Discover Top Welding Electrodes Suppliers: Your Complete Guide (2025)
Introduction: Navigating the Global Market for welding electrodes supplier
Navigating the global market for welding electrodes suppliers presents a unique set of challenges for international B2B buyers, particularly those from Africa, South America, the Middle East, and Europe. With the increasing demand for high-quality welding electrodes in various industries, sourcing these materials effectively is crucial. Buyers often face difficulties in identifying reliable suppliers, understanding the diverse types of welding electrodes available, and evaluating the best options for their specific applications. This guide aims to empower B2B buyers by providing an in-depth exploration of the welding electrodes market, including the different types, their applications, and key factors to consider when vetting suppliers.
In this comprehensive resource, we will cover essential topics such as the various types of welding electrodes and their suitability for different projects, practical tips for supplier vetting to ensure quality and reliability, and insights into cost considerations that can impact purchasing decisions. By leveraging this guide, buyers will gain the knowledge needed to make informed choices, minimizing risks and maximizing value in their sourcing strategies. Whether you are a manufacturer in South Africa, a construction firm in Brazil, or an engineering company in the Middle East, understanding the nuances of the welding electrodes market will enhance your procurement processes and contribute to your business’s overall success.
Understanding welding electrodes supplier Types and Variations
Type Name | Key Distinguishing Features | Primary B2B Applications | Brief Pros & Cons for Buyers |
---|---|---|---|
Mild Steel Electrodes | Versatile, suitable for general-purpose welding | Construction, manufacturing, automotive | Pros: Cost-effective, easy to use. Cons: Limited to mild steel applications. |
Stainless Steel Electrodes | High corrosion resistance, suitable for high-temperature applications | Food processing, chemical industries | Pros: Durable, excellent weld quality. Cons: Higher cost, requires skilled handling. |
Cast Iron Electrodes | Designed for welding cast iron, specialized formulations | Repair and maintenance of cast iron parts | Pros: Strong bond, good for repairs. Cons: Limited to specific materials. |
Low Hydrogen Electrodes | Reduces hydrogen-induced cracking, ideal for high-strength steels | Pressure vessels, pipelines | Pros: High strength, reliable for critical applications. Cons: Requires specific storage conditions. |
Flux-Cored Electrodes | Self-shielded or gas-shielded, versatile in outdoor conditions | Heavy fabrication, shipbuilding | Pros: High deposition rates, minimal cleanup. Cons: More expensive, can produce slag. |
What Are Mild Steel Electrodes and Their Applications?
Mild steel electrodes are among the most commonly used types of welding electrodes. They are versatile and suitable for general-purpose welding tasks, making them ideal for industries like construction, manufacturing, and automotive. When purchasing mild steel electrodes, buyers should consider factors such as welding position, joint design, and the specific requirements of the project. Their cost-effectiveness and ease of use make them a popular choice, although they are limited to mild steel applications.
How Do Stainless Steel Electrodes Differ in Performance?
Stainless steel electrodes are designed for applications requiring high corrosion resistance and durability, making them suitable for industries such as food processing and chemical manufacturing. These electrodes offer excellent weld quality and can withstand high temperatures, which is crucial for specific applications. Buyers should evaluate the type of stainless steel being welded and the potential exposure to corrosive environments. While they offer superior performance, the higher cost and the necessity for skilled handling can be potential drawbacks.
What Makes Cast Iron Electrodes Essential for Repairs?
Cast iron electrodes are specifically formulated for welding cast iron materials, which are commonly used in machinery and automotive parts. They provide a strong bond, making them ideal for repair and maintenance tasks. When sourcing cast iron electrodes, B2B buyers should consider the type of cast iron being welded and the anticipated stress on the weld. While they are advantageous for repairs, their specialized nature limits their use to specific materials.
Why Choose Low Hydrogen Electrodes for Critical Applications?
Low hydrogen electrodes are essential for welding high-strength steels and are designed to minimize hydrogen-induced cracking. This makes them particularly valuable in industries such as pressure vessel and pipeline construction. Buyers should consider storage and handling requirements, as these electrodes need to be kept in a dry environment to maintain their effectiveness. While they provide high strength and reliability, the need for specific storage conditions can be a challenge for some organizations.
What Are the Benefits of Using Flux-Cored Electrodes?
Flux-cored electrodes offer the flexibility of being self-shielded or gas-shielded, making them suitable for outdoor welding applications. They are commonly used in heavy fabrication and shipbuilding due to their high deposition rates and minimal cleanup requirements. When selecting flux-cored electrodes, buyers should assess the welding environment and the potential for slag formation. Although they can be more expensive than other types, their efficiency and effectiveness in challenging conditions make them a worthwhile investment.
Related Video: 5 Main types of Welding Electrodes
Key Industrial Applications of welding electrodes supplier
Industry/Sector | Specific Application of Welding Electrodes Supplier | Value/Benefit for the Business | Key Sourcing Considerations for this Application |
---|---|---|---|
Construction | Structural Steel Fabrication | Ensures strong, durable connections for safety and longevity | Quality certifications and compliance with local standards |
Automotive Manufacturing | Vehicle Body Assembly | Provides high-strength welds that withstand stress and impact | Availability of specialized electrodes for different metals |
Oil & Gas | Pipeline Welding | Facilitates safe transportation of resources over long distances | Resistance to corrosion and high temperatures |
Shipbuilding | Hull Construction | Enhances the structural integrity and durability of vessels | Custom electrode formulations for various marine applications |
Heavy Machinery | Equipment Repair and Maintenance | Reduces downtime and extends the lifespan of machinery | Compatibility with existing machinery and ease of use |
What Are the Key Applications of Welding Electrodes in the Construction Industry?
In the construction sector, welding electrodes are pivotal in structural steel fabrication. They create strong, durable connections that are essential for the safety and longevity of buildings and infrastructure. For international buyers, particularly those in Africa and South America, it is critical to source electrodes that meet local building codes and standards, ensuring compliance and quality assurance. Additionally, suppliers should provide detailed specifications on electrode types suitable for various environmental conditions, such as humidity and temperature extremes.
How Do Welding Electrodes Benefit Automotive Manufacturing?
