Discover Cost-Effective Solutions: Emergency Light China (2025)
Introduction: Navigating the Global Market for emergency light china
In an increasingly interconnected world, sourcing reliable emergency lighting solutions from China has become a critical challenge for international B2B buyers. With the growing emphasis on safety and compliance across various industries, understanding the intricacies of the emergency light market in China is essential. This comprehensive guide will cover a wide range of topics including the different types of emergency lights, their applications in various sectors, and strategic supplier vetting processes. Additionally, it will provide insights into pricing structures and cost management strategies to help you optimize your procurement efforts.
Navigating the global market for emergency lights made in China requires a keen understanding of both local manufacturing capabilities and international standards. This guide is designed to empower B2B buyers, particularly those from Africa, South America, the Middle East, and Europe—specifically Turkey and the UK—by equipping them with the knowledge needed to make informed purchasing decisions. By delving into market trends and supplier evaluations, you will be better positioned to select the best products that meet your operational needs while adhering to regulatory requirements. Ultimately, this resource aims to simplify the procurement process, ensuring that you can confidently invest in high-quality emergency lighting solutions that enhance safety and operational efficiency in your organization.
Understanding emergency light china Types and Variations
Type Name | Key Distinguishing Features | Primary B2B Applications | Brief Pros & Cons for Buyers |
---|---|---|---|
LED Emergency Lights | Energy-efficient, long lifespan, bright illumination | Hospitals, factories, public buildings | Pros: Low energy costs, minimal maintenance. Cons: Higher upfront cost than traditional options. |
Solar-Powered Emergency Lights | Operates on renewable energy, ideal for off-grid locations | Remote sites, outdoor events | Pros: Sustainable, no electricity required. Cons: Limited performance in cloudy conditions. |
Rechargeable Battery Lights | Portable, can be charged via AC or solar power | Construction sites, emergency kits | Pros: Versatile use, easy to transport. Cons: Battery lifespan may degrade over time. |
Fluorescent Emergency Lights | Bright light output, typically used in large spaces | Warehouses, parking lots | Pros: High visibility, cost-effective. Cons: Shorter lifespan compared to LEDs, requires more energy. |
Compact Emergency Lights | Small, portable design for easy storage and use | Vehicles, personal safety kits | Pros: Lightweight, convenient. Cons: Limited brightness and duration compared to larger models. |
What are the Characteristics and Suitability of LED Emergency Lights?
LED emergency lights are known for their energy efficiency and long lifespan, making them a popular choice among B2B buyers. These lights provide bright illumination, which is crucial in emergency situations. They are particularly suitable for environments like hospitals, factories, and public buildings where reliability is paramount. When considering LED lights, buyers should evaluate the initial investment against long-term savings on energy and maintenance.
How Do Solar-Powered Emergency Lights Function in Remote Locations?
Solar-powered emergency lights utilize renewable energy sources, making them ideal for off-grid applications. These lights are particularly useful in remote sites or outdoor events where traditional power sources are unavailable. While they promote sustainability, buyers should assess the potential limitations in performance during cloudy weather or extended periods without sunlight. Ensuring adequate battery storage capacity is also critical for continuous operation.
What Advantages Do Rechargeable Battery Lights Offer for B2B Applications?
Rechargeable battery lights are valued for their portability and versatility. They can be charged via AC power or solar energy, allowing for use in various settings, including construction sites and emergency kits. B2B buyers should consider the ease of transportation and adaptability of these lights, although they must be aware of potential battery degradation over time, which can affect performance.
Why Choose Fluorescent Emergency Lights for Large Spaces?
Fluorescent emergency lights are designed to deliver high visibility, making them suitable for large spaces like warehouses and parking lots. They offer a cost-effective solution for businesses needing reliable lighting. However, buyers should note that while they are less expensive upfront, their shorter lifespan compared to LED options and higher energy consumption can lead to increased operational costs over time.
What Are the Benefits of Compact Emergency Lights for Personal Use?
Compact emergency lights are characterized by their lightweight and portable design, making them easy to store and deploy in personal safety kits or vehicles. They are particularly advantageous for B2B buyers in sectors requiring quick access to emergency lighting. However, their limited brightness and operational duration compared to larger models can be a drawback, so it’s important for buyers to assess their specific needs before purchase.
Related Video: How to make High Quality Emergency Light
Key Industrial Applications of emergency light china
Industry/Sector | Specific Application of Emergency Light China | Value/Benefit for the Business | Key Sourcing Considerations for this Application |
---|---|---|---|
Healthcare | Emergency lighting in hospitals and clinics | Enhances patient safety during power outages and emergencies | Compliance with health regulations; durability; energy efficiency |
Manufacturing | Emergency lighting in factories and warehouses | Prevents accidents and ensures safe evacuation | Robustness; compatibility with existing systems; maintenance support |
Hospitality | Emergency lighting in hotels and restaurants | Improves guest safety and experience during emergencies | Aesthetic design; energy efficiency; ease of installation |
Transportation | Emergency lighting in public transport systems | Enhances passenger safety during emergencies and breakdowns | Compliance with safety standards; battery life; visibility |
Oil & Gas | Emergency lighting in offshore platforms and refineries | Ensures safety in hazardous environments | Explosion-proof certifications; reliability; weather resistance |
How is Emergency Light China Used in Healthcare Facilities?
