Discover Cost-Effective Welding Machines from China (2025)
Introduction: Navigating the Global Market for welding machines china
Navigating the global market for welding machines from China presents a unique set of challenges for international B2B buyers, especially those from regions such as Africa, South America, the Middle East, and Europe. Sourcing high-quality welding machines requires not just an understanding of the various types available, such as MIG, TIG, and stick welders, but also insight into their specific applications across different industries. This guide aims to provide a comprehensive overview that addresses key aspects of the procurement process, including supplier vetting, cost considerations, and the latest technology trends.
As an international buyer, you may face hurdles in identifying reliable suppliers, understanding the intricacies of shipping and customs, and ensuring compliance with local regulations. With this guide, you will be empowered to make informed purchasing decisions that align with your business needs. We delve into crucial factors such as the reputation of Chinese manufacturers, quality control measures, and effective negotiation strategies that can enhance your procurement process.
By equipping you with actionable insights and practical advice, this resource seeks to demystify the complexities of sourcing welding machines from China, ultimately enabling you to achieve greater efficiency and cost-effectiveness in your operations. Whether you are operating in sectors like construction, manufacturing, or automotive, this guide serves as your roadmap to successful procurement in the dynamic global marketplace.
Understanding welding machines china Types and Variations
Type Name | Key Distinguishing Features | Primary B2B Applications | Brief Pros & Cons for Buyers |
---|---|---|---|
MIG Welding Machines | Uses a continuous wire feed; ideal for thin materials | Automotive, manufacturing, and construction | Pros: High speed, easy to learn. Cons: Limited to clean surfaces. |
TIG Welding Machines | Uses a non-consumable tungsten electrode; offers precision | Aerospace, piping, and art fabrication | Pros: High-quality welds, versatility. Cons: Slower process, requires skill. |
Stick Welding Machines | Utilizes a consumable electrode; portable and versatile | Construction, repair, and maintenance | Pros: Works on rusted or dirty surfaces. Cons: Less efficient for thin materials. |
Plasma Arc Welding Machines | Uses a plasma torch; suitable for high-speed applications | Aerospace and heavy fabrication | Pros: High precision, speed. Cons: Higher operational costs. |
Submerged Arc Welding Machines | Fuses metal under a blanket of flux; ideal for thick materials | Shipbuilding and heavy structural work | Pros: Deep penetration, minimal fumes. Cons: Limited to flat or horizontal positions. |
What are the characteristics of MIG Welding Machines and their suitability for B2B buyers?
MIG (Metal Inert Gas) welding machines are characterized by their use of a continuous wire feed, making them particularly effective for welding thin materials. They are widely used in the automotive and manufacturing industries due to their high speed and ease of use. For B2B buyers, MIG welding machines are suitable for operations requiring quick turnaround times and less skilled labor, but they are best suited for clean surfaces, which might necessitate additional preparation work.
How does TIG Welding Machines provide precision in welding?
TIG (Tungsten Inert Gas) welding machines stand out for their precision, utilizing a non-consumable tungsten electrode. This type of welding is favored in industries such as aerospace and piping, where high-quality welds are critical. B2B buyers should consider TIG welding machines for applications that demand meticulous craftsmanship, though the process is slower and requires a higher level of skill compared to MIG welding. This can increase training costs but results in superior weld quality.
Why Stick Welding Machines are versatile for different applications?
Stick welding machines employ a consumable electrode and are known for their portability and versatility. They can operate effectively on rusted or dirty surfaces, making them ideal for construction and maintenance tasks. For B2B buyers, stick welding machines offer an advantage in diverse working conditions, although they may not be as efficient for thin materials. Their robustness and lower initial investment make them appealing for various industries.
What makes Plasma Arc Welding Machines suitable for high-speed applications?
Plasma arc welding machines utilize a plasma torch, allowing for high-speed and precise welding. This technology is particularly beneficial in aerospace and heavy fabrication sectors where speed and accuracy are paramount. B2B buyers should weigh the benefits of plasma arc welding against its higher operational costs, as it offers significant advantages in terms of weld quality and efficiency in demanding applications.
How do Submerged Arc Welding Machines excel in heavy structural work?
Submerged arc welding machines are designed to fuse metals under a blanket of flux, making them ideal for welding thick materials commonly found in shipbuilding and heavy structural work. They provide deep penetration and produce minimal fumes, which is advantageous for health and safety. For B2B buyers, the limitations of this method to flat or horizontal positions must be considered, but the efficiency and quality of welds make it a valuable investment for large-scale projects.
Related Video: 4 Types of Welding Explained: MIG vs TIG vs Stick vs Flux Core
Key Industrial Applications of welding machines china
Industry/Sector | Specific Application of welding machines china | Value/Benefit for the Business | Key Sourcing Considerations for this Application |
---|---|---|---|
Construction | Structural Steel Fabrication | Enhanced strength and durability of structures | Quality assurance, certifications, and after-sales support |
Automotive Manufacturing | Vehicle Body Assembly | Increased production speed and efficiency | Compatibility with existing systems and local regulations |
Oil and Gas | Pipeline Welding | Ensured integrity and safety of transportation | Compliance with international standards and material quality |
Shipbuilding | Hull Construction | Improved resistance to environmental factors | Availability of specialized welding techniques and equipment |
Heavy Machinery | Equipment Assembly | Enhanced performance and longevity of machinery | Technical support and adaptability to various materials |
How is Welding Machines China Used in the Construction Industry?
