Discover Top HDPE Manufacturers: A Complete Sourcing Guide (2025)
Introduction: Navigating the Global Market for HDPE Manufacturers
Navigating the intricate landscape of sourcing high-density polyethylene (HDPE) manufacturers can pose significant challenges for international B2B buyers, especially in diverse markets such as Africa, South America, the Middle East, and Europe. With the growing demand for HDPE across various applications—from packaging and construction to automotive and consumer goods—understanding the nuances of this market becomes essential. This guide serves as a comprehensive resource, offering insights into the types of HDPE products available, their myriad applications, and the critical factors to consider when vetting suppliers.
International buyers often grapple with issues such as fluctuating prices, varying quality standards, and supply chain complexities. This guide empowers you to make informed purchasing decisions by providing detailed information on cost structures, supplier vetting processes, and industry trends. Additionally, it addresses the unique challenges faced by businesses in different regions, ensuring that you can navigate the global market effectively.
By the end of this guide, you will have a robust framework to evaluate potential HDPE manufacturers, allowing you to forge partnerships that meet your operational needs and enhance your competitive edge. Whether you are a buyer in the UK looking for reliable suppliers or a Colombian enterprise seeking quality materials, this resource is designed to facilitate your journey in the HDPE market.
Understanding HDPE Manufacturers Types and Variations
Type Name | Key Distinguishing Features | Primary B2B Applications | Brief Pros & Cons for Buyers |
---|---|---|---|
General Purpose HDPE | Versatile, good impact resistance, and chemical stability | Packaging, construction, and agriculture | Pros: Cost-effective, widely available. Cons: May not be suitable for high-temperature applications. |
High-Density Polyethylene (HDPE) Pipe Manufacturers | Specializes in producing HDPE pipes for various industries | Water distribution, sewage systems, irrigation | Pros: Durable and resistant to corrosion. Cons: Higher initial cost compared to alternatives. |
HDPE Blow Molding Manufacturers | Focus on blow molding processes for creating containers | Bottles, tanks, and industrial containers | Pros: Efficient production of complex shapes. Cons: Limited to hollow products. |
Recycled HDPE Manufacturers | Utilize post-consumer recycled HDPE materials | Sustainable packaging, construction materials | Pros: Eco-friendly, cost savings on raw materials. Cons: Quality may vary based on the source of recycled material. |
HDPE Film Manufacturers | Specialize in producing HDPE films and sheets | Packaging, agriculture (e.g., greenhouse covers) | Pros: Lightweight and flexible. Cons: Less durable than rigid HDPE products. |
What Are the Characteristics of General Purpose HDPE Manufacturers?
General Purpose HDPE manufacturers produce a highly versatile polymer that is widely used across multiple industries. This type of HDPE offers excellent impact resistance and chemical stability, making it suitable for applications ranging from packaging to construction. B2B buyers should consider the cost-effectiveness and broad availability of these products, but may need to assess their suitability for high-temperature environments, as general-purpose HDPE can become less effective under extreme conditions.
Why Choose HDPE Pipe Manufacturers for Infrastructure Projects?
HDPE Pipe Manufacturers focus on creating durable and corrosion-resistant pipes that are essential for water distribution, sewage systems, and irrigation projects. These manufacturers utilize advanced techniques to ensure the pipes meet stringent quality standards. B2B buyers should weigh the higher initial costs against the long-term benefits of reduced maintenance and replacement needs, making HDPE pipes a wise investment for infrastructure projects.
How Do HDPE Blow Molding Manufacturers Operate?
HDPE Blow Molding Manufacturers specialize in producing hollow containers through a blow molding process. This technique allows for the efficient creation of complex shapes, making it ideal for bottles, tanks, and industrial containers. For B2B buyers, the advantages include quick production times and design flexibility. However, it’s important to note that this method is limited to hollow products, which may restrict application options.
What Are the Benefits of Working with Recycled HDPE Manufacturers?
Recycled HDPE Manufacturers focus on utilizing post-consumer materials to create new products, catering to the growing demand for sustainable solutions. This type of manufacturing supports eco-friendly initiatives while offering cost savings on raw materials. B2B buyers should consider the variability in quality based on the source of recycled material, as this can affect the performance and reliability of the end products.
What Should B2B Buyers Know About HDPE Film Manufacturers?
HDPE Film Manufacturers produce lightweight and flexible films that are widely used in packaging and agricultural applications, such as greenhouse covers. These films offer excellent moisture barriers and UV resistance. Buyers should appreciate the efficiency and adaptability of HDPE films but also be aware that they may not offer the same durability as rigid HDPE products, which could limit their application in more demanding environments.
Related Video: HDPE Electrofusion & Butt welding for drainage pipes & fittings
Key Industrial Applications of HDPE Manufacturers
Industry/Sector | Specific Application of HDPE Manufacturers | Value/Benefit for the Business | Key Sourcing Considerations for this Application |
---|---|---|---|
Packaging | Production of HDPE containers and bottles | Lightweight, durable, and recyclable packaging solutions | Quality of material, compliance with food safety regulations, cost-effectiveness |
Construction | Use in piping systems and geomembranes | High resistance to chemicals and environmental stressors | Specifications for pressure ratings, environmental certifications, availability of sizes |
Automotive | Manufacturing of fuel tanks and interior components | Enhanced safety and durability, lightweight for fuel efficiency | Material strength standards, compatibility with existing systems, supplier reliability |
Agriculture | Production of irrigation pipes and agricultural films | Improved water efficiency and crop yield | UV resistance, customization options, local regulations on agricultural materials |
Healthcare | Creation of medical devices and containers | Sterile, safe, and durable materials for medical applications | Compliance with healthcare regulations, sourcing from certified manufacturers, traceability of materials |
How is HDPE Used in the Packaging Industry?
