The Ultimate Guide to Bar Stool Manufacturer (2025)
Introduction: Navigating the Global Market for bar stool manufacturer
Navigating the complexities of sourcing bar stools can be a daunting task for international B2B buyers, particularly those operating in diverse markets like Africa, South America, the Middle East, and Europe. With an increasing demand for stylish yet functional seating solutions in hospitality and commercial spaces, understanding how to effectively source bar stools that meet quality, design, and cost expectations is crucial. This guide will provide a comprehensive overview of the bar stool manufacturing landscape, exploring various types, applications, and the critical factors involved in supplier vetting.
In addition to discussing material options and design trends, we will delve into cost considerations and logistical challenges that can impact sourcing decisions. By equipping you with actionable insights and strategies, this guide empowers B2B buyers to make informed purchasing decisions that align with their business needs and market demands. Whether you are based in Nigeria looking to enhance a trendy bar or in Poland seeking durable solutions for a restaurant chain, understanding the global bar stool market will enable you to navigate challenges effectively and capitalize on opportunities for growth.
Ultimately, this guide aims to streamline your sourcing process, ensuring that you can confidently choose the right bar stools that not only enhance your space but also provide excellent value for your investment.
Understanding bar stool manufacturer Types and Variations
Type Name | Key Distinguishing Features | Primary B2B Applications | Brief Pros & Cons for Buyers |
---|---|---|---|
Wooden Bar Stools | Crafted from solid wood, offering durability and classic aesthetics. | Restaurants, bars, cafes | Pros: Timeless design, sturdy; Cons: Can be heavy, may require maintenance. |
Metal Bar Stools | Sleek, modern designs often featuring steel or aluminum. | Nightclubs, outdoor venues | Pros: Lightweight, easy to clean; Cons: May not be as comfortable, can rust if not treated. |
Adjustable Bar Stools | Height adjustable features, often with a gas lift mechanism. | Home bars, offices | Pros: Versatile for different users, space-saving; Cons: Mechanisms may wear out over time. |
Upholstered Bar Stools | Soft padding and fabric coverings for enhanced comfort. | Hotels, lounges | Pros: Comfortable for long sitting; Cons: Can be difficult to clean, may wear out faster. |
Stackable Bar Stools | Designed to stack for easy storage, typically lightweight. | Events, temporary setups | Pros: Space-efficient, easy to transport; Cons: Less sturdy, limited design options. |
What Are the Characteristics of Wooden Bar Stools?
Wooden bar stools are favored for their durability and classic aesthetic appeal. Typically crafted from solid hardwood, these stools can withstand heavy usage in commercial settings such as restaurants and cafes. Their timeless design complements various decor styles, making them a versatile choice. When considering wooden stools, B2B buyers should assess the type of wood used, as different species offer varying levels of durability and maintenance needs.
How Do Metal Bar Stools Compare for B2B Use?
Metal bar stools are characterized by their modern, sleek designs, often made from steel or aluminum. They are particularly suitable for high-traffic environments like nightclubs and outdoor venues due to their lightweight nature and ease of cleaning. Buyers should consider the finish on metal stools, as untreated metal can be prone to rust. Additionally, while they are space-efficient, some designs may lack the comfort of upholstered options.
What Are the Benefits of Adjustable Bar Stools?
Adjustable bar stools feature a gas lift mechanism that allows users to modify the height, making them ideal for both home bars and office environments. Their versatility accommodates various table heights and user preferences, enhancing comfort. When purchasing, B2B buyers should evaluate the reliability of the adjustment mechanism and the overall build quality to ensure longevity, as these components can wear out over time.
Why Choose Upholstered Bar Stools for Comfort?
Upholstered bar stools are designed with soft padding and fabric coverings, providing enhanced comfort for extended sitting periods. They are often used in hotels and lounges where guest comfort is paramount. However, buyers should be aware of the cleaning challenges associated with upholstery, as spills and stains can be problematic. Selecting durable, stain-resistant fabrics can mitigate some of these concerns.
What Are the Advantages of Stackable Bar Stools?
Stackable bar stools are engineered for easy storage and transport, making them an excellent choice for events and temporary setups. Their lightweight design allows for quick rearrangement of seating arrangements. While they are space-efficient, B2B buyers should consider their sturdiness, as some models may not be as robust as non-stackable options. Additionally, the limited design variety might not suit all aesthetic preferences.
Related Video: HOW TO UPHOLSTER A ROUND LEATHER BAR STOOL
Key Industrial Applications of bar stool manufacturer
Industry/Sector | Specific Application of Bar Stool Manufacturer | Value/Benefit for the Business | Key Sourcing Considerations for this Application |
---|---|---|---|
Hospitality | Restaurants and Cafés | Enhances customer experience and aesthetic appeal | Durability, style options, and compliance with local regulations |
Entertainment | Bars and Nightclubs | Supports social interaction and maximizes space | Custom designs, comfort, and stability for heavy usage |
Retail | Showrooms and Retail Spaces | Provides functional seating while showcasing products | Versatility in design and material choices, ease of maintenance |
Office Spaces | Break Rooms and Collaborative Areas | Promotes casual interaction and relaxation | Ergonomics, adaptability to various office styles, and material sustainability |
Event Planning | Trade Shows and Exhibitions | Facilitates networking and comfort during events | Portability, easy setup, and diverse styling options |
How Are Bar Stools Used in the Hospitality Industry?