In the construction sector, welding machines from China are primarily used for structural steel fabrication. These machines enable the joining of steel components, ensuring that buildings and bridges have enhanced strength and durability. For international B2B buyers, especially from regions like Africa and South America, sourcing high-quality welding machines that comply with local building codes is crucial. Buyers should also consider the availability of technical support and spare parts to ensure operational continuity.
What Role Do Welding Machines Play in Automotive Manufacturing?
In automotive manufacturing, Chinese welding machines are essential for vehicle body assembly. They provide the capability to weld various materials together, which increases production speed and efficiency. For buyers in Europe and the Middle East, it’s important to select machines that meet stringent safety and quality standards. Additionally, compatibility with existing manufacturing systems and the ability to adapt to diverse material types can significantly influence purchasing decisions.
How Are Welding Machines Utilized in the Oil and Gas Industry?
Welding machines from China are critical in the oil and gas sector, particularly for pipeline welding. These machines ensure the integrity and safety of pipelines, which are essential for transporting oil and gas over long distances. Buyers in regions like Africa and the Middle East should prioritize sourcing machines that meet international safety standards and are capable of handling high-pressure environments. Understanding the specific material requirements and welding techniques is also vital for successful procurement.
What Are the Applications of Welding Machines in Shipbuilding?
In the shipbuilding industry, welding machines are employed for hull construction, where they improve resistance to environmental factors such as corrosion and harsh marine conditions. For B2B buyers from Europe and South America, sourcing welding equipment that offers specialized techniques, such as submerged arc welding, can enhance the durability of vessels. Additionally, evaluating the manufacturer’s experience in the maritime sector can provide insights into the reliability of the equipment.
How Do Welding Machines Benefit Heavy Machinery Manufacturing?
In heavy machinery manufacturing, Chinese welding machines are used for equipment assembly, significantly enhancing the performance and longevity of machinery. Buyers, particularly from South America and Africa, should consider machines that offer versatility in welding different materials and thicknesses. Furthermore, ensuring that the supplier provides adequate technical support and training can facilitate smoother operations and maintenance, thereby maximizing the investment in welding technology.
Related Video: KUKA Robots for the Welding Industry
3 Common User Pain Points for ‘welding machines china’ & Their Solutions
Scenario 1: Navigating Quality Assurance Challenges in Sourcing Welding Machines from China
The Problem: B2B buyers often face significant hurdles when sourcing welding machines from China due to concerns over quality assurance. In regions such as Africa and South America, where the manufacturing standards may vary, buyers worry about the durability and reliability of the machines they are importing. Poor quality can lead to increased downtime, additional costs for repairs, and even safety hazards, jeopardizing production schedules and profit margins.
The Solution: To mitigate these risks, buyers should implement a comprehensive quality assurance strategy. Start by thoroughly vetting suppliers—look for manufacturers with ISO certifications and a proven track record of producing high-quality welding equipment. Engage third-party inspection services to conduct pre-shipment audits. This step can help ensure that the machines meet international standards before they are shipped. Additionally, consider visiting the manufacturing facility if feasible, or request virtual tours to assess the production processes firsthand. Establishing a clear communication channel with suppliers can also facilitate better understanding of product specifications and expectations.
Scenario 2: Dealing with Language Barriers and Miscommunication
The Problem: Language barriers present a significant challenge for international B2B buyers when negotiating and placing orders for welding machines from China. Miscommunication can result in incorrect specifications, leading to the purchase of machines that do not meet operational needs. This can cause delays, frustration, and financial losses, particularly in fast-paced industries where time is of the essence.
The Solution: To overcome language barriers, buyers should utilize bilingual staff or hire professional translators during negotiations. It is also advisable to use detailed technical drawings and specifications in both English and the supplier’s native language to minimize misunderstandings. Employing project management tools that support multilingual communication can streamline collaboration. In addition, consider establishing a local representative in China who can act as a liaison. This representative can help facilitate clear communication, ensuring that all parties are on the same page regarding product features, delivery schedules, and payment terms.
Scenario 3: Understanding Compliance and Regulatory Issues
The Problem: B2B buyers often struggle with compliance and regulatory challenges when importing welding machines from China. Different countries have varying standards regarding safety, emissions, and operational regulations. Buyers may inadvertently import machines that do not meet local compliance requirements, leading to fines, product recalls, or even legal repercussions.
The Solution: To navigate these complexities, it is crucial for buyers to conduct thorough research on their country’s regulations pertaining to welding machinery. Engage legal experts or compliance consultants who specialize in international trade to ensure that all imported equipment adheres to local laws. Create a checklist of compliance requirements, including certifications such as CE marking for European markets or ANSI standards for the U.S. market. Before finalizing a purchase, request documentation from suppliers that confirms their machines meet all necessary standards. Additionally, consider engaging with trade associations or industry groups in your region that can provide resources and guidance on compliance issues.
By addressing these common pain points with actionable solutions, B2B buyers can streamline their sourcing processes and enhance their operational efficiency when dealing with welding machines from China.
Strategic Material Selection Guide for welding machines china
What Are the Key Materials Used in Welding Machines from China?
