Unlocking Value: The Complete Sierra Denali Custom Guide (2025)
Introduction: Navigating the Global Market for sierra denali custom
Navigating the global market for Sierra Denali custom products can be a daunting task for B2B buyers, especially those operating in diverse regions such as Africa, South America, the Middle East, and Europe. With the rising demand for tailored solutions that meet specific business needs, finding reliable suppliers while ensuring quality and cost-effectiveness is crucial. This guide is designed to address these challenges by offering comprehensive insights into the types of Sierra Denali custom products available, their various applications, and essential criteria for supplier vetting.
In this resource, we delve into the nuances of the Sierra Denali custom landscape, providing a thorough analysis of market trends, pricing structures, and key performance indicators. Buyers will gain valuable knowledge on how to assess suppliers based on quality certifications, production capabilities, and customer service excellence. Furthermore, the guide emphasizes the importance of understanding regional differences in logistics and market access, which can significantly impact purchasing decisions.
By equipping international B2B buyers with actionable insights and strategic approaches, this guide empowers them to make informed purchasing decisions. Whether you’re based in Mexico looking to diversify your supplier base or in Spain seeking innovative custom solutions, understanding the intricacies of the Sierra Denali market will enhance your procurement strategy and drive business success.
Understanding sierra denali custom Types and Variations
Type Name | Key Distinguishing Features | Primary B2B Applications | Brief Pros & Cons for Buyers |
---|---|---|---|
Sierra Denali Custom 1500 | Full-size truck, advanced safety features, luxury interior | Construction, logistics, and transportation | Pros: High towing capacity, comfort. Cons: Higher initial investment. |
Sierra Denali Custom 2500 | Heavy-duty capability, robust engine options, premium tech | Heavy equipment transport, fleet operations | Pros: Superior payload, reliability. Cons: Lower fuel efficiency. |
Sierra Denali Custom 3500 | Maximum towing capacity, dual-rear wheels option | Large-scale logistics, heavy-duty applications | Pros: Exceptional durability, versatile. Cons: Larger size can limit maneuverability. |
Sierra Denali Custom Elevation | Sporty design, advanced connectivity features | Urban delivery services, tech-oriented businesses | Pros: Modern aesthetics, tech-savvy. Cons: Less rugged than other variants. |
Sierra Denali Custom AT4 | Off-road capabilities, aggressive styling, enhanced suspension | Adventure tourism, outdoor equipment transport | Pros: Off-road versatility, unique design. Cons: May not suit all urban applications. |
What Are the Key Characteristics of Sierra Denali Custom 1500?
The Sierra Denali Custom 1500 is designed for businesses that require a balance of luxury and performance. With its advanced safety features and a comfortable interior, it is ideal for transportation and logistics sectors. Companies should consider its impressive towing capacity, making it suitable for hauling trailers and equipment. However, the higher initial investment may be a concern for budget-conscious buyers.
How Does the Sierra Denali Custom 2500 Stand Out?
The Sierra Denali Custom 2500 is tailored for heavy-duty applications, featuring a robust engine and premium technology. It is particularly well-suited for industries that need to transport heavy equipment or operate fleets. Buyers should note its superior payload capabilities, which enhance productivity. However, its lower fuel efficiency may impact operational costs, making it essential to evaluate total cost of ownership.
Why Choose the Sierra Denali Custom 3500?
For businesses requiring maximum towing capacity, the Sierra Denali Custom 3500 is the go-to option. Its dual-rear wheels provide enhanced stability, making it perfect for large-scale logistics and heavy-duty applications. While its exceptional durability and versatility make it appealing, potential buyers should consider the vehicle’s larger size, which may limit maneuverability in urban settings.
What Are the Benefits of the Sierra Denali Custom Elevation?
The Sierra Denali Custom Elevation targets urban delivery services and tech-oriented businesses with its sporty design and advanced connectivity features. This variant offers modern aesthetics that can enhance brand image. However, businesses should be aware that its less rugged nature may not be suitable for all operational environments, particularly those requiring heavy-duty performance.
How Does the Sierra Denali Custom AT4 Cater to Off-Road Needs?
The Sierra Denali Custom AT4 is designed for companies involved in adventure tourism or outdoor equipment transport, featuring off-road capabilities and aggressive styling. Its enhanced suspension allows for superior performance on rugged terrains. While it offers versatility for off-road applications, businesses should consider whether its design aligns with their operational needs, especially in urban environments.
Related Video: CUSTOM GMC DUALLY | The 2021 Sierra 3500 Denali With FULL Chrome Delete
Key Industrial Applications of sierra denali custom
Industry/Sector | Specific Application of sierra denali custom | Value/Benefit for the Business | Key Sourcing Considerations for this Application |
---|---|---|---|
Automotive | Custom Vehicle Modifications | Enhanced brand differentiation and customer loyalty | Compliance with local regulations and standards |
Renewable Energy | Solar Panel Mounting Structures | Increased efficiency and durability of installations | Material quality and resistance to environmental factors |
Construction | Prefabricated Building Components | Reduced construction time and labor costs | Supply chain reliability and logistical support |
Telecommunications | Custom Enclosures for Equipment | Improved equipment protection and operational efficiency | Compatibility with existing systems and scalability |
Agriculture | Precision Farming Tools | Optimized resource use and increased yield | Adaptability to local farming practices and climate conditions |
How is Sierra Denali Custom Used in the Automotive Sector?
In the automotive industry, Sierra Denali Custom applications focus on vehicle modifications tailored to meet specific customer needs. By providing custom body kits, enhanced performance features, or personalized interiors, businesses can significantly differentiate their offerings in a competitive market. This customization not only enhances brand loyalty but also allows manufacturers to cater to diverse consumer preferences across international markets such as Mexico and Spain. Buyers must ensure compliance with local regulations and standards to avoid costly modifications post-production.
What Role Does Sierra Denali Custom Play in Renewable Energy?
