Discover Top Benefits of Choosing a Silicone Manufacturer (2025)
Introduction: Navigating the Global Market for silicone manufacturer
Navigating the complexities of sourcing silicone manufacturers can be a daunting task for international B2B buyers, especially those operating in diverse markets such as Africa, South America, the Middle East, and Europe. The challenge often lies in identifying reliable suppliers that not only meet quality standards but also align with specific application needs, whether in automotive, healthcare, electronics, or consumer goods. This guide serves as a comprehensive resource to streamline the sourcing process for silicone products by providing insights into various types of silicone, their applications, and essential criteria for supplier vetting.
In this guide, we delve into the multifaceted world of silicone manufacturing, covering critical aspects such as material properties, production techniques, and the diverse applications of silicone products. We also offer actionable strategies for evaluating suppliers, understanding cost structures, and negotiating terms that benefit your business. By addressing these key areas, this guide empowers B2B buyers to make informed purchasing decisions, reducing the risks associated with supplier selection and ensuring high-quality outcomes for their projects.
Whether you are a procurement manager in Turkey looking for innovative silicone solutions or a buyer in South Africa seeking sustainable sourcing options, this guide is tailored to enhance your understanding and facilitate successful partnerships in the global silicone market.
Understanding silicone manufacturer Types and Variations
Type Name | Key Distinguishing Features | Primary B2B Applications | Brief Pros & Cons for Buyers |
---|---|---|---|
Liquid Silicone Rubber | High flexibility, excellent thermal stability, and low viscosity | Automotive, medical devices, electronics | Pros: Easy to mold, high precision; Cons: Longer curing time compared to solid silicone. |
Solid Silicone Rubber | Stiffer, excellent tensile strength, and heat resistance | Seals, gaskets, and industrial components | Pros: Durable, good for heavy-duty applications; Cons: Less flexible than liquid silicone. |
Silicone Foam | Lightweight, cushioning properties, and excellent insulation | Packaging, automotive interiors, and construction | Pros: Great thermal and acoustic insulation; Cons: May compress over time. |
Silicone Gel | Soft, pliable, and shock-absorbing properties | Medical implants, consumer electronics | Pros: Superior cushioning and comfort; Cons: Can be more expensive than other types. |
High-Temperature Silicone | Exceptional heat resistance and stability at elevated temperatures | Aerospace, automotive, and industrial applications | Pros: Maintains integrity under extreme conditions; Cons: Limited flexibility in some formulations. |
What are the Characteristics of Liquid Silicone Rubber?
Liquid Silicone Rubber (LSR) is known for its high flexibility and excellent thermal stability, making it ideal for applications that require intricate designs and high precision. Its low viscosity allows for easy molding and a smooth finish. In B2B contexts, LSR is commonly used in the automotive sector for seals and gaskets, in medical devices for safety and performance, and in electronics for insulation. Buyers should consider the curing time, as it can be longer than solid silicone, which may affect production timelines.
How Does Solid Silicone Rubber Compare to Other Types?
Solid Silicone Rubber is characterized by its stiffness and outstanding tensile strength, making it suitable for heavy-duty applications. It excels in environments that require durability, such as seals and gaskets used in industrial components. While it provides excellent resistance to heat and chemicals, it is less flexible than liquid silicone, which may limit its application in highly dynamic environments. B2B buyers should weigh the benefits of its durability against the need for flexibility in their specific applications.
What are the Advantages of Silicone Foam?
Silicone Foam is lightweight and provides excellent cushioning and insulation properties, making it a preferred choice for packaging and automotive interiors. It is particularly effective in thermal and acoustic insulation applications, contributing to energy efficiency and comfort in vehicles and buildings. However, buyers should be aware that silicone foam may compress over time, which could affect its long-term performance. Evaluating the application environment is crucial for ensuring suitability.
Why Choose Silicone Gel for Medical and Consumer Products?
Silicone Gel is renowned for its soft, pliable nature and shock-absorbing capabilities, making it ideal for applications in medical implants and consumer electronics. Its superior cushioning properties enhance comfort and safety, especially in products that come into direct contact with the skin. However, the cost can be a consideration, as silicone gel tends to be more expensive than other silicone types. B2B buyers in medical and consumer sectors should assess the balance between cost and performance when selecting silicone gel.
How Does High-Temperature Silicone Perform in Extreme Conditions?
High-Temperature Silicone is designed to withstand extreme heat and maintain stability in elevated temperatures, making it essential for aerospace and automotive applications. Its integrity under harsh conditions is a significant advantage, but some formulations may lack flexibility, which can be a drawback in certain applications. For buyers in industries that operate under high thermal stress, understanding the specific performance characteristics of high-temperature silicone is vital for ensuring product reliability and longevity.
Related Video: What Is Silicone And Its Uses?
Key Industrial Applications of silicone manufacturer
Industry/Sector | Specific Application of silicone manufacturer | Value/Benefit for the Business | Key Sourcing Considerations for this Application |
---|---|---|---|
Automotive | Engine gaskets and seals | Enhanced durability and heat resistance | Compliance with automotive standards and testing |
Electronics | Encapsulation of electronic components | Protection against moisture and dust | Customization options for different component sizes |
Healthcare | Medical device manufacturing | Biocompatibility and sterilization | Regulatory compliance and certification processes |
Construction & Building | Sealants and adhesives for construction | Weatherproofing and structural integrity | Longevity and performance in diverse climates |
Consumer Goods | Silicone bakeware and kitchen tools | Non-stick properties and heat resistance | Food-grade certifications and safety standards |
How is Silicone Used in the Automotive Industry?