When selecting welding machines from China, understanding the materials used in their construction is crucial for ensuring optimal performance and longevity. Here, we analyze four common materials: steel, aluminum, copper, and plastic composites. Each material has unique properties, advantages, and limitations that can significantly impact application suitability and operational efficiency.
How Does Steel Impact Welding Machine Performance?
Key Properties: Steel is renowned for its strength and durability. It typically has high-temperature ratings, making it suitable for high-pressure applications. Additionally, steel exhibits good corrosion resistance when treated with appropriate coatings.
Pros & Cons: The primary advantage of steel is its robustness, which translates to a longer lifespan for welding machines. However, its weight can be a disadvantage, especially in portable applications. Manufacturing complexity can also be higher due to the need for precision machining and welding.
Impact on Application: Steel is compatible with a variety of media, including gases and liquids, making it versatile for different welding environments. However, its susceptibility to rust in humid conditions can be a concern.
Considerations for International B2B Buyers: Buyers from regions like Africa and South America should ensure compliance with local standards, such as ASTM or DIN, to guarantee material quality. Understanding the specific corrosion resistance ratings required in their environments is essential.
What Role Does Aluminum Play in Welding Machines?
Key Properties: Aluminum is lightweight and has excellent thermal conductivity. It is also resistant to corrosion, making it ideal for outdoor applications.
Pros & Cons: The main advantage of aluminum is its weight, which facilitates portability. However, aluminum’s lower strength compared to steel may limit its use in high-stress applications. Additionally, welding aluminum can require specialized techniques and equipment.
Impact on Application: Aluminum is particularly suitable for applications involving lightweight structures, such as automotive and aerospace industries. Its compatibility with various welding processes, including TIG and MIG, enhances its versatility.
Considerations for International B2B Buyers: Buyers in Europe and the Middle East should be aware of the specific welding standards applicable to aluminum, such as EN or ISO. Additionally, understanding the thermal expansion properties of aluminum is crucial for ensuring joint integrity.
Why Is Copper Important for Welding Machines?
Key Properties: Copper is known for its excellent electrical conductivity and thermal properties. It can withstand high temperatures and is resistant to corrosion.
Pros & Cons: The key advantage of copper is its superior conductivity, making it ideal for applications requiring efficient heat transfer. However, copper can be more expensive than other materials and may require specialized welding techniques.
Impact on Application: Copper is often used in welding machines for components like electrodes and cables, where conductivity is paramount. Its compatibility with various welding processes enhances its application range.
Considerations for International B2B Buyers: Buyers should consider the cost implications of using copper in their machines, especially in regions where copper prices fluctuate. Compliance with standards such as JIS for electrical components is also essential.
How Do Plastic Composites Fit into Welding Machine Design?
Key Properties: Plastic composites are lightweight and resistant to corrosion and chemicals. They can be molded into complex shapes, allowing for innovative designs.
Pros & Cons: The primary advantage of plastic composites is their lightweight nature, which aids in portability. However, they may not withstand high temperatures as well as metals, limiting their use in certain applications.
Impact on Application: Plastic composites are often used in non-structural components of welding machines, such as casings and handles. Their resistance to corrosion makes them suitable for harsh environments.
Considerations for International B2B Buyers: Buyers should ensure that the plastic composites used meet relevant safety and environmental standards. Understanding the thermal limits of these materials is critical for application suitability.
Summary Table of Material Selection for Welding Machines from China
Material | Typical Use Case for welding machines china | Key Advantage | Key Disadvantage/Limitation | Relative Cost (Low/Med/High) |
---|---|---|---|---|
Steel | Structural components in heavy-duty machines | High strength and durability | Heavy and complex manufacturing | Medium |
Aluminum | Lightweight applications in automotive | Lightweight and corrosion-resistant | Lower strength than steel | High |
Copper | Electrical components and electrodes | Excellent conductivity | Higher cost and specialized welding | High |
Plastic Composites | Non-structural components like casings | Lightweight and corrosion-resistant | Limited temperature tolerance | Low |
This guide provides a comprehensive overview of the strategic selection of materials for welding machines from China, offering valuable insights for international B2B buyers in diverse regions. Understanding these materials’ properties and implications will enable buyers to make informed decisions tailored to their specific needs.
In-depth Look: Manufacturing Processes and Quality Assurance for welding machines china
What Are the Main Stages in the Manufacturing Process of Welding Machines from China?
The manufacturing process for welding machines in China involves several critical stages designed to ensure high-quality output and adherence to international standards. Understanding these stages can empower international B2B buyers to make informed purchasing decisions.
-
Material Preparation: This initial stage involves sourcing high-quality raw materials, such as steel and aluminum. Suppliers typically conduct a thorough inspection of incoming materials to ensure they meet specified standards. The use of advanced cutting techniques, such as laser cutting or plasma cutting, is common to achieve precise dimensions.
-
Forming: During this phase, the prepared materials undergo various forming processes, including bending, stamping, and welding. Techniques like CNC (Computer Numerical Control) machining enhance accuracy and repeatability, which are crucial for producing parts that fit together seamlessly.
-
Assembly: Once the components are formed, they are assembled into the final product. Skilled technicians perform this task, often using both automated and manual processes. The assembly stage may include integrating electronic components, which requires precision to ensure the machine operates effectively.
-
Finishing: This stage encompasses surface treatment processes such as powder coating or painting to enhance durability and aesthetics. Quality control checks are performed throughout this process to catch any defects before the machines are packaged and shipped.
