Discover Top Benefits of Choosing a Roller Manufacturer (2025)
Introduction: Navigating the Global Market for roller manufacturer
As international B2B buyers seek reliable partners in the roller manufacturing sector, navigating the complexities of this global market can be a daunting challenge. With a multitude of suppliers and varying product quality, sourcing high-performance rollers tailored to specific applications—such as industrial machinery, recreational activities, or transportation—becomes critical. This guide is designed to streamline your purchasing process by providing comprehensive insights into the diverse types of rollers available, their applications, and essential supplier vetting strategies.
Understanding the intricacies of roller manufacturing is vital for businesses in regions such as Africa, South America, the Middle East, and Europe, including emerging markets like Kenya and established hubs like the UAE. This guide delves into various facets of the industry, including cost considerations, material selections, and the latest technological advancements, ensuring that you make informed decisions that align with your operational needs and budget constraints.
By equipping you with the knowledge to assess and select the right roller manufacturers, this resource empowers B2B buyers to mitigate risks and enhance supply chain efficiency. Whether you are looking to expand your product offerings or improve your existing operations, our insights will help you navigate the global roller market with confidence, ultimately fostering sustainable business relationships that drive growth and innovation.
Understanding roller manufacturer Types and Variations
Type Name | Key Distinguishing Features | Primary B2B Applications | Brief Pros & Cons for Buyers |
---|---|---|---|
Industrial Rollers | Heavy-duty materials, high load capacity | Manufacturing, logistics | Pros: Durable, high performance; Cons: Higher initial cost. |
Conveyor Rollers | Designed for material handling systems | Warehousing, distribution centers | Pros: Efficient material transport; Cons: Limited to specific applications. |
Specialty Rollers | Custom designs for unique applications | Food processing, pharmaceuticals | Pros: Tailored solutions; Cons: Longer lead times, higher costs. |
Polyurethane Rollers | Soft, non-marking surfaces | Printing, packaging | Pros: Protects surfaces, quiet operation; Cons: May wear faster under heavy loads. |
Rubber Rollers | High friction surfaces, flexible designs | Textile, automotive industries | Pros: Excellent grip; Cons: Prone to degradation from heat and chemicals. |
What Are Industrial Rollers and Their Applications?
Industrial rollers are designed to withstand heavy loads and harsh environments, making them ideal for manufacturing and logistics applications. These rollers are typically constructed from robust materials such as steel or reinforced composites, ensuring longevity and reliability. When purchasing industrial rollers, buyers should consider load capacity, environmental conditions, and potential maintenance requirements. While the initial investment may be higher, the durability and performance of these rollers often justify the cost over time.
How Do Conveyor Rollers Enhance Efficiency?
Conveyor rollers are essential for material handling systems, facilitating the smooth transport of goods in warehouses and distribution centers. These rollers are engineered for specific applications, including gravity-fed systems or powered conveyors. Buyers should evaluate the compatibility of conveyor rollers with existing systems, as well as their load ratings and operational speed. The efficiency gained from using conveyor rollers can significantly reduce labor costs and improve throughput, making them a popular choice for B2B operations.
What Are Specialty Rollers and Their Benefits?
Specialty rollers are custom-designed to meet the unique needs of various industries, such as food processing and pharmaceuticals. These rollers can be tailored in terms of size, material, and surface finish to ensure compliance with industry standards. When considering specialty rollers, B2B buyers should assess the specific requirements of their application, including hygiene standards and environmental factors. Although these rollers may have longer lead times and higher costs, they often provide significant operational advantages through enhanced performance and compliance.
Why Choose Polyurethane Rollers?
Polyurethane rollers are known for their soft, non-marking surfaces, making them particularly suitable for applications in printing and packaging. These rollers offer excellent grip and noise reduction, which can be beneficial in environments where sound levels are a concern. When selecting polyurethane rollers, buyers should consider factors such as load capacity and the potential for wear under heavy use. While they provide many advantages, their lifespan may be shorter compared to harder materials, necessitating regular replacements.
What Are the Advantages of Rubber Rollers?
Rubber rollers are widely used in industries such as textiles and automotive for their high friction surfaces and flexibility. They are designed to provide excellent grip, which is crucial for processes that require precise handling of materials. Buyers should be aware of the environmental conditions that rubber rollers will face, as exposure to heat and chemicals can lead to quicker degradation. While they offer significant benefits in terms of grip and performance, careful consideration of their operating environment is essential to maximize their lifespan and effectiveness.
Related Video: Lead Screw, Ball Screw, and Roller Screw Cylinders: What’s the Difference?
Key Industrial Applications of roller manufacturer
Industry/Sector | Specific Application of roller manufacturer | Value/Benefit for the Business | Key Sourcing Considerations for this Application |
---|---|---|---|
Manufacturing | Conveyor systems for material handling | Increases efficiency and productivity | Quality standards, durability, and customization |
Agriculture | Agricultural machinery for crop processing | Enhances operational effectiveness | Resistance to wear, environmental adaptability |
Mining | Heavy-duty machinery for ore transportation | Improves safety and reduces downtime | Load capacity, reliability under harsh conditions |
Construction | Formwork systems for concrete structures | Ensures precision and reduces labor costs | Compliance with safety regulations, material quality |
Logistics & Warehousing | Automated sorting systems for package handling | Streamlines operations and reduces labor costs | Compatibility with existing systems, scalability |
How are Rollers Used in Manufacturing and What Are the Benefits?
