Unlock Cost Savings: The Ultimate Hub Manufacturer Guide (2025)
Introduction: Navigating the Global Market for hub manufacturer
In today’s fast-paced global market, sourcing reliable hub manufacturers can be a daunting challenge for international B2B buyers. Whether you are in Kenya seeking high-quality automotive components or in Saudi Arabia looking for durable industrial hubs, the pressure to find trustworthy suppliers who meet your specific requirements is immense. This guide addresses the complexities of navigating the hub manufacturing landscape, providing insights that empower you to make informed purchasing decisions.
What Types of Hub Manufacturers Are Available Globally?
From automotive to aerospace and industrial applications, the types of hub manufacturers vary significantly across regions. This guide will delve into the distinctions between these manufacturers, highlighting the unique offerings from Africa, South America, the Middle East, and Europe. Understanding these differences is crucial for aligning your sourcing strategies with your business needs.
How Can You Vet Potential Hub Suppliers Effectively?
Supplier vetting is a critical component of the purchasing process, especially when engaging with manufacturers in diverse markets. This guide will outline best practices for evaluating potential partners, including assessing certifications, production capabilities, and customer reviews. These insights will help you mitigate risks and ensure quality in your supply chain.
What Are the Cost Factors in Sourcing Hubs?
Cost considerations are paramount when sourcing from different regions. This guide will break down the various factors that influence pricing, such as material quality, production volume, and shipping logistics. By understanding these elements, you can optimize your budget while securing the best value for your investment.
Armed with this comprehensive knowledge, you will be well-equipped to navigate the global hub manufacturing market, ensuring that your sourcing decisions are strategic, informed, and aligned with your business objectives.
Understanding hub manufacturer Types and Variations
Type Name | Key Distinguishing Features | Primary B2B Applications | Brief Pros & Cons for Buyers |
---|---|---|---|
Standard Hub Manufacturers | Mass production, standardized sizes and designs | Automotive, industrial machinery | Pros: Cost-effective, widely available. Cons: Limited customization options. |
Custom Hub Manufacturers | Tailored designs, bespoke specifications | Aerospace, specialized machinery | Pros: High customization, specific performance needs. Cons: Higher costs, longer lead times. |
Modular Hub Systems | Interchangeable parts, scalable designs | Telecommunications, renewable energy | Pros: Flexibility, easy upgrades. Cons: Complexity in assembly, potential compatibility issues. |
Integrated Hub Solutions | All-in-one packages, includes additional components | Smart manufacturing, IoT applications | Pros: Streamlined procurement, reduced installation time. Cons: May include unnecessary features, higher costs. |
Eco-Friendly Hub Makers | Focus on sustainable materials and processes | Green technology, eco-conscious industries | Pros: Positive brand image, compliance with regulations. Cons: Potentially higher prices, limited availability. |
What are the characteristics of Standard Hub Manufacturers?
Standard hub manufacturers focus on mass production, offering a range of standardized sizes and designs. These hubs are typically made from durable materials and are suitable for high-volume applications such as automotive and industrial machinery. For B2B buyers, the key considerations include cost-effectiveness and availability, as these hubs are widely produced and can be sourced easily. However, the trade-off is limited customization, which may not meet specific performance requirements for specialized applications.
How do Custom Hub Manufacturers meet specialized needs?
Custom hub manufacturers provide tailored designs that cater to specific client requirements. These manufacturers excel in creating bespoke specifications, making them ideal for sectors like aerospace and specialized machinery where precision is critical. B2B buyers should consider the high level of customization offered, as it allows for optimal performance in unique applications. However, the higher costs and longer lead times associated with custom hubs can be a drawback for companies with tight budgets and timelines.
What advantages do Modular Hub Systems offer for scalability?
Modular hub systems are designed with interchangeable parts, allowing for scalability and flexibility in applications such as telecommunications and renewable energy. These systems enable businesses to upgrade or modify their setups without complete overhauls, which can save time and resources. For B2B buyers, the primary considerations include the ease of assembly and potential compatibility issues with existing systems. While modular designs offer significant advantages, they can introduce complexity that requires skilled personnel for proper installation and maintenance.
What are Integrated Hub Solutions and their benefits?
Integrated hub solutions combine multiple components into a single package, streamlining the procurement process for B2B buyers. These solutions are particularly beneficial in smart manufacturing and IoT applications, where efficiency and reduced installation time are crucial. Buyers should weigh the advantages of simplified sourcing against the possibility of paying for features they may not need. While these solutions can enhance operational efficiency, it’s essential to ensure that they align with specific business requirements to avoid unnecessary costs.
Why choose Eco-Friendly Hub Makers for sustainability?
Eco-friendly hub manufacturers prioritize sustainable materials and processes, appealing to businesses in green technology and eco-conscious industries. B2B buyers are increasingly looking for suppliers that align with their sustainability goals, as this can enhance their brand image and ensure compliance with environmental regulations. However, potential drawbacks include higher prices and limited availability, which may deter some buyers. Ultimately, the choice to work with eco-friendly hub makers can be a strategic move for businesses looking to strengthen their market position through sustainability initiatives.
Related Video: Heat Pump Thermostat O, B, and C Terminal Variations Explained
Key Industrial Applications of hub manufacturer
Industry/Sector | Specific Application of hub manufacturer | Value/Benefit for the Business | Key Sourcing Considerations for this Application |
---|---|---|---|
Automotive | Wheel hub assemblies for vehicles | Enhanced safety and performance in vehicle dynamics | Compliance with international automotive standards |
Renewable Energy | Hub components for wind turbines | Increased efficiency and reliability in energy production | Material durability and resistance to environmental factors |
Aerospace | Hubs for aircraft landing gear | Improved safety and operational efficiency | Certification requirements and weight considerations |
Industrial Machinery | Hubs in conveyor systems | Streamlined operations and reduced downtime | Precision engineering and compatibility with existing systems |
Marine Engineering | Hubs for propeller systems | Enhanced propulsion efficiency and reduced fuel costs | Corrosion resistance and material certifications |
How is Hub Manufacturing Used in the Automotive Industry?
