Boost Efficiency: Your Guide to Power Tools Supplier (2025)
Introduction: Navigating the Global Market for power tools supplier
Navigating the global market for power tools suppliers can be a daunting task for international B2B buyers, particularly when faced with an overwhelming array of options and varying standards across regions. Whether you are sourcing high-performance drills for construction projects in South America or robust woodworking tools for manufacturers in Europe, understanding the nuances of supplier selection is crucial. This guide provides comprehensive insights into the diverse types of power tools available, their applications across various industries, and practical strategies for vetting suppliers effectively.
In this guide, we will explore key factors such as product specifications, quality certifications, and supplier reliability that impact purchasing decisions. We will also delve into cost considerations, helping buyers navigate pricing structures and understand the implications of shipping and tariffs in different regions, particularly in Africa and the Middle East.
With a focus on empowering international buyers from diverse markets—including Vietnam, Italy, and beyond—this resource is designed to enhance your sourcing strategies. By equipping you with actionable insights and best practices, we aim to facilitate informed purchasing decisions that align with your business needs and project requirements. As you embark on your journey in the global power tools marketplace, let this guide serve as your trusted companion in achieving operational excellence.
Understanding power tools supplier Types and Variations
Type Name | Key Distinguishing Features | Primary B2B Applications | Brief Pros & Cons for Buyers |
---|---|---|---|
Manufacturers | Produce tools directly; often offer custom solutions | Construction, manufacturing, automotive | Pros: High quality, tailored solutions. Cons: Higher costs, longer lead times. |
Distributors | Act as intermediaries; stock a variety of brands | Retail, construction, maintenance services | Pros: Wide selection, quick delivery. Cons: May lack specialized knowledge. |
Online Marketplaces | E-commerce platforms; connect buyers with multiple suppliers | Small businesses, startups, DIY projects | Pros: Competitive pricing, convenience. Cons: Quality assurance can be challenging. |
Wholesale Suppliers | Bulk purchasing options; often lower prices | Large-scale construction, industrial projects | Pros: Cost-effective for bulk orders. Cons: Minimum order quantities may apply. |
Specialty Suppliers | Focus on niche markets or specific tool types | Specialized industries, unique projects | Pros: Expert knowledge, tailored products. Cons: Limited range, potentially higher prices. |
What Are the Characteristics of Power Tool Manufacturers?
Manufacturers of power tools are the backbone of the industry, directly producing tools and often offering custom solutions tailored to specific business needs. They typically have advanced production capabilities and can provide high-quality products. When considering purchasing from manufacturers, B2B buyers should evaluate the manufacturer’s reputation, production capacity, and ability to meet custom specifications. While their products may come at a premium price, the assurance of quality and durability can justify the investment for businesses that require reliable tools.
How Do Distributors Serve B2B Buyers?
Distributors serve as intermediaries between manufacturers and end-users, stocking a wide variety of brands and products. They are particularly beneficial for businesses that require quick access to a diverse range of tools without committing to high minimum orders. When selecting a distributor, buyers should consider factors such as inventory levels, delivery times, and customer service quality. While distributors may not provide the same level of specialized knowledge as manufacturers, their wide selection and quick turnaround can be crucial for maintaining project schedules.
What Benefits Do Online Marketplaces Offer for Power Tools?
Online marketplaces have revolutionized the way B2B buyers procure power tools by providing a platform where multiple suppliers can be accessed in one place. This convenience allows businesses to compare prices and products easily, which can lead to significant cost savings. However, buyers should be cautious about quality assurance, as products may vary widely in terms of reliability. It is essential to read reviews and check supplier ratings to ensure a satisfactory purchasing experience.
Why Choose Wholesale Suppliers for Bulk Orders?
Wholesale suppliers are ideal for businesses looking to purchase power tools in bulk at reduced prices. They cater to large-scale construction projects or industrial needs where cost-effectiveness is critical. However, buyers should be mindful of minimum order quantities that may be required, which could affect cash flow. When engaging with wholesale suppliers, it’s important to assess their delivery capabilities and terms of service to ensure that they align with project timelines.
What Are the Advantages of Specialty Suppliers?
Specialty suppliers focus on niche markets or specific types of power tools, providing expert knowledge and tailored products that meet unique industry needs. They are particularly valuable for businesses in specialized sectors that require tools designed for specific applications. While specialty suppliers may have a limited range of products compared to broader distributors, their expertise can lead to better product recommendations and customer support. Buyers should weigh the benefits of specialized knowledge against the potential for higher prices when considering these suppliers.
Related Video: Understanding Switching Mode Power Supplies
Key Industrial Applications of power tools supplier
Industry/Sector | Specific Application of Power Tools Supplier | Value/Benefit for the Business | Key Sourcing Considerations for this Application |
---|---|---|---|
Construction | Concrete Drilling and Cutting | Enhanced efficiency and precision in construction tasks | Quality of tools, supplier reliability, local support |
Manufacturing | Assembly Line Operations | Increased productivity and reduced labor costs | Compatibility with existing machinery, maintenance support |
Automotive | Vehicle Maintenance and Repair | Improved turnaround time for repairs | Tool durability, availability of parts, training resources |
Electrical Services | Electrical Installation and Maintenance | Ensured safety and compliance with regulations | Certification standards, tool safety features, warranty terms |
Woodworking and Carpentry | Precision Cutting and Joinery | Higher quality finishes and reduced material waste | Tool versatility, precision, after-sales service |
What Are the Key Industrial Applications of Power Tools Suppliers in Construction?
In the construction industry, power tools are essential for concrete drilling and cutting. These tools enable contractors to perform tasks with high efficiency and precision, significantly reducing project timelines. International buyers must consider the quality of tools, supplier reliability, and the availability of local support to ensure that they can quickly resolve any issues that arise during projects.
How Do Power Tools Enhance Manufacturing Operations?
In manufacturing, power tools are integral to assembly line operations. They help streamline processes, increase productivity, and reduce labor costs. For B2B buyers in this sector, it is crucial to ensure that the tools are compatible with existing machinery and that suppliers offer robust maintenance support, which can help minimize downtime and maximize output.