In the manufacturing sector, roller manufacturers provide essential components for conveyor systems that facilitate material handling. By implementing high-quality rollers, businesses can significantly enhance their operational efficiency and productivity. Key considerations for B2B buyers include ensuring that the rollers meet specific quality standards and are durable enough to withstand the rigors of continuous operation. Customization options are also important to fit various conveyor designs.
What Role Do Rollers Play in Agriculture?
In agriculture, rollers are critical in machinery used for crop processing, such as seeders and harvesters. They help improve the effectiveness of operations, ensuring that tasks such as planting and harvesting are executed efficiently. Buyers should prioritize sourcing rollers that are resistant to wear and can operate effectively in diverse environmental conditions, especially in regions like Africa and South America, where agricultural practices may vary significantly.
How Are Rollers Essential in the Mining Industry?
Rollers are integral to heavy-duty machinery used in mining operations, particularly for transporting ore. The use of robust rollers enhances safety and minimizes downtime, which is crucial in an industry where operational continuity is vital. For international buyers, especially in the Middle East and Africa, sourcing rollers with high load capacity and reliability under harsh conditions is essential to ensure safety and efficiency.
What Benefits Do Rollers Provide in Construction?
In the construction industry, rollers are used in formwork systems that aid in the construction of concrete structures. Their precise design ensures that concrete is poured accurately, reducing labor costs and improving project timelines. Buyers must consider compliance with safety regulations and the quality of materials used in roller manufacturing to ensure they meet the stringent demands of construction projects in Europe and beyond.
How Do Rollers Improve Efficiency in Logistics and Warehousing?
Rollers are vital in automated sorting systems utilized in logistics and warehousing, where they facilitate the efficient handling of packages. This technology streamlines operations and reduces labor costs, making it a key investment for businesses looking to enhance their logistics capabilities. Buyers should focus on sourcing rollers that are compatible with existing systems and offer scalability to adapt to future growth in their operations.
Related Video: Types of bearings and its applications
3 Common User Pain Points for ‘roller manufacturer’ & Their Solutions
Scenario 1: Difficulty Sourcing Quality Rollers from Manufacturers
The Problem:
B2B buyers often struggle to find reliable roller manufacturers who can consistently deliver high-quality products. This challenge is particularly pronounced for businesses in regions like Africa and South America, where local suppliers may lack the necessary certifications or quality control processes. Buyers may receive inconsistent product batches, leading to operational disruptions and increased costs due to returns and replacements.
The Solution:
To overcome this sourcing challenge, buyers should conduct thorough market research to identify established manufacturers with a proven track record. Utilize platforms such as trade shows, industry forums, and online marketplaces to gather reviews and ratings. Once potential suppliers are identified, request product samples and certifications to assess quality firsthand. Establish clear communication regarding quality standards and expectations before finalizing any agreements. Additionally, consider forming partnerships with manufacturers who offer customizable solutions, allowing you to tailor products to your specific needs and ensure consistency across orders.
Scenario 2: Inadequate Technical Support for Roller Maintenance
The Problem:
Another common pain point for B2B buyers is the lack of adequate technical support from roller manufacturers, especially regarding maintenance and repair. Buyers may find themselves without the necessary guidance on how to properly maintain their rollers, leading to premature wear and potential equipment failure. This is especially critical in industries like manufacturing and logistics, where equipment downtime can result in significant financial losses.
The Solution:
To address this issue, buyers should seek manufacturers that offer comprehensive after-sales support, including maintenance guides, training programs, and readily available customer service. Before purchasing, inquire about the technical support provided and whether they offer on-site training sessions for your team. Additionally, consider establishing a service contract that includes regular maintenance checks and access to technical expertise. Building a strong relationship with the manufacturer can also lead to better support, including priority access to parts and troubleshooting assistance when issues arise.
Scenario 3: Navigating Regulatory Compliance and Standards
The Problem:
B2B buyers often face the challenge of navigating various regulatory compliance requirements related to roller manufacturing and usage. This is particularly relevant for buyers in the Middle East and Europe, where strict safety and environmental regulations govern product standards. Failure to comply can result in hefty fines and damage to a company’s reputation.
The Solution:
To effectively navigate regulatory compliance, buyers should familiarize themselves with the relevant standards applicable in their region, such as ISO certifications or local safety regulations. Engage with manufacturers who are compliant with these standards and can provide documentation to prove it. It may also be beneficial to consult with legal experts or industry consultants who specialize in compliance to ensure all bases are covered. Additionally, consider implementing a compliance checklist when evaluating potential manufacturers, ensuring that all products meet the necessary regulations before making a purchase. This proactive approach minimizes risks and ensures smoother operations in the long run.
Strategic Material Selection Guide for roller manufacturer
When selecting materials for roller manufacturing, international B2B buyers must consider various factors that influence product performance, durability, and compliance with regional standards. Below, we analyze four common materials used in roller manufacturing, focusing on their properties, advantages, disadvantages, and specific considerations for buyers in Africa, South America, the Middle East, and Europe.
What Are the Key Properties of Polyurethane in Roller Manufacturing?
Polyurethane is widely recognized for its excellent abrasion resistance and flexibility, making it a top choice for roller manufacturers. It can withstand a temperature range of -30°C to 80°C and offers good chemical resistance, particularly against oils and solvents. This material’s elasticity allows for shock absorption, enhancing overall performance.
Pros and Cons:
– Pros: High durability, excellent wear resistance, and good shock absorption.
– Cons: Can be more expensive than other materials and may degrade under prolonged UV exposure.
