Discover Quality & Cost: The Ultimate Blade Manufacturer Guide (2025)
Introduction: Navigating the Global Market for blade manufacturer
Navigating the global market for blade manufacturing poses significant challenges for international B2B buyers, particularly those from Africa, South America, the Middle East, and Europe. The complexity of sourcing high-quality blades that meet industry standards while balancing cost and functionality can be daunting. This guide on blade manufacturers aims to simplify that process by providing a comprehensive overview of the various types of blades available, their applications across multiple industries, and strategies for effectively vetting suppliers.
In this guide, you will find detailed insights into the specifications that matter most when selecting blades, such as material composition, durability, and performance metrics. Additionally, we will explore the nuances of pricing structures and the factors that influence costs in different regions, ensuring you understand what constitutes a fair price. By examining case studies and supplier evaluations, this guide equips you with the knowledge to make informed purchasing decisions that align with your business needs.
Ultimately, this resource serves as a valuable tool for B2B buyers looking to navigate the complexities of the blade manufacturing sector. Whether you’re sourcing blades for industrial applications or specialized uses, this guide empowers you to approach your procurement process with confidence, ensuring you find the best suppliers that cater to your unique market demands.
Understanding blade manufacturer Types and Variations
Type Name | Key Distinguishing Features | Primary B2B Applications | Brief Pros & Cons for Buyers |
---|---|---|---|
Cutting Tool Blades | Designed for precision cutting, often made from high-speed steel or carbide. | Manufacturing, woodworking, metalworking | Pros: High precision, durability. Cons: Higher initial cost. |
Agricultural Blades | Specialized for farming equipment, often curved or serrated for specific crops. | Farming, landscaping | Pros: Optimized for specific tasks, enhances efficiency. Cons: Limited versatility. |
Industrial Blades | Heavy-duty blades for cutting, slitting, and shredding materials like paper and plastic. | Recycling, packaging, construction | Pros: Robust and long-lasting. Cons: Requires maintenance and replacement. |
Surgical Blades | Ultra-sharp blades made from stainless steel or carbon steel, designed for precision in medical applications. | Healthcare, laboratories | Pros: High precision and sterility. Cons: Single-use, can be costly. |
Specialty Blades | Custom-designed blades tailored for specific applications or industries. | Aerospace, automotive, custom projects | Pros: Tailored performance, unique designs. Cons: Longer lead times, potentially higher costs. |
What are the Key Characteristics of Cutting Tool Blades?
Cutting tool blades are integral to various manufacturing processes. Typically crafted from high-speed steel or carbide, these blades are designed for precision and durability. They are widely used in industries such as woodworking and metalworking, where exact cuts are essential. When purchasing, consider factors like the blade’s sharpness, material composition, and compatibility with your machinery, as these aspects significantly impact the overall performance and longevity of the tools.
How Do Agricultural Blades Differ from Other Types?
Agricultural blades are specifically designed to meet the needs of farming and landscaping. They often feature curved or serrated edges to optimize performance for specific crops or tasks, such as harvesting or tilling. Buyers should assess the blade’s compatibility with existing equipment and the types of crops they will be working with. While these blades enhance efficiency in agricultural operations, their specialization may limit their use in other applications.
What are the Applications of Industrial Blades?
Industrial blades are robust tools designed for heavy-duty applications, including cutting, slitting, and shredding materials like paper, plastics, and textiles. These blades are essential in recycling and packaging industries. When considering an industrial blade purchase, buyers should focus on the blade’s material, thickness, and intended application to ensure they choose the right tool for their specific needs. While these blades are known for their longevity, they may require regular maintenance and replacement.
What Makes Surgical Blades Unique?
Surgical blades are crafted for precision and sterility, making them indispensable in healthcare and laboratory settings. Typically made from stainless steel or carbon steel, these blades are designed for single-use to maintain hygiene. Buyers should prioritize the blade’s sharpness and compatibility with surgical instruments. Although surgical blades offer exceptional precision, their single-use nature can lead to higher long-term costs, necessitating bulk purchasing strategies.
Why Consider Specialty Blades?
Specialty blades are custom-designed to meet the unique needs of specific industries, such as aerospace or automotive. These blades may feature unique shapes or materials tailored to particular applications. While they provide tailored performance that can significantly enhance productivity, buyers should be aware of longer lead times and potentially higher costs associated with custom orders. Understanding the specific requirements of your project is crucial when considering these blades.
Related Video: Blade Design and Manufacturing
Key Industrial Applications of blade manufacturer
Industry/Sector | Specific Application of blade manufacturer | Value/Benefit for the Business | Key Sourcing Considerations for this Application |
---|---|---|---|
Food Processing | Industrial slicing blades for meat and vegetables | Increases efficiency and precision in food preparation processes | Durability, hygiene standards, and compliance with food safety regulations |
Automotive Manufacturing | Cutting tools for metal and composite materials | Enhances manufacturing speed and reduces waste | Material compatibility, precision engineering, and lead times |
Packaging | Blades for packaging and labeling machines | Improves packaging speed and reduces downtime | Reliability, blade life, and adaptability to different packaging materials |
Woodworking | Saw blades for milling and cutting wood products | Maximizes yield and quality of finished wood products | Blade sharpness, material type, and cutting speed |
Textile Industry | Cutting blades for fabric and garment manufacturing | Reduces fabric waste and improves cutting accuracy | Versatility in cutting various fabric types and blade longevity |
How Are Blades Used in Food Processing?
In the food processing industry, blade manufacturers provide industrial slicing blades designed for high-volume operations involving meat, vegetables, and other food items. These blades enhance efficiency by ensuring uniform cuts, which is crucial for maintaining quality and presentation in food products. International buyers must consider hygiene standards, blade durability, and compliance with food safety regulations when sourcing these blades, especially in regions like Africa and South America, where regulations may vary.
