Discover Cost-Effective Dining Room Chairs Custom Solutions (2025)
Introduction: Navigating the Global Market for dining room chairs custom
In the dynamic landscape of global trade, sourcing custom dining room chairs presents a unique challenge for B2B buyers. With a diverse range of styles, materials, and functionalities available, making the right choice can be daunting, especially for international buyers seeking quality and affordability. This comprehensive guide aims to demystify the process by providing actionable insights into various types of custom dining chairs, their applications across different markets, and critical factors to consider when vetting suppliers.
International buyers from regions like Africa, South America, the Middle East, and Europe—including countries such as Poland and Vietnam—will benefit from detailed analysis on cost structures, shipping logistics, and compliance with local regulations. We will explore not only the aesthetic and functional aspects of custom dining chairs but also the importance of understanding cultural preferences and market trends that influence purchasing decisions.
By equipping B2B buyers with the knowledge to navigate supplier landscapes, assess quality, and negotiate effectively, this guide empowers you to make informed purchasing decisions that enhance your business offerings. Whether you’re looking to furnish a hospitality venue, enhance a retail space, or supply commercial clients, understanding the nuances of the custom dining chair market is essential for achieving long-term success in a competitive environment.
Understanding dining room chairs custom Types and Variations
Type Name | Key Distinguishing Features | Primary B2B Applications | Brief Pros & Cons for Buyers |
---|---|---|---|
Upholstered Dining Chairs | Soft padding and various fabric options for comfort | Restaurants, hotels, and event venues | Pros: Comfort, aesthetic appeal; Cons: Higher maintenance, potential wear on fabric. |
Wooden Dining Chairs | Crafted from solid wood, offering durability and classic style | Cafés, fine dining, and upscale events | Pros: Long-lasting, timeless; Cons: Heavier, can be more expensive. |
Metal Frame Chairs | Lightweight with modern designs, often stackable | Outdoor dining, casual dining establishments | Pros: Easy to move, weather-resistant; Cons: Less comfort without padding, can be cold. |
Customizable Modular Chairs | Configurable designs that can be adjusted for space | Co-working spaces, flexible dining areas | Pros: Versatile, space-efficient; Cons: May require more planning for layout. |
Antique Replica Chairs | Vintage style with modern materials, often bespoke | Specialty restaurants, boutique hotels | Pros: Unique character, attracts niche markets; Cons: May have limited availability and higher costs. |
What are the characteristics of Upholstered Dining Chairs?
Upholstered dining chairs are characterized by their soft padding and diverse fabric options, providing a high level of comfort. They are particularly suitable for environments where guests may linger, such as restaurants and hotels. When purchasing, consider the fabric durability and ease of cleaning, as these chairs can be prone to staining. Additionally, upholstery can significantly influence the overall aesthetic of the dining area, making it essential to align with the venue’s theme.
How do Wooden Dining Chairs compare in durability and style?
Wooden dining chairs are known for their robustness and classic appeal, making them a staple in many dining environments, including cafés and fine dining establishments. They offer a timeless design that can complement various decor styles. Buyers should evaluate the type of wood used, as this affects durability and maintenance. While they are generally more durable than upholstered options, wooden chairs can be heavier and may require more effort to rearrange.
Why choose Metal Frame Chairs for casual dining?
Metal frame chairs are lightweight and often come in contemporary designs, making them ideal for casual dining settings, especially outdoors. Their stackable nature allows for easy storage, which is beneficial for businesses with limited space. However, buyers should keep in mind that these chairs may not provide the same level of comfort as upholstered options, and without cushions, they can be less inviting for longer dining experiences.
What are the benefits of Customizable Modular Chairs?
Customizable modular chairs are designed to adapt to various spatial configurations, making them an excellent choice for co-working spaces and flexible dining areas. These chairs can be rearranged to suit different events or layouts, enhancing the functionality of the space. When considering these options, businesses should assess the modularity and ease of reconfiguration, as well as the materials used, which can impact both comfort and durability.
How do Antique Replica Chairs attract niche markets?
Antique replica chairs combine vintage aesthetics with modern construction techniques, appealing to specialty restaurants and boutique hotels seeking unique character. These chairs can create a distinctive atmosphere that attracts customers looking for a memorable dining experience. However, potential buyers should be aware of the limited availability and potentially higher costs associated with bespoke designs, making it crucial to establish a reliable supplier who can meet specific needs.
Related Video: How to Mix and Match Dining Chairs
Key Industrial Applications of dining room chairs custom
Industry/Sector | Specific Application of dining room chairs custom | Value/Benefit for the Business | Key Sourcing Considerations for this Application |
---|---|---|---|
Hospitality | Custom dining chairs for hotels and restaurants | Enhances guest experience and brand identity | Material durability, design aesthetics, and compliance with local regulations |
Corporate Offices | Custom dining chairs for employee dining areas | Promotes employee satisfaction and comfort during meals | Ergonomics, customization options, and bulk order discounts |
Event Planning | Custom dining chairs for weddings and corporate events | Tailored aesthetics to match event themes and branding | Flexibility in design, rental options, and transportation logistics |
Educational Institutions | Custom dining chairs for cafeterias in schools/universities | Supports student comfort and engagement during meals | Safety standards, easy maintenance, and size adaptability |
Residential Projects | Custom dining chairs for luxury homes and apartments | Reflects personal style and enhances home aesthetics | Customization processes, lead times, and delivery logistics |
How Are Custom Dining Chairs Used in the Hospitality Sector?
