Discover Top Roller Conveyor Suppliers: Save Costs in 2025
Introduction: Navigating the Global Market for roller conveyor supplier
Navigating the complexities of sourcing roller conveyor suppliers can be a daunting task for international B2B buyers, especially those operating in diverse markets like Africa, South America, the Middle East, and Europe. As businesses increasingly seek to optimize their logistics and manufacturing processes, understanding how to efficiently procure roller conveyors tailored to specific operational needs is essential. This guide provides a comprehensive overview of the roller conveyor market, covering various types of conveyors, their applications across different industries, and crucial strategies for supplier vetting.
Buyers will gain insights into the critical factors influencing costs, including material quality, design specifications, and technological advancements in conveyor systems. Furthermore, the guide delves into the importance of evaluating supplier capabilities, including their production capacity, reliability, and after-sales support. By equipping B2B buyers with actionable knowledge and best practices, this resource empowers them to make informed purchasing decisions that align with their operational goals.
As we explore the global landscape of roller conveyor suppliers, this guide aims to bridge the gap between buyers and suppliers, facilitating seamless communication and negotiations. Whether you’re a small enterprise in Brazil or a large manufacturing firm in Germany, understanding the nuances of roller conveyor sourcing can lead to enhanced efficiency and competitiveness in your market.
Understanding roller conveyor supplier Types and Variations
Type Name | Key Distinguishing Features | Primary B2B Applications | Brief Pros & Cons for Buyers |
---|---|---|---|
Gravity Roller Conveyors | Operate without power; rely on gravity | Warehousing, assembly lines | Pros: Low maintenance, cost-effective. Cons: Limited speed control. |
Powered Roller Conveyors | Use motors for movement; adjustable speed | Distribution centers, packaging | Pros: High efficiency, flexible speed. Cons: Higher initial cost. |
Accumulation Roller Conveyors | Allow products to accumulate without stopping | Manufacturing, order fulfillment | Pros: Reduces product damage, increases throughput. Cons: More complex design. |
Flexible Roller Conveyors | Modular design; can be reconfigured easily | Temporary setups, trade shows | Pros: Versatile, easy to transport. Cons: Less durable for heavy loads. |
Stainless Steel Roller Conveyors | Corrosion-resistant; ideal for hygienic environments | Food processing, pharmaceuticals | Pros: High durability, easy to clean. Cons: Higher cost compared to other materials. |
What Are the Characteristics of Gravity Roller Conveyors?
Gravity roller conveyors are a fundamental type of conveyor system that operates solely on the principle of gravity. They are typically used in warehousing and assembly lines where products are moved down an incline. This type of conveyor is cost-effective and requires minimal maintenance since there are no motorized components. However, the lack of speed control may not suit all applications, particularly where precise movement is necessary.
How Do Powered Roller Conveyors Enhance Efficiency?
Powered roller conveyors utilize electric motors to drive the rollers, allowing for adjustable speeds and directional control. This feature makes them ideal for busy distribution centers and packaging operations where efficiency and speed are paramount. While they offer significant advantages in terms of throughput and flexibility, the initial investment and ongoing energy costs can be higher compared to gravity systems.
What Advantages Do Accumulation Roller Conveyors Offer?
Accumulation roller conveyors are designed to hold products in place without stopping their movement. This capability is particularly beneficial in manufacturing and order fulfillment environments, where it helps to minimize product damage and increase throughput. However, their more complex design can lead to higher maintenance requirements, and they may not be suitable for all product types.
Why Choose Flexible Roller Conveyors for Temporary Setups?
Flexible roller conveyors are characterized by their modular design, allowing for easy reconfiguration and transport. This makes them an excellent choice for temporary setups, such as at trade shows or in production scenarios that require frequent changes. While they provide versatility, they may not be as durable as fixed systems, especially when handling heavy loads.
What Makes Stainless Steel Roller Conveyors Ideal for Hygienic Applications?
Stainless steel roller conveyors are specifically designed for environments that require high hygiene standards, such as food processing and pharmaceuticals. Their corrosion-resistant properties and ease of cleaning make them a preferred choice in these industries. Despite their durability and suitability for sensitive applications, the cost of stainless steel conveyors is typically higher than that of their non-corrosive counterparts.
Related Video: Rexroth TS5 Powered Roller Conveyor System
Key Industrial Applications of roller conveyor supplier
Industry/Sector | Specific Application of roller conveyor supplier | Value/Benefit for the Business | Key Sourcing Considerations for this Application |
---|---|---|---|
Automotive Manufacturing | Assembly line automation for vehicle parts | Increases efficiency and reduces labor costs | Ensure compatibility with existing systems and load capacity |
Food and Beverage Processing | Transportation of packaged goods through production lines | Enhances hygiene and speeds up processing times | Look for food-grade materials and easy-to-clean designs |
Warehousing and Logistics | Order fulfillment and inventory management systems | Improves order accuracy and reduces picking times | Consider modular designs for flexibility and scalability |
Pharmaceuticals | Movement of products through packaging and labeling stations | Ensures compliance with health regulations and safety | Focus on precision engineering and durability |
Mining and Heavy Industries | Transporting raw materials and finished products | Increases throughput and minimizes manual handling | Assess environmental conditions and load-bearing capacities |
How is Roller Conveyor Used in Automotive Manufacturing?
