Discover Top Shopping Bag Suppliers: A Complete Guide (2025)
Introduction: Navigating the Global Market for shopping bag supplier
In the ever-evolving landscape of global commerce, sourcing the right shopping bag supplier is a critical challenge for international B2B buyers. Whether you are operating in the vibrant markets of Africa, the dynamic economies of South America, the fast-growing sectors in the Middle East, or the established industries of Europe, selecting a reliable supplier can significantly impact your brand’s image and operational efficiency. This guide offers a thorough exploration of the shopping bag supply chain, covering various types of bags, their applications across different sectors, and essential criteria for vetting potential suppliers.
Understanding the nuances of supplier selection is vital for businesses looking to thrive in competitive markets. This guide empowers you with actionable insights, from assessing the quality and sustainability of materials to evaluating pricing structures and shipping logistics. By delving into the costs associated with different shopping bag options and the implications of choosing local versus international suppliers, you will be equipped to make informed purchasing decisions that align with your business goals.
As you navigate the complexities of the global market, this resource serves as a roadmap, enabling you to identify the best shopping bag suppliers that meet your specific needs. With a keen focus on fostering fruitful partnerships, you will gain the confidence to enhance your supply chain strategy and ultimately drive your business forward.
Understanding shopping bag supplier Types and Variations
Type Name | Key Distinguishing Features | Primary B2B Applications | Brief Pros & Cons for Buyers |
---|---|---|---|
Eco-Friendly Suppliers | Focus on sustainable materials like jute, cotton, or recycled plastics | Retail, food service, events | Pros: Positive brand image, compliance with regulations. Cons: Often higher costs. |
Custom Printing Suppliers | Offer personalized designs and branding options | Retail, promotional events, corporate gifts | Pros: Enhances brand visibility, tailored to target audience. Cons: Longer lead times. |
Bulk Suppliers | Specialize in large quantities at competitive prices | Wholesale distribution, large retailers | Pros: Cost-effective for bulk purchases. Cons: Less flexibility in design. |
Luxury Bag Suppliers | Provide high-quality, aesthetically appealing bags | High-end retail, fashion, luxury goods | Pros: Elevates brand perception, attracts affluent customers. Cons: Higher price point. |
Disposable Bag Suppliers | Focus on single-use options, often made from plastic | Grocery stores, food delivery, events | Pros: Convenience, low cost. Cons: Environmental concerns, regulatory restrictions. |
What Are the Characteristics of Eco-Friendly Suppliers?
Eco-friendly suppliers focus on sustainable materials such as jute, organic cotton, and recycled plastics. These suppliers cater to businesses looking to enhance their sustainability initiatives, aligning with global trends toward eco-consciousness. When purchasing from eco-friendly suppliers, consider certifications such as FSC (Forest Stewardship Council) or GOTS (Global Organic Textile Standard) to ensure the authenticity of their claims. While these bags can be more expensive than traditional options, they offer significant branding benefits, especially among environmentally aware consumers.
How Do Custom Printing Suppliers Enhance Brand Visibility?
Custom printing suppliers specialize in providing shopping bags that can be tailored with specific branding elements, such as logos and unique designs. This customization allows businesses to create a memorable customer experience and effectively promote their brand. Key considerations include the minimum order quantities and production timelines, as custom designs may require longer lead times. While the initial investment may be higher, the potential for increased brand recognition and customer loyalty often justifies the cost.
Why Choose Bulk Suppliers for Cost-Effective Solutions?
Bulk suppliers focus on providing shopping bags in large quantities at competitive prices. They are ideal for businesses that require consistent supply without the need for customization. When working with bulk suppliers, it’s crucial to assess their production capabilities and delivery schedules to ensure they can meet your demand. While the cost savings can be substantial, buyers should be aware of the trade-off in terms of design flexibility and the ability to differentiate their products in a crowded market.
What Makes Luxury Bag Suppliers Stand Out?
Luxury bag suppliers create high-quality, aesthetically appealing bags designed to convey exclusivity and sophistication. These suppliers cater to high-end retail, fashion, and luxury goods markets. When considering luxury bags, businesses should evaluate the craftsmanship, material quality, and potential for customization. Although these bags come with a higher price point, they can significantly enhance brand perception and attract affluent customers, making them a worthwhile investment for businesses targeting premium segments.
What Are the Considerations for Disposable Bag Suppliers?
Disposable bag suppliers focus on providing single-use options, often made from plastic or paper. These bags are commonly used in grocery stores, food delivery services, and events. When purchasing from disposable suppliers, businesses should consider environmental regulations and the potential backlash from eco-conscious consumers. While these bags are cost-effective and convenient, the growing emphasis on sustainability may lead businesses to rethink their reliance on single-use products, especially in regions with stringent environmental policies.
Related Video: Paper Shopping Bag Making Machine price
Key Industrial Applications of shopping bag supplier
Industry/Sector | Specific Application of Shopping Bag Supplier | Value/Benefit for the Business | Key Sourcing Considerations for this Application |
---|---|---|---|
Retail | Custom-branded shopping bags for retail stores | Enhances brand visibility and customer loyalty | Material durability, customization options, and eco-friendliness |
Food and Beverage | Biodegradable bags for grocery and food packaging | Meets regulatory standards and promotes sustainability | Compliance with local regulations, bag strength, and sizing |
E-commerce | Protective packaging bags for shipping | Reduces product damage during transit | Shipping costs, bag dimensions, and weight considerations |
Events and Promotions | Promotional bags for trade shows and events | Increases brand exposure and customer engagement | Design flexibility, bulk order capabilities, and lead times |
Fashion and Apparel | Stylish reusable bags for clothing brands | Encourages repeat purchases and eco-conscious branding | Fashion trends, bag aesthetics, and material quality |
How Are Custom-Branded Shopping Bags Beneficial for Retail Businesses?
In the retail sector, shopping bags serve as a powerful marketing tool. Custom-branded bags not only facilitate product transport but also enhance brand visibility. By opting for durable and aesthetically pleasing designs, retailers can strengthen customer loyalty and encourage repeat purchases. For international buyers, sourcing bags that comply with local environmental regulations is crucial, especially in regions where sustainability is becoming a significant purchasing factor.