What Role Do Blades Play in Automotive Manufacturing?
In automotive manufacturing, cutting tools made by blade manufacturers are essential for processing metal and composite materials. These blades contribute to increased manufacturing speed and reduced waste, allowing companies to meet production demands effectively. Buyers in Europe, particularly in countries like Poland, should prioritize precision engineering and material compatibility to ensure the blades meet their specific production needs, while also considering lead times to avoid production delays.
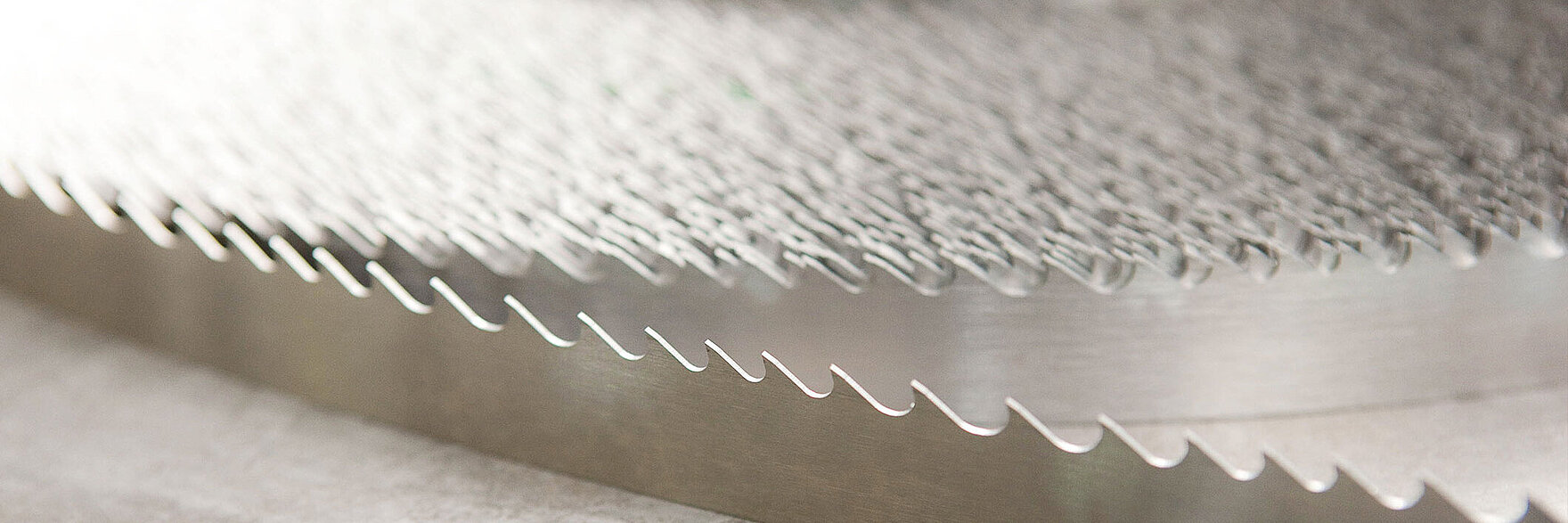
A stock image related to blade manufacturer.
How Are Blades Utilized in Packaging?
Blades are integral to packaging and labeling machines, where they significantly enhance the speed and efficiency of packaging processes. By utilizing high-quality blades, companies can minimize downtime and improve overall productivity. When sourcing blades for packaging applications, businesses should focus on reliability, blade longevity, and the ability to adapt to various packaging materials, especially in diverse markets across the Middle East and Africa.
Why Are Blades Important in Woodworking?
In the woodworking industry, saw blades from blade manufacturers are crucial for milling and cutting wood products. These blades maximize yield and ensure high-quality finishes, which are vital for customer satisfaction. Buyers should consider factors such as blade sharpness, the type of material being cut, and cutting speed to select the most appropriate blades for their operations, particularly in regions with varying wood types and processing standards.
How Are Blades Applied in the Textile Industry?
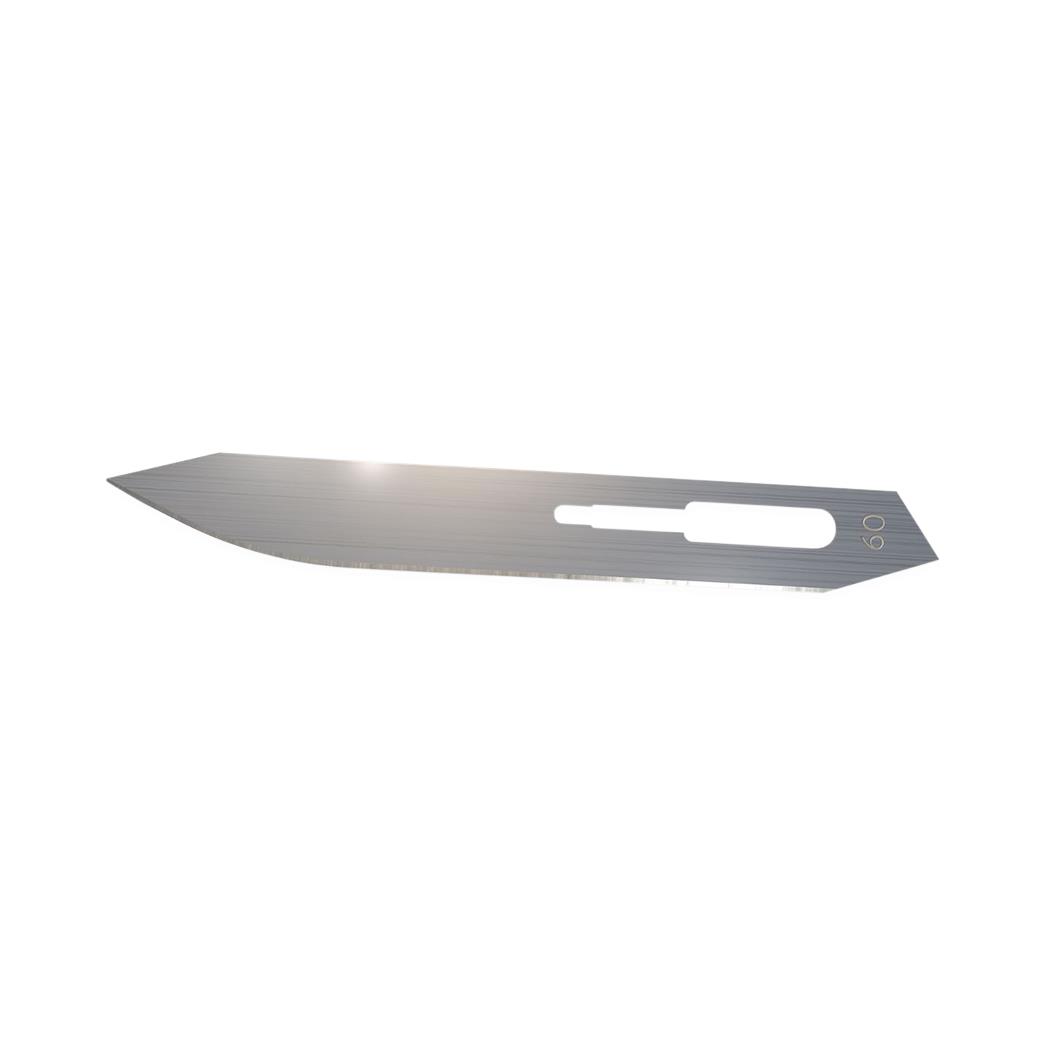
A stock image related to blade manufacturer.
