Discover Top Strategies to Source a Lamp Manufacturer (2025)
Introduction: Navigating the Global Market for lamp manufacturer
Navigating the global market for lamp manufacturers can be a daunting task for B2B buyers, especially when seeking reliable suppliers that meet specific lighting needs. Whether you are sourcing energy-efficient LED fixtures for an office in Cairo or decorative lighting solutions for a hotel in São Paulo, understanding the diverse landscape of lamp manufacturing is crucial. This guide offers a comprehensive overview of various types of lamps, their applications across different industries, and essential considerations for supplier vetting, pricing strategies, and cost management.
For international B2B buyers from Africa, South America, the Middle East, and Europe, this resource is designed to empower informed purchasing decisions. You will gain insights into the latest trends in lamp technology, the impact of regional regulations on sourcing, and practical tips for assessing supplier reliability. By addressing key challenges such as quality assurance, compliance with safety standards, and logistics, this guide aims to streamline the procurement process and enhance your sourcing strategy.
As you delve into the sections ahead, you will find actionable information tailored to your specific market, enabling you to navigate the complexities of the lamp manufacturing sector effectively. Ultimately, this guide is your partner in making strategic, informed choices that align with your business goals and operational needs.
Understanding lamp manufacturer Types and Variations
Type Name | Key Distinguishing Features | Primary B2B Applications | Brief Pros & Cons for Buyers |
---|---|---|---|
Traditional Lamp Manufacturers | Focus on classic designs, materials like glass and metal | Retail, hospitality, and decorative lighting | Pros: Timeless aesthetics; Cons: Less energy-efficient compared to modern options. |
LED Lamp Manufacturers | Specialize in energy-efficient LED technology | Commercial, industrial, and residential lighting | Pros: Long lifespan and low energy consumption; Cons: Higher upfront costs. |
Smart Lamp Manufacturers | Incorporate IoT technology for smart lighting solutions | Smart homes, offices, and urban infrastructure | Pros: Enhanced control and energy savings; Cons: Requires compatible systems and potential cybersecurity concerns. |
Specialty Lamp Manufacturers | Produce lamps for specific applications like medical or industrial use | Healthcare, manufacturing, and scientific research | Pros: Tailored solutions for unique needs; Cons: May have limited availability and higher costs. |
Custom Lamp Manufacturers | Offer bespoke design and manufacturing services | High-end retail, luxury interiors, and architectural projects | Pros: Unique designs that fit specific projects; Cons: Longer lead times and potentially higher prices. |
What Are the Characteristics of Traditional Lamp Manufacturers?
Traditional lamp manufacturers emphasize craftsmanship and timeless design, often utilizing materials such as glass and metal. These lamps are commonly used in retail, hospitality, and decorative applications, where aesthetics play a crucial role. B2B buyers should consider the durability and maintenance requirements of these products, as well as their energy efficiency, which may not be as high as modern alternatives.
How Do LED Lamp Manufacturers Stand Out?
LED lamp manufacturers focus on producing energy-efficient lighting solutions that have a significantly longer lifespan compared to traditional bulbs. These lamps are ideal for commercial and industrial applications, as well as residential settings. B2B buyers should weigh the initial investment against long-term savings on energy costs and maintenance, making them a wise choice for organizations looking to reduce their carbon footprint.
What Are the Benefits of Smart Lamp Manufacturers?
Smart lamp manufacturers are at the forefront of integrating IoT technology into lighting solutions, allowing for enhanced control through apps and automation. These lamps are particularly suitable for smart homes, offices, and urban infrastructure. B2B buyers should evaluate the compatibility of these systems with existing infrastructure and consider potential cybersecurity risks when implementing smart lighting solutions.
Why Choose Specialty Lamp Manufacturers?
Specialty lamp manufacturers cater to niche markets by producing lamps designed for specific applications, such as medical or industrial use. These lamps are essential in sectors like healthcare, manufacturing, and scientific research. B2B buyers must assess the unique requirements of their industries to ensure that the lamps meet regulatory standards and operational needs, even if they come at a premium price.
What Should B2B Buyers Know About Custom Lamp Manufacturers?
Custom lamp manufacturers provide bespoke design and manufacturing services, allowing businesses to create unique lighting solutions tailored to their specific needs. This is particularly valuable in high-end retail, luxury interiors, and architectural projects. While the advantage lies in obtaining a one-of-a-kind product, B2B buyers should be prepared for longer lead times and potentially higher costs associated with custom orders.
Key Industrial Applications of lamp manufacturer
Industry/Sector | Specific Application of lamp manufacturer | Value/Benefit for the Business | Key Sourcing Considerations for this Application |
---|---|---|---|
Retail | Energy-efficient LED lighting for stores | Reduces energy costs and enhances product visibility | Compliance with energy regulations and certifications |
Manufacturing | Industrial lighting for production facilities | Improves worker safety and productivity | Durability and resistance to hazardous environments |
Healthcare | Surgical and examination lighting | Ensures optimal visibility for medical procedures | Compliance with health regulations and sterilization |
Hospitality | Ambient and decorative lighting for hotels | Enhances guest experience and increases occupancy | Customization options and aesthetic appeal |
Agriculture | Grow lights for indoor farming | Maximizes crop yield and growth cycles | Energy efficiency and spectrum suitability for plants |
How is Lamp Manufacturing Applied in the Retail Sector?
In the retail industry, energy-efficient LED lighting plays a crucial role in enhancing product visibility and reducing energy costs. Lamp manufacturers provide a range of solutions tailored for retail environments, including track lighting, display lighting, and ambient lighting. For international B2B buyers, especially from regions like Africa and South America, sourcing lamps that comply with local energy regulations is essential. Additionally, manufacturers should offer warranties and support for energy-efficient products to ensure long-term value.
