Cut Costs with the Best Brake Pads Supplier Guide (2025)
Introduction: Navigating the Global Market for brake pads supplier
Navigating the global market for brake pads suppliers can be a daunting task for international B2B buyers, especially when faced with diverse supplier options and varying product standards. As businesses look to source high-quality brake pads that meet safety and performance standards, they often encounter challenges such as inconsistent quality, lack of transparency, and fluctuating prices. This comprehensive guide addresses these issues by providing a detailed overview of the brake pad market, covering types of brake pads, their applications across different vehicles, and essential supplier vetting processes.
International B2B buyers, particularly those from Africa, South America, the Middle East, and Europe, will benefit from actionable insights into sourcing strategies, pricing structures, and key factors influencing purchasing decisions. Whether you are a fleet manager in South America looking to optimize your supply chain or a distributor in Europe aiming to diversify your product offerings, this guide empowers you to make informed decisions that enhance operational efficiency and ensure compliance with local regulations.
In the sections that follow, we will explore the various types of brake pads available, their specific applications, and how to evaluate suppliers effectively. Additionally, we will delve into cost considerations, helping you to budget appropriately and negotiate better deals. By the end of this guide, you will be equipped with the knowledge needed to navigate the complexities of sourcing brake pads in today’s global market.
Understanding brake pads supplier Types and Variations
Type Name | Key Distinguishing Features | Primary B2B Applications | Brief Pros & Cons for Buyers |
---|---|---|---|
Organic Brake Pads | Made from natural materials, low dust emissions | Light-duty vehicles, fleet services | Pros: Eco-friendly, quieter operation. Cons: Shorter lifespan compared to others. |
Semi-Metallic Brake Pads | Mixture of metal fibers and resin for durability | Heavy-duty vehicles, performance cars | Pros: Excellent heat dissipation, longer lifespan. Cons: Can be noisier, more dust. |
Ceramic Brake Pads | Composed of ceramic fibers, quieter and cleaner | Passenger vehicles, luxury cars | Pros: Low dust, quieter operation. Cons: Higher cost, less effective under extreme conditions. |
Low-Metallic Brake Pads | Contain a small percentage of metal for performance | Sports cars, performance vehicles | Pros: Good performance and fade resistance. Cons: Higher noise levels, more dust. |
Carbon-Composite Brake Pads | Advanced materials for high performance | Motorsports, high-performance vehicles | Pros: Lightweight, exceptional heat resistance. Cons: Very expensive, specific applications only. |
What Are the Characteristics of Organic Brake Pads for B2B Buyers?
Organic brake pads are primarily made from natural materials such as rubber, fiber, and other organic compounds. They are ideal for light-duty vehicles and fleet services due to their eco-friendly nature and low dust emissions. Buyers should consider their application needs, as while these pads offer a quieter ride, they typically have a shorter lifespan compared to other options. This makes them suitable for businesses focused on sustainability but may lead to increased replacement frequency.
How Do Semi-Metallic Brake Pads Stand Out in Performance?
Semi-metallic brake pads are composed of a mix of metal fibers and resin, offering a balance of durability and performance. They are commonly used in heavy-duty vehicles and performance cars due to their excellent heat dissipation and longer lifespan. However, B2B buyers should be aware that these pads can generate more noise and dust, which may not align with the operational environment of all businesses. Therefore, evaluating the specific performance needs and noise tolerance is essential.
Why Choose Ceramic Brake Pads for Passenger Vehicles?
Ceramic brake pads are made from ceramic fibers and are known for their quiet operation and low dust production, making them particularly suited for passenger and luxury vehicles. B2B buyers may appreciate their durability and performance in everyday driving conditions. However, they come at a higher price point and may not perform as well under extreme braking conditions, making it crucial to assess the typical usage scenarios before making a purchase.
What Are the Advantages of Low-Metallic Brake Pads?
Low-metallic brake pads contain a small percentage of metal, which enhances their performance and fade resistance. They are suitable for sports cars and performance vehicles, providing good stopping power. However, these pads can be noisier and produce more dust compared to organic or ceramic options. B2B buyers should weigh the importance of performance against potential maintenance implications, especially in environments sensitive to noise and cleanliness.
When to Consider Carbon-Composite Brake Pads for Your Fleet?
Carbon-composite brake pads utilize advanced materials designed for high-performance applications, such as motorsports and specialized vehicles. They are lightweight and provide exceptional heat resistance, which can be critical in high-stress situations. However, these pads are usually more expensive and intended for specific applications. B2B buyers should carefully evaluate their operational requirements and budget constraints before opting for this high-end solution.
Related Video: The Best Brake Pads in the World and Why
Key Industrial Applications of brake pads supplier
Industry/Sector | Specific Application of brake pads supplier | Value/Benefit for the Business | Key Sourcing Considerations for this Application |
---|---|---|---|
Automotive | Supply of brake pads for passenger and commercial vehicles | Enhanced vehicle safety and performance, reducing liability risks | Quality certifications, compatibility with vehicle models, lead times |
Heavy Machinery | Brake pads for construction and mining equipment | Improved equipment reliability and reduced downtime | Custom specifications, durability requirements, environmental conditions |
Rail Transport | Brake pads for trains and trams | Enhanced braking performance, safety compliance | Compliance with safety regulations, material specifications, bulk purchasing |
Aerospace | Brake pads for aircraft landing gear | Critical for safety and performance in aviation | High-performance materials, rigorous testing standards, traceability |
Industrial Equipment | Brake pads for forklifts and conveyor systems | Increased operational efficiency and safety | Specific load capacities, compatibility with existing systems, supplier reliability |
What Are the Key Applications of Brake Pads in the Automotive Sector?
