Unlock Savings: The Ultimate Guide to Door Manufacturers (2025)
Introduction: Navigating the Global Market for door manufacturer
Navigating the global market for door manufacturers can be a daunting task for international B2B buyers, particularly when sourcing quality products that meet specific regional standards and customer expectations. In an era where the demand for durable, aesthetically pleasing, and energy-efficient doors is on the rise, understanding the nuances of different types, applications, and materials is essential. This guide serves as a comprehensive resource, addressing key challenges such as supplier vetting, pricing strategies, and compliance with local regulations across diverse markets, including Africa, South America, the Middle East, and Europe.
By leveraging this guide, B2B buyers can make informed purchasing decisions that enhance their supply chain efficiency. It delves into various door types—from residential to commercial solutions—and explores innovative designs tailored to meet the unique architectural styles of different regions. Furthermore, the guide emphasizes the importance of establishing robust relationships with manufacturers, ensuring that buyers can navigate potential pitfalls and secure favorable terms.
In summary, this resource empowers international B2B buyers by providing actionable insights and a strategic framework for sourcing high-quality doors. By understanding market dynamics and supplier capabilities, businesses can optimize their procurement processes and ultimately drive growth in their respective markets.
Understanding door manufacturer Types and Variations
Type Name | Key Distinguishing Features | Primary B2B Applications | Brief Pros & Cons for Buyers |
---|---|---|---|
Solid Wood Doors | Made from solid timber; high durability; aesthetic appeal | High-end residential, commercial offices | Pros: Excellent insulation, customizable; Cons: Higher cost, may warp in humid conditions |
Hollow Core Doors | Lightweight; constructed with a honeycomb core; cost-effective | Interior spaces in commercial and residential buildings | Pros: Affordable, lightweight; Cons: Lower durability, less sound insulation |
Steel Doors | Made from steel; high security; fire-resistant options available | Industrial, commercial entry points, security applications | Pros: Extremely durable, fire-resistant; Cons: Prone to rust, limited aesthetic options |
Fiberglass Doors | Insulated core; resistant to dents and scratches; versatile designs | Commercial and residential exteriors, entry doors | Pros: Energy-efficient, low maintenance; Cons: Can be expensive compared to wood |
Bi-fold and Sliding Doors | Space-saving design; contemporary aesthetics; large openings | Modern residential, retail spaces, and showrooms | Pros: Maximizes natural light, enhances space; Cons: Higher installation complexity, requires more maintenance |
What Are the Characteristics of Solid Wood Doors?
Solid wood doors are crafted from solid timber, providing exceptional strength and durability. They are often chosen for their aesthetic appeal, adding a touch of elegance to both residential and commercial properties. These doors are well-suited for high-end applications where insulation and soundproofing are essential. When purchasing solid wood doors, B2B buyers should consider the wood type, finish options, and potential for warping in humid environments, which can affect long-term performance.
How Do Hollow Core Doors Fit into B2B Applications?
Hollow core doors are constructed with a lightweight honeycomb core, making them an economical choice for interior spaces. They are primarily used in commercial and residential buildings where cost-effectiveness is a priority. While hollow core doors provide adequate functionality, buyers should assess their durability and sound insulation properties, as they may not be suitable for high-traffic or noise-sensitive environments.
Why Choose Steel Doors for Security Needs?
Steel doors are engineered for maximum security, making them ideal for industrial and commercial applications. They offer robust protection against forced entry and can be fire-resistant, providing added safety. B2B buyers should consider the door’s thickness, insulation properties, and rust resistance when selecting steel doors. While they offer superior durability, the aesthetic options may be limited compared to wood or fiberglass alternatives.
What Are the Benefits of Fiberglass Doors for Businesses?
Fiberglass doors are increasingly popular due to their energy efficiency and low maintenance requirements. They are designed with an insulated core, making them suitable for both commercial and residential exteriors. Buyers should evaluate the door’s resistance to dents and scratches, as well as its overall cost-effectiveness compared to traditional wood options. Fiberglass doors provide a balance of durability and aesthetic appeal, making them a versatile choice for many businesses.
How Do Bi-fold and Sliding Doors Enhance Space?
Bi-fold and sliding doors are designed to maximize natural light and create seamless transitions between indoor and outdoor spaces. They are particularly favored in modern residential and retail environments. B2B buyers should consider the installation complexity and maintenance requirements when choosing these doors, as they may require more frequent upkeep than traditional door types. Their contemporary design can significantly enhance the aesthetic appeal of a space, making them a valuable investment for businesses looking to impress customers.
Related Video: Automatic Roll Up High Speed Door | Avians | Best High Speed Door Manufacturer
Key Industrial Applications of door manufacturer
Industry/Sector | Specific Application of Door Manufacturer | Value/Benefit for the Business | Key Sourcing Considerations for this Application |
---|---|---|---|
Commercial Real Estate | High-security entrance doors for office buildings | Enhanced security and aesthetic appeal | Compliance with local building codes and security standards |
Healthcare Facilities | Hygienic, antimicrobial doors for hospitals | Improved patient safety and reduced infection rates | Material certifications and ease of cleaning |
Hospitality Industry | Soundproof doors for hotels and restaurants | Enhanced guest experience and privacy | Customization options and durability under high traffic |
Retail Sector | Automatic sliding doors for shopping malls | Increased accessibility and energy efficiency | Energy ratings and maintenance requirements |
Industrial Manufacturing | Heavy-duty industrial doors for factories | Improved safety and operational efficiency | Load capacity and weather resistance specifications |
How Are High-Security Entrance Doors Used in Commercial Real Estate?
