Discover Top LCD Display Suppliers: Your Complete Guide (2025)
Introduction: Navigating the Global Market for lcd display supplier
In today’s rapidly evolving digital landscape, sourcing an LCD display supplier that meets specific business needs can be a formidable challenge for international B2B buyers. The diverse range of display technologies—including TFT, OLED, and LPTS—each presents unique advantages and limitations that must be carefully considered. This comprehensive guide serves as an essential resource for navigating the complex global market of LCD display suppliers, providing insights into various types of displays, their applications, and best practices for supplier vetting.
This guide is tailored to empower B2B buyers from regions such as Africa, South America, the Middle East, and Europe, including key markets like Poland and Germany. It addresses critical factors such as cost analysis, technological compatibility, and performance metrics to ensure that buyers can make informed purchasing decisions. By understanding the nuances of display technologies and supplier capabilities, businesses can optimize their procurement strategies and secure high-quality LCD products that align with their operational goals.
Whether you are seeking to enhance product offerings, improve customer experiences, or streamline manufacturing processes, this guide equips you with the knowledge needed to confidently choose the right LCD display supplier for your unique requirements.
Understanding lcd display supplier Types and Variations
Type Name | Key Distinguishing Features | Primary B2B Applications | Brief Pros & Cons for Buyers |
---|---|---|---|
TFT LCD | High resolution, fast response time, vibrant colors | Consumer electronics, medical devices, monitors | Pros: Excellent display quality, good for dynamic content. Cons: Higher cost compared to other LCD types. |
IPS LCD | Wide viewing angles, better color reproduction | Professional displays, graphic design, automotive | Pros: Superior color accuracy, consistent brightness. Cons: More expensive, can be thicker than other types. |
VA LCD | High contrast ratios, deeper blacks, good for dark rooms | TVs, gaming monitors, industrial displays | Pros: Excellent contrast, good for movies and games. Cons: Slower response time, limited viewing angles. |
OLED | Self-emitting pixels, thinner design, vibrant colors | High-end smartphones, TVs, digital signage | Pros: Exceptional color depth, energy-efficient. Cons: Higher cost, shorter lifespan compared to LCDs. |
LPTS | Uses low-temperature polycrystalline silicon technology | High-resolution displays, tablets, laptops | Pros: High pixel density, excellent image quality. Cons: More complex manufacturing process, can be costlier. |
What are the Characteristics and Suitability of TFT LCD Displays for B2B Buyers?
TFT (Thin Film Transistor) LCDs are characterized by their ability to deliver high-resolution images with vibrant colors and fast response times. This makes them ideal for applications that require dynamic content, such as consumer electronics and medical devices. When considering a TFT display for B2B purposes, buyers should evaluate the display’s resolution and refresh rate, as these factors can significantly impact performance in critical applications.
Why Choose IPS LCD Displays for Professional Applications?
IPS (In-Plane Switching) LCDs are renowned for their wide viewing angles and superior color reproduction. This technology is particularly suitable for professional environments where color accuracy is paramount, such as graphic design and automotive displays. Buyers should consider IPS displays if their applications demand consistent brightness and color fidelity across different viewing angles, although the investment may be higher than other LCD types.
What Advantages Do VA LCD Displays Offer for Entertainment and Gaming?
VA (Vertical Alignment) LCDs are distinguished by their high contrast ratios and ability to produce deeper blacks, making them suitable for entertainment and gaming applications. They excel in dark environments, providing a more immersive experience for users. However, buyers should be aware of the slower response times and limited viewing angles, which may not be ideal for all use cases.
How Do OLED Displays Enhance Visual Experience in B2B Contexts?
OLED (Organic Light Emitting Diode) displays offer self-emitting pixels, allowing for thinner designs and vibrant colors. They are increasingly used in high-end smartphones, TVs, and digital signage due to their exceptional color depth and energy efficiency. While OLEDs provide a superior visual experience, buyers must consider their higher cost and shorter lifespan, which can affect long-term ROI.
What Should B2B Buyers Know About LPTS Displays?
LPTS (Low-Temperature Polycrystalline Silicon) displays are known for their high pixel density and excellent image quality. This technology is often used in high-resolution displays, tablets, and laptops. B2B buyers should consider LPTS displays for applications requiring detailed visuals and compact designs. However, the more complex manufacturing process can lead to higher costs, so it’s essential to weigh these factors against the specific needs of the application.
Related Video: LCD Monitor Panels Types – TN vs IPS vs VA as Fast As Possible
Key Industrial Applications of lcd display supplier
Industry/Sector | Specific Application of lcd display supplier | Value/Benefit for the Business | Key Sourcing Considerations for this Application |
---|---|---|---|
Automotive | Dashboard displays and infotainment systems | Enhances driver experience and vehicle aesthetics | Reliability, temperature resistance, and customization |
Healthcare | Medical imaging and patient monitoring devices | Improves diagnostic accuracy and patient care | Compliance with medical standards, durability, and clarity |
Retail | Digital signage and interactive kiosks | Boosts customer engagement and sales | Brightness, resolution, and ease of integration |
Consumer Electronics | Televisions and smart home devices | Provides high-quality visuals and user experience | Size, energy efficiency, and supply chain reliability |
Industrial Automation | Control panels and monitoring systems | Increases operational efficiency and process control | Robustness, compatibility with existing systems, and service support |
How Are LCD Displays Used in the Automotive Sector?
