Discover Top Heat Sink Manufacturers: A Complete Sourcing Guide (2025)
Introduction: Navigating the Global Market for Heat Sink Manufacturers
In an era where efficient thermal management is crucial for technological advancement, sourcing heat sink manufacturers presents a significant challenge for international B2B buyers. Whether you’re operating in Africa, South America, the Middle East, or Europe, navigating the complexities of global suppliers can be daunting. This guide serves as a comprehensive resource, covering various types of heat sinks, their applications across industries, and essential considerations for supplier vetting. By understanding the nuances of material selection, manufacturing processes, and cost factors, buyers can streamline their procurement strategies.
This guide empowers international B2B buyers by providing actionable insights that facilitate informed purchasing decisions. From detailed analyses of thermal performance to recommendations on cost-effective sourcing strategies, we aim to equip you with the knowledge needed to engage confidently with heat sink manufacturers. Buyers will gain clarity on what to look for in a supplier, including certifications, production capabilities, and delivery timelines, ensuring that the chosen partner aligns with their operational needs.
As you delve deeper into this guide, expect to discover best practices for negotiating contracts, understanding global market trends, and leveraging regional advantages. In a competitive landscape, being well-informed is not just an advantage—it’s a necessity. Let this guide be your roadmap to navigating the global market for heat sink manufacturers efficiently and effectively.
Understanding Heat Sink Manufacturers Types and Variations
Type Name | Key Distinguishing Features | Primary B2B Applications | Brief Pros & Cons for Buyers |
---|---|---|---|
Passive Heat Sinks | No moving parts; relies on natural convection. | Consumer electronics, LED lighting | Pros: Low maintenance, cost-effective. Cons: Limited cooling capacity in high-performance applications. |
Active Heat Sinks | Incorporates fans or other cooling devices. | Computer CPUs, GPUs, industrial equipment | Pros: Enhanced cooling efficiency. Cons: Higher noise levels, requires power. |
Heat Pipes | Utilizes phase change to transfer heat efficiently. | High-performance computing, aerospace | Pros: Excellent thermal conductivity. Cons: More complex design, can be costly. |
Liquid Cooling Systems | Circulates liquid for heat transfer; often integrates pumps. | Data centers, gaming PCs | Pros: Superior cooling performance. Cons: More expensive, requires maintenance. |
Custom Heat Sinks | Tailored designs for specific applications or environments. | Specialized industrial applications | Pros: Optimized performance for unique needs. Cons: Higher initial investment, longer lead times. |
What Are Passive Heat Sinks and When Should You Use Them?
Passive heat sinks are designed without moving parts, relying solely on natural convection to dissipate heat. They are commonly used in applications like consumer electronics and LED lighting, where space is limited and noise is a concern. When considering passive heat sinks, buyers should evaluate the thermal requirements of their applications, as these solutions may not suffice for high-performance environments where heat generation is significant.
How Do Active Heat Sinks Enhance Cooling?
Active heat sinks integrate fans or other cooling devices to improve airflow and enhance heat dissipation. They are widely used in computer CPUs, GPUs, and various industrial equipment. While active heat sinks provide superior cooling efficiency, buyers should be aware of potential noise levels and the need for a power source. It’s crucial to assess the balance between cooling performance and operational noise when selecting these units.
What Are Heat Pipes and Their Advantages?
Heat pipes are innovative cooling solutions that utilize phase change principles to transfer heat efficiently. They are particularly effective in high-performance computing and aerospace applications, where efficient heat management is critical. The key consideration for buyers is the complexity of the design; while heat pipes offer exceptional thermal conductivity, they can be more expensive and require precise integration into existing systems.
Why Choose Liquid Cooling Systems?
Liquid cooling systems circulate a coolant to transfer heat away from critical components, making them ideal for data centers and high-performance gaming PCs. Their superior cooling performance is a significant advantage, especially in environments where heat generation is high. However, buyers must consider the higher costs and maintenance requirements associated with these systems, as well as the need for proper installation to prevent leaks.
What Are the Benefits of Custom Heat Sinks?
Custom heat sinks are tailored to meet specific requirements of unique applications or environments, providing optimized performance. They are essential in specialized industrial applications where standard solutions may fall short. While custom designs can lead to better efficiency and performance, buyers should factor in the higher initial investment and potentially longer lead times for production. Understanding the specific thermal needs of the application is critical when opting for custom solutions.
Related Video: Extruded Heat sink | Wellste
Key Industrial Applications of Heat Sink Manufacturers
Industry/Sector | Specific Application of Heat Sink Manufacturers | Value/Benefit for the Business | Key Sourcing Considerations for this Application |
---|---|---|---|
Electronics Manufacturing | Thermal management in consumer electronics | Improved product reliability and performance | Material quality, design specifications, and certifications |
Automotive | Cooling systems in electric vehicles | Enhanced efficiency and battery life | Compliance with automotive standards and thermal performance |
Telecommunications | Heat dissipation in telecom equipment | Increased lifespan of devices and reduced downtime | Custom designs and rapid prototyping capabilities |
Renewable Energy | Heat sinks in solar inverters | Enhanced energy conversion efficiency | Environmental certifications and compatibility with existing systems |
Aerospace | Thermal control in avionics systems | Increased safety and reliability of critical systems | Lightweight materials and adherence to aerospace regulations |
How are Heat Sink Manufacturers Used in Electronics Manufacturing?
In the electronics manufacturing sector, heat sinks are critical for effective thermal management in consumer electronics such as smartphones, laptops, and gaming consoles. By dissipating excess heat generated by components like CPUs and GPUs, heat sinks enhance the reliability and performance of these devices. For international B2B buyers, particularly those from Africa and South America, sourcing high-quality heat sinks that meet specific design and material requirements is essential. Buyers should consider the supplier’s ability to provide certifications and the capacity for customization to align with unique product specifications.
