Improve Efficiency: Your Guide to Storage Rack Supplier (2025)
Introduction: Navigating the Global Market for storage rack supplier
In the ever-evolving landscape of global commerce, sourcing the right storage rack supplier is a critical challenge for international B2B buyers. Whether you are a business in Africa seeking to optimize warehouse space or a South American enterprise aiming to enhance operational efficiency, the decision to invest in quality storage solutions can significantly impact your logistics and inventory management. This guide provides a comprehensive overview of storage rack options, their various applications, and essential supplier vetting strategies, ensuring you make informed purchasing decisions.
Understanding the types of storage racks available—from pallet racks to cantilever racks—will allow you to align your selection with your specific business needs. Additionally, we delve into the importance of assessing supplier reliability, including certifications, customer reviews, and after-sales support, which are pivotal for establishing long-term partnerships. Cost considerations are also explored, providing insights on pricing structures and potential return on investment.
This guide is tailored specifically for B2B buyers from diverse regions, including Europe, the Middle East, and beyond. By empowering you with actionable insights and practical tools, we aim to facilitate your journey in navigating the global market for storage rack suppliers. Equip yourself with the knowledge needed to enhance your operations and drive your business towards greater efficiency and success.
Understanding storage rack supplier Types and Variations
Type Name | Key Distinguishing Features | Primary B2B Applications | Brief Pros & Cons for Buyers |
---|---|---|---|
Selective Racking | Adjustable shelves, direct access to all pallets | Warehousing, retail, manufacturing | Pros: Versatile, easy to configure; Cons: Limited space utilization for high-density storage. |
Drive-In Racking | High-density storage, allows forklift access | Cold storage, distribution centers | Pros: Maximizes storage space; Cons: Limited access to individual pallets. |
Cantilever Racking | Open design for long items, adjustable arms | Lumber yards, furniture stores | Pros: Ideal for long, bulky items; Cons: Requires more floor space. |
Push Back Racking | Multi-level storage, gravity-driven system | High-volume distribution, food services | Pros: Efficient space utilization; Cons: Higher initial investment. |
Mobile Racking | Racks mounted on wheels, compact design | Libraries, archives, manufacturing | Pros: Maximizes floor space; Cons: More complex to operate and maintain. |
What are the characteristics and suitability of Selective Racking?
Selective racking is one of the most common types of storage systems, characterized by adjustable shelves that allow for easy access to all pallets. This system is highly versatile and can accommodate various pallet sizes, making it suitable for a wide range of industries, including warehousing, retail, and manufacturing. When considering selective racking, buyers should evaluate the available warehouse space, the types of goods being stored, and the desired accessibility levels. It is a practical choice for businesses prioritizing flexibility and direct access.
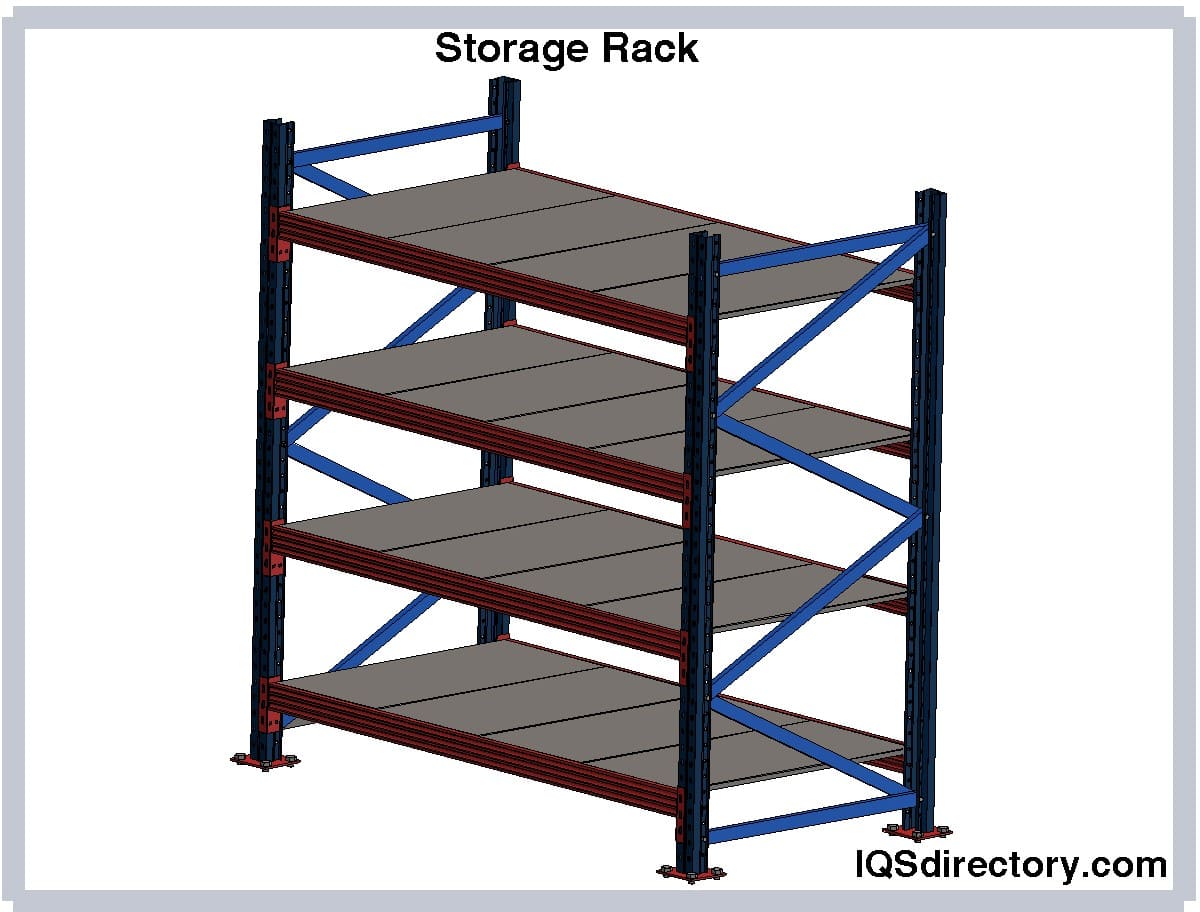
A stock image related to storage rack supplier.
