robust design | Minimal maintenance; tubing replacements needed periodically |
Best Use Case | Water treatment, chemical processing | Oil & gas, food processing | Medical applications, laboratory settings |
What Are the Advantages and Disadvantages of Positive Displacement Pumps?
Positive displacement pumps excel in applications requiring precise flow control and high viscosity handling. They can maintain a constant flow rate regardless of changes in pressure, making them ideal for industries such as oil and gas or food processing. However, their higher initial costs and potential complexity in installation may deter some buyers. Additionally, they can be less efficient at higher flow rates compared to centrifugal pumps.
How Do Peristaltic Pumps Compare in Terms of Application and Efficiency?
Peristaltic pumps are particularly suited for applications where the fluid must remain uncontaminated, such as in medical or laboratory settings. Their gentle pumping action minimizes shear stress on the fluid, making them ideal for sensitive materials. They are relatively easy to maintain, with most maintenance involving the replacement of tubing. However, they may not be suitable for large-scale operations due to their limited flow rates and potential for wear on the tubing over time.
Conclusion: How to Choose the Right Pumping Solution for Your Needs
When selecting a pumping solution, international B2B buyers must evaluate their specific application requirements, including fluid characteristics, flow rate needs, and budget constraints. Centrifugal pumps are advantageous for high flow and low-viscosity applications, while positive displacement pumps offer precision for viscous materials. Peristaltic pumps serve specialized niches requiring gentle handling of sensitive fluids. By analyzing these alternatives in terms of performance, cost, ease of implementation, maintenance, and best use cases, buyers can make informed decisions that align with their operational goals.
Essential Technical Properties and Trade Terminology for Centrifugal Pump Manufacturers
What Are the Key Technical Properties of Centrifugal Pumps That Buyers Should Know?
When sourcing centrifugal pumps, understanding the technical properties is crucial for making informed purchasing decisions. Here are some essential specifications to consider:
1. Material Grade: Why It Matters for Pump Durability
Centrifugal pumps are constructed from various materials, including stainless steel, cast iron, and plastic. The choice of material affects the pump’s resistance to corrosion, temperature extremes, and wear. For instance, stainless steel is ideal for applications involving corrosive fluids, while cast iron is suitable for general-purpose use. For B2B buyers, selecting the right material ensures longevity and reliability in their operations.
2. Tolerance Levels: Ensuring Precision and Performance
Tolerance levels refer to the permissible limits of variation in a pump’s dimensions and specifications. High precision in manufacturing is essential for ensuring optimal pump performance, reducing wear and tear, and extending service life. Buyers must consider tolerance levels to avoid operational inefficiencies and costly downtimes, particularly in high-stakes industries like oil and gas or pharmaceuticals.
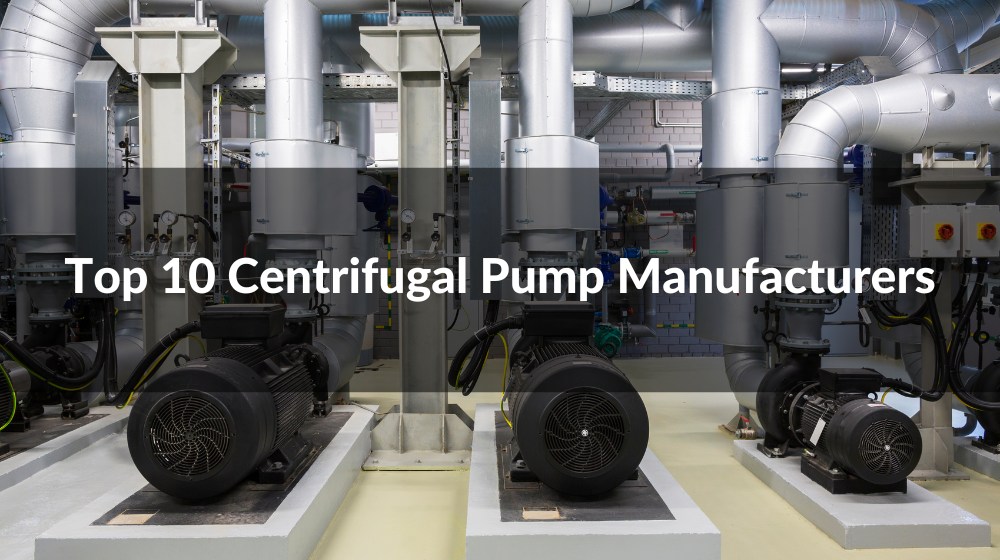
A stock image related to Centrifugal Pump Manufacturers.