In the automotive industry, brake pads are essential components for both passenger and commercial vehicles. They ensure effective stopping power, contributing significantly to vehicle safety. International buyers must consider the compatibility of brake pads with various vehicle models and the need for quality certifications. Suppliers should provide detailed specifications to meet different regulatory standards across regions, particularly for markets in Africa, South America, the Middle East, and Europe.
How Do Brake Pads Enhance Safety in Heavy Machinery?
Brake pads used in heavy machinery, such as construction and mining equipment, play a crucial role in enhancing operational safety and efficiency. These pads must withstand extreme conditions, including high pressures and temperatures. Buyers from industries that rely on heavy machinery should prioritize suppliers who can customize brake pads to meet specific durability requirements. Additionally, evaluating the supplier’s reputation for reliability can mitigate risks associated with equipment downtime.
What is the Role of Brake Pads in Rail Transport?
In the rail transport sector, brake pads are vital for the safe operation of trains and trams. They must deliver consistent braking performance under varying loads and speeds. Buyers should ensure that their suppliers comply with stringent safety regulations and offer materials that meet specific performance metrics. Bulk purchasing agreements can be advantageous for maintaining a steady supply chain, especially in regions with extensive rail networks.
Why Are Aerospace Brake Pads Critical for Aircraft Safety?
Aerospace applications require brake pads that meet the highest safety and performance standards. These pads are critical for aircraft landing gear, where reliability is paramount. International buyers in the aerospace sector must source brake pads that utilize high-performance materials and undergo rigorous testing. Traceability of materials is also essential to meet regulatory compliance, making it vital to partner with suppliers who demonstrate transparency in their manufacturing processes.
How Do Brake Pads Improve Efficiency in Industrial Equipment?
In industrial settings, brake pads are integral to the safe operation of forklifts and conveyor systems. They enhance operational efficiency by providing reliable stopping power, which reduces the risk of accidents. Buyers should look for suppliers who can meet specific load capacity requirements and ensure compatibility with existing machinery. Reliability and supplier responsiveness are also key factors, particularly in fast-paced industrial environments where downtime can significantly impact productivity.
3 Common User Pain Points for ‘brake pads supplier’ & Their Solutions
Scenario 1: Difficulty in Ensuring Quality and Compliance with Brake Pads
The Problem:
International B2B buyers often face challenges in ensuring that the brake pads they purchase meet industry standards and regulations specific to their markets. For instance, buyers in Europe must comply with stringent EU regulations regarding vehicle safety, whereas those in South America or Africa might deal with varying local standards. This inconsistency can lead to costly mistakes, including product recalls, legal liabilities, and damage to reputation if subpar products are used. Furthermore, buyers may not have the means to conduct thorough quality checks on their own, leading to uncertainty about what they are actually receiving from suppliers.
The Solution:
To navigate this challenge, B2B buyers should establish clear quality specifications before sourcing brake pads. This includes defining the necessary certifications (e.g., ISO, ECE R90) and requiring suppliers to provide documentation proving compliance. Engage in partnerships with reputable suppliers who have a proven track record of meeting international quality standards. Additionally, buyers can leverage third-party quality assurance services that specialize in automotive parts to conduct inspections and audits before shipment. This proactive approach not only ensures compliance but also builds a trustworthy relationship with suppliers, ultimately leading to better product quality.
Scenario 2: Long Lead Times and Unreliable Delivery Schedules
The Problem:
Many B2B buyers experience frustration with long lead times and unreliable delivery schedules when sourcing brake pads from suppliers. This can be particularly problematic for businesses operating in just-in-time (JIT) environments, where delays can halt production lines and lead to significant financial losses. Buyers from regions such as Africa and the Middle East may face additional logistical challenges due to limited infrastructure or political instability, further complicating timely deliveries.
The Solution:
To mitigate these risks, buyers should implement a multi-supplier strategy. By diversifying their supplier base, they can avoid over-reliance on a single source, which can lead to delays. Establishing clear communication channels with suppliers about expected delivery timelines is also crucial. Buyers should consider negotiating contractual terms that include penalties for late deliveries to incentivize timely fulfillment. Furthermore, utilizing advanced supply chain management software can help track orders and shipments in real-time, allowing businesses to adapt quickly to potential delays and maintain operational continuity.
Scenario 3: Challenges in Customization and Compatibility of Brake Pads
The Problem:
International buyers often encounter difficulties when trying to source brake pads that fit specific vehicle models or meet unique performance specifications. This challenge can be particularly acute in regions where vehicles are not standardized, leading to a mismatch between the brake pads supplied and the actual requirements of the vehicles in use. This can result in suboptimal performance, increased wear, and potential safety hazards.
The Solution:
To address these compatibility issues, buyers should invest time in detailed market research to understand the specific brake pad needs for the vehicles they service. This includes gathering data on popular vehicle models in their region and the corresponding brake specifications. When engaging with suppliers, buyers should clearly communicate these requirements and ask for samples to test compatibility before placing large orders. Additionally, buyers can collaborate with suppliers who offer customization options, allowing them to tailor products to their exact specifications. Building a strong relationship with suppliers who understand the local market dynamics can also facilitate better product offerings that meet unique needs.