In the automotive sector, hub manufacturers produce essential components like wheel hub assemblies, which play a crucial role in vehicle dynamics. These hubs are vital for maintaining the alignment and stability of vehicles, directly impacting safety and performance. International buyers, particularly from regions like Africa and Europe, should ensure that their suppliers comply with stringent automotive standards to guarantee quality and reliability. Additionally, sourcing hubs that offer enhanced performance can lead to better fuel efficiency and lower maintenance costs over time.
What Role Do Hubs Play in Renewable Energy Applications?
In the renewable energy sector, particularly in wind energy, hubs are integral components of wind turbines. They connect the rotor blades to the turbine shaft, and their design significantly influences energy output and turbine efficiency. For international B2B buyers from South America and the Middle East, selecting a hub manufacturer that provides durable materials resistant to harsh weather conditions is essential. This consideration ensures long-term reliability and reduced maintenance, ultimately enhancing the return on investment in renewable energy projects.
How are Hubs Utilized in Aerospace Applications?
Aerospace applications require precision-engineered hubs for critical components like landing gear. These hubs must meet rigorous safety standards and are subject to strict certification processes. Buyers in regions like Europe and the Middle East should prioritize manufacturers that demonstrate compliance with international aerospace standards, ensuring that the hubs can withstand extreme operational conditions. The right hubs can improve aircraft performance and safety, which is paramount in the aviation industry.
Why are Hubs Important in Industrial Machinery?
In industrial machinery, hubs are often used in conveyor systems, where they facilitate the movement of goods and materials. Efficiently designed hubs can streamline operations, reduce downtime, and enhance overall productivity. Buyers from Africa and South America should focus on sourcing hubs that are engineered for precision and compatibility with existing machinery to avoid costly retrofitting. Selecting the right hub manufacturer can lead to significant operational improvements and cost savings.
What Considerations are There for Hubs in Marine Engineering?
In marine engineering, hubs are critical components of propeller systems, directly influencing the efficiency of vessels. These hubs must be made from materials that resist corrosion and wear due to constant exposure to water and salt. B2B buyers in the Middle East and Europe should prioritize suppliers that offer certified materials and designs that enhance propulsion efficiency. By selecting high-quality hubs, businesses can reduce fuel costs and improve the overall performance of marine vessels, making them a vital investment for any maritime operation.
Related Video: What are all the Laboratory Apparatus and their uses?
3 Common User Pain Points for ‘hub manufacturer’ & Their Solutions
Scenario 1: Navigating Complex Supply Chain Disruptions
The Problem:
B2B buyers in regions like Africa and the Middle East often face significant supply chain challenges when sourcing hubs from manufacturers. For instance, a Kenyan automotive manufacturer may experience delays in receiving critical components due to port congestion or logistical issues. These delays can halt production lines, leading to financial losses and missed market opportunities. The added pressure of ensuring compliance with local regulations and standards further complicates the procurement process.
The Solution:
To mitigate these supply chain disruptions, buyers should establish strong relationships with multiple suppliers, creating a diversified sourcing strategy. This means identifying hub manufacturers that not only meet quality standards but also have proven track records of reliability and flexibility. Additionally, leveraging technology to track shipments in real-time can provide valuable insights into delivery statuses. Consider implementing a just-in-time inventory strategy that aligns closely with production schedules, ensuring that materials arrive as needed without overstocking. Furthermore, engaging local logistics partners can enhance delivery efficiency, minimizing the impact of global supply chain issues.
Scenario 2: Ensuring Quality and Compliance with Local Standards
The Problem:
A common pain point for B2B buyers in South America and Europe is the challenge of ensuring that the hubs they procure meet both international quality standards and local regulatory requirements. For example, a Brazilian industrial buyer may find that a hub manufacturer’s products are certified to European standards but lack the necessary certifications for compliance with Brazilian safety regulations. This gap can lead to costly rework, legal issues, and damage to the company’s reputation.
The Solution:
To navigate these compliance challenges, B2B buyers should conduct thorough due diligence before finalizing any procurement agreement. This includes requesting detailed documentation of certifications and quality assurance processes from potential suppliers. It is also advisable to engage with third-party quality assurance firms that can verify compliance with local standards. Establishing clear communication with manufacturers about specific local requirements at the onset can prevent misunderstandings later. Additionally, buyers can participate in industry forums or trade groups to stay informed about regulatory changes, ensuring that they remain compliant as standards evolve.
Scenario 3: Overcoming Technical Support and After-Sales Service Gaps
The Problem:
In regions with emerging markets, such as parts of the Middle East and Africa, technical support and after-sales service can be inconsistent or lacking altogether. A Saudi Arabian manufacturing company may purchase hubs from a foreign manufacturer, only to find that the support for installation and maintenance is inadequate. This can lead to operational inefficiencies and increased downtime, severely affecting productivity.
The Solution:
To address potential gaps in technical support, buyers should prioritize manufacturers that offer comprehensive after-sales services, including installation assistance, maintenance training, and responsive customer service. Before making a purchase, it’s beneficial to inquire about the manufacturer’s support structure, including the availability of local technicians or service representatives. Additionally, establishing a service-level agreement (SLA) with the manufacturer can ensure that response times and support quality are clearly defined and upheld. Buyers should also consider investing in training programs for their staff to enhance their capabilities in managing and maintaining the hubs effectively. This proactive approach not only minimizes downtime but also empowers the workforce with the skills needed for optimal equipment utilization.
