Discover the Best Slider Manufacturer: Your Ultimate Guide (2025)
Introduction: Navigating the Global Market for slider manufacturer
In today’s interconnected world, sourcing high-quality sliders from reliable manufacturers poses a significant challenge for international B2B buyers, especially those operating in diverse markets like Africa, South America, the Middle East, and Europe. Sliders, essential components in various industries—from automotive to electronics—require careful consideration in terms of quality, cost, and supplier credibility. This guide aims to demystify the global market for slider manufacturers, offering insights into the various types of sliders available, their applications, and the intricacies of supplier vetting processes.
Understanding the nuances of slider manufacturing can empower buyers to make informed purchasing decisions, ensuring that they select the right products for their specific needs. Throughout this guide, we will explore critical factors such as material specifications, design variations, and potential applications, while also addressing the importance of supplier certifications and quality assurance practices. Additionally, we will provide a comprehensive overview of cost considerations, helping buyers to navigate pricing structures effectively.
By equipping international B2B buyers with actionable insights and strategic approaches, this guide serves as a valuable resource in the quest for high-quality slider manufacturers. Whether you are based in bustling urban centers or emerging markets, the information presented here will enable you to forge successful partnerships and drive your business forward in the competitive landscape of slider manufacturing.
Understanding slider manufacturer Types and Variations
Type Name | Key Distinguishing Features | Primary B2B Applications | Brief Pros & Cons for Buyers |
---|---|---|---|
Linear Slider Manufacturers | Focus on linear motion systems with high precision and durability | Robotics, CNC machines, automation | Pros: High accuracy, robust construction. Cons: Typically higher costs. |
Rotary Slider Manufacturers | Designs that allow for rotational movement, often compact | Automotive, machinery, electronics | Pros: Space-saving, versatile. Cons: Limited range of motion compared to linear sliders. |
Miniature Slider Manufacturers | Small-sized sliders ideal for tight spaces and portable devices | Consumer electronics, medical devices | Pros: Lightweight, easy integration. Cons: May sacrifice strength for size. |
Heavy-Duty Slider Manufacturers | Built to withstand extreme conditions and heavy loads | Industrial machinery, construction | Pros: Exceptional durability, high load capacity. Cons: Bulkier and heavier. |
Adjustable Slider Manufacturers | Offer customizable features for varying applications | Furniture, HVAC systems, automotive | Pros: Flexibility in design, tailored solutions. Cons: Potentially complex installation. |
What are the Key Characteristics of Linear Slider Manufacturers?
Linear slider manufacturers specialize in products that facilitate linear motion, essential for applications requiring precise positioning. These sliders are often constructed from high-quality materials to ensure durability and reliability in demanding environments. They are particularly suitable for industries such as robotics and CNC machining, where precision is paramount. Buyers should consider the specific load capacities and dimensional tolerances when selecting linear sliders to ensure they meet their operational requirements.
How Do Rotary Slider Manufacturers Differ from Others?
Rotary slider manufacturers focus on producing sliders that allow for rotational movement, making them ideal for applications in automotive and electronic sectors. These sliders are typically designed to be compact, maximizing space efficiency in machinery and devices. B2B buyers should evaluate the range of motion and torque specifications to ensure compatibility with their projects. While rotary sliders offer versatility, their movement range may be limited compared to linear options, which is a critical consideration for certain applications.
What Advantages Do Miniature Slider Manufacturers Offer?
Miniature slider manufacturers create small-scale sliders that are perfect for applications in consumer electronics and medical devices where space is at a premium. These sliders are lightweight and easy to integrate into compact designs. Buyers should assess the strength and durability of miniature sliders, as they may not support as much load as larger counterparts. While they provide excellent space-saving solutions, the trade-off often involves reduced strength, making them suitable only for specific applications.
Why Choose Heavy-Duty Slider Manufacturers?
Heavy-duty slider manufacturers produce robust sliders designed to handle extreme conditions and heavy loads, making them ideal for industrial machinery and construction equipment. Their construction typically involves high-strength materials that provide exceptional durability. Buyers in sectors that require reliable performance under harsh conditions should prioritize heavy-duty options. However, these sliders can be bulkier and heavier, which may limit their use in applications where weight and space are concerns.
What Are the Benefits of Adjustable Slider Manufacturers?
Adjustable slider manufacturers focus on providing customizable slider solutions that can adapt to various applications, such as furniture and HVAC systems. These sliders allow for flexibility in design and can be tailored to meet specific operational needs. B2B buyers should consider the complexity of installation and potential need for adjustments in their setup. While adjustable sliders offer great versatility, they may require more time and resources to implement effectively compared to standard slider options.
Key Industrial Applications of slider manufacturer
Industry/Sector | Specific Application of slider manufacturer | Value/Benefit for the Business | Key Sourcing Considerations for this Application |
---|---|---|---|
Automotive | Adjustable sliders in vehicle seat mechanisms | Enhanced comfort and safety for passengers | Durability, compliance with safety standards, customization options |
Electronics | Volume control sliders in audio equipment | Improved user experience and product functionality | Precision, reliability, and compatibility with existing designs |
Industrial Automation | Linear position sliders in robotic arms | Increased efficiency and accuracy in manufacturing processes | Load capacity, ease of integration, and maintenance requirements |
Medical Devices | Adjustable sliders in diagnostic and therapeutic equipment | Enhanced patient comfort and precise diagnostics | Biocompatibility, regulatory compliance, and ease of cleaning |
Consumer Goods | Sliders in kitchen appliances for temperature control | Improved usability and customer satisfaction | Aesthetic design, durability, and energy efficiency |
How Are Sliders Used in the Automotive Industry?
