Discover Top Strategies to Choose a Harnes Manufacturer (2025)
Introduction: Navigating the Global Market for harnes manufacturer
In the increasingly interconnected global marketplace, sourcing high-quality harnesses is a critical challenge for international B2B buyers. Whether you are looking for harnesses for automotive, industrial, or consumer applications, understanding the nuances of different manufacturers can significantly impact your supply chain efficiency and product reliability. This comprehensive guide delves into the multifaceted world of harness manufacturers, exploring various types, applications, and the importance of supplier vetting.
Our aim is to equip B2B buyers from Africa, South America, the Middle East, and Europe—including key markets like Turkey and Germany—with actionable insights that facilitate informed purchasing decisions. From identifying the best materials and designs to understanding cost structures and compliance with international standards, this guide covers everything you need to know.
We will also discuss essential strategies for evaluating potential suppliers, ensuring that you choose partners who not only meet your quality requirements but also align with your business values. By addressing these critical aspects, this guide serves as your roadmap to navigating the global market for harness manufacturers, empowering you to make strategic decisions that enhance your business operations.
Understanding harnes manufacturer Types and Variations
Type Name | Key Distinguishing Features | Primary B2B Applications | Brief Pros & Cons for Buyers |
---|---|---|---|
Custom Harness Manufacturers | Tailored designs based on specific client needs | Aerospace, automotive, medical devices | Pros: Perfect fit for unique applications; Cons: Higher costs and longer lead times. |
Mass Production Harness Manufacturers | High-volume production with standardized designs | Consumer electronics, appliances | Pros: Cost-effective for large orders; Cons: Limited customization options. |
Specialty Harness Manufacturers | Focus on niche markets with specialized products | Military, industrial machinery | Pros: Expertise in specific applications; Cons: Potentially higher prices due to specialization. |
Wire Harness Assemblers | Assemble components into complete harnesses | Automotive, telecommunications | Pros: Streamlined assembly process; Cons: May require additional sourcing for components. |
Eco-friendly Harness Manufacturers | Use sustainable materials and processes | Renewable energy, eco-conscious brands | Pros: Aligns with sustainability goals; Cons: May have higher upfront costs. |
What are the characteristics of Custom Harness Manufacturers?
Custom harness manufacturers specialize in creating tailored solutions that meet specific client requirements. These manufacturers work closely with businesses to design harnesses that fit unique applications, particularly in industries such as aerospace, automotive, and medical devices. While these harnesses offer the advantage of a perfect fit, buyers should be prepared for potentially higher costs and longer lead times compared to off-the-shelf options. When purchasing, consider the importance of precise specifications and the potential for increased overall project efficiency.
How do Mass Production Harness Manufacturers operate?
Mass production harness manufacturers focus on high-volume production with standardized designs. This model is particularly beneficial for sectors such as consumer electronics and appliances, where economies of scale can significantly reduce costs. The primary advantage of this approach is the cost-effectiveness for large orders; however, buyers must be aware of the limitations in customization. When selecting a supplier, it is crucial to evaluate the balance between cost savings and the need for specific design features.
What makes Specialty Harness Manufacturers unique?
Specialty harness manufacturers cater to niche markets, providing products that are often highly specialized. Industries such as military and industrial machinery benefit from the expertise these manufacturers offer. Buyers can expect a higher level of customization and innovation, but this often comes at a premium price. When considering a specialty manufacturer, businesses should assess the importance of specialized knowledge and product performance against their budget constraints.
What is the role of Wire Harness Assemblers in the supply chain?
Wire harness assemblers play a crucial role in the assembly of components into complete harnesses, serving industries like automotive and telecommunications. They streamline the assembly process, which can lead to faster production times. However, buyers should note that assemblers may require additional sourcing for specific components, which could impact lead times. When engaging with wire harness assemblers, it is essential to ensure that all components meet the necessary quality standards to avoid downstream issues.
How do Eco-friendly Harness Manufacturers contribute to sustainability?
Eco-friendly harness manufacturers focus on using sustainable materials and processes, appealing to businesses that prioritize environmental responsibility. This approach is increasingly relevant in sectors like renewable energy and among eco-conscious brands. While these harnesses may align with sustainability goals, they often come with higher upfront costs. Buyers should weigh the long-term benefits of sustainability against initial investment, considering how eco-friendly practices can enhance brand reputation and customer loyalty.
Related Video: Heat Pump Thermostat O, B, and C Terminal Variations Explained
Key Industrial Applications of harnes manufacturer
Industry/Sector | Specific Application of harnes manufacturer | Value/Benefit for the Business | Key Sourcing Considerations for this Application |
---|---|---|---|
Automotive | Wiring harnesses for electric vehicles | Enhances vehicle performance and safety | Compliance with international safety standards, customization options |
Aerospace | Electrical harnesses for aircraft systems | Ensures reliability and performance in critical operations | Lightweight materials, resistance to extreme conditions |
Industrial Machinery | Custom harnesses for automation equipment | Improves efficiency and reduces downtime | Durability, compatibility with existing systems |
Telecommunications | Harnesses for network infrastructure | Supports high-speed data transfer and connectivity | Scalability, adaptability to new technologies |
Renewable Energy | Harnesses for solar and wind energy systems | Maximizes energy efficiency and system reliability | Environmental compliance, long-term durability |
How Are Wiring Harnesses Used in the Automotive Industry?
In the automotive sector, wiring harnesses are critical for electric vehicles (EVs) as they connect various electrical components, such as batteries, motors, and control units. These harnesses streamline the electrical architecture, enhancing performance and safety. For international buyers, especially from regions like Africa and South America, sourcing harnesses requires a keen understanding of local regulations, as well as the ability to customize solutions for specific vehicle models. Ensuring compliance with international safety standards is also paramount, as it affects both marketability and user safety.