The textile industry relies on cutting blades for fabric and garment manufacturing, where precision is key to reducing waste and improving cutting accuracy. These blades allow manufacturers to handle various fabric types efficiently, which is essential in a competitive market. When sourcing blades, buyers must assess the versatility of the blades and their longevity to ensure they can withstand the demands of high-volume production, particularly in South American textile markets.
3 Common User Pain Points for ‘blade manufacturer’ & Their Solutions
Scenario 1: Difficulty in Finding the Right Blade Specifications
The Problem:
B2B buyers often struggle with identifying the correct specifications for blades that will meet their operational needs. This challenge is particularly acute when dealing with various materials and applications, as different industries require blades that vary significantly in terms of size, shape, and material composition. For instance, a manufacturing company in South America might need blades for cutting hard metals, while a European packaging company may require blades designed for softer materials. Inadequate specifications can lead to purchasing the wrong blades, resulting in operational inefficiencies and increased costs.
The Solution:
To overcome this issue, buyers should engage directly with blade manufacturers to gain a comprehensive understanding of their product offerings. This involves asking specific questions regarding blade materials, coatings, and dimensions relevant to their applications. For example, buyers can request technical datasheets that outline the properties of different blades and their suitability for various materials. Additionally, utilizing online tools or calculators provided by manufacturers can help in selecting the correct blade based on operational parameters. Regularly consulting with suppliers for updates on new technologies and blade innovations can also provide insights that align with evolving industry standards.
Scenario 2: Inconsistent Blade Quality Leading to Downtime
The Problem:
Another common pain point for international B2B buyers is dealing with inconsistent blade quality, which can lead to unexpected downtime and reduced productivity. This issue is particularly prevalent when sourcing blades from multiple suppliers, as varying quality standards can affect the performance and lifespan of blades. For instance, a blade manufacturer in Africa might provide blades that wear out quickly compared to those from a European supplier, causing disruptions in production schedules and increasing operational costs due to frequent replacements.
The Solution:
To mitigate quality inconsistencies, buyers should establish long-term partnerships with reliable blade manufacturers known for their quality assurance processes. This includes requesting samples for testing before making bulk orders and visiting manufacturing facilities to understand the production processes. Additionally, implementing a robust vendor assessment process that includes performance reviews based on specific metrics such as blade lifespan and cutting efficiency can help identify and retain high-quality suppliers. Regular feedback loops with manufacturers can also facilitate improvements in product quality based on real-world performance data.
Scenario 3: Challenges in Blade Customization for Specialized Applications
The Problem:
B2B buyers often encounter difficulties when they require custom blades tailored for specialized applications. Many manufacturers may have standard products, but finding a supplier willing to create customized solutions can be a daunting task. This is especially true for businesses in sectors like aerospace or automotive, where precision and specific configurations are critical. A company in the Middle East needing blades for unique machinery might find that off-the-shelf options do not meet their specifications, leading to project delays and financial losses.
The Solution:
To address customization challenges, buyers should proactively communicate their specific needs to potential blade manufacturers. This includes providing detailed drawings, specifications, and expected performance criteria. Working with manufacturers that offer design consultation services can also be beneficial, as they can suggest modifications that can enhance performance while still being cost-effective. Additionally, establishing a collaborative relationship during the design process can lead to better outcomes, as manufacturers are more likely to invest time and resources in creating tailored solutions for clients who demonstrate a commitment to long-term partnership. Engaging in pilot projects with prototypes can also help refine the final product before mass production, ensuring it meets all operational requirements.
Strategic Material Selection Guide for blade manufacturer
When selecting materials for blade manufacturing, international B2B buyers must consider various factors that influence product performance, cost, and compliance with industry standards. Below is an analysis of four common materials used in blade manufacturing, focusing on their properties, advantages and disadvantages, and specific considerations for buyers from diverse regions including Africa, South America, the Middle East, and Europe.
What Are the Key Properties of Stainless Steel for Blade Manufacturing?
Stainless Steel is one of the most widely used materials in blade manufacturing due to its excellent corrosion resistance and durability. Its ability to withstand high temperatures and pressures makes it suitable for various applications, including industrial and culinary blades.