Strategic Material Selection Guide for brake pads supplier
When selecting brake pad materials, international B2B buyers must consider various factors that affect performance, durability, and compliance with regional standards. Below is an analysis of four common materials used in brake pad manufacturing, focusing on their properties, advantages, disadvantages, and implications for buyers from Africa, South America, the Middle East, and Europe.
What Are the Key Properties of Organic Brake Pad Materials?
Organic brake pads, often made from a mixture of fibers, fillers, and resins, are known for their low noise and dust production. They typically have a temperature rating of up to 300°C and offer good initial bite and modulation. However, they may wear out faster under high-stress conditions.
Pros:
– Low cost and easy to manufacture.
– Excellent for everyday driving conditions.
– Minimal wear on rotors.
Cons:
– Reduced performance in high-temperature scenarios.
– Shorter lifespan compared to other materials.
Impact on Application:
Organic materials are suitable for light-duty vehicles and urban driving, where high performance is not critical.
Considerations for Buyers:
Buyers should ensure compliance with local standards, such as ASTM or DIN, and consider the climate in their region, as organic materials may not perform well in extreme heat.
How Do Semi-Metallic Brake Pads Perform?
Semi-metallic brake pads contain a blend of metal fibers (like copper) and other materials. They can withstand higher temperatures (up to 600°C) and provide excellent braking performance, especially in demanding conditions.
Pros:
– Superior heat dissipation and performance under stress.
– Longer lifespan compared to organic pads.
– Good resistance to fade.
Cons:
– Can produce more noise and dust.
– Higher rotor wear due to metallic content.
Impact on Application:
These pads are suitable for high-performance vehicles and heavy-duty applications, making them ideal for regions with rugged terrain.
Considerations for Buyers:
International buyers should verify that the materials meet local regulations regarding copper content, especially in regions like California, where strict environmental laws apply.
What Are the Advantages of Ceramic Brake Pads?
Ceramic brake pads are made from ceramic fibers and other materials, offering a balance between performance and noise reduction. They typically operate effectively up to 400°C and are known for their longevity and low dust production.
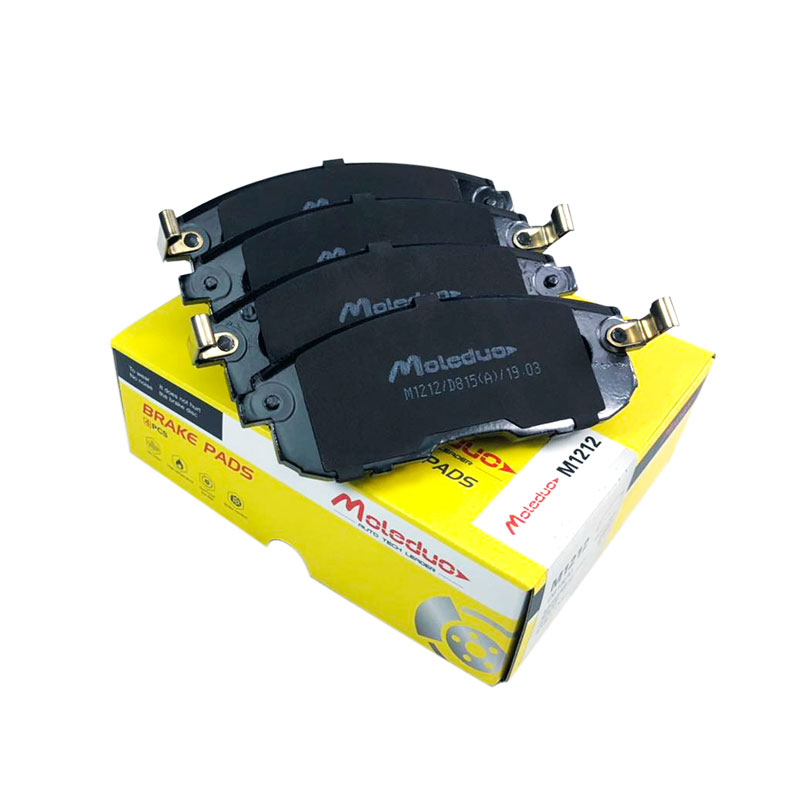
A stock image related to brake pads supplier.
Pros:
– Quiet operation and minimal dust.
– Longer lifespan than organic pads.
– Consistent performance across various temperatures.
Cons:
– Higher initial cost.
– May not perform as well under extreme conditions compared to semi-metallic pads.
Impact on Application:
Ceramic pads are ideal for passenger vehicles and light trucks, especially in urban environments.
Considerations for Buyers:
B2B buyers should assess the cost-benefit ratio, particularly in regions where budget constraints are significant, such as parts of Africa and South America.
Why Are Carbon-Composite Brake Pads Gaining Popularity?
Carbon-composite brake pads, made from a blend of carbon fibers and other materials, offer high performance and durability. They can withstand temperatures up to 800°C, making them suitable for high-performance applications.
Pros:
– Exceptional heat resistance and performance.
– Lightweight, reducing overall vehicle weight.
– Low wear on rotors.
Cons:
– Very high manufacturing costs.
– Limited availability compared to other materials.
Impact on Application:
These pads are primarily used in motorsport and high-performance vehicles, where cost is less of a concern compared to performance.
Considerations for Buyers:
Buyers in regions with a strong automotive performance market, like Europe, should consider the long-term benefits despite the initial investment.