Why choose Drive-In Racking for high-density storage?
Drive-in racking is designed for high-density storage, allowing forklifts to drive directly into the rack structure. This system is particularly effective in cold storage and distribution centers where maximizing storage space is critical. However, it limits access to individual pallets, as goods are stored in a last-in, first-out manner. Buyers should consider their inventory turnover rates and the need for quick access to specific items when opting for drive-in racking. This solution is ideal for businesses with high-volume, low-variability inventory.
How does Cantilever Racking serve specific industries?
Cantilever racking features an open design with adjustable arms, making it perfect for storing long or bulky items such as lumber, pipes, or furniture. This type of racking is commonly used in lumber yards and furniture stores due to its ability to hold items of varying lengths securely. When purchasing cantilever racking, buyers should assess the weight capacity needed and the layout of their storage area. While it requires more floor space than other systems, its ability to accommodate long items makes it a valuable solution for specific industries.
What are the benefits of Push Back Racking systems?
Push back racking utilizes a gravity-driven system that allows pallets to be stored in a multi-level configuration. This system is particularly beneficial for high-volume distribution centers and food service operations. Push back racking maximizes space utilization by allowing multiple pallets to be stored in a single lane. However, it requires a higher initial investment compared to selective racking. Buyers should evaluate their storage needs and consider the trade-off between upfront costs and long-term efficiency when choosing this type of racking.
Why consider Mobile Racking for dynamic storage needs?
Mobile racking systems consist of racks mounted on wheels, allowing for the compact storage of goods while maximizing floor space. This system is commonly used in libraries, archives, and manufacturing facilities where space is at a premium. Although mobile racking can significantly enhance storage capacity, it also requires more complex operation and maintenance. Buyers should consider their operational workflow and the potential need for staff training when investing in mobile racking systems. This solution is ideal for businesses looking to optimize limited storage space effectively.
Related Video: Elite Storage Solutions – Rack Supported Building & ASRS Installation
Key Industrial Applications of storage rack supplier
Industry/Sector | Specific Application of storage rack supplier | Value/Benefit for the Business | Key Sourcing Considerations for this Application |
---|---|---|---|
Retail and E-commerce | Display and storage racks for products | Maximizes space utilization and enhances product visibility | Durability, load capacity, and design flexibility |
Manufacturing | Heavy-duty storage racks for raw materials | Improves workflow efficiency and inventory management | Compliance with safety standards and customization options |
Warehousing and Logistics | Pallet racking systems for bulk storage | Increases storage density and reduces retrieval times | Compatibility with existing equipment and scalability |
Food and Beverage | Refrigerated storage racks for perishables | Ensures product safety and compliance with health regulations | Temperature control features and hygiene standards |
Automotive | Parts storage racks for automotive components | Streamlines inventory management and reduces downtime | Material quality and resistance to wear and tear |
How Are Storage Racks Utilized in Retail and E-commerce?
In the retail and e-commerce sector, storage racks play a crucial role in organizing and displaying products. Retailers utilize various types of display racks to enhance product visibility, which can lead to increased sales. For international buyers, especially from regions like Africa and South America, sourcing racks that are durable and adaptable to different product types is essential. Consideration should also be given to local market trends and consumer preferences to ensure effective merchandising.
What Are the Benefits of Storage Racks in Manufacturing?
Heavy-duty storage racks are vital in the manufacturing industry for holding raw materials and components. They help streamline operations by improving workflow efficiency and inventory management. Buyers from the Middle East and Europe must ensure that the racks comply with local safety standards and can be customized to fit specific production needs. This is particularly important in industries where space is limited and safety is a priority.
How Do Storage Racking Systems Enhance Warehousing and Logistics?
In warehousing and logistics, pallet racking systems are essential for maximizing storage density while allowing for easy access to goods. These systems help businesses reduce retrieval times, which is crucial for maintaining efficient supply chain operations. International buyers should consider the compatibility of racking systems with existing warehouse equipment and their scalability to meet future growth needs, especially in fast-developing markets.
Why Are Refrigerated Storage Racks Important in Food and Beverage?
The food and beverage industry relies heavily on specialized storage solutions, such as refrigerated racks, to ensure the safety of perishable items. These racks help maintain the necessary temperature and comply with health regulations. Buyers, particularly in Europe and the Middle East, must prioritize sourcing racks with effective temperature control features and materials that meet hygiene standards, as food safety is non-negotiable in this sector.
How Do Automotive Parts Storage Racks Improve Efficiency?
Automotive manufacturers and suppliers use parts storage racks to manage inventory effectively and reduce downtime in production. These racks facilitate quick access to components, which is essential for maintaining operational efficiency. When sourcing for this application, international buyers should focus on the quality of materials used in the racks, ensuring they are resistant to wear and tear, which is critical in high-use environments.
3 Common User Pain Points for ‘storage rack supplier’ & Their Solutions
Scenario 1: Inefficient Space Utilization in Warehouses
The Problem: Many B2B buyers, particularly in industries like retail and manufacturing, face significant challenges regarding space utilization in their warehouses. With rising costs and the need for efficiency, poorly organized storage solutions can lead to wasted space and increased operational costs. Buyers often find that existing shelving and storage racks do not fit their inventory needs, resulting in cluttered aisles and delays in order fulfillment.
The Solution: To overcome space utilization challenges, buyers should work closely with storage rack suppliers who specialize in custom solutions. By conducting a comprehensive needs assessment, including the types of products stored and the flow of operations, suppliers can recommend tailored storage systems. Consider investing in modular racking systems that can be adjusted as inventory levels change. Additionally, implementing vertical storage solutions can maximize vertical space, allowing for more efficient use of the warehouse floor. Regular reviews of inventory and storage practices will ensure that the racking system continues to meet operational needs.
Scenario 2: Safety Compliance Issues with Storage Racks
The Problem: Safety compliance is a critical concern for B2B buyers, especially in industries such as logistics and manufacturing. Many buyers struggle with outdated or improperly installed storage racks, which can pose serious safety risks, including structural failures and accidents. Non-compliance with safety regulations can lead to costly fines and increased liability, making it essential for companies to ensure their storage solutions meet industry standards.
