Enhance Productivity: The Ultimate PC Table Custom Guide (2025)
Introduction: Navigating the Global Market for pc table custom
In the ever-evolving landscape of global commerce, sourcing custom PC tables presents a unique set of challenges for B2B buyers, particularly in regions like Africa, South America, the Middle East, and Europe. As businesses increasingly prioritize ergonomic and functional designs to enhance productivity, understanding the nuances of materials, design specifications, and supplier reliability becomes paramount. This guide serves as a comprehensive resource, covering everything from the various types of custom PC tables and their applications to essential supplier vetting processes and cost considerations.
International buyers will find valuable insights into selecting the right materials, including the advantages of polycarbonate (PC) for durability and aesthetics. With this guide, you will gain the knowledge necessary to make informed purchasing decisions that align with your business needs, ensuring you procure high-quality products that meet industry standards. Moreover, by addressing critical factors such as local regulations, logistics, and market trends, this guide empowers you to navigate the complexities of the global market with confidence.
Whether you are seeking to enhance your office environment or fulfill large-scale project requirements, understanding the global market for custom PC tables will equip you with the tools to achieve your business objectives effectively.
Understanding pc table custom Types and Variations
Type Name | Key Distinguishing Features | Primary B2B Applications | Brief Pros & Cons for Buyers |
---|---|---|---|
Standard PC Tables | Made from polycarbonate sheets; lightweight and durable. | Office furniture, educational institutions | Pros: Lightweight, durable, and impact-resistant. Cons: May be prone to scratches without protective coatings. |
High-Temperature PC Tables | Designed to withstand elevated temperatures; reinforced with additives. | Laboratories, industrial settings | Pros: Excellent heat resistance. Cons: Higher cost due to specialized materials. |
UV-Resistant PC Tables | Coated or treated to resist UV degradation; maintains clarity over time. | Outdoor settings, exhibitions | Pros: Long-lasting clarity and appearance outdoors. Cons: UV treatments can increase manufacturing costs. |
Reinforced PC Tables | Enhanced with glass fibers or other materials for added strength. | Manufacturing, automotive sectors | Pros: Superior strength and durability. Cons: Heavier and potentially more expensive. |
Customizable PC Tables | Tailored shapes, sizes, and colors to meet specific client needs. | Retail displays, bespoke projects | Pros: Fully tailored solutions. Cons: Longer lead times and higher costs associated with customization. |
What are the characteristics of Standard PC Tables?
Standard PC tables are primarily constructed from polycarbonate sheets, which are known for their lightweight and durable properties. They are commonly used in office environments and educational institutions due to their impact resistance and ease of maintenance. When considering a purchase, B2B buyers should evaluate the table’s resistance to scratches and whether protective coatings are necessary to maintain its appearance over time.
How do High-Temperature PC Tables perform in industrial applications?
High-temperature PC tables are specifically designed to endure elevated temperatures, making them ideal for laboratory and industrial settings. These tables are reinforced with special additives that enhance their thermal stability. For B2B buyers, understanding the cost implications of these specialized materials is crucial, as they tend to be more expensive than standard options but offer significant advantages in high-heat environments.
Why are UV-Resistant PC Tables essential for outdoor use?
UV-resistant PC tables are treated or coated to withstand degradation from ultraviolet light, ensuring they maintain their clarity and color even when exposed to the sun. These tables are particularly useful in outdoor settings and exhibitions. Buyers should consider the long-term benefits of investing in UV-resistant options, despite the higher initial cost, as they lead to reduced replacement frequency and improved aesthetics.
What advantages do Reinforced PC Tables offer for demanding sectors?
Reinforced PC tables are enhanced with materials like glass fibers, providing exceptional strength and durability, making them suitable for demanding applications in manufacturing and the automotive sector. While these tables offer superior performance, B2B buyers should weigh the benefits against the potential for increased weight and cost, which may impact logistics and budget.
How can Customizable PC Tables meet unique business needs?
Customizable PC tables allow businesses to tailor the design, shape, size, and color to fit specific requirements, making them ideal for retail displays and bespoke projects. While these tables offer the flexibility to meet unique business needs, buyers should be prepared for longer lead times and potentially higher costs associated with the customization process. Understanding the trade-offs will help businesses make informed purchasing decisions.
Related Video: $13000 ULTIMATE Custom Water Cooled Desk Gaming PC Build – Time Lapse – 2080 ti i9 9980XE
Key Industrial Applications of pc table custom
Industry/Sector | Specific Application of pc table custom | Value/Benefit for the Business | Key Sourcing Considerations for this Application |
---|---|---|---|
Electronics Manufacturing | Custom housings for electronic devices | Enhanced protection and durability of components | Ensure compliance with international safety standards |
Automotive | Interior components and dashboards | Lightweight, impact-resistant materials improve safety | Look for suppliers with experience in automotive-grade materials |
Medical Devices | Equipment casings and protective barriers | Biocompatibility and strength for patient safety | Verify certifications for medical-grade materials |
Construction | Transparent barriers and safety shields | Increased visibility and safety in construction sites | Assess weather resistance and UV stability |
Consumer Products | Custom containers and packaging | Lightweight and durable solutions for better logistics | Confirm material safety and regulatory compliance |
What Are the Key Applications of PC Table Custom in Electronics Manufacturing?
In the electronics manufacturing sector, custom PC tables are used for creating housings for various electronic devices, including smartphones, tablets, and computers. These housings are crucial as they provide enhanced protection against physical impacts and environmental factors. By opting for custom solutions, businesses can ensure that their products maintain a sleek appearance while also being robust enough to withstand daily wear and tear. International buyers should prioritize suppliers who comply with safety standards to ensure product reliability in diverse markets.
