Discover Cost-Saving Tips from Top Panel Manufacturers (2025)
Introduction: Navigating the Global Market for panel manufacturer
Navigating the global market for panel manufacturing can be a daunting task for international B2B buyers, especially those in regions like Africa, South America, the Middle East, and Europe. Sourcing high-quality panels that meet specific requirements, whether for construction, automotive, or electronics, often presents challenges in terms of supplier reliability, product quality, and cost-effectiveness. This guide offers a comprehensive overview of the panel manufacturing landscape, detailing the various types of panels available, their applications, and the critical factors to consider when selecting suppliers.
By exploring the nuances of the panel manufacturing sector, this guide empowers B2B buyers to make informed purchasing decisions. We will delve into essential topics such as evaluating supplier credentials, understanding pricing structures, and identifying the latest trends in panel technology. Furthermore, we will provide insights tailored for buyers from diverse markets, including Colombia and Italy, ensuring relevance and applicability across different regions.
Ultimately, our goal is to equip you with the knowledge and tools necessary to navigate the complexities of sourcing panels in today’s competitive global marketplace. With this guide, you will not only enhance your procurement strategies but also foster long-lasting partnerships with reputable manufacturers, driving your business toward success.
Understanding panel manufacturer Types and Variations
Type Name | Key Distinguishing Features | Primary B2B Applications | Brief Pros & Cons for Buyers |
---|---|---|---|
Metal Panel Manufacturers | Focus on durability and strength; often custom designs available. | Construction, automotive, industrial machinery. | Pros: High durability, customizable. Cons: Heavier, may require specialized handling. |
Composite Panel Manufacturers | Utilizes a combination of materials for lightness and insulation. | Building facades, signage, transportation. | Pros: Lightweight, excellent insulation. Cons: Can be costlier than traditional materials. |
Plastic Panel Manufacturers | Variety of plastics used; often lightweight and versatile. | Packaging, construction, automotive interiors. | Pros: Cost-effective, resistant to corrosion. Cons: Less durable than metal options, may have lower aesthetic appeal. |
Wood Panel Manufacturers | Natural materials, often eco-friendly; available in various finishes. | Furniture, interior design, cabinetry. | Pros: Aesthetic appeal, sustainable options. Cons: Susceptible to moisture damage, requires maintenance. |
Glass Panel Manufacturers | Offers transparency and aesthetic appeal; often treated for safety. | Facades, windows, interior partitions. | Pros: Modern look, energy-efficient options available. Cons: Fragile, can be expensive. |
What Are the Key Characteristics of Metal Panel Manufacturers?
Metal panel manufacturers are recognized for their emphasis on strength and durability. They often provide custom designs tailored to specific project needs, making them ideal for heavy-duty applications such as construction and industrial machinery. Buyers should consider factors such as weight and handling requirements, as metal panels can be heavier and necessitate specialized equipment for installation.
How Do Composite Panel Manufacturers Stand Out?
Composite panel manufacturers utilize a combination of materials, usually combining lightweight cores with durable outer layers. This innovation leads to panels that are not only light but also offer superior insulation properties, making them suitable for building facades and transportation applications. Buyers should weigh the initial higher cost against the long-term energy savings and performance benefits.
What Are the Advantages of Plastic Panel Manufacturers?
Plastic panel manufacturers focus on versatility and cost-effectiveness, producing panels from various plastics that are lightweight and resistant to corrosion. They find applications in packaging, construction, and automotive interiors. Buyers should consider the trade-off between cost and durability, as plastic panels may not withstand harsh conditions as well as metal or composite options.
Why Choose Wood Panel Manufacturers for Your Projects?
Wood panel manufacturers offer natural materials that appeal to aesthetics and sustainability. These panels are frequently used in furniture, cabinetry, and interior design. However, buyers must consider the potential for moisture damage and the need for maintenance, which could impact long-term costs and usability in certain environments.
What Makes Glass Panel Manufacturers Unique?
Glass panel manufacturers provide products that combine transparency with modern aesthetics. These panels are often treated for safety and can enhance energy efficiency when used in facades and windows. While they offer an elegant solution, buyers should be mindful of the fragility and higher costs associated with glass panels, which may not be suitable for all applications.
Related Video: What are the types of electrical panels? | Types of HT Panel & LT Panel
Key Industrial Applications of panel manufacturer
Industry/Sector | Specific Application of Panel Manufacturer | Value/Benefit for the Business | Key Sourcing Considerations for this Application |
---|---|---|---|
Construction | Prefabricated Building Panels | Reduced construction time and labor costs | Compliance with local building codes and standards |
Renewable Energy | Solar Panel Manufacturing | Enhanced sustainability and energy efficiency | Quality certifications and warranty terms |
Automotive | Interior and Exterior Panels for Vehicles | Improved aesthetics and safety features | Material durability and weight considerations |
Electronics | Printed Circuit Boards (PCBs) | Higher reliability and performance in devices | Precision in manufacturing and supply chain stability |
Furniture | Decorative and Functional Panels for Furniture | Customization and design flexibility | Availability of diverse materials and finishes |
How are Prefabricated Building Panels Used in Construction?
Prefabricated building panels are revolutionizing the construction industry by allowing for rapid assembly and reduced on-site labor. These panels can be manufactured off-site and shipped to the construction site, significantly cutting down construction time. For international buyers in regions like Africa and South America, sourcing quality panels that meet local building codes is crucial to ensure safety and compliance. Additionally, understanding the logistics involved in transporting these panels can help mitigate potential delays.
What Role do Solar Panels Play in Renewable Energy?