What Role Do Electrical Harnesses Play in Aerospace Applications?
Electrical harnesses in aerospace are used to connect vital systems, including avionics, power distribution, and flight control systems. Given the critical nature of these applications, the harnesses must meet stringent reliability and performance standards. Buyers from Europe and the Middle East should focus on suppliers who offer lightweight materials and robust designs capable of withstanding extreme environmental conditions. Additionally, certifications and compliance with aviation regulations are essential considerations for sourcing.
How Are Custom Harnesses Beneficial for Industrial Machinery?
In the realm of industrial machinery, custom harnesses are designed to facilitate automation processes by connecting sensors, actuators, and control systems. This integration leads to improved operational efficiency and reduced downtime. Buyers in Africa and South America should prioritize sourcing harnesses that are durable and compatible with existing systems to avoid costly modifications. Understanding the specific requirements of machinery and the operational environment is crucial for selecting the right harness manufacturer.
Why Are Telecommunications Harnesses Important for Network Infrastructure?
In telecommunications, harnesses are integral to the infrastructure that supports high-speed data transfer and connectivity. They are used to connect various network components, ensuring efficient signal transmission. For international buyers, especially in developing regions, sourcing harnesses that offer scalability and adaptability to new technologies can greatly enhance network performance. It’s also important to consider the supplier’s ability to provide ongoing support and upgrades as technology evolves.
How Do Harnesses Support Renewable Energy Systems?
Harnesses are essential in renewable energy applications, particularly for solar and wind systems, where they connect solar panels, inverters, and battery storage units. These harnesses maximize energy efficiency and ensure the reliability of energy systems. Buyers should look for manufacturers that comply with environmental standards and offer long-term durability to withstand outdoor conditions. This is especially relevant for buyers from regions with varying climates, such as the Middle East and Europe, where harnesses must perform consistently over time.
3 Common User Pain Points for ‘harnes manufacturer’ & Their Solutions
Scenario 1: Inconsistent Quality Across Suppliers
The Problem:
B2B buyers often face challenges with inconsistent quality when sourcing harnesses from different manufacturers. This inconsistency can lead to product failures, increased returns, and ultimately, damage to a company’s reputation. Buyers may find that while one batch meets specifications, subsequent orders may not, resulting in operational disruptions and costly delays. This variability can be especially problematic for companies in sectors such as automotive or aerospace, where safety and reliability are paramount.
The Solution:
To mitigate this issue, buyers should adopt a stringent supplier evaluation process that includes quality assurance protocols. Begin by requesting detailed quality certifications, such as ISO 9001, from potential manufacturers. Establishing a quality agreement that outlines specific tolerances and testing requirements can also help ensure consistent quality. Additionally, consider implementing a pilot program where you order small batches initially to evaluate quality before committing to larger orders. Regular audits and performance reviews of the manufacturer can further ensure that they adhere to the agreed-upon quality standards.
Scenario 2: Complex Customization Needs
The Problem:
Many B2B buyers require customized harness solutions tailored to their unique applications, which can be a significant pain point. Manufacturers may lack the capability or flexibility to accommodate specific design changes, leading to misaligned expectations and project delays. This is particularly challenging for industries such as medical devices and specialized machinery, where the harness must integrate seamlessly with other components.
The Solution:
To address customization challenges, buyers should engage in early and open communication with potential manufacturers. Provide detailed specifications and use visual aids like CAD drawings to convey your requirements accurately. It’s also beneficial to discuss the manufacturer’s design capabilities upfront to assess their flexibility in accommodating changes. Establishing a collaborative relationship with the manufacturer can facilitate iterative design processes, allowing for adjustments based on prototypes and feedback. Lastly, consider manufacturers with in-house engineering teams, as they can often provide valuable insights and faster turnaround times for custom projects.
Scenario 3: Navigating Import Regulations and Compliance
The Problem:
For international B2B buyers, particularly those in regions like Africa and South America, navigating import regulations and compliance can be a daunting task. Different countries have varying standards for materials and manufacturing processes, which can complicate sourcing decisions. Non-compliance can lead to delays, fines, or even confiscation of products at customs, creating significant financial risks.
The Solution:
To effectively manage import regulations, buyers should conduct thorough research on the compliance requirements of their target markets. This includes understanding the specific certifications required for harnesses in your industry. Engage with local legal or compliance experts who can provide guidance on navigating these regulations. Additionally, partnering with manufacturers who have experience exporting to your region can be advantageous, as they will likely be familiar with the necessary documentation and standards. Establishing a clear communication channel with your manufacturer regarding compliance can ensure that all products meet the required standards before they are shipped, minimizing the risk of delays at customs.
Strategic Material Selection Guide for harnes manufacturer
What Are the Key Materials for Harnes Manufacturing?
When selecting materials for harness manufacturing, international B2B buyers must consider various factors, including performance characteristics, cost, and compliance with regional standards. Below are analyses of four common materials used in harness production, focusing on their properties, advantages, disadvantages, and specific considerations for buyers from Africa, South America, the Middle East, and Europe.
How Does Nylon Perform in Harness Manufacturing?
Nylon is a popular choice for harness manufacturing due to its high strength-to-weight ratio and excellent abrasion resistance. It can withstand temperatures ranging from -40°C to 120°C, making it suitable for various environments. However, nylon is susceptible to UV degradation and moisture absorption, which can affect its longevity and performance in outdoor applications.
Pros: Nylon is lightweight, durable, and cost-effective, making it ideal for applications requiring flexibility and strength. Its ease of manufacturing also allows for complex designs.
Cons: The material’s susceptibility to environmental factors can limit its use in harsh conditions. Additionally, while it is relatively inexpensive, the need for protective coatings can increase overall costs.