In the renewable energy sector, Sierra Denali Custom is pivotal in creating robust solar panel mounting structures. These custom solutions are designed to withstand varying environmental conditions, thus ensuring the efficiency and durability of solar installations. For international buyers from Africa and the Middle East, sourcing high-quality materials that can resist extreme weather is crucial. Additionally, understanding local installation practices can help optimize the performance of these structures, leading to better energy yield.
How Does Sierra Denali Custom Benefit the Construction Industry?
Sierra Denali Custom applications in construction include prefabricated building components that streamline the building process. By utilizing custom-designed elements, companies can significantly reduce construction time and associated labor costs. This is particularly beneficial for projects in Europe where efficiency is key to meeting tight deadlines. Buyers should prioritize sourcing from suppliers who can guarantee timely delivery and maintain high standards of quality to ensure structural integrity.
How is Sierra Denali Custom Applied in Telecommunications?
In telecommunications, Sierra Denali Custom provides specialized enclosures for equipment protection. These custom solutions safeguard sensitive devices from environmental hazards, enhancing operational efficiency. For businesses, especially in emerging markets, ensuring compatibility with existing systems is vital for seamless integration. Buyers should consider scalability and adaptability to accommodate future technology upgrades, ensuring long-term investment viability.
What Are the Benefits of Sierra Denali Custom in Agriculture?
In agriculture, Sierra Denali Custom is utilized for precision farming tools designed to optimize resource use and increase crop yields. Custom solutions can be tailored to specific farming practices prevalent in regions across South America and Africa, addressing unique agricultural challenges. Buyers should focus on sourcing adaptable tools that can integrate with local farming techniques and withstand diverse climate conditions, ensuring effective and sustainable agricultural practices.
Related Video: Top 4 BEST Exhaust Set Ups for GMC Sierra Denali 6.2L V8
3 Common User Pain Points for ‘sierra denali custom’ & Their Solutions
Scenario 1: Difficulty in Customization Options for Diverse Markets
The Problem: B2B buyers from regions like Africa and South America often struggle with the limited customization options available for the Sierra Denali Custom. These markets have unique consumer preferences and cultural nuances that require tailored solutions. Buyers may find that the standard offerings do not align with local tastes or functional needs, leading to dissatisfaction and lost sales opportunities.
The Solution: To effectively address this challenge, buyers should engage directly with manufacturers or authorized dealers to explore customization capabilities. It is essential to communicate specific regional requirements, such as preferred materials, color schemes, or functional features. Building a collaborative relationship with suppliers can also facilitate the development of bespoke solutions that cater to local demands. Buyers should consider forming focus groups with local customers to gather insights, which can then be presented to the supplier for a more tailored product offering. This proactive approach not only ensures product relevance but also enhances customer loyalty.
Scenario 2: Challenges in Product Sourcing and Delivery Timelines
The Problem: For international buyers, especially those in the Middle East and Europe, sourcing the Sierra Denali Custom can be fraught with logistical hurdles. Delays in shipping, customs clearance, and unexpected tariffs can disrupt supply chains, leading to increased costs and prolonged lead times that impact business operations.
The Solution: To mitigate these issues, buyers should establish a robust logistics plan before placing orders. This includes identifying reliable freight forwarders with experience in handling automotive products and understanding regional customs regulations. It may also be beneficial to negotiate shipping terms that provide clarity on delivery timelines and responsibilities. Additionally, buyers can consider maintaining a safety stock of essential components to buffer against potential delays. Leveraging technology, such as supply chain management software, can help track shipments and anticipate potential disruptions, allowing for proactive decision-making.
Scenario 3: Difficulty in After-Sales Support and Service Availability
The Problem: After-sales support is crucial for B2B buyers investing in high-value items like the Sierra Denali Custom. Buyers in regions such as Africa may face challenges in accessing timely and effective support services, including warranty claims, repairs, or parts replacements. This gap can result in significant downtime and financial losses for businesses relying on the vehicle for operations.
The Solution: To ensure robust after-sales support, buyers should thoroughly investigate the support infrastructure of the suppliers they engage with. This includes evaluating the availability of service centers, the responsiveness of customer service teams, and the accessibility of spare parts. Buyers should also inquire about warranty terms and conditions, ensuring they understand the process for claiming repairs or replacements. Establishing a service-level agreement (SLA) with the supplier can further enhance support commitments. Additionally, creating a network of local mechanics trained in servicing the Sierra Denali Custom can provide an added layer of support and reduce reliance on distant service centers, ensuring that operations remain uninterrupted.
Strategic Material Selection Guide for sierra denali custom
When selecting materials for the Sierra Denali Custom, international B2B buyers must consider various factors that influence product performance, cost, and compliance with regional standards. Below, we analyze four common materials used in Sierra Denali Custom applications, focusing on their properties, advantages, disadvantages, and specific considerations for buyers from Africa, South America, the Middle East, and Europe.
What Are the Key Properties of Aluminum in Sierra Denali Custom Applications?
Aluminum is a lightweight material known for its excellent strength-to-weight ratio and corrosion resistance. Its temperature rating can reach up to 400°F (204°C), making it suitable for various applications. Aluminum is also non-magnetic and has good thermal conductivity, which can be advantageous in specific environments.
Pros & Cons: The primary advantage of aluminum is its durability and resistance to corrosion, which extends the lifespan of the product. However, it can be more expensive than other materials, and its manufacturing complexity may require specialized processes, increasing production costs.
Impact on Application: Aluminum is compatible with various media, making it ideal for applications in automotive and aerospace industries. However, its lower tensile strength compared to steel may limit its use in high-stress environments.
Considerations for International Buyers: Buyers must ensure compliance with regional standards such as ASTM and EN. Additionally, sourcing aluminum from local suppliers can mitigate import costs and reduce lead times.
How Does Stainless Steel Compare for Sierra Denali Custom Products?
Stainless steel is renowned for its exceptional corrosion resistance and high strength, making it suitable for demanding applications. Its temperature rating can exceed 1,500°F (815°C), allowing it to perform well under extreme conditions.