The Solution: Buyers should prioritize sourcing storage racks from suppliers who provide clear compliance documentation and safety certifications. It’s essential to conduct regular inspections of existing racks to identify any signs of wear, damage, or misalignment. Collaborate with suppliers to schedule maintenance and training on proper usage and safety protocols for warehouse staff. Investing in safety features like rack protection systems and ensuring that racking is installed according to the manufacturer’s specifications will significantly reduce safety risks. Consider engaging in periodic safety audits to ensure ongoing compliance with local regulations.
Scenario 3: Limited Supplier Support and Service
The Problem: A frequent pain point for B2B buyers is inadequate support from storage rack suppliers after the purchase. Many buyers report difficulties in getting timely responses to their inquiries about installation, maintenance, or modifications, leading to frustration and potential operational downtime. This lack of support can hinder the effectiveness of the storage solution and negatively impact overall business efficiency.
The Solution: To mitigate this issue, buyers should choose storage rack suppliers who offer comprehensive post-purchase support, including installation services, training, and ongoing maintenance packages. Before finalizing a supplier, inquire about their customer service policies and response times. Establishing a clear communication channel with the supplier can facilitate quick resolutions to any problems that arise. Additionally, buyers should consider suppliers that provide resources such as online tutorials, maintenance guides, and access to customer support teams. Building a strong partnership with the supplier can enhance the overall experience and ensure that the storage systems remain efficient and effective over time.
Strategic Material Selection Guide for storage rack supplier
When selecting materials for storage racks, international B2B buyers must consider various factors that influence both performance and compliance. Below, we analyze four common materials used in storage rack construction, focusing on their properties, advantages, disadvantages, and specific considerations for buyers from Africa, South America, the Middle East, and Europe.
What Are the Key Properties of Steel for Storage Racks?
Steel is the most widely used material in storage rack construction due to its strength and durability. Key properties include:
- Temperature/Pressure Rating: Steel can withstand high loads and is suitable for heavy-duty applications, making it ideal for warehouses and industrial settings.
- Corrosion Resistance: While raw steel is prone to rust, galvanized or powder-coated steel options offer enhanced corrosion resistance.
Pros: Steel racks are known for their long lifespan and ability to bear heavy loads, making them suitable for various applications, including pallet racking and shelving systems.
Cons: The initial cost of steel racks can be high, and they may require additional treatments to prevent rust, particularly in humid environments.
Impact on Application: Steel racks are compatible with a wide range of media, including heavy machinery and bulk materials, making them versatile for different industries.
Considerations for International Buyers: Compliance with standards such as ASTM (American Society for Testing and Materials) or EN (European Norms) is crucial. Buyers should also consider local regulations regarding load capacities and safety standards.
How Does Aluminum Compare as a Material for Storage Racks?
Aluminum is increasingly popular for storage racks, especially in environments where weight and corrosion resistance are critical.
- Temperature/Pressure Rating: Aluminum racks are lightweight and can handle moderate loads, making them suitable for specific applications like retail or light industrial use.
- Corrosion Resistance: Aluminum naturally forms a protective oxide layer, providing excellent resistance to corrosion.
Pros: The lightweight nature of aluminum makes it easier to handle and install, reducing labor costs. It is also resistant to rust, making it ideal for humid or coastal environments.
Cons: Aluminum racks typically have lower load-bearing capacities than steel, which may limit their use in heavy-duty applications.
Impact on Application: Aluminum is ideal for environments that require frequent reconfiguration or where mobility is essential, such as in retail settings.
Considerations for International Buyers: Buyers should be aware of the differences in aluminum grades and ensure compliance with local standards, such as JIS (Japanese Industrial Standards) or EN.
What Are the Benefits and Limitations of Wood in Storage Rack Construction?
Wood is a traditional material used in storage racks, particularly in retail and home settings.
- Temperature/Pressure Rating: Wood racks can support moderate weights but are not suitable for heavy industrial applications.
- Corrosion Resistance: While wood is not susceptible to rust, it can be affected by moisture, leading to warping or decay.
Pros: Wood offers aesthetic appeal and is often more cost-effective than metal options. It can be easily customized to fit specific design needs.
Cons: Wood has a shorter lifespan compared to metal and is less durable under heavy loads or in humid environments.
Impact on Application: Wood is suitable for light-duty applications, such as displaying products in retail environments.
Considerations for International Buyers: Compliance with local regulations regarding sourcing and sustainability is essential, particularly in regions like Europe where environmental standards are stringent.
What Role Does Plastic Play in Storage Rack Solutions?
Plastic is an emerging material in storage rack design, particularly for specialized applications.
- Temperature/Pressure Rating: Plastic racks are generally suitable for light-duty applications and can withstand a range of temperatures.
- Corrosion Resistance: Plastic is inherently resistant to corrosion and moisture, making it ideal for wet environments.
Pros: Plastic racks are lightweight, easy to clean, and resistant to chemicals, making them ideal for laboratories and food storage.
Cons: They typically have lower load capacities and may not be suitable for heavy-duty applications.
Impact on Application: Plastic racks are ideal for environments requiring hygiene and cleanliness, such as food processing or pharmaceuticals.
Considerations for International Buyers: Buyers should ensure compliance with food safety standards and regulations, particularly in the food and pharmaceutical industries.
Summary Table of Material Selection for Storage Racks
Material | Typical Use Case for Storage Rack Supplier | Key Advantage | Key Disadvantage/Limitation | Relative Cost (Low/Med/High) |
---|---|---|---|---|
Steel | Heavy-duty industrial storage | High load-bearing capacity | Prone to rust without treatment | High |
Aluminum | Light-duty retail or industrial storage | Lightweight and corrosion-resistant | Lower load capacity than steel | Medium |
Wood | Retail displays and home storage | Aesthetic appeal and cost-effective | Shorter lifespan and less durable | Low |
Plastic | Laboratories and food storage | Lightweight and easy to clean | Lower load capacity | Medium |
In conclusion, selecting the right material for storage racks involves balancing performance, cost, and compliance with local standards. Understanding the properties and limitations of each material can help international B2B buyers make informed decisions tailored to their specific needs.
