Discover Cost-Effective Solutions: Welding Equipment China (2025)
Introduction: Navigating the Global Market for welding equipment china
Navigating the global market for welding equipment from China presents a unique challenge for international B2B buyers, particularly those from Africa, South America, the Middle East, and Europe. With an increasing demand for high-quality welding solutions, sourcing reliable suppliers can be daunting. This guide aims to illuminate the multifaceted landscape of welding equipment, encompassing various types, applications, and essential supplier vetting processes. By offering insights into cost considerations and market trends, this resource empowers decision-makers to make informed purchases that align with their operational needs.
The welding equipment sector in China is not only expansive but also competitive, making it crucial for buyers to understand the nuances of product offerings and supplier capabilities. Whether you are looking for arc welders, MIG welding machines, or specialized accessories, this guide will help you identify the best options available in the market. Furthermore, we will delve into practical tips for assessing supplier reliability, ensuring that your investments yield quality results and enhance productivity.
As you navigate this complex market, our comprehensive guide equips you with the knowledge and tools necessary to optimize your sourcing strategy, fostering stronger business relationships and ensuring that your welding operations thrive in a competitive global landscape.
Understanding welding equipment china Types and Variations
Type Name | Key Distinguishing Features | Primary B2B Applications | Brief Pros & Cons for Buyers |
---|---|---|---|
MIG Welding Machines | Uses a continuous wire feed and gas shielding. | Automotive, construction, and manufacturing. | Pros: High productivity; easy to learn. Cons: Less effective for thicker materials. |
TIG Welding Machines | Provides precise control with a non-consumable tungsten electrode. | Aerospace, art, and high-quality fabrication. | Pros: Excellent for thin materials; clean welds. Cons: Slower process; requires skill. |
Stick Welding Machines | Utilizes a consumable electrode and is versatile in various environments. | Heavy industry, pipeline, and repair work. | Pros: Portable; works in windy or outdoor conditions. Cons: More cleanup required; less control over weld quality. |
Plasma Arc Welding Machines | Employs a focused arc for high precision and speed. | Aerospace, automotive, and electronics. | Pros: High speed and precision; versatile in materials. Cons: Equipment can be costly; requires skilled operators. |
Multi-Process Welding Machines | Combines multiple welding processes in one unit. | General manufacturing and repair shops. | Pros: Flexible for various applications; saves space. Cons: Can be complex to operate; potential for higher maintenance. |
What are the Key Characteristics of MIG Welding Machines?
MIG (Metal Inert Gas) welding machines are designed for high-speed welding and are favored for their ease of use. They utilize a continuously fed wire electrode and a shielding gas to protect the weld from contamination. This method is ideal for projects that require high productivity, such as automotive manufacturing and construction. When considering a MIG welder, buyers should evaluate the machine’s duty cycle, wire feed speed, and compatibility with different materials to ensure it meets their specific needs.
Why Choose TIG Welding Machines for Precision Work?
TIG (Tungsten Inert Gas) welding machines are known for their ability to produce clean and precise welds, making them suitable for applications in aerospace and artistic metal fabrication. The process involves a non-consumable tungsten electrode and is capable of welding thin materials with minimal distortion. Buyers should consider the machine’s amperage range and features such as high-frequency start capabilities, which can enhance performance. Additionally, while TIG welding requires more skill and practice, the quality of the welds often justifies the investment.
How Do Stick Welding Machines Offer Versatility?
Stick welding machines, also known as SMAW (Shielded Metal Arc Welding) machines, are versatile and can be used in various environments, including outdoor and windy conditions. They utilize a consumable electrode that melts to form the weld, making them a popular choice for heavy industrial applications and pipeline work. When purchasing stick welders, buyers should look for portability, ease of maintenance, and the ability to work with different electrode types. The ability to perform well in adverse conditions makes stick welding machines a practical choice for many businesses.
What Advantages Do Plasma Arc Welding Machines Provide?
Plasma arc welding machines are recognized for their high precision and speed, utilizing a focused arc to melt the metal. This method is particularly effective for welding thin materials and is widely used in aerospace and automotive industries. Buyers should assess the equipment’s power settings, cooling systems, and compatibility with different materials when considering plasma welding machines. While they can be more expensive and require skilled operators, the quality and efficiency of plasma welding can significantly enhance production capabilities.
Why Invest in Multi-Process Welding Machines?
Multi-process welding machines offer the flexibility to perform various welding processes, such as MIG, TIG, and stick welding, all in one unit. This adaptability is particularly beneficial for general manufacturing and repair shops that handle diverse projects. When evaluating multi-process machines, buyers should consider the ease of switching between processes, the machine’s weight and portability, and the learning curve for operators. While they can be more complex and may require higher maintenance, the space-saving design and versatility can provide substantial long-term benefits for businesses.
Related Video: 4 Types of Welding Explained: MIG vs TIG vs Stick vs Flux Core
Key Industrial Applications of welding equipment china
Industry/Sector | Specific Application of Welding Equipment China | Value/Benefit for the Business | Key Sourcing Considerations for this Application |
---|---|---|---|
Automotive Manufacturing | Assembly of vehicle frames and components | Enhanced structural integrity and safety of vehicles | Compliance with international standards, durability, and efficiency of welding equipment. |
Construction | Fabrication of steel structures and frameworks | Increased project speed and reduced labor costs | Availability of customized solutions and after-sales support. |
Oil & Gas | Pipeline construction and repair | Ensured leak-proof joints and increased safety | Resistance to harsh environmental conditions and certification for safety standards. |
Shipbuilding | Hull fabrication and repair | Improved vessel durability and operational efficiency | Quality of materials used and adaptability to different welding techniques. |
Renewable Energy | Assembly of wind turbine components | Contribution to sustainable energy solutions | Availability of energy-efficient welding processes and compliance with environmental regulations. |
How is Welding Equipment from China Used in Automotive Manufacturing?