In the hospitality industry, custom dining chairs are essential for creating a memorable dining experience. Hotels and restaurants often opt for bespoke designs that reflect their brand identity and enhance the overall ambiance. International buyers from regions like Africa and South America may seek materials that withstand local climate conditions, while European buyers might prioritize design trends and sustainability. The ability to customize color, fabric, and style allows businesses to differentiate themselves in a competitive market, ultimately leading to increased customer satisfaction and loyalty.
What Role Do Custom Dining Chairs Play in Corporate Offices?
Corporate offices are increasingly recognizing the importance of employee well-being during meal times. Custom dining chairs can be tailored to fit the ergonomic needs of employees, promoting comfort and encouraging social interaction. For international buyers, especially in the Middle East and Europe, sourcing chairs that align with modern office design while also considering bulk order discounts can be crucial. Additionally, customization options that reflect the company’s branding can enhance the workplace environment, fostering a sense of belonging among employees.
How Are Custom Dining Chairs Utilized in Event Planning?
Event planners often require custom dining chairs to align with the specific themes of weddings and corporate functions. These bespoke chairs not only enhance the aesthetic appeal of an event but also provide comfort for guests. For buyers in regions like Africa and South America, understanding the logistics of transporting these chairs to remote locations is vital. Additionally, flexibility in design and rental options can significantly impact sourcing decisions, allowing planners to create unique experiences that leave lasting impressions.
Why Are Custom Dining Chairs Important for Educational Institutions?
In educational settings, custom dining chairs are essential for cafeterias in schools and universities. These chairs can be designed to cater to the unique needs of students, providing comfort and promoting engagement during meal times. Buyers from Europe and the Middle East may focus on safety standards and ease of maintenance when sourcing these products. Customization also allows institutions to create an inviting atmosphere that can enhance the dining experience and support students’ overall well-being.
How Do Custom Dining Chairs Enhance Residential Projects?
For luxury homes and high-end apartments, custom dining chairs serve as a reflection of personal style and taste. Buyers looking to furnish their residences with unique pieces often prioritize customization options that allow them to select materials, colors, and designs that fit their vision. In Europe and South America, understanding the lead times and delivery logistics associated with custom orders is critical to ensure timely completion of residential projects. Ultimately, these bespoke chairs contribute significantly to the overall aesthetic and functionality of living spaces.
Related Video: SQUARERULE FURNITURE – Making a Dining Chair – Bent Lamination
3 Common User Pain Points for ‘dining room chairs custom’ & Their Solutions
Scenario 1: Sizing Issues in Custom Dining Room Chairs
The Problem: One of the most common challenges faced by B2B buyers, especially those managing restaurants or hotels, is ensuring that custom dining room chairs fit the intended space perfectly. Incorrect sizing can lead to uncomfortable dining experiences and even limit the number of chairs that can be placed around a table. Buyers may struggle with dimensions, especially when adapting to unique layouts or existing furniture.
The Solution: To mitigate sizing issues, it’s crucial to conduct a thorough space analysis before placing an order. Measure the dimensions of the dining area, including the height and width of tables, and ensure that the chair dimensions align with these measurements. Engage with suppliers who offer customizable dimensions and provide detailed specifications for each chair model. Additionally, requesting prototypes or 3D models can help visualize how the chairs will fit in the designated space. It’s also advisable to consider ergonomics; selecting chairs that allow for comfortable movement and spacing will enhance the overall dining experience.
Scenario 2: Material Selection Dilemmas for Custom Dining Chairs
The Problem: Another significant pain point is the confusion surrounding material selection. B2B buyers often find themselves overwhelmed by the variety of upholstery, wood types, and finishes available. The choice of materials is crucial, as it affects not only the aesthetic appeal but also the durability and maintenance of the chairs. In regions with high humidity or varying temperatures, such as parts of Africa and South America, certain materials may perform better than others.
The Solution: To navigate material selection effectively, buyers should conduct research on the performance characteristics of different materials in relation to their specific environment. Collaborating with suppliers who specialize in custom dining chairs can provide insights into the best materials for durability and comfort. Additionally, requesting samples of various materials can help in making informed decisions. Consideration should also be given to maintenance requirements; selecting materials that are easy to clean and maintain will reduce long-term costs. Buyers should inquire about warranties or guarantees on materials to ensure their investment is protected.
Scenario 3: Long Lead Times and Delivery Issues with Custom Orders
The Problem: Delays in delivery and long lead times for custom dining chairs can disrupt business operations, particularly for hotels and restaurants preparing for events or seasonal openings. Buyers may experience frustration when suppliers fail to meet expected timelines, leading to potential financial losses and customer dissatisfaction.
The Solution: To address lead time concerns, B2B buyers should engage in proactive communication with suppliers. Establish clear timelines and expectations at the outset of the order process, and consider negotiating terms for expedited production if needed. It’s also beneficial to work with manufacturers who have a solid reputation for meeting deadlines and can provide realistic timelines based on current workloads. Buyers may also consider maintaining a small inventory of popular chair styles to mitigate delays for future orders. Utilizing a project management tool to track the progress of the order can further ensure that timelines are adhered to and any potential issues are addressed promptly.
Strategic Material Selection Guide for dining room chairs custom
When selecting materials for custom dining room chairs, international B2B buyers must consider various factors that influence performance, durability, and compliance with regional standards. Below, we analyze four common materials used in the production of dining room chairs, focusing on their properties, advantages, disadvantages, and specific considerations for buyers from Africa, South America, the Middle East, and Europe.
What Are the Key Properties of Wood for Custom Dining Room Chairs?
