Discover Top Benefits from Your Alternator Manufacturer (2025)
Introduction: Navigating the Global Market for alternator manufacturer
Navigating the global market for alternator manufacturers can be a daunting task for international B2B buyers, especially when faced with the challenge of sourcing reliable components that meet specific operational needs. Alternators are critical for ensuring the efficiency and functionality of various vehicles and machinery, making the selection of a trustworthy supplier paramount. This guide offers a comprehensive overview of the alternator manufacturing landscape, covering essential topics such as the different types of alternators, their applications across various industries, effective supplier vetting strategies, and cost considerations.
By delving into the intricacies of the alternator market, this guide empowers buyers from diverse regions—including Africa, South America, the Middle East, and Europe—to make informed purchasing decisions. It provides actionable insights into evaluating supplier capabilities, understanding market trends, and aligning product specifications with business requirements. Whether you are looking for high-performance alternators for automotive applications or robust solutions for industrial machinery, this guide serves as a valuable resource to enhance your sourcing strategy.
With the right knowledge and tools, you can confidently navigate the global market, ensuring you choose an alternator manufacturer that aligns with your quality standards and operational goals.
Understanding alternator manufacturer Types and Variations
Type Name | Key Distinguishing Features | Primary B2B Applications | Brief Pros & Cons for Buyers |
---|---|---|---|
Conventional Alternators | Uses electromagnetic induction; typically includes a voltage regulator. | Automotive, industrial machinery | Pros: Reliable and widely available. Cons: May require more maintenance. |
High-Output Alternators | Designed to produce higher voltage and current; often larger and heavier. | Performance vehicles, heavy machinery | Pros: Supports high-demand electrical systems. Cons: Higher cost and weight. |
Brushless Alternators | Utilizes permanent magnets and no brushes; lower maintenance. | Marine applications, aviation | Pros: Longer lifespan and less maintenance. Cons: Higher initial investment. |
Smart Alternators | Integrates with vehicle electronics; optimizes power delivery based on demand. | Modern vehicles, electric vehicles | Pros: Improves fuel efficiency and battery life. Cons: Complex systems may require specialized knowledge for repairs. |
Portable Alternators | Lightweight and compact; often used for temporary power solutions. | Construction sites, outdoor events | Pros: Easy to transport and set up. Cons: Limited power output compared to stationary models. |
What Are Conventional Alternators and Their Key Characteristics?
Conventional alternators are the most common type found in vehicles and machinery. They operate using electromagnetic induction and typically include a built-in voltage regulator. B2B buyers should consider these for standard applications where reliability and availability are crucial. While they are generally less expensive and widely accessible, they may require more frequent maintenance due to wear on brushes and other components.
How Do High-Output Alternators Differ in Performance?
High-output alternators are engineered to deliver increased voltage and current, making them ideal for performance vehicles and heavy machinery that require robust electrical systems. These alternators are larger and heavier, which can be a consideration for buyers prioritizing weight and space. The investment is justified for businesses that rely on high-demand electrical systems, though the upfront cost is typically higher.
Why Choose Brushless Alternators for Specific Applications?
Brushless alternators utilize permanent magnets instead of brushes, significantly reducing maintenance needs. This type is particularly suitable for marine and aviation applications where reliability is paramount. Although the initial purchase price is higher, the longevity and reduced maintenance costs make them appealing to B2B buyers looking for long-term solutions.
What Are the Benefits of Smart Alternators?
Smart alternators are designed to integrate with a vehicle’s electronic systems, optimizing power delivery based on real-time demand. This technology is particularly beneficial for modern and electric vehicles, enhancing fuel efficiency and battery life. However, the complexity of these systems may require specialized knowledge for installation and repairs, making them a consideration for buyers with technical expertise.
When Should You Consider Portable Alternators?
Portable alternators are lightweight and compact, making them ideal for temporary power solutions at construction sites or outdoor events. They offer the advantage of easy transport and setup, but their power output is limited compared to stationary models. Businesses requiring flexibility and mobility in their power solutions should weigh the pros and cons before making a purchase decision.