In commercial real estate, high-security entrance doors are essential for protecting sensitive information and assets. These doors often incorporate advanced locking systems and materials designed to withstand forced entry. International buyers, particularly in regions like Africa and the Middle East, must consider local security regulations and building codes when sourcing these doors. Additionally, aesthetics play a role; doors should align with the architectural vision of the office while providing the necessary security features.
What Are the Benefits of Hygienic Doors in Healthcare Facilities?
Hygienic, antimicrobial doors are crucial in healthcare settings, such as hospitals and clinics, where cleanliness is paramount. These doors help minimize the risk of healthcare-associated infections (HAIs) by inhibiting the growth of bacteria and viruses. Buyers in South America and Europe should prioritize sourcing doors that are certified for antimicrobial properties and easy to clean. This ensures compliance with health regulations and enhances patient safety, a top priority in the healthcare sector.
Why Are Soundproof Doors Important in the Hospitality Industry?
In the hospitality industry, soundproof doors significantly enhance the guest experience by providing privacy and reducing noise from hallways and outside environments. Hotels and restaurants can benefit from these specialized doors, which create a more inviting atmosphere. For B2B buyers in Europe, sourcing soundproof doors requires a focus on acoustic performance ratings and design compatibility with existing structures. Durability is also vital, as these doors must withstand frequent use.
How Do Automatic Sliding Doors Benefit the Retail Sector?
Automatic sliding doors are increasingly popular in retail environments, such as shopping malls and grocery stores, due to their convenience and accessibility. These doors facilitate a seamless entry and exit experience for customers, improving foot traffic and overall sales. International buyers, especially from Europe and South America, should consider energy efficiency ratings when sourcing these doors, as they contribute to lower operational costs. Maintenance requirements and the availability of spare parts are also critical factors in the sourcing process.
What Role Do Heavy-Duty Industrial Doors Play in Manufacturing?
Heavy-duty industrial doors are vital in manufacturing settings, providing security and durability against harsh conditions. These doors often feature high-load capacities and weather-resistant materials, making them suitable for factories and warehouses. Buyers from Africa and the Middle East should pay attention to load specifications and compliance with safety standards when sourcing these doors. The right heavy-duty doors not only enhance safety but also improve operational efficiency, making them a valuable investment for manufacturers.
Related Video: Ozone Premium Plus Automatic Sliding Door System | Installation Guide
3 Common User Pain Points for ‘door manufacturer’ & Their Solutions
Scenario 1: Supply Chain Disruptions in Door Manufacturing
The Problem:
B2B buyers often face significant challenges due to supply chain disruptions, which can delay the delivery of doors and related components. This is particularly problematic for construction projects in regions like Africa and the Middle East, where timely delivery is crucial for maintaining project schedules. Delays can lead to increased labor costs, contract penalties, and strained relationships with clients and contractors. Buyers may also struggle with the unpredictability of lead times, making it difficult to plan effectively.
The Solution:
To mitigate supply chain issues, B2B buyers should prioritize building strong relationships with multiple door manufacturers and suppliers. This diversification can safeguard against disruptions by providing alternative sourcing options. Additionally, implementing a Just-In-Time (JIT) inventory system can help manage stock levels efficiently while ensuring that materials arrive as needed. Buyers should also engage in open communication with manufacturers regarding their production schedules and potential delays. Regularly reviewing supply chain performance and establishing key performance indicators (KPIs) can help identify risks early, allowing buyers to make informed decisions quickly.
Scenario 2: Difficulty in Customization and Specifications
The Problem:
Many B2B buyers encounter challenges when it comes to customizing doors to meet specific project requirements. This is particularly relevant in markets like South America and Europe, where architectural styles and building codes can vary greatly. Buyers may find it difficult to communicate their needs effectively, leading to mismatched expectations and the delivery of unsuitable products. In some cases, manufacturers may not have the capability to produce doors that meet specific aesthetic or functional requirements, resulting in additional costs and delays.
The Solution:
To navigate customization challenges, B2B buyers should develop a clear and detailed specification document that outlines their requirements, including dimensions, materials, finishes, and any specific performance criteria. Engaging in early discussions with manufacturers about their capabilities and limitations can also facilitate a smoother customization process. Buyers should consider using visualization tools or software that allow them to see prototypes or renderings of their custom doors before production. This proactive approach can help identify potential issues before they arise, ultimately saving time and reducing costs.
Scenario 3: Quality Assurance and Compliance Concerns
The Problem:
Quality assurance is a major concern for B2B buyers, especially in sectors such as construction and manufacturing. Buyers may worry about the durability and compliance of doors with local building regulations and standards. This is particularly true in Europe, where compliance with stringent environmental and safety standards is mandatory. Poor-quality doors can lead to safety hazards, increased maintenance costs, and potential legal liabilities, which can severely impact a buyer’s reputation and bottom line.
The Solution:
To address quality assurance and compliance issues, B2B buyers should conduct thorough due diligence when selecting door manufacturers. This includes verifying certifications, quality control processes, and customer reviews. Establishing a quality assurance agreement with manufacturers can ensure that products meet specified standards before delivery. Additionally, buyers should consider conducting random inspections of products upon delivery and before installation. Regular audits of suppliers can also help maintain compliance and build a trustworthy relationship. By prioritizing quality and compliance from the outset, buyers can avoid costly mistakes and ensure that their projects run smoothly.
Strategic Material Selection Guide for door manufacturer
What Are the Key Properties of Common Materials Used in Door Manufacturing?
When selecting materials for door manufacturing, it is essential to consider their properties, as these directly affect performance, durability, and suitability for specific applications. Here, we analyze four common materials: wood, steel, fiberglass, and aluminum.
How Does Wood Perform as a Door Material?
