Discover Top Benefits: Choosing Your Air Compressor Supplier (2025)
Introduction: Navigating the Global Market for air compressor supplier
Navigating the global market for air compressor suppliers can be a daunting task for international B2B buyers, especially those operating in regions like Africa, South America, the Middle East, and Europe. Sourcing the right air compressors that meet specific operational needs while ensuring cost-effectiveness is often complicated by the diverse range of suppliers and products available. This comprehensive guide serves as a valuable resource, addressing critical aspects such as the various types of air compressors, their applications across different industries, and essential supplier vetting processes.
B2B buyers will gain insights into the nuances of air compressor specifications, helping them understand which models are best suited for their operations—whether for manufacturing, construction, or other industrial applications. Furthermore, the guide delves into pricing structures and cost considerations, equipping buyers with the knowledge to negotiate effectively and make informed purchasing decisions.
By offering a thorough examination of the air compressor market, this guide empowers international B2B buyers to confidently navigate their sourcing journey, ensuring they can find reliable suppliers that align with their business objectives and operational requirements. Whether you are based in the UAE, Nigeria, or elsewhere, the insights provided will facilitate smarter purchasing choices, ultimately enhancing productivity and efficiency in your operations.
Understanding air compressor supplier Types and Variations
Type Name | Key Distinguishing Features | Primary B2B Applications | Brief Pros & Cons for Buyers |
---|---|---|---|
Reciprocating Compressors | Positive displacement, variable speed options | Manufacturing, automotive, HVAC | Pros: High pressure, versatile. Cons: Noise, maintenance-intensive. |
Rotary Screw Compressors | Continuous operation, oil-injected or oil-free | Large-scale manufacturing, food processing | Pros: Efficient, low maintenance. Cons: Higher initial cost. |
Centrifugal Compressors | High flow rates, low pressure variations | Chemical processing, power generation | Pros: Energy-efficient for large volumes. Cons: Complex design, costly repairs. |
Scroll Compressors | Compact design, quiet operation | HVAC, refrigeration, medical devices | Pros: Quiet, reliable. Cons: Limited pressure capabilities. |
Diaphragm Compressors | No lubrication, high purity air | Pharmaceuticals, laboratories | Pros: Contaminant-free air. Cons: Lower flow rates, higher cost. |
What Are Reciprocating Compressors and Their B2B Suitability?
Reciprocating compressors operate by using a piston within a cylinder, which compresses air. They are well-suited for applications requiring high pressure and are commonly used in manufacturing, automotive, and HVAC systems. When considering a reciprocating compressor, B2B buyers should evaluate noise levels and maintenance requirements, as these units can be loud and require regular upkeep. Their ability to handle variable speeds makes them versatile for different operational needs.
How Do Rotary Screw Compressors Benefit Businesses?
Rotary screw compressors utilize two rotating screws to compress air continuously, making them ideal for large-scale manufacturing and food processing. Their efficiency and low maintenance needs are significant advantages, particularly for companies that require a steady air supply. However, the initial investment can be higher compared to other types, so businesses should assess their budget against the long-term savings in energy and maintenance costs.
Why Choose Centrifugal Compressors for High Volume Needs?
Centrifugal compressors are designed for high flow rates and are often used in chemical processing and power generation. Their energy efficiency makes them a preferred choice for operations that require large volumes of compressed air. However, their complex design can lead to costly repairs, which is an important consideration for B2B buyers. Companies should weigh the benefits of energy savings against potential maintenance challenges.
What Advantages Do Scroll Compressors Offer?
Scroll compressors feature a compact design and operate quietly, making them suitable for HVAC systems, refrigeration, and medical devices. Their reliability and low noise levels are appealing to businesses in sensitive environments. However, buyers should note that scroll compressors may have limitations in pressure capabilities, which could restrict their use in high-demand applications. Understanding these limitations is crucial for making an informed purchasing decision.
When Are Diaphragm Compressors the Right Choice?
Diaphragm compressors are known for providing high-purity air since they operate without lubrication, making them ideal for pharmaceuticals and laboratory settings. While they offer the advantage of contaminant-free air, they typically have lower flow rates and higher costs compared to other compressor types. B2B buyers should consider the specific purity requirements of their applications when evaluating diaphragm compressors, ensuring they align with their operational needs.
Related Video: Air Compressor Types, How They Work, and How to Choose the Right One
Key Industrial Applications of air compressor supplier
Industry/Sector | Specific Application of Air Compressor Supplier | Value/Benefit for the Business | Key Sourcing Considerations for this Application |
---|---|---|---|
Manufacturing | Pneumatic tools operation | Increases efficiency and productivity in assembly lines | Ensure compatibility with existing machinery; energy efficiency ratings; maintenance support availability |
Food and Beverage | Packaging and bottling processes | Enhances product preservation and extends shelf life | Compliance with food safety regulations; availability of clean air solutions; operational reliability |
Construction and Mining | Material handling and drilling | Improves project timelines and reduces labor costs | Durability in harsh environments; after-sales service; local support presence |
Automotive | Paint spraying and surface finishing | Achieves high-quality finishes and reduces waste | Specific pressure requirements; energy consumption; supplier reliability |
Healthcare | Medical air supply systems | Ensures patient safety and equipment functionality | Compliance with medical standards; availability of emergency support; long-term supply agreements |
How Are Air Compressors Used in Manufacturing?
In the manufacturing sector, air compressors are crucial for powering pneumatic tools used in assembly lines. These tools enhance efficiency and productivity, allowing for faster and more precise operations. International buyers, particularly from regions like Africa and South America, should consider sourcing compressors that are compatible with existing machinery and have high energy efficiency ratings to optimize operational costs. Additionally, maintenance support availability is vital to minimize downtime.
