Cut Costs with the Best Forging Manufacturer Guide (2025)
Introduction: Navigating the Global Market for forging manufacturer
Navigating the complex landscape of sourcing a reliable forging manufacturer can pose significant challenges for international B2B buyers, particularly those in Africa, South America, the Middle East, and Europe. With an increasing demand for high-quality forged products across various industries, understanding the nuances of the forging process, material specifications, and supplier capabilities is crucial. This guide aims to demystify the procurement process by providing a comprehensive overview of the different types of forging methods, their applications, and the criteria for effective supplier vetting.
International buyers must consider factors such as production capacity, quality assurance standards, and cost structures when selecting a forging manufacturer. Additionally, understanding the intricacies of global supply chains, including shipping logistics and regulatory compliance, can significantly impact purchasing decisions. This guide empowers B2B buyers by equipping them with actionable insights on how to assess potential suppliers, negotiate favorable terms, and ultimately make informed purchasing decisions that align with their business objectives.
Whether you are looking to source forged components for the automotive, aerospace, or construction sectors, this guide serves as a valuable resource, streamlining your search for the right forging manufacturer. By leveraging the information presented here, you can navigate the global market with confidence, ensuring that you partner with manufacturers who meet your exacting standards and business needs.
Understanding forging manufacturer Types and Variations
Type Name | Key Distinguishing Features | Primary B2B Applications | Brief Pros & Cons for Buyers |
---|---|---|---|
Open Die Forging | Simple tooling, versatile shapes | Aerospace, automotive, oil & gas | Pros: Cost-effective for large parts. Cons: Limited precision for complex shapes. |
Closed Die Forging | High precision, complex shapes | Medical devices, precision engineering | Pros: High dimensional accuracy. Cons: Higher tooling costs. |
Rolled Forging | Continuous process, large production volumes | Construction, heavy machinery | Pros: Economical for mass production. Cons: Limited to specific shapes. |
Drop Forging | High strength components, impact resistance | Defense, automotive, industrial applications | Pros: Excellent mechanical properties. Cons: Higher energy consumption. |
Precision Forging | Tight tolerances, specialized applications | Aerospace, high-performance automotive | Pros: Exceptional accuracy and finish. Cons: Higher costs and longer lead times. |
What are the Characteristics of Open Die Forging?
Open die forging is characterized by the use of flat or contoured dies that allow the metal to flow freely, making it suitable for simple shapes and large components. This method is widely used in industries such as aerospace and automotive due to its cost-effectiveness for producing large parts. Buyers should consider that while open die forging is economical, it may not achieve the precision required for more complex geometries.
How Does Closed Die Forging Differ from Other Types?
Closed die forging involves the use of pre-shaped dies that enclose the metal, allowing for higher precision and the ability to create intricate shapes. This method is often employed in the manufacturing of medical devices and precision engineering components. Buyers should weigh the higher initial tooling costs against the benefits of improved accuracy and reduced machining needs, making it ideal for high-value applications.
What are the Benefits of Rolled Forging?
Rolled forging is a continuous process that enables the production of large quantities of products with consistent quality. It is commonly used in construction and heavy machinery applications. The main advantages include cost-efficiency for mass production and the ability to create larger components. However, buyers should be mindful that rolled forging is limited in terms of the shapes that can be produced.
Why Choose Drop Forging for Strength?
Drop forging is known for its ability to produce high-strength components through the use of impact force during the forging process. It is particularly popular in defense and automotive industries where durability is paramount. While drop forging offers excellent mechanical properties, buyers must consider the higher energy consumption and operational costs associated with this method.
What Makes Precision Forging Ideal for Aerospace Applications?
Precision forging is designed for applications requiring tight tolerances and high-quality finishes, making it ideal for aerospace and high-performance automotive sectors. This method ensures exceptional accuracy but comes with increased costs and longer lead times. Buyers should assess whether the benefits of precision forging justify the investment in their specific applications, particularly when quality is non-negotiable.
Related Video: Forging
Key Industrial Applications of forging manufacturer
Industry/Sector | Specific Application of forging manufacturer | Value/Benefit for the Business | Key Sourcing Considerations for this Application |
---|---|---|---|
Automotive | Production of crankshafts and connecting rods | Enhanced durability and performance in engines | Quality certifications, compliance with international standards, and supplier reliability |
Aerospace | Manufacturing of turbine components | High strength-to-weight ratio, critical for flight safety | Precision engineering capabilities, traceability of materials, and adherence to strict regulatory requirements |
Oil and Gas | Creation of valves and fittings | Improved safety and efficiency in high-pressure environments | Material quality, resistance to corrosion, and supplier experience in handling critical applications |
Construction | Fabrication of structural components | Increased structural integrity and load-bearing capacity | Compliance with local building codes, material specifications, and lead times for project timelines |
Mining | Production of heavy-duty equipment parts | Enhanced wear resistance and extended equipment life | Supplier capacity, ability to handle large orders, and experience with specific mining applications |
How is Forging Used in the Automotive Industry?
In the automotive sector, forging manufacturers produce essential components such as crankshafts and connecting rods. These parts undergo immense stress and require superior strength and durability. By using forged materials, manufacturers can achieve components that withstand high temperatures and pressures, ultimately enhancing the vehicle’s performance and longevity. International buyers should prioritize suppliers with ISO certifications to ensure compliance with global standards and quality assurance.
What Role Does Forging Play in Aerospace Applications?