Impact on Application: Nylon harnesses are suitable for general-purpose applications but may not be ideal for environments with high UV exposure or moisture.
Considerations for International Buyers: Buyers should ensure compliance with ASTM standards, particularly for applications in industries like automotive and aerospace. In Europe, adherence to EN standards is also crucial.
What Are the Advantages of Polyester in Harnesses?
Polyester is another widely used material in harness manufacturing, known for its excellent resistance to UV light, moisture, and chemicals. It maintains its strength and flexibility over a broad temperature range, typically from -40°C to 130°C.
Pros: Polyester is highly durable and resistant to various environmental factors, making it suitable for outdoor applications. It also exhibits low moisture absorption, which helps maintain its integrity.
Cons: While polyester is generally more expensive than nylon, its longevity can justify the cost. However, it may have a lower tensile strength compared to nylon in certain applications.
Impact on Application: Polyester harnesses are particularly effective in applications exposed to sunlight or moisture, such as marine and agricultural settings.
Considerations for International Buyers: Compliance with JIS standards is important for buyers in Japan, while European buyers should look for compliance with EN standards to ensure quality and safety.
Why Is Steel a Preferred Material for Harness Components?
Steel is commonly utilized for hardware components in harnesses, such as buckles and connectors, due to its exceptional strength and durability. It can withstand high temperatures and pressures, making it suitable for heavy-duty applications.
Pros: Steel offers unmatched strength and resistance to deformation, making it ideal for high-load applications. Its cost-effectiveness in bulk manufacturing is also a significant advantage.
Cons: The primary drawback of steel is its susceptibility to corrosion, which can be mitigated through coatings or galvanization. Additionally, its weight can be a concern in applications where minimizing weight is critical.
Impact on Application: Steel harness components are widely used in automotive and industrial applications where strength and reliability are paramount.
Considerations for International Buyers: Buyers should ensure that steel components meet ASTM or DIN standards, particularly in Europe and the Middle East, where safety regulations are stringent.
How Do Composite Materials Enhance Harness Performance?
Composite materials, such as carbon fiber or fiberglass, are increasingly being used in harness manufacturing for their high strength-to-weight ratio and resistance to environmental stressors. These materials can withstand extreme temperatures and are often designed to be non-corrosive.
Pros: Composites offer superior strength while being lightweight, making them ideal for applications where weight savings are critical, such as aerospace and high-performance automotive sectors.
Cons: The manufacturing process for composites can be complex and costly, which may limit their use in budget-sensitive applications. Additionally, they may require specialized knowledge for proper handling and installation.
Impact on Application: Composite harnesses excel in high-performance environments, providing excellent durability without adding significant weight.
Considerations for International Buyers: Buyers should verify compliance with industry-specific standards, such as those set by ASTM or ISO, to ensure quality and performance.
Summary Table of Material Selection
Material | Typical Use Case for harnes manufacturer | Key Advantage | Key Disadvantage/Limitation | Relative Cost (Low/Med/High) |
---|---|---|---|---|
Nylon | General-purpose harnesses | Lightweight and durable | UV degradation susceptibility | Low |
Polyester | Outdoor harnesses | UV and moisture resistant | Higher cost than nylon | Med |
Steel | Hardware components | Exceptional strength | Corrosion susceptibility | Low |
Composite | High-performance applications | High strength-to-weight ratio | Complex and costly manufacturing | High |
This guide provides a foundational understanding of material selection for harness manufacturing, emphasizing the importance of aligning material properties with application requirements and regional compliance standards.
In-depth Look: Manufacturing Processes and Quality Assurance for harnes manufacturer
What Are the Main Stages of Manufacturing for Harness Manufacturers?
The manufacturing process for harnesses involves several critical stages, each designed to ensure that the final product meets the required specifications and quality standards. Understanding these stages will help international B2B buyers make informed decisions when selecting suppliers.
1. Material Preparation
The first stage of harness manufacturing begins with material preparation. This includes sourcing high-quality materials such as wires, connectors, and insulating materials. Buyers should inquire about the supplier’s sourcing practices, particularly for materials that meet international standards. For instance, using RoHS-compliant materials ensures that products are free from hazardous substances, which is essential for markets in Europe and North America.
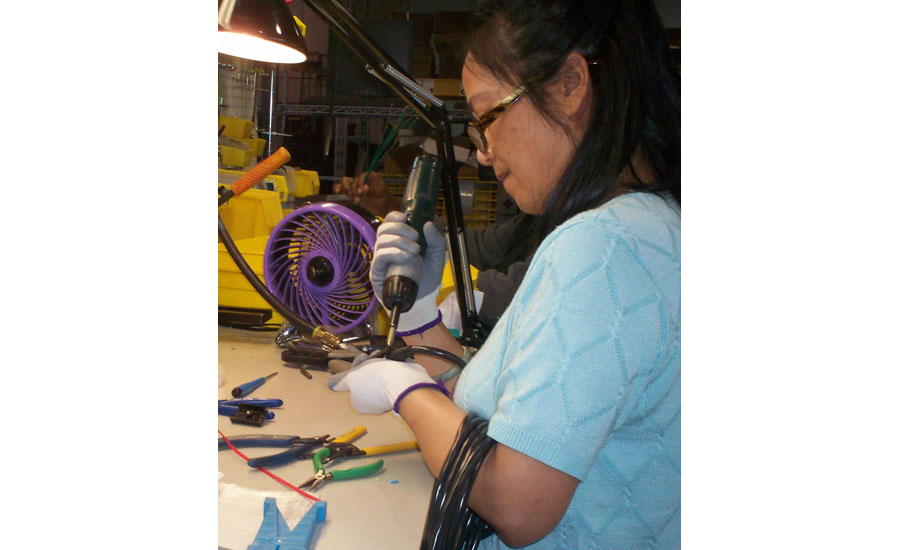
A stock image related to harnes manufacturer.