Wood is a traditional choice for dining room chairs, prized for its aesthetic appeal and structural integrity. Key properties include:
- Durability: High-quality hardwoods like oak or walnut can withstand significant wear and tear.
- Temperature Resistance: Wood can expand and contract with temperature changes, which may affect its longevity if not properly treated.
- Corrosion Resistance: While not applicable in the same way as metals, wood is resistant to rust but can be vulnerable to moisture if not sealed.
Pros & Cons: Wood chairs offer timeless elegance and can be customized with various finishes. However, they can be expensive and require more complex manufacturing processes, particularly for intricate designs. Additionally, wood is susceptible to scratches and dents.
Impact on Application: Wood is compatible with various upholstery fabrics, making it versatile for different design aesthetics. However, it may not be suitable for humid environments without proper treatment.
Considerations for International Buyers: Buyers should ensure that the wood complies with local regulations regarding sustainability and sourcing, such as the Forest Stewardship Council (FSC) certification. Preferences may vary by region, with some markets favoring locally sourced materials.
How Does Metal Perform in Custom Dining Room Chair Applications?
Metal, particularly steel or aluminum, is increasingly popular for its modern aesthetic and strength. Key properties include:
- Strength: Metal frames can support heavier weights and resist deformation.
- Corrosion Resistance: Stainless steel is highly resistant to rust, making it suitable for various environments.
- Temperature Resistance: Metals can conduct heat, which may not be comfortable in extreme temperatures without proper padding.
Pros & Cons: Metal chairs are durable and often require less maintenance than wood. However, they can be heavier and may have a higher manufacturing complexity due to welding and finishing processes.
Impact on Application: Metal frames can be paired with various seat materials, including wood or upholstered cushions, enhancing comfort and style.
Considerations for International Buyers: Compliance with standards like ASTM for metal quality is crucial. Additionally, buyers should consider the impact of local climates on metal finishes to prevent corrosion.
What Benefits Do Upholstered Materials Offer for Custom Dining Room Chairs?
Upholstered chairs provide comfort and style, making them a popular choice in dining settings. Key properties include:
- Comfort: Upholstered chairs offer greater comfort due to padding and fabric choices.
- Variety: A wide range of fabrics and colors allows for extensive customization.
- Durability: Quality upholstery fabrics can withstand significant wear but may require proper care to maintain appearance.
Pros & Cons: Upholstered chairs are inviting and can enhance the dining experience. However, they may be more challenging to clean and maintain compared to wooden or metal chairs.
Impact on Application: Upholstered chairs are suitable for both formal and casual dining environments, but fabric choice should consider stain resistance and durability.
Considerations for International Buyers: Buyers should be aware of fabric standards, such as those set by the International Organization for Standardization (ISO), to ensure quality and safety.
How Do Composite Materials Impact Custom Dining Room Chair Design?
Composite materials, such as engineered wood or synthetic plastics, are gaining popularity for their versatility and cost-effectiveness. Key properties include:
- Sustainability: Many composites are made from recycled materials, appealing to eco-conscious buyers.
- Cost-Effectiveness: Generally, composites are less expensive than solid wood or metal.
- Design Flexibility: Composites can be molded into various shapes and sizes, allowing for innovative designs.
Pros & Cons: Composite materials can be lightweight and easy to transport. However, they may not offer the same durability or aesthetic appeal as natural materials.
Impact on Application: Composites can be used in various environments, but their long-term performance may vary based on the quality of the material.
Considerations for International Buyers: Buyers should verify compliance with regional standards for composite materials, particularly regarding emissions and safety.
Summary Table of Material Selection for Custom Dining Room Chairs
Material | Typical Use Case for dining room chairs custom | Key Advantage | Key Disadvantage/Limitation | Relative Cost (Low/Med/High) |
---|---|---|---|---|
Wood | Traditional dining settings | Aesthetic appeal and durability | Higher cost and manufacturing complexity | High |
Metal | Modern and industrial designs | Strength and low maintenance | Heavier and complex manufacturing | Medium |
Upholstered | Casual and formal dining environments | Comfort and extensive customization | Challenging maintenance | Medium |
Composite | Budget-friendly and eco-conscious designs | Cost-effective and lightweight | Potentially lower durability | Low |
This strategic material selection guide provides actionable insights for international B2B buyers, ensuring informed decisions in the procurement of custom dining room chairs tailored to diverse markets.
In-depth Look: Manufacturing Processes and Quality Assurance for dining room chairs custom
What Are the Main Stages in the Manufacturing Process of Custom Dining Room Chairs?
The manufacturing process of custom dining room chairs typically consists of several key stages: material preparation, forming, assembly, and finishing. Understanding these stages is critical for B2B buyers looking to ensure quality and durability in their purchases.
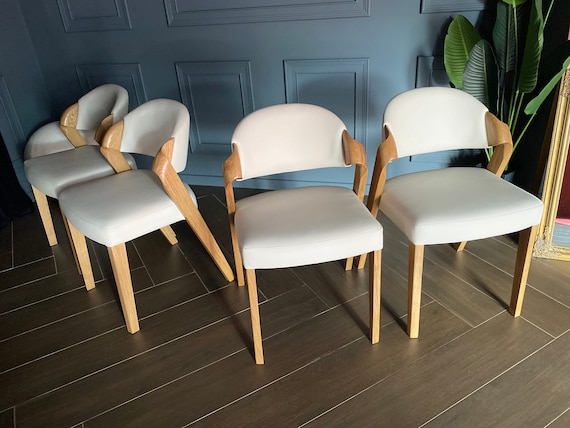
A stock image related to dining room chairs custom.