What Role Do Air Compressors Play in Food and Beverage Industries?
In the food and beverage industry, air compressors are essential for packaging and bottling processes. They provide the necessary pressure to fill containers and seal them efficiently, which enhances product preservation and extends shelf life. Buyers from the Middle East and Europe should ensure that the compressors comply with food safety regulations and offer clean air solutions to maintain product integrity. Operational reliability is also a key factor, as any failure can lead to significant losses.
How Are Air Compressors Utilized in Construction and Mining?
Air compressors are widely used in construction and mining for material handling and drilling applications. They improve project timelines by powering heavy-duty tools that facilitate excavation and material transport, ultimately reducing labor costs. Buyers in these sectors should focus on sourcing durable compressors that can withstand harsh environments. After-sales service and local support presence are crucial to ensure operational continuity and reduce the risk of equipment failure.
What Benefits Do Air Compressors Provide in the Automotive Sector?
In the automotive industry, air compressors are integral for paint spraying and surface finishing. They help achieve high-quality finishes and reduce waste during the painting process, which is essential for maintaining brand reputation. B2B buyers should pay attention to specific pressure requirements and energy consumption when sourcing compressors. Additionally, the reliability of the supplier is vital, as delays in production can significantly impact business operations.
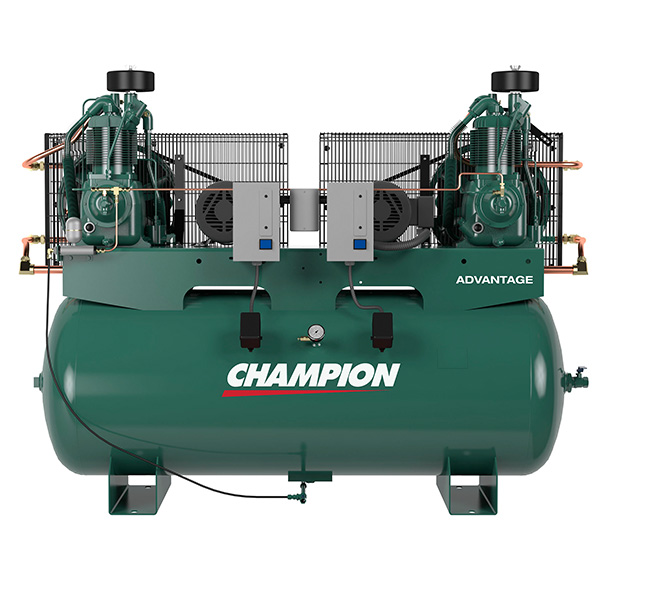
A stock image related to air compressor supplier.
Why Are Air Compressors Important in Healthcare Applications?
Air compressors play a critical role in healthcare, particularly in medical air supply systems. They ensure the safe delivery of air for respiratory equipment and other medical devices, which is essential for patient safety and equipment functionality. Buyers in this sector must ensure compliance with stringent medical standards and consider the availability of emergency support. Long-term supply agreements can provide stability and assurance in sourcing high-quality equipment.
Related Video: Air Compressor (Basics, Parts, Diagram, Working & Applications) Explained with Animation
3 Common User Pain Points for ‘air compressor supplier’ & Their Solutions
Scenario 1: Inconsistent Air Pressure Leading to Equipment Malfunction
The Problem: One of the most common issues faced by B2B buyers in industries such as manufacturing or construction is inconsistent air pressure from their air compressors. This inconsistency can lead to equipment malfunction, resulting in production delays and increased operational costs. For instance, in a factory where pneumatic tools are used, fluctuating air pressure can cause tools to underperform, leading to defective products and costly reworks. Buyers often find it challenging to identify the root cause of these pressure fluctuations, whether it be due to improper sizing of the compressor, lack of maintenance, or poor-quality components.
The Solution: To address this issue, it’s crucial for buyers to engage in a thorough evaluation of their air compressor needs before making a purchase. First, they should conduct a comprehensive assessment of their equipment’s air demand, considering peak usage scenarios. Utilizing software tools or consulting with an experienced air compressor supplier can aid in determining the optimal compressor size and type. Regular maintenance schedules should also be established, including periodic checks of air filters, pressure regulators, and hoses to ensure consistent airflow. Additionally, investing in quality components from reputable suppliers can significantly reduce the risk of pressure-related issues.
Scenario 2: Difficulty in Finding Reliable After-Sales Support
The Problem: International B2B buyers, particularly from regions like Africa and South America, often face challenges in accessing reliable after-sales support from air compressor suppliers. This can lead to prolonged downtimes when equipment malfunctions, as buyers struggle to find local technicians who are trained to service specific brands or models. The lack of timely support can severely impact productivity, especially in industries that rely heavily on compressed air systems.
The Solution: To mitigate this risk, buyers should prioritize suppliers that offer robust after-sales service agreements. It’s advisable to verify the supplier’s support network in the buyer’s region, including the availability of local service centers and trained technicians. Buyers can also consider asking suppliers for references or testimonials from other clients in similar geographical areas. Establishing a clear communication channel with the supplier for troubleshooting and service requests will further streamline support. Additionally, consider investing in training for in-house maintenance staff, which can reduce reliance on external technicians and minimize downtime.