2. Forming
Once materials are prepared, the forming stage begins. This involves cutting, stripping, and crimping wires to create the necessary components of the harness. Key techniques used in this stage include automated wire cutting machines and precision crimping tools. Buyers should assess the supplier’s capabilities in terms of machinery and technology, as advanced equipment can enhance precision and reduce lead times.
3. Assembly
The assembly stage is where the components are put together to form the final harness. This process can be manual or automated, depending on the complexity and volume of the order. Techniques such as soldering and ultrasonic welding may be employed to ensure secure connections. B2B buyers should ask for information on the assembly methods used, as well as any relevant certifications for automated processes that guarantee consistency and quality.
4. Finishing
Finally, the finishing stage involves inspecting, testing, and packaging the harnesses. This may include applying protective coatings, labeling, and ensuring that all harnesses meet the required specifications. Buyers should ensure that their suppliers have robust finishing processes in place to maintain product integrity during shipping and handling.
How Is Quality Assurance Integrated Into the Manufacturing Process?
Quality assurance (QA) is a critical component of the harness manufacturing process. It ensures that products meet industry standards and customer specifications. International B2B buyers must understand the QA practices employed by their suppliers to mitigate risks associated with quality failures.
Relevant International Standards for Harness Manufacturers
Harness manufacturers should adhere to various international standards such as ISO 9001, which outlines the requirements for a quality management system. Other relevant standards may include CE marking for products sold in Europe and specific industry certifications such as API for oil and gas applications. B2B buyers should confirm that their suppliers are certified and compliant with these standards, as this can significantly affect product quality and market acceptance.
What Are the Key Quality Control Checkpoints?
Quality control (QC) is typically divided into several checkpoints throughout the manufacturing process. These include:
-
Incoming Quality Control (IQC): This checkpoint ensures that all incoming materials meet specified quality standards before production begins. Buyers can request documentation regarding the acceptance criteria and testing methods used for incoming materials.
-
In-Process Quality Control (IPQC): During the manufacturing process, IPQC monitors the production to identify and rectify defects early. B2B buyers should inquire about the frequency and methods of in-process inspections.
-
Final Quality Control (FQC): This final checkpoint occurs after assembly and finishing. It includes comprehensive testing to ensure that the harnesses meet all specifications. Buyers should ask for detailed reports on the FQC process, including any testing methods used, such as electrical testing, insulation resistance testing, and mechanical strength tests.
What Common Testing Methods Are Used in Harness Manufacturing?
Testing methods are essential to verify that the harnesses perform reliably under various conditions. Common methods include:
-
Electrical Testing: This includes checking for continuity, insulation resistance, and voltage drop to ensure that the harness functions correctly.
-
Mechanical Testing: Harnesses may undergo tests for tensile strength and flexibility to ensure they can withstand physical stress during use.
-
Environmental Testing: Some harnesses are tested under extreme conditions (e.g., temperature variations, humidity) to confirm their durability and reliability.
B2B buyers should request test reports from suppliers to ensure that the harnesses have passed all necessary testing protocols.
How Can B2B Buyers Verify Supplier Quality Control?
B2B buyers can take several steps to verify the quality control practices of potential suppliers:
-
Supplier Audits: Conducting regular audits can help buyers assess the supplier’s manufacturing processes and quality control systems. This includes reviewing documentation and observing production practices.
-
Quality Reports: Requesting detailed quality reports can provide insight into the supplier’s adherence to quality standards. These reports should include IQC, IPQC, and FQC data.
-
Third-Party Inspections: Engaging third-party inspection services can provide an unbiased assessment of the supplier’s quality assurance processes. This is particularly useful for international buyers who may not be able to visit the manufacturing facility.
What Are the Quality Control Nuances for International B2B Buyers?
International B2B buyers, especially those from Africa, South America, the Middle East, and Europe, should be aware of certain nuances in quality control when sourcing from harness manufacturers:
-
Cultural Differences: Understanding the cultural approach to quality and business practices in different regions can help buyers manage expectations and communication with suppliers.
-
Regulatory Compliance: Different regions may have varying regulations regarding product safety and environmental standards. Buyers should familiarize themselves with these regulations to ensure compliance.
-
Logistics and Supply Chain Management: Consider how quality assurance practices can be impacted by logistics. For example, temperature-sensitive materials may require special handling during shipping.
By comprehensively evaluating manufacturing processes and quality assurance practices, B2B buyers can make informed decisions, ensuring that they partner with reliable harness manufacturers that meet their quality standards and business needs.
Practical Sourcing Guide: A Step-by-Step Checklist for ‘harnes manufacturer’
Introduction
Sourcing a reliable harness manufacturer is a critical task for international B2B buyers, especially those in Africa, South America, the Middle East, and Europe. This checklist serves as a practical guide to help you navigate the complexities of procurement, ensuring you make informed decisions and establish successful partnerships.
Step 1: Define Your Technical Specifications
Before reaching out to potential manufacturers, it’s essential to clearly outline your technical requirements. This includes the type of harness needed, materials, dimensions, and any industry-specific standards.
– Why It Matters: Clear specifications help prevent misunderstandings and ensure that suppliers can meet your needs effectively.
– What to Look For: Document all necessary details and consider creating a technical data sheet to share with suppliers.
Step 2: Research Potential Suppliers
Conduct thorough research to identify potential harness manufacturers. Utilize online directories, industry trade shows, and local chambers of commerce to compile a list of candidates.
– Why It Matters: A well-researched list will provide you with a range of options, making it easier to find a supplier that fits your specific requirements.
– What to Look For: Focus on manufacturers with experience in your industry and positive customer reviews.