In the healthcare sector, emergency lights are critical for ensuring patient safety during power outages or emergencies. Hospitals and clinics require reliable, high-intensity lighting to facilitate quick evacuations and assist healthcare professionals in providing care. Buyers should focus on sourcing emergency lights that comply with local health regulations and are designed for durability and energy efficiency. Key considerations include the lights’ brightness, battery life, and ease of installation, which can significantly impact operational readiness during crises.
What are the Benefits of Emergency Lighting in Manufacturing?
In manufacturing environments, emergency lighting is essential for maintaining safety standards and preventing accidents. These lights guide employees to exits during power failures, reducing panic and confusion. Buyers in this sector should prioritize sourcing robust emergency lights that can withstand harsh industrial conditions and are compatible with existing safety systems. Maintenance support and the lights’ ability to function in extreme temperatures are also crucial factors that can influence the safety and efficiency of manufacturing operations.
How Do Emergency Lights Enhance Safety in Hospitality?
In the hospitality industry, emergency lights play a vital role in enhancing guest safety and overall experience during emergencies. Hotels and restaurants must ensure that their premises are well-lit to guide guests safely to exits. When sourcing emergency lighting solutions, buyers should consider aesthetic designs that blend with the facility’s decor while also being energy-efficient. Additionally, ease of installation and compliance with local safety regulations are important to ensure a seamless integration into existing systems.
What Role Does Emergency Lighting Play in Transportation?
Emergency lighting is critical in transportation sectors, particularly for public transport systems. These lights not only enhance passenger safety during emergencies but also provide crucial visibility in situations like breakdowns or evacuations. International buyers should focus on sourcing emergency lights that comply with stringent safety standards and have long battery life. Visibility during adverse weather conditions and the lights’ ability to operate reliably in various environments are also key considerations that can affect passenger safety.
Why is Emergency Lighting Important in Oil & Gas Industries?
In the oil and gas sector, emergency lighting is indispensable for ensuring safety in hazardous environments such as offshore platforms and refineries. These lights must be explosion-proof and capable of withstanding extreme weather conditions. Buyers should look for emergency lights with certifications for safety and reliability, as well as those that can operate effectively in challenging environments. The focus should also be on sourcing products that offer longevity and require minimal maintenance, which can significantly reduce operational risks in this critical industry.
Related Video: Uses of Light in Everyday Life
3 Common User Pain Points for ’emergency light china’ & Their Solutions
Scenario 1: Inconsistent Quality and Reliability of Emergency Lights
The Problem: B2B buyers sourcing emergency lights from China often face significant quality control issues. Many suppliers may provide products that look appealing but fail to meet safety and performance standards. This inconsistency can lead to products that do not function during emergencies, risking both safety and financial loss. Buyers in regions with frequent power outages or safety regulations, such as Africa and the Middle East, feel this pain acutely. The challenge lies in identifying reliable suppliers who deliver high-quality products consistently.
The Solution: To mitigate the risk of inconsistent quality, B2B buyers should conduct thorough due diligence on potential suppliers. This includes requesting product samples and third-party certifications that validate compliance with international safety standards, such as ISO 9001 for quality management systems. Additionally, utilizing platforms like Alibaba or Global Sources can facilitate access to reviews and ratings from previous buyers. Implementing a robust supplier evaluation process that includes on-site inspections or audits can further ensure that the products meet required specifications. Establishing long-term relationships with trusted suppliers and negotiating quality assurance agreements will help maintain consistent product quality.
Scenario 2: Difficulty in Understanding Technical Specifications
The Problem: Many international buyers struggle to navigate the technical specifications of emergency lights, which can vary significantly across manufacturers. Terms like “lumen output,” “battery life,” and “run time” can be confusing, especially when considering how they impact the suitability of the product for specific applications. Buyers from South America and Europe, for example, may find it challenging to assess whether a product meets their unique needs, such as compliance with local regulations or suitability for specific environments.
The Solution: To address this issue, buyers should invest time in understanding the basic technical parameters of emergency lights. Creating a checklist that outlines key specifications—such as brightness (measured in lumens), battery capacity (measured in amp-hours), and operational duration during an outage—can help buyers make informed decisions. Engaging with suppliers to clarify these specifications and request detailed product documentation is also essential. Additionally, participating in industry webinars or training sessions can enhance buyers’ technical knowledge, enabling them to evaluate products more effectively and choose the right solutions for their specific needs.
Scenario 3: Challenges in After-Sales Support and Maintenance
The Problem: After-sales support is a critical concern for B2B buyers, especially when sourcing emergency lights from overseas. Many suppliers in China may not provide adequate after-sales service, making it difficult for buyers to obtain replacements or resolve issues post-purchase. This is particularly concerning for buyers in Europe and the Middle East, where compliance with stringent safety regulations is paramount. The absence of support can lead to prolonged downtime and increased operational risk.
The Solution: To ensure effective after-sales support, buyers should prioritize suppliers that offer comprehensive warranties and responsive customer service. Before finalizing a purchase, inquire about the supplier’s after-sales policies, including repair services, replacement parts availability, and response times for service requests. Establishing clear communication channels and a detailed service level agreement (SLA) will help set expectations for support. Buyers should also consider sourcing from suppliers who have a local presence or partnerships in their region, as this can facilitate quicker response times and access to necessary components. By taking these steps, buyers can ensure reliable support throughout the product lifecycle, minimizing the risk of operational disruptions.
