Discover Top Valve Manufacturers: Your Ultimate Sourcing Guide (2025)
Introduction: Navigating the Global Market for valve manufacturer
In an increasingly interconnected world, sourcing high-quality valves from reputable manufacturers is a critical challenge for international B2B buyers. Whether you’re operating in the oil and gas, water treatment, or manufacturing sectors, understanding the nuances of valve types, applications, and supplier reliability can significantly impact operational efficiency and cost management. This guide serves as a comprehensive resource, covering various types of valves—including ball valves, globe valves, and more—alongside their applications across different industries.
Additionally, we delve into essential factors for vetting suppliers, analyzing cost structures, and navigating international logistics, which are particularly crucial for buyers in Africa, South America, the Middle East, and Europe, including regions like Indonesia and Thailand. By equipping decision-makers with actionable insights and best practices, this guide empowers you to make informed purchasing decisions that not only meet technical specifications but also align with your strategic business objectives.
As the global market for valve manufacturing continues to evolve, this resource positions you to stay ahead of the curve, ensuring you can confidently select the right products and partners for your operational needs.
Understanding valve manufacturer Types and Variations
Type Name | Key Distinguishing Features | Primary B2B Applications | Brief Pros & Cons for Buyers |
---|---|---|---|
Ball Valve | Compact design, 90-degree turn for operation | Oil & gas, water supply, chemical processing | Pros: Quick operation, minimal pressure drop. Cons: Limited flow control. |
Globe Valve | S-shaped flow path, requires multiple turns to operate | Steam systems, HVAC, water treatment | Pros: Excellent flow regulation, durable. Cons: Higher pressure drop, slower operation. |
Gate Valve | Linear motion, full open/close position | Waterworks, oil pipelines, fire protection | Pros: Low pressure drop, suitable for on/off control. Cons: Slow operation, not for throttling. |
Check Valve | Allows flow in one direction, prevents backflow | Wastewater management, HVAC systems | Pros: Prevents backflow, reduces system damage. Cons: Can lead to water hammer if not properly installed. |
Butterfly Valve | Rotating disc for flow control, compact design | Chemical processing, food & beverage | Pros: Lightweight, quick operation. Cons: Less effective for throttling compared to globe valves. |
What are the Characteristics and Suitability of Ball Valves for B2B Buyers?
Ball valves are characterized by their compact design and the ability to operate with a simple 90-degree turn. This makes them ideal for applications requiring quick on/off control, such as in oil and gas, water supply, and chemical processing industries. Buyers should consider the fluid type and pressure ratings, as ball valves are suitable for high-pressure environments but may not provide the best flow control for all applications.
How Do Globe Valves Function and Where Are They Most Suitable?
Globe valves have an S-shaped flow path that requires multiple turns to open or close, making them excellent for flow regulation. They are commonly used in steam systems, HVAC, and water treatment applications. B2B buyers should note that while globe valves offer superior flow control, they also incur a higher pressure drop and are slower to operate compared to other valve types, making them less suitable for quick shut-off applications.
What Should Buyers Know About Gate Valves?
Gate valves are designed for linear motion and provide a full open or closed position, making them ideal for applications like waterworks and oil pipelines. They offer a low-pressure drop, which is advantageous for systems requiring high flow rates. However, they are not suitable for throttling and can be slow to operate, which may be a consideration for buyers needing quick response times.
What are the Benefits and Considerations of Check Valves?
Check valves allow fluid to flow in only one direction and are essential for preventing backflow in systems such as wastewater management and HVAC. Their primary advantage is that they help protect systems from damage due to reverse flow. Buyers should be aware that improper installation can lead to issues like water hammer, which can affect system integrity and performance.
Why are Butterfly Valves Popular in Various Industries?
Butterfly valves feature a rotating disc that controls flow and are known for their lightweight and compact design. They are widely used in chemical processing and food and beverage industries due to their quick operation and cost-effectiveness. However, buyers should consider that butterfly valves may not be as effective for throttling applications compared to globe valves, which can limit their use in certain scenarios.

A stock image related to valve manufacturer.
Related Video: Valves Explained – Control Valve Types (Gate Valve, Globe Valve, Ball Valve, Butterfly Valve, etc.)!
Key Industrial Applications of valve manufacturer
Industry/Sector | Specific Application of valve manufacturer | Value/Benefit for the Business | Key Sourcing Considerations for this Application |
---|---|---|---|
Oil & Gas | Flow control in pipelines and refineries | Ensures efficient operation and safety in transport | Quality certifications, material compatibility, and reliability |
Water Treatment | Regulation of water flow and pressure in treatment plants | Enhances water quality and compliance with standards | Durability against corrosion, maintenance requirements, and cost |
Chemical Processing | Control of chemical reactions and material flow | Increases safety and efficiency in production | Chemical resistance, precision control, and safety standards |
Power Generation | Steam and fluid control in turbines and boilers | Maximizes energy output and operational efficiency | High-temperature tolerance, energy efficiency, and lifecycle cost |
Food and Beverage | Hygiene control and flow management in processing | Ensures product safety and quality compliance | Sanitary design, material certification, and easy maintenance |
How Are Valves Used in the Oil & Gas Industry?