Step 3: Evaluate Supplier Certifications
Verify that potential suppliers hold relevant certifications such as ISO, CE, or industry-specific quality standards.
– Why It Matters: Certifications are a testament to a manufacturer’s commitment to quality and compliance with industry regulations.
– What to Look For: Request copies of certifications and check their validity with the issuing bodies.
Step 4: Request Samples and Prototypes
Once you have shortlisted potential suppliers, request samples or prototypes of their products.
– Why It Matters: This step allows you to assess the quality and craftsmanship of the harnesses before making a large commitment.
– What to Look For: Pay attention to material quality, stitching, and overall design, ensuring they align with your specifications.
Step 5: Analyze Pricing and Payment Terms
Obtain detailed quotes from each manufacturer and compare pricing structures, including any bulk discounts and payment terms.
– Why It Matters: Understanding the financial aspects helps you budget accurately and assess the overall value of the offer.
– What to Look For: Look for transparency in pricing and any hidden fees that may affect your total cost.
Step 6: Assess Production Capacity and Lead Times
Inquire about the manufacturer’s production capacity and expected lead times for your orders.
– Why It Matters: Knowing a supplier’s capacity ensures they can meet your demand without delays, particularly for urgent projects.
– What to Look For: Discuss potential rush orders and their ability to scale production if your needs increase.
Step 7: Establish Communication Protocols
Set clear communication protocols with your chosen supplier, including regular updates and points of contact.
– Why It Matters: Effective communication is vital for a smooth procurement process and helps mitigate misunderstandings.
– What to Look For: Ensure that the supplier is responsive and willing to provide regular updates on production status and any potential issues.
By following these steps, international B2B buyers can effectively navigate the sourcing process for harness manufacturers, ensuring they select a supplier that meets their specific needs while fostering a successful business relationship.
Comprehensive Cost and Pricing Analysis for harnes manufacturer Sourcing
What Are the Key Cost Components for Sourcing Harness Manufacturers?
When sourcing harness manufacturers, understanding the cost structure is crucial for making informed purchasing decisions. The primary cost components include:
-
Materials: The choice of materials significantly impacts costs. Common materials for harnesses include nylon, polyester, and metal components. Higher quality or specialized materials can increase costs but may offer better durability and performance.
-
Labor: Labor costs vary by region and manufacturing complexity. Countries with higher labor costs, like Germany, may produce more expensive harnesses, while regions in Africa and South America could offer lower labor costs, impacting overall pricing.
-
Manufacturing Overhead: This includes expenses related to factory operations, such as utilities and rent. Manufacturers with modern facilities may have higher overheads but can also provide better quality assurance and efficiency.
-
Tooling: Initial tooling costs can be significant, especially for custom harness designs. Buyers should inquire about these costs upfront, as they can affect the overall price, particularly for low-volume orders.
-
Quality Control (QC): Ensuring quality through rigorous QC processes can add to costs but is vital for compliance and reliability. Look for manufacturers that prioritize QC to minimize defects and returns.
-
Logistics: Transportation and shipping costs can vary widely depending on the supplier’s location and the Incoterms agreed upon. Understanding these logistics costs is essential for accurate budgeting.
-
Margin: Manufacturers typically include a profit margin in their pricing, which can vary based on market conditions and competitive positioning.
How Do Price Influencers Affect the Cost of Harness Manufacturing?
Several factors influence the pricing structure of harness manufacturing:
-
Volume/MOQ: Minimum order quantities (MOQ) can affect unit pricing. Higher volumes often lead to lower per-unit costs due to economies of scale, making it beneficial for buyers to consolidate orders.
-
Specifications and Customization: Custom designs and specifications can significantly increase costs. Clearly defining requirements upfront can help in getting accurate quotes and avoiding unexpected expenses.
-
Materials and Quality Certifications: The choice of materials and certifications (e.g., ISO, CE) can influence pricing. Manufacturers that offer certified materials may charge more but provide peace of mind regarding quality and compliance.
-
Supplier Factors: Supplier reputation, experience, and location can impact pricing. Established suppliers with a track record of reliability may charge a premium but could save costs in the long run through better quality and service.
-
Incoterms: The choice of Incoterms (e.g., FOB, CIF) plays a vital role in determining who bears shipping costs and risks, affecting the total landed cost of goods.
What Are Effective Buyer Tips for Negotiating Harness Manufacturing Prices?
For international B2B buyers, especially from Africa, South America, the Middle East, and Europe, here are some strategies to enhance negotiation outcomes:
-
Leverage Total Cost of Ownership (TCO): Instead of focusing solely on unit price, consider the TCO, including logistics, maintenance, and potential rework costs. This perspective can justify a higher upfront cost if it leads to better long-term value.
-
Negotiate Terms: Engage in discussions about payment terms, delivery schedules, and warranties. Favorable terms can improve cash flow and reduce risk.
-
Request Detailed Quotes: Ask suppliers for itemized quotes that break down costs. This transparency allows for better comparisons and highlights areas where negotiation is possible.
-
Build Relationships: Developing long-term relationships with suppliers can lead to better pricing and terms over time. Trust and reliability can often yield preferential treatment.
-
Be Aware of Pricing Nuances: Understand regional pricing differences and market conditions. For instance, European suppliers might have different pricing strategies than those in Africa or South America, impacting your negotiation approach.
Conclusion
Navigating the complexities of harness manufacturing costs requires diligence and an understanding of the various components and influencers involved. By leveraging the insights provided, international B2B buyers can make strategic sourcing decisions that align with their operational needs and budget constraints. Always remember that indicative prices can fluctuate based on market conditions, so continuous monitoring and communication with suppliers are essential.