Why Are Biodegradable Bags Important for Food and Beverage Industries?
The food and beverage industry increasingly relies on biodegradable shopping bags to meet both regulatory standards and consumer demand for eco-friendly options. These bags help businesses avoid penalties while enhancing their sustainability profile. For buyers in Africa, South America, the Middle East, and Europe, ensuring that suppliers can provide compliant products that maintain strength and integrity during food transport is essential.
What Are the Advantages of Using Protective Packaging Bags in E-commerce?
E-commerce businesses benefit significantly from protective packaging bags that minimize product damage during shipping. These bags help maintain product quality and reduce return rates, ultimately improving customer satisfaction. International buyers should consider sourcing options that balance cost-effectiveness with durability, ensuring that bags can withstand the rigors of global shipping while adhering to regional regulations.
How Can Promotional Bags Enhance Brand Engagement at Events?
Promotional bags are vital for businesses participating in trade shows and events. They not only provide a practical use for attendees but also serve as a mobile advertisement, increasing brand exposure. When sourcing these bags, companies should focus on design flexibility and the ability to handle bulk orders efficiently, especially for international events where lead times can impact marketing strategies.
Why Are Stylish Reusable Bags Essential for Fashion and Apparel Brands?
In the fashion industry, stylish reusable bags are a key element of brand identity. They encourage eco-conscious consumer behavior and facilitate repeat purchases by offering customers a fashionable way to carry their items. Buyers should prioritize sourcing high-quality materials that align with current fashion trends, ensuring that the bags not only serve a functional purpose but also resonate with the brand’s aesthetic and values.
Related Video: How Plastic Bag Manufactured || Plastic Bag Making & Manufacturing Process
3 Common User Pain Points for ‘shopping bag supplier’ & Their Solutions
Scenario 1: Supply Chain Delays Impacting Product Availability
The Problem: B2B buyers often face challenges with supply chain delays when sourcing shopping bags from suppliers. This can be particularly problematic for businesses that rely on timely deliveries for seasonal promotions or new product launches. For instance, a retailer in Europe may order eco-friendly shopping bags to coincide with a marketing campaign, only to find that the bags are delayed, resulting in missed sales opportunities and customer dissatisfaction.
The Solution: To mitigate supply chain delays, buyers should establish strong relationships with multiple suppliers and diversify their sourcing strategies. It is advisable to request lead time estimates and set clear delivery expectations upfront. Implementing a just-in-time (JIT) inventory strategy can also help manage stock levels more effectively, ensuring that businesses are not overly reliant on a single source. Additionally, utilizing technology for supply chain tracking can provide real-time insights into the status of orders, enabling buyers to make informed decisions and communicate effectively with their teams.
Scenario 2: Inconsistent Quality Across Batches
The Problem: Another common issue faced by B2B buyers is the inconsistency in quality of shopping bags received from suppliers. For example, a company in South America may order a bulk shipment of reusable bags, but upon inspection, they find that some bags have different stitching quality or material thickness than specified. This inconsistency can damage a brand’s reputation and lead to increased return rates.
The Solution: To ensure consistent quality, buyers should implement a robust quality assurance process. This includes specifying quality standards in the purchase agreement, conducting pre-production samples, and requesting third-party inspections before shipment. Establishing clear criteria for acceptable quality and ensuring that suppliers are aware of these standards is crucial. Furthermore, fostering open communication with suppliers can help address any quality concerns early in the production process, thus avoiding issues down the line.
Scenario 3: Limited Customization Options for Brand Identity
The Problem: B2B buyers often struggle with limited customization options for shopping bags, which can hinder their ability to promote brand identity effectively. For instance, a business in Africa might want to order branded shopping bags that reflect their unique logo and color scheme, but find that the supplier only offers generic designs with minimal customization. This can lead to a disconnect between the product and the brand’s image.
The Solution: Buyers should thoroughly research suppliers that specialize in custom shopping bag production. When approaching potential suppliers, it’s essential to discuss specific branding needs and inquire about the full range of customization options available, including size, material, printing techniques, and design capabilities. Requesting mock-ups or prototypes can also help visualize how the final product will align with the brand’s identity. Additionally, exploring partnerships with suppliers that have a strong track record in custom orders can lead to innovative solutions that enhance brand recognition while meeting practical requirements.
Strategic Material Selection Guide for shopping bag supplier
When selecting materials for shopping bags, international B2B buyers must consider various factors, including durability, cost, and compliance with regional standards. Below is an analysis of four common materials used in shopping bag manufacturing, focusing on their properties, advantages, disadvantages, and specific considerations relevant to buyers from Africa, South America, the Middle East, and Europe.
What Are the Key Properties of Non-Woven Polypropylene Bags?
Non-woven polypropylene is a popular choice for shopping bags due to its lightweight yet durable nature. This material is resistant to moisture and can withstand temperatures up to 80°C (176°F). Its non-toxic composition makes it safe for food contact, which is essential for retail environments.
Pros & Cons:
The primary advantage of non-woven polypropylene bags is their durability and reusability, making them an eco-friendly option. They are also cost-effective, with a relatively low manufacturing complexity. However, they may not be as strong as woven alternatives and can be susceptible to tearing under heavy loads.
Impact on Application:
These bags are suitable for a variety of retail applications, particularly in grocery and general merchandise sectors. However, they may not be ideal for heavy-duty applications requiring high tensile strength.
Considerations for International Buyers:
Buyers should ensure compliance with local regulations regarding material safety and recycling. For example, in Germany, adherence to the German Packaging Act (VerpackG) is crucial. Additionally, understanding the preferences of consumers in different regions can guide material selection.
How Do Cotton Bags Compare in Terms of Performance?
Cotton bags are renowned for their strength and biodegradability. They can withstand temperatures up to 100°C (212°F) and are resistant to wear and tear, making them suitable for repeated use.
Pros & Cons:
The key advantage of cotton bags is their environmental friendliness and durability. They can be printed with high-quality designs, enhancing branding opportunities. However, they tend to be more expensive than synthetic options and may require more complex manufacturing processes.