In the hospitality sector, bar stools are essential for restaurants and cafés, creating an inviting atmosphere that encourages patrons to linger longer. They enhance customer experience by providing comfortable seating options at counters and high tables, which are often key areas for social interaction. For international buyers, particularly from Africa and Europe, sourcing durable and aesthetically pleasing bar stools that comply with local safety regulations is crucial to avoid liabilities and ensure customer satisfaction.
What Role Do Bar Stools Play in Entertainment Venues?
In bars and nightclubs, bar stools are more than just seating; they are a focal point that encourages socializing and interaction among guests. They help maximize limited space, allowing venues to accommodate more patrons without sacrificing comfort. Buyers from South America and the Middle East should prioritize features such as custom designs that reflect the venue’s branding and durability to withstand high foot traffic, ensuring a good return on investment.
How Do Retail Spaces Benefit from Bar Stools?
In retail environments, bar stools serve a dual purpose: they provide seating for customers while also showcasing products in a relaxed setting. This can lead to increased sales as customers feel more comfortable engaging with the merchandise. For B2B buyers in Europe, sourcing versatile designs that complement various retail aesthetics and materials that are easy to clean and maintain is essential for maximizing longevity and customer satisfaction.
Why Are Bar Stools Important in Office Spaces?
In office settings, bar stools are increasingly utilized in break rooms and collaborative areas to foster casual interactions among employees. They promote a relaxed atmosphere that can enhance creativity and teamwork. International buyers, particularly from Africa, should consider ergonomics and adaptability in design, ensuring that the stools fit well within diverse office layouts while providing comfort for prolonged use.
How Do Bar Stools Enhance Event Planning?
For event planners, bar stools are a vital component in trade shows and exhibitions, where they provide a comfortable setting for networking and discussions. They can easily be moved and arranged to suit various event layouts, making them a practical choice for dynamic environments. Buyers should focus on sourcing lightweight and portable options that can be set up quickly and styled to match the event’s theme, ensuring an appealing and functional experience for attendees.
Related Video: Uses Of Polymers | Organic Chemistry | Chemistry | FuseSchool
3 Common User Pain Points for ‘bar stool manufacturer’ & Their Solutions
Scenario 1: Quality Assurance in Custom Orders
The Problem: International B2B buyers often face challenges related to quality assurance when placing custom orders with bar stool manufacturers. This issue is particularly pronounced for businesses in Africa and South America, where local standards may not align with international expectations. Buyers may receive products that do not meet their specifications, leading to increased costs, delays in project timelines, and potential damage to their business reputation.
The Solution: To mitigate quality assurance issues, buyers should establish clear and detailed specifications before placing orders. This includes providing manufacturers with comprehensive documentation that outlines material types, dimensions, weight capacity, and finish details. Additionally, buyers should request prototypes or samples before committing to larger orders. It is advisable to conduct factory visits or utilize third-party inspection services to ensure that the manufacturing process adheres to agreed-upon standards. This proactive approach not only helps in maintaining quality but also builds a stronger relationship with manufacturers, fostering trust and reliability.
Scenario 2: Navigating Compliance and Regulation Challenges
The Problem: B2B buyers, especially in Europe and the Middle East, frequently encounter compliance and regulatory challenges when sourcing bar stools. Different countries have varying safety and environmental regulations, which can complicate the procurement process. Non-compliance can lead to hefty fines, product recalls, and loss of market access, making it crucial for buyers to navigate these legal landscapes effectively.
The Solution: Buyers should conduct thorough research on the regulatory requirements specific to their target markets. This includes understanding safety standards such as weight limits, materials used, and any certifications required for bar stools. Collaborating with local legal experts or compliance consultants can provide valuable insights into these regulations. Furthermore, establishing a transparent dialogue with manufacturers regarding compliance can streamline the process, ensuring that all products meet necessary standards before they are shipped. Documenting all compliance measures taken can also serve as a protective measure should any regulatory issues arise post-purchase.
Scenario 3: Managing Supply Chain Disruptions
The Problem: Supply chain disruptions have become increasingly common in global trade, impacting the timely delivery of bar stools. Buyers from various regions, particularly those in Africa and South America, may find themselves facing unexpected delays due to shipping issues, shortages of raw materials, or geopolitical tensions. These disruptions can lead to inventory shortages and missed sales opportunities, ultimately affecting the bottom line.
The Solution: To effectively manage supply chain disruptions, buyers should adopt a multi-sourcing strategy. This involves identifying and establishing relationships with multiple manufacturers across different regions. By diversifying suppliers, buyers can reduce reliance on a single source and create contingency plans for potential disruptions. Additionally, leveraging technology such as supply chain management software can provide real-time insights into inventory levels, shipment tracking, and supplier performance. Regularly communicating with suppliers about their capabilities and constraints can also help buyers anticipate issues and adapt their strategies accordingly, ensuring a smoother procurement process and enhanced resilience against disruptions.
Strategic Material Selection Guide for bar stool manufacturer
When selecting materials for bar stools, manufacturers must consider various factors, including durability, cost, and suitability for specific environments. Below is an analysis of four common materials used in bar stool manufacturing, focusing on their properties, advantages, disadvantages, and implications for international B2B buyers.
What Are the Key Properties of Wood for Bar Stools?
Wood is a traditional material that offers aesthetic appeal and warmth. Key properties include:
- Durability: Solid hardwoods like oak and maple are highly durable and can withstand significant wear and tear.
- Temperature Resistance: Wood performs well in various temperatures but can warp or crack in extreme conditions.
- Corrosion Resistance: While not prone to corrosion, wood can be susceptible to moisture and requires proper sealing.