Alternatives Analysis: Comparing harnes manufacturer With Other Solutions
Exploring Alternatives to Harnes Manufacturer Solutions
In the competitive landscape of manufacturing and production, international B2B buyers are often faced with numerous options when it comes to sourcing products or solutions. Understanding the alternatives to a specific solution, such as a harnes manufacturer, can help organizations make informed decisions that align with their operational needs and budget constraints. This analysis will compare the harnes manufacturer with two viable alternatives: custom harness assembly services and off-the-shelf wiring solutions.
Comparison Aspect | Harnes Manufacturer | Custom Harness Assembly Services | Off-the-Shelf Wiring Solutions |
---|---|---|---|
Performance | High quality, tailored solutions for specific needs | Customization allows for optimized performance | Standardized, reliable performance |
Cost | Typically higher due to custom manufacturing | Can be cost-effective for larger orders | Generally lower upfront costs |
Ease of Implementation | May require longer lead times for production | Moderate; depends on complexity of design | Easy; readily available in the market |
Maintenance | Support for maintenance and repairs | Varies based on service provider | Minimal maintenance, easily replaceable |
Best Use Case | Unique applications needing specialized designs | Projects requiring customization for specific requirements | General applications with standard requirements |
What Are the Advantages and Disadvantages of Custom Harness Assembly Services?
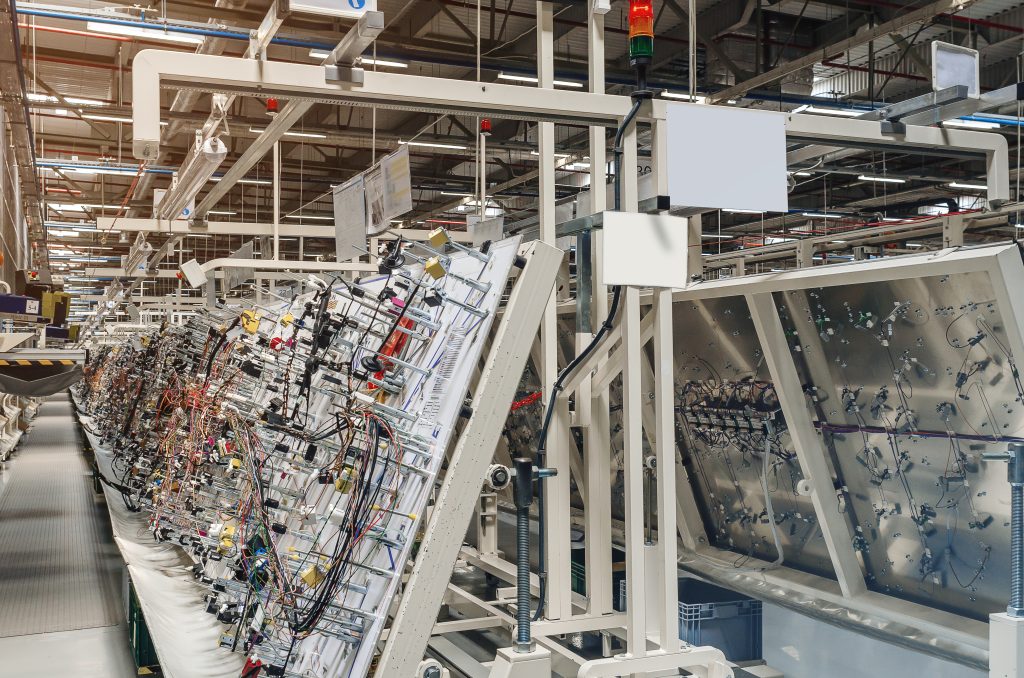
A stock image related to harnes manufacturer.
Custom harness assembly services cater to businesses that require unique wiring solutions tailored to specific applications. The primary advantage of this alternative is the ability to design and create harnesses that meet exact specifications, which can enhance performance in specialized environments. However, the downside is that this option may involve longer lead times and potentially higher costs for small batch orders. Companies in sectors like aerospace or automotive, where precision is critical, often benefit from custom solutions.
How Do Off-the-Shelf Wiring Solutions Compare?
Off-the-shelf wiring solutions provide standardized products that are ready for immediate use. These solutions are cost-effective, particularly for projects with limited budgets or timelines, making them an attractive option for businesses in various sectors. The ease of implementation is another significant advantage, as these products can be quickly sourced and installed. However, off-the-shelf solutions may not meet the unique requirements of specialized applications, which can lead to performance limitations in certain scenarios.
Conclusion: How Should B2B Buyers Choose the Right Solution?
When selecting between a harnes manufacturer and its alternatives, B2B buyers should carefully evaluate their specific needs, including performance requirements, budget constraints, and project timelines. If unique, high-performance solutions are necessary, investing in a harnes manufacturer may be justified despite higher costs. Conversely, for projects with standard requirements, custom harness assembly services or off-the-shelf wiring solutions may offer a more economical and timely approach. Ultimately, aligning the chosen solution with the operational goals will ensure optimal results and satisfaction in the long run.
Essential Technical Properties and Trade Terminology for harnes manufacturer
What Are the Essential Technical Properties for Harness Manufacturing?