In the automotive sector, welding equipment from China is critical for assembling vehicle frames and components. The equipment ensures high-quality welds that enhance the structural integrity and safety of vehicles. International B2B buyers, particularly from regions like Europe and South America, must consider equipment that meets stringent automotive industry standards and offers durability under continuous use. Additionally, the availability of advanced features such as automation can significantly improve production efficiency.
What Role Does Welding Equipment Play in Construction?
Welding equipment from China is extensively used in the construction industry for fabricating steel structures and frameworks. This application allows for faster project execution and reduced labor costs, which is crucial for competitive bidding in international markets. Buyers should prioritize sourcing equipment that can deliver consistent quality and support for large-scale projects, including the ability to handle various steel grades and thicknesses. After-sales support and service availability are also vital considerations.
How is Welding Equipment Critical for Oil & Gas Industries?
In the oil and gas sector, welding equipment is essential for constructing and repairing pipelines. The equipment must produce leak-proof joints that can withstand high pressure and harsh environmental conditions. International buyers from Africa and the Middle East should focus on sourcing equipment that complies with safety standards, ensuring operational safety and reliability. Additionally, features that enhance corrosion resistance and adaptability to different welding processes are key considerations.
What is the Importance of Welding Equipment in Shipbuilding?
Welding equipment is fundamental in shipbuilding for hull fabrication and repair. This equipment contributes to improved vessel durability and operational efficiency. Buyers in regions with a significant maritime industry, such as Europe, should look for welding solutions that offer high precision and adaptability to various materials used in ship construction. Quality assurance and certification for marine applications are crucial factors when sourcing welding equipment.
How Does Welding Equipment Support Renewable Energy Initiatives?
Welding equipment from China plays a pivotal role in assembling components for renewable energy solutions, such as wind turbines. The equipment aids in creating durable connections that are essential for the operational efficiency of these systems. International B2B buyers should seek out energy-efficient welding processes that align with sustainability goals. Compliance with environmental regulations and the availability of advanced welding technologies that minimize waste are also significant sourcing considerations for this sector.
Related Video: What is MIG Welding? (GMAW)
3 Common User Pain Points for ‘welding equipment china’ & Their Solutions
Scenario 1: Navigating Quality Assurance in Chinese Welding Equipment
The Problem: One of the foremost challenges faced by B2B buyers sourcing welding equipment from China is the inconsistency in product quality. Many buyers report receiving equipment that does not meet their specifications or fails to adhere to international safety standards. This inconsistency can lead to project delays, increased costs for rework, and potential safety hazards in the workplace. Buyers from regions like Africa and South America, where local regulations may differ significantly from those in China, often find themselves at a disadvantage, lacking the proper resources to verify the quality of the equipment before purchase.
The Solution: To mitigate quality concerns, international buyers should prioritize thorough supplier vetting processes. Engage in due diligence by requesting samples and conducting factory audits when feasible. Utilize third-party inspection services to evaluate product quality before shipment. Furthermore, buyers should familiarize themselves with international standards, such as ISO certifications relevant to welding equipment, and ensure that their suppliers comply. Establishing clear communication channels with suppliers, including detailed specifications and expectations, can also significantly enhance the quality assurance process. By investing time in these practices, buyers can reduce the risk of acquiring subpar equipment and ensure that their projects proceed smoothly.
Scenario 2: Overcoming Language and Cultural Barriers in Procurement
The Problem: Language and cultural differences pose significant hurdles for B2B buyers when dealing with Chinese manufacturers. Miscommunications can lead to errors in orders, incorrect specifications, and unmet expectations, which can be particularly frustrating for buyers from Europe or the Middle East who may have specific compliance requirements. Additionally, cultural nuances in negotiation styles can impact the buying process, leaving international buyers feeling sidelined or misunderstood.
The Solution: To bridge these gaps, buyers should consider hiring local intermediaries or agents who understand both the Chinese market and the buyer’s home region. These professionals can facilitate clearer communication and help navigate cultural differences effectively. Additionally, employing translation services can ensure that all specifications, contracts, and agreements are accurately conveyed and understood. It is also beneficial for buyers to invest time in learning about Chinese business etiquette and negotiation tactics, which can foster better relationships and create a more favorable negotiating environment. By taking these steps, buyers can enhance their procurement processes and build stronger partnerships with Chinese suppliers.
Scenario 3: Managing Logistics and Supply Chain Challenges
The Problem: Logistics and supply chain management present formidable challenges for B2B buyers sourcing welding equipment from China. Buyers often encounter issues such as unexpected shipping delays, high freight costs, and complications with customs clearance. These challenges can lead to significant project delays and increased operational costs, particularly for businesses in Africa and South America, where logistics infrastructure may be less developed.
The Solution: To effectively manage these logistics challenges, buyers should establish strong partnerships with reputable freight forwarders who have experience navigating the complexities of international shipping and customs. It is advisable to conduct thorough research to identify freight forwarders that specialize in the regions where the equipment will be delivered. Additionally, buyers should plan for potential delays by incorporating buffer times into project schedules. Using digital tools and platforms for tracking shipments can also provide real-time updates, enabling buyers to proactively address any issues that arise during transit. By adopting these strategies, buyers can streamline their logistics processes and minimize disruptions to their operations.