3. Flow Rate: Understanding Your Operational Needs
The flow rate, typically measured in liters per minute (LPM) or gallons per minute (GPM), indicates the volume of fluid that the pump can move within a specific timeframe. Buyers should assess their operational requirements to determine the necessary flow rate. A pump with a flow rate that meets or exceeds operational needs enhances efficiency and productivity.
4. Head Pressure: How It Affects System Design
Head pressure is a critical specification that defines the height to which a pump can raise water (or another fluid). It is measured in meters or feet and is influenced by factors such as pipe friction and elevation changes in the system. Understanding head pressure helps buyers select pumps that can effectively deliver fluids to their intended destinations, especially in complex system designs.
5. Efficiency Rating: Maximizing Energy Use
The efficiency rating of a centrifugal pump indicates how effectively it converts input energy into hydraulic energy. Higher efficiency means lower operational costs and reduced environmental impact. B2B buyers should prioritize pumps with high efficiency ratings to optimize their energy consumption and minimize long-term costs.
Which Trade Terms Should Buyers Be Familiar With When Purchasing Centrifugal Pumps?
Knowledge of industry-specific jargon can facilitate smoother transactions and negotiations. Here are some common trade terms relevant to centrifugal pump procurement:
1. OEM (Original Equipment Manufacturer): Understanding the Source
OEM refers to companies that manufacture products that are sold under another company’s brand name. Buyers often source pumps from OEMs to ensure quality and compatibility with existing systems. Understanding OEM relationships can help buyers make informed decisions about product reliability and support.
2. MOQ (Minimum Order Quantity): Managing Inventory Costs
MOQ indicates the minimum number of units a supplier is willing to sell in a single order. This term is crucial for B2B buyers aiming to manage inventory costs effectively. Knowing the MOQ helps businesses plan their purchases according to their budget and storage capacity.
3. RFQ (Request for Quotation): Streamlining the Procurement Process
An RFQ is a formal process where buyers request price quotes from suppliers for specific products or services. This term is vital for buyers to understand as it aids in obtaining competitive pricing and better negotiating power. An RFQ can help streamline the procurement process and ensure buyers receive accurate pricing information.
4. Incoterms (International Commercial Terms): Navigating Global Trade
Incoterms are a series of international sales terms that define the responsibilities of buyers and sellers in global trade. Familiarity with these terms is essential for B2B buyers, especially those sourcing pumps internationally. Understanding Incoterms helps clarify shipping costs, risks, and responsibilities, ensuring smoother transactions across borders.
By grasping these technical properties and trade terminologies, international B2B buyers can make more informed decisions, ultimately enhancing their operational efficiency and reducing costs.
Navigating Market Dynamics and Sourcing Trends in the Centrifugal Pump Manufacturers Sector
What Are the Key Trends Shaping the Centrifugal Pump Manufacturers Market?
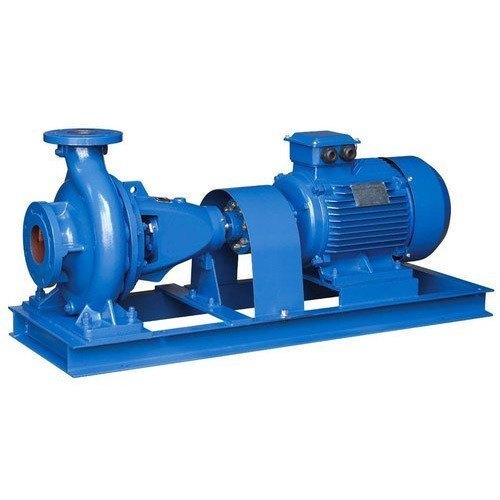
A stock image related to Centrifugal Pump Manufacturers.