What Role Do Heat Sink Manufacturers Play in the Automotive Industry?
In the automotive sector, particularly with the rise of electric vehicles (EVs), heat sinks are used in cooling systems to manage the thermal output of batteries and power electronics. Effective heat dissipation is crucial for maximizing the efficiency and lifespan of these components. B2B buyers in the Middle East and Europe should prioritize suppliers who can demonstrate compliance with automotive industry standards and provide solutions that ensure optimal thermal performance. Additionally, buyers should seek manufacturers with experience in working with lightweight materials to enhance vehicle efficiency.
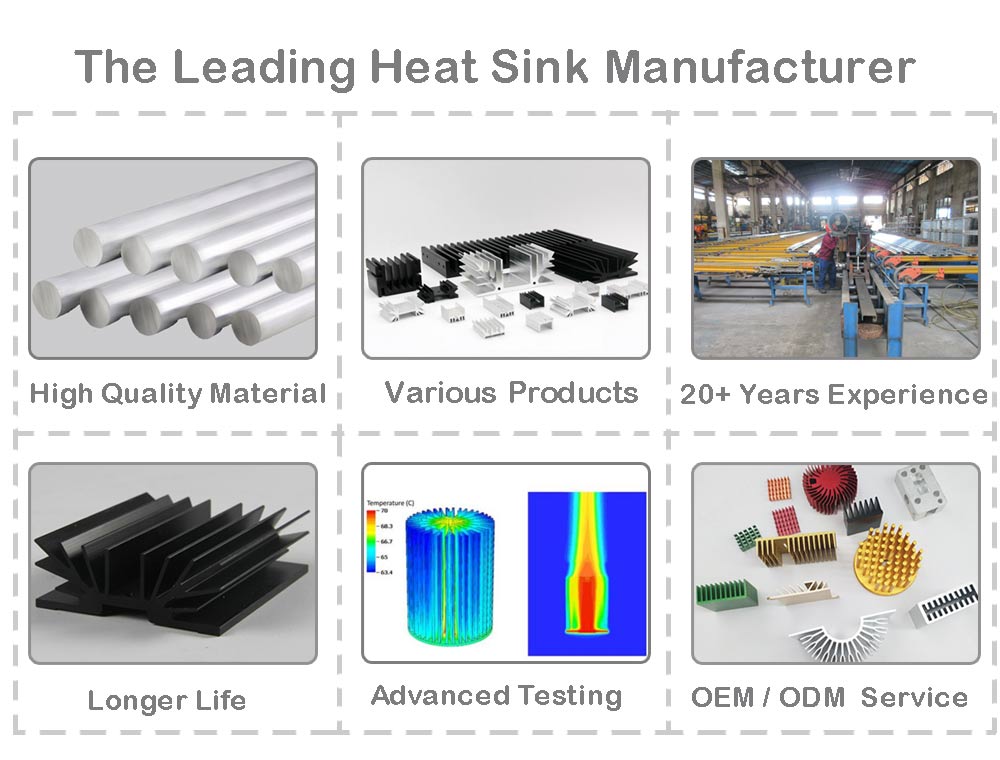
A stock image related to Heat Sink Manufacturers.
Why are Heat Sink Manufacturers Important for Telecommunications?
Telecommunications equipment, such as routers and base stations, generates significant heat during operation. Heat sinks are vital for maintaining optimal operating temperatures, thereby increasing the lifespan of the devices and reducing downtime. For B2B buyers in Europe, especially in Poland, it is important to partner with manufacturers that offer custom designs tailored to specific equipment needs and can provide rapid prototyping services. Ensuring the heat sinks are compatible with existing systems while meeting industry standards is also critical.
How Do Heat Sink Manufacturers Benefit Renewable Energy Applications?
In the renewable energy sector, heat sinks are used in solar inverters to dissipate heat generated during energy conversion processes. This thermal management is essential for improving the efficiency of solar panels and inverters, thereby increasing energy output. B2B buyers from South America looking to invest in renewable energy technologies should seek heat sink manufacturers that hold environmental certifications and can provide solutions that integrate seamlessly with existing systems. Understanding the compatibility of heat sinks with various inverter designs is also vital for optimal performance.
What is the Significance of Heat Sink Manufacturers in Aerospace?
Heat sinks are crucial in aerospace applications, particularly within avionics systems, where they manage heat generated by electronic components. Effective thermal control is necessary to ensure the safety and reliability of critical systems in aircraft. B2B buyers in the aerospace industry must source heat sinks made from lightweight materials that comply with stringent aerospace regulations. Additionally, manufacturers should be able to provide solutions that meet specific thermal performance requirements to ensure the functionality of avionics under various operational conditions.
Related Video: Industrial Heat Exchangers Explained
3 Common User Pain Points for ‘Heat Sink Manufacturers’ & Their Solutions
Scenario 1: Difficulty in Ensuring Thermal Efficiency
The Problem:
Many B2B buyers often face challenges in ensuring that the heat sinks they procure meet specific thermal efficiency requirements. This is particularly crucial for industries such as electronics and automotive, where even a slight increase in temperature can lead to performance degradation or component failure. Buyers may find themselves overwhelmed with the varying specifications offered by different manufacturers, unsure of which products will best suit their applications. This lack of clarity can result in costly delays and potential product recalls if the heat sinks fail to perform as expected.
The Solution:
To effectively address this challenge, buyers should prioritize communication with heat sink manufacturers about their specific thermal management needs. Request detailed thermal performance data, including thermal resistance and flow rate specifications, to ensure compatibility with your systems. Collaborating early in the design process can also help manufacturers tailor their products to meet your specifications. Additionally, consider utilizing thermal simulation software to predict performance under different operating conditions before making a purchase. This proactive approach not only saves time but also helps avoid costly errors in product design and implementation.