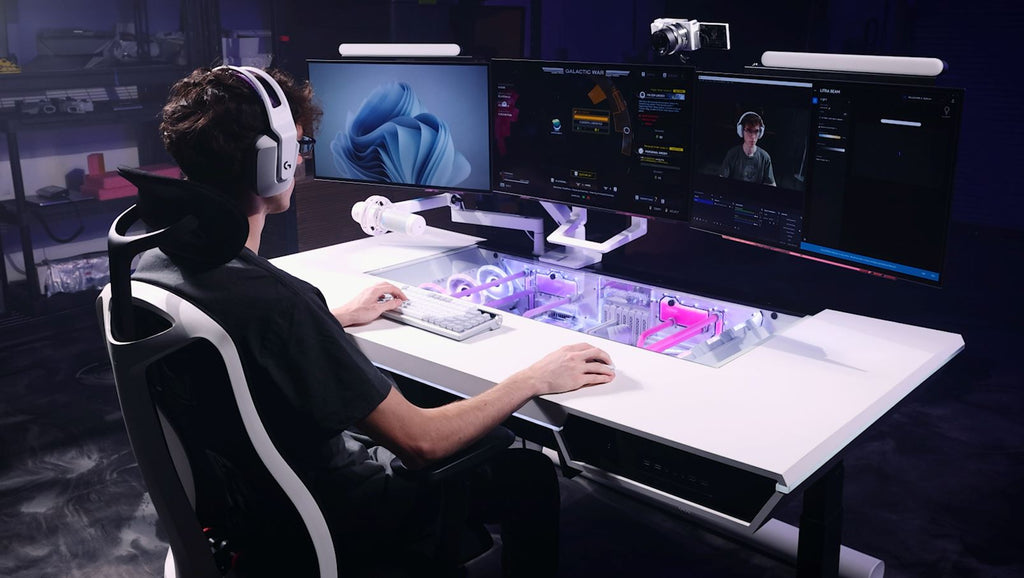
A stock image related to pc table custom.
How Is PC Table Custom Used in the Automotive Industry?
In the automotive industry, custom PC tables are often utilized for manufacturing interior components such as dashboards and trim pieces. The lightweight nature of polycarbonate helps improve fuel efficiency while maintaining high levels of impact resistance, which is essential for passenger safety. Buyers in this sector should focus on sourcing from manufacturers experienced in automotive-grade materials, ensuring that the products meet stringent industry standards and regulations.
What Role Does PC Table Custom Play in Medical Devices?
Custom PC tables find extensive application in the medical devices sector, where they are used for equipment casings and protective barriers. The biocompatibility and strength of polycarbonate materials make them ideal for products that require a high level of durability while ensuring patient safety. International buyers must verify that their suppliers have the necessary certifications for medical-grade materials to ensure compliance with health regulations in their respective markets.
How Are Custom PC Tables Utilized in Construction?
In construction, custom PC tables are employed to create transparent barriers and safety shields. These applications provide increased visibility on job sites while protecting workers from hazards. The durability and weather resistance of polycarbonate make it an excellent choice for outdoor applications. Buyers should assess the UV stability and overall performance of the materials to ensure they can withstand various environmental conditions.
Why Are Custom PC Tables Important for Consumer Products?
Custom PC tables are increasingly used in consumer products for creating containers and packaging solutions. The lightweight and durable nature of polycarbonate enhances logistics and reduces shipping costs. For international B2B buyers, it is crucial to confirm that the materials used comply with safety regulations, ensuring that the products are safe for consumer use and can withstand transportation challenges.
Related Video: Class 1 – Computer ~ USES OF A COMPUTER ~ CBSE / NCERT / CAIE
3 Common User Pain Points for ‘pc table custom’ & Their Solutions
Scenario 1: Struggling with Material Durability in Custom PC Tables
The Problem: One of the most pressing issues B2B buyers face when sourcing custom PC tables is the durability of materials used. Many businesses require tables that withstand heavy usage, especially in environments like workshops or design studios. However, some suppliers may not provide adequate information about the long-term performance of their materials, leading to unexpected wear and tear. Buyers often find themselves replacing tables sooner than anticipated, resulting in increased costs and operational disruptions.
The Solution: To combat this issue, buyers should prioritize sourcing tables made from high-quality polycarbonate (PC) materials known for their strength and impact resistance. When approaching suppliers, request detailed specifications on the material properties, including tensile strength, impact resistance, and resistance to stress-cracking. Additionally, consider implementing a rigorous testing protocol where possible, such as stress testing samples in realistic conditions before making a bulk purchase. This proactive approach will ensure that the tables can handle the demands of the intended environment, thus extending their lifespan and reducing replacement costs.
Scenario 2: Navigating Customization Challenges for PC Tables
The Problem: B2B buyers often encounter difficulties in specifying the exact dimensions and features they need for custom PC tables. Miscommunications with suppliers can lead to tables that do not fit the intended space or lack essential functionalities, such as integrated cable management or ergonomic designs. This not only results in wasted resources but can also hinder productivity if the tables are not user-friendly.
The Solution: To effectively navigate customization challenges, buyers should develop a comprehensive design brief that outlines all necessary specifications, including dimensions, weight capacity, and additional features. Visual aids, such as sketches or CAD drawings, can significantly enhance communication with suppliers. Moreover, engaging in collaborative discussions during the design phase can help clarify expectations and prevent misunderstandings. Finally, consider requesting prototypes or mock-ups before finalizing the order, allowing for adjustments that ensure the final product meets all operational requirements.
Scenario 3: Ensuring Compliance with Safety and Environmental Regulations
The Problem: International B2B buyers, particularly in regions like Europe and the Middle East, must navigate a complex landscape of safety and environmental regulations when sourcing custom PC tables. Failure to comply with these regulations can result in legal repercussions and damage to a company’s reputation. Buyers may struggle to find suppliers who provide materials that meet these stringent standards, particularly regarding chemical safety and sustainability.
The Solution: To ensure compliance, buyers should conduct thorough due diligence on potential suppliers, verifying that they adhere to relevant standards such as REACH (Registration, Evaluation, Authorization, and Restriction of Chemicals) in Europe or similar local regulations. Request certifications and material safety data sheets (MSDS) that outline the chemical properties of the PC used in the tables. Additionally, consider suppliers who have a proven track record of sustainability, as this not only helps with compliance but also enhances brand reputation. Establishing a checklist of regulatory requirements before initiating the sourcing process can streamline compliance efforts and ensure that all materials used are safe and environmentally friendly.