Impact on Application:
Polyurethane rollers are ideal for applications involving heavy loads and high-speed operations, such as conveyor systems in manufacturing plants.
Considerations for International Buyers:
Buyers should ensure compliance with ASTM D2240 for hardness and ASTM D412 for tensile strength. In regions like the UAE and Kenya, local standards may also dictate specific performance criteria.
How Does Steel Compare as a Material for Roller Manufacturing?
Steel is a traditional material known for its strength and rigidity. It typically has a high-temperature rating and is resistant to deformation under heavy loads. Steel rollers can handle extreme pressures, making them suitable for industrial applications.
Pros and Cons:
– Pros: Exceptional strength, long lifespan, and cost-effectiveness.
– Cons: Heavier than other materials, prone to rust without proper coatings, and less flexible.
Impact on Application:
Steel rollers are commonly used in heavy-duty applications, such as in mining and construction, where durability is paramount.
Considerations for International Buyers:
Compliance with DIN 17100 for steel grades is crucial. Buyers in regions with high humidity, such as parts of South America, should consider additional corrosion-resistant coatings.
What Are the Advantages of Using Nylon in Roller Manufacturing?
Nylon is a lightweight material that offers good chemical resistance and low friction properties. It operates effectively within a temperature range of -40°C to 120°C, making it suitable for various environments.
Pros and Cons:
– Pros: Lightweight, low friction, and good wear resistance.
– Cons: Less load-bearing capacity compared to steel and may absorb moisture, affecting performance.
Impact on Application:
Nylon rollers are often used in applications requiring low friction, such as in packaging and printing industries.
Considerations for International Buyers:
International buyers should check compliance with JIS K 6768 for nylon materials. In regions like Europe, where environmental regulations are stringent, ensuring the material’s compliance with REACH standards is essential.
How Does Rubber Perform as a Material for Rollers?
Rubber is known for its excellent grip and shock-absorbing properties. It typically operates well in temperatures ranging from -20°C to 70°C and is resistant to wear and tear.
Pros and Cons:
– Pros: Superior grip, excellent shock absorption, and cost-effective.
– Cons: Limited temperature range and may degrade over time due to environmental factors.
Impact on Application:
Rubber rollers are ideal for applications requiring high traction, such as in material handling and automotive industries.
Considerations for International Buyers:
Buyers should ensure compliance with ASTM D2000 for rubber materials. In the Middle East, where temperatures can be extreme, selecting heat-resistant rubber compounds is crucial.
Summary Table of Material Selection for Roller Manufacturing
Material | Typical Use Case for roller manufacturer | Key Advantage | Key Disadvantage/Limitation | Relative Cost (Low/Med/High) |
---|---|---|---|---|
Polyurethane | Conveyor systems in manufacturing | High durability | UV degradation | Medium |
Steel | Heavy-duty applications in mining | Exceptional strength | Prone to rust | Low |
Nylon | Packaging and printing industries | Low friction | Less load-bearing capacity | Medium |
Rubber | Material handling and automotive | Superior grip | Limited temperature range | Low |
In conclusion, understanding the properties, advantages, and limitations of each material is essential for international B2B buyers to make informed decisions that align with their specific applications and regional compliance standards.
In-depth Look: Manufacturing Processes and Quality Assurance for roller manufacturer
What Are the Main Stages in the Manufacturing Process of Roller Products?
The manufacturing process of roller products is a complex and multi-stage operation. Understanding each phase can help B2B buyers evaluate suppliers effectively. The typical stages include:
-
Material Preparation: The first step involves selecting high-quality raw materials, such as polyurethane, rubber, or metal, depending on the type of roller being produced. The materials undergo rigorous quality checks to ensure they meet the required specifications.
-
Forming: In this stage, the prepared materials are shaped into the desired roller form. Techniques such as injection molding, extrusion, and machining are commonly used. Each technique has its advantages: for instance, injection molding is ideal for producing complex shapes with high precision, while extrusion is suitable for long continuous sections.
-
Assembly: After forming, the various components of the roller (such as bearings, seals, and cores) are assembled. This step may involve manual labor or automated processes, depending on the scale of production. Precision during assembly is crucial to ensure the longevity and performance of the final product.
-
Finishing: The finishing stage includes processes like surface treatment, coating, and polishing. These steps enhance the durability and aesthetic appeal of the rollers. For example, applying a protective coating can significantly increase resistance to wear and environmental factors.
How Is Quality Assurance Implemented in Roller Manufacturing?
Quality assurance (QA) is integral to the manufacturing process of rollers, ensuring that products meet both international standards and customer expectations. Here are key aspects of QA in roller manufacturing:
-
International Standards Compliance: Many roller manufacturers adhere to standards such as ISO 9001, which focuses on quality management systems, and industry-specific certifications like CE for safety compliance in Europe or API for oil and gas applications. These certifications provide assurance that the manufacturer meets stringent quality criteria.
-
Quality Control Checkpoints: Quality control (QC) is typically divided into several checkpoints:
– Incoming Quality Control (IQC): This stage assesses the quality of raw materials before they enter production. It ensures that only materials that meet specified criteria are used.
– In-Process Quality Control (IPQC): Throughout the manufacturing process, various checks are performed to monitor the quality of the product. This includes measuring dimensions and verifying assembly accuracy.
– Final Quality Control (FQC): Once the rollers are completed, they undergo final inspections. This step may include performance testing and visual inspections to detect any defects. -
Common Testing Methods: Various testing methods are employed to ensure the quality of the rollers. Common methods include:
– Mechanical Testing: To assess durability and strength.
