Discover Top Inverter Manufacturers: Your Ultimate Guide (2025)
Introduction: Navigating the Global Market for inverter manufacturer
In today’s rapidly evolving energy landscape, sourcing reliable inverter manufacturers is crucial for businesses aiming to optimize their energy management systems. Whether you are an international buyer in Africa, South America, the Middle East, or Europe, understanding the nuances of inverter technology can significantly impact your operational efficiency and cost-effectiveness. This comprehensive guide delves into the various types of inverters available, their applications across different industries, and the key factors to consider when vetting suppliers.
Navigating the global market for inverters can be daunting, especially given the diversity of manufacturers and technologies available. This guide will equip you with actionable insights into the best practices for evaluating suppliers, assessing pricing structures, and understanding the technological specifications that best suit your business needs. We will explore the critical considerations for making informed purchasing decisions, including regulatory compliance, warranty terms, and service support, tailored specifically for buyers in regions like Saudi Arabia and Italy.
By arming yourself with the knowledge contained in this guide, you can streamline your procurement process and ensure that you are partnering with manufacturers who not only meet your technical specifications but also align with your strategic business goals. Empower yourself to make confident decisions in the global inverter market and enhance your organization’s energy efficiency and sustainability.
Understanding inverter manufacturer Types and Variations
Type Name | Key Distinguishing Features | Primary B2B Applications | Brief Pros & Cons for Buyers |
---|---|---|---|
String Inverters | Compact, cost-effective, suitable for small to medium systems | Residential solar, small commercial setups | Pros: Lower cost, easy installation. Cons: Limited scalability, less efficient in shading. |
Central Inverters | High capacity, designed for large-scale installations | Utility-scale solar farms | Pros: High efficiency, centralized management. Cons: Higher initial investment, complex maintenance. |
Microinverters | Individual unit per solar panel, optimized performance | Residential solar, complex roof layouts | Pros: Maximized energy production, better performance in shading. Cons: Higher cost per watt, more components to manage. |
Hybrid Inverters | Combines solar and battery storage capabilities | Off-grid systems, energy storage solutions | Pros: Flexibility, energy independence. Cons: Higher complexity, potential compatibility issues. |
Grid-Tie Inverters | Designed for connection to the utility grid | Commercial and residential solar installations | Pros: Net metering benefits, easy integration. Cons: Dependent on grid availability, potential regulatory challenges. |
What Are String Inverters and Their B2B Suitability?
String inverters are popular for their compact design and cost-effectiveness, making them ideal for residential solar systems and small commercial setups. They convert direct current (DC) from solar panels into alternating current (AC) for use in homes or businesses. When considering string inverters, buyers should assess the scale of their project, as they are best suited for installations without significant shading issues. Their lower upfront costs can be appealing, but buyers should weigh this against their limited scalability.
How Do Central Inverters Operate in Large-Scale Applications?
Central inverters are tailored for utility-scale solar farms, offering high capacity and centralized management. They convert DC electricity from multiple solar panels into AC and are known for their efficiency in large installations. B2B buyers should consider central inverters if they are managing large-scale projects, as they can reduce overall installation costs and improve energy output. However, the higher initial investment and complexity of maintenance may deter some buyers.
Why Choose Microinverters for Complex Installations?
Microinverters are installed on each solar panel, allowing for optimized performance and energy production, particularly in shaded environments. They are ideal for residential solar systems with complex roof layouts. B2B buyers should consider microinverters if maximizing energy output is critical, especially in locations prone to shading. Despite their higher cost per watt and increased number of components, the benefits of enhanced performance can justify the investment.
What Are the Advantages of Hybrid Inverters for Energy Independence?
Hybrid inverters are versatile devices that integrate solar energy generation with battery storage, providing significant flexibility in energy use. They are particularly beneficial for off-grid systems and energy storage solutions. B2B buyers looking for energy independence should consider hybrid inverters, as they allow for energy management during peak demand and outages. However, the complexity of these systems and potential compatibility issues with existing setups may pose challenges.
When Should You Consider Grid-Tie Inverters?
Grid-tie inverters are designed for installations that connect to the utility grid, making them suitable for both commercial and residential solar projects. These inverters allow users to benefit from net metering, where excess energy can be sold back to the grid. B2B buyers should consider grid-tie inverters if they are looking to maximize financial returns on their solar investments. However, reliance on the grid and potential regulatory challenges can affect the overall viability of these systems in certain regions.
Related Video: Installation layout of my Deye 8kVA hybrid inverter
Key Industrial Applications of inverter manufacturer
Industry/Sector | Specific Application of inverter manufacturer | Value/Benefit for the Business | Key Sourcing Considerations for this Application |
---|---|---|---|
Renewable Energy | Solar Power Inverters | Efficient conversion of solar energy to electricity, reducing energy costs and increasing sustainability. | Compatibility with solar panels, efficiency ratings, and local regulations. |
Industrial Automation | Variable Frequency Drives (VFDs) | Enhanced control of motor speeds, leading to reduced energy consumption and improved operational efficiency. | Motor compatibility, control interface requirements, and maintenance support. |
Electric Vehicles (EV) | EV Charging Inverters | Faster charging solutions that improve customer satisfaction and reduce downtime for EVs. | Charging speed, compatibility with various EV models, and compliance with local standards. |
Telecommunications | DC-AC Inverters for Data Centers | Reliable power supply ensures uninterrupted service and data integrity, minimizing operational risks. | Load capacity, redundancy features, and energy efficiency. |
HVAC Systems | Inverters for HVAC Applications | Improved energy efficiency and precise temperature control, leading to lower operational costs. | Compatibility with existing HVAC systems, control protocols, and local climate considerations. |
How Are Inverters Used in Renewable Energy Applications?
In the renewable energy sector, particularly solar energy, inverters play a critical role by converting the direct current (DC) generated by solar panels into alternating current (AC) used in homes and businesses. This conversion is essential for integrating renewable energy into the grid, providing a sustainable energy source that reduces reliance on fossil fuels. International buyers, especially from regions like Africa and South America, should consider the inverter’s efficiency ratings and compatibility with local solar technologies to optimize energy production.