Pros: Stainless steel blades are known for their longevity and ability to maintain sharpness over time. They are relatively easy to manufacture, which can lower production costs.
Cons: However, stainless steel can be more expensive than other materials. It may also require specialized coatings to enhance its performance in specific environments, which can complicate the manufacturing process.
Impact on Application: Stainless steel is compatible with a wide range of media, making it ideal for food processing, medical instruments, and industrial applications.
Considerations for International Buyers: Buyers should ensure compliance with international standards such as ASTM and DIN, particularly in regions like Europe where regulations are stringent.
How Does Carbon Steel Compare as a Material for Blades?
Carbon Steel is another popular choice for blade manufacturing, particularly in applications requiring high strength and edge retention.
Pros: Carbon steel is known for its hardness and ability to take a sharp edge, making it suitable for cutting tools and knives. It is generally less expensive than stainless steel, which can be a significant advantage for manufacturers.
Cons: The main drawback is its susceptibility to rust and corrosion, which necessitates regular maintenance and proper storage conditions.
Impact on Application: Carbon steel blades are particularly effective in dry environments or applications where moisture exposure is minimal.
Considerations for International Buyers: Buyers should be aware of the need for protective coatings or treatments to enhance corrosion resistance, especially in humid climates found in parts of Africa and South America.
What Are the Benefits of Using Tool Steel in Blade Manufacturing?
Tool Steel is specifically designed for manufacturing cutting tools and is characterized by its high hardness and wear resistance.
Pros: Tool steel can withstand high temperatures without losing its hardness, making it ideal for high-performance applications. Its durability ensures a longer lifespan for blades.
Cons: The complexity of manufacturing tool steel blades often leads to higher costs. Additionally, they can be more challenging to sharpen compared to other materials.
Impact on Application: Tool steel is particularly suited for industrial applications, including machining and manufacturing processes that require precision cutting.
Considerations for International Buyers: Compliance with specific industry standards is crucial, especially in Europe where tool steel grades must meet stringent specifications.
Why is Composite Material Gaining Popularity in Blade Manufacturing?
Composite Materials are increasingly being used in blade manufacturing due to their unique properties.
Pros: Composites can offer a combination of lightweight and high strength, making them suitable for specialized applications where weight reduction is essential. They also provide excellent resistance to corrosion and wear.
Cons: However, the manufacturing process for composite materials can be complex and costly. Additionally, they may not be suitable for all applications, particularly those requiring extreme sharpness.
Impact on Application: Composites are often used in aerospace and automotive applications, where performance and weight are critical.
Considerations for International Buyers: Buyers should evaluate the specific performance requirements and ensure that the composites used comply with relevant industry standards in their region.
Summary Table of Material Selection for Blade Manufacturing
Material | Typical Use Case for blade manufacturer | Key Advantage | Key Disadvantage/Limitation | Relative Cost (Low/Med/High) |
---|---|---|---|---|
Stainless Steel | Culinary knives, industrial blades | Excellent corrosion resistance | Higher cost, requires coatings | Medium |
Carbon Steel | Cutting tools, kitchen knives | High hardness, edge retention | Susceptible to rust, requires maintenance | Low |
Tool Steel | Industrial cutting tools | High wear resistance, durability | Higher manufacturing complexity | High |
Composite | Aerospace, automotive applications | Lightweight, high strength | Complex manufacturing process | Medium to High |
This guide provides a comprehensive overview of materials commonly used in blade manufacturing, allowing international B2B buyers to make informed decisions based on performance, cost, and compliance with industry standards.
In-depth Look: Manufacturing Processes and Quality Assurance for blade manufacturer
What Are the Typical Manufacturing Processes for Blade Manufacturers?
Manufacturing blades involves several critical stages, each designed to ensure that the final product meets stringent quality and performance standards. Understanding these processes is essential for B2B buyers to assess potential suppliers effectively.
How Is Material Prepared in Blade Manufacturing?
Material preparation is the first stage in the manufacturing process. High-quality raw materials, often stainless steel or carbon steel, are selected based on the intended application of the blade. The materials are then cut to size and undergo a series of treatments, such as heat treatment, to enhance their hardness and durability.
- Key Techniques:
- Heat Treatment: Involves processes such as annealing, quenching, and tempering to achieve desired mechanical properties.
- Surface Treatment: Techniques like nitriding or coating are applied to improve corrosion resistance and reduce friction.
What Are the Main Forming Techniques Used in Blade Production?
Once the materials are prepared, the next step is forming the blade into its desired shape. This can be accomplished using several techniques:
- Forging: A traditional method that involves shaping the metal using localized compressive forces. This technique enhances the grain structure and overall strength of the blade.
- CNC Machining: Computer Numerical Control (CNC) machines are employed for precision cutting and shaping. This method is particularly useful for complex designs and ensures high repeatability.
- Stamping: Used for mass production, stamping allows for the quick and efficient formation of blade shapes from flat sheets of metal.
How Are Blades Assembled and Finished?
The assembly and finishing stages are crucial for ensuring that the blade not only performs well but also meets aesthetic standards.
- Assembly: Blades may require various components, such as handles or guards, to be attached. This can involve welding, riveting, or using adhesives.
- Finishing: This stage includes grinding, polishing, and coating. Finishing techniques enhance the blade’s appearance and performance, ensuring smooth edges and a corrosion-resistant surface.
What Quality Control Measures Are Common in Blade Manufacturing?
Quality control (QC) is a vital component of the manufacturing process, ensuring that every blade produced meets industry standards and customer expectations.
Which International Standards Should B2B Buyers Be Aware Of?
For international B2B buyers, familiarity with relevant quality standards is essential. Common standards include:
- ISO 9001: This standard focuses on quality management systems and is applicable to any organization looking to improve customer satisfaction and operational efficiency.