Strategic Material Selection Guide for emergency light china
When selecting materials for emergency lights manufactured in China, international B2B buyers should consider various factors such as durability, cost, compliance with standards, and specific application requirements. Below is an analysis of four common materials used in emergency light production, focusing on their properties, advantages, disadvantages, and implications for buyers from diverse regions, including Africa, South America, the Middle East, and Europe.
What are the Key Properties of Polycarbonate in Emergency Light China?
Polycarbonate is a popular choice for the casing of emergency lights due to its excellent impact resistance and clarity. It can withstand temperatures ranging from -40°C to 120°C, making it suitable for various environments. Polycarbonate is also resistant to UV radiation, which prevents yellowing over time.
Pros & Cons:
– Advantages: High durability, lightweight, and good thermal stability.
– Disadvantages: It can be more expensive than other plastics and may scratch easily without proper coatings.
Impact on Application: Polycarbonate’s robustness makes it ideal for outdoor applications where exposure to harsh weather conditions is common. However, it may not be suitable for environments with high chemical exposure unless treated.
Considerations for International Buyers: Compliance with standards such as ASTM D256 for impact resistance is crucial. Buyers should also consider local preferences for materials that can withstand specific climatic conditions.
How Does Aluminum Benefit Emergency Light Manufacturing?
Aluminum is widely used in emergency light construction, particularly for frames and heat sinks. Its lightweight nature and excellent thermal conductivity make it an effective choice for dissipating heat generated by LED components.
Pros & Cons:
– Advantages: Corrosion-resistant, lightweight, and recyclable.
– Disadvantages: Prone to denting and may require additional surface treatments for enhanced durability.
Impact on Application: Aluminum is particularly effective in environments where heat management is critical, such as in high-output LED systems. Its recyclability also aligns with sustainability goals.
Considerations for International Buyers: Buyers should ensure that the aluminum used meets standards such as ASTM B221 for structural aluminum. Additionally, they should be aware of local regulations regarding recycling and material sourcing.
What Role Does Steel Play in Emergency Light Applications?
Steel, particularly stainless steel, is often used in emergency light applications that require enhanced strength and corrosion resistance. Stainless steel can endure high temperatures and is resistant to rust, making it suitable for various environments.
Pros & Cons:
– Advantages: Exceptional strength and durability, excellent corrosion resistance.
– Disadvantages: Heavier than other materials, which may impact installation and mounting options.
Impact on Application: Steel is ideal for industrial settings where lights may be exposed to mechanical stresses or harsh chemicals. Its strength makes it suitable for mounting in high-traffic areas.
Considerations for International Buyers: Compliance with standards like ASTM A240 for stainless steel is essential. Buyers should also consider the weight implications for installation in their specific applications.
Why is ABS Plastic a Common Choice for Emergency Lights?
Acrylonitrile Butadiene Styrene (ABS) is frequently utilized in the production of emergency light housings due to its good impact resistance and ease of manufacturing. It can withstand temperatures up to 80°C, making it suitable for indoor applications.
Pros & Cons:
– Advantages: Cost-effective, good mechanical properties, and easy to mold.
– Disadvantages: Lower temperature resistance compared to polycarbonate and can be less durable in outdoor settings.
Impact on Application: ABS is well-suited for indoor emergency lights where exposure to extreme temperatures is minimal. However, it may not be the best choice for outdoor applications due to its susceptibility to UV degradation.
Considerations for International Buyers: Buyers should ensure that ABS materials meet relevant standards such as ISO 179 for impact resistance. Understanding local preferences for materials based on climate and application is also vital.
Summary Table of Material Selection for Emergency Light China
Material | Typical Use Case for Emergency Light China | Key Advantage | Key Disadvantage/Limitation | Relative Cost (Low/Med/High) |
---|---|---|---|---|
Polycarbonate | Outdoor emergency lights | High impact resistance | Scratches easily | Medium |
Aluminum | Frames and heat sinks for LEDs | Lightweight and recyclable | Prone to denting | Medium |
Steel | Industrial emergency lighting | Exceptional strength | Heavier than alternatives | High |
ABS | Indoor emergency lights | Cost-effective and easy to mold | Lower temperature resistance | Low |
This guide provides international B2B buyers with essential insights into material selection for emergency lights manufactured in China, enabling informed decisions that align with their specific operational requirements and regional standards.
In-depth Look: Manufacturing Processes and Quality Assurance for emergency light china
What are the Typical Manufacturing Processes for Emergency Lights in China?
The manufacturing of emergency lights in China involves several critical stages that ensure the final product is reliable and meets international standards. The key processes include material preparation, forming, assembly, and finishing.
Material Preparation: What Materials are Used?
Material preparation is the first step in the manufacturing process. Manufacturers typically use high-quality plastics, aluminum, and LED components. The choice of materials is crucial for durability and performance. For instance, polycarbonate is often used for the outer casing due to its impact resistance and lightweight properties. Manufacturers must source materials that meet specific certifications, ensuring they are safe and environmentally friendly.
How is the Forming Process Conducted?
Once the materials are prepared, the next step is forming. This process involves shaping the raw materials into the desired components of the emergency light. Common techniques include injection molding for plastic parts and extrusion for aluminum housings. Advanced machinery is utilized to ensure precision and consistency in the dimensions of each component. This phase is critical as it directly impacts the performance and aesthetic quality of the final product.