Solar panel manufacturing is pivotal for businesses aiming to enhance sustainability and reduce energy costs. By investing in high-quality solar panels, companies can leverage renewable energy sources to power their operations, reducing reliance on fossil fuels. Buyers from the Middle East and Europe should consider the efficiency ratings and certifications of solar panels when sourcing, as these factors can influence long-term savings and performance. It’s also essential to evaluate the supplier’s ability to provide ongoing support and maintenance services.
How are Interior and Exterior Panels Used in the Automotive Industry?
In the automotive sector, interior and exterior panels are critical for both functionality and aesthetics. These panels contribute to vehicle safety, comfort, and design, making them essential components of modern automobiles. B2B buyers in Europe, particularly in Italy, should focus on sourcing panels that meet stringent safety standards while also offering customization options for branding. Furthermore, understanding the material properties, such as weight and durability, is vital for enhancing vehicle performance.
How are Printed Circuit Boards (PCBs) Utilized in Electronics?
Printed Circuit Boards (PCBs) are the backbone of electronic devices, ensuring reliable connections between components. For international buyers in the electronics sector, sourcing PCBs that meet specific performance criteria is essential for maintaining product quality. Buyers should prioritize manufacturers with advanced production capabilities and quality assurance processes to ensure that the PCBs can withstand the demands of modern electronics. Additionally, understanding the lead times and logistics involved in sourcing can prevent disruptions in the supply chain.
What Advantages do Decorative and Functional Panels Provide in Furniture?
Decorative and functional panels are increasingly popular in the furniture industry, allowing for customization and design flexibility. These panels can be used in a wide range of applications, from cabinetry to tabletops, enhancing the aesthetic appeal of furniture. Buyers in South America and Europe should consider the availability of various materials and finishes when sourcing, as these can significantly impact the final product’s look and feel. Furthermore, understanding the supplier’s capabilities for custom designs can lead to unique product offerings that cater to specific market demands.
Related Video: Industrial Control Panel Basics
3 Common User Pain Points for ‘panel manufacturer’ & Their Solutions
Scenario 1: Navigating Quality Control Issues in Panel Manufacturing
The Problem:
B2B buyers often face significant challenges when it comes to ensuring the quality of panels sourced from manufacturers, especially when dealing with international suppliers. For instance, a construction firm in South America may purchase panels for a large commercial project, only to discover upon arrival that the panels do not meet local building codes or specifications. This not only results in project delays but also incurs additional costs for reordering compliant materials, and potential penalties for non-compliance.
The Solution:
To mitigate quality control issues, buyers should implement a thorough supplier vetting process that includes site visits or third-party audits of manufacturing facilities. Establish clear specifications and standards before placing orders, ensuring that the manufacturer understands local regulations and quality expectations. Additionally, consider requesting samples before committing to larger orders, allowing for quality assessment and adjustments as needed. Engaging with suppliers who offer transparent quality assurance processes and certifications can also help minimize risks related to product compliance.
Scenario 2: Overcoming Language and Cultural Barriers in International Sourcing
The Problem:
For B2B buyers from Africa and Europe, language and cultural differences can pose significant challenges when negotiating with panel manufacturers in other regions. Misunderstandings can lead to incorrect orders, delays, and even damaged business relationships. A buyer in Italy negotiating with a supplier in the Middle East might find it difficult to articulate specific needs, resulting in miscommunication about product specifications or delivery timelines.
The Solution:
To bridge the language and cultural gaps, buyers should consider hiring a local intermediary or consultant familiar with both the panel manufacturing industry and the cultural nuances of the supplier’s region. This professional can facilitate communication, ensuring that specifications are accurately conveyed and understood. Additionally, utilizing translation services for important documents and contracts can prevent misunderstandings. Establishing a clear communication plan that includes regular updates and checkpoints can also help foster a collaborative relationship, reducing the likelihood of errors.
Scenario 3: Addressing Supply Chain Disruptions and Delivery Delays
The Problem:
Supply chain disruptions are a common pain point for B2B buyers in the panel manufacturing sector, particularly in today’s global market. A buyer in Africa might experience significant delays due to logistical challenges, such as port congestion or customs clearance issues, leading to stalled projects and increased costs. These disruptions can be unpredictable and difficult to manage, causing frustration and potential loss of business.
The Solution:
To combat supply chain issues, buyers should diversify their sourcing strategy by not relying solely on one supplier or region. Developing relationships with multiple manufacturers can provide backup options in case of disruptions. It’s also beneficial to work closely with logistics partners who have a proven track record in navigating international shipping challenges. Regularly assess the supply chain landscape, including potential risks related to geopolitical factors or natural disasters, and develop contingency plans to address these risks. Additionally, leveraging technology such as supply chain management software can enhance visibility into the logistics process, allowing buyers to anticipate and respond to potential delays proactively.
Strategic Material Selection Guide for panel manufacturer
When selecting materials for panel manufacturing, understanding the properties, advantages, disadvantages, and specific considerations for international markets is crucial. Below, we analyze four common materials used in panel manufacturing, focusing on their performance characteristics, application impacts, and relevance to international B2B buyers, particularly in regions such as Africa, South America, the Middle East, and Europe.
What Are the Key Properties of Aluminum Panels?
Aluminum is a lightweight metal known for its excellent strength-to-weight ratio, corrosion resistance, and thermal conductivity. Its temperature rating typically ranges from -200°C to 600°C, making it suitable for various environments.
Pros and Cons:
– Pros: Aluminum panels are durable, lightweight, and easy to fabricate. They offer good resistance to corrosion, which is critical in humid or coastal environments.
– Cons: The initial cost can be higher than other materials, and while they are durable, they can be prone to denting under impact.
Impact on Application:
Aluminum panels are ideal for applications requiring lightweight solutions, such as in the automotive and aerospace industries. They can also be used in architectural applications due to their aesthetic appeal.