Impact on Application:
Cotton bags are ideal for high-end retail and promotional applications, where aesthetics and sustainability are prioritized. However, they may not be suitable for wet or heavy items due to their absorbent nature.
Considerations for International Buyers:
Buyers should be aware of organic certification standards, such as GOTS (Global Organic Textile Standard), which may be required in certain markets, particularly in Europe. Understanding the cost implications of sourcing organic cotton is also essential.
What Are the Advantages of Using Paper Bags?
Paper bags are a traditional choice for shopping bags, known for their recyclability and biodegradability. They can handle moderate weights and are typically made from recycled materials, enhancing their eco-friendliness.
Pros & Cons:
A significant advantage of paper bags is their low environmental impact and the perception of being a sustainable option. They are also customizable and can be produced at a relatively low cost. However, they are less durable than fabric options and can be affected by moisture, leading to potential tearing.
Impact on Application:
Paper bags are widely used in retail, especially for clothing and food items. Their limitations in moisture resistance make them less suitable for wet products.
Considerations for International Buyers:
Compliance with local recycling standards is crucial, especially in regions like Europe where strict regulations are in place. Buyers should also consider the weight limits and design requirements that may vary by country.
What Makes Woven Polypropylene Bags a Strong Choice?
Woven polypropylene bags are known for their high strength and versatility. They can withstand heavy loads and are resistant to moisture and UV light, making them suitable for outdoor use.
Pros & Cons:
The primary advantage of woven polypropylene bags is their exceptional durability and load-bearing capacity. They are ideal for bulk items and can be produced at a moderate cost. However, they may have a higher manufacturing complexity compared to non-woven options.
Impact on Application:
These bags are particularly effective in agricultural and industrial applications, where heavy-duty performance is required. They are less common in consumer retail due to their utilitarian appearance.
Considerations for International Buyers:
Buyers should ensure that woven polypropylene bags meet the relevant ASTM or DIN standards for strength and safety. Understanding regional preferences for bag aesthetics can also influence material choice.
Summary Table of Material Selection for Shopping Bags
Material | Typical Use Case for shopping bag supplier | Key Advantage | Key Disadvantage/Limitation | Relative Cost (Low/Med/High) |
---|---|---|---|---|
Non-Woven Polypropylene | Grocery and general merchandise bags | Durable and eco-friendly | Susceptible to tearing | Low |
Cotton | High-end retail and promotional bags | Biodegradable and strong | Higher cost and complex mfg | High |
Paper | Clothing and food items | Low environmental impact | Less durable and moisture-sensitive | Low |
Woven Polypropylene | Agricultural and industrial applications | High strength and versatility | Higher manufacturing complexity | Medium |
This material selection guide offers valuable insights for international B2B buyers, enabling them to make informed decisions that align with their business needs and regional compliance requirements.
In-depth Look: Manufacturing Processes and Quality Assurance for shopping bag supplier
What Are the Main Stages in the Manufacturing Process of Shopping Bags?
The manufacturing process for shopping bags involves several critical stages that ensure the final product meets quality and durability standards. Understanding these stages is essential for B2B buyers who want to ensure they are sourcing high-quality products.
Material Preparation
The first step in the manufacturing process is material preparation. Shopping bags can be made from a variety of materials, including paper, plastic, and biodegradable options. Each material has its own preparation requirements. For example, paper bags typically start with the sourcing of high-quality pulp, while plastic bags require the procurement of resin pellets. During this stage, suppliers must ensure that the materials are free from defects and meet any necessary environmental standards.
Forming
The forming stage is where the raw materials are transformed into the shape of the shopping bag. For paper bags, this typically involves cutting the sheets of paper into the desired size and shape, followed by processes like folding and gluing. In the case of plastic bags, the resin is melted and extruded into sheets, which are then cut and sealed to create the bag structure. This stage is crucial because any errors can lead to weak seams or improper sizing, affecting the bag’s usability.
Assembly
After forming, the bags undergo an assembly process. This can involve adding handles, printing logos, or applying finishes that enhance the bag’s appearance and functionality. For instance, a shopping bag supplier might add reinforced handles to paper bags to improve load-bearing capacity. This stage often includes quality checks to ensure that any added components meet the specified standards.
Finishing
The finishing stage encompasses all final touches before the bags are packaged for shipping. This may include additional quality inspections, surface treatments, and packaging. For example, bags might be treated with a water-resistant coating or printed with custom designs. Proper finishing not only improves the bag’s aesthetic appeal but also its durability and usability.
What Quality Assurance Standards Should B2B Buyers Look For?
Quality assurance is vital in ensuring that shopping bags meet international standards and customer expectations. B2B buyers should familiarize themselves with various quality standards relevant to the industry.
International Standards
ISO 9001 is one of the most recognized quality management standards globally. It sets criteria for a quality management system and helps organizations ensure they meet customer and regulatory requirements. Suppliers who adhere to ISO 9001 demonstrate their commitment to quality and continuous improvement.
Industry-Specific Standards
In addition to ISO 9001, there are other industry-specific standards that may apply. For instance, the CE marking indicates that products comply with EU safety, health, and environmental protection standards. Similarly, the American Plastic Industry (API) provides guidelines for plastic materials, ensuring they are safe for consumers.