The centrifugal pump manufacturing sector is experiencing transformative shifts driven by globalization, technological advancements, and evolving buyer expectations. One of the primary global drivers is the increasing demand for efficient water management systems across various industries, particularly in regions like Africa and South America, where access to clean water remains a challenge. As urbanization accelerates in these areas, the need for reliable and cost-effective pumping solutions has surged.
Emerging technologies such as IoT (Internet of Things) and AI (Artificial Intelligence) are also revolutionizing the centrifugal pump industry. These technologies facilitate predictive maintenance and enhance operational efficiency, allowing manufacturers to offer more value to B2B buyers. Additionally, the integration of smart sensors in centrifugal pumps enables real-time monitoring, improving reliability and reducing downtime, which is critical for industries such as oil and gas, agriculture, and municipal water systems.
International B2B buyers are increasingly prioritizing suppliers who demonstrate agility in adapting to market dynamics. This includes a focus on local sourcing to reduce lead times and transportation costs. Regions such as the Middle East and Europe are witnessing heightened competition, compelling manufacturers to innovate their product offerings and pricing strategies. Buyers should consider suppliers’ capabilities in customization and responsiveness to specific regional needs, as these factors can significantly impact operational success.
How Important Is Sustainability and Ethical Sourcing in the Centrifugal Pump Sector?
Sustainability has become a central pillar in the procurement strategies of international B2B buyers, particularly in the centrifugal pump manufacturing sector. The environmental impact of traditional manufacturing processes has prompted buyers to seek suppliers committed to reducing their carbon footprint and utilizing sustainable materials. This shift is particularly relevant in regions like Europe, where stringent regulations on environmental sustainability are enforced.
Ethical sourcing is equally crucial. Buyers are increasingly aware of the implications of their purchasing decisions on global supply chains. They are looking for manufacturers who prioritize ethical labor practices and ensure fair treatment throughout their supply chains. Certifications such as ISO 14001 for environmental management and ISO 45001 for occupational health and safety are becoming essential criteria for supplier selection.
Moreover, the adoption of ‘green’ materials in centrifugal pump manufacturing, such as recycled metals and eco-friendly coatings, is gaining traction. This not only minimizes environmental impact but also appeals to a growing segment of environmentally conscious buyers. By focusing on sustainability and ethical sourcing, B2B buyers can enhance their corporate social responsibility (CSR) profiles and meet the increasing demand from consumers for environmentally friendly products.
What Is the Brief History of Centrifugal Pump Manufacturing?
The history of centrifugal pump manufacturing dates back to the late 17th century when the principles of fluid dynamics began to be understood. The first centrifugal pump was developed in the 1680s by the Italian engineer Giovanni Battista Venturi, who recognized that fluid could be moved efficiently through centrifugal force. Over the centuries, advancements in materials and engineering processes have significantly improved the efficiency and reliability of centrifugal pumps.
By the 19th century, industrialization spurred the mass production of centrifugal pumps, making them indispensable in various applications, including agriculture, mining, and municipal water systems. The introduction of electric motors in the early 20th century further transformed the industry, allowing for greater automation and efficiency.
Today, centrifugal pumps are at the forefront of numerous industries, reflecting a rich history of innovation and adaptation. For international B2B buyers, understanding this evolution can provide valuable insights into the technological advancements and quality standards expected in the current market landscape.
Frequently Asked Questions (FAQs) for B2B Buyers of Centrifugal Pump Manufacturers
-
How do I choose the right centrifugal pump for my application?
Choosing the right centrifugal pump involves assessing your specific application requirements. Consider factors such as the type of fluid being pumped, flow rate, pressure requirements, and the operational environment. Additionally, evaluate the pump’s material compatibility with the fluid to prevent corrosion or degradation. Consulting with manufacturers can provide insights into the best options available, including features like energy efficiency and maintenance needs. -
What are the key specifications to look for when sourcing centrifugal pumps?
When sourcing centrifugal pumps, focus on specifications such as flow rate (measured in gallons per minute or liters per second), head (the height the pump can lift fluid), power consumption, and efficiency ratings. Additionally, consider the pump’s material construction, seal types, and any certifications relevant to your industry standards. Ensuring these specifications align with your operational needs will lead to better performance and longevity. -
What payment terms should I expect when purchasing from centrifugal pump manufacturers?