Understanding the critical specifications of harness manufacturing is crucial for international B2B buyers. Here are some key technical properties to consider:
-
Material Grade
The choice of material affects durability, flexibility, and resistance to environmental factors. Common materials include PVC, nylon, and polypropylene. High-grade materials ensure the harness can withstand stress and last longer, which is vital for industries like automotive and aerospace. -
Tolerance Levels
Tolerance refers to the allowable deviation from a specified dimension. In harness manufacturing, tight tolerances are essential for ensuring that components fit together correctly and function as intended. For example, a tolerance of ±0.5mm may be necessary for connectors to ensure secure connections, which is critical in safety-sensitive applications. -
Load Capacity
Load capacity indicates the maximum weight the harness can safely support. It is particularly important in applications like lifting and safety equipment. Buyers should verify load ratings to ensure they meet industry standards and safety regulations, thereby minimizing risk in high-stakes environments. -
Temperature Resistance
Different applications may expose harnesses to extreme temperatures. Understanding the temperature range that materials can endure without degrading is essential for industries such as automotive and aerospace. This property helps in selecting the right harness for specific environmental conditions. -
Flame Retardancy
Flame-retardant materials are critical in applications where fire hazards exist. Buyers should inquire about certifications and test standards to ensure that the harness meets fire safety regulations, especially in sectors like aviation and transportation. -
Electrical Properties
In many applications, harnesses carry electrical signals. The electrical properties, such as insulation resistance and conductivity, are vital for preventing short circuits and ensuring efficient performance. It’s important for buyers to confirm these specifications to ensure compatibility with their systems.
Which Trade Terminology Should B2B Buyers Understand in Harness Manufacturing?
Familiarity with industry jargon can streamline communication and negotiations. Here are some common terms you should know:
-
OEM (Original Equipment Manufacturer)
This term refers to companies that produce parts or equipment that may be marketed by another manufacturer. For buyers, understanding OEM relationships can help in sourcing quality components that are compatible with existing products. -
MOQ (Minimum Order Quantity)
MOQ indicates the smallest number of units that a supplier is willing to sell. Knowing the MOQ is essential for budgeting and inventory management, particularly for businesses looking to maintain a steady supply without overcommitting. -
RFQ (Request for Quotation)
An RFQ is a document sent to suppliers to solicit price quotes for specific products or services. It helps buyers compare costs and make informed purchasing decisions. When issuing an RFQ, be clear about your specifications to receive accurate quotes. -
Incoterms (International Commercial Terms)
These are standardized trade terms that define the responsibilities of buyers and sellers regarding shipping, insurance, and tariffs. Familiarity with Incoterms can mitigate misunderstandings in international transactions, ensuring clarity on who bears costs and risks during transport. -
Lead Time
Lead time refers to the amount of time it takes from placing an order to receiving the product. Understanding lead times helps buyers plan their procurement processes and inventory management effectively, particularly in industries with tight project timelines. -
Certification Standards
Certifications like ISO, UL, or CE indicate compliance with international safety and quality standards. Buyers should prioritize suppliers with relevant certifications to ensure product reliability and safety, especially in regulated industries.
By grasping these technical properties and trade terminologies, B2B buyers can make informed decisions that align with their operational needs and industry standards.
Navigating Market Dynamics and Sourcing Trends in the harnes manufacturer Sector
What Are the Key Market Dynamics and Trends in the Harnes Manufacturer Sector?
The harnes manufacturing sector is witnessing significant transformations driven by global economic trends and technological advancements. Key factors influencing this market include the increasing demand for efficient and reliable harnesses across various industries, including automotive, aerospace, and renewable energy. B2B buyers from regions such as Africa, South America, the Middle East, and Europe (notably Turkey and Germany) should be aware of the following emerging trends:
-
Digital Transformation: The integration of Industry 4.0 technologies, including IoT and AI, is enhancing supply chain efficiency and product customization. Manufacturers are adopting smart manufacturing processes that allow for real-time monitoring and predictive maintenance, providing buyers with increased transparency and reliability.
-
Sourcing Strategies: As globalization continues to shape the market, international buyers are focusing on diversifying their supplier base. This trend mitigates risks associated with supply chain disruptions and ensures competitive pricing. Buyers should consider suppliers with robust logistics capabilities and flexibility to adapt to changing market demands.
-
Regional Growth: Emerging markets, particularly in Africa and South America, are experiencing rapid industrialization, leading to increased demand for harnesses. Buyers in these regions should explore local suppliers who understand the unique requirements of their markets while also considering partnerships with established manufacturers in Europe and the Middle East for high-quality products.
How Important Is Sustainability and Ethical Sourcing in the Harnes Manufacturing Industry?
Sustainability and ethical sourcing have become critical considerations for B2B buyers in the harnes manufacturing sector. The environmental impact of manufacturing processes and materials is under scrutiny as industries strive to meet regulatory requirements and consumer expectations for sustainable practices.
-
Environmental Impact: The production of harnesses can involve significant resource consumption and waste generation. Buyers should prioritize manufacturers that adopt eco-friendly practices, such as reducing energy usage and minimizing waste through efficient production techniques.
-
Ethical Supply Chains: The importance of ethical sourcing cannot be overstated. Buyers should assess potential suppliers based on their labor practices, material sourcing, and adherence to environmental regulations. Certifications such as ISO 14001 (Environmental Management) and other green certifications can serve as indicators of a manufacturer’s commitment to sustainability.
-
Green Materials: The shift towards sustainable materials is gaining momentum, with manufacturers exploring alternatives such as recycled plastics and bio-based materials. Buyers should inquire about the sourcing of materials and consider partnerships with manufacturers who prioritize sustainable practices to meet their own corporate responsibility goals.
How Has the Harnes Manufacturing Sector Evolved Over Time?
The harnes manufacturing sector has evolved significantly over the past few decades, adapting to technological advancements and changing market demands. Initially focused on traditional manufacturing methods, the industry has embraced automation and digitalization to enhance efficiency and product quality.
The introduction of advanced materials and manufacturing techniques, such as 3D printing, has enabled manufacturers to create more complex and lightweight harness designs. This evolution is particularly relevant for sectors like aerospace and automotive, where weight reduction is critical for performance and fuel efficiency.
Furthermore, the increased focus on sustainability has reshaped the industry’s landscape, encouraging manufacturers to adopt more responsible practices and materials. As the market continues to evolve, international B2B buyers must stay informed about these trends to make strategic sourcing decisions that align with their business objectives.