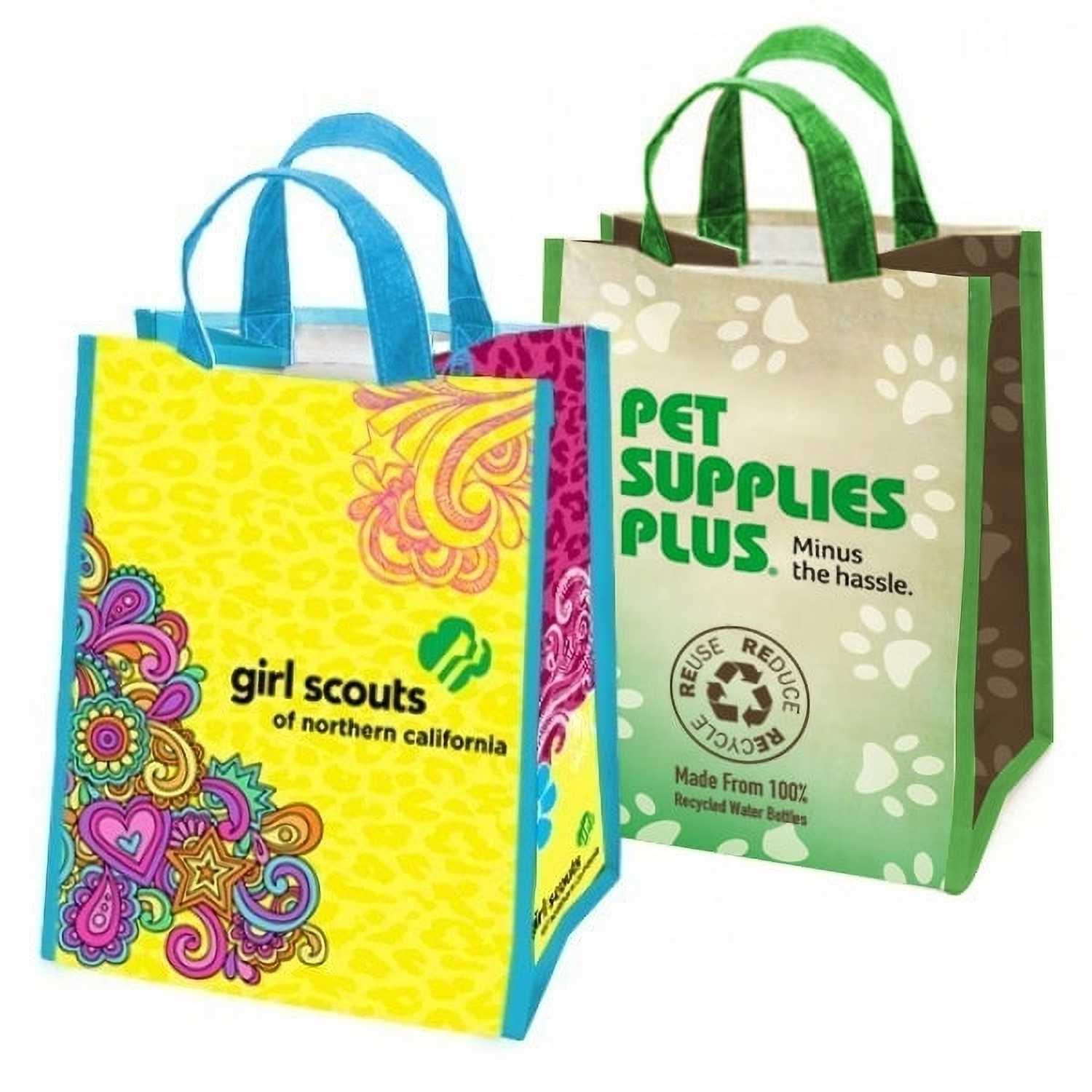
A stock image related to shopping bag supplier.
How Do Quality Control Checkpoints Work in the Shopping Bag Manufacturing Process?
Quality control (QC) is an integral part of the manufacturing process that helps ensure that defects are caught early and that the final product meets specifications. B2B buyers should be aware of common QC checkpoints during the shopping bag manufacturing process.
Incoming Quality Control (IQC)
IQC involves inspecting raw materials before they enter the production process. This is crucial because the quality of the raw materials directly affects the final product. Suppliers should conduct tests to verify that the materials meet the required specifications, such as thickness, weight, and tensile strength.
In-Process Quality Control (IPQC)
During production, IPQC is implemented to monitor the manufacturing process and catch any defects in real-time. This may involve regular inspections of machinery settings, material flow, and the quality of work performed at each stage. Employing statistical process control (SPC) techniques can help suppliers identify trends and make adjustments before defects occur.
Final Quality Control (FQC)
FQC is the last step before products are shipped. It involves a thorough inspection of the finished bags to ensure they meet all specifications. This may include checking for proper sealing, printing accuracy, and overall appearance. Random sampling techniques are often used during FQC to ensure a representative quality assessment.
How Can B2B Buyers Verify Supplier Quality Control Processes?
For international B2B buyers, verifying a supplier’s quality control processes is crucial in ensuring product quality. Here are effective methods to do so:
Conducting Audits
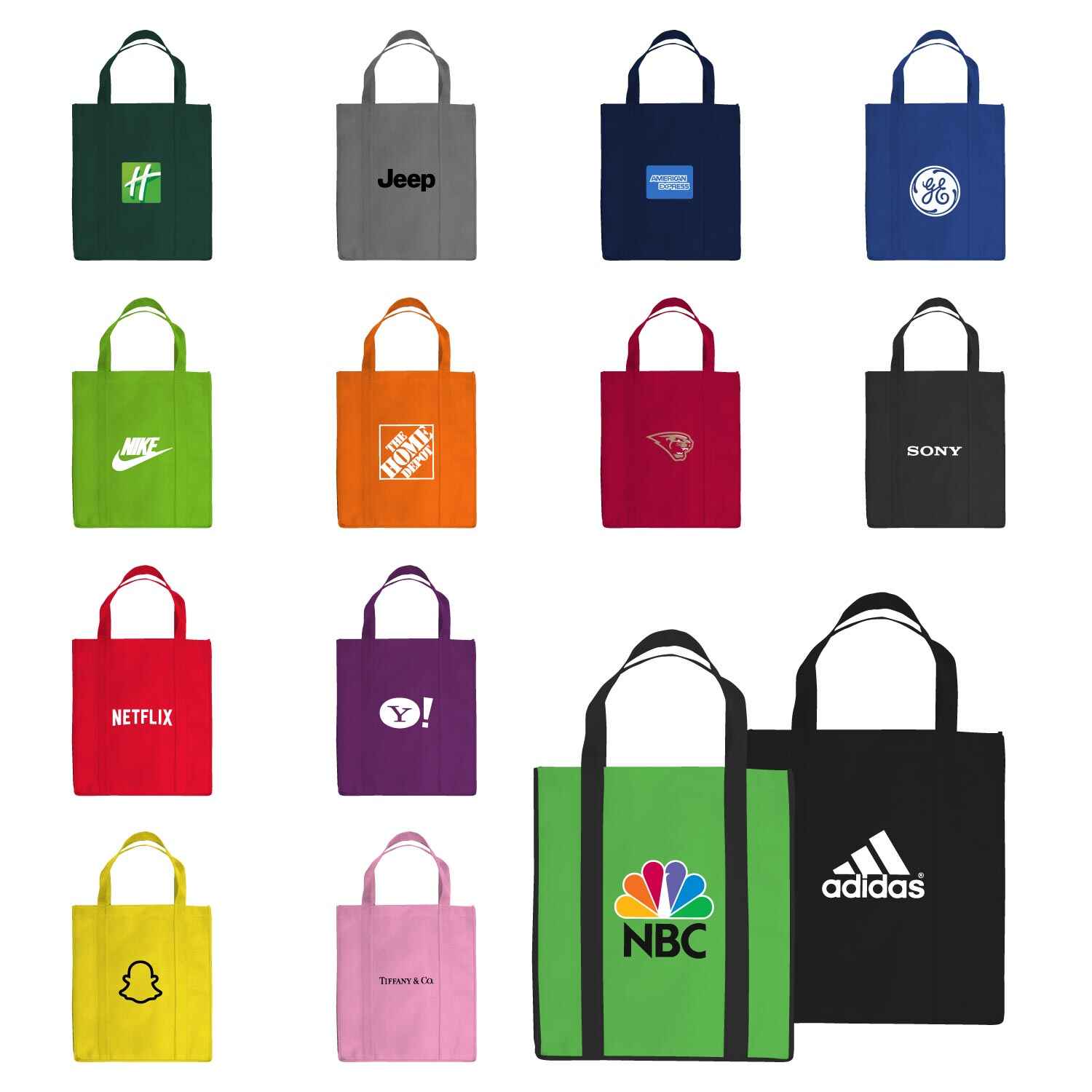
A stock image related to shopping bag supplier.