Scenario 3: Unclear Specifications Leading to Over- or Under-Sized Equipment
The Problem: Another prevalent pain point for B2B buyers is the confusion surrounding the specifications of air compressors, often resulting in over- or under-sized equipment. This miscalculation can lead to inefficiencies, such as increased energy costs from larger than necessary compressors or insufficient power supply for operational needs. This issue is particularly pressing for buyers in Europe and the Middle East, where energy costs can significantly impact overall operational expenses.
The Solution: To avoid this pitfall, buyers must engage in a detailed specification process before purchasing. This includes not only understanding the specific air requirements of their operations but also considering future growth projections. Collaborating with an experienced air compressor supplier can provide insights into the right specifications based on industry standards. Additionally, utilizing tools like air consumption calculators can help buyers accurately determine their requirements. It’s beneficial to request detailed technical documentation and to conduct site assessments to ensure that the selected compressor aligns with the operational demands. Finally, consider discussing energy efficiency ratings and maintenance requirements to make a fully informed decision.
Strategic Material Selection Guide for air compressor supplier
What Are the Key Materials Used in Air Compressors?
When selecting materials for air compressors, international B2B buyers must consider various factors, including performance characteristics, cost, and regional compliance. Below, we analyze four common materials used in air compressor manufacturing: aluminum, cast iron, stainless steel, and composite materials.
How Does Aluminum Perform in Air Compressors?
Key Properties: Aluminum is lightweight and has good thermal conductivity, making it suitable for components that require efficient heat dissipation. It typically has a moderate temperature rating, allowing it to perform well under standard operating conditions.
Pros & Cons: The primary advantages of aluminum include its low weight, which reduces the overall weight of the compressor, and its resistance to corrosion. However, aluminum can be less durable than other metals, making it susceptible to wear and tear under high-stress conditions. The manufacturing complexity is relatively low, but the cost can be moderate compared to heavier metals.
Impact on Application: Aluminum is often used in portable air compressors and applications where weight is a critical factor. Its compatibility with various media makes it a versatile choice, but buyers must ensure that it meets specific pressure requirements.
Considerations for International Buyers: Buyers in regions like Africa and South America should consider the availability of aluminum and its compliance with local standards such as ASTM. In the Middle East, where high temperatures may be prevalent, ensuring the aluminum’s temperature rating aligns with operational needs is crucial.
What Are the Benefits of Cast Iron in Air Compressors?
Key Properties: Cast iron is known for its excellent wear resistance and ability to withstand high pressures and temperatures, making it ideal for heavy-duty applications.
Pros & Cons: The key advantage of cast iron is its durability and longevity, which can lead to lower maintenance costs over time. However, it is heavier than aluminum, which can be a disadvantage in portable applications. The manufacturing process can be complex, leading to higher initial costs.
Impact on Application: Cast iron is often used in stationary air compressors and industrial applications where durability is paramount. Its compatibility with high-pressure air makes it a preferred choice for heavy-duty tasks.
Considerations for International Buyers: Buyers in Europe and the Middle East should ensure that the cast iron meets relevant standards such as DIN or JIS. The weight of cast iron may also pose logistical challenges for shipping and installation in regions with limited infrastructure.
Why Choose Stainless Steel for Air Compressors?
Key Properties: Stainless steel is highly resistant to corrosion and can withstand high temperatures and pressures, making it suitable for a variety of environments.
Pros & Cons: The primary advantage of stainless steel is its corrosion resistance, which extends the lifespan of compressor components. However, it is more expensive than both aluminum and cast iron, and the manufacturing process can be more complex, leading to higher costs.
Impact on Application: Stainless steel is ideal for applications that involve corrosive environments, such as chemical processing or marine applications. Its compatibility with various media is a significant advantage.
Considerations for International Buyers: Buyers in regions like the UAE and Nigeria should ensure that the stainless steel used complies with international standards. Additionally, the higher cost may require budget considerations, especially for large-scale projects.
How Do Composite Materials Fit into Air Compressor Design?
Key Properties: Composite materials are lightweight and can be engineered to provide specific performance characteristics, such as enhanced strength and thermal resistance.
Pros & Cons: The advantages of composite materials include their lightweight nature and the ability to customize properties for specific applications. However, they can be more expensive and may not always provide the same level of durability as metals.
Impact on Application: Composites are often used in specialized applications where weight savings are critical, such as in aerospace or automotive sectors.
Considerations for International Buyers: Buyers should be aware of the specific certifications required for composite materials in their region. Understanding the manufacturing processes and potential supply chain issues is also essential, particularly in regions with less developed infrastructure.
Summary Table of Material Selection for Air Compressors
Material | Typical Use Case for Air Compressor Supplier | Key Advantage | Key Disadvantage/Limitation | Relative Cost (Low/Med/High) |
---|---|---|---|---|
Aluminum | Portable air compressors | Lightweight and corrosion-resistant | Less durable under high stress | Medium |
Cast Iron | Stationary industrial compressors | Excellent durability and wear resistance | Heavy and complex manufacturing | Medium to High |
Stainless Steel | Corrosive environment applications | High corrosion resistance | Higher cost and manufacturing complexity | High |
Composite Materials | Specialized lightweight applications | Customizable properties | More expensive and less durable | High |
This strategic material selection guide provides international B2B buyers with essential insights to make informed decisions when sourcing air compressors, considering regional compliance, application requirements, and cost-effectiveness.
In-depth Look: Manufacturing Processes and Quality Assurance for air compressor supplier
What Are the Key Manufacturing Processes for Air Compressors?
The manufacturing of air compressors is a complex process that involves several critical stages. Understanding these stages is essential for B2B buyers looking to source high-quality compressors from reliable suppliers.
Material Preparation: How Are Raw Materials Selected?