In the automotive industry, LCD displays are integrated into dashboard systems and infotainment units. These displays provide real-time information about vehicle performance, navigation, and multimedia options. By enhancing the driver experience, they also contribute to vehicle aesthetics. International buyers, particularly from regions like Europe and the Middle East, should consider sourcing displays that are reliable and capable of withstanding extreme temperatures, ensuring durability and performance in diverse climates.
What Role Do LCD Displays Play in Healthcare Applications?
LCD displays are critical in healthcare settings for medical imaging and patient monitoring devices. They provide high-resolution images that enhance diagnostic accuracy, allowing healthcare professionals to make informed decisions quickly. Buyers from Africa and South America must ensure that their suppliers comply with medical standards, offering displays that are durable and can withstand frequent cleaning, while also providing clarity for critical visual tasks.
How Are LCD Displays Transforming Retail Environments?
In retail, LCD displays are widely used for digital signage and interactive kiosks. These applications not only engage customers but also drive sales by delivering targeted advertisements and promotions. For international B2B buyers, especially from South America and Europe, sourcing displays with high brightness and resolution is essential to ensure visibility in various lighting conditions. Additionally, ease of integration with existing systems can significantly enhance operational efficiency.
What Are the Key Applications of LCD Displays in Consumer Electronics?
LCD displays are integral to consumer electronics, particularly in televisions and smart home devices. They deliver high-quality visuals, enhancing user experience and satisfaction. Buyers from regions like Poland and Germany should focus on sourcing displays that balance size and energy efficiency, as consumers increasingly demand eco-friendly products. Reliability in supply chains is also crucial to meet the high demand for these devices.
Why Are LCD Displays Essential for Industrial Automation?
In industrial automation, LCD displays are used in control panels and monitoring systems. They play a vital role in increasing operational efficiency by providing real-time data and alerts. International buyers, especially from Africa and the Middle East, need to prioritize sourcing robust displays that are compatible with existing systems. Additionally, ongoing service support is an essential consideration to ensure long-term functionality and reliability in demanding industrial environments.
Related Video: Arduino-friendly 240×320 LCD Display Tutorial (ILI9341)
3 Common User Pain Points for ‘lcd display supplier’ & Their Solutions
Scenario 1: Navigating Quality Assurance Challenges with LCD Displays
The Problem:
International B2B buyers often grapple with the inconsistency in quality across different LCD display suppliers. This issue is particularly pronounced when sourcing from regions with varying manufacturing standards. Buyers may receive displays that do not meet their specifications, resulting in costly returns, project delays, and damaged relationships with end-users. The challenge is exacerbated for companies in Africa and South America, where access to reliable quality assurance protocols may be limited.
The Solution:
To navigate quality assurance challenges, B2B buyers should implement a robust supplier evaluation process. Start by requesting detailed product specifications and quality certifications from potential suppliers. Look for suppliers who comply with international quality standards, such as ISO 9001, and have a track record of successful deliveries in your industry.
Additionally, consider conducting on-site inspections or employing third-party quality assurance services to verify manufacturing processes. Establish clear communication channels with suppliers to address any concerns promptly. By doing so, buyers can ensure that they are sourcing high-quality LCD displays that align with their project requirements, thus minimizing the risk of defects and enhancing customer satisfaction.
Scenario 2: Overcoming Supply Chain Disruptions in LCD Display Procurement
The Problem:
Supply chain disruptions can significantly impact the procurement of LCD displays, leading to delays in product launches and increased costs. This scenario is common for B2B buyers in the Middle East and Europe, where geopolitical factors and transportation issues can create bottlenecks. Buyers often find themselves scrambling to find alternative suppliers at the last minute, which can compromise quality and increase lead times.
The Solution:
To mitigate supply chain disruptions, B2B buyers should diversify their supplier base across multiple regions. This strategy helps to reduce dependence on a single source and provides alternatives in case of disruptions. Create a list of potential suppliers from different geographical locations, and maintain relationships with them even when not actively sourcing.
Furthermore, implementing a just-in-time inventory system can help manage stock levels more effectively, ensuring that you have sufficient displays on hand without overcommitting financially. Buyers should also leverage technology by using supply chain management software to track supplier performance and forecast potential disruptions. By proactively managing their supply chain, buyers can maintain smoother operations and reduce the impact of unforeseen delays.
Scenario 3: Addressing Technical Support Limitations from LCD Display Suppliers
The Problem:
B2B buyers frequently encounter difficulties when it comes to technical support from LCD display suppliers. This issue can be particularly frustrating for businesses in Europe, where technological complexities of displays necessitate expert assistance for installation, maintenance, and troubleshooting. Inadequate support can lead to prolonged downtimes and increased operational costs, affecting the overall productivity of the buying organization.
The Solution:
To ensure adequate technical support, buyers should prioritize suppliers that offer comprehensive after-sales services, including training and technical assistance. Before finalizing a contract, inquire about the level of support provided, including response times for service requests and the availability of on-site training.
Additionally, consider suppliers that provide extensive documentation, such as installation manuals, troubleshooting guides, and online support resources. Engaging with suppliers who have a strong reputation for customer service and a dedicated technical support team can significantly enhance the buyer’s experience.
Establishing a clear communication plan with the supplier can also facilitate quicker resolutions to technical issues. By focusing on suppliers that prioritize technical support, buyers can reduce downtimes and enhance the operational efficiency of their LCD display applications.