In the packaging sector, HDPE is predominantly utilized for manufacturing containers and bottles due to its lightweight and durable characteristics. This material is ideal for a variety of products, including food and beverages, as it is resistant to impact and can be recycled, aligning with sustainable practices. International buyers, particularly from regions like Africa and South America, should prioritize suppliers who meet stringent food safety regulations and can offer cost-effective solutions while maintaining high quality.
What are the Applications of HDPE in Construction?
HDPE’s application in construction primarily revolves around piping systems and geomembranes, which are crucial for water management and environmental protection. Its resistance to chemicals and environmental stressors makes it a preferred choice for underground installations. Buyers in Europe and the Middle East must consider specifications such as pressure ratings and the availability of various sizes, ensuring that the materials meet local building codes and environmental standards.
How Does HDPE Benefit the Automotive Industry?
In the automotive industry, HDPE is used for manufacturing fuel tanks and various interior components. Its lightweight nature contributes to fuel efficiency, while its durability enhances safety. B2B buyers from Europe, particularly in countries like the UK, should focus on suppliers who can meet specific material strength standards and ensure compatibility with existing automotive systems to avoid costly modifications.
Why is HDPE Important in Agriculture?
HDPE plays a vital role in agriculture through the production of irrigation pipes and agricultural films. These applications enhance water efficiency and contribute to higher crop yields, making them essential for sustainable farming practices. Buyers from regions like South America should look for HDPE products that offer UV resistance and customization options to suit local agricultural practices and regulations.
How is HDPE Utilized in Healthcare?
In the healthcare sector, HDPE is utilized for creating medical devices and containers that require sterile and durable materials. Its compliance with healthcare regulations ensures safety in medical applications. International buyers must source from certified manufacturers who can provide traceability of materials, thereby ensuring adherence to stringent healthcare standards, particularly in the Middle East and Europe where regulatory compliance is critical.
Related Video: Knack Packaging – Manufacturers & Exporters of HDPE/PP Woven Sacks & BOPP Laminated PP Woven Bags.
3 Common User Pain Points for ‘HDPE Manufacturers’ & Their Solutions
Scenario 1: Difficulty in Sourcing Quality HDPE Materials
The Problem:
B2B buyers often face challenges in sourcing high-quality HDPE materials that meet specific industry standards. This is particularly true for businesses in Africa and South America, where local suppliers may not always provide the consistency or quality required for critical applications such as construction and packaging. Furthermore, buyers may encounter issues with suppliers who do not comply with international quality certifications, leading to delays and potential project failures.
The Solution:
To overcome sourcing challenges, buyers should prioritize establishing relationships with reputable, certified HDPE manufacturers who have a proven track record in their respective industries. It is essential to conduct thorough due diligence by reviewing suppliers’ certifications (such as ISO 9001), customer testimonials, and past project portfolios. Engaging in direct communication with manufacturers can also clarify their production capabilities and quality control measures. For those in regions with limited local options, utilizing online platforms that connect buyers with verified manufacturers can be advantageous. Ensuring that the selected supplier can provide samples and detailed product specifications before committing to large orders can further mitigate risks associated with quality inconsistencies.
Scenario 2: Navigating Price Fluctuations in HDPE Products
The Problem:
Price volatility is a significant pain point for B2B buyers of HDPE products, especially in regions like the Middle East and Europe, where market conditions can change rapidly due to geopolitical factors and supply chain disruptions. This unpredictability makes it difficult for companies to budget accurately and can lead to unexpected costs that affect overall project profitability.
The Solution:
To navigate price fluctuations effectively, buyers should consider implementing long-term contracts with their HDPE suppliers. Establishing fixed pricing agreements can provide stability and predictability in costs, allowing for better financial planning. Additionally, buyers should monitor market trends and have contingency plans in place, such as identifying alternative suppliers or materials that could be used in case of price surges. Engaging with suppliers who offer price-lock options or who can provide insights on market forecasts can further enhance a buyer’s ability to manage costs effectively.
Scenario 3: Ensuring Compliance with Regulatory Standards
The Problem:
International B2B buyers often struggle with ensuring that the HDPE products they procure meet the regulatory standards of their respective markets. For instance, buyers in Europe must comply with stringent environmental regulations such as REACH and RoHS, while those in Africa may face different local compliance requirements. Failing to meet these standards can result in costly fines, delays, or product recalls.
The Solution:
To ensure compliance, buyers should work closely with manufacturers that have a deep understanding of regulatory requirements across different regions. It is crucial to ask for documentation that verifies compliance with local and international standards, including safety data sheets (SDS) and product certifications. Buyers should also consider conducting regular audits of their suppliers to ensure ongoing compliance with regulations. Additionally, staying informed about changes in regulatory standards through industry associations and participating in relevant workshops can help buyers preemptively adjust their procurement strategies to remain compliant. By building a collaborative relationship with their suppliers, buyers can better navigate the complexities of regulatory compliance, ensuring that their procurement processes are both efficient and compliant.
Strategic Material Selection Guide for HDPE Manufacturers
When selecting materials for HDPE manufacturing, it is crucial to consider various factors that impact performance, cost, and suitability for specific applications. Here are some common materials used in conjunction with HDPE, along with their properties, advantages, disadvantages, and considerations for international B2B buyers.
What Are the Key Properties of Polypropylene (PP) in HDPE Manufacturing?
Polypropylene (PP) is often used alongside HDPE due to its favorable properties. It boasts a high melting point (around 160°C), making it suitable for applications involving elevated temperatures. PP also exhibits excellent chemical resistance, especially against acids and bases, which is vital for industries like packaging and automotive.
