Discover Cost-Saving Tips from Top Fuse Manufacturers (2025)
Introduction: Navigating the Global Market for fuse manufacturer
In today’s interconnected world, sourcing reliable fuse manufacturers poses significant challenges for international B2B buyers, particularly in emerging markets across Africa, South America, the Middle East, and Europe. With the critical role that fuses play in electrical systems, understanding the diverse types, applications, and quality standards is essential for making informed purchasing decisions. This guide provides a comprehensive overview of the fuse manufacturing landscape, covering everything from common fuse types and their specific applications to effective strategies for vetting suppliers and evaluating costs.
As you navigate the global market for fuse manufacturers, this guide will empower you with actionable insights tailored to your region’s unique requirements. It addresses key concerns, such as identifying reputable suppliers, understanding regulatory compliance, and optimizing procurement processes. By breaking down complex concepts and providing practical tips, we aim to enhance your purchasing strategy and ensure you select the right products for your business needs.
Whether you are based in Colombia, Indonesia, or elsewhere, this resource will equip you with the knowledge necessary to confidently engage with suppliers and secure quality fuses that meet your operational demands. Join us as we delve into the essential elements of sourcing from fuse manufacturers, ultimately paving the way for successful international trade and collaboration.
Understanding fuse manufacturer Types and Variations
Type Name | Key Distinguishing Features | Primary B2B Applications | Brief Pros & Cons for Buyers |
---|---|---|---|
Cartridge Fuses | Cylindrical design, replaceable elements | Industrial machinery, electrical panels | Pros: Easy to replace, compact size. Cons: Limited current ratings. |
Blade Fuses | Flat, plastic body with metal blades | Automotive, consumer electronics | Pros: Cost-effective, widely available. Cons: Not suitable for high voltage applications. |
Resettable Fuses | Automatically resets after overload | Power supplies, telecommunications | Pros: Reduces downtime, user-friendly. Cons: May not provide complete protection. |
Glass Fuses | Transparent casing for visibility | Small appliances, lighting circuits | Pros: Easy to inspect, low cost. Cons: Fragile, can break under impact. |
Semiconductor Fuses | Designed for high-speed circuits | Electronics, renewable energy systems | Pros: High precision, minimal energy loss. Cons: More expensive than traditional fuses. |
What Are the Key Characteristics of Cartridge Fuses?
Cartridge fuses are cylindrical in shape and typically feature a replaceable element inside. They are designed to protect circuits by melting and breaking the connection when excessive current flows through. These fuses are commonly used in industrial applications, including machinery and electrical panels, where space is a concern. When purchasing, buyers should consider the current rating and voltage capacity, as well as the ease of replacement.
Why Choose Blade Fuses for Automotive Applications?
Blade fuses are characterized by their flat, plastic body and metal blades that fit into a socket. They are predominantly used in automotive and consumer electronic applications due to their low cost and availability. When selecting blade fuses, buyers should focus on the amperage ratings and dimensions to ensure compatibility with existing systems. However, their limitations in high voltage scenarios can be a drawback.
How Do Resettable Fuses Enhance Operational Efficiency?
Resettable fuses, also known as polyfuses or PTCs (Positive Temperature Coefficient devices), automatically reset themselves after a fault condition is cleared. This feature makes them particularly useful in power supply applications and telecommunications, where minimizing downtime is crucial. When considering resettable fuses, buyers should evaluate their specific application needs, as these fuses may not provide the same level of protection as traditional fuses.
What Advantages Do Glass Fuses Offer in Small Appliances?
Glass fuses are easily identifiable due to their transparent casing, which allows for quick visual inspection. They are often used in small appliances and lighting circuits. While they are low-cost and simple to replace, buyers should be cautious of their fragility, as glass fuses can break under impact. It’s essential to consider the environment in which these fuses will be used to avoid premature failure.
Why Are Semiconductor Fuses Important for High-Speed Applications?
Semiconductor fuses are designed specifically for high-speed circuits and applications that require precise current interruption. They are commonly found in electronic devices and renewable energy systems, where they minimize energy loss and enhance performance. However, these fuses tend to be more expensive than traditional options, so buyers should weigh the benefits of high precision against their budget constraints when making a purchasing decision.
Related Video: The Differences Between Ceramic and Glass Mini Fuses and Mini Fuse Basics
Key Industrial Applications of fuse manufacturer
Industry/Sector | Specific Application of Fuse Manufacturer | Value/Benefit for the Business | Key Sourcing Considerations for this Application |
---|---|---|---|
Electrical Utilities | Overcurrent protection in substations | Prevents equipment damage and ensures reliable power supply | Compliance with local regulations and standards; sourcing from certified manufacturers |
Manufacturing | Protection in automated machinery | Minimizes downtime and maintenance costs | Durability and response time; compatibility with existing systems |
Automotive | Fuse systems in electric vehicles | Enhances safety and reliability of electrical systems | High-temperature resistance; adherence to automotive standards |
Construction | Circuit protection in building electrical systems | Reduces fire hazards and equipment failures | Availability of customized solutions for various voltages |
Telecommunications | Fuse protection in telecom equipment | Ensures uninterrupted service and equipment longevity | Sourcing from suppliers with a strong track record in telecom applications |
How is Fuse Manufacturer Used in Electrical Utilities?
In the electrical utilities sector, fuse manufacturers provide critical components for overcurrent protection in substations. Fuses are essential in safeguarding transformers, circuit breakers, and other equipment against overloads, which can lead to catastrophic failures and outages. For international B2B buyers, especially in regions like Africa and South America, it is vital to ensure that sourced fuses comply with local regulations and standards to maintain safety and operational efficiency.
What Role Do Fuses Play in Manufacturing Automation?