In the automotive industry, welding electrodes are used extensively in vehicle body assembly. They facilitate high-strength welds that can withstand significant stress and impact, which is vital for vehicle safety. Buyers from the Middle East and Europe should consider sourcing electrodes that are compatible with advanced automotive materials, such as high-strength steel and aluminum. It is also beneficial to inquire about the supplier’s ability to provide specialized electrodes that cater to specific manufacturing processes like spot welding or MIG welding.
What Role Do Welding Electrodes Play in Oil & Gas Pipeline Welding?
Welding electrodes are crucial in the oil and gas sector, particularly for pipeline welding. They ensure the safe transportation of resources over long distances by creating robust welds that are resistant to pressure and environmental factors. Buyers in regions with harsh climates, such as parts of Africa and the Middle East, should prioritize suppliers who offer electrodes with superior corrosion resistance and the ability to withstand high temperatures. It is also essential to verify that the electrodes comply with industry regulations and standards to prevent operational failures.
Why Are Welding Electrodes Important in Shipbuilding?
In shipbuilding, welding electrodes are integral to hull construction, enhancing the structural integrity and durability of vessels. The unique conditions at sea demand electrodes that can withstand harsh environments, including saltwater corrosion. For buyers in Europe and South America, sourcing electrodes designed specifically for marine applications is crucial. Suppliers should provide custom formulations that meet the specific needs of different ship types and construction methods, ensuring compliance with maritime safety standards.
How Do Welding Electrodes Aid in Heavy Machinery Maintenance?
Welding electrodes are vital for the repair and maintenance of heavy machinery, significantly reducing downtime and extending the lifespan of equipment. Buyers, especially from developing regions like Africa, should focus on sourcing electrodes that are compatible with various types of machinery and easy to use. Additionally, it is important to assess the supplier’s ability to provide technical support and training, ensuring that the electrodes can be utilized effectively in maintenance operations.
Related Video: Stick Welding Electrodes Explained: Stick Welding Basics for Beginners
3 Common User Pain Points for ‘welding electrodes supplier’ & Their Solutions
Scenario 1: Sourcing Quality Welding Electrodes in a Competitive Market
The Problem:
B2B buyers often struggle to find reliable suppliers of high-quality welding electrodes, particularly in regions like Africa and South America where local options may be limited. Buyers may face challenges such as inconsistent product quality, lack of certifications, and the inability to verify supplier credibility. This can lead to costly production delays, rework, and project failures, impacting the overall bottom line.
The Solution:
To overcome these challenges, buyers should conduct thorough due diligence when selecting welding electrode suppliers. Start by researching suppliers that have established a strong reputation in the market. Look for certifications such as ISO or AWS (American Welding Society) that validate their quality standards. Utilize platforms like industry-specific trade shows or online B2B marketplaces to assess potential suppliers’ product offerings and customer reviews. Establishing a small trial order can also help evaluate the quality before committing to larger purchases. Additionally, consider suppliers with a local presence for easier communication and logistics.
Scenario 2: Navigating Technical Specifications for Welding Electrodes
The Problem:
A common pain point for B2B buyers is understanding the technical specifications of welding electrodes. Different projects require specific types of electrodes that can handle varying conditions such as temperature, material type, and application methods. Misunderstanding these specifications can lead to choosing the wrong electrodes, resulting in poor weld quality and increased costs.
The Solution:
Buyers should invest time in understanding the technical details of welding electrodes, including their classifications (e.g., E6013, E7018) and the materials they are suitable for. Collaborating with welding engineers or technical experts can provide insights into the best electrodes for specific applications. Suppliers often provide technical datasheets; reviewing these documents can be invaluable. Additionally, buyers can seek suppliers who offer technical support or training sessions, ensuring that they have a solid grasp of the products they are purchasing.
Scenario 3: Managing Supply Chain Disruptions and Lead Times
The Problem:
Supply chain disruptions are an ever-present challenge in the global market, and welding electrodes are no exception. Buyers may encounter delays due to factors such as shipping issues, customs regulations, or even local market fluctuations. Such disruptions can halt production lines, leading to significant financial losses and project delays.
The Solution:
To mitigate the risk of supply chain disruptions, buyers should establish a diversified supplier network. Relying on a single supplier can be risky, so it is beneficial to have multiple sources for welding electrodes. Implementing just-in-time inventory management can also help maintain adequate stock levels without overcommitting capital. Additionally, developing strong relationships with suppliers can facilitate better communication during disruptions, allowing buyers to receive timely updates and alternative solutions. Regularly reviewing and updating supply chain strategies based on market trends and supplier performance will further enhance resilience against disruptions.
Strategic Material Selection Guide for welding electrodes supplier
When selecting welding electrodes, the choice of material is critical for ensuring performance, durability, and compatibility with specific applications. Below, we analyze four common materials used in welding electrodes, focusing on their properties, advantages, disadvantages, and implications for international B2B buyers, particularly from regions like Africa, South America, the Middle East, and Europe.