In the automotive manufacturing sector, roller conveyor systems are pivotal for assembly line automation. These conveyors facilitate the efficient movement of vehicle parts from one workstation to another, significantly enhancing production speed. By automating this process, manufacturers can reduce labor costs and improve overall efficiency. International B2B buyers should consider sourcing conveyors that are compatible with their existing systems and capable of handling the specific load capacities required for automotive components.
What Role Do Roller Conveyors Play in Food and Beverage Processing?
In food and beverage processing, roller conveyors are employed to transport packaged goods along production lines. This application is critical for maintaining hygiene standards while ensuring that products are moved quickly and efficiently. The use of roller conveyors minimizes human contact with products, which is essential in food safety. Buyers in this sector should prioritize sourcing food-grade materials that are easy to clean, ensuring compliance with health regulations.
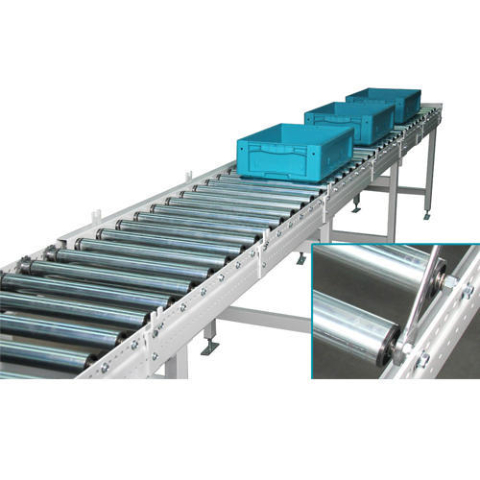
A stock image related to roller conveyor supplier.
How are Roller Conveyors Beneficial in Warehousing and Logistics?
Roller conveyors are integral to order fulfillment and inventory management systems within warehousing and logistics. They streamline the picking process, allowing items to be transported directly to packing stations, which improves order accuracy and reduces picking times. For international buyers, sourcing modular conveyor systems can offer the flexibility needed to adapt to varying warehouse layouts and future expansions, making them a smart investment.
What Advantages Do Roller Conveyors Offer in Pharmaceuticals?
In the pharmaceutical industry, roller conveyors are utilized to move products through various stages of packaging and labeling. This ensures that operations comply with stringent health regulations while maintaining product safety. The precision engineering of these conveyors allows for smooth transitions, reducing the risk of product damage. Buyers should focus on sourcing conveyors that offer durability and reliability, as well as the capability to meet specific regulatory requirements.
How are Roller Conveyors Applied in Mining and Heavy Industries?
In mining and heavy industries, roller conveyors are essential for transporting raw materials and finished products over long distances. Their robust design allows them to handle heavy loads, thereby increasing throughput while minimizing manual handling. For international buyers, it’s crucial to assess the environmental conditions in which these conveyors will operate, ensuring that they meet the necessary load-bearing capacities and are suited for the harsh conditions often found in mining environments.
3 Common User Pain Points for ‘roller conveyor supplier’ & Their Solutions
Scenario 1: Inadequate Customization Options for Specific Needs
The Problem: B2B buyers often face challenges when roller conveyor suppliers offer limited customization options. For industries requiring specific dimensions, load capacities, or material specifications, generic conveyor systems can lead to inefficiencies. This inadequacy might result in increased operational costs, bottlenecks in production lines, and even potential safety hazards due to improper handling of materials.
The Solution: To address this issue, B2B buyers should prioritize suppliers who offer tailored solutions. Start by conducting thorough research to identify roller conveyor manufacturers with a reputation for customization. Request detailed specifications and examples of past projects where the supplier successfully met unique client requirements. Establish clear communication to discuss your specific needs, ensuring that the supplier understands the operational context and challenges. Additionally, consider leveraging CAD (Computer-Aided Design) tools to visualize the conveyor system’s integration into your existing infrastructure, facilitating better design discussions.
Scenario 2: Lack of Reliable After-Sales Support and Maintenance
The Problem: After purchasing roller conveyors, many buyers experience frustration due to inadequate after-sales support. This can manifest as difficulty in accessing replacement parts, insufficient maintenance guidance, or unresponsive customer service. Such shortcomings can lead to prolonged downtimes and increased repair costs, severely impacting productivity.
The Solution: To mitigate this pain point, buyers should assess potential suppliers based on their after-sales service commitments before making a purchase. Inquire about warranty terms, availability of spare parts, and the responsiveness of their customer service team. A supplier that provides a dedicated support hotline and maintenance training can greatly enhance operational efficiency. It is also beneficial to establish a preventive maintenance schedule, which can be agreed upon during the negotiation phase. Document all maintenance activities and develop a partnership with the supplier for ongoing support, ensuring that you have a reliable contact for any future issues.
Scenario 3: Misalignment of Cost and Quality Expectations
The Problem: Many B2B buyers struggle with the balance between cost and quality when sourcing roller conveyors. A common scenario involves opting for the cheapest option, only to find that the equipment fails to meet performance standards or durability expectations. This misalignment can lead to higher long-term costs due to replacements or repairs, ultimately affecting the overall bottom line.
The Solution: To avoid this pitfall, B2B buyers should adopt a value-based procurement approach rather than a purely cost-driven one. Begin by identifying key performance indicators (KPIs) relevant to your operations, such as load capacity, speed, and energy efficiency. Use these KPIs to evaluate potential suppliers, requesting samples or case studies that demonstrate their equipment’s performance in similar applications. Engage in discussions with suppliers about the total cost of ownership (TCO), which includes installation, maintenance, and operational costs over the conveyor’s lifespan. By focusing on value and long-term benefits rather than upfront costs, you can make informed decisions that align with your operational goals.