Strategic Material Selection Guide for hub manufacturer
When selecting materials for hub manufacturing, international B2B buyers must consider various factors, including performance properties, cost-effectiveness, and compliance with regional standards. Below, we analyze four common materials used in hub manufacturing, highlighting their key properties, advantages, disadvantages, and specific considerations for buyers from Africa, South America, the Middle East, and Europe.
What Are the Key Properties of Steel in Hub Manufacturing?
Steel is a widely used material in hub manufacturing due to its excellent strength and durability. It typically offers high temperature and pressure ratings, making it suitable for heavy-duty applications. Steel also has good corrosion resistance when treated with appropriate coatings or alloys, such as stainless steel.
Pros and Cons of Steel:
– Pros: High tensile strength, excellent durability, and good machinability. It is also relatively cost-effective compared to other high-performance materials.
– Cons: While corrosion-resistant options exist, untreated steel can rust in humid environments. Additionally, it may require more complex manufacturing processes, such as welding.
Impact on Application:
Steel hubs are ideal for applications involving heavy loads and high-stress environments, such as in automotive and industrial machinery.
Considerations for International Buyers:
Buyers should ensure compliance with standards like ASTM A36 or DIN 17100. In regions like Saudi Arabia, where humidity can be high, opting for galvanized or stainless steel may be beneficial.
How Does Aluminum Compare for Hub Manufacturing?
Aluminum is another popular choice for hub manufacturing, particularly in applications where weight reduction is critical. Its lightweight nature, combined with good corrosion resistance, makes it suitable for various applications, including automotive and aerospace.
Pros and Cons of Aluminum:
– Pros: Lightweight, excellent corrosion resistance, and good thermal conductivity. It is also easier to machine than steel.
– Cons: Lower strength compared to steel, which may limit its use in heavy-load applications. Additionally, aluminum can be more expensive.
Impact on Application:
Aluminum hubs are often used in lightweight applications, such as in electric vehicles or aerospace components, where reducing weight is essential for efficiency.
Considerations for International Buyers:
Buyers should be aware of standards such as ASTM B221 for aluminum extrusions. In Europe, compliance with EN 573 is also important. Buyers in regions like Kenya may need to consider local availability and cost variations.
What Are the Advantages of Composite Materials in Hub Manufacturing?
Composite materials, such as fiberglass and carbon fiber, are gaining traction in hub manufacturing due to their unique properties. These materials offer high strength-to-weight ratios and excellent corrosion resistance.
Pros and Cons of Composites:
– Pros: Lightweight, high strength, and resistance to corrosion and chemical exposure. They also allow for design flexibility.
– Cons: Generally higher manufacturing costs and complexity. They may also require specialized skills for machining and assembly.
Impact on Application:
Composite hubs are particularly suitable for high-performance applications, such as in motorsports or specialized industrial equipment.
Considerations for International Buyers:
International buyers should be aware of specific manufacturing standards and certifications for composites, which can vary significantly by region. In the Middle East, for instance, compliance with local regulations regarding materials used in construction is crucial.
How Does Cast Iron Perform in Hub Manufacturing?
Cast iron is a traditional material used in hub manufacturing, known for its excellent wear resistance and ability to dampen vibrations. It is particularly suitable for applications requiring stability and durability.
Pros and Cons of Cast Iron:
– Pros: High wear resistance, good machinability, and excellent vibration dampening properties.
– Cons: Heavier than steel or aluminum, which may not be suitable for all applications. It is also more brittle and can crack under extreme stress.
Impact on Application:
Cast iron hubs are often used in heavy machinery and industrial applications where durability is paramount.
Considerations for International Buyers:
Buyers should ensure compliance with standards such as ASTM A48 for gray iron. In regions like South America, where mining and heavy machinery are prevalent, cast iron may be a preferred choice.
Summary Table of Material Selection for Hub Manufacturing
Material | Typical Use Case for hub manufacturer | Key Advantage | Key Disadvantage/Limitation | Relative Cost (Low/Med/High) |
---|---|---|---|---|
Steel | Heavy-duty machinery and automotive | High tensile strength | Prone to rust without treatment | Medium |
Aluminum | Lightweight automotive and aerospace | Lightweight and corrosion-resistant | Lower strength than steel | High |
Composite | High-performance motorsports | High strength-to-weight ratio | Higher manufacturing complexity | High |
Cast Iron | Heavy machinery and industrial equipment | Excellent wear resistance | Heavier and more brittle | Medium |
This guide serves as a strategic resource for international B2B buyers, enabling them to make informed decisions on material selection tailored to their specific operational needs and regional compliance requirements.
In-depth Look: Manufacturing Processes and Quality Assurance for hub manufacturer
What Are the Main Stages of Manufacturing for Hub Manufacturers?
The manufacturing process for hubs typically involves several key stages: material preparation, forming, assembly, and finishing. Understanding these stages helps international B2B buyers assess the capabilities and quality of potential suppliers.
1. Material Preparation
The first step in hub manufacturing is the preparation of raw materials. Common materials include aluminum, steel, and composite materials. Buyers should inquire about the sourcing and quality of these materials, as the strength and durability of the finished product rely heavily on this initial step. Suppliers often conduct metallurgical tests to ensure that the materials meet specific mechanical properties before proceeding.
2. Forming Techniques
Forming techniques for hubs can include processes such as casting, forging, and machining. Each method has its own advantages and suitability depending on the hub’s application:
- Casting: Suitable for complex shapes, this technique involves pouring molten metal into a mold. It’s commonly used for producing large quantities of hubs.
- Forging: This method enhances the material’s strength through deformation. It’s ideal for high-stress applications.
- Machining: This involves removing material to achieve precise dimensions and tolerances. CNC (Computer Numerical Control) machining is prevalent for high-precision hubs.
Buyers should ensure that the chosen forming technique aligns with their product specifications and performance requirements.
