Transform Your Space: The Ultimate Chair Custom Guide (2025)
Introduction: Navigating the Global Market for chair custom
In the increasingly competitive landscape of global commerce, sourcing custom chairs that meet specific ergonomic and aesthetic requirements can pose significant challenges for international B2B buyers. Whether you are looking for comfortable desk chairs to alleviate back pain or unique designs for hospitality venues, navigating the complexities of chair custom solutions is essential for enhancing workplace productivity and customer satisfaction. This comprehensive guide delves into the diverse types of custom chairs available, their various applications across industries, and effective strategies for supplier vetting, ensuring you make informed purchasing decisions.
Understanding the market dynamics is crucial for buyers from Africa, South America, the Middle East, and Europe, including countries like Argentina and Australia. This guide empowers you by providing actionable insights into cost considerations, quality standards, and design trends that are shaping the chair custom landscape. By leveraging this information, you can optimize your procurement strategies, align your purchases with your organization’s needs, and ultimately enhance your competitive edge in the market.
As you read through this guide, expect to gain a deeper understanding of how to identify reputable suppliers, assess product quality, and navigate logistical challenges. With a focus on delivering value and fostering successful partnerships, this resource is designed to help you confidently navigate the global market for custom chairs.
Understanding chair custom Types and Variations
Type Name | Key Distinguishing Features | Primary B2B Applications | Brief Pros & Cons for Buyers |
---|---|---|---|
Ergonomic Office Chairs | Adjustable height, lumbar support, swivel | Corporate offices, coworking spaces | Pros: Improves comfort and productivity; Cons: Higher initial investment. |
Accent Chairs | Unique designs, various materials (fabric, leather) | Hospitality, residential staging | Pros: Enhances aesthetic appeal; Cons: May require more frequent replacement. |
Dining Chairs | Sturdy construction, stackable options | Restaurants, event venues | Pros: Space-saving design; Cons: Limited customization options. |
Outdoor Chairs | Weather-resistant materials, easy to clean | Patios, outdoor dining areas | Pros: Durable in various climates; Cons: May lack comfort for extended use. |
Lounge Chairs | Wide seats, plush cushions, contemporary styles | Waiting areas, lounges | Pros: Provides relaxation space; Cons: Takes up more floor space. |
What Are Ergonomic Office Chairs and How Do They Benefit B2B Buyers?
Ergonomic office chairs are designed to support the natural posture of the user, featuring adjustable height, lumbar support, and swivel capabilities. These chairs are essential in corporate offices and coworking spaces where employees spend extended hours seated. When purchasing, B2B buyers should consider the chair’s adjustability, durability, and warranty options to ensure long-term satisfaction and productivity improvements.
How Do Accent Chairs Enhance Commercial Spaces?
Accent chairs are characterized by their unique designs and variety of materials, including fabric and leather. They are often used in hospitality settings and residential staging to create inviting atmospheres. For B2B buyers, the aesthetic appeal of accent chairs can significantly influence customer perceptions. However, it’s essential to balance style with durability, as these chairs may require more frequent replacement due to wear.
What Should B2B Buyers Know About Dining Chairs?
Dining chairs are typically designed for sturdiness and functionality, often featuring stackable options for space-saving. They are commonly used in restaurants and event venues where flexibility and durability are crucial. B2B buyers should evaluate the material quality and ease of maintenance, as these factors impact the longevity and overall cost-effectiveness of the investment.
Why Are Outdoor Chairs Essential for Commercial Use?
Outdoor chairs are crafted from weather-resistant materials and are designed for easy cleaning, making them ideal for patios and outdoor dining areas. For B2B buyers, investing in durable outdoor seating is critical for maintaining a welcoming environment in various climates. While they offer excellent durability, buyers should also consider comfort, as some outdoor chairs may not be suitable for prolonged use.
How Do Lounge Chairs Provide Value in Waiting Areas?
Lounge chairs are known for their wide seats and plush cushioning, making them perfect for waiting areas and lounges. They create a relaxed atmosphere that enhances customer experience in settings like clinics and hotels. When selecting lounge chairs, B2B buyers should assess the chair’s design, comfort level, and space requirements, as these factors will affect both customer satisfaction and overall space utilization.
Related Video: DIY Folding Adirondack Chair!
Key Industrial Applications of chair custom
Industry/Sector | Specific Application of chair custom | Value/Benefit for the Business | Key Sourcing Considerations for this Application |
---|---|---|---|
Hospitality | Custom lounge and dining chairs for restaurants | Enhances customer experience and brand image | Material durability, design aesthetics, local regulations |
Corporate Offices | Ergonomic office chairs tailored for employees | Increases productivity and employee satisfaction | Ergonomic certifications, customization options, bulk pricing |
Educational Institutions | Custom classroom seating for universities | Supports diverse learning environments | Flexibility in design, comfort, and durability |
Healthcare | Specialized chairs for patient comfort in clinics | Improves patient care and satisfaction | Compliance with health regulations, easy maintenance |
Event Planning | Customizable seating for events and conferences | Facilitates brand representation and attendee comfort | Portability, design versatility, rental agreements |
How is ‘chair custom’ utilized in the hospitality industry?
In the hospitality sector, custom lounge and dining chairs are essential for restaurants and hotels aiming to create a unique ambiance. These chairs can be designed to match the establishment’s theme, enhancing the overall customer experience and brand image. B2B buyers from regions like Africa and South America should consider sourcing materials that withstand high usage while adhering to local regulations on safety and durability.
What are the benefits of ergonomic office chairs in corporate offices?
Ergonomic office chairs tailored to employee needs are increasingly important in corporate environments. They not only promote health by reducing back pain but also boost productivity and employee satisfaction. International buyers, particularly from Europe and the Middle East, should prioritize suppliers that offer ergonomic certifications and customization options to fit their office aesthetics and employee preferences.
Why is custom seating crucial for educational institutions?