Strategic Material Selection Guide for lcd display supplier
When sourcing materials for LCD displays, international B2B buyers must consider several factors that directly impact product performance and suitability for their specific applications. Below, we analyze four common materials used in LCD display manufacturing, focusing on their properties, advantages, disadvantages, and implications for buyers in regions such as Africa, South America, the Middle East, and Europe.
What Are the Key Properties of Glass in LCD Displays?
Key Properties: Glass is the primary substrate material for LCD displays, known for its excellent optical clarity and rigidity. It can withstand high temperatures and has a low coefficient of thermal expansion, making it suitable for various environmental conditions.
Pros & Cons: Glass offers high durability and scratch resistance, ensuring long-term performance. However, its weight can be a disadvantage in portable applications, and it is more susceptible to shattering compared to other materials. The manufacturing complexity is moderate, as glass requires precise cutting and treatment processes.
Impact on Application: Glass is compatible with various media, including touch sensors and anti-reflective coatings, enhancing the display’s functionality.
Considerations for International Buyers: Buyers must ensure compliance with international standards such as ASTM and DIN for glass quality and safety. In Europe, for instance, REACH regulations may impact material sourcing.
How Does Plastic Compare as a Material for LCD Displays?
Key Properties: Plastic, often used in the form of polycarbonate or acrylic, is lightweight and offers good impact resistance. It can be manufactured to be transparent, making it suitable for display applications.
Pros & Cons: The primary advantage of plastic is its lightweight nature, which is ideal for portable devices. However, it is less scratch-resistant than glass and may yellow over time when exposed to UV light. The manufacturing process for plastic is generally simpler and less costly than glass.
Impact on Application: Plastic can be used in applications where weight savings are critical, such as mobile devices. However, it may not provide the same optical quality as glass.
Considerations for International Buyers: Buyers should be aware of the varying regulations regarding plastic materials in different regions. In Europe, for example, compliance with RoHS directives is essential to ensure that the materials are free from hazardous substances.
What Are the Benefits of Using Liquid Crystal Materials?
Key Properties: Liquid crystals are the core component of LCD technology, responsible for modulating light to create images. They are sensitive to temperature and require specific conditions to function optimally.
Pros & Cons: The advantage of liquid crystals is their ability to produce high-quality images with low power consumption. However, they can be sensitive to environmental factors such as temperature fluctuations, which may affect performance. The complexity of manufacturing liquid crystals is high, involving precise formulations and handling.
Impact on Application: Liquid crystals are crucial for applications requiring high-resolution displays, such as televisions and computer monitors.
Considerations for International Buyers: It is vital for buyers to consider the supply chain stability for liquid crystal materials, especially in regions with fluctuating market conditions. Compliance with international standards for chemical safety and performance is also critical.
Why Is Backlighting Important in LCD Displays?
Key Properties: Backlighting, typically provided by LEDs, is essential for illuminating LCD screens. LEDs are energy-efficient and have a long lifespan, making them suitable for modern displays.
Pros & Cons: The primary advantage of LED backlighting is its energy efficiency and ability to provide bright, even illumination. However, the initial cost can be higher compared to traditional backlighting methods. The manufacturing complexity is moderate, as it requires integration with the LCD panel.
Impact on Application: Backlighting is crucial for applications in low-light environments, enhancing visibility and user experience.
Considerations for International Buyers: Buyers should assess the energy efficiency ratings and compliance with environmental regulations for LED components in their respective markets.
Summary Table of Material Selection for LCD Displays
Material | Typical Use Case for lcd display supplier | Key Advantage | Key Disadvantage/Limitation | Relative Cost (Low/Med/High) |
---|---|---|---|---|
Glass | High-end monitors and TVs | High durability and optical clarity | Heavy and prone to shattering | High |
Plastic | Portable devices like smartphones | Lightweight and impact-resistant | Less scratch-resistant, UV sensitivity | Medium |
Liquid Crystals | High-resolution displays | Low power consumption, high quality | Sensitive to temperature fluctuations | High |
Backlighting (LED) | TVs and monitors in low-light settings | Energy-efficient and long lifespan | Higher initial cost | Medium |
By understanding these materials and their implications, international B2B buyers can make informed decisions that align with their specific needs and compliance requirements in their respective markets.
In-depth Look: Manufacturing Processes and Quality Assurance for lcd display supplier
What Are the Key Stages in the Manufacturing Process for LCD Displays?
The manufacturing process for LCD displays is complex and involves several critical stages, each playing a vital role in ensuring the final product meets quality standards. Understanding these stages can help B2B buyers from regions like Africa, South America, the Middle East, and Europe (including Poland and Germany) make informed purchasing decisions.
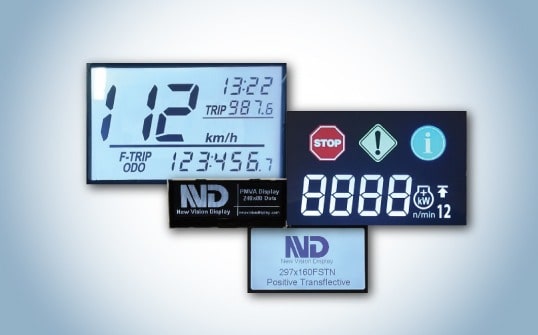
A stock image related to lcd display supplier.
