Unlock Savings: The Ultimate Coin Manufacturer Guide (2025)
Introduction: Navigating the Global Market for coin manufacturer
In the rapidly evolving landscape of global commerce, sourcing reliable coin manufacturers can present significant challenges for international B2B buyers. Whether you are seeking to produce commemorative coins, currency, or tokens, understanding the nuances of this niche market is crucial. This guide aims to illuminate the complexities of selecting the right coin manufacturer, covering essential aspects such as types of coins available, applications across various industries, supplier vetting processes, and cost considerations.
As buyers from regions like Africa, South America, the Middle East, and Europe navigate the global market, they face unique obstacles, including regulatory compliance and quality assurance. This comprehensive guide empowers you to make informed purchasing decisions, ensuring that your investment not only meets your specifications but also adheres to international standards.
With a focus on actionable insights, we will delve into the various types of coin manufacturing processes, the importance of material selection, and the latest technological advancements that can enhance production efficiency. Additionally, we will provide strategies for effectively vetting suppliers, understanding pricing structures, and negotiating favorable terms. By the end of this guide, you will be equipped with the knowledge needed to confidently engage with manufacturers and secure the best solutions for your coin production needs.
Understanding coin manufacturer Types and Variations
Type Name | Key Distinguishing Features | Primary B2B Applications | Brief Pros & Cons for Buyers |
---|---|---|---|
Government Mints | Operated by national governments, produce legal tender coins. | National currency production, commemorative coins. | Pros: Trustworthy, standardized quality. Cons: Limited customization options. |
Private Minting Companies | Independent entities that produce coins for various clients. | Custom coins, tokens, and promotional items. | Pros: High customization, flexibility. Cons: Potentially variable quality. |
Coin Press Manufacturers | Specialize in producing machinery for coin production. | Equipment supply for mints and private manufacturers. | Pros: Essential for starting production, advanced technology. Cons: High initial investment. |
Numismatic Manufacturers | Focus on creating collectible coins and medals. | Collectibles, investor-grade products. | Pros: Unique designs, high market value. Cons: Niche market, may not appeal to all buyers. |
Digital Currency Producers | Innovate in producing cryptocurrencies and digital tokens. | Blockchain applications, investment products. | Pros: Future-forward technology, high demand. Cons: Regulatory uncertainties, market volatility. |
What Are the Characteristics of Government Mints?
Government mints are state-operated facilities responsible for producing national currency and legal tender coins. They ensure that the coins meet strict quality and security standards, making them highly trusted among B2B buyers. These mints also produce commemorative coins that celebrate national events or figures, appealing to collectors and investors. When purchasing from government mints, buyers can expect consistent quality and reliability, although customization options may be limited.
How Do Private Minting Companies Differ?
Private minting companies are independent entities that cater to a diverse range of clients, producing custom coins, tokens, and promotional items. They are known for their flexibility and ability to create unique designs tailored to specific client needs. This adaptability makes them ideal for businesses looking to enhance their brand visibility through custom coinage. However, buyers should be aware of potential variations in quality and ensure they select reputable manufacturers.
What Role Do Coin Press Manufacturers Play in the Industry?
Coin press manufacturers specialize in producing the machinery used for minting coins. They provide essential equipment for both government mints and private manufacturers, enabling efficient coin production. Buyers looking to enter the coin manufacturing industry must consider the investment required for such machinery, as it can be significant. However, the advanced technology offered by these manufacturers can greatly enhance production efficiency and output quality.
Why Choose Numismatic Manufacturers for Collectibles?
Numismatic manufacturers focus on creating collectible coins and medals, often featuring intricate designs that appeal to collectors and investors. These manufacturers cater to a niche market where uniqueness and rarity can drive high market values. B2B buyers interested in collectibles should consider the reputation and design capabilities of these manufacturers, as the collectible market can be competitive. However, the appeal of collectible coins may not extend to all potential buyers, making this a more specialized option.
What Are the Advantages of Digital Currency Producers?
Digital currency producers are at the forefront of innovation, creating cryptocurrencies and digital tokens that cater to the growing demand for blockchain applications. These manufacturers are essential for businesses looking to invest in or leverage digital currencies. However, buyers should be cautious of regulatory uncertainties and market volatility that can affect the value and acceptance of digital currencies. Investing in this area requires thorough research and a clear understanding of the evolving landscape.
Related Video: HYPNOTIC Video Pure Gold Manufacturing Process,World’s Largest Gold Coin &Melting Gold Bars Casting
Key Industrial Applications of coin manufacturer
Industry/Sector | Specific Application of Coin Manufacturer | Value/Benefit for the Business | Key Sourcing Considerations for this Application |
---|---|---|---|
Banking and Financial Services | Custom Coinage for Transactions | Streamlined cash handling and customer transactions | Quality assurance, compliance with local regulations, and security features |
Gaming and Entertainment | Casino Tokens and Gaming Chips | Enhanced customer experience and security in transactions | Material durability, design customization, and anti-counterfeit measures |
Retail and Vending | Coin-Operated Machines | Increased revenue through automated transactions | Compatibility with existing machines, maintenance support, and bulk pricing |
Collectibles and Souvenirs | Commemorative Coins and Medals | Unique marketing tool to enhance brand loyalty | Design flexibility, production timelines, and minimum order quantities |
Transportation and Logistics | Fare Tokens for Public Transport | Efficient fare collection and improved customer flow | Compliance with transport regulations, ease of use, and durability |
How is Coin Manufacturer Used in Banking and Financial Services?