Key Industrial Applications of alternator manufacturer
Industry/Sector | Specific Application of alternator manufacturer | Value/Benefit for the Business | Key Sourcing Considerations for this Application |
---|---|---|---|
Automotive | Vehicle power generation and battery charging | Ensures reliable operation and longevity of vehicles | Quality standards, compatibility with vehicle models |
Renewable Energy | Wind turbine and solar panel energy conversion | Enhances energy efficiency and sustainability | Durability, environmental resistance, voltage regulation |
Construction | Heavy machinery and equipment power supply | Increases productivity and reduces downtime | Size, power output, and adaptability to various machines |
Marine | Powering onboard systems in ships | Guarantees operational reliability and safety at sea | Marine-grade materials, corrosion resistance, certification |
Telecommunications | Backup power systems for communication networks | Ensures uninterrupted service and data integrity | Voltage stability, compact design, and regulatory compliance |
How is the Alternator Used in the Automotive Sector?
In the automotive industry, alternators play a crucial role in generating electrical power for vehicle operations, including battery charging and powering onboard electronics. A reliable alternator ensures vehicles operate efficiently, reducing the risk of breakdowns. For international buyers, particularly from regions like Africa and South America, sourcing high-quality alternators that meet specific vehicle compatibility is essential. Buyers should consider factors such as voltage output and the alternator’s ability to handle varying climatic conditions.
What Role Does the Alternator Play in Renewable Energy Applications?
In renewable energy, alternators are integral to converting mechanical energy from wind turbines or solar panels into usable electrical energy. This application enhances energy efficiency and contributes to sustainability efforts. For buyers in the Middle East and Europe, it’s critical to source alternators that are durable and capable of withstanding environmental stresses. Key considerations include the alternator’s efficiency ratings and its compatibility with renewable energy systems.
How are Alternators Beneficial in Construction Equipment?
Heavy machinery in the construction industry relies on alternators for consistent power supply to operate various equipment. A dependable alternator minimizes downtime, directly impacting project timelines and profitability. Buyers from regions like Africa and South America should prioritize sourcing alternators that are robust and adaptable to different machinery types. It is essential to evaluate power output and size to ensure compatibility with specific equipment.
Why are Alternators Important for Marine Applications?
In the marine sector, alternators power essential onboard systems, including navigation and communication equipment. Their reliability is vital for safety and operational efficiency at sea. For international buyers, especially in regions with extensive maritime activities, sourcing marine-grade alternators that resist corrosion and meet specific safety certifications is crucial. Buyers should also consider the alternator’s size and voltage stability to ensure it meets the demands of various vessels.
What is the Importance of Alternators in Telecommunications?
Telecommunications networks require uninterrupted power supply, making alternators critical for backup systems. They ensure continuous operation and data integrity during power outages. Buyers from Europe and the Middle East should focus on sourcing alternators that provide stable voltage and compact designs, suitable for integration into existing systems. Regulatory compliance and efficiency ratings are also vital considerations to ensure reliability in high-demand environments.
Related Video: Synchronous Generator Working Principle || How Does An Alternator Works?
3 Common User Pain Points for ‘alternator manufacturer’ & Their Solutions
Scenario 1: Difficulty in Identifying the Right Alternator for Specific Applications
The Problem:
International B2B buyers, especially those in diverse markets like Africa and South America, often face challenges in identifying the right alternator for specific vehicles or equipment. This difficulty can stem from variations in vehicle specifications, power requirements, and compatibility issues. Without accurate information, buyers may end up purchasing alternators that do not meet their operational needs, leading to performance issues or the need for costly replacements.
The Solution:
To effectively source the right alternator, buyers should collaborate closely with manufacturers or suppliers that offer comprehensive databases of alternator specifications. Request detailed product catalogs that include information on voltage, amperage, and physical dimensions. Additionally, utilizing a vehicle compatibility tool can simplify the selection process. Buyers should also engage in direct communication with manufacturers to clarify any uncertainties regarding compatibility with their specific applications. This proactive approach ensures that the right product is sourced the first time, reducing downtime and enhancing operational efficiency.
Scenario 2: High Failure Rates Leading to Increased Maintenance Costs
The Problem:
Many businesses experience high failure rates of alternators, which can lead to increased maintenance costs and operational disruptions. This issue is particularly prevalent in harsh environments, such as those found in the Middle East, where extreme temperatures and dust can affect alternator longevity. Frequent alternator failures not only strain budgets but can also impact the overall reliability of the equipment they power.