What Role Do Inverters Play in Industrial Automation?
In industrial automation, Variable Frequency Drives (VFDs) utilize inverters to control the speed and torque of electric motors. This capability not only enhances operational efficiency but also leads to significant energy savings. Businesses in sectors like manufacturing and mining can benefit from reduced wear and tear on machinery, extending equipment lifespan. B2B buyers should assess the compatibility of inverters with existing motor systems and consider the level of technical support offered by manufacturers.
How Are Inverters Essential for Electric Vehicle Charging?
For the electric vehicle (EV) sector, inverters are vital in charging stations, converting AC power from the grid into the DC power that EVs require. The efficiency and speed of these inverters can significantly affect the charging time, thus impacting customer satisfaction. Companies in regions like the Middle East and Europe, where EV adoption is rapidly growing, must ensure that the inverters meet local charging standards and are compatible with a variety of EV models.
Why Are Inverters Important for Telecommunications?
In telecommunications, DC-AC inverters are crucial for data centers, providing a reliable power supply that safeguards against outages. The uninterrupted power ensures data integrity and maintains operational continuity, which is essential for service providers. Buyers in this sector should focus on inverters with high load capacities and features that enhance redundancy to mitigate risks associated with power failures.
How Do Inverters Enhance HVAC Systems?
In HVAC applications, inverters help regulate the speed of compressors and fans, leading to optimized energy consumption and enhanced temperature control. This technology is particularly beneficial in regions with extreme weather conditions, as it allows for precise climate management. For international buyers, it is important to ensure that inverters are compatible with existing HVAC systems and can adapt to local climate demands, which can vary significantly across regions like Europe and Africa.
Related Video: How to use butoon control speed how to set Frecon VFD VSD frequency inverter ac drive
3 Common User Pain Points for ‘inverter manufacturer’ & Their Solutions
Scenario 1: Sourcing Quality Inverters for Diverse Applications
The Problem: International B2B buyers, especially those in regions like Africa and South America, often face the challenge of sourcing high-quality inverters that meet specific technical requirements for various applications, such as renewable energy systems, industrial automation, or residential installations. With a saturated market filled with numerous manufacturers, distinguishing between reliable and subpar products can be daunting. Additionally, buyers may encounter issues with product compatibility, leading to operational inefficiencies and potential financial losses.
The Solution: To overcome this challenge, buyers should adopt a structured approach to sourcing inverters. Start by clearly defining your application requirements, such as power output, efficiency ratings, and compatibility with existing systems. Utilize resources like industry forums, technical specifications, and product reviews to create a shortlist of reputable manufacturers. Engaging in direct conversations with manufacturers can also help clarify technical details and assess their responsiveness to inquiries. Finally, consider requesting samples or pilot installations to evaluate the product’s performance in real-world conditions before committing to large orders.
Scenario 2: Navigating Warranty and Support Issues
The Problem: Another common pain point for B2B buyers in the inverter market is the complexity surrounding warranty terms and after-sales support. Buyers often find it challenging to navigate warranty policies, leading to confusion over coverage limits, repair timelines, and service availability. This issue is particularly critical in regions with limited access to technical support, where downtime can significantly impact business operations.
The Solution: To mitigate these risks, it is essential to thoroughly review warranty terms before making a purchase. Engage directly with manufacturers to discuss their warranty policies and after-sales support options. Ask specific questions regarding response times for repairs, availability of replacement parts, and whether technical support can be accessed remotely. Additionally, consider establishing a service-level agreement (SLA) that clearly outlines support expectations. Investing in training for your team on inverter operation and maintenance can also empower them to troubleshoot minor issues, reducing reliance on external support and enhancing overall system reliability.
Scenario 3: Understanding the Impact of Local Regulations and Standards
The Problem: B2B buyers operating in diverse regions such as the Middle East and Europe often face challenges related to local regulations and standards that govern inverter installation and operation. Compliance with these regulations is crucial; failing to adhere can result in legal penalties, project delays, and increased costs. However, keeping up with ever-changing regulatory landscapes can be overwhelming for buyers who are not well-versed in local laws.
The Solution: To effectively navigate this challenge, buyers should proactively research and stay informed about local regulations that affect inverter use in their specific industry. Collaborating with local industry associations or consultants who specialize in energy regulations can provide valuable insights into compliance requirements. Additionally, it is beneficial to choose manufacturers that have a strong track record of compliance with international and local standards. Request certifications and documentation from manufacturers that verify their products meet the necessary regulations. This due diligence not only helps avoid legal issues but also ensures that the inverters used are safe, efficient, and reliable in their operational context.
Strategic Material Selection Guide for inverter manufacturer
What Are the Common Materials Used in Inverter Manufacturing?
Inverter manufacturers must carefully select materials that will ensure optimal performance, durability, and compliance with international standards. Below, we analyze four common materials used in the production of inverters, focusing on their properties, advantages, disadvantages, and specific considerations for international B2B buyers.
How Does Aluminum Contribute to Inverter Performance?
Key Properties:
Aluminum is renowned for its lightweight nature and excellent thermal conductivity, making it ideal for heat dissipation in inverters. It typically withstands temperatures up to 150°C and exhibits good corrosion resistance, especially when anodized.
Pros & Cons:
The primary advantage of aluminum is its low weight, which facilitates easier handling and installation. However, it can be more expensive than other metals like steel, and its mechanical strength is lower, which may limit its use in high-stress applications.
Impact on Application:
Aluminum’s excellent thermal properties make it suitable for applications requiring efficient heat management. However, buyers should consider its compatibility with specific environmental conditions, particularly in humid or saline environments common in coastal regions.
Considerations for International Buyers:
Aluminum components must comply with international standards such as ASTM B221 for extruded aluminum and DIN 1725 for aluminum alloys. Buyers in regions like the Middle East and Africa should ensure that suppliers can meet these standards to avoid issues with product reliability.
What Role Does Copper Play in Inverter Manufacturing?