– Dimensional Inspection: To confirm that products meet specified tolerances.
– Performance Testing: To evaluate the roller’s performance under operational conditions.
How Can B2B Buyers Verify Supplier Quality Control?
B2B buyers need to ensure that their suppliers maintain high-quality standards. Here are actionable steps to verify supplier quality control:
-
Conduct Supplier Audits: Regular audits of suppliers can provide insights into their manufacturing processes and quality control practices. During an audit, assess whether they comply with international standards and their internal quality management systems.
-
Request Quality Control Reports: Suppliers should be able to provide detailed quality control reports that outline their QC processes, testing results, and any corrective actions taken for defects. This transparency is crucial for establishing trust.
-
Engage Third-Party Inspectors: Utilizing third-party inspection services can provide an unbiased evaluation of the supplier’s manufacturing and quality assurance practices. These inspectors can verify compliance with industry standards and perform additional testing if necessary.
What Are the Quality Control Nuances for International B2B Buyers?
For international B2B buyers, particularly from regions like Africa, South America, the Middle East, and Europe, understanding quality control nuances is essential:
-
Cultural and Regulatory Differences: Different regions may have varying standards and regulations regarding roller manufacturing. Buyers should familiarize themselves with local compliance requirements in their target markets, such as CE marking in Europe or local safety regulations in Africa and South America.
-
Logistical Challenges: Transporting rollers across borders can introduce quality risks. Ensure that suppliers have robust packaging and handling procedures to minimize damage during transit.
-
Communication: Clear communication regarding quality expectations and standards is vital. Establishing a direct line of communication with suppliers can help resolve any issues quickly and ensure that quality expectations are consistently met.
Conclusion
Understanding the manufacturing processes and quality assurance practices of roller manufacturers is crucial for B2B buyers. By focusing on material preparation, forming, assembly, and finishing, alongside rigorous quality control measures, buyers can make informed decisions when selecting suppliers. Verifying supplier quality through audits, reports, and third-party inspections further enhances the assurance of receiving high-quality products that meet international standards.
Practical Sourcing Guide: A Step-by-Step Checklist for ‘roller manufacturer’
This guide serves as a comprehensive checklist for international B2B buyers looking to source roller manufacturers effectively. By following these actionable steps, you can ensure that you select the right supplier who meets your specific needs and standards.
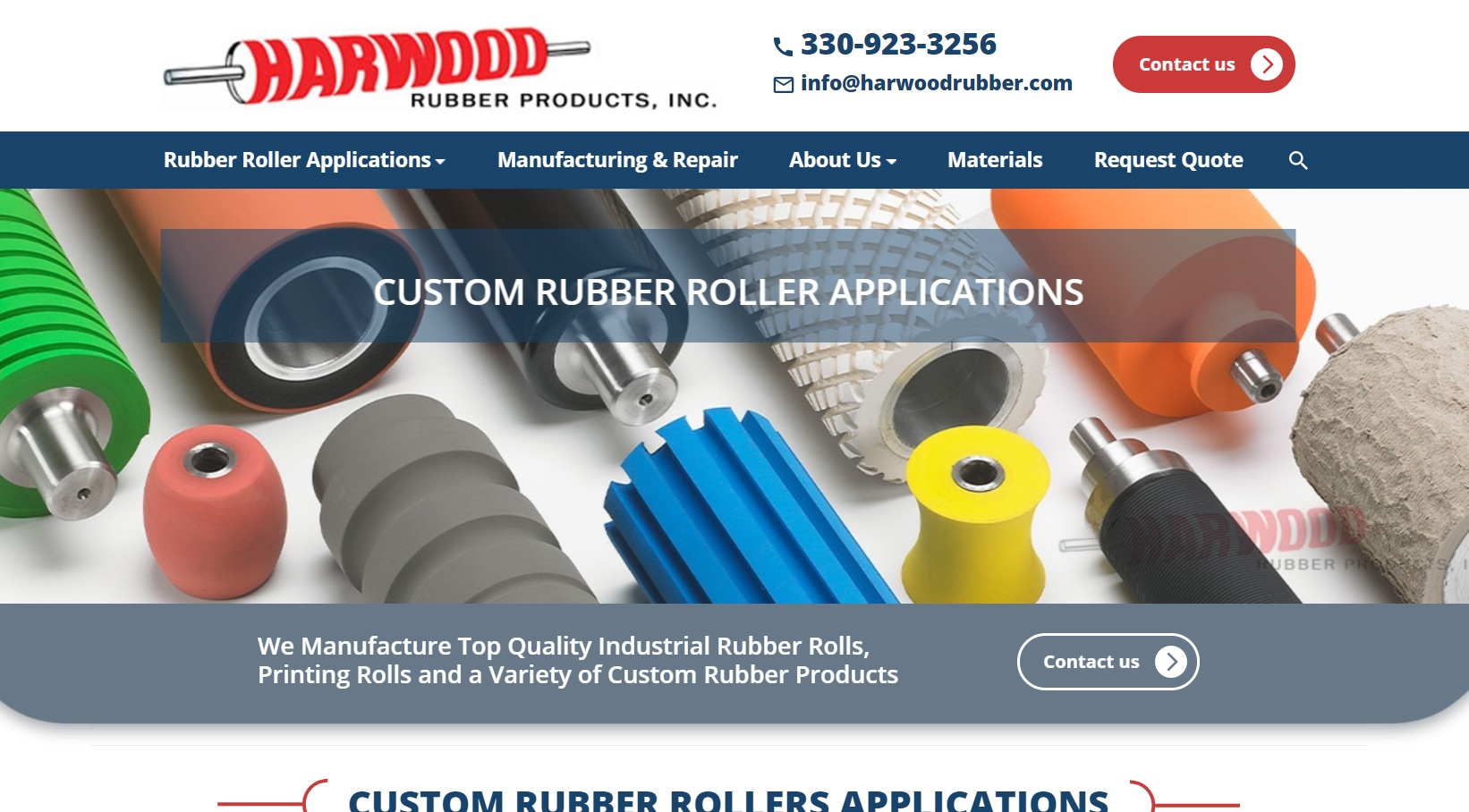
A stock image related to roller manufacturer.