What are the Key Applications of Lamp Manufacturing in Manufacturing Facilities?
In manufacturing, proper industrial lighting is vital for worker safety and productivity. Lamp manufacturers supply robust lighting solutions designed to withstand harsh conditions, such as high temperatures and dust. These products help prevent workplace accidents and improve efficiency. Buyers in the Middle East and Europe must consider the durability and maintenance requirements of lighting systems, ensuring they meet industry standards and can operate continuously in demanding environments.
How are Lamp Manufacturers Meeting Healthcare Lighting Needs?
Healthcare facilities require specialized lighting solutions for surgical and examination purposes. Lamp manufacturers design lighting that provides optimal visibility, crucial for medical procedures. The technology often includes adjustable brightness and color temperature features, enhancing the precision of healthcare professionals. International buyers, particularly from Europe and Africa, must ensure that sourced lighting products comply with health regulations and can be easily sterilized to maintain hygiene standards.
What Role Does Lighting Play in Enhancing Hospitality?
In the hospitality sector, ambient and decorative lighting significantly influences guest experience. Lamp manufacturers create aesthetically pleasing lighting solutions that enhance the atmosphere of hotels and restaurants, thus increasing occupancy rates. Buyers should prioritize customization options to align with their brand identity. Additionally, they must consider the energy efficiency of lighting solutions, especially in regions like South America, where energy costs can be a significant factor in operational budgets.
How is Lamp Manufacturing Transforming Agriculture?
In agriculture, particularly indoor farming, lamp manufacturers are instrumental in providing grow lights that maximize crop yield. These specialized lamps emit specific light spectrums that cater to plant growth cycles, significantly enhancing production efficiency. For B2B buyers in Africa and the Middle East, sourcing energy-efficient grow lights is crucial to minimize operational costs while ensuring optimal plant health. Manufacturers should be able to provide detailed specifications on energy consumption and light output to meet the specific needs of agricultural businesses.
Related Video: Uses of Light in Everyday Life
3 Common User Pain Points for ‘lamp manufacturer’ & Their Solutions
Scenario 1: Navigating Quality Assurance in Lamp Manufacturing
The Problem:
B2B buyers in regions like Africa and South America often face significant challenges when sourcing lamps from manufacturers. The risk of receiving products that do not meet the required quality standards is high, especially when dealing with suppliers who may not have robust quality assurance processes. This can lead to dissatisfaction among end-users, potential safety hazards, and financial losses due to returns or replacements.
The Solution:
To mitigate these risks, international buyers should implement a rigorous vendor evaluation process. Start by requesting samples and conducting quality inspections before placing bulk orders. Establish clear specifications that the lamps must meet, including certifications like CE or ISO, which indicate compliance with international quality standards. Additionally, consider using third-party inspection services to validate product quality prior to shipment. This proactive approach not only helps in securing high-quality products but also builds a reliable relationship with manufacturers who are committed to maintaining standards.
Scenario 2: Managing Supply Chain Disruptions
The Problem:
Supply chain issues are a common pain point for B2B buyers, particularly in the lamp manufacturing sector. Factors such as political instability, transportation delays, or material shortages can cause significant interruptions, affecting the availability of products when needed. Buyers in regions like the Middle East may find it particularly challenging to maintain consistent inventory levels due to these external factors.
The Solution:
To effectively manage supply chain disruptions, buyers should diversify their supplier base. This involves sourcing lamps from multiple manufacturers across different geographical locations to reduce dependency on a single source. Implementing a just-in-time inventory system can also help in managing stock levels efficiently, ensuring that you only order what you need when you need it. Additionally, consider establishing strong relationships with local distributors who can provide quicker access to products in times of need. This strategy not only safeguards against potential supply disruptions but also enhances flexibility in responding to market demands.
Scenario 3: Understanding Energy Efficiency Regulations
The Problem:
With the increasing focus on sustainability, B2B buyers are often faced with the complexity of navigating energy efficiency regulations in their respective markets. Buyers in Europe, for instance, must comply with strict EU regulations regarding energy consumption for lighting products. Failure to comply can result in penalties, product recalls, or damage to brand reputation.
The Solution:
To effectively address this challenge, buyers should stay informed about local and international energy efficiency regulations that pertain to lamp products. Collaborate with manufacturers who have a strong understanding of these regulations and can provide documentation confirming compliance. It’s advisable to conduct thorough research on energy labeling systems and certifications, such as ENERGY STAR or the EU Energy Label, which indicate a product’s energy performance. Engaging in training sessions or workshops on regulatory compliance can also empower procurement teams to make informed decisions. This proactive approach ensures that your sourcing strategy aligns with sustainability goals while minimizing regulatory risks.
Strategic Material Selection Guide for lamp manufacturer
When selecting materials for lamp manufacturing, international B2B buyers must consider several factors, including performance characteristics, cost implications, and compliance with regional standards. This guide analyzes four common materials used in lamp manufacturing, providing insights tailored for buyers from Africa, South America, the Middle East, and Europe.
What Are the Key Properties of Glass in Lamp Manufacturing?
Key Properties: Glass is a widely used material in lamp manufacturing due to its excellent optical clarity and heat resistance. It can withstand high temperatures, making it suitable for incandescent and halogen lamps. Glass is also resistant to corrosion and can be treated to enhance its durability.
Pros & Cons: The primary advantage of glass is its ability to provide clear light transmission while being aesthetically pleasing. However, it can be fragile and may require additional protective measures to prevent breakage during manufacturing and shipping. The cost of glass can vary significantly based on the type and treatment, with specialty glasses being more expensive.