In-depth Look: Manufacturing Processes and Quality Assurance for storage rack supplier
What Are the Key Stages in the Manufacturing Process for Storage Racks?
The manufacturing of storage racks involves several critical stages, each designed to ensure that the final product meets the required specifications and quality standards. Here’s a breakdown of the main stages:
1. Material Preparation
In this initial stage, raw materials such as steel sheets, beams, and other components are sourced based on design specifications. The choice of materials is crucial, as it impacts the strength, durability, and load-bearing capacity of the racks.
- Material Selection: Suppliers often utilize high-strength steel to ensure longevity and resistance to wear.
- Cutting and Shearing: Large sheets of steel are cut into manageable pieces using precision cutting tools, which ensures accuracy in dimensions.
2. Forming and Fabrication
Once the materials are prepared, they undergo various forming processes to create the desired shapes and structures.
- Bending and Punching: Techniques such as bending and punching are used to shape the steel components. Automated CNC machines are commonly employed to enhance precision and reduce labor costs.
- Welding: Components are welded together to form the frame of the storage rack. The quality of welding is vital, as it directly affects the structural integrity of the racks.
3. Assembly
After forming, the individual components are assembled into complete units.
- Assembly Techniques: This stage may involve manual assembly or the use of automated assembly lines. Each component, from beams to connectors, is checked for compatibility.
- Modular Designs: Many suppliers offer modular designs that allow for easy customization and scalability, which is particularly appealing to international buyers looking for versatile solutions.
4. Finishing
The final stage in the manufacturing process involves applying protective coatings and finishes.
- Painting and Coating: Racks are typically painted or coated with anti-corrosive materials to enhance durability, especially in environments prone to rust (e.g., humid climates).
- Quality Checks: Before moving on to quality assurance, finished racks undergo visual inspections to ensure that the surface finish is even and free from defects.
How Do International Standards Shape Quality Assurance in Storage Rack Manufacturing?
Quality assurance is a critical aspect of the manufacturing process, ensuring that products meet international safety and performance standards. For international B2B buyers, understanding these standards can facilitate better purchasing decisions.
1. Relevant International Standards
- ISO 9001: This standard outlines the criteria for a quality management system, focusing on continuous improvement and customer satisfaction. Suppliers compliant with ISO 9001 demonstrate their commitment to quality and consistency.
- CE Marking: For products sold in the European market, CE marking indicates compliance with health, safety, and environmental protection standards. It is essential for ensuring that storage racks meet EU regulations.
2. Industry-Specific Standards
- API Standards: In industries such as oil and gas, compliance with API (American Petroleum Institute) standards may be necessary. These standards ensure that products can withstand extreme conditions and are safe for industrial use.
What Are the Key Quality Control Checkpoints in Storage Rack Manufacturing?
Quality control (QC) is integrated throughout the manufacturing process, with several checkpoints established to ensure that products meet required standards.
1. Incoming Quality Control (IQC)
At this initial checkpoint, raw materials are inspected upon delivery.
- Material Verification: Suppliers check for certifications and conduct tests to verify material properties, such as tensile strength and corrosion resistance.
- Supplier Audits: Conducting audits of suppliers can provide insights into their material sourcing practices, ensuring they align with quality standards.
2. In-Process Quality Control (IPQC)
During manufacturing, ongoing inspections are crucial to identify any defects early in the process.
- Real-Time Monitoring: Utilizing automated systems can help in monitoring key parameters such as temperature during welding, ensuring that processes remain within acceptable limits.
- Dimensional Checks: Regular checks on the dimensions of components ensure that they fit together correctly during assembly.
3. Final Quality Control (FQC)
Before shipping, a thorough inspection is conducted on the completed racks.
- Load Testing: Racks may undergo load testing to confirm they meet specified weight capacities. This is particularly important for clients in sectors requiring high load-bearing solutions.
- Documentation: Suppliers should provide detailed QC reports and test certificates to verify compliance with international standards.
How Can B2B Buyers Verify Supplier Quality Control Practices?
To ensure that they are partnering with reliable storage rack suppliers, international B2B buyers should consider the following strategies:
1. Conduct Supplier Audits
Regular audits of potential suppliers can provide deeper insights into their manufacturing practices and quality assurance measures.
- On-Site Visits: If feasible, visiting the manufacturing facility allows buyers to see the processes in action and assess the working conditions and equipment used.
- Audit Reports: Requesting recent audit reports can help buyers evaluate a supplier’s compliance with industry standards.
2. Request Documentation and Certifications
Buyers should ask for documentation that confirms a supplier’s adherence to quality standards.
- Quality Management System Documentation: This includes ISO certifications and any other relevant compliance documents that reflect a commitment to quality.
- Test Reports: Suppliers should provide test reports for materials and finished products, ensuring transparency in their quality control practices.
3. Engage Third-Party Inspectors
Hiring independent third-party inspectors can enhance trust in the supplier’s quality assurance processes.
- Objective Assessments: Third-party inspections provide unbiased evaluations of the manufacturing processes and final products, ensuring adherence to agreed specifications.
- Risk Mitigation: Engaging third-party services can help mitigate risks associated with purchasing from overseas suppliers, especially for B2B buyers in regions with varying regulatory frameworks.
Conclusion
Understanding the manufacturing processes and quality assurance practices of storage rack suppliers is vital for international B2B buyers. By focusing on material preparation, forming, assembly, and finishing, alongside rigorous quality control measures, buyers can make informed decisions that align with their operational needs. Utilizing international standards, conducting supplier audits, and engaging third-party inspectors will further ensure that purchased products meet the highest quality and safety standards.
Practical Sourcing Guide: A Step-by-Step Checklist for ‘storage rack supplier’
To ensure a successful procurement process when sourcing storage racks, it is essential to follow a well-structured checklist. This guide provides actionable steps for international B2B buyers from Africa, South America, the Middle East, and Europe, helping you navigate the complexities of supplier selection.
Step 1: Define Your Storage Needs and Specifications
Clearly identifying your storage requirements is the first step toward successful procurement. Consider the types of goods you will store, their dimensions, and the expected weight load. This will influence the design and capacity of the storage racks.