The aerospace industry demands high precision and reliability, especially for critical components like turbine blades and landing gear. Forging manufacturers provide parts that have a high strength-to-weight ratio, crucial for improving fuel efficiency and safety in aircraft. Buyers from regions like Europe and the Middle East should consider suppliers that specialize in aerospace-grade materials and can offer detailed documentation to meet stringent regulatory requirements.
Why is Forging Important in the Oil and Gas Sector?
In oil and gas operations, forged components such as valves and fittings are vital for maintaining safety and efficiency in high-pressure systems. The forging process enhances the material’s resistance to wear and corrosion, which is essential for long-term performance in harsh environments. B2B buyers should focus on sourcing manufacturers with proven experience in the oil and gas sector and those who can provide materials that meet industry-specific standards.
How Does Forging Enhance Construction Projects?
Forging manufacturers contribute significantly to the construction industry by producing structural components that ensure safety and stability. Forged steel beams and reinforcements provide higher load-bearing capacities compared to welded or cast materials. Buyers should look for suppliers who can demonstrate compliance with local building codes and offer materials that meet specific engineering requirements to avoid costly project delays.
What Benefits Does Forging Provide in Mining Equipment?
In the mining sector, the durability of equipment is paramount. Forged parts, such as those used in heavy-duty machinery, offer enhanced wear resistance, which translates to longer service life and reduced downtime. International buyers need to consider suppliers that can handle large orders and have a solid reputation for producing mining-specific components, as this can significantly impact operational efficiency and cost-effectiveness.
Related Video: What is Cold Forging? || THORS Forging Basics Course Preview
3 Common User Pain Points for ‘forging manufacturer’ & Their Solutions
Scenario 1: Navigating Quality Assurance Challenges in Forging
The Problem:
B2B buyers often face significant challenges when it comes to ensuring the quality of forged products. In regions such as Africa and South America, where local suppliers may not adhere to stringent quality standards, buyers can find themselves receiving subpar products that lead to costly reworks or project delays. This concern is amplified when sourcing from international manufacturers, as the lack of clear quality assurance protocols can result in discrepancies in product specifications and performance.
The Solution:
To mitigate quality assurance issues, buyers should prioritize manufacturers that provide comprehensive documentation of their quality control processes. Look for forging manufacturers that are certified by recognized international standards such as ISO 9001. Additionally, implementing a robust supplier evaluation process is crucial. This can involve requesting samples for testing, conducting factory audits, and establishing clear communication channels to discuss quality expectations upfront. Collaborating closely with the manufacturer throughout the production process can also help ensure that quality standards are met consistently.
Scenario 2: Overcoming Long Lead Times for Forged Components
The Problem:
International B2B buyers often struggle with long lead times when ordering forged components, particularly when dealing with suppliers in Europe or the Middle East. These delays can disrupt supply chains and lead to missed deadlines, especially when urgent projects require quick turnarounds. Factors such as limited production capacity, shipping logistics, and customs clearance can exacerbate this issue, leaving buyers frustrated and financially impacted.
The Solution:
To address lead time challenges, buyers should consider establishing long-term relationships with multiple forging manufacturers to create a diverse supply chain. This strategy allows for better flexibility in meeting urgent demands. Additionally, buyers should engage in open dialogue with their chosen suppliers about production schedules and the possibility of expedited services. Setting up a just-in-time inventory system can also reduce lead time pressures by ensuring that the necessary components are available right when needed, minimizing the reliance on long manufacturing cycles.
Scenario 3: Managing Cost Fluctuations in Forging Services
The Problem:
Cost volatility is a common pain point for B2B buyers in the forging industry. Prices for raw materials, such as steel, can fluctuate due to market conditions, geopolitical events, or changes in supply and demand. This unpredictability can significantly impact project budgets and forecasting, particularly for buyers in the Middle East and Africa, where sourcing options may be limited.
The Solution:
To effectively manage cost fluctuations, buyers should engage in strategic sourcing practices that involve locking in prices through long-term contracts with suppliers. This not only stabilizes costs but also fosters a deeper partnership with manufacturers. Buyers can also explore alternative materials or manufacturing processes that may offer more cost-effective solutions without compromising quality. Additionally, staying informed about market trends and participating in industry networks can provide insights into potential price changes, allowing buyers to plan their procurement strategies accordingly.
Strategic Material Selection Guide for forging manufacturer
What Are the Key Properties of Common Materials Used in Forging?
When selecting materials for forging applications, international B2B buyers must consider various factors, including mechanical properties, cost, and application suitability. Below, we analyze four common materials used in forging processes, focusing on their properties, advantages, disadvantages, and implications for buyers from regions such as Africa, South America, the Middle East, and Europe.
How Does Carbon Steel Perform in Forging Applications?
Key Properties: Carbon steel is known for its excellent strength and hardness, making it suitable for high-stress applications. It typically withstands temperatures up to 800°C and exhibits good wear resistance. However, its corrosion resistance is relatively low compared to other materials.
Pros & Cons: Carbon steel is durable and cost-effective, making it a popular choice for various applications, including automotive and machinery parts. However, its susceptibility to rust and corrosion can limit its use in environments with high moisture or chemical exposure.
Impact on Application: Carbon steel is compatible with a wide range of media, but its low corrosion resistance may necessitate protective coatings or treatments in certain applications.
