Discover Top Benefits of Choosing a Book Manufacturer (2025)
Introduction: Navigating the Global Market for book manufacturer
Navigating the complexities of the global market for book manufacturing can be a daunting task for international B2B buyers, especially when it comes to sourcing high-quality printed materials that meet diverse regional demands. As businesses in Africa, South America, the Middle East, and Europe seek reliable suppliers, understanding the nuances of book manufacturing—ranging from types of books and their applications to supplier vetting and cost considerations—becomes essential. This guide aims to provide comprehensive insights into the various aspects of book manufacturing, enabling buyers to make informed purchasing decisions that align with their specific needs.
In this guide, you will discover the different types of book manufacturing processes, including offset printing, digital printing, and print-on-demand services. We will delve into the applications of these processes across various sectors, such as education, publishing, and marketing. Furthermore, we will outline the key criteria for evaluating potential suppliers, including quality assurance, production capabilities, and logistical considerations. Cost analysis will also be a focus, ensuring you can budget effectively while still achieving the desired quality.
By equipping you with actionable insights and practical strategies, this guide empowers international B2B buyers to navigate the global book manufacturing landscape confidently. Whether you are sourcing for educational institutions, corporate training materials, or promotional content, understanding these factors will enhance your procurement process and ultimately lead to successful partnerships with manufacturers worldwide.
Understanding book manufacturer Types and Variations
Type Name | Key Distinguishing Features | Primary B2B Applications | Brief Pros & Cons for Buyers |
---|---|---|---|
Offset Printing | High-volume production, cost-effective for large runs | Textbooks, novels, magazines | Pros: Low cost per unit, excellent quality. Cons: Not ideal for short runs. |
Digital Printing | Quick turnaround, ideal for short runs | Marketing materials, custom books | Pros: Flexible, no setup costs. Cons: Higher cost per unit for large volumes. |
Print-on-Demand (POD) | Books printed as ordered, no inventory needed | Self-publishing, niche markets | Pros: Low risk, tailored offerings. Cons: Longer shipping times, higher per-unit costs. |
Hardbound Book Printing | Durable, high-quality finish, often custom-designed | Premium publications, gifts | Pros: High perceived value, longevity. Cons: Higher production costs. |
Softcover Book Printing | Cost-effective, lightweight, flexible options | Mass-market paperbacks, manuals | Pros: Economical, versatile. Cons: Less durable than hardcovers. |
What Are the Characteristics of Offset Printing?
Offset printing is a traditional method favored for its efficiency in producing high-quality prints in large quantities. This technique utilizes plates to transfer ink onto the paper, making it ideal for projects such as textbooks, novels, and magazines. B2B buyers should consider offset printing when they require consistent quality and cost-effectiveness for large runs, as the cost per unit decreases significantly with volume. However, this method may not be suitable for projects that need quick turnaround times or small print quantities.
How Does Digital Printing Differ from Other Methods?
Digital printing is distinguished by its ability to produce high-quality prints quickly without the need for plate creation, making it perfect for short runs and customized materials. B2B applications include marketing materials and custom books. Buyers appreciate digital printing for its flexibility and speed, as it allows for rapid changes and updates to designs. However, the cost per unit can be higher compared to offset printing when producing large volumes, which may be a consideration for budget-sensitive projects.
What Are the Benefits of Print-on-Demand (POD)?
Print-on-demand (POD) offers a unique solution for businesses looking to minimize inventory costs and reduce risk. With this model, books are printed only as orders are received, making it an excellent choice for self-publishing authors and niche markets. Key B2B considerations include the ability to offer tailored products without upfront investment in inventory. However, buyers should be aware of potentially longer shipping times and higher per-unit costs, which can impact overall pricing strategies.
Why Choose Hardbound Book Printing?
Hardbound book printing is synonymous with durability and quality, often used for premium publications or gifts. This method involves binding pages between hard covers, providing a luxurious feel and increased longevity. B2B buyers often opt for hardbound printing to enhance the perceived value of their products. While the initial production costs are higher, the long-term benefits, such as reduced returns and increased customer satisfaction, can justify the investment for businesses targeting high-end markets.
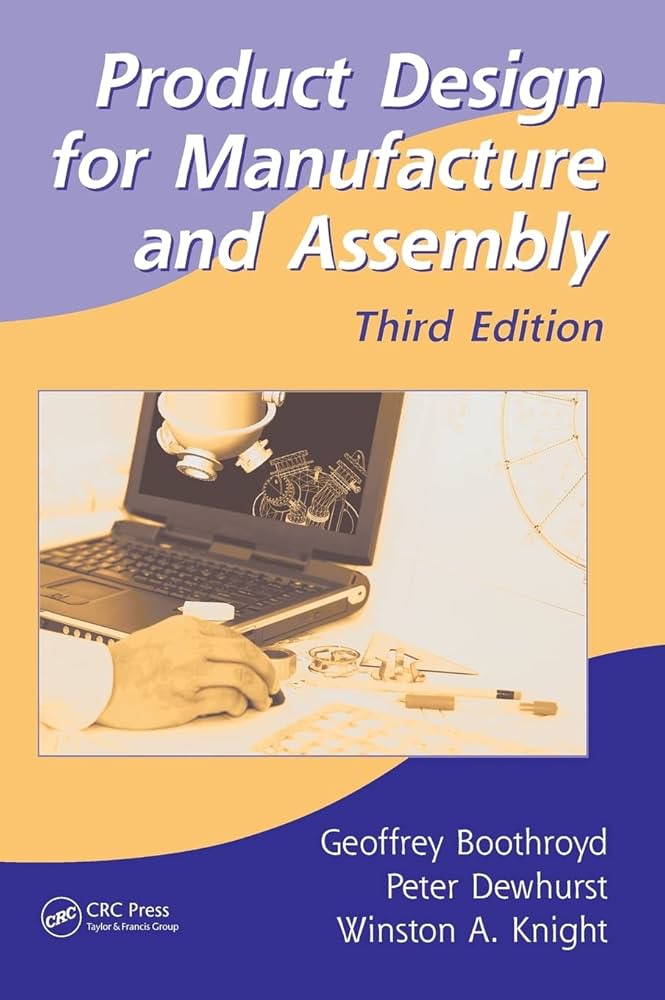
A stock image related to book manufacturer.