Strategic Material Selection Guide for pc table custom
What Are the Key Materials for Custom PC Tables?
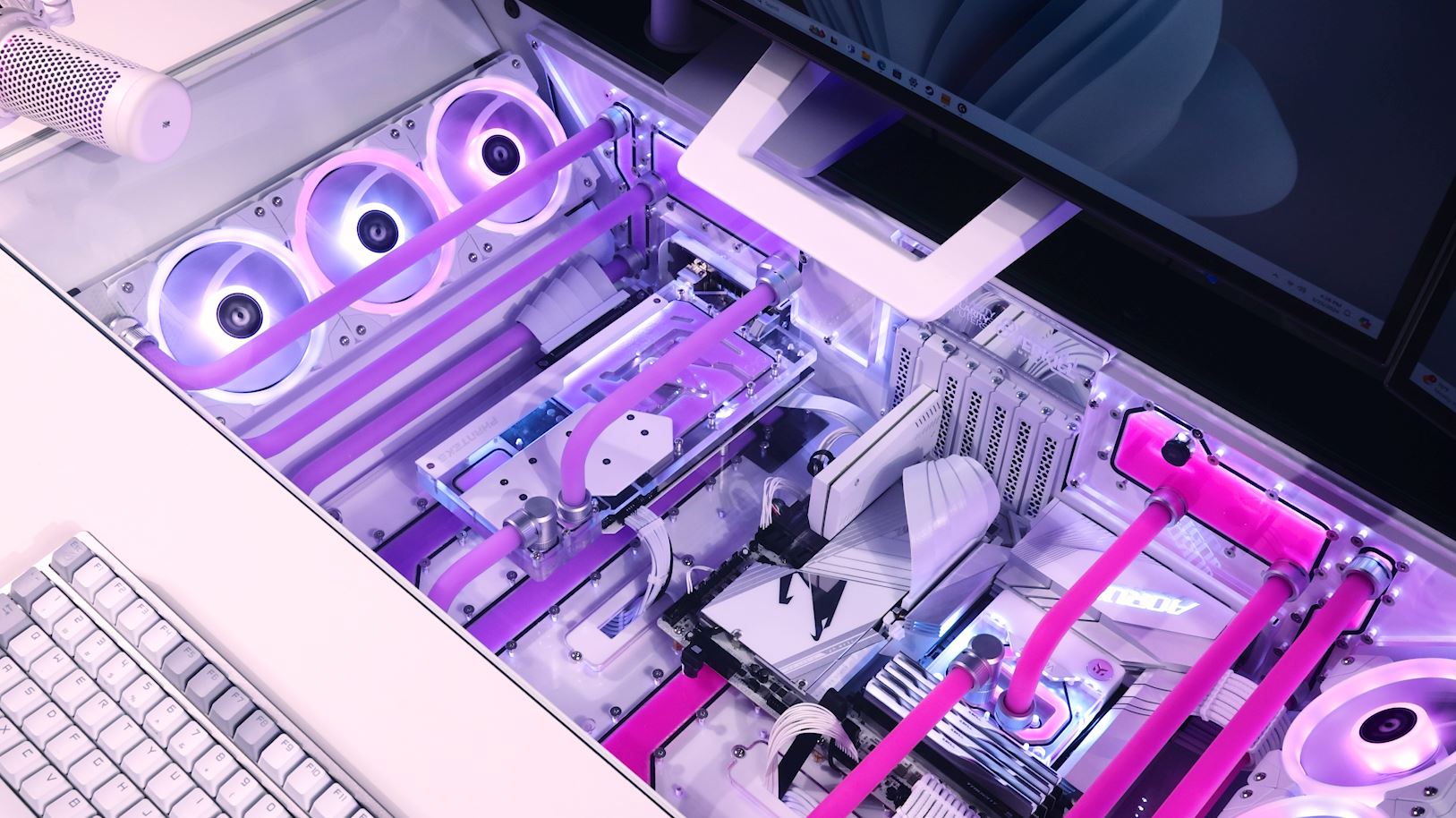
A stock image related to pc table custom.
When selecting materials for custom PC tables, international B2B buyers must consider several factors, including performance characteristics, manufacturing complexity, and compliance with regional standards. Below are analyses of four common materials used in the production of custom PC tables.
How Does Polycarbonate (PC) Perform in Custom PC Tables?
Key Properties: Polycarbonate is a thermoplastic known for its excellent impact resistance, high transparency, and good thermal stability, with a temperature rating up to 120°C. It is also resistant to UV radiation, making it suitable for indoor and outdoor applications.
Pros & Cons: The advantages of PC include its durability, lightweight nature, and resistance to shattering. However, it has limitations in terms of scratch resistance and fatigue, which can lead to wear over time. The manufacturing process can be complex due to its high melt viscosity, requiring careful temperature control during processing.
Impact on Application: PC is particularly suitable for applications requiring transparency and strength, such as tabletops that need to withstand heavy use. However, it is sensitive to certain chemicals and may require protective coatings in environments where it is exposed to harsh substances.
Considerations for International Buyers: Buyers in regions like Europe and the Middle East should ensure compliance with safety standards such as ASTM and DIN. In South Africa, specific regulations may apply regarding the use of materials containing BPA, which is present in some PC formulations.
What Are the Advantages of Using Acrylonitrile Butadiene Styrene (ABS) for PC Tables?
Key Properties: ABS is a thermoplastic known for its good impact resistance and toughness, with a temperature rating of around 80°C. It is also resistant to many chemicals, making it a versatile choice for various applications.
Pros & Cons: ABS is relatively easy to process and can be molded into complex shapes, making it a cost-effective option for custom designs. However, it can be less durable than PC in high-temperature environments and may not offer the same level of aesthetic appeal.