1. Material Preparation
The first stage involves selecting and preparing the materials, which can include various types of wood, metal, fabric, and foam. Quality of materials is paramount; hardwoods like oak and maple are preferred for their durability and aesthetic appeal.
- Key Techniques:
- Sourcing: Establish relationships with trusted suppliers for sustainable materials, which is increasingly important for international buyers concerned about environmental impact.
- Quality Checks: Inspect raw materials for defects, moisture content, and consistency in color and grain before proceeding.
2. Forming
Once materials are prepared, they undergo forming, where they are shaped into the components of the chair. This involves cutting, molding, or bending materials to achieve the desired design.
- Key Techniques:
- CNC Machining: This computer-controlled cutting technique ensures precision in creating chair parts, reducing waste and improving design accuracy.
- Upholstery Preparation: For upholstered chairs, the foam and fabric are cut to size and prepared for assembly. The choice of upholstery can significantly affect the chair’s comfort and durability.
3. Assembly
In the assembly phase, the various components are brought together to form the final product. This stage requires skilled craftsmanship to ensure that everything fits together properly.
- Key Techniques:
- Joinery Methods: Techniques such as mortise and tenon, doweling, or modern adhesives are used to join parts. Strong joints are crucial for long-lasting furniture.
- Quality Control: Throughout assembly, continuous checks are performed to ensure that each piece meets the design specifications and quality standards.
4. Finishing
The final stage is finishing, where the chair is sanded, stained, painted, or upholstered. This not only enhances the appearance but also protects the materials from wear and tear.
- Key Techniques:
- Surface Treatment: Applying finishes such as varnish or lacquer helps protect against moisture and damage.
- Final Upholstery: For upholstered chairs, the final fabric is applied, ensuring that it is taut and free of wrinkles.
What Quality Assurance Measures Are Necessary for Custom Dining Room Chairs?
Quality assurance (QA) is essential in the manufacturing of custom dining room chairs to meet international standards and customer expectations. B2B buyers must be aware of the various QA measures that can ensure product reliability.
Relevant International Standards: What Should Buyers Know?
The International Organization for Standardization (ISO) provides guidelines such as ISO 9001, which pertains to quality management systems. This certification assures buyers that manufacturers adhere to quality processes. Additionally, industry-specific certifications like CE for safety in Europe or API for materials used in certain applications may also be relevant.
What Are the Key Quality Control Checkpoints?
Quality control (QC) checkpoints include:
- Incoming Quality Control (IQC): Inspecting materials upon arrival to ensure they meet specifications.
- In-Process Quality Control (IPQC): Monitoring production processes at various stages to catch defects early.
- Final Quality Control (FQC): Conducting a thorough inspection of finished products before shipping to ensure they meet design and quality standards.
How Can B2B Buyers Verify Supplier Quality Control?
Verifying a supplier’s quality control processes is crucial for B2B buyers, particularly those from diverse markets like Africa, South America, the Middle East, and Europe. Here are actionable steps:
1. Conduct Supplier Audits
Regular audits can help assess a supplier’s compliance with quality standards. Buyers should inquire about the frequency and scope of these audits.
2. Request Quality Reports
Buyers can ask suppliers for detailed quality reports, including defect rates, inspection results, and corrective actions taken for any issues identified.
3. Engage Third-Party Inspectors
Utilizing third-party inspection services can provide an unbiased review of the manufacturing processes and final products. This is particularly beneficial for buyers unfamiliar with local suppliers.
What Are Common Testing Methods for Quality Assurance?
Testing methods play a vital role in ensuring that custom dining room chairs meet durability and safety standards. Common testing methods include:
- Load Testing: Chairs are subjected to weight tests to ensure they can support the expected load without structural failure.
- Durability Testing: This involves simulating years of use to assess the wear and tear of materials.
- Safety Testing: Ensuring that the chair complies with safety regulations, such as stability and absence of sharp edges.
What Quality Control Nuances Should International Buyers Be Aware Of?
International buyers must consider regional differences in quality standards and customer expectations. For instance, European markets may have stricter regulations regarding material safety and environmental impact compared to those in Africa or South America.
- Cultural Preferences: Buyers should also be aware of local design preferences, which can impact the choice of materials and finishes.
- Regulatory Compliance: Understanding local regulations regarding imports and product certifications can prevent delays and additional costs.
By navigating these manufacturing processes and quality assurance measures effectively, international B2B buyers can make informed decisions when sourcing custom dining room chairs. Ensuring quality at every step not only enhances customer satisfaction but also builds long-term partnerships with suppliers.
Practical Sourcing Guide: A Step-by-Step Checklist for ‘dining room chairs custom’
To assist international B2B buyers in sourcing custom dining room chairs effectively, this step-by-step guide outlines essential actions to ensure a successful procurement process. Each step is designed to help you navigate the complexities of customization while ensuring quality and suitability for your needs.
Step 1: Define Your Technical Specifications
Start by clearly outlining what you need in terms of design, materials, and dimensions. This step is crucial to communicate your requirements effectively to suppliers. Consider the following:
– Design Style: Traditional, modern, or bespoke?
– Materials: Wood types, upholstery fabrics, and finishes.
– Dimensions: Ensure measurements fit your dining space.
Step 2: Research Potential Suppliers
Conduct thorough research to identify suppliers that specialize in custom dining chairs. Utilize online platforms, industry forums, and trade shows to find reputable manufacturers. Look for:
– Industry Experience: Suppliers with a proven track record in custom furniture.