In the banking and financial services sector, coin manufacturers produce custom coinage that facilitates seamless transactions. These coins are vital for cash handling, ensuring accuracy and efficiency in customer transactions. International buyers need to consider quality assurance processes, compliance with local regulations, and security features to mitigate risks associated with counterfeit coins.
What Role Does Coin Manufacturer Play in Gaming and Entertainment?
Coin manufacturers supply casinos with tokens and gaming chips, which enhance the overall customer experience. These tokens not only serve as currency within the casino but also incorporate security features that prevent counterfeiting. B2B buyers from the gaming industry must prioritize material durability, design customization, and anti-counterfeit measures when sourcing these products to maintain integrity and customer trust.
How Do Coin Manufacturers Support Retail and Vending Industries?
In retail and vending sectors, coin manufacturers create coins specifically for coin-operated machines. These coins streamline cash transactions, contributing to increased revenue. Buyers in this industry should focus on compatibility with existing machines, maintenance support, and bulk pricing to ensure a cost-effective and efficient cash handling system.
What Benefits Do Collectors Gain from Coin Manufacturer?
Coin manufacturers produce commemorative coins and medals that serve as unique marketing tools for brands. These items can enhance brand loyalty and provide a tangible connection to the consumer. For international B2B buyers, considerations include design flexibility, production timelines, and minimum order quantities to meet specific promotional needs.
How is Coin Manufacturer Essential for Transportation and Logistics?
Coin manufacturers provide fare tokens for public transport systems, which facilitate efficient fare collection and improve customer flow. These tokens are designed to withstand heavy usage and must comply with transport regulations. Buyers in this sector should prioritize ease of use and durability to ensure a reliable fare collection system.
Related Video: Uses of Metals – Science 9
3 Common User Pain Points for ‘coin manufacturer’ & Their Solutions
Scenario 1: Difficulty in Sourcing Quality Coins for Currency Circulation
The Problem: International B2B buyers, particularly banks and financial institutions in Africa, South America, and the Middle East, often face challenges in sourcing high-quality coins that meet specific circulation standards. Poor quality coins can lead to operational inefficiencies, such as increased wear and tear on vending machines and coin-operated devices. Additionally, counterfeit coins entering circulation can undermine trust in the financial system, posing significant risks to both banks and consumers.
The Solution: To overcome sourcing challenges, buyers should engage directly with reputable coin manufacturers who specialize in producing high-quality currency. Conduct thorough research on potential manufacturers, focusing on their certifications, production processes, and quality assurance measures. It’s advisable to request samples before placing large orders to assess the quality firsthand. Building a relationship with manufacturers that have a proven track record in your region can also facilitate better communication and understanding of local needs, ensuring that the coins produced meet both aesthetic and functional requirements.
Scenario 2: Inefficiencies in Coin Distribution and Logistics
The Problem: A major pain point for B2B buyers dealing with coin manufacturers is managing the logistics of coin distribution. Delays in shipping can lead to shortages, affecting businesses that rely on coins for transactions, such as retailers and vending machine operators. Additionally, the process of transporting heavy coins can be costly and complicated, especially in regions with underdeveloped infrastructure.
The Solution: To mitigate distribution issues, buyers should establish clear logistical plans with their coin manufacturers. This includes discussing shipping methods, potential customs challenges, and local delivery options. Consider partnering with logistics firms that specialize in heavy goods to streamline the transport process. Utilizing technology such as GPS tracking can help monitor shipments in real-time, allowing buyers to anticipate delays and adjust their operations accordingly. Establishing a contingency plan, such as maintaining a buffer stock of coins, can also help businesses navigate unexpected disruptions.
Scenario 3: Compliance with Regulatory Standards and Quality Control
The Problem: B2B buyers in Europe and other regions must navigate a complex landscape of regulations regarding coin manufacturing and distribution. Compliance with local laws, such as the specifications set by central banks, can be daunting. Failure to adhere to these standards can result in legal repercussions and financial losses, as well as reputational damage.
The Solution: Buyers should familiarize themselves with the regulatory requirements specific to their region and ensure that their chosen coin manufacturer is compliant. This includes verifying that the manufacturer follows standards for metal content, weight, and design as stipulated by financial authorities. Regular audits and quality checks should be instituted as part of the procurement process. Working closely with legal experts in financial regulations can provide additional assurance that all aspects of the transaction are compliant, thus minimizing risk. Moreover, fostering transparency with the manufacturer about compliance requirements can ensure that they maintain the necessary standards throughout production.
Strategic Material Selection Guide for coin manufacturer
What Are the Key Properties of Common Materials Used in Coin Manufacturing?
When selecting materials for coin manufacturing, several factors come into play, including mechanical properties, corrosion resistance, and cost-effectiveness. Below, we analyze four common materials used in the industry: Copper-Nickel, Zinc, Brass, and Silver. Each material has unique characteristics that affect its performance and suitability for different applications.