Strategic Material Selection Guide for roller conveyor supplier
When selecting materials for roller conveyors, international B2B buyers must consider various factors that influence performance, cost, and suitability for specific applications. Here, we analyze four common materials used in roller conveyor systems: steel, aluminum, plastic, and stainless steel. Each material has distinct properties that affect its performance in various environments and applications.
What are the Key Properties of Steel for Roller Conveyors?
Steel is one of the most widely used materials in roller conveyor systems due to its strength and durability. It typically offers high temperature and pressure ratings, making it suitable for heavy-duty applications. Steel’s corrosion resistance can vary based on the type of steel used and any protective coatings applied.
Pros and Cons of Steel:
– Advantages: Steel is known for its high tensile strength and durability, making it ideal for heavy loads. It is also relatively low in cost compared to other materials.
– Disadvantages: Steel can be susceptible to rust and corrosion if not properly treated, which can lead to increased maintenance costs. Additionally, its weight can be a drawback in applications where weight reduction is critical.
How Does Aluminum Compare as a Material for Roller Conveyors?
Aluminum is another popular choice, especially in industries where weight and corrosion resistance are paramount. It has a lower density than steel, allowing for lighter conveyor systems that are easier to install and modify.
Pros and Cons of Aluminum:
– Advantages: Aluminum is lightweight, which reduces overall system weight and installation costs. It also has excellent corrosion resistance, making it suitable for humid or wet environments.
– Disadvantages: Aluminum generally has a lower tensile strength compared to steel, which may limit its use in heavy-duty applications. It is also more expensive than steel.
What are the Benefits of Using Plastic in Roller Conveyors?
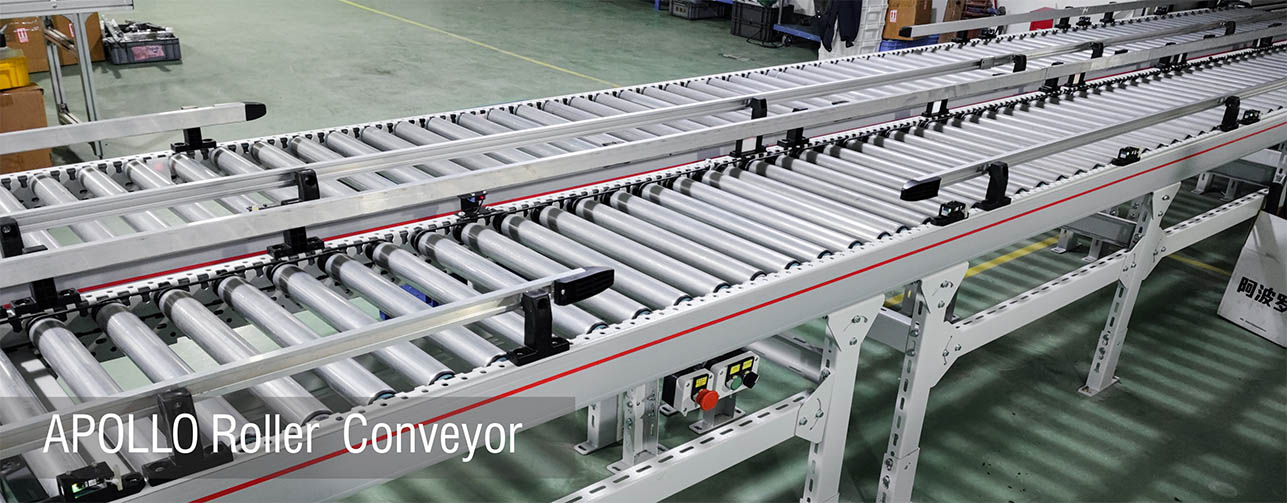
A stock image related to roller conveyor supplier.
Plastic materials, such as polyethylene and polypropylene, are increasingly used in roller conveyor systems, particularly in food processing and packaging industries due to their non-corrosive properties.
Pros and Cons of Plastic:
– Advantages: Plastic is lightweight, resistant to chemicals, and does not corrode, making it suitable for various applications. It is also quieter in operation compared to metal rollers.
– Disadvantages: Plastic may not withstand heavy loads as effectively as metal options, and its temperature resistance can be limited, which may affect its performance in high-temperature environments.
Why is Stainless Steel a Preferred Material for Certain Applications?
Stainless steel is favored in industries requiring high hygiene standards, such as food and pharmaceuticals. It offers excellent corrosion resistance and can withstand harsh cleaning chemicals.
Pros and Cons of Stainless Steel:
– Advantages: Stainless steel’s durability and corrosion resistance make it ideal for sanitary applications. It can handle high temperatures and is easy to clean.
– Disadvantages: The cost of stainless steel is typically higher than that of carbon steel or aluminum, which can impact budget considerations for some buyers.