Custom classroom seating in educational institutions supports diverse learning environments by allowing for flexible arrangements and comfort. This adaptability is especially valuable for universities that host various activities. Buyers should ensure that the furniture is durable and easy to maintain, considering the high turnover of students and the need for longevity in investment.
How does ‘chair custom’ improve patient care in healthcare settings?
In healthcare, specialized chairs designed for patient comfort are vital in clinics and hospitals. These custom chairs can be adjusted for various medical needs, improving patient care and satisfaction. B2B buyers must focus on compliance with health regulations and the ease of maintenance, as these factors significantly impact the overall patient experience.
What role does customizable seating play in event planning?
Customizable seating is crucial in event planning, allowing organizers to tailor arrangements to specific themes or branding requirements. This flexibility not only enhances attendee comfort but also facilitates effective brand representation. Buyers should consider aspects like portability and design versatility, especially when sourcing for large-scale events across different regions.
Related Video: Sci6 Q3 – Characteristics and Uses of Simple Machines
3 Common User Pain Points for ‘chair custom’ & Their Solutions
Scenario 1: Difficulty in Achieving Desired Aesthetics and Functionality
The Problem:
B2B buyers often struggle with sourcing custom chairs that meet both aesthetic and functional requirements. For instance, a hotel chain in South America may desire chairs that align with their luxury brand image while also being durable enough for high foot traffic. This dual need can lead to frustration when suppliers offer generic options that lack the unique design and durability specifications required, resulting in a mismatch between the buyer’s vision and the products available.
The Solution:
To overcome this challenge, it’s essential for buyers to engage with manufacturers who specialize in bespoke solutions. Start by conducting thorough market research to identify suppliers known for their expertise in custom furniture design. Use detailed design briefs that specify materials, colors, and styles, along with practical considerations like load capacity and ease of maintenance. Collaborating with the design team can also facilitate the development of prototypes, allowing buyers to visualize the end product before committing to large orders. This proactive approach not only ensures the final product aligns with brand identity but also meets the functional demands of the environment.
Scenario 2: Long Lead Times and Supply Chain Delays
The Problem:
International buyers often face significant delays when ordering custom chairs, which can disrupt project timelines. For instance, a corporate office in Europe may require new seating for an upcoming product launch, but unexpected delays from the manufacturer can push back the entire schedule, leading to a scramble for last-minute solutions. This situation can cause not only logistical headaches but also financial repercussions if deadlines are missed.
The Solution:
To mitigate lead time issues, establish clear communication channels with your suppliers from the outset. Discuss timelines and set realistic expectations based on historical performance. It’s beneficial to have contingency plans in place, such as alternative suppliers or temporary seating solutions that can be used while waiting for the custom orders to arrive. Additionally, consider working with local manufacturers who can provide quicker turnaround times, or explore expedited shipping options if sourcing from overseas is necessary. Regular follow-ups during the production phase can also help keep the project on track.
Scenario 3: Navigating Compliance and Safety Standards
The Problem:
B2B buyers must often navigate a complex landscape of compliance and safety regulations when ordering custom chairs. For example, a healthcare facility in Africa may require chairs that adhere to specific health and safety standards, which can vary significantly by region. Failing to meet these regulations can result in costly fines and a negative impact on reputation, making this a critical concern for buyers.
The Solution:
To address compliance issues, buyers should invest time in understanding the regulatory landscape relevant to their industry and region. Engage with experts who can provide insights into local laws and standards applicable to furniture design. When sourcing custom chairs, ensure that suppliers are certified and can demonstrate compliance with relevant safety standards. Request documentation that verifies the materials and processes used meet these regulations. Furthermore, conducting site visits to factories can help buyers assess the quality control measures in place, ensuring that the products not only look good but are also safe for use in their intended environments.
Strategic Material Selection Guide for chair custom
What Are the Key Properties of Common Materials Used in Custom Chairs?
When selecting materials for custom chairs, it is essential to consider their key properties. Common materials include wood, metal, plastic, and upholstery fabrics. Each material has unique characteristics that influence performance, durability, and suitability for various applications.
Wood: A Classic Choice for Custom Chairs
Wood is a traditional material known for its aesthetic appeal and structural integrity. Key properties include high strength-to-weight ratio and natural insulation, making it suitable for various climates. However, wood can be susceptible to moisture and temperature fluctuations, potentially leading to warping or cracking.
Pros:
– Durable and long-lasting when properly maintained.
– Offers a timeless look that appeals to various markets.
– Can be sourced sustainably, enhancing brand image.
Cons:
– Higher cost compared to synthetic materials.
– Requires more complex manufacturing processes, which can increase lead times.
– Vulnerable to pests and environmental damage.
For international buyers, compliance with local regulations regarding sustainable sourcing is crucial. Buyers from Europe may prioritize certifications like FSC (Forest Stewardship Council) to ensure responsible sourcing.
Metal: Strength and Versatility in Custom Chair Design
Metal, particularly steel and aluminum, is favored for its strength and durability. Key properties include high resistance to impact and corrosion, making it ideal for outdoor and commercial applications. Metal chairs can withstand heavy use and harsh environments.
Pros:
– Highly durable and low maintenance.
– Can be easily molded into various designs, offering versatility.
– Ideal for modern aesthetics and industrial designs.
Cons:
– Can be cold and uncomfortable without proper upholstery.
– Higher manufacturing complexity, especially for intricate designs.
– Susceptible to rust if not properly treated.
B2B buyers from regions with high humidity, such as parts of Africa and the Middle East, should prioritize corrosion-resistant finishes. Compliance with ASTM standards for metal products is also essential.
Plastic: Lightweight and Cost-Effective Material for Custom Chairs
Plastic is a lightweight, cost-effective option that is gaining popularity in custom chair design. Key properties include resistance to moisture and easy cleaning, making it suitable for various environments, including outdoor settings.
Pros:
– Affordable and readily available.
– Easy to mold into various shapes and colors, allowing for creative designs.
– Resistant to weather and UV damage.
Cons:
– Generally less durable than wood or metal.