The Solution:
To mitigate these issues, B2B buyers should prioritize sourcing alternators that are specifically designed for high durability and performance in challenging conditions. When evaluating manufacturers, look for those that provide warranty information and performance testing data. Request alternators that incorporate advanced materials and technologies, such as better insulation and enhanced cooling mechanisms, to withstand harsh operating environments. Furthermore, establishing a regular maintenance schedule to monitor alternator performance can help identify potential issues early, reducing the likelihood of sudden failures.
Scenario 3: Unclear Supply Chain and Delivery Issues
The Problem:
For international buyers, navigating the complexities of the supply chain can be daunting, particularly when it comes to the timely delivery of alternators. Delays in procurement can lead to significant operational setbacks, especially for companies relying on just-in-time inventory systems. Additionally, unclear communication regarding shipment timelines and customs processes can result in further complications and increased costs.
The Solution:
To address supply chain concerns, buyers should work with manufacturers who offer transparent communication and reliable logistics solutions. Establish clear expectations regarding lead times and delivery schedules before placing orders. It’s also beneficial to partner with suppliers who have a proven track record of handling international shipments and understand the customs regulations of the buyer’s region. Utilizing tracking systems can provide real-time updates on shipment status, allowing for better planning and resource allocation. Buyers should also consider developing relationships with multiple suppliers to create a more resilient supply chain that can adapt to unexpected challenges.
Strategic Material Selection Guide for alternator manufacturer
What Are the Key Materials Used in Alternator Manufacturing?
When selecting materials for alternator manufacturing, several factors must be considered, including performance characteristics, cost, and regional compliance standards. Below, we analyze four common materials used in alternators: aluminum, copper, steel, and plastic. Each material has unique properties, advantages, and limitations that can significantly impact the performance and longevity of the alternator.
How Does Aluminum Benefit Alternator Manufacturing?
Aluminum is a popular choice for alternator housings and components due to its lightweight nature and excellent corrosion resistance. It typically has a temperature rating of around 150°C, making it suitable for automotive applications where heat is a concern.
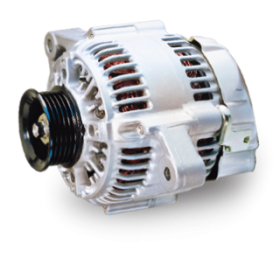
A stock image related to alternator manufacturer.
Pros: Aluminum’s low weight contributes to overall vehicle efficiency, and its resistance to corrosion extends the life of the alternator. Additionally, aluminum can be easily extruded and machined, which simplifies manufacturing processes.
Cons: While aluminum is durable, it can be more expensive than other materials like steel. It may also have lower tensile strength, which could be a concern in high-stress applications.
Impact on Application: Aluminum is particularly effective in environments where weight savings and corrosion resistance are critical, such as in vehicles operating in coastal regions with high humidity.
Considerations for International Buyers: Buyers from Africa, South America, the Middle East, and Europe should ensure compliance with regional standards such as ASTM and DIN. The availability of aluminum can vary by region, affecting lead times and costs.
What Role Does Copper Play in Alternator Efficiency?
Copper is essential in alternator manufacturing, primarily used for windings due to its excellent electrical conductivity. It can handle high temperatures, with a rating of approximately 200°C, making it ideal for electrical applications.
Pros: The high conductivity of copper ensures efficient energy transfer, reducing energy losses and improving overall alternator performance. It is also highly durable and resistant to corrosion.
Cons: Copper is relatively expensive compared to aluminum and can add significant costs to the manufacturing process. Additionally, its weight can be a drawback in applications where minimizing weight is a priority.
Impact on Application: Copper’s superior conductivity makes it suitable for high-performance alternators, particularly in vehicles requiring robust electrical systems.
Considerations for International Buyers: Buyers should be aware of fluctuating copper prices and ensure that suppliers adhere to international standards for electrical components.
How Does Steel Contribute to Alternator Durability?
Steel is often used for structural components of alternators, such as the frame and brackets. It has a high tensile strength and can withstand significant mechanical stress, with a temperature rating of around 300°C.
