Unlock Savings: Top Food Processing Machinery Manufacturers (2025)
Introduction: Navigating the Global Market for Food Processing Machinery Manufacturers
Navigating the global market for food processing machinery manufacturers can be daunting, especially for international B2B buyers seeking reliable suppliers. The challenge lies not only in sourcing high-quality equipment but also in ensuring that these machines meet diverse operational needs across various regions, including Africa, South America, the Middle East, and Europe. This guide is designed to demystify the complexities of purchasing food processing machinery by providing a comprehensive overview of the types of equipment available, their applications, and key factors to consider during supplier vetting.
In this guide, you will explore various categories of food processing machinery, from mixers and grinders to packaging and labeling systems. Each section will delve into specific applications, helping you understand which machines align best with your production goals. Furthermore, we will outline essential criteria for evaluating potential suppliers, including quality assurance practices, compliance with international standards, and cost considerations.
By equipping yourself with this knowledge, you will be empowered to make informed purchasing decisions that enhance operational efficiency and product quality. Whether you are a manufacturer in Brazil looking to upgrade your processing line or a distributor in Germany seeking reliable partners, this guide serves as your roadmap to navigating the dynamic landscape of food processing machinery. Together, we can ensure your business thrives in the competitive global market.
Understanding Food Processing Machinery Manufacturers Types and Variations
Type Name | Key Distinguishing Features | Primary B2B Applications | Brief Pros & Cons for Buyers |
---|---|---|---|
Batch Processing Machinery | Operates in batches, suitable for small to medium production. | Snack food production, dairy products | Pros: Flexibility in production; Cons: Slower output compared to continuous systems. |
Continuous Processing Machinery | Operates continuously, ideal for large-scale production. | Beverage production, canned foods | Pros: High efficiency; Cons: Higher initial investment. |
Packaging Machinery | Focuses on the packaging process, including filling and sealing. | Packaged foods, pharmaceuticals | Pros: Enhances shelf life; Cons: Complex maintenance requirements. |
Mixing and Blending Equipment | Used for combining ingredients uniformly. | Sauces, dressings, and baked goods | Pros: Ensures consistency; Cons: Requires careful calibration. |
Cooling and Freezing Machinery | Essential for preserving food quality and safety. | Frozen foods, ice cream production | Pros: Extends shelf life; Cons: Energy-intensive. |
What Are the Characteristics of Batch Processing Machinery?
Batch processing machinery is designed to handle production in discrete batches, making it ideal for businesses that require flexibility in their production schedules. This type of machinery is particularly suited for small to medium-sized operations, such as snack food production and dairy processing. When considering batch processing systems, B2B buyers should evaluate the machinery’s capacity, ease of cleaning, and adaptability to different recipes. While these systems allow for experimentation with new products, they typically produce at a slower pace compared to continuous systems.
Why Choose Continuous Processing Machinery?
Continuous processing machinery is tailored for high-volume production, operating without interruption to maximize efficiency. This type of equipment is prevalent in industries like beverage production and canned foods, where consistent output is essential. B2B buyers should consider factors such as energy consumption, maintenance needs, and scalability when investing in continuous processing solutions. While the initial costs can be higher, the long-term efficiency and reduced labor costs often justify the investment for businesses focusing on large-scale operations.
How Does Packaging Machinery Benefit B2B Buyers?
Packaging machinery plays a crucial role in the food processing sector by ensuring that products are packaged efficiently and securely. This equipment encompasses various processes, including filling, sealing, and labeling, and is vital for packaged foods and pharmaceuticals. Buyers should focus on the machinery’s compatibility with different packaging materials, speed, and automation capabilities. While packaging machinery can enhance product shelf life and reduce spoilage, it often comes with complex maintenance requirements that need to be addressed.
What Is the Importance of Mixing and Blending Equipment?
Mixing and blending equipment is essential for achieving uniform consistency in food products, such as sauces, dressings, and baked goods. This machinery allows manufacturers to combine various ingredients effectively, which is critical for maintaining quality and flavor. B2B buyers should assess the equipment’s mixing capacity, ease of use, and cleaning requirements. While these systems ensure product consistency, they require careful calibration to avoid variations in texture and taste, which can impact customer satisfaction.
Why Invest in Cooling and Freezing Machinery?
Cooling and freezing machinery is vital for preserving food quality, safety, and extending shelf life. This type of equipment is commonly used in the production of frozen foods and ice cream. B2B buyers must consider the energy efficiency, capacity, and technological advancements of cooling systems when making their purchasing decisions. Although these machines can be energy-intensive, the benefits of maintaining food quality and safety make them a crucial investment for food manufacturers aiming to meet consumer demands.
Related Video: Modern Ready Meal Food Factory 2020 Fully Automated Production Line | Advanced Food Processing Tech
Key Industrial Applications of Food Processing Machinery Manufacturers
Industry/Sector | Specific Application of Food Processing Machinery Manufacturers | Value/Benefit for the Business | Key Sourcing Considerations for this Application |
---|---|---|---|
Beverage Production | Automated bottling and packaging systems | Increases efficiency and reduces labor costs | Compatibility with existing production lines and scalability options |
Meat Processing | Meat slicing and dicing machinery | Enhances product consistency and reduces waste | Compliance with health regulations and ease of maintenance |
Dairy Processing | Pasteurization and homogenization equipment | Ensures product safety and extends shelf life | Energy efficiency and technology integration with existing systems |
Bakery Industry | Dough mixers and ovens | Improves product quality and consistency | Customization options and ability to handle various dough types |
Fruit and Vegetable Processing | Washing, peeling, and cutting machines | Increases throughput and improves food safety | Durability and ease of cleaning to meet hygiene standards |
How Are Food Processing Machinery Manufacturers Used in Beverage Production?
In the beverage production sector, automated bottling and packaging systems play a crucial role. These machines streamline the filling and sealing processes, significantly enhancing operational efficiency while minimizing labor costs. For international B2B buyers, particularly from regions like Africa and South America, sourcing such machinery requires an understanding of local production capacities and compatibility with existing systems. Buyers should also consider the scalability of machinery to accommodate future growth.