Step 1: Define Your Technical Specifications
Start by clearly outlining the technical specifications required for the rollers you need. This includes dimensions, materials, load capacities, and any specific industry standards your product must adhere to. Having precise specifications helps in narrowing down potential suppliers and ensures that the products you receive will meet your operational requirements.
Step 2: Research Potential Suppliers
Conduct thorough research to identify potential roller manufacturers. Utilize industry directories, trade shows, and online platforms to find companies that specialize in roller production. Pay attention to their market presence and reputation, as this can indicate their reliability and product quality.
- Tip: Look for suppliers with experience in your specific industry, as they will be more familiar with the unique challenges and requirements you face.
Step 3: Evaluate Supplier Certifications and Compliance
Verify that the manufacturers you are considering hold relevant certifications and comply with international quality standards, such as ISO 9001. Certifications ensure that the supplier maintains quality management systems and adheres to best practices in manufacturing.
- Look for: Evidence of compliance with safety and environmental regulations, particularly if your operations are subject to strict industry oversight.
Step 4: Request Samples and Prototypes
Before making a large order, request samples or prototypes of the rollers. This step is crucial to assess the quality, durability, and suitability of the product for your application. Testing samples in real-world conditions can provide invaluable insights into their performance.
- Considerations: Evaluate the samples against your specifications and ensure they meet your expectations for quality and functionality.
Step 5: Assess Production Capabilities and Lead Times
Understand the production capabilities of your potential suppliers, including their manufacturing processes and technology. Inquire about their lead times and production capacity to ensure they can meet your demands, especially during peak seasons.
- Important: Suppliers with advanced technology and sufficient capacity can often provide better quality products and faster delivery times.
Step 6: Negotiate Pricing and Terms
Once you have shortlisted potential suppliers, engage in negotiations regarding pricing, payment terms, and delivery schedules. Ensure that all terms are clear and documented to avoid misunderstandings later on.
- Tip: Consider total cost of ownership, not just the initial price, by factoring in shipping, customs, and potential tariffs, especially for international transactions.
Step 7: Establish Communication and Support Channels
Finally, establish clear communication channels with your chosen supplier. Regular communication is essential for addressing issues, managing expectations, and fostering a strong business relationship. Ensure that you have access to customer support for any after-sales inquiries or issues.
- Why it matters: A responsive supplier can greatly enhance your operational efficiency and help resolve problems quickly, minimizing disruptions in your supply chain.
By following this checklist, you can streamline your sourcing process and make informed decisions when selecting roller manufacturers that align with your business needs.
Comprehensive Cost and Pricing Analysis for roller manufacturer Sourcing
What Are the Key Cost Components in Roller Manufacturing?
When sourcing roller manufacturers, understanding the cost structure is crucial for international B2B buyers. The primary cost components include:
-
Materials: The choice of materials significantly impacts pricing. High-quality materials such as polyurethane or rubber can increase costs but may enhance performance and durability. Buyers should evaluate material specifications to align with their operational needs.
-
Labor: Labor costs vary by region and can be influenced by local wage standards and labor availability. Countries with lower labor costs might offer competitive pricing, but this could also affect quality and production efficiency.
-
Manufacturing Overhead: This encompasses all indirect costs related to production, such as utilities, rent, and administrative expenses. Understanding the overhead structure of potential suppliers can provide insights into their pricing strategies.
-
Tooling: Custom tooling can be a significant upfront cost, particularly for bespoke roller designs. Buyers should inquire about tooling costs and the potential for amortization over large order quantities.
-
Quality Control (QC): Implementing robust QC processes adds to manufacturing costs but is essential for ensuring product reliability. Buyers should assess the QC measures employed by manufacturers to minimize the risk of defects.
-
Logistics: Shipping costs, customs duties, and insurance are vital components of the total cost of ownership. Buyers should consider logistics solutions that balance cost with delivery speed and reliability.
-
Margin: Manufacturers typically include a profit margin in their pricing, which can vary based on market demand and competition. Understanding the margin expectations can aid in negotiating better terms.
How Do Price Influencers Affect Roller Sourcing?
Several factors can influence the pricing of roller manufacturing, including:
-
Volume and Minimum Order Quantity (MOQ): Larger orders often lead to lower per-unit costs due to economies of scale. Buyers should negotiate MOQs that align with their inventory capabilities while maximizing cost efficiencies.
-
Specifications and Customization: Custom rollers with specific dimensions or features can incur additional costs. Providing detailed specifications upfront helps manufacturers give accurate quotes, reducing the likelihood of unexpected price changes.
-
Material Quality and Certifications: Higher-quality materials or those that meet specific industry certifications may come at a premium. Buyers should evaluate whether the added cost corresponds to the expected performance and safety standards.