Impact on Application: Glass is compatible with various lighting media, including LED, incandescent, and fluorescent. Its transparency allows for effective light distribution, making it ideal for decorative and functional applications.
Considerations for International Buyers: Buyers should ensure that the glass used complies with safety standards such as ASTM C1036 (for flat glass) or DIN 52322 (for thermal shock resistance). Additionally, understanding local regulations regarding glass recycling and disposal is crucial.
How Does Metal Influence Lamp Durability and Performance?
Key Properties: Metals such as aluminum, brass, and steel are commonly used for lamp fixtures and components. They offer high strength, excellent thermal conductivity, and resistance to corrosion when treated appropriately.
Pros & Cons: Metals provide durability and a modern aesthetic, making them suitable for various lamp designs. However, they can be heavier than other materials, potentially increasing shipping costs. The manufacturing complexity can also rise with intricate designs, impacting production timelines.
Impact on Application: Metal components are essential in applications requiring robust structural integrity, such as outdoor lighting. Their thermal properties allow for effective heat dissipation, which is vital for maintaining the longevity of light sources.
Considerations for International Buyers: Buyers should be aware of the corrosion resistance standards applicable in their regions, such as JIS H 8601 for aluminum coatings. Additionally, understanding the implications of sourcing metals from sustainable practices can enhance brand reputation.
What Role Does Plastic Play in Lamp Design and Functionality?
Key Properties: Plastics, particularly polycarbonate and acrylic, are lightweight and versatile materials used in lamp manufacturing. They offer good impact resistance and can be molded into complex shapes.
Pros & Cons: The primary advantage of plastic is its cost-effectiveness and ease of manufacturing. However, plastics may not withstand high temperatures as well as glass or metal, which can limit their use in high-heat applications. Additionally, they may degrade over time when exposed to UV light.
Impact on Application: Plastic is suitable for indoor lamps and decorative lighting where weight and design flexibility are priorities. However, its thermal limitations should be considered in applications involving high wattage bulbs.
Considerations for International Buyers: Buyers should check for compliance with international standards such as ASTM D635 (for flammability) and ensure that the plastics used are recyclable or made from recycled materials to meet sustainability goals.
How Do Ceramics Enhance Lamp Performance and Aesthetics?
Key Properties: Ceramics are known for their excellent heat resistance and electrical insulation properties. They can withstand high temperatures without deforming, making them ideal for certain lamp components.
Pros & Cons: The durability and aesthetic appeal of ceramics make them a popular choice for decorative lamps. However, they can be brittle and may require careful handling during manufacturing and transport. The cost of ceramic materials can also be higher compared to plastics.
Impact on Application: Ceramics are particularly beneficial in applications requiring heat resistance, such as in high-intensity discharge (HID) lamps. Their ability to maintain structural integrity at high temperatures enhances the overall performance of the lamp.
Considerations for International Buyers: Buyers should ensure that ceramics meet relevant standards such as DIN 4102 (for fire behavior) and consider the implications of sourcing materials from regions with stringent environmental regulations.
Summary Table of Material Selection for Lamp Manufacturing
Material | Typical Use Case for lamp manufacturer | Key Advantage | Key Disadvantage/Limitation | Relative Cost (Low/Med/High) |
---|---|---|---|---|
Glass | Lamp shades and covers | Excellent light transmission | Fragile and can break easily | Medium |
Metal | Lamp fixtures and structural components | High durability and strength | Heavier, increasing shipping costs | Medium to High |
Plastic | Indoor decorative lamps | Cost-effective and lightweight | Limited heat resistance | Low |
Ceramic | High-intensity discharge lamps | Excellent heat resistance | Brittle and can be expensive | High |
This guide provides actionable insights for international B2B buyers, helping them make informed decisions regarding material selection for lamp manufacturing while considering regional compliance and market preferences.
In-depth Look: Manufacturing Processes and Quality Assurance for lamp manufacturer
What Are the Main Stages in the Manufacturing Process of Lamps?
The manufacturing process for lamps involves several critical stages that ensure both functionality and aesthetic appeal. Understanding these stages is essential for B2B buyers seeking quality products.
1. Material Preparation
The first step in lamp manufacturing is material preparation. This involves sourcing high-quality materials such as glass, plastics, metals, and electrical components. Suppliers often use materials that meet industry standards to ensure durability and safety. Buyers should inquire about the origin of materials and whether they comply with international standards, such as those set by the International Organization for Standardization (ISO).
2. Forming
The forming stage includes various techniques depending on the lamp design. Techniques can range from molding for plastic parts to glass blowing for shades. In metal components, processes like stamping or machining are commonly employed. Each of these methods has its own set of quality considerations, which can significantly impact the final product. Buyers should assess whether manufacturers utilize advanced technology and skilled labor to enhance precision during this phase.
3. Assembly
Once individual components are formed, the assembly stage begins. This involves fitting parts together, which may include wiring electrical components and securing lamp bases. A clean and organized assembly line is crucial for maintaining efficiency and minimizing errors. B2B buyers should ask about the assembly protocols and whether workers are trained in quality assurance practices, as this can affect product reliability.
4. Finishing
The final stage, finishing, includes painting, polishing, or coating to enhance the lamp’s appearance and protect it from wear and tear. Quality checks during this stage are vital to ensure that the final product meets aesthetic and functional requirements. Buyers should inquire about the types of finishes used and their compliance with safety standards, especially in regions with specific regulatory requirements.
How is Quality Assurance Implemented in Lamp Manufacturing?
Quality assurance (QA) is a critical component of lamp manufacturing, ensuring that products meet predefined standards and specifications. Here’s a closer look at the QA processes relevant to B2B buyers.