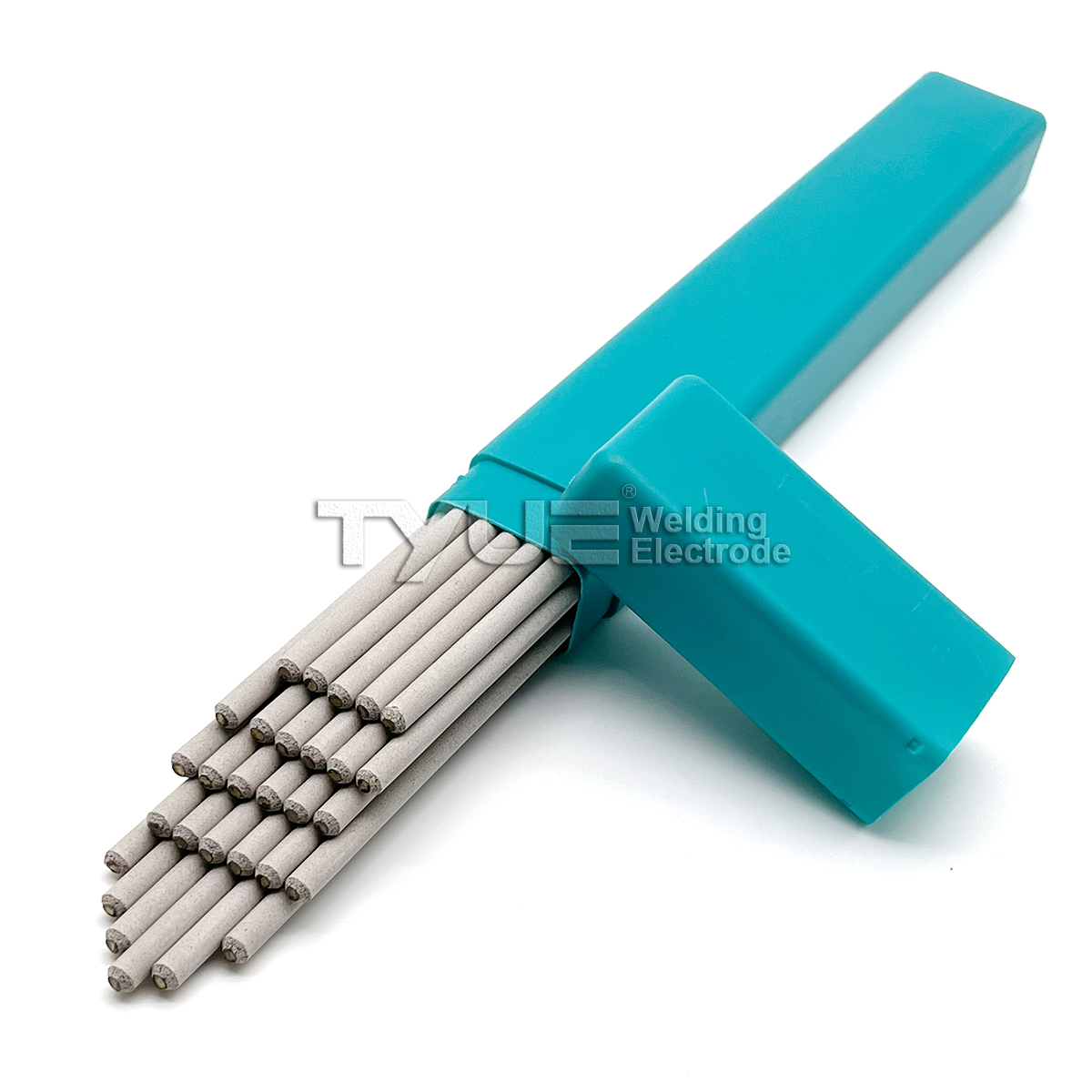
A stock image related to welding electrodes supplier.
What are the Key Properties of Mild Steel Electrodes?
Mild steel electrodes are among the most commonly used in welding applications. They are characterized by their excellent weldability and ductility, making them suitable for a wide range of applications.
- Key Properties: Mild steel electrodes typically have a temperature rating of around 600°C and exhibit good mechanical properties. They are also relatively resistant to corrosion under normal conditions.
- Pros & Cons: The advantages of mild steel electrodes include their low cost, ease of availability, and good performance in various welding processes. However, they may not perform well in high-stress or corrosive environments, limiting their application in specialized industries.
- Impact on Application: These electrodes are ideal for general fabrication and structural work but may not be suitable for applications requiring high corrosion resistance or extreme temperatures.
- Considerations for International Buyers: Buyers should ensure compliance with standards such as ASTM A36 or similar local standards. In regions with high humidity or corrosive environments, additional coatings or treatments may be necessary.
How Do Stainless Steel Electrodes Compare in Performance?
Stainless steel electrodes are favored for their corrosion resistance and strength, making them suitable for demanding applications.
- Key Properties: Stainless steel electrodes can withstand temperatures exceeding 800°C and are highly resistant to oxidation and corrosion.
- Pros & Cons: The main advantages include durability and the ability to maintain structural integrity in harsh environments. However, they are generally more expensive and can be more challenging to weld due to their thermal conductivity.
- Impact on Application: These electrodes are ideal for industries such as food processing, chemical manufacturing, and marine applications where corrosion resistance is paramount.
- Considerations for International Buyers: Compliance with standards such as ASTM A240 or EN 10088 is crucial. Buyers should also consider the specific grade of stainless steel required for their applications, as this can vary significantly.
What are the Benefits of Using Nickel-Based Electrodes?
Nickel-based electrodes are used in specialized applications, particularly in high-temperature and corrosive environments.
- Key Properties: They can operate effectively at temperatures up to 1000°C and are resistant to both oxidation and corrosion.
- Pros & Cons: The key advantage is their ability to perform under extreme conditions, making them suitable for aerospace and power generation industries. However, they are among the most expensive electrode materials and require skilled labor for proper application.
- Impact on Application: These electrodes are particularly effective in welding high-strength steels and alloys, where traditional materials may fail.
- Considerations for International Buyers: Buyers must ensure adherence to specific standards such as ASTM B168 and consider the availability of skilled labor familiar with nickel welding processes.
Why Choose Cast Iron Electrodes for Specific Applications?
Cast iron electrodes are specifically designed for welding cast iron components, which can be challenging due to their brittleness.
- Key Properties: These electrodes can withstand temperatures of around 500°C and are designed to minimize cracking during the welding process.
- Pros & Cons: The primary advantage is their ability to create strong welds on cast iron without compromising the base material. However, they can be more expensive and may require pre-heating and post-weld treatment to prevent cracking.
- Impact on Application: Ideal for repairing cast iron machinery and components, they are essential in industries such as automotive and manufacturing.
- Considerations for International Buyers: Compliance with standards like ASTM A48 is important, and buyers should ensure they have access to the appropriate welding equipment and expertise.
