Discover Top Tips to Choose a Chain Manufacturer (2025)
Introduction: Navigating the Global Market for chain manufacturer
Navigating the global market for chain manufacturers can be a daunting task for international B2B buyers, especially when aiming to source reliable and high-quality chains tailored to specific applications. With a myriad of suppliers and options available, understanding how to effectively vet manufacturers and ensure competitive pricing can feel overwhelming. This guide serves as a comprehensive resource, addressing the critical aspects of sourcing chains, including types, applications, supplier evaluation, and cost considerations.
As you explore this guide, you will gain insights into the diverse types of chains available—ranging from roller chains to specialty chains—each suited for different industrial applications. We will also delve into the nuances of supplier vetting, providing you with actionable strategies to assess quality, reliability, and compliance with international standards. Furthermore, we will cover cost factors that influence pricing, helping you make informed purchasing decisions that align with your budgetary constraints.
For B2B buyers from Africa, South America, the Middle East, and Europe—countries such as Spain and Italy—this guide empowers you to navigate the complexities of the global market with confidence. By equipping you with the knowledge to select the right chain manufacturers, we aim to enhance your sourcing experience and ultimately support your business’s operational efficiency.
Understanding chain manufacturer Types and Variations
Type Name | Key Distinguishing Features | Primary B2B Applications | Brief Pros & Cons for Buyers |
---|---|---|---|
Roller Chains | Comprised of interlocking links, high tensile strength | Manufacturing, agriculture | Pros: Durable, versatile; Cons: Requires regular lubrication, can be noisy. |
Block Chains | Short lengths of chain used for lifting and hoisting | Construction, mining | Pros: High load capacity, easy installation; Cons: Limited flexibility, heavy. |
Leaf Chains | Flat links that are lightweight and compact | Automotive, conveyor systems | Pros: Low weight, good for high-speed applications; Cons: Limited load capacity. |
Stainless Steel Chains | Corrosion-resistant, ideal for harsh environments | Food processing, pharmaceuticals | Pros: Long-lasting, hygienic; Cons: Higher cost, may require specialized fittings. |
Specialty Chains | Custom-designed chains for specific applications | Aerospace, robotics | Pros: Tailored solutions, optimized performance; Cons: Longer lead times, higher costs. |
What Are Roller Chains and Their B2B Suitability?
Roller chains are characterized by their interlocking links and are widely used due to their high tensile strength. They are suitable for various applications, including manufacturing and agriculture, where durability and versatility are paramount. When purchasing roller chains, consider the maintenance requirements such as lubrication and noise levels, as these can impact operational efficiency.
How Do Block Chains Differ from Other Types?
Block chains consist of short lengths designed for lifting and hoisting tasks, making them essential in construction and mining industries. Their high load capacity and ease of installation are significant advantages. However, buyers should be aware of their limited flexibility and the weight they add to lifting mechanisms, which could influence equipment design.
What Are the Advantages of Leaf Chains?
Leaf chains feature flat links, making them lightweight and compact, which is ideal for automotive and conveyor system applications. Their low weight allows for high-speed operations, but buyers must note their limited load capacity, which may not be suitable for heavier applications. Assessing the operational load requirements is crucial when considering leaf chains.
Why Choose Stainless Steel Chains?
Stainless steel chains are known for their corrosion resistance and are particularly suitable for harsh environments, such as food processing and pharmaceuticals. Their longevity and hygienic properties make them a preferred choice in industries where cleanliness is critical. However, the higher cost and potential need for specialized fittings should be factored into the purchasing decision.
What Are Specialty Chains and Their Unique Considerations?
Specialty chains are custom-designed for specific applications, such as aerospace and robotics. These chains offer tailored solutions and optimized performance, making them invaluable in niche markets. However, buyers should be prepared for longer lead times and potentially higher costs, which are often associated with custom manufacturing. Understanding the specific requirements of your application is essential for making an informed purchase.
Related Video: 01 What is a Supply Chain? and How can we Design them?
Key Industrial Applications of chain manufacturer
Industry/Sector | Specific Application of Chain Manufacturer | Value/Benefit for the Business | Key Sourcing Considerations for this Application |
---|---|---|---|
Manufacturing | Conveyors for assembly lines | Increases production efficiency and reduces labor costs | Durability, load capacity, and compatibility with existing systems |
Agriculture | Agricultural machinery for harvesting | Enhances productivity and reduces downtime during harvest | Corrosion resistance and adaptability to various environmental conditions |
Mining | Equipment for ore extraction | Improves safety and operational efficiency | Strength, resistance to wear, and ability to handle heavy loads |
Food Processing | Conveyors for food handling | Ensures hygiene and efficiency in food production | Compliance with health standards and easy cleaning features |
Logistics and Warehousing | Automated sorting systems | Optimizes space utilization and speeds up order fulfillment | Reliability, ease of maintenance, and availability of spare parts |
How is Chain Manufacturing Used in the Manufacturing Sector?
In the manufacturing sector, chains are integral to conveyor systems used on assembly lines. They facilitate the smooth transport of materials and components, significantly enhancing production efficiency. By minimizing manual handling, businesses can reduce labor costs and improve safety. International buyers should prioritize sourcing chains that offer durability and a high load capacity, ensuring compatibility with existing systems to avoid costly retrofits.
What Role Does Chain Manufacturing Play in Agriculture?
In agriculture, chains are vital components of machinery used for harvesting crops. They enable the efficient movement of equipment, which is crucial during peak harvest periods. This application enhances productivity and minimizes downtime, allowing farmers to maximize yield. When sourcing chains for agricultural applications, buyers should consider factors such as corrosion resistance and adaptability to diverse environmental conditions, as these can impact the longevity and performance of the equipment.
Why is Chain Manufacturing Important in the Mining Industry?