What Are the Advantages of Softcover Book Printing?
Softcover book printing is characterized by its lightweight and cost-effective nature, making it a popular choice for mass-market paperbacks and manuals. This method offers flexibility in terms of design and format, allowing businesses to produce a wide range of products at a lower cost. B2B buyers should consider softcover printing for projects with budget constraints or those requiring a quick turnaround. However, it is essential to note that softcovers are generally less durable than hardbound options, which may influence decisions based on the intended use of the books.
Related Video: The Genius Behind Bach’s Goldberg Variations: CANONS
Key Industrial Applications of book manufacturer
Industry/Sector | Specific Application of Book Manufacturer | Value/Benefit for the Business | Key Sourcing Considerations for this Application |
---|---|---|---|
Education | Custom Textbooks and Educational Materials | Enhanced learning outcomes through tailored content | Look for manufacturers with experience in educational publishing and localization capabilities. |
Publishing | Trade Books and Specialty Publications | Diverse offerings that cater to niche markets | Assess the manufacturer’s portfolio and their capacity for high-quality print runs. |
Corporate Training | Training Manuals and Employee Handbooks | Improved employee performance through structured training | Prioritize suppliers who can provide quick turnaround times and customization options. |
Marketing | Promotional Materials and Catalogs | Increased brand visibility and customer engagement | Evaluate manufacturers on their design services and print quality. |
Non-Profit Organizations | Awareness Campaign Materials | Effective communication of mission and values | Seek manufacturers experienced in producing high-impact, low-cost materials. |
How Does the Book Manufacturer Serve the Education Sector?
In the education sector, book manufacturers play a crucial role by producing custom textbooks and educational materials tailored to specific curricula. This application not only addresses the unique learning needs of students but also enhances educational outcomes. For international buyers, especially from regions like Africa and South America, it is vital to source manufacturers that understand local educational standards and can offer localization services to ensure content relevance and accessibility.
What Role Does Book Manufacturing Play in the Publishing Industry?
Book manufacturers are integral to the publishing industry, providing trade books and specialty publications that cater to diverse audiences. These manufacturers can help publishers expand their offerings into niche markets, which is particularly beneficial in Europe and the Middle East, where cultural diversity demands varied content. When sourcing, publishers should look for manufacturers with a strong portfolio, proven quality, and the ability to handle both small and large print runs efficiently.
How Can Book Manufacturers Enhance Corporate Training Programs?
In corporate training, book manufacturers supply training manuals and employee handbooks that are essential for structured employee development. These materials help improve performance by providing clear guidelines and training resources. For international B2B buyers, especially from Europe, it is crucial to partner with manufacturers who can offer quick turnaround times and customization options to adapt to specific corporate cultures and training methodologies.
Why Are Book Manufacturers Important for Marketing?
For marketing purposes, book manufacturers produce promotional materials and catalogs that significantly boost brand visibility and customer engagement. High-quality printed materials can effectively convey a brand’s message and enhance customer interaction. Buyers from South America and Africa should evaluate manufacturers based on their design capabilities and print quality to ensure that their marketing materials stand out in competitive markets.
How Do Book Manufacturers Assist Non-Profit Organizations?
Non-profit organizations often rely on book manufacturers to create awareness campaign materials that effectively communicate their mission and values. These materials are vital for fundraising and community outreach efforts. When sourcing manufacturers, non-profits should prioritize those experienced in producing impactful, cost-effective materials, ensuring their campaigns resonate with target audiences and drive engagement.
Related Video: Uses and Gratifications Theory
3 Common User Pain Points for ‘book manufacturer’ & Their Solutions
Scenario 1: Delays in Production and Delivery Timelines
The Problem: One of the most significant pain points for B2B buyers in the book manufacturing sector is delays in production and delivery timelines. Many companies depend on timely delivery for book launches, events, or educational purposes. When a manufacturer fails to meet deadlines, it can disrupt marketing campaigns, lead to missed sales opportunities, and damage reputations. This issue can be exacerbated when working with international suppliers, where time zones, communication barriers, and logistical challenges come into play.
The Solution: To combat this issue, buyers should prioritize working with manufacturers that have a proven track record of reliability and transparency. Start by conducting thorough due diligence on potential partners, including checking references, reading reviews, and understanding their production capacity. Establish clear communication channels and set up a timeline with milestones for key phases of production. Utilize project management tools to track progress and maintain regular check-ins. Additionally, consider having contingency plans in place, such as alternative suppliers or expedited shipping options, to mitigate any unforeseen delays.
Scenario 2: Quality Control Issues in Printing
The Problem: Quality control is paramount in book manufacturing, but buyers often face challenges with inconsistent print quality. Issues may include color discrepancies, poor binding, and misalignment of pages, which can tarnish the final product and lead to customer dissatisfaction. This is particularly concerning for publishers who must maintain high standards for their brand and cater to discerning audiences across various markets in Africa, South America, the Middle East, and Europe.