Wood is a traditional choice in door manufacturing, known for its aesthetic appeal and natural insulation properties. Key properties include good thermal insulation and moderate strength. However, wood is susceptible to moisture, which can lead to warping and decay if not properly treated.
Pros:
– Excellent insulation properties.
– Aesthetic versatility, allowing for various designs and finishes.
– Relatively easy to work with during manufacturing.
Cons:
– Prone to environmental damage (e.g., rot, insect infestation).
– Requires regular maintenance and treatment.
– Can be more expensive than synthetic alternatives.
For international buyers, especially in humid regions like parts of Africa and South America, it’s crucial to ensure that wood is treated for moisture resistance. Compliance with local building codes and standards, such as those set by ASTM, is also important.
What Advantages Does Steel Offer for Door Manufacturing?
Steel doors are renowned for their strength and security features. They typically have high pressure and temperature ratings, making them suitable for commercial and industrial applications. Steel is resistant to impact and can be treated for corrosion resistance.
Pros:
– High durability and security.
– Fire-resistant properties.
– Low maintenance requirements.
Cons:
– Can be prone to rust if not properly coated.
– Heavier than other materials, which may complicate installation.
– Limited aesthetic options compared to wood.
For buyers in the Middle East and Europe, understanding the corrosion resistance standards, such as DIN and JIS, is vital, especially in coastal areas where salt exposure can accelerate rusting.
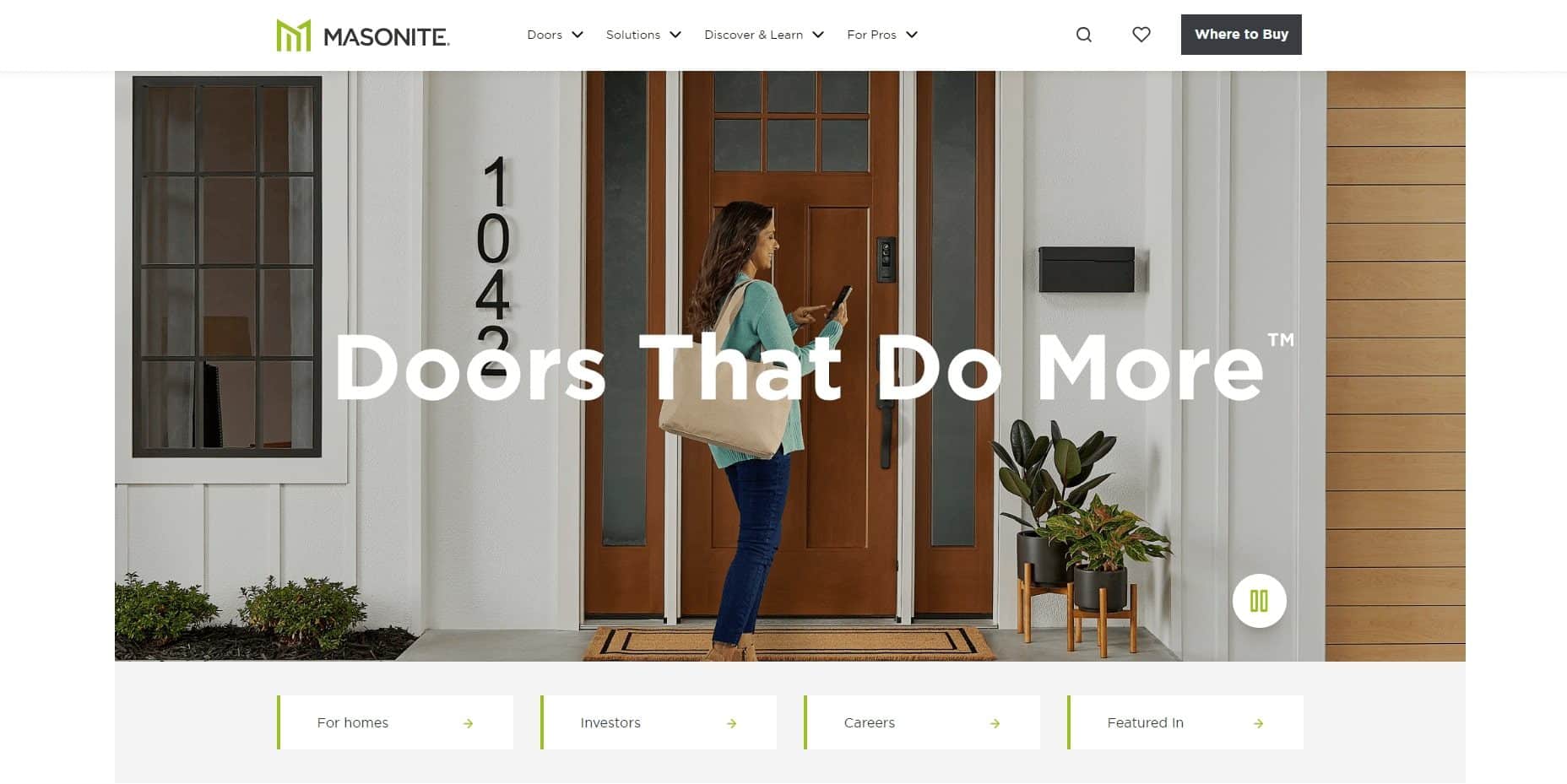
A stock image related to door manufacturer.
How Does Fiberglass Compare as a Door Material?
Fiberglass doors are increasingly popular due to their lightweight nature and versatility. They offer excellent insulation and can be molded into various designs. Fiberglass is also resistant to moisture and does not warp like wood.
Pros:
– Excellent thermal insulation.
– Resistant to moisture and insects.
– Low maintenance and high durability.