Summary of Material Selection for Roller Conveyors
Material | Typical Use Case for roller conveyor supplier | Key Advantage | Key Disadvantage/Limitation | Relative Cost (Low/Med/High) |
---|---|---|---|---|
Steel | Heavy-duty applications in manufacturing and logistics | High tensile strength and durability | Susceptible to rust and corrosion | Low |
Aluminum | Lightweight conveyors in packaging and assembly lines | Lightweight and corrosion-resistant | Lower strength for heavy loads | Medium |
Plastic | Food processing and packaging applications | Non-corrosive and quiet operation | Limited load capacity and temperature resistance | Medium |
Stainless Steel | Sanitary applications in food and pharmaceuticals | Excellent corrosion resistance and hygiene | Higher cost compared to other materials | High |
This guide aims to equip international B2B buyers, particularly from regions like Africa, South America, the Middle East, and Europe, with the necessary insights to make informed decisions regarding material selection for roller conveyors. Understanding the properties, advantages, and limitations of these materials will help ensure the chosen solution aligns with specific operational needs and compliance standards.
In-depth Look: Manufacturing Processes and Quality Assurance for roller conveyor supplier
What Are the Main Stages of Manufacturing Roller Conveyors?
The manufacturing process for roller conveyors involves several critical stages, each designed to ensure the final product meets the high standards expected by international B2B buyers. Understanding these stages can help buyers assess the capabilities and reliability of potential suppliers.
Material Preparation: What Materials Are Used in Roller Conveyor Manufacturing?
The first step in the manufacturing process is material preparation. Roller conveyors are typically made from various materials, including:
- Steel: Known for its strength and durability, steel is often used for heavy-duty applications.
- Aluminum: Lightweight and resistant to corrosion, aluminum is preferred for applications where weight and flexibility are crucial.
- Plastic: Used for specific applications requiring resistance to chemicals and moisture.
During this stage, materials are sourced from reputable suppliers, and quality checks are performed to ensure they meet specifications. Buyers should inquire about the suppliers’ material sourcing practices to ensure compliance with international standards.
Forming: How Are Roller Conveyor Components Shaped?
The forming stage involves shaping the materials into usable components. Key techniques include:
- Cutting: Materials are cut to precise dimensions using saws, lasers, or water jets.
- Bending and Welding: Techniques such as press braking and MIG welding are employed to form the structure of the conveyor.
- Machining: Additional processes like milling and drilling are applied to create the necessary fittings and components.
Buyers should ensure that suppliers use modern machinery and skilled labor to maintain high precision and reduce waste.
Assembly: What Does the Assembly Process Look Like for Roller Conveyors?
In the assembly stage, formed components are put together to create the final product. This process typically includes:
- Sub-Assembly: Components like rollers, frames, and belts are assembled separately before final assembly.
- Integration: Sub-assemblies are integrated into the main conveyor system, ensuring all components work seamlessly together.
Attention to detail is crucial during this stage, as any misalignment can affect the performance of the conveyor. B2B buyers should ask about the assembly techniques and whether the supplier employs automated systems for consistency.
Finishing: How Is the Final Product Prepared for Delivery?
The final stage, finishing, involves applying coatings and treatments to enhance durability and aesthetics. Common finishing techniques include:
- Painting: Protective coatings are applied to prevent corrosion and wear.
- Powder Coating: A more durable alternative to traditional paint, powder coating provides a tough finish.
- Quality Inspection: Before delivery, each conveyor undergoes a thorough quality inspection to ensure it meets specifications.
Buyers should request information about the finishing processes and any certifications related to surface treatment to ensure compliance with industry standards.
What Quality Assurance Practices Should B2B Buyers Expect from Roller Conveyor Suppliers?
Quality assurance is crucial in manufacturing roller conveyors, ensuring that products meet international standards and customer expectations. Here’s what buyers should know.
Which International Standards Are Relevant for Roller Conveyor Manufacturing?
Many suppliers adhere to international quality standards, such as:
- ISO 9001: This standard outlines requirements for quality management systems, focusing on customer satisfaction and continuous improvement.
- CE Marking: Indicates compliance with European health, safety, and environmental protection standards.
- API Standards: Relevant for conveyors used in the oil and gas industry, ensuring they meet specific operational criteria.
Understanding these standards can help buyers evaluate the credibility and reliability of potential suppliers.
What Are the Key Quality Control Checkpoints in the Manufacturing Process?
Quality control (QC) checkpoints are vital in the manufacturing process. Key checkpoints include:
- Incoming Quality Control (IQC): Inspection of raw materials upon arrival to ensure they meet specifications.
- In-Process Quality Control (IPQC): Ongoing inspections during the manufacturing process to identify defects early.
- Final Quality Control (FQC): A comprehensive inspection of the finished product to ensure it meets all quality standards before shipping.
B2B buyers should inquire about the QC processes in place and how frequently inspections are conducted.
How Can B2B Buyers Verify Supplier Quality Control Practices?
To ensure a supplier maintains high-quality standards, B2B buyers can take several steps:
- Conduct Audits: Regular audits of the supplier’s facilities can provide insights into their manufacturing practices and QC processes.
- Request Quality Reports: Suppliers should provide documentation of their quality control measures and results from inspections.
- Engage Third-Party Inspectors: Utilizing independent inspectors can give an unbiased assessment of the supplier’s quality assurance practices.
What Are the Common Testing Methods Used in Roller Conveyor Quality Assurance?
Testing methods are critical for ensuring the functionality and durability of roller conveyors. Common testing methods include:
- Load Testing: Evaluates the conveyor’s ability to handle specified loads without failure.
- Operational Testing: Ensures that the conveyor operates smoothly and meets performance specifications.
- Environmental Testing: Simulates conditions such as humidity, temperature, and exposure to chemicals to assess durability.