Pros: Steel’s durability ensures that the alternator can withstand harsh operating conditions. It is also relatively inexpensive compared to aluminum and copper.
Cons: Steel is heavier than aluminum, which may affect vehicle performance. Additionally, it is prone to corrosion if not properly treated or coated.
Impact on Application: Steel is ideal for applications requiring strength and durability, particularly in heavy-duty vehicles or environments with high mechanical stress.
Considerations for International Buyers: Buyers should consider the need for protective coatings to prevent rust, especially in humid or coastal regions. Compliance with standards like JIS for steel components is essential.
What Is the Role of Plastic in Alternator Components?
Plastic is increasingly used in alternator manufacturing for non-structural components like covers and insulation. It offers lightweight properties and good thermal resistance, typically rated up to 120°C.
Pros: Plastic is cost-effective and can be molded into complex shapes, allowing for design flexibility. It also provides good electrical insulation, which is crucial for safety.
Cons: Plastic may not be as durable as metals and can degrade over time, especially under high heat or exposure to chemicals.
Impact on Application: Plastic is suitable for applications where weight reduction and insulation are priorities, but it may not be appropriate for high-stress components.
Considerations for International Buyers: Buyers should ensure that the plastics used meet regional standards for automotive applications, particularly regarding heat resistance and durability.
Summary Table of Material Selection for Alternator Manufacturing
Material | Typical Use Case for alternator manufacturer | Key Advantage | Key Disadvantage/Limitation | Relative Cost (Low/Med/High) |
---|---|---|---|---|
Aluminum | Housings and non-load bearing components | Lightweight and corrosion-resistant | Lower tensile strength compared to steel | Medium |
Copper | Windings and electrical connections | Excellent electrical conductivity | Higher cost and weight | High |
Steel | Structural components like frames and brackets | High tensile strength and durability | Heavier and prone to corrosion | Low |
Plastic | Covers and insulation components | Cost-effective and design flexibility | Less durable and heat-sensitive | Low |
This strategic material selection guide provides international B2B buyers with essential insights into the materials used in alternator manufacturing, helping them make informed decisions that align with their operational needs and regional compliance requirements.
In-depth Look: Manufacturing Processes and Quality Assurance for alternator manufacturer
What Are the Key Stages in the Manufacturing Process of Alternators?
The manufacturing process of alternators involves several critical stages that ensure the production of high-quality and reliable products. For B2B buyers, understanding these stages can provide insights into the supplier’s capabilities and the quality of the alternators they offer.
-
Material Preparation
The manufacturing process begins with the selection and preparation of raw materials. High-grade materials such as copper for windings, steel for housings, and high-strength plastics for insulation are essential. Suppliers often conduct material tests to ensure compliance with international standards, such as ASTM or ISO certifications, which guarantees the durability and performance of the materials used. -
Forming
In this stage, the prepared materials are shaped into components. Techniques such as stamping and casting are commonly used for creating the alternator’s housing and rotor. Advanced manufacturing technologies, including CNC machining, ensure precision in forming components. Automation in this stage can enhance efficiency and reduce human error, leading to consistent quality across batches. -
Assembly
Once the components are formed, they are assembled into a complete alternator. This process typically involves:
– Winding: Copper wires are wound around the rotor to create the magnetic field necessary for power generation.
– Mounting: The rotor and stator are carefully positioned and secured within the housing.
– Integration of Electronics: Modern alternators include integrated voltage regulators and rectifiers, which are assembled during this phase. -
Finishing
The final stage involves applying protective coatings and conducting final assembly checks. This may include painting, surface treatments, and the installation of additional components such as bearings and cooling fans. Quality control measures are crucial at this stage to ensure that the alternator meets all specifications and standards.
What International Standards Should B2B Buyers Look for in Quality Assurance?
Quality assurance is paramount in the alternator manufacturing process. International standards provide a framework for ensuring product consistency and reliability. B2B buyers should pay attention to the following:
-
ISO 9001 Certification
This standard focuses on quality management systems and is essential for manufacturers aiming to ensure quality in their production processes. An ISO 9001 certification indicates that the manufacturer has established procedures to consistently provide products that meet customer and regulatory requirements. -
CE Marking
For buyers in Europe, CE marking signifies that the product complies with EU safety, health, and environmental protection standards. It is crucial for ensuring that the alternators meet the necessary requirements for sale in the European market. -
API Standards
In industries where alternators are used in heavy machinery or automotive applications, adhering to API (American Petroleum Institute) standards can be critical. These standards ensure that the products are suitable for the demanding environments in which they will operate.