– May not provide the same aesthetic appeal as natural materials.
– Environmental concerns regarding recyclability and sustainability.
For international buyers, especially in South America, understanding local recycling regulations is important. Buyers should also consider the environmental impact and look for suppliers who use recycled plastics.
Upholstery Fabrics: Comfort and Design Flexibility in Custom Chairs
Upholstery fabrics, including leather, microfiber, and natural fibers, play a crucial role in the comfort and aesthetics of custom chairs. Key properties vary widely, with some fabrics offering high durability and stain resistance, while others provide a luxurious feel.
Pros:
– Enhances comfort and visual appeal.
– Wide variety of options allows for customization.
– Can be treated for stain and water resistance.
Cons:
– Some fabrics may require special care or cleaning.
– Quality can vary significantly, impacting durability.
– Higher-end fabrics can increase overall costs.
For B2B buyers, particularly in Europe, compliance with fire safety regulations for upholstery is critical. Buyers should also consider the fabric’s environmental impact, opting for sustainable options when possible.
Summary Table of Material Selection for Custom Chairs
Material | Typical Use Case for chair custom | Key Advantage | Key Disadvantage/Limitation | Relative Cost (Low/Med/High) |
---|---|---|---|---|
Wood | Residential and upscale commercial chairs | Durable and aesthetically pleasing | Higher cost and complex manufacturing | High |
Metal | Office and outdoor chairs | Strong and low maintenance | Can be uncomfortable without upholstery | Medium |
Plastic | Casual and outdoor chairs | Lightweight and cost-effective | Less durable and potential environmental concerns | Low |
Upholstery Fabrics | Residential and luxury commercial chairs | Comfort and design flexibility | Care requirements and variable quality | Medium to High |
This guide provides international B2B buyers with actionable insights into material selection for custom chairs, helping them make informed decisions that align with their specific market needs and regulatory requirements.
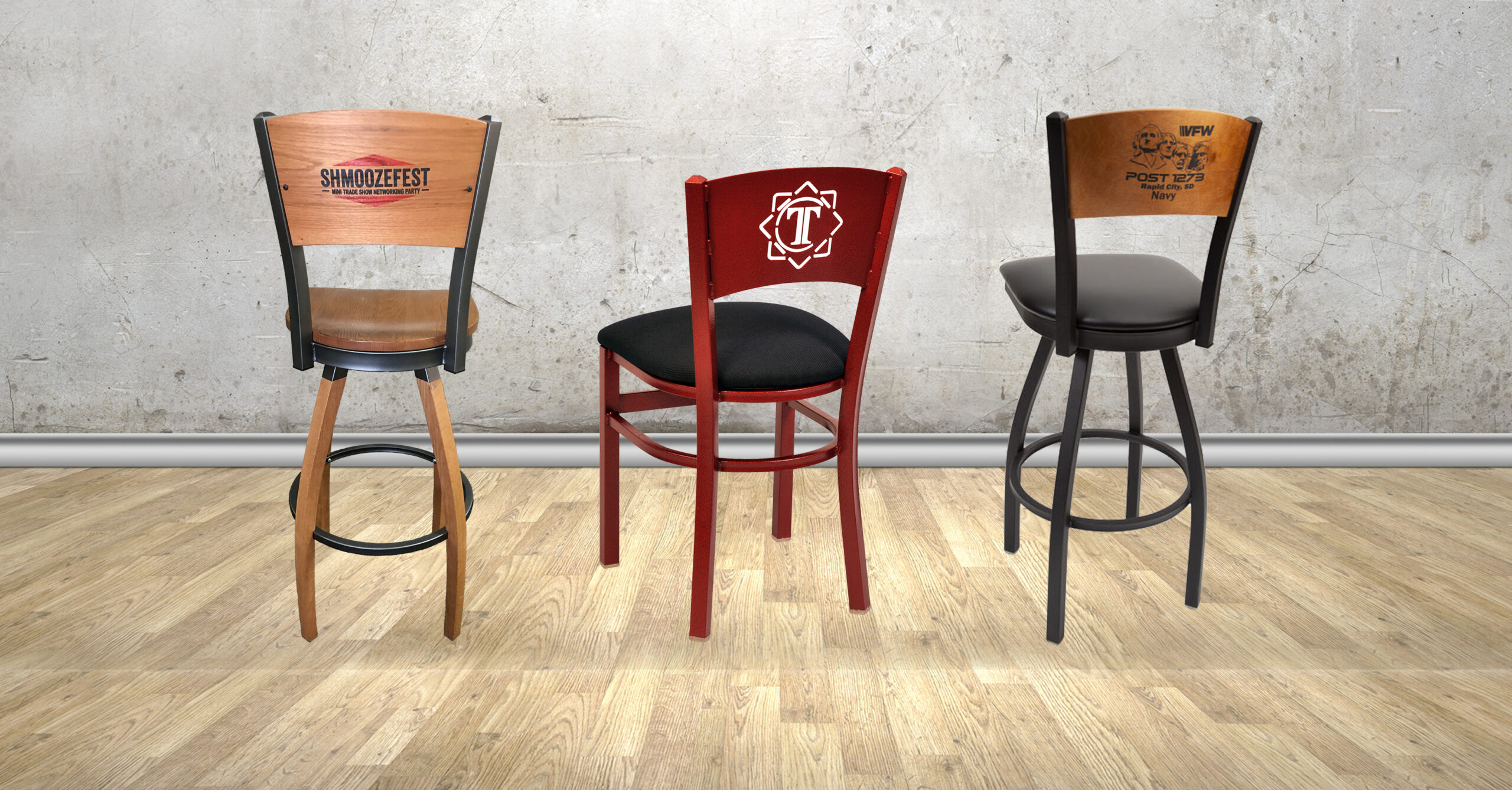
A stock image related to chair custom.
In-depth Look: Manufacturing Processes and Quality Assurance for chair custom
What Are the Main Stages of Manufacturing Custom Chairs?