1. Material Preparation: What Materials Are Used in LCD Manufacturing?
The first step in the manufacturing process involves selecting and preparing raw materials. This includes:
- Glass Substrates: High-quality glass is essential for forming the display panels. It must be free from defects to ensure clarity and durability.
- Liquid Crystals: The core component of LCD technology, liquid crystals must be carefully sourced and processed to maintain their unique properties.
- Thin Film Transistors (TFT): These are critical for controlling pixel behavior. The quality of the TFTs directly impacts the display’s performance.
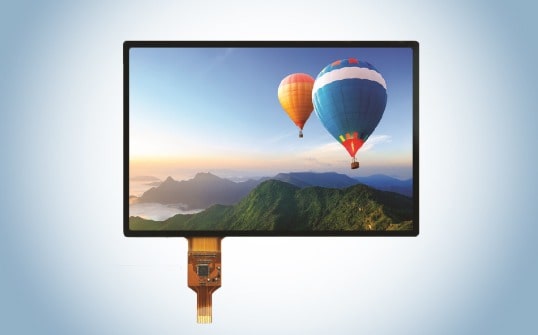
A stock image related to lcd display supplier.
Proper material preparation is crucial as it sets the foundation for the entire manufacturing process. Suppliers should have stringent sourcing protocols to ensure the quality of these materials.
2. Forming: How Are LCD Panels Shaped?
During the forming stage, the prepared materials are shaped into the desired form. This typically involves:
- Coating: Glass substrates are coated with a transparent conductive material, often indium tin oxide (ITO), which is essential for the operation of the liquid crystals.
- Alignment Layer Application: A layer is applied to align liquid crystal molecules in a specific direction, which is crucial for the display’s optical properties.
The techniques used in this stage must ensure uniformity across all panels, as variations can lead to inconsistencies in display quality.
3. Assembly: What Does the Assembly Process Look Like?
The assembly stage combines all individual components into a cohesive unit. This includes:
- Layering: The layers of glass, liquid crystals, and electrodes are carefully assembled. Precision is key to avoid air gaps that can cause display failures.
- Encapsulation: The assembled unit is sealed to protect the liquid crystals and ensure durability. This often involves adhesive materials that must be applied uniformly.
Proper assembly techniques are critical for maintaining the integrity of the display and ensuring longevity.
4. Finishing: What Final Touches Are Added?
In the finishing stage, additional enhancements are applied to improve the display’s overall performance and aesthetics. This can include:
- Polarizers: These are applied to enhance visibility and reduce glare.
- Testing and Calibration: Each display undergoes rigorous testing to ensure it meets specified performance standards, including brightness, color accuracy, and response time.
This stage is crucial for identifying any defects that may have occurred during previous manufacturing steps.
How Is Quality Assurance Implemented in LCD Display Manufacturing?
Quality assurance (QA) is a critical aspect of the LCD manufacturing process, ensuring that each display meets international standards and customer expectations.
1. What Are the Relevant International Standards for LCD Displays?
For B2B buyers, understanding the standards that suppliers adhere to is vital. Key standards include:
- ISO 9001: This standard focuses on quality management systems and is widely recognized across industries. It ensures that suppliers maintain consistent quality in their processes.
- CE Marking: Particularly relevant for suppliers in Europe, CE marking indicates compliance with health, safety, and environmental protection standards.
- API Standards: These may apply to specific applications, ensuring that products meet industry-specific requirements.
Buyers should request documentation proving compliance with these standards to ensure the supplier’s commitment to quality.
2. What Are the Key Quality Control Checkpoints in Manufacturing?
Quality control (QC) is integrated throughout the manufacturing process, with several key checkpoints:
- Incoming Quality Control (IQC): This initial stage verifies the quality of raw materials before they enter production. Suppliers conduct tests to ensure materials meet specified standards.
- In-Process Quality Control (IPQC): Throughout the manufacturing stages, inspections are conducted to identify and rectify any defects early in the process.
- Final Quality Control (FQC): After assembly, each display is thoroughly tested for performance, reliability, and visual quality. This step ensures that only products meeting high standards reach the market.
What Common Testing Methods Are Used in LCD Quality Control?
To maintain high quality, various testing methods are employed during the QC process:
- Visual Inspections: Technicians examine displays for defects such as dead pixels, color inconsistencies, and surface blemishes.
- Functional Testing: Each display undergoes operational tests to ensure it functions correctly under different conditions, including brightness and response time assessments.
- Environmental Testing: Displays are subjected to extreme temperatures and humidity to assess durability and performance in various environments.
Understanding these testing methods allows B2B buyers to gauge the reliability of their suppliers.
How Can B2B Buyers Verify Supplier Quality Control Practices?
For international buyers, especially those from regions like Africa, South America, and the Middle East, verifying supplier quality control practices is essential. Here are actionable steps:
-
Conduct Supplier Audits: Regular audits can help buyers assess a supplier’s manufacturing processes and QC practices firsthand. This provides insight into their operational standards.
-
Request Quality Reports: Suppliers should provide detailed reports on their QC processes, including results from testing and inspections. This documentation can serve as a benchmark for quality assurance.
-
Engage Third-Party Inspectors: Utilizing third-party inspection services can provide an unbiased assessment of a supplier’s quality standards. These inspectors can evaluate processes and products against international standards.
What Are the Quality Control Nuances for International B2B Buyers?