Considerations for International Buyers: Buyers should ensure compliance with international standards such as ASTM A36 or DIN 17100. It is essential to assess the local availability of carbon steel grades to minimize lead times and transportation costs.
What Are the Advantages of Alloy Steel in Forging?
Key Properties: Alloy steel, which includes elements like chromium, nickel, and molybdenum, offers enhanced mechanical properties, including improved toughness and wear resistance. It can typically handle higher temperatures (up to 900°C) and pressures than carbon steel.
Pros & Cons: The main advantage of alloy steel is its versatility in various applications, from aerospace to heavy machinery. However, it tends to be more expensive than carbon steel, and its manufacturing process can be more complex due to the need for precise alloying.
Impact on Application: Alloy steel is suitable for applications requiring high strength and resistance to extreme conditions, such as oil and gas exploration. Buyers must consider the specific alloy composition to ensure compatibility with the intended media.
Considerations for International Buyers: Compliance with standards like ASTM AISI 4140 or JIS G4105 is crucial. Buyers should also evaluate local suppliers’ capabilities to provide the desired alloy grades.
Why Choose Stainless Steel for Forging Applications?
Key Properties: Stainless steel is renowned for its excellent corrosion resistance and high-temperature tolerance, often exceeding 1000°C. It contains a minimum of 10.5% chromium, which forms a protective oxide layer.
Pros & Cons: The primary advantage of stainless steel is its durability and resistance to corrosion, making it ideal for food processing, chemical processing, and marine applications. However, it is generally more expensive than carbon and alloy steels, and its forging process can be more challenging due to its work-hardening properties.
Impact on Application: Stainless steel’s compatibility with corrosive media makes it suitable for applications in harsh environments. However, its cost may be a limiting factor for some projects.
Considerations for International Buyers: Buyers should look for compliance with standards such as ASTM A240 or DIN 1.4301. Understanding local market conditions for stainless steel can also help in negotiating better prices.
What Role Does Titanium Play in Forging?
Key Properties: Titanium is known for its exceptional strength-to-weight ratio and excellent corrosion resistance, particularly in high-temperature environments. It can withstand temperatures up to 600°C and is highly resistant to oxidation.
Pros & Cons: The key advantage of titanium is its lightweight nature combined with high strength, making it ideal for aerospace and medical applications. However, it is significantly more expensive than other materials, and its forging process requires specialized equipment.
Impact on Application: Titanium is particularly suitable for applications involving aggressive media, such as seawater or acidic environments. Its unique properties make it a preferred choice in industries where performance is critical.
Considerations for International Buyers: Buyers must ensure compliance with standards like ASTM B348 or JIS H4600. Given the high cost of titanium, buyers should assess the total lifecycle costs and potential savings in performance and maintenance.
Summary Table of Material Selection for Forging
Material | Typical Use Case for forging manufacturer | Key Advantage | Key Disadvantage/Limitation | Relative Cost (Low/Med/High) |
---|---|---|---|---|
Carbon Steel | Automotive and machinery parts | Cost-effective and durable | Low corrosion resistance | Low |
Alloy Steel | Aerospace and heavy machinery | Enhanced toughness and versatility | Higher cost and manufacturing complexity | Medium |
Stainless Steel | Food processing and chemical industries | Excellent corrosion resistance | Higher cost and challenging to forge | High |
Titanium | Aerospace and medical applications | Exceptional strength-to-weight ratio | Very high cost and specialized forging | High |
This guide provides a comprehensive overview of material selection for forging manufacturers, offering valuable insights for international B2B buyers to make informed decisions.
In-depth Look: Manufacturing Processes and Quality Assurance for forging manufacturer
What Are the Key Stages in the Manufacturing Process for Forging Manufacturers?
The manufacturing process for forging is critical for producing high-quality metal components. This process typically involves four main stages: material preparation, forming, assembly, and finishing.
-
Material Preparation
The first step involves selecting the right raw materials, often steel or aluminum alloys, based on the desired properties of the final product. The material is then cut into appropriate sizes, which may involve processes such as shearing or sawing. Prior to forging, the materials are often preheated to improve malleability, which aids in the forming process. -
Forming
The actual forging process can be done through various methods, including open-die forging, closed-die forging, and upset forging. Each technique has its advantages depending on the complexity and precision required for the component. Open-die forging is suitable for larger components, while closed-die forging is ideal for intricate shapes and tight tolerances. The choice of method directly impacts the mechanical properties and surface finish of the forged parts. -
Assembly
In some cases, multiple forged components may need to be assembled into a final product. This stage often involves processes such as welding or mechanical fastening. It is crucial that the assembly process maintains the integrity of the forged parts, ensuring that they meet the required specifications. -
Finishing
The finishing stage can include machining, surface treatment, and quality checks. Machining is often necessary to achieve precise dimensions and tolerances. Surface treatments, such as coating or heat treatment, enhance corrosion resistance and mechanical properties. The finishing process is vital in ensuring that the final product meets industry standards and customer specifications.
What Are the Key Quality Assurance Standards for Forging Manufacturers?
Quality assurance in forging manufacturing is essential for ensuring that products meet international standards and customer expectations. Key standards include:
-
ISO 9001: This internationally recognized standard outlines the requirements for a quality management system (QMS). It focuses on customer satisfaction and the continuous improvement of processes.
-
CE Marking: For products sold in the European Economic Area (EEA), CE marking indicates compliance with EU safety, health, and environmental protection standards.