The manufacturing process begins with the selection and preparation of raw materials. Common materials include cast iron, aluminum, and steel, chosen for their durability and ability to withstand high pressures. Suppliers often conduct preliminary tests on these materials to ensure they meet specified standards, which is crucial for long-term performance. Buyers should inquire about the material specifications and certifications to ensure quality.
Forming: What Techniques Are Used to Shape Components?
Once materials are prepared, the next stage is forming. This typically involves techniques such as casting, machining, and forging. For instance, the compressor housing may be cast from iron, while internal components might be machined to precise tolerances. Advanced suppliers utilize CNC (Computer Numerical Control) machines for high precision, reducing the likelihood of defects. B2B buyers should assess the forming techniques employed by suppliers, as these directly influence the reliability and efficiency of the final product.
Assembly: How Are Components Integrated?
The assembly phase is where the various components of the air compressor come together. This includes integrating the motor, pump, and other mechanical parts. Precision is vital; misalignment can lead to operational failures. Many manufacturers use assembly jigs and fixtures to maintain consistency and accuracy. Buyers should ask potential suppliers about their assembly processes and whether they employ skilled labor or automation, as this impacts the overall quality.
Finishing: What Final Touches Are Applied?
Finishing processes, such as painting, coating, and surface treatment, are crucial for enhancing the durability and aesthetic of the air compressor. These treatments protect against corrosion and wear, extending the equipment’s life. High-quality suppliers often implement stringent finishing standards, so buyers should ensure that the supplier adheres to internationally recognized finishing techniques.
What Quality Assurance Standards Should B2B Buyers Consider?
Quality assurance (QA) is a vital aspect of the manufacturing process for air compressors. Understanding the relevant standards and checkpoints can help buyers ensure they are sourcing reliable products.
Which International Standards Are Relevant for Air Compressors?
International standards such as ISO 9001 for quality management systems are critical in the manufacturing sector. Compliance with ISO 9001 ensures that the supplier maintains a consistent level of quality throughout their processes. Additionally, certifications like CE (Conformité Européenne) for European markets and API (American Petroleum Institute) for specific industrial applications are essential for air compressors. B2B buyers should request copies of these certifications to verify compliance.
What Are the Key Quality Control Checkpoints?
Quality control (QC) involves multiple checkpoints throughout the manufacturing process. The main stages include:
- Incoming Quality Control (IQC): This stage assesses the quality of raw materials before they enter the production line.
- In-Process Quality Control (IPQC): Continuous monitoring during the manufacturing process ensures that any defects are detected and corrected immediately.
- Final Quality Control (FQC): This final inspection checks the completed product against quality standards before shipment.
Buyers should inquire about the QC processes in place at potential suppliers to ensure thorough checks at each stage.
How Can B2B Buyers Verify Supplier Quality Control?
Verifying the quality control measures of an air compressor supplier is essential for mitigating risks associated with product failures. Here are actionable steps B2B buyers can take:
What Audit Practices Should Be Implemented?
Conducting audits is one of the most effective ways to assess a supplier’s quality control measures. Buyers can perform on-site audits or request recent audit reports from third-party organizations. This provides insight into the supplier’s adherence to quality standards and their overall manufacturing capabilities.
How Important Are Quality Reports and Testing Methods?
Suppliers should provide detailed quality reports, including results from various testing methods such as pressure testing, vibration analysis, and noise level assessments. These reports can help buyers gauge the reliability and performance of the air compressors. Understanding the testing methods used—such as destructive and non-destructive testing—is crucial for evaluating product quality.
What Nuances Should International Buyers Be Aware Of?
For international buyers, particularly from regions like Africa, South America, the Middle East, and Europe, there are specific nuances to consider when sourcing air compressors.
How Do Regional Standards Impact Sourcing Decisions?
Different regions may have varying standards and regulations that affect product specifications. For example, air compressors sold in Europe must meet CE certification, while those in the Middle East may need to comply with local standards. Buyers should familiarize themselves with these regulations to ensure compliance and avoid costly delays.
What Are the Challenges in Quality Assurance for International Transactions?
When engaging with suppliers from different countries, language barriers and differences in quality assurance practices can pose challenges. It is advisable for buyers to establish clear communication channels and ensure that all quality expectations are documented. This minimizes misunderstandings and sets a foundation for a successful business relationship.
Conclusion
Understanding the manufacturing processes and quality assurance standards for air compressors is crucial for B2B buyers aiming to make informed sourcing decisions. By focusing on material preparation, forming, assembly, and finishing processes, along with stringent quality control measures, buyers can ensure they partner with reliable suppliers. Verifying certifications, conducting audits, and being aware of regional nuances will further enhance the quality assurance process, ultimately leading to successful procurement outcomes.
Practical Sourcing Guide: A Step-by-Step Checklist for ‘air compressor supplier’
The purpose of this guide is to provide international B2B buyers with a structured approach to sourcing air compressor suppliers. This checklist will help you navigate the complexities of supplier selection, ensuring you make informed decisions that align with your operational needs and quality standards.
Step 1: Define Your Technical Specifications
Clearly articulate the specifications required for your air compressors, including capacity, power source, and intended applications. This step is critical as it sets the foundation for identifying suppliers that can meet your exact needs. Consider factors such as:
– Airflow requirements: Determine the volume of air needed for your operations.
– Operating environment: Assess whether the compressors will be used indoors or outdoors, which can influence durability and design.