The Solution: To ensure consistent quality, buyers should engage in proactive quality assurance measures. Start by requesting samples before placing a bulk order to assess the manufacturer’s quality standards firsthand. Clearly outline specifications regarding materials, colors, and binding techniques in the contract to avoid misunderstandings. Implement a quality control checklist that includes pre-production proofs and in-process inspections. It’s also beneficial to establish a relationship with a local quality assurance consultant who can oversee the production process and ensure adherence to quality standards.
Scenario 3: Navigating Cultural and Regulatory Differences
The Problem: International B2B buyers often encounter cultural and regulatory challenges when sourcing from book manufacturers across different regions. Differences in business practices, communication styles, and regulatory requirements can create misunderstandings and complications. For instance, a buyer from Europe may not be familiar with the import/export regulations in South America or the Middle East, leading to delays and additional costs.
The Solution: To navigate these complexities, buyers should invest in understanding the cultural and regulatory landscape of the countries they are sourcing from. This can include researching local business etiquette and legal requirements, such as copyright laws and import tariffs. Collaborating with local agents or consultants who have expertise in the specific market can provide invaluable insights and facilitate smoother transactions. Additionally, consider establishing partnerships with manufacturers who have experience working with international clients, as they will likely have processes in place to handle regulatory compliance and can offer guidance on best practices. Regularly attending industry conferences and networking events can also enhance understanding and build relationships with key stakeholders in different regions.
Strategic Material Selection Guide for book manufacturer
When selecting materials for book manufacturing, understanding the properties, advantages, and limitations of various materials is crucial for international B2B buyers. This guide focuses on four common materials used in book production: paper, binding materials, covers, and inks. Each material has distinct characteristics that can influence the overall quality and marketability of the final product.
What Are the Key Properties of Paper in Book Manufacturing?
Paper is the most fundamental material in book manufacturing, impacting both the tactile experience and visual appeal of the book. Key properties include weight (measured in grams per square meter, or GSM), opacity, brightness, and texture. Higher GSM typically indicates thicker, more durable paper, which is essential for books that will endure frequent handling.
Pros and Cons of Using Paper:
– Pros: Paper can be produced from various fibers, offering flexibility in texture and finish. It is generally cost-effective and widely available.
– Cons: Paper is susceptible to moisture, which can lead to warping or deterioration. Additionally, the quality of paper can vary significantly, impacting print quality and durability.
Impact on Application:
Different types of paper are suited for various genres. For example, glossy paper is ideal for photo books, while uncoated paper is preferred for novels due to its readability.
Considerations for International Buyers:
Buyers should be aware of local preferences for paper types and compliance with environmental standards (e.g., FSC certification). Understanding common standards such as ISO 9706 for permanence can also guide selection.
How Do Binding Materials Affect Book Durability?
Binding materials, including glue, thread, and cover materials, play a critical role in the book’s durability and usability. The choice of binding affects how well a book can withstand repeated use and how easily it can be opened.
Pros and Cons of Binding Materials:
– Pros: Strong binding materials enhance the longevity of books, especially for hardcovers. Options like perfect binding offer a professional finish at a lower cost.
– Cons: Some binding methods can be more expensive and complex to manufacture, such as case binding, which requires precise machinery and skilled labor.
Impact on Application:
The binding method chosen can dictate the book’s intended use. For instance, spiral binding is ideal for cookbooks or manuals that need to lie flat.
Considerations for International Buyers:
Buyers should consider the availability of binding materials in their region and the associated labor costs. Compliance with local regulations regarding adhesives and their environmental impact is also essential.
What Are the Benefits of Different Cover Materials?
Covers can be made from various materials, including paper, cloth, and synthetic materials. Each type offers unique benefits in terms of aesthetics and protection.
Pros and Cons of Cover Materials:
– Pros: Cloth covers provide a premium feel and durability, while synthetic covers are water-resistant and easy to clean.
– Cons: Cloth can be more expensive and may not be as widely available in certain regions. Synthetic materials may not appeal to eco-conscious consumers.
Impact on Application:
The choice of cover material can significantly influence the book’s marketability. For example, a hardcover with a cloth cover may be more appealing for gift editions.
Considerations for International Buyers:
Buyers should be aware of the cultural significance of cover materials in their target markets. Additionally, compliance with safety standards for synthetic materials is crucial in regions with strict regulations.
How Do Inks Impact the Quality of Printed Books?
Inks are vital for the visual quality of printed materials. The choice of ink can affect color vibrancy, drying time, and overall print quality.
Pros and Cons of Inks:
– Pros: High-quality inks provide better color accuracy and longevity. Eco-friendly inks can appeal to environmentally conscious consumers.
– Cons: Specialty inks can be more expensive and may require specific printing techniques, increasing production complexity.
Impact on Application:
The type of ink used can vary based on the book’s purpose. For example, vibrant inks are preferred for children’s books, while subdued colors may suit academic texts.
Considerations for International Buyers:
Buyers should consider local regulations regarding ink compositions, particularly in regions with stringent environmental laws. Understanding the preferences for ink types in different markets can also enhance product appeal.
Summary Table of Material Selection for Book Manufacturing
Material | Typical Use Case for book manufacturer | Key Advantage | Key Disadvantage/Limitation | Relative Cost (Low/Med/High) |
---|---|---|---|---|
Paper | General book pages | Wide variety and cost-effective | Susceptible to moisture and quality variability | Low |
Binding Materials | Book assembly | Enhances durability and usability | Can be complex and expensive to manufacture | Medium |
Cover Materials | Book exterior | Aesthetic appeal and protection | Cost and availability issues in some regions | Medium to High |
Inks | Printing text and images | Better color accuracy and longevity | Specialty inks can increase production complexity | Medium to High |
This strategic material selection guide provides actionable insights for international B2B buyers, helping them make informed decisions that align with their market needs and compliance requirements.