What Role Do Power Tools Play in Automotive Maintenance?
The automotive sector heavily relies on power tools for vehicle maintenance and repair. These tools enable mechanics to complete repairs more quickly, improving turnaround times and customer satisfaction. Buyers should prioritize tool durability and the availability of replacement parts, as well as training resources to ensure their teams can use the tools effectively.
Why Are Power Tools Important for Electrical Services?
In electrical services, power tools are vital for installation and maintenance tasks. They help ensure safety and compliance with industry regulations, which is critical in this field. B2B buyers should focus on sourcing tools that meet certification standards and feature advanced safety features, as these factors significantly impact operational safety and efficiency.
How Do Power Tools Improve Woodworking and Carpentry?
In woodworking and carpentry, precision cutting and joinery are essential for achieving high-quality finishes and reducing material waste. Power tools designed for these tasks allow craftsmen to work more efficiently and accurately. Buyers should look for tools that offer versatility and precision, as well as robust after-sales service, to support ongoing project needs.
Related Video: Industrial Control Panel Basics
3 Common User Pain Points for ‘power tools supplier’ & Their Solutions
Scenario 1: Navigating Quality Assurance in Power Tools
The Problem:
B2B buyers often encounter significant challenges when it comes to ensuring the quality and reliability of power tools supplied by various vendors. This is particularly true for buyers in regions like Africa and South America, where local standards may vary. Buyers may face situations where tools do not meet the necessary safety or performance standards, leading to project delays and potential safety hazards. The stakes are high; subpar tools can result in increased costs due to rework, injuries, and damage to reputation.
The Solution:
To navigate this challenge, it is crucial for buyers to implement a robust supplier evaluation process. Start by conducting thorough research on potential suppliers, looking into their certifications, customer reviews, and history of compliance with international quality standards such as ISO 9001. Engaging in site visits can provide insight into their manufacturing processes and quality control measures. Additionally, consider requesting samples or prototypes before making bulk purchases. This allows you to assess the quality firsthand and ensure that the tools meet your specific requirements. Establishing long-term relationships with suppliers who demonstrate consistent quality can also provide peace of mind, ensuring that your projects run smoothly.
Scenario 2: Managing Supply Chain Disruptions
The Problem:
Buyers often face supply chain disruptions that can delay the delivery of essential power tools. This issue is particularly pronounced in regions such as the Middle East and Europe, where geopolitical factors and trade regulations can impact supply chains. Delays can lead to significant project holdups, increased costs, and strained relationships with clients.
The Solution:
To mitigate supply chain risks, buyers should diversify their supplier base. Instead of relying on a single supplier, consider establishing relationships with multiple vendors across different regions. This strategy not only provides alternatives in case of disruptions but also enables you to negotiate better terms and pricing. Implementing a just-in-time (JIT) inventory system can also help manage stock levels effectively, ensuring that you have the right amount of tools available without overstocking. Moreover, staying informed about global trade policies and market trends will allow you to anticipate potential disruptions and adapt your sourcing strategies accordingly.
Scenario 3: Understanding Tool Specifications and Compatibility
The Problem:
Another common pain point for B2B buyers is the complexity involved in understanding tool specifications and ensuring compatibility with existing equipment. Buyers often struggle with technical jargon and specifications that can lead to purchasing the wrong tools, ultimately resulting in wasted resources and time.
The Solution:
To overcome this challenge, buyers should prioritize clear communication with suppliers regarding their specific needs. When requesting quotes or proposals, provide detailed information about the projects, including the types of materials to be worked on and the required tool specifications. Utilize online resources, such as product datasheets and comparison charts, to better understand the tools’ capabilities and limitations. Additionally, consider leveraging the expertise of technical consultants or industry specialists who can provide insights into the best tools for your applications. Hosting training sessions for your team on tool specifications and usage can also enhance their understanding and ensure that everyone is aligned on the tools required for various tasks.
Strategic Material Selection Guide for power tools supplier
What Are the Key Materials Used in Power Tools and Their Properties?
When selecting materials for power tools, understanding the properties, advantages, and limitations of common materials is crucial for international B2B buyers. Here, we analyze four prevalent materials: Steel, Aluminum, Plastic, and Composite Materials. Each material has unique characteristics that affect performance, durability, and cost, which are essential considerations for buyers, especially in diverse markets such as Africa, South America, the Middle East, and Europe.
How Does Steel Impact Power Tool Performance?
Key Properties:
Steel is known for its high tensile strength and durability. It can withstand high temperatures and pressures, making it ideal for heavy-duty applications. Additionally, it can be treated for corrosion resistance, extending its lifespan in various environments.
Pros & Cons:
The primary advantage of steel is its durability, making it suitable for tools that undergo heavy use. However, it is relatively heavy, which can affect the tool’s ergonomics. The manufacturing complexity can also increase costs, particularly if advanced treatments for corrosion resistance are required.
Impact on Application:
Steel is compatible with a wide range of media, including oils and solvents, but may corrode if exposed to moisture without proper treatment. Buyers should ensure that the steel used meets local standards for strength and corrosion resistance.
Considerations for International Buyers:
Compliance with international standards such as ASTM (American Society for Testing and Materials) or DIN (Deutsches Institut für Normung) is crucial. Buyers in regions like Africa and South America should also consider local sourcing options to reduce costs and ensure compliance with regional regulations.
Why Choose Aluminum for Power Tools?
Key Properties:
Aluminum is lightweight and has excellent corrosion resistance, making it suitable for tools that require portability. Its thermal conductivity allows for efficient heat dissipation, which is beneficial in high-performance applications.
Pros & Cons:
The primary advantage of aluminum is its lightweight nature, which enhances user comfort during prolonged use. However, aluminum is not as strong as steel, which may limit its application in high-stress environments. Additionally, the cost of aluminum can be higher than that of steel.
Impact on Application:
Aluminum tools are ideal for applications where weight is a critical factor, such as in construction or automotive repair. However, they may not be suitable for high-impact tasks.