In the automotive sector, silicone manufacturers provide critical components such as engine gaskets and seals. These silicone products are engineered to withstand extreme temperatures and pressures, significantly enhancing the longevity and performance of engines. For international B2B buyers, especially in regions like South Africa and Turkey, sourcing high-quality silicone materials that comply with automotive industry standards is essential. Buyers should prioritize manufacturers who can demonstrate rigorous testing and certification processes to ensure product reliability.
What Role Does Silicone Play in Electronics?
Silicone is extensively used in the electronics industry for encapsulating components, providing essential protection against moisture, dust, and thermal fluctuations. This application is vital for ensuring the longevity and functionality of electronic devices, particularly in harsh environments. B2B buyers from South America and the Middle East should consider manufacturers who offer tailored solutions, including custom sizes and formulations to meet specific component requirements. Reliability and performance in diverse operating conditions are key factors in sourcing decisions.
Why is Silicone Important in Healthcare?
In healthcare, silicone is crucial for the manufacturing of medical devices due to its biocompatibility and ease of sterilization. Silicone manufacturers supply materials that are safe for use in various medical applications, from implants to surgical instruments. For international buyers, particularly those in Europe, ensuring compliance with stringent regulatory standards is vital when sourcing silicone products. Buyers should seek manufacturers with proven track records in quality assurance and regulatory certifications to mitigate risks associated with medical device production.
How is Silicone Utilized in Construction?
Silicone serves as an essential component in construction, particularly in the form of sealants and adhesives. These products provide weatherproofing, ensuring structural integrity and energy efficiency in buildings. For B2B buyers in regions with diverse climates, such as Africa and the Middle East, sourcing high-performance silicone sealants that can withstand extreme weather conditions is crucial. Buyers should evaluate manufacturers based on the longevity of their products and their ability to meet local building codes and standards.
What are the Benefits of Silicone in Consumer Goods?
Silicone is increasingly popular in consumer goods, especially for kitchenware like bakeware and cooking tools. Its non-stick properties and heat resistance make it an ideal material for these applications. For international buyers, particularly in Europe, it is important to source silicone products that are food-grade certified and meet safety standards. Ensuring that manufacturers provide detailed information about their materials and compliance with health regulations is essential for maintaining consumer trust and product quality.
3 Common User Pain Points for ‘silicone manufacturer’ & Their Solutions
Scenario 1: Difficulty in Finding Reliable Silicone Suppliers
The Problem: B2B buyers often struggle to find reliable silicone manufacturers who can consistently meet their quality and delivery standards. This challenge is particularly pronounced for buyers in regions like Africa and South America, where local options may be limited. Factors such as language barriers, differing standards, and a lack of visibility into the supplier’s production capabilities can complicate the sourcing process. Buyers may also face difficulties in verifying the credibility and reputation of potential suppliers, leading to potential disruptions in their supply chain.
The Solution: To overcome this challenge, B2B buyers should leverage online platforms and industry networks that specialize in connecting manufacturers with buyers. Utilizing platforms like Alibaba or ThomasNet can provide access to a wider range of suppliers while offering reviews and ratings from previous clients. Buyers should conduct thorough due diligence by requesting samples and certifications that demonstrate compliance with international quality standards, such as ISO 9001. Engaging in direct communication with suppliers to discuss specific needs and expectations can also help establish a more reliable partnership. Additionally, attending trade shows or industry conferences can provide opportunities to meet suppliers in person and assess their capabilities firsthand.
Scenario 2: Inconsistent Product Quality Across Batches
The Problem: Another common pain point for B2B buyers is experiencing inconsistent product quality across different batches of silicone materials. This inconsistency can lead to production delays, increased costs, and compromised product integrity, particularly for industries like automotive or medical devices, where precision is critical. Buyers may find themselves in a situation where the first order meets their expectations, but subsequent orders do not, leading to frustration and financial losses.
The Solution: To mitigate this issue, buyers should establish clear specifications and quality control standards upfront. This includes detailed material data sheets and testing requirements that the manufacturer must follow. Implementing a robust quality assurance process is essential; buyers should consider conducting regular audits of the manufacturer’s production processes and quality control measures. Additionally, building a long-term relationship with a single, trusted supplier can lead to improved consistency, as manufacturers become more familiar with the buyer’s specific requirements over time. Utilizing third-party quality inspection services before shipment can also help ensure that the products meet the agreed-upon standards.
Scenario 3: Navigating Regulatory Compliance for Silicone Products
The Problem: B2B buyers often face challenges in navigating the regulatory landscape associated with silicone products, particularly in industries like food packaging, healthcare, and electronics. Each region has its own set of regulations, and non-compliance can result in significant legal repercussions, product recalls, and damage to brand reputation. Buyers may find it difficult to determine which certifications and compliance standards are necessary for their specific applications, especially when sourcing from international manufacturers.
The Solution: To effectively navigate these regulatory requirements, buyers should prioritize working with silicone manufacturers that are knowledgeable about the relevant regulations in their target markets. This includes ensuring that the manufacturer can provide necessary documentation, such as FDA compliance for food-grade silicones or biocompatibility certifications for medical applications. Buyers should also invest time in understanding the specific regulations that apply to their industry by consulting with legal experts or industry associations. Establishing a collaborative relationship with the supplier to stay updated on any changes in regulations can also be beneficial. Finally, considering manufacturers that are certified by recognized bodies can provide an additional layer of assurance regarding compliance and quality.
Strategic Material Selection Guide for silicone manufacturer
When selecting materials for silicone manufacturing, it is crucial for international B2B buyers to understand the properties, advantages, disadvantages, and application impacts of various materials. This guide focuses on four common materials used in silicone manufacturing: silicone rubber, fluorosilicone, silicone gel, and silicone foam. Each material has unique characteristics that can significantly influence product performance and end-user satisfaction.