How Do Quality Assurance Practices Impact the Reliability of Welding Machines?
Quality assurance (QA) is a fundamental aspect of manufacturing welding machines in China. The implementation of international and industry-specific standards ensures that products not only meet customer expectations but also comply with regulatory requirements.
-
International Standards: Many Chinese manufacturers adhere to ISO 9001, a globally recognized standard for quality management systems. Compliance with ISO 9001 indicates that a manufacturer has established processes to consistently provide products that meet customer and regulatory requirements.
-
Industry-Specific Certifications: Additional certifications, such as CE marking for European markets and API standards for the oil and gas industry, indicate compliance with specific safety and performance criteria. These certifications can significantly influence a buyer’s decision, especially in regulated markets.
What Are the Key Quality Control Checkpoints in Welding Machine Manufacturing?
Quality control (QC) checkpoints are vital throughout the manufacturing process. These checkpoints help ensure that any deviations from quality standards are identified and corrected promptly.
-
Incoming Quality Control (IQC): This initial checkpoint involves inspecting raw materials before they enter the production line. It ensures that only high-quality materials are used, reducing the likelihood of defects in the finished product.
-
In-Process Quality Control (IPQC): Continuous monitoring occurs during the manufacturing process to catch defects early. This includes measuring dimensions, checking weld quality, and ensuring that assembly procedures are followed correctly.
-
Final Quality Control (FQC): Before products leave the factory, a comprehensive final inspection is conducted. This includes functional tests to ensure that the welding machines operate as intended and meet all specified standards.
What Testing Methods Are Commonly Used for Welding Machines?
Testing is a crucial component of quality assurance for welding machines. Various methods are employed to validate the functionality and safety of the final products.
-
Functional Testing: This involves running the welding machine to ensure it performs as expected under operational conditions. Buyers should inquire about the specific tests conducted and the results.
-
Non-Destructive Testing (NDT): Techniques such as ultrasonic testing and magnetic particle inspection are used to detect internal and surface defects without damaging the components. This is particularly important for ensuring the integrity of welds.
-
Performance Testing: This assesses the machine’s capabilities, such as welding speed and penetration, under different settings. It provides valuable data on the machine’s efficiency and effectiveness.
How Can B2B Buyers Verify Quality Control Practices of Suppliers?
For international B2B buyers, particularly those in Africa, South America, the Middle East, and Europe, verifying the quality control practices of potential suppliers is essential to mitigate risks.
-
Supplier Audits: Conducting on-site audits is one of the most effective ways to assess a supplier’s manufacturing and QC processes. Buyers should look for evidence of compliance with relevant standards and certifications.
-
Quality Reports: Requesting detailed quality assurance reports can provide insights into a manufacturer’s QC processes. These reports often include data on defect rates, testing results, and compliance with international standards.
-
Third-Party Inspections: Engaging third-party inspection agencies to evaluate the manufacturing processes and products can provide an unbiased assessment of quality. This is particularly beneficial for buyers who cannot visit the manufacturing site.
What Nuances Should International Buyers Be Aware of Regarding QC Certifications?
Understanding the nuances of quality control certifications is crucial for international B2B buyers.
-
Certification Recognition: Not all certifications are recognized equally across different regions. For example, CE marking is essential for products entering the European market, while other regions may have different requirements. Buyers should verify that the certifications held by their suppliers are relevant to their target markets.
-
Local Regulations: Buyers should be aware of local regulations that may affect the acceptance of certain certifications. Engaging local experts or consultants can provide valuable guidance in navigating these complexities.
-
Continuous Improvement: Many reputable manufacturers engage in continuous improvement practices, often seeking to exceed the minimum requirements set by certifications. Buyers should inquire about the manufacturer’s commitment to ongoing quality enhancement initiatives.
By understanding the manufacturing processes, quality control checkpoints, testing methods, and verification strategies, international B2B buyers can confidently engage with suppliers of welding machines from China, ensuring they receive products that meet their operational needs and regulatory requirements.
Practical Sourcing Guide: A Step-by-Step Checklist for ‘welding machines china’
To successfully procure welding machines from China, international B2B buyers need a structured approach to navigate the complexities of sourcing. This guide offers a practical checklist designed to assist you in making informed decisions throughout the procurement process.
Step 1: Define Your Technical Specifications
Clearly outline your technical requirements before engaging with suppliers. This includes specifying the type of welding machine needed (MIG, TIG, Stick, etc.), power output, portability, and any special features required for your operations. Having a detailed specification helps suppliers provide accurate quotations and ensures that the machines meet your operational needs.
Step 2: Research and Shortlist Suppliers
Begin by researching potential suppliers through platforms such as Alibaba, Made-in-China, and Global Sources. Look for manufacturers with a strong reputation and positive reviews. Create a shortlist based on:
– Experience: Prefer suppliers with at least 5 years in the industry.
– Certifications: Check for ISO certifications and compliance with international standards.
Step 3: Verify Supplier Certifications
Before proceeding with negotiations, confirm that the suppliers possess the necessary certifications. This includes:
– Quality Management Systems: ISO 9001 certification ensures consistent quality.
– Product-Specific Certifications: Look for CE, RoHS, or other relevant certifications depending on your market requirements.
Valid certifications not only ensure product quality but also compliance with regulations in your region.