Pros: PP is lightweight, has good tensile strength, and is relatively inexpensive. Its manufacturing process is straightforward, allowing for quick production cycles.
Cons: However, PP can be less durable than HDPE in outdoor applications due to UV degradation. Additionally, it has a lower impact resistance, which may limit its use in high-stress environments.
Impact on Application: PP is compatible with various media, making it suitable for packaging and storage solutions. However, its lower environmental resistance may necessitate additional protective measures.
Considerations for International Buyers: Compliance with international standards like ASTM and ISO is crucial. Buyers from regions such as Africa and South America should also consider local regulations regarding plastic use and recycling.
How Does Polyvinyl Chloride (PVC) Compare in HDPE Applications?
Polyvinyl Chloride (PVC) is another common material that can complement HDPE in specific applications. PVC has excellent dimensional stability and can withstand temperatures up to 60°C. It is also known for its resistance to corrosion and chemical damage.
Pros: PVC is durable and cost-effective, making it a popular choice for piping and construction applications. Its versatility allows for various formulations, including flexible and rigid types.
Cons: However, PVC can become brittle over time, especially when exposed to UV light. The manufacturing process can also involve harmful chemicals, raising environmental concerns.
Impact on Application: PVC’s compatibility with water and various chemicals makes it suitable for plumbing and drainage systems. However, its limitations in high-temperature applications may restrict its use in certain industries.
Considerations for International Buyers: Buyers in Europe and the Middle East should be aware of stringent regulations regarding PVC usage and disposal. Compliance with standards like DIN and EN is essential for market entry.
What Are the Benefits of Using Ethylene Vinyl Acetate (EVA)?
Ethylene Vinyl Acetate (EVA) is a copolymer that offers unique properties beneficial for HDPE applications. With a lower melting point than HDPE, EVA can be easily processed and molded. It also provides excellent flexibility and impact resistance.
Pros: EVA is highly elastic and has good transparency, making it suitable for packaging applications. It also has a softer feel, which is advantageous for consumer products.
Cons: However, EVA can be more expensive than other materials and may not have the same level of chemical resistance as HDPE. Its thermal stability is also lower, limiting its use in high-temperature applications.
Impact on Application: EVA’s compatibility with various media makes it ideal for packaging, but its limitations in chemical resistance may require careful consideration in specific applications.
Considerations for International Buyers: Buyers should be aware of the varying regulations surrounding EVA in different regions, particularly in Europe, where environmental impact assessments are becoming increasingly important.
How Does Polystyrene (PS) Fit into HDPE Manufacturing?
Polystyrene (PS) is used in specific applications where rigidity and clarity are essential. It has a low melting point (around 100°C) and is easy to mold, making it suitable for various consumer products.
Pros: PS is lightweight and cost-effective, making it a popular choice for disposable products and packaging. Its clarity allows for excellent visibility of contents.
Cons: However, PS is not as durable as HDPE and has poor chemical resistance, which can limit its application scope. It is also more susceptible to environmental stress cracking.
Impact on Application: PS is often used for packaging and disposable items but may not be suitable for applications requiring high durability or chemical resistance.
Considerations for International Buyers: Buyers from regions like South America should consider local waste management practices, as PS is often less recyclable than other materials.
Summary Table of Material Selection for HDPE Manufacturers
Material | Typical Use Case for HDPE Manufacturers | Key Advantage | Key Disadvantage/Limitation | Relative Cost (Low/Med/High) |
---|---|---|---|---|
Polypropylene (PP) | Packaging, automotive components | High melting point, chemical resistance | Less durable outdoors, lower impact resistance | Medium |
Polyvinyl Chloride (PVC) | Plumbing, construction applications | Cost-effective, durable | Brittle over time, environmental concerns | Low |
Ethylene Vinyl Acetate (EVA) | Packaging, consumer products | High elasticity, good transparency | More expensive, lower thermal stability | Medium |
Polystyrene (PS) | Disposable products, packaging | Lightweight, cost-effective | Poor chemical resistance, less durable | Low |
This strategic material selection guide provides international B2B buyers with essential insights into the properties, advantages, and limitations of materials commonly used in HDPE manufacturing, ensuring informed decision-making tailored to their specific regional needs.
In-depth Look: Manufacturing Processes and Quality Assurance for HDPE Manufacturers
What Are the Main Stages of HDPE Manufacturing?
The manufacturing process of High-Density Polyethylene (HDPE) involves several critical stages, each designed to ensure that the final product meets industry standards for quality and performance. Understanding these stages is essential for B2B buyers, particularly those in regions such as Africa, South America, the Middle East, and Europe, where quality assurance is paramount.
-
Material Preparation
The process begins with the preparation of raw materials, which typically includes polyethylene resin and various additives. This stage may involve drying the resin to remove moisture, as water can negatively impact the polymerization process. For buyers, it’s crucial to ensure that the materials used are of high quality and sourced from reputable suppliers. -
Forming
Once the materials are prepared, they are subjected to forming processes such as extrusion, injection molding, or blow molding. In extrusion, the resin is melted and forced through a die to create sheets or tubes. Injection molding involves injecting molten plastic into a mold to create specific shapes, while blow molding is used for hollow objects. Buyers should inquire about the forming techniques used, as they can affect the durability and usability of the final product. -
Assembly
After forming, components may need to be assembled, especially in applications where multiple parts are required. This could involve welding or adhesive bonding. Buyers should verify that manufacturers use techniques that ensure structural integrity and reliability, particularly for applications in demanding environments. -
Finishing
The final stage involves finishing processes such as trimming, surface treatment, and packaging. These steps ensure that the product meets aesthetic and functional requirements. It’s advisable for buyers to understand the finishing processes to ensure that the product will perform as expected in their specific applications.