Considerations for International Buyers:
Buyers should be aware of the specific grades of aluminum used, as they can vary significantly in strength and corrosion resistance. Compliance with standards such as JIS (Japanese Industrial Standards) may also be relevant, especially for buyers in Asia.
What Role Does Plastic Play in Power Tool Design?
Key Properties:
Plastic materials are lightweight, resistant to corrosion, and can be molded into complex shapes, making them versatile for various applications. They also provide good electrical insulation.
Pros & Cons:
The main advantage of plastic is its low weight and cost-effectiveness. However, plastics may not withstand high temperatures or heavy loads, which limits their application in professional-grade tools.
Impact on Application:
Plastic components are often used in housings or handles, where strength is less critical. They are suitable for consumer-grade tools but may not be appropriate for industrial applications.
Considerations for International Buyers:
Buyers should evaluate the type of plastic used and its compliance with safety standards. In regions like Europe, adherence to RoHS (Restriction of Hazardous Substances) directives is essential.
How Do Composite Materials Enhance Power Tools?
Key Properties:
Composite materials combine different materials to achieve specific properties, such as enhanced strength-to-weight ratios and improved resistance to environmental factors.
Pros & Cons:
The primary advantage of composites is their ability to be tailored for specific applications, providing both strength and lightweight characteristics. However, they can be more expensive to manufacture and may require specialized knowledge for effective use.
Impact on Application:
Composites are suitable for high-performance applications where both weight and strength are critical, such as in aerospace or advanced manufacturing tools.
Considerations for International Buyers:
Understanding the specific composites used and their certifications is crucial. Buyers should also consider the supply chain for composite materials, as sourcing may be limited in some regions.
Summary Table of Material Selection for Power Tools
Material | Typical Use Case for power tools supplier | Key Advantage | Key Disadvantage/Limitation | Relative Cost (Low/Med/High) |
---|---|---|---|---|
Steel | Heavy-duty tools (drills, saws) | High durability and strength | Heavy and potentially costly | Medium |
Aluminum | Lightweight tools (portable drills) | Lightweight and corrosion-resistant | Lower strength than steel | Medium to High |
Plastic | Tool housings and handles | Low cost and lightweight | Limited temperature and load capacity | Low |
Composite | High-performance tools (aerospace tools) | Tailored properties for specific needs | Higher manufacturing complexity | High |
This strategic material selection guide provides B2B buyers with the insights necessary to make informed decisions when sourcing power tools, ensuring they choose materials that align with their operational needs and market standards.
In-depth Look: Manufacturing Processes and Quality Assurance for power tools supplier
What Are the Main Stages of Manufacturing Power Tools?
When sourcing power tools, understanding the manufacturing processes is crucial for B2B buyers to assess quality and reliability. The manufacturing of power tools generally encompasses several key stages:
-
Material Preparation: This initial phase involves selecting high-quality raw materials such as metals, plastics, and composites. Suppliers often use advanced techniques like laser cutting and CNC machining to ensure precise dimensions and material integrity. Buyers should inquire about the material sourcing and certifications to guarantee compliance with international standards.
-
Forming: In this stage, raw materials are shaped into parts through methods such as forging, stamping, and injection molding. For power tools, forming techniques must ensure durability and performance. Understanding the forming processes helps buyers evaluate the strength and longevity of the tools.
-
Assembly: The assembly stage involves the integration of various components, including motors, gears, and casing. Automated assembly lines are commonly employed to enhance efficiency and consistency. Buyers should look for suppliers that implement lean manufacturing principles to reduce waste and improve productivity.
-
Finishing: This final stage includes surface treatments such as painting, anodizing, or plating, which enhance aesthetics and protect against corrosion. The finishing process is vital for power tools used in harsh environments. B2B buyers should inquire about the types of finishes used and their respective durability ratings.
How Is Quality Assurance Implemented in Power Tool Manufacturing?
Quality assurance (QA) is a critical aspect of the manufacturing process for power tools, ensuring that products meet specified standards and customer expectations. Here are the key components of a robust QA system:
-
International Standards and Certifications: Suppliers should adhere to international standards such as ISO 9001, which focuses on quality management systems. Additionally, industry-specific certifications such as CE marking in Europe and API standards for certain tools are essential indicators of compliance. B2B buyers should request documentation of these certifications during supplier evaluations.
-
Quality Control Checkpoints: Effective QA involves multiple checkpoints throughout the manufacturing process:
– Incoming Quality Control (IQC): Inspecting raw materials upon arrival to ensure they meet specifications.
– In-Process Quality Control (IPQC): Monitoring production processes to identify and rectify issues in real-time.
– Final Quality Control (FQC): Conducting comprehensive testing of finished products before shipment to confirm they meet quality standards. -
Common Testing Methods: Power tools undergo various tests, including performance, safety, and durability assessments. Common methods include:
– Functional Testing: Ensures that tools operate as intended.
– Safety Testing: Verifies compliance with safety standards and regulations.
– Endurance Testing: Simulates prolonged use to assess durability.
How Can B2B Buyers Verify Supplier Quality Control?
For international B2B buyers, verifying the quality control processes of power tool suppliers is essential. Here are effective strategies:
-
Supplier Audits: Conducting on-site audits allows buyers to evaluate the manufacturing processes, quality control measures, and overall facility conditions. This firsthand observation can uncover potential risks and ensure compliance with quality standards.
-
Quality Reports: Requesting regular quality reports from suppliers can provide insights into defect rates, compliance with testing protocols, and overall performance metrics. These reports should be detailed and transparent to facilitate informed decision-making.
-
Third-Party Inspections: Engaging third-party inspection services can add an extra layer of assurance. These independent organizations can conduct audits and testing, providing unbiased evaluations of the supplier’s quality control processes.
What Are the Nuances of Quality Control for International B2B Buyers?