Strategic Material Selection Guide for welding equipment china
When selecting materials for welding equipment sourced from China, international B2B buyers must consider several factors, including performance properties, cost, and compliance with regional standards. Below, we analyze four common materials used in welding equipment, focusing on their characteristics, advantages, disadvantages, and implications for buyers from Africa, South America, the Middle East, and Europe.
What Are the Key Properties of Steel in Welding Equipment?
Steel is one of the most widely used materials in welding equipment due to its excellent mechanical properties. It typically exhibits high tensile strength, good ductility, and resistance to deformation under load. Steel can withstand high temperatures and pressures, making it suitable for various welding applications.
Pros & Cons:
– Advantages: Steel is durable, widely available, and relatively cost-effective. It can be easily fabricated and welded, allowing for versatile designs in equipment.
– Disadvantages: Steel is prone to corrosion if not properly treated, which can limit its lifespan in harsh environments. It may also require additional coatings or treatments to enhance its corrosion resistance.
Impact on Application:
Steel is compatible with a wide range of welding processes, including MIG, TIG, and stick welding, making it a preferred choice for diverse applications.
Considerations for International Buyers:
Buyers should ensure that the steel meets relevant standards such as ASTM A36 or DIN 17100, especially for projects in regions with strict compliance requirements, like Europe.
How Does Aluminum Compare as a Material for Welding Equipment?
Aluminum is another popular choice for welding equipment due to its lightweight and excellent corrosion resistance. It has a lower density than steel, which can reduce the overall weight of the equipment, making it easier to handle and transport.
Pros & Cons:
– Advantages: Aluminum is resistant to corrosion and does not rust, which is advantageous for equipment used in humid or marine environments. It also has good thermal conductivity.
– Disadvantages: Aluminum can be more expensive than steel and may require specialized welding techniques due to its lower melting point and thermal conductivity.
Impact on Application:
Aluminum is particularly suitable for applications where weight savings are critical, such as in aerospace or automotive industries.
Considerations for International Buyers:
Buyers should verify that aluminum components comply with standards like ASTM B221 or JIS H4000, particularly in regions where material specifications are stringent.
What Role Does Stainless Steel Play in Welding Equipment?
Stainless steel is renowned for its corrosion resistance and is often used in environments where exposure to chemicals or moisture is a concern. It maintains structural integrity at high temperatures, making it ideal for high-performance applications.
Pros & Cons:
– Advantages: Stainless steel offers exceptional durability and resistance to corrosion, which extends the lifespan of welding equipment. It is also aesthetically pleasing, which can be important for consumer-facing products.
– Disadvantages: The cost of stainless steel is generally higher than that of carbon steel or aluminum, and it can be more challenging to weld due to its thermal properties.
Impact on Application:
Stainless steel is commonly used in food processing, pharmaceuticals, and marine applications where hygiene and corrosion resistance are paramount.
Considerations for International Buyers:
Ensure compliance with standards such as ASTM A312 or EN 10088, especially for buyers in Europe and regions with strict health and safety regulations.
Why is Copper Used in Certain Welding Equipment?
Copper is often used in welding equipment for its excellent electrical conductivity and thermal properties. It is frequently found in components such as welding electrodes and cables.
Pros & Cons:
– Advantages: Copper’s high conductivity allows for efficient energy transfer, which is crucial in welding processes. It also has good corrosion resistance.
– Disadvantages: Copper is more expensive than steel and aluminum, and its mechanical strength is lower, making it less suitable for structural applications.
Impact on Application:
Copper is particularly beneficial in electrical applications, such as in TIG welding, where efficient heat transfer is essential.
Considerations for International Buyers:
Buyers should look for compliance with standards such as ASTM B170 or JIS H3100, particularly in regions where electrical safety is a priority.
Summary Table of Material Properties for Welding Equipment
Material | Typical Use Case for welding equipment china | Key Advantage | Key Disadvantage/Limitation | Relative Cost (Low/Med/High) |
---|---|---|---|---|
Steel | General welding equipment | High strength and durability | Prone to corrosion | Medium |
Aluminum | Lightweight applications | Excellent corrosion resistance | Higher cost and specialized welding needed | High |
Stainless Steel | Food processing, pharmaceuticals | Exceptional corrosion resistance | Higher cost and welding complexity | High |
Copper | Electrical components in welding | Excellent electrical conductivity | Expensive and lower mechanical strength | High |
This analysis provides a comprehensive overview of the materials commonly used in welding equipment sourced from China, helping international B2B buyers make informed decisions based on their specific needs and regional compliance requirements.
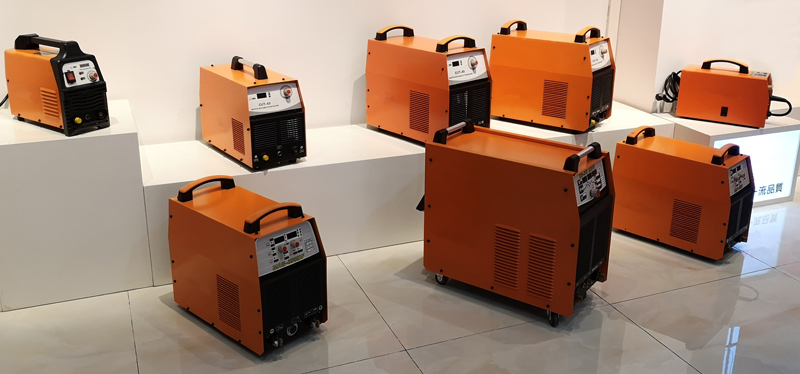
A stock image related to welding equipment china.