Considerations for International Buyers:
International buyers must ensure compliance with standards such as ASTM B209 for aluminum sheet and plate. In regions like Europe, EN 573-1 is also relevant. Additionally, buyers should consider the availability of aluminum in their local markets, as supply chains may vary significantly.
What Are the Advantages of Using Steel Panels?
Steel panels are renowned for their high strength and durability, making them ideal for structural applications. They have a high temperature rating, generally ranging from -20°C to 600°C.
Pros and Cons:
– Pros: Steel panels are robust and can withstand heavy loads, making them suitable for construction and industrial applications. They are also cost-effective compared to aluminum.
– Cons: Steel is heavier than aluminum, which can increase transportation costs. It is also susceptible to corrosion unless treated, necessitating protective coatings.
Impact on Application:
Steel panels are commonly used in construction, particularly for load-bearing structures. They are also used in manufacturing environments due to their strength.
Considerations for International Buyers:
Buyers should be aware of standards such as ASTM A1008 for cold-rolled steel and ASTM A992 for structural steel. In regions like the Middle East, where humidity can be high, corrosion-resistant coatings are essential.
How Do Composite Panels Benefit Panel Manufacturers?
Composite panels, often made from a combination of materials like aluminum and polyethylene, provide a unique balance of properties. They typically have a temperature rating of up to 80°C.
Pros and Cons:
– Pros: Composite panels are lightweight, offer excellent insulation properties, and have good aesthetic flexibility. They are also resistant to corrosion and UV light.
– Cons: While they are versatile, composite panels can be more expensive to manufacture, and the bond between materials can degrade over time.
Impact on Application:
These panels are widely used in architectural applications, including facades and interior partitions, due to their aesthetic versatility and insulation properties.
Considerations for International Buyers:
Compliance with standards such as ASTM C578 for rigid cellular polystyrene and EN 14509 for composite panels is essential. Buyers should also consider the environmental impact and recycling options for composite materials.
What Are the Key Features of Fiberglass Panels?
Fiberglass panels are made from glass fibers and resin, offering excellent strength and lightweight properties. They can withstand temperatures up to 120°C.
Pros and Cons:
– Pros: Fiberglass panels are highly resistant to corrosion, making them ideal for harsh environments. They are also lightweight and easy to install.
– Cons: The manufacturing process can be complex, leading to higher costs. Additionally, they may not be as structurally strong as metal panels.
Impact on Application:
Fiberglass panels are often used in applications requiring chemical resistance, such as in the chemical processing industry or for outdoor signage.
Considerations for International Buyers:
Standards such as ASTM D638 for tensile properties of plastics and ISO 9001 for quality management systems are relevant. Buyers should also consider the availability of skilled labor for installation, as fiberglass can require specialized handling.
Summary Table of Material Selection for Panel Manufacturing
Material | Typical Use Case for panel manufacturer | Key Advantage | Key Disadvantage/Limitation | Relative Cost (Low/Med/High) |
---|---|---|---|---|
Aluminum | Automotive and architectural applications | Lightweight and corrosion-resistant | Higher initial cost, dent-prone | Medium |
Steel | Construction and industrial applications | High strength and cost-effective | Heavier, corrosion-prone | Low |
Composite | Architectural facades and insulation | Excellent insulation and aesthetics | Higher manufacturing costs | High |
Fiberglass | Chemical processing and outdoor signage | Corrosion-resistant and lightweight | Complex manufacturing process | Medium |
This strategic material selection guide provides international B2B buyers with a comprehensive overview of common materials in panel manufacturing, helping them make informed decisions based on their specific regional needs and compliance requirements.
In-depth Look: Manufacturing Processes and Quality Assurance for panel manufacturer
The manufacturing processes and quality assurance practices for panel manufacturers are critical for B2B buyers seeking reliable suppliers. Understanding these processes can help buyers from regions like Africa, South America, the Middle East, and Europe (such as Colombia and Italy) make informed decisions.
What Are the Main Stages of the Manufacturing Process for Panel Manufacturers?
Manufacturing panels involves several key stages, each contributing to the final product’s quality and performance. The main stages include:
-
Material Preparation
This initial stage involves selecting and preparing raw materials such as metal sheets, plastics, or composites. Material quality is crucial; therefore, suppliers often conduct tests to ensure compliance with specifications. Buyers should inquire about the sourcing of materials and whether they meet industry standards. -
Forming
During the forming stage, raw materials are shaped into panels using techniques like stamping, extrusion, or molding. Advanced technologies such as CNC (Computer Numerical Control) machines are frequently employed to achieve precise dimensions and shapes. B2B buyers should ask about the machinery used and the capabilities of the production facility. -
Assembly
In this stage, different components of the panel, such as insulation and outer layers, are assembled. This may involve processes like welding, adhesive bonding, or fastening. The assembly stage is vital for ensuring structural integrity and thermal performance. Buyers should verify the methods used and whether they are consistent with best practices in the industry. -
Finishing
The final stage includes surface treatments, coatings, or painting to enhance aesthetics and durability. This step often involves quality checks to ensure that the finish meets specified requirements. Buyers should request details about finishing techniques and any protective measures used to ensure longevity.
How Is Quality Assurance Integrated Into the Manufacturing Process?
Quality assurance (QA) is a fundamental aspect of the manufacturing process for panel manufacturers. It involves various international standards and industry-specific regulations that ensure products meet customer expectations and safety requirements.
What Are the Relevant International Standards for Quality Assurance?
For B2B buyers, understanding the relevant quality standards is essential. Here are some key standards:
-
ISO 9001: This international standard outlines the criteria for a quality management system (QMS). It emphasizes customer satisfaction and continuous improvement. Buyers should verify if their suppliers are ISO 9001 certified, as this indicates a commitment to quality.