What Does the Assembly Process Entail?
The assembly stage brings together all the individual components, including the housing, LED lights, and battery systems. This process typically involves both manual and automated assembly techniques. Skilled workers handle delicate tasks, such as the installation of circuit boards, while automated machinery may be used for repetitive tasks. Manufacturers often implement lean manufacturing principles to optimize efficiency and reduce waste during this stage.
How is the Finishing Process Completed?
Finishing involves final touches that enhance the product’s appearance and functionality. This may include painting, surface treatment, and quality checks. Manufacturers often apply coatings that improve scratch resistance and provide additional protection against environmental factors. Finally, each unit undergoes a thorough inspection to ensure it meets quality standards before packaging.
What Quality Assurance Standards are Relevant for Emergency Lights?
Quality assurance is paramount in the production of emergency lights. Manufacturers must adhere to various international standards to ensure their products are safe and reliable.
Which International Standards Should B2B Buyers Be Aware Of?
One of the key quality management standards is ISO 9001, which emphasizes a systematic approach to management that enhances customer satisfaction through effective processes. Compliance with ISO standards indicates that the manufacturer has a robust quality management system in place.
Additionally, product-specific certifications such as CE (Conformité Européenne) for European markets and API (American Petroleum Institute) for specific applications are essential. These certifications demonstrate that the products meet safety and performance requirements.
What are the Key Quality Control Checkpoints During Manufacturing?
Quality control (QC) is integrated into every stage of the manufacturing process, ensuring that products meet specified standards. Here are the main QC checkpoints:
How Does Incoming Quality Control (IQC) Work?
Incoming Quality Control (IQC) is the first checkpoint, where raw materials are inspected upon arrival. This process verifies that the materials meet predefined specifications and are free from defects. Suppliers must provide documentation, such as certificates of conformity, to validate the quality of their materials.
What is In-Process Quality Control (IPQC)?
In-Process Quality Control (IPQC) occurs during the manufacturing process. This involves continuous monitoring of production parameters and conducting regular inspections of components as they are formed and assembled. Manufacturers often use statistical process control techniques to detect variations and implement corrective actions swiftly.
How is Final Quality Control (FQC) Conducted?
Final Quality Control (FQC) is the last checkpoint before products are packaged and shipped. This stage includes comprehensive testing of the finished emergency lights to ensure they function correctly and meet safety standards. Common tests include electrical safety checks, light output measurement, and battery performance evaluations.
How Can B2B Buyers Verify Supplier Quality Control Measures?
For international B2B buyers, especially from Africa, South America, the Middle East, and Europe, verifying a supplier’s quality control measures is crucial.
What Steps Should Buyers Take to Conduct Audits?
Buyers should consider conducting on-site audits to assess the manufacturing processes and quality control systems in place. During an audit, buyers can evaluate the equipment, review documentation, and ensure compliance with international standards. This step is vital for establishing trust and ensuring that the supplier can consistently deliver high-quality products.
How Can Buyers Use Third-Party Inspections?
Engaging third-party inspection services is another effective way to verify quality. These independent organizations can perform inspections at various stages of production, providing unbiased reports on the quality of materials and finished products. This can be particularly beneficial for buyers unfamiliar with local regulations or manufacturing practices.
What Nuances Should International Buyers Consider?
B2B buyers from different regions should be aware of specific nuances in quality control and certification processes. For example, European buyers may place a higher emphasis on CE certification, while buyers from the Middle East may prioritize compliance with local standards.
Furthermore, understanding the cultural and operational differences in manufacturing practices can help buyers set realistic expectations. Clear communication regarding quality requirements and compliance can foster better relationships with suppliers.
Conclusion: Ensuring Quality in Emergency Light Manufacturing
For international B2B buyers, understanding the manufacturing processes and quality assurance practices in the production of emergency lights in China is essential. By focusing on key manufacturing stages, international standards, and robust quality control measures, buyers can make informed decisions and select reliable suppliers that meet their specific needs.
Practical Sourcing Guide: A Step-by-Step Checklist for ’emergency light china’
Introduction
When sourcing emergency lights from China, it’s essential to follow a structured approach to ensure you find reliable suppliers that meet your quality and regulatory needs. This guide provides a step-by-step checklist designed for international B2B buyers from Africa, South America, the Middle East, and Europe. By adhering to these steps, you can streamline your procurement process and mitigate risks associated with international sourcing.
Step 1: Define Your Technical Specifications
Clearly outline the technical requirements for the emergency lights you need. This includes factors such as brightness (measured in lumens), battery life, charging time, and compliance with local standards. Having precise specifications will help you communicate effectively with potential suppliers and ensure that the products meet your operational needs.
Step 2: Conduct Market Research for Suppliers
Research potential suppliers in China who specialize in emergency lighting. Utilize platforms like Alibaba, Global Sources, or industry-specific directories to identify manufacturers. Assess their market reputation by reading reviews and checking their business licenses to ensure they are legitimate and capable of fulfilling your order.
Step 3: Verify Supplier Certifications
Ensure that your potential suppliers possess the necessary certifications, such as ISO 9001 for quality management and CE marking for compliance with European standards. Certifications can be indicative of a supplier’s commitment to quality and safety. Request copies of these certifications directly from the supplier to confirm their validity.