-
Supplier Factors: Supplier reputation, experience, and geographical location can all impact pricing. Established suppliers may charge more due to their proven reliability and quality assurance practices.
-
Incoterms: Understanding Incoterms (International Commercial Terms) is crucial for managing logistics costs and responsibilities. Different terms can significantly affect landed costs and should be clearly defined in contracts.
What Are Effective Buyer Tips for Negotiating Roller Prices?
When negotiating prices with roller manufacturers, international B2B buyers should consider the following strategies:
-
Leverage Total Cost of Ownership (TCO): Instead of focusing solely on the initial purchase price, consider the long-term costs associated with maintenance, operation, and disposal of rollers. This broader view can help justify higher upfront costs for better quality products.
-
Build Relationships: Establishing strong relationships with suppliers can lead to better pricing and terms. Long-term partnerships often result in more favorable conditions, such as discounts on future orders or priority in production scheduling.
-
Research Market Trends: Stay informed about market trends and pricing benchmarks within the roller manufacturing sector. This knowledge can empower buyers during negotiations and help identify competitive pricing.
-
Be Open to Alternative Solutions: Sometimes, suppliers may suggest alternative materials or designs that can reduce costs without compromising performance. Being flexible can lead to innovative solutions that benefit both parties.
Disclaimer on Indicative Prices
Prices for roller manufacturing can fluctuate based on various factors, including market demand, currency exchange rates, and geopolitical influences. Therefore, it is essential for buyers to seek updated quotes from manufacturers and factor in the aforementioned cost components and price influencers when making purchasing decisions.
Alternatives Analysis: Comparing roller manufacturer With Other Solutions
When evaluating solutions for roller manufacturing, it is essential to consider not only the primary option but also viable alternatives that could meet specific business needs. This analysis will compare ‘roller manufacturer’ with two other methods: 3D Printing and CNC Machining. These alternatives can provide diverse benefits and limitations depending on the context of use.
Comparison Table of Roller Manufacturing Alternatives
Comparison Aspect | Roller Manufacturer | 3D Printing | CNC Machining |
---|---|---|---|
Performance | High durability and precision | Good for complex designs but variable quality | Excellent precision and finish |
Cost | Moderate initial investment | Lower for small batches but higher for large volumes | Higher due to tooling costs |
Ease of Implementation | Requires skilled labor | User-friendly with software, but requires training | Requires skilled operators |
Maintenance | Moderate; depends on machinery | Low; mostly software updates | High; regular tooling and maintenance needed |
Best Use Case | Mass production and standard parts | Prototyping and custom designs | High-volume, precision parts |
What are the Pros and Cons of 3D Printing as an Alternative to Roller Manufacturing?
Pros:
– Flexibility: 3D printing allows for rapid prototyping and the ability to create intricate designs that may be impossible with traditional methods.
– Cost-Effective for Low Volumes: Ideal for small batches or unique custom parts, reducing waste material.
Cons:
– Variable Quality: Depending on the printer and material used, the quality can fluctuate, affecting the final product’s reliability.
– Speed Limitations for Mass Production: Not as efficient as traditional methods for high-volume production, leading to longer lead times.
How Does CNC Machining Compare to Roller Manufacturing?
Pros:
– Precision: CNC machining provides exceptional accuracy and surface finish, making it suitable for high-tolerance components.
– Scalability: Capable of handling large production runs effectively once the initial setup is complete.
Cons:
– Higher Initial Costs: Significant investment in machinery and tooling can be a barrier for small businesses or startups.
– Skilled Labor Requirement: Operates best with trained professionals, which can lead to increased labor costs and training needs.
Conclusion: How Can B2B Buyers Choose the Right Solution?
When selecting between roller manufacturing and its alternatives, B2B buyers should evaluate their specific needs, such as production volume, design complexity, and budget constraints. For businesses focused on mass production and standardization, traditional roller manufacturing remains a strong candidate. However, if innovation and customization are key, 3D printing may offer the flexibility needed for rapid development. On the other hand, CNC machining is best suited for projects requiring precision and scalability. Understanding these dynamics will allow international buyers, particularly from Africa, South America, the Middle East, and Europe, to make informed decisions that align with their operational goals and market demands.
Essential Technical Properties and Trade Terminology for roller manufacturer
What Are the Key Technical Properties for Roller Manufacturing?
Understanding the essential technical properties of rollers is crucial for international B2B buyers, especially when sourcing from manufacturers across Africa, South America, the Middle East, and Europe. Here are some critical specifications to consider:
-
Material Grade
– Definition: The quality and type of material used in roller manufacturing, such as steel, aluminum, or composite materials.
– B2B Importance: Material grade affects durability, weight, and resistance to environmental factors. Buyers should select a material that aligns with the intended application, ensuring longevity and performance. -
Tolerance
– Definition: The allowable variation in dimensions and physical properties of a roller.
– B2B Importance: Tight tolerances are essential for ensuring that rollers fit precisely in their applications. Poor tolerances can lead to premature wear or failure, impacting operational efficiency and safety. -
Load Capacity
– Definition: The maximum weight that a roller can support without failure.
– B2B Importance: Understanding load capacity is vital for ensuring that the selected roller can handle the specific demands of the application. This knowledge helps prevent costly downtimes and replacements. -
Surface Finish
– Definition: The texture and smoothness of the roller’s surface, which can be influenced by the manufacturing process.