What Are the Key Properties of Silicone Rubber for Manufacturers?
Silicone rubber is renowned for its excellent temperature stability, typically ranging from -50°C to 230°C. It also boasts remarkable flexibility and resilience, making it suitable for various applications, including seals, gaskets, and medical devices. Its resistance to UV light and ozone further enhances its durability in outdoor applications.
Pros and Cons: The primary advantage of silicone rubber is its versatility and durability, which allows it to withstand harsh environmental conditions. However, it can be more expensive than traditional rubber materials, and its manufacturing complexity may require specialized equipment.
Impact on Application: Silicone rubber is compatible with a wide range of media, including water, oils, and some chemicals. This makes it ideal for automotive and food processing industries, where hygiene and safety are paramount.
Considerations for International Buyers: Buyers from regions like Africa and the Middle East should be aware of compliance with local standards such as ASTM and DIN. Additionally, understanding the specific requirements for temperature and chemical exposure in their industries is vital.
How Does Fluorosilicone Compare in Terms of Performance?
Fluorosilicone is a specialized type of silicone that incorporates fluorine, enhancing its chemical resistance, particularly to fuels and solvents. It can typically withstand temperatures from -60°C to 200°C, making it suitable for aerospace and automotive applications.
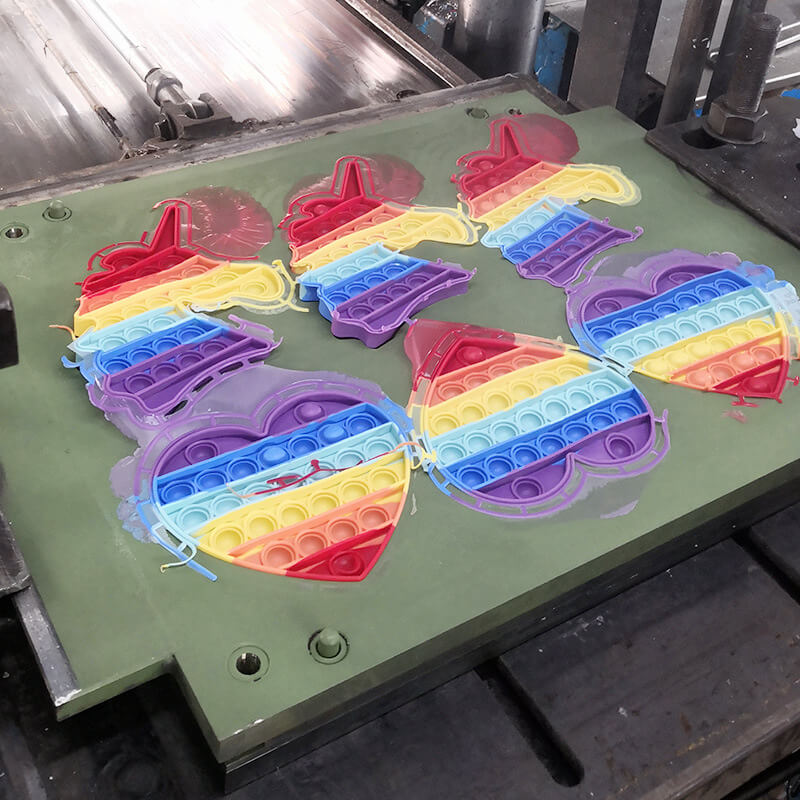
A stock image related to silicone manufacturer.
Pros and Cons: The key advantage of fluorosilicone is its superior chemical resistance, which is essential for applications involving aggressive substances. However, it is generally more costly than standard silicone rubber and may require more complex processing techniques.
Impact on Application: Fluorosilicone’s compatibility with harsh chemicals makes it an excellent choice for fuel systems and oil seals, where traditional silicone may fail.
Considerations for International Buyers: Buyers in South America and Europe should ensure that fluorosilicone products meet industry-specific regulations, particularly in the automotive sector, where compliance with standards like JIS is crucial.
What Are the Unique Benefits of Silicone Gel?
Silicone gel is a softer, more flexible material that provides cushioning and shock absorption. It is often used in applications such as medical devices, personal care products, and electronics.
Pros and Cons: The primary advantage of silicone gel is its excellent cushioning properties, making it ideal for sensitive applications. However, it may not offer the same level of durability as solid silicone materials and can be more prone to degradation over time.
Impact on Application: Silicone gel is particularly effective in applications requiring vibration dampening or impact resistance, such as in consumer electronics and medical implants.
Considerations for International Buyers: Buyers from Turkey and South Africa should consider the specific regulatory requirements for medical-grade silicone gel, ensuring compliance with local health and safety standards.
How Does Silicone Foam Enhance Product Performance?
Silicone foam is a lightweight, flexible material that provides excellent thermal insulation and sound dampening properties. It is commonly used in automotive, construction, and HVAC applications.
Pros and Cons: The key advantage of silicone foam is its lightweight nature combined with effective insulation properties. However, it may not be as durable as solid silicone and can be more susceptible to moisture absorption.
Impact on Application: Silicone foam’s insulation capabilities make it ideal for applications requiring temperature control, such as in HVAC systems.
Considerations for International Buyers: Buyers in regions with extreme weather conditions should consider the thermal performance ratings of silicone foam to ensure it meets their specific application needs.