Chains are essential in the mining industry, particularly in equipment designed for ore extraction. They enhance safety by providing reliable movement of heavy loads and materials. Additionally, robust chains improve operational efficiency by reducing downtime caused by equipment failures. For international buyers in this sector, key considerations include the strength of the chain and its resistance to wear, as these factors directly affect the equipment’s performance under harsh conditions.
How Does Chain Manufacturing Benefit the Food Processing Industry?
In the food processing sector, chains are utilized in conveyor systems that handle food products. These systems are designed to ensure hygiene while efficiently moving items through various stages of production. The use of chains in this context helps maintain food safety standards and boosts overall production efficiency. Buyers should focus on sourcing chains that comply with health regulations and feature easy cleaning mechanisms to facilitate maintenance and sanitation.
What Advantages Does Chain Manufacturing Offer in Logistics and Warehousing?
In logistics and warehousing, chains are crucial for automated sorting systems that streamline the movement of goods. They optimize space utilization and enhance the speed of order fulfillment, which is vital in today’s fast-paced market. When sourcing chains for these applications, buyers should prioritize reliability and ease of maintenance, as well as the availability of spare parts, to ensure uninterrupted operations and minimize potential downtime.
Related Video: ‘Complete garbage’: GOP uses gimmick to make Trump’s awful spending bill seem like it’s not so bad
3 Common User Pain Points for ‘chain manufacturer’ & Their Solutions
Scenario 1: Difficulty in Sourcing Quality Chains for Diverse Applications
The Problem: B2B buyers often encounter challenges in sourcing chains that meet specific quality standards and application requirements. For instance, a manufacturing company in South America may need chains that can withstand high temperatures and corrosive environments, yet local suppliers may not offer suitable options. This situation leads to operational delays, increased costs, and potential safety hazards.
The Solution: To effectively source high-quality chains, buyers should begin by conducting a thorough market analysis to identify reputable chain manufacturers with a proven track record in producing specialized chains. Networking at industry trade shows and utilizing platforms like LinkedIn to connect with industry experts can provide insights into reliable manufacturers. Additionally, buyers should ask for samples and detailed product specifications, ensuring that the chains are tested under relevant conditions. Establishing long-term relationships with suppliers who understand your specific needs can lead to better pricing and consistent quality over time.
Scenario 2: Inconsistent Chain Performance Leading to Downtime
The Problem: Inconsistencies in chain performance can lead to frequent breakdowns and unplanned downtime, affecting productivity. A European company utilizing automated machinery may find that the chains supplied are not consistently meeting performance standards, resulting in increased maintenance costs and disruptions in production schedules.
The Solution: To mitigate performance issues, buyers must prioritize working with manufacturers who provide comprehensive performance data and warranties for their products. Implementing a robust quality assurance process that includes regular inspections and performance testing of chains can help identify potential issues before they escalate. Furthermore, buyers should invest in training for their maintenance teams on proper installation and care of chains, as well as creating a feedback loop with the manufacturer to communicate performance observations. This proactive approach fosters collaboration and ensures that manufacturers can make necessary adjustments to improve product reliability.
Scenario 3: Navigating Complex International Shipping and Regulations
The Problem: B2B buyers, especially those operating in Africa or the Middle East, frequently face challenges related to international shipping and compliance with local regulations when importing chains. Delays in shipping, unexpected tariffs, and regulatory hurdles can complicate procurement processes and lead to unexpected costs.
The Solution: To streamline international procurement, buyers should engage logistics partners who specialize in shipping industrial products and are familiar with customs regulations in their region. Conducting due diligence on the chosen manufacturers to ensure they have experience with international shipping can also prevent potential pitfalls. It is advisable for buyers to develop a comprehensive understanding of their country’s import regulations, including any specific documentation required for chains. Additionally, leveraging trade agreements between countries can help reduce tariffs and expedite the shipping process. Establishing a clear communication channel with the manufacturer regarding shipping expectations and timelines is crucial to avoid disruptions in the supply chain.
Strategic Material Selection Guide for chain manufacturer
What Are the Key Properties of Common Materials Used in Chain Manufacturing?
When selecting materials for chain manufacturing, it is crucial to consider the specific properties that will affect the performance and longevity of the product. Here, we analyze four common materials used in the industry: carbon steel, stainless steel, plastic, and alloy steel. Each material presents unique characteristics that can significantly influence the end product’s suitability for various applications.
How Does Carbon Steel Perform in Chain Manufacturing?
Key Properties: Carbon steel is known for its high tensile strength and durability, making it suitable for heavy-duty applications. It typically has a temperature rating of up to 400°F (204°C) and can withstand moderate pressure levels. However, it is susceptible to corrosion if not properly treated.
Pros & Cons: The primary advantage of carbon steel is its cost-effectiveness and ease of manufacturing. It is readily available and can be produced in various grades to meet specific needs. On the downside, its susceptibility to rust and corrosion can limit its use in environments with high humidity or exposure to chemicals.
Impact on Application: Carbon steel chains are ideal for applications in construction, mining, and agriculture, where strength is paramount. However, they may not be suitable for marine or chemical processing applications due to corrosion risks.
Considerations for International Buyers: Buyers from regions such as Africa and South America should ensure compliance with local standards, as carbon steel grades can vary. Familiarity with ASTM or DIN specifications can aid in selecting the right grade.
What Are the Benefits of Using Stainless Steel for Chains?
Key Properties: Stainless steel offers excellent corrosion resistance, making it suitable for applications exposed to moisture or chemicals. It can handle temperatures up to 1,500°F (815°C) and is available in various grades, including 304 and 316, which provide differing levels of corrosion resistance.
Pros & Cons: The key advantage of stainless steel is its durability and ability to maintain structural integrity in harsh environments. However, it is typically more expensive than carbon steel and may require more complex manufacturing processes.
Impact on Application: Stainless steel chains are commonly used in food processing, pharmaceuticals, and marine applications where hygiene and corrosion resistance are critical.