How Does Copper-Nickel Perform in Coin Manufacturing?
Key Properties: Copper-Nickel alloys, often referred to as cupronickel, exhibit excellent corrosion resistance and good mechanical strength. They perform well in various environmental conditions, making them suitable for coins that will circulate widely.
Pros & Cons: The primary advantage of Copper-Nickel is its durability; it resists tarnishing and wear, which is critical for coins that see extensive use. However, the manufacturing process can be complex and costlier than other options, which may affect the overall production cost.
Impact on Application: Copper-Nickel is particularly compatible with seawater and urban environments, where corrosion from pollutants is a concern. This makes it a popular choice for coins in coastal regions.
Considerations for International Buyers: B2B buyers from Africa, South America, the Middle East, and Europe should ensure compliance with relevant standards such as ASTM B171. Additionally, buyers should consider local preferences for coin materials, as some regions may favor specific alloys based on historical or cultural significance.
What Advantages Does Zinc Offer as a Coin Material?
Key Properties: Zinc is lightweight and has a relatively low melting point, making it easy to mold and shape. It also has decent corrosion resistance, although it is not as robust as Copper-Nickel.
Pros & Cons: The primary advantage of Zinc is its low cost, making it an economical choice for mass production. However, its lower durability compared to other materials can lead to quicker wear and tear, which may not be ideal for high-circulation coins.
Impact on Application: Zinc is often used in lower-value coins or tokens, where cost is a more significant factor than longevity. It is less suitable for coins that will be exposed to harsh environmental conditions.
Considerations for International Buyers: Buyers should be aware of the varying regulations regarding the use of Zinc in coin production across different regions. Compliance with standards like ASTM B69 is crucial to ensure product quality and safety.
How Does Brass Compare in Terms of Suitability for Coinage?
Key Properties: Brass, an alloy of copper and zinc, offers good corrosion resistance and a bright, attractive appearance. It is durable and can withstand the rigors of circulation.
Pros & Cons: The aesthetic appeal of Brass is a significant advantage, making it suitable for commemorative coins. However, the cost can be higher than Zinc, and the manufacturing process may require more energy and resources.
Impact on Application: Brass is commonly used for mid-range value coins, balancing cost and durability. Its resistance to tarnish makes it suitable for coins that require a longer lifespan.
Considerations for International Buyers: B2B buyers should consider the local market’s acceptance of Brass coins, as some regions may have preferences for specific materials. Compliance with international standards such as ISO 2099 is also essential.
What Role Does Silver Play in Coin Manufacturing?
Key Properties: Silver is renowned for its high conductivity, malleability, and corrosion resistance. It has a distinctive luster that makes it highly desirable for collectors and investors.
Pros & Cons: The primary advantage of Silver is its value, which enhances the appeal of coins to collectors. However, the high cost of Silver can limit its use in everyday currency, making it less practical for mass production.
Impact on Application: Silver is often used for limited edition coins or high-value currency, where the intrinsic value of the metal is a selling point.
Considerations for International Buyers: Buyers should be aware of market fluctuations in Silver prices and ensure compliance with local regulations regarding precious metals. Standards such as ASTM B1008 may also apply.
Summary Table of Material Selection for Coin Manufacturing
Material | Typical Use Case for Coin Manufacturer | Key Advantage | Key Disadvantage/Limitation | Relative Cost (Low/Med/High) |
---|---|---|---|---|
Copper-Nickel | General circulation coins | Excellent corrosion resistance | Higher manufacturing complexity | Medium |
Zinc | Low-value coins or tokens | Low cost | Lower durability | Low |
Brass | Mid-range value coins | Attractive appearance | Higher cost and energy-intensive process | Medium |
Silver | Limited edition or high-value coins | High intrinsic value | Very high cost | High |
This guide provides a comprehensive overview of the materials used in coin manufacturing, equipping international B2B buyers with the necessary insights to make informed decisions that align with their operational and market needs.
In-depth Look: Manufacturing Processes and Quality Assurance for coin manufacturer
What Are the Main Stages of the Coin Manufacturing Process?
Coin manufacturing is a sophisticated process that involves several key stages, each critical to producing high-quality currency. The primary stages include material preparation, forming, assembly, and finishing.
1. Material Preparation: What Materials Are Used in Coin Production?
The first step in the coin manufacturing process is selecting the right materials. Common materials used include copper, nickel, and zinc, which are often alloyed to achieve desired properties such as durability and corrosion resistance. The raw materials undergo a thorough inspection to ensure they meet specific standards, including purity and composition. This stage is crucial as the quality of the raw materials directly affects the final product’s integrity.
2. How Is Coin Forming Achieved?
Coin forming typically employs techniques such as blanking and striking.
- Blanking involves cutting out circular discs (blanks) from metal sheets. The thickness and diameter of these blanks are meticulously controlled to ensure uniformity.
- Striking is the process where the blank is pressed with a die to imprint designs and inscriptions. This step uses high-pressure machines to ensure that the design is clearly defined and the coin’s edges are shaped correctly.
Advanced technologies such as computer numerical control (CNC) machining may be employed to enhance precision during this stage.