What Role Does Food Processing Machinery Play in Meat Processing?
Meat processing heavily relies on advanced slicing and dicing machinery to ensure product uniformity and minimize waste. These machines not only enhance the consistency of meat products but also address challenges related to labor shortages and food safety. For buyers in Europe and the Middle East, it’s essential to prioritize equipment that complies with stringent health regulations, ensuring that the machinery is easy to maintain and operates efficiently within regulatory frameworks.
How Is Food Processing Machinery Beneficial in Dairy Processing?
In the dairy processing industry, pasteurization and homogenization equipment are vital for ensuring product safety and extending shelf life. These processes eliminate harmful bacteria while maintaining the quality of dairy products. International buyers, especially from Africa and South America, should focus on energy-efficient machinery that can integrate seamlessly with their current operations. Additionally, understanding local regulations on dairy processing is critical for compliance and operational success.
Why Is Bakery Machinery Important for the Bakery Industry?
Bakery operations utilize specialized machinery, such as dough mixers and ovens, to enhance product quality and consistency. These machines allow for precise control over mixing and baking processes, which is essential for producing high-quality baked goods. Buyers from Europe, particularly Germany, should look for equipment that offers customization options to cater to various dough types and production scales, ensuring that their investment meets specific production needs.
What Are the Advantages of Food Processing Machinery in Fruit and Vegetable Processing?
In the fruit and vegetable processing sector, washing, peeling, and cutting machines significantly increase throughput while improving food safety standards. These machines help in efficiently preparing raw materials for further processing or packaging. For B2B buyers in regions like Africa and the Middle East, sourcing durable machinery that is easy to clean is essential to meet hygiene standards and maintain product quality throughout the processing stages.
Related Video: Industrial Cleaning: Food Processing Overview
3 Common User Pain Points for ‘Food Processing Machinery Manufacturers’ & Their Solutions
Scenario 1: Navigating Compliance and Regulatory Challenges in Food Processing
The Problem:
B2B buyers in the food processing industry often face significant challenges navigating the complex landscape of compliance and regulatory requirements. This is especially true for companies operating across international borders, such as those in Africa, South America, the Middle East, and Europe. Regulations regarding food safety, machinery standards, and environmental impact can vary dramatically by region. Buyers may struggle to ensure that the machinery they purchase meets the necessary certifications, leading to potential fines, production delays, and reputational damage if standards are not met.
The Solution:
To effectively navigate these compliance challenges, buyers should begin by conducting thorough research on the specific regulations relevant to their region and the countries they export to. Engaging with local industry associations can provide valuable insights and updates on regulatory changes. When sourcing food processing machinery, it is crucial to partner with manufacturers who have a proven track record of compliance and can provide detailed documentation of certifications. Buyers should ask for proof of compliance with international standards such as ISO 22000 for food safety management systems. Additionally, consider investing in machinery that offers built-in compliance features, such as safety sensors and automated reporting capabilities, which can streamline adherence to regulations. Regular training for staff on compliance standards is also essential, ensuring that everyone involved understands the importance of these regulations and how to maintain compliance effectively.
Scenario 2: Addressing High Maintenance Costs and Downtime
The Problem:
High maintenance costs and unexpected downtime are critical pain points for B2B buyers in the food processing sector. Manufacturers often rely on complex machinery that requires regular upkeep and may experience breakdowns due to heavy usage or lack of proper maintenance. This can lead to significant production halts, affecting supply chain efficiency and profitability. Buyers from regions with limited access to technical support may find it particularly challenging to manage these issues, resulting in lost revenue and trust from customers.
The Solution:
To mitigate maintenance costs and minimize downtime, buyers should consider investing in machinery that is designed for durability and ease of maintenance. Look for manufacturers that provide comprehensive maintenance plans, including warranty options and access to replacement parts. Establishing a preventive maintenance schedule can significantly reduce the likelihood of unexpected failures. Additionally, leveraging technology such as predictive maintenance tools that utilize IoT sensors can help monitor machinery performance in real-time, allowing for timely interventions before issues escalate. Buyers should also prioritize training for their operational staff on proper usage and maintenance procedures to ensure the machinery is operated efficiently and any minor issues are addressed proactively.
Scenario 3: Customization Needs and Scalability for Diverse Markets
The Problem:
Many B2B buyers in the food processing industry encounter the challenge of finding machinery that can be customized to meet specific production needs. As consumer preferences evolve and businesses expand into new markets, the ability to adapt machinery for different products and production volumes becomes crucial. Buyers may feel limited by one-size-fits-all solutions that do not accommodate the unique requirements of their operations, which can hinder growth and competitiveness.
The Solution:
To address customization needs, buyers should prioritize manufacturers that offer modular machinery solutions. This allows for easy upgrades and modifications as production demands change. Engaging in discussions with manufacturers about specific needs and potential customizations can lead to tailored solutions that enhance productivity. Buyers should also consider collaborating with manufacturers that provide flexible production lines capable of handling a variety of products, which is particularly beneficial for businesses targeting diverse markets. Building a strong relationship with the manufacturer can facilitate better communication and support for future scalability. Finally, conducting pilot tests with new machinery before full-scale implementation can help ensure that it meets the required specifications and functions well within the existing production environment.
Strategic Material Selection Guide for Food Processing Machinery Manufacturers
What Are the Key Properties of Stainless Steel in Food Processing Machinery?
Stainless steel is a widely used material in food processing machinery due to its excellent corrosion resistance, high strength, and ability to withstand extreme temperatures. It typically has a temperature rating of up to 800°C and can handle high-pressure environments, making it suitable for various applications. The most common grades used in food processing include 304 and 316 stainless steel, with the latter offering superior corrosion resistance, particularly against chlorides.
Pros & Cons of Stainless Steel:
– Advantages: Its durability ensures a long lifespan, reducing the need for frequent replacements. Stainless steel is also easy to clean, which is crucial for maintaining hygiene standards in food processing.
– Disadvantages: The initial cost can be higher compared to other materials, and manufacturing complexity can increase due to the need for specialized welding techniques.