Summary Table of Material Selection for Welding Electrodes
Material | Typical Use Case for welding electrodes supplier | Key Advantage | Key Disadvantage/Limitation | Relative Cost (Low/Med/High) |
---|---|---|---|---|
Mild Steel | General fabrication and structural work | Low cost and good weldability | Limited corrosion resistance | Low |
Stainless Steel | Food processing, chemical manufacturing | Excellent corrosion resistance | Higher cost and welding complexity | High |
Nickel-Based | Aerospace and power generation | High-temperature performance | Very high cost and skilled labor required | High |
Cast Iron | Repairing cast iron machinery | Strong welds on brittle materials | Requires pre-heating and post-weld treatment | Medium |
This guide provides a strategic overview for international B2B buyers to make informed decisions when selecting welding electrodes. Understanding the properties and implications of each material can significantly impact the success of their welding projects.
In-depth Look: Manufacturing Processes and Quality Assurance for welding electrodes supplier
What Are the Main Stages of Manufacturing Welding Electrodes?
The manufacturing process of welding electrodes is intricate and involves several critical stages. Understanding these stages is essential for B2B buyers looking for reliable suppliers. Here are the primary steps involved in the manufacturing of welding electrodes:
-
Material Preparation:
The first step involves selecting and preparing the raw materials, which typically include ferrous and non-ferrous metals, flux materials, and alloying elements. This stage may also involve the melting and refining of metals to ensure purity and eliminate impurities that could affect the performance of the electrodes. Buyers should inquire about the sourcing and quality of these materials, as they are pivotal to the final product’s quality. -
Forming:
Once the materials are prepared, they are formed into the desired shape. This can be achieved through processes such as extrusion or rolling, where the raw materials are shaped into rods of specific diameters and lengths. Understanding the forming techniques used by suppliers can provide insight into the production efficiency and potential lead times for orders. -
Assembly:
After forming, the electrodes are assembled with coatings and flux materials. This coating is essential for the welding process as it helps in the formation of a protective gas shield and facilitates better weld penetration. The assembly stage may also involve adding specific properties to the electrodes, such as increased arc stability or better resistance to oxidation. -
Finishing:
The final stage involves finishing processes that enhance the electrodes’ usability and performance. This may include drying, cutting to size, and packaging. Finishing processes are crucial as they ensure that the electrodes are ready for shipping and meet the required specifications. B2B buyers should confirm the finishing standards with suppliers to ensure compatibility with their welding applications.
What Quality Assurance Standards Should B2B Buyers Look for in Welding Electrodes?
Quality assurance is paramount in the manufacturing of welding electrodes, as it directly affects the performance and safety of welding operations. Here are essential quality assurance standards and checkpoints that international B2B buyers should consider:
-
International Standards:
Suppliers should comply with recognized international quality management standards such as ISO 9001. This standard ensures that the supplier maintains a consistent quality management system that meets customer requirements and enhances satisfaction. Buyers from regions like Africa, South America, the Middle East, and Europe should specifically look for suppliers that hold ISO certifications to ensure reliability. -
Industry-Specific Certifications:
Beyond ISO, industry-specific certifications such as CE marking, API (American Petroleum Institute) standards, and AWS (American Welding Society) certifications can provide additional assurance regarding the quality and safety of the electrodes. These certifications indicate that the products have met stringent safety and performance criteria that are often required in specialized applications. -
Quality Control Checkpoints:
The manufacturing process should include several quality control checkpoints:
– Incoming Quality Control (IQC): This involves inspecting raw materials before they enter the production line to ensure they meet specified standards.
– In-Process Quality Control (IPQC): This includes ongoing checks during the manufacturing process to detect any deviations from quality standards.
– Final Quality Control (FQC): This is the last line of defense before products are shipped, ensuring that all electrodes meet the required specifications and are free from defects. -
Common Testing Methods:
Various testing methods are employed to ensure the quality of welding electrodes. These include tensile strength tests, impact tests, and metallographic examination. Buyers should inquire about the testing protocols used by suppliers and request access to testing reports.
How Can B2B Buyers Verify the Quality Control of Welding Electrode Suppliers?
Verifying the quality control processes of welding electrode suppliers is crucial for establishing trust and ensuring that the products will meet operational needs. Here are actionable strategies for B2B buyers:
-
Conduct Audits:
One of the most effective ways to verify a supplier’s quality control processes is through on-site audits. During these audits, buyers can assess the manufacturing facilities, quality control systems, and adherence to international standards. Consider scheduling regular audits to maintain ongoing oversight. -
Request Documentation:
Suppliers should be able to provide documentation that outlines their quality control processes and results. This includes certifications, inspection reports, and compliance with industry standards. Requesting these documents can help buyers assess the supplier’s commitment to quality. -
Engage Third-Party Inspectors:
Utilizing third-party inspection services can provide an unbiased evaluation of the supplier’s quality assurance processes. These inspectors can conduct thorough assessments of the manufacturing processes and product quality, offering insights that may not be available through supplier-provided documentation. -
Understand QC Nuances for International Trade:
B2B buyers should be aware of specific quality control nuances that may arise in international trade, particularly regarding compliance with local regulations and standards in their regions. Buyers from Africa, South America, the Middle East, and Europe should familiarize themselves with both the supplier’s and their own region’s regulatory requirements to ensure smooth transactions.
What Are the Benefits of Ensuring Quality in Welding Electrodes?
Investing time and resources in verifying the quality of welding electrodes can lead to several significant benefits for B2B buyers:
- Enhanced Safety: High-quality welding electrodes reduce the risk of weld failures, which can lead to safety hazards in construction and manufacturing environments.
- Improved Performance: Quality electrodes contribute to better weld quality, ensuring that the final products meet performance specifications and customer expectations.
- Cost Efficiency: By ensuring quality upfront, buyers can minimize the costs associated with rework, returns, and project delays caused by subpar materials.
In conclusion, understanding the manufacturing processes and quality assurance practices of welding electrode suppliers is vital for B2B buyers. By focusing on material preparation, forming, assembly, finishing, and stringent quality control measures, buyers can make informed decisions that lead to successful partnerships and high-quality welding outcomes.
Practical Sourcing Guide: A Step-by-Step Checklist for ‘welding electrodes supplier’
Introduction: How to Source Welding Electrodes Suppliers Effectively
Sourcing welding electrodes suppliers requires a systematic approach to ensure you find a reliable partner that meets your technical and logistical needs. This guide provides a step-by-step checklist tailored for international B2B buyers, particularly from Africa, South America, the Middle East, and Europe. By following these actionable steps, you can enhance your procurement process and establish a fruitful supplier relationship.