In-depth Look: Manufacturing Processes and Quality Assurance for welding equipment china
What Are the Main Stages in the Manufacturing Process of Welding Equipment in China?
The manufacturing of welding equipment in China involves several critical stages that ensure both efficiency and quality.
-
Material Preparation: This initial stage involves sourcing high-quality raw materials, including steel and aluminum alloys, which are essential for the durability of welding equipment. Suppliers often use advanced technologies like laser cutting and water jet cutting to prepare materials with precision. B2B buyers should ensure that suppliers maintain proper certifications for their materials, which can affect the overall quality of the finished products.
-
Forming: During this stage, the prepared materials undergo various forming processes such as stamping, bending, and welding. Techniques such as CNC machining are commonly utilized to achieve high accuracy in the dimensions of the components. Understanding the forming techniques used by suppliers can help buyers gauge the potential quality of the final products.
-
Assembly: The assembly process involves integrating the various components produced in the previous stages. This may include the installation of electrical systems, controls, and safety features. Skilled labor is essential at this stage, and many manufacturers employ automated assembly lines to increase efficiency. B2B buyers should inquire about the assembly methods used, as these can impact the reliability and performance of the welding equipment.
-
Finishing: Finally, the finishing stage includes surface treatments such as painting, powder coating, or galvanizing, which protect the equipment from corrosion and wear. Quality control checks are critical at this stage to ensure that the finishing meets both aesthetic and functional standards. Buyers should request information on the finishing processes and any certifications related to environmental safety and durability.
How is Quality Assurance Implemented in the Manufacturing of Welding Equipment?
Quality assurance (QA) is paramount in the manufacturing of welding equipment, especially when catering to international markets.
-
International Standards: Many Chinese manufacturers comply with international standards such as ISO 9001, which outlines quality management systems. Additionally, industry-specific certifications such as CE (Conformité Européenne) for the European market and API (American Petroleum Institute) for the oil and gas sector are crucial. Buyers should verify that suppliers possess the necessary certifications relevant to their specific market.
-
Quality Control Checkpoints: Quality control in welding equipment manufacturing typically includes three primary checkpoints:
– Incoming Quality Control (IQC): This initial check involves inspecting raw materials to ensure they meet specified standards before production begins.
– In-Process Quality Control (IPQC): During manufacturing, various checks are performed to monitor the quality of processes and components. This includes evaluating tolerances and dimensions at different stages.
– Final Quality Control (FQC): After assembly, the finished products undergo thorough testing and inspection to verify that they meet all quality standards and specifications. -
Common Testing Methods: Manufacturers often employ a variety of testing methods, including:
– Non-destructive testing (NDT): Techniques such as ultrasonic testing and X-ray inspection ensure that welds and materials are free of defects without damaging the equipment.
– Functional Testing: This involves operating the equipment under conditions that simulate actual use to ensure performance standards are met.
How Can B2B Buyers Verify the Quality Control Processes of Suppliers?
For international B2B buyers, verifying the quality control processes of suppliers in China is crucial to ensure they receive reliable and compliant products.
-
Supplier Audits: Conducting supplier audits is an effective way to assess a manufacturer’s quality control processes. This can be done through on-site visits or by hiring third-party inspection services. Auditors will evaluate the manufacturing processes, quality management systems, and compliance with international standards.
-
Requesting Quality Reports: Buyers should ask suppliers for detailed quality reports that document their quality control measures. These reports often include information on inspection results, testing methodologies, and compliance with certifications.
-
Third-Party Inspections: Engaging third-party inspection agencies can provide an unbiased assessment of the manufacturing processes and quality controls in place. These organizations can conduct pre-shipment inspections to ensure that products meet the agreed-upon specifications before they leave the factory.
What Are the QC and Certification Nuances for International B2B Buyers?
International B2B buyers, particularly those from regions such as Africa, South America, the Middle East, and Europe, should be aware of specific nuances regarding quality control and certifications when sourcing welding equipment from China.
-
Understanding Local Regulations: Different countries have unique regulations regarding the import of welding equipment. For instance, European countries require CE marking for compliance with EU safety standards. Buyers should familiarize themselves with these regulations to avoid costly penalties or product rejections upon arrival.
-
Cultural and Communication Factors: Cultural differences can affect the communication of quality expectations. Buyers should establish clear specifications and maintain open lines of communication with suppliers to ensure that quality standards are understood and met.
-
Market-Specific Certifications: In addition to general international standards, certain markets may require specific certifications. For example, equipment intended for the oil and gas industry may need API certifications. Buyers should clarify these requirements with suppliers to ensure compliance and facilitate smoother import processes.
Conclusion
Understanding the manufacturing processes and quality assurance measures in the production of welding equipment in China is crucial for international B2B buyers. By focusing on the main stages of manufacturing, the importance of quality control, and how to verify supplier practices, buyers can make informed decisions that align with their operational needs and compliance requirements. Engaging with suppliers who demonstrate adherence to international standards and effective quality management practices will ultimately lead to better product reliability and performance.
Practical Sourcing Guide: A Step-by-Step Checklist for ‘welding equipment china’
In the ever-evolving landscape of industrial procurement, sourcing welding equipment from China presents both opportunities and challenges for international B2B buyers. This step-by-step checklist is designed to provide actionable insights, ensuring that your procurement process is efficient, cost-effective, and tailored to your specific needs.
Step 1: Define Your Technical Specifications
Understanding your specific welding requirements is crucial for sourcing the right equipment. Consider the types of materials you’ll be welding, the thickness of the materials, and the welding processes you intend to use (e.g., MIG, TIG, Stick). Clearly defined specifications will streamline your search and help suppliers provide accurate quotes.