Considerations for International Buyers: Buyers in Europe, particularly in countries like Italy and Spain, often prefer stainless steel due to stringent hygiene regulations. Understanding the specific grades and compliance with EU standards is essential.
How Do Plastic Chains Compare in Terms of Performance?
Key Properties: Plastic chains are lightweight and resistant to corrosion, making them an attractive option for specific applications. They can withstand temperatures ranging from -40°F to 200°F (-40°C to 93°C) and are generally non-conductive.
Pros & Cons: The primary advantage of plastic chains is their low weight and resistance to various chemicals. However, they may not offer the same strength or durability as metal chains and can be more susceptible to wear under heavy loads.
Impact on Application: Plastic chains are ideal for conveyor systems in the food industry, where cleanliness is essential. They are also used in environments where metal chains may corrode.
Considerations for International Buyers: Buyers from the Middle East should be aware of the specific chemical compatibility of plastic materials, as high temperatures can affect performance. Compliance with local standards can also vary.
What Advantages Do Alloy Steel Chains Offer?
Key Properties: Alloy steel combines carbon steel with other elements, such as chromium or nickel, to enhance its properties. It typically has a higher tensile strength and better wear resistance than standard carbon steel, with temperature ratings similar to carbon steel.
Pros & Cons: The advantage of alloy steel is its superior performance in demanding applications, offering a balance between cost and durability. However, it can be more expensive and may require specialized manufacturing techniques.
Impact on Application: Alloy steel chains are commonly used in heavy machinery, automotive, and aerospace applications where strength and reliability are critical.
Considerations for International Buyers: Buyers in South America should consider the availability of alloy steel grades and ensure compliance with ASTM standards. Understanding the specific requirements for their industry can help in selecting the right material.
Summary Table of Material Selection for Chain Manufacturing
Material | Typical Use Case for chain manufacturer | Key Advantage | Key Disadvantage/Limitation | Relative Cost (Low/Med/High) |
---|---|---|---|---|
Carbon Steel | Construction, mining, agriculture | Cost-effective, high strength | Susceptible to corrosion | Low |
Stainless Steel | Food processing, pharmaceuticals | Excellent corrosion resistance | Higher cost, complex manufacturing | High |
Plastic | Conveyor systems in food industry | Lightweight, corrosion-resistant | Lower strength, wear susceptibility | Medium |
Alloy Steel | Heavy machinery, automotive, aerospace | Superior performance and durability | More expensive, specialized manufacturing | Medium to High |
This strategic material selection guide provides international B2B buyers with essential insights into the properties, advantages, and limitations of different materials used in chain manufacturing. Understanding these factors can aid in making informed purchasing decisions tailored to specific applications and regional requirements.
In-depth Look: Manufacturing Processes and Quality Assurance for chain manufacturer
What Are the Main Stages of Manufacturing Processes for Chain Manufacturers?
The manufacturing of chains involves several critical stages that ensure the production of high-quality and durable products. Understanding these stages is vital for international B2B buyers, as it directly affects the performance and reliability of the chains being sourced.
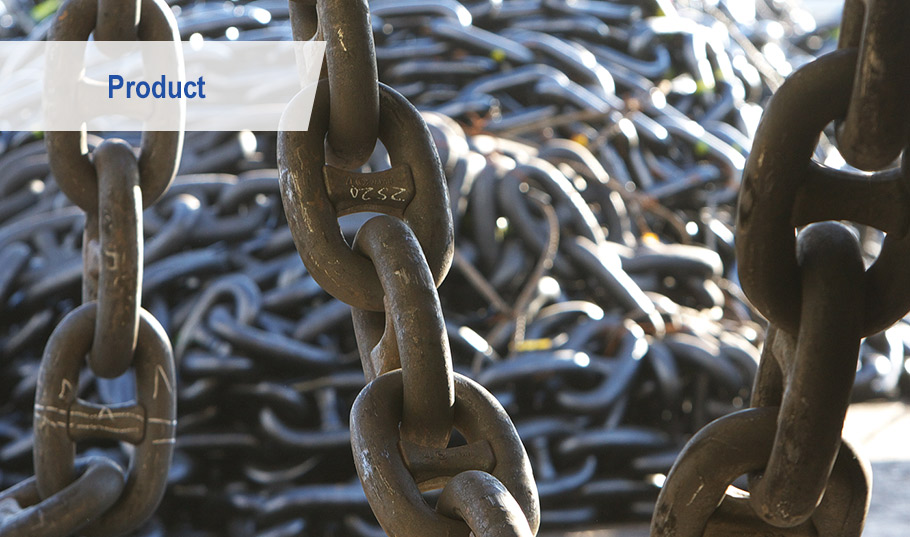
A stock image related to chain manufacturer.
1. Material Preparation: What Materials Are Commonly Used in Chain Manufacturing?
The first step in chain manufacturing is material preparation, which typically involves selecting high-quality steel or alloy materials. Common materials include carbon steel, stainless steel, and other alloys that provide strength and corrosion resistance.
- Material Testing: Before processing, materials undergo testing for tensile strength and hardness to ensure they meet specified standards. This step is crucial for buyers who require chains for demanding applications.
2. Forming: How Are Chains Shaped?
In the forming stage, raw materials are shaped into the desired chain components. This process often includes techniques such as:
- Forging: This method uses compressive forces to shape the metal, resulting in improved structural integrity.
- Casting: Molten metal is poured into a mold to create specific chain links or components.
- Machining: Components are further refined using CNC machines to achieve precise dimensions.
Each technique has its advantages and is selected based on the intended use of the chain, making it essential for buyers to understand these nuances.
3. Assembly: What Are the Key Steps in Chain Assembly?
The assembly process involves connecting the formed components to create the final chain product. This may include:
- Link Assembly: Individual links are connected using pins or other fasteners.
- Heat Treatment: Chains may undergo heat treatment to enhance hardness and wear resistance.