– Client Reviews: Testimonials and case studies to gauge reliability and quality.
Step 3: Evaluate Supplier Capabilities
Before committing, assess each supplier’s ability to meet your specifications. Request detailed information about their production processes and customization options. Pay attention to:
– Manufacturing Techniques: Are they using modern technology or traditional craftsmanship?
– Customization Flexibility: Can they accommodate specific requests without compromising quality?
Step 4: Request Samples and Prototypes
Always ask for samples of materials and prototypes of designs before placing a bulk order. This step allows you to evaluate quality firsthand and make necessary adjustments. Consider:
– Material Quality: Check durability and finish.
– Comfort and Ergonomics: Ensure the chairs are comfortable for extended use.
Step 5: Verify Supplier Certifications and Compliance
Ensure that your chosen suppliers adhere to industry standards and regulations. This is particularly important for international sourcing to avoid legal issues. Look for:
– Quality Certifications: ISO, CE, or other relevant certifications.
– Sustainability Practices: Suppliers that prioritize eco-friendly materials and processes.
Step 6: Negotiate Terms and Conditions
Once you’ve selected a supplier, negotiate the terms of your order, including pricing, delivery timelines, and payment options. Clear agreements help avoid misunderstandings. Focus on:
– Payment Terms: Upfront payments vs. payment on delivery.
– Lead Times: Understand the time frame from order to delivery.
Step 7: Establish a Communication Plan
Effective communication is vital throughout the sourcing process. Set up a clear plan for regular updates and feedback. Consider:
– Point of Contact: Designate a representative from both sides for streamlined communication.
– Progress Updates: Schedule regular check-ins to monitor the production status.
By following these steps, B2B buyers can navigate the complexities of sourcing custom dining room chairs with confidence, ensuring they receive products that meet their specific needs and quality standards.
Comprehensive Cost and Pricing Analysis for dining room chairs custom Sourcing
What Are the Key Cost Components for Custom Dining Room Chairs?
When sourcing custom dining room chairs, understanding the cost structure is essential for B2B buyers. The main components influencing the overall price include:
-
Materials: The choice of materials significantly impacts the cost. High-quality hardwoods, metals, or eco-friendly materials will typically command higher prices. Fabrics for upholstery also vary in cost based on durability and design.
-
Labor: Custom manufacturing often involves skilled craftsmanship, which can increase labor costs. Artisans may charge more for intricate designs or specialized finishes.
-
Manufacturing Overhead: This includes expenses related to factory operations, such as utilities, equipment maintenance, and administrative costs. Overhead can vary significantly based on the production scale and location.
-
Tooling: Custom designs often require specific tools and molds, which can add to initial costs. Buyers should inquire about tooling fees, particularly for unique designs.
-
Quality Control (QC): Ensuring that each chair meets quality standards requires investment in inspection processes. Higher QC standards can lead to increased costs but ensure better product reliability.
-
Logistics: Shipping costs can be substantial, especially for international orders. Consideration of freight, customs duties, and insurance is crucial for the total cost.
-
Margin: Manufacturers typically include a profit margin, which can vary based on their business model and market conditions.
How Do Price Influencers Affect Custom Dining Room Chair Costs?
Several factors influence the pricing of custom dining room chairs, which B2B buyers must consider:
-
Volume/MOQ (Minimum Order Quantity): Higher order volumes often result in lower per-unit costs. Suppliers may offer tiered pricing based on order size, making it beneficial for buyers to consolidate orders.
-
Specifications and Customization: The level of customization requested can significantly affect pricing. Unique designs or modifications often incur additional charges.
-
Material Quality and Certifications: Chairs made from certified sustainable materials or those that comply with specific safety standards may cost more. Buyers should assess if these certifications are necessary for their market.
-
Supplier Factors: Supplier reputation, location, and reliability can impact pricing. Established suppliers may charge more due to their experience and quality assurance processes.
-
Incoterms: Understanding the agreed Incoterms (International Commercial Terms) is vital, as they define responsibilities for shipping, insurance, and tariffs, ultimately influencing the final price.
What Buyer Tips Should International B2B Buyers Consider?
For international B2B buyers, particularly from regions like Africa, South America, the Middle East, and Europe, here are some actionable tips:
-
Negotiate Wisely: Engage in price negotiations with suppliers, especially for large orders. Building a relationship can lead to better deals and flexibility in pricing.
-
Focus on Cost-Efficiency: Evaluate the Total Cost of Ownership (TCO), which includes acquisition costs, maintenance, and expected lifespan. A lower initial price may not always equate to long-term savings.
-
Understand Pricing Nuances: Be aware that pricing structures can vary by region due to local economic conditions, labor costs, and material availability. Researching local market trends can provide leverage in negotiations.
-
Request Detailed Quotes: Ensure that suppliers provide comprehensive quotes that break down all cost components. This transparency helps in comparing offers and identifying potential hidden costs.
-
Consider Logistics and Lead Times: Factor in logistics costs and delivery timelines when comparing suppliers. Delays in shipping can lead to increased costs and impact your business operations.