– B2B Importance: A proper surface finish minimizes friction and wear, improving performance and extending the roller’s life. Buyers should consider the surface finish in relation to the operating environment. -
Operating Temperature Range
– Definition: The range of temperatures within which a roller can operate effectively.
– B2B Importance: Different applications may expose rollers to extreme temperatures. Understanding this specification ensures that the roller will perform optimally under varying conditions, reducing the risk of failure.
Which Trade Terminology Should B2B Buyers Understand?
Familiarity with trade terminology can streamline communication and negotiations in the roller manufacturing industry. Here are some common terms that buyers should know:
-
OEM (Original Equipment Manufacturer)
– Definition: A company that produces parts or equipment that may be marketed by another manufacturer.
– Importance: Understanding OEM relationships can help buyers identify quality and reliability in parts used for rollers, ensuring they meet the required specifications. -
MOQ (Minimum Order Quantity)
– Definition: The smallest quantity of a product that a supplier is willing to sell.
– Importance: Knowing the MOQ helps buyers gauge whether they can meet the supplier’s requirements without overcommitting resources, which is especially critical for smaller businesses. -
RFQ (Request for Quotation)
– Definition: A document sent to suppliers asking for a price quote for specific goods or services.
– Importance: Issuing an RFQ allows buyers to compare prices and terms from different suppliers, facilitating informed purchasing decisions. -
Incoterms (International Commercial Terms)
– Definition: A set of rules that define the responsibilities of sellers and buyers in international transactions.
– Importance: Familiarity with Incoterms helps buyers understand shipping costs, risks, and responsibilities, ensuring clarity in contracts and avoiding disputes. -
Lead Time
– Definition: The total time it takes from placing an order until it is delivered.
– Importance: Understanding lead times is crucial for effective inventory management and planning, particularly in just-in-time manufacturing environments.
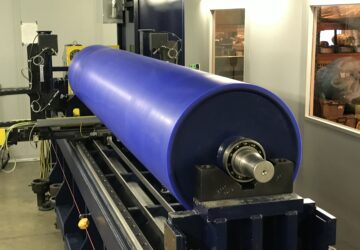
A stock image related to roller manufacturer.
- Certification Standards
– Definition: Compliance with specific industry standards and regulations (e.g., ISO certifications).
– Importance: Certifications assure buyers of the quality and safety of the rollers, making it easier to meet regulatory requirements in their respective markets.
By grasping these technical properties and trade terms, B2B buyers can make informed decisions, ensuring that their roller purchases meet operational needs while optimizing cost and performance.
Navigating Market Dynamics and Sourcing Trends in the roller manufacturer Sector
What Are the Key Market Dynamics and Sourcing Trends in the Roller Manufacturer Sector?
The roller manufacturing sector is experiencing significant transformation driven by technological advancements, shifting consumer preferences, and global market dynamics. As international B2B buyers from regions such as Africa, South America, the Middle East, and Europe (including countries like the UAE and Kenya) explore sourcing opportunities, understanding these trends is essential.
One of the primary drivers is the increasing demand for high-performance rollers in various applications, including industrial machinery, transportation, and sports equipment. This demand is fueled by the growth of manufacturing and logistics sectors globally, particularly in developing markets where infrastructure development is a priority. The introduction of smart manufacturing technologies, such as IoT and AI, is reshaping production processes, enhancing efficiency, and reducing costs. For B2B buyers, this translates to better quality products and more competitive pricing.
Another emerging trend is the shift towards digital sourcing platforms that facilitate easier access to suppliers and manufacturers. These platforms allow buyers to compare products, read reviews, and engage directly with manufacturers, streamlining the procurement process. Buyers from different regions should leverage these digital tools to enhance their sourcing strategies and make informed decisions.
How Important Is Sustainability and Ethical Sourcing in the Roller Manufacturer Sector?
Sustainability and ethical sourcing are becoming increasingly critical in the roller manufacturing sector. The environmental impact of manufacturing processes and materials used in roller production cannot be overlooked. International B2B buyers are increasingly prioritizing suppliers who demonstrate a commitment to sustainable practices. This includes the use of eco-friendly materials, energy-efficient manufacturing processes, and waste reduction strategies.
Moreover, ethical supply chains are crucial for building brand reputation and consumer trust. Buyers should look for manufacturers that are certified with ‘green’ certifications, such as ISO 14001 for environmental management, or those utilizing recycled materials in their products. These certifications not only signify compliance with international standards but also enhance the overall sustainability profile of the products.
For buyers from Africa, South America, the Middle East, and Europe, aligning with manufacturers that prioritize sustainability can lead to long-term partnerships and improved market positioning. As regulations around environmental impact tighten globally, early adoption of sustainable sourcing practices will provide a competitive edge.
What Is the Brief Evolution and History of the Roller Manufacturing Sector?
The roller manufacturing sector has evolved significantly over the past few decades. Initially dominated by traditional manufacturing methods, the industry has embraced modernization through advanced technologies. The introduction of synthetic materials in the mid-20th century marked a turning point, allowing for lighter, more durable, and versatile rollers suitable for various applications.
As global trade expanded, manufacturers began to focus on customization and specialization, catering to diverse markets from industrial to recreational sectors. The rise of e-commerce and digital marketplaces has further propelled the industry, enabling manufacturers to reach international buyers directly. Understanding this evolution helps B2B buyers appreciate the current landscape and the potential for innovation within the roller manufacturing sector.
In conclusion, navigating the market dynamics and sourcing trends in the roller manufacturer sector requires a keen awareness of technological advancements, sustainability imperatives, and historical context. By leveraging these insights, international B2B buyers can make informed decisions and foster successful partnerships in a rapidly changing environment.