- CE Marking: Essential for products sold within the European Economic Area, indicating compliance with health, safety, and environmental protection standards.
- API Standards: Particularly relevant for blades used in the oil and gas industry, ensuring they meet specific performance and safety requirements.
What Are the Key QC Checkpoints in Blade Manufacturing?
Quality assurance involves several checkpoints throughout the manufacturing process:
- Incoming Quality Control (IQC): Checks the quality of raw materials upon arrival to ensure they meet specified standards.
- In-Process Quality Control (IPQC): Ongoing inspections during the manufacturing process to identify and rectify defects early.
- Final Quality Control (FQC): Conducted before shipment, this stage verifies that the finished products meet all specifications and standards.
Which Testing Methods Are Commonly Used in Blade Quality Assurance?
To ensure blades meet the required standards, several testing methods are utilized:
- Visual Inspection: A basic but effective method to detect surface defects and overall finish.
- Hardness Testing: Measures the hardness of the blade to ensure it meets the specified requirements.
- Tensile Testing: Assesses the strength of the blade material to ensure it can withstand operational stresses.
How Can B2B Buyers Verify Supplier Quality Control?
For B2B buyers, verifying a supplier’s quality control processes is essential to ensure that the blades meet their requirements. Here are several methods to consider:
- Supplier Audits: Conducting on-site audits allows buyers to evaluate the supplier’s manufacturing processes, quality control measures, and overall operations.
- Quality Reports: Requesting detailed quality reports can provide insights into the supplier’s testing methods, results, and compliance with international standards.
- Third-Party Inspections: Engaging independent inspection agencies can provide an unbiased assessment of the supplier’s product quality and adherence to standards.
What Nuances Should International B2B Buyers Consider Regarding QC?
When sourcing blades internationally, especially from regions like Africa, South America, the Middle East, and Europe, buyers should consider:
- Cultural Differences: Understanding local manufacturing practices and quality perceptions can aid in establishing effective communication and expectations.
- Regulatory Compliance: Different regions may have varying regulations that impact product standards. Being aware of these can help avoid compliance issues.
- Logistics and Supply Chain: The complexity of international shipping can affect lead times and product integrity. Establishing clear logistics plans can mitigate these risks.
By comprehensively understanding the manufacturing processes and quality assurance measures associated with blade manufacturing, international B2B buyers can make informed decisions, ensuring they partner with suppliers that meet their quality and performance standards.
Practical Sourcing Guide: A Step-by-Step Checklist for ‘blade manufacturer’
The following guide provides a practical checklist for international B2B buyers looking to source blade manufacturers effectively. This step-by-step approach ensures that you make informed decisions and establish successful partnerships.
Step 1: Define Your Technical Specifications
Clearly outline the technical requirements for the blades you need. This includes materials, dimensions, tolerances, and specific applications. By detailing these specifications upfront, you can streamline the selection process and ensure that potential suppliers can meet your needs.
- Consider industry standards: Familiarize yourself with relevant industry standards to ensure compliance.
- Include performance criteria: Specify any performance metrics that the blades must achieve, such as durability or efficiency.
Step 2: Conduct Market Research
Investigate the landscape of blade manufacturers in your target regions, such as Africa, South America, the Middle East, and Europe. Understanding the market dynamics will help you identify potential suppliers and gauge their capabilities.
- Identify key players: Create a list of leading manufacturers and their specialties.
- Analyze trends: Look for emerging trends in blade technology and manufacturing processes that might influence your sourcing decisions.
Step 3: Evaluate Potential Suppliers
Before committing to a supplier, it’s essential to conduct thorough evaluations. Request detailed company profiles, case studies, and references from buyers in similar industries or regions. This will provide insights into their reliability and product quality.
- Assess financial stability: Ensure the supplier has a solid financial standing to avoid disruptions.
- Review product certifications: Check for relevant industry certifications that validate their manufacturing processes.
Step 4: Verify Supplier Certifications
Ensure that your selected suppliers hold the necessary certifications and adhere to quality management systems like ISO 9001. Certifications provide assurance that the manufacturer follows industry best practices and maintains high-quality standards.
- Request documentation: Ask for copies of certification documents and quality assurance policies.
- Check for compliance: Verify that their certifications are up-to-date and relevant to your specific needs.
Step 5: Request Samples and Prototypes
Before finalizing your order, request samples or prototypes of the blades. This step allows you to assess the quality and suitability of the products for your application.
- Evaluate performance: Test the samples under real-world conditions to ensure they meet your requirements.
- Provide feedback: Communicate any issues or adjustments needed to the supplier, which can improve the final product.
Step 6: Negotiate Terms and Conditions
Once you’ve identified a suitable supplier, engage in negotiations to establish favorable terms. This includes pricing, payment terms, delivery schedules, and warranty agreements.
- Be clear on expectations: Clearly outline your expectations to avoid misunderstandings.
- Consider long-term partnerships: If the supplier meets your needs, discuss the potential for long-term collaboration, which can lead to better pricing and service.
Step 7: Establish a Communication Plan
Effective communication is vital to a successful sourcing relationship. Set up a plan for regular updates and feedback to ensure both parties are aligned throughout the manufacturing and delivery process.
- Utilize multiple channels: Use emails, calls, and video conferences to maintain open lines of communication.
- Document agreements: Keep records of all communications and agreements for future reference.
By following this checklist, B2B buyers can ensure they make informed decisions while sourcing blade manufacturers, leading to successful partnerships and high-quality products.
Comprehensive Cost and Pricing Analysis for blade manufacturer Sourcing
What Are the Key Cost Components in Blade Manufacturing?
Understanding the cost structure of blade manufacturing is crucial for B2B buyers aiming to make informed purchasing decisions. The main components that contribute to the overall cost include:
-
Materials: The choice of raw materials significantly influences the pricing. High-quality steel or specialized alloys will increase costs but may enhance performance and longevity.