Key Properties:
Copper is known for its outstanding electrical conductivity, with a conductivity rating of 97% IACS (International Annealed Copper Standard). It can handle high temperatures and has good corrosion resistance, especially when coated.
Pros & Cons:
The main advantage of copper is its superior electrical performance, which enhances inverter efficiency. However, it is relatively expensive compared to alternatives like aluminum and can be heavier, which may impact the overall design.
Impact on Application:
Copper is critical in applications requiring high electrical performance, such as power inverters for renewable energy systems. Its compatibility with various media makes it a versatile choice for different inverter designs.
Considerations for International Buyers:
Copper components must adhere to standards such as ASTM B3 for bare copper wire and JIS H 3100 for copper alloys. Buyers from Europe and South America should verify that suppliers can provide certification for these standards to ensure quality.
How Does Steel Compare as a Material for Inverters?
Key Properties:
Steel is a strong and durable material, capable of withstanding high mechanical stress and temperatures. Its corrosion resistance can be enhanced through galvanization or coatings.
Pros & Cons:
Steel’s primary advantage is its strength, making it suitable for structural components of inverters. However, it is heavier than aluminum and copper, which may complicate transportation and installation. Additionally, its thermal conductivity is lower, which can affect heat dissipation.
Impact on Application:
Steel is ideal for applications requiring robust structural integrity, such as in industrial settings. However, its weight can be a disadvantage in portable inverter designs.
Considerations for International Buyers:
Steel components must meet standards like ASTM A36 for carbon structural steel and DIN 17100 for general structural steel. Buyers in regions with strict compliance regulations, such as Europe, should ensure that suppliers can provide the necessary certifications.
What Advantages Does Plastic Offer in Inverter Design?
Key Properties:
Plastics, particularly engineering plastics like polycarbonate and ABS, offer excellent insulation properties and resistance to environmental factors. They can withstand temperatures ranging from -40°C to 120°C, depending on the type.
Pros & Cons:
The lightweight nature and high corrosion resistance of plastics make them advantageous for housing and insulation applications. However, they may not be suitable for high-stress components due to lower mechanical strength compared to metals.
Impact on Application:
Plastics are ideal for applications requiring insulation and protection from moisture and dust. However, their compatibility with high temperatures must be assessed to avoid deformation.
Considerations for International Buyers:
Plastics must comply with standards such as ASTM D638 for tensile properties and ISO 9001 for quality management. Buyers in regions with diverse climates, like Africa and the Middle East, should ensure that the selected plastics can withstand local environmental conditions.
Summary Table of Material Selection for Inverter Manufacturing
Material | Typical Use Case for inverter manufacturer | Key Advantage | Key Disadvantage/Limitation | Relative Cost (Low/Med/High) |
---|---|---|---|---|
Aluminum | Heat sinks and enclosures | Lightweight and excellent thermal conductivity | Higher cost and lower mechanical strength | Medium |
Copper | Electrical connections and wiring | Superior electrical conductivity | Expensive and heavier than alternatives | High |
Steel | Structural components | High strength and durability | Heavier and lower thermal conductivity | Medium |
Plastic | Insulation and housing | Lightweight and corrosion-resistant | Lower mechanical strength | Low |
This guide provides a comprehensive overview of the materials commonly used in inverter manufacturing, along with considerations for international B2B buyers. Understanding these factors will help ensure that your inverter products meet performance and compliance standards across various markets.
In-depth Look: Manufacturing Processes and Quality Assurance for inverter manufacturer
What Are the Key Stages in the Manufacturing Process of Inverters?
The manufacturing process for inverters typically consists of several critical stages: material preparation, forming, assembly, and finishing. Each of these stages is essential to ensure that the final product meets the required specifications and quality standards.
-
Material Preparation: This initial phase involves sourcing high-quality raw materials, such as semiconductors, capacitors, and other electronic components. Suppliers should provide documentation verifying the quality and origin of materials, ensuring they comply with industry standards. For international buyers, particularly in Africa and South America, it’s vital to assess suppliers’ material sourcing practices to avoid counterfeit components.
-
Forming: In this stage, raw materials undergo various processes, including cutting, shaping, and molding. Advanced techniques such as laser cutting and CNC machining are commonly employed to achieve precise dimensions. Buyers should inquire about the technology used in the forming stage, as this can significantly impact the reliability and efficiency of the inverter.
-
Assembly: The assembly process combines all components into the final inverter unit. This can be done manually or through automated systems, depending on the manufacturer’s capabilities. Key aspects to evaluate include the experience of assembly line workers and the use of automated testing systems during assembly to catch potential issues early.
-
Finishing: The final stage involves applying protective coatings, labeling, and packaging the inverters for shipment. This step is crucial for ensuring that the product can withstand environmental factors during transport and use. Buyers should ensure that manufacturers follow appropriate finishing processes that comply with international standards, especially for products intended for diverse climates in regions like the Middle East and Africa.
How Is Quality Assurance Implemented in Inverter Manufacturing?
Quality assurance (QA) is a critical component of the manufacturing process, ensuring that the final product meets both international and industry-specific standards.
-
International Standards: Many inverter manufacturers adhere to ISO 9001, a globally recognized quality management standard. Compliance with ISO 9001 indicates a commitment to quality processes, including continuous improvement and customer satisfaction. Additionally, certifications like CE marking are important for products sold in Europe, ensuring they meet safety and environmental requirements.
-
Industry-Specific Standards: Depending on the application, inverters may also need to comply with specific standards like API (American Petroleum Institute) for use in oil and gas applications or IEC (International Electrotechnical Commission) standards for electrical devices. Buyers should verify that manufacturers hold relevant certifications for their target markets.
-
Quality Control Checkpoints: Quality control (QC) is typically implemented at various stages of the manufacturing process:
– Incoming Quality Control (IQC): Raw materials are inspected upon arrival to ensure they meet specifications.
– In-Process Quality Control (IPQC): Regular inspections and tests are performed during the manufacturing process to identify defects early.