How Do HDPE Manufacturers Ensure Quality Assurance?
Quality assurance (QA) is a vital component of the manufacturing process, especially in the production of HDPE, where material integrity is crucial. Manufacturers often adhere to international standards such as ISO 9001, which outlines requirements for a quality management system (QMS).
-
International Standards and Certifications
In addition to ISO 9001, HDPE manufacturers may comply with industry-specific standards such as CE marking for safety, API standards for oil and gas applications, and various local regulations. B2B buyers should request documentation of these certifications to ensure compliance with relevant standards. -
Quality Control Checkpoints
Effective quality control (QC) involves several checkpoints during the manufacturing process, including:
– Incoming Quality Control (IQC): Inspection of raw materials before production.
– In-Process Quality Control (IPQC): Monitoring of processes during manufacturing to catch defects early.
– Final Quality Control (FQC): Comprehensive testing of finished products before shipment.
Understanding these checkpoints can help buyers assess the thoroughness of a manufacturer’s QC processes.
- Common Testing Methods
Various testing methods are employed to verify the quality of HDPE products, including:
– Mechanical Testing: Assessing tensile strength, impact resistance, and elasticity.
– Chemical Testing: Ensuring chemical compatibility and resistance.
– Thermal Testing: Evaluating performance under temperature variations.
Buyers should inquire about the specific tests performed and the results of those tests to ensure the product meets their requirements.
How Can B2B Buyers Verify Supplier Quality Control?
For international B2B buyers, verifying the quality control measures of HDPE manufacturers is essential for ensuring product reliability. Here are several strategies:
-
Conducting Audits
Regular audits of suppliers can help buyers assess compliance with quality standards. This can include on-site inspections of manufacturing facilities and reviewing quality management systems. Buyers from regions such as Africa and South America may face challenges in conducting audits due to distance; therefore, leveraging local representatives or third-party inspection services can be beneficial. -
Requesting Quality Reports
Manufacturers should provide detailed quality reports that outline testing results and compliance with international standards. Buyers should not hesitate to request these documents and review them thoroughly to ensure they meet their specifications. -
Utilizing Third-Party Inspection Services
Engaging third-party inspection services can provide an unbiased evaluation of a manufacturer’s quality control processes. This is particularly valuable for buyers in the Middle East and Europe, where regulatory compliance is strict. Third-party inspectors can perform random checks and provide certification that can be crucial for supply chain management.
What Are the Nuances of Quality Control and Certification for International B2B Buyers?
Quality control and certification can vary significantly based on geographic location and industry requirements. Here are some nuances that international B2B buyers should consider:
-
Regional Regulations
Different regions may have specific regulations governing the production and quality of HDPE products. For example, European buyers must be aware of REACH regulations concerning chemical safety. Understanding these local regulations can help buyers ensure compliance and avoid potential legal issues. -
Cultural Considerations
Cultural differences may affect communication and expectations regarding quality assurance. Buyers from Africa and South America should approach negotiations with an understanding of local practices and emphasize the importance of quality standards in their purchasing decisions. -
Supply Chain Transparency
Increasingly, buyers are demanding transparency in the supply chain. This includes knowing the source of raw materials and the manufacturing processes involved. Buyers should prioritize manufacturers who are willing to provide detailed information about their supply chains, as this can lead to better quality assurance.
Conclusion
In conclusion, understanding the manufacturing processes and quality assurance measures of HDPE manufacturers is essential for international B2B buyers. By focusing on the key stages of manufacturing, relevant standards, and effective verification strategies, buyers can make informed decisions that ensure they receive high-quality products that meet their specific needs. Whether operating in Africa, South America, the Middle East, or Europe, a thorough understanding of these processes will enhance buyer confidence and satisfaction.
Practical Sourcing Guide: A Step-by-Step Checklist for ‘HDPE Manufacturers’
Introduction
Sourcing high-density polyethylene (HDPE) manufacturers is a crucial step for businesses looking to procure quality materials for various applications. This checklist provides a structured approach to help international B2B buyers, particularly those from Africa, South America, the Middle East, and Europe, identify and engage with suitable HDPE suppliers effectively. Following these steps will ensure you make informed decisions, minimizing risks and enhancing supply chain efficiency.
Step 1: Define Your Technical Specifications
Clearly outline the technical requirements for the HDPE products you need. This includes dimensions, grades, and any specific properties such as UV resistance or food-grade compliance. Having a precise specification helps in communicating effectively with potential suppliers and ensures they can meet your needs.
- Consider the application: Different uses may require varying grades of HDPE; for example, packaging, piping, or automotive parts.
- Document everything: A detailed specification document can serve as a reference point during negotiations and quality checks.
Step 2: Conduct Market Research
Research potential suppliers to understand the market landscape. This includes identifying manufacturers that specialize in HDPE and assessing their geographical locations, production capabilities, and reputations.
- Utilize online platforms: Websites like Alibaba, Global Sources, and industry-specific directories can help you find credible manufacturers.
- Evaluate regional advantages: Consider suppliers that are closer to your location to reduce shipping costs and lead times.
Step 3: Evaluate Potential Suppliers
Before committing, it’s crucial to vet suppliers thoroughly. Request company profiles, case studies, and references from buyers in a similar industry or region.
- Check for certifications: Ensure the suppliers comply with international standards such as ISO 9001, which indicates a commitment to quality management.
- Assess production capacity: Confirm that the supplier can meet your volume requirements without compromising quality.
Step 4: Request Samples
Always request product samples before placing a bulk order. This allows you to assess the quality of the HDPE materials firsthand and ensure they meet your specifications.
- Conduct testing: Evaluate the samples for durability, flexibility, and other critical properties relevant to your application.