3. What Does the Assembly Process Entail?
In the assembly stage, coins may undergo additional treatments, such as annealing, which softens the metal and improves its malleability. This is particularly important for coins that will undergo further processing, such as edge lettering or additional striking.
Quality checks are performed at this stage to ensure that the coins meet dimensional and design specifications.
4. What Are the Final Finishing Techniques for Coins?
Finishing techniques may include cleaning, polishing, and applying protective coatings. These processes enhance the aesthetic appeal of the coins and improve their longevity. The final products are then packaged and prepared for distribution.
How Is Quality Assurance Implemented in Coin Manufacturing?
Quality assurance (QA) is critical in the coin manufacturing process, ensuring that the produced coins meet international standards and customer expectations. Several quality control (QC) checkpoints and testing methods are employed throughout the manufacturing process.
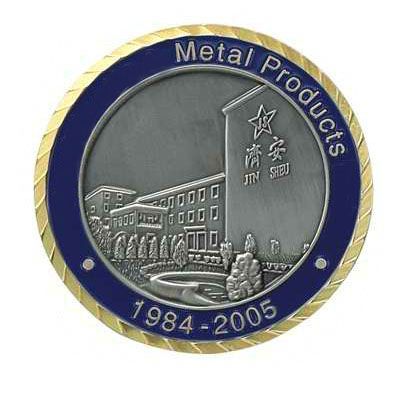
A stock image related to coin manufacturer.
What International Standards Guide Coin Manufacturing Quality?
International standards such as ISO 9001 play a significant role in guiding quality management systems in coin manufacturing. Compliance with these standards ensures that manufacturers maintain consistent quality and improve operational efficiency.
Additionally, industry-specific certifications like CE marking or API (American Petroleum Institute) standards may apply, depending on the intended use and market. Understanding these standards can help B2B buyers verify the reliability of their suppliers.
What Are the Key QC Checkpoints in the Manufacturing Process?
Quality control is integrated into various stages of the manufacturing process, typically categorized into three main checkpoints:
-
Incoming Quality Control (IQC): This checkpoint focuses on the quality of raw materials upon arrival. Suppliers must provide documentation and certifications regarding material properties and compliance with relevant standards.
-
In-Process Quality Control (IPQC): During manufacturing, processes are continuously monitored. This includes measurements for dimensions, weight, and visual inspections to identify defects early.
-
Final Quality Control (FQC): Once coins are produced, a comprehensive inspection is conducted. This includes testing for weight, diameter, design accuracy, and surface finish. Coins that do not meet specifications are rejected.
What Common Testing Methods Are Used in Coin Quality Control?
Several testing methods are employed to ensure coin quality, including:
- Dimensional Testing: Using calipers and micrometers to measure the thickness and diameter of coins.
- Visual Inspection: Inspecting for defects in design, surface finish, and minting errors.
- Weight Testing: Ensuring that the coins conform to established weight standards, which is essential for preventing counterfeiting.
How Can B2B Buyers Verify Supplier Quality Control?
B2B buyers should take proactive steps to ensure their suppliers adhere to stringent quality control standards. Here are some actionable strategies:
1. Conduct Supplier Audits
Regular audits can help B2B buyers assess a supplier’s manufacturing processes and quality control measures. An audit should evaluate compliance with ISO standards, review QC protocols, and inspect production facilities.
2. Request Quality Reports
Buyers should request detailed QC reports from suppliers, including documentation of testing results, certificates of compliance, and records of any non-conformities. This transparency helps establish trust and ensures accountability.
3. Engage Third-Party Inspectors
Hiring third-party inspection services can provide an unbiased assessment of the supplier’s quality control practices. These inspectors can perform audits, verify compliance with international standards, and ensure that the products meet the specified requirements.
What Are the Quality Control Nuances for International B2B Buyers?
For international B2B buyers, particularly from regions such as Africa, South America, the Middle East, and Europe, understanding the nuances of quality control is essential.
-
Cultural Differences: Be aware that quality expectations may vary across different regions. Engage in open communication with suppliers to align on quality standards.
-
Regulatory Requirements: Different countries may have specific regulations regarding coin production and quality standards. Ensure that your supplier complies with local laws and regulations.
-
Logistical Challenges: Consider the implications of logistics on quality. For example, the method of transport can affect the coins’ condition upon arrival. Ensure that suppliers have robust packaging and handling procedures.
By understanding these processes and quality assurance measures, international B2B buyers can make informed decisions when sourcing coins, ensuring they receive high-quality products that meet their specific needs.
Practical Sourcing Guide: A Step-by-Step Checklist for ‘coin manufacturer’
To assist international B2B buyers in the procurement of coin manufacturing services, this practical sourcing guide outlines essential steps to ensure you partner with the right manufacturer. This checklist will help streamline your sourcing process, enhance supplier evaluation, and mitigate risks.
Step 1: Define Your Technical Specifications
Establishing clear technical specifications is vital for aligning your needs with manufacturer capabilities. Determine the types of coins required, including size, weight, material (e.g., metals like copper, nickel, or zinc), and design intricacies. Detailed specifications help prevent misunderstandings and ensure the manufacturer can meet your exact requirements.