International B2B buyers need to consider several nuances regarding quality control:
- Cultural Differences: Understanding local manufacturing practices and cultural attitudes towards quality can influence supplier selection. Buyers should seek suppliers with a proven track record in their respective regions.
- Logistical Challenges: Importing LCD displays can introduce risks, including damage during shipping. It’s essential for buyers to work with suppliers who have robust packaging and shipping practices.
- Regulatory Compliance: Different countries have varying regulations that affect product quality. Buyers should ensure their suppliers are compliant with both local and international regulations.
By being aware of these factors, B2B buyers can make more informed decisions when selecting LCD display suppliers, ultimately leading to better product quality and reliability.
Practical Sourcing Guide: A Step-by-Step Checklist for ‘lcd display supplier’
Introduction
Sourcing LCD displays for your business requires a structured approach to ensure you select the right supplier that meets your needs. This checklist will guide international B2B buyers, especially from Africa, South America, the Middle East, and Europe, through the essential steps in evaluating and procuring LCD displays. By following these steps, you can minimize risks and ensure a successful procurement process.
Step 1: Define Your Technical Specifications
Clearly outline the technical requirements for the LCD displays you need. This includes screen size, resolution, backlight type (TFT, OLED, etc.), and any specific features such as touch capability or durability standards.
– Why It’s Important: Accurate specifications help in filtering suppliers who can meet your needs and reduce misunderstandings during the procurement process.
Step 2: Research Potential Suppliers
Conduct thorough research to identify potential suppliers in the LCD display market. Look for manufacturers with a proven track record in quality and reliability.
– What to Look For: Supplier ratings, reviews, and industry reputation. Pay attention to their experience with clients from your region to ensure they understand local requirements.
Step 3: ✅ Verify Supplier Certifications
Ensure that the suppliers you are considering have relevant certifications, such as ISO 9001 for quality management or RoHS compliance for environmental standards.
– Why It Matters: Certifications indicate that a supplier adheres to international standards, which can mitigate risks associated with product quality and compliance.
Step 4: Evaluate Production Capabilities
Assess the supplier’s production capacity to ensure they can meet your volume requirements within your timeline. This includes their manufacturing technology and labor resources.
– Key Considerations: Ask about their lead times, scalability of production, and whether they can handle custom orders or modifications to existing products.
Step 5: Request Product Samples
Before finalizing your order, request samples of the LCD displays to evaluate their quality firsthand. This step is vital for assessing color accuracy, contrast, and overall performance.
– What to Observe: Look for defects, color consistency, and responsiveness, particularly if touch functionality is involved.
Step 6: Discuss Payment Terms and Conditions
Clarify payment terms and conditions before placing an order. Discuss options such as deposit amounts, payment methods, and credit terms to avoid misunderstandings.
– Importance of Transparency: Clear payment terms can prevent potential disputes and ensure a smoother transaction process.
Step 7: Establish Communication Protocols
Set up clear communication channels with your supplier for ongoing support and updates. Regular communication can help address issues promptly and enhance collaboration.
– Best Practices: Utilize platforms that both parties are comfortable with, and agree on regular check-ins to discuss production status and any concerns.
By following this practical sourcing guide, you will be better equipped to navigate the complexities of selecting an LCD display supplier that aligns with your business needs and standards.
Comprehensive Cost and Pricing Analysis for lcd display supplier Sourcing
What Are the Key Cost Components in LCD Display Supplier Pricing?
Understanding the cost structure of LCD displays is crucial for international B2B buyers. The primary components include:
-
Materials: The cost of raw materials such as liquid crystals, glass substrates, and electronic components significantly impacts overall pricing. Prices can fluctuate based on global supply chain dynamics and availability of these materials.
-
Labor: Labor costs vary by region. Countries with lower labor costs might offer more competitive pricing, but this can affect quality. Understanding the labor rates in countries like China, South Korea, and Taiwan, which dominate LCD manufacturing, is essential.
-
Manufacturing Overhead: This encompasses costs related to factory operations, including utilities, maintenance, and administrative expenses. These costs can vary widely depending on the operational efficiency of the supplier.
-
Tooling: Custom tooling for specific display designs can add significant upfront costs. Buyers should consider whether the supplier has the capability to handle unique designs without incurring excessive tooling fees.
-
Quality Control (QC): Rigorous QC processes ensure the reliability and performance of displays, but they also contribute to costs. Buyers should inquire about the QC measures implemented by suppliers to ensure product consistency.
-
Logistics: Shipping costs can vary based on the Incoterms used and the destination. International buyers should factor in customs duties, taxes, and shipping fees when evaluating total costs.
-
Margin: Supplier profit margins can vary based on their market position and competition. Understanding typical margins in the industry can help buyers assess the fairness of quoted prices.
What Influences Pricing in LCD Display Sourcing?
Several factors can influence the pricing of LCD displays:
-
Volume/MOQ: Higher order volumes often lead to lower per-unit costs due to economies of scale. Buyers should negotiate minimum order quantities (MOQ) to achieve better pricing.
-
Specifications and Customization: Custom specifications or unique features can increase production costs. Buyers should balance their need for customization with budget constraints.
-
Materials and Quality Certifications: The choice of materials affects both cost and quality. Displays that meet international quality certifications may command higher prices but offer better reliability.
-
Supplier Factors: The reputation and reliability of the supplier can influence pricing. Established suppliers might charge more due to their proven track record and quality assurance.