In-depth Look: Manufacturing Processes and Quality Assurance for book manufacturer
What Are the Main Stages of Manufacturing in Book Production?
The manufacturing process for books is complex and involves several key stages, each contributing to the final product’s quality and durability. The primary stages include material preparation, forming, assembly, and finishing.
How Is Material Prepared for Book Manufacturing?
The first step in book manufacturing is the preparation of materials. This involves selecting high-quality paper, ink, and binding materials. The paper is typically sourced based on specifications such as weight, texture, and opacity. For instance, offset printing requires different paper types than digital printing.
Once the materials are selected, they undergo treatment processes such as cutting, folding, and coating to ensure they are ready for the next stages. For example, paper may be treated for moisture resistance or coated for enhanced print quality. This preparation stage is crucial as it sets the foundation for the entire manufacturing process.
What Techniques Are Used in Forming Books?
The forming stage encompasses the processes that shape the book’s physical structure. This includes printing, which can be achieved through various methods like offset, digital, or screen printing. Each method has its pros and cons, influencing factors such as print quality, speed, and cost.
After printing, the sheets are typically folded into signatures, which are groups of pages. This stage may also involve the use of special techniques, such as die-cutting for unique shapes or adding embossed elements for aesthetic appeal. The choice of forming techniques will depend on the book’s intended use and target market, which is essential for B2B buyers to consider.
How Is Assembly Done in Book Manufacturing?
Assembly is where the various components of the book come together. This involves collating the folded signatures, binding them using techniques such as perfect binding, case binding, or saddle stitching. Perfect binding is commonly used for paperbacks, while case binding is preferred for hardcovers due to its durability.
During this stage, any additional features such as endpapers, bookmarks, or covers are also added. Attention to detail in assembly is vital, as misalignment or poor binding can lead to quality issues that affect customer satisfaction.
What Finishing Touches Are Important in Book Production?
Finishing processes enhance the book’s aesthetic appeal and durability. This may include trimming the edges, applying lamination, or adding foil stamping. Each finishing technique contributes to the book’s overall look and feel, making it more appealing to potential buyers.
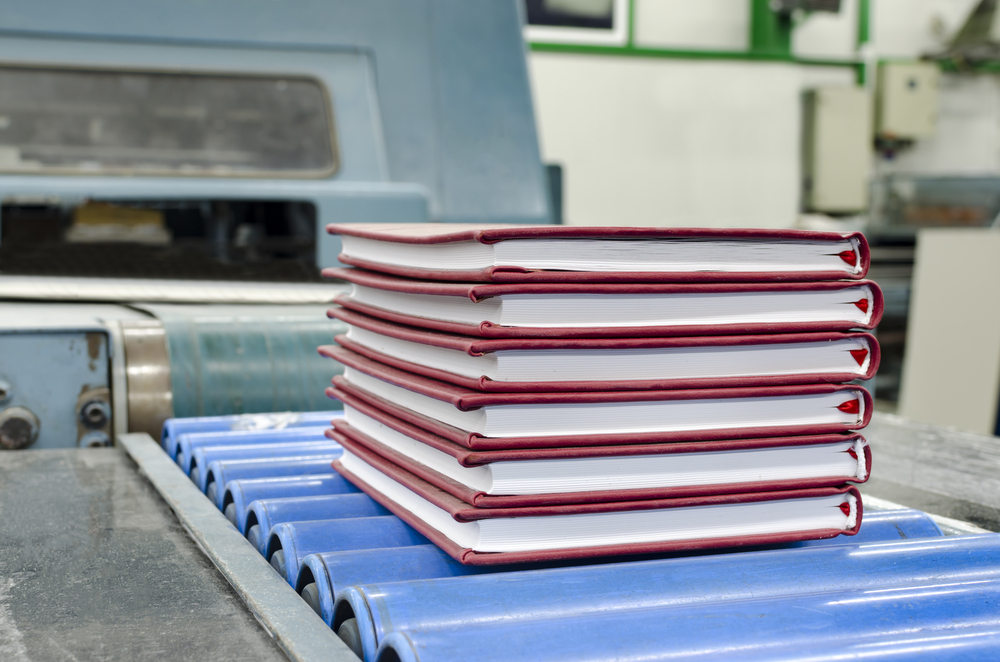
A stock image related to book manufacturer.
For instance, lamination can protect the cover from wear and tear, while foil stamping adds a luxurious touch. The right finishing techniques can differentiate a product in a competitive market, thus influencing B2B buyers’ purchasing decisions.
What Quality Assurance Practices Are Crucial in Book Manufacturing?
Quality assurance (QA) is a critical aspect of book manufacturing that ensures products meet specific standards before reaching the market. It involves both international and industry-specific standards, along with systematic checks throughout the production process.
Which International Standards Should B2B Buyers Be Aware Of?
International standards such as ISO 9001 are essential for ensuring consistent quality management systems. Compliance with ISO 9001 indicates that a manufacturer has established processes for maintaining quality throughout their operations.
Additionally, industry-specific standards such as CE marking (for products sold in Europe) and API (American Petroleum Institute) standards can also apply, depending on the book’s intended use and market. For B2B buyers, verifying compliance with these standards is crucial, as it reflects the manufacturer’s commitment to quality.
What Are the Key Quality Control Checkpoints in Book Manufacturing?
Quality control (QC) checkpoints are strategically placed throughout the manufacturing process to catch defects early. Common checkpoints include:
- Incoming Quality Control (IQC): Inspection of raw materials upon arrival to ensure they meet specified standards.