-
CE Marking: Particularly important for products sold in Europe, CE marking signifies compliance with health, safety, and environmental protection standards. Buyers in Europe should ensure that suppliers provide CE certification for their panels.
-
API Standards: For panels used in specific industries like oil and gas, adherence to American Petroleum Institute (API) standards is vital. Buyers should inquire whether suppliers can meet these industry-specific requirements.
What Are the Key Quality Control Checkpoints in the Manufacturing Process?
Quality control (QC) is implemented at various checkpoints throughout the manufacturing process. These checkpoints typically include:
-
Incoming Quality Control (IQC): This initial inspection stage assesses the quality of incoming materials to ensure they meet specifications.
-
In-Process Quality Control (IPQC): Conducted during the manufacturing process, IPQC ensures that production processes are followed correctly, and any deviations are addressed promptly.
-
Final Quality Control (FQC): This final inspection stage occurs before the product is shipped. FQC checks the finished panels against quality standards and specifications.
What Testing Methods Are Commonly Used in Panel Manufacturing?
Testing is an integral part of the QC process. Common testing methods include:
-
Dimensional Inspection: Measurements are taken to ensure that the panels meet specified dimensions and tolerances.
-
Material Testing: This can involve tensile testing, impact testing, or hardness testing to verify the material properties of the panels.
-
Performance Testing: Panels may undergo tests for thermal insulation, fire resistance, or load-bearing capabilities, depending on their intended use.
B2B buyers should request detailed reports of these tests to ensure the panels meet their specific requirements.
How Can B2B Buyers Verify Supplier Quality Control?
Verifying the quality control processes of potential suppliers is crucial for B2B buyers. Here are some strategies:
-
Supplier Audits: Conducting on-site audits allows buyers to assess the manufacturing processes, equipment, and quality assurance practices firsthand. This can provide valuable insights into the supplier’s capabilities.
-
Quality Control Reports: Requesting access to QC reports and certifications can help buyers gauge the supplier’s adherence to international standards and internal quality measures.
-
Third-Party Inspections: Engaging third-party inspection agencies can provide an impartial evaluation of the supplier’s quality assurance processes. This can be particularly beneficial for buyers who are unable to conduct audits themselves.
What Are the Quality Control Nuances for International B2B Buyers?
For B2B buyers from diverse regions, understanding the nuances of quality control is vital:
-
Cultural and Regulatory Differences: Buyers should be aware that quality expectations and regulatory requirements can vary significantly between regions. For example, European standards may be stricter than those in other regions.
-
Language Barriers: Effective communication is essential when discussing quality requirements. Buyers should ensure that suppliers can provide documentation in a language that is understood by all parties involved.
-
Logistics and Transportation: Quality can be affected during transportation. Buyers should consider how panels are packaged and transported to minimize damage and ensure quality upon delivery.
By understanding these manufacturing processes and quality assurance practices, B2B buyers can make informed decisions when selecting panel manufacturers, ensuring they receive high-quality products that meet their specific needs.
Practical Sourcing Guide: A Step-by-Step Checklist for ‘panel manufacturer’
When sourcing a panel manufacturer, it’s essential to follow a structured approach to ensure that you partner with a reliable supplier who meets your specific needs. This guide provides a checklist to help international B2B buyers navigate the sourcing process effectively.
Step 1: Define Your Technical Specifications
Establishing clear technical specifications is crucial for communicating your requirements to potential suppliers. This includes details such as the type of panels needed (e.g., solar panels, insulation panels), dimensions, material quality, and compliance with local standards. Well-defined specifications help avoid misunderstandings and ensure that the products meet your operational requirements.
Step 2: Research Potential Suppliers
Conduct comprehensive research to identify potential panel manufacturers. Use trade directories, industry associations, and online platforms like Alibaba or ThomasNet to compile a list. Pay attention to suppliers with a strong reputation and positive reviews, as this often indicates reliability and quality.
Step 3: Verify Supplier Certifications
Before proceeding, it’s essential to verify that the suppliers hold relevant certifications and quality assurances. Look for ISO certifications, compliance with international standards (like CE or UL), and any other specific certifications relevant to your industry. This step is critical to ensure the products are safe, reliable, and meet quality expectations.
Step 4: Request Samples
Requesting samples from shortlisted manufacturers allows you to evaluate the quality of their products firsthand. Analyze the materials, craftsmanship, and overall performance of the samples. This practical assessment will help you determine if the supplier’s offerings align with your quality standards and expectations.
Step 5: Evaluate Pricing and Payment Terms
Once you’ve narrowed down your options, compare pricing among the manufacturers. Ensure you understand the payment terms, including upfront deposits, payment schedules, and any potential hidden costs. Transparent pricing structures can help avoid unexpected expenses later on and contribute to a smoother transaction process.
Step 6: Assess Manufacturing Capabilities
Understanding the manufacturing capabilities of your chosen suppliers is vital. Inquire about their production capacity, lead times, and technology used in the manufacturing process. This information will help you gauge whether they can meet your order volumes and timelines consistently.
Step 7: Check References and Past Performance
Finally, before making a commitment, reach out to previous clients for references. Ask about their experiences with the supplier, focusing on product quality, delivery timelines, and customer service. This insight can provide valuable context and help you make an informed decision about whether to proceed with the partnership.
By following these steps, B2B buyers can ensure a systematic approach to sourcing panel manufacturers, ultimately leading to successful procurement and long-term partnerships.
Comprehensive Cost and Pricing Analysis for panel manufacturer Sourcing
What Are the Key Cost Components in Panel Manufacturing?