In the oil and gas sector, valve manufacturers supply critical components that regulate the flow of oil, gas, and other fluids within pipelines and refineries. These valves are essential for maintaining operational efficiency and ensuring safety during transport and processing. Buyers in this industry must prioritize sourcing high-quality valves that meet rigorous safety and performance standards, as failures can lead to significant environmental and financial repercussions. Additionally, understanding the specific material compatibility with various fluids is crucial.
What Role Do Valves Play in Water Treatment Facilities?
Valves are integral to water treatment plants, where they control the flow and pressure of water during purification processes. Proper regulation is vital for ensuring water quality and compliance with environmental regulations. B2B buyers in this sector should focus on sourcing durable valves that can withstand corrosive environments and require minimal maintenance. Additionally, valves must be compliant with local and international water safety standards to ensure that treated water meets health regulations.
How Are Valves Applied in Chemical Processing?
In chemical processing, valves are used to control the flow of reactants and products during manufacturing. They play a key role in maintaining safety by preventing leaks and ensuring precise control over chemical reactions. Buyers should consider sourcing valves that offer high chemical resistance and can handle extreme temperatures and pressures typical in chemical plants. Additionally, adherence to safety standards is paramount, as any malfunction can lead to hazardous situations.
Why Are Valves Important in Power Generation?
Power generation facilities utilize valves to manage the flow of steam and fluids in turbines and boilers. Efficient valve operation is crucial for maximizing energy output and minimizing operational costs. International buyers must look for valves that can endure high temperatures and pressures while maintaining energy efficiency. Understanding the lifecycle costs and maintenance requirements of these valves can also significantly impact operational efficiency and budget management.
How Do Valves Enhance Safety in the Food and Beverage Industry?
In the food and beverage sector, valves are used for flow management and hygiene control during processing. They help ensure that products are safe for consumption and comply with health regulations. Buyers should prioritize sourcing valves designed for sanitary applications, which require specific material certifications and easy maintenance features. Additionally, understanding the regulatory landscape in different regions is crucial for compliance and product safety.
Related Video: Types of Valves | All in One Guide to Industrial Valve Types
3 Common User Pain Points for ‘valve manufacturer’ & Their Solutions
Scenario 1: Sourcing Quality Valves in a Competitive Market
The Problem:
International B2B buyers often face significant challenges when sourcing high-quality valves. With numerous manufacturers claiming to provide top-notch products, distinguishing between reliable suppliers and those with subpar offerings can be daunting. This uncertainty can lead to costly mistakes, as low-quality valves may result in system failures, increased maintenance costs, and potential downtime. Buyers from regions like Africa and South America, where industrial standards may vary, often find it particularly challenging to ensure compliance with international quality standards.
The Solution:
To effectively source quality valves, buyers should begin by establishing clear specifications that align with their operational needs. This includes identifying the valve type (e.g., ball valves, globe valves), material requirements, and pressure ratings. Next, leverage industry networks and online platforms to gather recommendations and reviews from other businesses that have previously engaged with valve manufacturers. Consider requesting samples or prototypes to evaluate quality before committing to larger orders. Additionally, establish partnerships with manufacturers that provide transparency about their production processes and certifications, such as ISO standards. This approach not only mitigates risks but also fosters long-term relationships with reputable suppliers.
Scenario 2: Ensuring Timely Deliveries to Avoid Production Delays
The Problem:
Timely delivery of valves is critical for maintaining production schedules. B2B buyers often encounter delays due to factors such as supply chain disruptions, inadequate inventory management by manufacturers, or unexpected demand spikes. Such delays can lead to halted production lines, increased operational costs, and strained relationships with customers, particularly in regions like the Middle East and Europe where project timelines are strictly adhered to.
The Solution:
To ensure timely deliveries, buyers should implement a proactive procurement strategy. Start by evaluating potential suppliers based on their historical performance regarding delivery times. Engage manufacturers early in the planning process to discuss lead times and set realistic expectations. Utilize inventory management software to track usage patterns and forecast needs accurately, allowing for timely reorders. Building buffer stock for critical valve types can also mitigate the impact of unforeseen delays. Furthermore, establishing clear communication channels with suppliers can facilitate quicker resolutions to potential issues, ensuring that production schedules remain on track.
Scenario 3: Navigating Technical Specifications and Compatibility Issues
The Problem:
B2B buyers frequently grapple with the complexities of technical specifications and compatibility when selecting valves for their systems. Different industries may require specific valve types that must be compatible with existing infrastructure, which can vary widely based on local practices and standards. This issue is especially prevalent in regions like South America, where infrastructure may differ significantly from European standards, leading to challenges in integration and operational efficiency.
The Solution:
To navigate technical specifications effectively, buyers should conduct a thorough assessment of their existing systems and operational requirements. Collaborate with engineers or technical experts to define the necessary specifications, including size, pressure ratings, and materials. When engaging with valve manufacturers, request detailed product datasheets and compatibility information. It may also be beneficial to conduct pilot tests or simulations to evaluate performance under actual operating conditions before full-scale implementation. Additionally, consider suppliers that offer technical support and can assist in the integration process. This collaborative approach will not only enhance compatibility but also optimize overall system performance, reducing the likelihood of operational disruptions.
Strategic Material Selection Guide for valve manufacturer
What Are the Key Properties of Common Materials Used in Valve Manufacturing?