In the automotive sector, sliders are integral to adjustable seating mechanisms, allowing users to customize their seating position for comfort and safety. They solve issues related to ergonomics and space management, accommodating different body types and preferences. For international buyers, it’s crucial to consider the durability of materials used in sliders, ensuring they meet safety regulations specific to their regions, such as those in Europe or the Middle East.
What Role Do Sliders Play in Electronics?
In electronics, sliders are commonly found in volume control knobs for audio devices. They enhance the user experience by providing intuitive control over sound levels. Buyers in this sector should prioritize precision engineering and reliability, as these factors significantly influence product performance and customer satisfaction. Ensuring compatibility with existing electronic designs is also essential for seamless integration.
How Are Sliders Beneficial in Industrial Automation?
Sliders are utilized in robotic arms within industrial automation, allowing for linear position adjustments. This application increases manufacturing efficiency and accuracy, addressing common challenges in production lines. For B2B buyers, sourcing sliders requires a focus on load capacity and ease of integration with existing systems. Maintenance considerations are also important to ensure long-term reliability in high-demand environments.
Why Are Sliders Important in Medical Devices?
In the medical field, sliders are incorporated into diagnostic and therapeutic equipment to allow for adjustable settings that enhance patient comfort and treatment accuracy. They help solve problems related to patient positioning and equipment usability. Buyers in this industry must consider biocompatibility and compliance with medical regulations, along with the ease of cleaning and maintenance to ensure optimal hygiene.
How Do Sliders Enhance Consumer Goods?
In consumer goods, sliders are often found in kitchen appliances, facilitating temperature control for ovens and refrigerators. This feature significantly enhances usability and customer satisfaction by allowing precise adjustments. When sourcing sliders for these applications, buyers should consider aesthetic design, durability, and energy efficiency to meet the demands of eco-conscious consumers and align with market trends.
Related Video: Types Of Flowmeters And Their Industrial Applications.
3 Common User Pain Points for ‘slider manufacturer’ & Their Solutions
Scenario 1: Inconsistent Quality in Slider Manufacturing
The Problem:
B2B buyers often face significant challenges with inconsistent quality from slider manufacturers. For instance, a buyer from South America sourcing sliders for a new product line may receive batches that vary in dimensions, materials, or performance. This inconsistency can lead to delays in production, increased costs due to rework, and ultimately damage to the buyer’s reputation in the market. In industries where precision is paramount, such as automotive or aerospace, even minor discrepancies can result in severe operational issues.
The Solution:
To mitigate quality inconsistencies, buyers should adopt a rigorous supplier evaluation process. This includes conducting thorough audits of the manufacturer’s facilities and quality control systems. Implementing a quality assurance agreement that specifies acceptable tolerances and performance metrics is essential. Additionally, establishing a robust communication channel with the manufacturer can facilitate real-time updates on production processes and any potential issues. Buyers should also consider integrating third-party inspections or certifications to ensure the sliders meet their specifications before shipment. By investing time in supplier relationships and quality assurance measures, buyers can significantly reduce the risk of receiving subpar products.
Scenario 2: Limited Customization Options for Specific Applications
The Problem:
International buyers often encounter difficulties when seeking customized slider solutions tailored to their unique applications. For example, a company in the Middle East may require sliders that can withstand extreme temperatures and humidity for outdoor equipment. However, many manufacturers offer only standard options, leaving buyers frustrated and forced to compromise on their specifications, which can lead to performance failures and safety concerns.
The Solution:
To address this pain point, buyers should proactively communicate their specific needs during the initial stages of engagement with manufacturers. It is crucial to provide detailed specifications, including environmental conditions and load requirements. Buyers should seek out manufacturers with a proven track record in customization and those who offer flexible design services. Engaging in collaborative product development can also yield tailored solutions that meet exact requirements. It may be beneficial to explore regional manufacturers who understand local conditions and can provide bespoke designs. By emphasizing customization early in the procurement process, buyers can ensure they receive sliders that enhance product performance and reliability.
Scenario 3: Long Lead Times and Supply Chain Disruptions
The Problem:
Long lead times and unpredictable supply chain disruptions are common challenges faced by B2B buyers, particularly in Africa and Europe. A buyer may plan a product launch based on a specific timeline, but if the slider manufacturer experiences delays due to material shortages or logistical issues, the entire project can be jeopardized. This unpredictability not only strains resources but also impacts customer satisfaction and market competitiveness.
The Solution:
To combat lead time issues, buyers should prioritize manufacturers with robust supply chain management practices and transparent communication. Establishing long-term contracts can help secure priority status for orders, thereby reducing lead times. Buyers should also consider diversifying their supplier base to include multiple manufacturers, which can provide alternatives in case one supplier faces disruptions. Utilizing technology, such as supply chain tracking systems, can offer real-time updates on order status and potential delays. By being proactive and flexible in their sourcing strategies, buyers can better navigate the complexities of lead times and ensure a smoother procurement process.
Strategic Material Selection Guide for slider manufacturer
When selecting materials for slider manufacturing, international B2B buyers must consider various factors that influence product performance, durability, and cost-effectiveness. Below is an analysis of four common materials used in slider manufacturing, focusing on their properties, advantages, disadvantages, and specific considerations for buyers from Africa, South America, the Middle East, and Europe.