Buyers should ensure that suppliers conduct these tests and provide certifications as proof of compliance.
How Do Quality Control Nuances Affect International B2B Buyers?
International B2B buyers, particularly from diverse regions such as Africa, South America, the Middle East, and Europe, should be aware of specific nuances:
- Cultural Differences: Different regions may have varying expectations regarding quality and service. Understanding these can enhance communication and expectations.
- Regulatory Compliance: Buyers must ensure that suppliers comply with local regulations and standards, which can vary significantly from one region to another.
- Supply Chain Logistics: The geographical distance can affect lead times and shipping costs, impacting the overall procurement process.
By understanding these factors, international buyers can make informed decisions when selecting roller conveyor suppliers.
Practical Sourcing Guide: A Step-by-Step Checklist for ‘roller conveyor supplier’
The following guide serves as a practical checklist for international B2B buyers looking to procure roller conveyors. It outlines essential steps to ensure that you choose a reliable supplier who meets your technical and logistical needs.
Step 1: Define Your Technical Specifications
Before reaching out to potential suppliers, clearly outline your technical requirements for the roller conveyor. Consider factors such as load capacity, conveyor length, width, and material type.
- Why It Matters: Clearly defined specifications help suppliers provide accurate quotes and ensure that the conveyors meet your operational needs.
- What to Look For: Include any unique features needed for your application, such as adjustable speeds or integration with existing systems.
Step 2: Research Potential Suppliers
Conduct thorough research to identify potential suppliers. Utilize online directories, industry forums, and trade shows to gather a list of manufacturers.
- Why It Matters: A well-researched list ensures you have multiple options to compare quality, prices, and services.
- What to Look For: Pay attention to suppliers with a strong reputation in your region, especially those who have experience dealing with companies similar to yours.
Step 3: Evaluate Supplier Experience and Reputation
Assess the experience and reputation of potential suppliers. Request information about their history, previous projects, and customer testimonials.
- Why It Matters: Suppliers with extensive experience are more likely to understand your specific needs and can provide tailored solutions.
- What to Look For: Check for case studies or references, particularly from companies in your industry or geographical area.
Step 4: Verify Certifications and Compliance
Ensure that the suppliers comply with international standards and hold necessary certifications, such as ISO or CE markings.
- Why It Matters: Compliance with industry standards guarantees that the products meet safety and quality benchmarks, reducing the risk of operational failures.
- What to Look For: Ask for copies of certifications and check their validity with the issuing bodies.
Step 5: Request Detailed Quotations
Once you have shortlisted suppliers, request detailed quotations that include pricing, delivery timelines, and payment terms.
- Why It Matters: A comprehensive quotation allows for accurate comparison and helps identify any hidden costs.
- What to Look For: Ensure that the quote breaks down costs for materials, labor, shipping, and installation.
Step 6: Negotiate Terms and Conditions
Engage in negotiations to ensure favorable terms and conditions, including warranty, support, and after-sales service.
- Why It Matters: Clear terms help protect your investment and ensure ongoing support for maintenance and troubleshooting.
- What to Look For: Look for suppliers who offer robust after-sales support and clear warranty policies.
Step 7: Establish Communication Protocols
Finally, set up effective communication channels with your chosen supplier to facilitate smooth transactions and project updates.
- Why It Matters: Good communication is essential for addressing any issues quickly and ensuring the project stays on track.
- What to Look For: Establish regular check-ins or updates, particularly during critical stages like production and shipping.
Following this structured checklist will enhance your procurement process, ensuring that you select a roller conveyor supplier that meets your needs effectively and efficiently.
Comprehensive Cost and Pricing Analysis for roller conveyor supplier Sourcing
What Are the Key Cost Components in Roller Conveyor Supplier Sourcing?
When sourcing roller conveyors, understanding the cost structure is vital for international B2B buyers. The primary components contributing to the overall cost include:
-
Materials: The choice of materials significantly impacts pricing. High-quality steel, for instance, will increase costs but may provide better durability and performance. Suppliers often offer different grades of materials, which can affect both the upfront price and long-term operational costs.
-
Labor: Labor costs vary based on the supplier’s location and the complexity of the manufacturing process. For example, suppliers in regions with higher wage rates, such as parts of Europe, may present higher labor costs compared to those in South America or Africa.
-
Manufacturing Overhead: This includes costs related to facilities, utilities, and equipment maintenance. A supplier with advanced technology may charge more due to their higher overhead, but this can lead to better efficiency and reduced lead times.
-
Tooling: Custom tooling for specific conveyor designs can add significant costs. If your project requires specialized parts, be prepared for increased initial expenses.
-
Quality Control (QC): Implementing stringent QC processes ensures product reliability but can also inflate costs. Ensure you understand the supplier’s QC practices, as this can prevent costly errors in the long run.
-
Logistics: Shipping costs, including customs duties and insurance, should be factored into the total cost. The choice of shipping methods can greatly influence delivery times and expenses.
-
Margin: Supplier profit margins can vary. Understanding the typical margins in your industry can help you gauge whether you are receiving a fair price.
How Do Price Influencers Affect Roller Conveyor Costs?
Several factors influence the pricing of roller conveyors, making it essential for buyers to consider these aspects during negotiations:
-
Volume and Minimum Order Quantity (MOQ): Suppliers often provide discounts for larger orders. Understanding the MOQ can help you strategize purchases effectively, especially if you have storage capabilities.