When selecting materials for valve manufacturing, understanding the key properties of each material is crucial for ensuring optimal performance in various applications. Here we analyze four common materials: Stainless Steel, Brass, PVC, and Cast Iron, focusing on their properties, advantages, disadvantages, and specific considerations for international B2B buyers.
Stainless Steel: A Versatile Choice for High-Pressure Applications
Stainless steel is renowned for its excellent corrosion resistance and high strength, making it suitable for high-pressure and high-temperature applications. It typically has a temperature rating of up to 800°F (427°C) and can withstand significant pressure, often exceeding 1500 psi.
Pros: Stainless steel valves are durable, resistant to rust and corrosion, and can handle a wide range of media, including water, steam, and chemicals. They also have a long service life, which reduces replacement costs over time.
Cons: The primary drawbacks include higher manufacturing costs and complexity, especially for intricate designs. Additionally, stainless steel can be more challenging to machine compared to other materials.
Impact on Application: Stainless steel is ideal for applications requiring hygiene, such as food processing and pharmaceuticals, due to its non-reactive nature.
Considerations for International Buyers: Buyers from regions like Africa and South America should ensure compliance with local standards such as ASTM and DIN, as well as consider the availability of stainless steel grades suitable for their specific environmental conditions.
Brass: An Economical Option with Good Corrosion Resistance
Brass is a popular choice for valves due to its good corrosion resistance and machinability. It typically operates effectively at temperatures up to 250°F (121°C) and can handle pressures around 600 psi.
Pros: Brass valves are relatively inexpensive, easy to manufacture, and provide excellent sealing properties, making them suitable for a variety of applications, including water and gas.
Cons: However, brass is less durable than stainless steel and can corrode in certain environments, especially when exposed to chlorinated water or aggressive chemicals.
Impact on Application: Brass valves are commonly used in plumbing and HVAC systems, where their lower cost can be a significant advantage.
Considerations for International Buyers: Buyers in the Middle East and Europe should be aware of local regulations regarding lead content in brass, as many countries are moving towards lead-free alternatives.
PVC: A Lightweight Alternative for Chemical Applications
Polyvinyl Chloride (PVC) is a lightweight and cost-effective material that is increasingly used in valve manufacturing, particularly for chemical applications. PVC valves can typically handle temperatures up to 140°F (60°C) and pressures around 150 psi.
Pros: PVC is resistant to a wide range of chemicals, making it ideal for corrosive environments. It is also lightweight, which simplifies installation and reduces shipping costs.
Cons: The main limitation of PVC is its lower temperature and pressure ratings compared to metals, which may restrict its use in high-stress applications.
Impact on Application: PVC valves are commonly used in irrigation, chemical processing, and wastewater treatment.
Considerations for International Buyers: Buyers should verify compliance with local standards such as JIS and ASTM, particularly in regions where chemical compatibility is critical.
Cast Iron: A Durable Choice for Heavy-Duty Applications
Cast iron is known for its strength and durability, making it suitable for heavy-duty applications. It can typically handle temperatures up to 400°F (204°C) and pressures around 300 psi.
Pros: Cast iron valves are robust and can withstand high pressures and temperatures, making them ideal for steam and water applications. They also have good wear resistance.
Cons: However, cast iron is prone to corrosion and is heavier than other materials, which can complicate installation and increase transportation costs.
Impact on Application: Cast iron is often used in municipal water systems and industrial applications where durability is paramount.
Considerations for International Buyers: Buyers from Europe and the Middle East should ensure that cast iron valves meet local standards for pressure and temperature ratings, as well as corrosion resistance.
Summary Table of Material Selection for Valve Manufacturing
Material | Typical Use Case for valve manufacturer | Key Advantage | Key Disadvantage/Limitation | Relative Cost (Low/Med/High) |
---|---|---|---|---|
Stainless Steel | High-pressure applications, food processing | Excellent corrosion resistance | Higher manufacturing costs | High |
Brass | Plumbing, HVAC systems | Economical and easy to manufacture | Less durable, can corrode in certain environments | Medium |
PVC | Chemical processing, irrigation | Lightweight and chemical-resistant | Lower temperature and pressure ratings | Low |
Cast Iron | Municipal water systems, industrial | Robust and durable | Prone to corrosion, heavier | Medium |
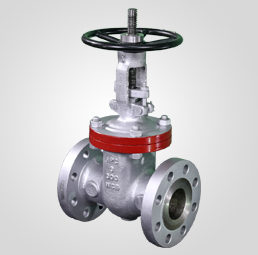
A stock image related to valve manufacturer.
This strategic material selection guide aims to equip international B2B buyers with the necessary insights to make informed decisions when sourcing valves, ensuring compatibility with their specific applications and compliance with regional standards.
In-depth Look: Manufacturing Processes and Quality Assurance for valve manufacturer
What Are the Main Stages of Manufacturing for Valve Manufacturers?
The manufacturing process for valves involves several critical stages that ensure the final product meets both functional and quality standards. For international B2B buyers, understanding these stages can help in assessing potential suppliers.
1. Material Preparation
The first step in valve manufacturing is the selection and preparation of raw materials. Common materials include various grades of stainless steel, carbon steel, and special alloys, depending on the application. Material selection is crucial as it directly impacts the valve’s durability and performance.
In this stage, materials are sourced from certified suppliers who comply with international standards. Buyers should verify the material certificates to ensure they meet the required specifications for their applications.