Summary Table of Material Selection for Silicone Manufacturing
Material | Typical Use Case for Silicone Manufacturer | Key Advantage | Key Disadvantage/Limitation | Relative Cost (Low/Med/High) |
---|---|---|---|---|
Silicone Rubber | Seals and gaskets in automotive | Excellent temperature stability | Higher cost than traditional rubber | Medium |
Fluorosilicone | Fuel systems and oil seals | Superior chemical resistance | More expensive and complex to process | High |
Silicone Gel | Medical devices and electronics | Excellent cushioning properties | Less durable than solid silicone | Medium |
Silicone Foam | HVAC and automotive insulation | Lightweight with good insulation | Susceptible to moisture absorption | Medium |
This guide provides a comprehensive overview of material selection for silicone manufacturing, empowering international B2B buyers to make informed decisions based on their specific needs and regional compliance requirements.
In-depth Look: Manufacturing Processes and Quality Assurance for silicone manufacturer
What Are the Key Stages in the Manufacturing Process of Silicone Products?
The manufacturing process for silicone products involves several critical stages, each designed to ensure the highest quality and performance of the final product. Here’s a breakdown of the main stages involved in silicone manufacturing:
-
Material Preparation: This initial phase involves sourcing high-quality silicone raw materials. Depending on the application, silicone may come in various forms, including liquid silicone rubber (LSR) or high-consistency rubber (HCR). The materials are typically mixed with additives to enhance properties such as durability, temperature resistance, and color.
-
Forming: In this stage, the prepared silicone is shaped into desired forms using various techniques. Common methods include:
– Injection Molding: Ideal for high-volume production, this technique involves injecting silicone into a mold where it cures into a solid form.
– Compression Molding: Suitable for larger parts, silicone is placed into an open mold and compressed to shape it.
– Extrusion: This method is used for continuous shapes like tubing, where silicone is forced through a die. -
Assembly: If the silicone product consists of multiple components, assembly is required. This may involve bonding different silicone parts together or integrating silicone with other materials (like metal or plastic) to create a composite product.
-
Finishing: The final stage includes surface treatments such as polishing, coating, or printing. These processes enhance the aesthetic appeal and functional properties of the silicone products, ensuring they meet the specific requirements of the buyers.
How Do Quality Assurance Practices Ensure the Integrity of Silicone Manufacturing?
Quality assurance (QA) is paramount in silicone manufacturing, especially for B2B buyers who demand reliability and compliance with international standards. Here are the key components of QA in silicone manufacturing:
-
International Standards Compliance: Manufacturers often adhere to several international quality standards, including:
– ISO 9001: This standard focuses on quality management systems and ensures consistent product quality and customer satisfaction.
– CE Marking: Particularly important for products sold within the European Economic Area, CE marking indicates conformity with health, safety, and environmental protection standards.
– API Standards: For silicone used in medical or pharmaceutical applications, compliance with American Petroleum Institute (API) standards is crucial. -
Quality Control Checkpoints: Effective quality control (QC) involves several checkpoints throughout the manufacturing process:
– Incoming Quality Control (IQC): This involves inspecting raw materials upon arrival to ensure they meet specifications.
– In-Process Quality Control (IPQC): Continuous monitoring during production to catch defects early, ensuring that products are manufactured within specified parameters.
– Final Quality Control (FQC): Comprehensive testing of the finished products before shipment to verify they meet the required standards. -
Common Testing Methods: Various testing methods are employed to ensure product quality, including:
– Mechanical Testing: Evaluates the physical properties of silicone, such as tensile strength and elasticity.
– Thermal Testing: Assesses performance under extreme temperatures.
– Chemical Resistance Testing: Determines how well silicone withstands exposure to various chemicals.
How Can B2B Buyers Verify the Quality Control Processes of Silicone Manufacturers?
International B2B buyers must ensure that their suppliers maintain rigorous quality control processes. Here are some actionable steps to verify QC practices:
-
Supplier Audits: Conducting on-site audits can provide insights into the manufacturer’s QC processes. During these audits, buyers can assess compliance with international standards and evaluate the manufacturing environment.
-
Requesting Quality Reports: Buyers should request documentation of QC processes, including IQC, IPQC, and FQC reports. These documents should detail the tests performed, results, and any corrective actions taken for non-conformities.
-
Third-Party Inspections: Engaging a third-party inspection service can offer an unbiased assessment of the manufacturer’s compliance with quality standards. These inspections can be particularly useful for buyers in regions like Africa and South America, where supply chain complexities may arise.
-
Certifications and Accreditations: Verify the manufacturer’s certifications to ensure they comply with relevant industry standards. Look for certifications such as ISO 9001 or specific industry certifications relevant to your sector (e.g., medical device certifications).
What Quality Control Nuances Should International B2B Buyers Be Aware Of?
When dealing with silicone manufacturers across different regions, international B2B buyers should consider several nuances:
-
Regulatory Differences: Quality standards and regulations can vary significantly between regions. Buyers must familiarize themselves with local regulations in Africa, South America, the Middle East, and Europe to ensure compliance.
-
Cultural and Operational Practices: Understanding the cultural context and operational practices in different regions can impact quality expectations. For example, manufacturers in Turkey may have different practices than those in South Africa, affecting timelines and quality assurance.
-
Communication Barriers: Language differences can lead to misunderstandings regarding quality expectations. Establishing clear communication channels and using standardized documentation can mitigate these risks.
-
Logistical Challenges: Ensure that the manufacturer has robust logistics and supply chain management practices to prevent delays or quality issues during transportation.
By understanding the manufacturing processes and quality assurance practices, international B2B buyers can make informed decisions when selecting silicone manufacturers. This knowledge not only helps in ensuring product quality but also fosters long-term relationships with reliable suppliers.