-
API Certification: For manufacturers producing components for the oil and gas industry, compliance with American Petroleum Institute (API) standards ensures that products meet rigorous industry requirements.
How Is Quality Control Implemented Throughout the Manufacturing Process?
Quality control (QC) is integrated at various checkpoints throughout the forging manufacturing process to maintain high standards. Key QC checkpoints include:
-
Incoming Quality Control (IQC)
This initial stage involves inspecting raw materials upon delivery to ensure they meet specified standards. Tests may include chemical composition analysis and mechanical property testing. -
In-Process Quality Control (IPQC)
During the forming and assembly stages, regular inspections are conducted to monitor the processes. This may involve dimensional checks and visual inspections to identify any defects early in the manufacturing cycle. -
Final Quality Control (FQC)
Once the product is finished, a comprehensive inspection is performed. This includes testing for dimensional accuracy, surface finish, and mechanical properties. Common testing methods include tensile testing, hardness testing, and non-destructive testing (NDT) techniques such as ultrasonic testing or radiography.
How Can B2B Buyers Verify Supplier Quality Control Practices?
International B2B buyers, particularly from Africa, South America, the Middle East, and Europe, must ensure that their suppliers adhere to stringent quality control measures. Here are actionable steps to verify supplier QC practices:
-
Conduct Supplier Audits
Regular audits of suppliers’ facilities can provide insights into their manufacturing processes and QC measures. An on-site audit allows buyers to assess compliance with international standards and observe QC practices firsthand. -
Request Quality Assurance Reports
Suppliers should provide detailed QC reports that document testing results and compliance with relevant standards. These reports should be reviewed to ensure they align with the buyer’s requirements. -
Engage Third-Party Inspection Services
Hiring independent third-party inspection services can offer an unbiased evaluation of the supplier’s quality control practices. These services can conduct audits, testing, and certification processes, enhancing trust in the supplier’s capabilities.
What Nuances Should International B2B Buyers Consider Regarding Quality Control?
When dealing with international suppliers, B2B buyers must navigate several nuances related to quality control:
-
Understanding Local Standards: Different regions may have varying quality standards and regulations. Buyers should familiarize themselves with local norms to ensure compliance and avoid potential legal issues.
-
Language Barriers: Communication can be challenging due to language differences. Buyers should ensure that quality documentation is available in a language they understand, facilitating better oversight.
-
Cultural Differences in Business Practices: Cultural approaches to business and quality can vary significantly. Buyers should be aware of these differences and establish clear expectations regarding quality standards and practices.
-
Logistical Challenges: International shipping can pose risks to product quality. Implementing strict shipping and handling protocols is essential to maintain product integrity during transit.
By understanding these aspects of the manufacturing processes and quality assurance in forging, international B2B buyers can make informed decisions and establish strong partnerships with reliable suppliers.
Practical Sourcing Guide: A Step-by-Step Checklist for ‘forging manufacturer’
In the competitive landscape of global manufacturing, sourcing the right forging manufacturer is critical for ensuring product quality and operational efficiency. This practical guide provides a step-by-step checklist designed to help B2B buyers, particularly those in Africa, South America, the Middle East, and Europe, navigate the sourcing process effectively.
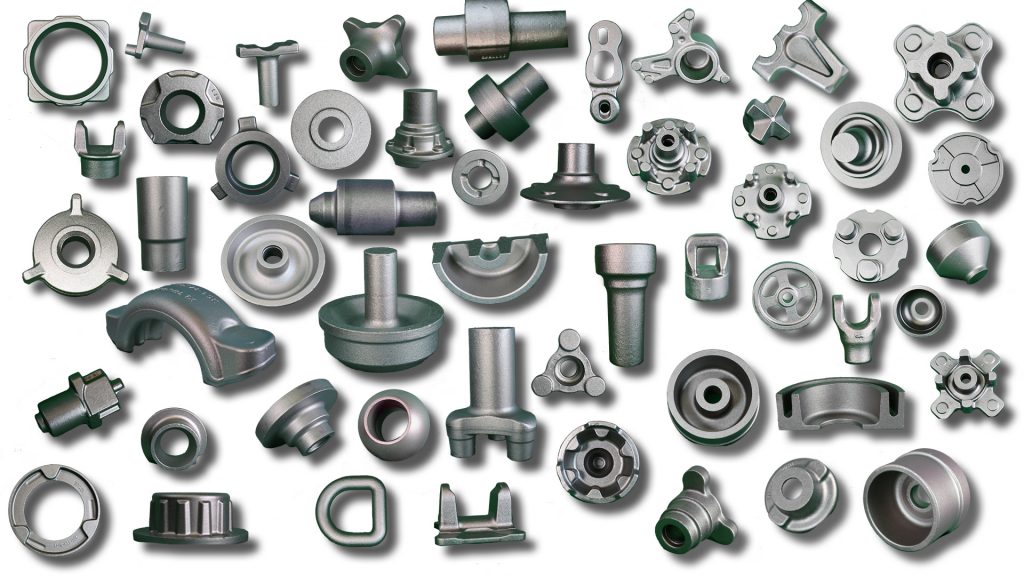
A stock image related to forging manufacturer.
Step 1: Define Your Technical Specifications
Begin by outlining your specific requirements for the forged components. This includes material types, dimensions, tolerances, and any special treatments or finishes needed. Having clear specifications helps in communicating your needs effectively to potential suppliers and ensures that the products meet your operational standards.