2. Forming Techniques
Once materials are prepared, the next step is forming. This process can involve casting, forging, machining, or a combination of these techniques.
- Casting is often used for complex shapes, while forging is preferred for high-strength applications.
- Machining involves cutting and shaping the material to achieve precise dimensions. Advanced CNC (Computer Numerical Control) machines are commonly employed for this purpose, ensuring high accuracy and repeatability.
Buyers should inquire about the specific forming techniques used by manufacturers and their capabilities to handle custom designs.
3. Assembly Process
The assembly stage involves bringing together various components of the valve, such as the body, bonnet, stem, and seals.
- Automated assembly lines are often utilized to enhance efficiency and consistency.
- Each component must be inspected for defects before assembly to ensure quality.
It is essential for buyers to understand the assembly processes employed and the skill level of the workforce involved in this stage.
4. Finishing Techniques
Finishing processes are applied to enhance the valve’s surface quality and corrosion resistance. Common finishing techniques include:
- Polishing to achieve a smooth surface.
- Coating with protective layers to prevent corrosion, especially in harsh environments.
Quality buyers should check if the finishing processes adhere to industry standards, which can significantly affect the valve’s longevity.
How Is Quality Assurance Integrated into Valve Manufacturing?
Quality assurance (QA) is integral to the manufacturing process, ensuring that products meet both customer specifications and regulatory requirements.
1. What Are the Relevant International Standards for Valve Quality Control?
International standards play a crucial role in valve manufacturing. ISO 9001 is the most recognized quality management system standard, emphasizing continuous improvement and customer satisfaction.
In addition to ISO standards, specific certifications such as CE (European Conformity) and API (American Petroleum Institute) standards are critical for valves used in specific applications, such as oil and gas. Buyers should always request proof of compliance with these standards to ensure product reliability.
2. What Are the Key Quality Control Checkpoints?
Quality control in valve manufacturing typically involves several checkpoints:
- Incoming Quality Control (IQC): This is conducted on raw materials to ensure they meet specified standards before production begins.
- In-Process Quality Control (IPQC): During manufacturing, continuous monitoring is performed to catch any defects early in the process.
- Final Quality Control (FQC): After assembly, final inspections are conducted to verify that the finished product meets all specifications and standards.
International B2B buyers should inquire about the specific quality control processes and documentation that suppliers maintain at each checkpoint.
What Testing Methods Are Commonly Used in Valve Quality Assurance?
Testing methods are crucial for validating the performance and safety of valves. Common testing methods include:
- Hydrostatic Testing: This involves testing the valve under pressure to ensure it can handle the required operating conditions without leaks.
- Functional Testing: Valves are tested for their operational capabilities, ensuring they open and close correctly under simulated conditions.
- Non-Destructive Testing (NDT): Techniques like ultrasonic and radiographic testing are employed to detect any internal flaws without damaging the valve.
B2B buyers should confirm that suppliers conduct these tests and provide test reports to verify compliance with relevant standards.
How Can B2B Buyers Verify Supplier Quality Control Practices?
To ensure the reliability of valve suppliers, B2B buyers should take proactive steps in verifying quality control practices:
1. Conduct Supplier Audits
Regular audits can help assess a supplier’s manufacturing processes and quality control measures. Buyers should establish a checklist based on international standards and industry-specific requirements to guide their audits.
2. Request Quality Control Documentation
Buyers should request detailed quality control documentation, including inspection reports, test results, and certificates of compliance with standards like ISO 9001, CE, or API. This documentation should be readily available and up-to-date.
3. Engage Third-Party Inspection Services
Engaging independent third-party inspection services can provide an unbiased assessment of the supplier’s quality control practices. This is particularly important for international buyers who may not be able to visit the manufacturing site.
What Are the Quality Control Nuances for International Buyers?
For international B2B buyers, particularly those from Africa, South America, the Middle East, and Europe, there are specific nuances to consider regarding quality control:
- Cultural Differences: Understanding cultural differences in manufacturing practices and communication styles can aid in establishing effective partnerships with suppliers.
- Regulatory Compliance: Different regions may have varying regulatory requirements; therefore, buyers must ensure that suppliers are compliant with both local and international standards.
- Logistics and Supply Chain Management: Quality control doesn’t end at manufacturing. Buyers should consider the entire supply chain, including transportation and storage, as these factors can impact product quality.
By comprehensively understanding the manufacturing processes and quality assurance measures, international B2B buyers can make informed decisions when selecting valve manufacturers, ensuring they receive high-quality products that meet their specific needs.
Practical Sourcing Guide: A Step-by-Step Checklist for ‘valve manufacturer’
In today’s competitive landscape, sourcing the right valve manufacturer is crucial for ensuring the efficiency and reliability of industrial processes. This guide provides a step-by-step checklist to help international B2B buyers, especially from Africa, South America, the Middle East, and Europe, navigate the procurement process effectively.
Step 1: Define Your Technical Specifications
Before reaching out to suppliers, it is essential to outline your technical requirements clearly. This includes the type of valves needed (e.g., ball valves, globe valves), material specifications, pressure ratings, and any certifications required for compliance with local regulations.
- Consider the specific application of the valves, as different industries may require different features.
- Documenting these details will streamline communication with potential suppliers and help prevent misunderstandings.