Pros & Cons: The key advantage of stainless steel is its durability and resistance to rust and corrosion, making it ideal for outdoor and marine applications. However, it tends to be heavier and more expensive than aluminum, which may not be suitable for all projects.
Impact on Application: Stainless steel is compatible with a wide range of media, including aggressive chemicals, making it a preferred choice in the food and beverage industry.
Considerations for International Buyers: Buyers should be aware of the various grades of stainless steel (e.g., 304, 316) and their respective compliance with international standards. Understanding local regulations regarding food safety can also influence material selection.
What Are the Benefits of Composite Materials for Sierra Denali Custom?
Composite materials, often made from a combination of fibers and resins, offer unique properties such as lightweight construction and high strength. They can withstand temperatures up to 300°F (149°C) depending on the resin used.
Pros & Cons: The main advantage of composites is their excellent strength-to-weight ratio, which can lead to reduced shipping costs and improved fuel efficiency in transport applications. However, they can be more expensive and complex to manufacture, requiring specialized knowledge and equipment.
Impact on Application: Composites are particularly suitable for applications where weight reduction is critical, such as in the aerospace and automotive sectors. However, compatibility with certain chemicals may limit their use.
Considerations for International Buyers: Buyers should verify the certifications of composite materials to ensure they meet local standards and regulations. Additionally, understanding the environmental impact and recyclability of composites can be crucial for sustainability-focused companies.
Why Is Polycarbonate a Viable Option for Sierra Denali Custom?
Polycarbonate is a thermoplastic material known for its high impact resistance and optical clarity. It can withstand temperatures ranging from -40°F to 240°F (-40°C to 116°C), making it versatile for various applications.
Pros & Cons: The key advantage of polycarbonate is its lightweight nature and high impact resistance, which makes it ideal for protective applications. However, it is less resistant to UV radiation unless treated, which can limit its outdoor use.
Impact on Application: Polycarbonate is suitable for applications requiring transparency, such as safety shields or protective covers. Its compatibility with various media is generally good, but care must be taken with solvents that may degrade the material.
Considerations for International Buyers: Buyers should ensure that polycarbonate materials comply with local safety standards, especially in regions with stringent regulations on plastics. Understanding the environmental impact and potential recycling options is also essential.
Summary Table of Material Selection for Sierra Denali Custom
Material | Typical Use Case for Sierra Denali Custom | Key Advantage | Key Disadvantage/Limitation | Relative Cost (Low/Med/High) |
---|---|---|---|---|
Aluminum | Automotive components | Lightweight and corrosion-resistant | Higher cost and manufacturing complexity | Medium |
Stainless Steel | Marine applications | Exceptional durability | Heavier and more expensive | High |
Composite | Aerospace parts | High strength-to-weight ratio | Expensive and complex to manufacture | High |
Polycarbonate | Protective covers | High impact resistance | Less UV resistance without treatment | Medium |
This strategic material selection guide provides essential insights for international B2B buyers, enabling informed decisions that align with both performance requirements and regional compliance standards.
In-depth Look: Manufacturing Processes and Quality Assurance for sierra denali custom
What Are the Main Stages of Manufacturing for Sierra Denali Custom?
The manufacturing process for Sierra Denali Custom products typically involves several key stages: material preparation, forming, assembly, and finishing. Understanding these stages is crucial for B2B buyers to ensure the quality and reliability of the products they source.
-
Material Preparation
The first stage involves selecting high-quality raw materials that meet specific industry standards. For Sierra Denali Custom, materials may include metals, plastics, or composites, depending on the product requirements. Suppliers often conduct rigorous material inspections to confirm compliance with international standards such as ASTM or ISO. Buyers should inquire about the material sourcing process and any certifications that the materials possess. -
Forming
This stage encompasses various techniques like machining, molding, or stamping to shape the raw materials into specific components. Advanced technologies, such as CNC machining and 3D printing, are increasingly utilized to enhance precision and efficiency. Buyers should assess whether the supplier employs modern forming techniques that can accommodate their unique specifications and volume needs. -
Assembly
After forming, components are assembled using methods like welding, adhesive bonding, or mechanical fastening. The choice of assembly technique can greatly influence the final product’s durability and performance. B2B buyers should ask about the assembly process and whether the supplier has automated systems in place to enhance consistency and reduce human error. -
Finishing
The final stage involves applying surface treatments such as painting, coating, or polishing. This not only improves the aesthetic appeal but also enhances corrosion resistance and durability. Buyers should ensure that the finishing processes align with their quality requirements and that the supplier can provide samples for approval.
How Is Quality Assurance Implemented in Sierra Denali Custom Manufacturing?
Quality assurance (QA) is a critical component of the manufacturing process, ensuring that products meet specific standards and customer expectations. For Sierra Denali Custom, several international and industry-specific standards guide the QA process.
-
What International Standards Are Relevant for Quality Assurance?
One of the most recognized standards is ISO 9001, which outlines requirements for a quality management system (QMS). This certification demonstrates a supplier’s commitment to consistent quality and customer satisfaction. Other relevant standards may include CE marking for products sold in Europe and API standards for the oil and gas industry. B2B buyers should prioritize suppliers with these certifications as they indicate adherence to stringent quality guidelines. -
What Are the Key Quality Control Checkpoints?
Quality control (QC) involves several checkpoints throughout the manufacturing process:
– Incoming Quality Control (IQC): This initial stage inspects raw materials upon arrival to ensure they meet specifications.
– In-Process Quality Control (IPQC): Continuous monitoring during manufacturing helps identify defects early, reducing waste and rework.
– Final Quality Control (FQC): The final inspection ensures that the completed product meets all quality standards before shipment. -
What Common Testing Methods Are Used?
Various testing methods are employed to assess product quality, including:
– Dimensional Inspection: Verifying that components meet specified measurements.
– Functional Testing: Ensuring that the product performs as intended under operational conditions.
– Durability Testing: Assessing how well the product withstands environmental stressors.
Buyers should request documentation of these tests to verify compliance with quality standards.