Pros & Cons: Wood provides a classic look and can be easily customized. However, it can be more expensive than other materials and may require regular maintenance to prevent damage from moisture and pests.
Impact on Application: Wood is suitable for indoor environments and can be finished to resist spills and stains. However, it may not be the best choice for high-moisture areas like poolside bars.
Considerations for International Buyers: Buyers from regions like Europe and the Middle East should ensure compliance with local regulations regarding sustainable sourcing and treatment of wood products. Standards such as FSC certification may be relevant.
How Does Metal Compare as a Material for Bar Stools?
Metal, particularly steel and aluminum, is another popular choice for bar stools. Its key properties include:
- Durability: Metals are incredibly strong and can support significant weight.
- Corrosion Resistance: Stainless steel offers excellent corrosion resistance, making it suitable for outdoor use.
- Temperature Resistance: Metals can become hot or cold depending on the environment, which may affect comfort.
Pros & Cons: Metal stools are often more affordable and easier to maintain than wooden stools. However, they can be less comfortable without additional cushioning and may not provide the warmth of wood.
Impact on Application: Metal is ideal for both indoor and outdoor settings, particularly in commercial environments where durability is paramount.
Considerations for International Buyers: Buyers should look for compliance with standards such as ASTM for metals. In regions like Africa, where corrosion due to humidity can be an issue, selecting stainless steel or powder-coated finishes is advisable.
What Are the Advantages of Plastic in Bar Stool Manufacturing?
Plastic materials, including polypropylene and polycarbonate, have gained popularity due to their versatility. Key properties include:
- Durability: High-quality plastics can be very durable and resistant to impacts.
- Corrosion Resistance: Plastics do not corrode, making them suitable for various environments.
- Temperature Resistance: Plastics can deform under high temperatures, so they must be rated for specific applications.
Pros & Cons: Plastic stools are lightweight, easy to clean, and often more affordable. However, they may not have the same aesthetic appeal as wood or metal and can be less durable under heavy use.
Impact on Application: Plastic is ideal for casual settings and outdoor use, where weight and ease of transport are significant factors.
Considerations for International Buyers: Buyers should ensure that the plastics used meet safety standards such as REACH in Europe or similar regulations in other regions.
How Do Upholstered Bar Stools Stand Up in Terms of Material Selection?
Upholstered bar stools combine various materials, including wood or metal frames with fabric or leather coverings. Key properties include:
- Durability: The durability depends on the frame material and the upholstery used.
- Comfort: Upholstered stools offer enhanced comfort, making them suitable for long-term seating.
- Maintenance: Different fabrics have varying levels of stain resistance and ease of cleaning.
Pros & Cons: Upholstered stools provide comfort and style but can be more expensive and require more maintenance than other materials.
Impact on Application: These stools are ideal for restaurants and bars where comfort is a priority.
Considerations for International Buyers: Compliance with fire safety regulations and fabric durability standards is crucial, especially in regions like Europe where such regulations are stringent.
Summary Table of Material Selection for Bar Stool Manufacturers
Material | Typical Use Case for Bar Stool Manufacturer | Key Advantage | Key Disadvantage/Limitation | Relative Cost (Low/Med/High) |
---|---|---|---|---|
Wood | Indoor residential and commercial settings | Aesthetic appeal and warmth | Requires maintenance and can warp | High |
Metal | Commercial and outdoor settings | High durability and low maintenance | Can be uncomfortable without cushions | Medium |
Plastic | Casual and outdoor environments | Lightweight and easy to clean | Less aesthetic appeal and durability | Low |
Upholstered | Restaurants and bars | Enhanced comfort and style | Higher cost and maintenance needs | High |
This comprehensive analysis should assist international B2B buyers in making informed decisions regarding material selection for bar stools, taking into account regional preferences and compliance requirements.
In-depth Look: Manufacturing Processes and Quality Assurance for bar stool manufacturer
What Are the Key Stages in the Manufacturing Process of Bar Stools?
The manufacturing process of bar stools involves several critical stages that ensure the final product is both functional and aesthetically pleasing. Understanding these stages can help B2B buyers from regions like Africa, South America, the Middle East, and Europe make informed purchasing decisions.
-
Material Preparation
The first step involves selecting appropriate materials, which typically include wood, metal, and upholstery fabrics. Each material has its own properties affecting durability, comfort, and appearance. Suppliers often conduct tests to ensure that materials meet specific standards for strength and resilience. -
Forming
This stage includes processes like cutting, bending, and shaping the materials into the required components. For wooden stools, CNC machines are often used to achieve precise cuts, while metal components may undergo processes like welding or stamping. This stage is crucial for ensuring the components fit together seamlessly. -
Assembly
After forming, the components are assembled. This may involve attaching the seat to the legs, adding footrests, or incorporating additional features like swivel mechanisms. Skilled labor is essential in this phase to ensure durability and stability. The assembly process may include the use of adhesives, screws, or brackets, depending on the design. -
Finishing
The final stage involves applying finishes such as stains, paints, or varnishes to enhance the aesthetic appeal and protect the materials from wear and tear. Upholstered stools may also undergo this stage, where fabrics are stretched and secured to the seat. Quality control during this phase is critical, as imperfections can affect the final appearance and customer satisfaction.
How Is Quality Assurance Implemented in Bar Stool Manufacturing?
Quality assurance (QA) is vital in ensuring that bar stools meet the expectations of B2B buyers. Adhering to international standards and industry-specific regulations can significantly enhance a manufacturer‘s credibility.