Step 2: Conduct Market Research
Understanding the market landscape is key to identifying reputable valve manufacturers. Research various suppliers to compare their offerings, market presence, and customer reviews.
- Utilize online platforms, industry reports, and trade associations to gather insights on top manufacturers.
- Pay attention to suppliers that specialize in your specific industry needs, as they are more likely to understand the nuances of your requirements.
Step 3: Evaluate Potential Suppliers
Before committing to a supplier, thorough vetting is essential. Request company profiles, case studies, and references from buyers in a similar industry or region.
- Assess their experience, particularly with projects similar to yours.
- Inquire about their production capabilities and lead times to ensure they can meet your demands.
Step 4: Verify Supplier Certifications
Ensuring that your chosen supplier holds the necessary certifications is vital for quality assurance and compliance. Look for certifications such as ISO 9001, which indicates a commitment to quality management systems.
- Check if they comply with industry standards relevant to your sector (e.g., API, ASME).
- Certifications not only reflect quality but also enhance the supplier’s credibility in the global market.
Step 5: Request Samples or Prototypes
Once you have shortlisted potential suppliers, request samples or prototypes of the valves. This step allows you to evaluate the quality and suitability of the products for your specific applications.
- Inspect the samples for craftsmanship, materials used, and overall functionality.
- This hands-on evaluation can prevent costly mistakes in bulk orders.
Step 6: Assess After-Sales Support and Warranty Policies
Understanding the after-sales support and warranty policies of your chosen supplier is crucial for ongoing maintenance and service.
- Inquire about technical support, training for your staff, and the availability of spare parts.
- A robust warranty policy indicates the manufacturer’s confidence in their product quality and can save you costs in the long run.
Step 7: Negotiate Terms and Finalize the Agreement
Once you have selected a supplier, negotiate terms of the contract including pricing, delivery schedules, and payment terms.
- Ensure that all agreed-upon specifications and expectations are documented in the contract.
- Clear communication at this stage can mitigate potential disputes later on.
By following this checklist, international B2B buyers can make informed decisions when sourcing valve manufacturers, ensuring they choose a partner that meets their technical, financial, and operational needs.
Comprehensive Cost and Pricing Analysis for valve manufacturer Sourcing
What Are the Key Cost Components in Valve Manufacturing?
Understanding the cost structure of valve manufacturing is essential for international B2B buyers. The primary cost components include:
-
Materials: The choice of materials significantly impacts the overall cost. Common materials for valves include stainless steel, carbon steel, brass, and specialized alloys for high-temperature or corrosive environments. Prices can vary based on market demand, availability, and specific material certifications.
-
Labor: Labor costs can fluctuate based on geographical location, skill level required, and the complexity of the manufacturing process. In regions like Africa and South America, labor may be less expensive compared to Europe, but this can be offset by lower productivity or skill levels.
-
Manufacturing Overhead: This encompasses indirect costs such as utilities, maintenance, and factory rent. Efficient manufacturing processes can help reduce overhead costs, thus lowering the final price of valves.
-
Tooling: Tooling costs involve the creation of molds and dies necessary for production. Custom tooling can be expensive, and it is crucial to consider these costs when sourcing specialized valve designs.
-
Quality Control (QC): Investing in robust quality control processes ensures that the valves meet required standards and specifications. This can add to the overall cost but is essential for maintaining product reliability, especially in critical applications like oil and gas.
-
Logistics: Transportation and handling costs can vary widely based on the distance from the manufacturer to the buyer, shipping methods, and whether duties or tariffs apply. Understanding Incoterms can aid in negotiating better shipping arrangements.
-
Margin: Manufacturers typically set a profit margin based on their operational costs and market competition. This margin can vary significantly between suppliers, making it an important factor in pricing.
How Do Price Influencers Affect Valve Sourcing?
Several factors can influence pricing for valve manufacturers, particularly for international buyers:
-
Volume and Minimum Order Quantity (MOQ): Bulk purchases often lead to lower per-unit costs. Buyers should negotiate MOQs to optimize costs, especially for large-scale projects.
-
Specifications and Customization: Custom-designed valves will generally cost more than standard models. Providing clear specifications upfront can help manufacturers provide accurate quotes.
-
Material Choices: Selecting standard materials over specialized ones can lead to significant savings. Buyers should evaluate the necessity of using premium materials based on their application.
-
Quality and Certifications: Valves used in critical applications may require additional certifications (e.g., API, ISO). While these can increase costs, they may be essential for compliance and safety.
-
Supplier Factors: The reputation and reliability of the supplier can influence pricing. Established manufacturers may charge a premium for their reputation, while emerging suppliers might offer lower prices to gain market share.
-
Incoterms: Understanding the terms of shipping and delivery can impact overall costs. Buyers should clarify whether the price includes shipping, insurance, and customs duties to avoid unexpected expenses.
What Are the Best Practices for Negotiating Valve Prices?
International B2B buyers can adopt several strategies to ensure cost-efficient valve sourcing:
-
Conduct Market Research: Understanding current market rates for valves and materials can empower buyers during negotiations. This includes exploring prices in local markets in Africa, South America, the Middle East, and Europe.
-
Evaluate Total Cost of Ownership (TCO): Rather than focusing solely on upfront costs, consider the TCO, which includes maintenance, operational costs, and potential downtime. This holistic view can lead to better purchasing decisions.