B2B buyers from regions like Africa, South America, the Middle East, and Europe should be aware of specific nuances in quality control when sourcing power tools:
-
Regional Compliance Requirements: Different regions have distinct regulations and standards. For instance, European buyers must ensure products meet CE marking requirements, while Middle Eastern markets may have specific certifications related to local safety standards. Understanding these differences is vital for compliance.
-
Cultural and Communication Factors: Effective communication is crucial in international transactions. Buyers should establish clear quality expectations and ensure that suppliers understand compliance requirements. Language barriers and cultural differences can impact quality assurance processes, so fostering good relationships is essential.
-
Logistics and Supply Chain Considerations: The logistics of transporting power tools can influence quality. International shipments may expose products to harsh conditions, so understanding how suppliers package and transport their products is crucial. Buyers should discuss logistics with suppliers to mitigate risks during transit.
Conclusion: Ensuring Quality in Power Tool Procurement
For international B2B buyers, a thorough understanding of manufacturing processes and quality assurance practices is critical when sourcing power tools. By focusing on the main stages of manufacturing, verifying quality control measures, and being aware of regional nuances, buyers can ensure they procure reliable, high-quality tools that meet their operational needs. Engaging with suppliers who prioritize quality and compliance will ultimately lead to better business outcomes and enhanced customer satisfaction.
Practical Sourcing Guide: A Step-by-Step Checklist for ‘power tools supplier’
In today’s competitive landscape, sourcing power tools from reliable suppliers is essential for international B2B buyers. This checklist provides actionable steps to help you navigate the procurement process effectively, ensuring you select the right partners for your business needs.
Step 1: Define Your Technical Specifications
Clearly outline the technical requirements for the power tools you need. This includes specifications such as power ratings, dimensions, and any specialized features. A well-defined specification helps suppliers understand your needs and enables you to compare products more effectively.
- Consider Industry Standards: Ensure your specifications align with local and international standards to avoid compliance issues.
- Think About Future Needs: Anticipate future requirements to ensure the tools will serve your business in the long run.
Step 2: Conduct Market Research for Suppliers
Research potential suppliers to identify those that specialize in the types of power tools you require. Utilize online directories, trade shows, and industry publications to gather information.
- Focus on Experience and Reputation: Look for suppliers with a proven track record in your industry and positive customer reviews.
- Evaluate Geographic Considerations: Consider suppliers from regions with strong manufacturing capabilities, such as Europe or South America, to ensure quality and reliability.
Step 3: Verify Supplier Certifications
Check if the suppliers have the necessary certifications that validate their compliance with industry standards. This is crucial for ensuring product quality and safety.
- Look for ISO Certifications: An ISO certification demonstrates adherence to quality management standards.
- Check for Compliance with Local Regulations: Ensure that the supplier meets the regulatory requirements specific to your region, especially if you are sourcing from international markets.
Step 4: Request Samples and Conduct Trials
Before making a bulk purchase, request samples or conduct trials of the power tools. This allows you to evaluate their performance and suitability for your specific applications.
- Assess Quality and Durability: Use the samples in real-world scenarios to determine their effectiveness and longevity.
- Engage Your Team: Involve end-users in the evaluation process to gather insights on usability and performance.
Step 5: Negotiate Terms and Conditions
Once you have selected a potential supplier, negotiate favorable terms and conditions. This includes pricing, payment terms, delivery schedules, and warranties.
- Consider Total Cost of Ownership (TCO): Evaluate not just the purchase price but also maintenance and operational costs over the tool’s lifecycle.
- Establish Clear Communication Channels: Ensure that both parties understand the terms to avoid misunderstandings later.
Step 6: Establish a Trial Period
Before committing to a long-term partnership, consider setting a trial period. This allows you to assess the supplier’s reliability and product performance over time.
- Monitor Performance Metrics: Track delivery timelines, product quality, and customer service during the trial.
- Evaluate Responsiveness: Ensure that the supplier is responsive to queries and issues that may arise.
Step 7: Build Long-Term Relationships
Once you’ve established a successful partnership, focus on building a long-term relationship with your supplier. This can lead to better pricing, priority service, and collaborative opportunities.
- Engage in Regular Communication: Schedule periodic reviews to discuss performance and explore new opportunities.
- Provide Feedback: Share your experiences and insights with the supplier to foster mutual growth and improvement.
By following this checklist, B2B buyers can ensure they make informed decisions when sourcing power tools, ultimately leading to improved operational efficiency and business success.
Comprehensive Cost and Pricing Analysis for power tools supplier Sourcing
When sourcing power tools, understanding the comprehensive cost structure is critical for international B2B buyers. Different factors contribute to the total cost, and being aware of these can help you make more informed purchasing decisions.
What Are the Key Cost Components in Power Tools Supply?
Materials
The raw materials used in power tools significantly influence the final price. Common materials include high-carbon steel, aluminum, and durable plastics. Prices for these materials can fluctuate based on market demand and availability, which impacts overall pricing.
Labor Costs
Labor costs vary considerably by region. In countries with lower labor costs, such as some in Africa and South America, you may find more competitive pricing. However, keep in mind that lower labor costs can sometimes compromise quality, especially if the workers lack adequate training.
Manufacturing Overhead
Manufacturing overhead includes expenses related to utilities, facility maintenance, and depreciation of manufacturing equipment. Companies with advanced manufacturing technologies may have higher overhead costs but can offer better precision and efficiency in production.
Tooling and Setup Costs
Tooling refers to the costs associated with creating the molds and tools necessary for production. For custom designs or specialized tools, these costs can be substantial. Understanding the tooling expenses is vital when negotiating prices, especially for low-volume orders.
Quality Control (QC)
Investing in quality control measures ensures that the power tools meet industry standards and customer expectations. Suppliers with robust QC processes may charge a premium, but this investment can lead to fewer defects and returns, ultimately enhancing your total cost of ownership.
Logistics and Shipping
Logistics encompasses all costs related to transporting tools from the manufacturer to your location. Factors like distance, shipping method, and Incoterms can significantly impact logistics costs. Buyers should consider local shipping regulations and customs duties, especially when importing tools from different continents.