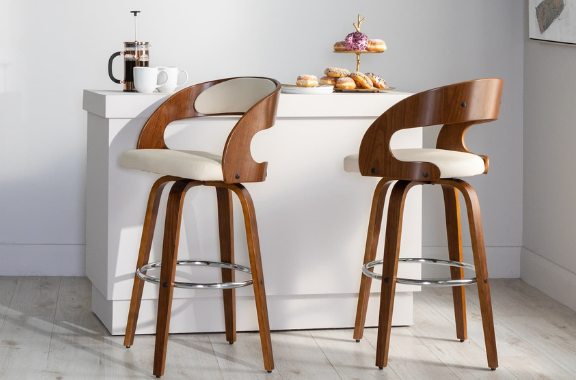
A stock image related to bar stool manufacturer.
-
Relevant International Standards
Many bar stool manufacturers adhere to standards such as ISO 9001, which outlines requirements for a quality management system (QMS). Compliance with these standards ensures that manufacturing processes are consistently monitored and improved. Additionally, certifications like CE (Conformité Européenne) indicate that the products meet European safety and environmental protection standards. -
Quality Control Checkpoints
– Incoming Quality Control (IQC): This initial checkpoint involves inspecting raw materials upon arrival. Suppliers should verify that materials meet specified standards before they enter the production process.
– In-Process Quality Control (IPQC): During manufacturing, various checkpoints are established to monitor the assembly and finishing stages. This includes checking for dimensional accuracy, structural integrity, and surface quality.
– Final Quality Control (FQC): Once production is complete, a final inspection is conducted to ensure that the finished products meet all quality specifications. This may include testing for load-bearing capabilities and visual inspections for defects. -
Common Testing Methods
Various testing methods are employed to ensure quality, including:
– Load Testing: To assess the strength and durability of the stools.
– Stability Testing: Ensuring that the stools remain upright under various conditions.
– Finish Testing: Checking the durability and appearance of the applied finishes.
How Can B2B Buyers Verify Supplier Quality Control?
International B2B buyers need to ensure that their suppliers maintain high-quality standards. Here are some actionable strategies to verify supplier quality control:
-
Audits
Conducting supplier audits is an effective way to assess manufacturing practices and quality control measures. These audits can be either announced or unannounced, providing insights into the supplier’s operational integrity. -
Requesting Quality Reports
Buyers should ask suppliers for detailed quality reports that outline inspection results, testing methods, and compliance with relevant standards. This transparency can help establish trust and ensure that the manufacturer prioritizes quality. -
Third-Party Inspections
Engaging third-party inspection services can provide an unbiased assessment of a supplier’s quality control processes. These inspectors can verify compliance with international standards and provide detailed reports on their findings.
What Nuances Should International B2B Buyers Consider Regarding QC?
B2B buyers from diverse regions like Africa, South America, the Middle East, and Europe should be aware of specific nuances related to quality control:
-
Cultural and Regulatory Differences
Understanding local regulations and cultural expectations regarding quality can impact purchasing decisions. For instance, European buyers may place higher emphasis on environmental sustainability and material sourcing compared to buyers from other regions. -
Language Barriers
Communication challenges may arise when discussing quality control standards. Buyers should ensure that suppliers provide documentation in a language they understand, or consider hiring translators to facilitate clear communication. -
Logistical Challenges
The geographical location of suppliers can influence lead times and shipping costs. Buyers should consider whether suppliers can meet their quality standards within reasonable shipping times to avoid delays.
By understanding the manufacturing processes and quality assurance practices of bar stool manufacturers, international B2B buyers can make informed decisions that align with their quality expectations and business needs.
Practical Sourcing Guide: A Step-by-Step Checklist for ‘bar stool manufacturer’
In the competitive landscape of sourcing bar stools, international B2B buyers must navigate a series of critical steps to ensure they select the right manufacturer. This guide offers a practical checklist to streamline the sourcing process, from defining your requirements to evaluating potential suppliers.
Step 1: Define Your Technical Specifications
Establishing clear technical specifications is the foundation of a successful sourcing strategy. Determine the materials, dimensions, weight capacity, and design features that align with your market needs. This clarity will help you communicate effectively with potential suppliers and ensure that the products meet your quality standards.
Step 2: Research and Identify Potential Suppliers
Conduct thorough research to create a list of potential bar stool manufacturers. Utilize online platforms, industry directories, and trade shows to gather information. Look for suppliers with a solid reputation and experience in producing similar products. This step is vital as it sets the stage for your sourcing decisions.
Step 3: Evaluate Supplier Certifications and Compliance
Before proceeding with any supplier, verify their certifications and compliance with industry standards. Check for ISO certifications, safety standards, and any relevant regulatory compliance specific to your target market. This due diligence minimizes risks associated with quality issues and ensures that your products adhere to necessary regulations.
Step 4: Request Samples for Quality Assessment
Always request product samples before placing a bulk order. This allows you to assess the quality, craftsmanship, and durability of the bar stools firsthand. Inspect the materials used and the overall finish. Samples provide an opportunity to identify any discrepancies between what was promised and what is delivered.
Step 5: Analyze Pricing and Payment Terms
Once you have shortlisted suppliers, analyze their pricing structures and payment terms. Ensure the pricing aligns with your budget while also considering the quality of the product. Look for transparency in payment terms, including deposits, balance payments, and any additional fees that may apply. This understanding helps in managing your cash flow effectively.
Step 6: Check References and Customer Feedback
Reach out to previous customers to gain insights into their experiences with the supplier. Ask about product quality, delivery times, and after-sales support. Customer feedback is invaluable in assessing the reliability and credibility of a manufacturer, especially when sourcing from international suppliers.