In manufacturing environments, fuses are integral to the protection of automated machinery. They help minimize downtime and reduce maintenance costs by preventing electrical faults that could disrupt production lines. Buyers from Europe and the Middle East should prioritize sourcing fuses that offer durability and quick response times to ensure compatibility with existing systems and enhance overall productivity.
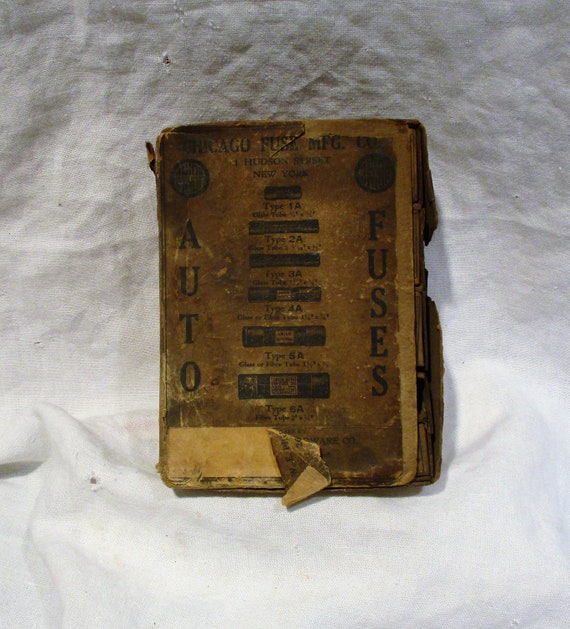
A stock image related to fuse manufacturer.
How Are Fuses Essential for Automotive Applications?
In the automotive industry, fuse manufacturers supply fuse systems for electric vehicles (EVs) and traditional cars alike. These fuses enhance the safety and reliability of electrical systems, which are critical as vehicles become increasingly reliant on electronics. Buyers should focus on fuses that exhibit high-temperature resistance and comply with automotive standards, ensuring that sourced components can withstand the rigors of automotive environments.
Why Are Fuses Crucial in Construction Electrical Systems?
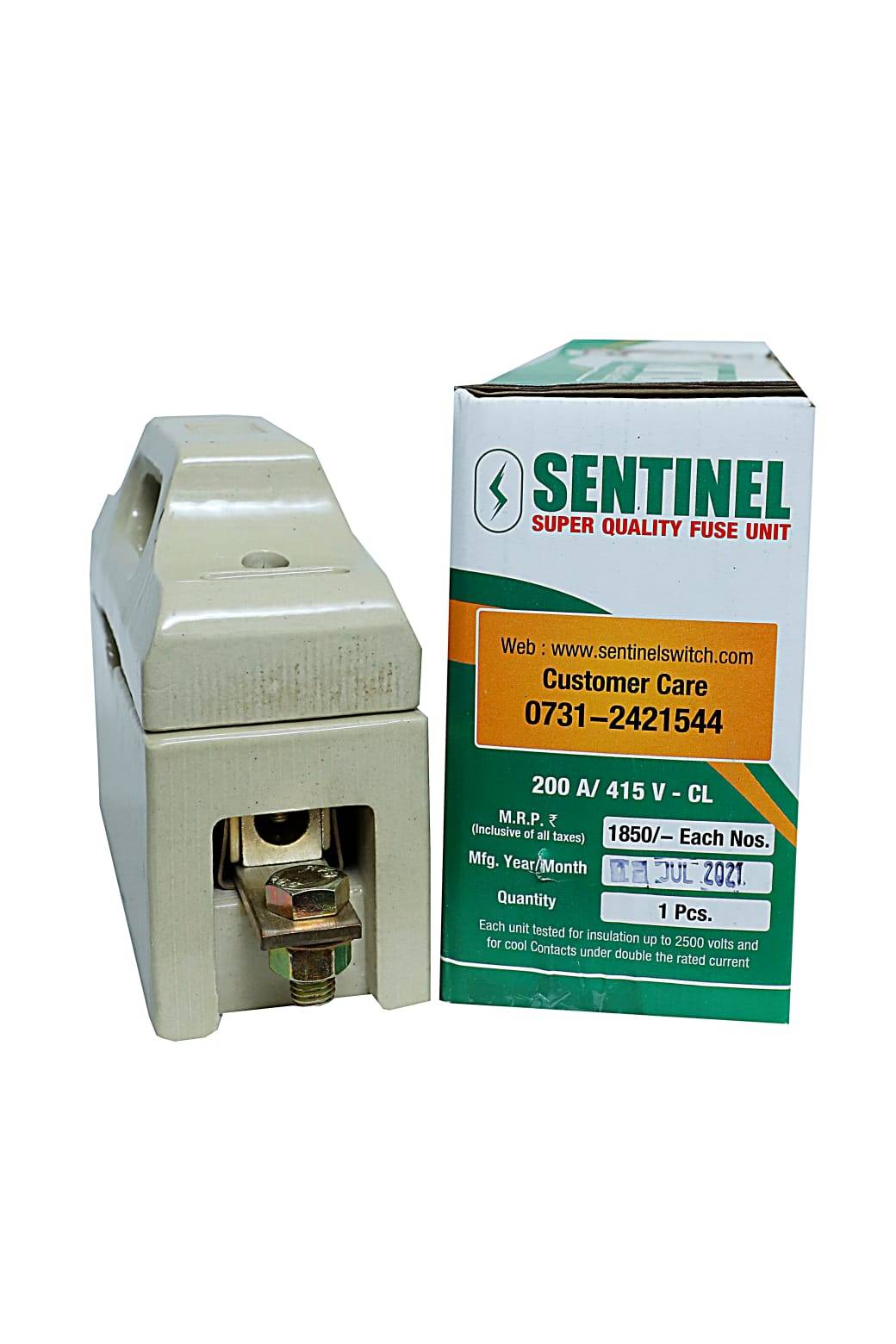
A stock image related to fuse manufacturer.