-
Specifications and Customization: Custom designs or specifications may lead to increased costs. Clearly define your requirements to avoid unexpected charges.
-
Materials Quality and Certifications: Products with higher certifications (e.g., ISO standards) may command higher prices. Evaluate the importance of certifications in relation to your operational needs.
-
Supplier Factors: Reputation, reliability, and experience of the supplier can impact pricing. Established suppliers with a solid track record may charge more but offer better service and product quality.
-
Incoterms: These terms define the responsibilities of buyers and sellers in international shipping. Different Incoterms can affect overall costs, including who pays for shipping and insurance.
What Are Effective Buyer Tips for Roller Conveyor Sourcing?
International B2B buyers should adopt several strategies to ensure cost-effective procurement of roller conveyors:
-
Negotiation Tactics: Leverage your understanding of the supplier’s cost structure to negotiate better terms. Highlight the potential for repeat business to secure favorable pricing.
-
Focus on Total Cost of Ownership (TCO): Instead of only considering the initial price, evaluate long-term costs associated with maintenance, energy consumption, and potential downtime. A slightly higher initial cost may lead to significant savings over time.
-
Understand Pricing Nuances for Different Regions: Be aware of regional economic factors, currency fluctuations, and trade agreements that may affect pricing. For instance, buyers from Africa may benefit from specific trade agreements with suppliers in Europe.
-
Request Indicative Prices: While suppliers may hesitate to provide exact quotes without specifications, asking for indicative pricing can help you establish a budget and assess competitiveness.
Conclusion
In summary, a comprehensive understanding of cost components and pricing influencers, along with effective negotiation strategies, is crucial for international B2B buyers sourcing roller conveyors. By focusing on the total cost of ownership and remaining aware of regional pricing nuances, buyers can make informed decisions that align with their operational needs and budget constraints.
Alternatives Analysis: Comparing roller conveyor supplier With Other Solutions
Understanding Alternatives to Roller Conveyor Suppliers
In the dynamic landscape of supply chain management and logistics, the choice of material handling systems is crucial for operational efficiency. Roller conveyors are widely recognized for their ability to facilitate the movement of goods, but there are alternative solutions that may offer distinct advantages depending on the specific needs of a business. This analysis will compare roller conveyor suppliers with two viable alternatives: belt conveyors and automated guided vehicles (AGVs).
Comparison Table of Material Handling Solutions
Comparison Aspect | Roller Conveyor Supplier | Belt Conveyor | Automated Guided Vehicles (AGVs) |
---|---|---|---|
Performance | High throughput for unit loads | Moderate to high throughput; best for continuous transport | Flexible and adaptable for various layouts |
Cost | Moderate initial cost, low operating cost | Lower initial cost, moderate operating cost | High initial investment, but low labor costs |
Ease of Implementation | Requires significant space and planning | Easier to install in various layouts | Requires advanced planning and integration |
Maintenance | Low maintenance, durable components | Moderate maintenance; belt wear can be an issue | Regular maintenance required for battery and navigation systems |
Best Use Case | Ideal for heavy, stable items | Suitable for bulk materials and small packages | Best for dynamic environments needing flexibility |
Detailed Breakdown of Alternatives
What are the advantages of using belt conveyors over roller conveyor suppliers?
Belt conveyors are often favored for their versatility in handling a wide range of materials, including bulk goods and smaller items. Their continuous transport capability allows for a smooth flow of products, reducing the likelihood of jams. Additionally, belt conveyors generally require a lower initial investment compared to roller conveyors. However, they may incur higher maintenance costs due to wear and tear on the belts, making them less durable over time.
How do automated guided vehicles (AGVs) compare to roller conveyor suppliers?
AGVs represent a cutting-edge solution in material handling, offering unparalleled flexibility in routing and layout adaptability. These vehicles can navigate autonomously, allowing for efficient transportation of goods across various locations without the need for fixed pathways. While AGVs can significantly reduce labor costs, they require a higher upfront investment and ongoing maintenance to ensure operational efficiency. This technology is particularly beneficial in environments where product flow changes frequently or where space constraints exist.
Conclusion: How to Choose the Right Solution for Your Business Needs
Selecting the appropriate material handling solution involves evaluating your specific operational needs and constraints. For businesses focused on high-volume, stable product transport, roller conveyors may be the most efficient choice. Conversely, if your operations involve diverse product types or require flexibility, belt conveyors or AGVs could provide the adaptability needed to optimize your supply chain. Consider factors such as cost, maintenance, and implementation ease to make an informed decision that aligns with your strategic goals. By carefully analyzing these alternatives, B2B buyers from regions like Africa, South America, the Middle East, and Europe can enhance their operational efficiency and drive business success.
Essential Technical Properties and Trade Terminology for roller conveyor supplier
What Are the Essential Technical Properties of Roller Conveyors?