Step 2: Research Potential Manufacturers
Conduct thorough research to identify potential coin manufacturers that operate within your target regions, such as Africa, South America, the Middle East, and Europe. Utilize online directories, trade shows, and industry associations to compile a list. Pay attention to manufacturers with experience in producing coins similar to your needs, as this can significantly impact quality and turnaround time.
Step 3: Evaluate Supplier Certifications
Before proceeding, verify that potential suppliers hold necessary certifications and comply with industry standards. Look for ISO certifications or any local regulatory approvals pertinent to coin manufacturing. Such certifications not only ensure quality but also demonstrate the manufacturer’s commitment to best practices.
Step 4: Request and Analyze Samples
Request samples of the manufacturer’s previous work to assess their quality and craftsmanship. Inspect the coins for details such as finish, design accuracy, and durability. Engaging in this step allows you to visualize the end product and provides a basis for comparison among various suppliers.
Step 5: Assess Production Capabilities
Understanding a supplier’s production capacity is crucial to ensure they can meet your order volumes and deadlines. Inquire about their manufacturing processes, machinery, and workforce size. Additionally, evaluate their ability to scale production if your demand increases, as flexibility can be a significant advantage in the long term.
Step 6: Review Pricing Structures
Analyze the pricing models of potential manufacturers, considering factors such as bulk discounts, shipping costs, and payment terms. It’s essential to balance cost with quality; the cheapest option may not always deliver the best results. Engage in negotiations to clarify any ambiguous pricing details.
Step 7: Check References and Reviews
Finally, seek references from other businesses that have previously worked with the manufacturer. Look for testimonials or case studies that highlight the supplier’s reliability and customer service. Additionally, researching online reviews can provide insights into the experiences of other B2B buyers, enabling you to make a more informed decision.
By following this structured checklist, international B2B buyers can efficiently navigate the complexities of sourcing coin manufacturers, ensuring they partner with a reliable supplier that meets their specific needs and quality expectations.
Comprehensive Cost and Pricing Analysis for coin manufacturer Sourcing
What Are the Key Cost Components in Coin Manufacturing?
When sourcing from a coin manufacturer, understanding the cost structure is crucial for B2B buyers. The primary cost components include:
-
Materials: The choice of metals (copper, nickel, zinc, etc.) significantly influences the overall cost. Precious metals like silver or gold will escalate costs, impacting the final price of the coins.
-
Labor: Skilled labor is essential for both the design and production processes. Labor costs can vary greatly depending on the region, with countries in Europe generally having higher labor costs compared to those in Africa or South America.
-
Manufacturing Overhead: This includes costs related to utilities, equipment maintenance, and factory operations. Efficient production processes can minimize overhead, ultimately benefiting the buyer.
-
Tooling: Specialized molds and tools are necessary for coin production. The initial investment in tooling can be substantial, but it is amortized over larger production runs, making it essential to consider order volumes.
-
Quality Control (QC): Ensuring that the coins meet specific standards often requires rigorous QC measures. This can add to the cost, but it is vital for maintaining quality and compliance with international standards.
-
Logistics: Shipping costs can be significant, especially for international buyers. Factors such as distance, shipping method, and customs duties must be accounted for in the total cost.
-
Margin: Manufacturers will typically include a profit margin in their pricing, which can vary based on market demand and competition.
How Do Price Influencers Affect Coin Manufacturing Costs?
Several factors influence the pricing of coin manufacturing, including:
-
Volume and Minimum Order Quantity (MOQ): Larger orders often lead to lower per-unit costs. Buyers should negotiate MOQs to optimize their costs, especially when planning for large-scale projects.
-
Specifications and Customization: Custom designs or unique specifications can increase costs. Buyers should be clear about their requirements to avoid unnecessary expenses.
-
Material Quality and Certifications: Higher quality materials or specific certifications (such as ISO standards) can drive up costs. However, these may be necessary for certain markets or applications.
-
Supplier Factors: The reputation and reliability of the supplier can also influence pricing. Established manufacturers may charge more due to their experience and quality assurance processes.
-
Incoterms: Understanding Incoterms is essential for international transactions. They define the responsibilities of buyers and sellers, which can affect the overall cost structure.
What Are the Best Buyer Tips for Cost-Efficiency in Coin Manufacturing?
To maximize cost-efficiency when sourcing from a coin manufacturer, consider the following tips:
-
Negotiate Effectively: Develop a strong negotiation strategy that emphasizes your long-term partnership potential. Highlighting future orders can help secure better pricing.
-
Focus on Total Cost of Ownership (TCO): Evaluate not just the initial purchase price but also ongoing costs such as shipping, handling, and storage. Understanding TCO can lead to better financial decisions.
-
Be Aware of Pricing Nuances for International Transactions: Currency fluctuations, local taxes, and import duties can impact pricing. Buyers from regions like Africa or South America should assess these factors thoroughly.
-
Request Detailed Quotations: Ensure that quotes include a breakdown of all costs. This transparency helps in comparing suppliers and understanding where savings can be made.
-
Build Relationships with Suppliers: Establishing a good rapport with manufacturers can lead to better terms and priority service, especially in times of high demand.
Disclaimer on Indicative Pricing
Prices in the coin manufacturing industry can fluctuate based on various factors, including market demand, material costs, and geopolitical influences. It is essential for buyers to conduct thorough research and obtain updated quotes to ensure they are making informed purchasing decisions.