Scenario 2: Navigating Quality Assurance Issues
The Problem:
Quality assurance remains a significant pain point for international B2B buyers of heat sinks. In regions such as Africa and South America, where manufacturing standards may vary, buyers often grapple with the risk of receiving subpar products that do not meet their specifications. This can lead to increased warranty claims and damage to brand reputation if faulty heat sinks are integrated into critical systems. The lack of standardized testing and certification processes across manufacturers adds to this complexity.
The Solution:
To mitigate quality assurance issues, buyers should establish clear quality criteria before engaging with manufacturers. Request certifications such as ISO 9001 or industry-specific standards that demonstrate a commitment to quality. Conduct on-site visits or audits to evaluate the manufacturing processes and quality control measures in place. Furthermore, consider sourcing from manufacturers that offer comprehensive product testing and validation reports. This diligence ensures that the products you receive will meet your operational standards, ultimately protecting your business from the repercussions of quality failures.
Scenario 3: Challenges in Customization and Prototyping
The Problem:
Customization is often necessary for heat sink applications, yet many buyers struggle with the limitations of standard products offered by manufacturers. This challenge is particularly pronounced in sectors such as telecommunications and aerospace, where specific geometries and materials are essential for optimal performance. Buyers may find that the lead times for custom designs are lengthy, delaying project timelines and increasing costs.
The Solution:
To overcome customization challenges, it is vital to engage manufacturers that specialize in bespoke solutions. Clearly communicate your requirements, including dimensions, materials, and thermal properties, from the outset. Leverage rapid prototyping technologies, such as 3D printing, which many manufacturers now offer, to create test samples quickly. This allows for real-time adjustments and iterative design improvements before final production. Additionally, forming strategic partnerships with manufacturers who have a robust R&D department can expedite the customization process, ensuring that your specific needs are met efficiently and effectively. By adopting this approach, buyers can significantly reduce lead times and enhance product performance.
Strategic Material Selection Guide for Heat Sink Manufacturers
What Are the Key Properties of Aluminum for Heat Sink Manufacturing?
Aluminum is one of the most popular materials used in heat sink manufacturing due to its excellent thermal conductivity, lightweight nature, and corrosion resistance. With a thermal conductivity rating of approximately 205 W/mK, aluminum efficiently dissipates heat, making it ideal for high-performance applications. Additionally, it has a good strength-to-weight ratio, which is crucial in industries such as automotive and aerospace where weight savings are essential.
Pros and Cons of Aluminum
The advantages of aluminum include its affordability, ease of machining, and ability to be anodized for enhanced corrosion resistance. However, it can be less durable than other metals like copper and may require additional coatings for specific environments. Aluminum is suitable for various applications, including consumer electronics and LED lighting, but may not be the best choice for extreme thermal conditions.
Considerations for International Buyers
For B2B buyers in Africa, South America, the Middle East, and Europe, understanding local regulations and standards is vital. Aluminum heat sinks must comply with standards such as ASTM and DIN, especially in industries like automotive and electronics. Buyers should also consider the availability of aluminum in their region and the associated shipping costs.
How Does Copper Compare as a Material for Heat Sinks?
Copper is renowned for its superior thermal conductivity, rated at around 400 W/mK, which makes it an excellent choice for high-performance heat sinks. Its ability to dissipate heat quickly is unmatched, making it ideal for applications requiring rapid thermal management.
Pros and Cons of Copper
Copper’s primary advantage is its thermal efficiency, which allows for smaller and lighter designs in high-performance applications. However, it is significantly more expensive than aluminum and can be more challenging to manufacture due to its weight and the need for specialized machining processes. Copper is often used in high-end electronics, automotive, and industrial applications where performance is critical.
Considerations for International Buyers
International buyers must consider copper’s higher cost and potential supply chain issues. Compliance with industry standards such as ASTM and JIS is essential, particularly in regions with stringent regulations. Additionally, copper’s susceptibility to corrosion requires buyers to assess the environmental conditions of their applications.
What Role Does Thermal Interface Material (TIM) Play in Heat Sink Performance?
Thermal Interface Materials (TIMs) are critical in enhancing the thermal performance of heat sinks. Common TIMs include silicone-based compounds and phase change materials (PCMs), which improve the thermal contact between the heat sink and the component being cooled.
Pros and Cons of TIMs
The key advantage of TIMs is their ability to fill microscopic gaps that may exist between surfaces, thus improving thermal conductivity. However, they can add complexity to the manufacturing process and may require careful application to avoid performance issues. TIMs are widely used in electronics, automotive, and aerospace applications.
Considerations for International Buyers
B2B buyers should be aware of the various types of TIMs available and their compatibility with different materials. Compliance with international standards is crucial, especially for applications in regulated industries. Buyers should also consider the thermal performance requirements specific to their applications.
What Are the Benefits of Using Composite Materials in Heat Sink Manufacturing?