Step 1: Define Your Technical Specifications
Before initiating the sourcing process, it’s vital to outline your technical requirements for welding electrodes. This includes understanding the types of materials you will be welding and the specific electrode characteristics needed, such as diameter, coating type, and strength.
- Why it matters: Clear specifications help you communicate effectively with suppliers and ensure they can meet your production needs.
- What to look for: Detail any industry standards or certifications that the electrodes must comply with, such as AWS or ISO specifications.
Step 2: Research Potential Suppliers
Start your search by compiling a list of potential suppliers through online directories, trade shows, and industry networks. Pay attention to suppliers that specialize in the types of electrodes you require.
- Why it matters: A thorough research phase can uncover suppliers who are well-regarded in the industry.
- What to look for: Prioritize suppliers with positive reviews, a strong track record, and relevant experience in your region.
Step 3: Evaluate Supplier Certifications and Compliance
Verify that potential suppliers hold the necessary certifications and comply with local and international regulations. Certifications such as ISO 9001 for quality management and ISO 3834 for welding quality assurance are essential.
- Why it matters: Certifications ensure that suppliers adhere to quality standards, which can significantly reduce risks in your supply chain.
- What to look for: Request copies of certifications and verify their authenticity through the issuing bodies.
Step 4: Request Samples and Product Specifications
Once you have narrowed down your list of suppliers, request samples of the welding electrodes along with detailed product specifications. This allows you to assess the quality and suitability of the products for your applications.
- Why it matters: Testing samples helps you identify any potential issues before committing to a larger order.
- What to look for: Evaluate the electrodes for performance, usability, and compatibility with your existing equipment.
Step 5: Discuss Pricing and Payment Terms
Engage in discussions regarding pricing structures and payment terms with shortlisted suppliers. Ensure that you understand all costs involved, including shipping and handling.
- Why it matters: Transparent pricing helps in budgeting and prevents unexpected expenses later in the procurement process.
- What to look for: Negotiate terms that suit your cash flow, and inquire about bulk purchase discounts.
Step 6: Conduct Site Visits or Virtual Meetings
If feasible, arrange site visits to the supplier’s facilities or conduct virtual meetings to get a better understanding of their operations. This personal engagement can reveal a lot about their capabilities and reliability.
- Why it matters: Seeing the production process firsthand can increase your confidence in the supplier’s ability to meet your needs.
- What to look for: Assess their production capacity, quality control measures, and overall working conditions.
Step 7: Establish a Trial Order
Before committing to a long-term partnership, place a trial order to evaluate the supplier’s performance in real-time. Monitor the delivery timelines, product quality, and customer service.
- Why it matters: A trial order allows you to assess the supplier’s reliability and responsiveness before making larger commitments.
- What to look for: Pay attention to how well the supplier communicates throughout the process and their willingness to resolve any issues that arise.
By following this checklist, B2B buyers can ensure a structured and effective sourcing process for welding electrodes, leading to successful partnerships and enhanced operational efficiency.
Comprehensive Cost and Pricing Analysis for welding electrodes supplier Sourcing
What Are the Key Cost Components in Welding Electrodes Supplier Sourcing?
When evaluating the cost structure of welding electrodes suppliers, international B2B buyers should focus on several key components. These include:
-
Materials: The choice of materials significantly impacts the overall cost. High-quality raw materials such as steel and alloying elements can lead to higher prices, but they also enhance the performance and durability of the electrodes.
-
Labor: Labor costs vary by region and can influence the final price of welding electrodes. Countries with higher wages may result in increased manufacturing costs. Buyers should consider sourcing from regions with competitive labor costs without compromising quality.
-
Manufacturing Overhead: This encompasses costs related to production facilities, utilities, and administrative expenses. A supplier with advanced technology and efficient processes may have lower overhead costs, which can be beneficial for buyers.
-
Tooling and Setup: Customization of welding electrodes, such as special coatings or sizes, requires specific tooling. This initial investment can increase costs, especially for low-volume orders.
-
Quality Control (QC): Rigorous QC processes ensure that the electrodes meet industry standards. While this adds to the cost, it minimizes the risk of defects and ensures compliance with certifications, which can be crucial for international buyers.
-
Logistics: Shipping costs, including freight and customs duties, can vary significantly based on the supplier’s location and the buyer’s destination. Understanding Incoterms and logistics can help buyers anticipate these costs.
-
Margin: Suppliers typically include a profit margin in their pricing. This can vary based on market conditions, competition, and the supplier’s business model.
How Do Price Influencers Affect Welding Electrodes Sourcing?
Several factors can influence the pricing of welding electrodes:
-
Volume and Minimum Order Quantity (MOQ): Suppliers often provide discounts for bulk purchases. Understanding the MOQ and negotiating for larger orders can lead to cost savings.
-
Specifications and Customization: Custom specifications, such as specific material grades or dimensions, can lead to higher prices. Buyers should weigh the necessity of customization against potential cost increases.
-
Quality and Certifications: Electrodes that meet specific quality standards or certifications (e.g., ISO, AWS) may come at a premium. However, investing in certified products can enhance safety and performance, potentially saving costs in the long run.
-
Supplier Factors: The reputation and reliability of the supplier can impact pricing. Established suppliers may charge more due to their quality assurance and customer service.
-
Incoterms: Understanding the terms of sale (e.g., FOB, CIF) can help buyers gauge total shipping costs and responsibilities, affecting the final price.
What Tips Can Help International Buyers Optimize Costs?
International B2B buyers should employ strategic approaches to optimize costs when sourcing welding electrodes:
-
Negotiate Pricing: Engage suppliers in discussions about pricing structures, especially for larger orders. Leverage competitive quotes to negotiate better terms.
-
Consider Total Cost of Ownership: Beyond the initial purchase price, evaluate the total cost of ownership, including operational efficiency, maintenance, and potential downtime costs due to inferior products.
-
Understand Pricing Nuances: Different markets may exhibit varying pricing trends. For instance, suppliers in Europe might offer more advanced products due to stricter regulations, while suppliers in Africa or South America may provide more cost-effective options.