What Are the Key Quality Control Checkpoints During Alternator Manufacturing?
Quality control (QC) is integrated throughout the manufacturing process, with specific checkpoints designed to catch defects and ensure product integrity:
-
Incoming Quality Control (IQC)
This initial checkpoint involves inspecting raw materials and components before they enter the manufacturing process. Materials are tested for compliance with specifications, and documentation is reviewed to verify certifications. -
In-Process Quality Control (IPQC)
During assembly, continuous monitoring is conducted to ensure that each step meets quality standards. This includes checking the precision of component fitting, the integrity of electrical connections, and the proper functioning of integrated circuits. -
Final Quality Control (FQC)
After assembly, finished alternators undergo rigorous testing. Common tests include:
– Electrical Testing: Measuring output voltage, current, and efficiency.
– Mechanical Testing: Evaluating the durability and resistance of components under load.
– Environmental Testing: Assessing performance under varying temperature and humidity conditions.
How Can B2B Buyers Verify Supplier Quality Control Practices?
For international B2B buyers, verifying the quality control practices of potential suppliers is essential for ensuring product reliability. Here are actionable steps:
-
Conduct Audits
Regular audits of the manufacturing facility can provide insights into the supplier’s quality management systems. Buyers should request to review audit reports and corrective action plans to understand how suppliers address quality issues. -
Request Quality Reports
Suppliers should provide documentation of their quality assurance processes, including test results and compliance certifications. This transparency can help build trust in the supplier’s commitment to quality. -
Engage Third-Party Inspectors
Utilizing third-party inspection services can offer an unbiased assessment of the supplier’s quality control measures. These services can conduct random inspections and provide detailed reports on manufacturing practices and product quality.
What Are the Quality Control Nuances for International B2B Buyers?
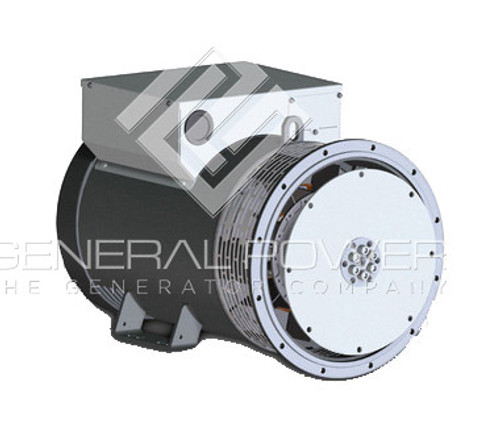
A stock image related to alternator manufacturer.
Understanding the nuances of quality control is vital for international B2B buyers, especially those from diverse regions like Africa, South America, the Middle East, and Europe. Here are some key considerations:
-
Regulatory Compliance
Different regions may have specific regulatory requirements for electrical components. Buyers must ensure that the alternators meet the regulations applicable in their respective markets. -
Cultural Differences in Quality Standards
Quality expectations can vary significantly between regions. B2B buyers should be aware of local industry standards and practices to ensure alignment with their expectations. -
Supplier Communication
Clear communication with suppliers regarding quality standards and expectations is essential. Buyers should establish protocols for reporting defects, handling returns, and addressing quality concerns to facilitate smooth transactions.
By understanding the manufacturing processes and quality assurance practices in alternator production, B2B buyers can make informed decisions and select suppliers that meet their needs for reliability and performance.
Practical Sourcing Guide: A Step-by-Step Checklist for ‘alternator manufacturer’
To ensure a successful procurement process for alternators, international B2B buyers must navigate various considerations that affect both quality and cost. This checklist serves as a practical guide for sourcing reliable alternator manufacturers, particularly for buyers from Africa, South America, the Middle East, and Europe.
Step 1: Define Your Technical Specifications
Before engaging with manufacturers, outline the specific technical requirements for the alternators you need. Consider parameters such as voltage, amperage, mounting types, and compatibility with existing systems.