Impact on Application: Stainless steel is compatible with a wide range of food products and is often used in equipment that processes acidic or salty foods.
Considerations for International Buyers: Compliance with standards such as ASTM and DIN is essential, especially in regions like Europe and Germany, where regulations are stringent. Buyers from Africa and South America should also consider local standards and availability of grades.
How Does Plastic Compare as a Material for Food Processing Machinery?
Plastic, particularly food-grade polymers like polyethylene and polypropylene, is another common material in food processing machinery. These materials are lightweight and can be molded into complex shapes, which can be beneficial for specific applications.
Pros & Cons of Plastic:
– Advantages: Plastics are generally lower in cost and can be produced in various colors and designs, which may appeal to branding efforts. They also offer good chemical resistance, especially against acids and bases.
– Disadvantages: Plastics may not withstand high temperatures or pressures as effectively as metals, limiting their use in certain applications. Their durability is also less than that of stainless steel.
Impact on Application: Plastics are suitable for non-heat applications and can be used in food storage and packaging equipment.
Considerations for International Buyers: Buyers should ensure that the plastic materials comply with food safety regulations in their respective regions, such as FDA compliance in the U.S. or EU regulations in Europe.
What Role Does Aluminum Play in Food Processing Machinery?
Aluminum is another material option for food processing machinery, known for its lightweight and good strength-to-weight ratio. It typically has a temperature rating of around 600°C, making it suitable for various applications.
Pros & Cons of Aluminum:
– Advantages: Aluminum is often more cost-effective than stainless steel and can be easily machined, allowing for complex designs. Its lightweight nature makes it easier to handle and install.
– Disadvantages: Aluminum is less corrosion-resistant than stainless steel, particularly in acidic environments, which can lead to a shorter lifespan in certain applications.
Impact on Application: Aluminum is commonly used in equipment that requires lightweight components, such as conveyor systems and packaging machines.
Considerations for International Buyers: Buyers should be aware of the specific grades of aluminum that are suitable for food processing and ensure compliance with relevant standards.
What Are the Benefits of Using Carbon Steel in Food Processing Machinery?
Carbon steel is less common but still relevant in specific food processing applications. It is known for its high strength and wear resistance but requires proper treatment to prevent corrosion.
Pros & Cons of Carbon Steel:
– Advantages: Carbon steel is generally more affordable than stainless steel and can be very durable when properly treated.
– Disadvantages: It is prone to rust and corrosion, especially when exposed to moisture, which can be a significant drawback in food processing environments.
Impact on Application: Carbon steel is often used in equipment that does not come into direct contact with food or in applications where high strength is required.
Considerations for International Buyers: Buyers should consider the need for protective coatings or treatments to enhance corrosion resistance and ensure compliance with local food safety standards.
Summary Table of Material Selection for Food Processing Machinery
Material | Typical Use Case for Food Processing Machinery Manufacturers | Key Advantage | Key Disadvantage/Limitation | Relative Cost (Low/Med/High) |
---|---|---|---|---|
Stainless Steel | Equipment for processing acidic or salty foods | Excellent durability and hygiene | Higher initial cost | High |
Plastic | Food storage and packaging equipment | Lightweight and cost-effective | Limited high-temperature use | Low |
Aluminum | Conveyor systems and lightweight components | Cost-effective and easy to machine | Less corrosion-resistant | Medium |
Carbon Steel | Non-food contact applications requiring high strength | Affordable and durable when treated | Prone to rust and corrosion | Low |
This strategic material selection guide provides key insights for international B2B buyers in the food processing machinery sector, helping them make informed decisions based on specific application needs and regional compliance standards.
In-depth Look: Manufacturing Processes and Quality Assurance for Food Processing Machinery Manufacturers
What Are the Key Stages in the Manufacturing Process of Food Processing Machinery?
Manufacturing food processing machinery involves several critical stages that ensure efficiency and quality. Understanding these stages can help B2B buyers from Africa, South America, the Middle East, and Europe make informed purchasing decisions.
Material Preparation: How Is the Right Material Chosen?
The first stage in the manufacturing process is material preparation. Manufacturers typically select materials based on durability, resistance to corrosion, and compliance with food safety standards. Common materials include stainless steel, which is favored for its non-reactive properties, and aluminum for lightweight applications.
B2B buyers should inquire about the source and quality of materials used, as well as any certifications that guarantee compliance with international standards. Suppliers should provide documentation that outlines material specifications, including traceability information.
Forming: What Techniques Are Used to Shape Machinery Components?
The forming stage involves various techniques to shape the materials into components. Common methods include:
- CNC Machining: Computer Numerical Control (CNC) machining is widely used for precision parts. It ensures that components meet exact specifications, reducing waste and enhancing efficiency.
- Injection Molding: This technique is often used for plastic components, allowing for complex shapes and designs with minimal waste.
- Welding and Fabrication: For joining metal parts, welding techniques such as TIG and MIG are employed. Fabrication processes may also include bending and cutting to achieve desired shapes.
Buyers should look for manufacturers that utilize advanced technologies in forming processes to ensure high-quality output.
Assembly: How Is Machinery Assembled for Optimal Performance?
The assembly stage is where individual components come together to form the complete machinery. This process can vary significantly depending on the complexity of the equipment.
- Modular Assembly: Many manufacturers adopt a modular approach, allowing for easier upgrades and repairs. This method can be particularly beneficial for B2B buyers who may need to adapt machinery to evolving production needs.
- Quality Control during Assembly: Implementing quality checks at this stage is crucial. Common practices include verifying the alignment of parts and ensuring proper fit.
B2B buyers should assess the assembly processes of potential suppliers, focusing on their ability to customize solutions to meet specific operational requirements.
Finishing: What Finishing Techniques Ensure Quality and Durability?
Finishing processes enhance the appearance and durability of food processing machinery. Techniques may include:
- Surface Treatment: Processes like anodizing or passivation are used to improve corrosion resistance.
- Painting and Coating: Applying protective coatings can prevent wear and enhance the longevity of machinery, particularly in harsh environments.