3. Assembly Process
The assembly of hubs involves integrating various components, such as bearings, seals, and fasteners. This stage requires skilled labor and precise assembly techniques to ensure that each hub functions correctly. Buyers should look for manufacturers that implement standardized assembly procedures and use high-quality components. Automated assembly lines can also enhance consistency and reduce human error.
4. Finishing Touches
The finishing process may include surface treatments, such as anodizing, plating, or powder coating, which enhance corrosion resistance and aesthetic appeal. Buyers should request information on the types of finishing treatments used and their suitability for specific environments, especially for applications in diverse climates like those in Africa or the Middle East.
How Is Quality Assurance Implemented in Hub Manufacturing?
Quality assurance (QA) is crucial in hub manufacturing to ensure that products meet both international standards and customer expectations. Understanding the QA measures in place can help B2B buyers make informed decisions.
What International Standards Should B2B Buyers Be Aware Of?
Many hub manufacturers adhere to international quality standards such as ISO 9001, which establishes criteria for a quality management system. Compliance with these standards demonstrates a commitment to continuous improvement and customer satisfaction. Additionally, industry-specific certifications like CE (European Conformity) and API (American Petroleum Institute) certification may be relevant depending on the intended application of the hubs.
What Are the Key Quality Control Checkpoints?
Quality control (QC) checkpoints are integral to the manufacturing process. Key stages include:
- Incoming Quality Control (IQC): This involves inspecting raw materials upon receipt. Buyers should ensure suppliers have rigorous IQC procedures to prevent defects from the start.
- In-Process Quality Control (IPQC): Ongoing inspections during the manufacturing process help catch issues early. Automated systems can monitor parameters in real time, ensuring that any deviations are corrected promptly.
- Final Quality Control (FQC): This final inspection checks the finished product against specifications. It may include functional testing to ensure the hub operates as intended.
B2B buyers should inquire about the specific QC measures employed at each stage to gauge the reliability of the manufacturing process.
What Common Testing Methods Are Used for Hubs?
Various testing methods are employed to ensure the durability and performance of hubs. These include:
- Dimensional Testing: Ensures that the hub meets specified measurements and tolerances.
- Load Testing: Assesses the hub’s performance under simulated operational conditions.
- Non-Destructive Testing (NDT): Techniques like ultrasonic testing or magnetic particle inspection help identify internal flaws without damaging the product.
Buyers should ask for detailed testing reports to verify that the products meet required standards.
How Can B2B Buyers Verify Supplier Quality Control?
Verifying a supplier’s quality control measures is crucial for international buyers. Here are several strategies to ensure that suppliers maintain high-quality standards:
Conducting Supplier Audits
Regular audits of potential suppliers can provide insights into their manufacturing processes and quality management systems. Buyers should consider engaging third-party auditing firms to conduct these assessments, ensuring an unbiased evaluation.
Requesting Quality Reports
Suppliers should be able to provide documentation of their quality control processes, including test results, inspection reports, and certifications. Buyers should review these documents to understand the supplier’s commitment to quality.
Utilizing Third-Party Inspection Services
Engaging third-party inspection services can provide additional assurance of product quality before shipment. These services can perform inspections at various stages of production and verify compliance with international standards.
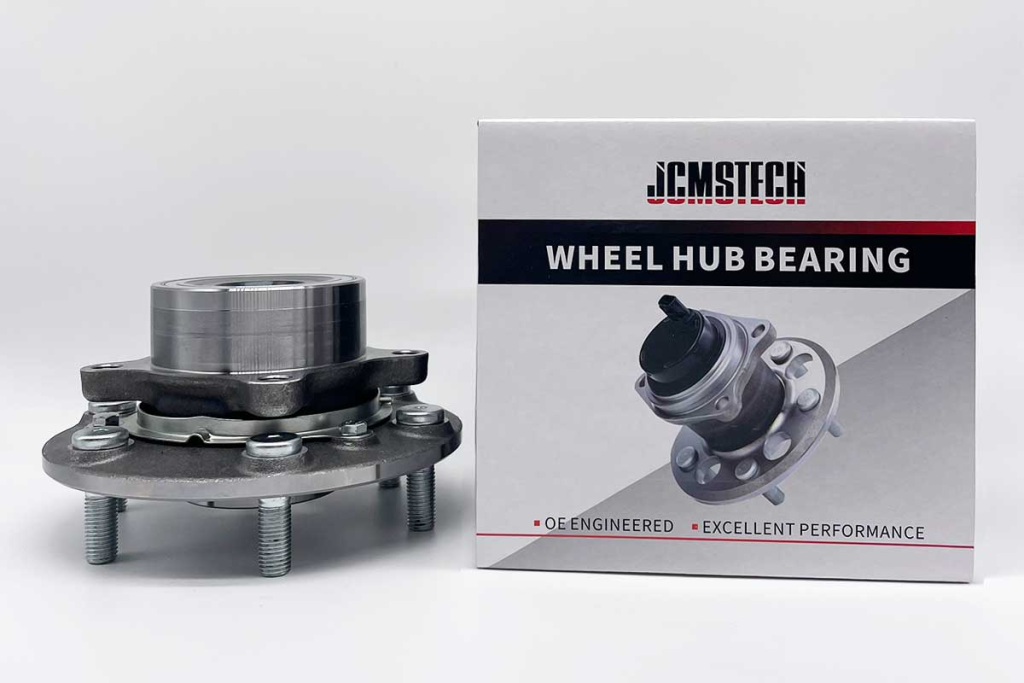
A stock image related to hub manufacturer.
What Are the QC and Certification Nuances for International B2B Buyers?
Navigating QC and certification nuances can be particularly complex for international B2B buyers. Factors to consider include:
- Regional Compliance: Different regions may have varying regulatory requirements. For example, CE marking is essential for products sold within the European Union.