Manufacturing custom chairs involves several critical stages, each designed to ensure that the final product meets the specific requirements of B2B buyers. The main stages include material preparation, forming, assembly, and finishing.
How Is Material Prepared for Custom Chair Manufacturing?
Material preparation is the first step in the manufacturing process. This stage involves selecting the right types of wood, metal, foam, and upholstery materials based on the design and functional specifications.
- Wood Selection: High-quality hardwoods, such as oak or maple, are often chosen for their durability and aesthetic appeal.
- Metal Components: For chairs that require metal frames or supports, suppliers often use steel or aluminum due to their strength and lightweight properties.
- Foam and Upholstery: The choice of foam density and upholstery fabric is crucial for comfort and longevity. B2B buyers should inquire about the materials used to ensure they meet durability and comfort standards.
Once the materials are selected, they undergo cutting and preparation to fit the design specifications.
What Techniques Are Used in Forming Custom Chairs?
The forming stage involves shaping the prepared materials into the components needed for the chair. This can include:
- CNC Machining: Computer Numerical Control (CNC) machines are frequently used for precise cutting and shaping of wood and metal parts, allowing for intricate designs that meet exact specifications.
- Molding and Casting: For certain chair designs, especially those with complex shapes, manufacturers may use molding techniques for foam and plastic components.
- Upholstery Techniques: Techniques such as stitching, tufting, and wrapping are employed to cover the chair frame with fabric or leather. The upholstery process should adhere to ergonomic and aesthetic standards.
How Are Custom Chairs Assembled?
The assembly stage is where the individual components come together to form the complete chair. This typically involves:
- Joining Techniques: Various joining methods, such as doweling, screwing, or using adhesive, are employed to ensure structural integrity.
- Quality Checks During Assembly: Manufacturers often conduct preliminary quality checks during assembly to identify any defects early in the process.
B2B buyers should ensure that suppliers have skilled labor who are trained in assembly techniques to enhance the final product’s quality.
What Finishing Techniques Are Used in Custom Chair Manufacturing?
Finishing is the final stage of the manufacturing process, adding both aesthetic appeal and protective features to the chair. Common finishing techniques include:
- Sanding and Staining: Wooden components are sanded to a smooth finish and may be stained to enhance their appearance.
- Painting and Varnishing: For metal and wood surfaces, paint or varnish is applied to protect against wear and environmental factors.
- Final Upholstery Treatment: Upholstered surfaces may receive treatments to repel stains or enhance durability.
Buyers should inquire about the finishing processes to ensure they align with their quality expectations and environmental standards.
What International Standards Govern Quality Assurance in Chair Manufacturing?
Quality assurance (QA) is a vital component of the manufacturing process, ensuring that products meet specified standards. Relevant international standards include:
- ISO 9001: This standard sets the criteria for a quality management system (QMS). It ensures that organizations consistently provide products that meet customer and regulatory requirements.
- CE Marking: For products sold in the European Economic Area, CE marking indicates conformity with health, safety, and environmental protection standards.
- API Certification: While more common in industrial applications, some chair manufacturers may pursue API certification to demonstrate quality in specific materials or processes.
What Are the Key Quality Control Checkpoints in Custom Chair Manufacturing?
Quality control (QC) involves several checkpoints throughout the manufacturing process, ensuring that defects are identified and rectified. Key QC checkpoints include:
- Incoming Quality Control (IQC): This step involves inspecting raw materials upon arrival to ensure they meet specifications before production begins.
- In-Process Quality Control (IPQC): During the assembly stage, regular checks are performed to monitor for defects or inconsistencies.
- Final Quality Control (FQC): The final product is thoroughly inspected before shipping, including functional tests and aesthetic evaluations.
B2B buyers should look for suppliers that implement a robust QC process to minimize risks associated with defective products.
How Can B2B Buyers Verify Supplier Quality Control Processes?
Verifying the quality control processes of suppliers is crucial for B2B buyers, especially in international markets. Here are several actionable steps:
- Supplier Audits: Conducting regular audits of suppliers can help assess their adherence to quality standards and manufacturing practices.
- Requesting Quality Reports: B2B buyers should ask for detailed reports on quality checks, including IQC, IPQC, and FQC results.
- Third-Party Inspections: Engaging third-party inspection agencies can provide an unbiased assessment of the manufacturer’s quality control processes.
What Nuances Should International B2B Buyers Consider for Quality Control?
International B2B buyers, particularly from regions like Africa, South America, the Middle East, and Europe, must navigate various challenges and nuances in quality control:
- Cultural Differences: Understanding local manufacturing practices and cultural attitudes toward quality can influence the effectiveness of QC measures.
- Regulatory Compliance: Different regions have unique regulatory requirements. Buyers should familiarize themselves with local standards and ensure their suppliers comply.
- Language Barriers: Clear communication is vital in QC processes. Buyers should consider working with suppliers who can provide documentation and support in their preferred language.
By focusing on these key areas, international B2B buyers can effectively navigate the complexities of manufacturing processes and quality assurance for custom chairs, ensuring they receive high-quality products that meet their needs.
Practical Sourcing Guide: A Step-by-Step Checklist for ‘chair custom’
In the global marketplace, sourcing custom chairs can be a complex process, particularly for international B2B buyers from diverse regions such as Africa, South America, the Middle East, and Europe. This guide provides a practical, step-by-step checklist to ensure a successful procurement process, focusing on quality, compliance, and cost-effectiveness.
Step 1: Define Your Technical Specifications
Before initiating the sourcing process, clearly define the technical specifications of the custom chairs you need. This includes dimensions, materials, weight capacity, and design style. Having detailed specifications helps suppliers provide accurate quotes and reduces the risk of miscommunication.
- Consider ergonomics: Ensure that the chairs meet ergonomic standards to promote comfort and health.
- Identify materials: Specify materials based on durability and aesthetics, such as wood, metal, or upholstery options.
Step 2: Research Potential Suppliers
Conduct thorough research to identify potential suppliers who specialize in custom chair manufacturing. Look for companies with a proven track record in your specific industry.