- Compare with competitors: If possible, obtain samples from multiple suppliers to make informed comparisons.
Step 5: Negotiate Terms and Pricing
Once you have narrowed down your options, initiate discussions on pricing, payment terms, and delivery schedules. Effective negotiation can lead to better pricing and favorable terms that benefit both parties.
- Be clear on expectations: Outline your requirements regarding minimum order quantities and delivery timelines.
- Consider long-term partnerships: If you find a reliable supplier, discuss potential long-term agreements which may offer cost savings.
Step 6: Verify Logistics and Shipping Arrangements
Confirm the logistics and shipping arrangements with your chosen supplier. This includes understanding the shipping methods, lead times, and costs involved.
- Ask about customs processes: Ensure that the supplier is familiar with the customs regulations for your region, which can prevent delays.
- Discuss packaging requirements: Proper packaging is essential to protect HDPE products during transit.
Step 7: Establish a Quality Assurance Process
Implement a quality assurance process to monitor the quality of the HDPE products you receive. This includes setting criteria for inspections and specifying how defects will be handled.
- Define inspection protocols: Establish who will conduct inspections and how often they will occur.
- Create a feedback loop: Communicate regularly with your supplier to address any quality issues promptly and maintain a good relationship.
By following this checklist, international B2B buyers can streamline their sourcing process for HDPE manufacturers, ensuring they select a reliable partner that meets their needs effectively.
Comprehensive Cost and Pricing Analysis for HDPE Manufacturers Sourcing
What Are the Key Cost Components in HDPE Manufacturing?
When sourcing HDPE (High-Density Polyethylene) products, understanding the cost structure is crucial for international B2B buyers. The primary cost components include:
-
Materials: The cost of raw HDPE resin is a significant portion of the overall expenditure. Prices can fluctuate based on global oil prices and availability of resin types. Buyers should stay informed about market trends and consider sourcing from regions with stable prices.
-
Labor: Labor costs vary widely depending on the manufacturing location. Regions with lower wage standards may offer competitive pricing, but this can sometimes affect quality. Understanding the local labor market is essential for assessing total costs.
-
Manufacturing Overhead: This includes utilities, maintenance, and administrative expenses associated with production. Efficient manufacturing processes can help reduce these costs, so inquire about the supplier’s operational efficiency.
-
Tooling: The initial cost of molds and machinery can be substantial. Custom tooling for specific products may lead to higher upfront costs but can provide long-term savings through improved production efficiency.
-
Quality Control (QC): Ensuring product quality is paramount, especially for industries with strict regulatory requirements. Suppliers may charge more for rigorous QC processes, but investing in quality can reduce costs related to defects and returns.
-
Logistics: Transportation and shipping costs can significantly affect the overall price. Consider the distance from the supplier to your location, shipping modes, and any associated customs duties or tariffs.
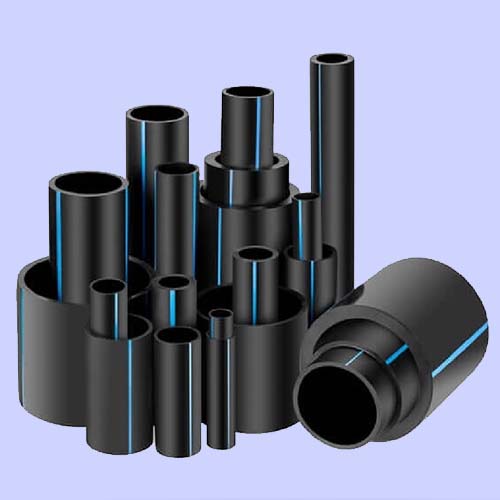
A stock image related to HDPE Manufacturers.
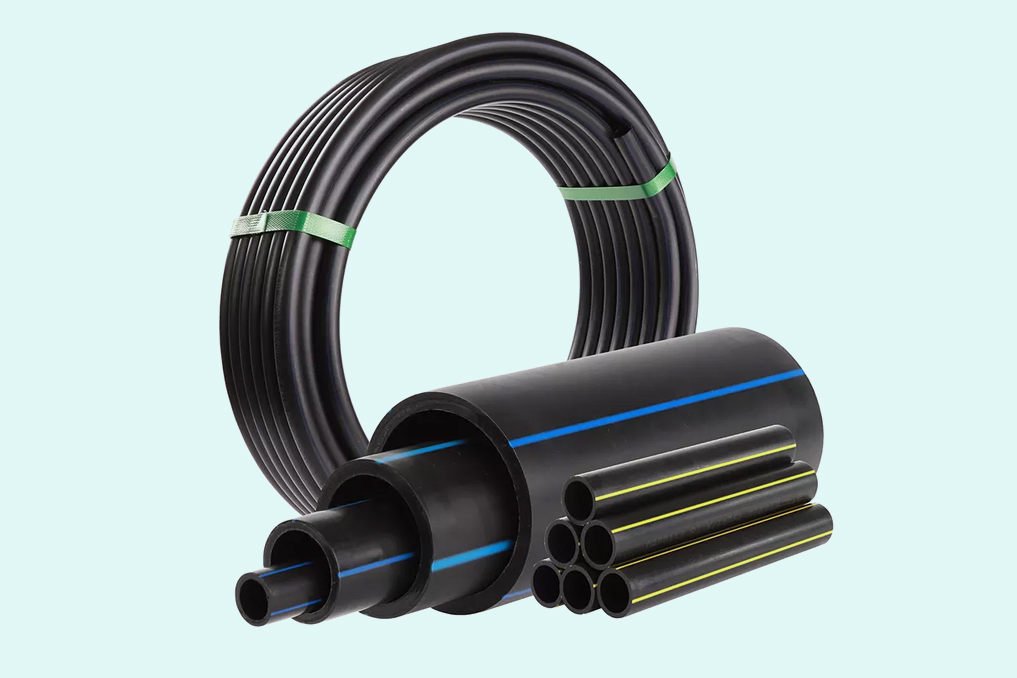
A stock image related to HDPE Manufacturers.