In the construction sector, fuses play a vital role in protecting electrical systems within buildings. They reduce the risk of fire hazards and equipment failures by ensuring that circuits are protected from overloads. International buyers should consider sourcing customized fuse solutions that cater to various voltage requirements, ensuring that they meet the specific needs of their projects while adhering to safety regulations.
How Do Fuses Support Telecommunications Equipment?
Fuse manufacturers also provide essential protection for telecommunications equipment, ensuring uninterrupted service and prolonging equipment longevity. As telecom networks expand, the reliability of electrical systems becomes paramount. B2B buyers should seek suppliers with a proven track record in telecom applications, focusing on the availability of high-quality fuses that meet stringent performance standards.
Related Video: Glass Fusing 101: How To Fuse Glass
3 Common User Pain Points for ‘fuse manufacturer’ & Their Solutions
Scenario 1: Navigating Compliance and Certification Challenges in Fuse Procurement
The Problem:
B2B buyers in industries such as manufacturing and construction often face the daunting task of ensuring that the fuses they source comply with local and international safety standards. This is particularly challenging for buyers in regions like Africa and South America, where regulatory frameworks may differ significantly from those in Europe or the Middle East. The lack of clear certification documentation can lead to delays in production, legal liabilities, or even project shutdowns.
The Solution:
To effectively navigate compliance issues, buyers should conduct thorough research on the certifications required for fuses in their specific industry and region. Engage with reputable fuse manufacturers who can provide detailed product specifications and compliance documentation upfront. Consider establishing relationships with suppliers who have a proven track record in your market and can assist in navigating local regulations. Additionally, investing in a compliance management system can streamline the process by tracking certification requirements and ensuring all products sourced are compliant, thereby reducing the risk of costly delays or penalties.
Scenario 2: Addressing Supply Chain Disruptions for Fuse Availability
The Problem:
Supply chain disruptions have become increasingly common, with global events affecting the availability of critical components like fuses. B2B buyers often find themselves scrambling to source fuses at the last minute, which can lead to inflated costs and project delays. This scenario is particularly prevalent in regions with less established supply chains, such as parts of Africa and South America.
The Solution:
To mitigate supply chain risks, buyers should adopt a proactive sourcing strategy. Start by identifying multiple suppliers and diversifying your supply base to reduce dependence on a single source. Establishing long-term contracts with fuse manufacturers can provide a buffer against price fluctuations and ensure consistent availability. Additionally, implementing a just-in-time inventory system can help manage stock levels efficiently, reducing the need for large upfront purchases while ensuring you have access to necessary components when required. Regularly communicating with suppliers about their production capacities and potential disruptions can also help in planning accordingly.
Scenario 3: Overcoming Technical Specification Confusion for Fuses
The Problem:
B2B buyers often encounter confusion when it comes to the technical specifications of fuses, especially when dealing with different manufacturers who may use varying terminologies and standards. This confusion can lead to the procurement of incorrect fuses, resulting in compatibility issues, equipment failures, and increased costs. Buyers in the Middle East and Europe may find this particularly challenging due to the variety of standards in use.
The Solution:
To overcome technical specification confusion, buyers should develop a comprehensive understanding of the specific fuse types required for their applications. This involves not only familiarizing oneself with industry standards but also engaging directly with fuse manufacturers to clarify specifications and compatibility. Utilizing digital tools, such as product configurators or specification sheets, can provide additional clarity. Furthermore, establishing a technical advisory relationship with manufacturers can facilitate better understanding and enable buyers to receive tailored recommendations based on their unique operational needs. Documenting these specifications in a centralized database can also streamline future procurement processes and reduce errors.
By addressing these common pain points with actionable strategies, B2B buyers can ensure smoother operations and more successful procurement outcomes in their sourcing of fuses.
Strategic Material Selection Guide for fuse manufacturer
What Are the Key Materials Used in Fuse Manufacturing?
When selecting materials for fuse manufacturing, understanding the properties, advantages, and limitations of various materials is crucial for ensuring product performance and compliance with international standards. Below, we analyze four common materials used in fuse production: copper, aluminum, silver, and ceramic.
How Does Copper Benefit Fuse Manufacturing?
Copper is one of the most widely used materials in fuse manufacturing due to its excellent electrical conductivity and thermal properties.
- Key Properties: Copper has a high melting point of about 1,984°F (1,085°C) and excellent corrosion resistance, making it suitable for various environments.
- Pros: Its high conductivity ensures minimal energy loss, enhancing fuse efficiency. Copper is also relatively easy to work with, allowing for complex designs.
- Cons: The primary drawback of copper is its cost, which can be higher than alternative materials. Additionally, copper can be susceptible to oxidation if not properly coated.
- Impact on Application: Copper fuses are ideal for high-current applications and environments where conductivity is paramount. However, they may not be suitable for corrosive environments without protective coatings.
- Considerations for International Buyers: Buyers from regions like Africa and South America should consider local availability and pricing fluctuations. Compliance with standards such as ASTM B170 for copper may also be necessary.
What Role Does Aluminum Play in Fuse Manufacturing?
Aluminum is another popular choice for fuse manufacturing, known for its lightweight and cost-effective properties.
- Key Properties: Aluminum has a lower melting point (1,221°F or 660°C) compared to copper but offers good conductivity and corrosion resistance.
- Pros: Its lightweight nature makes it easier to handle and install, reducing shipping costs. Additionally, aluminum is generally less expensive than copper.
- Cons: Aluminum’s lower conductivity means that larger cross-sections are required for equivalent performance, which can complicate design. It is also more prone to oxidation, necessitating protective measures.
- Impact on Application: Aluminum fuses are suitable for applications where weight is a concern, such as in portable equipment. However, they may not perform as well in high-temperature environments.