– Types of Racks: Determine whether you need pallet racks, shelving units, or specialized storage systems.
– Space Constraints: Assess the available space to ensure that the selected racks fit without compromising safety or accessibility.
Step 2: Research Potential Suppliers
Conduct thorough research to compile a list of potential suppliers. Look for companies with a strong reputation in the industry, especially those that have experience serving businesses in your region.
– Online Resources: Utilize industry directories and online platforms like Alibaba or ThomasNet to find suppliers.
– Local Trade Shows: Attend relevant trade shows to meet suppliers in person and evaluate their products firsthand.
Step 3: Evaluate Supplier Certifications and Compliance
Before making a commitment, it’s vital to verify that suppliers meet necessary industry standards and regulations. Certifications ensure that the racks are safe and reliable for use.
– ISO Certification: Look for suppliers with ISO 9001 certification, which indicates quality management practices.
– Safety Standards: Ensure compliance with local and international safety standards, such as EN 15512 or AS/NZS 4084, depending on your market.
Step 4: Request Quotes and Compare Pricing
Once you have narrowed down your list of suppliers, request detailed quotes. This will allow you to compare pricing, terms, and conditions effectively.
– Breakdown of Costs: Ensure the quotes include costs for materials, shipping, and installation if applicable.
– Long-term Value: Don’t just choose the lowest price; consider the durability and warranty offered, which can affect long-term costs.
Step 5: Assess Supplier Reliability and Reputation
A supplier’s reliability is crucial for maintaining your operations. Investigate their history and reputation in the market.
– Customer Reviews: Look for testimonials and case studies from other businesses that have used their products.
– Financial Stability: Check the supplier’s financial health to ensure they can meet your ongoing needs without risk of bankruptcy.
Step 6: Negotiate Terms and Conditions
Once you’ve selected a preferred supplier, it’s time to negotiate the terms of the contract. Aim for a balance between cost-effectiveness and quality assurance.
– Payment Terms: Discuss payment schedules that align with your cash flow needs.
– Delivery Timeline: Ensure that the delivery schedule meets your project timelines to avoid operational delays.
Step 7: Plan for Installation and After-Sales Support
Finally, consider the installation process and the level of after-sales support provided by the supplier. Proper installation is essential for safety and efficiency.
– Installation Services: Confirm if the supplier offers installation services or if you need to hire a third party.
– Support and Maintenance: Inquire about ongoing support, warranties, and maintenance services to ensure your storage racks remain in optimal condition.
By following this practical sourcing guide, B2B buyers can confidently procure storage racks that meet their operational needs while ensuring quality, reliability, and value.
Comprehensive Cost and Pricing Analysis for storage rack supplier Sourcing
What Are the Key Cost Components in Storage Rack Supplier Sourcing?
When sourcing storage racks, understanding the cost structure is critical. The main components include:
-
Materials: The type of materials used, such as steel, aluminum, or composite materials, significantly impacts cost. High-quality materials may have a higher upfront cost but can offer better durability and longevity.
-
Labor: Labor costs can vary based on the region and the complexity of the manufacturing process. Skilled labor might demand higher wages, but investing in expertise can enhance the quality of the product.
-
Manufacturing Overhead: This includes costs associated with utilities, equipment depreciation, and indirect labor. Efficient manufacturing processes can help in reducing these overhead costs.
-
Tooling: Custom storage solutions may require specialized tooling, which can add to the initial cost. Buyers should consider whether the tooling costs are amortized over large production runs.
-
Quality Control (QC): Implementing stringent QC measures ensures that the storage racks meet safety and quality standards. While this adds to the cost, it can prevent expensive recalls or replacements later.
-
Logistics: Transportation costs can fluctuate based on distance, shipping method, and regional tariffs. Efficient logistics planning can help in minimizing these expenses.
-
Margin: Suppliers will typically add a margin to cover their costs and ensure profitability. Understanding the supplier’s margin expectations can aid in negotiation.
How Do Price Influencers Affect Storage Rack Costs?
Several factors influence the pricing of storage racks:
-
Volume and Minimum Order Quantity (MOQ): Bulk orders often attract discounts. Understanding the MOQ can help buyers negotiate better prices.
-
Specifications and Customization: Customized racks designed for specific needs will generally cost more. Buyers should weigh the benefits of customization against the increased costs.
-
Materials and Quality Certifications: Higher quality materials and certifications (like ISO or CE) may lead to higher costs. However, they can also enhance product reliability and safety.
-
Supplier Factors: The reputation and experience of the supplier can influence pricing. Established suppliers might charge more due to their proven track record, while newer suppliers may offer lower prices to gain market share.
-
Incoterms: These terms define the responsibilities of buyers and sellers in shipping. Understanding Incoterms is crucial as they can affect total costs, including insurance and duties.
What Are the Best Negotiation Tips for International B2B Buyers?
For international buyers, particularly from Africa, South America, the Middle East, and Europe, effective negotiation can lead to significant savings:
-
Understand Total Cost of Ownership (TCO): Evaluate not just the purchase price, but also installation, maintenance, and potential future upgrades. TCO helps in making informed decisions.
-
Leverage Bulk Purchasing: If possible, consolidate orders across different locations or departments to meet MOQs and secure better pricing.
-
Be Clear About Specifications: Clearly communicate your needs to avoid misunderstandings that can lead to costly revisions or delays.
-
Build Relationships with Suppliers: Establishing a rapport can lead to more favorable terms and potential discounts.
-
Stay Informed About Market Trends: Being aware of market conditions can give you leverage during negotiations. For instance, if steel prices are dropping, it may be an excellent time to renegotiate contracts.
What Should International Buyers Know About Pricing Nuances?
Pricing structures can vary significantly across regions due to economic conditions, labor costs, and materials availability. For example, suppliers in Europe might have different cost structures compared to those in Africa or South America. Additionally, currency fluctuations can impact pricing.
Buyers should approach international procurement with a clear understanding of these nuances to avoid unforeseen costs. Also, be aware of local regulations and compliance standards, as they can influence both pricing and the overall purchasing process.
Disclaimer on Indicative Prices
Prices for storage racks can fluctuate based on market conditions, supplier changes, and currency exchange rates. Always request quotes from multiple suppliers and consider all associated costs to ensure an accurate budget.