- Margin: Suppliers will add a profit margin to cover their costs and ensure profitability. Understanding the typical margins in the industry can help you gauge whether a quoted price is reasonable.
How Do Price Influencers Impact HDPE Sourcing?
Several factors can influence the pricing of HDPE products, particularly for international buyers:
-
Volume/MOQ (Minimum Order Quantity): Larger orders often lead to lower per-unit costs. Buyers should assess their demand to negotiate favorable terms.
-
Specifications and Customization: Custom specifications can drive up costs. It’s essential to balance the need for specific features against budget constraints.
-
Material Quality and Certifications: Higher quality materials or those meeting international certifications can result in increased prices. Ensure that the benefits of premium materials justify their costs.
-
Supplier Factors: Supplier reliability, reputation, and financial stability can influence pricing. Established suppliers might charge more due to their consistent quality and service levels.
-
Incoterms: The agreed terms of delivery (e.g., FOB, CIF) can affect the total cost. Buyers should understand these terms to avoid unexpected charges.
What Are the Best Buyer Tips for Cost-Efficiency in HDPE Sourcing?
To maximize cost-efficiency when sourcing HDPE products, consider the following strategies:
-
Negotiation: Engage in open discussions about pricing, especially for large orders. Suppliers may have flexibility in pricing based on volume or long-term contracts.
-
Total Cost of Ownership (TCO): Evaluate not just the purchase price but the total cost of ownership, which includes logistics, handling, storage, and potential waste. This holistic view can reveal more cost-effective options.
-
Leverage Regional Insights: Buyers from Africa, South America, the Middle East, and Europe should leverage regional insights into logistics and supplier dynamics. Understanding local market conditions can enhance negotiation power.
-
Stay Informed on Market Trends: Regularly monitor resin price trends and geopolitical factors that could affect supply chains. Being proactive can help in planning and budgeting.
-
Request Price Breakdown: When obtaining quotes, ask for a detailed price breakdown. This transparency can help identify areas for potential cost savings.
Conclusion
Understanding the comprehensive cost structure and pricing dynamics of HDPE manufacturing is essential for international B2B buyers. By being informed about cost components, price influencers, and effective negotiation strategies, buyers can make educated sourcing decisions that align with their budget and quality requirements. Always remember that quoted prices are indicative and can vary based on multiple factors.
Alternatives Analysis: Comparing HDPE Manufacturers With Other Solutions
When considering the procurement of materials for industrial applications, it’s crucial for international B2B buyers to explore various solutions available in the market. HDPE (High-Density Polyethylene) is widely recognized for its strength and versatility, but alternative materials and methods can also meet specific needs. Below, we compare HDPE manufacturers with two viable alternatives: Polypropylene (PP) and PVC (Polyvinyl Chloride).
Comparison Table of HDPE Manufacturers and Alternatives
Comparison Aspect | HDPE Manufacturers | Polypropylene (PP) | PVC (Polyvinyl Chloride) |
---|---|---|---|
Performance | Excellent resistance to impact and chemicals; suitable for outdoor use. | Good chemical resistance; less impact strength than HDPE. | Strong, rigid, good chemical resistance but can become brittle in cold. |
Cost | Generally moderate; price varies by grade and supplier. | Often lower than HDPE; cost-effective for large-scale applications. | Usually cheaper than both HDPE and PP; however, long-term durability may be a concern. |
Ease of Implementation | Requires specific processing conditions; may need specialized equipment. | Easier to process; compatible with various manufacturing techniques. | Highly versatile; can be easily molded and extruded. |
Maintenance | Low maintenance; resistant to environmental stress cracking. | Low maintenance; however, may require UV stabilization for outdoor use. | Moderate maintenance; susceptible to degradation if not properly stabilized. |
Best Use Case | Ideal for containers, piping, and geomembranes in harsh environments. | Suitable for packaging, textiles, and automotive parts. | Commonly used in plumbing, electrical cable insulation, and flooring. |
What Are the Advantages and Disadvantages of Polypropylene (PP)?
Polypropylene is a thermoplastic polymer known for its versatility and cost-effectiveness. One of its primary advantages is its lightweight nature, which can lead to reduced shipping costs. Additionally, PP has good chemical resistance and is often used in applications requiring durability against acids and bases. However, it lacks the impact resistance of HDPE, making it less suitable for high-stress environments. Furthermore, in outdoor applications, polypropylene may require additional UV stabilization to prevent degradation from sunlight exposure.
How Does PVC Compare to HDPE in Various Applications?
PVC is another widely used alternative to HDPE. It is typically less expensive and offers good rigidity and strength, making it suitable for a variety of applications, including plumbing and construction materials. PVC can be easily molded and extruded, offering versatility in manufacturing. However, its performance can be compromised in extreme temperatures, as it may become brittle in cold conditions. Additionally, while PVC has good chemical resistance, it may not perform as well as HDPE in certain aggressive environments, which could limit its application in specialized settings.
Conclusion: How to Choose the Right Solution for Your Needs?
When selecting between HDPE manufacturers and alternative materials like polypropylene or PVC, B2B buyers should evaluate their specific application requirements, including performance needs, budget constraints, and environmental considerations. Each material offers distinct advantages and disadvantages that can significantly impact the final decision. It is advisable to conduct a thorough analysis based on the intended use case and to consult with manufacturers to ensure the selected material aligns with operational goals and regulatory standards. By taking these factors into account, businesses can make informed decisions that enhance efficiency and sustainability in their operations.