- Considerations for International Buyers: Buyers should ensure compliance with standards like ASTM B221 for aluminum products. In regions with high humidity, additional considerations for oxidation resistance are essential.
How Does Silver Enhance Fuse Performance?
Silver is often used in specialized fuses due to its superior conductivity and thermal properties.
- Key Properties: Silver has the highest electrical conductivity of all metals and a melting point of 1,763°F (961.8°C), making it ideal for high-performance applications.
- Pros: Its excellent conductivity reduces heat generation, enhancing fuse reliability and longevity. Silver also exhibits good corrosion resistance.
- Cons: The primary limitation is its high cost, which can make silver fuses prohibitively expensive for many applications.
- Impact on Application: Silver fuses are ideal for high-precision applications, such as in electronic devices, where performance is critical. However, their cost may restrict usage to specialized sectors.
- Considerations for International Buyers: Compliance with international standards for precious metals, such as ASTM B700, is crucial. Buyers should also consider the economic implications of using silver in regions with fluctuating metal prices.
Why Are Ceramics Important in Fuse Manufacturing?
Ceramics are increasingly used in fuse manufacturing due to their excellent insulation properties and thermal stability.
- Key Properties: Ceramics can withstand high temperatures (up to 2,600°F or 1,426°C) and are non-conductive, making them ideal for insulating applications.
- Pros: Their durability and resistance to thermal shock make ceramics suitable for harsh environments. They also provide excellent dielectric strength.
- Cons: The main drawback is their brittleness, which can lead to breakage during handling or installation. Additionally, ceramics can be more complex to manufacture.
- Impact on Application: Ceramic fuses are ideal for high-voltage applications where insulation is critical. However, their fragility may limit their use in portable or high-impact environments.
- Considerations for International Buyers: Buyers should ensure compliance with standards like IEC 60269 for fuse links. Additionally, understanding local manufacturing capabilities for ceramics can impact sourcing decisions.
Summary Table of Material Selection for Fuse Manufacturing
Material | Typical Use Case for Fuse Manufacturer | Key Advantage | Key Disadvantage/Limitation | Relative Cost (Low/Med/High) |
---|---|---|---|---|
Copper | High-current applications | Excellent conductivity | Higher cost, oxidation susceptibility | High |
Aluminum | Portable equipment | Lightweight and cost-effective | Lower conductivity, oxidation issues | Medium |
Silver | High-precision electronics | Superior conductivity | Very high cost | High |
Ceramic | High-voltage applications | Excellent insulation and durability | Brittleness and manufacturing complexity | Medium |
This guide serves as a strategic overview for international B2B buyers in selecting the appropriate materials for fuse manufacturing, considering performance, cost, and compliance with relevant standards.
In-depth Look: Manufacturing Processes and Quality Assurance for fuse manufacturer
What Are the Main Stages of Manufacturing Processes for Fuse Production?
Manufacturing fuses involves several critical stages that ensure the final product meets quality and performance standards. Here’s a breakdown of the typical manufacturing process:
1. Material Preparation
The first step in the fuse manufacturing process is the selection and preparation of raw materials. Common materials used include copper, aluminum, and ceramic for the fuse body, as well as various alloys for the conductive elements.
- Material Sourcing: B2B buyers should prioritize suppliers that source materials from reputable suppliers to ensure quality and consistency.
- Preliminary Testing: Before production, materials undergo testing for electrical conductivity, thermal resistance, and mechanical strength.
2. Forming
The forming stage involves shaping the raw materials into the required components of the fuse. This process can include:
- Stamping: For metal components, stamping machines create the necessary shapes and sizes from sheets of metal.
- Molding: For ceramic or plastic parts, molding techniques are used to form the fuse bodies.
3. Assembly
Once the components are formed, they are assembled into a complete fuse. This stage typically involves:
- Joining Techniques: Methods such as soldering or welding are employed to connect the metal elements securely.
- Integration of Safety Features: Many modern fuses include safety features like indicators for blown fuses or thermal fuses that disconnect under specific conditions.
4. Finishing
The finishing stage enhances the fuse’s durability and performance. This can include:
- Coating: Applying protective coatings to prevent corrosion and enhance thermal stability.
- Labeling: Clear labeling is critical for compliance with international standards and for ease of use by end-users.
How is Quality Assurance Implemented in Fuse Manufacturing?
Quality assurance (QA) is crucial in the fuse manufacturing process to ensure reliability and safety. Here are the key components of a robust QA system:
International Standards for Quality Control
B2B buyers should look for manufacturers that comply with internationally recognized standards. Key certifications include:
- ISO 9001: This standard focuses on quality management systems and is applicable across industries, ensuring consistent quality in products and services.
- CE Marking: For products sold in Europe, CE marking indicates compliance with health, safety, and environmental protection standards.
Industry-Specific Standards
Beyond general quality management, certain industries have specific requirements:
- API (American Petroleum Institute): For fuses used in oil and gas applications, adherence to API standards is crucial.
- IEC (International Electrotechnical Commission): Compliance with IEC standards ensures that electrical components meet international safety and performance criteria.
What Are the Key QC Checkpoints in Fuse Manufacturing?
Quality control (QC) checkpoints are vital to maintaining high standards throughout the manufacturing process. Key checkpoints include:
-
Incoming Quality Control (IQC): At this stage, raw materials are inspected for quality before being used in production. This includes checking for defects and verifying certifications.
-
In-Process Quality Control (IPQC): During manufacturing, regular inspections are conducted to ensure that each stage of the process adheres to established specifications. This includes monitoring machinery and techniques to prevent defects.
-
Final Quality Control (FQC): Once the fuses are assembled, they undergo a final inspection. This includes testing for electrical performance, mechanical strength, and safety features.
What Testing Methods Are Commonly Used for Fuses?
Testing is critical to ensuring that fuses operate correctly under expected conditions. Common testing methods include:
-
Electrical Testing: This involves checking the current rating and performance under load conditions. Buyers should ensure that suppliers use calibrated equipment for accuracy.