How Can B2B Buyers Verify Supplier Quality Control Practices?
To ensure that suppliers maintain high-quality standards, B2B buyers can take several proactive steps:
-
Conduct Supplier Audits
Regular audits can provide insights into the supplier’s manufacturing processes and quality control measures. Buyers should prepare a checklist based on industry standards to evaluate the supplier’s compliance effectively. -
Request Quality Assurance Reports
Suppliers should be willing to provide quality assurance reports detailing their QC processes, test results, and any corrective actions taken. This transparency builds trust and confidence in the supplier’s commitment to quality. -
Utilize Third-Party Inspection Services
Engaging third-party inspection firms can offer an unbiased assessment of the supplier’s quality control processes. These firms can conduct inspections at various stages of manufacturing, providing B2B buyers with a comprehensive overview of product quality.
What Are the Nuances of Quality Certification for International B2B Buyers?
B2B buyers from Africa, South America, the Middle East, and Europe should be aware of specific nuances when it comes to quality certification:
-
Understanding Regional Standards
Different regions may have varying quality standards and certifications. For instance, products entering the European market must comply with CE marking, while those in the Middle East may require GSO certification. Buyers should familiarize themselves with these regional requirements to ensure compliance. -
Navigating Certification Costs and Timelines
Obtaining quality certifications can be costly and time-consuming. Buyers should account for these factors when selecting suppliers. Understanding the supplier’s certification timeline can help buyers plan their procurement schedules effectively. -
Evaluating Supplier Experience with International Markets
Suppliers experienced in exporting to international markets are more likely to understand and comply with various quality standards. Buyers should assess the supplier’s track record in dealing with international clients, as this can significantly impact the reliability and quality of products.
Conclusion
For international B2B buyers, particularly from Africa, South America, the Middle East, and Europe, understanding the manufacturing processes and quality assurance practices for Sierra Denali Custom products is vital. By focusing on key manufacturing stages, relevant quality standards, and effective verification methods, buyers can make informed decisions that enhance their procurement strategies and ensure product reliability.
Practical Sourcing Guide: A Step-by-Step Checklist for ‘sierra denali custom’
This sourcing guide aims to equip international B2B buyers, particularly from Africa, South America, the Middle East, and Europe, with actionable insights for procuring the Sierra Denali Custom. The following checklist outlines critical steps to ensure a successful sourcing process, minimizing risks and maximizing value.
Step 1: Define Your Technical Specifications
Establishing clear technical specifications is essential to ensure that the Sierra Denali Custom meets your operational requirements. This includes dimensions, materials, performance standards, and any customization features you may need. Having detailed specifications helps in comparing suppliers and products effectively.
- Key considerations:
- Identify specific needs such as load capacity and engine specifications.
- Determine any regulatory compliance requirements in your region.
Step 2: Conduct Market Research
Understanding the market landscape is vital for informed decision-making. Research potential suppliers, their product offerings, and market reputation. This step helps identify competitive pricing and availability, enabling you to gauge where to find the best value.
- What to analyze:
- Supplier reviews and case studies from other B2B buyers.
- Trends in the Sierra Denali Custom market, including popular features and enhancements.
Step 3: Evaluate Potential Suppliers
Before making a commitment, thoroughly vet potential suppliers. Request detailed company profiles, product catalogs, and references from buyers in similar industries or regions. This step is crucial to ensure that the supplier is reliable and capable of meeting your requirements.
- Important factors to consider:
- Supplier certifications and quality assurance processes.
- Historical performance and customer satisfaction levels.
Step 4: Request Quotes and Compare Offers
Once you have shortlisted potential suppliers, request detailed quotes that include pricing, delivery timelines, and payment terms. Comparing these offers will provide insights into the best financial option while also highlighting differences in service levels and product features.
- What to look for:
- Hidden costs, such as shipping and customs fees.
- Flexibility in payment terms and conditions.
Step 5: Negotiate Terms and Conditions
Negotiation is a crucial step in securing favorable terms. Engage in discussions around pricing, delivery schedules, warranties, and after-sales support. Effective negotiation can lead to better deals and stronger partnerships.
- Focus areas during negotiation:
- Quantity discounts and bulk purchasing options.
- Guarantees on product quality and after-sales support.
Step 6: Verify Supplier Certifications
Ensuring that your chosen supplier has the necessary certifications is vital for compliance and quality assurance. This includes ISO certifications and any local regulatory approvals relevant to the Sierra Denali Custom.
- Why it matters:
- Certifications often indicate a commitment to quality and reliability.
- They can also be a legal requirement, depending on your market.
Step 7: Establish Communication Channels
Setting up clear communication channels with your supplier is crucial for ongoing collaboration. Discuss preferred methods of communication, response times, and points of contact. Effective communication can help prevent misunderstandings and foster a strong working relationship.
- Best practices:
- Use project management tools for transparency.
- Schedule regular check-ins to discuss progress and address any issues.
By following this comprehensive checklist, international B2B buyers can navigate the sourcing process for the Sierra Denali Custom with confidence, ensuring that they make informed decisions that align with their business needs.
Comprehensive Cost and Pricing Analysis for sierra denali custom Sourcing
When considering the comprehensive cost structure for sourcing Sierra Denali custom products, international B2B buyers must navigate various cost components that directly impact pricing. Understanding these elements is crucial for effective budgeting and ensuring a successful procurement strategy.
What Are the Key Cost Components in Sierra Denali Custom Sourcing?
-
Materials: The type of materials used is foundational in determining cost. Sierra Denali custom products may employ high-quality, durable materials that enhance performance but also increase the base cost. Buyers should assess the material specifications to ensure they align with their quality requirements while remaining within budget.
-
Labor: Labor costs can vary significantly based on the geographical location of the manufacturing facility. In regions with higher labor costs, such as parts of Europe, buyers may encounter higher prices. Conversely, sourcing from countries with lower labor costs may present opportunities for savings, albeit with potential trade-offs in quality or lead times.