Profit Margin
Finally, the supplier’s profit margin will affect the price you pay. Different suppliers may have varying margins based on their market positioning, brand strength, and value-added services.
How Do Price Influencers Affect Power Tools Sourcing?
Volume and Minimum Order Quantity (MOQ)
Larger orders often lead to reduced per-unit costs. Suppliers may offer discounts based on volume, making it essential to assess your purchasing needs carefully. However, be cautious of MOQs that may lead to excess inventory.
Specifications and Customization
Customization requests, such as specific features or branding, can increase costs. Ensure your specifications are clear to avoid unexpected price hikes. Suppliers may also charge more for tools that require specialized manufacturing processes.
Material Quality and Certifications
The quality of materials and certifications (e.g., ISO, CE) can influence the price. Tools made with high-quality materials or those that meet specific certifications will typically command higher prices. For international buyers, verifying these certifications ensures compliance with local regulations.
Supplier Factors
The supplier’s reputation and experience can also affect pricing. Established suppliers may charge more due to their proven track record, while newer entrants might offer lower prices to gain market share. Evaluating supplier reliability and service quality is essential for long-term partnerships.
Incoterms and Terms of Sale
Understanding Incoterms can help you gauge the responsibilities of the buyer and seller regarding shipping costs and risks. Choosing the right Incoterms can lead to significant savings and smoother transactions.
What Tips Can Help Buyers Negotiate Better Prices for Power Tools?
Effective Negotiation Techniques
Leverage your purchasing power by establishing relationships with suppliers. Regular communication and transparency can lead to better negotiation outcomes. Don’t hesitate to request multiple quotes to compare and leverage better deals.
Focus on Cost Efficiency
Consider the total cost of ownership rather than just the upfront price. Factor in durability, maintenance, and warranty services, which can influence long-term costs. Tools that may appear expensive initially could save money over time if they require less maintenance or have a longer lifespan.
Understand Pricing Nuances for International Sourcing
Each region has unique economic conditions and supplier dynamics. Familiarize yourself with local market trends, currency fluctuations, and trade agreements that could affect pricing. This knowledge can empower you to negotiate more effectively and make informed decisions.
Disclaimer for Indicative Prices
Prices for power tools can vary widely based on specifications, market conditions, and supplier relationships. Always conduct thorough market research and consult multiple suppliers to obtain the most accurate pricing information tailored to your specific needs.
Alternatives Analysis: Comparing power tools supplier With Other Solutions
Understanding Alternatives in Power Tools Supply
In the B2B landscape, choosing the right supplier for power tools is crucial for operational efficiency and cost management. However, it’s essential to evaluate alternatives that may offer comparable benefits or address specific needs more effectively. This section explores two viable alternatives to traditional power tool suppliers: Tool Rental Services and Battery-Powered Tools. Each alternative presents unique advantages and challenges, making it vital for international buyers from regions like Africa, South America, the Middle East, and Europe to understand these options thoroughly.
Comparison Table of Power Tools Supplier and Alternatives
Comparison Aspect | Power Tools Supplier | Tool Rental Services | Battery-Powered Tools |
---|---|---|---|
Performance | High | Moderate | High |
Cost | High initial investment | Lower upfront costs | Moderate |
Ease of Implementation | Straightforward | Requires logistics | User-friendly |
Maintenance | Regular maintenance required | Minimal maintenance | Battery replacement |
Best Use Case | Long-term projects | Short-term projects | Mobility-focused tasks |
Detailed Breakdown of Alternatives
What are the Advantages and Disadvantages of Tool Rental Services?
Tool rental services provide a flexible solution for businesses that may not require tools on a permanent basis. This option significantly reduces upfront costs, allowing companies to allocate funds to other critical areas. However, the performance may not always match that of purchased tools, especially if specialized equipment is required. Additionally, logistical considerations, such as transportation and availability, can complicate the implementation process.
How Do Battery-Powered Tools Compare?
Battery-powered tools have gained popularity due to their portability and ease of use. They are particularly advantageous for projects requiring mobility, allowing workers to operate in areas without direct access to power sources. However, the cost of high-quality battery-powered tools can be moderate, and battery replacement can add to ongoing expenses. Moreover, while performance is generally high, it may not reach the levels of traditional electric tools for certain heavy-duty tasks.
Conclusion: How Can B2B Buyers Choose the Right Solution?
When evaluating the best option between a traditional power tools supplier, tool rental services, and battery-powered tools, B2B buyers should consider several factors. Assess the nature of your projects—long-term versus short-term—and the frequency of tool usage. Analyze your budget constraints and the total cost of ownership, including maintenance and replacement. Additionally, consider the specific requirements of your operations, such as mobility and performance needs. By thoroughly understanding these alternatives, international buyers can make informed decisions that align with their operational objectives and budgetary constraints.
Essential Technical Properties and Trade Terminology for power tools supplier
What Are the Essential Technical Properties of Power Tools?
Understanding the technical specifications of power tools is crucial for B2B buyers, especially when sourcing from international suppliers. Below are some of the key technical properties that should be considered:
1. Material Grade
Material grade refers to the type and quality of materials used in the manufacturing of power tools. Common materials include high-carbon steel, aluminum, and various plastics. The material grade impacts durability, performance, and resistance to wear and tear. For instance, tools made from high-carbon steel are typically more durable but may be heavier, while aluminum tools are lightweight and easier to handle. Buyers should evaluate material grades to ensure they meet the specific demands of their applications.
2. Tolerance
Tolerance is the permissible limit of variation in a physical dimension or measured value of a power tool. It is crucial for ensuring that parts fit together correctly and perform as intended. Tight tolerances may indicate higher manufacturing precision and quality, which can be essential for tools used in critical applications. B2B buyers should inquire about tolerance levels to ensure that the tools will perform reliably in their operations.
3. Power Rating
Power rating, usually measured in watts or horsepower, indicates the tool’s efficiency and capacity to perform tasks. Higher power ratings generally allow tools to work more effectively, especially in demanding environments. For instance, a power drill with a higher wattage can drill through tougher materials without overheating. Buyers should match the power rating with their intended use to optimize performance.