Disclaimer on Indicative Prices
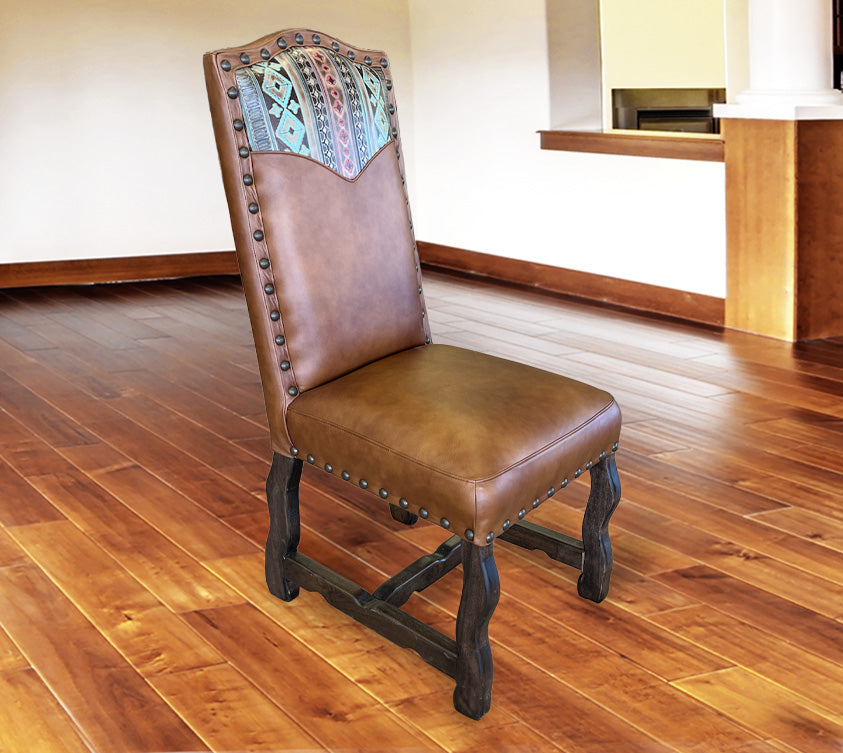
A stock image related to dining room chairs custom.
Prices for custom dining room chairs can vary widely based on the factors outlined above. It is advisable for buyers to seek multiple quotes and conduct thorough market research to ensure they receive competitive pricing that aligns with their specific needs.
Alternatives Analysis: Comparing dining room chairs custom With Other Solutions
Introduction: What Are the Alternatives to Custom Dining Room Chairs?
When considering dining room chairs for a business setting, custom options often stand out due to their tailored design and potential for enhanced branding. However, various alternatives can provide similar functionality and aesthetic appeal. This section explores how custom dining room chairs compare to pre-manufactured furniture and ergonomic chair solutions, helping international B2B buyers make informed decisions that align with their specific needs.
Comparison Table of Dining Room Chair Solutions
Comparison Aspect | Dining Room Chairs Custom | Pre-Manufactured Chairs | Ergonomic Dining Chairs |
---|---|---|---|
Performance | High durability and tailored comfort | Moderate durability, design options vary | Designed for comfort, but may lack style |
Cost | Higher initial investment; long-term value | Lower upfront costs; less customization | Mid-range pricing; varies by brand |
Ease of Implementation | Longer lead time; requires planning | Quick delivery and setup | Moderate setup time; requires space consideration |
Maintenance | Requires periodic upkeep depending on materials | Generally low maintenance | Low maintenance with easy-to-clean surfaces |
Best Use Case | High-end restaurants, bespoke venues | Budget-conscious businesses, uniform settings | Health-focused environments, frequent dining |
Detailed Breakdown of Alternatives
What Are Pre-Manufactured Chairs?
Pre-manufactured chairs are mass-produced options that come in various styles and finishes. They are typically available at lower price points compared to custom chairs, making them an attractive option for budget-conscious businesses. The primary advantage of pre-manufactured chairs is their quick availability and ease of implementation. However, they may not provide the same level of durability or unique design that custom options offer, potentially limiting the branding experience.
How Do Ergonomic Dining Chairs Compare?
Ergonomic dining chairs focus on providing comfort and support, often incorporating features like lumbar support and adjustable heights. These chairs are particularly beneficial in environments where patrons may spend extended periods sitting, such as corporate dining facilities or long business meetings. While ergonomic chairs can be stylish, they may sacrifice some aesthetic appeal in favor of functionality. Additionally, they typically fall within a mid-range price point, making them accessible without the high investment required for custom options.
Conclusion: How Should B2B Buyers Choose the Right Dining Room Chair Solution?
When selecting the ideal dining room chair solution, B2B buyers must consider their specific use cases, budget constraints, and desired aesthetic. Custom dining room chairs offer unmatched personalization and durability, making them suitable for high-end venues. On the other hand, pre-manufactured options provide a cost-effective and quick solution for businesses prioritizing budget over uniqueness. Ergonomic chairs serve a niche market where comfort is paramount. By evaluating these alternatives against their unique business needs, buyers can make an informed decision that enhances both functionality and brand image in their dining spaces.
Essential Technical Properties and Trade Terminology for dining room chairs custom
What Are the Key Technical Properties of Custom Dining Room Chairs?
Understanding the technical properties of custom dining room chairs is essential for B2B buyers to ensure they are making informed purchasing decisions. Here are some critical specifications to consider:
1. Material Grade: What Should You Look For?
The material used in dining room chairs can significantly impact durability, aesthetics, and comfort. Common materials include hardwoods like oak and walnut, softwoods like pine, and engineered materials like plywood or MDF. High-grade materials not only enhance the chair’s longevity but also its resistance to wear and tear, making them ideal for commercial settings. Always inquire about the material grade to ensure it meets your specific needs.
2. Tolerance: How Does It Affect Fit and Functionality?
Tolerance refers to the allowable deviation from specified dimensions in the manufacturing process. For custom dining chairs, precise tolerances are crucial to ensure that all components fit together correctly. Poor tolerance can lead to instability or discomfort for users. When ordering, specify your tolerance requirements to avoid quality issues.