-
Incoterms: The chosen Incoterms can significantly affect total costs. For instance, DDP (Delivered Duty Paid) may be more expensive upfront but could simplify logistics for the buyer.
How Can B2B Buyers Optimize Costs When Sourcing LCD Displays?
-
Negotiation Strategies: Engage in transparent discussions with suppliers about pricing structures. Leverage your purchasing power and establish long-term relationships to negotiate better terms.
-
Focus on Total Cost of Ownership (TCO): Evaluate not just the purchase price but the total cost of ownership, including maintenance and potential failure costs over the product’s lifespan. This approach ensures that cheaper upfront costs do not lead to higher long-term expenses.
-
Be Aware of Pricing Nuances: Buyers from regions such as Africa, South America, the Middle East, and Europe should be conscious of currency fluctuations and international trade policies that could affect pricing. Understanding local market conditions can provide leverage in negotiations.
-
Market Research: Conduct thorough market research to compare prices and offerings from multiple suppliers. This will help you identify competitive pricing and understand the prevailing market rates.
Disclaimer on Indicative Prices
Prices for LCD displays can vary widely based on numerous factors, including market conditions, supplier capabilities, and buyer requirements. The information provided herein serves as a guideline for B2B buyers and should be validated with suppliers to ensure accuracy and relevance to specific purchasing scenarios.
Alternatives Analysis: Comparing lcd display supplier With Other Solutions
Exploring Alternative Solutions to LCD Display Suppliers
When considering the procurement of display technologies, international B2B buyers face a multitude of options beyond traditional LCD displays. This section delves into viable alternatives, including OLED and TFT technologies, to provide a comprehensive understanding of their comparative advantages and potential drawbacks.
Comparison Table of Display Technologies
Comparison Aspect | LCD Display Supplier | OLED (Organic Light Emitting Diode) | TFT (Thin Film Transistor) |
---|---|---|---|
Performance | Good color accuracy, moderate response times | Superior contrast, vibrant colors, faster response | High resolution, good color reproduction |
Cost | Generally lower cost | Higher initial investment, but decreasing | Moderate cost, varies with specifications |
Ease of Implementation | Widely available, easy integration | Requires specific conditions for optimal performance | Simple integration in many devices |
Maintenance | Low maintenance, long lifespan | Moderate, susceptible to burn-in | Low, reliable technology |
Best Use Case | General applications, budget-conscious projects | High-end displays, professional use | Mobile devices, gaming, and high-performance applications |
Detailed Breakdown of Alternatives
What Are the Advantages and Disadvantages of OLED Technology?
OLED technology stands out for its ability to produce deep blacks and vibrant colors due to its self-emissive nature. Each pixel emits its own light, eliminating the need for a backlight, which leads to thinner displays. However, OLED screens are generally more expensive than LCDs, which can be a barrier for budget-conscious buyers. Additionally, while OLED displays offer excellent viewing angles and fast response times, they have a shorter lifespan and can suffer from image retention, making them less suitable for static images over extended periods.
Why Should Buyers Consider TFT Displays?
TFT technology, a variant of LCD, utilizes thin-film transistors to enhance display performance. This technology offers high resolution and good color reproduction, making it ideal for mobile devices and gaming applications. TFT displays are widely integrated into various devices due to their reliability and relatively lower costs. However, they may not match the color vibrancy and contrast levels of OLED displays. Buyers should weigh the performance benefits against the specific requirements of their applications.
How Can B2B Buyers Choose the Right Display Solution?
When selecting a display technology, B2B buyers must consider their specific use cases, budget constraints, and performance needs. For general applications where cost is a primary concern, LCD remains a strong choice. Conversely, if high-quality visuals and superior performance are crucial, OLED could be the better investment despite its higher initial cost. TFT displays offer a reliable middle ground, particularly for mobile and gaming industries. Ultimately, understanding the unique characteristics of each technology will empower buyers to make informed decisions that align with their operational goals and market demands.
Essential Technical Properties and Trade Terminology for lcd display supplier
What Are the Essential Technical Properties of LCD Displays for B2B Buyers?
When sourcing LCD displays, understanding key technical properties is crucial for making informed purchasing decisions. Below are critical specifications that B2B buyers should consider:
1. Resolution
Resolution refers to the number of pixels that make up the display, typically expressed as width x height (e.g., 1920×1080). Higher resolutions provide clearer images and sharper text, which is essential for applications requiring detailed visuals, such as medical imaging or design work. For international buyers, particularly in Europe and the Middle East, higher resolution displays may be expected to meet industry standards.
2. Brightness
Brightness is measured in nits and indicates how well the display can be seen in different lighting conditions. A higher brightness rating is particularly important for outdoor applications or environments with strong ambient light. For buyers from Africa and South America, where sunlight can be intense, selecting displays with higher brightness can enhance visibility and user experience.
3. Color Gamut
The color gamut indicates the range of colors a display can reproduce. A wider color gamut allows for more vibrant and accurate color representation, which is vital for industries like gaming and graphic design. Buyers should assess if the LCD supplier can provide displays that meet specific color standards (e.g., sRGB, Adobe RGB) relevant to their applications.
4. Response Time
Response time measures how quickly a pixel can change from one color to another, typically expressed in milliseconds (ms). A lower response time is crucial for applications involving fast-moving images, such as gaming or video playback. International buyers should inquire about response times to ensure that the displays can handle their specific use cases without blurring or ghosting.