Alternatives Analysis: Comparing storage rack supplier With Other Solutions
In the competitive landscape of warehousing and inventory management, selecting the right storage solution is crucial for operational efficiency. While traditional storage rack suppliers have been the go-to choice for many businesses, exploring alternatives can unveil more cost-effective and innovative options. This analysis compares storage rack suppliers with other viable solutions, aiding international B2B buyers in making informed decisions.
Comparison Aspect | Storage Rack Supplier | Mobile Shelving System | Automated Storage and Retrieval Systems (AS/RS) |
---|---|---|---|
Performance | High load capacity; customizable designs | Moderate load capacity; space-efficient | Very high; rapid retrieval and storage |
Cost | Moderate to high initial investment | Lower initial cost; variable long-term costs | High initial investment; lower long-term operational costs |
Ease of Implementation | Requires professional installation; time-consuming | Easier to install; can be DIY | Complex installation; requires specialized knowledge |
Maintenance | Moderate; regular inspections needed | Low; minimal upkeep | Low; automated systems require less manual intervention |
Best Use Case | Heavy-duty storage needs; long-term use | Space-constrained environments; flexible storage | High-volume operations; fast-paced environments |
What Are the Advantages and Disadvantages of Mobile Shelving Systems?
Mobile shelving systems are designed to maximize storage in limited spaces by utilizing compact shelving units that move along tracks. This solution is particularly beneficial in environments where floor space is at a premium, allowing businesses to store a larger quantity of goods without the need for extensive structural changes.
Pros:
– Cost-effective initial investment compared to traditional racks.
– Flexible configuration and scalability to accommodate changing inventory needs.
Cons:
– Moderate load capacity, which may not be suitable for heavy items.
– Potentially higher long-term costs due to the need for periodic maintenance and repairs.
How Do Automated Storage and Retrieval Systems (AS/RS) Enhance Efficiency?
Automated Storage and Retrieval Systems (AS/RS) are advanced technologies that integrate robotics and software to optimize inventory management. These systems can significantly reduce labor costs and improve order accuracy, making them ideal for businesses with high throughput and frequent inventory turnover.
Pros:
– Very high performance in terms of speed and accuracy, particularly in high-volume settings.
– Lower operational costs over time due to reduced labor needs and minimized human error.
Cons:
– High initial setup costs can be a barrier for smaller enterprises.
– Complex installation and maintenance require specialized knowledge and training.
How Can B2B Buyers Determine the Right Storage Solution?
When considering storage solutions, B2B buyers should evaluate their unique operational needs, including volume, load requirements, available space, and budget constraints. While storage rack suppliers offer robust and customizable options, alternatives like mobile shelving and AS/RS can provide enhanced efficiency and flexibility for specific contexts.
Ultimately, the decision should align with the business’s long-term strategy, considering factors such as scalability, future growth, and the nature of the inventory. By carefully assessing the pros and cons of each option, international buyers can ensure they choose a solution that not only meets their current needs but also supports their future objectives.
Essential Technical Properties and Trade Terminology for storage rack supplier
What Are the Key Technical Properties of Storage Racks for B2B Buyers?
When considering storage racks, understanding the technical properties can significantly influence purchasing decisions. Here are some critical specifications to keep in mind:
1. Material Grade: What Should You Look For?
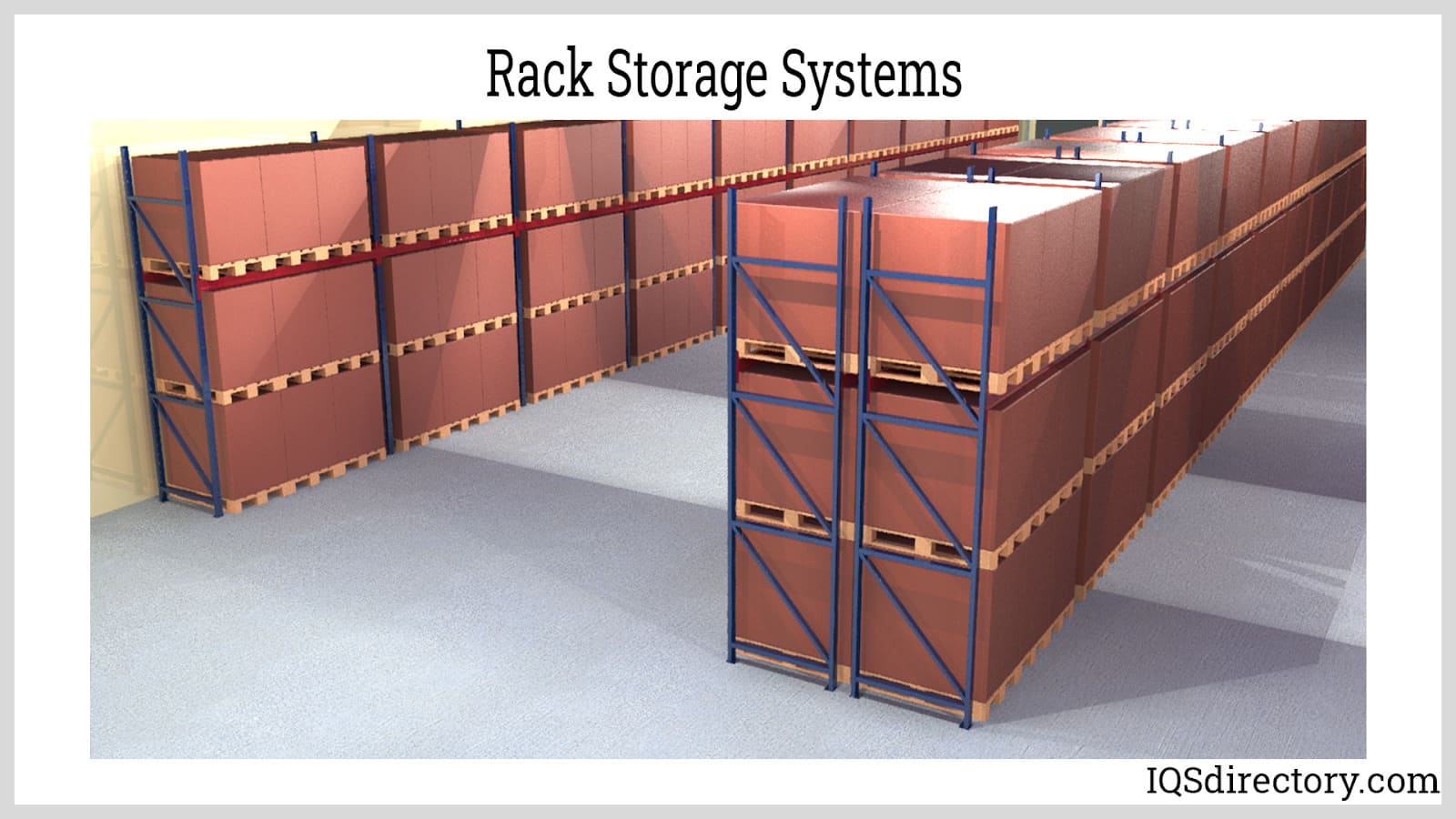
A stock image related to storage rack supplier.