When evaluating suppliers, buyers should request information on finishing processes to ensure that the machinery will withstand the rigors of food processing.
What Quality Assurance Practices Should B2B Buyers Expect from Food Processing Machinery Manufacturers?
Quality assurance (QA) is essential in the manufacturing of food processing machinery, as it directly impacts performance and safety. Here are some key QA practices that international B2B buyers should consider:
Which International Standards Should Manufacturers Comply With?
International standards play a crucial role in ensuring the quality and safety of food processing machinery. Key standards include:
- ISO 9001: This standard outlines criteria for a quality management system and is applicable to any organization, regardless of its size or industry. Compliance indicates that a manufacturer has a systematic approach to managing quality.
- CE Marking: Particularly relevant for European buyers, CE marking signifies that a product meets EU safety, health, and environmental protection requirements.
- API Standards: For machinery involved in processing oils or fats, adherence to American Petroleum Institute (API) standards is essential.
B2B buyers should verify that potential suppliers are certified and compliant with these standards.
What Quality Control Checkpoints Should Buyers Expect?
Quality control checkpoints throughout the manufacturing process ensure that products meet specified standards. Common checkpoints include:
- Incoming Quality Control (IQC): This initial stage checks raw materials for compliance with quality standards before production begins.
- In-Process Quality Control (IPQC): Conducted during the manufacturing process, this stage involves monitoring operations and conducting tests to identify defects early.
- Final Quality Control (FQC): This final inspection ensures that the completed machinery meets all specifications before delivery.
Buyers should inquire about the specific QC processes and documentation that suppliers maintain at each stage.
Which Testing Methods Are Commonly Used in Quality Assurance?
Testing methods are crucial for validating the performance and safety of food processing machinery. Common methods include:
- Functional Testing: Ensures that machinery operates as intended under normal operating conditions.
- Stress Testing: Evaluates how machinery performs under extreme conditions to assess durability and reliability.
- Hygiene Testing: Particularly relevant for food processing, this testing checks for contamination and compliance with food safety standards.
B2B buyers should request detailed reports on testing methods used by suppliers to ensure comprehensive quality assurance.
How Can B2B Buyers Verify Supplier Quality Control?
Verifying a supplier’s quality control processes is vital for mitigating risks associated with procurement. Here are actionable steps B2B buyers can take:
What Role Do Audits Play in Supplier Quality Assurance?
Conducting regular audits of potential suppliers helps buyers assess compliance with quality standards and operational practices. Audits can be:
- Internal Audits: Suppliers may conduct their own audits to ensure adherence to quality processes.
- External Audits: Buyers can engage third-party firms to perform independent audits, providing an unbiased assessment of a supplier’s capabilities.
How Can Buyers Utilize Reports and Third-Party Inspections?
Buyers should request access to quality control reports and documentation from suppliers. This includes:
- Test Reports: Detailed results from functional, stress, and hygiene tests should be provided.
- Certification Documents: Proof of compliance with international standards like ISO 9001 and CE marking should be readily available.
Engaging third-party inspection services can further validate supplier claims and ensure that machinery meets buyer specifications.
What Are the Unique Quality Control Considerations for International B2B Buyers?
For international B2B buyers, especially from diverse regions like Africa, South America, the Middle East, and Europe, understanding regional regulations and standards is crucial.
- Cultural and Regulatory Differences: Buyers must navigate varying quality standards and regulations in different countries. Familiarizing themselves with local requirements will help in selecting compliant suppliers.
- Logistics and Supply Chain Factors: Transporting machinery across borders can introduce additional risks. Buyers should ensure that suppliers have robust logistics and supply chain management practices to mitigate potential delays or damages.
By thoroughly understanding manufacturing processes and quality assurance practices, B2B buyers can make informed decisions that align with their operational needs and regulatory requirements.
Practical Sourcing Guide: A Step-by-Step Checklist for ‘Food Processing Machinery Manufacturers’
In the competitive landscape of food processing machinery procurement, international B2B buyers must navigate a complex array of options and considerations. This practical sourcing guide serves as a step-by-step checklist to ensure informed decision-making when selecting food processing machinery manufacturers.
Step 1: Define Your Technical Specifications
Establishing clear technical specifications is crucial for aligning supplier capabilities with your operational needs. Consider factors such as production capacity, machine dimensions, and energy efficiency. Make sure to include any industry-specific requirements, such as compliance with food safety regulations, to avoid costly mistakes later.
Step 2: Conduct Market Research
Understanding the market landscape helps identify potential suppliers and their offerings. Utilize industry reports, trade publications, and online resources to gather insights on leading manufacturers in your region of interest, whether it’s Africa, South America, the Middle East, or Europe. Focus on aspects like market share, innovation trends, and customer reviews to gauge supplier reputation.
Step 3: Evaluate Potential Suppliers
Before committing, it’s essential to vet suppliers thoroughly. Request company profiles, case studies, and references from buyers in a similar industry or region. Look for suppliers who demonstrate a strong track record of reliability and quality; don’t just rely on their website claims.
- Considerations:
- Ask for third-party certifications (e.g., ISO, CE) to ensure compliance with international standards.
- Investigate their customer service and support capabilities, as ongoing maintenance may be required.
Step 4: Request and Compare Quotes
Once you have a shortlist of suppliers, request detailed quotes that outline pricing, delivery timelines, and warranty terms. Comparing these quotes side by side will reveal not only the best price but also the value offered by each supplier. Pay attention to hidden costs, such as shipping fees and potential import duties, especially when dealing with international suppliers.
Step 5: Assess After-Sales Support and Service
The relationship with your supplier should extend beyond the initial purchase. Evaluate the after-sales support, including installation assistance, training for your staff, and availability of spare parts. Reliable after-sales support ensures that your machinery operates efficiently and minimizes downtime.
- Key Questions:
- What is the supplier’s response time for service requests?
- Are there training programs available for your team?
Step 6: Verify Compliance with Local Regulations
Ensure that the machinery complies with local regulations and standards in your country or region. This is particularly important in the food processing industry, where health and safety regulations are stringent. Non-compliance can lead to legal issues and product recalls, impacting your business reputation.