Summary Table of Brake Pad Materials
Material | Typical Use Case for brake pads supplier | Key Advantage | Key Disadvantage/Limitation | Relative Cost (Low/Med/High) |
---|---|---|---|---|
Organic | Everyday passenger vehicles | Low cost and quiet operation | Short lifespan under high stress | Low |
Semi-Metallic | Heavy-duty and performance vehicles | Superior heat resistance | Higher rotor wear and noise | Medium |
Ceramic | Passenger vehicles and light trucks | Long lifespan and low dust | Higher initial cost | Medium |
Carbon-Composite | Motorsport and high-performance vehicles | Exceptional performance and lightweight | Very high manufacturing costs | High |
This strategic material selection guide provides valuable insights for B2B buyers, enabling informed decisions based on performance, cost, and regional compliance.
In-depth Look: Manufacturing Processes and Quality Assurance for brake pads supplier
What Are the Main Stages of Brake Pad Manufacturing?
The manufacturing process for brake pads involves several critical stages, each designed to ensure that the final product meets stringent performance and safety standards. Understanding these stages can help B2B buyers identify reliable suppliers.
1. Material Preparation
The first step in brake pad manufacturing is the preparation of raw materials. Brake pads are typically made from a blend of materials, including:
- Friction materials: These can be organic, semi-metallic, or ceramic compounds, each offering different performance characteristics.
- Backing plates: Usually made of steel or aluminum, these plates provide structural integrity.
- Adhesives and fillers: Used to bind the friction materials to the backing plate and enhance performance.
During this stage, suppliers must ensure that all materials meet international quality standards and specifications.
2. Forming
Once the materials are prepared, the next stage is forming the brake pads. This typically involves:
- Mixing: The friction materials are blended to achieve the desired properties.
- Molding: The mixture is pressed into molds under high pressure to form the brake pad shape.
- Curing: The molded pads are then cured in ovens to harden the materials and ensure structural integrity.
This process is critical for achieving uniformity and consistency in the brake pads, which directly affects performance.
3. Assembly
After forming, the brake pads are assembled. This includes:
- Attaching backing plates: The cured friction material is bonded to the backing plate using high-strength adhesives or mechanical fasteners.
- Quality checks: Initial quality control checks are performed to identify any defects before moving to the finishing stage.
Effective assembly ensures that the brake pads will perform reliably under various driving conditions.
4. Finishing
The finishing stage involves several steps to ensure the brake pads meet all specifications:
- Surface finishing: Pads are ground to achieve a smooth surface, which enhances contact with the brake rotor.
- Coating: Some manufacturers apply protective coatings to reduce corrosion and improve longevity.
- Final inspection: A thorough inspection is conducted to ensure that the pads meet design specifications and quality standards.
This stage is essential for ensuring that the brake pads will function effectively and safely in real-world conditions.
How Is Quality Assurance Implemented in Brake Pad Manufacturing?
Quality assurance (QA) is integral to the brake pad manufacturing process. Suppliers must adhere to both international and industry-specific standards to ensure product safety and reliability.
Relevant International Standards
International standards play a vital role in the manufacturing of brake pads. Key standards include:
- ISO 9001: This standard focuses on quality management systems and is crucial for ensuring consistent product quality.
- ISO 14001: Environmental management is increasingly important, especially for buyers focused on sustainability.
- CE Marking: For products sold in Europe, CE marking indicates compliance with EU safety, health, and environmental protection standards.
Understanding these standards can help B2B buyers evaluate potential suppliers.
What Are the Key Quality Control Checkpoints?
Effective quality control involves multiple checkpoints throughout the manufacturing process:
- Incoming Quality Control (IQC): Raw materials are inspected upon arrival to ensure they meet specified standards.
- In-Process Quality Control (IPQC): Continuous monitoring occurs during the manufacturing stages to detect any deviations from quality standards.
- Final Quality Control (FQC): The finished brake pads undergo rigorous testing to ensure they meet all performance and safety criteria.
These checkpoints are essential for maintaining high-quality production standards.
What Common Testing Methods Are Used for Brake Pads?
Brake pads undergo various testing methods to ensure their reliability and safety. Common testing techniques include:
- Friction testing: Evaluates the coefficient of friction under different conditions to ensure effective stopping power.
- Wear testing: Measures how the pads wear over time, which is crucial for understanding longevity.
- Thermal testing: Assesses how the pads perform under extreme temperatures, which is vital for safety.
- Noise testing: Evaluates the noise levels produced during operation, as excessive noise can indicate quality issues.
These tests help ensure that the brake pads will perform effectively under a variety of conditions.
How Can B2B Buyers Verify Supplier Quality Control?
For B2B buyers, verifying a supplier’s quality control processes is essential to ensure product reliability. Here are actionable strategies:
- Supplier Audits: Conducting regular audits of potential suppliers can provide insights into their manufacturing processes and quality assurance practices.
- Quality Reports: Requesting detailed quality reports can help assess a supplier’s adherence to standards and their commitment to quality.
- Third-Party Inspections: Engaging third-party inspection services can provide an unbiased assessment of the supplier’s quality control measures.
These strategies can help buyers mitigate risks and ensure they partner with reliable suppliers.
What Are the QC and Certification Nuances for International B2B Buyers?
International B2B buyers must navigate various nuances regarding quality control and certifications:
- Local Regulations: Buyers should be aware of specific regulations in their region that may affect product compliance.
- Cultural Differences: Understanding cultural attitudes towards quality and safety can help buyers set appropriate expectations with suppliers.