Regular audits of suppliers can provide valuable insights into their quality control practices. Buyers should consider scheduling on-site audits to observe the manufacturing process firsthand, assess compliance with quality standards, and review documentation related to QC processes.
Reviewing Quality Reports
Suppliers should provide detailed quality reports that outline their QC processes, inspection results, and any corrective actions taken in response to defects. Buyers should request these reports to assess the supplier’s commitment to quality and continuous improvement.
Engaging Third-Party Inspection Services
Utilizing third-party inspection services can provide an unbiased evaluation of the supplier’s quality control measures. These services can conduct inspections at various stages of production, ensuring that products meet the required specifications before shipment.
What Are the Nuances of Quality Control for International B2B Buyers?
When sourcing shopping bags from suppliers in different regions such as Africa, South America, the Middle East, and Europe, B2B buyers must navigate various nuances in quality control:
Regional Standards
Different regions may have distinct quality standards and regulations. For instance, European suppliers may be more inclined to comply with CE marking requirements, while suppliers in Africa may follow different local standards. Buyers should familiarize themselves with these regulations to ensure compliance.
Cultural Considerations
Cultural differences can also impact quality control practices. Understanding how suppliers approach quality assurance in their respective regions can help buyers establish better communication and expectations. Building strong relationships with suppliers can lead to improved quality outcomes.
Conclusion
In summary, understanding the manufacturing processes and quality assurance measures for shopping bags is crucial for international B2B buyers. By being aware of the main manufacturing stages, quality standards, control checkpoints, and verification methods, buyers can make informed decisions and ensure they are sourcing high-quality products that meet their needs.
Practical Sourcing Guide: A Step-by-Step Checklist for ‘shopping bag supplier’
In the dynamic world of B2B procurement, sourcing the right shopping bag supplier is essential for businesses looking to enhance their brand image and meet consumer demands. This guide provides a structured checklist to streamline your sourcing process, ensuring you make informed decisions that align with your business objectives.
Step 1: Define Your Technical Specifications
Begin by outlining your specific requirements for shopping bags. Consider the materials, sizes, and designs that will best suit your brand and target market.
– Material Considerations: Decide if you need eco-friendly options, durable plastics, or paper bags based on your sustainability goals and customer preferences.
– Size and Design: Think about the intended use and aesthetic appeal, ensuring the bags reflect your brand identity.
Step 2: Conduct Market Research for Suppliers
Research potential suppliers within your regions of interest, such as Africa, South America, the Middle East, and Europe. This step is crucial for understanding the market landscape and identifying reputable suppliers.
– Use Trade Directories: Explore platforms like Alibaba, Global Sources, or regional directories to find suppliers with positive reviews.
– Industry Events: Attend trade shows and exhibitions to meet suppliers face-to-face, allowing for better relationship building.
Step 3: Evaluate Potential Suppliers
Before committing, it’s crucial to vet suppliers thoroughly. Request company profiles, case studies, and references from buyers in a similar industry or region.
– Check Reviews and Testimonials: Look for feedback from other businesses to gauge reliability and quality.
– Assess Capabilities: Ensure the supplier can meet your order volume and delivery timelines.
Step 4: Verify Supplier Certifications and Compliance
Ensure that your chosen suppliers adhere to relevant industry standards and regulations. This step is essential for maintaining quality and sustainability.
– Certification Checks: Look for certifications such as ISO, FSC, or any local environmental certifications that align with your values.
– Compliance with Local Laws: Make sure suppliers comply with the regulations in their respective countries, especially if they will be exporting to your region.
Step 5: Request Samples and Conduct Quality Checks
Once you have narrowed down potential suppliers, request samples of their shopping bags. This is vital to assess the quality and design before placing a bulk order.
– Evaluate Durability and Design: Test the samples for strength, usability, and aesthetic appeal to ensure they meet your expectations.
– Feedback from Your Team: Involve key stakeholders in evaluating the samples to gather diverse opinions on the product.
Step 6: Negotiate Terms and Conditions
Engage in discussions regarding pricing, payment terms, and delivery schedules. Clear negotiations will help establish a strong working relationship and prevent future misunderstandings.
– Transparent Pricing: Ensure that all costs are outlined, including shipping and potential import duties.
– Flexible Payment Options: Discuss payment terms that suit both parties, considering options like deposits or net payment terms.