Cons:
– Can be more expensive than wood and steel.
– Limited strength compared to steel.
– May not have the same aesthetic appeal as natural wood.
For international buyers, particularly in Europe, it is important to consider compliance with energy efficiency standards, as fiberglass doors can contribute significantly to energy savings in buildings.
What Are the Key Features of Aluminum Doors?
Aluminum is a lightweight, corrosion-resistant material that is ideal for modern architectural designs. It is highly durable and can be finished in various colors and textures. Aluminum doors are often used in commercial settings due to their strength and low maintenance.
Pros:
– Lightweight and easy to install.
– Excellent corrosion resistance.
– Versatile design options.
Cons:
– Less insulating than wood or fiberglass.
– Can dent or scratch more easily than steel.
– Higher initial cost compared to some alternatives.
For buyers in regions like South America and Africa, understanding the local climate and potential for corrosion is essential. Compliance with local standards for thermal performance and safety is also critical.
Summary Table of Material Selection for Door Manufacturing
Material | Typical Use Case for door manufacturer | Key Advantage | Key Disadvantage/Limitation | Relative Cost (Low/Med/High) |
---|---|---|---|---|
Wood | Residential doors, decorative applications | Aesthetic appeal and insulation | Prone to moisture damage | Medium |
Steel | Commercial and industrial doors | High durability and security | Susceptible to rust | Medium to High |
Fiberglass | Energy-efficient residential doors | Excellent insulation and low maintenance | Higher cost than wood | High |
Aluminum | Commercial entryways and modern designs | Lightweight and corrosion-resistant | Less insulating than wood | Medium to High |
This analysis provides a comprehensive overview of the materials commonly used in door manufacturing, along with actionable insights tailored for international B2B buyers. Understanding these factors will aid in making informed decisions that align with specific application requirements and regional standards.
In-depth Look: Manufacturing Processes and Quality Assurance for door manufacturer
What Are the Main Stages of the Door Manufacturing Process?
The manufacturing process for doors involves several critical stages that ensure the final product meets quality and performance standards. The main stages include material preparation, forming, assembly, and finishing.
How Is Material Prepared for Door Manufacturing?
Material preparation is the first step in door manufacturing. This stage involves selecting the right type of material, which can include wood, steel, fiberglass, or composite materials. Each material has its unique properties and applications.
-
Sourcing Quality Materials: B2B buyers should focus on suppliers who source high-quality raw materials. Look for certifications or documentation that confirm the sustainability and quality of the materials used.
-
Pre-Processing: After sourcing, materials undergo processes such as cutting, drying, and treatment to ensure they are ready for forming. For instance, wood may need to be kiln-dried to prevent warping.
What Techniques Are Used in the Forming Stage?
The forming stage shapes the prepared materials into the desired door specifications. This can involve various techniques depending on the material being used.
-
Pressing and Molding: For composite and fiberglass doors, materials are often pressed into molds. This ensures uniformity and allows for intricate designs.
-
Cutting and Shaping: For wooden doors, CNC machines are commonly employed to cut and shape the wood precisely. This technology enhances accuracy and reduces waste.
-
Metal Stamping: In the case of metal doors, stamping techniques are used to create panels and frames, ensuring strength and durability.
How Is Assembly Conducted in Door Manufacturing?
Once the components are formed, the assembly stage combines these parts into a complete door.
-
Joining Techniques: Common joining methods include adhesives, screws, and dowels. The choice of method can affect the door’s strength and longevity.
-
Quality Checkpoints: During assembly, it’s essential to incorporate checkpoints to verify that components fit correctly and meet design specifications.
What Finishing Processes Are Essential for Quality Doors?
The finishing stage enhances both the aesthetic appeal and functional properties of the door.
-
Surface Treatments: Depending on the door type, treatments may include staining, painting, or applying protective coatings. These treatments not only improve appearance but also protect against environmental factors.
-
Final Quality Inspection: Before packaging, a final inspection ensures that the door meets all quality standards. This includes checking for defects in the finish, alignment, and functionality.
What Quality Assurance Measures Are Commonly Used in Door Manufacturing?
Quality assurance (QA) is critical in ensuring that manufactured doors meet international standards and customer expectations.
Which International Standards Are Relevant for Door Manufacturers?
B2B buyers should be aware of relevant international standards that ensure quality and safety in door manufacturing.
-
ISO 9001: This is a widely recognized quality management standard that emphasizes consistent quality and customer satisfaction. Manufacturers certified under ISO 9001 demonstrate their commitment to maintaining quality systems.
-
CE Marking: In Europe, doors must comply with CE marking requirements, which indicate conformity with health, safety, and environmental protection standards.
-
API Standards: For specialized doors, such as those used in industrial applications, adherence to API standards may be necessary. These standards focus on specific performance criteria relevant to the industry.
How Are Quality Control Checkpoints Established?
Quality control (QC) checkpoints are critical in the manufacturing process to ensure that defects are identified and corrected early.
-
Incoming Quality Control (IQC): This step involves inspecting raw materials upon arrival. B2B buyers can request IQC reports to verify that materials meet specified standards.
-
In-Process Quality Control (IPQC): During manufacturing, samples are taken at various stages to ensure compliance with quality standards. This includes checking dimensions, finishes, and assembly integrity.
-
Final Quality Control (FQC): Before shipment, a final inspection is conducted to ensure the finished product meets all specifications. This is where buyers can verify that their orders are free from defects.
How Can B2B Buyers Verify Supplier Quality Control Practices?
Verifying a supplier’s quality control practices is essential for B2B buyers, especially when sourcing from international markets.
-
Conducting Supplier Audits: Regular audits can provide insights into a supplier’s quality management processes. Buyers can assess whether the supplier adheres to international standards and their internal QA protocols.