-
Manufacturing Overhead: This encompasses all indirect costs associated with production, including utilities, rent, and administrative expenses. Understanding how these overheads are allocated in the pricing structure can help buyers evaluate the competitiveness of a supplier’s quote.
-
Tooling: Custom projects often require specialized tooling, which can add to the upfront cost. The tooling cost is typically amortized over the production run, so buyers should inquire about the minimum order quantity (MOQ) to optimize their investment.
-
Quality Control (QC): Rigorous quality assurance processes are essential for maintaining product standards. Suppliers who invest in comprehensive QC may charge a premium, but this can be a worthwhile investment to reduce defects and returns.
-
Logistics: Shipping and handling costs can greatly affect the total cost of ownership. Buyers should consider factors such as distance, shipping method, and potential tariffs or duties, particularly when sourcing internationally.
-
Margin: Finally, the supplier’s profit margin will influence the final price. Understanding typical margins in the industry can help buyers negotiate more effectively.
What Factors Influence the Pricing of Sierra Denali Custom Products?
-
Volume/MOQ: Pricing often benefits from economies of scale. Higher order volumes can lead to lower per-unit costs, making it essential for buyers to balance their needs with their budget constraints.
-
Specifications and Customization: Custom features can significantly alter pricing. Buyers should clearly define their specifications and understand how customization impacts costs, particularly regarding design complexity and production adjustments.
-
Materials and Quality Certifications: The quality and certification of materials used can affect pricing. Buyers should request documentation to verify compliance with international standards, particularly in industries where safety and quality are paramount.
-
Supplier Factors: The reputation and reliability of the supplier can also influence pricing. Established suppliers with proven track records may charge higher prices, but they may also offer better service and reliability.
-
Incoterms: The choice of Incoterms can impact overall costs. Understanding the responsibilities and risks associated with different shipping terms can help buyers make informed decisions and avoid unexpected expenses.
What Are the Best Negotiation Tips for International B2B Buyers?
-
Research and Benchmarking: Conduct thorough market research to understand average pricing and terms for Sierra Denali custom products. This knowledge will empower buyers during negotiations.
-
Focus on Total Cost of Ownership (TCO): Consider not just the purchase price but all associated costs, including shipping, customs, and potential maintenance. A supplier offering a slightly higher price may provide long-term savings through superior quality or reliability.
-
Build Relationships: Establishing strong relationships with suppliers can lead to better pricing and terms. Trust can facilitate negotiations and foster long-term partnerships.
-
Be Clear and Direct: Clearly communicate your needs and expectations from the outset. This clarity can prevent misunderstandings and streamline the negotiation process.
-
Understand Regional Pricing Nuances: Be aware of regional pricing dynamics, especially when sourcing from diverse markets in Africa, South America, the Middle East, and Europe. Factors such as local economic conditions, currency fluctuations, and trade regulations can influence costs.
Disclaimer on Indicative Prices
Pricing for Sierra Denali custom products can vary widely based on the aforementioned factors. Buyers should treat any indicative prices as a starting point for discussions rather than fixed costs. Engaging directly with suppliers for tailored quotes will yield the most accurate and relevant pricing information.
Alternatives Analysis: Comparing sierra denali custom With Other Solutions
Understanding Alternative Solutions to Sierra Denali Custom
In the landscape of B2B solutions, it’s essential for international buyers to explore various alternatives to a specific product or method. This not only helps in making informed purchasing decisions but also ensures that businesses can find the best fit for their operational needs. The Sierra Denali Custom, while a strong contender, may not always be the best option for every organization. Below, we compare it with two viable alternatives to provide a comprehensive understanding of their features and benefits.
Comparison Table of Sierra Denali Custom and Alternatives
Comparison Aspect | Sierra Denali Custom | Alternative 1: Custom Solution A | Alternative 2: Off-the-Shelf Solution B |
---|---|---|---|
Performance | High performance with tailored features | Moderate performance, highly adaptable | Good performance, limited customization |
Cost | Premium pricing for custom development | Variable costs, potentially lower | Fixed pricing, generally more affordable |
Ease of Implementation | Requires significant time and expertise | Moderate complexity, requires some training | Quick to implement, user-friendly |
Maintenance | Ongoing support needed, higher maintenance | Moderate maintenance, flexible support | Low maintenance, standard support |
Best Use Case | Large enterprises needing specific functionalities | Medium-sized businesses needing flexibility | Small to medium businesses with standard needs |
In-Depth Analysis of Alternatives
What are the Advantages and Disadvantages of Custom Solution A?
Custom Solution A is designed for businesses that prioritize flexibility and adaptability over specific performance metrics. The primary advantage of this alternative is its ability to evolve with the company’s changing needs. Businesses can modify features as their requirements grow. However, it may lack the high performance of the Sierra Denali Custom and could require more training for staff, making the initial phase challenging.
How Does Off-the-Shelf Solution B Compare?
Off-the-Shelf Solution B offers a balance between cost and performance, making it ideal for small to medium-sized enterprises. The main advantage of this solution is its quick implementation; businesses can start using the product almost immediately. However, it lacks the customization options that Sierra Denali Custom provides, which may be a drawback for companies with unique operational needs. The fixed pricing model also makes budgeting easier, but it may not offer the same scalability as the other two options.
How to Choose the Right Solution for Your Business Needs?
When selecting between Sierra Denali Custom and its alternatives, international B2B buyers should consider their specific operational requirements, budget constraints, and the level of customization needed. Large enterprises with unique needs may find the Sierra Denali Custom to be the best fit, despite its higher cost and maintenance requirements. On the other hand, medium-sized businesses might benefit from the adaptability of Custom Solution A, while small to medium enterprises seeking a cost-effective option may prefer Off-the-Shelf Solution B for its ease of use and implementation.