- Documentation: Ensuring that suppliers provide the necessary documentation to prove compliance with international standards is crucial.
Being aware of these nuances can facilitate smoother transactions and partnerships between buyers and suppliers across different regions, including Africa, South America, the Middle East, and Europe.
In conclusion, understanding the manufacturing processes and quality assurance practices for brake pads is essential for international B2B buyers. By focusing on the key stages of manufacturing and the importance of quality control, buyers can make informed decisions and establish reliable partnerships with suppliers.
Practical Sourcing Guide: A Step-by-Step Checklist for ‘brake pads supplier’
The following checklist provides a comprehensive guide for B2B buyers looking to source brake pads suppliers. This step-by-step approach aims to streamline the procurement process and ensure that you partner with a reliable supplier.
Step 1: Define Your Technical Specifications
Before initiating your search, it’s crucial to establish clear technical specifications for the brake pads you require. This includes understanding the material composition, dimensions, performance standards, and certifications necessary for your region. Clear specifications help avoid misunderstandings and ensure that suppliers provide products that meet your operational needs.
- Considerations:
- Identify the vehicle types and models the brake pads will be used for.
- Specify performance attributes such as noise levels, wear resistance, and heat dissipation.
Step 2: Research Potential Suppliers
Conduct thorough research to compile a list of potential brake pad suppliers. Utilize online platforms, industry directories, and trade shows to identify suppliers that specialize in your required specifications. This step is vital to understand the market landscape and identify suppliers with a proven track record.
- Tips:
- Look for suppliers with industry certifications, such as ISO or TS16949.
- Check for customer reviews and testimonials to gauge supplier reliability.
Step 3: Evaluate Supplier Capabilities
Once you have a list of potential suppliers, evaluate their capabilities to ensure they can meet your needs. This includes assessing their production capacity, quality control processes, and technological capabilities. A capable supplier will not only meet your current demands but also adapt to future requirements.
- Questions to Ask:
- What is the supplier’s production capacity and lead time?
- How do they ensure quality control throughout the manufacturing process?
Step 4: Verify Supplier Certifications
Before proceeding, confirm that the suppliers hold relevant certifications that comply with international standards. This step is critical to ensure the brake pads meet safety and quality requirements specific to your market. Non-compliance can lead to significant risks.
- Key Certifications:
- ISO 9001 for quality management.
- Environmental certifications like ISO 14001.
Step 5: Request Samples and Conduct Testing
Request product samples from shortlisted suppliers to evaluate the quality and performance of their brake pads. Conduct thorough testing under conditions that reflect your operational environment. This practical assessment is essential to avoid costly mistakes later on.
- Testing Considerations:
- Assess durability, noise levels, and braking efficiency.
- Compare the performance of samples against your specifications.
Step 6: Negotiate Terms and Conditions
Once you’ve selected a suitable supplier, negotiate terms and conditions that align with your business objectives. This includes pricing, payment terms, delivery schedules, and warranty agreements. Clear agreements help establish a strong foundation for your business relationship.
- Negotiation Tips:
- Be clear about your expectations regarding delivery and quality.
- Discuss penalties for non-compliance to ensure accountability.
Step 7: Establish a Relationship and Monitor Performance
After finalizing the agreement, focus on building a strong relationship with your supplier. Regular communication and feedback are vital for maintaining quality and addressing any issues that may arise. Monitor supplier performance against agreed metrics to ensure ongoing compliance and satisfaction.
- Performance Metrics:
- Delivery times and accuracy.
- Quality of products received and responsiveness to issues.
By following this checklist, you can navigate the sourcing process effectively, ensuring you find a brake pads supplier that meets your technical requirements and business needs.
Comprehensive Cost and Pricing Analysis for brake pads supplier Sourcing
What Are the Key Cost Components in Brake Pads Supplier Sourcing?
Understanding the cost structure of brake pad suppliers is critical for B2B buyers aiming to make informed purchasing decisions. The primary cost components include:
-
Materials: The type of materials used in manufacturing brake pads significantly impacts costs. High-quality friction materials, adhesives, and backing plates can increase the price but also enhance performance and longevity.
-
Labor: Labor costs vary by region and manufacturing processes. In areas with higher labor costs, such as Europe, the overall production cost might increase. However, automation can mitigate these costs in certain manufacturing environments.
-
Manufacturing Overhead: This includes costs related to facility maintenance, utilities, and administrative expenses. Efficient manufacturing processes can reduce these overhead costs, impacting the final price.
-
Tooling: Initial tooling costs for custom designs can be substantial. Buyers should assess whether these costs are amortized over large production runs or if they are one-time expenses for low-volume orders.
-
Quality Control (QC): Implementing rigorous QC processes ensures product reliability but also adds to costs. Certifications (e.g., ISO, ECE) may require additional investment, which can be reflected in the pricing.
-
Logistics: Shipping costs can fluctuate based on distance, weight, and chosen Incoterms. Buyers should factor in these logistics expenses when evaluating supplier prices.
-
Margin: Suppliers typically apply a markup to cover their costs and desired profit margins. Understanding the supplier’s business model can help buyers negotiate better terms.
How Do Price Influencers Affect Brake Pad Costs?
Several factors can influence the pricing of brake pads beyond the basic cost components:
-
Volume/MOQ (Minimum Order Quantity): Ordering in bulk can lead to significant discounts. Suppliers often have tiered pricing models, where larger orders reduce per-unit costs.