Step 7: Establish a Long-Term Relationship
After selecting your supplier, focus on building a strong, long-term partnership. Regular communication and feedback can help improve processes and product offerings over time.
– Continuous Improvement: Share insights about market trends and consumer feedback to help the supplier adapt.
– Regular Reviews: Schedule periodic evaluations of the supplier’s performance to ensure they continue to meet your standards.
By following this checklist, international B2B buyers can effectively source high-quality shopping bag suppliers that align with their business needs and consumer expectations.
Comprehensive Cost and Pricing Analysis for shopping bag supplier Sourcing
What Are the Key Cost Components in Shopping Bag Supplier Sourcing?
When sourcing shopping bags, understanding the cost structure is crucial for international B2B buyers. The primary cost components include:
-
Materials: The choice of materials significantly impacts the overall cost. Common materials for shopping bags include plastic, paper, and fabric, each varying in price based on quality and environmental certifications. For example, eco-friendly materials may have a higher upfront cost but could enhance brand reputation and customer appeal.
-
Labor: Labor costs can differ widely based on the supplier’s location. In regions with higher wages, such as Europe, labor costs will be more substantial compared to countries in Africa or South America. It’s important to consider labor regulations and the skill level required for production, which can affect pricing.
-
Manufacturing Overhead: This includes expenses related to factory operations, such as utilities, rent, and administrative costs. Suppliers with more advanced manufacturing processes or technologies might charge higher overhead, which can reflect in the final pricing.
-
Tooling: If custom designs or specific sizes are required, tooling costs for molds or dies may be necessary. These initial costs can be significant but are often amortized over larger production runs.
-
Quality Control (QC): Implementing stringent quality control measures can increase costs but is essential for ensuring product reliability and compliance with international standards. Buyers should inquire about the QC processes in place to avoid costly defects.
-
Logistics: Shipping costs can vary significantly based on distance, shipping method, and the weight of the goods. Buyers should consider logistics as a part of their total cost, including customs duties and taxes.
-
Margin: Finally, the supplier’s profit margin will influence the final price. Understanding the supplier’s pricing strategy and market position can help buyers negotiate better terms.
How Do Price Influencers Affect Shopping Bag Costs?
Several factors can influence the pricing of shopping bags, particularly for international B2B transactions:
-
Volume/MOQ: Suppliers often have minimum order quantities (MOQs), which can impact unit pricing. Larger orders typically yield lower per-unit costs, making it beneficial for buyers to consolidate orders.
-
Specifications and Customization: Customized bags with specific branding, colors, or sizes can incur additional costs. Buyers should weigh the benefits of customization against the potential price increase.
-
Material Quality and Certifications: Higher quality materials and certifications (e.g., biodegradable, recyclable) can raise costs. However, such attributes may align better with sustainability goals and consumer preferences.
-
Supplier Factors: The supplier’s reputation, reliability, and production capabilities can affect pricing. Established suppliers might charge a premium due to their proven track record.
-
Incoterms: Understanding Incoterms is vital for calculating total landed costs. Terms such as FOB (Free on Board) or CIF (Cost, Insurance, and Freight) can significantly impact pricing and responsibilities regarding logistics.
What Are the Best Practices for Negotiating Shopping Bag Prices?
For international buyers, particularly from regions like Africa, South America, the Middle East, and Europe, employing strategic negotiation practices can lead to cost savings:
-
Total Cost of Ownership (TCO): Evaluate the total cost beyond just the purchase price. This includes logistics, potential tariffs, and long-term quality implications. Understanding TCO helps justify higher upfront costs for better quality or service.
-
Research Market Prices: Familiarize yourself with market rates for different types of shopping bags. This knowledge equips you to negotiate effectively and avoid overpaying.
-
Establish Long-Term Relationships: Building a rapport with suppliers can lead to better pricing and terms over time. Suppliers may offer discounts for repeat business or larger orders.
-
Request Samples: Before committing to a large order, request samples to assess quality and compliance with specifications. This can prevent costly mistakes and ensure satisfaction with the final product.
-
Leverage Competitive Bids: Solicit quotes from multiple suppliers to create competition. This can lead to more favorable pricing and terms.
Conclusion: Navigating the Shopping Bag Supplier Landscape
Understanding the comprehensive cost structure and price influencers in shopping bag sourcing is essential for international B2B buyers. By focusing on key cost components, being aware of pricing influences, and employing effective negotiation strategies, buyers can make informed decisions that align with their business objectives while ensuring quality and sustainability. Always remember that indicative prices can fluctuate, and it’s prudent to engage in thorough discussions with suppliers to establish clear expectations and terms.
Alternatives Analysis: Comparing shopping bag supplier With Other Solutions
When considering suppliers for shopping bags, it’s essential to explore alternative solutions that can meet similar requirements. This analysis will compare the traditional shopping bag supplier with other viable options, including reusable bags and digital shopping solutions. Each option has its own set of advantages and drawbacks, which should be carefully evaluated by international B2B buyers.
Comparison Aspect | Shopping Bag Supplier | Reusable Bags | Digital Shopping Solutions |
---|---|---|---|
Performance | High durability | Medium to high durability | Low (depends on user access) |
Cost | Moderate to high | Initially high, long-term low | Variable (subscription-based) |
Ease of Implementation | Straightforward | Requires training and promotion | Requires tech infrastructure |
Maintenance | Low (bulk purchase) | Medium (cleaning and storage) | Low (software updates) |
Best Use Case | Retail environments | Eco-conscious brands | E-commerce platforms |
What Are the Pros and Cons of Using Reusable Bags as an Alternative?
Reusable bags have gained popularity as a sustainable option for businesses aiming to reduce environmental impact. The initial cost of purchasing reusable bags can be higher than traditional shopping bags, but they often lead to long-term savings due to their durability. Businesses can promote their brand through custom designs on reusable bags, enhancing visibility. However, they require proper maintenance, including cleaning and storage, which can complicate their use in high-traffic retail environments.
How Do Digital Shopping Solutions Compare to Traditional Suppliers?