– Final Quality Control (FQC): The completed inverters undergo comprehensive testing to verify functionality and performance against specifications.
What Testing Methods Are Commonly Used in Inverter Quality Control?
Various testing methods are employed to ensure that inverters perform reliably under different conditions. Some common testing techniques include:
-
Electrical Testing: This includes tests for voltage, current, and power output, ensuring that the inverter operates within specified limits. Buyers should ask for detailed electrical test reports to understand performance metrics.
-
Thermal Testing: Inverters must withstand heat generated during operation. Thermal testing assesses how the unit performs under high temperatures, simulating real-world conditions.
-
Environmental Testing: This involves subjecting the inverter to humidity, dust, and vibration tests to ensure durability. For international buyers, particularly those in extreme climates, understanding the environmental testing standards used by manufacturers is crucial.
-
Safety Testing: Ensuring that inverters meet safety standards is vital. Tests for short circuits, overloads, and insulation resistance can help prevent hazards during operation.
How Can B2B Buyers Verify Supplier Quality Control?
For international B2B buyers, particularly from Africa, South America, the Middle East, and Europe, verifying a manufacturer’s quality control processes is essential to mitigate risks. Here are actionable steps to take:
-
Supplier Audits: Conducting on-site audits allows buyers to assess manufacturing processes, quality control measures, and compliance with international standards. This hands-on approach can reveal a manufacturer’s commitment to quality.
-
Requesting Quality Reports: Suppliers should provide detailed QC reports that outline inspection results and compliance with relevant standards. Reviewing these documents can help buyers understand the level of scrutiny applied throughout the manufacturing process.
-
Third-Party Inspections: Engaging third-party inspection agencies can provide an unbiased assessment of the manufacturer’s capabilities and adherence to quality standards. This is particularly useful for buyers in regions where direct oversight is challenging.
-
Certification Verification: Buyers should verify that manufacturers possess the necessary certifications (e.g., ISO, CE) through official channels. This can help ensure that the products meet the required quality and safety benchmarks.
What Are the Unique Quality Control Considerations for International Buyers?
International buyers must navigate various challenges when assessing quality control practices. Key considerations include:
-
Cultural Differences: Understanding cultural attitudes toward quality and compliance can help buyers communicate expectations clearly and foster better relationships with suppliers.
-
Regulatory Variations: Different regions may have varying regulations regarding product safety and quality standards. Buyers should familiarize themselves with the requirements in their markets, such as the EU’s REACH regulations or specific local standards in Africa.
-
Logistical Challenges: Shipping and logistics can impact the condition of inverters upon arrival. Buyers should discuss packaging and handling processes with suppliers to minimize damage during transit.
By focusing on these aspects, international B2B buyers can make informed decisions and establish partnerships with inverter manufacturers that prioritize quality and reliability, ultimately leading to successful business outcomes.
Practical Sourcing Guide: A Step-by-Step Checklist for ‘inverter manufacturer’
Introduction
Navigating the procurement process for inverter manufacturing can be complex, especially for international B2B buyers from regions like Africa, South America, the Middle East, and Europe. This guide provides a step-by-step checklist designed to streamline your sourcing efforts, ensuring that you select a reliable and competent manufacturer that meets your specific needs.
Step 1: Define Your Technical Specifications
Before beginning the sourcing process, clearly outline your technical requirements for the inverters. This includes understanding the type (e.g., grid-tied, off-grid), capacity, efficiency rating, and any specific features that are essential for your application.
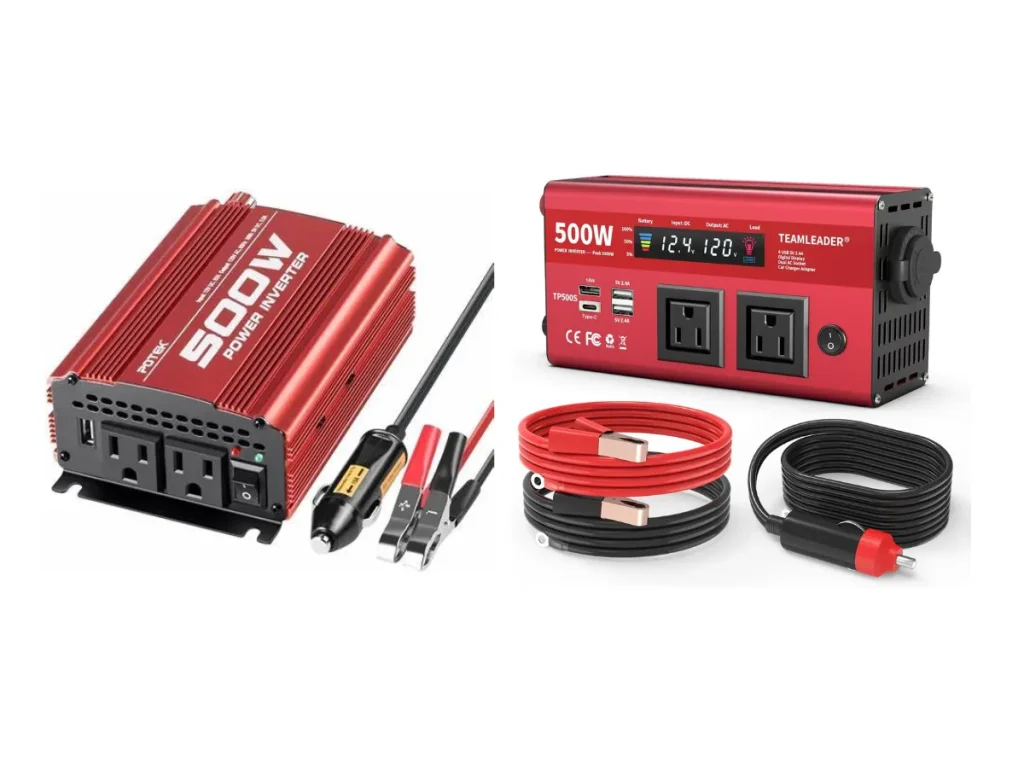
A stock image related to inverter manufacturer.