Relevant International Standards for Lamp Quality
Manufacturers often adhere to various international quality standards, such as ISO 9001, which outlines a framework for quality management systems. Additionally, industry-specific certifications like CE marking (Conformité Européenne) indicate compliance with European safety standards, while the American National Standards Institute (ANSI) governs safety standards in the U.S. Buyers should verify that suppliers hold these certifications, as they reflect a commitment to quality and safety.
What Are the QC Checkpoints in Lamp Manufacturing?
Quality control (QC) in lamp manufacturing typically involves several checkpoints throughout the production process:
-
Incoming Quality Control (IQC): This initial checkpoint involves inspecting raw materials upon arrival to ensure they meet specified standards. Any defective materials can lead to flaws in the final product, so rigorous inspections are essential.
-
In-Process Quality Control (IPQC): During the manufacturing process, IPQC ensures that components are being produced within the specified tolerances. Regular inspections can help catch defects early, reducing waste and improving efficiency.
-
Final Quality Control (FQC): After assembly, lamps undergo final inspections to verify functionality and adherence to quality standards. This includes testing electrical components, checking for any physical defects, and ensuring packaging meets transport requirements.
What Common Testing Methods Are Used for Lamps?
Testing methods play a crucial role in verifying the quality and safety of lamps. Common testing procedures include:
-
Electrical Testing: This involves checking for electrical safety, including insulation resistance and grounding continuity. Compliance with electrical safety standards is critical, especially in regions with strict electrical codes.
-
Durability Testing: Lamps are subjected to stress tests, simulating years of usage to ensure they can withstand environmental conditions without failing.
-
Light Output Testing: Measuring lumen output helps ensure the lamp performs as advertised. This is particularly important for energy-efficient products, as buyers often seek specific brightness levels.
How Can B2B Buyers Verify Supplier Quality Control?
To ensure that suppliers maintain high-quality standards, B2B buyers can implement several verification strategies:
-
Supplier Audits: Conducting regular audits of suppliers’ facilities can provide insight into their manufacturing processes and quality control measures. This can include reviewing documentation of quality checks and certifications.
-
Quality Reports: Requesting detailed quality reports can help buyers understand the frequency and types of defects encountered during production. Suppliers should provide transparency regarding their QC processes and results.
-
Third-Party Inspections: Engaging third-party inspection services can offer an unbiased assessment of product quality before shipment. This can be particularly beneficial for international buyers who may not have the capacity to conduct on-site inspections.
What Are the QC and Certification Nuances for International B2B Buyers?
For international buyers, understanding the nuances of quality control and certification is vital. Different regions may have varying requirements for safety and quality standards. For instance, a lamp sold in Europe must meet CE certification, whereas products sold in the U.S. might need to comply with UL (Underwriters Laboratories) standards.
B2B buyers from regions such as Africa, South America, and the Middle East should be aware of local regulations and ensure that their suppliers are compliant. This may involve additional documentation and testing to satisfy both local and international standards. Buyers should also consider logistics implications, as non-compliance can lead to costly delays at customs.
In summary, understanding the manufacturing processes and quality assurance measures in lamp manufacturing enables B2B buyers to make informed decisions. By focusing on key stages, quality checkpoints, and certification requirements, buyers can better assess potential suppliers and ensure the products they procure meet the necessary standards for safety and performance.
Practical Sourcing Guide: A Step-by-Step Checklist for ‘lamp manufacturer’
In the competitive landscape of B2B procurement, sourcing a reliable lamp manufacturer requires a structured approach to ensure quality, compliance, and value. This guide provides a step-by-step checklist tailored for international buyers, particularly those in Africa, South America, the Middle East, and Europe, to navigate the complexities of the lamp manufacturing market effectively.
Step 1: Define Your Technical Specifications
Establishing clear technical specifications is fundamental to sourcing the right lamp products. Consider factors such as wattage, energy efficiency ratings, design requirements, and compliance with local regulations. Detailed specifications will help communicate your needs effectively to potential suppliers and ensure that the products meet your quality and performance expectations.
Step 2: Conduct Market Research for Lamp Manufacturers
Before making any commitments, perform thorough market research to identify potential lamp manufacturers. Focus on regions known for their lamp production, such as Asia and Europe, and utilize online platforms and trade shows to gather information. Pay attention to industry reviews, certifications, and market presence, as these factors can indicate a manufacturer‘s reliability and reputation.
Step 3: Evaluate Potential Suppliers
Before committing to a supplier, it is crucial to vet them thoroughly. Request company profiles, case studies, and references from buyers in a similar industry or region. Key evaluation criteria include:
– Production Capacity: Ensure the manufacturer can meet your volume requirements.
– Quality Control Processes: Inquire about their quality assurance methods and certifications (e.g., ISO 9001).
– Lead Times: Understand their production timelines to align with your project schedules.
Step 4: Verify Supplier Certifications and Compliance
Check that the potential manufacturers comply with international standards and local regulations. Certifications such as CE, RoHS, or UL can assure you of the product’s safety and environmental compliance. This verification is particularly important for international buyers to avoid legal and operational issues in their respective markets.
Step 5: Request Samples for Quality Assessment
Before finalizing a supplier, request product samples to assess quality firsthand. Evaluate the samples based on your defined specifications, paying close attention to aspects such as material quality, finish, and functionality. This step is crucial to ensure that the final products will meet your expectations and avoid costly mistakes down the line.
Step 6: Negotiate Terms and Conditions
Once you have selected a supplier, engage in negotiations to establish favorable terms and conditions. Discuss pricing, payment terms, delivery schedules, and warranty policies. Clear agreements will help prevent misunderstandings and ensure a smooth procurement process.
Step 7: Establish a Communication Plan
Effective communication is vital for successful sourcing. Set up a structured communication plan that includes regular updates and feedback channels. This plan should involve key contacts from both your organization and the manufacturer to facilitate timely resolution of any issues that may arise during production or shipping.