– Why it matters: Clear specifications help in avoiding miscommunication and ensure that you receive products that meet your operational needs.
– What to look for: Create a detailed list of required features and performance metrics.
Step 2: Research Manufacturer Reputation
Conduct thorough research on potential manufacturers. Look for reviews, testimonials, and case studies from previous clients, especially those within your industry.
– Why it matters: A manufacturer’s reputation can significantly influence product quality and reliability.
– What to look for: Check platforms like industry forums, trade publications, and social media for unbiased feedback.
Step 3: Verify Supplier Certifications
Ensure that the manufacturers possess relevant certifications, such as ISO 9001 or other industry-specific standards.
– Why it matters: Certifications are indicators of quality management practices and adherence to international standards.
– What to look for: Request copies of certifications and check their validity through the issuing bodies.
Step 4: Evaluate Production Capacity and Lead Times
Assess the manufacturer’s production capabilities and understand their lead times for order fulfillment.
– Why it matters: Knowing the production capacity helps ensure that the manufacturer can meet your demand without delays, which is crucial for maintaining your supply chain.
– What to look for: Inquire about their average production volume and how they handle urgent orders.
Step 5: Request Samples for Testing
Before making a large order, request samples to evaluate the quality of the alternators.
– Why it matters: Testing samples can reveal potential issues in performance and compatibility that may not be evident from specifications alone.
– What to look for: Pay attention to build quality, functionality, and adherence to your specifications.
Step 6: Negotiate Pricing and Terms
Engage in negotiations regarding pricing, payment terms, and warranty conditions.
– Why it matters: Understanding pricing structures and terms can help you optimize costs and mitigate financial risks.
– What to look for: Compare quotes from multiple suppliers and be clear about your budget constraints and expectations.
Step 7: Establish a Communication Plan
Develop a communication plan with the manufacturer to facilitate ongoing dialogue throughout the procurement process.
– Why it matters: Effective communication helps address issues promptly and fosters a strong relationship with the supplier.
– What to look for: Define contact points, response times, and preferred communication channels to streamline interactions.
By following this step-by-step checklist, B2B buyers can enhance their sourcing strategy for alternators, ensuring they partner with manufacturers that align with their technical needs and business objectives.
Comprehensive Cost and Pricing Analysis for alternator manufacturer Sourcing
What Are the Key Cost Components in Alternator Manufacturing?
When sourcing alternators for B2B applications, understanding the cost structure is crucial. The primary cost components include:
-
Materials: The quality and type of materials used—such as copper for windings, steel for the housing, and rare earth metals for magnets—greatly influence the cost. High-grade materials can enhance performance but may also increase the price.
-
Labor: Labor costs vary by region and skill level. Countries with lower labor costs may provide more competitive pricing, but this can affect the quality of craftsmanship and assembly.
-
Manufacturing Overhead: This includes utilities, rent, and other indirect costs associated with production. Efficient manufacturing processes can help mitigate these costs.
-
Tooling: The initial investment in tooling can be substantial, especially for customized designs. Buyers should inquire about the amortization of these costs over production runs.
-
Quality Control (QC): Ensuring that alternators meet specific standards requires investment in quality assurance processes. Certifications (e.g., ISO) may add to costs but are essential for reliability.
-
Logistics: Shipping and handling costs, particularly for international transactions, should be factored in. The choice of transport mode (air vs. sea) will also impact costs.
-
Margin: Manufacturers will typically add a margin to cover their costs and profit. This can vary significantly based on market demand and competition.
How Do Price Influencers Affect Alternator Costs?
Several factors influence the pricing of alternators:
-
Volume/MOQ: Higher order volumes often lead to lower per-unit costs due to economies of scale. Understanding Minimum Order Quantities (MOQ) is essential for budget planning.
-
Specifications and Customization: Custom alternators may incur additional costs. Buyers should clearly define their specifications to avoid unexpected expenses.
-
Materials: Premium materials improve performance but increase costs. Buyers should evaluate the trade-off between cost and quality.
-
Quality and Certifications: Alternators with recognized certifications may command higher prices but often provide better reliability and warranty coverage.
-
Supplier Factors: The reputation and reliability of the supplier can influence pricing. Established suppliers may charge more for their expertise and service.