Alternatives Analysis: Comparing coin manufacturer With Other Solutions
Understanding the Need for Alternatives in Coin Manufacturing
In the rapidly evolving landscape of currency production, B2B buyers must consider various solutions beyond traditional coin manufacturing. The emergence of alternative technologies and methods has made it essential to analyze and compare these options to determine the most suitable for specific business needs. This section explores key alternatives to coin manufacturing, focusing on their performance, cost, ease of implementation, maintenance, and best use cases.
Comparison Table of Coin Manufacturing Alternatives
Comparison Aspect | Coin Manufacturer | Digital Currency Solutions | Automated Coin Counting Machines |
---|---|---|---|
Performance | High durability and accuracy in production | Instant transactions, scalable | Efficient counting, reduces manual labor |
Cost | High initial investment; long-term savings | Lower transaction fees | Moderate upfront cost; low operational costs |
Ease of Implementation | Complex setup and regulatory compliance | Easy integration with existing systems | Simple installation; user-friendly |
Maintenance | Requires skilled labor and regular updates | Minimal maintenance; software updates needed | Requires occasional servicing |
Best Use Case | Physical currency production for local economies | E-commerce, remittances, and microtransactions | Retail environments with high coin turnover |
What Are Digital Currency Solutions and How Do They Compare?
Digital currency solutions, such as cryptocurrencies and blockchain technology, offer a modern alternative to traditional coin manufacturing. They enable instantaneous transactions and are easily scalable, making them ideal for businesses involved in e-commerce or international remittances. However, the initial setup can involve navigating regulatory frameworks and integrating new technologies, which may require additional resources. While transaction fees are generally lower than traditional banking systems, the volatility of cryptocurrencies can pose financial risks.
How Do Automated Coin Counting Machines Function as an Alternative?
Automated coin counting machines present a practical solution for businesses dealing with large volumes of coins. These machines can quickly and accurately count coins, significantly reducing the manual labor involved in the process. They are particularly beneficial in retail environments where cash transactions are frequent. The initial investment in these machines is moderate, but they incur low operational costs, making them a cost-effective choice for businesses looking to streamline their cash handling processes. However, they do require occasional maintenance and servicing to ensure optimal performance.
Conclusion: Choosing the Right Solution for Your Business Needs
When considering alternatives to coin manufacturing, B2B buyers should assess their specific requirements, including transaction volume, budget constraints, and operational capabilities. Each option—whether it’s digital currency solutions, automated counting machines, or traditional manufacturing—has its unique advantages and drawbacks. By thoroughly evaluating these alternatives, businesses can make informed decisions that align with their strategic goals and enhance operational efficiency.
Essential Technical Properties and Trade Terminology for coin manufacturer
What Are the Key Technical Properties for Coin Manufacturing?
When engaging with coin manufacturers, understanding the essential technical properties is crucial for B2B buyers. Here are the most critical specifications to consider:
1. Material Grade: Why Is It Important?
The material grade refers to the quality and type of metal used in coin production, such as copper, nickel, or precious metals like gold and silver. Different grades offer varying levels of durability, corrosion resistance, and overall aesthetic appeal. Buyers should specify the desired material grade to ensure the coins meet both functional and visual standards, particularly in markets where quality perception directly influences customer trust and marketability.
2. Tolerance Levels: How Do They Affect Coin Quality?
Tolerance levels define the allowable deviation from specified dimensions in coin production. For example, a tolerance of ±0.1 mm may be acceptable for the diameter of a coin. Tight tolerances are critical for ensuring consistency across batches, which is especially important for coins used in vending machines or automated processes. Understanding tolerance levels helps buyers ensure the coins will perform as expected in their intended applications.
3. Coin Weight: Why Is It a Critical Specification?
Coin weight is a fundamental property that affects both the perceived value of the coin and its functionality in circulation. Variations in weight can lead to issues in transactions and may cause problems in automated systems like coin sorters. Buyers should specify the exact weight required to maintain uniformity and reliability in their coinage.
4. Surface Finish: What Role Does It Play?
The surface finish refers to the texture and appearance of the coin’s surface, which can range from matte to highly polished. A high-quality finish not only enhances the coin’s aesthetic appeal but also affects its resistance to wear and tear. Buyers should consider the intended use of the coins when selecting the surface finish, as this can impact branding and customer perception.
5. Production Method: Why Should It Matter to Buyers?
The production method encompasses the techniques used in manufacturing coins, such as stamping, casting, or electroforming. Each method has its advantages, affecting factors like cost, production speed, and the level of detail achievable in the coin design. Buyers should understand these methods to choose a manufacturer that aligns with their production needs and budget constraints.
What Are Common Trade Terms in Coin Manufacturing?
Understanding industry jargon is essential for effective communication with coin manufacturers. Here are some common terms that B2B buyers should know:
1. OEM (Original Equipment Manufacturer): What Does It Mean?
An OEM is a company that produces parts or equipment that may be marketed by another manufacturer. In the coin manufacturing industry, this term often refers to manufacturers that produce coins for other companies or governments. Understanding OEM relationships can help buyers identify reliable sources for custom coin production.