- Cultural Differences: Understanding the local manufacturing culture can help buyers assess the reliability and transparency of suppliers. Establishing a strong communication channel can mitigate misunderstandings.
- Logistics and Supply Chain Considerations: Buyers should evaluate how a supplier’s QC processes affect lead times and delivery schedules, especially when importing products across continents.
By gaining a comprehensive understanding of the manufacturing processes and quality assurance measures employed by hub manufacturers, B2B buyers can make more informed sourcing decisions, ensuring that they partner with reliable suppliers who meet their quality expectations.
Practical Sourcing Guide: A Step-by-Step Checklist for ‘hub manufacturer’
In the dynamic world of international B2B procurement, sourcing from a hub manufacturer requires a structured approach to ensure you find the right partner. This checklist aims to guide buyers, especially from Africa, South America, the Middle East, and Europe, through the essential steps in procuring from a hub manufacturer. Each step is designed to minimize risks and maximize the potential for successful partnerships.
Step 1: Define Your Technical Specifications
Clearly articulating your technical specifications is the foundation of successful sourcing. This includes understanding the materials, dimensions, tolerances, and certifications required for your product. A well-defined specification not only aids in communicating your needs to potential suppliers but also helps in evaluating their capabilities accurately.
- Consider industry standards: Ensure your specifications align with relevant industry standards and regulations in your target market.
- Document everything: Create detailed documents that can be shared with potential suppliers to avoid misunderstandings.
Step 2: Research Potential Manufacturers
Conduct thorough research to identify potential hub manufacturers that meet your criteria. This involves looking into their history, expertise, and market reputation. A well-informed selection process can save you time and resources later.
- Utilize online platforms: Leverage B2B marketplaces and industry-specific directories to find reputable manufacturers.
- Seek recommendations: Connect with industry peers and associations for insights and recommendations based on their experiences.
Step 3: Evaluate Supplier Capabilities
Before committing to a supplier, evaluate their capabilities in detail. This means assessing their production capacity, technology, and quality control processes.
- Request production samples: Ask for samples of their products to gauge quality and consistency.
- Inquire about certifications: Ensure they hold relevant certifications (e.g., ISO, CE) that validate their production processes and quality standards.
Step 4: Check Financial Stability
Understanding the financial health of a potential supplier is crucial to ensure they can meet your demands over the long term. A financially stable manufacturer is more likely to invest in quality and maintain production schedules.
- Review financial statements: Request recent financial documents to assess their profitability and liquidity.
- Look for credit ratings: Utilize credit rating agencies to evaluate their creditworthiness.
Step 5: Verify Supplier Certifications
Certifications are a vital indicator of a manufacturer’s commitment to quality and compliance. Verifying these certifications is essential to mitigate risks.
- Check for industry-relevant certifications: Ensure that the manufacturer has certifications relevant to your industry, which may include environmental or safety certifications.
- Validate with certifying bodies: Contact the certifying bodies to confirm the authenticity of the supplier’s certifications.
Step 6: Assess Logistics and Supply Chain Efficiency
Logistics plays a significant role in the procurement process. Evaluate the manufacturer’s supply chain capabilities, including their logistics management and shipping options.
- Understand their shipping options: Inquire about shipping methods, lead times, and costs to ensure they align with your timelines and budget.
- Evaluate their local partnerships: Check if they have established partnerships with local logistics providers to facilitate smoother operations.
Step 7: Negotiate Terms and Establish Communication Channels
Once you have identified a suitable supplier, negotiate terms that are favorable for both parties. Establishing clear communication channels is crucial for ongoing collaboration.
- Discuss payment terms: Ensure you agree on payment methods and terms that suit both parties.
- Set up regular updates: Establish a schedule for regular communication to address any issues promptly and maintain a strong working relationship.
By following this checklist, B2B buyers can navigate the complexities of sourcing from hub manufacturers with confidence, ensuring they select the right partner for their business needs.
Comprehensive Cost and Pricing Analysis for hub manufacturer Sourcing
What are the Key Cost Components in Hub Manufacturer Sourcing?
When sourcing hubs, understanding the cost structure is crucial for international B2B buyers. The primary cost components include:
-
Materials: The choice of raw materials significantly impacts the overall cost. High-grade metals or specialized composites may enhance performance but can increase expenses. It’s essential to balance quality and cost.
-
Labor: Labor costs can vary greatly depending on the manufacturing location. Regions like Europe may have higher labor costs compared to South America or Africa, but they may also offer higher quality and efficiency.
-
Manufacturing Overhead: This includes utilities, facility costs, and administrative expenses. Manufacturers in regions with lower operational costs can offer more competitive pricing, making location a vital consideration.
-
Tooling: The initial investment in tooling for custom hub designs can be substantial. It’s important to factor this into the total cost, particularly for buyers needing unique specifications.
-
Quality Control (QC): Ensuring that the product meets required standards is critical. Rigorous QC processes may add to manufacturing costs but can save money in the long run by reducing defects and returns.
-
Logistics: Shipping and handling can significantly impact the final price. Buyers should consider freight costs, customs duties, and the potential for delays, especially when sourcing from distant regions.
-
Margin: Finally, the manufacturer’s profit margin will affect pricing. Understanding the typical margins in your specific industry can aid in negotiations.
How Do Price Influencers Affect Hub Manufacturing Costs?
Several factors can influence the pricing of hubs, including:
-
Volume/MOQ (Minimum Order Quantity): Larger orders often lead to reduced per-unit costs. Negotiating favorable terms can help lower the overall investment.
-
Specifications and Customization: Customized hubs may come at a premium. Clearly defining requirements at the outset can prevent costly changes later in the process.
-
Material Choices: The type of materials specified can drive costs up or down. Discussing alternatives with suppliers can help identify cost-effective solutions without compromising quality.