-
Thermal Testing: Fuses are subjected to temperature variations to assess their response to overheating and ensure they will trip under fault conditions.
-
Mechanical Testing: Evaluating the physical integrity of the fuse, including stress tests to simulate real-world conditions.
How Can B2B Buyers Verify Supplier Quality Control Processes?
Verifying a supplier’s quality control processes is essential for international B2B buyers to ensure reliability. Here are several methods to consider:
-
Supplier Audits: Conducting on-site audits allows buyers to assess the manufacturing environment, equipment, and QA processes directly. This is particularly important for buyers in Africa and South America, where local manufacturing standards may vary.
-
Quality Reports: Requesting detailed quality reports from suppliers can provide insights into their QC processes, testing results, and compliance with international standards.
-
Third-Party Inspections: Engaging independent inspection agencies can provide an unbiased evaluation of a supplier’s manufacturing and quality assurance practices.
What Are the Nuances of Quality Control for International B2B Buyers?
International B2B buyers must navigate various challenges when assessing quality control in fuse manufacturing:
-
Understanding Regional Standards: Different regions may have unique standards and regulations. Buyers should familiarize themselves with local compliance requirements in their respective markets, such as those in the Middle East or Europe.
-
Language Barriers: Communication issues can arise when dealing with suppliers from different countries. Ensure that documentation and reports are available in a language that is easily understandable.
-
Cultural Differences: Cultural nuances may affect business practices and quality expectations. Building strong relationships with suppliers can help mitigate misunderstandings and ensure a shared commitment to quality.
By considering these aspects, international B2B buyers can make informed decisions when sourcing fuses, ensuring that they partner with manufacturers who uphold high standards of quality and reliability.
Practical Sourcing Guide: A Step-by-Step Checklist for ‘fuse manufacturer’
In the competitive landscape of B2B procurement, sourcing fuses from reliable manufacturers requires a strategic approach. This guide provides a step-by-step checklist to help international buyers, particularly from Africa, South America, the Middle East, and Europe, efficiently navigate the sourcing process.
Step 1: Define Your Technical Specifications
Before initiating contact with suppliers, clarify your technical requirements. This includes the type of fuses needed (e.g., blade fuses, cartridge fuses), voltage ratings, current ratings, and any specific standards (like IEC or UL certifications) that must be met. A well-defined specification will streamline discussions and ensure you receive suitable products.
Step 2: Research Potential Manufacturers
Conduct thorough research to identify potential fuse manufacturers. Utilize industry directories, trade shows, and online platforms to compile a list of suppliers. Focus on manufacturers with a proven track record and positive reviews from previous clients. This research phase is critical to ensure you are considering reputable companies.
Step 3: Evaluate Supplier Certifications
✅ Verify Supplier Certifications
Check that the manufacturers hold relevant certifications, such as ISO 9001 for quality management or specific electrical safety certifications. These certifications indicate a commitment to quality and compliance with international standards, reducing the risk of faulty products.
Step 4: Request Samples for Testing
Before placing a bulk order, request samples of the fuses for testing. This allows you to assess the quality, performance, and compatibility of the products with your applications. Ensure the samples meet your specifications and perform as expected under operational conditions.
Step 5: Analyze Pricing Structures
When comparing suppliers, analyze their pricing structures carefully. Look beyond the base price; consider factors such as minimum order quantities, bulk discounts, and shipping costs. Understanding the total cost of acquisition will help you make informed financial decisions.
Step 6: Assess Supplier Communication and Support
Evaluate the responsiveness and professionalism of potential suppliers. Effective communication is vital for addressing issues and ensuring a smooth procurement process. A supplier that provides clear answers and support can significantly enhance your sourcing experience.
Step 7: Negotiate Terms and Place Your Order
Once you have selected a supplier, engage in negotiations to finalize the terms of your purchase. Discuss payment terms, delivery schedules, and return policies. A well-negotiated agreement will lay the foundation for a successful long-term partnership.
By following this checklist, B2B buyers can effectively source fuses from reputable manufacturers, ensuring quality products that meet their operational needs.
Comprehensive Cost and Pricing Analysis for fuse manufacturer Sourcing
What Are the Key Cost Components in Fuse Manufacturing?
When sourcing fuses, understanding the cost structure is essential for B2B buyers. The primary cost components include:
-
Materials: The choice of materials significantly influences the cost. Common materials for fuses include copper, aluminum, and specialized alloys. High-quality materials may increase initial costs but can reduce failure rates and increase longevity, ultimately leading to lower Total Cost of Ownership (TCO).
-
Labor: Labor costs vary by region and can impact overall pricing. In regions with higher labor costs, such as parts of Europe, manufacturers may pass these costs onto buyers. Conversely, suppliers in countries with lower labor costs may offer more competitive pricing.
-
Manufacturing Overhead: This includes costs related to facility maintenance, utilities, and administrative expenses. Understanding how a supplier allocates these costs can provide insight into their pricing model.
-
Tooling: Custom tooling for specific fuse designs can be a significant upfront cost. Buyers should consider whether the supplier has the necessary tooling already or if additional charges will apply for custom designs.
-
Quality Control (QC): Implementing rigorous QC processes ensures product reliability and compliance with international standards. Suppliers with robust QC measures may charge more, but this can mitigate risks associated with product failures.
-
Logistics: Shipping costs vary based on the Incoterms chosen, the shipping method, and the distance to the destination. Understanding logistics costs is crucial for calculating the total landed cost of the product.
-
Margin: Suppliers will include a profit margin in their pricing. This margin can vary based on competition, demand, and the uniqueness of the product.
How Do Pricing Influencers Affect Fuse Sourcing?