Step 7: Negotiate Terms and Finalize the Contract
Once you have selected a supplier, engage in negotiations to finalize the terms of the contract. Discuss payment terms, delivery schedules, and any other critical aspects that impact your operations. A well-negotiated contract can protect your interests and clarify expectations for both parties.
By following this step-by-step checklist, international B2B buyers can make informed decisions when sourcing food processing machinery, ultimately leading to successful partnerships and enhanced operational efficiency.
Comprehensive Cost and Pricing Analysis for Food Processing Machinery Manufacturers Sourcing
What Are the Key Cost Components in Food Processing Machinery Manufacturing?
When sourcing food processing machinery, understanding the cost structure is essential for B2B buyers. The primary cost components include:
-
Materials: The quality and type of materials used directly influence the cost. For instance, stainless steel is commonly used for its durability and hygiene properties but may come at a premium compared to other materials.
-
Labor: Labor costs can vary significantly based on location. Manufacturers in regions with higher wage standards, such as Europe, may face increased labor costs compared to those in Africa or South America.
-
Manufacturing Overhead: This encompasses the indirect costs of production, such as utilities, rent, and administrative expenses. Efficient manufacturers aim to minimize overhead to offer competitive pricing.
-
Tooling: The cost of tooling can be substantial, especially for custom machinery. Investments in high-quality tooling may lead to better production efficiency and quality.
-
Quality Control (QC): Implementing robust QC processes ensures that the machinery meets industry standards and buyer specifications. This can add to the cost but is essential for long-term reliability.
-
Logistics: Shipping costs can be significant, particularly for international buyers. Factors such as distance, shipping mode, and regulatory compliance can influence logistics expenses.
-
Margin: Manufacturers typically mark up costs to achieve a profit margin. Understanding this markup can help buyers negotiate better prices.
How Do Pricing Influencers Affect Food Processing Machinery Costs?
Several factors can influence the pricing of food processing machinery, including:
-
Volume and Minimum Order Quantity (MOQ): Larger orders often lead to discounted pricing. Buyers should assess their needs and consider bulk purchasing to reduce per-unit costs.
-
Specifications and Customization: Custom-built machinery tailored to specific processes may incur higher costs. Clear communication of requirements can help avoid unnecessary expenses.
-
Materials and Quality Certifications: Machinery that meets international quality standards, such as ISO certifications, may be priced higher. Buyers should weigh the benefits of certification against the costs.
-
Supplier Factors: The reliability and reputation of the supplier can impact pricing. Established manufacturers with proven track records may charge a premium for their services.
-
Incoterms: Understanding Incoterms (International Commercial Terms) is crucial as they define the responsibilities of buyers and sellers regarding shipping, insurance, and tariffs. This knowledge can help buyers avoid unexpected costs.
What Are the Best Practices for Negotiating Prices in Food Processing Machinery Procurement?
International B2B buyers should employ several strategies to ensure cost-efficiency:
-
Conduct Thorough Market Research: Understand the average pricing for the machinery you need. This knowledge equips you for effective negotiation and helps identify fair pricing.
-
Evaluate Total Cost of Ownership (TCO): Consider not just the purchase price but also installation, maintenance, and operational costs. This holistic view can reveal hidden costs associated with cheaper machinery.
-
Leverage Relationships with Suppliers: Building strong relationships with suppliers can lead to better pricing and terms. Long-term partnerships often yield benefits such as discounts and priority service.
-
Negotiate for Transparency: Request a breakdown of costs from suppliers. Understanding how pricing is structured can help identify areas for negotiation.
-
Be Aware of Pricing Nuances in International Markets: Different regions may have varying pricing structures due to local market conditions, tariffs, and demand levels. Buyers from Africa, South America, the Middle East, and Europe should tailor their negotiation strategies to these factors.
Conclusion
Navigating the costs and pricing of food processing machinery requires a comprehensive understanding of various components and influences. By employing strategic negotiation techniques and considering the total cost of ownership, international B2B buyers can make informed decisions that optimize their procurement process. Always remember that indicative prices may fluctuate based on market conditions and specific requirements.
Alternatives Analysis: Comparing Food Processing Machinery Manufacturers With Other Solutions
When considering food processing, international B2B buyers must evaluate various solutions available in the market. While food processing machinery manufacturers offer specialized equipment tailored for efficiency and productivity, alternative methods and technologies may also achieve similar goals. This analysis aims to provide a comprehensive comparison of food processing machinery against two viable alternatives: manual processing techniques and outsourcing to third-party processors.
Comparison Table of Food Processing Solutions
Comparison Aspect | Food Processing Machinery Manufacturers | Manual Processing Techniques | Outsourcing to Third-Party Processors |
---|---|---|---|
Performance | High efficiency, consistent output | Variable efficiency, labor-dependent | High efficiency, but dependent on vendor capabilities |
Cost | High initial investment, low operating costs | Low initial cost, high labor costs | Moderate to high costs, depending on contract terms |
Ease of Implementation | Requires training and setup | Simple, requires skilled labor | Quick implementation, dependent on vendor availability |
Maintenance | Regular maintenance required | Minimal maintenance needed | No maintenance responsibility for buyer |
Best Use Case | Large-scale production, standardized output | Small-scale, artisanal production | Businesses lacking in-house processing capabilities |
What Are the Pros and Cons of Manual Processing Techniques?
Manual processing techniques involve human labor to perform food preparation and processing tasks.
Pros:
– Low Initial Investment: Setting up manual processing requires minimal upfront costs compared to purchasing machinery.
– Flexibility: Artisanal producers can easily adapt processes to accommodate specific customer requests or seasonal ingredients.
Cons:
– Labor-Intensive: This method relies heavily on skilled labor, which can be a limiting factor in scalability.
– Inconsistent Quality: Variability in labor can lead to inconsistent product quality, affecting customer satisfaction.
How Does Outsourcing to Third-Party Processors Compare?
Outsourcing food processing to third-party companies can provide businesses with an efficient alternative to in-house processing.