Step 2: Conduct Market Research
Before reaching out to suppliers, perform thorough market research to identify potential vendors in China. Utilize online platforms such as Alibaba, Made-in-China, and Global Sources to gather a list of manufacturers. Pay attention to reviews and ratings, as well as the types of welding equipment they specialize in, to narrow down your options.
Step 3: Evaluate Potential Suppliers
Before committing to a supplier, it’s essential to vet them thoroughly. Request company profiles, case studies, and references from buyers in similar industries or regions. Look for suppliers with a proven track record of reliability and quality, as this will reduce risks associated with procurement.
- Check for Certifications: Ensure that the supplier holds relevant certifications, such as ISO 9001 or CE, which indicate adherence to international quality standards.
- Request Samples: If possible, ask for samples or demonstration units to assess the quality of the welding equipment firsthand.
Step 4: Verify Supplier Certifications
Certification verification is a critical step in ensuring product quality and compliance with international standards. Check if the supplier has the necessary certifications relevant to your market, such as safety and environmental compliance certifications.
- Understand Compliance Requirements: Each region may have different regulatory standards, so familiarize yourself with the requirements in your region (e.g., CE marking in Europe, ANSI standards in the U.S.).
Step 5: Negotiate Terms and Conditions
Once you’ve selected potential suppliers, engage in negotiations to establish favorable terms. Discuss pricing, payment methods, lead times, and shipping options.
- Consider Total Cost of Ownership: Look beyond the initial purchase price; factor in shipping, customs duties, and potential maintenance costs to get a true picture of the financial commitment.
- Set Clear Payment Terms: Clarify payment schedules and conditions to avoid misunderstandings later on.
Step 6: Establish Quality Control Procedures
Quality control is paramount when sourcing welding equipment. Develop a quality assurance plan that outlines inspection criteria and testing methods for the equipment upon arrival.
- Plan for On-Site Inspections: If feasible, consider arranging for inspections at the supplier’s facility before shipping, or use third-party inspection services to ensure compliance with your specifications.
Step 7: Plan for After-Sales Support
Finally, ensure that your supplier offers robust after-sales support, including warranty terms, maintenance services, and technical assistance.
- Ask About Training Options: Inquire whether the supplier provides training for your staff on using and maintaining the equipment, which can enhance productivity and safety.
By following this structured checklist, international B2B buyers can navigate the complexities of sourcing welding equipment from China, ensuring they make informed decisions that align with their operational needs and business goals.
Comprehensive Cost and Pricing Analysis for welding equipment china Sourcing
What Are the Key Cost Components in Sourcing Welding Equipment from China?
When sourcing welding equipment from China, understanding the cost structure is crucial for international B2B buyers. The primary cost components include:
-
Materials: The cost of raw materials can vary significantly based on quality and availability. For instance, high-grade steel or specialized alloys used in welding equipment will increase costs. Buyers should consider bulk purchasing to lower material costs.
-
Labor: Labor costs in China are generally lower than in Europe or the Americas, but they can vary by region and skill level. For specialized welding equipment, skilled labor may be necessary, which could raise production costs.
-
Manufacturing Overhead: This includes utilities, equipment maintenance, and factory rent. Overhead costs can fluctuate based on the manufacturing facility’s location and operational efficiency.
-
Tooling: Initial tooling costs can be substantial, especially for custom equipment. It’s essential to factor these into the overall cost, as they can influence the final pricing.
-
Quality Control (QC): Implementing stringent quality control measures adds to the cost. However, investing in quality assurance can minimize returns and defects, providing long-term savings.
-
Logistics: Shipping costs from China to your location can vary widely based on distance, shipping method, and current freight rates. With rising shipping costs globally, it’s essential to incorporate this into your budget.
-
Margin: Supplier profit margins can vary based on the supplier’s position in the market and the competitiveness of the pricing. Understanding market rates can help in negotiations.
How Do Price Influencers Impact the Cost of Welding Equipment?
Several factors can influence the price of welding equipment when sourcing from China:
-
Volume and Minimum Order Quantity (MOQ): Larger orders often lead to lower per-unit costs. Suppliers may have MOQs that can affect pricing, so it’s beneficial to negotiate these terms.
-
Specifications and Customization: Custom specifications can lead to higher costs. If standard equipment suffices, opting for non-customized solutions can reduce expenses.
-
Materials and Quality Certifications: Higher-quality materials and necessary certifications (like ISO or CE) can increase costs. Assess the necessity of these certifications based on your market requirements.
-
Supplier Factors: Established suppliers with a solid reputation may charge more due to their reliability and service quality. It’s essential to evaluate whether the additional cost is justified by the value provided.
-
Incoterms: Understanding Incoterms (International Commercial Terms) is vital as they dictate the responsibilities of buyers and sellers in shipping and logistics. Terms like FOB (Free on Board) or CIF (Cost, Insurance, and Freight) can significantly affect the total landed cost.
What Are Some Effective Buyer Tips for Cost-Efficiency?
To optimize costs when sourcing welding equipment from China, international buyers should consider the following strategies:
-
Negotiate Wisely: Always negotiate terms with suppliers. Building a relationship can lead to better pricing and terms in future transactions.
-
Evaluate Total Cost of Ownership (TCO): Look beyond the initial purchase price. Consider maintenance, operational costs, and potential downtime when assessing equipment.
-
Understand Pricing Nuances: Be aware of seasonal fluctuations in pricing, particularly during peak manufacturing times or holidays in China. Planning purchases around these periods can yield better prices.