-
Quality Certifications: Hubs that meet international quality standards may incur higher production costs. However, these certifications can enhance product reliability and marketability.
-
Supplier Factors: The reputation and reliability of the supplier can influence pricing. A well-established supplier may charge more but can offer better quality assurance and support.
-
Incoterms: Understanding International Commercial Terms (Incoterms) is vital for cost management. These terms define the responsibilities of buyers and sellers in shipping, which can affect total costs.
What Are the Best Negotiation and Cost-Efficiency Tips for B2B Buyers?
For international buyers, particularly from Africa, South America, the Middle East, and Europe, effective negotiation strategies are essential:
-
Conduct a Total Cost of Ownership (TCO) Analysis: Assess not just the purchase price, but all associated costs, including maintenance, logistics, and disposal. This holistic view can reveal more cost-effective options.
-
Leverage Market Knowledge: Research the market to understand typical pricing and supplier capabilities in different regions. This knowledge can enhance negotiation positions.
-
Establish Long-Term Relationships: Building strong relationships with suppliers can lead to better pricing and terms over time. Consider strategic partnerships rather than one-off transactions.
-
Request Multiple Quotes: Obtaining quotes from various suppliers helps in benchmarking costs. It also provides leverage in negotiations, as you can discuss competitive offers with potential suppliers.
-
Be Flexible with Specifications: If possible, consider minor adjustments to specifications that could lower costs without sacrificing essential functionality.
Conclusion: Navigating the Cost Landscape of Hub Manufacturing
In summary, a comprehensive understanding of the cost structure and pricing influencers is crucial for B2B buyers in the hub manufacturing sector. By focusing on cost components, leveraging negotiation strategies, and considering the Total Cost of Ownership, buyers can make informed decisions that align with their budget and operational needs. Always remember that prices can vary significantly based on numerous factors, and what is quoted may be indicative rather than final.
Alternatives Analysis: Comparing hub manufacturer With Other Solutions
When evaluating potential solutions for your operational needs, it’s crucial to consider various alternatives to ensure you’re making the best choice for your business. This section provides a comparative analysis of ‘hub manufacturer’ against two viable alternatives: ‘Distributed Manufacturing’ and ‘Centralized Production’. Each option has unique advantages and challenges that can significantly influence your decision-making process.
Comparison Aspect | Hub Manufacturer | Distributed Manufacturing | Centralized Production |
---|---|---|---|
Performance | High throughput, reliable | Variable, depends on local capabilities | Consistent, but may face bottlenecks |
Cost | Moderate initial investment, variable operating costs | Lower setup costs, but higher logistics costs | High initial investment, potentially lower per-unit cost |
Ease of Implementation | Requires specialized setup and training | Easier to implement, but may require local partnerships | Complex setup, but streamlined processes once established |
Maintenance | Ongoing support needed, complex systems | Local maintenance, easier to manage | High maintenance due to centralized systems |
Best Use Case | High-volume production with specific quality needs | Custom or low-volume production, agility | Standardized high-volume production |
What Are the Pros and Cons of Distributed Manufacturing?
Distributed manufacturing allows businesses to produce goods closer to the end customer, reducing logistics costs and time. This method is particularly advantageous for companies that require flexibility in production and want to adapt quickly to market demands. However, the performance can vary widely depending on the local manufacturing capabilities and workforce skills. Additionally, while the initial setup costs are generally lower, ongoing logistical costs may increase, especially if materials need to be transported from centralized suppliers.
How Does Centralized Production Compare to Hub Manufacturing?
Centralized production offers the benefits of economies of scale and consistent product quality, making it ideal for companies focused on standardization and large-volume outputs. The streamlined nature of this method can lead to lower per-unit costs once the initial investment is recouped. However, centralized systems can be prone to bottlenecks, especially during demand spikes or supply chain disruptions. Maintenance can also be a challenge, as repairs and upgrades must be handled on a larger scale, which can lead to downtime and operational inefficiencies.
How Can B2B Buyers Choose the Right Solution for Their Needs?
Selecting the right manufacturing solution hinges on a thorough understanding of your operational requirements, budget constraints, and market dynamics. For international B2B buyers from regions like Africa, South America, the Middle East, and Europe, considerations such as local resource availability, labor skills, and logistical infrastructure are essential. By weighing the performance, cost, ease of implementation, and maintenance needs of ‘hub manufacturer’ against its alternatives, businesses can make informed decisions that align with their long-term strategic goals. Ultimately, the right choice will depend on your specific production needs and market conditions, ensuring that you remain competitive and responsive to customer demands.
Essential Technical Properties and Trade Terminology for hub manufacturer
What Are the Essential Technical Properties for Hub Manufacturers?
When sourcing hubs from manufacturers, understanding key technical properties is crucial for ensuring product quality and compatibility. Here are several essential specifications that international B2B buyers should consider:
-
Material Grade
– The material grade of a hub determines its strength, durability, and resistance to wear and corrosion. Common materials include aluminum, steel, and composite materials. Selecting the appropriate grade is vital, as it impacts the hub’s performance in various environments. Buyers should assess material certifications to ensure compliance with industry standards. -
Tolerance
– Tolerance refers to the permissible limit of variation in a physical dimension or measured value. For hubs, tight tolerances are critical for ensuring proper fit and function within assemblies. A slight deviation can lead to performance issues or mechanical failures. Buyers should specify tolerances that meet their operational requirements to avoid costly rework or downtime. -
Weight Capacity
– Understanding the weight capacity of a hub is essential, particularly for applications in heavy machinery or automotive sectors. The weight capacity should match or exceed the operational load to ensure safety and functionality. Buyers should request load testing data from manufacturers to validate claims. -
Surface Finish
– The surface finish of a hub affects not only its aesthetic appeal but also its performance and longevity. Common finishes include anodizing, powder coating, and plating. A good surface finish can enhance corrosion resistance and reduce friction. Buyers should specify their surface finish requirements to ensure optimal performance in their specific applications. -
Dynamic Balance
– Dynamic balance refers to the distribution of mass around the hub’s axis during operation. An unbalanced hub can cause vibrations, leading to premature wear and failure. Buyers should inquire about the balancing methods used by manufacturers to ensure the hubs will perform smoothly in their applications.