Digital shopping solutions, such as e-commerce platforms, provide a modern approach to shopping that eliminates the need for physical bags altogether. This method is particularly effective for businesses operating in regions with high internet penetration. While the cost can vary significantly based on subscription models or transaction fees, the initial investment in technology can be daunting for some businesses. Additionally, digital solutions may not be suitable for all customer demographics, particularly in areas where internet access is limited.
Conclusion: How to Choose the Right Solution for Your Business Needs?
Selecting the right shopping bag solution hinges on understanding your specific business needs and customer preferences. If your focus is on sustainability and brand visibility, reusable bags may be the best option. However, for businesses with a strong online presence, digital shopping solutions could streamline operations and reduce costs associated with physical inventory. Analyzing factors such as performance, cost, ease of implementation, and maintenance will empower B2B buyers from Africa, South America, the Middle East, and Europe to make informed decisions that align with their operational goals and market demands.
Essential Technical Properties and Trade Terminology for shopping bag supplier
What Are the Key Technical Properties of Shopping Bags?
When sourcing shopping bags, international B2B buyers must understand several critical technical properties that can affect product quality and performance. Here are some essential specifications:
-
Material Grade
The material grade refers to the type of material used in manufacturing shopping bags, such as high-density polyethylene (HDPE), low-density polyethylene (LDPE), or recycled paper. Each material has distinct properties affecting strength, durability, and environmental impact. For instance, HDPE bags are known for their robustness, making them suitable for heavy items, while biodegradable options appeal to eco-conscious consumers. -
Weight Capacity
Weight capacity indicates the maximum load a shopping bag can carry without tearing or deforming. This property is crucial for B2B buyers in retail, as it determines how well the bags can serve their intended purpose. Understanding the weight capacity helps buyers select bags that align with their product offerings, ensuring customer satisfaction and reducing the risk of bag failure during use. -
Tolerance Levels
Tolerance levels define the allowable variations in dimensions and weight of the bags during production. This is important in B2B transactions as it ensures consistency in the product received. For example, if a buyer orders bags of a specific size, understanding tolerance levels helps in assessing whether the received bags meet the required specifications. -
Seal Strength
Seal strength refers to the durability of the bag’s seals, which can be heat-sealed or glued. A strong seal prevents bag failure under load and is particularly important for bags that will carry heavy or sharp items. Buyers should inquire about the seal strength to ensure the bags meet their operational demands. -
Environmental Compliance
Environmental compliance indicates whether the bags meet specific environmental regulations or certifications, such as being recyclable or made from recycled materials. With growing consumer demand for sustainability, B2B buyers must consider environmental compliance to align with market trends and enhance their brand image.
Which Trade Terms Should B2B Buyers Understand When Sourcing Shopping Bags?
Understanding industry jargon is vital for navigating the procurement process effectively. Here are some common terms used in the shopping bag supply chain:
-
OEM (Original Equipment Manufacturer)
An OEM refers to a company that manufactures products based on the specifications of another company, which then sells them under its brand. For B2B buyers, working with an OEM can provide customized solutions tailored to specific market needs, enhancing brand differentiation. -
MOQ (Minimum Order Quantity)
MOQ represents the smallest quantity of a product that a supplier is willing to sell. This term is crucial for buyers as it impacts inventory management and cash flow. Understanding MOQ helps buyers gauge whether they can meet the supplier’s requirements while maintaining their budget. -
RFQ (Request for Quotation)
An RFQ is a document used by buyers to solicit price quotes from suppliers for specific products or services. This process allows B2B buyers to compare prices and terms from different suppliers, facilitating informed purchasing decisions. -
Incoterms (International Commercial Terms)
Incoterms are a set of rules that define the responsibilities of buyers and sellers regarding shipping, insurance, and tariffs. Familiarity with Incoterms is essential for international transactions, helping buyers understand their obligations, shipping costs, and risks involved in the transportation of shopping bags. -
Lead Time
Lead time refers to the time taken from placing an order to receiving the product. This is a critical factor for B2B buyers as it affects inventory levels and fulfillment capabilities. Understanding lead times helps buyers plan their supply chains more effectively and avoid stockouts.
By grasping these technical properties and trade terms, B2B buyers can make more informed decisions when selecting shopping bag suppliers, ultimately leading to successful procurement strategies.
Navigating Market Dynamics and Sourcing Trends in the shopping bag supplier Sector
What Are the Current Market Dynamics and Key Trends in the Shopping Bag Supplier Sector?
The shopping bag supplier sector is experiencing significant growth driven by various global factors. Increasing consumer awareness regarding sustainability is pushing businesses to seek eco-friendly packaging solutions. This trend is particularly prominent in Europe and is gaining traction in Africa and South America, where consumers are increasingly favoring brands that prioritize environmental responsibility. Additionally, the rise of e-commerce has amplified the demand for durable, high-quality shopping bags that can withstand shipping and handling, thereby influencing suppliers to innovate and diversify their product offerings.
Emerging technologies are reshaping sourcing practices within the sector. Digital platforms are streamlining the procurement process, allowing international buyers to connect with suppliers across borders more efficiently. Blockchain technology is gaining attention for its potential to enhance supply chain transparency, enabling businesses to track the origin of materials and ensure ethical sourcing practices. Furthermore, automation and AI-driven analytics are being utilized to optimize inventory management and predict market trends, making it crucial for B2B buyers to stay informed about these technological advancements.
How Is Sustainability and Ethical Sourcing Influencing the Shopping Bag Supplier Market?
Environmental impact is a pressing concern in the shopping bag supplier sector. Traditional plastic bags contribute significantly to pollution and waste, prompting a shift towards biodegradable and recyclable materials. B2B buyers are increasingly prioritizing suppliers that offer “green” certifications, such as FSC (Forest Stewardship Council) or Cradle to Cradle certifications, which indicate responsible sourcing and manufacturing practices.
Ethical supply chains are also gaining importance. Buyers are not only focused on the end product but are also concerned about the working conditions of those involved in the production process. This has led to a rise in demand for suppliers who can demonstrate fair labor practices and transparency in their operations. By choosing suppliers committed to sustainability and ethical sourcing, businesses can enhance their brand reputation and appeal to the growing segment of environmentally conscious consumers.
What Is the Brief Evolution and History of the Shopping Bag Supplier Sector?