Impact on Application: ABS is suitable for applications where durability and cost-effectiveness are prioritized. However, it may not be ideal for environments exposed to high heat or direct sunlight, as it can warp or discolor over time.
Considerations for International Buyers: Buyers should check for compliance with local regulations regarding plastic materials. In Europe, for example, ABS must meet REACH regulations, while South American buyers should consider local environmental standards.
How Does Medium-Density Fiberboard (MDF) Compare for Custom PC Tables?
Key Properties: MDF is an engineered wood product made from wood fibers, wax, and resin, offering a smooth surface and excellent machinability. It has a moderate temperature resistance, typically around 50-70°C.
Pros & Cons: The main advantage of MDF is its cost-effectiveness and ease of finishing, allowing for a variety of surface treatments. However, it is less durable than plastic materials and can be susceptible to moisture damage, which limits its use in humid environments.
Impact on Application: MDF is ideal for applications where aesthetics are important, such as decorative tabletops. However, it may not be suitable for environments where water exposure is a concern.
Considerations for International Buyers: Buyers should be aware of the formaldehyde emissions from MDF and ensure compliance with local emissions standards, particularly in Europe, where stricter regulations apply.
What Role Does Steel Play in Custom PC Table Construction?
Key Properties: Steel is a robust material known for its high strength and durability, with excellent temperature resistance. It can withstand high pressures and is resistant to corrosion when treated properly.
Pros & Cons: The primary advantage of steel is its structural integrity and longevity. However, it can be heavy and may require additional treatments to prevent rust, especially in humid environments.
Impact on Application: Steel is often used for the frame of custom PC tables, providing stability and support. It is suitable for high-load applications but may not be as aesthetically pleasing as other materials unless finished properly.
Considerations for International Buyers: Buyers should ensure that the steel used complies with international standards for corrosion resistance, particularly in coastal regions where salt exposure can accelerate rusting.
Summary Table of Material Selection for Custom PC Tables
Material | Typical Use Case for pc table custom | Key Advantage | Key Disadvantage/Limitation | Relative Cost (Low/Med/High) |
---|---|---|---|---|
Polycarbonate (PC) | Transparent tabletops requiring high impact resistance | Excellent durability and transparency | Scratch sensitivity and fatigue issues | Medium |
Acrylonitrile Butadiene Styrene (ABS) | Cost-effective custom designs | Easy to process and mold | Less durable in high-temperature environments | Low |
Medium-Density Fiberboard (MDF) | Decorative tabletops with smooth finishes | Cost-effective and versatile | Susceptible to moisture damage | Low |
Steel | Structural frame for high-load applications | High strength and durability | Heavy and requires corrosion treatment | Medium |
This guide provides a comprehensive overview of the materials suitable for custom PC tables, helping international B2B buyers make informed decisions based on their specific needs and regional standards.
In-depth Look: Manufacturing Processes and Quality Assurance for pc table custom
What Are the Key Stages in the Manufacturing Process for Custom PC Tables?
The manufacturing process for custom PC tables typically involves several critical stages: material preparation, forming, assembly, and finishing. Each stage is crucial for ensuring the final product meets both functional and aesthetic requirements.
Material Preparation: What Materials Are Used and How Are They Processed?
The primary material used for PC tables is polycarbonate (PC), known for its durability and transparency. The preparation stage involves sourcing high-quality PC resin, which can be in the form of granules or sheets.
-
Sourcing: Select suppliers who provide high-grade PC materials compliant with international standards. This is particularly important for B2B buyers in regions like Europe, where material regulations can be stringent.
-
Drying: PC materials often require drying to remove moisture before processing. This is crucial because excess moisture can cause defects during the forming process.
-
Coloring and Additives: Depending on the design specifications, manufacturers may add colorants or UV stabilizers during this stage to enhance the appearance and durability of the final product.
How Is the Forming Process Conducted for Custom PC Tables?
The forming process converts the prepared PC materials into shapes suitable for PC tables. Common techniques include:
-
Injection Molding: This method involves heating the PC until it is molten, then injecting it into molds that shape the table components. It is ideal for producing complex shapes with high precision.
-
Thermoforming: For larger panels, thermoforming is often used. Sheets of PC are heated until pliable and then formed over molds. This method is particularly useful for creating curved or custom designs.
-
CNC Machining: After initial forming, CNC (Computer Numerical Control) machining can refine edges and create precise cutouts for components such as cable management systems.
What Are the Assembly Techniques for Custom PC Tables?
Once the individual components are formed, the next step is assembly, which involves joining parts together to create the final product.
-
Mechanical Fastening: This includes screws, bolts, and brackets. This method is preferred for its ease of disassembly, allowing for repairs or modifications.
-
Adhesive Bonding: In some designs, adhesives may be used to create a seamless look. High-strength adhesives specifically designed for PC can provide a durable bond.
-
Quality Inspection During Assembly: Implementing quality checks at this stage ensures that components fit together correctly and adhere to design specifications.
How Is the Finishing Process Performed for Custom PC Tables?
The finishing stage enhances the table’s aesthetic appeal and functionality. This may include:
-
Surface Treatment: Techniques like polishing or coating can improve the table’s visual appeal and scratch resistance.
-
Assembly of Additional Features: Features such as cable management trays, adjustable legs, or integrated lighting systems can be added during this phase.
-
Final Quality Control Checks: Before the final product leaves the manufacturing facility, a comprehensive inspection ensures that all components meet quality standards.
What Are the Quality Assurance Standards Relevant to Custom PC Table Manufacturing?
Quality assurance is vital in the manufacturing process to ensure that products are safe, reliable, and meet customer expectations. Various international standards apply, notably ISO 9001, which focuses on quality management systems.
Which International Standards Should B2B Buyers Be Aware Of?
-
ISO 9001: This standard outlines requirements for a quality management system and is applicable to any organization, regardless of size or industry. Compliance indicates a commitment to quality and continuous improvement.
-
CE Marking: For buyers in Europe, CE marking signifies compliance with health, safety, and environmental protection standards. It is essential for products intended for the European market.