- In-Process Quality Control (IPQC): Ongoing inspections during production to monitor processes and identify issues.
- Final Quality Control (FQC): Comprehensive checks before packaging and shipping to ensure that the finished product meets quality standards.
These checkpoints help in minimizing defects and ensuring that only high-quality products reach the end consumer.
How Can B2B Buyers Verify Supplier Quality Control?
B2B buyers should adopt several strategies to verify a supplier’s quality control measures:
- Conduct Audits: Regular audits of suppliers can provide insights into their quality control processes and adherence to standards.
- Request Quality Reports: Suppliers should provide documentation of their quality control procedures, inspection results, and compliance with relevant standards.
- Engage Third-Party Inspections: Utilizing third-party inspection services can provide an unbiased assessment of the supplier’s quality control practices.
These measures help ensure that suppliers are reliable and capable of delivering high-quality books consistently.
What Testing Methods Are Commonly Used in Book Quality Assurance?
Various testing methods are employed to assess the quality of books throughout the production process. Common methods include:
- Physical Testing: Assessing the book’s durability, such as spine strength and page adhesion, through stress testing.
- Print Quality Testing: Evaluating the clarity, color accuracy, and alignment of printed materials.
- Environmental Testing: Checking the book’s resistance to moisture, temperature changes, and UV exposure to ensure longevity.
Understanding these testing methods is critical for B2B buyers, as they can influence purchasing decisions based on the expected quality and durability of the product.
What Are the QC and Certification Nuances for International B2B Buyers?
For international B2B buyers, understanding the nuances of quality control and certification is essential. Different regions may have varying standards and regulations that affect product quality and compliance.
- Region-Specific Certifications: Buyers should be aware of certifications specific to their regions, such as EN71 for toys in Europe or ASTM standards in the U.S.
- Cultural Expectations: Different markets may have unique expectations regarding book design, content, and quality. Understanding these can help in selecting the right manufacturers.
- Supply Chain Transparency: It’s important for buyers to ensure that suppliers maintain transparency in their manufacturing processes and quality control practices, which can mitigate risks associated with product quality.
By being informed about these aspects, B2B buyers can make more educated decisions when sourcing from international book manufacturers, ensuring they receive high-quality products that meet their specific needs.
Practical Sourcing Guide: A Step-by-Step Checklist for ‘book manufacturer’
In today’s competitive landscape, finding the right book manufacturer is essential for ensuring quality production and timely delivery. This guide offers a practical checklist to help international B2B buyers streamline their sourcing process, particularly for those in Africa, South America, the Middle East, and Europe.
Step 1: Identify Your Specific Needs
Before reaching out to manufacturers, clearly define what you need. Consider the types of books (e.g., hardcover, paperback, educational, or specialty books) and the volume of production you require. This clarity will help you communicate effectively with potential suppliers and ensure they can meet your specific requirements.
- Book Types: Different manufacturers may specialize in different formats, so identify what suits your project best.
- Volume: Knowing your order size can impact pricing and lead times.
Step 2: Research Potential Manufacturers
Conduct thorough research to compile a list of potential book manufacturers. Utilize online directories, trade shows, and industry contacts to find reputable suppliers. Look for those with experience in producing the type of books you need.
- Industry Directories: Websites like Alibaba and ThomasNet can be valuable resources.
- Trade Shows: Attending book fairs and publishing expos can provide firsthand insights into manufacturers’ capabilities.
Step 3: Evaluate Supplier Credentials
It’s crucial to verify the credentials and reputation of potential suppliers. Request certifications, such as ISO standards, and check for any industry awards or recognitions.
- Quality Certifications: These indicate adherence to quality management standards.
- Client Testimonials: Look for reviews or case studies from other businesses that have worked with them.
Step 4: Request Samples
Before making a large commitment, request samples of their work. This allows you to assess the quality of their printing, binding, and overall craftsmanship.
- Sample Quality: Pay attention to print clarity, color accuracy, and binding durability.
- Customization Options: Ensure they can accommodate any specific design features you require.
Step 5: Discuss Pricing and Payment Terms
Engage in discussions about pricing structures, payment terms, and any potential hidden costs. Understanding the total cost upfront can prevent budget overruns later in the project.
- Pricing Models: Some manufacturers may offer tiered pricing based on volume, while others may have fixed rates.
- Payment Flexibility: Discuss terms such as deposits, payment schedules, and acceptable payment methods.
Step 6: Evaluate Production Capabilities and Lead Times
Assess the manufacturer’s production capabilities to ensure they can meet your deadlines. Discuss lead times and what factors could influence production schedules.
- Production Capacity: Confirm their ability to handle your order size within the required timeframe.
- Flexibility: Inquire about their capacity to manage rush orders if necessary.
Step 7: Establish Clear Communication Channels
Effective communication is key to a successful partnership. Establish clear lines of communication and set expectations for updates throughout the production process.
- Point of Contact: Designate a single point of contact to streamline communication.
- Regular Updates: Agree on how frequently you will receive status updates on your order.
By following these steps, B2B buyers can confidently navigate the sourcing process for book manufacturers, ensuring they find a partner that meets their quality standards and production needs.
Comprehensive Cost and Pricing Analysis for book manufacturer Sourcing
When sourcing from book manufacturers, understanding the cost structure and pricing dynamics is crucial for international B2B buyers. This analysis breaks down the essential components and influencers of pricing while offering actionable insights tailored for buyers from Africa, South America, the Middle East, and Europe.
What Are the Key Cost Components in Book Manufacturing?
-
Materials: The choice of paper, ink, and cover materials significantly impacts cost. High-quality materials typically yield better durability and aesthetics, but at a higher price point. Buyers should evaluate the trade-off between quality and cost based on their target market’s expectations.