What Are the Key Properties of Aluminum for Slider Manufacturing?
Aluminum is a lightweight metal known for its excellent strength-to-weight ratio, corrosion resistance, and thermal conductivity. It typically has a temperature rating of up to 150°C, making it suitable for various applications, including automotive and electronics.
Pros:
– Durability: Aluminum is resistant to rust and corrosion, ensuring longevity in outdoor and humid environments.
– Cost-Effectiveness: It is relatively inexpensive compared to other metals like stainless steel.
– Manufacturing Flexibility: Aluminum can be easily extruded and machined, allowing for complex designs.
Cons:
– Lower Strength: While strong for its weight, aluminum may not be suitable for high-stress applications compared to steel.
– Thermal Expansion: Its thermal expansion properties can lead to dimensional changes under extreme temperatures.
Impact on Application:
Aluminum sliders are ideal for applications requiring lightweight components, such as in automotive or portable devices. However, they may not be suitable for high-pressure environments.
How Does Stainless Steel Compare as a Material for Sliders?
Stainless steel is renowned for its exceptional strength, corrosion resistance, and high-temperature tolerance, often rated up to 800°C. It is commonly used in food processing and medical equipment due to its hygienic properties.
Pros:
– High Durability: Stainless steel is highly resistant to wear and tear, making it suitable for heavy-duty applications.
– Corrosion Resistance: It withstands harsh chemicals and environmental conditions, ensuring a longer lifespan.
– Aesthetic Appeal: Stainless steel has a polished finish that is visually appealing for consumer products.
Cons:
– Cost: Stainless steel is more expensive than aluminum, which can impact overall project budgets.
– Manufacturing Complexity: Machining stainless steel can be more challenging, requiring specialized tools and techniques.
Impact on Application:
Stainless steel sliders are perfect for applications in harsh environments, such as chemical processing or food production. They comply with international standards, making them a preferred choice for B2B buyers in regulated industries.
What Are the Benefits of Using Plastics in Slider Manufacturing?
Plastics, such as polycarbonate and nylon, offer a lightweight and cost-effective alternative for slider components. They can withstand temperatures from -40°C to 120°C, depending on the type.
Pros:
– Lightweight: Plastics significantly reduce the overall weight of products, enhancing portability.
– Cost-Effective: Generally cheaper than metals, making them ideal for budget-sensitive projects.
– Versatile: Available in various colors and finishes, allowing for customization.
Cons:
– Lower Strength: Plastics may not endure heavy loads or high-stress applications.
– Chemical Sensitivity: Some plastics can degrade when exposed to certain chemicals.
Impact on Application:
Plastic sliders are suitable for low-stress applications, such as consumer electronics and household items. Buyers must ensure compatibility with the intended media to avoid degradation.
Why Consider Composite Materials for Slider Applications?
Composite materials, like fiberglass-reinforced plastics, combine the benefits of different materials to enhance performance. They can be engineered for specific applications, offering tailored properties.
Pros:
– Tailored Properties: Composites can be designed to meet specific strength, weight, and thermal requirements.
– Corrosion Resistance: Many composites resist environmental degradation, extending product life.
– Lightweight: They provide a significant weight advantage over metals.
Cons:
– Cost: Composites can be more expensive than traditional materials due to specialized manufacturing processes.
– Manufacturing Complexity: The production of composite materials can be more complex, requiring skilled labor.
Impact on Application:
Composite sliders are ideal for high-performance applications in aerospace and automotive sectors, where weight and strength are critical. Compliance with international standards is essential for global buyers.
Summary Table of Material Selection for Slider Manufacturing
Material | Typical Use Case for Slider Manufacturer | Key Advantage | Key Disadvantage/Limitation | Relative Cost (Low/Med/High) |
---|---|---|---|---|
Aluminum | Automotive components | Lightweight and corrosion-resistant | Lower strength compared to steel | Medium |
Stainless Steel | Food processing equipment | High durability and corrosion resistance | Higher cost and manufacturing complexity | High |
Plastics | Consumer electronics | Lightweight and cost-effective | Lower strength and chemical sensitivity | Low |
Composites | Aerospace applications | Tailored properties and lightweight | Higher cost and manufacturing complexity | High |
This guide provides a comprehensive overview of material selection for slider manufacturing, helping international B2B buyers make informed decisions based on their specific needs and regional considerations.
In-depth Look: Manufacturing Processes and Quality Assurance for slider manufacturer
What Are the Key Stages in the Manufacturing Process of Sliders?
The manufacturing of sliders, commonly used in various applications such as electronics and automotive, involves several critical stages that ensure the final product meets the required specifications and standards. The main stages in the manufacturing process include material preparation, forming, assembly, and finishing.
-
Material Preparation:
The first step involves selecting and preparing high-quality materials, such as plastics or metals, suitable for slider production. This may include cutting raw materials to size, cleaning them to remove impurities, and ensuring they meet specified material standards. -
Forming Techniques:
During this stage, the prepared materials undergo various forming techniques. For plastic sliders, injection molding is a common method where heated plastic is injected into molds to create the desired shapes. For metal sliders, processes such as stamping, extrusion, or machining may be employed to achieve precise dimensions. -
Assembly Process:
After forming, the components are assembled. This could involve inserting sliders into housings, attaching them to other components, or integrating them with electronic circuitry. Automated assembly lines are often used for efficiency, though some complex assemblies may require manual intervention. -
Finishing:
The final stage involves surface treatment and finishing processes to enhance the product’s durability and aesthetic appeal. This can include painting, coating, or polishing, and may also involve quality checks to ensure that the finish meets customer specifications.