By following this checklist, international B2B buyers can navigate the sourcing process for lamp manufacturers more efficiently, ensuring they select a supplier that aligns with their business needs and quality standards.
Comprehensive Cost and Pricing Analysis for lamp manufacturer Sourcing
What Are the Key Cost Components in Lamp Manufacturing?
Understanding the cost structure in lamp manufacturing is crucial for international B2B buyers aiming to make informed sourcing decisions. The primary cost components include:
-
Materials: The choice of materials significantly impacts the overall cost. Common materials such as glass, metal, and plastics vary in price based on quality and sourcing location. For instance, sourcing high-grade materials from Europe may be costlier than acquiring locally sourced materials in Africa or South America.
-
Labor: Labor costs fluctuate based on geographic location and the skill level required for manufacturing. Regions with lower labor costs can offer competitive pricing, but it’s essential to assess the quality of workmanship, as this directly influences product durability.
-
Manufacturing Overhead: This includes utilities, rent, and equipment maintenance. Efficient manufacturing processes can help reduce overhead costs, allowing manufacturers to offer better pricing.
-
Tooling: The setup costs for molds and fixtures can be significant, especially for customized lamp designs. Buyers should consider these costs when evaluating quotes.
-
Quality Control (QC): Robust QC processes ensure product reliability and compliance with international standards. Implementing stringent QC measures may raise costs, but they are essential for maintaining brand reputation.
-
Logistics: Shipping and handling costs can vary widely depending on the origin of the goods and the chosen transportation method. International buyers should factor in these costs to understand the total landed price.
-
Margin: The profit margin for manufacturers is influenced by competition and market demand. Understanding typical margins in the industry can help buyers gauge the fairness of pricing.
How Do Pricing Influencers Affect Lamp Sourcing?
Several factors can influence the pricing of lamps, impacting how B2B buyers negotiate and strategize their purchases:
-
Volume/MOQ (Minimum Order Quantity): Larger orders often lead to lower per-unit prices. Buyers should evaluate their needs carefully to balance inventory costs against potential savings.
-
Specifications and Customization: Custom designs or specific requirements can lead to increased costs due to additional tooling and labor. It’s advisable to clearly communicate specifications early in the negotiation process.
-
Material Selection: High-quality or specialized materials can significantly increase costs. Buyers should weigh the benefits of premium materials against their budget constraints.
-
Quality and Certifications: Compliance with international quality standards can affect pricing. Buyers should inquire about certifications and quality assurance processes to ensure product integrity.
-
Supplier Factors: The supplier’s reputation, reliability, and service levels can influence pricing. Establishing a relationship with reputable suppliers can lead to better negotiation outcomes.
-
Incoterms: The chosen Incoterms can impact the total cost of ownership, including shipping responsibilities and risk. Buyers should understand the implications of different Incoterms to avoid unexpected expenses.
What Are Effective Buyer Tips for Lamp Sourcing?
For international B2B buyers, particularly those from Africa, South America, the Middle East, and Europe, several strategies can enhance sourcing efficiency:
-
Negotiation Tactics: Always approach negotiations with a clear understanding of your budget and the market rates. Leverage volume commitments to negotiate better pricing.
-
Cost-Efficiency Strategies: Evaluate total cost of ownership, including shipping and duties, to make informed purchasing decisions. This holistic view helps in comparing quotes from different suppliers.
-
Understanding Pricing Nuances: Be aware of regional pricing differences. For instance, manufacturers in emerging markets may offer lower prices but could have longer lead times or different quality standards.
-
Building Relationships: Developing strong relationships with suppliers can lead to better service and pricing. Regular communication and feedback help foster trust and reliability.
-
Disclaimer on Indicative Prices: Prices can fluctuate based on market conditions, currency exchange rates, and other external factors. Always request updated quotes and confirm pricing before finalizing orders.
By comprehensively understanding these cost components and pricing influencers, B2B buyers can navigate the complexities of lamp manufacturing sourcing more effectively, ensuring they obtain high-quality products at competitive prices.
Alternatives Analysis: Comparing lamp manufacturer With Other Solutions
When considering a lamp manufacturer, it is essential for international B2B buyers to evaluate various alternatives that might fulfill their lighting needs more effectively or economically. This section will compare traditional lamp manufacturing with innovative lighting solutions that have emerged in the market, providing actionable insights tailored for buyers from Africa, South America, the Middle East, and Europe.
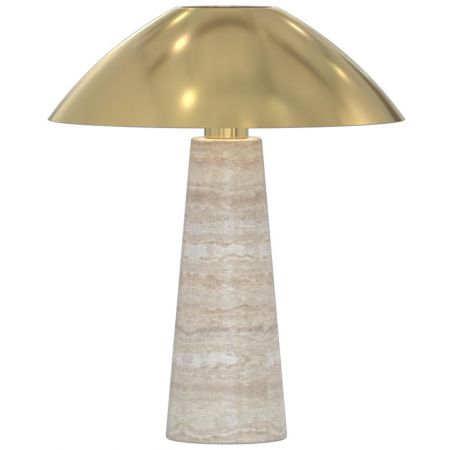
A stock image related to lamp manufacturer.
Comparison Table of Lamp Manufacturer and Alternatives
Comparison Aspect | Lamp Manufacturer | LED Lighting Solutions | Solar-Powered Lighting |
---|---|---|---|
Performance | High-quality, reliable illumination | Superior energy efficiency and longevity | Variable performance based on sunlight availability |
Cost | Moderate initial investment | Higher upfront costs, lower long-term costs | Initial investment can be high, but minimal operational costs |
Ease of Implementation | Standard installation processes | Requires specialized installation | Simple installation, but requires site assessment |
Maintenance | Regular bulb replacements | Minimal maintenance; long lifespan | Occasional cleaning and battery replacement |
Best Use Case | General indoor and outdoor lighting | Commercial and residential applications | Remote areas or off-grid applications |
Pros and Cons of Alternatives
What Are the Advantages and Disadvantages of LED Lighting Solutions?