Several factors can influence the pricing of fuses, including:
-
Volume and Minimum Order Quantity (MOQ): Higher order volumes often lead to lower unit prices. Buyers should negotiate MOQ terms to achieve cost efficiencies, particularly if they anticipate future demand growth.
-
Specifications and Customization: Customized fuses tailored to specific applications may incur higher costs. Buyers should assess whether the customization aligns with their operational needs and budget constraints.
-
Materials and Quality Certifications: The quality and source of materials can affect pricing. Fuses that meet international quality certifications (like ISO or IEC standards) may command a premium but provide assurance of reliability.
-
Supplier Factors: A supplier’s reputation, reliability, and experience can also influence pricing. Well-established suppliers may charge more due to their proven track record and quality assurance practices.
-
Incoterms: The terms of sale can significantly impact overall costs. For instance, using DDP (Delivered Duty Paid) may simplify logistics but could also increase upfront costs compared to EXW (Ex Works), where the buyer assumes more responsibility.
What Are the Best Buyer Tips for Cost-Efficient Fuse Sourcing?
For international B2B buyers, particularly those from Africa, South America, the Middle East, and Europe, consider the following strategies:
-
Negotiate Terms: Engage suppliers in discussions about pricing, MOQ, and payment terms. Leveraging relationships can lead to better pricing structures.
-
Focus on Total Cost of Ownership (TCO): Evaluate not just the purchase price but also maintenance, operational costs, and potential downtime costs associated with fuse failures. This holistic view can guide smarter purchasing decisions.
-
Understand Pricing Nuances: Be aware that pricing can fluctuate based on currency exchange rates, tariffs, and local market conditions. This is particularly relevant when sourcing from different continents.
-
Request Samples: Before committing to large orders, request samples to assess quality. This can help avoid costly mistakes and ensure the supplier meets your specifications.
-
Explore Multiple Suppliers: Don’t settle for the first quote. Comparing multiple suppliers can provide a clearer picture of the market and help in negotiating better terms.
Disclaimer on Indicative Prices
While this analysis provides a framework for understanding costs and pricing in fuse manufacturing, actual prices can vary widely based on market conditions, supplier capabilities, and specific buyer requirements. It is advisable to conduct thorough market research and engage directly with suppliers for the most accurate pricing information.
Alternatives Analysis: Comparing fuse manufacturer With Other Solutions
Exploring Alternatives to Fuse Manufacturers
In the realm of electrical protection devices, selecting the appropriate solution is crucial for international B2B buyers. While fuse manufacturers are a common choice for safeguarding electrical circuits, there are several alternative solutions that may offer distinct advantages depending on specific operational needs and regional considerations.
Comparison Table of Fuse Manufacturer and Alternatives
Comparison Aspect | Fuse Manufacturer | Circuit Breakers | Surge Protection Devices |
---|---|---|---|
Performance | Effective for overload protection, but limited in response time. | Instantaneous response to overloads and short circuits, can reset automatically. | Protects against voltage spikes but not against overloads. |
Cost | Generally lower initial cost but requires replacement after failure. | Higher upfront cost but long-term savings due to durability. | Moderate cost depending on specifications and installation complexity. |
Ease of Implementation | Simple installation process, requiring basic electrical knowledge. | Installation can be more complex, often needing a professional electrician. | Installation complexity varies; some can be DIY, while others need professional help. |
Maintenance | Minimal; requires replacement when blown. | Low maintenance; periodic testing recommended. | Requires regular inspection to ensure effectiveness. |
Best Use Case | Ideal for residential and small commercial applications. | Best for industrial settings or high-load applications needing frequent resets. | Suitable for protecting sensitive electronics in both residential and commercial settings. |
Detailed Breakdown of Alternatives
What Are Circuit Breakers and Why Consider Them?
Circuit breakers are devices that protect electrical circuits by automatically shutting off power when an overload or short circuit is detected. Their instantaneous response time can prevent potential damage to equipment and reduce fire hazards. While circuit breakers come at a higher upfront cost compared to fuses, their ability to reset without replacement can lead to long-term savings, especially in environments with frequent power fluctuations. For B2B buyers, especially those in industrial sectors, circuit breakers may provide a more reliable solution despite the initial investment.
How Do Surge Protection Devices Function?
Surge protection devices (SPDs) are designed to safeguard electronic equipment from voltage spikes caused by lightning strikes or sudden changes in electricity supply. While they do not provide overload protection like fuses or circuit breakers, SPDs are essential for protecting sensitive electronics, such as computers and communication equipment. Their cost can vary, but they are generally seen as a worthwhile investment in environments where electrical surges are frequent. For businesses in sectors that rely heavily on electronics, such as IT or telecommunications, integrating SPDs into their electrical systems can mitigate costly equipment damage.
Conclusion: How to Choose the Right Solution for Your Needs
When deciding between a fuse manufacturer and alternative solutions like circuit breakers or surge protection devices, B2B buyers should consider their specific operational requirements, budget constraints, and the potential for future scalability. Assessing the performance, cost, ease of implementation, and maintenance needs will help in making an informed decision. Ultimately, the right choice will depend on balancing immediate costs with long-term benefits, ensuring that the selected solution aligns with both current and future business needs.
Essential Technical Properties and Trade Terminology for fuse manufacturer
What Are the Essential Technical Properties of Fuses for B2B Buyers?