-
API Standards: For buyers in specific industries like oil and gas, API (American Petroleum Institute) standards may apply, especially for components that may interact with hazardous materials.
How Are Quality Control Checkpoints Implemented in Custom PC Table Manufacturing?
Quality control (QC) is implemented at multiple checkpoints throughout the manufacturing process to identify and rectify issues early.
-
Incoming Quality Control (IQC): This involves inspecting raw materials upon arrival to ensure they meet specified standards before production begins.
-
In-Process Quality Control (IPQC): During manufacturing, continuous monitoring ensures that processes adhere to predetermined specifications. This can involve regular checks of temperature, pressure, and material dimensions.
-
Final Quality Control (FQC): After assembly, a thorough inspection ensures that the final product meets all quality standards and specifications before shipping.
What Testing Methods Are Commonly Used for Custom PC Tables?
To verify quality, various testing methods are employed, including:
-
Impact Testing: To assess the durability of the PC material against impacts, ensuring it meets safety standards.
-
Thermal Testing: Evaluating the material’s performance under high temperatures to prevent deformation or failure.
-
UV Resistance Testing: Since PC can degrade under UV exposure, this test ensures longevity when used in environments exposed to sunlight.
How Can B2B Buyers Verify Supplier Quality Control?
B2B buyers need to ensure that their suppliers maintain high-quality standards. Here are actionable steps to verify supplier quality control:
-
Conduct Audits: Regular audits of suppliers can provide insights into their manufacturing processes, quality control systems, and compliance with standards.
-
Request Quality Reports: Suppliers should provide documentation of their quality control processes, including test results and compliance with international standards.
-
Third-Party Inspections: Engaging third-party inspection services can provide an unbiased assessment of the manufacturing process and product quality.
What Are the Nuances of QC and Certification for International B2B Buyers?
For international buyers, particularly from diverse regions like Africa, South America, the Middle East, and Europe, understanding the nuances of QC and certification is vital.
-
Regional Standards: Be aware of specific regional standards that may differ from international norms. For instance, EU regulations may impose stricter requirements than those in South America.
-
Cultural and Business Practices: Understand that business practices and quality expectations may vary by region. Building relationships and clear communication with suppliers can enhance mutual understanding of quality standards.
-
Documentation and Traceability: Ensure that suppliers maintain thorough documentation of their quality control processes and can trace materials back to their sources, which is crucial for accountability and safety.
By following these guidelines, international B2B buyers can confidently navigate the complexities of manufacturing processes and quality assurance for custom PC tables, ensuring they receive high-quality products that meet their business needs.
Practical Sourcing Guide: A Step-by-Step Checklist for ‘pc table custom’
Introduction
This practical sourcing guide aims to assist international B2B buyers in procuring custom PC tables, specifically tailored to meet their unique business needs. From understanding material specifications to evaluating suppliers, this checklist will ensure that your sourcing process is efficient and effective, ultimately leading to informed purchasing decisions.
Step 1: Define Your Technical Specifications
Clearly outline the requirements for your custom PC table. This includes dimensions, weight capacity, design preferences, and any specific features such as cable management or modular components. Understanding these parameters is crucial for communicating your needs to potential suppliers and ensuring that the final product aligns with your expectations.
- Material Considerations: Specify if you need polycarbonate for its durability and transparency.
- Design Preferences: Consider ergonomic designs or aesthetics that match your branding.
Step 2: Research Potential Suppliers
Conduct thorough research to identify potential suppliers who specialize in custom PC tables. Utilize online platforms, industry directories, and trade shows to compile a list of manufacturers with a strong reputation for quality and reliability.
- Supplier Credentials: Look for certifications such as ISO 9001, which indicate a commitment to quality management.
- Market Reputation: Read reviews and testimonials from other B2B buyers to gauge supplier reliability.
Step 3: Evaluate Supplier Capabilities
Assess the manufacturing capabilities of potential suppliers. This includes understanding their production capacity, technology used, and lead times. A supplier’s ability to scale production to meet your demands is crucial, especially for larger orders.
- Technology and Innovation: Evaluate if the supplier employs advanced manufacturing techniques that could enhance product quality.
- Flexibility in Production: Determine if they can accommodate custom designs or modifications.
Step 4: Request Samples
Before placing a large order, request product samples. This allows you to evaluate the quality of the materials and craftsmanship firsthand. Testing samples can help you make an informed decision and reduce the risk of receiving subpar products.
- Quality Assessment: Check for defects, finish quality, and overall durability.
- Functionality Testing: Ensure that the table meets your specified requirements in terms of usability and design.
Step 5: Verify Supplier Certifications
Ensure that your chosen supplier holds relevant certifications. Certifications related to environmental standards, safety, and quality control are essential for maintaining compliance with international regulations.
- ISO Certification: Look for ISO 14001 (Environmental Management) or other industry-specific certifications.
- Sustainability Practices: Inquire about their sustainability practices to align with your corporate social responsibility goals.
Step 6: Negotiate Terms and Conditions
Engage in negotiations to establish favorable terms and conditions. Discuss pricing, payment terms, delivery schedules, and warranty provisions. Clear agreements will help prevent misunderstandings and ensure a smooth transaction process.
- Payment Options: Explore flexible payment terms that suit your cash flow needs.
- Warranty and Support: Clarify warranty coverage and after-sales support to safeguard your investment.
Step 7: Establish a Communication Plan
Set up a clear communication plan with your supplier. Regular updates during the manufacturing process and a point of contact for inquiries will foster a strong relationship and facilitate smoother transactions.
- Regular Check-ins: Schedule periodic updates to monitor progress and address any issues promptly.
- Feedback Loop: Create a mechanism for providing feedback on the products and services received to enhance future collaborations.
By following this checklist, international B2B buyers can streamline their sourcing process for custom PC tables, ensuring that they make informed decisions that meet their business requirements.
Comprehensive Cost and Pricing Analysis for pc table custom Sourcing
What Are the Key Cost Components for Custom PC Table Sourcing?