-
Build Relationships: Establishing long-term relationships with suppliers can lead to better pricing and favorable terms. A reliable supplier is more likely to accommodate requests for customization or volume discounts.
Disclaimer on Indicative Prices
Prices for welding electrodes can fluctuate based on market conditions, material availability, and supplier pricing strategies. Buyers should always seek updated quotes and conduct thorough market research to ensure they are making informed purchasing decisions.
Alternatives Analysis: Comparing welding electrodes supplier With Other Solutions
When considering the procurement of welding solutions, it is essential to evaluate the various options available in the market. While welding electrodes suppliers offer a traditional and widely used method for welding, there are alternative solutions that may better suit specific operational needs and objectives. Below, we will explore two viable alternatives to welding electrodes suppliers: Laser Welding and MIG (Metal Inert Gas) Welding.
Comparison Table of Welding Solutions
Comparison Aspect | Welding Electrodes Supplier | Laser Welding | MIG Welding |
---|---|---|---|
Performance | High, suitable for various metals | Very high, precise control | High, versatile for different applications |
Cost | Moderate, depends on type and quantity | High initial investment | Moderate, equipment and gas costs vary |
Ease of Implementation | Requires skilled labor | Requires specialized training | Easier, can be learned quickly |
Maintenance | Regular checks and replacements needed | Low, but requires calibration | Moderate, depends on usage |
Best Use Case | Heavy-duty applications | Precision tasks, thin materials | General-purpose welding |
What Are the Advantages and Disadvantages of Laser Welding?
Laser welding is recognized for its high precision and ability to weld thin materials without distortion. This method uses a focused laser beam to melt the materials being joined, making it particularly beneficial for applications in the automotive and aerospace industries where precision is critical. However, the downside is the high initial cost of equipment and the need for specialized training to operate the machinery effectively. This can be a barrier for smaller businesses or those in regions with limited access to advanced technology.
How Does MIG Welding Compare as an Alternative Solution?
MIG welding, or Metal Inert Gas welding, is a widely adopted method due to its versatility and ease of use. This process involves feeding a continuous solid wire electrode through the welding gun while simultaneously supplying a shielding gas to protect the weld pool. It is an excellent choice for various materials and thicknesses, making it ideal for construction and manufacturing sectors. The main advantage of MIG welding is that it is relatively easy to learn, allowing companies to train employees quickly. However, it may not perform as well as laser welding in precision tasks or for very thin materials.
Conclusion: How Can B2B Buyers Choose the Right Welding Solution?
Selecting the appropriate welding solution involves a comprehensive analysis of operational requirements, budget constraints, and skill availability. For businesses that prioritize precision and have the budget to invest in advanced technology, laser welding could be the optimal choice. In contrast, for companies seeking a balance between versatility and ease of training, MIG welding represents a practical solution. Traditional welding electrodes suppliers remain a strong option for heavy-duty applications where robustness is critical. Ultimately, understanding the specific needs of your project and the capabilities of each alternative will guide you in making an informed purchasing decision.
Essential Technical Properties and Trade Terminology for welding electrodes supplier
What Are the Key Technical Properties of Welding Electrodes?
When sourcing welding electrodes, understanding the essential technical properties is crucial for ensuring compatibility with your projects. Here are some key specifications to consider:
-
Material Grade
The material grade of a welding electrode indicates its chemical composition and mechanical properties. Common grades include E6010, E6011, E6013, and E7018, each designed for specific applications, such as mild steel or low-alloy steel. For B2B buyers, choosing the correct grade affects the quality and integrity of the weld, directly impacting project outcomes. -
Diameter
The diameter of welding electrodes typically ranges from 1.6 mm to 6.4 mm. The choice of diameter affects the heat input and penetration depth during welding. A larger diameter may be more suitable for thicker materials, while a smaller diameter is often preferred for thinner materials. Understanding these nuances helps buyers select electrodes that match their welding conditions. -
Coating Type
The coating on welding electrodes plays a significant role in the arc stability and the quality of the weld. Common coatings include cellulose, rutile, and basic. Each type offers different characteristics, such as slag removal and arc stability. Buyers should consider the specific requirements of their welding processes when evaluating coating options. -
Tensile Strength
Tensile strength measures how much force a welded joint can withstand before failing. It is critical to match the tensile strength of the electrode with the base materials to ensure structural integrity. For international buyers, understanding tensile strength specifications helps in selecting electrodes that meet local and international standards. -
Current Type
Welding electrodes are designed for either alternating current (AC) or direct current (DC). The choice of current affects the electrode’s performance and the ease of use. Buyers must consider the type of welding equipment available and the specific requirements of their projects to make informed decisions. -
Weld Bead Appearance
The quality of the weld bead can significantly influence the aesthetic and structural qualities of the final product. Factors such as bead size, shape, and consistency can vary depending on the electrode used. Buyers should evaluate electrodes based on their ability to produce the desired weld bead appearance for their applications.
What Are Common Trade Terms in the Welding Industry?
Familiarizing yourself with industry jargon can streamline communication with suppliers and enhance your purchasing strategy. Here are some essential terms:
-
OEM (Original Equipment Manufacturer)
This term refers to companies that produce products that are sold under another company’s brand. In the welding industry, OEMs can provide custom electrodes tailored to specific client needs, which is valuable for international buyers seeking unique solutions. -
MOQ (Minimum Order Quantity)
MOQ indicates the smallest quantity of a product that a supplier is willing to sell. Understanding MOQ is crucial for buyers to manage inventory costs and ensure they meet supplier requirements, especially in regions where storage space may be limited. -
RFQ (Request for Quotation)
An RFQ is a document sent to suppliers requesting price quotes for specific products or services. It’s a vital tool for B2B buyers to compare costs and negotiate terms effectively, ensuring they receive competitive pricing. -
Incoterms (International Commercial Terms)
Incoterms are a set of predefined international trade terms that clarify the responsibilities of buyers and sellers in shipping and delivery. Understanding these terms helps buyers navigate logistics, minimizing potential disputes over shipping costs and responsibilities. -
Lead Time
Lead time refers to the time it takes from placing an order to receiving the products. For welding electrodes, understanding lead times can help buyers plan their projects and manage workflow effectively, especially in regions with longer shipping distances. -
Certification Standards
Certification standards, such as ISO or AWS (American Welding Society), ensure that welding electrodes meet specific quality and safety requirements. Buyers should verify certification status to ensure compliance with local regulations and industry standards.