-
Incoterms: The chosen Incoterms can affect total costs, including shipping responsibilities and insurance. Buyers should understand the implications of different terms to avoid additional charges.
What Tips Can Help International B2B Buyers Negotiate Better Pricing?
To achieve cost efficiency when sourcing alternators, consider the following tips:
-
Negotiate Wisely: Leverage your purchasing power by negotiating terms and pricing based on your volume and long-term partnership potential. Suppliers may offer discounts for repeat orders or bulk purchases.
-
Evaluate Total Cost of Ownership (TCO): Beyond initial pricing, consider maintenance, warranty, and lifecycle costs. A lower initial price may lead to higher TCO if the product is less durable.
-
Understand Pricing Nuances for International Buyers: Currency fluctuations can affect pricing. Establishing payment terms that mitigate this risk is advisable.
-
Research Market Trends: Stay informed about market conditions and material costs. Understanding these dynamics can empower you in negotiations.
-
Build Relationships with Suppliers: A strong relationship can lead to better pricing, priority during shortages, and improved service.
Disclaimer on Indicative Prices
Prices for alternators can vary widely based on the factors outlined above. It is essential to obtain quotes from multiple suppliers to ensure competitive pricing. Always consider the total cost implications and not just the upfront costs when making purchasing decisions.
Alternatives Analysis: Comparing alternator manufacturer With Other Solutions
When considering the purchase of an alternator, it’s essential to evaluate not only the specific manufacturer but also alternative solutions that can meet your operational needs. Understanding the various options available can help international B2B buyers, especially from diverse regions like Africa, South America, the Middle East, and Europe, make informed decisions. Below is a comparative analysis of traditional alternator manufacturers against alternative technologies.
Comparison Aspect | Alternator Manufacturer | Lithium-Ion Battery Systems | Fuel Cell Technology |
---|---|---|---|
Performance | High efficiency in voltage regulation and power supply for vehicles and machinery. | Excellent energy density and can provide power with lower weight. | Generates electricity through a chemical reaction, offering continuous power as long as fuel is supplied. |
Cost | Generally lower upfront costs but varies by brand and capacity. | Higher initial investment but lower operational costs over time. | High initial setup costs, with ongoing fuel costs depending on hydrogen prices. |
Ease of Implementation | Easy to integrate into existing systems with standardized designs. | May require redesign of electrical systems; compatibility varies. | Requires significant infrastructure for hydrogen supply and storage. |
Maintenance | Regular checks needed; typically low maintenance if installed correctly. | Minimal maintenance but requires monitoring of battery health. | Ongoing maintenance for fuel cells and hydrogen storage systems. |
Best Use Case | Ideal for traditional vehicles and machinery requiring reliable power supply. | Best suited for electric vehicles and portable power applications. | Suitable for applications needing continuous power and where hydrogen infrastructure is available. |
What Are the Advantages and Disadvantages of Lithium-Ion Battery Systems?
Lithium-ion battery systems present a viable alternative to traditional alternators, particularly in electric vehicles (EVs). They offer high energy density, which means they can store more energy in a smaller space compared to lead-acid batteries. This can lead to lower vehicle weight and improved efficiency. However, the higher initial investment and need for specialized charging infrastructure can deter some businesses from adopting this technology. Additionally, the performance of lithium-ion batteries can degrade over time, necessitating careful monitoring and potential replacement.
How Does Fuel Cell Technology Compare?
Fuel cell technology is another alternative that generates electricity through the chemical reaction of hydrogen and oxygen. This method offers the advantage of continuous power generation, making it particularly suitable for applications where extended operation is necessary without frequent refueling or recharging. However, the costs associated with setting up hydrogen infrastructure can be prohibitive, and the technology is still not as widely adopted as traditional alternators. Furthermore, the availability and pricing of hydrogen can fluctuate, impacting operational costs.
Conclusion: How to Choose the Right Solution for Your Needs
For international B2B buyers, the decision to choose between an alternator manufacturer and alternative solutions such as lithium-ion battery systems or fuel cell technology should hinge on specific operational requirements and budget considerations. If your application demands reliable power generation with lower initial costs, traditional alternators may be the best fit. However, if your focus is on sustainability and longer-term savings, investing in lithium-ion or fuel cell technologies could be advantageous. Assessing the unique needs of your business, including performance, maintenance, and cost, will guide you towards the optimal choice for your energy solution.