Step 4: Request Samples
Once you have narrowed down your list, request samples of the welding machines you are interested in. Evaluate the samples based on:
– Performance: Test the machine to ensure it meets your specifications.
– Build Quality: Assess the durability and materials used in construction.
Samples provide a hands-on way to gauge whether the supplier can meet your standards before placing a larger order.
Step 5: Evaluate Pricing and Payment Terms
Engage in price negotiations with your shortlisted suppliers. Consider factors such as:
– Bulk Discounts: Inquire about pricing for larger orders.
– Payment Terms: Understand the payment schedule, including deposits and final payments.
Establishing clear pricing and payment terms helps prevent misunderstandings and ensures that you stay within budget.
Step 6: Assess Shipping and Logistics
Understand the shipping options available and the associated costs. Key points to consider include:
– Incoterms: Determine whether you will handle shipping (FOB) or if the supplier will manage it (CIF).
– Delivery Times: Clarify expected shipping durations and any potential delays.
Having a clear logistics plan is crucial for timely project execution and helps in budgeting for additional costs.
Step 7: Conduct a Final Quality Inspection
Before accepting the final shipment, arrange for a quality inspection. This can be done through third-party inspection companies that will:
– Verify Specifications: Ensure that the machines conform to your original specifications.
– Check for Damage: Inspect for any shipping damages or defects.
Conducting a final inspection minimizes the risk of receiving substandard equipment that could impact your operations.
By following this checklist, international buyers can navigate the complexities of sourcing welding machines from China effectively, ensuring that they make informed decisions that align with their business needs.
Comprehensive Cost and Pricing Analysis for welding machines china Sourcing
What Are the Key Cost Components for Welding Machines Sourcing from China?
When sourcing welding machines from China, understanding the cost structure is crucial for international B2B buyers. The primary cost components include:
-
Materials: The cost of raw materials such as steel, aluminum, and electronic components directly affects the pricing of welding machines. Buyers should consider the fluctuations in material costs due to market demand and global supply chain issues.
-
Labor: Labor costs in China can vary significantly based on the region and the complexity of the welding machine being manufactured. Skilled labor is often more expensive, impacting the overall cost.
-
Manufacturing Overhead: This includes expenses related to factory operations, utilities, and equipment maintenance. A well-managed facility can help keep these costs down, which can be beneficial for buyers.
-
Tooling: Custom tooling may be necessary for specialized welding machines. The initial investment in tooling can be substantial, but it can result in lower per-unit costs when producing larger quantities.
-
Quality Control (QC): Ensuring quality can involve additional costs, including inspections and certifications. Investing in QC can prevent costly defects and returns, making it a worthwhile expense for buyers.
-
Logistics: Shipping costs from China to the destination country should not be overlooked. Factors such as shipping method, distance, and customs duties can significantly affect the total cost.
-
Margin: Suppliers typically add a profit margin to cover their costs and generate profit. Understanding this margin can help buyers negotiate better prices.
How Do Price Influencers Affect Welding Machine Costs?
Several factors can influence the pricing of welding machines when sourced from China:
-
Volume/MOQ (Minimum Order Quantity): Larger orders often lead to lower per-unit costs. Buyers should assess their needs carefully to maximize cost efficiency.
-
Specifications/Customization: Custom features or specifications can increase the cost. Buyers should clearly define their requirements to avoid unexpected expenses.
-
Materials Used: The choice of materials can greatly impact pricing. Higher quality materials typically incur higher costs but can enhance the machine’s longevity and performance.
-
Quality and Certifications: Machines that meet international quality standards or have specific certifications (like ISO) may command higher prices. However, they often offer better reliability, which can be a critical factor for buyers.
-
Supplier Factors: Different suppliers may have varying pricing strategies based on their production capabilities, brand reputation, and operational efficiency. Conducting thorough supplier evaluations can yield significant savings.
-
Incoterms: The terms of shipment (like FOB, CIF, etc.) dictate who is responsible for shipping costs and risks. Understanding these terms can help buyers estimate their total costs more accurately.
What Negotiation and Cost-Efficiency Tips Should International B2B Buyers Consider?
When engaging with Chinese suppliers, international B2B buyers can adopt several strategies to enhance cost-efficiency:
-
Negotiation: Be prepared to negotiate not just price but also payment terms, delivery schedules, and warranties. Building a strong relationship with suppliers can lead to better deals over time.
-
Total Cost of Ownership (TCO): Look beyond the initial purchase price. Consider maintenance costs, potential downtime, and the machine’s operational efficiency when evaluating overall value.
-
Pricing Nuances: Be aware of regional pricing differences within China. Suppliers in major industrial zones may offer more competitive pricing due to economies of scale.
-
Market Research: Conduct thorough research on market prices for welding machines. This knowledge can empower buyers during negotiations, ensuring they secure a fair deal.
Disclaimer on Indicative Prices
Prices for welding machines sourced from China can fluctuate based on market conditions, currency exchange rates, and changes in material costs. Therefore, it is essential for buyers to seek updated quotes and conduct regular market assessments to ensure they are making informed purchasing decisions.
Alternatives Analysis: Comparing welding machines china With Other Solutions
When considering the procurement of welding solutions, it’s essential for international B2B buyers to evaluate alternatives that can meet their specific operational needs. While “welding machines China” are known for their affordability and varied options, other technologies may offer distinct advantages depending on the application and environment. Below, we compare welding machines from China with two viable alternatives: laser welding systems and MIG (Metal Inert Gas) welding machines.