Step 2: Research Potential Suppliers
Conduct thorough research to compile a list of potential suppliers. Utilize online directories, industry associations, and trade shows to find reputable manufacturers. This step is vital because a well-researched supplier list can significantly reduce risks. Look for:
– Supplier reputation: Check online reviews and testimonials.
– Market presence: Assess their experience and longevity in the industry.
Step 3: Verify Supplier Certifications
Ensure that potential suppliers hold relevant certifications, such as ISO, CE, or specific industry standards. Certification indicates compliance with international quality and safety standards, which is crucial for minimizing operational risks. Pay attention to:
– Certification validity: Check the expiration dates and renewals.
– Scope of certification: Ensure it covers the specific products you intend to purchase.
Step 4: Request Detailed Proposals
Reach out to shortlisted suppliers and request detailed proposals, including pricing, lead times, and payment terms. This allows for direct comparisons and negotiations. A comprehensive proposal will also clarify the supplier’s understanding of your needs. Be sure to evaluate:
– Customization options: Inquire about the possibility of tailoring products to your specifications.
– After-sales support: Understand the level of service you can expect post-purchase.
Step 5: Evaluate Supplier Capabilities
Assess the manufacturing capabilities and technology used by each supplier. Understanding their production processes can help gauge their ability to deliver quality products consistently. Consider factors such as:
– Production capacity: Ensure they can meet your order volume.
– Quality control measures: Investigate their quality assurance processes to ensure product reliability.
Step 6: Check References and Case Studies
Before finalizing a supplier, check references and ask for case studies from clients in similar industries. This step is essential for validating the supplier’s track record and reliability. Look for:
– Client feedback: Direct insights from other businesses can reveal strengths and weaknesses.
– Project outcomes: Successful case studies can demonstrate the supplier’s capability and expertise.
Step 7: Negotiate Terms and Finalize Contracts
Once you have selected a supplier, engage in negotiations to finalize terms that are favorable for both parties. This is a crucial step to ensure that all aspects of the purchase, including delivery schedules and warranties, are clearly defined. Key elements to negotiate include:
– Pricing structures: Discuss bulk discounts or payment terms.
– Service level agreements (SLAs): Establish expectations regarding delivery timelines and product support.
By following this structured checklist, B2B buyers can confidently navigate the sourcing process for air compressors, ensuring they select the best suppliers to meet their operational needs.
Comprehensive Cost and Pricing Analysis for air compressor supplier Sourcing
What Are the Key Cost Components in Air Compressor Supplier Sourcing?
When sourcing air compressors, understanding the cost structure is crucial for international B2B buyers. The primary cost components include:
-
Materials: The quality and type of materials used significantly affect the overall cost. High-grade materials may increase initial expenses but can lead to lower maintenance costs and longer equipment life.
-
Labor: Labor costs can vary by region. In countries with higher labor rates, such as those in Europe, the production costs might increase. Conversely, sourcing from countries with lower labor costs, like some regions in Africa and South America, can provide savings.
-
Manufacturing Overhead: This includes indirect costs associated with production, such as utilities, rent, and equipment depreciation. Understanding how these costs are allocated can help buyers assess the pricing structure of suppliers.
-
Tooling: Custom tooling for specific air compressor designs can add to the upfront costs. Buyers should evaluate whether the tooling costs are justified based on the expected volume of orders.
-
Quality Control (QC): Implementing rigorous QC processes ensures product reliability and performance. However, it can also add to the overall cost. Buyers should inquire about a supplier’s QC protocols to balance cost and quality effectively.
-
Logistics: Shipping costs can vary significantly based on the distance from the supplier, the mode of transport, and the chosen Incoterms. Buyers should consider these factors when evaluating total costs.
-
Margin: Suppliers typically include a profit margin in their pricing. Understanding standard margins in different markets can provide leverage during negotiations.
How Do Price Influencers Affect Air Compressor Costs?
Several factors can influence the pricing of air compressors:
-
Volume/MOQ: Minimum order quantities (MOQs) often affect pricing. Higher order volumes usually lead to lower per-unit costs. Buyers should negotiate MOQs that align with their needs while keeping costs manageable.
-
Specifications and Customization: Customized air compressors tailored to specific applications can increase costs. Buyers should assess whether the customization is necessary or if standard models suffice.
-
Materials and Quality Certifications: High-quality materials and certifications (like ISO or CE) can increase costs but also enhance reliability and compliance. Buyers should weigh the importance of these factors against their budget constraints.
-
Supplier Factors: The reputation and reliability of the supplier can impact pricing. Well-established suppliers may charge more for their expertise and reliability, while new entrants might offer lower prices to attract business.
-
Incoterms: The agreed-upon Incoterms (International Commercial Terms) dictate the responsibilities of buyers and suppliers regarding shipping, insurance, and tariffs. Understanding these terms can help buyers manage costs effectively.
What Buyer Tips Can Enhance Cost Efficiency in Air Compressor Sourcing?
International B2B buyers can leverage several strategies to optimize their sourcing costs:
-
Effective Negotiation: Building a strong relationship with suppliers can facilitate better negotiation outcomes. Prepare to discuss volume commitments and long-term partnerships to secure favorable pricing.
-
Total Cost of Ownership (TCO): Evaluate the TCO rather than just the purchase price. Consider ongoing maintenance, energy consumption, and potential downtime costs associated with the compressors.
-
Pricing Nuances for Different Regions: Buyers from regions like Africa, South America, the Middle East, and Europe should be aware of regional pricing differences influenced by local market conditions, tariffs, and currency fluctuations.
-
Request for Quotation (RFQ): Sending RFQs to multiple suppliers can provide a clearer picture of market prices and help identify competitive offers.