- Material Requirements: Specify the type of metal or alloy required for your applications.
- Tolerances and Standards: Include industry standards that must be adhered to, which can influence the manufacturing process.
Step 2: Research Potential Suppliers
Conduct thorough research to identify a list of potential forging manufacturers. Utilize online directories, industry associations, and trade shows to gather a broad selection of suppliers that meet your criteria.
- Online Resources: Use platforms like ThomasNet or Alibaba to find manufacturers with good reviews.
- Industry Connections: Leverage your network to get recommendations for reputable suppliers.
Step 3: Evaluate Supplier Capabilities
Once you have a list of potential suppliers, assess their manufacturing capabilities. This includes reviewing their production capacity, technology, and quality control processes. Understanding their capabilities ensures they can meet your demands.
- Production Capacity: Confirm whether they can handle your order volume without compromising lead times.
- Technology and Equipment: Investigate if they use advanced forging technologies that can enhance product quality.
Step 4: Verify Supplier Certifications
Before finalizing a supplier, verify their certifications and compliance with industry standards. Certifications such as ISO 9001 or specific industry-related standards demonstrate a commitment to quality and reliability.
- Quality Assurance: Ask for documentation that proves adherence to quality management systems.
- Regulatory Compliance: Ensure they comply with regulations relevant to your industry, which can vary by region.
Step 5: Request Quotes and Compare Pricing
Request detailed quotes from shortlisted suppliers, ensuring they include all relevant costs such as tooling, shipping, and taxes. Comparing quotes allows you to assess the overall value rather than just the base price.
- Breakdown of Costs: Look for transparency in pricing to avoid hidden fees later.
- Volume Discounts: Inquire about pricing for larger orders, which can significantly affect your budget.
Step 6: Conduct Site Visits or Virtual Audits
If feasible, arrange site visits to the manufacturing facilities of potential suppliers. If travel is not an option, consider virtual audits to assess their operations and capabilities.
- Facility Inspection: Observe the production processes and workplace conditions to gauge quality assurance.
- Cultural Fit: Evaluate whether their business practices align with your company’s values and expectations.
Step 7: Establish Clear Communication Channels
Once you select a supplier, establish clear communication channels for ongoing interaction. Effective communication is vital for addressing any issues that may arise during production.
- Regular Updates: Set expectations for progress updates and timelines.
- Point of Contact: Designate a primary contact person on both sides to streamline communication.
By following this checklist, B2B buyers can enhance their sourcing strategies, ensuring they select a forging manufacturer that meets their technical and operational requirements while fostering a successful business relationship.
Comprehensive Cost and Pricing Analysis for forging manufacturer Sourcing
What Are the Key Cost Components in Forging Manufacturing?
When sourcing from a forging manufacturer, understanding the cost structure is vital for international B2B buyers. The primary cost components include:
-
Materials: The choice of materials significantly affects pricing. Common materials include carbon steel, alloy steel, and aluminum. Prices can fluctuate based on market demand and availability, which can be especially volatile in emerging markets.
-
Labor: Skilled labor is essential in forging processes, often impacting the cost. Labor rates can vary widely by region, with countries in Europe generally having higher labor costs compared to those in Africa or South America.
-
Manufacturing Overhead: This includes costs related to facility maintenance, utilities, and administrative expenses. Overhead can vary significantly based on the manufacturer’s location and operational efficiencies.
-
Tooling: Tooling costs can be substantial, particularly for custom parts. This includes dies and molds that may need to be produced for specific projects. The complexity and durability of the tooling will influence its cost.
-
Quality Control (QC): Ensuring product quality is non-negotiable. The costs associated with QC can include inspections, testing, and certifications, which are crucial for meeting international standards.
-
Logistics: Shipping and handling costs can vary based on distance, mode of transport, and whether the supplier manages logistics. Understanding Incoterms is crucial for determining who is responsible for these costs.
-
Margin: Manufacturers will typically include a profit margin in their pricing. This margin can be influenced by the manufacturer’s reputation, the complexity of the order, and market competition.
How Do Price Influencers Affect Sourcing Decisions?
Several factors influence the pricing from forging manufacturers:
-
Volume and Minimum Order Quantity (MOQ): Larger orders often lead to lower per-unit costs. Buyers should negotiate terms that leverage their purchasing power.
-
Specifications and Customization: Custom parts require additional processing, which can increase costs. Be clear about specifications to avoid unexpected charges.
-
Materials and Quality Certifications: High-quality materials and certifications (like ISO) may lead to higher upfront costs but can reduce the total cost of ownership due to lower failure rates and longer product life.
-
Supplier Factors: The reputation and reliability of the supplier can impact pricing. Established manufacturers may charge more due to their proven track record and quality assurance processes.
-
Incoterms: Understanding Incoterms is crucial for managing logistics costs. Terms like FOB (Free on Board) and CIF (Cost, Insurance, and Freight) dictate who bears responsibility for shipping and risk during transport.
What Are the Best Negotiation Tips for B2B Buyers?
B2B buyers from Africa, South America, the Middle East, and Europe should consider the following negotiation strategies:
-
Conduct Thorough Market Research: Understand the market rates for materials and labor in the supplier’s region. This knowledge empowers buyers during negotiations.
-
Evaluate Total Cost of Ownership (TCO): Instead of focusing solely on the initial price, consider the TCO, which includes maintenance, logistics, and potential downtime costs.