Essential Technical Properties and Trade Terminology for HDPE Manufacturers
What Are the Key Technical Properties of HDPE for B2B Buyers?
Understanding the essential technical properties of High-Density Polyethylene (HDPE) is crucial for international B2B buyers, especially when sourcing materials for manufacturing and construction. Here are some of the most critical specifications:
1. Material Grade
Material grade indicates the specific formulation of HDPE, which affects its mechanical properties, chemical resistance, and suitability for various applications. Common grades include HDPE 3000, HDPE 4000, and others. For buyers, selecting the correct grade ensures that the final product meets performance standards and compliance regulations.
2. Density
Density is a significant property of HDPE, typically ranging from 0.93 to 0.97 g/cm³. Higher density generally translates to improved strength and durability, making it ideal for applications requiring load-bearing capabilities. Buyers must consider density when evaluating the suitability of HDPE for specific applications like pipes, containers, and films.
3. Tolerance
Tolerance refers to the allowable variation in the dimensions of the HDPE product. It is critical in manufacturing processes where precision is paramount. For B2B buyers, understanding tolerance levels ensures that the products fit together correctly in assembly processes, reducing waste and improving efficiency.
4. Melt Flow Index (MFI)
The Melt Flow Index measures the flow characteristics of HDPE during processing. A lower MFI indicates higher viscosity, which is ideal for applications requiring strength, while a higher MFI is suitable for injection molding. Buyers should consider MFI when determining processing methods and expected performance in end-use applications.
5. Impact Resistance
Impact resistance is a measure of how well HDPE can withstand sudden force or shock. This property is crucial for applications exposed to harsh environments or mechanical stress. Buyers need to assess impact resistance to ensure that the materials will perform adequately in their intended applications.
What Are Common Trade Terms Used in the HDPE Industry?
Familiarity with industry jargon is essential for B2B buyers to navigate procurement efficiently. Here are some common terms:
1. OEM (Original Equipment Manufacturer)
OEM refers to a company that produces parts or equipment that may be marketed by another manufacturer. In the HDPE industry, understanding OEM relationships can help buyers identify reliable suppliers and ensure they are sourcing quality materials that meet specific industry standards.
2. MOQ (Minimum Order Quantity)
MOQ indicates the smallest quantity of a product that a supplier is willing to sell. For international buyers, knowing the MOQ is vital for budgeting and inventory management. It can also affect the overall cost and feasibility of sourcing HDPE, especially for smaller operations.
3. RFQ (Request for Quotation)
An RFQ is a document used by buyers to solicit price quotes from suppliers. It typically includes specifications, quantities, and terms. For B2B buyers, issuing an RFQ can streamline the procurement process and ensure competitive pricing and terms from multiple suppliers.
4. Incoterms (International Commercial Terms)
Incoterms are a series of pre-defined commercial terms published by the International Chamber of Commerce (ICC) that clarify the responsibilities of buyers and sellers in international trade. Understanding Incoterms is essential for B2B buyers to mitigate risks related to shipping, insurance, and delivery.
5. Lead Time
Lead time refers to the amount of time it takes from placing an order until the product is delivered. For buyers, understanding lead times is crucial for project planning and inventory management. This knowledge helps in coordinating production schedules and meeting deadlines.
By grasping these technical properties and trade terminologies, international B2B buyers can make informed decisions when sourcing HDPE, ultimately enhancing their procurement strategies and operational efficiency.
Navigating Market Dynamics and Sourcing Trends in the HDPE Manufacturers Sector
What Are the Key Trends Shaping the HDPE Manufacturers Market?
The global HDPE (High-Density Polyethylene) market is currently experiencing a surge in demand driven by several key factors. One of the primary drivers is the increasing need for lightweight yet durable materials across various sectors, including packaging, automotive, and construction. Additionally, technological advancements are playing a significant role in shaping sourcing trends. The adoption of digital platforms and Industry 4.0 technologies enables manufacturers to streamline operations, reduce costs, and improve supply chain transparency.
For international B2B buyers, particularly from Africa, South America, the Middle East, and Europe, understanding regional market dynamics is crucial. In Africa, the focus is on enhancing local production capabilities to reduce dependency on imports. South America is witnessing a rise in demand for HDPE in agriculture and packaging, driven by population growth and urbanization. The Middle East, with its vast petrochemical industry, is poised to become a leading supplier of HDPE. Meanwhile, Europe is increasingly emphasizing sustainability, pushing manufacturers to adopt eco-friendly practices.
Emerging trends such as circular economy principles, where waste materials are repurposed into new products, are also gaining traction. Buyers should consider these trends when sourcing HDPE to align with global standards and consumer preferences, ensuring their supply chains remain competitive and resilient.
How Is Sustainability Influencing Sourcing Decisions for HDPE Manufacturers?
Sustainability has become a central theme in the HDPE manufacturing sector, significantly impacting sourcing decisions. The environmental impact of plastic production and disposal is under scrutiny, prompting buyers to prioritize ethical sourcing practices. This includes selecting manufacturers that adhere to stringent environmental regulations and demonstrate a commitment to reducing carbon footprints.
Ethical supply chains are increasingly becoming a prerequisite for B2B buyers. Companies are seeking out suppliers that utilize recycled materials or renewable energy in their manufacturing processes. Certifications such as ISO 14001 (Environmental Management) and the Cradle to Cradle certification are becoming essential for manufacturers aiming to showcase their commitment to sustainability.
Moreover, buyers are encouraged to evaluate the entire lifecycle of HDPE products, from production to end-of-life disposal. Engaging with suppliers who offer take-back programs or recycling initiatives can enhance a company’s sustainability profile, attracting environmentally conscious clients and consumers.