-
Requesting Quality Assurance Documentation: Buyers should ask for detailed QA reports, including IQC, IPQC, and FQC documentation. This transparency helps build trust and ensures accountability.
-
Utilizing Third-Party Inspection Services: Engaging third-party inspection services can provide an unbiased assessment of a supplier’s quality control measures. These services can conduct inspections at various stages of production and offer certification.
What Are the Unique Quality Control Considerations for International Buyers?
International B2B buyers, particularly from regions like Africa, South America, the Middle East, and Europe, face unique challenges when it comes to quality control.
-
Understanding Local Regulations: Each region may have specific regulations that affect product standards. Buyers should familiarize themselves with these regulations to ensure compliance.
-
Cultural Differences in Quality Perception: Quality standards can vary significantly across cultures. Buyers should communicate their quality expectations clearly and ensure that suppliers understand them.
-
Logistics and Transportation Factors: Consideration must be given to how doors will be transported. Quality assurance should include measures to protect products during shipping to avoid damage.
By understanding the manufacturing processes and quality assurance measures, B2B buyers can make informed decisions when selecting door manufacturers, ensuring that they receive products that meet their specific needs and standards.
Practical Sourcing Guide: A Step-by-Step Checklist for ‘door manufacturer’
To effectively source door manufacturing services, international B2B buyers must navigate a series of critical steps to ensure they partner with reputable suppliers. This guide provides a comprehensive checklist designed to streamline the sourcing process, particularly for buyers from Africa, South America, the Middle East, and Europe.
Step 1: Define Your Technical Specifications
Establishing clear technical specifications is essential before approaching suppliers. Consider the materials, dimensions, design, and performance characteristics required for your project. This clarity will not only help suppliers understand your needs but also facilitate accurate quotations.
- Material Selection: Determine if you need solid wood, steel, fiberglass, or composite materials based on durability and design preferences.
- Design Requirements: Specify whether you require custom designs or standardized options to streamline production.
Step 2: Conduct Market Research
Understanding the market landscape is critical for identifying potential suppliers. Research the local and international manufacturers that specialize in doors, focusing on their product offerings and market reputation.
- Industry Trends: Keep abreast of emerging trends in door manufacturing, such as eco-friendly materials or smart door technology.
- Competitor Analysis: Analyze competitors’ choices to gauge industry standards and expectations.
Step 3: Evaluate Potential Suppliers
Thoroughly vet potential suppliers to ensure they meet your standards. Request company profiles, case studies, and references from buyers in similar industries or regions.
- Certifications and Compliance: Verify that suppliers adhere to relevant industry standards and regulations, such as ISO certifications or regional compliance.
- Production Capacity: Assess whether the supplier can meet your order volume within your required timelines.
Step 4: Request Samples
Before finalizing a supplier, request samples of their products to evaluate quality. This step is crucial for assessing the craftsmanship and materials used in their doors.
- Quality Assurance: Look for signs of quality in the finish, durability, and overall construction of the sample.
- Customization Options: Ensure that the supplier can replicate the sample’s quality in larger orders.
Step 5: Negotiate Terms and Pricing
Once you have selected a potential supplier, engage in negotiations to finalize pricing, payment terms, and delivery schedules. Transparency in this stage is vital for a smooth transaction.
- Volume Discounts: Inquire about pricing breaks for larger orders, which can significantly impact your overall budget.
- Payment Options: Discuss payment methods and terms to establish a mutually beneficial agreement.
Step 6: Establish a Communication Plan
Effective communication is key to a successful partnership. Develop a clear communication plan that outlines how you will interact with the supplier throughout the project.
- Regular Updates: Schedule regular check-ins to discuss progress, address concerns, and adjust plans if necessary.
- Point of Contact: Designate a primary contact on both sides to streamline communication and decision-making.
Step 7: Monitor Production and Quality Control
Once production begins, monitor the process closely to ensure that the final products meet your specifications and quality standards.
- Site Visits: If feasible, conduct site visits to observe the production process firsthand and address any potential issues.
- Quality Inspections: Implement a system for quality checks at different stages of production to mitigate risks of defects.
By following this structured checklist, B2B buyers can enhance their sourcing strategy for door manufacturers, ensuring they make informed decisions that align with their business goals.
Comprehensive Cost and Pricing Analysis for door manufacturer Sourcing
What Are the Key Cost Components in Door Manufacturing?
Understanding the cost structure of door manufacturing is crucial for international B2B buyers. The primary cost components include:
-
Materials: The choice of materials significantly affects the overall cost. Common materials include wood, steel, fiberglass, and composite materials. Each has its own pricing, with wood generally being more expensive than steel. Specialty materials, such as eco-friendly options or high-performance composites, can further increase costs.
-
Labor: Labor costs vary widely based on geographic location. In regions like Europe, higher labor costs are often offset by increased productivity and quality. In contrast, manufacturers in regions like Africa or South America may offer lower labor costs but may have varying levels of skill and efficiency.
-
Manufacturing Overhead: This encompasses costs related to factory operations, utilities, and equipment maintenance. A manufacturer’s overhead can fluctuate based on production volume and facility efficiency.
-
Tooling: The initial investment in tooling is significant, especially for custom designs. The cost of molds, dies, and jigs must be factored into the pricing, especially for unique or bespoke products.
-
Quality Control (QC): Effective QC processes ensure product reliability and compliance with international standards. However, implementing rigorous QC can raise costs, particularly if certifications are required for specific markets.
-
Logistics: Shipping and handling can account for a substantial portion of the total cost, especially for international buyers. Factors such as shipping distance, mode of transport, and local tariffs can influence logistics costs.