Step 4: Request Samples for Testing
Before placing a bulk order, request samples of the emergency lights. This allows you to evaluate the product’s quality, performance, and compliance with your specifications. During testing, check factors such as durability, brightness, and battery efficiency to ensure they meet your standards.
Step 5: Assess Production Capabilities and Lead Times
Inquire about the supplier’s production capacity and lead times. Understanding their ability to meet your order volume and delivery timeline is crucial for planning. Consider asking for production schedules and any past performance data related to similar orders to gauge reliability.
Step 6: Negotiate Pricing and Payment Terms
Once you have selected a supplier, engage in negotiations regarding pricing, payment terms, and order quantities. Be clear about your budget and any additional costs such as shipping and customs duties. Establishing favorable payment terms can protect your investment and minimize financial risk.
Step 7: Establish a Quality Control Process
Implement a quality control process for your order. This may include setting up inspections during production and prior to shipment. Clearly communicate your quality expectations to the supplier and consider hiring a third-party inspection service to ensure that the products meet your specifications before they leave China.
By following this checklist, B2B buyers can make informed decisions when sourcing emergency lights from China, ensuring both product quality and supplier reliability.
Comprehensive Cost and Pricing Analysis for emergency light china Sourcing
What Are the Key Cost Components in Emergency Light Manufacturing from China?
Understanding the cost structure is essential for B2B buyers sourcing emergency lights from China. The primary cost components include:
-
Materials: The quality and type of materials used, such as LED bulbs, batteries, and casings, significantly affect the price. High-quality materials may incur higher upfront costs but can lead to better performance and durability.
-
Labor: Labor costs in China can vary based on the region and the skill level required. Skilled workers may demand higher wages, but their expertise can improve production quality.
-
Manufacturing Overhead: This includes utilities, rent, and administrative expenses associated with running a manufacturing facility. Efficient factories often have lower overhead costs, impacting the final price.
-
Tooling: Initial tooling costs for molds and production setups can be substantial, especially for custom designs. However, these costs can be amortized over large production runs, reducing the per-unit cost.
-
Quality Control (QC): Implementing rigorous QC processes is crucial for ensuring product reliability, particularly for emergency lights. While this adds to the cost, it can prevent costly returns and warranty claims.
-
Logistics: Shipping costs, including freight and insurance, can fluctuate based on distance and shipping methods. Incoterms (International Commercial Terms) chosen will also affect the logistics cost.
-
Margin: Suppliers typically add a margin to cover their costs and profit. This can vary significantly based on the supplier’s pricing strategy and market conditions.
How Do Price Influencers Affect Sourcing Costs for Emergency Lights?
Several factors influence the pricing of emergency lights sourced from China:
-
Volume/MOQ (Minimum Order Quantity): Suppliers often provide better pricing for larger orders. Negotiating for higher quantities can yield significant savings.
-
Specifications and Customization: Customized products may come with additional design and tooling costs. Clearly defining specifications can help avoid unexpected expenses.
-
Materials: The choice between standard and premium materials will directly impact the cost. Buyers should weigh the long-term benefits of higher-quality materials against initial costs.
-
Quality and Certifications: Products with certifications (e.g., CE, UL) may have higher costs due to compliance testing and documentation. However, these certifications can enhance marketability and customer trust.
-
Supplier Factors: The reputation and reliability of the supplier can affect pricing. Established suppliers may charge more due to their quality assurance processes and service levels.
-
Incoterms: Choosing the right Incoterm can significantly affect total costs. For instance, terms like FOB (Free on Board) place more responsibility on the buyer for shipping, while terms like DDP (Delivered Duty Paid) can simplify logistics but may come at a higher price.
What Are the Best Buyer Tips for Cost-Efficiency in Emergency Light Sourcing?
To maximize cost efficiency when sourcing emergency lights from China, consider the following strategies:
-
Negotiate Effectively: Establish a strong relationship with suppliers and engage in thorough negotiations. Understanding the supplier’s cost structure can provide leverage during discussions.
-
Evaluate Total Cost of Ownership (TCO): Look beyond the purchase price. Consider factors such as durability, energy efficiency, and maintenance costs when assessing the overall value of emergency lights.
-
Research and Compare Suppliers: Conduct thorough market research to identify potential suppliers. Comparing quotes and quality can lead to better pricing and product selection.
-
Understand Pricing Nuances: Be aware of seasonal fluctuations in pricing and demand, as these can impact costs. For instance, prices may rise during peak manufacturing seasons or in response to increased demand due to natural disasters.
Disclaimer on Indicative Prices
Prices for emergency lights can vary widely based on the aforementioned factors. Buyers should request detailed quotes from multiple suppliers and consider the total cost implications before making purchasing decisions.
Alternatives Analysis: Comparing emergency light china With Other Solutions
When considering emergency lighting solutions, it’s essential to evaluate various alternatives to ensure the best fit for your organization’s needs. While ‘Emergency Light China’ represents a popular choice, several other technologies and methods exist that may offer distinct advantages or suit specific operational requirements better. This analysis compares ‘Emergency Light China’ with two viable alternatives: LED Emergency Lighting Systems and Solar-Powered Emergency Lights.