- Why It Matters: Defining these specifications helps narrow down potential suppliers and ensures that the products you receive will meet your operational demands.
- What to Look For: Ensure that your specifications align with industry standards and regulations in your target market.
Step 2: Research Potential Suppliers
Conduct thorough research to identify potential inverter manufacturers. Utilize industry directories, trade shows, and online platforms to compile a list of candidates.
- Why It Matters: A well-researched list will save time and improve the quality of your options.
- What to Look For: Focus on manufacturers with a proven track record, positive customer reviews, and expertise in the specific type of inverter you need.
Step 3: Evaluate Supplier Certifications
Check for relevant certifications that demonstrate the manufacturer’s compliance with international quality and safety standards, such as ISO 9001 or IEC standards.
- Why It Matters: Certifications provide assurance that the manufacturer adheres to industry standards, which is crucial for product reliability and safety.
- What to Look For: Request copies of certifications and verify their authenticity through the issuing bodies.
Step 4: Request Product Samples
Before making a bulk purchase, request samples of the inverters. This allows you to assess the quality and performance firsthand.
- Why It Matters: Testing samples can reveal potential issues and ensure that the product meets your specifications and expectations.
- What to Look For: Evaluate the build quality, performance metrics, and compatibility with your existing systems.
Step 5: Assess Manufacturing Capabilities
Investigate the manufacturer’s production capacity and capabilities to ensure they can meet your demand. This includes understanding their lead times, production processes, and technology used.
- Why It Matters: A manufacturer’s ability to meet your order volume and timelines is crucial for maintaining your supply chain.
- What to Look For: Inquire about their production schedule, flexibility to scale, and any recent investments in technology or processes.
Step 6: Analyze Pricing and Payment Terms
Request detailed quotes from shortlisted suppliers, including pricing, payment terms, and any additional costs such as shipping and customs duties.
- Why It Matters: Understanding the total cost of procurement helps in budgeting and financial planning.
- What to Look For: Compare not only the pricing but also the value offered in terms of warranty, support, and after-sales service.
Step 7: Establish Communication Channels
Choose a supplier with effective communication practices. Establish clear lines of communication for ongoing support and updates throughout the procurement process.
- Why It Matters: Effective communication can help resolve issues quickly and ensure that you remain informed throughout the sourcing journey.
- What to Look For: Assess their responsiveness, language capabilities, and willingness to engage in regular updates and discussions.
By following this checklist, B2B buyers can ensure a systematic and thorough approach to sourcing inverter manufacturers, ultimately leading to successful procurement and long-term partnerships.
Comprehensive Cost and Pricing Analysis for inverter manufacturer Sourcing
What Are the Key Cost Components in Inverter Manufacturing?
When sourcing inverters, understanding the cost structure is crucial for international B2B buyers. The primary cost components include:
-
Materials: The quality and type of materials used directly impact the cost. Common materials include semiconductors, capacitors, and metal enclosures. Sourcing high-quality materials can increase upfront costs but may reduce long-term failure rates.
-
Labor: Labor costs vary significantly based on geographical location. Countries with lower labor costs may offer competitive pricing, but this could come at the expense of quality. Buyers should assess the skill level and training of workers to ensure a reliable manufacturing process.
-
Manufacturing Overhead: This encompasses all indirect costs associated with production, such as utilities, rent, and equipment depreciation. Manufacturers with efficient processes can keep these costs lower, allowing for more competitive pricing.
-
Tooling: Initial costs for tooling and machinery setup can be significant, especially for custom inverter designs. Understanding the tooling costs is essential, particularly for buyers requiring specific modifications.
-
Quality Control (QC): Effective QC processes are crucial for ensuring product reliability. The costs associated with testing and certification should be factored into the overall pricing. Buyers should inquire about the manufacturer’s quality standards and any relevant certifications.
-
Logistics: Shipping costs, including packaging, transportation, and customs duties, can significantly affect overall costs. For international buyers, understanding Incoterms can help clarify responsibilities and potential additional costs.
-
Margin: Manufacturers will typically include a profit margin in their pricing. This margin can vary based on market competition, demand, and the manufacturer’s brand reputation.
How Do Price Influencers Affect Inverter Sourcing?
Several factors can influence the pricing of inverters. These include:
-
Volume and Minimum Order Quantity (MOQ): Larger orders often lead to volume discounts. Understanding the MOQ can help buyers negotiate better pricing.
-
Specifications and Customization: Custom specifications usually incur additional costs. Buyers should assess whether standard models could meet their needs to avoid unnecessary expenses.
-
Materials and Quality Certifications: The choice of materials and certifications like ISO or CE can affect pricing. Premium materials may lead to higher costs but can enhance the product’s lifespan and reliability.
-
Supplier Factors: Supplier reputation, reliability, and previous customer feedback can influence price negotiations. Established manufacturers may charge more due to their track record.
-
Incoterms: These terms define the responsibilities of buyers and sellers in shipping. Understanding Incoterms can help buyers anticipate additional costs related to transportation and customs.
What Are the Best Buyer Tips for Cost-Efficiency in Inverter Sourcing?
International B2B buyers can leverage several strategies to enhance cost-efficiency:
-
Negotiate Terms: Don’t hesitate to negotiate pricing, especially if ordering in bulk. Suppliers may be willing to offer discounts to secure large orders.
-
Evaluate Total Cost of Ownership (TCO): Consider not just the purchase price but also operational costs, maintenance, and potential downtime. A lower upfront cost may not always translate to lower overall expenses.
-
Research Local Market Conditions: Understanding the economic landscape in your region can aid in better negotiations. For instance, knowing typical labor costs in different countries can provide leverage in discussions.
-
Seek Multiple Quotes: Comparing quotes from various manufacturers can help identify competitive pricing and uncover hidden costs associated with different suppliers.
-
Stay Informed on Market Trends: Keeping abreast of changes in material costs, labor availability, and technological advancements can provide insights for better sourcing decisions.