-
Specifications and Customization: Custom specifications (e.g., specific dimensions or performance characteristics) can increase costs. Buyers should balance the need for customization with budget constraints.
-
Materials and Quality Certifications: Higher-quality materials and recognized certifications can justify higher prices. Buyers should evaluate whether the added cost aligns with performance needs.
-
Supplier Factors: Supplier reputation, reliability, and production capabilities can influence pricing. Established suppliers may charge more due to their proven track record, but they often deliver superior quality and service.
-
Incoterms: The chosen Incoterms can significantly affect final pricing. Terms like FOB (Free on Board) or CIF (Cost, Insurance, and Freight) will define who bears the shipping costs and risks, impacting the total expenditure.
What Buyer Tips Can Enhance Cost-Efficiency in Brake Pad Sourcing?
Navigating the complexities of brake pad sourcing requires strategic insight:
-
Negotiation: Always negotiate pricing and terms with suppliers. Leverage volume commitments or long-term contracts to secure better rates.
-
Total Cost of Ownership (TCO): Focus on TCO rather than just the upfront price. Assess factors such as durability, performance, and potential maintenance costs to understand the long-term financial impact.
-
Pricing Nuances for International Buyers: International buyers, particularly from Africa, South America, the Middle East, and Europe, should be aware of currency fluctuations and import duties. It is advisable to factor these elements into the overall cost calculation.
-
Research and Benchmarking: Conduct thorough market research and benchmark prices across different suppliers. This will provide leverage during negotiations and ensure competitive pricing.
-
Quality Over Price: While it may be tempting to opt for the lowest price, prioritize quality and reliability to avoid costly failures and replacements in the future.
Disclaimer on Pricing
The prices associated with brake pads can fluctuate based on market conditions, material costs, and supplier capabilities. Therefore, it is essential for buyers to conduct due diligence and obtain multiple quotations to ensure they are making the best-informed purchasing decision.
Alternatives Analysis: Comparing brake pads supplier With Other Solutions
Understanding Alternatives to Brake Pads Suppliers
When evaluating brake pads suppliers, international B2B buyers must consider various alternative solutions that could meet their operational needs. These alternatives range from different types of braking systems to innovative materials and technologies. Each option comes with its own set of advantages and disadvantages, which can significantly impact performance, cost, and overall value.
Comparison Table of Brake Pads Supplier and Alternatives
Comparison Aspect | Brake Pads Supplier | Alternative 1: Ceramic Brake Pads | Alternative 2: Regenerative Braking Systems |
---|---|---|---|
Performance | High durability and consistent stopping power | Excellent heat dissipation and reduced noise | Improves energy efficiency and extends vehicle range |
Cost | Moderate to high cost depending on quality | Generally higher upfront costs but lower lifetime costs | Higher initial investment due to complex technology |
Ease of Implementation | Straightforward installation in most vehicles | Requires specific vehicle compatibility | Complex installation requiring specialized knowledge |
Maintenance | Regular inspection needed; moderate wear | Lower wear and longer lifespan reduce maintenance frequency | Minimal maintenance but requires monitoring of battery systems |
Best Use Case | Standard vehicles and heavy-duty applications | Performance vehicles and eco-friendly options | Electric vehicles and hybrid systems for energy recovery |
Detailed Breakdown of Alternatives
What Are the Advantages and Disadvantages of Ceramic Brake Pads?
Ceramic brake pads are a popular alternative to traditional brake pads. They provide excellent stopping power while generating less dust and noise. This makes them ideal for performance vehicles where both efficiency and comfort are essential. However, ceramic pads tend to have a higher upfront cost compared to standard pads and may not be suitable for all vehicle types, particularly heavy-duty applications. Their heat dissipation is superior, which can enhance performance but may require specific vehicle compatibility.
How Do Regenerative Braking Systems Work and What Are Their Pros and Cons?
Regenerative braking systems offer a different approach by recovering energy during braking and converting it into electrical energy, which can recharge the vehicle’s battery. This technology is primarily found in electric and hybrid vehicles. The advantages include significant energy efficiency improvements and reduced wear on traditional brake components, resulting in lower maintenance costs. However, regenerative systems come with a higher initial investment and require specialized installation. They also necessitate an understanding of battery management, which can complicate maintenance.
Conclusion: How Should B2B Buyers Choose the Right Braking Solution?
Choosing the right braking solution requires a careful assessment of specific needs and operational contexts. B2B buyers should evaluate factors such as vehicle type, typical usage scenarios, and budget constraints. While traditional brake pads from a reliable supplier may suffice for standard applications, alternatives like ceramic pads or regenerative braking systems could offer enhanced performance or efficiency for specialized uses. By weighing the pros and cons of each option, buyers can make informed decisions that align with their strategic objectives and operational requirements.
Essential Technical Properties and Trade Terminology for brake pads supplier
What Are the Essential Technical Properties of Brake Pads for B2B Buyers?
When selecting brake pads, understanding their technical properties is crucial for ensuring safety, performance, and compatibility with specific vehicle requirements. Here are some of the critical specifications to consider:
1. Material Grade
Brake pads are typically made from various materials, including organic, semi-metallic, and ceramic composites. Each material has distinct characteristics that affect performance. For instance, organic pads are quieter and produce less dust, making them suitable for urban driving. In contrast, semi-metallic pads offer superior heat dissipation and durability, ideal for high-performance vehicles. For B2B buyers, selecting the appropriate material grade is essential to meet customer needs and regulatory standards.