-
Leverage Volume Discounts: Buyers should negotiate for volume discounts, especially if they foresee repeat orders. Establishing a long-term relationship with a supplier can also lead to better pricing over time.
-
Be Transparent About Needs: Providing suppliers with clear and detailed requirements can lead to more accurate quotes and reduce the likelihood of unexpected costs arising from miscommunication.
-
Consider Local Sourcing: In regions like Africa and South America, local suppliers might offer competitive pricing and reduced logistics costs. However, ensure they meet quality and certification standards.
Disclaimer on Indicative Prices
Prices for valves can vary significantly based on the factors discussed above, including location, market conditions, and specific buyer requirements. Always request detailed quotations from multiple suppliers to ensure competitive pricing and best value for your investment.
Alternatives Analysis: Comparing valve manufacturer With Other Solutions
In the competitive landscape of industrial solutions, B2B buyers often seek alternatives to traditional valve manufacturers. Understanding these alternatives can lead to more informed purchasing decisions and optimized operational efficiency. Below, we explore viable alternatives to conventional valve manufacturing, comparing their merits against established valve solutions.
Comparison Aspect | Valve Manufacturer | Alternative 1: Electric Actuated Valves | Alternative 2: Pneumatic Valves |
---|---|---|---|
Performance | High reliability and durability in various conditions. | Fast operation with precise control. | Quick response times with high force output. |
Cost | Generally higher initial investment with long-term savings. | Moderate initial cost; energy consumption can add to long-term costs. | Lower initial cost but may require more frequent maintenance. |
Ease of Implementation | Requires skilled labor for installation. | Relatively simple installation but needs electrical infrastructure. | Easy to install but requires compressed air systems. |
Maintenance | Low maintenance with proper care; longer lifespan. | Moderate maintenance; electrical components may require attention. | Regular maintenance needed for air supply systems. |
Best Use Case | Ideal for high-pressure applications in oil and gas. | Best for applications requiring precise flow control in automation. | Suitable for quick on-off applications in manufacturing. |
What Are the Advantages and Disadvantages of Electric Actuated Valves?
Electric actuated valves are designed for applications that demand precise control over fluid flow and rapid operation. One of their primary advantages is the ability to integrate seamlessly with automated systems, providing precise modulation of flow rates. This feature is particularly beneficial in industries such as pharmaceuticals and food processing, where accuracy is critical. However, the initial investment can be moderate to high, and the energy consumption may add to operational costs. Additionally, reliance on electrical infrastructure may limit deployment in remote locations without stable power sources.
How Do Pneumatic Valves Compare in Terms of Performance and Cost?
Pneumatic valves offer a compelling alternative, especially in environments where compressed air is readily available. They are known for their quick response times and high force output, making them ideal for applications that require rapid on-off cycling. The initial costs are generally lower compared to electric actuated valves, which can be attractive for budget-conscious operations. However, they may require more frequent maintenance, particularly if the air supply is not properly filtered or if there are leaks in the system. This can lead to higher long-term costs due to increased downtime and repairs.
How Can B2B Buyers Choose the Right Solution for Their Needs?
When selecting between valve manufacturers and alternative solutions, B2B buyers should consider their specific operational requirements, including performance needs, budget constraints, and maintenance capabilities. Understanding the unique advantages and limitations of each option is crucial. Buyers should also evaluate the compatibility of these solutions with their existing systems, as well as any long-term operational costs that may arise. Engaging with suppliers for tailored solutions and conducting thorough market research can further assist in making a well-informed decision.
In conclusion, while traditional valve manufacturers provide robust solutions, exploring alternatives like electric actuated and pneumatic valves can lead to optimized processes and potentially lower costs. Each option has its own set of advantages and drawbacks that must be carefully weighed against the specific needs of the business.
Essential Technical Properties and Trade Terminology for valve manufacturer
What Are the Key Technical Properties of Valves for B2B Buyers?
Understanding the technical specifications of valves is critical for B2B buyers, especially those involved in industries such as oil and gas, water treatment, and manufacturing. Here are some essential properties to consider:
1. Material Grade: What is the Impact on Performance?
The material grade of a valve significantly affects its durability, corrosion resistance, and overall performance. Common materials include stainless steel, carbon steel, and brass. Each material offers unique benefits; for instance, stainless steel is known for its resistance to corrosion, making it ideal for harsh environments. Buyers must select the appropriate material based on the operating conditions and the fluids being handled.
2. Pressure Rating: How Does It Affect Valve Selection?
Pressure rating, often measured in pounds per square inch (PSI), defines the maximum pressure a valve can withstand. This specification is vital for ensuring safety and reliability in high-pressure applications. B2B buyers should assess their system’s pressure requirements to choose valves that can perform effectively without risk of failure.
3. Temperature Tolerance: Why Is It Crucial?
Temperature tolerance indicates the range of temperatures a valve can operate under without degrading. Valves used in high-temperature environments, such as power plants, need to be rated for higher temperatures to maintain functionality. Understanding this specification helps in selecting valves that will not fail prematurely under extreme conditions.
4. Tolerance Levels: What Do They Mean for Quality?
Tolerance levels refer to the permissible limits of variation in a valve’s dimensions. High precision in manufacturing ensures that the valve fits correctly within the system, preventing leaks and operational failures. Buyers should inquire about tolerance levels to ensure they receive quality products that meet their specifications.