-
Labor: Skilled labor is essential for precision manufacturing. Labor costs vary by region; for instance, manufacturers in Europe may have higher labor costs compared to those in Africa or South America.
-
Manufacturing Overhead: This includes utilities, facility maintenance, and administrative expenses. Efficient manufacturing processes can help reduce overhead, impacting the final price.
-
Tooling: The cost of tools and machinery used in production is a significant factor. Custom tooling for specialized blade designs can escalate initial costs but may be necessary for bespoke orders.
-
Quality Control (QC): Ensuring that blades meet safety and performance standards requires investment in quality control processes. This is particularly important for industries like aerospace or automotive, where standards are stringent.
-
Logistics: Shipping and handling costs can vary widely based on distance, mode of transportation, and the chosen Incoterms. Buyers should be aware of these costs, especially for international transactions.
-
Margin: Manufacturers typically add a profit margin to cover risks and business sustainability. This can vary based on market conditions and competitive landscape.
How Do Price Influencers Affect Blade Manufacturing Costs?
Several factors influence the pricing of blades, impacting the total cost for buyers:
-
Volume and Minimum Order Quantity (MOQ): Larger orders often lead to discounts due to economies of scale. Buyers should negotiate MOQs to achieve better pricing.
-
Specifications and Customization: Custom blades tailored to specific applications may incur higher costs. Buyers must weigh the benefits of customization against the additional expense.
-
Materials and Quality Certifications: The choice of materials directly affects both the performance and cost. Additionally, blades that meet international quality certifications may carry a premium.
-
Supplier Factors: The reliability and reputation of the supplier can influence pricing. Established suppliers may charge more due to their proven track record.
-
Incoterms: Understanding Incoterms is vital for international buyers. They dictate the responsibilities of buyers and sellers in shipping, which can affect overall costs.
What Are Effective Buyer Tips for Cost-Efficient Blade Sourcing?
For international B2B buyers, particularly from Africa, South America, the Middle East, and Europe, here are several actionable insights:
-
Negotiate Terms: Always negotiate pricing, payment terms, and delivery schedules. Suppliers may offer better deals for long-term partnerships or larger volumes.
-
Assess Total Cost of Ownership (TCO): Consider not just the purchase price but also maintenance, operational efficiency, and lifespan of the blades. A higher upfront cost may result in lower TCO if the blades are more durable.
-
Understand Pricing Nuances: Be aware that prices can fluctuate based on market conditions, material costs, and geopolitical factors. Regularly review supplier pricing structures.
-
Leverage Regional Insights: Each region has unique cost structures and supplier networks. Utilize local knowledge to find competitive pricing and reliable suppliers.
-
Conduct Supplier Audits: Regularly evaluate suppliers for quality assurance and compliance with industry standards. This helps ensure you receive value for your investment.
What Should Buyers Keep in Mind Regarding Indicative Prices?
It is essential to note that pricing in blade manufacturing can be highly variable. Factors such as market demand, raw material availability, and currency fluctuations can lead to significant price changes. Always request updated quotes and be prepared for negotiation to ensure you secure the best possible deal.
Alternatives Analysis: Comparing blade manufacturer With Other Solutions
Understanding Alternatives to Blade Manufacturing Solutions
In the dynamic landscape of industrial manufacturing, selecting the right blade technology is crucial for optimizing performance and cost efficiency. While traditional blade manufacturers have established themselves as reliable sources, various alternative solutions can also fulfill similar needs. This analysis compares blade manufacturing with two viable alternatives: laser cutting technology and waterjet cutting systems. Each alternative presents unique advantages and challenges that can influence a B2B buyer’s decision-making process.
Comparison Table
Comparison Aspect | Blade Manufacturer | Laser Cutting Technology | Waterjet Cutting Systems |
---|---|---|---|
Performance | High precision, suitable for various materials | Exceptional speed and accuracy, ideal for thin materials | Versatile, effective on thick and brittle materials |
Cost | Moderate initial investment, lower operational costs | Higher initial costs, but lower long-term expenses | Moderate to high initial costs, dependent on system size |
Ease of Implementation | Straightforward setup, requires skilled operators | Requires training for operators, but setup is relatively simple | Complex setup, requires skilled technicians for operation |
Maintenance | Regular maintenance needed, parts may need replacing | Low maintenance, but optics require periodic checks | High maintenance due to wear on abrasive materials and pumps |
Best Use Case | General manufacturing, diverse applications | Metal fabrication, signage, and intricate designs | Aerospace, automotive, and art applications |
What Are the Advantages and Disadvantages of Laser Cutting Technology?
Laser cutting technology is renowned for its speed and precision, making it a popular choice for industries that require intricate designs and quick turnaround times. The primary advantage of laser cutting is its ability to cut through thin materials with minimal distortion, which is particularly beneficial in sectors like metal fabrication and signage production. However, the initial investment can be significantly higher than traditional blade manufacturing, which may deter some buyers. Additionally, while maintenance is generally low, operators need specific training to handle laser systems effectively.
How Does Waterjet Cutting Compare to Traditional Blade Manufacturing?
Waterjet cutting systems utilize a high-pressure jet of water, often mixed with abrasives, to cut through a wide variety of materials, including metals, glass, and ceramics. One of the significant advantages of waterjet cutting is its versatility; it can handle both thick and brittle materials without generating heat, which preserves the integrity of the material. However, the complexity of the setup and the need for skilled technicians can pose challenges for companies looking to implement this technology. Moreover, while operational costs can be favorable, ongoing maintenance can be high due to the wear on pumps and abrasives.
Conclusion: How Should B2B Buyers Choose the Right Cutting Solution?