Understanding the cost structure of panel manufacturing is crucial for B2B buyers to make informed purchasing decisions. The primary cost components include:
-
Materials: The choice of raw materials, such as composites, metals, or plastics, significantly impacts the overall cost. High-quality materials may increase initial expenses but can lead to lower long-term maintenance costs.
-
Labor: Labor costs vary widely depending on the region and the skill level required for manufacturing. In countries with lower labor costs, like some parts of Africa and South America, buyers may find more competitive pricing.
-
Manufacturing Overhead: This includes indirect costs such as utilities, rent, and administrative expenses. Efficient manufacturing processes can help minimize overhead, affecting the final price.
-
Tooling: The initial investment in tooling can be substantial, especially for custom panel designs. Buyers should consider whether the tooling costs are included in the quoted price or billed separately.
-
Quality Control (QC): Implementing rigorous QC processes can lead to higher costs upfront but ensures product reliability and reduces the risk of defects, which can be especially important in industries like construction and automotive.
-
Logistics: Shipping costs depend on the distance, volume, and mode of transportation. Buyers should factor in these costs when evaluating suppliers, especially for international sourcing.
-
Margin: The profit margin added by manufacturers can vary. Understanding typical margins in the panel manufacturing industry can help buyers gauge the fairness of the pricing offered.
How Do Price Influencers Affect Panel Manufacturing Costs?
Several factors can influence the pricing of panel manufacturing, including:
-
Volume and Minimum Order Quantity (MOQ): Larger orders often qualify for bulk discounts. Buyers should assess their needs and consider consolidating orders to achieve better pricing.
-
Specifications and Customization: Custom designs typically incur higher costs due to the additional resources required for tooling and production. Buyers should weigh the benefits of customization against the added costs.
-
Materials and Quality Certifications: Higher-grade materials and certifications (like ISO or CE) may elevate costs but can provide assurance of product quality and regulatory compliance.
-
Supplier Factors: The reputation and reliability of suppliers can impact pricing. Established manufacturers may charge more due to their proven track record, while newer players might offer lower prices to gain market share.
-
Incoterms: Understanding international shipping terms (like FOB, CIF) is crucial for estimating total costs. The choice of Incoterms can affect who bears the shipping risk and costs, influencing the final price.
What Are the Best Buyer Tips for Cost Efficiency in Panel Manufacturing?
B2B buyers can leverage several strategies to enhance cost efficiency in sourcing panels:
-
Effective Negotiation: Always negotiate terms and pricing. Understand the market rates and be prepared to walk away if the offer doesn’t meet your budget.
-
Focus on Total Cost of Ownership (TCO): Evaluate not just the purchase price but also factors like maintenance, potential warranty claims, and energy efficiency. A lower upfront cost may lead to higher long-term expenses.
-
Understand Pricing Nuances for International Buyers: Buyers from regions like Africa or South America may face different logistical challenges and tariffs. Researching local regulations and shipping costs can help mitigate unexpected expenses.
-
Request Detailed Quotes: When approaching multiple suppliers, request itemized quotes that break down costs into components. This transparency allows for better comparison and negotiation.
-
Be Aware of Currency Fluctuations: For international transactions, exchange rate volatility can affect pricing. Consider locking in rates or using financial instruments to hedge against currency risks.
Conclusion
While prices in panel manufacturing can vary widely based on numerous factors, understanding the cost structure and price influencers allows B2B buyers to make informed decisions. By implementing strategic purchasing practices, buyers can optimize their sourcing processes and achieve better value from their investments. Always remember that indicative prices are subject to change based on market conditions, so continuous engagement with suppliers is essential for maintaining competitive pricing.
Alternatives Analysis: Comparing panel manufacturer With Other Solutions
Introduction to Alternative Solutions in Panel Manufacturing
When considering panel manufacturing solutions, it is essential to explore various alternatives that can meet your business’s specific requirements. Understanding these alternatives helps international B2B buyers from regions like Africa, South America, the Middle East, and Europe make informed decisions that align with their operational goals, budget constraints, and technological capabilities. The following analysis compares traditional panel manufacturing with other viable solutions, focusing on performance, cost, ease of implementation, maintenance, and best use cases.
Comparison Table of Panel Manufacturing Solutions
Comparison Aspect | Panel Manufacturer | Modular Panel Systems | Advanced Composite Materials |
---|---|---|---|
Performance | High durability and strength | Good strength-to-weight ratio | Excellent thermal and acoustic insulation |
Cost | Moderate to high | Generally lower initial costs | Higher upfront costs |
Ease of Implementation | Requires skilled labor | Easier to assemble, less labor-intensive | Complex manufacturing process |
Maintenance | Moderate maintenance needs | Low maintenance requirements | Moderate maintenance, depending on usage |
Best Use Case | Industrial and commercial applications | Quick construction projects | High-performance applications (e.g., aerospace) |
Detailed Breakdown of Alternative Solutions
What are Modular Panel Systems and How Do They Compare?
Modular panel systems are prefabricated panels designed for easy assembly on-site, making them an attractive alternative for many construction projects. One of their primary advantages is the lower initial cost compared to traditional panel manufacturing. They also require less skilled labor for installation, which can significantly reduce labor costs and time. However, while they provide good structural integrity, their performance may not match that of custom-manufactured panels in extreme conditions. These systems are best suited for projects with tight timelines and budgets, such as residential buildings or temporary structures.
How Do Advanced Composite Materials Measure Up?
Advanced composite materials, often used in specialized applications such as aerospace and automotive industries, offer unique benefits. They provide excellent thermal and acoustic insulation and possess a high strength-to-weight ratio, making them ideal for applications requiring lightweight yet durable solutions. However, the manufacturing process for composites can be complex and typically involves higher upfront costs. Maintenance is generally moderate, depending on the environment and usage. This solution is best for high-performance applications where weight and insulation are critical factors.