5. Flow Coefficient (Cv): How Does It Influence System Efficiency?
The flow coefficient (Cv) measures the flow capacity of a valve. A higher Cv indicates that the valve can pass more fluid at a given pressure drop, which is essential for maintaining system efficiency. Buyers should consider Cv when evaluating valves for applications that require precise flow control.
What Are Common Trade Terms in the Valve Manufacturing Industry?
Familiarity with industry jargon can streamline communication and negotiations between buyers and manufacturers. Here are some important terms:
1. OEM (Original Equipment Manufacturer): What Does It Mean?
An OEM refers to a company that produces parts or equipment that may be marketed by another manufacturer. For B2B buyers, understanding OEM relationships can lead to better procurement strategies and pricing.
2. MOQ (Minimum Order Quantity): How Does It Affect Purchasing?
MOQ is the smallest quantity of a product that a supplier is willing to sell. This term is crucial for buyers as it influences inventory costs and the ability to scale operations. Knowing the MOQ helps in planning purchases and managing budgets effectively.
3. RFQ (Request for Quotation): What Is Its Purpose?
An RFQ is a document issued by a buyer to solicit price bids from suppliers for specific products. It is an essential part of the procurement process that allows buyers to compare prices and terms from different manufacturers, aiding in informed decision-making.
4. Incoterms: Why Are They Important in International Trade?
Incoterms (International Commercial Terms) define the responsibilities of buyers and sellers in international trade, including shipping, insurance, and tariffs. Understanding these terms helps B2B buyers mitigate risks associated with shipping and ensure compliance with international laws.
5. Lead Time: How Does It Impact Project Timelines?
Lead time is the period from placing an order to receiving the goods. For B2B buyers, understanding lead times is critical for project planning and ensuring that operations run smoothly without delays.
Conclusion
Navigating the technical properties and trade terminology of valves is essential for B2B buyers seeking to make informed decisions. By understanding these specifications and terms, buyers can enhance their procurement processes, optimize their operations, and ultimately achieve greater success in their industries.
Navigating Market Dynamics and Sourcing Trends in the valve manufacturer Sector
What Are the Current Market Dynamics and Sourcing Trends in the Valve Manufacturing Sector?
The valve manufacturing sector is currently experiencing transformative changes driven by various global factors. A key driver is the increasing demand for efficient fluid control systems across industries such as oil and gas, water treatment, and chemicals. In regions like Africa and South America, rapid industrialization and urbanization are propelling investments in infrastructure, thereby boosting the demand for reliable valve solutions. Conversely, in Europe and the Middle East, stricter regulations around safety and environmental standards are shaping the market dynamics, compelling manufacturers to innovate and enhance product offerings.
Emerging technologies are playing a significant role in sourcing trends. The integration of IoT (Internet of Things) and AI (Artificial Intelligence) into valve systems is enabling real-time monitoring and predictive maintenance, which is particularly appealing to B2B buyers looking to enhance operational efficiency. Furthermore, digital platforms are becoming increasingly popular for sourcing, allowing international buyers to access a broader range of suppliers, compare prices, and evaluate product specifications more efficiently. This shift towards digital sourcing is particularly beneficial for buyers in remote regions, providing them with access to global markets.
Another trend is the growing preference for customized valve solutions. B2B buyers are seeking manufacturers who can provide tailored products that meet specific operational requirements. This demand for customization is pushing manufacturers to adopt more flexible production methods, such as additive manufacturing (3D printing), which allows for rapid prototyping and reduced lead times. As a result, understanding the nuances of these market dynamics is crucial for international buyers to make informed sourcing decisions.
How Is Sustainability Influencing Sourcing Decisions in the Valve Manufacturing Sector?
Sustainability has become a pivotal concern in the valve manufacturing sector, influencing both sourcing strategies and product development. The environmental impact of valve production and usage has prompted buyers to prioritize suppliers who demonstrate a commitment to sustainable practices. This includes the use of eco-friendly materials, energy-efficient manufacturing processes, and waste reduction initiatives.
Ethical sourcing is also gaining traction, as international buyers are increasingly aware of the social and environmental implications of their procurement choices. Suppliers that provide transparency regarding their supply chains, labor practices, and environmental certifications are more likely to earn the trust of buyers. Certifications such as ISO 14001 (Environmental Management) and LEED (Leadership in Energy and Environmental Design) are becoming essential for manufacturers seeking to distinguish themselves in a competitive marketplace.
Moreover, the demand for ‘green’ materials, such as recycled metals and biodegradable components, is on the rise. Buyers are actively seeking valve manufacturers that can offer products made from sustainable materials, aligning with their corporate social responsibility (CSR) goals. By prioritizing suppliers with strong sustainability credentials, B2B buyers not only contribute to environmental conservation but also enhance their own brand reputation in an increasingly eco-conscious market.
What Is the Historical Context of the Valve Manufacturing Industry?
The valve manufacturing industry has a rich history that dates back to ancient civilizations, where basic forms of valves were used in water management systems. Over the centuries, the evolution of valve technology has been closely linked to advancements in engineering and industrial processes. The 19th century marked a significant turning point with the advent of the industrial revolution, which spurred the demand for more sophisticated valves to manage steam and other fluids in burgeoning factories.