What Quality Control Measures Are Essential for Slider Manufacturers?
Quality assurance (QA) is crucial in the manufacturing of sliders to ensure that products meet international standards and customer expectations. For B2B buyers, understanding the quality control processes is essential for verifying supplier reliability.
-
Adherence to International Standards:
Most slider manufacturers aim to comply with internationally recognized quality standards such as ISO 9001. This standard ensures that manufacturers implement a quality management system focused on continuous improvement and customer satisfaction. Other industry-specific certifications, like CE marking for safety in Europe or API for oil and gas applications, may also be relevant. -
Key Quality Control Checkpoints:
Quality control is typically integrated into the manufacturing process through several checkpoints:
– Incoming Quality Control (IQC): This involves inspecting incoming raw materials to ensure they meet specified quality standards before production begins.
– In-Process Quality Control (IPQC): Throughout the manufacturing process, inspections are conducted to monitor the production stages and identify any defects early. This helps in maintaining quality consistency.
– Final Quality Control (FQC): Once the sliders are fully assembled, a final inspection is performed to ensure they meet all design and functional specifications before packaging and shipping. -
Common Testing Methods:
Manufacturers often employ a range of testing methods to validate product quality. These include:
– Dimensional Inspection: Using tools such as calipers or coordinate measuring machines (CMM) to ensure that the sliders are produced to the correct specifications.
– Functional Testing: Testing the sliders under operational conditions to ensure they perform as expected.
– Durability Tests: Assessing the sliders’ resistance to wear, environmental conditions, and other stressors to ensure longevity.
How Can B2B Buyers Verify Supplier Quality Control Processes?
For international B2B buyers, particularly those from Africa, South America, the Middle East, and Europe, verifying the quality control measures of potential suppliers is vital. Here are several strategies to consider:
-
Conducting Audits:
Regular audits of potential suppliers can provide insights into their manufacturing processes and quality control measures. Buyers can request to see the documentation of their quality management systems, including procedures, standards compliance, and records of past audits. -
Reviewing Quality Reports:
Suppliers should be able to provide detailed quality reports that outline their inspection results, defect rates, and corrective actions taken. This transparency can help buyers assess the reliability of the supplier’s quality control. -
Third-party Inspections:
Engaging third-party inspection services can offer an unbiased evaluation of the supplier’s manufacturing and quality control processes. These inspections can be particularly beneficial for buyers unfamiliar with local manufacturing standards or practices.
What Are the Unique Quality Assurance Considerations for International B2B Buyers?
International B2B buyers need to be aware of specific nuances in quality assurance when sourcing sliders from different regions:
-
Cultural and Regulatory Differences:
Different regions may have varying expectations regarding quality standards and compliance. For instance, European buyers might emphasize compliance with CE regulations, while Middle Eastern buyers may focus more on local certifications. Understanding these differences can help in evaluating suppliers effectively. -
Communication Barriers:
Language differences and cultural nuances can impact the flow of information regarding quality standards. Buyers should ensure that communication with suppliers is clear and that expectations regarding quality are well-defined and documented. -
Risk Management:
Buyers should implement risk management strategies to address potential quality issues. This may include developing contingency plans, establishing clear contractual obligations regarding quality, and maintaining ongoing communication with suppliers to address issues as they arise.
By focusing on these manufacturing processes and quality assurance practices, B2B buyers can make informed decisions when selecting slider manufacturers, ensuring they receive high-quality products that meet their operational requirements.
Practical Sourcing Guide: A Step-by-Step Checklist for ‘slider manufacturer’
Introduction
In the competitive landscape of B2B procurement, sourcing from slider manufacturers requires a systematic approach to ensure quality, reliability, and cost-effectiveness. This checklist serves as a practical guide for international buyers, especially those from Africa, South America, the Middle East, and Europe, aiming to streamline their sourcing process for slider manufacturing.
Step 1: Define Your Technical Specifications
Clearly outline the specifications of the sliders you need, including dimensions, materials, and performance requirements. This step is crucial because it sets the foundation for your sourcing process. Having precise specifications helps you communicate effectively with potential suppliers and ensures that you receive products that meet your operational needs.
- Consider the application: Different applications may require specific types of sliders, such as those that are waterproof or have high durability.
- Include tolerances and standards: Specify any industry standards that must be adhered to, such as ISO certifications.
Step 2: Conduct Market Research
Investigate the market to identify potential suppliers and understand pricing trends. Conducting thorough market research allows you to compare options effectively and make informed decisions.
- Utilize online platforms: Use B2B marketplaces and industry directories to find reputable slider manufacturers.
- Check industry reviews: Look for feedback on suppliers from other businesses to gauge their reliability and product quality.
Step 3: Evaluate Potential Suppliers
Before committing to any supplier, it’s essential to vet them thoroughly. Request company profiles, case studies, and references from buyers in similar industries or regions. This step is vital to ensure that you are partnering with a trustworthy manufacturer.
- Assess their production capabilities: Ensure the supplier has the necessary equipment and workforce to meet your production needs.