Pros:
– Cost-Effective for Small Businesses: For small to medium enterprises, outsourcing eliminates the need for capital investment in machinery and infrastructure.
– Focus on Core Competencies: Companies can concentrate on their primary business activities, leaving food processing to specialized providers.
Cons:
– Quality Control Issues: Relying on external vendors may result in a loss of control over product quality and consistency.
– Dependency on Vendor: Businesses become reliant on third-party processors’ capabilities and timelines, which may lead to delays or supply chain disruptions.
How Can B2B Buyers Choose the Right Food Processing Solution?
Choosing the right solution for food processing hinges on various factors, including the scale of production, budget constraints, and specific operational needs. B2B buyers from regions like Africa, South America, the Middle East, and Europe should first assess their production volumes and target markets. If large-scale production is a priority, investing in food processing machinery may be the best approach. However, for businesses looking to maintain flexibility or lower initial costs, manual processing or outsourcing could be more appropriate. Ultimately, it is vital to conduct thorough market research and consider long-term implications to make an informed decision that aligns with business objectives.
Essential Technical Properties and Trade Terminology for Food Processing Machinery Manufacturers
What Are the Key Technical Properties of Food Processing Machinery?
Understanding the essential technical properties of food processing machinery is critical for B2B buyers, particularly in diverse markets like Africa, South America, the Middle East, and Europe. Here are some of the most important specifications to consider:
1. Material Grade: Why Is It Crucial for Food Safety?
The material grade of machinery used in food processing directly impacts food safety and product quality. Common materials include stainless steel, which is preferred for its resistance to corrosion and ability to withstand rigorous cleaning processes. Buyers should ensure that machinery meets food-grade standards, such as FDA or EU regulations, to avoid contamination and ensure compliance with health regulations.
2. Tolerance Levels: How Do They Affect Product Consistency?
Tolerance levels refer to the acceptable variations in dimensions during manufacturing. In food processing, precise tolerances are vital for ensuring product consistency, minimizing waste, and maintaining operational efficiency. Machinery with tight tolerances can significantly reduce the risk of defects, leading to improved product quality and customer satisfaction.
3. Power Consumption: Why Should Buyers Care?
Power consumption is an essential specification that affects operational costs. Machinery that is energy-efficient can lead to significant savings over time, especially for large-scale operations. Buyers should look for equipment with energy-efficient ratings and technologies that optimize power usage without compromising performance.
4. Processing Capacity: How to Match Machinery to Production Needs?
Processing capacity indicates the volume of food that can be processed within a given time frame. For B2B buyers, understanding their production requirements is crucial. Machinery that aligns with production needs can enhance workflow efficiency and prevent bottlenecks, ensuring that businesses can meet market demands effectively.
5. Maintenance Requirements: What to Consider for Long-Term Operation?
The ease of maintenance is another critical property. Machinery that is designed for easy access to components can reduce downtime and maintenance costs. Buyers should evaluate the manufacturer’s guidelines for maintenance frequency and the availability of spare parts to ensure that operations remain uninterrupted.
What Are Common Trade Terms in the Food Processing Machinery Industry?
Familiarity with industry jargon is essential for effective communication and negotiation in B2B transactions. Here are some common terms:
1. OEM (Original Equipment Manufacturer): What Does It Mean for Buyers?
OEM refers to companies that produce parts and equipment that may be marketed by another manufacturer. For buyers, sourcing from OEMs can ensure high-quality components that meet specific industry standards, which is particularly important for machinery reliability and performance.
2. MOQ (Minimum Order Quantity): How Does It Affect Purchasing Decisions?
MOQ is the smallest number of units a supplier is willing to sell. Understanding MOQ is vital for buyers to ensure that they can meet their production needs without overcommitting financially. It can also influence negotiations, especially for smaller companies looking to enter the market.
3. RFQ (Request for Quotation): Why Is It Essential in Sourcing?
An RFQ is a document sent to suppliers to request pricing and terms for specific products or services. For buyers, issuing an RFQ allows for comparing offers from different suppliers, helping them make informed decisions based on price, quality, and delivery terms.
4. Incoterms (International Commercial Terms): How Do They Simplify Trade?
Incoterms are a series of pre-defined commercial terms that clarify the responsibilities of buyers and sellers in international transactions. Understanding these terms helps buyers navigate shipping, insurance, and delivery obligations, reducing misunderstandings and potential disputes in cross-border transactions.
5. Lead Time: What Should Buyers Expect?
Lead time refers to the time it takes from placing an order to receiving the goods. For B2B buyers, knowing the lead time is crucial for planning production schedules and inventory management. Suppliers that can provide shorter lead times can help businesses respond more quickly to market demands.
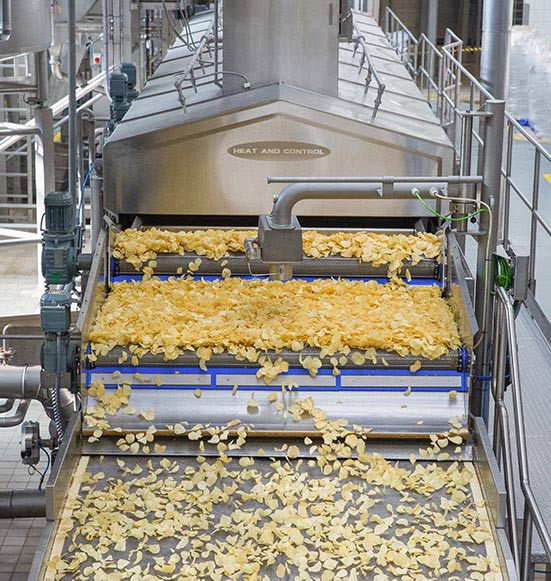
A stock image related to Food Processing Machinery Manufacturers.
By mastering these technical specifications and trade terms, B2B buyers can make informed decisions, ensuring they invest in machinery that meets their operational requirements while navigating the complexities of international trade effectively.