2. Friction Coefficient
The friction coefficient measures the brake pad’s ability to generate stopping power. A higher coefficient indicates better performance but may lead to increased wear on both the pads and rotors. For international buyers, understanding the friction coefficients of different brake pads helps in choosing the right product for varying driving conditions and regulatory requirements across regions.
3. Tolerance Levels
Tolerance levels refer to the allowable variations in dimensions and performance characteristics of brake pads. These specifications are critical for ensuring proper fitment and function. For example, a pad that does not meet specified tolerances may lead to uneven wear, noise, or reduced braking efficiency. B2B buyers should prioritize suppliers that adhere to strict tolerance standards to ensure product reliability.
4. Thermal Stability
Thermal stability indicates how well brake pads can withstand high temperatures without losing performance. Brake pads are subjected to intense heat during operation, and materials that degrade under high temperatures can compromise safety. Understanding thermal stability is vital for B2B buyers, especially in regions with extreme driving conditions, as it influences the longevity and effectiveness of the brake system.
5. Noise and Vibration Characteristics
Noise and vibration are critical factors in brake pad performance. High-quality pads are designed to minimize squeaking and vibrations, enhancing driver comfort. B2B buyers should consider these characteristics when selecting products, as they directly impact customer satisfaction and brand reputation.
What Are Common Trade Terminology Terms for Brake Pads Suppliers?
Familiarity with industry jargon is essential for effective communication and negotiation in the B2B brake pad market. Here are some common terms:
1. OEM (Original Equipment Manufacturer)
OEM refers to parts that are made by the vehicle’s original manufacturer. B2B buyers often prefer OEM brake pads for their compatibility and reliability, especially in fleet management and vehicle maintenance.
2. MOQ (Minimum Order Quantity)
MOQ is the smallest quantity of products a supplier is willing to sell. Understanding MOQ is crucial for B2B buyers, as it can affect inventory management and cash flow. Buyers should negotiate MOQs to ensure they can meet demand without overcommitting resources.
3. RFQ (Request for Quotation)
An RFQ is a document that buyers use to solicit price quotes from suppliers. It typically outlines product specifications, quantities, and delivery timelines. For B2B buyers, crafting a clear RFQ helps ensure they receive accurate and competitive pricing.
4. Incoterms (International Commercial Terms)
Incoterms are standardized trade terms that define the responsibilities of buyers and sellers in international transactions. Understanding these terms is vital for B2B buyers in managing shipping, insurance, and risk. Common terms include FOB (Free On Board) and CIF (Cost, Insurance, and Freight).
5. Aftermarket
The aftermarket refers to parts and accessories sold after the original sale of the vehicle. B2B buyers targeting the aftermarket must understand market trends and customer preferences to effectively position their brake pads.
By comprehensively understanding these technical properties and trade terminologies, B2B buyers can make informed decisions when sourcing brake pads, ensuring they meet the demands of their clients while maintaining high safety and performance standards.
Navigating Market Dynamics and Sourcing Trends in the brake pads supplier Sector
What Are the Key Market Dynamics and Trends for Brake Pad Suppliers?
The global brake pads market is experiencing robust growth, driven by rising automotive production and the increasing demand for vehicle safety. As international B2B buyers from Africa, South America, the Middle East, and Europe navigate this landscape, understanding key trends is crucial. The shift towards electric vehicles (EVs) is significantly influencing brake pad sourcing, with suppliers adapting their product lines to meet the specific requirements of EVs, such as reduced noise and improved durability. Additionally, the integration of advanced technologies, such as IoT for predictive maintenance and blockchain for supply chain transparency, is becoming increasingly prevalent.
B2B buyers should also note the increasing importance of local sourcing strategies, particularly in light of recent supply chain disruptions. Establishing partnerships with regional suppliers can not only mitigate risks but also enhance responsiveness to market changes. In terms of pricing, fluctuations in raw material costs, particularly in steel and composites, are impacting the overall pricing strategies of brake pad suppliers. Buyers are advised to stay informed about these dynamics to negotiate better deals and ensure they are sourcing competitively.
How Is Sustainability Influencing Brake Pad Sourcing Trends?
Sustainability has become a fundamental consideration in the sourcing of brake pads. The environmental impact of automotive components is under scrutiny, prompting B2B buyers to prioritize suppliers that adhere to sustainable practices. This includes the use of eco-friendly materials, such as non-asbestos organic (NAO) compounds and recycled materials, which significantly reduce the carbon footprint of brake pads.
Moreover, ethical sourcing is gaining traction as businesses aim to align with consumer expectations regarding corporate responsibility. Buyers should seek suppliers with transparent supply chains and certifications that demonstrate compliance with environmental and social governance (ESG) criteria. Certifications such as ISO 14001 for environmental management systems and LEED for sustainable materials can provide assurance of a supplier’s commitment to sustainability. By prioritizing suppliers with strong sustainability credentials, international buyers can not only enhance their brand reputation but also contribute to a more sustainable automotive industry.
What Is the Historical Context of the Brake Pad Industry?
The brake pad industry has evolved significantly over the last century, transitioning from rudimentary materials to advanced composites designed for safety and performance. Initially, brake pads were made from leather and wood, which offered limited effectiveness. The introduction of materials like asbestos provided better performance but raised serious health concerns, leading to a shift towards safer, more sustainable alternatives in the late 20th century.