Practical Sourcing Guide: A Step-by-Step Checklist for ‘silicone manufacturer’
Introduction
Sourcing silicone manufacturers can be a complex process, particularly for international B2B buyers. This step-by-step checklist is designed to guide you through the critical stages of the procurement process, ensuring you make informed decisions that align with your business needs. Whether you’re based in Africa, South America, the Middle East, or Europe, these actionable insights will help streamline your sourcing efforts.
Step 1: Define Your Technical Specifications
Before reaching out to potential suppliers, it’s essential to clearly define your technical specifications for the silicone products you need. This includes understanding the required material properties, dimensions, and any industry-specific standards that must be met.
- What to consider:
- Application of the silicone (e.g., automotive, medical, consumer goods).
- Required certifications (e.g., FDA, ISO).
Step 2: Research Potential Suppliers
Conduct thorough research to identify potential silicone manufacturers that align with your specifications. Look for suppliers with a proven track record in your industry and those who can demonstrate a commitment to quality and innovation.
- Where to find suppliers:
- Industry directories and trade shows.
- Online platforms that specialize in B2B sourcing.
Step 3: Evaluate Supplier Capabilities
Before committing, evaluate the capabilities of each supplier. This involves assessing their production capacity, technology used, and ability to meet your volume requirements.
- Key questions to ask:
- What is their minimum order quantity (MOQ)?
- Can they handle custom formulations or modifications?
Step 4: ✅ Verify Supplier Certifications
It’s crucial to verify that potential suppliers hold the necessary certifications relevant to your industry. Certifications indicate compliance with international standards and can reflect the quality of their products.
- What to check:
- ISO certifications (e.g., ISO 9001 for quality management).
- Product-specific certifications (e.g., RoHS, REACH compliance).
Step 5: Request Samples for Testing
Once you have shortlisted potential suppliers, request samples of the silicone materials. Testing samples allows you to evaluate the quality, performance, and suitability of the products for your specific applications.
- What to test for:
- Durability and elasticity.
- Compatibility with other materials used in your products.
Step 6: Assess Pricing and Payment Terms
Understanding the pricing structure and payment terms is vital for budgeting and financial planning. Compare quotes from different suppliers, considering factors such as shipping costs, lead times, and payment flexibility.
- Considerations include:
- Are there discounts for bulk orders?
- What are the payment options available (e.g., upfront, net 30)?
Step 7: Negotiate Terms and Finalize Agreements
Once you’ve selected a supplier, negotiate the terms of your contract. This should include pricing, delivery timelines, quality assurance processes, and potential penalties for non-compliance.
- Important aspects to include:
- Clauses for quality inspections and returns.
- Confidentiality agreements if applicable.
By following this checklist, you can ensure a more structured and effective sourcing process for silicone manufacturers, helping you secure the best partnership for your business needs.
Comprehensive Cost and Pricing Analysis for silicone manufacturer Sourcing
What Are the Key Cost Components in Silicone Manufacturing?
When sourcing silicone products, understanding the cost structure is essential for making informed purchasing decisions. The primary cost components include:
-
Materials: Silicone itself is derived from silica and other chemical compounds. Prices can vary significantly based on market conditions, purity, and the source of the raw materials. It is advisable to establish relationships with multiple suppliers to mitigate risks associated with price fluctuations.
-
Labor: Labor costs encompass wages for skilled workers involved in the manufacturing process, including production, quality control, and management. Regions with lower labor costs, such as parts of Africa and South America, may offer competitive pricing, but potential buyers should also consider the skill level and training of the workforce.
-
Manufacturing Overhead: This includes expenses related to factory operations, utilities, and equipment maintenance. Efficient production processes can help reduce overhead costs, which can influence the final price of silicone products.
-
Tooling: The cost of molds and tooling can be significant, especially for custom silicone products. Buyers should be aware that initial tooling costs can be amortized over larger production runs, making it crucial to assess the order volume and long-term needs.
-
Quality Control (QC): Implementing stringent QC measures ensures that products meet industry standards. While this adds to the cost, it is essential for minimizing defects and maintaining customer satisfaction.
-
Logistics: Shipping and handling costs vary based on the origin of the materials and the destination. Understanding Incoterms (International Commercial Terms) is crucial, as they define the responsibilities of buyers and sellers in the transportation process.
-
Margin: Manufacturers typically include a profit margin on top of their costs. This margin can vary based on the competitive landscape and the perceived value of the product.
How Do Price Influencers Affect Silicone Product Pricing?
Several factors can influence the pricing of silicone products in the B2B market:
-
Volume/MOQ (Minimum Order Quantity): Higher order volumes often lead to lower per-unit costs due to economies of scale. Buyers should negotiate for better pricing based on their projected needs.
-
Specifications and Customization: Customized products tailored to specific requirements can incur additional costs. Buyers should clarify their specifications early in the negotiation process to avoid unexpected expenses.
-
Materials: The choice of materials can significantly impact pricing. High-performance or specialty silicones may command higher prices, while standard grades may be more affordable.
-
Quality and Certifications: Products with certifications (e.g., ISO, FDA) may be priced higher due to the added assurance of quality. Buyers should consider their end-use applications when evaluating the necessity of certifications.
-
Supplier Factors: The supplier’s reputation, reliability, and production capabilities can influence pricing. A well-established supplier with a track record of quality may justify higher prices.
-
Incoterms: Understanding the implications of different Incoterms can affect the overall cost of sourcing. Terms like FOB (Free On Board) or CIF (Cost, Insurance, and Freight) will dictate the allocation of shipping costs and risks.
What Are Effective Buyer Tips for Cost-Efficiency in Silicone Sourcing?