Quality during assembly is critical, as any misalignment can lead to premature failure. B2B buyers should inquire about the assembly techniques used by manufacturers to ensure reliability.
4. Finishing: What Finishing Techniques Are Commonly Used?
Finishing processes enhance the chain’s appearance and performance. Common finishing techniques include:
- Coating: Protective coatings, such as galvanization or powder coating, are applied to prevent corrosion.
- Polishing: This process improves the surface finish, reducing friction and wear.
These finishing touches not only enhance aesthetics but also extend the lifespan of the chain, making them a vital consideration for buyers from various regions, including Africa, South America, and Europe.
What Quality Assurance Measures Should B2B Buyers Expect from Chain Manufacturers?
Quality assurance (QA) is integral to the manufacturing process, ensuring that the final products meet international standards and customer specifications. Understanding the QA measures in place can help B2B buyers make informed decisions.
1. What International Standards Are Relevant for Chain Manufacturers?
Several international standards govern quality assurance in manufacturing, including:
- ISO 9001: This standard outlines the requirements for a quality management system (QMS). Manufacturers certified to ISO 9001 demonstrate their ability to consistently provide products that meet customer and regulatory requirements.
- CE Marking: Commonly required in Europe, this marking indicates that a product conforms to health, safety, and environmental protection standards.
- API Specifications: For chains used in the oil and gas industry, adherence to American Petroleum Institute (API) standards is critical.
Buyers should verify that their suppliers possess relevant certifications, as this can significantly impact product quality.
2. What Are the Key Quality Control Checkpoints in Chain Manufacturing?
Quality control (QC) is typically divided into several checkpoints throughout the manufacturing process:
- Incoming Quality Control (IQC): Materials are inspected upon arrival to ensure they meet specifications.
- In-Process Quality Control (IPQC): Regular inspections during manufacturing identify defects early in the process.
- Final Quality Control (FQC): The finished products undergo rigorous testing to confirm they meet quality standards before shipping.
Each checkpoint serves to catch potential issues that could affect product quality, making them essential for B2B buyers to understand.
3. What Testing Methods Are Commonly Used in Chain Quality Assurance?
Various testing methods are employed to ensure the durability and reliability of chains:
- Tensile Testing: Measures the force required to pull the chain until it breaks, ensuring it can withstand operational loads.
- Fatigue Testing: Assesses the chain’s ability to endure repeated stress over time.
- Corrosion Resistance Testing: Evaluates how well the chain can resist environmental factors that may lead to rust or degradation.
B2B buyers should request information on testing methods used by manufacturers to confirm that products meet their operational needs.
How Can B2B Buyers Verify Supplier Quality Control?
Verifying the quality control processes of suppliers is crucial for B2B buyers, especially when sourcing from international markets.
1. What Should Buyers Look for in Supplier Audits?
Conducting supplier audits is an effective way to assess quality control practices. Buyers should consider:
- Frequency of Audits: Regular audits indicate a commitment to maintaining quality standards.
- Audit Reports: Reviewing past audit reports can provide insights into the supplier’s performance and areas for improvement.
2. How Can Buyers Utilize Third-Party Inspections?
Engaging third-party inspection services can offer an unbiased assessment of the manufacturer’s quality control processes. These inspections can verify compliance with international standards and ensure that the products meet the buyer’s specifications before shipment.
3. What Documentation Should Buyers Request from Suppliers?
Buyers should request the following documentation to validate quality control measures:
- Certificates of Compliance: Proof that the products meet specific standards.
- Test Reports: Documentation of results from various testing methods.
- Quality Assurance Manuals: Information on the manufacturer’s quality management system.
By asking for these documents, buyers can gain confidence in the quality of the products they are sourcing.
Conclusion: How Can Understanding Manufacturing Processes and Quality Assurance Benefit B2B Buyers?
A comprehensive understanding of the manufacturing processes and quality assurance measures in chain manufacturing empowers B2B buyers to make informed sourcing decisions. By focusing on material preparation, forming, assembly, finishing, and rigorous quality control, buyers can ensure they are selecting reliable suppliers that adhere to international standards. This knowledge not only helps mitigate risks associated with product failures but also enhances the overall value of their procurement strategies.
Practical Sourcing Guide: A Step-by-Step Checklist for ‘chain manufacturer’
In the competitive landscape of B2B procurement for chain manufacturing, having a structured sourcing guide can significantly streamline the process. This checklist is designed to help international buyers from Africa, South America, the Middle East, and Europe effectively navigate their sourcing journey.
Step 1: Define Your Technical Specifications
Before reaching out to suppliers, clearly outline your technical requirements. This includes the type of chain (e.g., roller chain, conveyor chain), dimensions, load capacity, and material specifications. Having precise specifications ensures that you attract suppliers who can meet your needs, reducing the risk of miscommunication and ensuring quality.
Step 2: Research Potential Suppliers
Start by compiling a list of potential suppliers based on your specifications. Utilize online directories, industry trade shows, and referrals from industry contacts. Ensure that the suppliers have a proven track record in manufacturing the specific type of chain you need, as this will be critical to your project’s success.
Step 3: Evaluate Supplier Certifications and Compliance
Verify that your potential suppliers hold relevant certifications, such as ISO 9001 for quality management. Compliance with international standards ensures that the products meet safety and performance criteria. Additionally, inquire about environmental certifications, which can be a significant factor for buyers in Europe and other regions focused on sustainability.
Step 4: Request Detailed Quotations
Once you have a shortlist of suppliers, request detailed quotations that include pricing, lead times, payment terms, and shipping costs. This transparency allows for better comparison and negotiation. Ensure that the quotes specify whether the prices are per unit or in bulk, as this can affect your overall budgeting.