Disclaimer
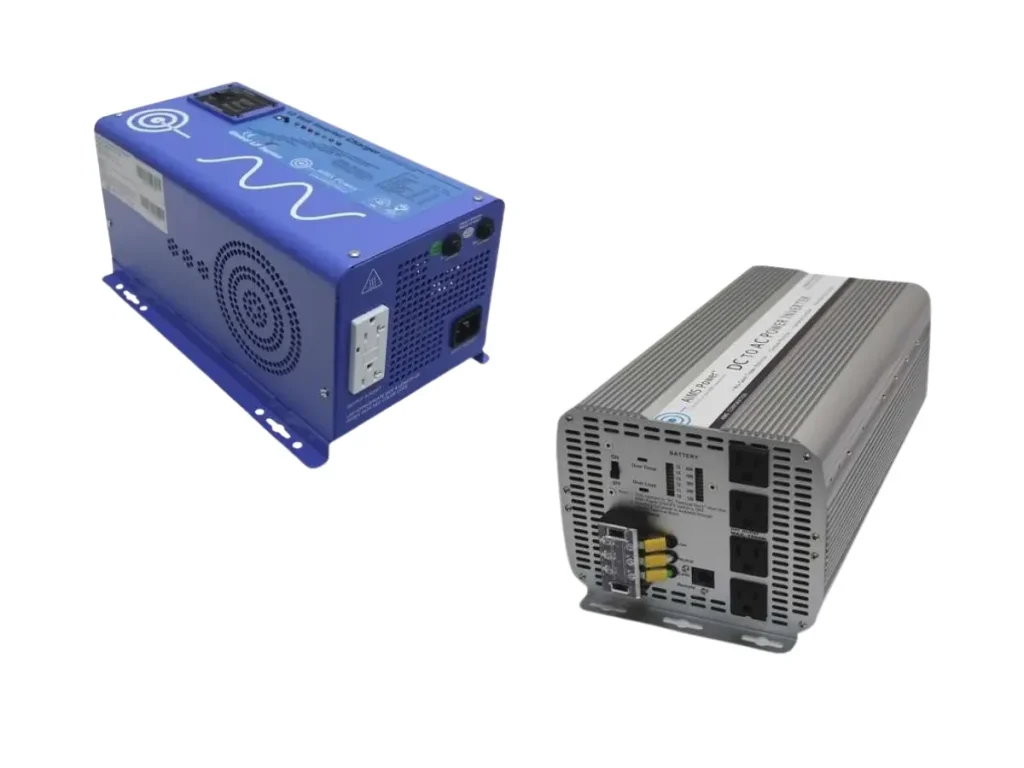
A stock image related to inverter manufacturer.
The pricing and cost components outlined here are indicative and may vary based on specific project requirements, market conditions, and supplier capabilities. Always conduct thorough due diligence before finalizing any agreements.
Alternatives Analysis: Comparing inverter manufacturer With Other Solutions
In the competitive landscape of energy solutions, B2B buyers must carefully evaluate various technologies to meet their needs. Inverter manufacturers provide essential services for converting direct current (DC) to alternating current (AC), which is crucial for solar energy systems and other applications. However, buyers may also consider alternative solutions that could fit their operational requirements more effectively or economically. This section compares inverter manufacturers with two viable alternatives: Energy Storage Systems (ESS) and Grid-Tied Systems.
Comparison Table of Inverter Manufacturer vs Alternatives
Comparison Aspect | Inverter Manufacturer | Energy Storage Systems (ESS) | Grid-Tied Systems |
---|---|---|---|
Performance | High efficiency in energy conversion | High capacity for energy storage | Continuous power supply |
Cost | Medium to high initial investment | High upfront cost, but savings over time | Lower initial costs; variable costs based on grid rates |
Ease of Implementation | Requires professional installation | Complex setup requiring skilled labor | Generally easier to integrate with existing infrastructure |
Maintenance | Regular maintenance required | Low maintenance; battery replacement needed periodically | Minimal maintenance; dependent on grid stability |
Best Use Case | Ideal for off-grid solar applications | Suitable for peak load management and backup power | Best for consistent supply in grid-connected environments |
What Are the Pros and Cons of Energy Storage Systems (ESS)?
Energy Storage Systems (ESS) allow businesses to store excess energy generated during peak production times and use it during high-demand periods. This can lead to significant cost savings and enhanced energy security. The primary advantage of ESS is its ability to provide backup power during outages and optimize energy consumption during peak pricing hours. However, the high initial investment can be a deterrent, and battery life may limit long-term viability, necessitating periodic replacements.
How Do Grid-Tied Systems Compare?
Grid-Tied Systems are designed to operate in conjunction with the existing electrical grid. This solution minimizes the need for extensive energy storage and allows for a seamless transition between solar energy and grid power. One of the main advantages is the reduced initial investment compared to standalone systems. Grid-tied systems can take advantage of net metering, where excess energy can be sold back to the grid. However, reliance on grid availability can be a drawback during outages, making them less suitable for businesses needing guaranteed power supply.
Conclusion: How Can B2B Buyers Choose the Right Energy Solution?
When evaluating energy solutions, B2B buyers must consider their specific operational needs, budget constraints, and long-term goals. Inverter manufacturers are ideal for businesses looking for high-efficiency energy conversion, particularly in off-grid applications. In contrast, Energy Storage Systems offer flexibility and reliability for those needing backup power and peak load management. Grid-Tied Systems provide a cost-effective solution for businesses connected to the grid but may lack the independence some operations require. Ultimately, the choice will depend on a careful assessment of performance, cost, ease of implementation, and maintenance needs to align with the buyer’s strategic energy goals.
Essential Technical Properties and Trade Terminology for inverter manufacturer
What Are the Essential Technical Properties of Inverters?
Understanding the technical specifications of inverters is crucial for B2B buyers, especially those in emerging markets in Africa, South America, the Middle East, and Europe. Here are some key properties to consider:
1. Material Grade
Material grade refers to the composition and quality of materials used in the inverter’s construction. High-grade materials enhance durability, efficiency, and thermal resistance. For buyers, selecting inverters made from superior materials can lead to longer service life and lower maintenance costs, which is particularly important in regions with harsh environmental conditions.