The material grade of storage racks typically refers to the type of steel used, such as cold-rolled or hot-rolled steel. Higher-grade materials provide better strength, durability, and resistance to corrosion. This is essential for B2B buyers, as investing in high-quality materials can reduce maintenance costs and extend the lifespan of the racks.
2. Load Capacity: How Much Weight Can They Handle?
Load capacity indicates the maximum weight a storage rack can support. This property is crucial for businesses that plan to store heavy items. Buyers should look for racks that offer a load capacity that exceeds their maximum anticipated weight to ensure safety and compliance with industry standards.
3. Tolerance Levels: Why Are They Important?
Tolerance levels refer to the allowable deviation from specified dimensions in the manufacturing process. High tolerance levels ensure that racks fit together correctly and maintain structural integrity under load. For B2B buyers, this is vital as it affects the overall stability and safety of the storage system.
4. Dimensions: How Do They Fit Your Space?
The dimensions of storage racks—including height, width, and depth—must align with the available space in your warehouse or facility. Accurate measurements help prevent overloading and ensure efficient use of vertical space. B2B buyers should consider custom sizes if standard options do not meet their needs.
5. Surface Treatment: What Should You Consider?
Surface treatment options, such as powder coating or galvanization, enhance the durability and resistance of storage racks to environmental factors like moisture and chemicals. For international buyers, especially from humid regions, selecting the right surface treatment can prevent rust and extend the product’s lifespan.
What Are Common Trade Terms in the Storage Rack Industry?
Understanding industry terminology is crucial for effective communication and negotiations with suppliers. Here are some common trade terms:
1. OEM (Original Equipment Manufacturer): What Does It Mean?
An OEM refers to a company that produces parts or equipment that may be marketed by another manufacturer. In the context of storage racks, buyers might work directly with OEMs for customized solutions, ensuring that products meet specific requirements.
2. MOQ (Minimum Order Quantity): Why Is It Important?
MOQ is the smallest quantity of a product that a supplier is willing to sell. This term is particularly relevant for B2B buyers, as understanding MOQ can help in budgeting and inventory management. Negotiating a lower MOQ can be advantageous for smaller businesses looking to reduce upfront costs.
3. RFQ (Request for Quotation): How Should You Use It?
An RFQ is a document sent to suppliers asking for pricing and terms for specific products or services. For buyers, crafting a detailed RFQ ensures that suppliers provide accurate quotes, making it easier to compare options and make informed decisions.
4. Incoterms: What Do They Cover?
Incoterms, or International Commercial Terms, are a set of predefined rules that define the responsibilities of buyers and sellers in international transactions. Familiarity with Incoterms is essential for B2B buyers, as they determine shipping costs, risk, and responsibilities, impacting overall procurement strategies.
5. Lead Time: What Should You Expect?
Lead time is the duration from placing an order to receiving the product. Understanding lead times is critical for inventory planning and ensuring that storage solutions arrive when needed. Buyers should communicate expected lead times to avoid disruptions in their operations.
By grasping these technical properties and trade terms, international B2B buyers can make informed decisions when selecting storage rack suppliers, ultimately enhancing efficiency and operational effectiveness.
Navigating Market Dynamics and Sourcing Trends in the storage rack supplier Sector
What Are the Current Market Dynamics and Key Trends in the Storage Rack Supplier Sector?
The global storage rack supplier market is experiencing significant growth, driven by the rising demand for efficient warehouse management and logistics optimization. This demand is particularly evident in regions such as Africa, South America, the Middle East, and Europe, where urbanization and e-commerce expansion are reshaping supply chains. International B2B buyers are increasingly looking for innovative storage solutions that enhance space utilization, improve operational efficiency, and adapt to fluctuating inventory levels.
Emerging technologies such as automation and the Internet of Things (IoT) are transforming traditional storage practices. Automated storage and retrieval systems (AS/RS) and smart racks that integrate real-time tracking and monitoring capabilities are becoming mainstream. These technologies not only streamline warehouse operations but also reduce labor costs, making them attractive to B2B buyers. Moreover, the adoption of modular and customizable storage solutions is gaining traction as businesses seek to optimize their space while accommodating varying inventory sizes.
Regional dynamics also play a crucial role in sourcing trends. For instance, in Africa and South America, the growth of the retail sector is driving demand for versatile storage solutions. Conversely, in Europe and the Middle East, stringent regulations around safety and sustainability are influencing buyers’ decisions, compelling them to prioritize suppliers who comply with these standards.
How Does Sustainability and Ethical Sourcing Impact the Storage Rack Supplier Industry?
The environmental impact of manufacturing and sourcing storage racks has become a critical concern for international B2B buyers. Companies are increasingly focused on sustainability and ethical sourcing practices, seeking suppliers who can demonstrate a commitment to reducing their carbon footprint. This is particularly relevant in regions like Europe, where regulatory frameworks encourage sustainable business practices.
Sustainable materials, such as recycled metals and eco-friendly coatings, are gaining popularity among storage rack suppliers. B2B buyers are encouraged to look for certifications like ISO 14001, which indicates a company’s commitment to environmental management. Additionally, many suppliers are adopting life cycle assessments (LCA) to evaluate the environmental impact of their products from production to disposal.