When sourcing custom PC tables, understanding the cost structure is crucial for international B2B buyers. The primary cost components include:
-
Materials: The main material, polycarbonate (PC), is known for its durability and optical clarity. The price of PC can fluctuate based on market demand, supply chain issues, and the specific grade required for the tables. Additional materials, such as metal frames or wood accents, will also contribute to the overall cost.
-
Labor: Labor costs vary significantly based on the manufacturing location. For example, labor costs in South America may differ greatly from those in Europe or Africa. Additionally, skilled labor for custom designs may demand higher wages.
-
Manufacturing Overhead: This includes costs related to factory operations, such as utilities, rent, and equipment maintenance. Efficient manufacturing processes can help reduce these overheads, affecting the final price.
-
Tooling: Custom designs often require specialized tooling, which can be a significant upfront cost. Buyers should consider how these costs will be amortized over production runs.
-
Quality Control (QC): Ensuring that the final product meets specifications is vital. Investment in QC can increase initial costs but can prevent costly returns or rework later.
-
Logistics: Shipping and handling costs can vary based on distance, shipping mode, and the size of the order. Understanding Incoterms is essential as they dictate the responsibilities of buyers and sellers in terms of shipping costs and risks.
-
Margin: Suppliers will add a profit margin to cover their costs and risks, which can vary widely depending on competition, market conditions, and the supplier’s positioning.
How Do Price Influencers Impact Custom PC Table Costs?
Several factors can influence the pricing of custom PC tables:
-
Volume/MOQ: Bulk orders typically benefit from lower per-unit costs due to economies of scale. Buyers should negotiate minimum order quantities (MOQs) that align with their needs without incurring excess inventory costs.
-
Specifications and Customization: Highly customized designs may incur additional costs. Buyers should clearly communicate their requirements to avoid unexpected expenses.
-
Materials Quality and Certifications: Higher quality materials and compliance with specific certifications (e.g., ISO, environmental standards) can increase costs but may be necessary for certain markets, particularly in Europe.
-
Supplier Factors: Reliability, reputation, and location of the supplier can impact pricing. Local suppliers may offer lower logistics costs but might not have the same material quality or production capabilities as international ones.
-
Incoterms: Understanding the shipping terms can significantly influence the total cost. Terms like FOB (Free on Board) or CIF (Cost, Insurance, and Freight) can affect who bears the shipping costs and risks.
What Are the Best Buyer Tips for Cost-Efficiency in Custom PC Table Sourcing?
To maximize cost-efficiency, international B2B buyers should consider the following strategies:
-
Negotiation Skills: Cultivating strong negotiation skills can lead to better prices and terms. Engage multiple suppliers to foster competition.
-
Total Cost of Ownership (TCO): Look beyond the initial price and consider long-term costs, including maintenance, durability, and potential resale value. A higher upfront cost may lead to lower TCO if the product lasts longer.
-
Pricing Nuances for International Buyers: Understanding local market conditions in Africa, South America, the Middle East, and Europe is crucial. Currency fluctuations, import duties, and taxes can affect the final pricing.
-
Supplier Relationships: Building long-term relationships with suppliers can lead to better pricing, priority service, and enhanced collaboration on future projects.
-
Market Research: Conduct thorough market research to understand pricing trends and competitor offerings, which can inform your negotiation strategy.
Disclaimer on Indicative Prices
Prices for custom PC tables can vary widely based on the aforementioned factors. Buyers are encouraged to seek multiple quotes and conduct due diligence to ensure they receive competitive pricing tailored to their specific requirements.
Alternatives Analysis: Comparing pc table custom With Other Solutions
Understanding Alternatives to pc table custom Solutions
When considering the implementation of a pc table custom solution, it is crucial to explore viable alternatives that can meet similar requirements. Each solution may offer distinct advantages and challenges, influencing the overall decision-making process for international B2B buyers. This section evaluates how pc table custom compares with two notable alternatives: laminated wood tables and metal tables.
Comparison Table
Comparison Aspect | pc table custom | Laminated Wood Tables | Metal Tables |
---|---|---|---|
Performance | High impact resistance, durability, and aesthetic appeal | Moderate durability, susceptible to scratches and water damage | High strength, excellent durability, and weather resistance |
Cost | Moderate to high, depending on customization | Generally lower, varies based on wood quality | Varies widely; can be low to high depending on material and design |
Ease of Implementation | Requires skilled labor for customization | Easier to produce and install | Moderate; may require specialized equipment for assembly |
Maintenance | Low; resistant to stains and scratches | Moderate; needs regular cleaning and protection | Low; easy to clean and maintain |
Best Use Case | Ideal for high-end office spaces and design-focused environments | Suitable for budget-conscious projects and interior applications | Excellent for industrial settings and outdoor use |
Detailed Breakdown of Alternatives
Laminated Wood Tables
Laminated wood tables are a popular choice for many businesses due to their cost-effectiveness and aesthetic versatility. They typically feature a layer of protective laminate over a wood base, providing a decent level of durability and a variety of finishes. However, they may not withstand heavy impacts or exposure to moisture as effectively as pc table custom solutions. While they are easier to produce and install, they require more frequent maintenance to prevent scratches and water damage.
Metal Tables
Metal tables represent a robust alternative, particularly favored in industrial and outdoor settings. Their high strength and resistance to environmental factors make them suitable for various applications. Although they may vary significantly in cost, depending on the type of metal used, they are generally easy to clean and maintain. However, metal tables can lack the aesthetic appeal that pc table custom solutions provide, making them less desirable for design-centric environments.
Conclusion: How to Choose the Right Solution for Your Needs
Selecting the right table solution involves assessing your specific requirements against the benefits and drawbacks of each option. For buyers in Africa, South America, the Middle East, and Europe, considerations may include budget constraints, desired aesthetics, and intended use. If durability and customization are paramount, pc table custom may be the ideal choice. Conversely, if cost and ease of maintenance are more critical, laminated wood or metal tables might be more appropriate. Careful evaluation of these factors will lead to a well-informed decision that aligns with your business objectives.