- Use B2B platforms: Websites like Alibaba, ThomasNet, and global trade directories can be great resources.
- Check industry reviews: Seek feedback from other buyers to gauge supplier reliability and product quality.
Step 3: Evaluate Supplier Certifications
Ensure that potential suppliers possess the necessary certifications to comply with international standards. This is crucial for maintaining quality and safety.
- ISO Certifications: Look for ISO 9001 for quality management and ISO 14001 for environmental management.
- Regional compliance: Verify that suppliers meet any local regulations relevant to your target market.
Step 4: Request Samples
Before finalizing your order, request samples of the custom chairs. This step is vital to assess the quality and craftsmanship of the product.
- Evaluate comfort and aesthetics: Ensure that the samples meet your expectations in terms of design and comfort.
- Check for defects: Inspect the samples for any manufacturing defects or inconsistencies.
Step 5: Negotiate Terms and Pricing
Once you have selected a supplier, negotiate terms, including pricing, payment methods, and delivery timelines. Clear agreements can prevent misunderstandings later on.
- Consider bulk discounts: If ordering in large quantities, discuss potential discounts.
- Establish payment terms: Decide on upfront payments, milestones, or letters of credit to secure transactions.
Step 6: Finalize Logistics and Shipping
Coordinate logistics to ensure timely delivery of your custom chairs. This includes arranging shipping, customs clearance, and final delivery.
- Choose the right shipping method: Consider air freight for speed or sea freight for cost-effectiveness, depending on urgency and budget.
- Understand import duties: Be aware of any tariffs or duties applicable to your region to avoid unexpected costs.
Step 7: Conduct Quality Control Upon Arrival
Once the chairs arrive, perform a thorough quality control check to ensure they meet the agreed-upon specifications and quality standards.
- Inspect quantities and conditions: Verify that the number of chairs matches your order and that they are free from damage.
- Document discrepancies: If any issues arise, document them immediately for resolution with the supplier.
By following this checklist, B2B buyers can streamline the sourcing process for custom chairs, minimizing risks and ensuring that they receive high-quality products that meet their specific needs.
Comprehensive Cost and Pricing Analysis for chair custom Sourcing
What Are the Key Cost Components in Chair Custom Sourcing?
Understanding the cost structure for chair custom sourcing is essential for international B2B buyers. The primary components include:
-
Materials: The choice of materials significantly impacts the cost. High-quality woods, metals, or sustainable materials can increase the price but also enhance durability and appeal.
-
Labor: Labor costs vary by region. Countries in Africa and South America may have lower labor costs compared to Europe, but the skill level and craftsmanship quality can differ widely.
-
Manufacturing Overhead: This includes costs related to factory operations, such as utilities, rent, and equipment depreciation. Efficient manufacturing processes can help mitigate these costs.
-
Tooling: Custom tooling for specific chair designs can be a significant upfront investment. This cost is often amortized over production runs, making it essential to consider order volume when sourcing.
-
Quality Control (QC): Ensuring product quality through rigorous QC processes can add to the cost but is crucial for maintaining brand reputation and customer satisfaction.
-
Logistics: Shipping and handling costs can vary significantly based on distance, mode of transport, and the complexity of the supply chain. Buyers should consider these costs in their total budget.
-
Margin: Suppliers will include a profit margin in their pricing, which can vary widely depending on the supplier’s market position and the perceived value of their products.
How Do Price Influencers Affect Chair Customization Costs?
Several factors influence pricing in chair custom sourcing, which can be pivotal for B2B buyers:
-
Volume and Minimum Order Quantity (MOQ): Larger orders typically reduce per-unit costs due to economies of scale. Understanding a supplier’s MOQ can help in negotiating better pricing.
-
Specifications and Customization: Highly customized chairs will incur additional costs for design changes and specialized materials. Buyers should be clear about their needs to avoid unexpected expenses.
-
Material Selection: Premium materials not only elevate the cost but also affect durability and aesthetics. Buyers should balance quality with budget constraints.
-
Quality Certifications: Chairs that meet specific safety and quality standards may come at a premium. However, investing in certified products can lead to long-term cost savings and risk mitigation.
-
Supplier Factors: The supplier’s reputation, location, and production capacity can influence pricing. Engaging with reputable suppliers may yield better quality and reliability.
-
Incoterms: The agreed-upon shipping terms can significantly affect overall costs. Understanding terms like FOB (Free on Board) or CIF (Cost, Insurance, and Freight) is crucial for accurate budgeting.
What Are the Best Buyer Tips for Negotiating Chair Custom Pricing?
For international B2B buyers, especially from diverse regions like Africa, South America, the Middle East, and Europe, the following strategies can enhance cost-efficiency:
-
Negotiate Terms: Always engage in negotiations regarding price, payment terms, and delivery schedules. Suppliers often have flexibility, especially for larger orders.
-
Consider Total Cost of Ownership (TCO): Evaluate not just the purchase price but also maintenance, durability, and potential resale value. This comprehensive view can help justify higher upfront costs for better-quality chairs.
-
Understand Pricing Nuances: Be aware of regional price variations due to local market conditions, tariffs, and currency fluctuations. Building relationships with local suppliers can also yield better pricing.
-
Conduct Market Research: Familiarize yourself with average prices for similar products in different markets. This knowledge can empower you during negotiations and sourcing decisions.
Disclaimer on Indicative Prices
It is essential to recognize that the prices for chair custom sourcing can fluctuate based on numerous factors, including market demand, raw material costs, and geopolitical conditions. Always consult multiple suppliers and conduct thorough due diligence to ensure competitive pricing tailored to your specific needs.
Alternatives Analysis: Comparing chair custom With Other Solutions
Understanding Alternatives to Chair Customization
When considering chair customization, international B2B buyers have several alternatives that can address their specific needs. Each option comes with unique advantages and drawbacks, making it essential to evaluate them against the desired outcomes, budget constraints, and operational requirements. This analysis will help buyers, particularly from Africa, South America, the Middle East, and Europe, to make informed decisions.