-
Labor: Labor costs vary by region. In countries with higher labor costs, such as those in Western Europe, manufacturers might charge more. Understanding the local labor market can help buyers identify competitive pricing.
-
Manufacturing Overhead: This includes expenses related to utilities, rent, and administrative costs. Manufacturers with efficient operations may pass on savings to buyers, so it’s beneficial to inquire about their operational efficiencies.
-
Tooling: Initial setup costs for printing presses or binding machines can be substantial. Custom tooling for specialized book formats or finishes can lead to higher upfront costs, which should be factored into the total pricing.
-
Quality Control (QC): Rigorous QC processes ensure product reliability and adherence to specifications. While this can increase costs, it ultimately protects the buyer’s brand reputation.
-
Logistics: Shipping costs can fluctuate based on distance, shipping method, and current fuel prices. For international buyers, understanding Incoterms can clarify who bears responsibility for shipping and associated costs.
-
Margin: Manufacturers typically add a profit margin to their costs. This margin can vary based on competition, demand, and the perceived value of the product.
How Do Price Influencers Affect Book Manufacturing Costs?
-
Volume/MOQ (Minimum Order Quantity): Higher order volumes often lead to lower per-unit costs due to economies of scale. Buyers should consider their sales forecasts when negotiating MOQs.
-
Specifications and Customization: Unique specifications or custom features can raise costs. Buyers should clearly define their requirements to avoid unexpected charges.
-
Materials and Quality Certifications: Premium materials and certifications (like FSC for sustainable sourcing) can increase costs but may be essential for market acceptance, especially in environmentally conscious regions.
-
Supplier Factors: The reputation and reliability of the supplier can influence pricing. Established suppliers may charge a premium but often deliver higher quality and reliability.
-
Incoterms: Understanding the terms of shipment can prevent unforeseen costs. For example, DDP (Delivered Duty Paid) means the seller bears all costs, which can simplify budgeting for the buyer.
What Tips Can Help Buyers Optimize Costs When Sourcing Books?
-
Negotiation: Engaging in open discussions about pricing and terms can often yield discounts, especially for repeat orders or larger volumes. Be prepared to negotiate on both price and payment terms.
-
Cost Efficiency: Conduct a Total Cost of Ownership analysis to consider all costs associated with sourcing, including potential returns, shipping, and storage. This approach helps in making informed decisions beyond the initial price.
-
Pricing Nuances for International Buyers: Different regions may have varying expectations regarding quality, delivery times, and pricing structures. Understanding local market dynamics can aid in negotiations and sourcing strategies.
- Disclaimer for Indicative Prices: It is essential to note that prices can vary widely based on specific project requirements, market conditions, and the chosen supplier. Always request a detailed quotation that reflects your specific needs.
By understanding these components and leveraging the provided insights, international B2B buyers can make informed decisions when sourcing from book manufacturers, ultimately leading to better cost management and enhanced product quality.
Alternatives Analysis: Comparing book manufacturer With Other Solutions
In today’s global market, B2B buyers often face a variety of choices when it comes to sourcing products and services. For those in the book publishing industry, understanding the alternatives to traditional book manufacturing can be crucial for optimizing costs, quality, and delivery times. This analysis provides a comparative overview of book manufacturers against viable alternatives such as print-on-demand services and digital publishing platforms.
Comparison Aspect | Book Manufacturer | Print-on-Demand Service | Digital Publishing Platform |
---|---|---|---|
Performance | High-quality print runs, consistent quality | Variable quality, depends on provider | Instant distribution, no physical limitations |
Cost | Higher initial investment, economies of scale with large orders | Lower upfront cost, but higher per unit for small runs | Minimal upfront costs, but ongoing platform fees |
Ease of Implementation | Requires planning, inventory management | Simple setup, no inventory needed | Easy to publish, no physical logistics |
Maintenance | Ongoing maintenance of equipment, quality checks | Limited maintenance, provider handles issues | Regular updates, platform-dependent |
Best Use Case | Large volume print runs, customized products | Small batches, niche markets | E-books, multimedia content, quick distribution |
What are the Benefits and Drawbacks of Print-on-Demand Services?
Print-on-demand (POD) services are an excellent alternative for businesses that do not require large print runs. The main advantage of POD is its cost-effectiveness for small quantities, which eliminates the need for large upfront investments in inventory. Additionally, POD services enable quick turnaround times and the ability to test new titles without significant financial risk. However, the quality can vary depending on the provider, and the per-unit cost can be higher than traditional printing methods for larger volumes.
How Does Digital Publishing Compare to Traditional Book Manufacturing?
Digital publishing platforms offer a modern approach that eliminates the need for physical production altogether. This method allows for instant distribution to a global audience and supports various multimedia formats, such as e-books and interactive content. While the initial costs are typically lower, ongoing platform fees can accumulate over time. Digital publishing is particularly effective for authors and publishers looking to reach niche markets or experiment with new content without the overhead costs of traditional manufacturing.
Making the Right Choice for Your Business Needs
When deciding between a traditional book manufacturer and alternative solutions, B2B buyers should consider their specific needs and constraints. For businesses focused on high-volume, high-quality production, a book manufacturer remains the best choice. Conversely, if you are looking to minimize costs and have flexibility in order sizes, print-on-demand may be more suitable. Digital publishing is ideal for those wanting to innovate and reach audiences quickly without the limitations of physical distribution.
Ultimately, the best solution will depend on factors such as budget, target market, and the type of content being produced. By carefully evaluating these alternatives, B2B buyers can make informed decisions that align with their business goals.