-
Conduct Thorough Research: Research different suppliers and compare their offerings. Utilize platforms like Alibaba or Global Sources to find competitive prices and reviews from other buyers.
-
Local Partnerships: Consider partnering with local firms in China to facilitate the sourcing process. They can provide insights into the market and assist with negotiations and logistics.
Disclaimer on Indicative Prices
Prices for welding equipment can fluctuate based on market conditions, currency exchange rates, and supplier pricing strategies. Therefore, the figures discussed should be viewed as indicative rather than fixed. Always request updated quotes from suppliers to ensure accurate budgeting.
Alternatives Analysis: Comparing welding equipment china With Other Solutions
When considering welding solutions, international B2B buyers face a multitude of options that can significantly impact their operational efficiency and costs. While ‘welding equipment from China’ offers unique advantages, exploring alternatives is crucial for making informed purchasing decisions. This section evaluates various welding technologies and methodologies, comparing them against Chinese welding equipment to help buyers identify the best fit for their specific needs.
Comparison Aspect | Welding Equipment China | MIG Welding Machines | TIG Welding Systems |
---|---|---|---|
Performance | High, suitable for mass production | Excellent for versatile applications | Superior for precision work |
Cost | Generally lower initial investment | Moderate cost, higher consumables | Higher initial investment but lower long-term costs |
Ease of Implementation | Easy to set up and use | Requires some training | Requires specialized training |
Maintenance | Low maintenance needs | Moderate maintenance required | High maintenance demands |
Best Use Case | High-volume production | General fabrication, automotive | Aerospace, intricate designs |
What are the Advantages and Disadvantages of MIG Welding Machines?
MIG (Metal Inert Gas) welding machines are an excellent alternative to welding equipment from China, especially for businesses looking for versatility. They provide a good balance between performance and cost, making them suitable for various applications, including automotive and general fabrication. However, while the initial investment is moderate, the consumables can add up over time, impacting long-term costs. Additionally, some training is required to operate MIG machines effectively, which could be a consideration for businesses with limited technical expertise.
How do TIG Welding Systems Compare to Welding Equipment from China?
TIG (Tungsten Inert Gas) welding systems are recognized for their precision and are ideal for applications requiring high-quality welds, such as aerospace and intricate designs. Although the initial investment is higher than that of Chinese welding equipment, TIG systems often result in lower long-term costs due to their efficient use of materials and energy. However, they require specialized training to operate effectively, and maintenance can be demanding, which might not be suitable for all businesses, especially those with limited resources.
Conclusion: How Can B2B Buyers Choose the Right Welding Solution?
In selecting the right welding solution, B2B buyers must consider various factors such as performance requirements, budget constraints, and the level of expertise available within their teams. While welding equipment from China may offer a cost-effective and efficient option for mass production, alternatives like MIG and TIG welding systems provide unique advantages that can cater to specific needs. By evaluating the comparative aspects outlined in this analysis, buyers can make informed decisions that align with their operational goals and long-term strategies.
Essential Technical Properties and Trade Terminology for welding equipment china
What Are the Essential Technical Properties of Welding Equipment from China?
When considering welding equipment from China, understanding key technical properties is crucial for making informed purchasing decisions. Here are some essential specifications that B2B buyers should prioritize:
-
Material Grade
– Definition: Material grade indicates the quality and composition of the materials used in welding equipment, such as steel or aluminum alloys.
– Importance: Higher-grade materials offer better durability, corrosion resistance, and overall performance. This is vital for industries that operate in harsh environments, ensuring the longevity of the equipment and minimizing downtime. -
Welding Current Range
– Definition: This specification refers to the range of electric current that the welding machine can use, typically measured in amperes (A).
– Importance: A wider current range allows for versatility in welding different materials and thicknesses. For B2B buyers, this means they can utilize one machine for multiple applications, reducing the need for additional equipment. -
Duty Cycle
– Definition: The duty cycle measures the percentage of time a welding machine can operate continuously within a set period, usually expressed over 10 minutes.
– Importance: Understanding the duty cycle is crucial for ensuring that the equipment can handle the workload without overheating. A higher duty cycle translates to increased efficiency and productivity in manufacturing processes. -
Voltage Input
– Definition: This refers to the voltage requirement for the welding equipment to operate effectively.
– Importance: Knowing the voltage input is essential for compatibility with local power supply systems. Incorrect voltage can lead to equipment failure or safety hazards, making this a critical consideration for international buyers. -
Weight and Portability
– Definition: The weight of the welding equipment and its design for ease of transportation.
– Importance: Lighter, portable machines are often preferred for on-site jobs or projects requiring mobility. Buyers should consider how the weight will affect shipping and handling costs, especially when importing from overseas. -
Control Features
– Definition: This includes features such as digital displays, automatic settings, and user interface options.
– Importance: Advanced control features enhance precision and ease of use, which can lead to better-quality welds and reduced training time for operators. For B2B buyers, investing in equipment with superior control can improve operational efficiency.
What Are Common Trade Terminologies in the Welding Equipment Industry?
Understanding industry jargon is vital for effective communication and negotiations in the B2B landscape. Here are some common terms you should know:
-
OEM (Original Equipment Manufacturer)
– Definition: A company that produces parts and equipment that may be marketed by another manufacturer.
– Relevance: Knowing if a supplier is an OEM can assure buyers of the quality and authenticity of the equipment, as OEM products typically adhere to strict manufacturing standards. -
MOQ (Minimum Order Quantity)
– Definition: The smallest quantity of a product that a supplier is willing to sell.