LED lighting solutions represent a significant advancement in lighting technology. They offer superior energy efficiency, consuming up to 80% less power than traditional incandescent lamps. This not only leads to substantial cost savings over time but also contributes to lower carbon emissions, making them an environmentally friendly choice. However, the initial costs can be higher, which might deter some buyers. Additionally, installation may require specialized expertise, particularly for commercial applications.
How Do Solar-Powered Lighting Systems Compare?
Solar-powered lighting is another viable alternative, especially for regions with abundant sunlight. These systems harness solar energy, resulting in negligible ongoing costs after installation. They are particularly advantageous for remote or off-grid locations, where traditional power sources may be unavailable. However, their performance is contingent on sunlight availability, which can vary seasonally and geographically. Maintenance is minimal, but regular cleaning of solar panels and periodic battery replacement is necessary to ensure optimal functionality.
Conclusion: How Should B2B Buyers Choose the Right Lighting Solution?
Selecting the right lighting solution involves a careful assessment of specific needs and circumstances. For buyers in urban areas with reliable electricity, traditional lamp manufacturers or LED solutions may be suitable. In contrast, businesses in remote locations or those focusing on sustainability might benefit more from solar-powered options. Ultimately, understanding the performance, costs, ease of implementation, and maintenance needs of each alternative will empower B2B buyers to make informed decisions that align with their operational goals and budget constraints.
Essential Technical Properties and Trade Terminology for lamp manufacturer
What Are the Key Technical Properties That Matter for Lamp Manufacturers?
When sourcing lamps for international markets, understanding the essential technical properties is crucial for B2B buyers. Here are six critical specifications:
-
Material Grade
– Definition: This refers to the quality of materials used in lamp manufacturing, including metals, glass, and plastics.
– Importance: Higher-grade materials typically result in better durability, thermal resistance, and aesthetics. For buyers, knowing the material grade ensures the products meet local regulations and customer expectations. -
Wattage
– Definition: Wattage indicates the power consumption of the lamp, directly affecting brightness and energy efficiency.
– Importance: Selecting the correct wattage is vital for energy compliance and cost-efficiency. Buyers should consider their market’s standards for energy consumption to avoid penalties. -
Color Temperature
– Definition: Measured in Kelvin (K), this property describes the color of the light emitted by the lamp, ranging from warm (below 3000K) to cool (above 5000K).
– Importance: Different applications require specific color temperatures. For instance, warm lights are preferred in residential settings, while cooler lights are suitable for workspaces. Buyers must align their product offerings with customer preferences. -
Lifespan
– Definition: This indicates how long a lamp is expected to last before it needs replacement, typically measured in hours.
– Importance: A longer lifespan reduces replacement frequency, leading to cost savings for end-users. Buyers should prioritize products with a proven lifespan to enhance customer satisfaction. -
IP Rating (Ingress Protection)
– Definition: This rating classifies the degree of protection against solid objects and liquids, indicated by two digits (e.g., IP65).
– Importance: Understanding the IP rating is essential for applications in harsh environments, such as outdoor or industrial settings. Buyers should ensure the lamps meet the necessary ratings for their target applications. -
Voltage Rating
– Definition: This indicates the electrical voltage that the lamp can operate on, commonly 120V or 230V.
– Importance: Voltage compatibility is critical for ensuring product functionality in different regions. Buyers must be aware of local voltage standards to avoid compatibility issues.
What Are Common Trade Terms Used in the Lamp Manufacturing Industry?
Familiarity with industry jargon is essential for effective communication and negotiation. Here are six common terms every B2B buyer should know:
-
OEM (Original Equipment Manufacturer)
– Definition: A company that produces parts or equipment that may be marketed by another manufacturer.
– Application: Buyers often work with OEMs to customize lamps to their specifications, ensuring alignment with their brand. -
MOQ (Minimum Order Quantity)
– Definition: The smallest quantity of a product that a supplier is willing to sell.
– Application: Understanding the MOQ helps buyers manage inventory costs and determine feasibility for large-scale purchases. -
RFQ (Request for Quotation)
– Definition: A document issued by a buyer to solicit price quotes from suppliers for specific quantities and specifications.
– Application: Issuing an RFQ allows buyers to compare prices and terms from multiple suppliers, facilitating informed decision-making. -
Incoterms (International Commercial Terms)
– Definition: A set of predefined international trade terms published by the International Chamber of Commerce that clarify the responsibilities of buyers and sellers.
– Application: Familiarity with Incoterms helps buyers understand shipping responsibilities, risks, and costs associated with international transactions. -
Lead Time
– Definition: The amount of time between the initiation of a process and its completion, particularly in manufacturing and shipping.
– Application: Knowing the lead time is essential for buyers to plan inventory levels and meet market demand efficiently. -
Certification Standards
– Definition: Regulatory benchmarks that products must meet to ensure safety and performance, such as CE marking in Europe or UL certification in the U.S.
– Application: Buyers should verify that lamps meet relevant certification standards to ensure compliance and consumer safety in their markets.
Understanding these technical properties and trade terms equips international B2B buyers with the knowledge needed to make informed purchasing decisions in the lamp manufacturing industry.
Navigating Market Dynamics and Sourcing Trends in the lamp manufacturer Sector
What Are the Current Market Dynamics and Key Trends in the Lamp Manufacturing Sector?