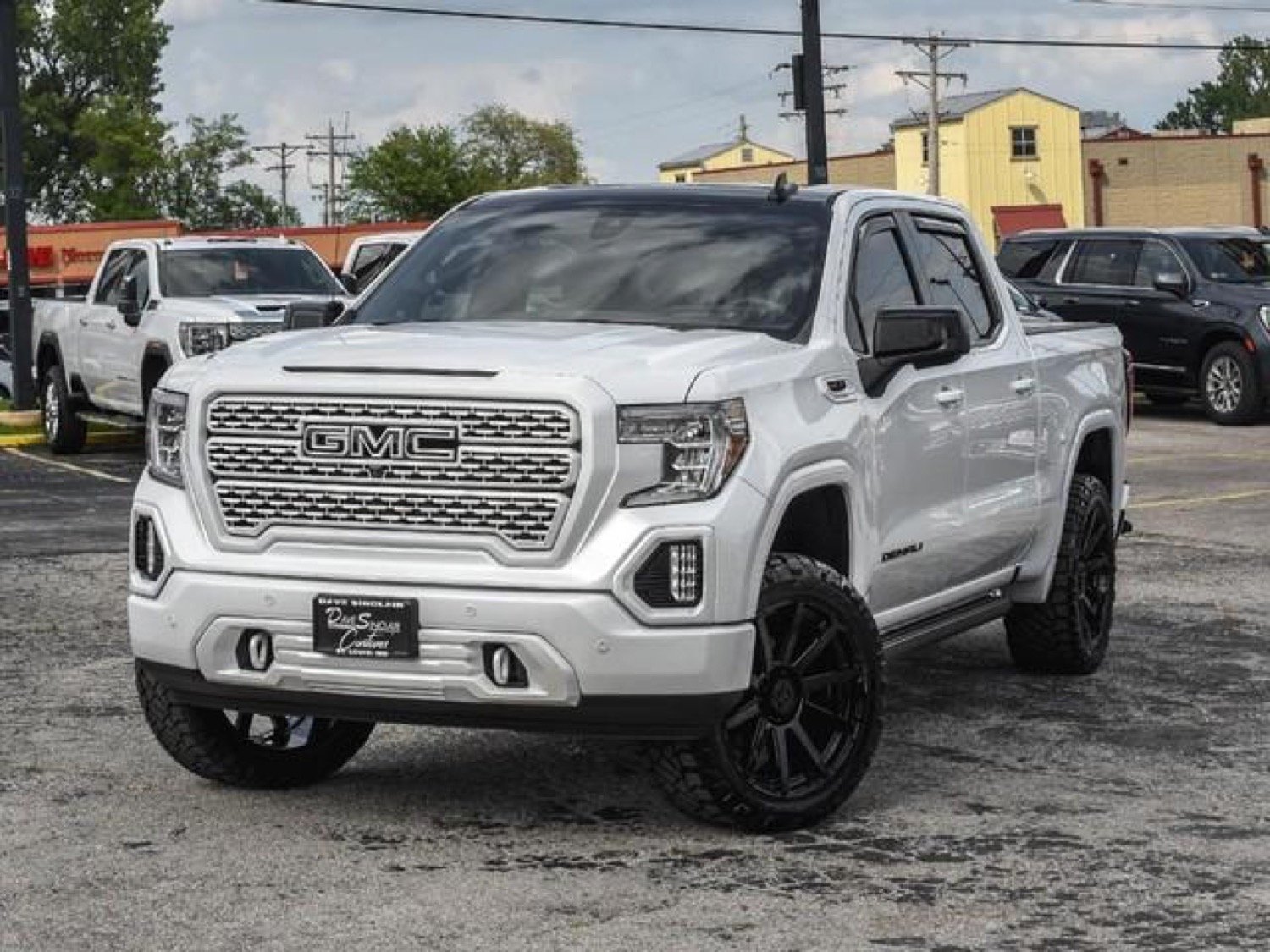
A stock image related to sierra denali custom.
In summary, understanding the nuances of each solution helps buyers make informed decisions that align with their business strategies and operational goals. By carefully evaluating performance, cost, ease of implementation, maintenance, and best use cases, businesses can choose a solution that not only meets their current needs but also supports future growth.
Essential Technical Properties and Trade Terminology for sierra denali custom
What Are the Essential Technical Properties of Sierra Denali Custom?
When evaluating Sierra Denali Custom products, understanding their technical properties is crucial for making informed purchasing decisions. Below are some key specifications to consider:
1. Material Grade: What Does It Mean for Durability?
The material grade of Sierra Denali Custom refers to the classification of the raw materials used in production. This can include metals, plastics, or composites, each with unique properties that affect strength, weight, and corrosion resistance. For B2B buyers, selecting the right material grade ensures the product meets specific performance standards, ultimately impacting the longevity and reliability of the end-use application.
2. Tolerance: Why Is Precision Important in Manufacturing?
Tolerance indicates the permissible limit of variation in a physical dimension of the product. It is a critical specification that affects the interchangeability of parts and overall product quality. For international B2B buyers, understanding tolerance levels is essential, as tighter tolerances often equate to higher manufacturing costs but provide greater precision, which can be crucial in sectors like aerospace or automotive.
3. Finish: How Does Surface Treatment Affect Performance?
The finish of Sierra Denali Custom products refers to the surface quality and treatment applied post-manufacturing, such as anodizing or powder coating. This not only enhances aesthetic appeal but also improves durability and resistance to environmental factors. Buyers must consider the finish, as it can significantly impact maintenance costs and the product’s lifespan, especially in harsh conditions typical in Africa and the Middle East.
4. Weight Capacity: What Should Buyers Know About Load Limits?
Weight capacity is the maximum load a product can safely support without failure. This specification is vital for industries that rely on structural integrity, such as construction or logistics. Understanding weight capacity helps B2B buyers ensure that the products they procure can handle operational demands, reducing the risk of costly failures or accidents.
5. Performance Standards: How Do They Ensure Quality?
Performance standards are benchmarks that products must meet to be deemed acceptable for specific applications. These may include industry certifications or compliance with international standards. For buyers, understanding these standards is crucial for risk management, ensuring that the products will perform adequately in their intended applications and meet regulatory requirements.