Step 7: Negotiate Terms and Finalize the Agreement
After selecting a supplier, engage in negotiations to finalize terms that benefit both parties. Discuss lead times, minimum order quantities, and any customization options. A well-structured agreement should cover warranties, return policies, and dispute resolution mechanisms, ensuring that you are protected throughout the transaction.
By following these steps, B2B buyers can effectively navigate the complexities of sourcing bar stools and establish fruitful partnerships with reliable manufacturers. This proactive approach not only mitigates risks but also enhances the overall quality and satisfaction of your procurement process.
Comprehensive Cost and Pricing Analysis for bar stool manufacturer Sourcing
When sourcing bar stools, international B2B buyers must understand the comprehensive cost structure and pricing analysis. This knowledge will empower buyers from regions like Africa, South America, the Middle East, and Europe to make informed purchasing decisions.
What Are the Key Cost Components in Bar Stool Manufacturing?
Understanding the cost components involved in bar stool manufacturing can provide insight into pricing structures. Here are the primary cost elements:
-
Materials: The choice of materials significantly impacts cost. Common materials include wood, metal, and upholstery. Higher-quality materials typically yield a higher price but can enhance durability and aesthetic appeal.
-
Labor: Labor costs vary by region and manufacturing process. Countries with lower wage standards may offer competitive pricing, but this could affect quality and craftsmanship.
-
Manufacturing Overhead: This includes costs related to factory operations such as utilities, rent, and equipment maintenance. Efficient production processes can help minimize these costs.
-
Tooling: Initial tooling costs can be substantial, especially for custom designs. Buyers should consider whether the tooling cost is absorbed in the unit price or charged separately.
-
Quality Control (QC): Investing in quality control ensures that products meet specified standards. This cost is often reflected in the final pricing, as manufacturers who prioritize QC may charge more.
-
Logistics: Shipping costs can vary widely based on distance, shipping method, and volume. Understanding these logistics is critical for budgeting.
-
Margin: Manufacturers typically add a profit margin to their costs. This can vary based on market competition and demand.
How Do Price Influencers Affect Bar Stool Costs?
Several factors can influence the pricing of bar stools beyond the basic cost structure:
-
Volume and Minimum Order Quantity (MOQ): Larger orders usually lead to lower per-unit costs. Understanding a supplier’s MOQ can help buyers negotiate better deals.
-
Specifications and Customization: Custom designs or specifications can increase costs due to additional materials or labor. Buyers should weigh the benefits of customization against potential price hikes.
-
Materials and Quality Certifications: Premium materials and certifications (e.g., eco-friendly or safety standards) can lead to higher prices. Buyers should evaluate whether these factors align with their brand values and target market.
-
Supplier Factors: The reliability and reputation of suppliers can impact pricing. Established suppliers may charge more for their assurance of quality and service.
-
Incoterms: The choice of Incoterms can significantly affect total costs. Buyers should clarify who bears responsibility for shipping, insurance, and customs duties to avoid unexpected expenses.
What Tips Can Help B2B Buyers Negotiate Better Prices?
For international B2B buyers, particularly those from Nigeria, Poland, and other regions, here are actionable tips for securing favorable pricing:
-
Negotiate Terms: Don’t hesitate to negotiate payment terms, delivery schedules, and bulk pricing. Suppliers may be willing to offer discounts or favorable terms to secure a deal.
-
Focus on Cost-Efficiency: Evaluate total cost of ownership rather than just the purchase price. Consider factors like durability, maintenance, and shipping costs over the product’s lifecycle.
-
Understand Pricing Nuances: Familiarize yourself with regional pricing trends and currency fluctuations. This knowledge can help you negotiate more effectively and avoid overpaying.
-
Build Relationships: Establishing a good rapport with suppliers can lead to better pricing and terms. Long-term partnerships often result in loyalty discounts and priority service.
Disclaimer for Indicative Prices
Prices can fluctuate based on market conditions, material availability, and supplier changes. Buyers should obtain detailed quotes tailored to their specific needs to ensure accurate budgeting and decision-making.
Alternatives Analysis: Comparing bar stool manufacturer With Other Solutions
Understanding Alternatives to Bar Stool Manufacturing
In the competitive realm of furniture production, particularly in the bar stool sector, it’s essential to evaluate various manufacturing methods and solutions. This analysis provides insights into alternative approaches to traditional bar stool manufacturing, highlighting their advantages and drawbacks. International B2B buyers, especially from regions like Africa, South America, the Middle East, and Europe, can benefit from understanding these options to make informed purchasing decisions.
Comparison Table of Bar Stool Manufacturing vs. Alternatives
Comparison Aspect | Bar Stool Manufacturer | Modular Furniture Systems | 3D Printing Solutions |
---|---|---|---|
Performance | High durability; customizable designs | Flexible configurations; moderate durability | Rapid prototyping; limited material choices |
Cost | Moderate to high (bulk discounts available) | Varies widely; potential for lower initial costs | High setup costs; material costs can add up |
Ease of Implementation | Requires dedicated space and skilled labor | Easy assembly; minimal training needed | Requires specialized knowledge and equipment |
Maintenance | Regular upkeep needed; sturdy | Low maintenance; easy to clean | Limited lifespan; material degradation over time |
Best Use Case | Bars, restaurants, high-end venues | Casual dining, flexible spaces | Prototyping, unique design projects |
Detailed Breakdown of Alternative Solutions
What Are Modular Furniture Systems and Their Advantages?