Comparison Aspect | Welding Machines China | Laser Welding Systems | MIG Welding Machines |
---|---|---|---|
Performance | Good for general use; varies by model | High precision; ideal for thin materials | Versatile; suitable for various thicknesses |
Cost | Generally low-cost; affordable for bulk | High initial investment; long-term savings on labor | Moderate; equipment and consumables can add up |
Ease of Implementation | Generally easy setup; requires basic training | Requires specialized training; setup can be complex | Relatively easy; minimal training needed |
Maintenance | Varies by model; parts can be sourced locally | Low maintenance; requires specialized service | Regular maintenance required; easy to source parts |
Best Use Case | General fabrication, construction | Automotive, electronics, and precision industries | Construction, automotive, and repair industries |
What Are the Advantages and Disadvantages of Laser Welding Systems?
Laser welding systems are known for their precision and speed, making them ideal for applications requiring high-quality welds on thin materials. The main advantage is their ability to produce clean, precise joints with minimal heat affected zones, reducing the need for post-weld processing. However, the high initial investment and the requirement for skilled operators can be barriers for many businesses, particularly in developing regions.
How Does MIG Welding Compare to Welding Machines from China?
MIG welding machines are versatile and widely used across various industries. They are easier to operate than many alternatives, requiring less specialized training. The equipment is generally more affordable than laser systems and can handle a range of materials and thicknesses. However, the ongoing costs for consumables and the need for regular maintenance can add up over time. Additionally, MIG welding may not achieve the same level of precision as laser welding, making it less suitable for high-tech applications.
Conclusion: How Can B2B Buyers Choose the Right Welding Solution?
When selecting the appropriate welding solution, B2B buyers should consider their specific operational requirements, budget constraints, and the level of expertise available within their workforce. Welding machines from China may offer a cost-effective solution for general applications, while laser welding systems may be better suited for high-precision tasks. Conversely, MIG welding machines provide a good balance of versatility and ease of use. Ultimately, the choice should align with the buyer’s production goals, financial constraints, and long-term operational strategies.
Essential Technical Properties and Trade Terminology for welding machines china
When sourcing welding machines from China, understanding the essential technical properties and trade terminology is crucial for making informed purchasing decisions. This section outlines the key specifications and terms that every international B2B buyer should be familiar with.
What are the Critical Specifications of Welding Machines?
-
Material Grade
– The material grade of welding machines typically refers to the quality of the metal used in their construction. Common grades include carbon steel, stainless steel, and aluminum. For B2B buyers, selecting the appropriate material grade is vital as it affects the machine’s durability, performance, and suitability for specific applications. Higher-grade materials often translate to longer lifespans and reduced maintenance costs. -
Welding Current Range
– This specification indicates the range of welding currents that the machine can deliver, usually measured in Amperes (A). A broader current range allows for versatility in welding different materials and thicknesses. Buyers should consider their specific applications to ensure that the machine can handle the required welding processes effectively. -
Duty Cycle
– The duty cycle is defined as the percentage of time a welding machine can operate within a specific period without overheating. For instance, a 60% duty cycle means the machine can operate for 6 minutes out of 10 at a given load. Understanding the duty cycle is essential for B2B buyers, as it directly impacts productivity and efficiency in high-demand environments. -
Voltage Input
– Welding machines operate on different voltage inputs, such as 110V, 220V, or 380V. The choice of voltage input affects the machine’s compatibility with local power supplies and its operational efficiency. Buyers should confirm the voltage requirements to avoid complications upon delivery. -
Weight and Portability
– The weight of a welding machine can influence its portability and ease of use on job sites. Lightweight models may be easier to transport and set up, which can be advantageous for mobile operations. Buyers should assess their needs for portability versus the machine’s stability and performance.
What Are Common Trade Terms in the Welding Machine Industry?
-
OEM (Original Equipment Manufacturer)
– An OEM refers to a company that manufactures products or components that are marketed by another company. In the context of welding machines, understanding OEM relationships can help buyers identify reputable manufacturers and ensure product quality. -
MOQ (Minimum Order Quantity)
– MOQ is the smallest number of units a supplier is willing to sell. Buyers should inquire about MOQs when sourcing welding machines, as this affects inventory management and initial investment costs. Lower MOQs can provide flexibility for smaller businesses or projects. -
RFQ (Request for Quotation)
– An RFQ is a formal document used by buyers to request pricing and other information from suppliers. It is an essential step in the procurement process, allowing buyers to compare offers and negotiate terms effectively. -
Incoterms (International Commercial Terms)
– Incoterms define the responsibilities of buyers and sellers regarding shipping, insurance, and tariffs. Familiarity with Incoterms is crucial for B2B transactions, as they clarify who bears the risk and cost at different stages of shipping. Common terms include FOB (Free on Board) and CIF (Cost, Insurance, and Freight). -
Lead Time
– Lead time refers to the time taken from placing an order to receiving the product. Understanding lead times is critical for project planning and inventory management, especially in industries with tight deadlines.
By grasping these specifications and trade terms, international B2B buyers can navigate the complexities of sourcing welding machines from China, ultimately leading to more informed decisions and successful procurement strategies.
Navigating Market Dynamics and Sourcing Trends in the welding machines china Sector
What Are the Current Market Dynamics and Key Trends in the Welding Machines Sector from China?