Step 5: Assess Production Capacity and Lead Times
Understanding a supplier’s production capacity is vital. Ask about their current workload and the typical lead times for orders similar to yours. Suppliers with flexible production capabilities can better accommodate changes in your order volume or delivery schedule, which is particularly important for international buyers facing logistical challenges.
Step 6: Check Customer Reviews and References
Request references from existing clients and check online reviews to gauge supplier reliability and product quality. Engaging with other companies that have sourced from the supplier can provide insights into their customer service and responsiveness. This step is crucial for avoiding potential pitfalls and ensuring a reliable partnership.
Step 7: Negotiate Terms and Finalize the Agreement
Once you have selected a supplier, engage in negotiations to finalize terms. Discuss pricing, delivery schedules, and after-sales support. Ensure that all agreements are documented in a formal contract, which protects both parties and clarifies expectations. This step is essential for establishing a clear framework for your ongoing relationship with the supplier.
By following this structured sourcing guide, B2B buyers can enhance their procurement process for chain manufacturing, ensuring they select the right partners to meet their operational needs effectively.
Comprehensive Cost and Pricing Analysis for chain manufacturer Sourcing
What are the Key Cost Components in Chain Manufacturing?
When analyzing the cost structure of chain manufacturing, several critical components need to be considered:
-
Materials: The cost of raw materials, such as steel or plastic, significantly impacts the overall pricing. Fluctuations in global commodity prices can affect sourcing strategies, particularly for international buyers from Africa, South America, the Middle East, and Europe.
-
Labor: Labor costs vary widely depending on the region and local wage standards. Understanding the labor market in the supplier’s location is essential for assessing total costs.
-
Manufacturing Overhead: This includes indirect costs such as utilities, rent, and administrative expenses. Efficient manufacturing processes can help reduce these overheads, allowing for competitive pricing.
-
Tooling: The initial investment in tooling can be substantial, especially for customized chains. Buyers should inquire about tooling costs and whether they are included in the quoted price.
-
Quality Control (QC): Implementing rigorous QC processes ensures product reliability, which can lead to higher initial costs but ultimately reduces long-term expenses due to lower failure rates.
-
Logistics: Shipping costs, including freight, customs duties, and warehousing, can significantly affect the final price. Understanding Incoterms can help buyers navigate logistics costs effectively.
-
Margin: Suppliers typically include a profit margin in their pricing. This margin can vary based on competition, market demand, and perceived value.
How Do Price Influencers Affect Chain Manufacturing Costs?
Several factors influence the pricing of chain manufacturing, particularly for international buyers:
-
Volume and Minimum Order Quantity (MOQ): Bulk orders often lead to lower per-unit costs. Buyers should negotiate MOQs that align with their demand to maximize cost efficiency.
-
Specifications and Customization: Custom chains or specific engineering requirements can increase costs. Buyers should clearly define specifications to avoid unexpected charges.
-
Materials and Quality Certifications: Higher quality materials and certifications (e.g., ISO, CE) can raise prices. However, investing in quality can reduce long-term operational costs.
-
Supplier Factors: The supplier’s reputation, reliability, and financial stability can influence pricing. Establishing long-term relationships with reputable suppliers can lead to better pricing and service.
-
Incoterms: Understanding Incoterms is critical for international transactions. They define responsibilities for shipping, insurance, and tariffs, which can affect the total cost of ownership.
What Are Effective Negotiation and Cost-Efficiency Strategies for Buyers?
To secure favorable pricing and ensure cost-efficiency, international B2B buyers should consider the following strategies:
-
Conduct Thorough Market Research: Understanding market trends and pricing benchmarks within the chain manufacturing industry helps in negotiating better terms.
-
Leverage Total Cost of Ownership (TCO): Evaluate not just the purchase price but the entire lifecycle cost, including maintenance, replacement, and operational costs. This broader perspective can justify higher upfront investments in quality products.
-
Build Relationships with Suppliers: Establishing strong relationships can lead to better pricing, improved service, and preferential treatment in terms of lead times and custom orders.
-
Be Transparent About Your Needs: Clearly communicate your volume requirements and any specific needs. This transparency can lead to tailored pricing solutions that benefit both parties.
-
Explore Multiple Suppliers: Don’t rely on a single supplier. Engaging multiple suppliers can create competitive pressure and lead to better pricing.
Are There Specific Pricing Nuances for International Buyers?
International B2B buyers, particularly from regions such as Africa, South America, the Middle East, and Europe (including Spain and Italy), should be aware of the following nuances:
-
Currency Fluctuations: Be mindful of exchange rates, as they can significantly affect pricing. Consider negotiating prices in a stable currency.
-
Tariffs and Trade Policies: Import duties can impact the final cost. Stay informed about trade agreements and tariffs that may apply to your transactions.
-
Cultural Differences in Negotiation: Different regions have distinct negotiation styles. Understanding these cultural nuances can facilitate smoother discussions and agreements.
Disclaimer on Indicative Prices
It is important to note that prices can vary widely based on the aforementioned factors. Always request detailed quotations and clarify any terms before finalizing agreements to avoid misunderstandings.
Alternatives Analysis: Comparing chain manufacturer With Other Solutions
Understanding Alternatives to Chain Manufacturers for B2B Buyers
In the competitive landscape of manufacturing and supply chain management, international B2B buyers often seek alternatives to traditional chain manufacturers. These alternatives may offer different benefits in terms of performance, cost, and flexibility. This section provides a detailed comparison between chain manufacturers and two viable alternatives: additive manufacturing (3D printing) and outsourcing to specialized suppliers.