-
Margin: The manufacturer’s profit margin is a vital component of pricing. Margins vary widely based on market competition, brand reputation, and product uniqueness.
How Do Price Influencers Affect Sourcing Decisions for Doors?
Several factors influence pricing in door manufacturing, which can impact sourcing strategies:
-
Volume/MOQ: Manufacturers often have minimum order quantities (MOQ) that can affect pricing. Higher volumes typically lead to discounts, making it advantageous for buyers to consolidate orders.
-
Specifications and Customization: Custom doors or those with specific features (e.g., fire ratings, soundproofing) can significantly raise costs. Clear communication of requirements can help avoid unexpected charges.
-
Materials and Quality Certifications: Premium materials and certifications (such as ISO or CE) can elevate prices. Buyers should evaluate whether these are necessary for their specific applications to manage costs effectively.
-
Supplier Factors: Supplier reputation, reliability, and production capabilities play a role in pricing. Established suppliers may command higher prices due to perceived quality and service levels.
-
Incoterms: The choice of Incoterms (International Commercial Terms) impacts the total cost. Different terms dictate who bears shipping costs and responsibilities, affecting the overall financial burden on the buyer.
What Are the Best Negotiation Tips for International B2B Buyers?
For B2B buyers, especially those in Africa, South America, the Middle East, and Europe, negotiating effectively can lead to cost savings:
-
Research and Benchmarking: Understand market prices and competitor offerings. This knowledge can empower buyers during negotiations and help identify fair pricing.
-
Leverage Total Cost of Ownership (TCO): When discussing pricing, consider not just the initial purchase price but also long-term costs such as maintenance, energy efficiency, and potential resale value.
-
Build Relationships: Establishing a strong relationship with suppliers can lead to better pricing and terms. Suppliers are often more willing to negotiate with buyers they trust.
-
Seek Multiple Quotes: Obtaining quotes from several manufacturers can create competition, which may lead to better pricing and terms.
-
Be Transparent About Your Needs: Clearly outline your requirements and expectations. This can prevent misunderstandings and ensure that quotes reflect your needs accurately.
Conclusion and Disclaimer on Pricing Insights
Pricing in the door manufacturing sector is influenced by a complex interplay of factors. While the insights provided can guide international B2B buyers, it is essential to understand that prices can vary significantly based on specific circumstances. Always consult with suppliers for precise quotes tailored to your unique requirements.
Alternatives Analysis: Comparing door manufacturer With Other Solutions
In the competitive landscape of B2B procurement, understanding alternative solutions to traditional door manufacturing is crucial for making informed purchasing decisions. Buyers must evaluate various options to determine the best fit for their specific operational needs, budget constraints, and long-term strategic goals.
Comparison Aspect | Door Manufacturer | Alternative 1: Smart Door Technology | Alternative 2: Modular Door Systems |
---|---|---|---|
Performance | High durability and security | Enhanced security features; automation capabilities | Flexible design options; quick assembly |
Cost | Moderate to high initial investment | Higher upfront costs; potential long-term savings through efficiency | Generally lower initial cost; scalability can increase expenses |
Ease of Implementation | Requires professional installation | May require advanced technical skills for setup | Easy to assemble; often requires minimal tools |
Maintenance | Regular upkeep needed; long lifespan | Requires software updates; potential for complex repairs | Minimal maintenance; parts can be easily replaced |
Best Use Case | Commercial buildings needing security | Smart homes and businesses looking for automation | Temporary structures or spaces needing adaptability |
What Are the Benefits and Drawbacks of Smart Door Technology?
Smart door technology integrates advanced features such as biometric access, remote locking, and monitoring systems. This option is particularly advantageous for businesses in high-security sectors, allowing for enhanced control and monitoring of entry points. However, the initial investment can be significantly higher than traditional doors, and ongoing maintenance involves software updates and troubleshooting potential tech issues. Businesses considering this option should assess their need for security against their budget for technology.
How Do Modular Door Systems Compare to Traditional Manufacturing?
Modular door systems offer a flexible and cost-effective alternative to standard door manufacturing. These systems can be quickly assembled on-site, making them ideal for temporary structures or projects with tight timelines. The cost is generally lower, but buyers should be aware that scaling up with modular systems might lead to increased long-term expenses. Additionally, while these doors are easy to maintain, they may not provide the same level of durability and security as traditional manufactured doors, making them less suitable for high-risk environments.
Conclusion: How Can B2B Buyers Choose the Right Door Solution?
When evaluating door solutions, B2B buyers should start by defining their specific requirements, including security needs, budget constraints, and installation capabilities. Each alternative offers unique advantages that can align with different operational goals. Traditional door manufacturers provide high security and durability, while smart door technology offers automation and enhanced control. Modular systems present flexibility and cost savings for temporary applications. By understanding these options, buyers can make strategic decisions that best serve their business objectives while optimizing their investment.
Essential Technical Properties and Trade Terminology for door manufacturer
What Are the Essential Technical Properties for Door Manufacturing?