In summary, grasping these essential technical properties and trade terminology is invaluable for international B2B buyers. This knowledge not only enhances procurement decisions but also fosters stronger partnerships with suppliers in the welding industry.
Navigating Market Dynamics and Sourcing Trends in the welding electrodes supplier Sector
What Are the Current Market Dynamics and Key Trends in the Welding Electrodes Sector?
The global welding electrodes market is experiencing significant growth driven by increasing industrial activities, particularly in the automotive, construction, and manufacturing sectors. Emerging economies in Africa, South America, and the Middle East are witnessing a surge in infrastructure projects, which in turn fuels the demand for welding electrodes. Additionally, advancements in technology, such as automation and Industry 4.0, are reshaping sourcing strategies. B2B buyers are increasingly leveraging digital platforms for procurement, enhancing efficiency and transparency in the supply chain.
A notable trend is the shift towards customized solutions. Suppliers are increasingly offering tailored welding electrodes to meet specific application requirements, thus enhancing operational efficiency and reducing costs for buyers. Furthermore, the rise of e-commerce in B2B transactions facilitates easier access to a broader range of suppliers, allowing international buyers to compare prices and quality more effectively. The integration of predictive analytics and AI in inventory management is also helping suppliers optimize their stock levels and respond more swiftly to market changes.
How Can Sustainability and Ethical Sourcing Impact the Welding Electrodes Supply Chain?
Sustainability has become a critical concern in the welding electrodes sector, with increasing pressure from regulatory bodies and consumers for environmentally friendly practices. B2B buyers should prioritize suppliers who adhere to sustainable practices, such as using eco-friendly materials and processes that minimize waste. The adoption of ‘green’ certifications, such as ISO 14001 or the Eco-Label, is becoming a common benchmark for evaluating suppliers’ environmental credentials.
Ethical sourcing is equally crucial, as buyers are more inclined to partner with suppliers who maintain fair labor practices and transparency throughout their supply chains. This not only enhances the reputation of businesses but also mitigates risks associated with supply chain disruptions. For instance, sourcing welding electrodes from suppliers that ensure responsible mining of raw materials can significantly reduce the environmental impact. Buyers in Africa, South America, the Middle East, and Europe should actively seek suppliers committed to sustainability and ethical practices, as this can lead to long-term partnerships and improved brand loyalty.
What Is the Evolution of the Welding Electrodes Industry?
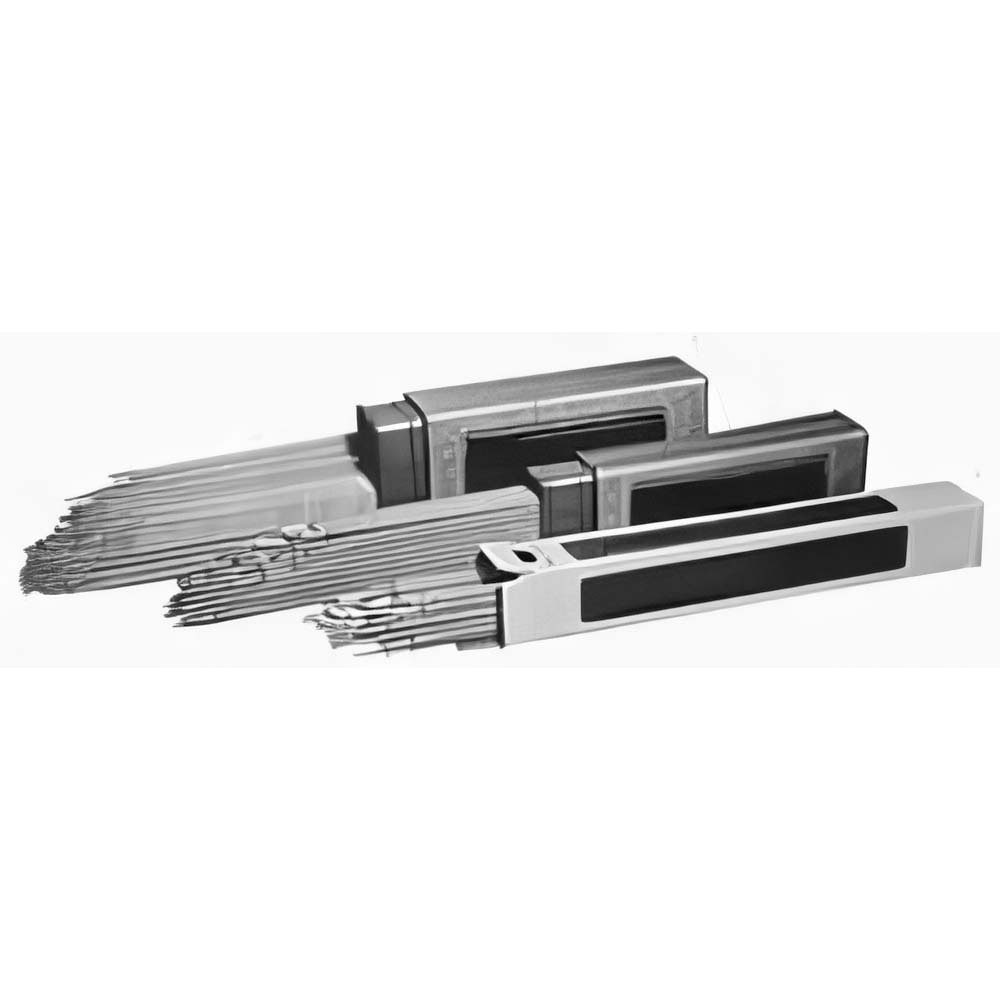
A stock image related to welding electrodes supplier.
The welding electrodes industry has evolved significantly since its inception. Initially dominated by manual welding processes, the sector has undergone a transformation with the introduction of advanced technologies and materials. The development of coated electrodes and flux-cored wires has enhanced the efficiency and quality of welding processes, enabling operators to achieve better results with less effort.