4. Speed Settings
Speed settings refer to the adjustable rates at which a power tool operates, often measured in RPM (revolutions per minute). Different tasks may require different speeds; for example, low speeds are ideal for driving screws, while high speeds are better for drilling. Understanding the speed settings available can help buyers select tools that offer versatility for various applications.
5. Ergonomics
Ergonomics involves the design of tools to maximize comfort and efficiency for users. Features such as handle design, weight distribution, and vibration dampening can significantly affect user experience and productivity. B2B buyers should consider ergonomic factors, especially for tools that will be used for extended periods, to reduce fatigue and enhance safety.
What Are Common Trade Terms in the Power Tools Industry?
Familiarity with industry jargon can streamline communication and negotiations with suppliers. Here are some essential trade terms:
1. OEM (Original Equipment Manufacturer)
OEM refers to a company that produces parts or equipment that may be marketed by another manufacturer. In the power tools sector, OEMs supply components that are integrated into the final products. Understanding OEM relationships can help buyers identify quality suppliers and ensure compatibility in parts.
2. MOQ (Minimum Order Quantity)
MOQ is the smallest quantity of a product that a supplier is willing to sell. This term is vital for buyers as it can impact inventory management and cash flow. Knowing the MOQ can help B2B buyers negotiate better terms and avoid overstocking or understocking situations.
3. RFQ (Request for Quotation)
An RFQ is a document sent to suppliers to solicit price quotes for specific products or services. It typically includes detailed specifications and quantities. For B2B buyers, issuing an RFQ can lead to competitive pricing and better supplier relationships, as it encourages suppliers to provide their best offers.
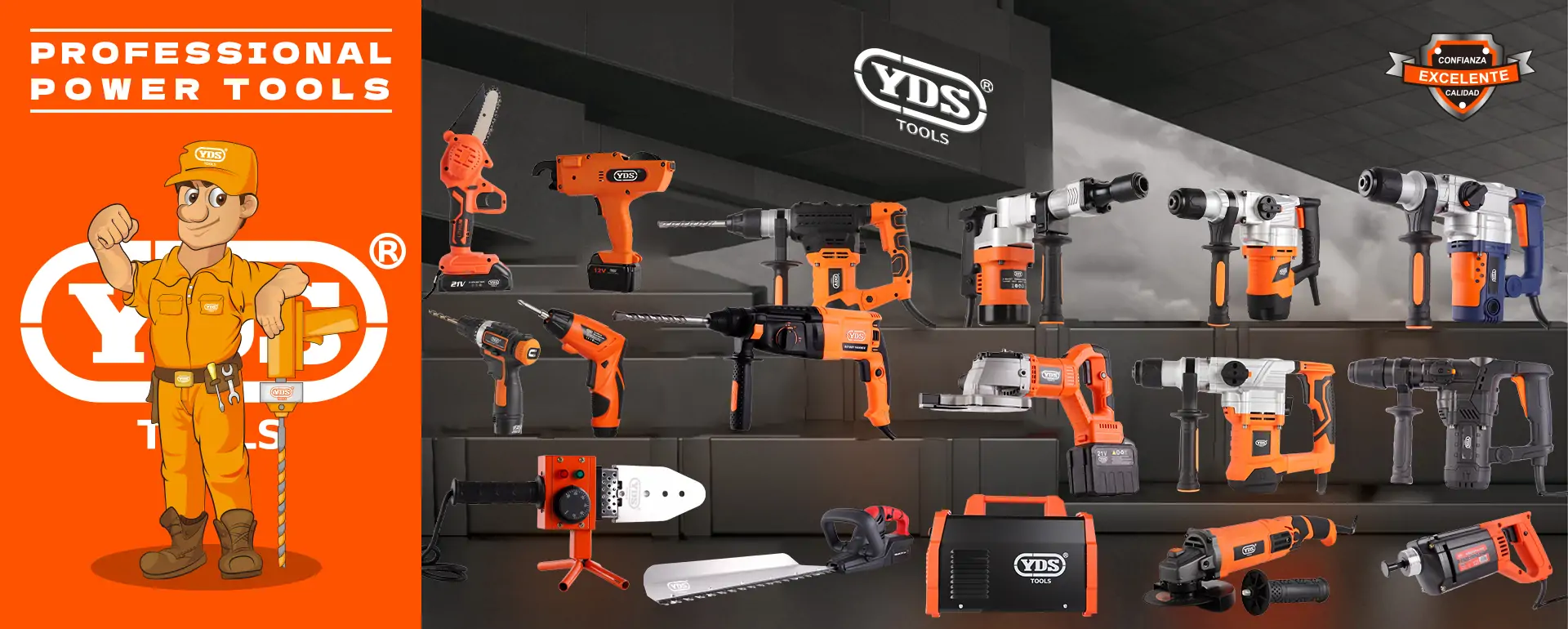
A stock image related to power tools supplier.
4. Incoterms (International Commercial Terms)
Incoterms are a set of international rules that define the responsibilities of buyers and sellers regarding the shipping and delivery of goods. Understanding these terms is crucial for international trade, as they clarify who is responsible for shipping costs, insurance, and risk during transit. Familiarity with Incoterms can help buyers negotiate better shipping terms and reduce potential disputes.