When considering roller conveyors for your operations, understanding the technical specifications is crucial. Here are several key properties that should guide your purchasing decisions:
-
Material Grade
– Roller conveyors are typically made from materials such as steel, aluminum, or plastic. The choice of material affects the durability, weight capacity, and corrosion resistance of the conveyor. For example, stainless steel is preferred in environments prone to moisture or chemical exposure, while aluminum is lightweight and ideal for mobile applications. Selecting the right material ensures longevity and efficiency in your operations. -
Load Capacity
– This specification indicates the maximum weight that the conveyor can handle without compromising its structural integrity. Load capacity varies based on the design and materials used in the rollers. Assessing your operational needs against the conveyor’s load capacity is essential to prevent breakdowns and ensure smooth workflow. -
Roller Diameter and Spacing
– The diameter of the rollers and the spacing between them influence the type of products that can be transported. Larger diameters are suitable for heavy items, while smaller ones work better for lighter products. Additionally, appropriate spacing ensures stability and prevents products from falling off the conveyor. Understanding these dimensions is vital for selecting a conveyor that fits your specific product handling requirements. -
Belt Speed
– This property refers to how quickly products can move along the conveyor system. It is measured in feet per minute (FPM). The right belt speed is necessary to match the pace of your production line and minimize bottlenecks. If the speed is too slow, it can lead to delays; too fast, and items may become damaged or misaligned. -
Tolerance Levels
– Tolerance levels refer to the acceptable range of deviation from the specified dimensions during manufacturing. High precision in manufacturing tolerances ensures that components fit together correctly, leading to smoother operations and fewer maintenance issues. This is particularly important for automated systems where misalignment can lead to significant operational disruptions.
What Are Common Trade Terms Related to Roller Conveyors?
Understanding industry jargon is equally important for effective communication with suppliers and ensuring a smooth procurement process. Here are some common terms you should know:
-
OEM (Original Equipment Manufacturer)
– An OEM is a company that produces parts or equipment that may be marketed by another manufacturer. In the context of roller conveyors, working with OEMs can ensure that you receive high-quality components that are compatible with your existing systems. -
MOQ (Minimum Order Quantity)
– MOQ refers to the smallest number of units a supplier is willing to sell. Understanding MOQ is crucial for budgeting and inventory management, especially for international buyers who might face additional shipping costs if ordering below this threshold. -
RFQ (Request for Quotation)
– An RFQ is a standard business process where a buyer solicits price quotes from suppliers for specific products or services. For roller conveyor systems, an RFQ helps in comparing prices and terms from different suppliers, facilitating informed decision-making. -
Incoterms
– International Commercial Terms (Incoterms) define the responsibilities of buyers and sellers in international transactions, including who is responsible for shipping, insurance, and tariffs. Familiarity with Incoterms can help you negotiate better terms and avoid unexpected costs when sourcing roller conveyors from global suppliers.
-
Lead Time
– This term indicates the time between placing an order and receiving the goods. Understanding lead times is essential for planning your production schedules and ensuring that you have the necessary equipment when you need it. -
Customs Clearance
– This refers to the process of passing goods through customs so they can enter or leave a country. Being aware of customs regulations and documentation requirements can prevent delays and additional costs in international shipping of roller conveyors.
By familiarizing yourself with these technical properties and trade terms, you will be better equipped to make informed decisions when sourcing roller conveyors for your business.
Navigating Market Dynamics and Sourcing Trends in the roller conveyor supplier Sector
What Are the Current Market Dynamics and Sourcing Trends in the Roller Conveyor Supplier Sector?
The roller conveyor supplier sector is experiencing significant transformation driven by various global factors. Increased automation in manufacturing and logistics, especially in regions like Africa, South America, the Middle East, and Europe, has heightened demand for efficient material handling systems. The rise of e-commerce has further propelled this trend, necessitating faster and more reliable conveyor systems to streamline operations. Technological advancements, such as IoT integration and AI, are enabling suppliers to offer smart roller conveyors that enhance operational efficiency and maintenance through predictive analytics.
Another key trend is the diversification of sourcing strategies. International B2B buyers are increasingly looking for suppliers who can provide not just products, but also comprehensive solutions that include installation, maintenance, and after-sales support. This shift is particularly noticeable among buyers from emerging markets in Africa and South America, where local suppliers are beginning to offer competitive alternatives to established European and Middle Eastern manufacturers. As a result, global suppliers must adapt their strategies to remain competitive, focusing on flexibility and customization to meet diverse regional needs.
How Is Sustainability Shaping the Roller Conveyor Supplier Sector?
Sustainability has become a paramount concern for B2B buyers across all regions, affecting sourcing decisions in the roller conveyor supplier sector. The environmental impact of manufacturing processes and the materials used in conveyor systems are now under scrutiny. Buyers are increasingly prioritizing suppliers who adopt sustainable practices, such as using recycled materials and minimizing waste during production. This shift is particularly significant in Europe, where regulatory pressures and consumer demand for sustainable products are driving companies to adopt greener practices.
Additionally, the importance of ethical sourcing cannot be overstated. B2B buyers are seeking suppliers who can demonstrate transparency in their supply chains and uphold ethical labor practices. Certifications such as ISO 14001 (Environmental Management) and ISO 45001 (Occupational Health and Safety) are becoming essential for suppliers aiming to appeal to conscientious buyers. By prioritizing sustainability and ethical sourcing, suppliers not only contribute to environmental protection but also strengthen their market position and brand reputation.
What Is the Evolution of the Roller Conveyor Supplier Sector?
The roller conveyor supplier sector has evolved significantly over the decades, transitioning from simple mechanical systems to sophisticated automated solutions. Initially, roller conveyors were primarily utilized in manufacturing settings for basic material handling. However, the advent of automation in the late 20th century marked a pivotal shift, with suppliers incorporating advanced technologies that enhanced efficiency and adaptability.