In the 20th century, the introduction of new materials and manufacturing techniques, such as cast iron and later stainless steel, revolutionized valve production. As industries expanded globally, the need for standardized valves became apparent, leading to the establishment of international standards. Today, the valve manufacturing sector continues to evolve, driven by technological innovations and changing market demands, particularly in the context of sustainability and digital transformation. Understanding this historical backdrop is vital for B2B buyers as it provides insights into the industry’s current landscape and future direction.
Frequently Asked Questions (FAQs) for B2B Buyers of valve manufacturer
-
How do I evaluate the quality of valves from a manufacturer?
To assess the quality of valves from a manufacturer, start by reviewing their certifications, such as ISO 9001 or API standards. Request samples to test their performance under actual conditions relevant to your application. Investigate their production processes, materials used, and any third-party testing they may conduct. Additionally, gather feedback from current users to understand their experiences regarding durability and reliability. -
What is the best type of valve for industrial applications?
The best type of valve for industrial applications depends on the specific requirements, such as flow control, pressure, and medium type. For rapid on/off control, a ball valve is often ideal due to its durability and quick operation. Conversely, if precise flow regulation is necessary, a globe valve might be more suitable. Evaluate the operating conditions, including temperature and pressure, to make an informed decision. -
How can I ensure the valve manufacturer complies with international standards?
To ensure compliance with international standards, verify that the manufacturer holds relevant certifications such as ISO, ASME, or CE markings. Request documentation proving their adherence to quality management systems and product specifications. Additionally, consider conducting audits or inspections to assess their manufacturing processes and product quality in real-time. -
What are the typical minimum order quantities (MOQs) for valves?
Minimum order quantities (MOQs) for valves can vary significantly between manufacturers and types of valves. Generally, MOQs range from 50 to 500 units, depending on the complexity and customization of the product. It’s advisable to discuss your needs directly with the manufacturer, as some may offer flexibility, especially for new customers or bulk orders. -
What payment terms should I expect when sourcing valves internationally?
Payment terms when sourcing valves internationally typically include options like wire transfers, letters of credit, or PayPal. Most manufacturers require a deposit (often 30-50%) upon order confirmation, with the balance due before shipment. Negotiate terms that suit your cash flow and ensure that both parties agree on currency exchange rates and any additional fees. -
How do I vet potential valve suppliers effectively?
To vet potential valve suppliers, start by researching their reputation in the industry through online reviews and testimonials. Request references from previous clients and check their financial stability. Consider visiting their facilities if possible or conducting a virtual audit. Additionally, assess their responsiveness and willingness to accommodate your specific needs, which can indicate their customer service quality. -
What factors should I consider for logistics when importing valves?
When importing valves, consider factors such as shipping methods, costs, and lead times. Evaluate whether to use air or sea freight based on urgency and budget. Understand customs regulations in your country, including duties and taxes that may apply. Collaborate with a reliable logistics partner familiar with international shipping to navigate potential challenges and ensure timely delivery. -
Can I customize valves to meet specific application needs?
Yes, many valve manufacturers offer customization options to cater to specific application needs. This can include variations in size, materials, or operational mechanisms. When approaching a manufacturer, provide detailed specifications and requirements to facilitate the customization process. Be prepared for discussions regarding lead times and potential cost implications associated with custom orders.
Important Disclaimer & Terms of Use
⚠️ Important Disclaimer
The information provided in this guide, including content regarding manufacturers, technical specifications, and market analysis, is for informational and educational purposes only. It does not constitute professional procurement advice, financial advice, or legal advice.
While we have made every effort to ensure the accuracy and timeliness of the information, we are not responsible for any errors, omissions, or outdated information. Market conditions, company details, and technical standards are subject to change.
B2B buyers must conduct their own independent and thorough due diligence before making any purchasing decisions. This includes contacting suppliers directly, verifying certifications, requesting samples, and seeking professional consultation. The risk of relying on any information in this guide is borne solely by the reader.
Strategic Sourcing Conclusion and Outlook for valve manufacturer
What Are the Key Takeaways for B2B Buyers in Valve Manufacturing?
In conclusion, the strategic sourcing of valves is essential for international B2B buyers to optimize operational efficiency and enhance product quality. By understanding the differences between various valve types, such as ball valves and globe valves, buyers can make informed decisions that align with their specific industry requirements. Additionally, prioritizing suppliers with a proven track record in quality assurance and compliance with international standards can significantly mitigate risks associated with procurement.
How Can Buyers Leverage Strategic Sourcing for Competitive Advantage?
As the global market evolves, particularly in regions like Africa, South America, the Middle East, and Europe, the importance of strategic sourcing becomes even more pronounced. Buyers are encouraged to engage in collaborative partnerships with manufacturers who demonstrate innovation and responsiveness to market needs. This approach not only ensures a reliable supply chain but also fosters innovation in product development, providing a competitive edge.
What Should Buyers Do Next?
Looking ahead, it is crucial for B2B buyers to stay informed about industry trends and technological advancements that impact valve manufacturing. By actively participating in industry forums and engaging with suppliers, buyers can cultivate valuable insights that drive strategic sourcing decisions. Embrace the opportunity to enhance your sourcing strategy today and position your business for sustained success in the dynamic valve market.