5. Lead Time
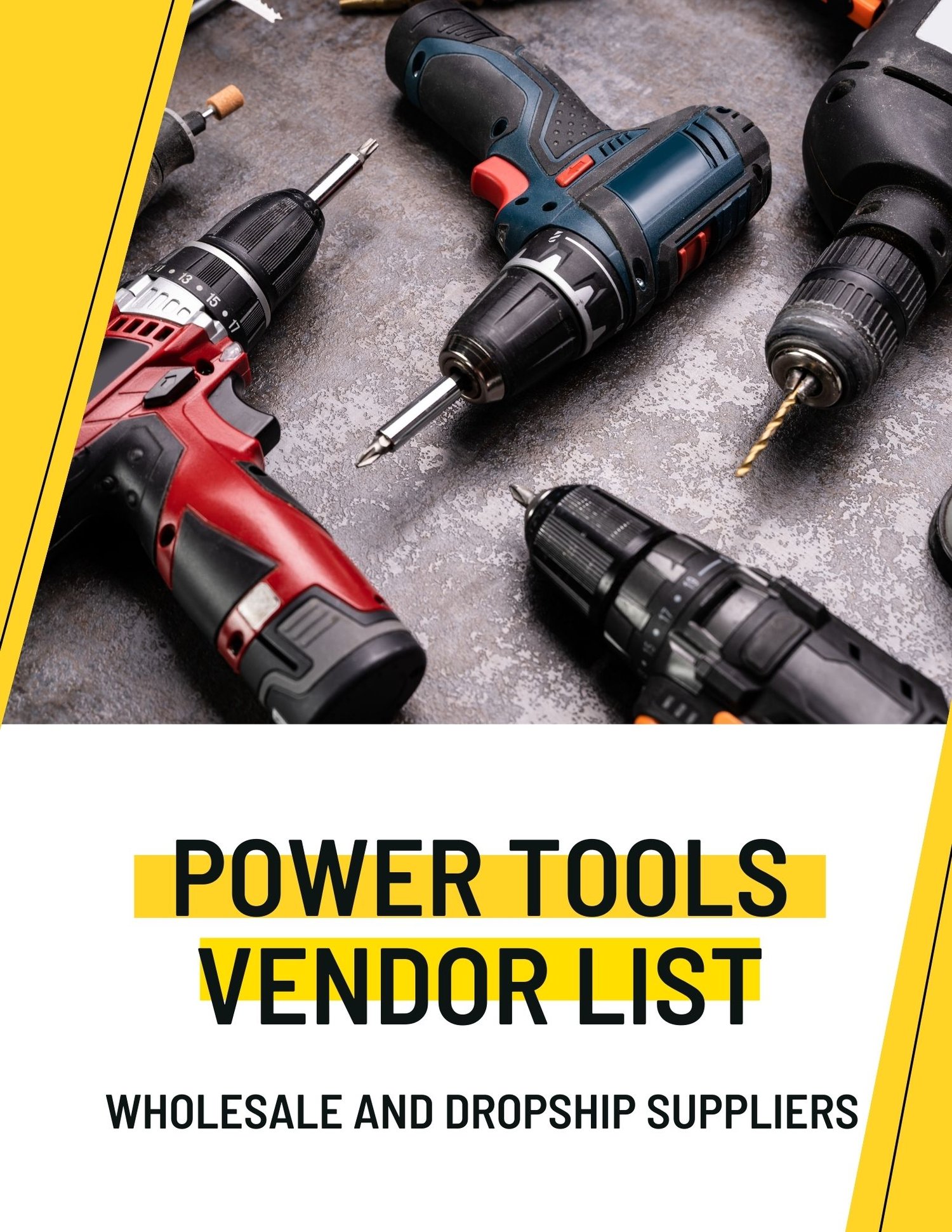
A stock image related to power tools supplier.
Lead time refers to the amount of time it takes from placing an order to receiving the goods. In the power tools industry, lead times can vary significantly based on factors such as production capacity and shipping distances. B2B buyers should consider lead times in their planning to ensure that they have the necessary tools available when needed.
By understanding these essential technical properties and trade terminologies, B2B buyers can make informed decisions when sourcing power tools, ultimately enhancing their operational efficiency and competitiveness in the market.
Navigating Market Dynamics and Sourcing Trends in the power tools supplier Sector
What Are the Current Market Dynamics and Key Trends for Power Tools Suppliers?
The global power tools supplier market is experiencing dynamic shifts driven by technological advancements, changing consumer preferences, and the increasing importance of sustainability. In regions such as Africa, South America, the Middle East, and Europe, B2B buyers are witnessing a surge in demand for innovative and efficient power tools. Key trends include the adoption of smart technologies, such as IoT-enabled tools that enhance connectivity and functionality. These tools not only improve operational efficiency but also provide valuable data analytics for maintenance and usage patterns.
Moreover, the rise of e-commerce platforms is transforming the sourcing landscape. International buyers are increasingly turning to online marketplaces for greater access to a diverse range of suppliers and competitive pricing. This shift has been particularly pronounced in South America and Africa, where traditional supply chains are being disrupted by digital solutions. Buyers are advised to leverage these platforms to explore new suppliers and negotiate better terms.
Another significant trend is the focus on product durability and performance. B2B buyers are prioritizing high-quality tools that offer longevity and reliability, as these factors directly impact operational costs. Suppliers that emphasize product testing and certification can gain a competitive edge in attracting discerning buyers. Understanding these market dynamics is crucial for international B2B buyers aiming to make informed sourcing decisions.
How Is Sustainability Shaping the Power Tools Supplier Sector?
Sustainability has become a cornerstone of sourcing strategies in the power tools supplier sector. As environmental concerns rise globally, B2B buyers are increasingly scrutinizing the environmental impact of the tools they purchase. This includes evaluating suppliers based on their carbon footprint, waste management practices, and the use of sustainable materials.
Ethical sourcing is also gaining traction. Buyers are now seeking suppliers that adhere to fair labor practices and have transparent supply chains. This not only aligns with corporate social responsibility goals but also caters to the growing consumer demand for ethically produced goods. Certifications such as ISO 14001 (Environmental Management) and FSC (Forest Stewardship Council) are becoming essential for suppliers looking to establish credibility in the market.
Moreover, the trend towards using ‘green’ materials in power tools—such as recycled plastics and sustainably sourced metals—is reshaping product offerings. B2B buyers should prioritize suppliers that provide eco-friendly options, as these products are often more appealing to end-users who are conscious of their environmental impact. By investing in sustainable sourcing, buyers can enhance their brand reputation while contributing to a healthier planet.
What Is the Historical Context of the Power Tools Supplier Industry?