Conclusion: Choosing the Right Solution for Your Needs
Selecting the right panel manufacturing solution requires a thorough understanding of your specific needs and constraints. B2B buyers should consider the performance requirements, budgetary limitations, and the complexity of implementation when evaluating options. For projects that prioritize cost and speed, modular panel systems may be the best fit. In contrast, for applications demanding high performance and durability, advanced composite materials could be the ideal choice. Ultimately, aligning the chosen solution with your operational goals will lead to greater efficiency and success in your projects.
Essential Technical Properties and Trade Terminology for panel manufacturer
What Are the Essential Technical Properties for Panel Manufacturing?
In the realm of panel manufacturing, understanding the critical specifications can significantly influence purchasing decisions. Here are some essential technical properties:
1. Material Grade: What Should Buyers Know?
Material grade refers to the specific type and quality of the materials used in panel production, such as plywood, MDF (Medium Density Fiberboard), or particleboard. Different grades indicate varying levels of durability, moisture resistance, and strength. For B2B buyers, selecting the appropriate material grade is crucial for ensuring that the panels meet the required performance standards for their intended applications, such as construction or furniture manufacturing.
2. Tolerance: Why Is It Important?
Tolerance defines the allowable deviation from specified dimensions in panel production. This specification is vital for ensuring that panels fit together correctly during assembly, impacting overall structural integrity. For international buyers, understanding tolerance levels can help prevent costly errors and ensure compatibility with existing systems or components.
3. Thickness: How Does It Affect Performance?
Thickness is a critical specification that influences a panel’s strength, weight, and insulation properties. Panels may come in various thicknesses, and the choice often depends on the application—thicker panels can provide better sound insulation and structural support. Buyers must assess their specific needs to choose the right thickness that balances durability and cost.
4. Surface Finish: What Are the Options?
The surface finish of a panel can significantly affect its aesthetic appeal and functionality. Common finishes include melamine, laminate, and veneer. Each offers different benefits, such as ease of cleaning, scratch resistance, and design versatility. Buyers should consider the environment in which the panels will be used when selecting a surface finish, as this can impact maintenance and longevity.
5. Density: How Does It Impact Quality?
Density refers to the mass of the material per unit volume and is a critical factor in determining the strength and durability of panels. Higher density panels typically offer better performance in terms of load-bearing capacity and resistance to wear and tear. Buyers should evaluate their application requirements to select panels with the appropriate density.
What Are Common Trade Terms in Panel Manufacturing?
Familiarity with industry jargon is essential for effective communication and negotiation in the B2B space. Here are several key terms:
1. OEM (Original Equipment Manufacturer): What Does It Mean?
An OEM refers to a company that produces components or products that are used in another company’s end product. In the panel manufacturing context, an OEM may supply panels for furniture manufacturers. Understanding OEM relationships can help buyers identify reliable suppliers and ensure product quality.
2. MOQ (Minimum Order Quantity): How Does It Affect Purchases?
MOQ is the smallest quantity of a product that a supplier is willing to sell. This term is critical for buyers to understand, as it can affect inventory costs and cash flow. For international buyers, negotiating MOQs can lead to cost savings, especially when considering bulk purchases.
3. RFQ (Request for Quotation): Why Is It Important?
An RFQ is a document sent to suppliers requesting a quote for specific products or services. It outlines the buyer’s requirements, including quantities, specifications, and delivery timelines. Using RFQs effectively allows buyers to compare offers and ensure they receive competitive pricing.
4. Incoterms: What Should Buyers Know?
Incoterms (International Commercial Terms) are internationally recognized rules that define the responsibilities of buyers and sellers in international transactions. Familiarity with these terms can help buyers understand shipping costs, risk management, and delivery timelines, which is particularly important for international transactions.
5. Lead Time: Why Is It Critical for Planning?
Lead time refers to the total time taken from placing an order to receiving it. Understanding lead times is crucial for supply chain management, as it affects project timelines and inventory management. Buyers should factor in lead times when planning their procurement strategies to avoid delays in production.
By grasping these essential technical properties and trade terminology, B2B buyers can make informed decisions that enhance their purchasing strategies and optimize supply chain efficiency.
Navigating Market Dynamics and Sourcing Trends in the panel manufacturer Sector
What Are the Current Market Dynamics and Key Trends in the Panel Manufacturing Sector?
The global panel manufacturing sector is experiencing significant transformation driven by technological advancements and shifting market demands. Key trends include the rise of smart panels, which integrate IoT technology for enhanced functionality, appealing to B2B buyers seeking innovative solutions. Additionally, manufacturers are increasingly adopting automation and AI in production processes, improving efficiency and reducing costs. This trend is particularly beneficial for international buyers from regions like Africa, South America, the Middle East, and Europe, where operational cost management is crucial.
Emerging sourcing trends include a shift towards localized supply chains, spurred by geopolitical factors and the need for resilience against disruptions. Buyers are looking for manufacturers that can provide shorter lead times and adaptability in production. Furthermore, the emphasis on digital platforms for procurement and supplier management is growing, enabling buyers to streamline processes and enhance transparency. For instance, platforms that facilitate real-time tracking of orders and inventory can significantly improve operational efficiency for B2B buyers.