5. Viewing Angle
Viewing angle refers to the maximum angle at which the display can be viewed without significant degradation in image quality. Displays with wide viewing angles (e.g., 178 degrees) are essential for applications where multiple viewers might be observing the screen simultaneously, such as in conference rooms or public displays. Understanding this property helps buyers from various regions ensure optimal performance in different settings.
What Common Trade Terms Should B2B Buyers Know When Sourcing LCD Displays?
Navigating the trade landscape involves familiarizing oneself with key industry terminology. Here are some essential terms that B2B buyers should understand:
1. OEM (Original Equipment Manufacturer)
OEM refers to a company that produces parts or equipment that may be marketed by another manufacturer. In the context of LCD displays, buyers should determine whether the supplier offers OEM services, which can provide customized solutions tailored to specific needs.
2. MOQ (Minimum Order Quantity)
MOQ is the smallest number of units that a supplier is willing to sell. Understanding the MOQ is vital for buyers to ensure they can meet their procurement needs without excessive inventory. This is particularly relevant for international buyers who may have different market demands.
3. RFQ (Request for Quotation)
An RFQ is a document that buyers send to suppliers to request pricing and terms for specific products. This term is essential for initiating the procurement process and comparing supplier offers. B2B buyers should prepare detailed RFQs to receive accurate and competitive quotes.
4. Incoterms (International Commercial Terms)
Incoterms define the responsibilities of buyers and sellers in international trade, including who is responsible for shipping, insurance, and tariffs. Familiarity with these terms is crucial for buyers from Africa, South America, and Europe to avoid misunderstandings and ensure smooth transactions.
5. Lead Time
Lead time refers to the time taken from placing an order to delivery. Understanding lead times helps buyers plan their inventory and production schedules effectively. Buyers should communicate their timeline requirements clearly to suppliers to avoid delays.
By grasping these essential technical properties and trade terms, international B2B buyers can streamline their procurement processes, make informed decisions, and establish successful partnerships with LCD display suppliers.
Navigating Market Dynamics and Sourcing Trends in the lcd display supplier Sector
What Are the Current Market Dynamics in the LCD Display Supplier Sector?
The LCD display supplier sector is experiencing significant shifts driven by advancements in technology and changing consumer preferences. Globally, the demand for high-quality displays continues to rise, spurred by the growth of sectors like consumer electronics, automotive, and healthcare. For international B2B buyers, particularly from regions such as Africa, South America, the Middle East, and Europe (notably Poland and Germany), understanding these dynamics is crucial for effective sourcing.
Emerging trends include the increasing integration of LCD technology with IoT and AI, enhancing functionality and user experience. The transition from traditional LCD to OLED displays also presents both challenges and opportunities. Buyers should consider suppliers that invest in R&D to stay competitive and offer innovative solutions. Furthermore, the supply chain landscape is becoming more complex, with a shift towards localized sourcing to mitigate risks associated with global disruptions.
For B2B buyers, leveraging data analytics to assess supplier performance and market trends can lead to more informed purchasing decisions. As sustainability becomes a priority, aligning with suppliers who prioritize eco-friendly practices and materials can enhance brand reputation and meet regulatory requirements.
How Is Sustainability Influencing Sourcing Decisions in the LCD Display Sector?
Sustainability and ethical sourcing are becoming paramount considerations for B2B buyers in the LCD display sector. The environmental impact of manufacturing processes, particularly concerning waste and energy consumption, is under scrutiny. Companies are increasingly held accountable for their supply chain practices, prompting buyers to seek suppliers that demonstrate a commitment to sustainable operations.
Incorporating ‘green’ certifications and materials into the procurement process is essential. Buyers should prioritize suppliers who utilize recyclable materials and adhere to international sustainability standards, such as ISO 14001. This not only reduces the ecological footprint but also enhances the overall brand image, appealing to environmentally-conscious consumers.
Moreover, ethical sourcing involves ensuring fair labor practices and safe working conditions throughout the supply chain. Buyers should conduct thorough due diligence to verify that their suppliers adhere to ethical labor standards. Building partnerships with suppliers committed to sustainability can lead to long-term benefits, including improved product quality and customer loyalty.
What Has Been the Evolution of the LCD Display Supplier Sector?
The evolution of the LCD display supplier sector has been marked by rapid technological advancements and changing market demands. Initially, CRT (Cathode Ray Tube) technology dominated the display market until the introduction of LCDs in the late 20th century, which offered a more compact, energy-efficient alternative. As LCD technology improved, features like higher resolution, better color accuracy, and faster response times became standard.
The shift towards mobile and portable devices further accelerated the demand for LCD displays, leading to innovations such as TFT (Thin Film Transistor) technology, which enhanced display quality and performance. Today, LCDs face competition from OLED technology, which offers superior contrast and color reproduction. This ongoing evolution underscores the importance for B2B buyers to stay informed about technological trends and supplier capabilities to ensure competitive sourcing strategies.
Frequently Asked Questions (FAQs) for B2B Buyers of lcd display supplier
-
How do I choose the right LCD display supplier for my business needs?