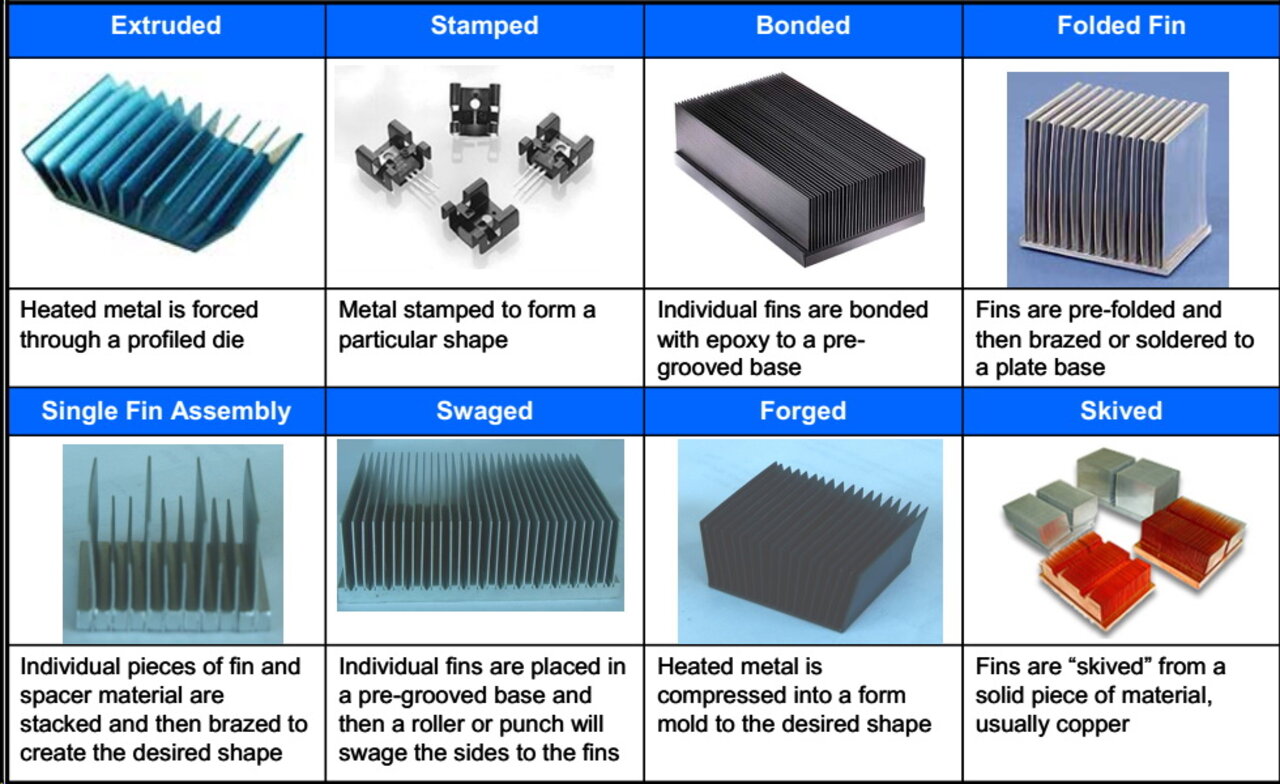
A stock image related to Heat Sink Manufacturers.
Composite materials, such as metal matrix composites (MMCs), combine metals with other materials to enhance thermal conductivity and reduce weight. These materials are increasingly being explored for advanced heat sink applications.
Pros and Cons of Composites
The primary advantage of composites is their tailored properties, which can be optimized for specific applications. However, they can be more expensive and complex to manufacture than traditional materials. Composites are particularly suitable for aerospace and high-performance electronics applications.
Considerations for International Buyers
Buyers should evaluate the availability of composite materials in their region and the associated costs. Understanding the specific performance characteristics and compliance with international standards is critical for ensuring the suitability of composites in their applications.
Summary Table of Material Selection for Heat Sink Manufacturers
Material | Typical Use Case for Heat Sink Manufacturers | Key Advantage | Key Disadvantage/Limitation | Relative Cost (Low/Med/High) |
---|---|---|---|---|
Aluminum | Consumer electronics, LED lighting | Lightweight, good thermal conductivity | Less durable than copper | Medium |
Copper | High-end electronics, automotive | Superior thermal conductivity | High cost, heavier | High |
Thermal Interface Material (TIM) | Electronics, automotive | Improves thermal contact | Adds complexity to manufacturing | Medium |
Composite Materials | Aerospace, high-performance electronics | Tailored properties | Higher cost, complex manufacturing | High |
This guide provides a comprehensive overview of material options for heat sink manufacturers, helping international B2B buyers make informed decisions based on performance, cost, and compliance considerations.
In-depth Look: Manufacturing Processes and Quality Assurance for Heat Sink Manufacturers
What Are the Key Stages in the Manufacturing Process of Heat Sinks?
Manufacturing heat sinks involves several critical stages that ensure optimal performance and quality. The main stages include material preparation, forming, assembly, and finishing. Each stage employs specific techniques tailored to the heat sink’s intended application.
-
Material Preparation: The choice of material is paramount. Common materials for heat sinks include aluminum and copper due to their excellent thermal conductivity. Suppliers must ensure that the raw materials meet the necessary specifications, which often involves checking for impurities and verifying the material’s thermal properties.
-
Forming Techniques: This stage typically employs methods like extrusion, die-casting, and machining.
– Extrusion is widely used for aluminum heat sinks, allowing for continuous profiles with complex shapes, enhancing surface area for heat dissipation.
– Die-Casting is more common for copper heat sinks, providing high precision and a smooth finish.
– Machining processes, such as CNC machining, are essential for achieving tight tolerances and specific geometries. -
Assembly: In some designs, heat sinks are integrated with other components, such as fans or thermal interface materials. This stage may require soldering or the use of thermal adhesives to ensure optimal thermal contact.
-
Finishing: Finally, finishing processes like anodizing or powder coating enhance corrosion resistance and aesthetic appeal while improving thermal performance. Anodizing, in particular, increases the surface area and conductivity of aluminum heat sinks.
What Quality Assurance Standards Should B2B Buyers Be Aware Of?
Quality assurance in heat sink manufacturing is vital for ensuring reliability and performance. International standards such as ISO 9001 are fundamental for establishing a quality management system that governs the manufacturing process. Additionally, industry-specific certifications, such as CE marking for compliance with European standards or API standards for specific industrial applications, are crucial for assuring product quality.
Key Quality Control Checkpoints in the Manufacturing Process
-
Incoming Quality Control (IQC): This initial checkpoint assesses the quality of incoming materials. Suppliers should provide certificates of compliance to verify that materials meet specified standards.
-
In-Process Quality Control (IPQC): Throughout the manufacturing process, continuous monitoring is essential. This includes checking dimensions during machining and ensuring that forming processes adhere to defined specifications.