What Are Common Trade Terms Used in Sierra Denali Custom Transactions?
Familiarity with industry terminology can streamline negotiations and improve communication between buyers and suppliers. Here are some essential trade terms:
1. OEM (Original Equipment Manufacturer): What Role Does It Play?
OEM refers to companies that produce parts or equipment that may be marketed by another manufacturer. In the context of Sierra Denali Custom, knowing whether a supplier operates as an OEM can help buyers identify potential sources for customized products, ensuring compatibility and quality.
2. MOQ (Minimum Order Quantity): Why Is It Important for Bulk Purchases?
MOQ signifies the smallest quantity of a product that a supplier is willing to sell. This term is particularly important for B2B buyers looking to manage inventory costs. Understanding the MOQ helps buyers negotiate better terms and optimize their procurement strategies, especially when entering new markets or expanding operations.
3. RFQ (Request for Quotation): How Does It Facilitate Pricing Transparency?
An RFQ is a document used to invite suppliers to bid on specific products or services. For international buyers, submitting an RFQ can clarify pricing and terms, enabling better comparisons between suppliers. This process enhances transparency and aids in making informed purchasing decisions.
4. Incoterms: What Do They Mean for International Shipping?
Incoterms are a series of international commercial terms that define the responsibilities of buyers and sellers in global trade. They specify who is responsible for shipping, insurance, and tariffs. For B2B buyers, understanding Incoterms is essential for managing shipping costs and logistics, ensuring that all parties are aligned on their obligations.
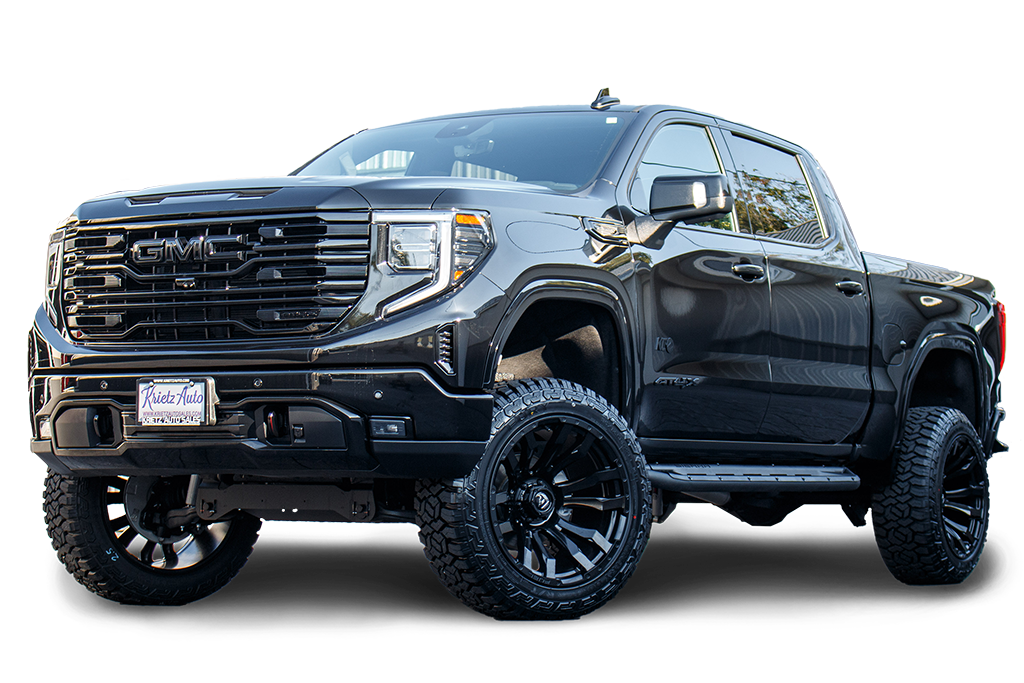
A stock image related to sierra denali custom.
By grasping these essential technical properties and trade terms, international B2B buyers can navigate the complexities of sourcing Sierra Denali Custom products more effectively, ultimately leading to better purchasing decisions and optimized supply chains.
Navigating Market Dynamics and Sourcing Trends in the sierra denali custom Sector
What Are the Current Market Dynamics and Key Trends in the Sierra Denali Custom Sector?
The Sierra Denali custom sector is experiencing significant growth driven by a combination of global demand for personalized solutions and advancements in B2B technology. Buyers from regions such as Africa, South America, the Middle East, and Europe (notably Mexico and Spain) are increasingly seeking customized products that align with their unique operational needs. This trend is fueled by a shift towards digital transformation, where technologies like AI and machine learning are optimizing supply chain management and enhancing product customization capabilities.
Emerging trends indicate that buyers are prioritizing flexibility in sourcing. The rise of e-commerce platforms and digital marketplaces has made it easier for international buyers to connect with manufacturers, enabling them to access a wider range of custom options. Additionally, there is a growing emphasis on data analytics, which helps businesses understand consumer preferences and market demands, allowing for more tailored offerings. Understanding these dynamics is crucial for B2B buyers to make informed purchasing decisions and to stay competitive in a rapidly changing market landscape.
How Is Sustainability Shaping the Sourcing Strategies in the Sierra Denali Custom Sector?
Sustainability has become a central focus for B2B buyers in the Sierra Denali custom sector, particularly for those looking to enhance their brand reputation and meet regulatory demands. International buyers are increasingly aware of the environmental impact of their sourcing choices, prompting a shift towards ethical supply chains. This includes selecting suppliers that prioritize sustainable practices, such as using eco-friendly materials and minimizing waste in production processes.
The importance of green certifications and materials cannot be overstated. Buyers are now more inclined to partner with manufacturers that possess recognized certifications, such as ISO 14001 for environmental management or FSC certification for sustainable forestry practices. These certifications not only assure buyers of responsible sourcing but also appeal to end consumers who are increasingly making purchasing decisions based on sustainability. By integrating sustainability into their sourcing strategies, international B2B buyers can enhance their market position and contribute positively to global environmental efforts.