-
Stay Informed on Market Trends: Keeping abreast of industry trends, technology advancements, and material costs can empower buyers to make informed purchasing decisions.
Disclaimer on Indicative Prices
Prices for air compressors can fluctuate based on market conditions, supplier dynamics, and changes in material costs. Buyers should conduct thorough market research and obtain multiple quotes to ensure they receive competitive pricing tailored to their specific needs.
Alternatives Analysis: Comparing air compressor supplier With Other Solutions
When evaluating options for compressed air solutions, it’s essential to consider various alternatives to traditional air compressor suppliers. Each solution comes with unique features, advantages, and drawbacks that can significantly impact operational efficiency and overall costs. Below, we provide a comprehensive comparison of air compressor suppliers against alternative technologies such as vacuum pumps and gas generators.
Comparison Table of Air Compressor Supplier and Alternatives
Comparison Aspect | Air Compressor Supplier | Vacuum Pumps | Gas Generators |
---|---|---|---|
Performance | High air pressure output for various applications | Limited air pressure but efficient for specific tasks | Produces gas for combustion engines or turbines |
Cost | Moderate to high initial cost, depending on capacity | Generally lower initial cost but may require additional equipment | Higher initial investment but lower operational costs over time |
Ease of Implementation | Requires skilled installation and setup | Easier to install with less technical expertise needed | Complex installation needing specialized knowledge |
Maintenance | Regular maintenance needed for optimal performance | Lower maintenance requirements, fewer moving parts | Requires periodic maintenance for engine and fuel systems |
Best Use Case | Suitable for manufacturing, automotive, and construction sectors | Ideal for applications needing vacuum creation, like food packaging | Best for remote locations or industries needing reliable power sources |
What Are the Advantages and Disadvantages of Vacuum Pumps?
Vacuum pumps serve as a viable alternative to air compressors, particularly in applications requiring vacuum creation rather than compressed air. One significant advantage is their generally lower cost and simpler installation process. They often require less maintenance due to having fewer moving parts, which can lead to cost savings over time. However, vacuum pumps typically cannot achieve the high pressures that air compressors can, limiting their use in specific industrial applications. They are best suited for food packaging, medical applications, and other scenarios where vacuum conditions are essential.
How Do Gas Generators Compare to Air Compressor Suppliers?
Gas generators, particularly those powered by diesel or natural gas, offer a unique alternative for industries that require a steady supply of energy rather than compressed air. Their primary advantage is that they can operate in remote locations without access to the electrical grid, providing a reliable power source for various applications. While they generally have a higher initial investment, their operational costs can be lower in the long run due to fuel efficiency. However, gas generators necessitate complex installations and regular maintenance, which may not be practical for all businesses. They are most beneficial in construction sites, outdoor events, and areas lacking reliable electricity.
How to Choose the Right Solution for Your B2B Needs?
Selecting the right solution depends on your specific operational requirements, budget constraints, and maintenance capabilities. If your industry primarily requires high-pressure air for manufacturing or pneumatic tools, a traditional air compressor supplier may be the best fit. For businesses focusing on vacuum applications, vacuum pumps provide a cost-effective and efficient alternative. Conversely, if your operations are located in remote areas, gas generators can ensure a continuous power supply. Careful consideration of these aspects will lead to a more informed purchasing decision that aligns with your company’s operational goals.
Essential Technical Properties and Trade Terminology for air compressor supplier
What Are the Essential Technical Properties of Air Compressors for B2B Buyers?
When selecting an air compressor, understanding its technical properties is crucial for making informed purchasing decisions. Here are some key specifications that international B2B buyers should consider:
-
Pressure Rating (PSI)
Pressure rating indicates the maximum pressure the compressor can generate, typically measured in pounds per square inch (PSI). For industries such as manufacturing or construction, knowing the required PSI is vital, as it affects the compressor’s ability to power pneumatic tools and machinery. Higher PSI ratings often translate to greater versatility but may also require additional safety measures. -
Flow Rate (CFM)
The flow rate, measured in cubic feet per minute (CFM), determines the volume of air the compressor can deliver at a specific pressure. This metric is essential for assessing whether the compressor can meet the demands of specific tools or processes. A higher CFM is particularly important for applications requiring continuous air supply, such as painting or sandblasting. -
Tank Size
The tank size, expressed in gallons, influences how much compressed air is stored and available for use. Larger tanks can sustain longer periods of operation without the compressor needing to cycle on and off frequently. This can be particularly beneficial in high-demand scenarios, reducing wear on the compressor and improving efficiency. -
Power Source
Air compressors can be powered by electricity, gasoline, or diesel. The choice of power source affects portability, operational costs, and maintenance. Electric compressors are often quieter and suitable for indoor use, while gasoline or diesel models provide greater mobility and are ideal for outdoor applications. -
Material and Build Quality
The materials used in the compressor’s construction, such as aluminum or steel, impact durability, weight, and resistance to corrosion. Buyers should consider the operating environment (e.g., humid or dusty conditions) to ensure the compressor can withstand wear and tear, ultimately affecting its lifespan and maintenance costs.
What Are Common Trade Terms in the Air Compressor Industry?