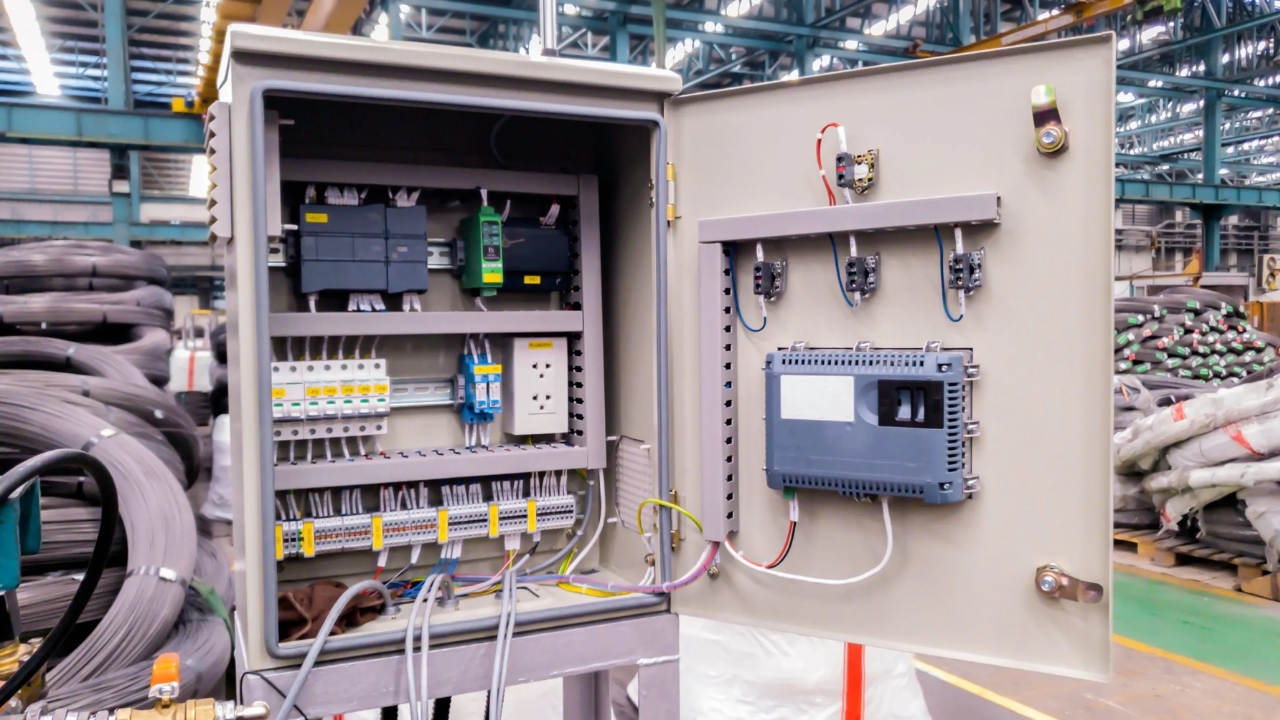
A stock image related to panel manufacturer.
How Does Sustainability Impact Sourcing Decisions in Panel Manufacturing?
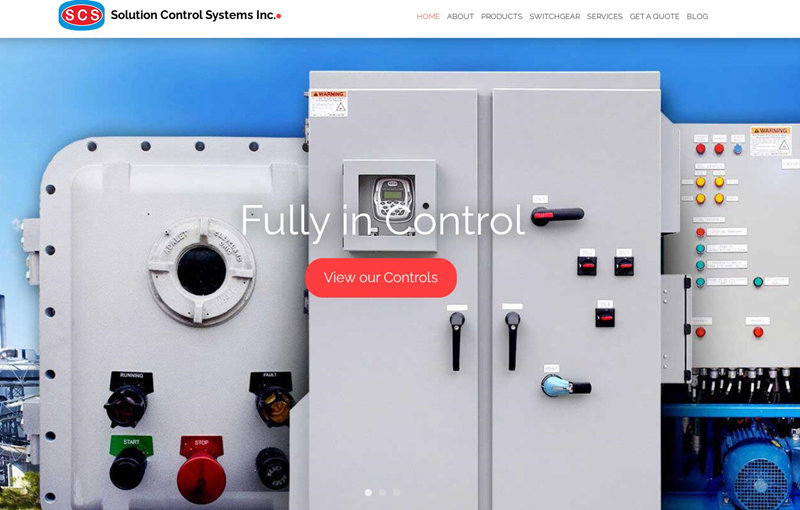
A stock image related to panel manufacturer.
Sustainability is becoming a central theme in the panel manufacturing sector, influencing sourcing decisions among international B2B buyers. The environmental impact of manufacturing processes has led to a heightened awareness of the need for ethical sourcing and sustainable practices. Buyers are increasingly prioritizing manufacturers that demonstrate a commitment to reducing their carbon footprint and utilizing renewable resources.
The importance of ethical supply chains cannot be overstated. Buyers are now scrutinizing the sourcing of raw materials, favoring suppliers who adhere to ethical labor practices and environmental regulations. Green certifications, such as LEED or ISO 14001, are becoming essential for manufacturers looking to attract international buyers. These certifications not only enhance brand reputation but also align with the growing consumer demand for environmentally friendly products.
Moreover, the use of sustainable materials—such as recycled composites or sustainably sourced wood—has gained traction. B2B buyers are urged to engage with manufacturers that innovate in material science to meet sustainability goals without compromising on quality or performance.
What Is the Historical Evolution of the Panel Manufacturing Sector?
The panel manufacturing sector has evolved considerably over the past few decades. Initially dominated by traditional manufacturing methods, the industry has witnessed a shift towards advanced technologies such as CNC machining and automated assembly lines. This evolution is driven by the need for precision and scalability to meet the growing demands of various sectors, including construction, automotive, and electronics.
In the early 2000s, the introduction of composite materials revolutionized the industry, allowing for lighter and more durable panels. Today, the focus has shifted towards integrating smart technologies and sustainability into panel designs, reflecting the broader trends in global manufacturing. As international B2B buyers increasingly seek innovative and sustainable solutions, understanding this historical context is crucial for making informed sourcing decisions.