Modular furniture systems offer flexibility and adaptability, making them ideal for businesses that require dynamic setups. These systems can be rearranged to suit various layouts, which is particularly beneficial in restaurants and cafes that change their configurations frequently. The major advantage is the ease of assembly, which reduces labor costs and time. However, while they are often more affordable upfront, the durability may not match that of traditional bar stools, making them less suitable for high-traffic environments.
How Can 3D Printing Solutions Transform Bar Stool Design?
3D printing is a revolutionary technology that allows for rapid prototyping and the creation of highly customizable designs. This method is perfect for businesses looking to create unique bar stools that reflect their brand identity. The major advantage of 3D printing is the ability to produce intricate designs with minimal material waste. However, the initial setup costs can be high, and the range of materials available may limit the durability and functionality of the stools. This option is best suited for businesses focusing on innovation and design rather than mass production.
Conclusion: Choosing the Right Solution for Your Needs
When deciding between traditional bar stool manufacturing and alternative solutions, B2B buyers must consider their specific requirements, including budget, design flexibility, and long-term maintenance. Buyers in Africa, South America, the Middle East, and Europe should assess the volume of stools needed, the nature of their business, and how frequently they anticipate needing to change their setup. By weighing these factors against the performance, cost, and ease of implementation of each option, buyers can make an informed choice that best suits their operational needs.
Essential Technical Properties and Trade Terminology for bar stool manufacturer
What Are the Essential Technical Properties for Bar Stool Manufacturing?
When sourcing bar stools, understanding the technical properties is crucial for ensuring quality, durability, and safety. Here are some key specifications that international B2B buyers should consider:
-
Material Grade
The material used in bar stools significantly influences their strength and durability. Common materials include metal (such as stainless steel and aluminum), wood (varieties like oak or maple), and synthetic materials (like polypropylene). For instance, stainless steel offers corrosion resistance, making it ideal for high-humidity environments like bars. Buyers should verify the grade of materials to ensure they meet industry standards and customer expectations. -
Weight Capacity
Each bar stool must be able to support a specific weight limit to ensure safety and usability. Typically, commercial-grade bar stools should accommodate at least 250-300 pounds. Manufacturers often provide this information in their specifications, which is vital for B2B buyers to consider, especially for high-traffic venues. -
Tolerance Levels
Tolerance refers to the acceptable range of variation in a product’s dimensions. For bar stools, this might include height, width, and depth. Tight tolerances ensure that parts fit together correctly during assembly and that the final product meets design specifications. Buyers should look for manufacturers who can maintain precise tolerances to avoid issues in functionality and aesthetic appeal. -
Finish Quality
The finish on bar stools not only impacts their appearance but also their resistance to wear and tear. Common finishes include powder coating, varnishing, and anodizing. Each finish has its benefits; for instance, powder-coated finishes are durable and easy to clean, making them suitable for commercial use. Understanding the type of finish can help buyers predict the maintenance required over the product’s lifespan. -
Ergonomics
Ergonomic design is crucial for comfort, especially in commercial settings where patrons may sit for extended periods. Features such as seat height, backrest angle, and footrest placement can enhance the user experience. B2B buyers should prioritize manufacturers who emphasize ergonomics in their designs to ensure customer satisfaction.
What Are Common Trade Terms Used in Bar Stool Manufacturing?
Understanding industry jargon is essential for effective communication and negotiation. Here are some common terms that B2B buyers should be familiar with:
-
OEM (Original Equipment Manufacturer)
OEM refers to a company that produces parts or equipment that may be marketed by another manufacturer. For bar stools, buyers may engage with OEMs to customize products to meet specific needs, such as branding or design variations. -
MOQ (Minimum Order Quantity)
MOQ is the smallest number of units that a supplier is willing to sell. This is particularly important for international buyers as it can impact pricing and inventory management. Understanding MOQ helps in planning purchases effectively and negotiating better terms with suppliers. -
RFQ (Request for Quotation)
An RFQ is a document sent to suppliers to solicit price quotes for specific products or services. In the context of bar stools, buyers use RFQs to gather competitive pricing and terms from multiple manufacturers, facilitating informed decision-making. -
Incoterms (International Commercial Terms)
Incoterms are internationally recognized standard trade terms that define the responsibilities of buyers and sellers in international transactions. Understanding these terms is crucial for buyers to know their obligations regarding shipping, insurance, and customs clearance, which can significantly affect overall costs. -
Lead Time
Lead time refers to the amount of time it takes from placing an order until the product is delivered. For bar stools, lead times can vary significantly based on manufacturing processes and shipping logistics. Buyers should clarify lead times during negotiations to align with their project timelines.
By familiarizing themselves with these technical properties and trade terms, B2B buyers can make more informed decisions when sourcing bar stools, ensuring they meet both quality standards and business needs.
Navigating Market Dynamics and Sourcing Trends in the bar stool manufacturer Sector
What Are the Key Market Dynamics and Trends in the Bar Stool Manufacturing Sector?
The bar stool manufacturing sector is experiencing significant transformations driven by evolving consumer preferences, technological advancements, and global supply chain dynamics. One of the primary drivers is the growing demand for customizable and ergonomic designs, particularly in hospitality and residential settings. Buyers from regions such as Africa, South America, the Middle East, and Europe are increasingly looking for unique styles that cater to local tastes while maintaining functionality.