Essential Technical Properties and Trade Terminology for book manufacturer
What Are the Key Technical Properties for Book Manufacturing?
When sourcing books from manufacturers, understanding the technical properties is crucial for ensuring quality and meeting your business needs. Here are some essential specifications to consider:
1. Material Grade: What Does It Mean for Quality?
The material grade refers to the quality and type of paper used in book production, such as coated, uncoated, or specialty paper. High-grade materials can enhance the durability and aesthetic appeal of a book, which is vital for both consumer satisfaction and brand reputation. For instance, books printed on acid-free paper resist yellowing over time, making them ideal for archival purposes.
2. Tolerance: Why Is It Important in Book Production?
Tolerance in book manufacturing indicates the allowable variation in dimensions and specifications during the production process. This is crucial for ensuring that the final product meets industry standards and client expectations. For example, a tolerance of ±1mm for book dimensions ensures that books fit appropriately in packaging and on shelves, reducing returns due to sizing issues.
3. Binding Type: How Does It Affect Durability?
The binding type, such as saddle-stitch, perfect binding, or case binding, significantly affects the durability and usability of a book. Each binding method has different applications; for instance, case binding is ideal for hardcover books that require longevity. Understanding the binding types helps buyers select the most appropriate option for their target market.
4. Print Resolution: What Impact Does It Have on Visual Quality?
Print resolution, measured in dots per inch (DPI), determines the clarity and quality of images and text in printed materials. A higher DPI (300 or above) is essential for high-quality photo books, while lower DPI may suffice for text-heavy publications. This property is particularly important for publishers aiming to deliver visually appealing products.
5. Ink Type: What Should You Consider?
The type of ink used in book printing can influence color vibrancy and environmental impact. Eco-friendly inks, such as soy or vegetable-based inks, are gaining popularity due to their lower environmental footprint. Buyers should inquire about ink types to align with sustainability goals and consumer preferences.
What Are Common Trade Terms in Book Manufacturing?
Familiarity with trade terminology enhances communication and negotiation with manufacturers. Here are key terms every B2B buyer should know:
1. OEM (Original Equipment Manufacturer): What Does It Signify?
OEM refers to companies that produce products that are sold under another company’s brand. In the book manufacturing context, this means a manufacturer can produce books according to your specifications, allowing for customized branding and design. Understanding OEM agreements can help businesses maintain brand identity while leveraging the manufacturer’s expertise.
2. MOQ (Minimum Order Quantity): How Does It Affect Your Purchasing Decisions?
MOQ is the smallest quantity of a product that a supplier is willing to sell. For book manufacturers, MOQs can vary significantly based on the complexity and type of book. Understanding MOQs is essential for budget management, especially for smaller publishers or startups.
3. RFQ (Request for Quotation): Why Is It Essential?
An RFQ is a formal request for pricing from suppliers. It outlines your specific requirements, including quantities, materials, and deadlines. Sending an RFQ to multiple manufacturers can provide comparative pricing, helping buyers make informed decisions.
4. Incoterms: How Do They Affect Shipping and Delivery?
Incoterms are internationally recognized terms that define the responsibilities of buyers and sellers in shipping agreements. They clarify aspects such as who is responsible for shipping costs, insurance, and customs duties. Understanding these terms is vital for international buyers to avoid unexpected expenses and delays.
5. Lead Time: What Is Its Significance in Book Production?
Lead time refers to the time taken from placing an order to the delivery of the product. In book manufacturing, lead times can vary based on production schedules and complexity. Buyers should consider lead times in their planning to ensure timely availability of products for market launches or promotions.
By grasping these technical properties and trade terms, international B2B buyers can navigate the complexities of book manufacturing more effectively, leading to better purchasing decisions and successful partnerships.
Navigating Market Dynamics and Sourcing Trends in the book manufacturer Sector
What Are the Current Market Dynamics and Sourcing Trends in the Book Manufacturing Sector?
The book manufacturing sector is experiencing significant transformations driven by technology advancements, shifting consumer preferences, and global market dynamics. In recent years, the rise of digital publishing has reshaped traditional print methods, prompting manufacturers to adopt more flexible and efficient production techniques. International B2B buyers from regions such as Africa, South America, the Middle East, and Europe are increasingly seeking suppliers who can offer innovative solutions, such as on-demand printing and digital integration, which allow for reduced lead times and lower inventory costs.
Emerging technologies such as artificial intelligence and automation are streamlining operations, improving quality control, and enhancing supply chain management. Buyers should consider suppliers who leverage these technologies to ensure competitive pricing and timely delivery. Additionally, there is a growing trend towards customization, with businesses looking for manufacturers that can produce tailored products to meet specific market demands.
As global sourcing becomes more prevalent, buyers must navigate various regulatory environments and trade agreements that affect pricing and availability. Understanding local market conditions and establishing relationships with reliable manufacturers will be crucial for mitigating risks associated with currency fluctuations and geopolitical tensions.
How Is Sustainability and Ethical Sourcing Impacting the Book Manufacturing Industry?
Sustainability has become a key consideration for B2B buyers in the book manufacturing sector. The environmental impact of paper production and book printing processes is significant, with deforestation and waste generation being major concerns. Buyers are increasingly prioritizing suppliers who implement sustainable practices, such as using recycled materials, eco-friendly inks, and energy-efficient production methods.
Ethical sourcing is equally important, as consumers demand transparency in the supply chain. Manufacturers that adhere to ethical labor practices and ensure fair wages for workers are gaining favor among international buyers. Certifications such as Forest Stewardship Council (FSC) and Sustainable Forestry Initiative (SFI) are becoming essential for companies looking to demonstrate their commitment to sustainability.