-
Build Relationships: Establishing a strong relationship with suppliers can lead to better pricing and terms in the long run. Trust can facilitate more favorable negotiation outcomes.
-
Seek Multiple Quotes: Obtaining quotes from various suppliers can provide leverage in negotiations. It also gives insight into market pricing trends.
-
Clarify Payment Terms: Negotiate payment terms that align with cash flow needs. Longer payment terms can help manage upfront costs.
Are Indicative Prices Available for Forging Manufacturing?
While indicative prices can provide a baseline for budgeting, they can vary widely based on the factors mentioned above. It is essential for buyers to request detailed quotes from multiple manufacturers, taking into account the specific needs of their projects. This ensures a more accurate understanding of potential costs involved in forging manufacturing.
Alternatives Analysis: Comparing forging manufacturer With Other Solutions
Understanding Alternatives to Forging Manufacturers
In the competitive landscape of manufacturing, businesses often seek various methods to achieve their production goals efficiently and cost-effectively. Forging manufacturers are widely recognized for their ability to produce durable components through the deformation of metals. However, buyers should consider alternative solutions that may offer unique advantages depending on their specific needs, budget constraints, and production requirements.
Comparison Table of Forging Manufacturer and Alternatives
Comparison Aspect | Forging Manufacturer | Casting Process | CNC Machining |
---|---|---|---|
Performance | High strength and durability | Moderate strength; depends on material and design | High precision with excellent surface finish |
Cost | Generally higher due to tooling and setup | Lower initial costs, but can incur higher waste | Moderate; tooling costs can be significant |
Ease of Implementation | Requires skilled labor and specialized machinery | Easier setup; less skilled labor needed | High skill requirement for programming and operation |
Maintenance | Low maintenance if well-designed | Moderate; depends on mold quality | Requires regular calibration and maintenance |
Best Use Case | High-volume production of strong parts | Complex shapes and low-volume runs | Custom parts with intricate designs and tight tolerances |
Detailed Breakdown of Alternative Solutions
What Are the Pros and Cons of the Casting Process?
Casting is a manufacturing process where liquid material is poured into a mold and allowed to solidify. This method is particularly effective for creating complex shapes that would be difficult to achieve through forging. The primary advantages of casting include lower initial setup costs and the ability to produce intricate geometries. However, the downside includes potential issues with strength and defects, depending on the material and the quality of the mold used. Casting is ideal for low-volume runs or parts that do not require the high strength typically offered by forged components.
How Does CNC Machining Compare to Forging?
CNC (Computer Numerical Control) machining is a subtractive manufacturing process that utilizes computer-controlled tools to remove material from a workpiece. This method excels in producing parts with high precision and excellent surface finishes, making it suitable for applications that demand tight tolerances. While CNC machining can be cost-effective for small batches or custom parts, it generally incurs higher tooling costs and requires skilled operators for programming and machine setup. CNC machining is best suited for projects where precision is paramount, and the production volume is lower.
Conclusion: Which Solution Should You Choose?
When evaluating the best manufacturing solution, B2B buyers must assess their specific needs, including production volume, cost constraints, and required material properties. Forging manufacturers offer unmatched strength and durability, making them ideal for high-volume production of critical components. In contrast, casting and CNC machining present viable alternatives for different applications, particularly where complex shapes or precise tolerances are required. By understanding the unique advantages and limitations of each method, buyers can make informed decisions that align with their operational objectives and budgetary constraints.
Essential Technical Properties and Trade Terminology for forging manufacturer
What Are the Essential Technical Properties of Forging Manufacturers?
Understanding the technical properties of forged products is crucial for international B2B buyers. These properties not only influence the quality and performance of the final products but also impact the overall cost-effectiveness and reliability in various applications. Here are some critical specifications to consider:
-
Material Grade
Material grade refers to the specific classification of the raw materials used in forging. Common grades include carbon steel, alloy steel, stainless steel, and others. Each grade has unique mechanical properties such as tensile strength, yield strength, and corrosion resistance. Buyers should choose a material grade that meets the specific requirements of their application, ensuring durability and performance. -
Tolerance Levels
Tolerance levels define the acceptable limits of variation in dimensions and other characteristics of the forged parts. They are critical for ensuring that components fit together properly in assemblies. For example, tighter tolerances may be necessary for precision-engineered products. Understanding tolerance requirements can help buyers avoid costly rework or failure in the field. -
Heat Treatment Specifications
Heat treatment is a process applied to enhance the mechanical properties of forged parts, including hardness, toughness, and ductility. Different heat treatment processes, such as annealing, quenching, and tempering, yield different properties. Buyers should be aware of the heat treatment processes used by manufacturers to ensure that the final products meet their specific performance criteria. -
Surface Finish Standards
The surface finish of forged products affects their aesthetic quality and functional performance, especially in applications where friction or corrosion resistance is critical. Common surface finishes include as-forged, machined, or coated. Buyers should specify surface finish requirements to ensure compatibility with their intended applications. -
Impact Toughness
Impact toughness measures a material’s ability to absorb energy and resist fracture under sudden loads. This property is particularly important in industries such as automotive and aerospace, where components may experience high-stress conditions. Buyers should inquire about the impact toughness of forged products to ensure they can withstand operational demands.
What Are Common Trade Terms Used in Forging Manufacturing?