- Review their quality assurance processes: Inquire about quality control measures to ensure product consistency.
Step 4: Verify Certifications and Compliance
Ensure that the suppliers hold relevant certifications that comply with international standards. This step is critical for minimizing risks associated with quality and safety.
- Check for ISO certifications: ISO 9001 is a standard that indicates a commitment to quality management.
- Inquire about environmental compliance: If sustainability is important to your business, verify that the supplier adheres to environmental regulations.
Step 5: Request Samples
Before making a bulk order, request samples of the sliders to evaluate their quality and performance. This step is essential for validating that the product meets your specifications and quality expectations.
- Test for functionality: Ensure that the samples perform as required in your specific application.
- Assess materials and durability: Evaluate the materials used to determine if they meet your standards for longevity and performance.
Step 6: Negotiate Terms and Conditions
Once you have selected a potential supplier, negotiate the terms and conditions of the purchase. This step is crucial for establishing a mutually beneficial relationship and ensuring clarity on expectations.
- Discuss pricing and payment terms: Aim for transparency regarding costs, including shipping and potential tariffs.
- Clarify delivery schedules: Ensure that timelines for production and delivery align with your project requirements.
Step 7: Establish a Communication Plan
Effective communication is vital for successful collaboration with your supplier. Establish a clear communication plan that outlines how you will interact throughout the procurement process.
- Set regular check-ins: Schedule updates to discuss progress, address concerns, and make adjustments as necessary.
- Use collaborative tools: Consider using project management tools to facilitate better communication and tracking of deliverables.
By following these steps, international B2B buyers can navigate the complexities of sourcing sliders effectively, ensuring that they partner with the right manufacturers to meet their business needs.
Comprehensive Cost and Pricing Analysis for slider manufacturer Sourcing
What Are the Key Cost Components in Slider Manufacturing?
When sourcing sliders for your business, understanding the cost structure is crucial. The main components that contribute to the overall cost of slider manufacturing include:
-
Materials: The type and quality of materials used significantly affect pricing. Common materials include plastics, metals, and rubber, with high-quality materials commanding higher prices. Sustainable or specialty materials can further influence costs.
-
Labor: Labor costs vary by region and can be influenced by local wage rates, skill levels, and labor laws. Countries with lower labor costs may provide more competitive pricing but could also affect quality and lead times.
-
Manufacturing Overhead: This encompasses indirect costs related to production, such as utilities, rent, and equipment maintenance. Efficient manufacturing processes can help keep overhead low.
-
Tooling: Initial setup costs for molds and tooling can be substantial, especially for customized sliders. These costs are often amortized over larger production runs, making high-volume orders more cost-effective.
-
Quality Control (QC): Ensuring that sliders meet required specifications incurs costs related to inspection and testing. High-quality certifications (like ISO) can enhance product value but also add to the overall cost.
-
Logistics: Shipping and handling costs are crucial, especially for international buyers. Factors such as distance, shipping method, and customs duties can significantly impact total costs.
-
Margin: Manufacturers typically add a profit margin to cover business expenses and ensure profitability. This margin varies depending on market conditions and competitive positioning.
How Do Price Influencers Affect Slider Costs?
Several factors can influence the final price of sliders, particularly for international buyers:
-
Volume and Minimum Order Quantity (MOQ): Larger orders often lead to lower per-unit costs due to economies of scale. Understanding the MOQ for each manufacturer can help in negotiating better pricing.
-
Specifications and Customization: Custom designs or specific features can increase production complexity and costs. Clear specifications can help manufacturers provide accurate quotes.
-
Material Quality and Certifications: Higher quality materials and certifications can justify a premium price. It’s essential to balance quality needs with budget constraints.
-
Supplier Factors: The reputation and reliability of the supplier can influence pricing. Established suppliers may charge more but can offer better quality assurance and service.
-
Incoterms: Understanding Incoterms (International Commercial Terms) is vital for determining who bears shipping costs and risks. This can affect the total cost of ownership.
What Are Effective Buyer Tips for Sourcing Sliders?
For international B2B buyers, particularly from Africa, South America, the Middle East, and Europe, here are some actionable tips:
-
Negotiate with Suppliers: Don’t hesitate to negotiate pricing, especially for large orders or long-term contracts. Establishing a good relationship can lead to more favorable terms.
-
Focus on Cost-Efficiency: Consider the Total Cost of Ownership (TCO), which includes purchase price, shipping, handling, and potential warranty costs. A lower initial price may not always result in overall savings.
-
Understand Pricing Nuances: Different regions may have varied pricing structures based on local market conditions, tariffs, and logistics costs. Researching these nuances can inform better sourcing decisions.
-
Request Sample Products: Before committing to large orders, requesting samples can help assess quality and suitability. This step can prevent costly mistakes down the line.
-
Stay Informed on Market Trends: Keeping abreast of trends in materials and manufacturing processes can provide insights into potential cost savings and innovative solutions.
Disclaimer on Indicative Prices
It is important to note that prices can fluctuate based on market conditions, currency exchange rates, and supplier negotiations. Always seek updated quotes from multiple suppliers to ensure competitive pricing tailored to your specific needs.
Alternatives Analysis: Comparing slider manufacturer With Other Solutions
Understanding Alternatives to Slider Manufacturer Solutions
In the rapidly evolving landscape of industrial components, B2B buyers often face a critical decision: whether to invest in traditional slider manufacturers or explore alternative solutions that may offer enhanced performance, cost-effectiveness, or unique functionalities. This section delves into a comparative analysis of ‘slider manufacturer‘ against viable alternatives, helping buyers make informed choices tailored to their operational needs.