Understanding industry jargon is just as important as knowing technical specifications. Here are several common terms that B2B buyers should familiarize themselves with:
-
OEM (Original Equipment Manufacturer)
An OEM produces parts or equipment that may be marketed by another company. In the context of air compressors, purchasing from an OEM can ensure compatibility and quality assurance, which is critical for maintaining operational efficiency. -
MOQ (Minimum Order Quantity)
MOQ refers to the smallest number of units a supplier is willing to sell. Understanding MOQ is essential for B2B buyers to ensure they are not overcommitting to a purchase that exceeds their immediate needs, which can tie up capital unnecessarily. -
RFQ (Request for Quotation)
An RFQ is a document sent to suppliers requesting pricing and terms for specific products or services. For air compressor procurement, issuing an RFQ can help buyers compare options and negotiate better terms, ensuring they get the best value for their investment. -
Incoterms (International Commercial Terms)
Incoterms define the responsibilities of buyers and sellers in international shipping, including delivery points and risk allocation. Familiarity with Incoterms helps buyers from regions such as Africa or South America understand their obligations and costs, facilitating smoother transactions. -
Warranty Period
The warranty period specifies the duration during which the supplier is responsible for repairs or replacements due to defects. Knowing the warranty terms is crucial for risk management, as it impacts long-term maintenance costs and operational reliability.
By understanding these technical properties and trade terms, B2B buyers can make informed decisions that align with their operational needs and budget constraints, ultimately ensuring a successful procurement process in the air compressor market.
Navigating Market Dynamics and Sourcing Trends in the air compressor supplier Sector
What Are the Current Market Dynamics and Key Trends in the Air Compressor Supplier Sector?
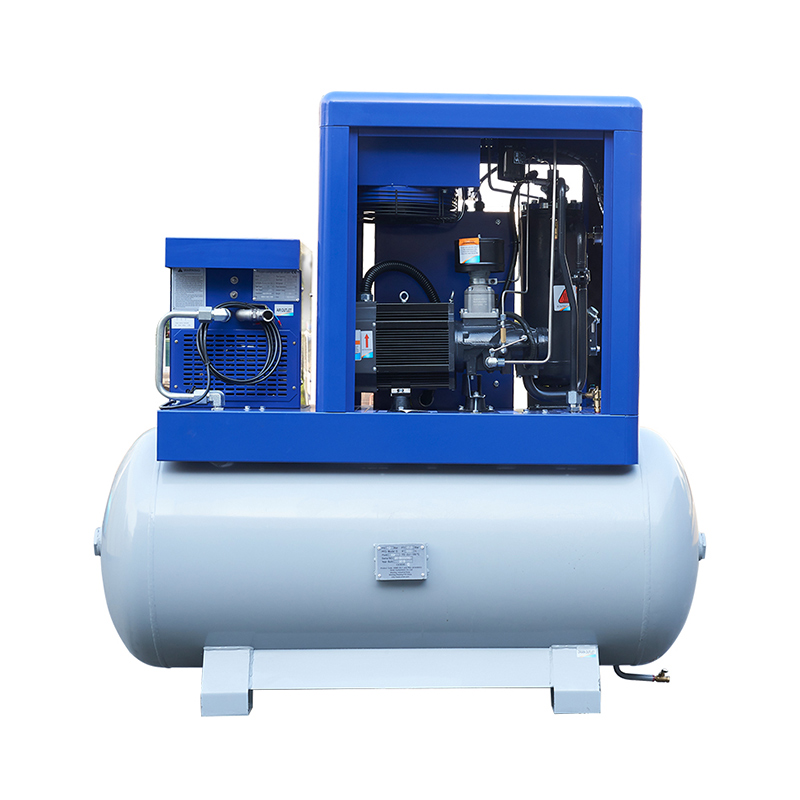
A stock image related to air compressor supplier.
The global air compressor supplier market is experiencing significant transformation driven by technological advancements and changing customer demands. Key drivers include the increasing need for energy-efficient equipment, the growing industrial sector, and the rising adoption of automation in manufacturing processes. As businesses in Africa, South America, the Middle East, and Europe seek to enhance operational efficiency, the demand for advanced air compressors—such as variable speed drive (VSD) compressors—continues to rise. These systems not only reduce energy consumption but also provide better control over pressure and flow rates.
Emerging B2B tech trends like IoT integration are also reshaping the market. Manufacturers are now offering smart air compressors equipped with sensors that provide real-time data analytics, enabling predictive maintenance and reducing downtime. This trend is particularly relevant for international buyers who prioritize reliability and efficiency in their operations. Furthermore, there is a growing emphasis on digital procurement processes, allowing businesses to source air compressors more efficiently through online platforms and marketplaces, enhancing transparency and competition among suppliers.
How Is Sustainability and Ethical Sourcing Influencing the Air Compressor Supplier Market?
Sustainability is becoming a critical factor in the sourcing decisions of international B2B buyers. The environmental impact of air compressors—particularly in terms of energy consumption and greenhouse gas emissions—has prompted manufacturers to adopt greener technologies. Buyers are increasingly seeking suppliers that adhere to sustainability standards and utilize eco-friendly materials. Certifications such as ISO 14001 for environmental management systems and Energy Star ratings for energy efficiency are becoming essential criteria in the supplier selection process.
Ethical sourcing is also gaining traction, with businesses aiming to ensure that their supply chains are free from exploitative practices. This includes verifying that materials used in the production of air compressors are sourced responsibly, minimizing environmental degradation, and promoting fair labor practices. By prioritizing suppliers that demonstrate a commitment to sustainability and ethical standards, international buyers can enhance their corporate social responsibility (CSR) profiles while contributing to a more sustainable future.
How Has the Air Compressor Supplier Market Evolved Over Time?
The air compressor supplier market has undergone significant evolution since its inception in the late 19th century. Initially, air compressors were primarily mechanical devices used in industrial applications. However, as technology advanced, manufacturers began to innovate, leading to the development of electric and portable air compressors, which significantly broadened their applications.