-
Final Quality Control (FQC): The finished products undergo rigorous testing before shipment. This includes thermal performance tests, dimensional checks, and visual inspections for defects.
How Can B2B Buyers Verify Supplier Quality Control Practices?
For international B2B buyers, especially those from diverse regions like Africa, South America, the Middle East, and Europe, verifying a supplier’s quality control practices is critical. Here are actionable insights on how to do so:
-
Conduct Audits: Regular audits of suppliers’ facilities can provide insights into their quality control processes. Buyers should look for adherence to international standards and the presence of certified quality management systems.
-
Review Quality Reports: Request comprehensive quality reports that detail the results of IQC, IPQC, and FQC. These documents should include data on defect rates, testing methodologies, and corrective actions taken for non-compliance.
-
Third-Party Inspections: Engaging third-party inspection services can offer an unbiased evaluation of the supplier’s quality control processes. These inspections can verify compliance with international standards and provide additional assurance.
What Common Testing Methods Are Used in Heat Sink Quality Assurance?
Heat sink manufacturers employ several testing methods to validate the performance and reliability of their products:
-
Thermal Conductivity Tests: Assessing the material’s ability to conduct heat is crucial. Techniques such as laser flash analysis can provide accurate thermal conductivity measurements.
-
Dimensional Inspection: Using tools like calipers and laser scanners, manufacturers ensure that the heat sinks meet specified dimensions and tolerances.
-
Mechanical Testing: This may include tensile strength tests and thermal cycling tests to evaluate the durability of heat sinks under varying operational conditions.
-
Surface Finish Assessment: Techniques like profilometry can assess the surface roughness and finish quality, which are vital for thermal performance.
What Are the Quality Control Nuances for International B2B Buyers?
When sourcing heat sinks internationally, buyers must be aware of various nuances in quality control that can affect their procurement decisions:
-
Cultural Differences in Quality Standards: Different regions may have varying interpretations of quality standards. Buyers should familiarize themselves with local regulations and expectations to ensure compliance.
-
Certification Validity: Ensure that certifications are not only claimed but are valid and recognized in the buyer’s region. This is especially important in regions with stringent import regulations.
-
Communication and Documentation: Clear communication regarding quality expectations is essential. Buyers should establish a robust documentation process that includes quality agreements and specifications.
-
Post-Sale Support: Understanding the supplier’s post-sale support for quality issues is critical. Ensure that they have a mechanism for addressing defects or performance failures after the sale.
Conclusion
For international B2B buyers, particularly those from Africa, South America, the Middle East, and Europe, understanding the manufacturing processes and quality assurance practices of heat sink manufacturers is essential for making informed purchasing decisions. By focusing on material preparation, forming techniques, and thorough quality control checkpoints, buyers can ensure they are selecting reliable suppliers that meet their specific needs. Engaging in thorough verification and testing processes will further enhance confidence in the products sourced.
Practical Sourcing Guide: A Step-by-Step Checklist for ‘Heat Sink Manufacturers’
This practical sourcing guide is designed to assist international B2B buyers, particularly from regions like Africa, South America, the Middle East, and Europe, in effectively procuring heat sinks from reliable manufacturers. By following this step-by-step checklist, you can ensure that your sourcing process is thorough and efficient.
Step 1: Define Your Technical Specifications
Clearly outlining your technical requirements is essential for effective sourcing. This includes the material type, dimensions, thermal performance, and any specific certifications needed for your application. By having a detailed specification, you can better communicate your needs to potential suppliers and evaluate their offerings against your criteria.
Step 2: Research and Shortlist Potential Manufacturers
Conduct thorough research to identify reputable heat sink manufacturers. Look for companies that specialize in your required specifications and have a proven track record. Utilize online directories, industry trade shows, and recommendations from industry peers to compile a shortlist of potential suppliers.
Step 3: Evaluate Potential Suppliers
Before committing, it’s crucial to vet suppliers thoroughly. Request company profiles, case studies, and references from buyers in a similar industry or region. Look for the following:
– Experience: How long has the manufacturer been in business?
– Clientele: Do they have experience supplying similar companies or industries?
– Quality Assurance: What quality control measures do they implement?
Step 4: Verify Certifications and Compliance
Ensure that your chosen manufacturers meet relevant industry standards and certifications. This may include ISO certifications, RoHS compliance, or specific regional regulations. Verifying these credentials is vital to guarantee product quality and compliance with local laws, especially in regulated markets.
Step 5: Request Samples and Conduct Testing
Before finalizing your order, request samples to evaluate the product quality. Conduct performance tests to ensure that the heat sinks meet your thermal management requirements. Testing samples can help identify potential issues early on and validate the manufacturer’s claims about their products.
Step 6: Negotiate Terms and Conditions
Once you have selected a manufacturer, engage in negotiations regarding pricing, delivery schedules, payment terms, and warranties. It’s important to clarify all aspects of the agreement to avoid misunderstandings later. Consider including penalties for late delivery or non-compliance to ensure accountability.
Step 7: Establish Clear Communication Channels
Effective communication is key to a successful partnership. Establish clear channels for ongoing communication with your supplier to facilitate updates, feedback, and issue resolution. Regular check-ins can help maintain a strong relationship and ensure that any potential problems are addressed promptly.
By following this checklist, B2B buyers can streamline their sourcing process for heat sinks, ensuring they partner with manufacturers who meet their technical needs and quality expectations.
Comprehensive Cost and Pricing Analysis for Heat Sink Manufacturers Sourcing
What Are the Key Cost Components for Heat Sink Manufacturers?
Understanding the cost structure of heat sink manufacturing is critical for international B2B buyers. The primary cost components include:
-
Materials: The choice of materials significantly impacts the overall cost. Common materials for heat sinks include aluminum and copper. Aluminum is generally more cost-effective, while copper offers superior thermal conductivity but at a higher price point.