The shopping bag supplier sector has evolved significantly over the past few decades. Initially dominated by single-use plastic bags, the industry has undergone a transformative shift towards sustainable alternatives. The introduction of regulations banning plastic bags in many countries, particularly in Europe, has accelerated this change. As consumers became more environmentally aware, suppliers began to innovate with materials such as organic cotton, jute, and recycled plastics.
Over time, the market has diversified, with suppliers now offering a range of customizable options to meet the specific needs of businesses. This evolution reflects broader societal changes and the growing recognition of the role that packaging plays in environmental conservation. Today, the sector is characterized by a strong emphasis on sustainability, ethical sourcing, and technological innovation, making it a dynamic space for international B2B buyers looking to align their purchasing practices with global sustainability goals.
Frequently Asked Questions (FAQs) for B2B Buyers of shopping bag supplier
-
How do I ensure the quality of shopping bags from a supplier?
To ensure the quality of shopping bags from a supplier, start by requesting samples. Evaluate the material, stitching, and overall durability. Look for certifications such as ISO or compliance with local regulations that demonstrate adherence to quality standards. Additionally, consider visiting the supplier’s production facility if possible, or utilizing third-party inspection services to verify quality before placing larger orders. Establishing clear quality expectations in your contract can also help mitigate risks. -
What are the minimum order quantities (MOQ) for shopping bags?
Minimum order quantities (MOQ) for shopping bags vary widely depending on the supplier and the customization options. Generally, MOQs can range from 100 to several thousand units. When sourcing internationally, be sure to discuss your specific needs with potential suppliers. Some suppliers may offer flexible MOQs for first-time buyers or smaller businesses, while others may have strict limits. Always clarify the MOQ upfront to avoid any surprises during the ordering process. -
What payment terms should I expect when sourcing shopping bags?
Payment terms when sourcing shopping bags typically include options such as advance payment, letter of credit, or payment upon delivery. Many suppliers may require a deposit (often 30-50%) upfront to initiate production, with the balance due before shipping. It’s important to negotiate terms that align with your cash flow while ensuring the supplier feels secure. Always document payment terms in your purchase agreement to avoid misunderstandings. -
How can I customize shopping bags for my brand?
To customize shopping bags for your brand, start by discussing your design preferences with potential suppliers. Most suppliers offer various customization options, including printing your logo, selecting bag colors, and choosing materials. Provide the supplier with your design files in the required format and specify any additional features like handles or closures. Ensure you get a digital proof or sample before final production to confirm that the customization meets your expectations. -
What logistics considerations should I keep in mind when importing shopping bags?
When importing shopping bags, consider logistics aspects such as shipping methods, transit times, and customs regulations. Choose a shipping method that balances cost and delivery speed—options typically include air freight for faster delivery and sea freight for larger shipments. Familiarize yourself with import duties, taxes, and necessary documentation to ensure smooth customs clearance. Partnering with a reliable freight forwarder can help streamline the logistics process. -
What factors should I consider when vetting a shopping bag supplier?
When vetting a shopping bag supplier, consider factors such as their manufacturing capabilities, experience in the industry, and customer reviews. Check for certifications that indicate compliance with quality and safety standards. Request references from previous clients to gauge their reliability and service quality. Additionally, assess their communication responsiveness and willingness to accommodate your specific needs, as these can significantly impact your business relationship. -
How do I handle potential disputes with a shopping bag supplier?
Handling disputes with a shopping bag supplier begins with clear communication. Address issues promptly, outlining your concerns and seeking a resolution amicably. If a satisfactory agreement cannot be reached, refer to your contract for dispute resolution procedures, which may include mediation or arbitration. Always document all interactions regarding the dispute for future reference. Establishing a good relationship with your supplier can often prevent disputes from escalating. -
What are the environmental considerations when sourcing shopping bags?
When sourcing shopping bags, consider the environmental impact of the materials used. Look for suppliers who offer eco-friendly options, such as biodegradable or recyclable materials. Inquire about the supplier’s sustainability practices, including waste management and carbon footprint reduction measures. Additionally, consider the lifecycle of the bags and how they can contribute to your brand’s sustainability goals. Aligning your sourcing decisions with environmental values can enhance your brand’s reputation in the market.
Important Disclaimer & Terms of Use
⚠️ Important Disclaimer
The information provided in this guide, including content regarding manufacturers, technical specifications, and market analysis, is for informational and educational purposes only. It does not constitute professional procurement advice, financial advice, or legal advice.
While we have made every effort to ensure the accuracy and timeliness of the information, we are not responsible for any errors, omissions, or outdated information. Market conditions, company details, and technical standards are subject to change.
B2B buyers must conduct their own independent and thorough due diligence before making any purchasing decisions. This includes contacting suppliers directly, verifying certifications, requesting samples, and seeking professional consultation. The risk of relying on any information in this guide is borne solely by the reader.
Strategic Sourcing Conclusion and Outlook for shopping bag supplier
As international B2B buyers navigate the evolving landscape of shopping bag suppliers, the importance of strategic sourcing cannot be overstated. By prioritizing quality, sustainability, and supplier reliability, companies can enhance their brand reputation while meeting consumer demands for eco-friendly products. Strategic sourcing not only reduces costs but also fosters long-term partnerships that can lead to innovation and improved supply chain efficiency.
How Can B2B Buyers Leverage Strategic Sourcing for Shopping Bags?
International buyers, particularly those from Africa, South America, the Middle East, and Europe, should focus on understanding local market trends and regulations surrounding packaging materials. Engaging with suppliers who demonstrate a commitment to sustainability and ethical practices will not only align with global environmental goals but also resonate with conscious consumers.
What Does the Future Hold for Shopping Bag Suppliers?
Looking ahead, the demand for customized and sustainable shopping bags is set to grow. Buyers should stay informed about emerging materials and technologies that can enhance the functionality and appeal of shopping bags. By taking proactive steps now, businesses can position themselves as leaders in their respective markets, ready to capitalize on future opportunities.
In conclusion, investing time in strategic sourcing today will yield significant benefits tomorrow. Embrace the challenge of finding the right shopping bag supplier and be part of the movement toward a more sustainable and responsible retail environment.