Comparison Table of Chair Custom vs. Alternatives
Comparison Aspect | Chair Custom | Modular Office Furniture | Pre-Designed Ergonomic Chairs |
---|---|---|---|
Performance | High adaptability to needs | Good for flexible spaces | Standardized comfort |
Cost | Higher initial investment | Moderate cost, scalable | Cost-effective |
Ease of Implementation | Requires design collaboration | Easy assembly, less time | Immediate availability |
Maintenance | Varies by materials used | Minimal, standard upkeep | Minimal, standard upkeep |
Best Use Case | Unique environments, branding | Dynamic workspaces | Traditional office settings |
What Are the Advantages and Disadvantages of Modular Office Furniture?
Modular office furniture provides a versatile solution suitable for dynamic workspaces. Its primary advantage lies in the ability to adapt to changing office layouts easily. This flexibility allows businesses to scale up or down without significant additional costs. However, while modular furniture is cost-effective, it may not provide the same level of customization as bespoke solutions, which could be a drawback for brands looking for unique designs that reflect their identity.
How Do Pre-Designed Ergonomic Chairs Compare?
Pre-designed ergonomic chairs are a popular alternative for companies that prioritize comfort and health without needing extensive customization. These chairs are readily available, making them a quick solution for immediate needs. The cost is generally lower, appealing to budget-conscious buyers. However, the limitation lies in the lack of personalization; organizations may find it challenging to align these chairs with their branding or specific ergonomic needs.
Making the Right Choice for Your Business Needs
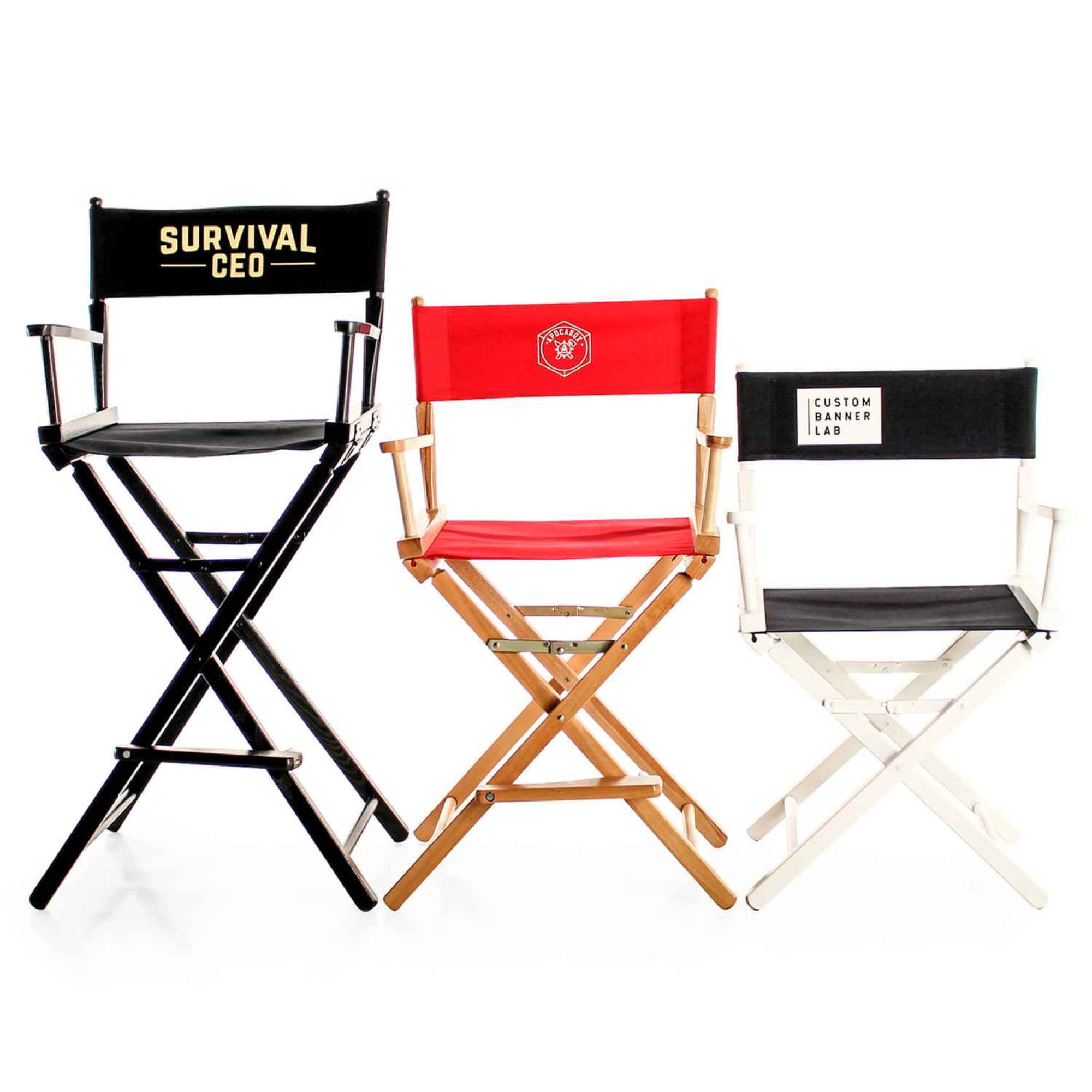
A stock image related to chair custom.
Choosing the right chair solution hinges on evaluating the specific requirements of your organization. For B2B buyers in diverse regions such as Africa, South America, the Middle East, and Europe, understanding local market conditions, cultural preferences, and budget limitations is crucial. Custom chairs might be the best fit for businesses needing unique designs or branding elements. In contrast, modular office furniture could be ideal for companies anticipating growth or changes in their workspace layout. Pre-designed ergonomic chairs may serve well for organizations prioritizing comfort and immediate availability.
By carefully considering these alternatives and their implications, businesses can align their chair selection with operational goals and workforce needs, ultimately enhancing workplace productivity and satisfaction.