Comparison Table of Slider Manufacturer and Alternatives
Comparison Aspect | Slider Manufacturer | Linear Actuators | Digital Control Systems |
---|---|---|---|
Performance | High precision and reliability | Moderate precision, speed varies | High precision, programmable |
Cost | Moderate to high investment | Moderate investment | Higher initial investment |
Ease of Implementation | Straightforward installation | Requires technical setup | Requires software integration |
Maintenance | Low maintenance | Moderate maintenance | Low maintenance |
Best Use Case | Manual adjustments in machinery | Automated systems needing linear movement | Applications needing precise control |
In-Depth Look at Alternative Solutions
What Are Linear Actuators and How Do They Compare?
Linear actuators are mechanical devices that create linear motion from a rotational force. They are particularly useful in applications requiring automated movement, such as assembly lines and robotic systems.
Pros:
– Offer automation capabilities, reducing manual labor.
– Can achieve various speeds and force levels depending on the design.
Cons:
– Installation may require specialized knowledge, making initial setup more complex.
– Performance can vary widely based on the actuator type (electric, hydraulic, pneumatic).
How Do Digital Control Systems Enhance Performance?
Digital control systems leverage software to manage and control the movement of machinery and equipment. They allow for programmability, enabling precise control over various parameters.
Pros:
– Provide high precision and flexibility in operations.
– Programmable settings allow for customization based on specific tasks.
Cons:
– Typically come with a higher upfront cost due to the need for advanced technology.
– Require software and hardware integration, which may necessitate additional training for staff.
Conclusion: Choosing the Right Solution for Your Needs
When selecting between a slider manufacturer and alternative solutions like linear actuators or digital control systems, B2B buyers must assess their specific operational requirements, budget constraints, and desired performance levels. If your operations rely on manual adjustments and straightforward applications, a slider manufacturer may be ideal. Conversely, if automation and precise control are priorities, investing in linear actuators or digital control systems could offer significant long-term benefits. Ultimately, understanding the unique advantages and limitations of each solution will empower buyers to make the most informed decisions for their businesses.
Essential Technical Properties and Trade Terminology for slider manufacturer
What Are the Essential Technical Properties of Sliders for Manufacturers?
When sourcing sliders, international B2B buyers should understand key technical properties that influence performance, durability, and suitability for specific applications. Here are some critical specifications:
-
Material Grade
The material used in sliders significantly affects their strength, durability, and resistance to environmental factors. Common materials include stainless steel, aluminum, and plastic composites. Buyers should prioritize high-grade materials that align with the intended use, ensuring longevity and performance under varying conditions. -
Tolerance Levels
Tolerance refers to the allowable variation in dimensions of the slider components. High tolerance levels are crucial for applications requiring precision, such as in machinery or electronic devices. Understanding tolerance specifications helps buyers ensure compatibility with other components and maintain operational efficiency. -
Load Capacity
The load capacity indicates the maximum weight a slider can support without failure. This property is essential for applications in construction, automotive, and heavy machinery. Buyers should carefully assess load requirements to avoid product failure and ensure safety. -
Operating Temperature Range
Sliders may be subjected to various temperatures based on their application. Knowing the operating temperature range ensures that the chosen slider will perform optimally without deformation or degradation. Buyers in regions with extreme climates must pay special attention to this specification. -
Corrosion Resistance
Particularly for sliders used in outdoor or industrial settings, corrosion resistance is vital. Buyers should look for sliders treated with coatings or made from corrosion-resistant materials to prolong service life and reduce maintenance costs. -
Ease of Maintenance
Sliders that are easy to maintain can significantly reduce downtime and operational costs. Features like self-lubricating mechanisms or easy access for cleaning can enhance product value. Buyers should inquire about maintenance requirements to optimize long-term use.
What Are Common Trade Terms Used in Slider Manufacturing?
Familiarity with industry jargon can streamline communication and negotiations for international buyers. Here are some essential trade terms:
-
OEM (Original Equipment Manufacturer)
This term refers to a company that produces parts or equipment that may be marketed by another manufacturer. Understanding OEM relationships helps buyers identify reliable sources for custom sliders that meet specific needs. -
MOQ (Minimum Order Quantity)
MOQ is the smallest quantity of a product that a supplier is willing to sell. This term is crucial for budget planning, as higher MOQs may affect cash flow, especially for small businesses or startups. -
RFQ (Request for Quotation)
An RFQ is a document sent by buyers to suppliers requesting pricing and terms for specific products. Crafting a clear RFQ can lead to more accurate quotes and better negotiation outcomes. -
Incoterms (International Commercial Terms)
These are standardized terms that define the responsibilities of buyers and sellers in international trade. Familiarity with Incoterms helps buyers understand shipping costs, risk management, and delivery obligations. -
Lead Time
Lead time refers to the time taken from placing an order to the delivery of the product. Understanding lead times is vital for planning production schedules and inventory management. -
Certification Standards
Certifications, such as ISO or CE, indicate that a product meets specific safety and quality standards. Buyers should prioritize suppliers who comply with relevant certification standards to ensure product reliability and compliance with local regulations.
By understanding these technical properties and trade terms, international B2B buyers can make informed decisions when sourcing sliders, ultimately leading to better product performance and business success.