When selecting fuses for industrial applications, understanding their technical properties is crucial. Here are some critical specifications to consider:
-
Material Grade
Fuses are typically made from materials like copper, aluminum, or alloy compositions. The material choice impacts the fuse’s conductivity, melting point, and overall durability. For B2B buyers, selecting the right material ensures optimal performance and compliance with safety standards. -
Current Rating
This specification indicates the maximum continuous current a fuse can handle without tripping. It is essential for preventing equipment damage and ensuring operational efficiency. Buyers must match the current rating to their specific application to avoid premature failures or unsafe conditions. -
Voltage Rating
Voltage rating specifies the maximum voltage the fuse can safely interrupt. Inadequate voltage ratings can lead to catastrophic failures, making it imperative for buyers to understand the voltage requirements of their electrical systems when sourcing fuses. -
Response Time
The response time of a fuse refers to how quickly it can interrupt an overload or short circuit. Fast-acting fuses are critical for sensitive electronic equipment, while time-delay fuses may be more suitable for motor applications. Buyers should assess the required response time based on their operational needs. -
Breaking Capacity
This indicates the maximum fault current a fuse can safely interrupt without causing an explosion or fire. Understanding breaking capacity is vital for ensuring safety and compliance with local regulations, which can vary significantly across regions, including Africa and South America. -
Temperature Coefficient
This property measures how a fuse’s resistance changes with temperature. A low temperature coefficient means that the fuse maintains consistent performance across varying temperatures, which is essential for applications in extreme conditions. Buyers should consider the operating environment when evaluating this specification.
What Are the Key Trade Terms B2B Buyers Should Know in the Fuse Industry?
Understanding industry jargon is essential for effective communication and negotiation in the fuse manufacturing sector. Here are some important terms:
-
OEM (Original Equipment Manufacturer)
OEM refers to companies that produce parts or equipment that may be marketed by another manufacturer. For fuse buyers, working with OEMs ensures that they receive products that meet specific quality and compatibility standards. -
MOQ (Minimum Order Quantity)
MOQ is the smallest quantity of a product that a supplier is willing to sell. Understanding MOQ is crucial for buyers to manage inventory costs effectively and negotiate better terms with suppliers, especially when sourcing from international markets. -
RFQ (Request for Quotation)
An RFQ is a document issued by a buyer to solicit price quotes from suppliers. It typically includes specifications, quantities, and delivery requirements. Crafting a clear RFQ can streamline the procurement process and help buyers receive accurate and competitive pricing. -
Incoterms
Incoterms are international commercial terms that define the responsibilities of buyers and sellers in international transactions. Familiarity with these terms can help B2B buyers understand shipping costs, risk, and insurance, particularly when dealing with suppliers from different continents. -
Lead Time
Lead time refers to the time taken from placing an order to the delivery of the product. For fuse manufacturers, understanding lead times is essential for planning production schedules and meeting project deadlines. -
Certification Standards
These are regulatory benchmarks that fuses must meet to ensure safety and reliability. Common standards include IEC, UL, and ISO certifications. Buyers should verify that their suppliers comply with relevant certification standards to ensure product quality and safety in their applications.
By grasping these technical properties and trade terms, B2B buyers from diverse regions can make informed decisions when sourcing fuses, enhancing operational safety and efficiency in their respective industries.
Navigating Market Dynamics and Sourcing Trends in the fuse manufacturer Sector
What Are the Current Market Dynamics and Key Trends in the Fuse Manufacturing Sector?
The global fuse manufacturing market is experiencing significant growth driven by increasing demand for electrical safety and reliability across various industries. Key drivers include the expansion of renewable energy sources, the rise of electric vehicles (EVs), and the ongoing digitalization of industrial operations. In regions like Africa and South America, infrastructure development and urbanization are catalyzing investments in electrical systems, which in turn boosts the demand for high-quality fuses.
Emerging technologies such as IoT and smart grid solutions are reshaping sourcing trends. These advancements necessitate fuses that can handle higher voltages and currents, thereby pushing manufacturers to innovate continuously. Additionally, the adoption of automation in manufacturing processes is enhancing production efficiency and product consistency, which are critical for meeting the quality standards expected by international B2B buyers.
For international buyers, particularly those from Europe, the Middle East, and emerging markets, understanding local regulations and compliance standards is essential. This includes knowledge of safety certifications and environmental regulations that govern the use of electrical components. The market is also seeing a shift towards sourcing from manufacturers that can provide traceability and transparency in their supply chains, particularly in regions with stringent regulatory environments.
How Is Sustainability Influencing Sourcing Decisions in the Fuse Manufacturing Sector?
Sustainability has become a crucial factor for B2B buyers in the fuse manufacturing sector. The environmental impact of manufacturing processes and the materials used in fuses are under increasing scrutiny. Companies are now prioritizing suppliers that implement sustainable practices and utilize eco-friendly materials, such as recyclable components and low-impact manufacturing processes.
The importance of ethical supply chains cannot be overstated. Buyers are more inclined to partner with manufacturers who are committed to reducing their carbon footprint and who adhere to internationally recognized standards for ethical sourcing. Certifications like ISO 14001 for environmental management and other ‘green’ certifications are becoming prerequisites for many buyers when selecting suppliers.
Moreover, the push for sustainability is not just about compliance; it is also a market differentiator. Companies that can demonstrate their commitment to sustainable practices often gain a competitive edge, appealing to increasingly environmentally conscious consumers and businesses. This trend is particularly evident in Europe, where sustainability regulations are stringent, but is gaining traction in Africa and South America as well, driven by a growing awareness of environmental issues.
What Is the Historical Context of the Fuse Manufacturing Sector for B2B Buyers?
The fuse manufacturing sector has evolved significantly since its inception in the early 19th century. Initially designed as simple safety devices to prevent electrical overloads, fuses have transformed into sophisticated components that are integral to modern electrical systems. This evolution has been driven by advancements in materials science and technology, allowing for more reliable and efficient products.
In the mid-20th century, the introduction of circuit breakers began to change the landscape of electrical safety, leading to a decline in traditional fuse use. However, fuses have made a strong comeback due to their reliability, simplicity, and cost-effectiveness in various applications, from residential to industrial.
For B2B buyers today, understanding this historical context is vital. It highlights the importance of choosing suppliers that not only provide high-quality products but also possess a deep understanding of the evolution of electrical safety standards and technologies. This knowledge can lead to better sourcing decisions and ultimately contribute to the long-term success of their operations.