2. MOQ (Minimum Order Quantity): Why Is It Relevant?
MOQ indicates the smallest quantity of a product that a supplier is willing to sell. In coin manufacturing, MOQs can vary significantly based on the material and design complexity. Buyers should be aware of MOQs to ensure they can meet their budget and inventory needs without over-committing resources.
3. RFQ (Request for Quotation): How to Use It Effectively?
An RFQ is a document sent to suppliers asking for pricing and terms for specific products. In the context of coin manufacturing, an RFQ allows buyers to compare prices, lead times, and production capabilities. Crafting a detailed RFQ can help ensure that potential suppliers provide accurate and competitive quotes.
4. Incoterms: Why Are They Important for International Trade?
Incoterms (International Commercial Terms) are a set of rules that define the responsibilities of buyers and sellers in international transactions. These terms clarify who pays for shipping, insurance, and tariffs, which is particularly important for B2B buyers importing coins from manufacturers abroad. Understanding Incoterms can help avoid misunderstandings and streamline the procurement process.
By grasping these essential technical properties and trade terms, international B2B buyers can make informed decisions when selecting coin manufacturers, ensuring they receive high-quality products that meet their specific needs.
Navigating Market Dynamics and Sourcing Trends in the coin manufacturer Sector
What Are the Key Market Dynamics and Trends Impacting the Coin Manufacturing Sector?
The global coin manufacturing sector is experiencing dynamic shifts driven by several key factors. Notably, the rise of digital currencies is prompting traditional coin manufacturers to innovate and adapt. While physical coinage remains essential, there is an increasing demand for more secure, tamper-proof coins that can withstand advanced counterfeiting techniques. Additionally, the integration of Industry 4.0 technologies, such as IoT and AI, is revolutionizing manufacturing processes, enabling real-time monitoring and predictive maintenance. For international B2B buyers, especially in regions like Africa, South America, the Middle East, and Europe, understanding these trends is crucial for making informed sourcing decisions.
Emerging sourcing trends also highlight a shift towards local sourcing to mitigate supply chain disruptions. This is particularly pertinent for buyers in Africa and South America, where logistical challenges can hinder timely delivery. Manufacturers are increasingly focusing on supply chain transparency and resilience, ensuring that they can respond to fluctuations in demand effectively. Furthermore, the emphasis on customization is growing, with buyers seeking unique designs that reflect local culture and values, thus enhancing the appeal of the coins in their respective markets.
How Is Sustainability and Ethical Sourcing Shaping the Coin Manufacturing Industry?
Sustainability is becoming a non-negotiable aspect of the coin manufacturing sector. As environmental concerns rise globally, manufacturers are under pressure to reduce their carbon footprint and utilize eco-friendly materials. This includes the sourcing of recycled metals, which not only minimizes environmental impact but also appeals to ethically-minded consumers and businesses. For international B2B buyers, understanding the sustainability practices of their suppliers is essential.
Ethical sourcing is gaining traction, with buyers increasingly favoring manufacturers who uphold high standards in labor practices and environmental stewardship. Certifications such as ISO 14001 for environmental management and Fair Trade for labor practices are becoming critical criteria for supplier selection. Buyers from regions like Europe and the Middle East, where regulatory pressures are strong, must prioritize suppliers who demonstrate commitment to sustainability and ethical practices. This not only aligns with corporate social responsibility goals but can also enhance brand reputation and customer loyalty.
What Is the Historical Context of Coin Manufacturing and Its Relevance Today?
The history of coin manufacturing dates back thousands of years, with coins originally serving as a medium of exchange and a symbol of state power. The evolution from hand-crafted coins to modern mass production techniques reflects broader technological advancements and changing economic landscapes. In the 20th century, the introduction of automated minting processes significantly increased production efficiency and reduced costs.
Today, this historical context is vital for B2B buyers as it informs current practices and innovations within the sector. Understanding the traditional significance of coins can aid buyers in appreciating the value of cultural and historical designs in modern coin production. Moreover, as buyers navigate the complexities of sourcing, they can leverage historical insights to foster partnerships with manufacturers who respect traditional craftsmanship while embracing modern technologies. This blend of history and innovation can create unique products that resonate with consumers across diverse markets.
Frequently Asked Questions (FAQs) for B2B Buyers of coin manufacturer
-
How do I ensure the quality of coins from a manufacturer?
To ensure the quality of coins from a manufacturer, it’s vital to perform thorough due diligence. Request samples to assess the material, design, and finish. Verify the manufacturer’s certifications and compliance with international standards, such as ISO or ASTM. Consider visiting the manufacturing facility if possible, or use third-party quality assurance firms to conduct inspections. Establish clear quality criteria and communicate them during negotiations, and incorporate quality clauses in your contracts to protect your interests. -
What are the common payment terms for international coin manufacturing?
Payment terms can vary widely, but common practices include a 30% deposit before production and the balance upon completion or before shipment. Some manufacturers may offer letters of credit or escrow services for larger orders. It’s essential to discuss and agree on payment methods upfront, considering factors such as currency exchange risks and transaction fees. Ensure that the payment terms are documented in your contract to avoid disputes later. -
What are the minimum order quantities (MOQ) for custom coin manufacturing?