Choosing the right LCD display supplier involves evaluating several factors. Start by assessing the supplier’s experience and reputation in the industry. Look for testimonials or case studies from previous clients, especially those in your region (Africa, South America, the Middle East, or Europe). Ensure they offer technical support and have a clear understanding of your specific requirements, such as display size, resolution, and intended application. Additionally, inquire about their manufacturing capabilities, lead times, and quality assurance processes to ensure they can meet your demands. -
What are the common customization options available when sourcing LCD displays?
Most LCD display suppliers offer a variety of customization options tailored to your needs. Common customizations include screen size, resolution, aspect ratio, brightness levels, and touch capabilities. You may also request specific backlight technologies or housing designs to fit your product’s aesthetic. Discussing your requirements upfront can help the supplier provide you with the most suitable options, as well as associated costs and timelines for custom orders. -
What is the typical minimum order quantity (MOQ) for LCD displays?
Minimum order quantities (MOQ) for LCD displays can vary significantly depending on the supplier and the complexity of the product. Generally, MOQs can range from a few hundred units to several thousand. For smaller businesses or startups, it’s advisable to negotiate with suppliers who are open to lower MOQs, especially for custom designs. This flexibility can help you manage inventory and reduce upfront costs while still meeting your display needs. -
What payment terms should I expect when sourcing LCD displays internationally?
Payment terms can vary widely among suppliers, but it’s common to encounter options such as upfront payments, letters of credit, or payment on delivery. Many suppliers may require a deposit (often 30-50%) before production begins, with the balance due upon shipment. For international transactions, consider discussing secure payment methods that protect both parties, such as escrow services. Always ensure you have a clear understanding of the payment terms before finalizing any agreements. -
How can I verify the quality of LCD displays from a potential supplier?
To verify the quality of LCD displays, request samples before placing a large order. Testing samples for performance, durability, and color accuracy is crucial. Additionally, inquire about the supplier’s quality assurance processes, including certifications like ISO 9001 or compliance with relevant industry standards. It’s also beneficial to read customer reviews and seek references from other businesses that have sourced displays from the supplier to gauge their reliability and product quality. -
What logistics considerations should I keep in mind when importing LCD displays?
Logistics plays a vital role in the successful importation of LCD displays. Consider shipping methods, transit times, and associated costs, including duties and taxes. Work with suppliers who have experience in international shipping to ensure compliance with customs regulations. Additionally, establish a clear communication plan regarding tracking shipments and managing potential delays. Choosing a reliable freight forwarder can also help streamline the process and mitigate risks. -
How do I handle warranty and after-sales support for LCD displays?
When sourcing LCD displays, it’s essential to clarify warranty terms and after-sales support policies upfront. Most suppliers offer warranties that cover defects in materials or workmanship, typically ranging from one to three years. Ensure you understand the process for claiming warranty repairs or replacements. Additionally, inquire about the availability of technical support and resources for troubleshooting issues that may arise after purchase, as ongoing support can significantly impact your business operations. -
What are the key trends in LCD display technology that I should be aware of?
Staying informed about key trends in LCD display technology can enhance your purchasing decisions. Current trends include advancements in energy efficiency, higher resolutions (such as 4K and beyond), and the integration of touch capabilities. Additionally, developments in flexible and curved displays are becoming increasingly popular for various applications. Understanding these trends can help you choose displays that not only meet your current needs but also align with future market demands.
Important Disclaimer & Terms of Use
⚠️ Important Disclaimer
The information provided in this guide, including content regarding manufacturers, technical specifications, and market analysis, is for informational and educational purposes only. It does not constitute professional procurement advice, financial advice, or legal advice.
While we have made every effort to ensure the accuracy and timeliness of the information, we are not responsible for any errors, omissions, or outdated information. Market conditions, company details, and technical standards are subject to change.
B2B buyers must conduct their own independent and thorough due diligence before making any purchasing decisions. This includes contacting suppliers directly, verifying certifications, requesting samples, and seeking professional consultation. The risk of relying on any information in this guide is borne solely by the reader.
Strategic Sourcing Conclusion and Outlook for lcd display supplier
Why is Strategic Sourcing Essential for LCD Display Suppliers?
In the ever-evolving landscape of LCD display technology, strategic sourcing emerges as a pivotal element for international B2B buyers. By leveraging strong supplier relationships and fostering a comprehensive understanding of market dynamics, businesses can optimize their procurement processes and reduce costs. This approach enables buyers to access advanced technologies, such as TFT and OLED, ensuring that they remain competitive and meet the diverse needs of their end-users.
What Key Takeaways Should Buyers Consider?
B2B buyers, particularly from Africa, South America, the Middle East, and Europe, should prioritize suppliers that offer not only quality products but also robust after-sales support and innovative solutions. It is crucial to evaluate suppliers based on their manufacturing capabilities, sustainability practices, and adaptability to market changes. Furthermore, understanding regional supply chain logistics can significantly impact lead times and cost efficiencies.
How Can Buyers Prepare for Future Trends in LCD Technology?
As the demand for high-performance displays grows, buyers must stay informed about emerging technologies and market trends. Engaging in continuous dialogue with suppliers and participating in industry forums can provide valuable insights into future innovations. By adopting a proactive sourcing strategy, businesses can position themselves to capitalize on advancements in display technology.
In conclusion, the path forward is clear: international B2B buyers should embrace strategic sourcing as a means to enhance their competitive edge in the LCD display market. By aligning with the right suppliers and remaining agile in their procurement strategies, businesses can not only meet current demands but also anticipate future opportunities.