Comparison Table
Comparison Aspect | Chain Manufacturer | Additive Manufacturing (3D Printing) | Outsourcing to Specialized Suppliers |
---|---|---|---|
Performance | High durability and strength | Customizable and complex designs possible | Variable performance based on supplier |
Cost | Higher upfront costs, lower per-unit cost at scale | Lower initial cost, high cost per unit for small runs | Variable costs, often cheaper for low volume |
Ease of Implementation | Requires significant setup time and resources | Quick setup, especially for prototypes | Relatively simple if the supplier is reliable |
Maintenance | Requires regular maintenance and quality checks | Minimal maintenance, dependent on technology | Maintenance handled by the supplier |
Best Use Case | Large scale production of standard products | Prototyping, low-volume custom parts | Custom parts and unique designs from specialized providers |
Detailed Breakdown of Alternatives
What Are the Advantages and Disadvantages of Additive Manufacturing (3D Printing)?
Additive manufacturing, commonly known as 3D printing, offers unique advantages such as the ability to produce highly customized and complex designs without the need for expensive tooling. This makes it an ideal choice for prototyping or producing low-volume components. However, the cost per unit can be significantly higher for larger production runs, making it less economically viable compared to chain manufacturing. Additionally, the technology requires a skilled workforce to operate and maintain the printers, which can be a barrier for some companies.
How Does Outsourcing to Specialized Suppliers Compare?
Outsourcing to specialized suppliers can provide B2B buyers with flexibility and cost savings, particularly for low-volume orders or unique products that require specific expertise. This approach allows companies to leverage the capabilities of suppliers who may have advanced technologies or specialized skills that are not available in-house. However, the variability in performance and quality can be a risk, as it heavily depends on the reliability of the chosen supplier. Effective communication and quality assurance processes are crucial to mitigate these risks.
How Can B2B Buyers Choose the Right Solution for Their Needs?
When selecting between chain manufacturers and alternative solutions, B2B buyers should carefully evaluate their specific needs regarding production volume, customization, and budget. If the project requires high durability and large-scale production, chain manufacturing may be the most suitable option. Conversely, for projects that prioritize customization and rapid prototyping, additive manufacturing could be the better choice. Outsourcing is ideal for businesses looking to reduce overhead costs while maintaining quality for specialized products. Ultimately, understanding the unique advantages and limitations of each option will enable buyers to make informed decisions that align with their strategic goals.
Essential Technical Properties and Trade Terminology for chain manufacturer
What Are the Key Technical Properties for Chain Manufacturing?
Understanding the essential technical properties of chains is crucial for international B2B buyers, especially when sourcing from manufacturers across Africa, South America, the Middle East, and Europe. Here are several critical specifications that should be considered:
-
Material Grade
The material grade of a chain significantly affects its strength, durability, and application suitability. Common materials include stainless steel, carbon steel, and alloy steel. For instance, stainless steel chains resist corrosion, making them ideal for marine or food processing applications. Buyers should assess the specific environmental conditions the chain will face to choose the appropriate material grade. -
Tensile Strength
Tensile strength is the maximum amount of tensile (pulling) stress that a chain can withstand before failing. This property is vital for applications involving heavy loads. A higher tensile strength often means a more robust chain, which can lead to increased safety and longevity. Buyers should consult manufacturers for detailed tensile strength data to ensure the chain meets their operational requirements. -
Tolerance
Tolerance refers to the permissible limit or limits of variation in a physical dimension of the chain. Precision in manufacturing ensures that chains fit correctly into their intended applications, reducing wear and increasing efficiency. Buyers should inquire about the tolerance specifications during the procurement process to avoid compatibility issues. -
Pitch
The pitch of a chain is the distance between the centers of two consecutive pins. It is a critical measurement that affects the chain’s compatibility with sprockets and its overall performance. For example, industrial chains typically have a standard pitch size that must align with the machinery they are used in. Buyers should verify pitch specifications when sourcing chains to ensure seamless integration. -
Surface Treatment
Surface treatments, such as galvanization or plating, enhance the chain’s resistance to environmental factors like corrosion and wear. These treatments can significantly prolong the lifespan of the chain, making them a worthwhile investment. Buyers should consider the operational environment and opt for appropriate surface treatments to maximize durability.
What Are Common Trade Terminology and Jargon in Chain Manufacturing?
Familiarity with industry jargon can streamline communication and enhance negotiations. Here are several essential terms that B2B buyers should know:
-
OEM (Original Equipment Manufacturer)
An OEM refers to a company that produces parts or equipment that may be marketed by another manufacturer. Understanding this term is vital for buyers who need to source chains that fit existing machinery or systems. Engaging with OEMs can also provide insights into compatibility and performance standards. -
MOQ (Minimum Order Quantity)
MOQ indicates the smallest quantity of a product that a supplier is willing to sell. This term is crucial for budgeting and inventory management, especially for international buyers who may face additional shipping costs. Understanding MOQ can help buyers negotiate better terms and avoid overstock situations. -
RFQ (Request for Quotation)
An RFQ is a document sent to suppliers to solicit price quotes for specific products or services. This is an essential step in the procurement process, allowing buyers to compare prices and terms from various manufacturers. A well-structured RFQ can lead to more accurate responses and better pricing. -
Incoterms (International Commercial Terms)
Incoterms define the responsibilities of buyers and sellers in international trade, particularly regarding shipping, insurance, and tariffs. Familiarity with these terms helps buyers understand their obligations and those of the supplier, ensuring smoother transactions. Key Incoterms include FOB (Free on Board) and CIF (Cost, Insurance, and Freight). -
Lead Time
Lead time refers to the amount of time it takes from placing an order to receiving the product. Understanding lead times is crucial for supply chain planning and inventory management. Buyers should always inquire about lead times during the ordering process to ensure timely delivery.
By grasping these technical properties and trade terms, international B2B buyers can make informed decisions, optimize their procurement strategies, and enhance their overall supply chain efficiency.
Navigating Market Dynamics and Sourcing Trends in the chain manufacturer Sector
What Are the Key Market Dynamics and Sourcing Trends in the Chain Manufacturer Sector?