When sourcing doors in the B2B market, understanding technical properties is crucial for making informed purchasing decisions. Here are key specifications that international buyers should consider:
-
Material Grade
The material grade indicates the quality and durability of the door. Common materials include solid wood, engineered wood, steel, and fiberglass. Each material has unique properties affecting strength, insulation, and resistance to environmental factors. For instance, steel doors offer high security and are often used in commercial buildings, while fiberglass doors provide excellent insulation, making them ideal for residential use. -
Tolerance Levels
Tolerance levels define the acceptable limits for dimensions during manufacturing. This specification ensures that doors fit precisely within frames and function correctly. For example, a door with a tolerance of +/- 1/16 inch ensures a snug fit, reducing the risk of drafts or operational issues. Understanding tolerance is vital for maintaining quality standards in construction projects. -
Fire Rating
Fire ratings assess how long a door can withstand exposure to fire. They are critical for safety in commercial and public buildings. Fire-rated doors are classified into categories such as 20, 45, 60, and 90 minutes, indicating the duration they can resist flames. Buyers should prioritize fire ratings to comply with safety regulations and protect assets and personnel. -
Insulation Value (R-Value)
The insulation value, often measured in R-Value, indicates the door’s energy efficiency. A higher R-Value means better thermal insulation, which can lead to significant energy savings. For instance, doors with an R-Value of 5 or higher are ideal for regions with extreme temperatures, as they help maintain indoor climates and reduce heating and cooling costs. -
Finish and Coating
The finish and coating of a door impact its aesthetics and durability. Options include paint, stain, and varnish, each offering varying levels of protection against moisture, UV rays, and wear. Selecting the right finish is essential for ensuring the door’s longevity and maintaining its visual appeal over time.
What Are Common Trade Terms in Door Manufacturing?
Understanding industry terminology is essential for effective communication and negotiation with suppliers. Here are some key terms to know:
-
OEM (Original Equipment Manufacturer)
An OEM is a company that produces parts or equipment that may be marketed by another manufacturer. In the door industry, this could refer to a manufacturer that supplies doors or components to larger brands. Knowing whether a supplier is an OEM can help buyers understand product quality and compatibility. -
MOQ (Minimum Order Quantity)
MOQ refers to the smallest quantity of a product that a supplier is willing to sell. This term is crucial for budgeting and inventory management. Buyers should ensure that the MOQ aligns with their project needs to avoid excess inventory or higher costs. -
RFQ (Request for Quotation)
An RFQ is a document sent to suppliers to solicit price quotes for specific products or services. Including detailed specifications in an RFQ ensures that suppliers provide accurate pricing, which is essential for comparing costs and making informed purchasing decisions. -
Incoterms (International Commercial Terms)
Incoterms are a set of international rules that define the responsibilities of buyers and sellers in global trade. These terms clarify who is responsible for shipping, insurance, and tariffs, which is particularly important for international buyers from regions like Africa and South America, where logistics can be complex. -
Lead Time
Lead time refers to the amount of time it takes from placing an order until the product is delivered. Understanding lead times is vital for project planning, especially in construction where timing can affect overall schedules. Buyers should negotiate clear lead times to ensure timely project completion.
By comprehensively understanding these technical properties and trade terms, international B2B buyers can make better-informed decisions when sourcing doors, leading to successful procurement outcomes.
Navigating Market Dynamics and Sourcing Trends in the door manufacturer Sector
What Are the Key Market Trends Impacting the Door Manufacturing Sector?
The global door manufacturing market is witnessing significant transformations driven by various factors, including technological advancements, changing consumer preferences, and regulatory pressures. For international B2B buyers, particularly from regions like Africa, South America, the Middle East, and Europe, understanding these dynamics is crucial for effective sourcing and strategic decision-making.
One of the most prominent trends is the increasing adoption of smart door technologies. These innovations, which include keyless entry systems and integrated security features, cater to the growing demand for enhanced convenience and safety. B2B buyers should prioritize suppliers that offer these advanced solutions, as they not only meet modern security standards but also appeal to environmentally conscious consumers.
Moreover, sustainability is emerging as a critical factor in the decision-making process. Manufacturers are increasingly using eco-friendly materials and production methods to minimize environmental impact. Buyers from Europe, for instance, are particularly attuned to sustainability metrics, seeking partners who can provide transparency in their supply chains and demonstrate a commitment to reducing carbon footprints.
In addition, the rise of e-commerce is reshaping sourcing strategies. Many manufacturers are now offering online platforms for easier access to products and services. This trend allows B2B buyers to compare options quickly, evaluate product specifications, and streamline procurement processes.
How Is Sustainability Shaping the Door Manufacturing Sector?
Sustainability is no longer just a buzzword; it has become a significant driver of change in the door manufacturing sector. With increasing awareness of environmental issues, B2B buyers are placing greater emphasis on sourcing from manufacturers who prioritize ethical practices and sustainable materials.
The environmental impact of traditional door manufacturing processes has led to a shift toward greener alternatives. For example, manufacturers are now utilizing recycled materials and responsibly sourced timber to create doors that not only meet aesthetic and functional requirements but also align with eco-friendly standards. Buyers should look for suppliers who offer certifications such as FSC (Forest Stewardship Council) or LEED (Leadership in Energy and Environmental Design), which guarantee that the materials used are sustainably sourced.
Moreover, the importance of ethical supply chains cannot be overstated. Buyers are encouraged to engage with manufacturers who uphold labor rights and fair trade practices, ensuring that their sourcing decisions positively impact communities. This approach not only enhances brand reputation but also fosters long-term partnerships that are built on trust and shared values.
What Is the Historical Context of the Door Manufacturing Sector?
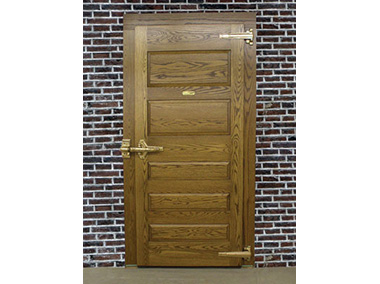
A stock image related to door manufacturer.
The door manufacturing sector has evolved significantly over the years, adapting to the changing needs of consumers and advancements in technology. Historically, doors were primarily constructed from solid wood, providing durability and security. However, the introduction of metal and composite materials in the mid-20th century expanded the possibilities for design and functionality.