2. Tolerance Levels
Tolerance levels indicate the allowable deviation from specified dimensions in the manufacturing process. A tighter tolerance ensures better performance and reliability of the inverter. For international buyers, understanding tolerance levels can help in assessing whether the inverter will meet specific operational needs and standards, particularly in regulated markets.
3. Efficiency Rating
The efficiency rating, often expressed as a percentage, measures how effectively an inverter converts DC (direct current) to AC (alternating current). A higher efficiency rating means less energy loss during conversion. For B2B buyers, prioritizing high-efficiency inverters can lead to reduced energy costs and a lower carbon footprint, aligning with global sustainability goals.
4. Input Voltage Range
This specification defines the range of input voltages that the inverter can accept. A wide input voltage range is beneficial, particularly in regions with fluctuating power supply. Buyers should consider this property to ensure the inverter can operate effectively under varying voltage conditions, thus preventing potential equipment damage.
5. Thermal Management
Thermal management refers to the inverter’s ability to dissipate heat generated during operation. Effective thermal management systems help maintain optimal operating temperatures, enhancing reliability and longevity. Buyers should look for inverters with robust cooling mechanisms, especially in hot climates where overheating could lead to failures.
6. Protection Features
Inverters come with various protection features like over-voltage protection, short-circuit protection, and surge protection. These features safeguard the inverter and connected equipment from electrical anomalies. For buyers, understanding these protections is vital to mitigate risks associated with electrical surges and faults, ensuring operational continuity.
Which Trade Terms Are Important for Inverter Purchases?
Familiarity with industry jargon can streamline communication and negotiations between manufacturers and buyers. Here are some essential terms:
1. OEM (Original Equipment Manufacturer)
An OEM is a company that produces parts or equipment that may be marketed by another manufacturer. Understanding OEM relationships can help buyers identify reliable suppliers and assess product quality.
2. MOQ (Minimum Order Quantity)
MOQ refers to the smallest quantity of a product that a supplier is willing to sell. Knowing the MOQ is crucial for buyers to plan their purchases and manage inventory effectively, particularly for smaller businesses or new entrants in the market.
3. RFQ (Request for Quotation)
An RFQ is a document used to invite suppliers to bid on specific products or services. For buyers, issuing an RFQ can lead to competitive pricing and better terms, ensuring they receive the best value for their investment.
4. Incoterms (International Commercial Terms)
Incoterms define the responsibilities of buyers and sellers in international transactions, including shipping, insurance, and tariffs. Understanding Incoterms is vital for buyers to clarify terms of delivery and avoid unexpected costs in international shipments.
5. Lead Time
Lead time refers to the period from placing an order to receiving the product. For B2B buyers, understanding lead times is essential for project planning and ensuring timely availability of inverters, especially in industries where delays can lead to significant losses.
6. Warranty Period
The warranty period indicates how long a manufacturer guarantees the inverter’s performance. Buyers should consider warranty terms to assess product reliability and the manufacturer’s confidence in their product, which can also influence the total cost of ownership.
By understanding these essential technical properties and trade terminologies, international B2B buyers can make informed decisions when sourcing inverters, ultimately leading to more successful procurement strategies.
Navigating Market Dynamics and Sourcing Trends in the inverter manufacturer Sector
What Are the Key Market Dynamics and Trends in the Inverter Manufacturer Sector?
The inverter manufacturing sector is experiencing significant growth driven by the global transition towards renewable energy sources and the increasing demand for energy efficiency. As countries aim to meet international climate agreements, the need for solar inverters, wind energy inverters, and energy storage systems is rising sharply. In regions like Africa and South America, where energy access remains a challenge, inverter technology is crucial for enabling off-grid renewable solutions. Meanwhile, Europe, particularly Italy and Germany, continues to lead in high-efficiency inverter technologies that support smart grid integration.
Emerging B2B technology trends include the adoption of smart inverters that provide real-time data analytics and grid management capabilities. These advancements not only enhance operational efficiency but also facilitate predictive maintenance, which is particularly valuable for international buyers seeking reliability in their supply chains. Moreover, the trend towards modular inverter systems allows for scalability and customization, appealing to diverse market needs across different regions.
For international B2B buyers, understanding local regulations and standards, such as CE marking in Europe or certification requirements in Saudi Arabia, is crucial for compliance and successful market entry. Additionally, the growing emphasis on digitalization and automation in manufacturing processes is reshaping sourcing strategies, pushing buyers to consider suppliers who leverage Industry 4.0 practices.
How Can Sustainability and Ethical Sourcing Impact Your Inverter Manufacturing Choices?
Sustainability is becoming a non-negotiable aspect of the inverter manufacturing sector. The environmental impact of sourcing materials, such as metals used in inverter production, has drawn attention to the importance of ethical supply chains. International buyers are increasingly prioritizing suppliers who demonstrate a commitment to sustainable practices, including responsible sourcing of raw materials and reducing carbon footprints throughout the supply chain.
The presence of ‘green’ certifications, such as ISO 14001 or the Global Reporting Initiative (GRI), can significantly influence purchasing decisions. These certifications provide buyers with assurance that their suppliers adhere to stringent environmental standards. Furthermore, the use of eco-friendly materials and recyclable components is gaining traction, which not only aligns with global sustainability goals but also enhances brand reputation among environmentally-conscious consumers.
In regions like the Middle East and Africa, where energy infrastructure development is critical, ethical sourcing can also mitigate risks associated with supply chain disruptions. By investing in sustainable practices, companies can enhance their resilience and ensure long-term viability in increasingly competitive markets.
How Has the Inverter Manufacturing Sector Evolved Over Time?
The inverter manufacturing sector has evolved from simple mechanical devices to sophisticated electronic systems capable of managing complex energy sources. Initially, inverters were primarily used in small-scale applications; however, advancements in technology have transformed them into essential components of large-scale renewable energy systems.