– Relevance: Understanding MOQ is essential for budgeting and inventory management. Buyers should negotiate MOQ to align with their operational needs, especially when entering new markets. -
RFQ (Request for Quotation)
– Definition: A document sent to suppliers requesting pricing and terms for specific products or services.
– Relevance: An RFQ allows buyers to compare offers from different suppliers, enabling better decision-making based on price and terms. -
Incoterms (International Commercial Terms)
– Definition: A set of internationally recognized rules that define the responsibilities of sellers and buyers in international transactions.
– Relevance: Familiarity with Incoterms helps buyers understand shipping costs, risk management, and insurance responsibilities, which are critical for international transactions. -
Lead Time
– Definition: The time taken from placing an order to delivery.
– Relevance: Knowing the lead time is crucial for project planning and inventory management. Buyers should communicate expectations clearly to avoid delays that could impact production schedules. -
Certification Standards
– Definition: Refers to compliance with industry standards such as ISO or CE, which ensure the quality and safety of equipment.
– Relevance: Equipment certified to international standards is often more reliable and accepted in various markets. Buyers should prioritize suppliers that can provide certification documentation.
By understanding these essential technical properties and trade terminologies, international B2B buyers can navigate the complexities of sourcing welding equipment from China with greater confidence and efficiency.
Navigating Market Dynamics and Sourcing Trends in the welding equipment china Sector
What Are the Current Market Dynamics and Key Trends in the Welding Equipment Sector in China?
The welding equipment market in China is experiencing rapid evolution, driven by global demand for advanced manufacturing solutions and a growing emphasis on automation. Key trends impacting international B2B buyers include the rise of Industry 4.0 technologies, which incorporate IoT, AI, and robotics into welding processes. This shift is leading to more efficient production lines and enhanced quality control, making it crucial for buyers from Africa, South America, the Middle East, and Europe to consider suppliers that invest in these technologies.
Another significant trend is the increasing demand for portable and lightweight welding equipment, catering to the needs of diverse industries, including construction, automotive, and shipbuilding. As businesses seek to optimize their operations, they are prioritizing equipment that enhances mobility without compromising performance. Additionally, the push for greater customization in welding solutions is gaining traction, as manufacturers aim to meet the specific needs of various sectors.
Furthermore, international buyers should be aware of the competitive landscape in the Chinese welding equipment market. With a myriad of manufacturers vying for attention, understanding the reputation and reliability of suppliers is essential. Conducting thorough due diligence, including reviewing certifications and customer feedback, can help mitigate risks associated with sourcing from this region.
How Does Sustainability and Ethical Sourcing Impact the Welding Equipment Sector in China?
Sustainability is becoming a vital consideration for B2B buyers in the welding equipment sector. The environmental impact of manufacturing processes, including energy consumption and waste generation, is under scrutiny. Buyers are increasingly looking for suppliers that adhere to sustainable practices, such as using energy-efficient machinery and minimizing harmful emissions.
Moreover, ethical sourcing is gaining importance as consumers and businesses alike demand transparency in supply chains. This shift necessitates that international buyers from regions like Africa, South America, the Middle East, and Europe prioritize suppliers who demonstrate commitment to fair labor practices and environmentally responsible materials. Certifications such as ISO 14001 (Environmental Management) and ISO 45001 (Occupational Health and Safety) are indicators of a supplier’s dedication to sustainability and ethical standards.
As a response to these demands, many Chinese manufacturers are adopting ‘green’ certifications and utilizing recyclable materials in their welding equipment production. This not only reduces environmental footprints but also aligns with the growing trend of corporate social responsibility in global supply chains. Buyers are encouraged to engage with suppliers who are proactive in sustainability efforts, as this can enhance brand reputation and customer loyalty.
What Is the Evolution of the Welding Equipment Market in China?
The welding equipment market in China has undergone significant transformation over the past few decades. Initially dominated by traditional welding methods, the industry has rapidly adopted modern technologies and practices, becoming one of the largest producers of welding equipment globally. This evolution can be attributed to several factors, including increased industrialization, a burgeoning manufacturing sector, and the integration of advanced technologies.
In the early 2000s, China began to embrace automation, leading to the development of sophisticated welding machines that improved efficiency and precision. As the global market expanded, Chinese manufacturers started focusing on quality and innovation, competing with established brands from Europe and North America. Today, China not only supplies a significant portion of the world’s welding equipment but also exports advanced solutions tailored to the needs of various industries. This historical context is essential for international buyers to understand the capabilities and competitive advantages of sourcing from Chinese suppliers.
Frequently Asked Questions (FAQs) for B2B Buyers of welding equipment china
-
How do I find reliable suppliers for welding equipment in China?
To find reliable suppliers of welding equipment in China, start by utilizing platforms such as Alibaba, Made-in-China, and Global Sources. Look for suppliers with verified status, positive reviews, and a significant number of transactions. Engaging in trade shows, such as the China International Welding Exhibition, can also provide direct access to manufacturers. Always request references and conduct background checks to ensure credibility. Additionally, consider visiting factories to assess their production capabilities and quality control measures firsthand. -
What are the common payment terms when purchasing welding equipment from China?
Payment terms can vary significantly among Chinese suppliers, but common practices include a 30% deposit upfront and the balance before shipment. Letter of Credit (L/C) is also widely used, particularly for larger transactions, providing security for both parties. It’s advisable to negotiate terms that suit your cash flow while ensuring protection against fraud. Always clarify payment methods accepted, including bank transfers, PayPal, or trade assurance services offered by platforms like Alibaba. -
What should I consider regarding the minimum order quantity (MOQ) for welding equipment?