What Is the Historical Context of the Sierra Denali Custom Sector for B2B Buyers?
The Sierra Denali custom sector has evolved significantly over the past few decades. Initially characterized by limited customization options and traditional manufacturing processes, the industry has transformed with the advent of technology and changing consumer preferences. As globalization expanded, so did the opportunities for international collaboration and the sharing of innovative practices.
In the early 2000s, the introduction of advanced manufacturing techniques, such as 3D printing and CNC machining, revolutionized the customization landscape, allowing for greater precision and flexibility. This evolution has enabled B2B buyers to source highly personalized products that cater specifically to their operational requirements. Understanding this historical context is vital for current buyers as it highlights the trajectory of innovation and the importance of adapting to ongoing changes in the market.
Frequently Asked Questions (FAQs) for B2B Buyers of sierra denali custom
-
How do I ensure the quality of Sierra Denali Custom products?
To guarantee the quality of Sierra Denali Custom products, start by requesting samples before committing to a larger order. Verify the supplier’s certifications, such as ISO or industry-specific standards, which indicate adherence to quality management practices. It’s also beneficial to conduct a factory audit if possible, or use third-party inspection services to assess product quality before shipment. Establishing clear quality assurance parameters in your contract can help set expectations and reduce the risk of receiving subpar products. -
What are the typical payment terms for Sierra Denali Custom orders?
Payment terms for Sierra Denali Custom orders can vary significantly based on the supplier and the order size. Common arrangements include a 30% deposit upfront with the balance due upon delivery or after inspection. For larger orders, suppliers may offer more flexible terms, including letters of credit or staggered payments based on production milestones. Always clarify payment methods accepted (bank transfer, PayPal, etc.) and ensure terms are documented in your contract to prevent misunderstandings. -
What is the minimum order quantity (MOQ) for Sierra Denali Custom products?
The MOQ for Sierra Denali Custom products typically ranges from 100 to 500 units, depending on the supplier and the complexity of customization. Some suppliers may offer lower MOQs for initial orders to build relationships, while others might require higher quantities to justify production costs. Always communicate your needs clearly and negotiate if necessary, especially if you are entering a new market or trying to establish a long-term partnership. -
How can I vet suppliers of Sierra Denali Custom products effectively?
To vet suppliers effectively, start by researching their reputation through online reviews and industry forums. Request references from previous clients and check their business credentials. Conducting background checks on their operational history, financial stability, and production capabilities is crucial. Additionally, consider engaging with trade associations or chambers of commerce in their country for further insights, and if possible, visit their facilities to assess their operations firsthand. -
What logistics considerations should I keep in mind when sourcing Sierra Denali Custom products?
When sourcing Sierra Denali Custom products, consider factors like shipping times, costs, and customs regulations. It’s essential to understand the incoterms (International Commercial Terms) that will govern your shipment, such as FOB (Free on Board) or CIF (Cost, Insurance, and Freight). Additionally, factor in potential delays at customs, especially in regions like Africa or South America, where regulations may vary. Collaborating with a reliable freight forwarder can streamline logistics and help navigate these complexities effectively. -
How can I customize Sierra Denali Custom products to meet my specific needs?
Customization of Sierra Denali Custom products often involves discussing your specific requirements with the supplier early in the negotiation process. Provide detailed specifications, including material preferences, design elements, and functionality. Many suppliers offer design support or prototyping services to help visualize the final product. Ensure that all customization details are documented in your purchase agreement to prevent any discrepancies during production. -
What are the common challenges faced when sourcing Sierra Denali Custom products internationally?
Common challenges include language barriers, differing business practices, and varying quality standards. Additionally, navigating international shipping logistics and customs can be daunting, leading to potential delays and increased costs. To mitigate these issues, consider working with local intermediaries or consultants who understand the market and can facilitate smoother transactions. Establishing strong communication channels with your supplier is also crucial to address any issues promptly. -
What should I do if I encounter issues with my Sierra Denali Custom order?
If you encounter issues with your Sierra Denali Custom order, such as quality discrepancies or delivery delays, address them immediately with your supplier. Document all communications and concerns in writing to maintain a clear record. Most reputable suppliers will have a process for handling complaints or disputes, which may include refunds, replacements, or negotiations for future orders. If the situation cannot be resolved amicably, consider seeking mediation or legal advice to protect your interests.
Important Disclaimer & Terms of Use
⚠️ Important Disclaimer
The information provided in this guide, including content regarding manufacturers, technical specifications, and market analysis, is for informational and educational purposes only. It does not constitute professional procurement advice, financial advice, or legal advice.
While we have made every effort to ensure the accuracy and timeliness of the information, we are not responsible for any errors, omissions, or outdated information. Market conditions, company details, and technical standards are subject to change.
B2B buyers must conduct their own independent and thorough due diligence before making any purchasing decisions. This includes contacting suppliers directly, verifying certifications, requesting samples, and seeking professional consultation. The risk of relying on any information in this guide is borne solely by the reader.
Strategic Sourcing Conclusion and Outlook for sierra denali custom
As the landscape of global trade continues to evolve, the importance of strategic sourcing for Sierra Denali Custom cannot be overstated. International B2B buyers from Africa, South America, the Middle East, and Europe stand to gain significant competitive advantages by embracing a meticulous approach to sourcing. Key takeaways include the necessity of understanding regional market dynamics, building strong supplier relationships, and leveraging technology to streamline procurement processes.
Why is strategic sourcing vital for international buyers? It not only reduces costs but also enhances product quality and delivery times, crucial for maintaining market relevance. By actively engaging with local suppliers and fostering collaboration, businesses can adapt to regional needs while ensuring compliance with local regulations.
Looking ahead, businesses must remain agile and open to innovation. The future of strategic sourcing will likely involve greater reliance on data analytics and sustainability practices. For international B2B buyers, particularly those in emerging markets, now is the time to reassess sourcing strategies, invest in robust supplier networks, and commit to sustainable practices. This proactive approach will position businesses favorably in an increasingly interconnected global market.