Frequently Asked Questions (FAQs) for B2B Buyers of fuse manufacturer
-
1. How do I choose the right fuse manufacturer for my business needs?
When selecting a fuse manufacturer, consider their product range, certifications, and industry reputation. Look for manufacturers that comply with international standards such as IEC or UL certifications, which indicate quality and reliability. Assess their experience in your specific industry and request samples to evaluate product performance. Additionally, seek references from other clients to gauge their satisfaction and reliability. Finally, ensure that the manufacturer can meet your specific requirements, including customization options and delivery timelines. -
2. What factors should I consider when evaluating fuse quality?
Evaluate fuse quality by examining material composition, manufacturing processes, and compliance with international safety standards. High-quality fuses typically use durable materials that can withstand environmental stresses. Investigate the manufacturer’s testing protocols, including routine quality assurance checks and third-party certifications. Additionally, consider the manufacturer’s ability to provide documentation, such as test reports and compliance certificates, to ensure transparency and reliability. -
3. What customization options are typically available when sourcing fuses?
Many fuse manufacturers offer customization options to meet specific needs. Common customizations include different voltage ratings, sizes, and mounting configurations. Some manufacturers can also provide personalized labeling, branding, and packaging to align with your company’s requirements. Discuss your specific needs with the manufacturer early in the sourcing process to ensure they can accommodate your requests and to understand any additional costs or lead times associated with customization. -
4. What is the typical minimum order quantity (MOQ) for fuses from manufacturers?
Minimum order quantities (MOQ) can vary widely among fuse manufacturers, often ranging from a few hundred to several thousand units, depending on the type of fuse and the manufacturer’s policies. Larger manufacturers may have more flexibility in MOQs, while smaller or specialized manufacturers may require higher quantities. It’s essential to communicate your needs during the initial discussions to find a manufacturer who can accommodate your order size without incurring prohibitive costs. -
5. How can I ensure timely delivery and logistics when sourcing fuses internationally?
To ensure timely delivery, establish clear communication with your chosen manufacturer regarding lead times, shipping methods, and potential delays. Utilize reputable logistics providers experienced in international shipping to minimize risks. Consider setting up a Just-In-Time (JIT) inventory system to align your orders with production schedules. Additionally, inquire about the manufacturer’s ability to provide real-time tracking information to monitor your shipment and stay informed about its status. -
6. What payment terms should I expect when dealing with fuse manufacturers?
Payment terms can vary significantly based on the manufacturer’s policies and your business relationship. Common terms include upfront payments, deposits, and net terms (e.g., 30, 60, or 90 days). It’s crucial to negotiate terms that balance your cash flow needs with the manufacturer’s requirements. Consider using secure payment methods such as letters of credit or escrow services for larger orders to protect both parties. Always ensure that you have a written agreement outlining the payment terms before proceeding. -
7. How do I verify the credibility of a fuse manufacturer before placing an order?
To verify a fuse manufacturer’s credibility, conduct thorough research, including checking their business licenses, certifications, and online reviews. Look for customer testimonials and case studies that demonstrate their reliability and product quality. Additionally, visit their facility if possible or request virtual tours to assess their production capabilities. Engaging with industry forums or trade associations can also provide insights into the manufacturer’s reputation and track record. -
8. What are the common challenges faced when sourcing fuses internationally, and how can I mitigate them?
Common challenges in international sourcing include language barriers, cultural differences, and varying regulations. To mitigate these issues, work with manufacturers who have experience exporting to your region and can provide multilingual support. Familiarize yourself with local regulations regarding electrical components to ensure compliance. Establish clear communication channels and consider hiring a local agent or representative to facilitate negotiations and logistics. Building strong relationships with manufacturers can also help navigate challenges effectively.
Important Disclaimer & Terms of Use
⚠️ Important Disclaimer
The information provided in this guide, including content regarding manufacturers, technical specifications, and market analysis, is for informational and educational purposes only. It does not constitute professional procurement advice, financial advice, or legal advice.
While we have made every effort to ensure the accuracy and timeliness of the information, we are not responsible for any errors, omissions, or outdated information. Market conditions, company details, and technical standards are subject to change.
B2B buyers must conduct their own independent and thorough due diligence before making any purchasing decisions. This includes contacting suppliers directly, verifying certifications, requesting samples, and seeking professional consultation. The risk of relying on any information in this guide is borne solely by the reader.
Strategic Sourcing Conclusion and Outlook for fuse manufacturer
Why is Strategic Sourcing Essential for Fuse Manufacturers?
In the competitive landscape of fuse manufacturing, strategic sourcing emerges as a critical component for international B2B buyers. It allows companies to optimize procurement processes, reduce costs, and ensure the highest quality of products. By establishing strong relationships with reliable suppliers, businesses in Africa, South America, the Middle East, and Europe can not only enhance their supply chain resilience but also leverage diverse market opportunities.
What Are the Key Takeaways for B2B Buyers?
- Quality Assurance: Prioritize suppliers with proven track records in manufacturing high-quality fuses that meet international standards.
- Cost Management: Analyze total cost of ownership rather than just unit price, ensuring long-term value.
- Market Intelligence: Utilize data-driven insights to anticipate market trends and adjust sourcing strategies accordingly.
How Can Buyers Prepare for Future Challenges?
As the global market evolves, B2B buyers should remain agile and proactive. Embracing digital tools and analytics can streamline sourcing decisions and enhance collaboration with suppliers.
What Should International Buyers Do Next?
Engage in strategic sourcing today to secure a competitive edge in the fuse manufacturing sector. Explore partnerships with innovative suppliers who can deliver not just products, but also insights into future technologies and market demands. By taking decisive action now, businesses can position themselves for success in a dynamic marketplace.