Emerging trends include the integration of smart technology into furniture design, enhancing user experience with features such as adjustable height and built-in charging ports. Additionally, the use of e-commerce platforms for sourcing is on the rise, enabling international buyers to access a broader range of manufacturers and products. This shift is particularly beneficial for buyers in Nigeria and Poland, where online purchasing can significantly streamline procurement processes.
The market dynamics are also influenced by fluctuations in raw material costs and availability, necessitating strategic partnerships with suppliers. For international B2B buyers, understanding these trends is crucial for making informed sourcing decisions and staying competitive in a rapidly changing marketplace.
How Can Sustainability and Ethical Sourcing Impact Bar Stool Manufacturing?
Sustainability has become a cornerstone in the bar stool manufacturing sector, reflecting a growing awareness of environmental impact among consumers and businesses alike. International buyers are increasingly prioritizing suppliers who demonstrate a commitment to sustainable practices, such as using reclaimed wood, recycled metals, and eco-friendly finishes.
Ethical sourcing is equally important; it ensures that materials are obtained from suppliers who adhere to fair labor practices and environmental regulations. Certifications such as FSC (Forest Stewardship Council) for wood products and ISO standards for manufacturing processes are becoming essential for buyers in regions like Europe, where regulatory compliance is stringent.
Incorporating sustainable materials not only reduces the carbon footprint but also appeals to eco-conscious consumers, thereby enhancing brand reputation. For buyers in the Middle East and South America, sourcing from manufacturers who prioritize ethical supply chains can provide a competitive edge in markets increasingly driven by corporate social responsibility.
What is the Historical Context of the Bar Stool Manufacturing Sector?
The bar stool manufacturing sector has evolved significantly over the past century, transitioning from basic, functional designs to sophisticated, ergonomic solutions that reflect current lifestyle trends. Initially, bar stools were predominantly made from heavy materials like wood and metal, focusing primarily on durability.
With the rise of the mid-century modern movement in the 1950s and 1960s, designs began to incorporate lighter materials and innovative forms, catering to a more diverse clientele. In recent years, the focus has shifted toward customization and sustainability, with manufacturers adopting advanced technologies such as CNC machining and 3D printing to meet diverse consumer demands.
For B2B buyers, understanding this evolution is essential for identifying potential suppliers that align with contemporary market demands and sustainability goals. Recognizing the historical context of the sector can aid in making informed purchasing decisions that resonate with current consumer trends.
Frequently Asked Questions (FAQs) for B2B Buyers of bar stool manufacturer
-
How do I find a reliable bar stool manufacturer for my business?
Finding a reliable bar stool manufacturer involves thorough research and vetting. Start by checking online directories, trade platforms, and industry associations. Look for manufacturers with a proven track record and positive reviews from previous clients. Contact them to inquire about their production capabilities, quality control processes, and client references. Additionally, consider visiting their factory if possible to assess their operations firsthand, ensuring they meet your quality and ethical standards. -
What customization options are available when sourcing bar stools?
Most bar stool manufacturers offer a range of customization options including materials, colors, sizes, and styles. You can request specific designs that align with your brand identity, such as unique upholstery or finishes. It’s essential to communicate your requirements clearly and verify if the manufacturer can accommodate your requests within your budget and timeline. Some manufacturers may also provide prototype samples to help visualize the final product before bulk production. -
What is the minimum order quantity (MOQ) for bar stools?
The minimum order quantity (MOQ) for bar stools varies by manufacturer and can range from as low as 50 to over 500 units. Larger manufacturers may offer lower MOQs, while smaller or specialized producers might have higher requirements. When negotiating, consider your current inventory needs and budget. It’s also beneficial to ask about tiered pricing options for larger orders, which can help reduce costs per unit. -
What payment terms should I expect when purchasing bar stools internationally?
Payment terms in international B2B transactions typically include options like wire transfers, letters of credit, or payment through secure escrow services. Common practices involve a deposit upfront (usually 30-50%) with the balance due upon shipment or delivery. Ensure you clarify payment terms with the manufacturer before finalizing your order to avoid misunderstandings. Additionally, consider the implications of currency exchange rates and potential transaction fees. -
How can I ensure quality assurance for my bar stools?
To ensure quality assurance, request detailed information about the manufacturer’s quality control processes. This includes inspections at different production stages and compliance with international standards (e.g., ISO certification). You might also consider third-party quality inspection services before shipment to verify that the products meet your specifications. Establishing clear quality expectations in your contract can further protect your interests. -
What logistics considerations should I keep in mind when importing bar stools?
When importing bar stools, consider shipping methods, costs, and timelines. Discuss with the manufacturer whether they handle logistics or if you need to arrange transportation. Understand the incoterms (International Commercial Terms) that specify who is responsible for shipping, insurance, and customs clearance. Additionally, be aware of import duties and regulations in your country to avoid unexpected costs and delays. -
Are there any specific regulations for importing furniture like bar stools?
Yes, importing furniture, including bar stools, may involve compliance with specific regulations regarding safety, materials, and labeling. Different countries have different standards, such as fire safety requirements and restrictions on certain materials (e.g., chemicals used in finishes). It’s crucial to research and ensure that the products meet your country’s regulations to avoid customs issues and potential fines. -
What are the trends influencing the bar stool market today?
Current trends in the bar stool market include a growing demand for sustainable materials, ergonomic designs, and multifunctional furniture that suits various spaces. Consumers are increasingly looking for stylish options that complement their interior design while providing comfort. Manufacturers are responding by offering eco-friendly materials and customizable designs. Staying informed about these trends can help you select products that appeal to your target market and enhance your competitive edge.