What Is the Historical Context of HDPE Manufacturing?
The history of HDPE manufacturing dates back to the 1950s, when it was first developed as a lightweight, versatile plastic. Initially used for applications such as milk bottles and piping, the material quickly gained popularity due to its strength and resistance to impact and chemicals. Over the decades, advancements in polymer technology have led to the development of various grades of HDPE, expanding its applications in sectors like automotive and construction.
As environmental concerns grew in the late 20th century, the industry began to shift towards more sustainable practices. Today, HDPE is not only recognized for its utility but also for its potential for recycling and reusability, making it a key player in the global move towards sustainable materials. Understanding this evolution helps B2B buyers appreciate the opportunities and responsibilities associated with sourcing HDPE in today’s market.
Frequently Asked Questions (FAQs) for B2B Buyers of HDPE Manufacturers
-
How can I identify reliable HDPE manufacturers for international sourcing?
To identify reliable HDPE manufacturers, start by researching industry certifications such as ISO 9001 and ISO 14001, which indicate quality management systems and environmental management practices. Utilize platforms like Alibaba, ThomasNet, or Global Sources to find reputable suppliers. Always check for customer reviews and request references to validate their credibility. Additionally, consider visiting trade shows or exhibitions relevant to the plastics industry to meet manufacturers face-to-face and assess their operations directly. -
What are the minimum order quantities (MOQs) for HDPE products?
Minimum order quantities (MOQs) for HDPE products can vary significantly between manufacturers. Typically, MOQs range from 500 kg to several tons depending on the product type and customization requirements. Smaller manufacturers may offer lower MOQs to accommodate small businesses, while larger manufacturers might set higher thresholds to optimize production efficiency. Always discuss MOQs upfront to ensure they align with your business needs and budget. -
What customization options are available when sourcing HDPE materials?
Many HDPE manufacturers offer a variety of customization options, including color, thickness, and specific formulations to meet unique application requirements. You can also request tailored dimensions and shapes based on your project needs. When reaching out to suppliers, provide detailed specifications and inquire about their capabilities to ensure they can meet your customization requests effectively. -
What payment terms are typically offered by HDPE manufacturers?
Payment terms can vary widely among HDPE manufacturers, but common practices include a 30% deposit upfront and the remaining 70% before shipment. Some suppliers may offer flexible terms like letter of credit or extended payment periods for established customers. It’s essential to negotiate payment terms that are suitable for both parties, ensuring financial security while maintaining a good relationship with the manufacturer.
-
How do I ensure quality assurance when sourcing HDPE products?
To ensure quality assurance, request samples before placing a bulk order to evaluate the material’s properties. Verify if the manufacturer has a quality control process in place, including testing for compliance with industry standards. You can also consider third-party inspections to assess the quality of the products before shipment. Establishing clear quality expectations and regular communication with the supplier will further enhance product reliability. -
What logistics considerations should I be aware of when importing HDPE materials?
When importing HDPE materials, consider factors such as shipping methods, lead times, and customs regulations in your country. Evaluate the total landed cost, including shipping, duties, and taxes, to avoid unexpected expenses. Work with a freight forwarder experienced in handling plastics to navigate logistics smoothly. Understanding local regulations regarding plastic imports is crucial to ensure compliance and avoid delays. -
How can I mitigate risks associated with international trade of HDPE materials?
To mitigate risks, conduct thorough due diligence on potential suppliers, including financial stability and production capabilities. Utilize contracts that specify terms of trade, delivery schedules, and penalties for non-compliance. Consider using a letter of credit to secure payments, reducing the risk of financial loss. Additionally, maintaining open communication with your suppliers can help address any issues proactively. -
What are the key factors to consider when selecting an HDPE manufacturer?
When selecting an HDPE manufacturer, consider factors such as production capacity, lead times, product quality, and customer service. Evaluate their experience in the industry and their ability to meet your specific needs. Assess their compliance with environmental regulations and sustainability practices, as these are increasingly important in global trade. Lastly, compare pricing structures and payment terms to ensure they align with your budget and financial planning.
Important Disclaimer & Terms of Use
⚠️ Important Disclaimer
The information provided in this guide, including content regarding manufacturers, technical specifications, and market analysis, is for informational and educational purposes only. It does not constitute professional procurement advice, financial advice, or legal advice.
While we have made every effort to ensure the accuracy and timeliness of the information, we are not responsible for any errors, omissions, or outdated information. Market conditions, company details, and technical standards are subject to change.
B2B buyers must conduct their own independent and thorough due diligence before making any purchasing decisions. This includes contacting suppliers directly, verifying certifications, requesting samples, and seeking professional consultation. The risk of relying on any information in this guide is borne solely by the reader.
Strategic Sourcing Conclusion and Outlook for HDPE Manufacturers
In today’s competitive landscape, strategic sourcing is crucial for HDPE manufacturers looking to optimize their supply chains and enhance operational efficiency. By leveraging global sourcing strategies, businesses can not only mitigate risks associated with supply disruptions but also capitalize on cost-saving opportunities. Buyers from Africa, South America, the Middle East, and Europe should prioritize suppliers who demonstrate reliability, innovation, and sustainability in their practices.
Furthermore, as the demand for HDPE products continues to rise, staying informed about market trends and technological advancements will be essential. Engaging with suppliers who invest in research and development can provide a significant competitive edge, ensuring access to high-quality materials and cutting-edge solutions.
As we look to the future, international B2B buyers are encouraged to cultivate strong partnerships with HDPE manufacturers that align with their strategic goals. Embrace a proactive approach to sourcing and explore new markets to enhance your supply chain resilience. By making informed decisions today, you position your business for success in the evolving global marketplace.