The chain manufacturer sector is currently experiencing significant transformations driven by globalization, technological advancements, and shifting consumer demands. International B2B buyers, particularly from Africa, South America, the Middle East, and Europe, are witnessing a surge in demand for high-quality, durable chains used in various applications, including automotive, construction, and industrial machinery. The global market is projected to expand at a compound annual growth rate (CAGR) of approximately 4% over the next five years, fueled by the growing industrial sector and infrastructural developments in emerging markets.
Emerging technologies, such as IoT and AI, are reshaping sourcing strategies. B2B buyers are increasingly leveraging data analytics to optimize supply chains and enhance decision-making processes. For instance, IoT-enabled devices can provide real-time tracking of chain products, improving inventory management and reducing lead times. Moreover, the rise of e-commerce platforms is facilitating easier access to suppliers, enabling international buyers to source products more efficiently and cost-effectively.
Sustainability is becoming a critical factor in procurement decisions. International buyers are now prioritizing suppliers who demonstrate commitment to environmentally responsible practices. This shift is particularly relevant in Europe, where stringent regulations regarding emissions and waste management are being enforced. Consequently, manufacturers are adopting sustainable practices in production, such as using recycled materials and reducing energy consumption.
How Is Sustainability Shaping Sourcing Trends in the Chain Manufacturer Sector?
The environmental impact of manufacturing processes is a growing concern for B2B buyers in the chain manufacturing sector. As global awareness of climate change and resource depletion increases, businesses are under pressure to adopt sustainable practices throughout their supply chains. Buyers are now looking for manufacturers that prioritize sustainability, which often includes sourcing materials that are environmentally friendly and ethically produced.
Ethical sourcing is gaining traction, with a focus on ensuring fair labor practices and reducing the environmental footprint. Certifications such as ISO 14001 (Environmental Management) and ISO 45001 (Occupational Health and Safety) are becoming essential for suppliers aiming to gain the trust of international buyers. Additionally, the use of green materials, such as biodegradable lubricants or recycled steel, is increasingly being recognized as a competitive advantage.
For B2B buyers, understanding the sustainability credentials of potential suppliers can significantly impact procurement decisions. Suppliers that emphasize transparency and provide evidence of their sustainability initiatives are more likely to attract international buyers seeking to enhance their own corporate social responsibility (CSR) profiles.
How Has the Chain Manufacturing Sector Evolved Over Time?
The chain manufacturing sector has evolved significantly over the last few decades, driven by technological advancements and changing market demands. Initially dominated by traditional manufacturing processes, the industry has seen a shift towards automation and precision engineering. The introduction of computer-aided design (CAD) and computer numerical control (CNC) machining has allowed for greater accuracy and efficiency in production.
In recent years, globalization has further transformed the landscape, enabling manufacturers to source materials and components from various regions, thereby reducing costs and expanding their market reach. This evolution has also led to increased competition, pushing manufacturers to innovate continuously and improve product quality.
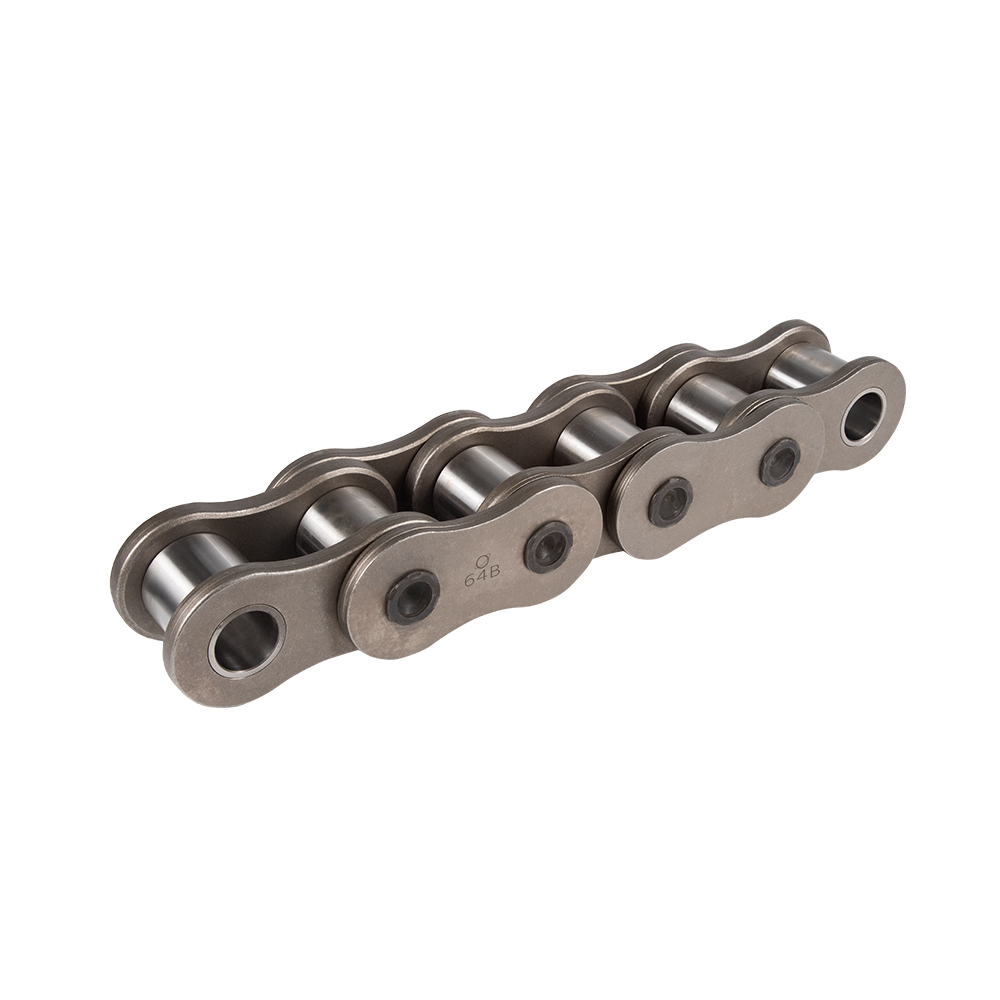
A stock image related to chain manufacturer.