The global market for welding machines is experiencing significant growth, driven by rapid industrialization, increased infrastructure development, and advancements in welding technologies. For international B2B buyers, particularly from regions like Africa, South America, the Middle East, and Europe, understanding these dynamics is crucial for effective sourcing strategies.
One of the primary trends is the shift towards automation in welding processes. With the advent of Industry 4.0, manufacturers are increasingly adopting robotic welding systems to enhance precision and efficiency. This trend is particularly relevant for buyers in sectors such as automotive, construction, and shipbuilding, where quality and speed are paramount. Additionally, the demand for portable and lightweight welding machines is rising, catering to the needs of smaller enterprises and on-site applications.
Another significant factor is the increasing focus on digitalization and smart technologies. B2B buyers are now looking for welding machines that offer connectivity features, allowing for real-time monitoring and data analytics. This shift is enhancing productivity and reducing downtime, making it an attractive proposition for businesses looking to optimize their operations.
Lastly, as global supply chains face disruptions, buyers are encouraged to diversify their sourcing options. Establishing relationships with multiple suppliers in China can mitigate risks associated with geopolitical tensions and trade tariffs. By leveraging China’s vast manufacturing capabilities, buyers can ensure a steady supply of welding machines that meet their specific needs.
How Is Sustainability Influencing Sourcing Trends for Welding Machines from China?
Sustainability is becoming a critical consideration in the sourcing of welding machines. International B2B buyers are increasingly aware of the environmental impacts associated with manufacturing processes and are seeking suppliers who prioritize sustainable practices.
One of the key aspects of this trend is the demand for eco-friendly welding machines. Buyers are looking for equipment that minimizes energy consumption and reduces emissions during operation. Manufacturers in China are responding by developing machines that incorporate energy-efficient technologies, such as inverter welding systems, which significantly lower energy use compared to traditional models.
Moreover, ethical sourcing has gained traction, with buyers placing emphasis on transparency in the supply chain. They are increasingly seeking suppliers who adhere to ethical labor practices and demonstrate a commitment to corporate social responsibility. Certifications like ISO 14001 (Environmental Management) and ISO 45001 (Occupational Health and Safety) are becoming essential criteria for selecting suppliers.
In addition, the use of sustainable materials in welding machines is a growing concern. Buyers are encouraged to inquire about the sourcing of raw materials and the presence of any certifications for green materials. This not only aligns with global sustainability goals but also enhances the brand image of businesses committed to environmental stewardship.
What Is the Historical Context of Welding Machines from China?
The welding machines sector in China has evolved remarkably over the past few decades. Initially, the market was dominated by low-cost, low-quality machines aimed primarily at domestic consumption. However, as China’s manufacturing capabilities advanced, the focus shifted towards producing high-quality welding equipment that meets international standards.
In the early 2000s, Chinese manufacturers began investing in research and development, leading to innovations in welding technologies. This period marked the emergence of advanced features such as inverter technology and automated welding systems, which gained popularity among global buyers.
Today, China’s welding machine industry is recognized as one of the largest and most competitive in the world. With a blend of affordability and technological sophistication, Chinese manufacturers are well-positioned to serve diverse international markets, making it an attractive sourcing destination for B2B buyers across various sectors.
Frequently Asked Questions (FAQs) for B2B Buyers of welding machines china
-
How do I choose the right welding machine for my business needs?
Selecting the appropriate welding machine hinges on your specific applications. Consider factors such as the materials you will be welding (steel, aluminum, etc.), the thickness of the materials, and the welding process required (MIG, TIG, or stick welding). Additionally, assess the machine’s duty cycle, portability, and power supply compatibility. Consulting with suppliers who can provide technical specifications and support is crucial to ensure you make an informed decision. -
What are the key features to look for in a welding machine from China?
When sourcing welding machines from China, prioritize features such as reliability, ease of use, and the availability of spare parts. Look for machines with advanced technology, such as inverter technology for improved energy efficiency, and those that comply with international safety standards. Additionally, consider machines that offer adjustable settings for different welding techniques and materials, ensuring versatility for various projects. -
How can I effectively vet Chinese suppliers for welding machines?
To vet Chinese suppliers, begin by checking their business licenses and certifications, such as ISO or CE. Request references from previous international clients and evaluate their online presence, including reviews and ratings. Consider visiting the supplier’s facility or using third-party inspection services to assess their manufacturing capabilities. Building a relationship with the supplier through clear communication about your requirements can also help ensure reliability. -
What are the minimum order quantities (MOQ) for welding machines from China?
Minimum order quantities can vary significantly between suppliers, typically ranging from 1 to 100 units. Some manufacturers may offer lower MOQs for custom orders, while others may require higher quantities for cost-effectiveness. When negotiating, clarify whether the MOQ applies to specific models or if it can be a mix of different products, which can provide flexibility for your purchasing needs. -
What payment terms should I expect when buying welding machines from China?
Payment terms for purchasing welding machines from China usually include options like T/T (telegraphic transfer), L/C (letter of credit), and sometimes PayPal for smaller transactions. Commonly, suppliers may request a 30% deposit upfront and the remaining 70% before shipment. It’s essential to negotiate terms that suit your cash flow, and consider using escrow services for added security, especially for larger orders. -
How do I ensure quality assurance when sourcing welding machines from China?