Essential Technical Properties and Trade Terminology for chair custom
What Are the Key Technical Properties for Custom Chairs?
When sourcing custom chairs, understanding the technical specifications is crucial for making informed purchasing decisions. Here are several critical properties to consider:
1. Material Grade
The material grade indicates the quality and durability of the chair. Common materials include hardwood, plywood, metal, and various upholstery fabrics. For example, high-grade hardwoods like oak or walnut offer superior strength and longevity, making them ideal for commercial settings. Understanding material grade helps buyers ensure the chairs will withstand daily use and meet their aesthetic requirements.
2. Weight Capacity
Weight capacity specifies the maximum load a chair can support safely. This is particularly important in environments like offices or restaurants, where varying user weights are common. Chairs designed for higher weight capacities are typically constructed with reinforced frames and sturdy materials. Buyers should consider this property to avoid potential liability issues and ensure customer satisfaction.
3. Dimensional Tolerance
Dimensional tolerance refers to the acceptable range of measurement for the chair’s dimensions. This property is vital for ensuring that chairs fit appropriately within designated spaces. For custom orders, clear specifications on height, width, and depth can prevent costly errors in production. Tighter tolerances often indicate higher manufacturing quality and attention to detail.
4. Finish Type
The finish type affects both the chair’s appearance and its resistance to wear and tear. Common finishes include varnish, lacquer, and powder coating. Each type has different maintenance requirements and durability levels. For instance, a UV-resistant finish is essential for outdoor chairs exposed to sunlight. Buyers should consider the intended use and environmental factors when selecting a finish.
5. Upholstery Durability Rating
This rating, often measured by the Martindale test, indicates how well the upholstery will hold up under abrasion. A higher durability rating is crucial for high-traffic areas where the chairs will be frequently used. Understanding this rating helps buyers select materials that will maintain their appearance and comfort over time.
What Are the Common Trade Terms Used in the Custom Chair Industry?
Familiarizing yourself with industry terminology can enhance communication with suppliers and streamline the procurement process. Here are key terms to know:
1. OEM (Original Equipment Manufacturer)
OEM refers to a company that produces parts or equipment that may be marketed by another manufacturer. In the chair industry, this often means sourcing components from specialized manufacturers to create a custom design. Understanding OEM relationships can help buyers navigate supply chain complexities and ensure quality.
2. MOQ (Minimum Order Quantity)
MOQ is the smallest quantity of a product that a supplier is willing to sell. This term is crucial for budget-conscious buyers, as it can impact inventory levels and overall costs. Understanding MOQ helps businesses plan their orders effectively, ensuring they meet demand without overcommitting resources.
3. RFQ (Request for Quotation)
An RFQ is a document sent to suppliers to solicit pricing and terms for specific products. For custom chairs, this allows buyers to compare options and negotiate better deals. A well-structured RFQ can streamline the procurement process and lead to more favorable terms.
4. Incoterms
Incoterms (International Commercial Terms) are a set of rules that define the responsibilities of buyers and sellers in international trade. They clarify who is responsible for shipping, insurance, and tariffs. Familiarity with these terms is essential for B2B buyers to avoid misunderstandings and ensure smooth transactions.
5. Lead Time
Lead time refers to the time between placing an order and receiving the product. This is particularly important in custom chair manufacturing, where design and production can vary significantly. Understanding lead times helps buyers plan their projects and manage expectations effectively.
By grasping these essential technical properties and trade terminologies, international B2B buyers can make informed decisions, mitigate risks, and foster successful relationships with suppliers in the custom chair market.
Navigating Market Dynamics and Sourcing Trends in the chair custom Sector
What Are the Key Trends Shaping the Global Chair Custom Market?
The global chair custom market is experiencing significant transformation driven by various factors. One of the most prominent trends is the increasing demand for personalized and customizable furniture solutions. International B2B buyers, particularly from regions like Africa, South America, the Middle East, and Europe, are seeking unique designs that reflect local culture and preferences. This trend is fueled by the rise of e-commerce platforms that facilitate direct engagement between manufacturers and buyers, allowing for tailored solutions that meet specific needs.
Moreover, technology plays a crucial role in shaping sourcing strategies. Innovations such as 3D printing and augmented reality are enhancing the customization experience, enabling buyers to visualize products before purchase. This technological shift not only streamlines the design process but also reduces lead times, making it easier for international buyers to source bespoke chairs efficiently.
Another significant market dynamic is the growing focus on ergonomic designs, driven by an increased awareness of health and wellness in the workplace. As remote work continues to dominate, businesses are investing in ergonomic office chairs that promote productivity and well-being. This trend presents lucrative opportunities for B2B buyers looking to enhance their workspace offerings.
How Is Sustainability Influencing Sourcing Decisions in the Chair Custom Sector?
Sustainability is becoming a non-negotiable factor for international B2B buyers in the chair custom sector. The environmental impact of furniture production is under scrutiny, prompting buyers to prioritize ethical sourcing and sustainable materials. This shift is particularly relevant in regions such as Europe, where stringent regulations regarding environmental standards are in place.
Buyers are increasingly demanding products made from renewable materials and those certified by recognized ‘green’ standards, such as FSC (Forest Stewardship Council) or LEED (Leadership in Energy and Environmental Design). By sourcing sustainable chairs, businesses not only mitigate their environmental footprint but also enhance their brand reputation among eco-conscious consumers.
Furthermore, suppliers are adapting to this trend by integrating sustainable practices into their manufacturing processes. This includes minimizing waste, utilizing eco-friendly finishes, and adopting circular economy principles. For B2B buyers, aligning with suppliers who prioritize sustainability can lead to competitive advantages and better market positioning.
What Historical Context Should B2B Buyers Consider in the Chair Custom Market?
The chair custom market has evolved significantly over the decades, transitioning from traditional craftsmanship to modern manufacturing techniques. In the early 20th century, chairs were predominantly handcrafted, focusing on unique designs and personalized touches. However, the post-war era ushered in mass production, leading to uniformity and reduced customization options.