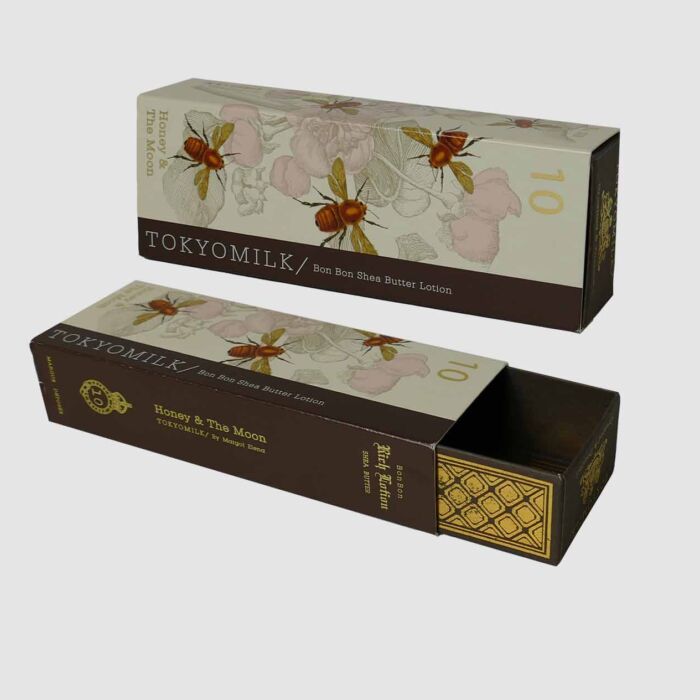
A stock image related to slider manufacturer.
Navigating Market Dynamics and Sourcing Trends in the slider manufacturer Sector
What Are the Current Market Dynamics and Sourcing Trends in the Slider Manufacturer Sector?
The slider manufacturing sector is witnessing significant transformation driven by technological advancements, market demands, and regional dynamics. A key global driver is the increasing automation and digitization across industries, particularly in manufacturing, electronics, and automotive sectors. This has led to a higher demand for precision-engineered sliders that can support advanced functionalities, such as smart home devices and automotive applications.
Emerging B2B tech trends include the integration of IoT (Internet of Things) capabilities into sliders, enabling real-time monitoring and control. Additionally, the rise of e-commerce platforms has shifted sourcing strategies, allowing international buyers from Africa, South America, the Middle East, and Europe to access a wider range of manufacturers. This has resulted in more competitive pricing and greater flexibility in sourcing options.
Moreover, market dynamics are heavily influenced by regional economic conditions. For instance, African buyers may focus on cost-effective solutions due to budget constraints, while European buyers might prioritize quality and sustainability. Understanding these regional nuances is essential for B2B buyers to effectively navigate the market and establish profitable partnerships.
How Is Sustainability Reshaping the Slider Manufacturer Supply Chain?
Sustainability is becoming a pivotal factor in sourcing decisions for B2B buyers in the slider manufacturing sector. The environmental impact of manufacturing processes has drawn increasing scrutiny, prompting companies to adopt greener practices. This shift is not only beneficial for the planet but also aligns with consumer preferences for environmentally responsible products.
Ethical sourcing is now a top priority, with businesses seeking suppliers that adhere to sustainable practices. This includes using recycled materials, minimizing waste, and ensuring fair labor conditions. Certifications such as ISO 14001 for environmental management and Fair Trade certifications are gaining prominence, as they provide assurance of a supplier’s commitment to sustainability.
For international buyers, particularly in regions like the Middle East and Europe, partnering with manufacturers that prioritize sustainability can enhance their brand image and appeal to eco-conscious consumers. As demand for ‘green’ products continues to rise, incorporating sustainability into sourcing strategies is not just an ethical imperative but a competitive advantage in the marketplace.
What Is the Historical Context of the Slider Manufacturing Industry?
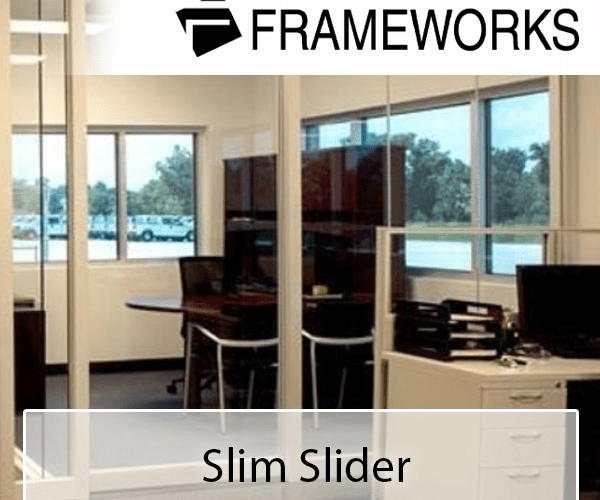
A stock image related to slider manufacturer.
The slider manufacturing industry has evolved significantly over the past few decades. Initially, sliders were primarily mechanical components used in basic applications. However, advancements in technology have transformed sliders into sophisticated devices that serve critical roles in various high-tech applications.
In the early 2000s, the introduction of electronic sliders marked a turning point, allowing for enhanced functionality and precision. As industries began embracing automation, the demand for high-quality sliders surged. Today, the focus has shifted toward integrating smart technology and sustainable practices, reflecting broader trends in consumer preferences and global economic conditions. This evolution underscores the importance of staying informed about technological advancements and market shifts for B2B buyers looking to source sliders effectively.