What Are Common Trade Terms Used in Hub Manufacturing?
Familiarizing yourself with industry jargon can streamline communication and negotiations with hub manufacturers. Below are some key terms that B2B buyers should understand:
-
OEM (Original Equipment Manufacturer)
– An OEM is a company that produces parts and equipment that may be marketed by another manufacturer. Understanding whether a hub manufacturer is an OEM can help buyers assess the quality and reliability of the products. OEMs often have higher standards and better control over the manufacturing process. -
MOQ (Minimum Order Quantity)
– MOQ refers to the smallest number of units that a manufacturer is willing to produce or sell. This term is crucial for buyers to understand, as it affects inventory management and costs. Buyers should negotiate MOQs based on their needs to avoid excess stock and ensure efficient supply chain management. -
RFQ (Request for Quotation)
– An RFQ is a document that buyers send to manufacturers to obtain pricing for specific products or services. It typically includes details about specifications, quantities, and delivery timelines. Crafting a comprehensive RFQ can help buyers receive accurate quotes and facilitate competitive bidding. -
Incoterms (International Commercial Terms)
– Incoterms are a set of predefined commercial terms published by the International Chamber of Commerce. They define the responsibilities of buyers and sellers in international transactions. Understanding Incoterms helps buyers clarify shipping, insurance, and delivery responsibilities, reducing the risk of disputes. -
Lead Time
– Lead time is the period between placing an order and receiving the goods. It encompasses manufacturing and shipping times. Buyers should factor in lead times when planning their projects to avoid delays and disruptions in their supply chain.
By understanding these technical properties and trade terms, B2B buyers from regions like Africa, South America, the Middle East, and Europe can make informed decisions when sourcing hubs, ensuring they receive products that meet their specific needs and standards.
Navigating Market Dynamics and Sourcing Trends in the hub manufacturer Sector
What Are the Key Market Dynamics and Trends Affecting Hub Manufacturers?
The hub manufacturing sector is experiencing a transformative phase driven by several global factors. Increased demand for electric vehicles (EVs) and advanced automotive technologies has led to a surge in the need for high-quality hubs. This shift is particularly evident in regions like Europe, where regulatory pressures are propelling the automotive industry toward sustainability. Furthermore, the rise of e-commerce and logistics has intensified the demand for robust hub systems in supply chains across Africa and South America.
Emerging technologies such as Artificial Intelligence (AI) and the Internet of Things (IoT) are revolutionizing sourcing strategies within the hub manufacturing sector. Companies are leveraging data analytics to optimize production processes and enhance supply chain visibility. For international B2B buyers, understanding these technological advancements is crucial for making informed sourcing decisions. Additionally, the trend toward local sourcing is gaining traction in regions like the Middle East, where geopolitical factors and trade policies are influencing purchasing strategies.
Buyers should also consider the implications of fluctuating raw material costs and supply chain disruptions, which have been exacerbated by recent global events. A proactive approach to market research and supplier diversification can mitigate risks associated with these dynamics, ensuring a steady supply of high-quality hubs.
How Is Sustainability Influencing Sourcing in the Hub Manufacturing Sector?
Sustainability has become a central tenet in the hub manufacturing sector, pushing companies to prioritize environmentally friendly practices. The impact of manufacturing processes on the environment has led to increased scrutiny from consumers and regulatory bodies alike. Buyers are now more inclined to partner with manufacturers who demonstrate a commitment to sustainable practices, such as using recycled materials and implementing energy-efficient processes.
Ethical sourcing is also gaining prominence. Buyers are encouraged to assess their suppliers’ adherence to ethical labor practices and environmental standards. Certifications such as ISO 14001 for environmental management and Fair Trade for ethical sourcing are becoming essential benchmarks. In regions like Africa and South America, where there are growing concerns about labor practices, buyers should actively seek out suppliers who can demonstrate compliance with these certifications.
Additionally, the use of ‘green’ materials in hub production is on the rise. Manufacturers are increasingly utilizing biodegradable lubricants and eco-friendly coatings, which not only reduce environmental impact but also appeal to a growing segment of eco-conscious consumers. By prioritizing sustainability and ethical sourcing, international B2B buyers can not only contribute to environmental preservation but also enhance their brand reputation and customer loyalty.
How Has the Hub Manufacturing Sector Evolved Over Time?
The evolution of the hub manufacturing sector is marked by significant technological advancements and shifts in consumer demands. Originally, hub manufacturing focused primarily on traditional materials and basic engineering. However, the advent of advanced materials such as composites and high-strength alloys has revolutionized product offerings, enabling manufacturers to produce lighter and more durable hubs.
Over the years, the industry has also witnessed the integration of automation and robotics, enhancing production efficiency and precision. This evolution has been particularly beneficial for international B2B buyers, who now have access to a wider range of high-quality products that meet stringent performance standards. As the market continues to evolve, staying abreast of these changes will empower buyers to make strategic sourcing decisions that align with their business objectives.
Frequently Asked Questions (FAQs) for B2B Buyers of hub manufacturer
-
How do I choose the right hub manufacturer for my business needs?
Selecting the right hub manufacturer involves evaluating several key factors, including product quality, manufacturing capabilities, and industry experience. Start by assessing the manufacturer’s portfolio and client testimonials to gauge their reliability. It’s also crucial to consider their compliance with international standards, especially if you’re importing to regions like Africa or Europe. Engaging in direct communication to discuss your specific requirements can help you determine their capability to meet your needs effectively. -
What are the most important quality assurance practices in hub manufacturing?