-
Labor: Labor costs can vary widely depending on the manufacturing location. Regions with lower labor costs, such as parts of Asia or Eastern Europe, may offer competitive pricing. However, labor quality and skill level should not be compromised for cost savings.
-
Manufacturing Overhead: This includes fixed costs such as rent, utilities, and equipment maintenance. Efficient manufacturers will have lower overhead costs, which can positively influence pricing.
-
Tooling: Initial tooling costs can be substantial, especially for custom designs. Buyers should consider these costs when assessing quotes from suppliers.
-
Quality Control (QC): Implementing stringent QC processes is essential for ensuring product reliability. Quality assurance procedures may add to the manufacturing cost but are crucial for maintaining standards.
-
Logistics: Shipping and handling costs can vary based on the supplier’s location and the shipping terms agreed upon (Incoterms). Buyers should factor in these costs when calculating the total expense.
-
Margin: Manufacturers typically include a profit margin in their pricing, which can fluctuate based on market demand and competition.
What Influences Pricing for Heat Sink Manufacturers?
Several factors can influence the pricing structure of heat sinks:
-
Volume/MOQ (Minimum Order Quantity): Larger orders often lead to reduced unit costs. Buyers should negotiate for favorable terms based on their purchasing volume.
-
Specifications and Customization: Customized heat sinks designed for specific applications may incur additional costs. Buyers should clearly outline their requirements to receive accurate quotes.
-
Materials and Quality Certifications: Higher-grade materials and certifications (like RoHS or ISO) can increase costs but may be necessary for certain industries. Buyers should weigh the benefits against the costs.
-
Supplier Factors: Supplier reputation, reliability, and production capacity can affect pricing. Established suppliers may charge a premium due to their experience and proven track record.
-
Incoterms: Understanding the agreed shipping terms is vital. Incoterms dictate who is responsible for shipping costs, insurance, and liability, impacting the final price.
How Can Buyers Optimize Costs When Sourcing Heat Sinks?
B2B buyers can implement several strategies to optimize costs:
-
Negotiation: Always negotiate pricing, especially when placing large orders. Suppliers may offer discounts for long-term contracts or larger volumes.
-
Focus on Total Cost of Ownership (TCO): Evaluate not just the purchase price but also the long-term costs associated with the product. Consider factors like energy efficiency and maintenance requirements.
-
Research and Compare Suppliers: Conduct thorough research to compare multiple suppliers. Request samples to assess quality before making bulk purchases.
-
Understand Pricing Nuances for International Transactions: Buyers from Africa, South America, the Middle East, and Europe should be aware of currency fluctuations, import duties, and other regional factors that can influence pricing.
-
Leverage Technology for Communication: Utilize digital platforms for clear communication with suppliers. This can help clarify specifications and reduce misunderstandings that may lead to additional costs.
Conclusion
Understanding the cost structure and pricing influences in the heat sink manufacturing sector is essential for international B2B buyers. By analyzing these components and employing strategic purchasing practices, buyers can make informed decisions that align with their operational needs while optimizing costs. Always remember to approach sourcing with a comprehensive view of both immediate and long-term expenses to ensure the best value.
Alternatives Analysis: Comparing Heat Sink Manufacturers With Other Solutions
Exploring Alternatives to Heat Sink Manufacturers
In the realm of thermal management, heat sinks are widely recognized for their ability to dissipate heat from electronic components effectively. However, B2B buyers should consider alternative solutions that may offer comparable or even superior performance in specific applications. This section will compare heat sinks with two alternative technologies: Liquid Cooling Systems and Thermoelectric Coolers (TECs).
Comparison Table of Heat Sink Manufacturers and Alternatives
Comparison Aspect | Heat Sink Manufacturers | Liquid Cooling Systems | Thermoelectric Coolers (TECs) |
---|---|---|---|
Performance | High efficiency for passive cooling; limited by ambient temperature. | Superior cooling performance; can maintain low temperatures under high loads. | Moderate cooling, effective for localized cooling but less efficient at scale. |
Cost | Generally low initial cost; requires minimal components. | Higher upfront costs due to pumps, radiators, and coolant. | Moderate cost; efficiency can lead to savings over time but may require specialized components. |
Ease of Implementation | Simple to install; often requires minimal technical expertise. | Complex installation; requires knowledge of fluid dynamics and system integration. | Relatively simple to integrate; needs careful power management. |
Maintenance | Low maintenance; periodic cleaning may be required. | Requires regular maintenance of pumps and coolant levels. | Low maintenance; solid-state devices with no moving parts. |
Best Use Case | Ideal for standard electronics where space is limited and passive cooling is sufficient. | Best for high-performance applications like gaming PCs or servers. | Suitable for precise temperature control in specific components, such as lasers or CPUs. |
What Are the Advantages and Disadvantages of Liquid Cooling Systems?
Liquid cooling systems utilize coolant to absorb heat from components and dissipate it through radiators.
Pros:
– High Efficiency: They can handle higher thermal loads than traditional heat sinks, making them ideal for high-performance applications.
– Space-Saving: The ability to use smaller components allows for more compact designs.
Cons:
– Higher Cost: The initial investment is significantly higher due to the complexity of the system.
– Maintenance Needs: They require regular upkeep, which may not be feasible for all organizations, especially those with limited technical resources.
How Do Thermoelectric Coolers (TECs) Compare to Heat Sink Solutions?
Thermoelectric coolers are solid-state devices that use the Peltier effect to create a heat flux between the junction of two different materials.
Pros:
– Localized Cooling: They provide precise temperature control, which is beneficial for sensitive electronics.
– No Moving Parts: This results in higher reliability and lower maintenance compared to mechanical systems.
Cons:
– Efficiency Issues: TECs are less efficient than liquid cooling systems and often require additional heat sinks to dissipate heat effectively.