When selecting the appropriate cutting technology, B2B buyers should consider their specific operational requirements, including the types of materials they process, the desired precision and speed, and their budget constraints. Blade manufacturing remains a reliable option for general applications, while laser cutting excels in speed and detail for thin materials. Waterjet cutting offers unmatched versatility for diverse materials, albeit with higher maintenance demands. Evaluating these alternatives in the context of their unique business needs will empower buyers to make informed decisions that enhance productivity and cost-effectiveness in their operations.
Essential Technical Properties and Trade Terminology for blade manufacturer
What Are the Essential Technical Properties for Blade Manufacturers?
When sourcing blades for industrial applications, understanding the technical specifications is crucial. Here are some of the key properties that B2B buyers should consider:
1. Material Grade
The material grade of a blade significantly impacts its durability and performance. Common materials include high-speed steel (HSS), carbide, and stainless steel. Each material has distinct properties, such as hardness, wear resistance, and corrosion resistance. For example, carbide blades are ideal for cutting hard materials, while HSS blades are better suited for general-purpose applications. Selecting the right material grade ensures that the blades will perform optimally in their intended applications.
2. Tolerance
Tolerance refers to the allowable variation in the dimensions of the blade. This specification is critical for ensuring that the blade fits correctly in its application, whether in machinery or tooling. Tight tolerances are essential in precision cutting applications, where even minor deviations can affect the quality of the finished product. Understanding tolerance requirements can help buyers avoid costly mistakes and ensure compatibility with existing equipment.
3. Coating
Blade coatings, such as titanium nitride (TiN) or diamond-like carbon (DLC), enhance performance by reducing friction and increasing wear resistance. Coatings can also provide additional protection against corrosion, extending the blade’s lifespan. When evaluating blades, consider the coating type and its suitability for the specific cutting application. This can lead to improved efficiency and reduced downtime due to blade replacements.
4. Edge Geometry
The geometry of the blade edge, including its angle and shape, determines cutting efficiency and precision. Various edge designs, such as straight, serrated, or scalloped, cater to different cutting tasks. Understanding the application requirements will guide buyers in selecting the appropriate edge geometry, which can significantly impact operational efficiency and output quality.
5. Hardness
Hardness is a measure of a material’s resistance to deformation and wear. It is typically measured on the Rockwell scale. For blades, hardness is vital as it influences cutting performance and durability. A harder blade will maintain its sharpness longer, while a softer blade may require more frequent sharpening. Evaluating hardness in relation to the intended application can help buyers achieve optimal performance.
What Are Common Trade Terms in the Blade Manufacturing Industry?
Familiarity with industry jargon can streamline communication and enhance the procurement process. Here are some essential trade terms:
1. OEM (Original Equipment Manufacturer)
An OEM is a company that produces parts or equipment that may be marketed by another manufacturer. In the context of blades, working with an OEM can ensure that buyers receive high-quality products tailored to specific needs. Understanding OEM relationships is important for buyers looking for reliability and customization in their sourcing.
2. MOQ (Minimum Order Quantity)
MOQ refers to the minimum number of units that a supplier is willing to sell in a single order. This term is crucial for budgeting and inventory management. Buyers should assess their operational needs against the MOQ set by suppliers to ensure they do not overstock or understock their inventories.
3. RFQ (Request for Quotation)
An RFQ is a document that a buyer sends to suppliers to request pricing and terms for specific products. Issuing an RFQ allows buyers to compare offers from multiple suppliers and negotiate better terms. Understanding how to effectively draft and issue RFQs can lead to cost savings and improved supplier relationships.
4. Incoterms
Incoterms (International Commercial Terms) define the responsibilities of buyers and sellers in international transactions, including shipping, insurance, and tariffs. Familiarity with these terms is vital for B2B buyers engaged in cross-border procurement, as they clarify who is responsible for various costs and risks throughout the shipping process.
5. Lead Time
Lead time is the amount of time from placing an order to receiving the product. This term is crucial for planning and supply chain management. Understanding lead times can help buyers manage production schedules and avoid delays, ensuring that they maintain efficient operations.
By grasping these technical properties and trade terms, B2B buyers can make informed decisions that optimize their procurement processes and enhance operational efficiency.
Navigating Market Dynamics and Sourcing Trends in the blade manufacturer Sector
What Are the Current Market Dynamics and Key Trends in the Blade Manufacturing Sector?
The blade manufacturing sector is undergoing significant transformation driven by various global factors. Economic growth in emerging markets such as Africa and South America is increasing demand for high-quality blades across multiple industries, including manufacturing, construction, and energy. Technological advancements in production processes—such as automation and Industry 4.0—are enhancing efficiency and reducing costs, making it crucial for international B2B buyers to stay informed about these innovations. Moreover, the integration of digital platforms for sourcing and procurement is becoming prevalent, allowing buyers to access a broader range of suppliers and streamline their purchasing processes.
Another emerging trend is the shift toward customized solutions. Buyers are increasingly seeking blades that are tailored to specific applications, which necessitates deeper collaboration between manufacturers and their clients. This trend is particularly evident in sectors like renewable energy, where specialized blades for wind turbines are in high demand. Furthermore, with the rise of e-commerce, many manufacturers are enhancing their online presence, allowing for easier access to product information and customer service, thus facilitating smoother transactions for international buyers.
How Is Sustainability and Ethical Sourcing Influencing B2B Purchasing Decisions in Blade Manufacturing?
Sustainability has become a key consideration for B2B buyers in the blade manufacturing sector. With growing awareness of environmental issues, companies are increasingly prioritizing suppliers who adhere to sustainable practices. This includes sourcing raw materials responsibly, minimizing waste, and reducing carbon footprints during the manufacturing process. For buyers from Europe, particularly in countries like the UK and Poland, compliance with strict environmental regulations is essential, making the choice of suppliers who prioritize sustainability a crucial aspect of their procurement strategy.