Ethical supply chains are also becoming essential, as buyers seek transparency in sourcing practices. This includes ensuring that labor standards are met and that the supply chain does not contribute to environmental degradation. By prioritizing suppliers with green certifications and transparent sourcing practices, international buyers can mitigate risks and enhance their brand reputation.
What Is the Brief Evolution of the Storage Rack Supplier Sector?
The storage rack supplier sector has evolved significantly over the past few decades, transitioning from simple, static shelving systems to sophisticated, modular storage solutions. Initially, storage racks were primarily designed for heavy-duty industrial applications. However, as the logistics and warehousing industries have expanded, so too has the need for more versatile and efficient storage options.
In the late 20th century, the introduction of pallet racking systems marked a significant turning point, allowing for better space utilization and easier inventory access. The rise of e-commerce in the 2000s further accelerated innovation, as suppliers began to develop more dynamic and automated storage solutions to meet the demands of rapid fulfillment and inventory turnover.
Today, the focus is on integrating technology into storage solutions, with smart racks and automated systems leading the way. This evolution reflects a broader trend towards digitalization in supply chain management, offering B2B buyers enhanced capabilities to optimize their operations and respond to market changes efficiently.
Frequently Asked Questions (FAQs) for B2B Buyers of storage rack supplier
-
How do I assess the quality of storage racks from suppliers?
To evaluate the quality of storage racks, request samples or detailed specifications from suppliers. Look for certifications such as ISO 9001, which indicates adherence to quality management standards. Additionally, inquire about the materials used, load capacity, and any warranty or guarantee offered. Conducting a site visit to the supplier’s manufacturing facility can also provide insights into their production practices and quality control measures. -
What are the key factors to consider when choosing a storage rack supplier?
When selecting a storage rack supplier, consider their industry experience, reputation, and customer reviews. Evaluate their product range for customization options and compliance with local safety standards. Assess their logistics capabilities, including delivery timelines and costs, as well as their after-sales support and maintenance services. It’s also beneficial to ensure they have a transparent communication process for resolving potential issues. -
How can I determine the best storage rack type for my business needs?
Identifying the best storage rack type involves analyzing your specific storage requirements, including the types of products, volume, and weight. For example, selective pallet racks are suitable for easy access, while drive-in racks maximize storage density for bulk items. Consider your warehouse layout and the flow of goods. Consulting with suppliers can provide tailored recommendations based on your operational needs. -
What customization options should I expect from storage rack suppliers?
Most storage rack suppliers offer various customization options, including rack dimensions, color, and material type. Some suppliers may also provide specialized designs to accommodate unique storage needs, such as adjustable shelving or integrated safety features. Discuss your specific requirements with potential suppliers to ensure they can meet your expectations and provide prototypes if necessary. -
What is the minimum order quantity (MOQ) for storage racks, and how does it vary by supplier?
The minimum order quantity for storage racks can vary significantly among suppliers, ranging from a few units to several hundred. It often depends on the supplier’s production capabilities and your specific requirements. Always clarify the MOQ before proceeding with negotiations, as this can affect pricing and lead times. Suppliers may offer flexibility for larger orders or long-term contracts. -
What payment terms should I negotiate with my storage rack supplier?
When negotiating payment terms, consider options like upfront payments, installment plans, or letters of credit to mitigate risks. Standard terms often range from 30 to 60 days post-delivery. Ensure you understand any additional fees or currency exchange implications, especially when dealing with international suppliers. Establishing clear terms upfront can prevent misunderstandings later in the process. -
How do logistics and shipping impact the procurement of storage racks?
Logistics and shipping play a critical role in the timely delivery of storage racks. Factors such as the supplier’s location, shipping methods, and customs regulations can affect lead times and costs. Ensure that your supplier has reliable logistics partners and understands the intricacies of international shipping, particularly if you’re importing racks from regions like Europe or Asia. Discussing these aspects upfront can help manage expectations. -
What quality assurance measures should be in place for storage racks?
Quality assurance measures for storage racks should include regular inspections during production, load testing, and adherence to safety standards. Suppliers should provide documentation of compliance with relevant regulations and certifications. Request information about their quality control processes and whether they offer post-installation inspections to ensure the racks meet safety and performance expectations after deployment.
Important Disclaimer & Terms of Use
⚠️ Important Disclaimer
The information provided in this guide, including content regarding manufacturers, technical specifications, and market analysis, is for informational and educational purposes only. It does not constitute professional procurement advice, financial advice, or legal advice.
While we have made every effort to ensure the accuracy and timeliness of the information, we are not responsible for any errors, omissions, or outdated information. Market conditions, company details, and technical standards are subject to change.
B2B buyers must conduct their own independent and thorough due diligence before making any purchasing decisions. This includes contacting suppliers directly, verifying certifications, requesting samples, and seeking professional consultation. The risk of relying on any information in this guide is borne solely by the reader.
Strategic Sourcing Conclusion and Outlook for storage rack supplier
In the complex landscape of global supply chains, strategic sourcing remains a cornerstone for international B2B buyers, especially those operating in Africa, South America, the Middle East, and Europe. By prioritizing strategic sourcing, businesses can optimize costs, enhance supplier relationships, and ensure access to high-quality storage rack solutions tailored to their specific operational needs.
What Are the Key Takeaways for B2B Buyers in Strategic Sourcing?
Understanding the nuances of the storage rack market is essential. Engage with suppliers who not only provide competitive pricing but also demonstrate a commitment to sustainability and innovation. Buyers should leverage technology to streamline procurement processes, ensuring timely deliveries and robust inventory management.
How Can Buyers Prepare for Future Supply Chain Challenges?
As global dynamics shift, staying ahead of market trends and supplier capabilities will be critical. Embrace agility in sourcing strategies to adapt quickly to changes in demand and supply fluctuations.
In conclusion, the path forward for international B2B buyers involves a proactive approach to sourcing that emphasizes collaboration and informed decision-making. Now is the time to forge strong partnerships with reliable storage rack suppliers to enhance operational efficiency and drive business growth. Start exploring your options today to secure the best solutions for your logistics needs.