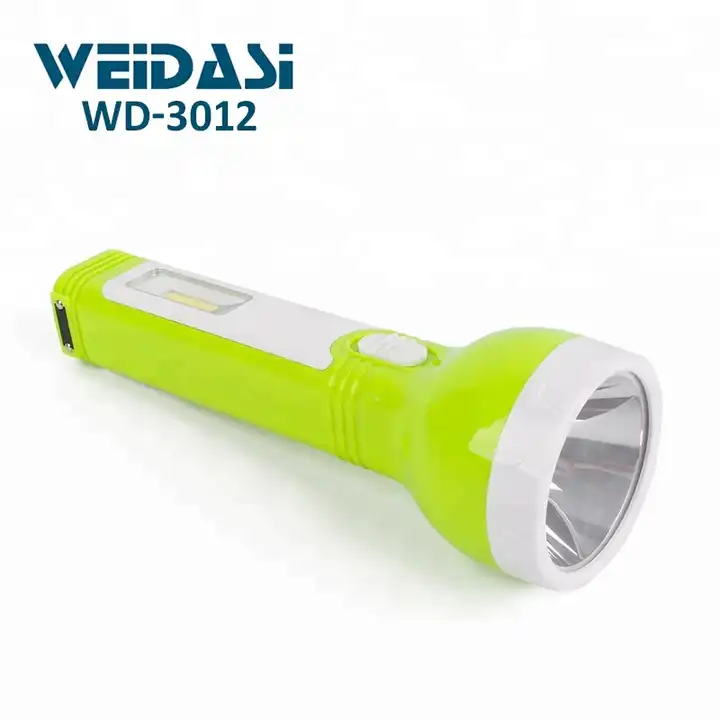
A stock image related to emergency light china.
Comparison Table of Emergency Lighting Solutions
Comparison Aspect | Emergency Light China | LED Emergency Lighting Systems | Solar-Powered Emergency Lights |
---|---|---|---|
Performance | Reliable illumination for short durations | High brightness, longer duration | Variable; depends on sunlight availability |
Cost | Competitive pricing | Higher initial investment but lower long-term costs | Moderate; savings on electricity, but initial setup can be high |
Ease of Implementation | Straightforward installation | Requires planning for optimal placement | Installation can be complex; requires space for solar panels |
Maintenance | Low maintenance; battery replacement needed | Minimal maintenance; LED lifespan is long | Periodic cleaning and battery checks required |
Best Use Case | Short-term outages, industrial settings | Long-term solutions for commercial buildings | Areas with abundant sunlight, remote locations |
What Are the Advantages and Disadvantages of LED Emergency Lighting Systems?
LED Emergency Lighting Systems are increasingly popular due to their superior performance and efficiency. They provide high brightness levels that can illuminate large areas effectively. The lifespan of LED bulbs is significantly longer than traditional bulbs, leading to reduced maintenance costs over time. However, the initial investment can be higher, making them less attractive for businesses with tight budgets. Additionally, proper installation is crucial to maximize their effectiveness, which may require skilled personnel.
How Do Solar-Powered Emergency Lights Compare?
Solar-Powered Emergency Lights offer a sustainable alternative that harnesses solar energy, making them ideal for locations with ample sunlight. They can significantly reduce electricity costs and are environmentally friendly. However, their performance is contingent on weather conditions; during cloudy days or in regions with limited sunlight, their effectiveness can be compromised. Moreover, installation may be more complex due to the need for solar panels, which requires adequate space and orientation to capture sunlight efficiently.
Conclusion: How Can B2B Buyers Choose the Right Emergency Lighting Solution?
Selecting the right emergency lighting solution hinges on evaluating your specific operational needs, budget constraints, and environmental factors. ‘Emergency Light China’ may be the most cost-effective option for businesses requiring reliable short-term lighting. However, for those looking for long-term solutions with minimal maintenance, LED Emergency Lighting Systems may provide better value. Conversely, if sustainability and reduced energy costs are paramount, Solar-Powered Emergency Lights could be the best fit. By carefully assessing these alternatives and understanding their respective advantages and disadvantages, B2B buyers can make informed decisions that align with their strategic goals.
Essential Technical Properties and Trade Terminology for emergency light china
What Are the Key Technical Properties of Emergency Lights from China?
When sourcing emergency lights from China, it’s vital for international B2B buyers to understand the key technical properties that influence both performance and compliance. Below are critical specifications that should be evaluated:
-
Material Grade
– Emergency lights are typically made from materials like polycarbonate or aluminum. Polycarbonate is favored for its durability and impact resistance, while aluminum offers lightweight and excellent heat dissipation. Knowing the material grade helps buyers assess the product’s longevity and suitability for various environments. -
Lumen Output
– This metric indicates the total amount of light emitted by the emergency light. A higher lumen output is essential for effective illumination during emergencies. Buyers should consider the lumen requirements based on the intended application, ensuring adequate brightness for safety. -
Battery Life
– The duration that an emergency light can operate on battery power is crucial. A longer battery life means less frequent recharging or replacement, which is critical in emergency situations. Buyers must inquire about battery type (e.g., lithium-ion, lead-acid) and expected runtime to ensure reliability. -
Charging Time
– This property refers to how long it takes for the emergency light to fully recharge. Efficient charging times are essential for readiness, especially in regions where power supply may be inconsistent. Buyers should seek products that balance quick charging with battery longevity. -
Ingress Protection Rating (IP Rating)
– The IP rating indicates the level of protection against dust and water. For outdoor or industrial applications, a higher IP rating (e.g., IP65 or IP67) ensures the emergency lights can withstand harsh conditions. Understanding this rating helps buyers select suitable products for specific environments. -
Tolerance Levels
– This specification refers to the permissible limits of variation in dimensions and performance. High tolerance levels ensure that the lights function as intended and fit perfectly within their designated installations. Buyers should verify tolerance specifications to avoid compatibility issues.