Minimum Order Quantity (MOQ) is a critical factor when sourcing welding equipment. MOQs can range from a few units to several hundred, depending on the supplier and the type of equipment. Assess your project requirements and budget before negotiating MOQs, as some suppliers may be flexible, especially for repeat customers. If you’re a small business or startup, consider consolidating orders with other buyers to meet MOQs or look for suppliers willing to accommodate smaller orders. -
How can I ensure quality assurance when sourcing welding equipment from China?
To ensure quality assurance, request certifications like ISO 9001, CE, or other relevant quality standards from suppliers. Implement a rigorous inspection process, which may include third-party quality control services to inspect goods before shipment. Establish a clear agreement on quality expectations, including material specifications and testing protocols. Additionally, consider ordering samples before committing to larger purchases to evaluate the equipment’s performance and durability. -
What are the logistics considerations when importing welding equipment from China?
When importing welding equipment from China, consider logistics aspects such as shipping methods, customs clearance, and delivery timelines. Decide between air freight for faster delivery or sea freight for cost-effectiveness. Ensure your supplier provides complete shipping documents, including the bill of lading and commercial invoice. It’s also essential to understand local customs regulations and duties in your country to avoid unexpected fees. Partnering with a reliable freight forwarder can help streamline the logistics process. -
Can I customize welding equipment to meet specific needs?
Yes, many Chinese manufacturers offer customization options for welding equipment, including modifications in size, capacity, and features. When discussing customization, provide detailed specifications and requirements to ensure the supplier understands your needs. Be aware that custom orders may have higher MOQs and longer lead times. Always confirm that the supplier has experience with custom projects and request prototypes if necessary to validate the final product.
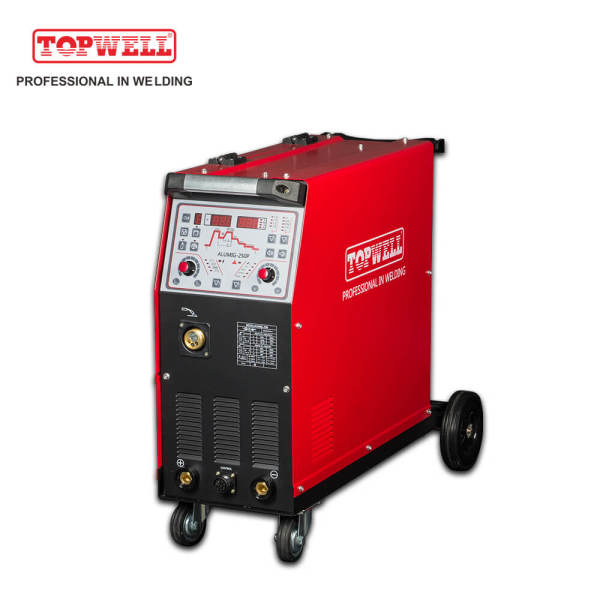
A stock image related to welding equipment china.
-
What types of welding equipment are commonly sourced from China?
Commonly sourced welding equipment from China includes MIG welders, TIG welders, stick welders, plasma cutting machines, and welding accessories like helmets and protective gear. The variety allows buyers to select equipment suitable for their specific applications, from industrial manufacturing to DIY projects. It’s crucial to evaluate the supplier’s specialization in the type of equipment you need, as this can affect the quality and reliability of the products. -
How do I handle disputes with Chinese suppliers effectively?
Handling disputes with Chinese suppliers requires clear communication and documentation of all agreements and transactions. If issues arise, attempt to resolve them amicably through direct negotiation. Utilize platforms like Alibaba, which offer dispute resolution services, if the supplier is uncooperative. Always maintain a professional demeanor and document all correspondence. In severe cases, consider legal action or mediation, but this should be a last resort due to the complexities of international trade laws.
Important Disclaimer & Terms of Use
⚠️ Important Disclaimer
The information provided in this guide, including content regarding manufacturers, technical specifications, and market analysis, is for informational and educational purposes only. It does not constitute professional procurement advice, financial advice, or legal advice.
While we have made every effort to ensure the accuracy and timeliness of the information, we are not responsible for any errors, omissions, or outdated information. Market conditions, company details, and technical standards are subject to change.
B2B buyers must conduct their own independent and thorough due diligence before making any purchasing decisions. This includes contacting suppliers directly, verifying certifications, requesting samples, and seeking professional consultation. The risk of relying on any information in this guide is borne solely by the reader.
Strategic Sourcing Conclusion and Outlook for welding equipment china
What Are the Key Takeaways for B2B Buyers Sourcing Welding Equipment from China?
In conclusion, international B2B buyers from regions such as Africa, South America, the Middle East, and Europe must recognize the critical importance of strategic sourcing when procuring welding equipment from China. By understanding the unique market dynamics, leveraging supplier relationships, and focusing on quality assurance, businesses can enhance their operational efficiencies and reduce costs.
How Can Strategic Sourcing Drive Competitive Advantage?
Strategic sourcing not only facilitates access to a diverse range of high-quality welding equipment but also fosters innovation and sustainability in procurement practices. Buyers should prioritize suppliers who demonstrate compliance with international standards and are responsive to market changes. This proactive approach will empower companies to adapt swiftly in an increasingly competitive landscape.
What Should Buyers Do Next?
Looking ahead, it is essential for B2B buyers to engage in thorough market research and establish clear communication channels with Chinese suppliers. By doing so, they can navigate challenges effectively and capitalize on emerging opportunities. Now is the time to take action—invest in strategic partnerships that align with your business goals and watch your welding operations thrive in a global marketplace.