Navigating Market Dynamics and Sourcing Trends in the Food Processing Machinery Manufacturers Sector
What Are the Current Market Dynamics and Key Trends Affecting Food Processing Machinery Manufacturers?
The food processing machinery sector is experiencing significant transformation driven by several global factors. The increasing demand for processed foods, fueled by urbanization and changing consumer lifestyles, is pushing manufacturers to innovate and enhance production capabilities. In Africa and South America, the growing middle class is shifting preferences towards convenient and packaged food products, creating opportunities for machinery manufacturers to cater to these markets. In Europe, stricter food safety regulations and sustainability initiatives are encouraging the adoption of advanced technologies.
Emerging technologies such as automation, Internet of Things (IoT), and artificial intelligence (AI) are reshaping the landscape. These innovations enable manufacturers to improve efficiency, reduce downtime, and enhance product quality. For B2B buyers, understanding these tech trends is crucial for selecting machinery that not only meets current operational needs but is also adaptable to future requirements. Additionally, the rise of Industry 4.0 is prompting companies to invest in smart factories, where interconnected systems optimize production processes and enhance supply chain visibility.
Another key trend is the focus on local sourcing and shorter supply chains. International buyers are increasingly looking for manufacturers who can provide reliable, high-quality machinery with reduced lead times. This trend is particularly relevant for buyers in the Middle East, where geopolitical factors may affect supply chain stability. As a result, manufacturers are investing in regional partnerships and localized production to mitigate risks and enhance responsiveness to market demands.
How Is Sustainability Shaping the Sourcing Strategies of Food Processing Machinery Manufacturers?
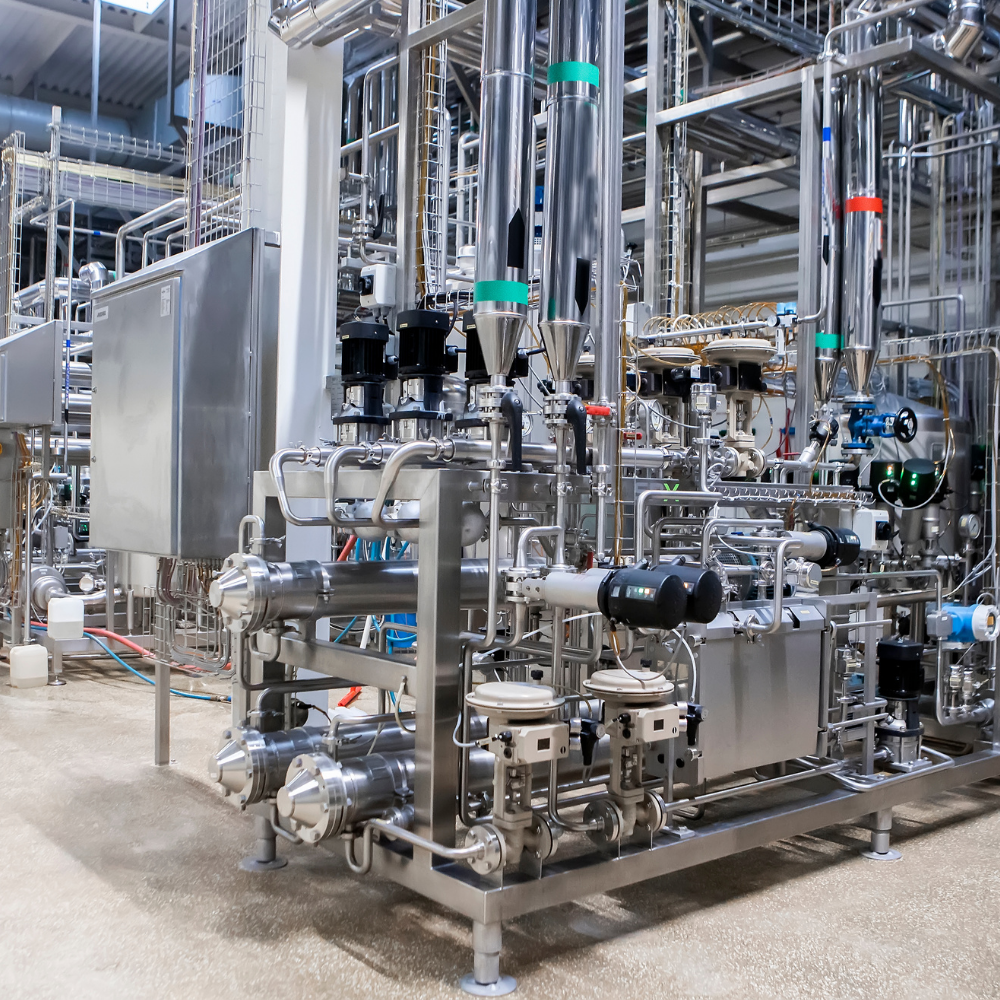
A stock image related to Food Processing Machinery Manufacturers.
Sustainability has become a pivotal consideration for B2B buyers in the food processing machinery sector. The environmental impact of manufacturing processes is under scrutiny, and companies are increasingly held accountable for their carbon footprints. This shift is prompting manufacturers to adopt sustainable practices, such as using energy-efficient machinery and sourcing renewable materials.
Ethical sourcing is equally important, with buyers prioritizing suppliers who demonstrate a commitment to sustainable practices. Certifications such as ISO 14001 for environmental management and specific ‘green’ certifications for machinery can serve as indicators of a manufacturer’s dedication to sustainability. B2B buyers should look for manufacturers that not only comply with these standards but also actively promote transparency in their supply chains.
Moreover, the concept of circular economy is gaining traction, encouraging manufacturers to design machinery that is not only efficient but also recyclable and repairable. This shift towards sustainable design can lead to long-term cost savings for buyers, as machinery with a longer lifespan reduces the need for frequent replacements. For international buyers, particularly those from Europe, aligning purchasing decisions with sustainability goals can enhance brand reputation and customer loyalty.
What Has Been the Evolution of Food Processing Machinery Manufacturers?
The food processing machinery sector has evolved significantly over the past century. Initially characterized by manual labor and rudimentary tools, the industry began to transform in the early 20th century with the introduction of mechanization. This period saw the advent of assembly lines and standardized processes, which significantly increased production capacity and efficiency.