The global lamp manufacturing sector is witnessing transformative changes driven by technological advancements, consumer preferences, and sustainability concerns. The rise of LED technology has been a game-changer, leading to energy-efficient and longer-lasting lighting solutions. This shift not only reduces electricity consumption but also lowers operational costs for businesses, making it an attractive option for international B2B buyers, especially in regions like Africa, South America, the Middle East, and Europe.
Emerging trends in B2B sourcing include the adoption of smart lighting systems, which integrate IoT technologies for enhanced control and automation. This trend is particularly relevant for industries seeking to optimize energy usage and improve operational efficiency. Additionally, a growing emphasis on design and aesthetics has led manufacturers to innovate in terms of product offerings, catering to diverse market needs. As international buyers explore sourcing options, they should consider suppliers that are not only technologically advanced but also responsive to regional market demands.
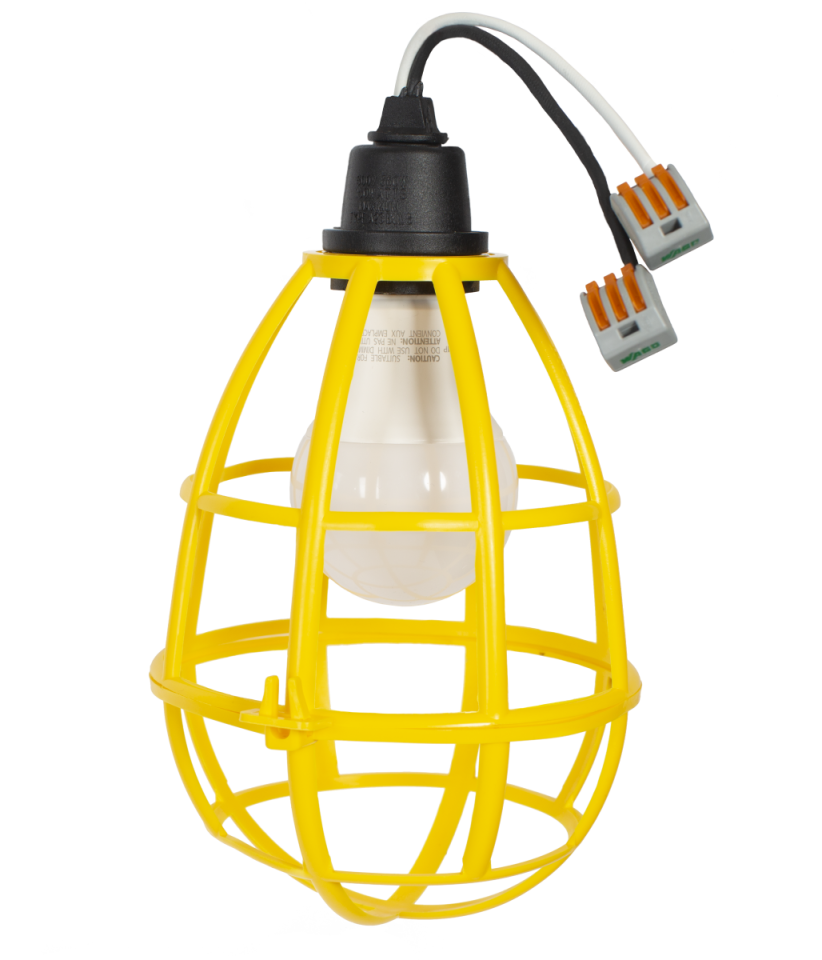
A stock image related to lamp manufacturer.
Moreover, the increasing importance of e-commerce platforms in the procurement process is reshaping the landscape for B2B buyers. Online marketplaces provide access to a broader range of suppliers and facilitate price comparisons, helping buyers make informed decisions. Understanding these market dynamics can empower international B2B buyers to navigate the lamp manufacturing sector effectively, ensuring they align with suppliers who meet their specific needs.
How Is Sustainability and Ethical Sourcing Impacting the Lamp Manufacturing Industry?
Sustainability has emerged as a cornerstone in the lamp manufacturing sector, influencing sourcing strategies and supplier selection. The environmental impact of traditional lighting solutions has spurred demand for eco-friendly alternatives. International B2B buyers are increasingly prioritizing suppliers who adhere to sustainable practices, such as using recyclable materials and minimizing waste during production processes.
Ethical sourcing is another critical consideration. Buyers should seek manufacturers that maintain transparency in their supply chains and demonstrate a commitment to fair labor practices. Certifications such as Energy Star and RoHS (Restriction of Hazardous Substances) are essential indicators of a supplier’s dedication to sustainability and safety standards. By choosing partners with these certifications, buyers can ensure that their sourcing decisions contribute positively to environmental conservation and social responsibility.
Furthermore, the integration of ‘green’ materials in lamp production is gaining traction. Biodegradable plastics and natural fibers are being explored as alternatives to conventional materials, aligning with the broader movement towards sustainable consumption. For B2B buyers, leveraging these insights can enhance their brand image and appeal to environmentally conscious consumers, fostering long-term loyalty.
What Is the Brief Evolution and History of the Lamp Manufacturing Sector?
The lamp manufacturing sector has evolved significantly over the centuries, transitioning from simple oil lamps to sophisticated LED lighting solutions. The invention of the electric light bulb in the late 19th century marked a pivotal moment, revolutionizing how people illuminate their spaces. Over the years, advancements in technology have led to the development of various lighting types, including incandescent, fluorescent, and ultimately, LED lamps.