Important Disclaimer & Terms of Use
⚠️ Important Disclaimer
The information provided in this guide, including content regarding manufacturers, technical specifications, and market analysis, is for informational and educational purposes only. It does not constitute professional procurement advice, financial advice, or legal advice.
While we have made every effort to ensure the accuracy and timeliness of the information, we are not responsible for any errors, omissions, or outdated information. Market conditions, company details, and technical standards are subject to change.
B2B buyers must conduct their own independent and thorough due diligence before making any purchasing decisions. This includes contacting suppliers directly, verifying certifications, requesting samples, and seeking professional consultation. The risk of relying on any information in this guide is borne solely by the reader.
Strategic Sourcing Conclusion and Outlook for bar stool manufacturer
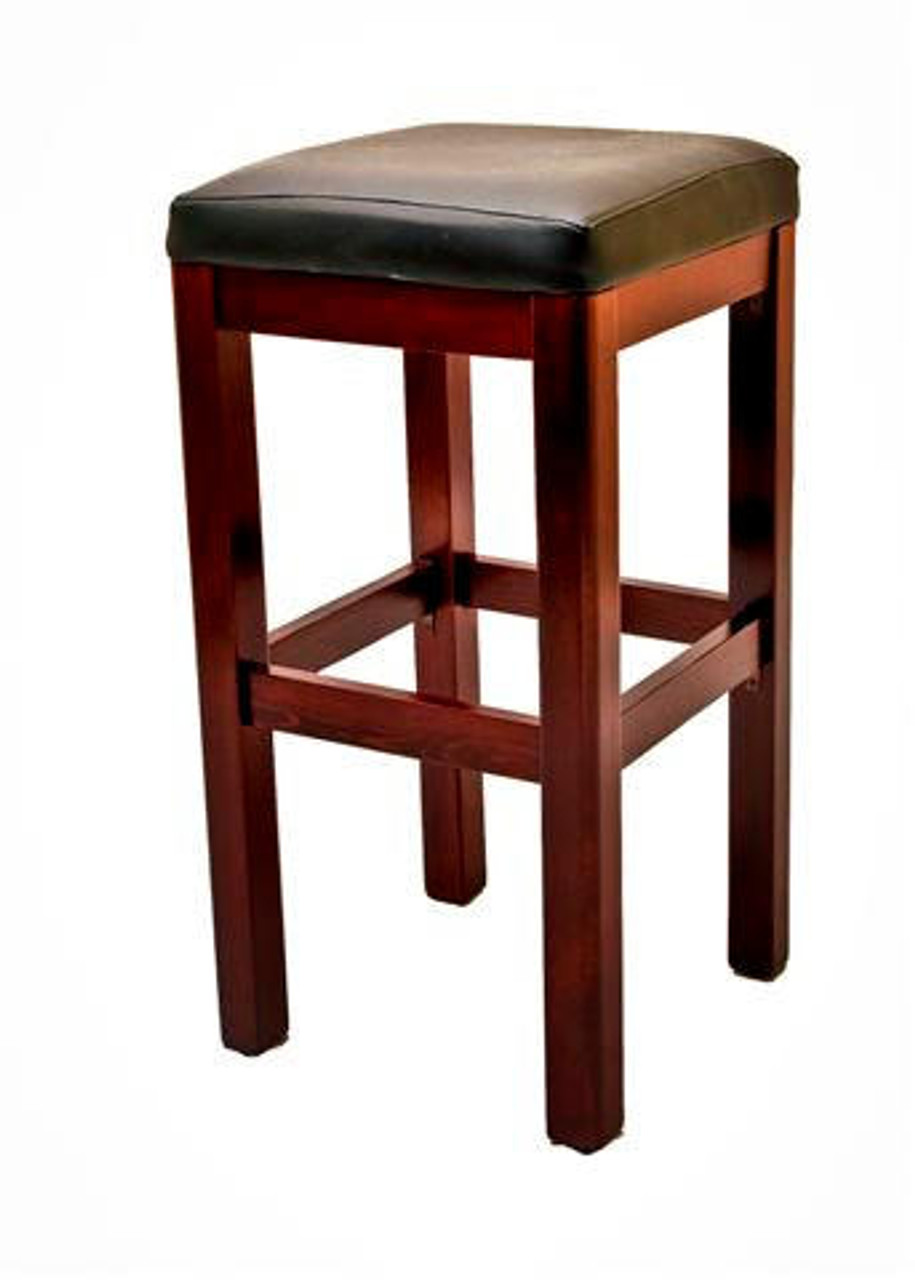
A stock image related to bar stool manufacturer.
Strategic sourcing is essential for international B2B buyers in the bar stool manufacturing industry, particularly those from Africa, South America, the Middle East, and Europe. By leveraging strategic sourcing practices, buyers can enhance supplier relationships, optimize costs, and ensure a consistent supply of high-quality products that meet regional preferences and regulatory standards. Key takeaways include the importance of thorough supplier vetting, understanding local market dynamics, and being aware of logistical considerations that can impact delivery timelines and costs.
As markets continue to evolve, particularly in emerging economies, buyers must remain agile and informed. Engaging with manufacturers that prioritize sustainability and innovation will not only align with global trends but also resonate with increasingly conscious consumers.
Looking ahead, the bar stool market presents vast opportunities for growth and diversification. International B2B buyers are encouraged to take proactive steps in their sourcing strategies. By forging partnerships with reputable manufacturers and staying updated on industry trends, businesses can position themselves for long-term success. Now is the time to harness the power of strategic sourcing to drive competitive advantage and meet the demands of a dynamic marketplace.