As automotive technology advanced, so did brake pad designs, incorporating various materials such as ceramic and metallic compounds that offer better heat dissipation and longevity. The rise of global automotive manufacturing has further influenced the brake pad market, prompting suppliers to innovate continuously and meet diverse regional standards. For international B2B buyers, understanding this evolution is essential as it informs current product offerings and future developments in brake pad technology.
Frequently Asked Questions (FAQs) for B2B Buyers of brake pads supplier
-
How do I choose the right brake pads supplier for my business needs?
When selecting a brake pads supplier, consider factors such as product quality, certifications, and their experience in the industry. Research potential suppliers by checking reviews and testimonials from other businesses. Additionally, assess their ability to meet your specific needs, such as customization options and minimum order quantities (MOQ). Establishing a good relationship with the supplier can enhance communication and reliability, ensuring that you receive the best products and services for your operations. -
What are the common customization options offered by brake pads suppliers?
Most brake pads suppliers provide a range of customization options to meet specific requirements. These may include variations in materials, sizes, friction formulations, and branding options. Some suppliers may also offer tailored solutions for specific vehicle types or performance conditions. When discussing customization, be clear about your requirements and expectations to ensure the supplier can deliver a product that meets your needs. -
What should I know about minimum order quantities (MOQ) from brake pads suppliers?
Minimum order quantities (MOQ) vary significantly among brake pads suppliers and can impact your purchasing decisions. Many suppliers set an MOQ to cover production costs and ensure profitability. As an international B2B buyer, inquire about the MOQ and whether it can be adjusted based on your needs, especially if you are a smaller business. Understanding the MOQ can help you budget effectively and manage inventory levels. -
What payment terms can I expect when working with brake pads suppliers?
Payment terms can differ widely among brake pads suppliers, and it’s crucial to clarify these before finalizing any agreements. Common payment options include upfront payments, payment upon delivery, or installment plans. Some suppliers may offer credit terms based on your business relationship and payment history. Ensure that you discuss and agree on payment terms that align with your cash flow and operational needs. -
How do I assess the quality assurance processes of brake pads suppliers?
Quality assurance is vital in the brake pads industry, as it directly impacts safety and performance. When vetting suppliers, inquire about their quality control processes, including testing standards, certifications (such as ISO), and compliance with international regulations. Request documentation and samples to evaluate the quality of their products. A reliable supplier will be transparent about their QA procedures and willing to provide evidence of their product reliability. -
What logistics considerations should I be aware of when importing brake pads?
When importing brake pads, logistics play a crucial role in ensuring timely delivery and cost efficiency. Consider factors such as shipping methods, customs regulations, and potential tariffs or duties specific to your region. Work with suppliers who have experience in international shipping and can assist with documentation and compliance. Establishing clear communication regarding shipping timelines and responsibilities can help prevent delays in your supply chain. -
How can I effectively communicate my needs to a brake pads supplier?
Clear communication is essential when working with brake pads suppliers. Start by providing a detailed overview of your requirements, including product specifications, expected delivery timelines, and any customization needs. Utilize visual aids, such as diagrams or samples, to illustrate your expectations. Regular check-ins and updates can help maintain alignment and address any potential issues early in the process, fostering a strong working relationship. -
What are the advantages of sourcing brake pads from international suppliers?
Sourcing brake pads from international suppliers can offer several advantages, such as access to a wider range of products, competitive pricing, and advanced technologies that may not be available locally. Suppliers from regions with established automotive manufacturing may provide high-quality products at lower costs due to economies of scale. However, it’s important to conduct thorough due diligence on potential suppliers to mitigate risks related to quality, logistics, and compliance with international standards.
Important Disclaimer & Terms of Use
⚠️ Important Disclaimer
The information provided in this guide, including content regarding manufacturers, technical specifications, and market analysis, is for informational and educational purposes only. It does not constitute professional procurement advice, financial advice, or legal advice.
While we have made every effort to ensure the accuracy and timeliness of the information, we are not responsible for any errors, omissions, or outdated information. Market conditions, company details, and technical standards are subject to change.
B2B buyers must conduct their own independent and thorough due diligence before making any purchasing decisions. This includes contacting suppliers directly, verifying certifications, requesting samples, and seeking professional consultation. The risk of relying on any information in this guide is borne solely by the reader.
Strategic Sourcing Conclusion and Outlook for brake pads supplier
How Can Strategic Sourcing Enhance Your Brake Pad Procurement?
In conclusion, strategic sourcing remains a pivotal approach for international B2B buyers seeking brake pad suppliers. By leveraging comprehensive market analysis, buyers can identify suppliers that not only meet their quality standards but also align with their operational needs. Prioritizing factors such as supplier reliability, product innovation, and sustainability can lead to better procurement outcomes and foster long-term partnerships.
What Are the Next Steps for International Buyers?
As you navigate the complexities of sourcing brake pads, consider engaging with suppliers who demonstrate a commitment to transparency and quality assurance. Emphasize the importance of certifications and compliance with international standards, particularly for markets in Africa, South America, the Middle East, and Europe.
Looking Forward: How to Stay Ahead in Brake Pad Sourcing?
The future of brake pad procurement will likely be shaped by advancements in technology and increasing environmental regulations. Buyers should stay informed about emerging trends such as electric vehicle demands and eco-friendly materials. By adopting a proactive approach, you can position your business for success in a competitive landscape.
Take action today by evaluating your current suppliers and exploring new partnerships that align with your strategic goals. Investing in strategic sourcing now will ensure your organization is well-equipped to meet future challenges in the automotive supply chain.