Historically, welding electrodes were primarily produced using traditional methods, which limited their application scope. However, with the industrial revolution and the subsequent rise of manufacturing, the demand for more reliable and versatile welding solutions became apparent. This led to innovations in electrode composition and manufacturing techniques, paving the way for specialized electrodes that cater to diverse industrial needs.
Today, as the industry faces new challenges like environmental regulations and the demand for high-performance products, the focus is shifting towards sustainable practices and innovation in electrode design. This evolution presents a unique opportunity for international B2B buyers to engage with suppliers who not only understand these dynamics but are also equipped to meet the challenges of a rapidly changing market.
Frequently Asked Questions (FAQs) for B2B Buyers of welding electrodes supplier
-
How do I choose the right welding electrodes supplier for my business?
Selecting the right welding electrodes supplier involves assessing their product range, quality certifications, and industry experience. Look for suppliers with a proven track record in your specific industry, whether it be construction, automotive, or manufacturing. Additionally, consider their ability to meet your customization needs and minimum order quantities (MOQ). Request samples to evaluate the quality of their welding electrodes, and ensure they offer robust customer service and technical support. -
What are the key factors to consider when vetting a welding electrodes supplier?
When vetting a welding electrodes supplier, consider factors such as their production capacity, quality assurance processes, and compliance with international standards. Check for certifications like ISO 9001 or AWS (American Welding Society) standards. Investigate their reputation through online reviews and testimonials from other B2B buyers. Additionally, assess their logistics capabilities, including shipping times and costs, to ensure they can meet your delivery requirements. -
What is the typical minimum order quantity (MOQ) for welding electrodes?
The minimum order quantity for welding electrodes can vary significantly between suppliers. Typically, it ranges from 100 kg to several tons, depending on the supplier and the type of electrodes needed. For smaller businesses or those testing new products, some suppliers may offer lower MOQs or allow for mixed product orders. It’s crucial to discuss your specific needs with potential suppliers to negotiate an MOQ that aligns with your purchasing strategy. -
What payment terms should I expect from welding electrodes suppliers?
Payment terms for welding electrodes suppliers often vary based on the supplier’s policies and your business relationship. Common terms include advance payment, net 30, or net 60 days. Some suppliers may offer discounts for upfront payments or larger orders. It’s essential to establish clear payment terms during negotiations to avoid misunderstandings and ensure smooth transactions, especially for international purchases where currency exchange and transfer fees may apply. -
How can I ensure the quality of welding electrodes before placing a large order?
To ensure the quality of welding electrodes, request product samples for testing prior to a large order. Conduct thorough inspections and tests to verify their performance, such as tensile strength and weldability. Additionally, inquire about the supplier’s quality assurance measures, including certifications and testing protocols. Engaging a third-party inspection service can also provide an unbiased evaluation of the product quality before committing to a significant purchase. -
What are the logistics considerations when sourcing welding electrodes internationally?
When sourcing welding electrodes internationally, consider logistics aspects such as shipping methods, lead times, and customs regulations. Air freight may be faster but more expensive, while sea freight is cost-effective for larger shipments. Ensure the supplier can provide necessary documentation for customs clearance, such as certificates of origin and compliance. Understanding incoterms (International Commercial Terms) will also help clarify responsibilities regarding shipping costs and risks. -
Can welding electrodes be customized for specific applications?
Yes, many welding electrodes suppliers offer customization options tailored to specific applications. This may include variations in diameter, coating types, and chemical compositions to suit particular welding processes or materials. Discuss your unique requirements with potential suppliers and ask for their capability to provide custom formulations. Ensure that any custom products are backed by appropriate certifications to guarantee their performance in your applications. -
What are the common types of welding electrodes available in the market?
The market offers various types of welding electrodes, including stick electrodes (SMAW), MIG wires (GMAW), and TIG rods (GTAW). Stick electrodes are versatile and commonly used in construction and maintenance, while MIG wires are favored for their speed and efficiency in industrial applications. TIG rods provide high precision for thin materials. Understanding the specific requirements of your projects will help you choose the appropriate type of electrode for optimal results.
Important Disclaimer & Terms of Use
⚠️ Important Disclaimer
The information provided in this guide, including content regarding manufacturers, technical specifications, and market analysis, is for informational and educational purposes only. It does not constitute professional procurement advice, financial advice, or legal advice.
While we have made every effort to ensure the accuracy and timeliness of the information, we are not responsible for any errors, omissions, or outdated information. Market conditions, company details, and technical standards are subject to change.
B2B buyers must conduct their own independent and thorough due diligence before making any purchasing decisions. This includes contacting suppliers directly, verifying certifications, requesting samples, and seeking professional consultation. The risk of relying on any information in this guide is borne solely by the reader.
Strategic Sourcing Conclusion and Outlook for welding electrodes supplier
What Are the Key Takeaways for B2B Buyers in Strategic Sourcing of Welding Electrodes?
In conclusion, strategic sourcing for welding electrodes is pivotal for international buyers aiming to optimize quality, cost, and supply chain efficiency. By focusing on suppliers that demonstrate not only product excellence but also a commitment to sustainability and innovation, buyers can ensure they are equipped to meet the demands of their respective markets in Africa, South America, the Middle East, and Europe. Establishing strong relationships with reliable suppliers can lead to better pricing, consistent quality, and timely delivery, which are crucial for maintaining competitive advantages in the welding industry.
How Can International Buyers Prepare for Future Trends in Welding Electrodes?
Looking ahead, international B2B buyers should remain vigilant about emerging trends such as automation and digitalization within the welding sector. Engaging with suppliers who leverage technology can enhance operational efficiency and reduce costs. Furthermore, buyers are encouraged to participate in industry exhibitions and forums to network with potential suppliers and stay updated on innovations.
What Should You Do Next as a B2B Buyer?
As you navigate the landscape of welding electrodes suppliers, consider conducting thorough market research and supplier assessments. This proactive approach will empower you to make informed decisions that align with your long-term business objectives. Embrace the opportunity to collaborate with suppliers who share your vision for quality and innovation, paving the way for mutual growth in this dynamic industry.