What Are Common Trade Terms Related to Emergency Lights?
In addition to technical specifications, understanding industry terminology is vital for smooth transactions and negotiations. Here are some common terms used in the emergency lights trade:
-
OEM (Original Equipment Manufacturer)
– This term refers to a company that produces parts or equipment that may be marketed by another manufacturer. In the context of emergency lights, an OEM might create custom designs or specifications for a buyer’s brand. Knowing about OEM options can provide flexibility in product offerings. -
MOQ (Minimum Order Quantity)
– This is the smallest quantity of a product that a supplier is willing to sell. Understanding MOQ is essential for buyers, as it affects inventory management and initial investment. Buyers should negotiate MOQs that align with their purchasing needs and market demand. -
RFQ (Request for Quotation)
– An RFQ is a document that a buyer sends to suppliers to request pricing and other details for specific products. This process allows buyers to compare offers and select the most competitive options. Crafting a clear RFQ can facilitate better pricing and terms. -
Incoterms (International Commercial Terms)
– These are international rules that define the responsibilities of sellers and buyers in shipping contracts. Understanding Incoterms helps clarify who is responsible for shipping costs, insurance, and risk during transit. Familiarity with these terms aids in negotiating favorable shipping conditions. -
Lead Time
– This term refers to the time it takes from placing an order to receiving the product. For emergency lights, shorter lead times can be critical, especially in urgent situations. Buyers should inquire about lead times to ensure timely delivery for their projects. -
Warranty Period
– The warranty period indicates how long the manufacturer guarantees the product against defects. A longer warranty can be a sign of quality and reliability. Buyers should carefully review warranty terms to protect their investment and ensure product support.
By understanding these technical properties and trade terms, B2B buyers can make informed decisions when sourcing emergency lights from China, ensuring they meet their operational needs while navigating international trade complexities effectively.
Navigating Market Dynamics and Sourcing Trends in the emergency light china Sector
What Are the Current Market Dynamics and Key Trends in the Emergency Light Sector?
The emergency light sector is experiencing significant growth driven by several global factors, including increased urbanization, the rise in natural disasters, and a growing emphasis on safety regulations. For international B2B buyers, particularly those from Africa, South America, the Middle East, and Europe, understanding these dynamics is crucial for making informed sourcing decisions. The demand for reliable and efficient emergency lighting solutions is on the rise, particularly in regions prone to power outages and emergencies.
Emerging technologies such as LED advancements and smart lighting systems are reshaping the market landscape. These innovations not only enhance energy efficiency but also provide features like motion sensors and remote monitoring capabilities. Furthermore, the increasing integration of IoT (Internet of Things) in emergency lighting systems allows for real-time monitoring and alerts, which is particularly valuable for businesses in sectors such as healthcare, hospitality, and industrial facilities. Buyers should seek suppliers that offer these advanced technologies to stay competitive.
Another trend is the shift towards localized sourcing. B2B buyers are increasingly looking to source emergency lights from local manufacturers to reduce lead times and transportation costs. This trend is particularly pronounced in Europe and parts of Africa, where supply chain disruptions have highlighted the importance of regional sourcing. Understanding local regulations and compliance standards is essential for ensuring that products meet safety requirements in different markets.
How Can International Buyers Ensure Sustainability and Ethical Sourcing in Emergency Light Procurement?
Sustainability is becoming a critical factor in the procurement process for emergency lights. International buyers must consider the environmental impact of their sourcing choices, as the production and disposal of lighting products can contribute significantly to pollution and waste. Buyers should prioritize suppliers who utilize eco-friendly materials and manufacturing processes.
Certifications such as Energy Star, RoHS (Restriction of Hazardous Substances), and ISO 14001 can serve as indicators of a supplier’s commitment to sustainability. These certifications ensure that products are energy-efficient and produced with minimal environmental impact. Buyers from regions like Europe, where sustainability regulations are stringent, should place a strong emphasis on these certifications when evaluating potential suppliers.
Moreover, ethical sourcing practices are essential to foster positive brand reputation and compliance with international labor laws. Buyers should conduct due diligence on suppliers to ensure that their supply chains are free from exploitative labor practices. This includes assessing supplier labor practices and ensuring they comply with the International Labour Organization’s (ILO) guidelines. By prioritizing suppliers committed to ethical practices, buyers can contribute to a more sustainable and responsible global marketplace.
What Is the Brief History of Emergency Lighting Solutions in the Global Market?
The evolution of emergency lighting solutions dates back to the early 20th century when basic battery-powered lights were developed for use in commercial buildings. Over the decades, advancements in technology have transformed emergency lighting into sophisticated systems integrated with modern safety protocols.
The introduction of LED technology in the late 20th century marked a significant turning point, offering longer lifespans and improved energy efficiency. In recent years, the focus has shifted towards smart emergency lighting systems that connect to broader building management systems, reflecting a growing trend towards automation and efficiency in emergency preparedness.