3. Upholstery Options: Which Fabrics Are Best?
Upholstery plays a vital role in both comfort and style. Fabrics can vary from natural fibers like cotton and linen to synthetic options like polyester and vinyl. Each fabric type has its own durability rating and maintenance requirements. For high-traffic areas, consider stain-resistant or easy-to-clean fabrics. Discuss upholstery options with suppliers to find the best fit for your target market.
4. Weight Capacity: What Is the Recommended Limit?
Understanding the weight capacity of dining room chairs is essential, especially for commercial environments. Most chairs are designed to support a standard weight of around 250-300 pounds, but custom options can be made to accommodate higher weights. Make sure to specify your weight requirements to manufacturers to ensure safety and functionality.
5. Finish and Coating: How Important Are They?
The finish applied to dining room chairs not only affects the appearance but also protects the material from scratches, moisture, and UV damage. Common finishes include lacquer, varnish, and oil. Discuss the finish options with your supplier to ensure that they align with your aesthetic preferences and maintenance capabilities.
What Are Common Trade Terms Related to Custom Dining Room Chairs?
Familiarizing yourself with industry jargon can facilitate smoother transactions and negotiations. Here are some key trade terms to know:
1. OEM (Original Equipment Manufacturer): Why Is It Relevant?
OEM refers to companies that produce parts or products that are used in another company’s end product. In the context of custom dining chairs, OEM manufacturers can create chairs designed to the specifications of your brand. This term is crucial when looking for suppliers who can deliver tailored solutions.
2. MOQ (Minimum Order Quantity): What Does It Mean for Your Orders?
MOQ denotes the smallest quantity of products that a supplier is willing to sell. Understanding the MOQ is essential for budgeting and inventory management. Custom dining chairs may have higher MOQs due to the bespoke nature of production, so clarify this with suppliers early in the negotiation process.
3. RFQ (Request for Quotation): How Do You Use It?
An RFQ is a document sent to suppliers to request pricing and terms for specific products. For custom dining chairs, an RFQ should include detailed specifications, desired materials, and any customization options. Utilizing RFQs can help you gather competitive pricing and streamline the procurement process.
4. Incoterms: What Are They and Why Do They Matter?
Incoterms are international commercial terms that define the responsibilities of buyers and sellers in a transaction. These terms clarify who is responsible for shipping, insurance, and tariffs. Understanding Incoterms is vital for international buyers, as they can significantly affect the overall cost and logistics of importing custom dining chairs.
5. Lead Time: Why Is It Critical for Custom Orders?
Lead time refers to the amount of time required to manufacture and deliver products after an order is placed. For custom dining chairs, lead times can vary based on complexity and materials. Knowing the lead time helps you plan your inventory and meet customer demand effectively.
By grasping these technical properties and trade terms, B2B buyers can make well-informed decisions when sourcing custom dining room chairs, ensuring that they meet both quality standards and market demands.
Navigating Market Dynamics and Sourcing Trends in the dining room chairs custom Sector
What Are the Current Market Dynamics and Sourcing Trends in the Custom Dining Chairs Sector?
The custom dining chairs market is witnessing significant evolution driven by global consumer preferences and technological advancements. International B2B buyers, particularly those from Africa, South America, the Middle East, and Europe, are increasingly seeking personalized products that align with their unique cultural aesthetics and functional needs. Notably, the rise of e-commerce platforms has facilitated easier access to suppliers from diverse regions, enabling buyers to compare prices and designs effortlessly.
Emerging trends such as augmented reality (AR) are transforming how buyers visualize products before purchase. This technology allows potential buyers to see how a specific chair would fit into their existing space, enhancing the decision-making process. Additionally, the growing trend towards multifunctional furniture is reshaping designs, with custom dining chairs now often incorporating storage solutions or convertible features, appealing to urban consumers facing space constraints.
As sustainability becomes a priority, buyers are increasingly favoring suppliers who adopt eco-friendly practices. This includes sourcing responsibly harvested wood and using low-impact materials in upholstery. Furthermore, the demand for quick turnaround times without compromising on quality is pushing manufacturers to adopt lean production techniques, ensuring they can meet the fast-paced demands of the global market.
How Are Sustainability and Ethical Sourcing Shaping the Custom Dining Chairs Market?
Sustainability and ethical sourcing are at the forefront of the custom dining chairs market, reflecting a broader shift in consumer consciousness. Buyers are increasingly aware of the environmental impact of their purchasing decisions. As a result, they are actively seeking suppliers who can demonstrate commitment to sustainable practices. This includes using certified sustainable wood, such as FSC (Forest Stewardship Council) certified materials, which ensures that the wood is sourced responsibly.
In addition to materials, the importance of ethical supply chains cannot be overstated. Buyers are more inclined to partner with manufacturers who uphold fair labor practices and transparency in their sourcing processes. Certifications such as Fair Trade can serve as indicators of a supplier’s commitment to ethical practices.
Moreover, the use of ‘green’ materials—such as organic fabrics and non-toxic finishes—has become a significant selling point. Companies that embrace sustainable practices not only reduce their environmental footprint but also appeal to a growing segment of eco-conscious buyers. As such, integrating sustainability into the sourcing strategy is not just a trend but a necessity for staying competitive in the global market.
How Has the Custom Dining Chairs Market Evolved Over Time?
The custom dining chairs market has evolved significantly over the last few decades, transitioning from traditional craftsmanship to modern, technology-driven production methods. Historically, custom furniture was primarily associated with high-end artisanship, where bespoke pieces were handcrafted for individual clients. This made custom dining chairs a luxury, often limited to affluent markets.