The latter half of the century brought technological advancements, including the integration of electronics and automation, which revolutionized manufacturing practices. Today, the sector is witnessing the rise of smart technologies and digital solutions, making it essential for B2B buyers to understand this evolution. By recognizing the historical context and technological trajectory, buyers can make informed decisions about the machinery that best aligns with their operational strategies and future growth plans.
Frequently Asked Questions (FAQs) for B2B Buyers of Food Processing Machinery Manufacturers
-
How do I evaluate food processing machinery manufacturers for quality and reliability?
To assess the quality and reliability of food processing machinery manufacturers, begin by reviewing their certifications, such as ISO 9001, which ensures adherence to quality management standards. Check for customer testimonials and case studies that highlight their success with similar projects. Additionally, inquire about their after-sales support, warranty terms, and maintenance services. Engaging in direct communication with the manufacturer can also provide insights into their responsiveness and commitment to customer satisfaction. -
What are the key factors to consider when selecting food processing equipment?
When selecting food processing equipment, consider factors such as the type of food products you will process, production volume requirements, and the specific processes involved (e.g., mixing, cooking, packaging). Evaluate the machine’s efficiency, energy consumption, and ease of maintenance. Customization options are also crucial—ensure that the equipment can be tailored to your specific needs. Lastly, consider the manufacturer’s reputation and their ability to provide support and training for your team. -
What customization options are available for food processing machinery?
Many food processing machinery manufacturers offer customization options to meet specific production needs. This may include altering machine sizes, modifying processing speeds, or integrating additional features such as automated controls or specialized feeding systems. Discuss your requirements with potential suppliers to determine their capabilities. Customization can significantly enhance operational efficiency and product quality, making it a vital consideration for B2B buyers. -
What is the minimum order quantity (MOQ) for food processing machinery?
The minimum order quantity (MOQ) for food processing machinery can vary significantly between manufacturers and types of equipment. Some suppliers may have a low MOQ for standard machines, while custom-built equipment may require larger orders. It’s essential to clarify the MOQ during your discussions with manufacturers to ensure it aligns with your production needs and budget. Additionally, consider the potential for bulk purchasing discounts, which can enhance cost-effectiveness. -
What payment terms should I expect when dealing with food processing machinery manufacturers?
Payment terms with food processing machinery manufacturers can differ widely. Common arrangements include upfront deposits, progress payments during production, and final payments upon delivery. It is crucial to negotiate terms that suit your cash flow and financial planning. Some manufacturers may also offer financing options or flexible payment plans, especially for larger orders. Always ensure that payment terms are documented in the contract to avoid misunderstandings. -
How can I ensure quality assurance (QA) during the machinery procurement process?
Ensuring quality assurance during the procurement process involves several steps. First, conduct a thorough supplier audit, assessing their manufacturing processes and quality control protocols. Request documentation of their QA processes, including inspection reports and compliance with industry standards. Additionally, consider arranging a factory visit to observe production firsthand. Finally, establish clear acceptance criteria for the equipment before shipment to ensure it meets your specifications. -
What logistics considerations should I keep in mind when importing food processing machinery?
When importing food processing machinery, logistics considerations include shipping methods, freight costs, and customs regulations. Determine whether you prefer sea freight for cost-effectiveness or air freight for speed. Ensure you understand the import duties and taxes applicable in your region, as these can significantly affect your total costs. Partnering with a logistics provider experienced in handling machinery can help streamline the process and ensure compliance with all regulations. -
How can I build a long-term relationship with food processing machinery suppliers?
Building a long-term relationship with food processing machinery suppliers involves consistent communication and collaboration. Start by clearly articulating your needs and expectations, fostering transparency from the outset. Regularly provide feedback on equipment performance and service quality to help suppliers improve. Additionally, consider engaging them in your future projects, and explore opportunities for joint ventures or exclusive partnerships. A mutually beneficial relationship can lead to better pricing, priority service, and collaborative innovation over time.
Important Disclaimer & Terms of Use
⚠️ Important Disclaimer
The information provided in this guide, including content regarding manufacturers, technical specifications, and market analysis, is for informational and educational purposes only. It does not constitute professional procurement advice, financial advice, or legal advice.
While we have made every effort to ensure the accuracy and timeliness of the information, we are not responsible for any errors, omissions, or outdated information. Market conditions, company details, and technical standards are subject to change.
B2B buyers must conduct their own independent and thorough due diligence before making any purchasing decisions. This includes contacting suppliers directly, verifying certifications, requesting samples, and seeking professional consultation. The risk of relying on any information in this guide is borne solely by the reader.
Strategic Sourcing Conclusion and Outlook for Food Processing Machinery Manufacturers
In today’s competitive landscape, strategic sourcing is paramount for food processing machinery manufacturers aiming to optimize their supply chains and enhance operational efficiency. By understanding the specific needs of their markets—whether in Africa, South America, the Middle East, or Europe—businesses can forge partnerships that not only lower costs but also improve product quality and innovation.
How Can International Buyers Leverage Strategic Sourcing?
International buyers should focus on establishing long-term relationships with reliable suppliers who understand regional market dynamics and regulatory requirements. Implementing a data-driven approach to sourcing can help businesses identify the best suppliers, manage risks, and ensure compliance with local standards. Additionally, investing in technology and automation can streamline procurement processes, leading to faster turnaround times and reduced operational costs.
What Is the Future of Food Processing Machinery Sourcing?
Looking ahead, the food processing industry is poised for transformation driven by technological advancements and sustainability concerns. Buyers should stay informed about emerging trends, such as plant-based processing technologies and eco-friendly machinery, to remain competitive. As the global market continues to evolve, proactive sourcing strategies will be essential for capitalizing on new opportunities and mitigating challenges.
In conclusion, international B2B buyers are encouraged to embrace strategic sourcing as a critical component of their procurement strategies. By doing so, they can not only enhance their supply chain resilience but also position themselves for future growth in an increasingly interconnected marketplace.