Payment terms can vary significantly between manufacturers, but commonly include options like upfront deposits, net 30, or net 60 terms. In international transactions, consider using letters of credit or escrow services to mitigate risk. Always negotiate terms that align with your cash flow and project timelines, and clarify any potential additional costs, such as shipping or customs duties, to avoid surprises. -
How can I verify the credibility of centrifugal pump manufacturers?
To verify the credibility of manufacturers, conduct thorough research by reviewing customer testimonials, case studies, and industry certifications. Request references from previous clients and assess their reputation through platforms like LinkedIn or industry-specific forums. Additionally, consider visiting their facilities if possible, or attending trade shows to engage directly with manufacturers and gain firsthand insights into their operations. -
What are the minimum order quantities (MOQ) for centrifugal pumps?
Minimum order quantities can vary widely among manufacturers based on their production capabilities and the specific pump models. Some manufacturers may allow orders as low as one unit, while others may require bulk orders to meet MOQ thresholds. Always inquire about MOQs before engaging in negotiations, as this will impact your inventory management and cash flow. -
Can centrifugal pumps be customized for specific industrial applications?
Yes, many manufacturers offer customization options for centrifugal pumps to meet specific industrial requirements. Customizations can include modifications in size, material, impeller design, and additional features like variable speed drives. Engaging in a detailed discussion with the manufacturer about your application will help ensure the pump meets all operational demands and efficiency standards. -
What logistics considerations should I keep in mind when sourcing centrifugal pumps internationally?
When sourcing centrifugal pumps internationally, consider logistics factors such as shipping methods, lead times, and customs regulations. Ensure that the manufacturer provides clear shipping terms and is experienced in exporting to your region. Additionally, evaluate the costs of transportation, potential tariffs, and the availability of local support for installation and maintenance to streamline the process. -
How do I ensure quality assurance when purchasing centrifugal pumps?
To ensure quality assurance, look for manufacturers that follow recognized quality management systems like ISO 9001. Request information on their testing procedures, including performance and durability tests, and whether they provide warranties for their products. Engaging in third-party inspections before shipment can also be beneficial, particularly for large orders, to verify that the pumps meet your specifications and industry standards.
Important Disclaimer & Terms of Use
⚠️ Important Disclaimer
The information provided in this guide, including content regarding manufacturers, technical specifications, and market analysis, is for informational and educational purposes only. It does not constitute professional procurement advice, financial advice, or legal advice.
While we have made every effort to ensure the accuracy and timeliness of the information, we are not responsible for any errors, omissions, or outdated information. Market conditions, company details, and technical standards are subject to change.
B2B buyers must conduct their own independent and thorough due diligence before making any purchasing decisions. This includes contacting suppliers directly, verifying certifications, requesting samples, and seeking professional consultation. The risk of relying on any information in this guide is borne solely by the reader.
Strategic Sourcing Conclusion and Outlook for Centrifugal Pump Manufacturers
In conclusion, strategic sourcing for centrifugal pumps is not merely a procurement task; it is a pivotal aspect of enhancing operational efficiency and reducing costs for businesses across Africa, South America, the Middle East, and Europe. By engaging with reputable manufacturers and understanding the intricacies of pump specifications, buyers can ensure they select the most suitable solutions for their specific applications.
How Can International Buyers Benefit from Strategic Sourcing?
International B2B buyers should prioritize building strong relationships with centrifugal pump manufacturers that demonstrate reliability, innovation, and a commitment to sustainability. This approach not only helps in negotiating better terms but also fosters collaboration for future projects. Additionally, utilizing data analytics to assess supplier performance and market trends can empower buyers to make informed decisions, optimizing their supply chain.
What’s Next for Buyers in the Centrifugal Pump Market?
Looking forward, the centrifugal pump market is poised for growth, driven by advancements in technology and increasing demand for efficient fluid transfer solutions. Buyers are encouraged to remain proactive, exploring emerging trends such as digitalization and eco-friendly technologies. By doing so, they can position themselves at the forefront of the industry, leveraging strategic sourcing to enhance their competitive edge. Engage with manufacturers now to secure the best opportunities in this evolving landscape.