However, with advancements in manufacturing technology and the rise of digital design tools, the accessibility of custom dining chairs has broadened. Manufacturers can now produce high-quality custom pieces at scale, allowing for a wider range of styles and affordability. This evolution has led to a democratization of design, where consumers from various economic backgrounds can access tailored furniture solutions.
The integration of online platforms has further accelerated this shift, enabling consumers from diverse regions to explore and purchase custom dining chairs without geographical limitations. As the market continues to evolve, embracing both tradition and innovation will be crucial for suppliers aiming to meet the diverse needs of international B2B buyers.
Frequently Asked Questions (FAQs) for B2B Buyers of dining room chairs custom
-
How do I choose the right custom dining chairs for my business needs?
Choosing the right custom dining chairs involves assessing your target market, the intended use, and the aesthetic you want to convey. Consider factors such as durability, material, and comfort, especially if the chairs will be used in a high-traffic area. Collaborate with suppliers who offer customization options to meet specific design requirements. Request samples to evaluate quality and comfort before making bulk purchases. -
What are the common customization options available for dining room chairs?
Common customization options for dining room chairs include fabric selection, color choices, dimensions, and design features such as armrests or leg styles. Many manufacturers also offer bespoke services where you can design a chair from scratch. Pay attention to the upholstery materials, as they can significantly affect comfort and durability. Always request a prototype or mock-up before finalizing your order. -
What is the minimum order quantity (MOQ) for custom dining chairs?
Minimum order quantities (MOQs) for custom dining chairs vary by supplier and can range from a few pieces to hundreds. It’s essential to discuss your requirements with potential suppliers to understand their MOQ policies. Some manufacturers may be flexible with smaller orders, especially if you are willing to pay a higher per-unit cost. Always confirm the MOQ before proceeding with negotiations to avoid unexpected costs. -
What payment terms should I expect when sourcing custom dining chairs internationally?
Payment terms for international orders can differ widely among suppliers. Common practices include a deposit upon order confirmation (usually 30-50%) and the balance due before shipment. Some suppliers may offer letter of credit options for larger orders, providing added security. Always clarify payment terms in advance and consider using an escrow service for large transactions to mitigate risk. -
How do I vet suppliers for custom dining chairs?
Vetting suppliers involves researching their reputation, experience, and production capabilities. Look for reviews, testimonials, and case studies from previous clients. Request references and verify their business credentials. Additionally, consider visiting their manufacturing facility if possible, or request a video tour. Conducting a small trial order can also help assess quality and reliability before committing to larger orders. -
What quality assurance measures should I consider for custom dining chairs?
Implementing quality assurance measures is crucial to ensure the chairs meet your specifications and industry standards. Request detailed information on the materials used and the manufacturing process. Establish clear quality benchmarks and conduct inspections at various stages of production. Consider hiring third-party quality control services to perform on-site inspections before shipment to minimize defects and returns. -
What logistics considerations should I keep in mind when importing dining chairs?
When importing dining chairs, consider shipping costs, lead times, and customs regulations specific to your country. Ensure that the supplier can provide necessary documentation for customs clearance, such as invoices and certificates of origin. Factor in warehousing and distribution logistics, particularly if you plan to sell in multiple regions. Collaborating with a reliable freight forwarder can streamline the shipping process and mitigate potential delays. -
How can I ensure that my custom dining chairs comply with international safety standards?
To ensure compliance with international safety standards, familiarize yourself with the regulations applicable to your target markets. Communicate these requirements to your supplier, ensuring they use compliant materials and processes. Request certifications or test results from recognized laboratories that verify the safety and durability of the chairs. Regular audits and inspections can also help maintain compliance throughout the production process.
Important Disclaimer & Terms of Use
⚠️ Important Disclaimer
The information provided in this guide, including content regarding manufacturers, technical specifications, and market analysis, is for informational and educational purposes only. It does not constitute professional procurement advice, financial advice, or legal advice.
While we have made every effort to ensure the accuracy and timeliness of the information, we are not responsible for any errors, omissions, or outdated information. Market conditions, company details, and technical standards are subject to change.
B2B buyers must conduct their own independent and thorough due diligence before making any purchasing decisions. This includes contacting suppliers directly, verifying certifications, requesting samples, and seeking professional consultation. The risk of relying on any information in this guide is borne solely by the reader.
Strategic Sourcing Conclusion and Outlook for dining room chairs custom
As the custom dining chair market continues to expand, the importance of strategic sourcing cannot be overstated. International B2B buyers from Africa, South America, the Middle East, and Europe must prioritize a deep understanding of their suppliers’ capabilities, production processes, and customization options. This insight will enable them to select partners that align with their unique design requirements and quality standards.
What are the key benefits of strategic sourcing in this sector? Firstly, it allows buyers to tap into global craftsmanship, ensuring that they receive not only aesthetically pleasing but also durable and functional products. Secondly, effective sourcing practices can lead to cost efficiencies, especially when ordering in bulk or negotiating favorable terms with manufacturers. Lastly, the ability to customize dining chairs opens up opportunities for differentiation in competitive markets, catering to specific consumer preferences.
Looking forward, the demand for bespoke dining solutions will only grow. Buyers are encouraged to engage with manufacturers who are transparent about their processes and open to collaboration. By investing in strategic sourcing now, you can position your business to thrive in the evolving landscape of custom dining furniture. Don’t miss out—start exploring potential partnerships today to elevate your product offerings!