In recent years, the resurgence of artisanal craftsmanship alongside technological advancements has created a hybrid market where buyers can enjoy the benefits of both worlds. This evolution has empowered B2B buyers to demand not only functionality and comfort but also aesthetic value and cultural relevance in their chair selections.
Understanding this historical context can provide international buyers with valuable insights into current market dynamics and help them make informed decisions when sourcing custom chairs that align with their brand identity and customer expectations.
Frequently Asked Questions (FAQs) for B2B Buyers of chair custom
-
How do I find reliable suppliers for custom chairs in international markets?
Finding reliable suppliers for custom chairs involves thorough research and vetting. Start by leveraging online B2B marketplaces like Alibaba or Global Sources, where you can view supplier ratings and reviews. Additionally, attend industry trade shows to meet suppliers face-to-face and assess their offerings. Always request samples to evaluate quality before making large orders. Lastly, consider using a third-party inspection service to ensure compliance with your specifications and quality standards. -
What are the key factors to consider when customizing chairs for my business?
When customizing chairs, focus on design, materials, functionality, and ergonomics. Determine the specific purpose of the chairs—are they for office use, dining, or lounge areas? Choose materials that align with your brand image and durability requirements. Ergonomic designs improve user comfort, which can be a selling point. Additionally, consider your target market’s preferences regarding style and color to ensure your products resonate with potential customers. -
What are the typical minimum order quantities (MOQs) for custom chair orders?
Minimum order quantities for custom chairs can vary widely based on the supplier and design complexity. Generally, MOQs range from 50 to 500 units. Larger suppliers often have lower MOQs due to their production capacity, while smaller manufacturers may require higher MOQs to justify setup costs. Always discuss MOQs upfront with suppliers to ensure they align with your budget and demand forecasts. -
How can I negotiate favorable payment terms with suppliers for custom chair orders?
Negotiating payment terms is crucial for maintaining cash flow. Start by proposing a payment schedule that aligns with your production timeline, such as a 30% deposit and 70% upon delivery. Demonstrating a long-term partnership intention can also strengthen your negotiating position. Consider offering to pay higher deposits for lower prices or extended payment terms. Always document agreed terms in a contract to avoid misunderstandings. -
What quality assurance measures should I implement when sourcing custom chairs?
Implementing quality assurance measures involves establishing clear product specifications and conducting regular inspections. Before production begins, work with suppliers to create prototypes that meet your standards. During production, schedule inspections at various stages to catch defects early. Post-production, consider using third-party quality control firms to conduct final inspections. This ensures that the chairs you receive meet your expectations and reduce the risk of returns. -
What logistics considerations should I keep in mind when importing custom chairs?
When importing custom chairs, consider shipping costs, lead times, and customs regulations. Choose a reliable shipping method that balances cost and delivery speed. Understand the import duties applicable in your country to avoid unexpected costs. Collaborate with freight forwarders who specialize in furniture to streamline the logistics process. Lastly, ensure that your supplier is familiar with packaging requirements to prevent damage during transit. -
How do cultural preferences impact chair design in different regions?
Cultural preferences significantly influence chair design, as they dictate aesthetics, comfort, and functionality. For instance, in Europe, modern and minimalist designs may be preferred, while in Africa, traditional motifs and vibrant colors might resonate more. Research regional trends and consumer preferences before finalizing designs. Collaborating with local designers can also provide valuable insights into cultural nuances, ensuring your products are well-received in diverse markets. -
What are the common challenges faced when sourcing custom chairs from international suppliers?
Common challenges include communication barriers, quality discrepancies, and shipping delays. Language differences can lead to misunderstandings regarding specifications, so clear communication is essential. Quality issues may arise if suppliers do not fully understand your requirements, so providing detailed specifications and samples is crucial. Additionally, international shipping can encounter delays due to customs clearance, so factor in buffer time in your planning to mitigate disruptions in your supply chain.
Important Disclaimer & Terms of Use
⚠️ Important Disclaimer
The information provided in this guide, including content regarding manufacturers, technical specifications, and market analysis, is for informational and educational purposes only. It does not constitute professional procurement advice, financial advice, or legal advice.
While we have made every effort to ensure the accuracy and timeliness of the information, we are not responsible for any errors, omissions, or outdated information. Market conditions, company details, and technical standards are subject to change.
B2B buyers must conduct their own independent and thorough due diligence before making any purchasing decisions. This includes contacting suppliers directly, verifying certifications, requesting samples, and seeking professional consultation. The risk of relying on any information in this guide is borne solely by the reader.
Strategic Sourcing Conclusion and Outlook for chair custom
What Are the Key Takeaways for Strategic Sourcing in Custom Chairs?
Strategic sourcing for custom chairs is essential for international B2B buyers seeking to optimize their procurement processes. Understanding market trends, quality standards, and regional design preferences can significantly enhance sourcing strategies. Buyers should prioritize suppliers that offer flexibility in customization, ensuring that designs align with local aesthetics and functionality needs. Leveraging technology to facilitate communication and order tracking can also streamline the sourcing process, reducing lead times and enhancing efficiency.
How Can Buyers Prepare for Future Trends in Chair Customization?
As the demand for unique and ergonomic furniture grows, it is crucial for buyers to remain adaptable. Anticipating trends such as sustainable materials and multifunctional designs will allow businesses to stay competitive in the global marketplace. Engaging with manufacturers who prioritize eco-friendly practices can not only enhance brand reputation but also appeal to a growing demographic of environmentally conscious consumers.
What Should International Buyers Do Next?
For international B2B buyers from Africa, South America, the Middle East, and Europe, the time to act is now. By focusing on strategic sourcing, you can ensure a steady supply of custom chairs that meet your market’s demands. Collaborate with reliable partners, embrace innovation, and stay informed about industry trends. As you navigate this evolving landscape, remember that proactive sourcing strategies will position your business for long-term success in the competitive furniture market.