To ensure cost-effective sourcing of silicone products, international buyers should consider the following tips:
-
Negotiate Effectively: Building a strong rapport with suppliers can lead to better pricing and terms. Clearly communicate your needs and explore options for long-term partnerships.
-
Assess Total Cost of Ownership (TCO): Beyond the purchase price, consider additional costs such as shipping, import duties, and potential tariffs. A lower initial cost might not always translate to savings if other expenses are high.
-
Stay Informed About Market Trends: Keep abreast of global market trends that could affect silicone prices, such as changes in raw material availability or regulatory shifts.
-
Leverage Regional Advantages: Buyers from regions like Turkey or South Africa should explore local suppliers who may offer competitive pricing due to lower operational costs.
-
Request Samples: Before committing to large orders, request samples to evaluate quality and ensure that the product meets your specifications.
Disclaimer on Indicative Prices
While this analysis provides a framework for understanding costs and pricing in silicone manufacturing, prices can fluctuate based on market conditions, material availability, and supplier negotiations. Always seek updated quotes and conduct thorough due diligence when sourcing silicone products.
Alternatives Analysis: Comparing silicone manufacturer With Other Solutions
When evaluating the best materials and solutions for industrial applications, it is crucial to consider alternatives to silicone. Silicone manufacturers offer unique properties, but other solutions may also meet specific needs effectively. Below, we compare silicone with two viable alternatives: polyurethane and thermoplastic elastomers (TPE). This comparison will help international B2B buyers, especially from Africa, South America, the Middle East, and Europe, make informed decisions.
Comparison Table of Silicone Manufacturer vs. Alternatives
Comparison Aspect | Silicone Manufacturer | Polyurethane | Thermoplastic Elastomers (TPE) |
---|---|---|---|
Performance | Excellent thermal stability, flexibility, and chemical resistance | High abrasion resistance and durability | Good elasticity and flexibility, moderate chemical resistance |
Cost | Generally higher initial cost | Moderate cost, varies by formulation | Lower cost, depending on grade |
Ease of Implementation | Requires specialized processes | More versatile in processing methods | Easy to mold and process |
Maintenance | Low maintenance but can degrade under UV | Moderate maintenance; can yellow over time | Low maintenance, generally stable |
Best Use Case | High-performance applications (e.g., medical devices) | Industrial applications requiring durability (e.g., wheels, seals) | Consumer products and soft-touch applications (e.g., grips, toys) |
What Are the Pros and Cons of Polyurethane as an Alternative to Silicone?
Polyurethane is a versatile polymer that offers excellent abrasion resistance and durability, making it suitable for various industrial applications. Its moderate cost and adaptability in processing methods allow for easier integration into existing production lines. However, polyurethane can be more susceptible to degradation from UV exposure, which may require additional maintenance or protective coatings in outdoor applications.
How Does Thermoplastic Elastomer (TPE) Compare to Silicone?
Thermoplastic elastomers (TPE) are gaining popularity due to their good elasticity and flexibility, making them ideal for consumer products and applications where a soft-touch feel is essential. TPEs are generally lower in cost than silicone and are easy to mold, which can lead to reduced production time. However, their chemical resistance may not match that of silicone, making them less suitable for demanding environments or applications involving harsh chemicals.
How Can B2B Buyers Choose the Right Solution for Their Needs?
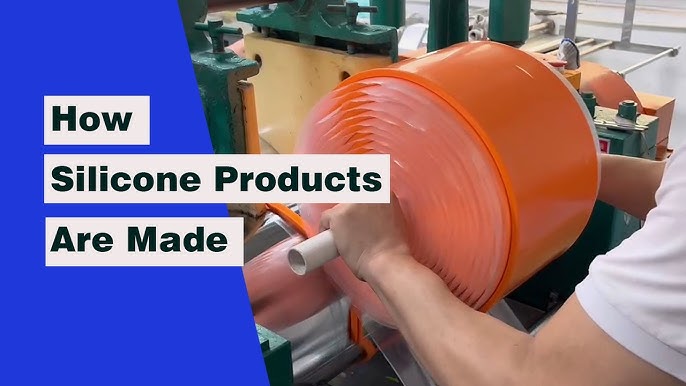
A stock image related to silicone manufacturer.
Selecting the right material depends on specific application requirements, including performance needs, budget constraints, and production capabilities. Buyers should assess the environmental conditions the product will face, such as exposure to chemicals or UV light, and consider the long-term maintenance implications. Engaging with manufacturers to understand the properties and processing requirements of each alternative will provide valuable insights that align with their operational goals. Ultimately, the right choice will balance cost-effectiveness with the necessary performance attributes to ensure product longevity and reliability.
Essential Technical Properties and Trade Terminology for silicone manufacturer
What Are the Key Technical Properties for Silicone Manufacturing?
Understanding the essential technical properties of silicone is crucial for international B2B buyers, especially when sourcing materials for applications in diverse industries. Here are some of the critical specifications to consider:
1. Material Grade
Material grade refers to the specific classification of silicone based on its chemical composition and performance characteristics. Grades can range from general-purpose silicone to specialized formulations designed for high-temperature or medical applications. For buyers, selecting the appropriate material grade ensures that the silicone meets the performance requirements of their specific application, whether it be in automotive, electronics, or healthcare.
2. Hardness (Shore A)
Hardness, measured in Shore A durometer, indicates the stiffness of silicone rubber. A lower Shore A value corresponds to a softer material, while a higher value indicates increased rigidity. Understanding the hardness is vital for manufacturers to ensure compatibility with other materials and the desired flexibility or durability in the final product. For instance, softer silicones may be preferred for applications requiring cushioning, while harder grades might be necessary for structural components.