Familiarity with industry jargon is essential for effective communication and negotiation with forging manufacturers. Here are some commonly used trade terms:
-
OEM (Original Equipment Manufacturer)
An OEM refers to a company that produces parts or equipment that may be marketed by another manufacturer. In the forging industry, OEMs often source forged components from manufacturers to incorporate into their final products. Understanding the OEM relationship can help buyers identify reliable suppliers for their specific needs. -
MOQ (Minimum Order Quantity)
MOQ denotes the smallest quantity of a product that a supplier is willing to sell. This term is crucial for buyers as it affects inventory management and cost efficiency. Knowing the MOQ helps businesses assess whether a supplier aligns with their purchasing strategy, especially for startups or smaller enterprises. -
RFQ (Request for Quotation)
An RFQ is a formal document sent to suppliers requesting a quote for specific products or services. It typically includes detailed specifications, quantities, and delivery timelines. For buyers, issuing an RFQ is a vital step in the procurement process, enabling them to compare offers and negotiate better terms. -
Incoterms (International Commercial Terms)
Incoterms are a set of internationally recognized rules that define the responsibilities of buyers and sellers in the shipping process. Terms like FOB (Free on Board) and CIF (Cost, Insurance, and Freight) clarify who is responsible for shipping costs, insurance, and risk during transit. Understanding Incoterms is essential for buyers to avoid unexpected costs and ensure smooth logistics. -
Lead Time
Lead time refers to the duration from the placement of an order to its delivery. It is a critical factor in supply chain management. Buyers should discuss lead times with manufacturers to align production schedules and inventory needs, ensuring timely delivery of forged components.
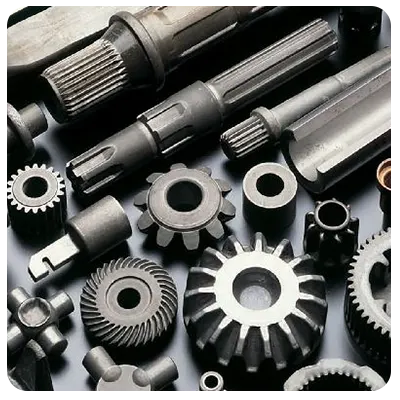
A stock image related to forging manufacturer.
By grasping these essential technical properties and trade terms, international B2B buyers can make informed decisions, ensuring they procure high-quality forged products that meet their specific requirements while effectively navigating the complexities of the forging industry.
Navigating Market Dynamics and Sourcing Trends in the forging manufacturer Sector
What Are the Key Market Dynamics and Trends Affecting the Forging Manufacturer Sector?
The forging manufacturing sector is experiencing significant shifts driven by global economic conditions and technological advancements. Key trends include the increasing adoption of Industry 4.0 technologies, which integrate IoT, AI, and automation into manufacturing processes. This transition allows for improved efficiency and reduced production costs, making it an attractive option for B2B buyers. Additionally, the demand for high-performance materials continues to rise, particularly in industries such as automotive, aerospace, and energy, where durability and precision are paramount.
Emerging markets in Africa and South America are becoming crucial players in the global forging landscape. These regions are witnessing a surge in local manufacturing capabilities, driven by government initiatives aimed at enhancing local production and reducing dependency on imports. For international buyers, this opens opportunities to source competitively priced products while supporting local economies.
Furthermore, geopolitical factors, such as trade agreements and tariffs, are influencing sourcing strategies. Buyers must remain agile and informed about these changes to navigate potential risks effectively. The adoption of digital procurement platforms is another trend, streamlining the sourcing process and enhancing transparency in supplier relationships.
How Is Sustainability Shaping Sourcing Trends in Forging Manufacturing?
Sustainability is becoming a pivotal consideration for B2B buyers in the forging sector. The environmental impact of manufacturing processes, particularly concerning energy consumption and waste generation, is under increased scrutiny. Buyers are encouraged to evaluate the sustainability practices of their suppliers, focusing on those that implement eco-friendly techniques and materials.
Ethical sourcing is equally important, with a growing emphasis on supply chain transparency. Many companies are adopting ‘green’ certifications, such as ISO 14001, to demonstrate their commitment to environmental management. Buyers should seek suppliers who prioritize sustainable practices, including the use of recycled materials and energy-efficient production methods.
The trend toward sustainability is not merely regulatory; it is also driven by consumer demand for responsible products. Companies that align their sourcing strategies with sustainability goals can enhance their brand reputation and appeal to a broader market segment. In this context, B2B buyers are encouraged to engage with suppliers who showcase a clear commitment to ethical sourcing and environmental stewardship.
What Is the Historical Context of Forging Manufacturing and Its Relevance Today?
The forging manufacturing sector has a rich history that dates back thousands of years, evolving from traditional blacksmithing to modern industrial processes. Initially, forging was a manual craft, but the advent of steam and later electrical power revolutionized production capabilities, allowing for mass manufacturing of forged components.
In the contemporary landscape, the sector has embraced advanced technologies, such as computer-aided design (CAD) and precision forging techniques, which enhance quality and consistency. This evolution is significant for B2B buyers, as it highlights the importance of selecting suppliers who leverage modern methods to ensure superior product performance. Understanding this historical context can provide insight into the reliability and innovation potential of suppliers in today’s competitive market.
By aligning sourcing strategies with these insights, international B2B buyers can make informed decisions that not only fulfill their operational needs but also support broader economic and environmental goals.