Furthermore, the rise of digital platforms has changed how buyers and suppliers interact, facilitating easier access to information and enabling more informed purchasing decisions. As the sector continues to adapt to market dynamics, B2B buyers can expect ongoing changes in sourcing strategies, product offerings, and sustainability practices.
Frequently Asked Questions (FAQs) for B2B Buyers of chain manufacturer
-
How do I identify a reliable chain manufacturer for my business needs?
To identify a reliable chain manufacturer, start by researching their market reputation through online reviews and testimonials. Look for manufacturers with a strong presence in your industry and those who can provide case studies of past projects. Verify their certifications and compliance with international quality standards, such as ISO. Networking through industry trade shows and forums can also help you connect with reputable suppliers. Finally, request samples and assess their customer service responsiveness to gauge their commitment to quality and support. -
What are the key factors to consider when sourcing chain manufacturers internationally?
When sourcing chain manufacturers internationally, consider factors such as production capacity, lead times, and shipping logistics. Assess their ability to meet your specific requirements, including material specifications and customization options. It’s also vital to understand the manufacturer’s compliance with international trade regulations and quality assurance processes. Currency exchange rates and payment terms can significantly impact your overall costs, so ensure clarity on these aspects before proceeding with an order. -
How can I ensure the quality of chains from international suppliers?
To ensure the quality of chains from international suppliers, request detailed product specifications and certifications that align with your industry standards. Implement a robust quality assurance (QA) process that includes pre-shipment inspections and testing. Consider establishing a trial order to evaluate product quality before committing to larger quantities. Additionally, maintain open communication with the supplier regarding quality expectations and any issues that may arise during production. -
What are common minimum order quantities (MOQ) for chain manufacturers?
Minimum order quantities (MOQ) for chain manufacturers can vary widely depending on the type of chain and the manufacturer’s policies. Typically, MOQs can range from 100 to 1,000 units, but some manufacturers may accommodate smaller orders for specific products. When negotiating with suppliers, express your needs clearly and inquire if they offer flexibility in MOQs, especially for new customers or trial orders. Understanding MOQs is crucial for effective inventory management and cash flow. -
What payment terms should I expect when dealing with chain manufacturers?
Payment terms with chain manufacturers can differ significantly, but common practices include a deposit (usually 30-50%) upfront and the balance upon delivery or before shipment. Some manufacturers may offer credit terms based on your business relationship and order history. Always clarify payment methods accepted (e.g., wire transfer, credit card) and ensure that you understand any additional fees related to international transactions. This clarity can help avoid misunderstandings and financial strain. -
How do I handle logistics and shipping when sourcing chains from overseas?
Handling logistics and shipping when sourcing chains from overseas involves coordinating with your supplier and a reliable freight forwarder. Discuss shipping options such as air or sea freight, taking into account cost, speed, and reliability. Ensure you understand customs regulations in your country to prevent delays. It’s beneficial to negotiate Incoterms with your supplier to clarify responsibilities for shipping costs and risk. Proper logistics planning will help you manage lead times effectively and maintain inventory levels.
-
What customization options are typically available for chain products?
Many chain manufacturers offer a range of customization options, including material selection, size, and design modifications to suit specific applications. It’s essential to communicate your requirements clearly and inquire about the manufacturer’s capabilities. Some suppliers may also provide prototyping services, allowing you to test designs before full-scale production. Customization can enhance the functionality of the chains for your specific use, making this an important consideration during your sourcing process. -
How can I assess the sustainability practices of chain manufacturers?
Assessing the sustainability practices of chain manufacturers involves reviewing their environmental policies and certifications, such as ISO 14001 for environmental management. Inquire about their sourcing of raw materials and whether they use recycled or eco-friendly materials. Evaluate their production processes for waste management and energy efficiency. Engaging in dialogue with manufacturers about their sustainability initiatives can provide insights into their commitment to responsible practices, which is increasingly important for businesses today.
Important Disclaimer & Terms of Use
⚠️ Important Disclaimer
The information provided in this guide, including content regarding manufacturers, technical specifications, and market analysis, is for informational and educational purposes only. It does not constitute professional procurement advice, financial advice, or legal advice.
While we have made every effort to ensure the accuracy and timeliness of the information, we are not responsible for any errors, omissions, or outdated information. Market conditions, company details, and technical standards are subject to change.
B2B buyers must conduct their own independent and thorough due diligence before making any purchasing decisions. This includes contacting suppliers directly, verifying certifications, requesting samples, and seeking professional consultation. The risk of relying on any information in this guide is borne solely by the reader.
Strategic Sourcing Conclusion and Outlook for chain manufacturer
In the rapidly evolving landscape of chain manufacturing, strategic sourcing emerges as a critical component for international B2B buyers aiming to optimize supply chains and enhance operational efficiency. By focusing on the strategic procurement of materials and components, companies can significantly reduce costs while ensuring the quality and reliability of their products. This approach not only fosters better supplier relationships but also enables buyers to leverage global market opportunities, particularly in regions like Africa, South America, the Middle East, and Europe.
What are the long-term benefits of adopting a strategic sourcing approach? Companies that invest in thorough market analysis, supplier evaluation, and risk management are better positioned to adapt to market fluctuations and supply chain disruptions. This proactive strategy ultimately leads to improved profitability and competitive advantage.
As we look to the future, B2B buyers should prioritize building resilient supply chains that can withstand global challenges. By embracing technology and data analytics, organizations can make informed decisions that drive value and innovation. Now is the time for international buyers, especially those in Spain and Italy, to act decisively and explore the vast potential of strategic sourcing in chain manufacturing. The path to enhanced operational success and sustainable growth begins with informed sourcing decisions.