3. Temperature Resistance
Silicone exhibits excellent temperature stability, typically ranging from -60°C to +250°C (-76°F to +482°F) depending on the formulation. This property is particularly important for applications exposed to extreme heat or cold. Buyers should assess their specific operational temperature ranges to select silicone that can withstand environmental conditions without degrading.
4. Chemical Resistance
The chemical resistance of silicone refers to its ability to withstand exposure to various substances such as oils, solvents, and acids. This property is crucial for industries like food processing, pharmaceuticals, and automotive, where materials may come into contact with harsh chemicals. Understanding chemical compatibility helps buyers avoid material failures and ensures longevity in applications.
5. Tensile Strength
Tensile strength measures the maximum amount of tensile (pulling) stress that silicone can withstand before breaking. It is an essential specification for ensuring that the silicone parts will perform adequately under mechanical stress. For B2B buyers, knowing the tensile strength helps in selecting the right silicone for applications that require durability and resistance to tearing.
What Common Trade Terms Should International B2B Buyers Know?
Navigating the silicone manufacturing industry involves familiarity with specific jargon and trade terms. Here are some key terms that buyers should understand:
1. OEM (Original Equipment Manufacturer)
OEM refers to companies that produce parts and equipment that may be marketed by another manufacturer. In the silicone industry, an OEM might source silicone components for use in their products. Understanding OEM relationships can help buyers identify reliable suppliers and ensure quality in the components they purchase.
2. MOQ (Minimum Order Quantity)
MOQ is the minimum number of units that a supplier is willing to sell. This term is particularly important for B2B buyers as it impacts inventory management and cost-effectiveness. Knowing the MOQ can help buyers negotiate better terms and plan their purchasing strategies accordingly.
3. RFQ (Request for Quotation)
An RFQ is a formal document issued by a buyer to solicit price quotes from suppliers for specific products or services. This process helps buyers compare prices and terms across different manufacturers. Crafting a detailed RFQ that includes specifications can lead to more accurate quotations and better decision-making.
4. Incoterms (International Commercial Terms)
Incoterms are standardized international trade terms that define the responsibilities of buyers and sellers regarding shipping, insurance, and tariffs. Familiarity with these terms helps buyers understand shipping costs and risks associated with international transactions, ultimately aiding in smoother logistics management.
5. Lead Time
Lead time refers to the time it takes from placing an order until it is delivered. For B2B buyers, understanding lead times is crucial for project planning and ensuring that production schedules are met. Shorter lead times can provide a competitive edge, especially in fast-paced industries.
Conclusion
By grasping these essential technical properties and industry terminology, international B2B buyers can make informed decisions when sourcing silicone materials. This knowledge not only facilitates better supplier negotiations but also enhances product quality and operational efficiency across various applications.
Navigating Market Dynamics and Sourcing Trends in the silicone manufacturer Sector
What Are the Key Market Dynamics and Trends in the Silicone Manufacturing Sector?
The silicone manufacturing sector is experiencing significant transformation driven by various global factors. The increasing demand for high-performance materials across diverse industries—including automotive, healthcare, electronics, and construction—has positioned silicone as a versatile choice. B2B buyers from regions such as Africa, South America, the Middle East, and Europe (including Turkey and South Africa) should note that innovations in silicone formulations are enhancing properties such as durability, heat resistance, and chemical stability.
Emerging technologies like 3D printing and advanced molding techniques are also influencing sourcing trends. These technologies facilitate rapid prototyping and customization, allowing companies to meet specific client needs more efficiently. Additionally, the adoption of Industry 4.0 practices, including smart manufacturing and IoT integration, is reshaping supply chain management, enhancing transparency, and improving operational efficiency.
Furthermore, geopolitical factors and trade agreements are creating shifts in sourcing strategies, compelling international buyers to diversify their supplier base. This trend is particularly relevant for buyers in regions with fluctuating economic stability, as it mitigates risks associated with reliance on single markets.
How Is Sustainability Shaping Sourcing Decisions in Silicone Manufacturing?
Sustainability has emerged as a critical factor in the sourcing strategies of B2B buyers in the silicone manufacturing sector. The environmental impact of silicone production, including energy consumption and waste generation, is prompting companies to seek eco-friendly alternatives. Buyers should prioritize suppliers that adhere to sustainable practices, such as using renewable energy sources and reducing carbon footprints in their manufacturing processes.
The importance of ethical supply chains cannot be overstated. Consumers and businesses alike are increasingly demanding transparency regarding the sourcing of materials. B2B buyers should consider suppliers with green certifications, such as ISO 14001 for environmental management or certifications for sustainable sourcing of raw materials. These certifications not only demonstrate a commitment to sustainability but also enhance brand reputation and consumer trust.
Moreover, the development of bio-based silicones—derived from renewable resources—represents a growing segment within the market. These materials offer comparable performance characteristics to traditional silicones while minimizing environmental impact. By integrating sustainable practices into their procurement strategies, B2B buyers can drive positive change within the industry while meeting regulatory requirements and consumer expectations.
What Is the Historical Context of the Silicone Manufacturing Sector?
The silicone manufacturing sector has evolved significantly since its inception in the mid-20th century. Initially used in niche applications, silicones have grown in popularity due to their unique properties, such as thermal stability and chemical resistance. Over the decades, advancements in polymer chemistry have expanded the range of silicone products available, leading to widespread adoption across various industries.
The historical shift towards automation and digitalization has further transformed the sector, enhancing production efficiency and enabling more complex applications. As a result, silicone materials are now integral to modern technological advancements, from medical devices to consumer electronics, making them a vital consideration for B2B buyers aiming to stay competitive in an increasingly dynamic marketplace.