– Power Consumption: They can consume significant power, which may not be ideal for all applications.
How Can B2B Buyers Choose the Right Cooling Solution?
When selecting a cooling solution, B2B buyers should assess their specific application requirements, including thermal load, space constraints, and budget. Heat sinks are excellent for standard applications where passive cooling suffices. Conversely, liquid cooling systems are better suited for high-performance environments, while TECs can be ideal for niche applications requiring precise temperature control. Evaluating these factors will enable buyers to make informed decisions that align with their operational needs and objectives.
Essential Technical Properties and Trade Terminology for Heat Sink Manufacturers
What Are the Key Technical Properties of Heat Sinks That B2B Buyers Should Know?
When considering heat sinks for electronic applications, understanding their technical properties is crucial for making informed purchasing decisions. Here are some essential specifications:
1. Material Grade
The choice of material significantly influences the heat sink’s performance. Common materials include aluminum, copper, and their alloys. Aluminum is lightweight and offers good thermal conductivity, making it a popular choice for many applications. Copper, while heavier and more expensive, provides superior thermal conductivity. Buyers should assess the material properties based on their project’s heat dissipation requirements and budget constraints.
2. Tolerance
Tolerance refers to the permissible limit of variation in a physical dimension. In heat sink manufacturing, tight tolerances ensure that components fit correctly within electronic devices, which is critical for maintaining thermal efficiency. For instance, a tolerance of ±0.1 mm can be vital in applications where precision is paramount. Buyers should inquire about the tolerances offered by manufacturers to ensure compatibility with their designs.
3. Thermal Resistance
Thermal resistance measures the ability of a heat sink to dissipate heat. It is typically expressed in degrees Celsius per watt (°C/W). Lower thermal resistance indicates better performance in transferring heat away from components. When evaluating suppliers, B2B buyers should look for thermal resistance values that meet or exceed their system requirements to prevent overheating.
4. Surface Finish
The surface finish affects both thermal performance and aesthetic appeal. Common finishes include anodized, painted, or bare metal. Anodizing can enhance thermal performance by increasing surface area and improving heat dissipation. Buyers should consider how the surface finish aligns with both functional requirements and the visual design of their products.
5. Size and Form Factor
The dimensions and shape of a heat sink are crucial for fitting into designated spaces within electronic devices. Buyers should provide manufacturers with precise specifications regarding size and form factor to ensure that the heat sinks will fit seamlessly into their applications.
Which Trade Terminology Should B2B Buyers Understand When Purchasing Heat Sinks?
Understanding industry jargon can facilitate smoother communication with suppliers. Here are some common terms:
1. OEM (Original Equipment Manufacturer)
OEM refers to a company that produces parts or equipment that may be marketed by another manufacturer. For B2B buyers, partnering with OEMs can ensure that heat sinks are designed specifically for their products, enhancing compatibility and performance.
2. MOQ (Minimum Order Quantity)
MOQ indicates the minimum number of units a manufacturer is willing to produce for an order. This is crucial for buyers to know, as it can affect budgeting and inventory management. Understanding MOQ can help in negotiating with suppliers and ensuring that production runs align with demand.
3. RFQ (Request for Quotation)
An RFQ is a formal process where buyers request price quotes from suppliers for specific quantities and types of products. This process is essential for B2B buyers to gather competitive pricing and terms before making purchasing decisions.
4. Incoterms
Incoterms, short for International Commercial Terms, define the responsibilities of buyers and sellers in international trade. Understanding these terms is vital for B2B buyers to clarify shipping, liability, and insurance responsibilities. This knowledge can help prevent misunderstandings and ensure smoother transactions.
5. Lead Time
Lead time refers to the time taken from placing an order to receiving the product. For heat sink manufacturers, this can vary based on complexity and order size. B2B buyers should consider lead times when planning production schedules to avoid delays in their projects.
By familiarizing themselves with these technical properties and trade terminologies, B2B buyers can make more strategic decisions and foster better relationships with heat sink manufacturers.
Navigating Market Dynamics and Sourcing Trends in the Heat Sink Manufacturers Sector
What Are the Current Market Dynamics in the Heat Sink Manufacturers Sector?
The global market for heat sinks is being driven by advancements in electronics, the rising demand for thermal management solutions, and the increasing emphasis on energy efficiency across various industries. Notably, sectors such as automotive, telecommunications, and consumer electronics are witnessing a surge in the need for efficient thermal management systems. Emerging trends indicate a shift towards lightweight materials and compact designs, which cater to the growing demand for miniaturization in devices.
International B2B buyers, particularly from Africa, South America, the Middle East, and Europe, should be aware of the competitive landscape that includes both established manufacturers and innovative startups. The market is also witnessing an increasing trend towards customization, where manufacturers are tailoring heat sink solutions to meet specific client needs. Buyers should prioritize suppliers who demonstrate flexibility and responsiveness to design requirements. Additionally, the integration of advanced technologies such as 3D printing is transforming sourcing processes, enabling faster prototyping and production.
How Is Sustainability Shaping Sourcing Trends in Heat Sink Manufacturing?
Sustainability is becoming a crucial factor in the sourcing decisions of B2B buyers in the heat sink manufacturing sector. The environmental impact of manufacturing processes, including energy consumption and material waste, is under scrutiny. Buyers are increasingly favoring suppliers who implement sustainable practices, such as using recyclable materials and minimizing carbon footprints.
The importance of ethical supply chains cannot be overstated, particularly as global consumers demand transparency and accountability from manufacturers. Buyers should look for heat sink manufacturers that have obtained ‘green’ certifications, such as ISO 14001, which demonstrates commitment to environmental management. Additionally, sourcing materials that are environmentally friendly—like aluminum and copper that can be recycled—can enhance a company’s sustainability profile. By prioritizing ethical sourcing, B2B buyers can not only comply with regulations but also appeal to a growing segment of eco-conscious consumers.