Essential Technical Properties and Trade Terminology for pc table custom
What Are the Key Technical Properties of PC for Custom Tables?
When considering the procurement of custom polycarbonate (PC) tables, understanding the material’s technical properties is crucial for making informed purchasing decisions. Here are several critical specifications that B2B buyers should be aware of:
-
Material Grade
Material grades indicate the quality and performance characteristics of PC. For instance, food-grade PC is essential for tables used in restaurants or cafes to ensure safety and compliance with health regulations. Selecting the appropriate grade can prevent issues related to toxicity and durability. -
Impact Resistance
PC is renowned for its exceptional impact resistance, making it ideal for environments where durability is paramount. This characteristic allows the tables to withstand heavy use, reducing the likelihood of breakage and the need for frequent replacements. Buyers should consider this property when assessing long-term cost-effectiveness. -
Thermal Stability
The ability of PC to maintain its integrity across a broad temperature range (from -60°C to 120°C) is vital for regions with varying climates. Tables that can withstand high temperatures without warping or degrading are particularly valuable in outdoor settings or kitchens. -
UV Resistance
UV stability is essential for tables exposed to sunlight. PC can degrade and discolor over time when subjected to UV rays. Selecting UV-stabilized PC tables is important for ensuring longevity and maintaining aesthetic appeal, especially in sunny regions like South Africa or parts of South America. -
Surface Finish Options
The surface finish of PC tables can vary from matte to glossy, impacting both aesthetics and functionality. A matte finish may reduce glare, making it suitable for office environments, while a glossy finish can enhance visual appeal in retail settings. Understanding these options allows buyers to tailor their products to their target market. -
Tolerances
Tolerances refer to the permissible limit of variation in dimensions during manufacturing. Tight tolerances are crucial for ensuring that tables fit into specific spaces or align with existing furniture. Buyers should verify the manufacturer’s capabilities to meet their dimensional requirements.
What Are Common Trade Terms in the PC Table Custom Industry?
Familiarity with industry jargon is essential for effective communication and negotiation. Here are some common terms that B2B buyers should understand:
-
OEM (Original Equipment Manufacturer)
This term refers to companies that produce parts or products that are used in another company’s end product. Buyers often engage with OEMs for custom PC tables, ensuring that the products meet specific design and quality standards. -
MOQ (Minimum Order Quantity)
MOQ denotes the smallest quantity of a product that a supplier is willing to sell. Understanding the MOQ is crucial for budget planning and inventory management, particularly for small businesses or startups looking to purchase custom tables. -
RFQ (Request for Quotation)
An RFQ is a document that buyers send to suppliers to obtain pricing for specific products. Including detailed specifications in an RFQ for custom PC tables can help suppliers provide accurate quotes, facilitating better budgeting and planning. -
Incoterms
International Commercial Terms (Incoterms) define the responsibilities of buyers and sellers in international transactions. Familiarizing oneself with these terms, such as FOB (Free on Board) and CIF (Cost, Insurance, and Freight), is essential for understanding shipping costs and risk management. -
Lead Time
Lead time refers to the period between placing an order and receiving the product. Understanding lead times for custom PC tables can help buyers plan their inventory and production schedules effectively, ensuring timely project completion. -
Certification Standards
Certification standards, such as ISO or ASTM, indicate that products meet specific quality and safety benchmarks. Buyers should inquire about these certifications to ensure that the custom tables comply with relevant industry regulations, particularly in sectors like hospitality and healthcare.
By grasping these technical properties and trade terminologies, international B2B buyers can make more informed decisions when sourcing custom PC tables, ultimately ensuring better product quality and market success.
Navigating Market Dynamics and Sourcing Trends in the pc table custom Sector
What Are the Key Trends in the Global PC Table Custom Market?
The global market for custom PC tables is witnessing significant growth, driven by increasing demand for ergonomic solutions, particularly in the context of remote work and flexible office environments. This trend is particularly pronounced in regions such as Europe and North America, where there is a strong emphasis on worker health and productivity. For international B2B buyers, particularly in Africa, South America, and the Middle East, the challenge lies in sourcing high-quality materials that meet both performance and aesthetic requirements.
Emerging technologies, such as 3D printing and modular design, are transforming how custom PC tables are manufactured. These innovations allow for greater customization, enabling businesses to offer tailored solutions that cater to specific customer needs. Additionally, the rise of e-commerce platforms facilitates easier access to suppliers across the globe, providing B2B buyers with a wider range of options.
Moreover, the sustainability movement is reshaping sourcing strategies. Buyers are increasingly prioritizing suppliers that demonstrate a commitment to environmental responsibility, which includes the use of recycled materials and energy-efficient manufacturing processes. This shift not only enhances brand reputation but also aligns with consumer preferences, especially among environmentally conscious buyers in Europe and beyond.
How Can Sustainability and Ethical Sourcing Impact the PC Table Custom Sector?
Sustainability is no longer just a buzzword; it has become a critical consideration for B2B buyers in the custom PC table market. The environmental impact of manufacturing processes, from raw material extraction to final product delivery, is under scrutiny. Buyers are increasingly aware of the carbon footprint associated with their purchases and are seeking suppliers that can demonstrate sustainable practices.
Ethical sourcing is equally important. B2B buyers should ensure that their suppliers adhere to fair labor practices and contribute positively to the communities from which they source materials. Certifications such as ISO 14001 for environmental management and FSC (Forest Stewardship Council) for wood products can serve as indicators of a supplier’s commitment to sustainability. By choosing suppliers with these certifications, buyers can mitigate risks associated with unethical practices and enhance their brand’s reputation.
Furthermore, the demand for ‘green’ materials, such as recycled plastics and sustainably sourced wood, is on the rise. These materials not only reduce environmental impact but also appeal to a growing segment of consumers who prioritize eco-friendly products. As a result, integrating sustainability into sourcing strategies can provide B2B buyers with a competitive edge in the market.