To ensure quality, request detailed specifications and certifications from your supplier. Conduct pre-shipment inspections through third-party services to verify that the machines meet your standards. Establish a quality assurance agreement outlining acceptable quality levels and inspection processes. Additionally, consider starting with a smaller order to evaluate the product’s performance before committing to larger quantities. -
What logistics considerations should I keep in mind when importing welding machines from China?
When importing welding machines, consider shipping methods (air freight vs. sea freight), costs, and transit times. Ensure that your supplier provides necessary documentation such as commercial invoices and packing lists. Be aware of customs regulations in your country, including duties and taxes, and choose a reliable freight forwarder to assist with the logistics process. Proper planning can help avoid delays and additional charges. -
What are the common challenges faced when sourcing welding machines from China, and how can I mitigate them?
Common challenges include language barriers, cultural differences, and varying quality standards. To mitigate these issues, invest time in building a strong relationship with your supplier and using clear, concise communication. Utilize professional translation services if necessary, and consider engaging with local trade experts who understand the Chinese market. Establishing trust and setting clear expectations can significantly reduce misunderstandings and enhance collaboration.
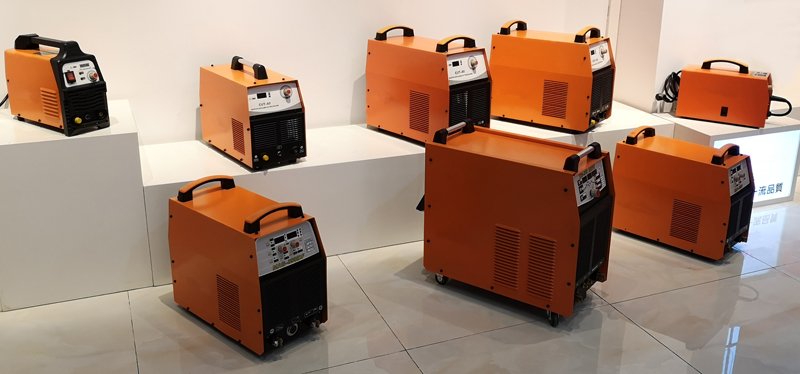
A stock image related to welding machines china.
Important Disclaimer & Terms of Use
⚠️ Important Disclaimer
The information provided in this guide, including content regarding manufacturers, technical specifications, and market analysis, is for informational and educational purposes only. It does not constitute professional procurement advice, financial advice, or legal advice.
While we have made every effort to ensure the accuracy and timeliness of the information, we are not responsible for any errors, omissions, or outdated information. Market conditions, company details, and technical standards are subject to change.
B2B buyers must conduct their own independent and thorough due diligence before making any purchasing decisions. This includes contacting suppliers directly, verifying certifications, requesting samples, and seeking professional consultation. The risk of relying on any information in this guide is borne solely by the reader.
Strategic Sourcing Conclusion and Outlook for welding machines china
What Are the Key Takeaways for B2B Buyers in the Welding Machine Market?
In conclusion, strategic sourcing of welding machines from China presents significant advantages for international B2B buyers, particularly from Africa, South America, the Middle East, and Europe. Key takeaways include the importance of understanding supplier capabilities, quality assurance practices, and the potential for cost savings. Establishing strong relationships with Chinese manufacturers can lead to better negotiation terms and enhanced customization options, ensuring that your specific operational needs are met.
How Can Buyers Enhance Their Sourcing Strategy?
As you navigate the complexities of sourcing, consider leveraging technology to streamline communication and supply chain management. Utilizing platforms that facilitate direct connections with manufacturers can enhance transparency and efficiency. Additionally, investing in local market research will provide deeper insights into trends and preferences, allowing you to make informed purchasing decisions.
What Does the Future Hold for Welding Machine Sourcing?
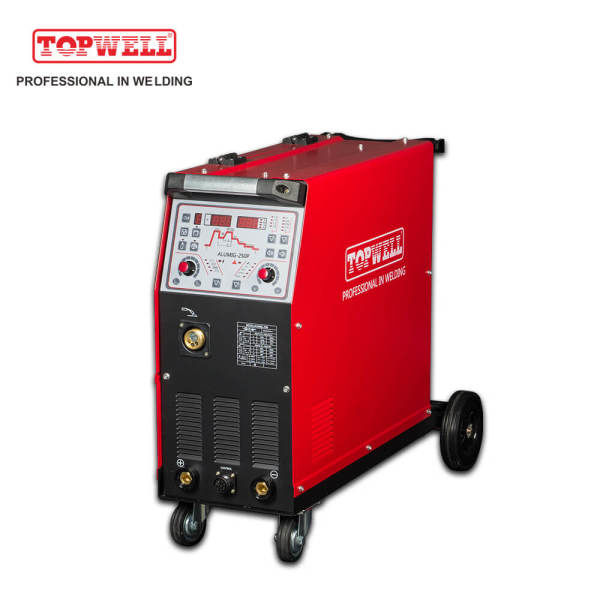
A stock image related to welding machines china.
Looking ahead, the welding machine market in China is poised for growth, driven by innovations in technology and increasing global demand. International buyers should remain proactive, adapting their strategies to embrace these changes. By doing so, you position your business to capitalize on emerging opportunities and stay ahead of the competition. Engage with trusted suppliers today to ensure a robust and competitive supply chain for tomorrow.