For international B2B buyers, understanding this historical context can provide valuable insights into the capabilities and reliability of modern emergency lighting solutions, enabling them to make informed decisions when sourcing products for their organizations.
Frequently Asked Questions (FAQs) for B2B Buyers of emergency light china
-
How do I find reliable suppliers for emergency lights in China?
Finding reliable suppliers in China for emergency lights involves several steps. Start by researching manufacturers on platforms like Alibaba, Global Sources, or Made-in-China. Look for suppliers with verified credentials, positive reviews, and a robust business history. Request references and verify them to ensure quality. Consider attending trade shows or industry expos in China to meet suppliers face-to-face. Additionally, engage third-party inspection companies to audit potential suppliers before making a commitment. -
What certifications should I look for when sourcing emergency lights from China?
When sourcing emergency lights from China, ensure that suppliers possess relevant certifications such as CE, UL, and RoHS, which indicate compliance with safety and environmental standards. Depending on your target market, additional certifications like ISO 9001 for quality management systems may also be beneficial. These certifications not only ensure the product’s safety but also enhance credibility and trust among your customers. -
What is the minimum order quantity (MOQ) for emergency lights from Chinese suppliers?
The minimum order quantity (MOQ) for emergency lights varies by supplier and can range from 100 to 1,000 units. Some manufacturers may offer lower MOQs for specific product lines or during promotional periods. However, lower MOQs may come with higher per-unit costs. It’s advisable to negotiate with suppliers based on your purchase volume and explore potential discounts for larger orders. -
What payment terms are commonly used in international trade for emergency lights?
Common payment terms in international trade for emergency lights include T/T (telegraphic transfer), L/C (letter of credit), and PayPal for smaller transactions. Typically, suppliers may require a 30% upfront deposit, with the remaining balance due before shipment. Ensure to clarify payment terms in your contract to avoid misunderstandings and consider using escrow services for added security. -
How can I ensure the quality of emergency lights sourced from China?
To ensure quality, implement a thorough quality assurance (QA) process. Request samples before placing a large order to assess product quality firsthand. Establish clear specifications and standards in your purchase agreement. Consider hiring third-party quality inspection services to conduct on-site inspections during production and before shipment. Regular communication with suppliers throughout the production process also helps address potential issues early. -
What logistics considerations should I keep in mind when importing emergency lights from China?
When importing emergency lights from China, consider shipping methods (air vs. sea freight), customs regulations, and potential tariffs. Assess lead times and choose a logistics partner experienced in handling international shipments. Ensure proper documentation, including commercial invoices and packing lists, to facilitate smooth customs clearance. Additionally, factor in storage and distribution costs upon arrival in your target market. -
What customization options are available for emergency lights sourced from China?
Many Chinese manufacturers offer customization options for emergency lights, including design alterations, branding, and specific functionality. Discuss your requirements directly with suppliers to explore available options. Customization may involve additional costs and longer lead times, so ensure these factors are considered in your planning. Request a prototype before committing to large orders to ensure the final product meets your specifications. -
How do international trade regulations affect sourcing emergency lights from China?
International trade regulations can significantly impact sourcing emergency lights from China. It’s essential to be aware of import tariffs, trade agreements, and compliance with safety standards in your target market. Research the specific regulations that apply to electrical products, including labeling requirements and environmental regulations. Consulting with a trade expert or legal advisor can help navigate these complexities and ensure compliance with local laws.
Important Disclaimer & Terms of Use
⚠️ Important Disclaimer
The information provided in this guide, including content regarding manufacturers, technical specifications, and market analysis, is for informational and educational purposes only. It does not constitute professional procurement advice, financial advice, or legal advice.
While we have made every effort to ensure the accuracy and timeliness of the information, we are not responsible for any errors, omissions, or outdated information. Market conditions, company details, and technical standards are subject to change.
B2B buyers must conduct their own independent and thorough due diligence before making any purchasing decisions. This includes contacting suppliers directly, verifying certifications, requesting samples, and seeking professional consultation. The risk of relying on any information in this guide is borne solely by the reader.
Strategic Sourcing Conclusion and Outlook for emergency light china
What Are the Key Takeaways for B2B Buyers in Emergency Lighting from China?
In the rapidly evolving landscape of emergency lighting solutions, strategic sourcing remains paramount for international B2B buyers, particularly those operating in Africa, South America, the Middle East, and Europe. Understanding the regional market dynamics and regulatory requirements is crucial for selecting reliable suppliers. Buyers should prioritize manufacturers that not only offer high-quality products but also demonstrate compliance with international safety standards and certifications.
How Can Strategic Sourcing Enhance Your Supply Chain?
Investing in strategic sourcing can significantly enhance your supply chain resilience. By fostering partnerships with reputable Chinese manufacturers, businesses can gain access to innovative technologies and cost-effective solutions tailored to meet diverse emergency lighting needs. Additionally, leveraging data analytics can help identify trends and optimize procurement processes, ensuring that your organization remains competitive in an increasingly globalized market.
What Is the Future Outlook for Emergency Lighting Solutions?
As the demand for reliable emergency lighting continues to rise, particularly in regions prone to natural disasters or infrastructural challenges, the outlook for sourcing from China appears promising. Buyers are encouraged to stay ahead by embracing sustainable practices and exploring emerging technologies such as smart lighting systems. Now is the time to act—evaluate your sourcing strategies and engage with reputable suppliers to secure a competitive edge in this essential market.