Quality assurance in hub manufacturing typically involves rigorous testing and inspection processes. Look for manufacturers that implement ISO certifications, as these indicate adherence to international quality standards. Ask about their quality control measures, such as raw material testing, in-process inspections, and final product evaluations. Additionally, inquire about their return policies and warranty terms, as these can provide insights into their commitment to quality. -
What is the typical minimum order quantity (MOQ) for hub manufacturers?
Minimum order quantities (MOQs) can vary significantly among hub manufacturers, often ranging from a few hundred to several thousand units. Factors influencing MOQs include manufacturing processes, material costs, and customization requirements. When sourcing, clarify the MOQ with potential suppliers and evaluate whether it aligns with your inventory strategy. If your needs are smaller, consider manufacturers that offer flexible MOQs or those willing to negotiate terms based on your business relationship. -
What customization options should I expect from hub manufacturers?
Many hub manufacturers offer a variety of customization options, including design modifications, material choices, and branding. When discussing your project, clearly outline your specific needs and preferences. Inquire about their ability to accommodate custom designs and the associated costs and lead times. Understanding the limits of their customization capabilities will help you find a manufacturer that aligns with your vision and product specifications. -
What payment terms should I negotiate with hub manufacturers?
Payment terms can vary widely, so it’s essential to negotiate terms that protect your financial interests. Common arrangements include upfront deposits, partial payments during production, and final payments upon delivery. Consider discussing payment methods such as letters of credit or escrow services, especially for international transactions. Establishing favorable terms can mitigate risks and foster a trustworthy relationship with your manufacturer. -
How can I verify the reliability of a hub manufacturer before placing an order?
To verify a hub manufacturer’s reliability, conduct thorough due diligence. Start by checking their business credentials, including registration and certifications. Request references from previous clients and conduct online research for reviews. Additionally, consider visiting their facility if possible or using third-party inspection services to assess their operations. This comprehensive approach can help you make informed decisions and avoid potential pitfalls. -
What logistics considerations should I keep in mind when sourcing from hub manufacturers?
Logistics play a crucial role in international sourcing. Consider the manufacturer’s location relative to your business to evaluate shipping times and costs. Understand the customs regulations in your country and the manufacturer’s country to ensure compliance and avoid delays. Additionally, discuss the shipping methods offered and the terms of delivery, such as Incoterms, to clarify responsibilities for transportation and risk. -
How do I handle communication and time zone differences with manufacturers in different regions?
Effective communication is key when working with manufacturers across different time zones. Utilize technology tools such as email, instant messaging, and video conferencing to facilitate discussions. Establish a clear communication schedule that accommodates both parties’ time zones, ensuring regular updates and prompt responses. Additionally, consider designating a liaison or project manager familiar with both cultures to enhance understanding and streamline interactions.
Important Disclaimer & Terms of Use
⚠️ Important Disclaimer
The information provided in this guide, including content regarding manufacturers, technical specifications, and market analysis, is for informational and educational purposes only. It does not constitute professional procurement advice, financial advice, or legal advice.
While we have made every effort to ensure the accuracy and timeliness of the information, we are not responsible for any errors, omissions, or outdated information. Market conditions, company details, and technical standards are subject to change.
B2B buyers must conduct their own independent and thorough due diligence before making any purchasing decisions. This includes contacting suppliers directly, verifying certifications, requesting samples, and seeking professional consultation. The risk of relying on any information in this guide is borne solely by the reader.
Strategic Sourcing Conclusion and Outlook for hub manufacturer
What Are the Key Takeaways for B2B Buyers in Hub Manufacturing?
As we conclude this guide on hub manufacturing, it’s crucial to reiterate the importance of strategic sourcing for international B2B buyers. By carefully selecting suppliers, companies can enhance product quality, reduce costs, and foster innovation. This approach is particularly vital for buyers from regions like Africa, South America, the Middle East, and Europe, where diverse markets demand tailored solutions that address local needs.
How Can Strategic Sourcing Enhance Supply Chain Resilience?
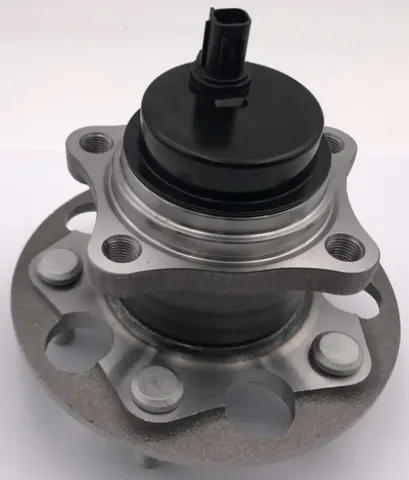
A stock image related to hub manufacturer.
Investing in strategic sourcing not only strengthens supply chain resilience but also mitigates risks associated with geopolitical uncertainties and fluctuating market conditions. Buyers should prioritize establishing relationships with reliable manufacturers who possess a proven track record and the capability to meet specific regional demands. The emphasis should be on sustainability and ethical practices, as these factors are increasingly becoming decision-making criteria for buyers globally.
What Is the Future Outlook for International B2B Buyers in Hub Manufacturing?
Looking ahead, the hub manufacturing landscape is poised for significant transformation, driven by technological advancements and shifting market dynamics. International B2B buyers are encouraged to stay informed about emerging trends and innovations that can optimize their sourcing strategies. By leveraging data analytics and market intelligence, buyers can make informed decisions that align with their long-term objectives.
In conclusion, now is the time for B2B buyers to embrace strategic sourcing as a cornerstone of their procurement strategy. Engage with trusted manufacturers, explore innovative partnerships, and position your business for sustainable growth in an ever-evolving marketplace.