In conclusion, understanding the market dynamics, sustainability trends, and historical evolution of the silicone manufacturing sector equips international B2B buyers with the insights necessary to make informed sourcing decisions, ultimately driving business success in a competitive landscape.
Frequently Asked Questions (FAQs) for B2B Buyers of silicone manufacturer
-
How do I choose the right silicone manufacturer for my business needs?
Selecting the right silicone manufacturer involves evaluating several factors, including their industry experience, production capabilities, and quality certifications. Start by assessing their product range to ensure they can meet your specific requirements, such as food-grade or medical-grade silicone. Additionally, request samples to evaluate product quality and ask for references from previous clients. For international buyers, consider manufacturers with experience in exporting to your region to ensure they understand local regulations and logistics. -
What are the common applications of silicone in various industries?
Silicone is versatile and used across numerous industries, including automotive, healthcare, construction, and electronics. In automotive applications, silicone seals and gaskets provide durability and resistance to extreme temperatures. In healthcare, silicone is used for medical devices and implants due to its biocompatibility. Understanding the specific applications relevant to your industry will help you identify manufacturers who specialize in those areas, ensuring you receive tailored solutions. -
What should I consider regarding Minimum Order Quantities (MOQs) when sourcing silicone products?
When sourcing silicone products, MOQs vary significantly between manufacturers. Some may have low MOQs suitable for small businesses, while others require large orders. Consider your production needs and budget when negotiating MOQs. It’s also wise to ask about flexibility in order sizes, especially if you’re testing a new product line. Understanding the implications of MOQs on your cash flow and inventory management is crucial for effective planning. -
What payment terms should I expect when dealing with silicone manufacturers?
Payment terms can vary widely among silicone manufacturers. Typically, international buyers might encounter options like 30% upfront payment and 70% upon shipment. Some manufacturers may offer payment through letters of credit, which provide security for both parties. Always discuss payment terms upfront to avoid misunderstandings later. Consider negotiating terms that align with your cash flow needs, and ensure that you have a clear invoice and payment process in place. -
How can I ensure quality assurance when sourcing silicone products?
Quality assurance (QA) is critical when sourcing silicone products. First, inquire about the manufacturer’s quality control processes, including testing for compliance with international standards such as ISO 9001. Request certifications and documentation demonstrating their commitment to quality. Additionally, consider implementing third-party inspections or audits, especially for large orders, to verify that products meet your specifications before shipment. -
What logistics considerations should I keep in mind when importing silicone products?
When importing silicone products, logistics play a vital role in ensuring timely delivery. Consider factors such as shipping methods (air vs. sea), lead times, and customs clearance processes specific to your country. Work closely with your manufacturer to understand their shipping capabilities and the associated costs. It may also be beneficial to partner with a freight forwarder who can navigate complex international logistics and ensure compliance with local regulations. -
How can I customize silicone products to meet my specific requirements?
Customization of silicone products is often available, allowing you to tailor items to your specific needs. When discussing customization, be clear about your requirements regarding size, color, and functional properties. Manufacturers may offer options such as adding specific additives for enhanced performance or designing molds for unique shapes. Ensure that you communicate your specifications clearly and request prototypes to evaluate before final production.
- What are the key factors to consider when vetting a silicone manufacturer?
When vetting a silicone manufacturer, focus on their reputation, experience, and compliance with industry standards. Investigate their production capabilities, including technology used and scalability for future growth. Check for customer reviews and case studies that reflect their reliability and product quality. Additionally, assess their communication responsiveness and willingness to engage in discussions about your specific needs, as these factors can significantly impact your overall purchasing experience.
Important Disclaimer & Terms of Use
⚠️ Important Disclaimer
The information provided in this guide, including content regarding manufacturers, technical specifications, and market analysis, is for informational and educational purposes only. It does not constitute professional procurement advice, financial advice, or legal advice.
While we have made every effort to ensure the accuracy and timeliness of the information, we are not responsible for any errors, omissions, or outdated information. Market conditions, company details, and technical standards are subject to change.
B2B buyers must conduct their own independent and thorough due diligence before making any purchasing decisions. This includes contacting suppliers directly, verifying certifications, requesting samples, and seeking professional consultation. The risk of relying on any information in this guide is borne solely by the reader.
Strategic Sourcing Conclusion and Outlook for silicone manufacturer
What Are the Key Takeaways for B2B Buyers in Strategic Sourcing of Silicone Products?
In conclusion, the strategic sourcing of silicone products presents significant opportunities for international B2B buyers, particularly those in Africa, South America, the Middle East, and Europe. By leveraging local and global suppliers, businesses can enhance their supply chain resilience and reduce costs. Understanding the unique applications of silicone in various industries—such as automotive, healthcare, and consumer goods—can lead to more informed purchasing decisions that align with specific business needs.
How Can Strategic Sourcing Benefit Your Business?
Strategic sourcing not only optimizes procurement processes but also fosters long-term partnerships with manufacturers, which can lead to innovation and improved product quality. As businesses face increasing pressure to adopt sustainable practices, sourcing silicone from environmentally responsible manufacturers can also enhance brand reputation and comply with global standards.
What Should You Consider Moving Forward?
As you navigate the complexities of sourcing silicone products, consider the importance of due diligence in supplier selection and the impact of geopolitical factors on supply chains. By staying informed about market trends and emerging technologies in silicone manufacturing, you can position your business for future growth.
We encourage you to take proactive steps in your sourcing strategy today. Explore potential partnerships, assess supplier capabilities, and embrace the strategic sourcing approach to unlock the full potential of silicone products in your operations.