Frequently Asked Questions (FAQs) for B2B Buyers of forging manufacturer
-
How do I ensure the quality of products from a forging manufacturer?
To ensure product quality from a forging manufacturer, start by requesting samples of previous work to evaluate their craftsmanship and material quality. It’s essential to verify the manufacturer’s certifications, such as ISO 9001, which indicates adherence to quality management standards. Additionally, consider conducting on-site visits to inspect production processes and facilities. Establishing clear quality assurance protocols in your contract, including third-party inspections, can further safeguard against defects. -
What are the key factors to consider when selecting a forging manufacturer?
When selecting a forging manufacturer, evaluate their industry experience, technical capabilities, and production capacity. Assess the range of materials they work with and their ability to handle specific requirements, such as custom designs or high-volume orders. Customer reviews and case studies can provide insights into their reliability and service quality. Lastly, consider their location and logistics capabilities, especially if you are sourcing from regions like Africa or South America, where transport can be challenging.
-
How can I negotiate favorable payment terms with a forging manufacturer?
Negotiating favorable payment terms involves clear communication of your financial expectations and flexibility. Consider proposing payment structures such as a deposit upfront, followed by milestone payments based on production stages. This approach mitigates risk for both parties. Additionally, offering to pay in bulk for large orders can sometimes yield discounts. Be sure to document all agreements in your contract to avoid misunderstandings. -
What is the minimum order quantity (MOQ) for forging products?
Minimum order quantities (MOQ) can vary significantly between manufacturers, typically ranging from a few dozen to several hundred units. Factors influencing MOQ include the complexity of the forging process, material costs, and the manufacturer’s production capacity. When negotiating, express your needs clearly and see if the manufacturer can accommodate smaller orders, particularly if you are testing a new product line or entering a new market. -
How do I evaluate the customization options available with a forging manufacturer?
To evaluate customization options, discuss your specific requirements with potential manufacturers, including dimensions, material grades, and surface finishes. Request detailed documentation on their capabilities, including examples of past customized projects. It’s beneficial to inquire about their design and engineering support, as some manufacturers may offer services to help refine your specifications. Ensure that they have the necessary equipment and expertise to handle your customization needs effectively. -
What logistics considerations should I keep in mind when sourcing from international forging manufacturers?
When sourcing from international forging manufacturers, logistics considerations include shipping times, costs, and compliance with import/export regulations. Evaluate the manufacturer’s proximity to shipping ports and their history of managing logistics efficiently. Also, consider the potential for delays at customs and ensure you have a clear understanding of tariffs and duties that may apply. Collaborating with a logistics provider familiar with your target region can streamline the process. -
How can I assess the reliability of a forging manufacturer before placing an order?
To assess the reliability of a forging manufacturer, start by conducting thorough research, including reviewing their business history, customer testimonials, and case studies. Request references from past clients and contact them to gauge satisfaction levels. An on-site visit can also provide valuable insights into their operations and workforce. Additionally, consider their financial stability, which can be indicative of their ability to fulfill your order without disruptions. -
What are common quality assurance practices in the forging industry?
Common quality assurance practices in the forging industry include conducting regular inspections throughout the production process, from raw material sourcing to final product testing. Manufacturers often implement statistical process control (SPC) techniques to monitor production metrics and identify deviations. Certifications such as ISO 9001 or AS9100 are indicators of a robust quality management system. Engaging third-party inspectors for independent assessments can also enhance the credibility of the quality assurance measures in place.
Important Disclaimer & Terms of Use
⚠️ Important Disclaimer
The information provided in this guide, including content regarding manufacturers, technical specifications, and market analysis, is for informational and educational purposes only. It does not constitute professional procurement advice, financial advice, or legal advice.
While we have made every effort to ensure the accuracy and timeliness of the information, we are not responsible for any errors, omissions, or outdated information. Market conditions, company details, and technical standards are subject to change.
B2B buyers must conduct their own independent and thorough due diligence before making any purchasing decisions. This includes contacting suppliers directly, verifying certifications, requesting samples, and seeking professional consultation. The risk of relying on any information in this guide is borne solely by the reader.
Strategic Sourcing Conclusion and Outlook for forging manufacturer
What Are the Key Takeaways for International B2B Buyers in Forging Manufacturing?
In conclusion, strategic sourcing in the forging industry is crucial for international B2B buyers, particularly those operating in Africa, South America, the Middle East, and Europe. By prioritizing quality, supplier reliability, and cost-effectiveness, buyers can significantly enhance their supply chain efficiency. Establishing strong partnerships with reputable forging manufacturers not only mitigates risks but also opens doors to innovation and tailored solutions that meet specific industry needs.
How Can Strategic Sourcing Impact Your Business Success?
The value of strategic sourcing transcends mere cost savings; it fosters long-term relationships that can lead to competitive advantages in the marketplace. By leveraging local suppliers in emerging markets, businesses can also benefit from reduced lead times and improved responsiveness to market demands. Engaging in a comprehensive evaluation of potential partners will ensure alignment with your operational goals and ethical standards.
What’s Next for International B2B Buyers in Forging?
As the forging industry continues to evolve, buyers should remain proactive in adapting to technological advancements and changing market dynamics. Investing in supplier development and engaging in sustainable practices will not only enhance operational resilience but also contribute to a more responsible supply chain. Explore new partnerships and stay informed about industry trends to ensure your business remains at the forefront of innovation. Embrace this opportunity to elevate your sourcing strategy and drive your business success forward.