Conclusion
In summary, international B2B buyers in the panel manufacturing sector must navigate a landscape characterized by rapid technological advancements, an emphasis on sustainability, and evolving sourcing strategies. By staying informed about market dynamics, prioritizing ethical sourcing, and understanding the sector’s historical evolution, buyers can make strategic decisions that align with their operational goals and sustainability commitments.
Frequently Asked Questions (FAQs) for B2B Buyers of panel manufacturer
-
How do I choose the right panel manufacturer for my business needs?
Selecting the right panel manufacturer involves evaluating several key factors. Start by defining your specific requirements, such as the type of panels needed (e.g., solar panels, acoustic panels), expected volume, and customization options. Research potential manufacturers by reviewing their certifications, industry reputation, and customer feedback. Additionally, consider their geographical location, as this can affect shipping times and costs. Establishing clear communication and understanding their production capabilities will also ensure they align with your business needs. -
What are the minimum order quantities (MOQ) I should expect from panel manufacturers?
Minimum order quantities can vary significantly between manufacturers, often influenced by the type of panels and production capabilities. For standard products, MOQs may range from 50 to 500 units, while custom orders might require larger quantities. Before finalizing a deal, discuss MOQs with potential suppliers to determine if they fit your purchasing strategy. Negotiating smaller orders for initial trials can also help mitigate risk while assessing product quality and suitability for your market. -
What customization options are available when sourcing panels from manufacturers?
Many panel manufacturers offer customization to meet specific business requirements. Customization options may include size, color, material, and technical specifications, such as energy efficiency ratings for solar panels. It’s crucial to communicate your needs clearly and inquire about the manufacturer’s ability to accommodate these requests. Additionally, ask about the lead time for customized products and any associated costs, as these factors can impact your project timeline and budget. -
What payment terms are typically offered by panel manufacturers?
Payment terms can vary widely among panel manufacturers, typically ranging from upfront payments to net 30 or net 60 days after delivery. Some suppliers may also accept letters of credit or escrow services for larger orders, providing security for both parties. Before entering into a contract, clarify payment terms and negotiate them to suit your cash flow needs. Ensure that you understand any penalties for late payments or discounts for early settlements. -
How can I ensure quality assurance from my panel manufacturer?
Quality assurance is critical when sourcing panels. Start by verifying the manufacturer’s certifications, such as ISO 9001 or industry-specific standards, which indicate adherence to quality management systems. Request samples for testing before placing large orders and inquire about their quality control processes, including inspections and testing methods. Establishing a clear agreement on quality expectations in your contract will help mitigate risks associated with defective products. -
What logistics considerations should I keep in mind when sourcing panels internationally?
When sourcing panels from international manufacturers, logistics plays a crucial role in the supply chain. Consider factors like shipping methods, lead times, and customs clearance processes. It’s essential to understand the total landed cost, including shipping fees, tariffs, and insurance, to avoid unexpected expenses. Collaborating with experienced logistics partners can facilitate smoother operations and help navigate international shipping complexities, ensuring timely delivery to your location. -
How do I vet potential panel manufacturers before making a purchase?
Vetting potential panel manufacturers involves thorough research and due diligence. Start by checking their business credentials, such as registration, licenses, and industry certifications. Look for customer testimonials and case studies to gauge their reputation. Engaging in direct communication can also provide insights into their responsiveness and professionalism. Consider requesting site visits or third-party audits to assess their production facilities and capabilities firsthand. -
What should I know about the warranty and after-sales support from panel manufacturers?
Understanding warranty terms and after-sales support is vital when sourcing panels. Warranties can range from one to twenty years, depending on the type of panel and manufacturer. Ensure that you clearly understand what the warranty covers, including defects and performance guarantees. Inquire about the manufacturer’s after-sales support, such as technical assistance, replacement policies, and service availability. A robust support system can enhance your experience and ensure that you maximize the value of your purchase.
Important Disclaimer & Terms of Use
⚠️ Important Disclaimer
The information provided in this guide, including content regarding manufacturers, technical specifications, and market analysis, is for informational and educational purposes only. It does not constitute professional procurement advice, financial advice, or legal advice.
While we have made every effort to ensure the accuracy and timeliness of the information, we are not responsible for any errors, omissions, or outdated information. Market conditions, company details, and technical standards are subject to change.
B2B buyers must conduct their own independent and thorough due diligence before making any purchasing decisions. This includes contacting suppliers directly, verifying certifications, requesting samples, and seeking professional consultation. The risk of relying on any information in this guide is borne solely by the reader.
Strategic Sourcing Conclusion and Outlook for panel manufacturer
In conclusion, strategic sourcing in the panel manufacturing sector is essential for international B2B buyers seeking to optimize their procurement processes. By focusing on supplier diversification, quality assurance, and cost-efficiency, businesses can enhance their competitive edge in today’s global marketplace. This approach not only ensures access to superior products but also fosters long-term partnerships with reliable manufacturers.
How can international buyers enhance their strategic sourcing practices? By leveraging data analytics and market insights, companies from Africa, South America, the Middle East, and Europe can make informed sourcing decisions that align with their specific needs. Furthermore, engaging with suppliers who prioritize sustainability and innovation will be crucial as industries evolve.
As we look toward the future, the demand for high-quality panel solutions will only grow. Buyers are encouraged to proactively seek out partnerships that align with their strategic goals and embrace the opportunities presented by emerging technologies. The time to invest in strategic sourcing is now—empower your business by choosing the right panel manufacturers that meet your evolving needs and drive your success in the global market.