What Is the Historical Context of Heat Sink Manufacturing?
The evolution of heat sink manufacturing dates back to the mid-20th century, when the rapid growth of electronics necessitated effective thermal management solutions. Initially, heat sinks were simple metal blocks, but as technology advanced, manufacturers began to innovate with designs that improved heat dissipation and efficiency. The introduction of materials such as aluminum and copper significantly enhanced performance, making heat sinks more effective in various applications.
Over the years, the industry has adapted to meet the demands of smaller, more powerful electronic devices. This evolution has led to the development of specialized heat sinks tailored for specific applications, such as high-performance computing and electric vehicles. Understanding this historical context enables B2B buyers to appreciate the technological advancements and market dynamics that shape today’s sourcing strategies in the heat sink manufacturing sector.
Frequently Asked Questions (FAQs) for B2B Buyers of Heat Sink Manufacturers
- How do I choose the right heat sink manufacturer for my specific needs?
Choosing the right heat sink manufacturer involves assessing several factors. Start by identifying your technical requirements, such as size, material, and thermal performance. Research potential suppliers to evaluate their expertise and experience in producing heat sinks for your industry. Request samples to test quality and performance, and consider their production capabilities, lead times, and certifications. Additionally, check customer reviews and testimonials to gauge reliability and customer support.
-
What are the common customization options available from heat sink manufacturers?
Most heat sink manufacturers offer a range of customization options to meet specific customer needs. This may include alterations in size, shape, material, and surface treatments. Manufacturers can also provide tailored thermal performance specifications, such as fin designs or integrated features. Ensure you communicate your requirements clearly and inquire about the feasibility of customizations during the initial discussions to avoid potential delays. -
What is the typical minimum order quantity (MOQ) for heat sinks, and how does it vary by supplier?
The minimum order quantity (MOQ) for heat sinks can significantly vary depending on the manufacturer and the complexity of the design. Generally, MOQs can range from 100 to 1,000 units for standard products. For customized designs, the MOQ may be higher due to the setup costs involved in production. It’s crucial to discuss your needs with potential suppliers and understand their MOQ policies to align with your production schedules. -
What payment terms should I expect when sourcing heat sinks internationally?
Payment terms for international heat sink purchases can vary widely among manufacturers. Common terms include payment upfront, partial payment upon order confirmation, and balance upon delivery. Some suppliers may offer net payment terms (30, 60, or 90 days), especially for established relationships. Always clarify the payment terms before finalizing the order, and consider using secure payment methods like letters of credit for added protection. -
How can I ensure quality assurance when sourcing heat sinks from overseas manufacturers?
To ensure quality assurance, start by selecting manufacturers with established certifications like ISO 9001. Request detailed specifications and material certifications for the heat sinks you are sourcing. Consider conducting factory audits or hiring third-party inspection services to verify compliance with your quality standards. Additionally, establish clear communication channels for ongoing quality feedback throughout the production process. -
What logistical challenges should I consider when importing heat sinks from abroad?
When importing heat sinks, consider logistical factors such as shipping costs, customs duties, and lead times. Evaluate the shipping methods available, including air freight for faster delivery or sea freight for cost savings. Understand the import regulations in your country to ensure compliance and avoid delays. Building a relationship with a reliable logistics partner can help streamline the import process and mitigate potential challenges. -
How do I evaluate the reliability of a heat sink supplier?
Evaluating the reliability of a heat sink supplier involves researching their track record, financial stability, and customer service. Look for suppliers with a history of on-time delivery and consistent product quality. Request references from other clients, particularly those in your industry, and check online reviews or industry ratings. Engaging in direct communication about your specific needs can also provide insights into their responsiveness and professionalism. -
What role does thermal analysis play in the selection of heat sinks for my application?
Thermal analysis is crucial in selecting the right heat sink for your application, as it helps predict thermal performance under specific operating conditions. Conducting thermal simulations can reveal the effectiveness of various designs and materials in dissipating heat. Collaborate with your heat sink manufacturer to perform these analyses early in the design phase, ensuring that the selected heat sink meets your thermal management needs effectively.
Important Disclaimer & Terms of Use
⚠️ Important Disclaimer
The information provided in this guide, including content regarding manufacturers, technical specifications, and market analysis, is for informational and educational purposes only. It does not constitute professional procurement advice, financial advice, or legal advice.
While we have made every effort to ensure the accuracy and timeliness of the information, we are not responsible for any errors, omissions, or outdated information. Market conditions, company details, and technical standards are subject to change.
B2B buyers must conduct their own independent and thorough due diligence before making any purchasing decisions. This includes contacting suppliers directly, verifying certifications, requesting samples, and seeking professional consultation. The risk of relying on any information in this guide is borne solely by the reader.
Strategic Sourcing Conclusion and Outlook for Heat Sink Manufacturers
In navigating the complexities of global supply chains, strategic sourcing emerges as a pivotal component for heat sink manufacturers. By leveraging a diverse supplier base, companies can enhance their resilience against market fluctuations and ensure consistent product quality. Buyers from Africa, South America, the Middle East, and Europe should prioritize partnerships that offer not only competitive pricing but also innovation and flexibility in production capabilities.
Understanding the specific thermal management needs of various applications—ranging from consumer electronics to industrial machinery—will empower buyers to make informed decisions. Engaging with manufacturers that demonstrate a commitment to sustainability and advanced engineering practices can further enhance product efficiency and reduce environmental impact.
As the demand for high-performance thermal solutions continues to rise, now is the time for international B2B buyers to reassess their sourcing strategies. By actively seeking out manufacturers that prioritize quality, reliability, and technological advancement, businesses can position themselves for success in a rapidly evolving marketplace. Take the next step in optimizing your supply chain—connect with heat sink manufacturers today to explore tailored solutions that meet your unique requirements.