The advent of microinverters and string inverters has allowed for greater efficiency and flexibility, catering to the needs of both residential and commercial installations. This evolution has been further accelerated by the integration of smart technologies, enabling inverters to communicate with other energy systems and optimize energy usage. As the global market continues to shift towards renewable energy, understanding this historical context provides valuable insights into current trends and future developments for B2B buyers in the inverter sector.
By staying informed about these dynamics, international B2B buyers can make strategic sourcing decisions that align with their long-term business objectives and sustainability goals.
Frequently Asked Questions (FAQs) for B2B Buyers of inverter manufacturer
-
How do I choose the right inverter manufacturer for my business needs?
Choosing the right inverter manufacturer involves assessing several factors including product quality, technology, customization capabilities, and after-sales support. Start by reviewing the manufacturer’s certifications and compliance with international standards, particularly for your target markets in Africa, South America, the Middle East, and Europe. It’s also crucial to evaluate their experience in your specific application area, such as renewable energy or industrial use. Finally, consider their reputation and customer testimonials to gauge reliability and service quality. -
What are the key features to look for in an inverter?
When sourcing inverters, focus on features that align with your operational requirements. Key features include efficiency ratings (look for models with at least 95% efficiency), durability under local environmental conditions, and the ability to handle peak loads. Additionally, consider smart features like remote monitoring, grid compatibility, and safety certifications, which are essential for international markets. Understanding these specifications ensures that you invest in a product that meets your long-term needs. -
What is the minimum order quantity (MOQ) for inverters from manufacturers?
Minimum order quantities (MOQs) can vary significantly among inverter manufacturers. Some may offer flexible MOQs for new buyers or smaller businesses, while others might require larger orders to optimize production costs. It’s advisable to discuss your needs directly with potential suppliers and negotiate terms that suit your purchasing power. Understanding the MOQ can help you manage your inventory and cash flow more effectively, especially when entering new markets. -
How can I verify the credibility of an inverter supplier?
Verifying the credibility of an inverter supplier involves several steps. Start by checking their business licenses and certifications relevant to your industry and region. Request references from previous clients to understand their experiences. Additionally, consider visiting the manufacturing facility or arranging a virtual tour to inspect production practices and quality control measures. Participating in trade shows or industry forums can also help you connect with reputable suppliers and gather market insights. -
What payment terms should I expect when sourcing inverters internationally?
International payment terms can vary widely based on the supplier’s policies and your negotiation skills. Common arrangements include letters of credit, advance payments, and payment upon delivery. It’s essential to clarify these terms upfront to avoid misunderstandings. Consider using secure payment methods that offer buyer protection, especially for significant transactions. Additionally, familiarize yourself with currency exchange risks and fees that may apply in international trade. -
How does customization work with inverter manufacturers?
Customization options depend on the manufacturer’s capabilities and your specific requirements. Many manufacturers offer tailored solutions, such as custom voltage ratings, enclosure designs, and integrated smart technology. When discussing customization, be clear about your specifications and desired features. Understand that custom orders may have different lead times and cost implications, so plan accordingly to ensure timely delivery for your projects. -
What quality assurance practices should I look for in inverter production?
Quality assurance practices are crucial in inverter production to ensure reliability and performance. Look for manufacturers that follow ISO 9001 standards or similar quality management systems. Inquire about their testing procedures, including component testing, functional testing, and stress testing under various conditions. Additionally, check if they provide warranties or guarantees, as this reflects their confidence in product quality and their commitment to customer satisfaction. -
What logistics considerations should I keep in mind when importing inverters?
When importing inverters, logistics considerations include shipping methods, import duties, and compliance with local regulations. Determine the best shipping options based on urgency and cost-effectiveness, and factor in lead times for international shipping. Understand the customs requirements in your country, including documentation needed for clearance. Collaborating with experienced freight forwarders can streamline the logistics process, helping you navigate potential challenges and ensuring timely delivery of your inverters.
Important Disclaimer & Terms of Use
⚠️ Important Disclaimer
The information provided in this guide, including content regarding manufacturers, technical specifications, and market analysis, is for informational and educational purposes only. It does not constitute professional procurement advice, financial advice, or legal advice.
While we have made every effort to ensure the accuracy and timeliness of the information, we are not responsible for any errors, omissions, or outdated information. Market conditions, company details, and technical standards are subject to change.
B2B buyers must conduct their own independent and thorough due diligence before making any purchasing decisions. This includes contacting suppliers directly, verifying certifications, requesting samples, and seeking professional consultation. The risk of relying on any information in this guide is borne solely by the reader.
Strategic Sourcing Conclusion and Outlook for inverter manufacturer
What Are the Key Takeaways for International B2B Buyers in Inverter Manufacturing?
In summary, strategic sourcing remains a vital component for international B2B buyers in the inverter manufacturing sector. By leveraging a comprehensive understanding of global supply chains, buyers can identify reliable manufacturers who offer competitive pricing and superior quality. It’s crucial to evaluate suppliers not just on cost but also on their ability to deliver innovative solutions that align with evolving market demands. Engaging with manufacturers that prioritize sustainability and adhere to international standards can significantly enhance the long-term viability of your procurement strategy.
How Can B2B Buyers Prepare for Future Trends in Inverter Technology?
As we look ahead, the inverter manufacturing landscape is poised for transformation driven by advancements in technology and increasing demand for renewable energy solutions. Buyers should stay informed about emerging technologies such as smart inverters and energy storage integration, which can provide additional value and efficiency. Establishing partnerships with forward-thinking manufacturers can help companies in Africa, South America, the Middle East, and Europe position themselves as leaders in their respective markets.
What Action Should B2B Buyers Take Now?
Now is the time for international B2B buyers to take proactive steps towards refining their sourcing strategies. Consider initiating discussions with potential suppliers, attending industry trade shows, and investing in market research. By doing so, you can ensure that your organization not only meets current energy demands but is also prepared for the innovations that lie ahead. Embrace strategic sourcing as a pathway to sustainable growth and enhanced competitiveness in the inverter manufacturing sector.