In recent decades, the focus has shifted towards efficiency and sustainability, driven by global energy concerns and regulatory pressures. The integration of digital technologies, such as IoT and AI, has further transformed the landscape, enabling real-time monitoring and optimization of compressor performance. As a result, today’s air compressor systems are not only more efficient but also smarter and more responsive to the needs of modern industries. This historical context is crucial for international buyers looking to understand the product evolution and make informed sourcing decisions.
Frequently Asked Questions (FAQs) for B2B Buyers of air compressor supplier
-
How do I choose the right air compressor supplier for my business needs?
Selecting the right air compressor supplier involves assessing their product range, quality certifications, and industry experience. Look for suppliers with a proven track record in your specific sector, as they will understand your unique requirements. Additionally, consider their customer service responsiveness, technical support, and warranty offerings. Reading reviews and testimonials from other businesses can provide valuable insights into their reliability and service quality. -
What types of air compressors are available for industrial applications?
There are several types of air compressors suitable for industrial use, including rotary screw compressors, reciprocating piston compressors, and centrifugal compressors. Rotary screw compressors are ideal for continuous operation and are highly efficient, while reciprocating compressors are better for intermittent use and lower pressure applications. Centrifugal compressors are used for high-capacity applications requiring constant airflow. Assess your specific air pressure and volume needs to determine the best fit. -
What are the typical minimum order quantities (MOQ) when sourcing air compressors?
Minimum order quantities can vary significantly between suppliers and depend on the type of air compressor. Generally, MOQs may range from one unit for smaller suppliers to several units for larger manufacturers. It is crucial to clarify these terms upfront, as some suppliers may offer flexibility for first-time buyers or bulk purchases. Engaging in discussions about your projected needs can sometimes lead to better negotiation outcomes. -
How can I ensure the quality of air compressors from international suppliers?
To ensure quality, request product certifications such as ISO 9001 or specific industry standards relevant to your region. Conduct thorough due diligence on potential suppliers, including factory visits or third-party inspections. Additionally, seek samples before placing bulk orders and establish clear quality assurance protocols in your purchase agreement. Regular communication during production can also help address any concerns proactively. -
What payment terms should I negotiate with air compressor suppliers?
Payment terms can vary widely, but it is common to negotiate terms such as 30% upfront and the balance before shipment. For larger orders, consider discussing letters of credit or installment payments based on milestones. Always ensure that the terms are clearly documented in your contract to avoid misunderstandings. Understanding the supplier’s payment preferences and regional practices can also help in negotiations. -
What logistics considerations should I keep in mind when sourcing air compressors internationally?
When sourcing internationally, consider shipping methods, customs duties, and delivery timelines. Choose a reliable freight forwarder familiar with your supplier’s region and local regulations. Ensure that your supplier provides all necessary documentation for customs clearance. Additionally, factor in lead times for production and shipping to avoid disruptions in your operations.
-
How can I customize air compressors to meet my specific business requirements?
Many air compressor suppliers offer customization options, including modifications to capacity, pressure settings, and additional features like soundproofing or energy-saving technologies. Communicate your specific needs clearly during the initial discussions, and be prepared to work collaboratively with the supplier’s engineering team to ensure your requirements are met. It’s also beneficial to review previous customization projects they’ve completed for other clients. -
What after-sales support should I expect from an air compressor supplier?
After-sales support is crucial for maintaining operational efficiency. Look for suppliers that offer comprehensive warranties, parts availability, and technical support. This may include routine maintenance services, troubleshooting assistance, and access to spare parts. Establishing a good relationship with your supplier can enhance your support experience, ensuring timely responses to any issues that arise post-purchase.
Important Disclaimer & Terms of Use
⚠️ Important Disclaimer
The information provided in this guide, including content regarding manufacturers, technical specifications, and market analysis, is for informational and educational purposes only. It does not constitute professional procurement advice, financial advice, or legal advice.
While we have made every effort to ensure the accuracy and timeliness of the information, we are not responsible for any errors, omissions, or outdated information. Market conditions, company details, and technical standards are subject to change.
B2B buyers must conduct their own independent and thorough due diligence before making any purchasing decisions. This includes contacting suppliers directly, verifying certifications, requesting samples, and seeking professional consultation. The risk of relying on any information in this guide is borne solely by the reader.
Strategic Sourcing Conclusion and Outlook for air compressor supplier
What Are the Key Takeaways for B2B Buyers in Air Compressor Sourcing?
Strategic sourcing is essential for international B2B buyers seeking air compressor suppliers. By understanding local market dynamics, such as regulations and availability of parts, buyers can make informed decisions that enhance operational efficiency and cost-effectiveness. Additionally, developing relationships with multiple suppliers can mitigate risks associated with supply chain disruptions, ensuring continuous access to high-quality products.
How Can Buyers Prepare for Future Trends in Air Compressors?
As industries evolve, the demand for energy-efficient and environmentally friendly air compressors will increase. Buyers should stay informed about technological advancements and sustainability initiatives in the air compressor market. Investing in suppliers who prioritize innovation and eco-friendly practices will not only meet regulatory demands but also enhance brand reputation in a competitive marketplace.
What Should B2B Buyers Do Next?
For B2B buyers from regions like Africa, South America, the Middle East, and Europe, the time to act is now. Leverage strategic sourcing to foster partnerships with reliable suppliers who can provide tailored solutions. Engage in discussions and negotiations that align with your operational goals, and consider attending industry trade shows to expand your network. The future of air compressor sourcing is promising—embrace it to drive your business forward.