In recent decades, the focus has shifted towards energy efficiency and sustainability, driven by both regulatory pressures and consumer demand. This evolution has prompted manufacturers to innovate continuously, exploring new materials and technologies to meet changing market needs. For international B2B buyers, understanding this historical context is crucial for making informed sourcing decisions, as it highlights the industry’s trajectory towards greater efficiency and environmental stewardship. As the sector continues to evolve, staying abreast of these trends will be vital for buyers seeking to partner with forward-thinking manufacturers.
Frequently Asked Questions (FAQs) for B2B Buyers of lamp manufacturer
-
How do I determine the right lamp manufacturer for my needs?
To find the best lamp manufacturer, consider factors like production capacity, quality certifications (such as ISO), and experience in your specific market. Engage in direct communication with potential suppliers to assess their responsiveness and willingness to customize products. Additionally, seek out reviews or testimonials from other B2B buyers in your region to gauge reliability and product quality. Attending trade shows can also provide firsthand insights into manufacturers’ offerings. -
What are the key considerations when sourcing lamps internationally?
When sourcing lamps internationally, prioritize understanding local regulations regarding safety and energy efficiency standards. Assess the manufacturer’s ability to meet these requirements and their experience with exporting to your region. Payment terms, shipping logistics, and lead times are also critical; ensure that you have clear agreements in place to avoid unexpected delays. Lastly, consider the total landed cost, including tariffs and taxes, to evaluate the overall feasibility of the purchase. -
What customization options should I expect from lamp manufacturers?
Most lamp manufacturers offer various customization options, including design, size, color, and lighting technology (such as LED or incandescent). When discussing customization, be clear about your specific requirements and ask about the minimum order quantities (MOQs) for customized products. Additionally, inquire about the design process—some manufacturers may provide prototypes or samples before full-scale production, which can help ensure the final product meets your expectations. -
What are typical payment terms when working with lamp manufacturers?
Payment terms can vary significantly between manufacturers, but common practices include a deposit (typically 30-50%) upfront, with the balance due upon shipment or after inspection. It’s crucial to negotiate these terms early in the discussions to ensure they align with your cash flow needs. Some manufacturers may also offer financing options or letter of credit arrangements, which can provide additional security for both parties involved. -
How can I verify the quality of lamps before placing a large order?
To ensure product quality, request samples from the manufacturer before committing to a large order. Conduct a thorough inspection of these samples, focusing on materials, finish, and functionality. Additionally, consider third-party quality assurance services that can conduct factory audits or product inspections on your behalf. Establishing a clear quality assurance protocol in your contract can also help mitigate risks associated with defective products. -
What logistics considerations should I keep in mind when importing lamps?
Effective logistics planning is essential when importing lamps. Evaluate shipping options and timelines, considering factors like freight costs, customs clearance processes, and potential delays. Collaborating with a freight forwarder can streamline this process, as they can handle documentation and compliance with local regulations. Additionally, ensure that your chosen shipping method is suitable for the type of lamps being transported, as some may require special handling. -
What are the minimum order quantities (MOQs) I should expect from lamp manufacturers?
Minimum order quantities can vary widely among lamp manufacturers, often ranging from a few dozen to several hundred units depending on the product type and customization level. It’s essential to discuss MOQs upfront, as they can impact your purchasing decisions. Some manufacturers may offer lower MOQs for standard products while setting higher MOQs for customized orders, so clarify these details to ensure they fit your business needs. -
How can I build a long-term relationship with a lamp manufacturer?
Building a long-term relationship with a lamp manufacturer involves consistent communication and transparency. Provide feedback on product quality and performance, and share your future needs and forecasts to help them plan accordingly. Consider negotiating favorable terms for repeat orders, and stay engaged through regular check-ins. Attending trade shows or manufacturer events can also strengthen your partnership and keep you informed about new products or innovations.
Important Disclaimer & Terms of Use
⚠️ Important Disclaimer
The information provided in this guide, including content regarding manufacturers, technical specifications, and market analysis, is for informational and educational purposes only. It does not constitute professional procurement advice, financial advice, or legal advice.
While we have made every effort to ensure the accuracy and timeliness of the information, we are not responsible for any errors, omissions, or outdated information. Market conditions, company details, and technical standards are subject to change.
B2B buyers must conduct their own independent and thorough due diligence before making any purchasing decisions. This includes contacting suppliers directly, verifying certifications, requesting samples, and seeking professional consultation. The risk of relying on any information in this guide is borne solely by the reader.
Strategic Sourcing Conclusion and Outlook for lamp manufacturer
In the dynamic landscape of lamp manufacturing, strategic sourcing remains a pivotal approach for international B2B buyers. By prioritizing quality, sustainability, and innovation, businesses can enhance their supply chain resilience and meet the growing demand for energy-efficient lighting solutions. Buyers from regions such as Africa, South America, the Middle East, and Europe should focus on establishing partnerships with manufacturers who not only understand local market nuances but also adhere to international quality standards.
How Can Strategic Sourcing Enhance Your Lamp Procurement?
Implementing a strategic sourcing framework allows organizations to leverage market insights, optimize costs, and improve product quality. By engaging directly with manufacturers, buyers can negotiate favorable terms and ensure a reliable supply of products that meet specific requirements. Furthermore, as sustainability becomes a key consideration, sourcing from manufacturers committed to eco-friendly practices can significantly bolster a company’s brand reputation and appeal to environmentally conscious consumers.
What’s Next for International Buyers in the Lamp Industry?
Looking ahead, the lamp manufacturing sector is poised for growth, driven by technological advancements and increasing energy regulations. International buyers are encouraged to stay informed about emerging trends, such as smart lighting solutions and the integration of IoT technologies. By embracing these innovations and fostering strong supplier relationships, businesses can position themselves for success in an evolving marketplace. Make strategic sourcing a cornerstone of your procurement strategy today to harness the full potential of the lamp manufacturing industry.