In recent years, the focus has expanded to include sustainability and smart technology, reflecting broader industrial trends. Today, suppliers must navigate a complex landscape marked by rapid technological advancement and increasing buyer expectations for sustainability. This evolution presents both challenges and opportunities for international B2B buyers looking to source cutting-edge roller conveyor solutions that align with their operational goals and ethical standards.
Frequently Asked Questions (FAQs) for B2B Buyers of roller conveyor supplier
-
How do I choose the right roller conveyor supplier for my business needs?
Choosing the right roller conveyor supplier involves several key considerations. Start by evaluating the supplier’s reputation and track record in your industry. Look for customer reviews and case studies that demonstrate their experience with similar projects. Additionally, assess their product quality, customization options, and compliance with international standards. Request samples or prototypes to gauge performance. Finally, consider their customer service and support capabilities to ensure they can assist you throughout the lifecycle of your equipment. -
What are the common customization options available for roller conveyors?
Customization options for roller conveyors can vary widely among suppliers. Common features include adjustable roller speeds, different roller materials (such as steel, plastic, or aluminum), and various widths and lengths to fit specific applications. Additionally, you may have options for integrating controls, sensors, and other automation features. Discuss your specific requirements with potential suppliers to determine what customization options are available and how they can enhance your operational efficiency. -
What is the typical minimum order quantity (MOQ) for roller conveyors?
Minimum order quantities (MOQs) for roller conveyors can vary significantly depending on the supplier and the complexity of the product. Generally, MOQs can range from a single unit for standard models to larger quantities for custom designs. Suppliers may set MOQs to ensure cost-effectiveness in production. It’s advisable to negotiate terms with suppliers, especially if you’re a smaller business or are testing the market with a new product line. -
What payment terms should I expect when sourcing roller conveyors internationally?
Payment terms for international purchases of roller conveyors can differ based on the supplier’s policies and the nature of the transaction. Common terms include a deposit upon order confirmation, with the balance due prior to shipment. Some suppliers may offer flexible payment options, such as letters of credit or installment plans. Always clarify the payment terms upfront and ensure they are documented in the contract to avoid any misunderstandings. -
How do I ensure quality assurance when purchasing roller conveyors?
To ensure quality assurance in your roller conveyor purchase, request detailed specifications and quality certifications from the supplier. Many reputable suppliers follow international quality standards such as ISO 9001. Consider conducting factory audits or third-party inspections during production. Additionally, establish a clear return and warranty policy before completing your purchase, ensuring that you have recourse should any issues arise with the equipment after delivery. -
What logistics considerations should I keep in mind when importing roller conveyors?
When importing roller conveyors, logistics considerations are crucial for ensuring timely delivery and compliance with regulations. Research shipping options, including freight forwarders experienced in heavy machinery transport. Understand the customs duties and tariffs applicable to your country, and ensure all necessary documentation is in order to avoid delays. Additionally, factor in the lead time for production and shipping when planning your project timeline. -
How can I assess the reliability of a roller conveyor supplier?
Assessing the reliability of a roller conveyor supplier involves several steps. Start by checking their business credentials, such as years in operation, industry certifications, and partnerships with reputable organizations. Request references from past clients and inquire about their experiences regarding product quality and service. Look for suppliers that provide transparent communication and support throughout the procurement process, which is often indicative of their reliability. -
What are the advantages of using roller conveyors in my operations?
Roller conveyors offer numerous advantages for businesses looking to enhance operational efficiency. They facilitate the smooth and efficient movement of goods, reducing manual handling and associated labor costs. Their modular design allows for easy reconfiguration to adapt to changing workflows. Roller conveyors can also handle various product types and sizes, making them versatile for different industries. Additionally, they can be integrated with automation systems to improve overall productivity and reduce bottlenecks in your supply chain.
Important Disclaimer & Terms of Use
⚠️ Important Disclaimer
The information provided in this guide, including content regarding manufacturers, technical specifications, and market analysis, is for informational and educational purposes only. It does not constitute professional procurement advice, financial advice, or legal advice.
While we have made every effort to ensure the accuracy and timeliness of the information, we are not responsible for any errors, omissions, or outdated information. Market conditions, company details, and technical standards are subject to change.
B2B buyers must conduct their own independent and thorough due diligence before making any purchasing decisions. This includes contacting suppliers directly, verifying certifications, requesting samples, and seeking professional consultation. The risk of relying on any information in this guide is borne solely by the reader.
Strategic Sourcing Conclusion and Outlook for roller conveyor supplier
In conclusion, strategic sourcing for roller conveyor suppliers is crucial for international B2B buyers, particularly those operating in Africa, South America, the Middle East, and Europe. By focusing on quality, reliability, and cost-effectiveness, buyers can enhance their supply chain efficiency and operational performance. It’s important to evaluate suppliers not just on price but on their ability to deliver innovative solutions and exceptional customer service.
Investing time in building relationships with suppliers can lead to long-term partnerships that yield mutual benefits. Engaging with suppliers who understand local market dynamics and regulatory requirements will ensure compliance and adaptability in an ever-evolving global landscape. Additionally, leveraging technology and data analytics can provide insights into supplier performance and market trends, helping buyers make informed decisions.
As we look to the future, the demand for roller conveyor systems is expected to grow, driven by advancements in automation and logistics. International B2B buyers are encouraged to proactively seek partnerships with suppliers who are committed to sustainability and innovation. By doing so, they can position themselves competitively in the marketplace. Embrace the opportunity to refine your sourcing strategies and secure a reliable supply chain that meets your business needs.