The power tools supplier industry has evolved significantly over the past century. Initially dominated by manual tools, the sector underwent a transformation with the introduction of electric power tools in the early 20th century. This innovation not only increased efficiency but also expanded the scope of applications in construction, manufacturing, and DIY projects.
By the late 20th century, advancements in battery technology led to the rise of cordless power tools, which offered greater convenience and mobility. The introduction of lithium-ion batteries further enhanced performance, making these tools more appealing to both professional and amateur users. Today, the market is characterized by rapid technological advancements, including automation and smart technology integration, which continue to reshape the industry landscape.
For international B2B buyers, understanding the historical context of the power tools supplier sector is essential for recognizing the innovations that have shaped current market dynamics and trends. This knowledge can inform sourcing strategies and help buyers identify suppliers that are well-positioned to meet future demands.
Frequently Asked Questions (FAQs) for B2B Buyers of power tools supplier
-
How do I choose the right power tools supplier for my business needs?
Selecting the right power tools supplier involves evaluating several key factors. Start by assessing the supplier’s product range to ensure they offer the specific tools you need. Check their reputation through reviews and testimonials, and consider their experience in the industry. Additionally, verify their certifications and compliance with international standards, which can indicate reliability. It’s also beneficial to engage in direct communication to gauge their customer service and responsiveness, which are crucial for ongoing support. -
What are the typical payment terms when sourcing power tools internationally?
Payment terms can vary significantly among suppliers, but common practices include advance payment, letters of credit, and open account terms. It’s essential to discuss payment options upfront and negotiate terms that align with your cash flow and risk tolerance. For new relationships, consider using escrow services to mitigate risks. Ensure you understand any potential currency conversion fees and the implications of international payment processing times. -
How can I verify the quality of power tools before making a bulk purchase?
To ensure quality, request product samples or prototypes from the supplier before committing to a large order. Conduct thorough inspections or use third-party quality assurance services to assess the tools’ functionality and durability. Additionally, inquire about the supplier’s manufacturing processes and quality control measures. Checking for relevant certifications, such as ISO standards, can further assure you of the product’s quality and safety. -
What is the minimum order quantity (MOQ) for power tools, and how does it affect pricing?
Minimum order quantities (MOQs) for power tools can vary widely depending on the supplier and the specific products. Suppliers often set MOQs to manage production costs and inventory efficiently. Generally, larger orders may lead to lower per-unit costs, but consider your own inventory needs and cash flow. If MOQs are high, explore options for shared shipments with other buyers or negotiate for lower MOQs if you’re a first-time buyer. -
What customization options are available for power tools when sourcing from suppliers?
Many power tools suppliers offer customization options, including branding, color variations, and specific feature modifications. To explore customization, communicate your requirements clearly and ask the supplier about their capabilities. Keep in mind that custom orders may require higher MOQs and longer lead times. Ensure that any modifications still comply with safety standards and regulations in your target market. -
How can I assess the reliability of an international power tools supplier?
Assessing a supplier’s reliability involves multiple strategies. Start by researching their business history and client testimonials. Utilize platforms like Alibaba or Global Sources to check their ratings and feedback. Consider visiting their facilities if feasible, or request virtual tours. Additionally, confirm their compliance with international trade regulations and certifications, which can indicate a commitment to quality and reliability. -
What logistics considerations should I keep in mind when importing power tools?
Logistics play a crucial role in the timely delivery of power tools. Factors to consider include shipping methods (air vs. sea), customs clearance processes, and potential tariffs or duties. Work with a freight forwarder who understands the specifics of your destination market. It’s also wise to account for lead times, warehousing needs, and distribution channels in your planning to avoid delays and additional costs. -
How do I handle disputes or issues with my power tools supplier?
Handling disputes effectively requires clear communication and documentation. Start by addressing the issue directly with the supplier, providing evidence and details about the problem. If necessary, refer to the terms outlined in your contract or purchase agreement. In cases where resolution is not reached, consider mediation or arbitration, as stipulated in your agreement. Maintaining a professional demeanor throughout the process can help preserve the business relationship.
Important Disclaimer & Terms of Use
⚠️ Important Disclaimer
The information provided in this guide, including content regarding manufacturers, technical specifications, and market analysis, is for informational and educational purposes only. It does not constitute professional procurement advice, financial advice, or legal advice.
While we have made every effort to ensure the accuracy and timeliness of the information, we are not responsible for any errors, omissions, or outdated information. Market conditions, company details, and technical standards are subject to change.
B2B buyers must conduct their own independent and thorough due diligence before making any purchasing decisions. This includes contacting suppliers directly, verifying certifications, requesting samples, and seeking professional consultation. The risk of relying on any information in this guide is borne solely by the reader.
Strategic Sourcing Conclusion and Outlook for power tools supplier
In the realm of power tools sourcing, strategic partnerships are essential for maximizing value and ensuring quality. By carefully selecting suppliers who align with your business needs, international B2B buyers can enhance operational efficiency and reduce costs. Understanding regional market dynamics—especially in Africa, South America, the Middle East, and Europe—empowers businesses to make informed decisions, fostering resilience against supply chain disruptions.
What Are the Key Takeaways for B2B Buyers in Power Tools Sourcing?
Investing in strategic sourcing not only leads to better pricing but also ensures access to innovative technologies and sustainable practices. Buyers should prioritize suppliers that offer robust after-sales support and adhere to international quality standards. Establishing long-term relationships with reliable suppliers can mitigate risks associated with fluctuating market conditions.
How Can Buyers Prepare for Future Sourcing Challenges?
Looking ahead, the power tools industry will continue to evolve, driven by technological advancements and changing consumer demands. B2B buyers must remain agile, adapting to these changes by leveraging data analytics and market insights. Engage actively with suppliers to explore opportunities for collaboration, ensuring that your sourcing strategy is not just reactive but also proactive.
In conclusion, as international B2B buyers navigate the complexities of the power tools market, embracing strategic sourcing will be pivotal. Equip your business for future success by fostering strong supplier relationships and staying informed about industry trends. The time to act is now—begin your journey towards a more resilient and innovative sourcing strategy today.