As urbanization accelerated and building regulations became more stringent, manufacturers began to innovate by incorporating insulation and fire-resistant properties into their products. Today, the focus has shifted toward integrating smart technologies and sustainable practices, reflecting the contemporary priorities of safety, efficiency, and environmental responsibility.
For international B2B buyers, understanding this evolution is vital. It highlights the industry’s adaptability and the importance of selecting suppliers who are not only aware of current trends but are also positioned to lead future innovations in the door manufacturing sector.
Frequently Asked Questions (FAQs) for B2B Buyers of door manufacturer
-
How do I ensure quality when sourcing doors from international manufacturers?
To ensure quality when sourcing doors internationally, it’s essential to conduct thorough supplier vetting. Start by checking certifications like ISO 9001, which indicates a commitment to quality management systems. Request samples of the doors to evaluate material and craftsmanship firsthand. Additionally, consider visiting the manufacturer’s facility or hiring third-party quality assurance services to perform inspections before shipment. Establish clear quality standards in your purchase agreement to hold suppliers accountable. -
What are the key factors to consider when selecting a door manufacturer?
When selecting a door manufacturer, consider factors such as production capacity, lead times, and the range of materials offered. Evaluate the manufacturer’s experience in the industry and their ability to customize products to meet your specific needs. Additionally, assess their reputation through customer reviews and references. Financial stability is also crucial; ensure they can fulfill large orders without compromising quality or delivery times. -
What is the minimum order quantity (MOQ) for doors, and how can I negotiate it?
Minimum order quantities (MOQs) for doors can vary significantly by manufacturer and product type. Typically, MOQs range from 50 to 500 units. To negotiate a lower MOQ, demonstrate your potential for long-term business by discussing future orders or providing a detailed forecast. Building a relationship with the supplier can also help; consider placing a smaller initial order to establish trust before scaling up. -
What payment terms should I expect when dealing with international door manufacturers?
Payment terms can differ among international door manufacturers, but common practices include a 30% deposit upon order confirmation and the remaining 70% before shipping. Some suppliers may offer net terms, allowing payment within a specified period post-delivery. Always negotiate favorable terms that protect your cash flow, and consider using secure payment methods like letters of credit to mitigate risks associated with international transactions. -
How can I customize doors to fit my specific business needs?
Customizing doors involves working closely with your manufacturer to define specifications, including size, material, color, and design features. Most manufacturers offer a variety of options to cater to specific market demands. Provide detailed drawings or prototypes to the manufacturer, and inquire about their capabilities for custom production. Be mindful of lead times and potential costs associated with customization to ensure it aligns with your project budget. -
What logistics considerations should I keep in mind when importing doors?
When importing doors, consider logistics factors such as shipping methods, freight costs, and delivery timelines. Choose between air freight for speed or sea freight for cost-effectiveness based on your urgency and budget. Ensure you understand customs regulations and documentation requirements in your country to avoid delays. Collaborating with a freight forwarder can streamline the shipping process and help navigate any complexities related to international trade. -
How do I handle disputes with door manufacturers?
Handling disputes with door manufacturers requires a proactive approach. Start by clearly documenting all communications and agreements related to the order. If issues arise, initiate a discussion with the supplier to resolve the matter amicably. If resolution is not possible, refer to the terms outlined in your contract, including any arbitration clauses. Consider engaging a mediator if necessary, and always seek legal advice if the situation escalates. -
What certifications should I look for in door manufacturers to ensure compliance with international standards?
When sourcing doors, look for certifications that indicate compliance with international standards, such as CE marking in Europe or ANSI certification in the United States. These certifications ensure that the doors meet safety, performance, and environmental standards. Additionally, consider certifications related to sustainability, such as FSC (Forest Stewardship Council) certification, which indicates responsible sourcing of materials. Verify that the manufacturer can provide documentation for these certifications to ensure authenticity.
Important Disclaimer & Terms of Use
⚠️ Important Disclaimer
The information provided in this guide, including content regarding manufacturers, technical specifications, and market analysis, is for informational and educational purposes only. It does not constitute professional procurement advice, financial advice, or legal advice.
While we have made every effort to ensure the accuracy and timeliness of the information, we are not responsible for any errors, omissions, or outdated information. Market conditions, company details, and technical standards are subject to change.
B2B buyers must conduct their own independent and thorough due diligence before making any purchasing decisions. This includes contacting suppliers directly, verifying certifications, requesting samples, and seeking professional consultation. The risk of relying on any information in this guide is borne solely by the reader.
Strategic Sourcing Conclusion and Outlook for door manufacturer
How Can Strategic Sourcing Enhance Your Door Manufacturing Supply Chain?
In conclusion, strategic sourcing is a pivotal component in optimizing the supply chain for door manufacturers. By focusing on building strong relationships with suppliers across Africa, South America, the Middle East, and Europe, businesses can achieve significant cost savings, enhance product quality, and mitigate risks associated with supply disruptions. International B2B buyers should prioritize suppliers that demonstrate reliability, sustainability, and innovation to stay competitive in the evolving market landscape.
What Should International Buyers Consider Moving Forward?
As the door manufacturing industry continues to adapt to global trends, buyers must remain agile and proactive. Embracing technology, such as advanced analytics and digital procurement tools, can significantly enhance sourcing strategies. Additionally, fostering collaboration with suppliers can lead to joint development of new products that meet changing consumer demands.
Why Is Now the Time to Act?
The future of door manufacturing is promising, with opportunities for growth and innovation. International B2B buyers are encouraged to leverage strategic sourcing to not only streamline operations but also to enhance their market position. Now is the time to engage with suppliers who align with your business goals and values. Take the first step towards a more resilient and efficient supply chain today.