Frequently Asked Questions (FAQs) for B2B Buyers of slider manufacturer
-
How do I select the right slider manufacturer for my business needs?
Choosing the right slider manufacturer involves assessing various factors. Start by defining your specific requirements, including the type of slider, material specifications, and intended application. Research potential suppliers by checking their portfolios, customer reviews, and certifications. Engage in direct communication to understand their production capabilities, lead times, and willingness to accommodate customization. It’s also wise to request samples to evaluate quality before making a commitment. -
What are the key factors to consider when evaluating slider manufacturers?
When evaluating slider manufacturers, consider their industry experience, technological capabilities, and quality assurance processes. Look for manufacturers with a proven track record in producing sliders similar to your specifications. Certifications like ISO or industry-specific standards can indicate quality practices. Additionally, assess their production capacity, delivery timelines, and after-sales support to ensure they can meet your business demands consistently. -
What customization options are available when sourcing sliders from manufacturers?
Most slider manufacturers offer a range of customization options, including size, material, color, and functionality. You can often specify unique features such as locking mechanisms, surface finishes, or integration with other components. It’s essential to communicate your specific requirements early in the sourcing process. Requesting a prototype or sample can help verify that the manufacturer can meet your customization needs effectively. -
What is the typical minimum order quantity (MOQ) for sliders from manufacturers?
Minimum order quantities (MOQ) for sliders can vary significantly among manufacturers, typically ranging from 100 to 1,000 units or more. Factors influencing MOQ include the complexity of the slider design, material costs, and the manufacturer’s production capacity. When negotiating with suppliers, it’s beneficial to inquire about flexibility in MOQs, especially if you are a smaller business or just starting. -
What payment terms should I expect when dealing with slider manufacturers?
Payment terms can vary widely depending on the manufacturer and your negotiation. Common terms include a deposit (often 30-50%) upfront, with the balance due upon completion or before shipping. Some manufacturers may offer credit terms for established relationships. It’s crucial to clarify payment methods accepted, such as bank transfers or letters of credit, and ensure that these align with your financial practices. -
How can I ensure quality assurance when sourcing sliders internationally?
To ensure quality assurance when sourcing sliders, start by selecting manufacturers with robust quality management systems in place. Request documentation of their quality control processes, such as inspection reports and certifications. Consider conducting factory audits or hiring third-party inspection services to assess product quality before shipment. Establishing clear specifications and standards in your purchase agreement can also safeguard against quality issues. -
What logistics considerations should I keep in mind when importing sliders?
When importing sliders, consider logistics factors such as shipping methods, customs regulations, and delivery timelines. Choose between air freight for speed or sea freight for cost-effectiveness, depending on your urgency and budget. Research the import duties and taxes applicable in your country to avoid unexpected costs. Collaborating with a freight forwarder can help streamline the shipping process and ensure compliance with all regulations. -
How do I handle communication and time zone differences with international slider suppliers?
Effective communication with international slider suppliers is crucial, especially with time zone differences. Establish a regular communication schedule that accommodates both parties, utilizing tools like video calls or messaging apps for real-time discussions. Document all communications and agreements in writing to avoid misunderstandings. Consider using professional translation services if language barriers exist, ensuring clarity in technical specifications and expectations.
Important Disclaimer & Terms of Use
⚠️ Important Disclaimer
The information provided in this guide, including content regarding manufacturers, technical specifications, and market analysis, is for informational and educational purposes only. It does not constitute professional procurement advice, financial advice, or legal advice.
While we have made every effort to ensure the accuracy and timeliness of the information, we are not responsible for any errors, omissions, or outdated information. Market conditions, company details, and technical standards are subject to change.
B2B buyers must conduct their own independent and thorough due diligence before making any purchasing decisions. This includes contacting suppliers directly, verifying certifications, requesting samples, and seeking professional consultation. The risk of relying on any information in this guide is borne solely by the reader.
Strategic Sourcing Conclusion and Outlook for slider manufacturer
What Are the Key Takeaways for International B2B Buyers in Slider Manufacturing?
In the competitive landscape of slider manufacturing, strategic sourcing emerges as a pivotal approach for international B2B buyers. By focusing on quality, reliability, and innovation, buyers from regions such as Africa, South America, the Middle East, and Europe can unlock a wealth of opportunities. Establishing strong relationships with manufacturers ensures access to cutting-edge technology and materials, which can enhance product offerings and streamline operations.
How Can Strategic Sourcing Enhance Your Competitive Edge?
By implementing a strategic sourcing framework, businesses can reduce costs while improving supply chain efficiency. This approach not only mitigates risks associated with procurement but also fosters sustainability by promoting ethical sourcing practices. Buyers are encouraged to prioritize manufacturers who demonstrate a commitment to sustainable practices, thereby aligning with global standards and customer expectations.
What’s Next for International B2B Buyers in Slider Manufacturing?
Looking ahead, the demand for innovative slider solutions is expected to rise, driven by advancements in technology and changing consumer preferences. International B2B buyers should actively seek partnerships with forward-thinking manufacturers who are ready to adapt to market changes. Embrace this opportunity to enhance your supply chain and drive business growth by engaging with manufacturers that align with your strategic goals. Start today by exploring potential partnerships that can elevate your product offerings and position your company for success in the evolving marketplace.