Buyers should engage with manufacturers who can provide detailed information about their sourcing practices and certifications. This not only enhances brand reputation but also aligns with the growing consumer demand for environmentally responsible products.
How Has the Book Manufacturing Sector Evolved Over Time?
The evolution of the book manufacturing sector has been marked by significant technological advancements and changes in consumer behavior. Initially dominated by traditional printing methods, the industry has gradually integrated digital technologies, allowing for greater flexibility and efficiency in production. The introduction of print-on-demand services has revolutionized the way books are produced, enabling publishers to minimize waste and respond rapidly to market demands.
Moreover, the rise of e-books and digital content has compelled traditional manufacturers to adapt, leading to a convergence of print and digital technologies. This evolution has opened new avenues for international B2B buyers, providing opportunities to partner with manufacturers that offer both print and digital solutions tailored to diverse markets.
In summary, the book manufacturing sector continues to navigate a landscape influenced by technology, sustainability, and evolving consumer preferences, presenting unique opportunities for international B2B buyers. Understanding these dynamics is essential for making informed sourcing decisions that align with global trends and ethical standards.
Frequently Asked Questions (FAQs) for B2B Buyers of book manufacturer
-
How do I choose the right book manufacturer for my business needs?
When selecting a book manufacturer, consider factors such as production capacity, quality of materials, and previous client reviews. Assess their ability to meet your specific requirements, such as custom sizes, binding types, and cover finishes. Additionally, inquire about their experience in your niche, as manufacturers with industry-specific expertise may provide better insights and suggestions. -
What factors should I consider when determining the minimum order quantity (MOQ) with a book manufacturer?
MOQs can vary widely between manufacturers. It’s essential to evaluate your budget, storage capabilities, and market demand. If you’re a startup, discuss options for smaller runs to mitigate risk. Consider factors like production lead times and costs per unit, as lower MOQs may result in higher prices. Always negotiate to find a balance that suits your needs. -
What types of customization options are available when working with book manufacturers?
Most book manufacturers offer a range of customization options, including cover materials, sizes, paper types, binding methods, and printing techniques. Some may also provide services like embossing, foil stamping, or custom illustrations. Discuss your specific requirements with the manufacturer to understand their capabilities and ensure they can deliver your vision effectively. -
How can I ensure quality assurance when sourcing books from manufacturers?
Quality assurance is critical in maintaining product standards. Request samples before placing a large order to evaluate the print quality, paper durability, and overall craftsmanship. Establish clear quality control protocols, including inspections at various production stages. Additionally, consider certifications or industry standards the manufacturer adheres to, which can provide added assurance of their commitment to quality. -
What payment terms should I expect when dealing with international book manufacturers?
Payment terms can vary significantly. Typically, manufacturers may require a deposit (often 30-50%) upfront, with the balance due upon completion or delivery. Some may offer flexible terms based on your relationship or order size. Always clarify payment methods accepted, such as bank transfers, letters of credit, or online payment platforms, to ensure smooth transactions. -
How do logistics and shipping work when importing books from manufacturers?
Logistics can be complex, involving freight forwarders and customs regulations. Discuss shipping options with your manufacturer, including incoterms like FOB (Free On Board) or CIF (Cost, Insurance, and Freight). Plan for potential delays by considering lead times for production and shipping. Research import duties and taxes in your country to avoid unexpected costs upon arrival. -
What are the common challenges in international trade when sourcing books?
Common challenges include navigating customs regulations, managing currency fluctuations, and ensuring timely communication across different time zones. Additionally, language barriers may pose difficulties in negotiations. Establishing a reliable supply chain and maintaining transparent communication with your manufacturer can help mitigate these issues. Consider working with local partners or consultants familiar with the region. -
How can I build a long-term relationship with a book manufacturer?
Building a long-term partnership involves consistent communication, transparency, and mutual respect. Provide constructive feedback and recognize their efforts in meeting your needs. Discuss future projects and explore opportunities for collaboration on new titles or formats. Additionally, maintaining regular check-ins can help strengthen the relationship, fostering loyalty and better pricing in the long run.
Important Disclaimer & Terms of Use
⚠️ Important Disclaimer
The information provided in this guide, including content regarding manufacturers, technical specifications, and market analysis, is for informational and educational purposes only. It does not constitute professional procurement advice, financial advice, or legal advice.
While we have made every effort to ensure the accuracy and timeliness of the information, we are not responsible for any errors, omissions, or outdated information. Market conditions, company details, and technical standards are subject to change.
B2B buyers must conduct their own independent and thorough due diligence before making any purchasing decisions. This includes contacting suppliers directly, verifying certifications, requesting samples, and seeking professional consultation. The risk of relying on any information in this guide is borne solely by the reader.
Strategic Sourcing Conclusion and Outlook for book manufacturer
In the dynamic landscape of book manufacturing, strategic sourcing emerges as a critical component for international B2B buyers. By leveraging a well-structured sourcing strategy, businesses can enhance their procurement processes, optimize costs, and ensure quality. Understanding the diverse needs of different markets—such as those in Africa, South America, the Middle East, and Europe—allows buyers to tailor their sourcing approaches effectively.
As you navigate the complexities of sourcing, consider the importance of establishing strong relationships with manufacturers who prioritize sustainability and innovation. This not only aligns with global trends but also enhances your brand’s reputation and appeal.
Looking ahead, the book manufacturing industry is poised for growth, driven by technological advancements and changing consumer preferences. Now is the time for international buyers to engage proactively with suppliers and explore new opportunities. Embrace this moment to refine your sourcing strategies and secure your position in a competitive market. Your next step could be the key to unlocking greater value and efficiency in your supply chain.