Frequently Asked Questions (FAQs) for B2B Buyers of harnes manufacturer
-
How do I select the right harnes manufacturer for my needs?
Selecting the right harnes manufacturer involves evaluating several factors. Start by assessing their industry experience and expertise in producing the specific type of harnes you require, whether for automotive, aerospace, or industrial applications. Request samples to evaluate quality and craftsmanship. Additionally, check customer reviews and case studies to gauge reliability. It’s crucial to ensure they comply with international quality standards, such as ISO certifications, especially if you are importing to regions like Africa or South America where compliance may vary. -
What are the minimum order quantities (MOQ) for harnes manufacturers?
Minimum order quantities (MOQ) can vary significantly among harnes manufacturers. Typically, MOQs range from 100 to 1,000 units, depending on the manufacturer’s production capabilities and the complexity of the harnes design. Some manufacturers may offer lower MOQs for prototype or custom orders, while others might require higher quantities for cost-effectiveness. Always discuss your specific needs upfront, as some manufacturers might be flexible in accommodating smaller orders, especially for international buyers looking to test the market. -
What customization options are available when sourcing harnes?
Many harnes manufacturers provide extensive customization options, including materials, colors, sizes, and design specifications. You can often request unique features such as special connectors or insulation types tailored to your application. When discussing customization, provide detailed requirements and, if possible, prototypes or sketches to ensure clarity. Collaborating closely with the manufacturer during the design phase can help achieve a final product that meets your exact specifications and performance needs. -
What payment terms should I expect when dealing with harnes manufacturers?
Payment terms with harnes manufacturers can vary based on your relationship and order size. Common terms include a deposit (usually 30-50%) before production, with the balance due upon completion or before shipment. For first-time buyers, manufacturers may require full upfront payment. Additionally, discuss acceptable payment methods, such as wire transfers or letters of credit, especially when dealing with international transactions. Establishing clear payment terms upfront can help avoid misunderstandings later in the process. -
How can I ensure quality assurance when sourcing harnes?
To ensure quality assurance when sourcing harnes, begin by verifying the manufacturer’s quality control processes. Request documentation of their quality assurance certifications, such as ISO 9001. It’s beneficial to conduct factory visits or audits if possible, or utilize third-party inspection services to assess product quality before shipment. Additionally, establish clear specifications and testing criteria in your contract to ensure that the harnes meets your standards and performance requirements. -
What logistics considerations should I keep in mind when importing harnes?
When importing harnes, logistics play a crucial role in ensuring timely delivery. Consider the shipping method (air vs. sea freight) based on your budget and urgency. Be aware of customs regulations in your country and ensure all documentation is in order to prevent delays. It’s also important to factor in shipping costs, insurance, and potential tariffs or duties. Collaborating with a reliable freight forwarder can simplify the logistics process and provide guidance on best practices for international shipping. -
How do I vet potential harnes suppliers effectively?
Vetting potential harnes suppliers involves a thorough evaluation of their credentials, production capabilities, and reputation. Start by checking their business licenses, certifications, and industry experience. Request references from previous clients to gain insights into their reliability and customer service. Additionally, assess their manufacturing processes and quality control measures through site visits or audits. Engaging in direct communication can also help gauge their responsiveness and willingness to collaborate on your specific requirements. -
What are the common challenges faced when sourcing harnes internationally?
Common challenges when sourcing harnes internationally include language barriers, cultural differences, and varying quality standards. Additionally, navigating customs regulations and logistics can pose difficulties, leading to delays and unexpected costs. To mitigate these issues, establish clear communication channels and consider hiring local intermediaries or agents who understand the market. It’s also essential to conduct comprehensive due diligence on potential suppliers to ensure they align with your quality and compliance expectations.
Important Disclaimer & Terms of Use
⚠️ Important Disclaimer
The information provided in this guide, including content regarding manufacturers, technical specifications, and market analysis, is for informational and educational purposes only. It does not constitute professional procurement advice, financial advice, or legal advice.
While we have made every effort to ensure the accuracy and timeliness of the information, we are not responsible for any errors, omissions, or outdated information. Market conditions, company details, and technical standards are subject to change.
B2B buyers must conduct their own independent and thorough due diligence before making any purchasing decisions. This includes contacting suppliers directly, verifying certifications, requesting samples, and seeking professional consultation. The risk of relying on any information in this guide is borne solely by the reader.
Strategic Sourcing Conclusion and Outlook for harnes manufacturer
What Are the Key Takeaways for International B2B Buyers in Strategic Sourcing?
In conclusion, strategic sourcing is essential for harness manufacturers aiming to optimize their supply chains and enhance competitiveness in global markets. By prioritizing supplier relationships, conducting thorough market analysis, and leveraging technology, businesses can significantly reduce costs and improve product quality. International buyers, particularly from Africa, South America, the Middle East, and Europe, should focus on identifying reliable manufacturers that align with their operational needs and ethical standards.
How Can You Leverage Strategic Sourcing for Long-Term Success?
The future of harness manufacturing will increasingly rely on adaptability and innovation. Buyers are encouraged to remain proactive in monitoring market trends and shifts in consumer demand, ensuring their sourcing strategies are agile. As sustainability becomes a critical factor in procurement decisions, integrating eco-friendly practices into sourcing strategies will not only enhance brand reputation but also meet the growing demand for sustainable products.
What Should You Do Next to Enhance Your Sourcing Strategy?
For international B2B buyers, the call to action is clear: engage with manufacturers who demonstrate a commitment to quality, sustainability, and innovation. Building strategic partnerships can facilitate better negotiation terms, foster collaboration, and ultimately drive business growth. By taking these steps, you position your organization for success in the dynamic landscape of harness manufacturing.