Frequently Asked Questions (FAQs) for B2B Buyers of roller manufacturer
-
How do I choose the right roller manufacturer for my business needs?
Choosing the right roller manufacturer involves assessing several key factors. Start by evaluating the manufacturer’s experience and reputation in the industry. Look for certifications and compliance with international quality standards. Additionally, consider their production capacity, lead times, and ability to customize products according to your specifications. Gathering testimonials and case studies from previous clients can also provide insights into their reliability and product quality. Finally, initiate direct communication to gauge their customer service and responsiveness to your inquiries. -
What are the typical minimum order quantities (MOQs) for roller products?
Minimum order quantities (MOQs) can vary significantly among roller manufacturers, often ranging from 100 to 1,000 units depending on the product type and complexity. It’s essential to discuss your specific requirements with potential suppliers to understand their MOQ policies. Some manufacturers may offer flexibility for first-time buyers or smaller businesses, while others may have strict minimums to ensure production efficiency. Always inquire about the possibility of lower MOQs for customized products, as this could be a viable option depending on the manufacturer.
-
What payment terms should I expect when sourcing rollers internationally?
Payment terms can differ widely based on the manufacturer and your negotiation capabilities. Common practices include a deposit (typically 30-50%) upfront, with the balance due before shipment or upon delivery. Some suppliers may also accept letters of credit or offer financing options for larger orders. Be sure to clarify all payment terms in the contract, including any penalties for late payments or discounts for early settlement. It’s advisable to use secure payment methods to mitigate risks associated with international transactions. -
How can I ensure quality assurance when sourcing rollers from manufacturers?
To ensure quality assurance, start by requesting samples of the rollers to evaluate their quality firsthand. It’s also beneficial to ask about the manufacturer’s quality control processes, including certifications such as ISO 9001. Consider conducting audits or inspections during the production process, especially for large orders. Additionally, establish clear specifications and standards within your purchase agreement. Collaborating closely with the manufacturer throughout the production process can also help maintain quality. -
What are the key considerations for logistics when importing rollers?
Logistics is critical when importing rollers, involving factors such as shipping methods, customs clearance, and delivery timelines. Determine the most suitable shipping method (air, sea, or land) based on your urgency and budget. Understand the customs regulations in your country and ensure that all necessary documentation is prepared to avoid delays. Partnering with a reliable freight forwarder can streamline the logistics process, ensuring timely and efficient delivery. Be aware of additional costs like duties, taxes, and insurance to avoid unexpected expenses. -
What customization options are available when ordering rollers?
Many roller manufacturers offer customization options, including size, material, color, and design features. When discussing your needs with potential suppliers, be specific about your requirements and inquire about their capabilities for customization. Some manufacturers may provide design services or assist in developing prototypes. Keep in mind that custom orders may have higher MOQs and longer lead times, so factor these elements into your planning and budget accordingly. -
How can I vet a roller manufacturer to avoid potential risks?
To vet a roller manufacturer, conduct thorough research on their business history, financial stability, and reputation. Request references from other clients and check online reviews or industry forums for feedback on their performance. Evaluate their production facilities and quality control measures by requesting factory visits or third-party inspections. Additionally, verify their certifications and compliance with relevant industry standards. Establishing a clear communication channel throughout the vetting process can also help build trust and transparency. -
What should I do if I encounter issues with my roller order?
If you encounter issues with your roller order, such as defects or delays, promptly communicate with the manufacturer. Document the problem with clear evidence, including photos and descriptions, to facilitate a constructive discussion. Most reputable manufacturers will have policies in place for addressing such issues, including returns, exchanges, or refunds. If resolution attempts fail, consider escalating the matter through formal channels or seeking legal advice. Always maintain records of all communications to support your case.
Important Disclaimer & Terms of Use
⚠️ Important Disclaimer
The information provided in this guide, including content regarding manufacturers, technical specifications, and market analysis, is for informational and educational purposes only. It does not constitute professional procurement advice, financial advice, or legal advice.
While we have made every effort to ensure the accuracy and timeliness of the information, we are not responsible for any errors, omissions, or outdated information. Market conditions, company details, and technical standards are subject to change.
B2B buyers must conduct their own independent and thorough due diligence before making any purchasing decisions. This includes contacting suppliers directly, verifying certifications, requesting samples, and seeking professional consultation. The risk of relying on any information in this guide is borne solely by the reader.
Strategic Sourcing Conclusion and Outlook for roller manufacturer
In the evolving landscape of roller manufacturing, strategic sourcing has emerged as a critical factor for international B2B buyers. By understanding supplier capabilities, market trends, and regional demands, companies can optimize their procurement processes. This not only reduces costs but also enhances product quality and ensures timely delivery, which is vital for maintaining competitive advantage.
For buyers in regions such as Africa, South America, the Middle East, and Europe, leveraging strategic sourcing can unlock significant opportunities. Engaging with manufacturers who prioritize sustainable practices and innovative technologies can lead to superior product offerings and improved supply chain resilience. Furthermore, building strong relationships with suppliers fosters collaboration and responsiveness to market changes.
Looking ahead, as the demand for high-quality roller products continues to grow, it is essential for international B2B buyers to adopt a proactive approach to sourcing. Embrace the opportunity to explore diverse markets and build partnerships that align with your business objectives. The future of roller manufacturing is promising; seize this moment to enhance your sourcing strategies and drive your business forward.