Minimum order quantities can vary significantly between manufacturers, often depending on the complexity of the coin design and the materials used. Typically, MOQs can range from 100 to several thousand pieces. It’s advisable to negotiate MOQs during the initial discussions, especially if you are a smaller buyer or looking to test the market with a limited run. Some manufacturers may offer flexibility in MOQs for repeat customers or bulk orders. -
How can I verify the credibility of a coin manufacturer?
To verify a coin manufacturer’s credibility, start by checking their business registration and industry certifications. Look for reviews or testimonials from previous clients, which can be found on platforms like LinkedIn or trade forums. Request references from other businesses that have previously worked with the manufacturer. Additionally, consider using third-party verification services to assess the manufacturer’s financial stability and production capabilities. -
What customization options are available for coin manufacturing?
Customization options in coin manufacturing can include various aspects such as size, shape, design, and materials. Many manufacturers offer services like engraving, color plating, and unique finishes to suit specific branding needs. Discuss your requirements early in the negotiation process to understand the capabilities and limitations of the manufacturer. Providing detailed specifications and examples can help ensure that the final product meets your expectations. -
What are the logistics considerations for shipping coins internationally?
When shipping coins internationally, consider factors such as customs regulations, shipping costs, and delivery timelines. Work with a logistics provider experienced in handling precious metals or coins to navigate potential challenges. Ensure that your shipping agreement includes insurance to cover loss or damage during transit. Additionally, confirm that the manufacturer is familiar with the necessary documentation for customs clearance to prevent delays. -
How can I address potential language barriers with an international manufacturer?
Addressing language barriers can be crucial in ensuring clear communication with an international manufacturer. If possible, work with a bilingual representative or hire a professional translator during negotiations. Utilize visual aids, such as diagrams or sample designs, to convey your requirements more effectively. Establish clear communication protocols, including regular updates via email or video calls, to facilitate understanding and minimize misunderstandings. -
What are the common challenges in international trade for coin manufacturing?
Common challenges in international trade for coin manufacturing include navigating complex customs regulations, managing currency exchange fluctuations, and ensuring compliance with both local and international standards. Additionally, differences in business practices and communication styles can create misunderstandings. To mitigate these issues, conduct thorough market research, establish strong relationships with local partners, and stay informed about trade policies that may affect your operations.
Important Disclaimer & Terms of Use
⚠️ Important Disclaimer
The information provided in this guide, including content regarding manufacturers, technical specifications, and market analysis, is for informational and educational purposes only. It does not constitute professional procurement advice, financial advice, or legal advice.
While we have made every effort to ensure the accuracy and timeliness of the information, we are not responsible for any errors, omissions, or outdated information. Market conditions, company details, and technical standards are subject to change.
B2B buyers must conduct their own independent and thorough due diligence before making any purchasing decisions. This includes contacting suppliers directly, verifying certifications, requesting samples, and seeking professional consultation. The risk of relying on any information in this guide is borne solely by the reader.
Strategic Sourcing Conclusion and Outlook for coin manufacturer
As the demand for coin manufacturing continues to evolve, international B2B buyers must prioritize strategic sourcing to secure reliable partnerships. What are the key benefits of strategic sourcing for coin manufacturers? By leveraging strategic sourcing, buyers can enhance cost efficiency, ensure consistent quality, and foster innovation. This approach enables companies to evaluate suppliers based on their capabilities, sustainability practices, and ability to meet specific market demands, especially in emerging regions such as Africa and South America.
How can B2B buyers prepare for future trends in coin manufacturing? Staying informed about technological advancements and regulatory changes is essential. Buyers should actively engage with suppliers to understand their production capabilities and sustainability initiatives. This proactive approach will not only mitigate risks but also open doors to new opportunities in diverse markets.
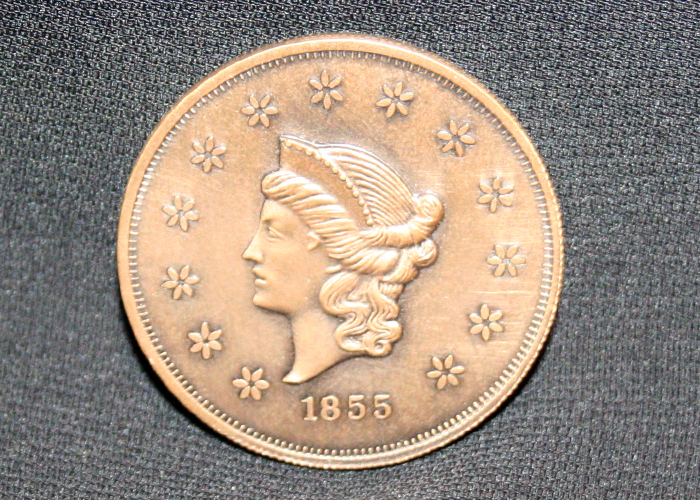
A stock image related to coin manufacturer.
In conclusion, the landscape of coin manufacturing is ripe with potential for those who embrace strategic sourcing. What steps can you take today to enhance your sourcing strategy? As you navigate this dynamic industry, consider forming alliances with manufacturers that align with your business values and growth objectives. The future of coin manufacturing is bright, and your strategic decisions today will pave the way for success tomorrow.