What Is the Historical Context of the PC Table Custom Market?
The custom PC table market has evolved significantly over the past few decades. Initially, furniture manufacturing was dominated by traditional materials like wood and metal, but the advent of advanced materials such as polycarbonate (PC) has revolutionized the industry. Introduced in the late 20th century, PC’s unique properties—such as high impact resistance, lightweight nature, and transparency—have made it a popular choice for modern furniture design.
As businesses began to recognize the importance of ergonomics in the workplace, the demand for customized solutions surged. This shift was further accelerated by the rise of remote work and the need for adaptable office environments. Today, the market is characterized by a blend of innovation and sustainability, with a growing emphasis on ethical sourcing and environmental impact.
By understanding these historical trends, B2B buyers can better navigate the current landscape and make informed decisions that align with both market demands and their organizational values.
Frequently Asked Questions (FAQs) for B2B Buyers of pc table custom
1. How do I choose the right supplier for custom PC tables?
Selecting the right supplier for custom PC tables involves assessing their experience, reputation, and production capabilities. Look for suppliers who specialize in engineered plastics and have a proven track record in delivering high-quality products. Request samples of their previous work and check customer reviews or testimonials. It’s also essential to verify their compliance with international quality standards, especially if you’re sourcing from regions like Africa or South America, where manufacturing practices may vary.
2. What customization options are available for PC tables?
Customization options for PC tables typically include size, shape, color, and finish. Additionally, you can request specific features such as integrated cable management, adjustable heights, or unique design elements tailored to your business needs. When discussing customization, ensure that you communicate your requirements clearly to the supplier, including any industry-specific standards or regulations that must be met.
3. What is the minimum order quantity (MOQ) for custom PC tables?
The minimum order quantity (MOQ) for custom PC tables can vary significantly among suppliers. Generally, MOQs range from 50 to 500 units, depending on the supplier’s production capacity and material costs. It’s advisable to confirm this with your chosen supplier, especially if you are a smaller business or just starting, as some suppliers may offer flexibility for first-time buyers.
4. How can I ensure quality assurance when sourcing custom PC tables?
To ensure quality assurance, request a detailed quality control plan from your supplier. This plan should outline the inspection processes, testing methods, and certifications that the tables will undergo. Additionally, consider conducting a factory audit to assess their manufacturing processes firsthand. Establishing clear communication channels for updates and potential issues during production can also help maintain quality throughout the sourcing process.
5. What are the typical payment terms for international B2B transactions?
Payment terms for international B2B transactions often include options such as a 30% upfront deposit with the balance due before shipment, or payment through letters of credit. Some suppliers may also accept payment via PayPal or bank transfer. It’s crucial to negotiate terms that protect both parties and ensure timely delivery. Always clarify any fees associated with currency exchange or international transactions to avoid unexpected costs.
6. What logistics considerations should I keep in mind when sourcing custom PC tables?
When sourcing custom PC tables, logistics considerations include shipping methods, customs clearance, and delivery timelines. Determine whether the supplier handles logistics or if you need to engage a freight forwarder. Be aware of customs regulations in your country to avoid delays. Additionally, confirm the supplier’s ability to provide tracking information for shipments, which can help you monitor delivery progress.
7. How do I handle disputes or issues with my custom PC table order?
Handling disputes requires clear communication with your supplier. Start by documenting the issue with photos and detailed descriptions. Reach out to the supplier to discuss the problem, referencing any agreements or contracts made prior. If a resolution cannot be reached, consider mediation or arbitration, as outlined in your contract. Maintaining a professional tone throughout the process can help facilitate a constructive resolution.
8. Are there specific regulations for importing PC tables into Europe or Africa?
Yes, importing PC tables into Europe or Africa may be subject to specific regulations. In Europe, products must comply with REACH (Registration, Evaluation, Authorisation, and Restriction of Chemicals) regulations, which govern the use of hazardous substances. In Africa, regulations can vary by country, so it’s vital to research local standards for materials and safety. Ensure your supplier provides documentation proving compliance with these regulations to facilitate a smooth import process.
Important Disclaimer & Terms of Use
⚠️ Important Disclaimer
The information provided in this guide, including content regarding manufacturers, technical specifications, and market analysis, is for informational and educational purposes only. It does not constitute professional procurement advice, financial advice, or legal advice.
While we have made every effort to ensure the accuracy and timeliness of the information, we are not responsible for any errors, omissions, or outdated information. Market conditions, company details, and technical standards are subject to change.
B2B buyers must conduct their own independent and thorough due diligence before making any purchasing decisions. This includes contacting suppliers directly, verifying certifications, requesting samples, and seeking professional consultation. The risk of relying on any information in this guide is borne solely by the reader.
Strategic Sourcing Conclusion and Outlook for pc table custom
In the rapidly evolving landscape of custom PC table manufacturing, strategic sourcing emerges as a pivotal element for international B2B buyers. By focusing on high-quality polycarbonate (PC) materials, businesses can leverage the unique benefits of this engineering plastic, such as exceptional impact resistance, thermal stability, and optical clarity.
How Can Strategic Sourcing Enhance Your PC Table Customization Efforts?
Engaging in strategic sourcing enables buyers to establish strong relationships with reliable suppliers, ensuring the procurement of superior materials that meet stringent industry standards. This approach not only reduces risks associated with supply chain disruptions but also fosters innovation through collaborative product development.
What Future Trends Should B2B Buyers in Africa, South America, the Middle East, and Europe Consider?
Looking ahead, the demand for sustainable materials and processes is expected to rise. Buyers should prioritize suppliers who demonstrate a commitment to eco-friendly practices and offer recyclable or bio-based alternatives to traditional PC.
In conclusion, as international B2B buyers navigate the complexities of the global market, embracing strategic sourcing will be essential for fostering resilience and driving growth. By aligning with trusted partners and focusing on innovation, your business can thrive in the dynamic world of custom PC table manufacturing. Engage with suppliers today to secure a competitive edge for tomorrow.