Moreover, ethical sourcing is gaining traction among international buyers. Companies are expected to ensure that their supply chains are free from exploitation and that workers’ rights are respected. Certifications such as ISO 14001 for environmental management and Fair Trade practices are becoming vital indicators of a supplier’s commitment to sustainability and ethical standards. By partnering with manufacturers who hold these certifications, buyers can enhance their brand reputation and meet the growing consumer demand for ethically produced products.
What Is the Evolution of the Blade Manufacturing Sector Relevant to Today’s B2B Landscape?
The blade manufacturing sector has evolved significantly over the past few decades. Initially dominated by traditional manufacturing methods, the industry has seen a shift towards advanced technologies, including CNC machining and additive manufacturing. These innovations have not only improved product quality but also reduced lead times, allowing manufacturers to respond more quickly to market demands.
Historically, the industry was heavily reliant on local suppliers; however, globalization has expanded the sourcing landscape. Buyers now have access to a wide array of international suppliers, which has increased competition and driven innovation. This evolution necessitates that B2B buyers remain agile and well-informed about global market trends, ensuring they can leverage the best sourcing opportunities available.
In conclusion, the blade manufacturing sector is characterized by dynamic market trends that emphasize technological advancements, sustainability, and ethical sourcing. International B2B buyers, particularly from Africa, South America, the Middle East, and Europe, must navigate these trends effectively to enhance their procurement strategies and maintain competitive advantage.
Frequently Asked Questions (FAQs) for B2B Buyers of blade manufacturer
-
How do I select the right blade manufacturer for my business needs?
When selecting a blade manufacturer, consider factors such as product quality, manufacturing capabilities, certifications, and customer service. Research their experience in your specific industry and ask for references or case studies. Additionally, assess their ability to customize products to meet your specifications and their responsiveness to inquiries. It’s also beneficial to evaluate their logistics capabilities to ensure timely delivery to your region. -
What are the common customization options available with blade manufacturers?
Many blade manufacturers offer customization options such as size, material, shape, and coating. Depending on your application, you may also request specific features like serration patterns or heat treatments. Before placing an order, discuss your requirements with the manufacturer to ensure they can meet your specifications while maintaining quality standards. -
What minimum order quantities (MOQs) should I expect from blade manufacturers?
Minimum order quantities can vary significantly among manufacturers. Typically, MOQs range from a few dozen to several hundred units, depending on the type of blade and the manufacturer’s production processes. It’s important to communicate your needs clearly and negotiate MOQs that align with your inventory management and budget constraints. -
What payment terms are usually offered by blade manufacturers?
Payment terms can vary widely, but many manufacturers offer options like upfront payments, net 30, or net 60 days. Some may also accept letters of credit or installment payments for larger orders. Always clarify payment terms before finalizing your order to ensure they align with your financial planning and cash flow needs. -
How can I ensure quality assurance when sourcing blades from manufacturers?
To ensure quality assurance, request certifications such as ISO 9001 or other relevant industry standards from potential manufacturers. Additionally, inquire about their quality control processes, including inspections and testing methods. If possible, visit their facility or request samples to evaluate the quality of their products before placing a larger order. -
What logistics considerations should I keep in mind when sourcing blades internationally?
When sourcing blades from international manufacturers, consider shipping times, costs, and potential customs duties. Work with manufacturers who have experience in exporting to your region and can provide clear information on logistics. Additionally, ensure that they comply with international shipping regulations and offer tracking options for your orders. -
How do I vet potential blade suppliers to avoid scams?
Vetting potential suppliers involves checking their business credentials, reviews, and industry reputation. Utilize platforms like Alibaba or ThomasNet to find verified manufacturers. Additionally, request references from previous clients and conduct background checks. Engaging in small initial orders can also help assess their reliability before committing to larger contracts. -
What role does after-sales support play in selecting a blade manufacturer?
After-sales support is crucial in ensuring ongoing satisfaction with your purchase. It includes assistance with product installation, maintenance tips, and handling any issues that may arise post-purchase. Inquire about the manufacturer’s support services, warranty policies, and responsiveness to customer inquiries to ensure you receive comprehensive support throughout the lifespan of the blades.
Important Disclaimer & Terms of Use
⚠️ Important Disclaimer
The information provided in this guide, including content regarding manufacturers, technical specifications, and market analysis, is for informational and educational purposes only. It does not constitute professional procurement advice, financial advice, or legal advice.
While we have made every effort to ensure the accuracy and timeliness of the information, we are not responsible for any errors, omissions, or outdated information. Market conditions, company details, and technical standards are subject to change.
B2B buyers must conduct their own independent and thorough due diligence before making any purchasing decisions. This includes contacting suppliers directly, verifying certifications, requesting samples, and seeking professional consultation. The risk of relying on any information in this guide is borne solely by the reader.
Strategic Sourcing Conclusion and Outlook for blade manufacturer
What Are the Key Takeaways for International B2B Buyers in Blade Manufacturing?
In conclusion, the strategic sourcing of blades is not just about cost savings; it’s about building long-term partnerships that drive innovation and efficiency. For international B2B buyers, particularly in Africa, South America, the Middle East, and Europe, understanding the dynamics of supply chains and leveraging local expertise can significantly enhance procurement outcomes. Buyers should prioritize suppliers who demonstrate sustainability practices and quality assurance to mitigate risks and ensure product reliability.
How Can Strategic Sourcing Enhance Your Business Operations?
Emphasizing strategic sourcing allows companies to optimize their operational processes, reduce lead times, and improve product quality. By fostering relationships with manufacturers who align with their business values, buyers can gain access to advanced technologies and customized solutions tailored to specific industry needs.
What’s Next for B2B Buyers in the Blade Manufacturing Sector?
As we look to the future, the blade manufacturing industry is poised for growth, driven by technological advancements and increasing demand for specialized products. Now is the time for international B2B buyers to act—evaluate potential suppliers, invest in strategic partnerships, and embrace innovation. By doing so, they can secure a competitive edge in a rapidly evolving market landscape.