Essential Technical Properties and Trade Terminology for alternator manufacturer
What Are the Key Technical Properties to Consider When Sourcing Alternators?
When sourcing alternators, understanding the technical specifications is essential for ensuring compatibility and performance. Here are some critical properties to consider:
1. Material Grade
The materials used in alternator construction significantly influence durability and efficiency. Common materials include aluminum for housings due to its lightweight and corrosion-resistant properties, and copper for windings, which provide excellent conductivity. For B2B buyers, selecting alternators with high-grade materials can lead to longer service life and reduced maintenance costs.
2. Output Voltage and Current Ratings
Alternators are rated by their output voltage (typically between 12V and 24V) and current (measured in amperes). These specifications are crucial as they determine the alternator’s ability to power various vehicle systems. Buyers should match these ratings with their specific applications to avoid underperformance or potential damage to electrical systems.
3. Tolerance Levels
Tolerance refers to the permissible limits of variation in dimensions and performance. For alternators, tight tolerances in rotor and stator alignment are vital for efficient operation and minimizing wear. Understanding tolerance requirements helps buyers ensure that the alternators meet the operational standards necessary for their specific applications.
4. Efficiency Rating
The efficiency of an alternator indicates how effectively it converts mechanical energy into electrical energy. High-efficiency alternators minimize energy loss, leading to better fuel economy and reduced emissions in automotive applications. For B2B buyers focused on sustainability, opting for high-efficiency models can align with corporate responsibility goals.
5. Cooling Mechanism
Alternators generate heat during operation, and effective cooling mechanisms (such as integrated fans or heat sinks) are critical for preventing overheating and extending lifespan. Buyers should inquire about the cooling design of the alternator to ensure it meets the thermal management needs of their application.
6. Noise and Vibration Levels
Noise and vibration can affect the comfort and performance of the vehicle. Alternators should be designed to minimize these factors. Buyers looking for alternators for commercial vehicles should prioritize models that meet specific noise and vibration standards to enhance user experience.
What Common Trade Terminology Should B2B Buyers Know When Purchasing Alternators?
Understanding industry jargon can streamline the procurement process and enhance communication between buyers and manufacturers. Here are some essential terms:
1. OEM (Original Equipment Manufacturer)
OEM refers to companies that produce components that are used in another company’s end products. For alternators, OEM parts are often preferred because they are made to the same specifications as the original equipment, ensuring compatibility and reliability.
2. MOQ (Minimum Order Quantity)
MOQ is the smallest quantity of a product that a supplier is willing to sell. This term is crucial for B2B buyers as it can impact inventory costs and cash flow. Understanding MOQ helps in negotiating better terms and ensuring that the purchase aligns with business needs.
3. RFQ (Request for Quotation)
An RFQ is a formal document that buyers send to suppliers to request pricing and terms for specific products. It is a crucial step in the procurement process, allowing buyers to compare costs and conditions from different manufacturers before making a decision.
4. Incoterms (International Commercial Terms)
Incoterms are a set of rules that define the responsibilities of buyers and sellers in international trade. They clarify who is responsible for shipping, insurance, and tariffs, which can significantly impact the total cost of procurement. Familiarity with Incoterms helps buyers manage risks and costs effectively.
5. Lead Time
Lead time refers to the amount of time it takes from placing an order to receiving the product. Understanding lead times is vital for inventory management and planning, especially for businesses that rely on just-in-time manufacturing processes.
6. Warranty Terms
Warranty terms outline the manufacturer’s commitment to repair or replace faulty products within a specified period. Knowledge of warranty conditions helps buyers assess the reliability and support they can expect, providing peace of mind in their investment.
By understanding these technical properties and trade terms, B2B buyers can make informed decisions when sourcing alternators, ensuring they select products that meet their operational requirements and business goals.
Navigating Market Dynamics and Sourcing Trends in the alternator manufacturer Sector
What Are the Key Market Dynamics in the Alternator Manufacturing Sector?
The alternator manufacturing sector is currently experiencing notable shifts influenced by several global drivers. The increasing demand for electric vehicles (EVs) is propelling advancements in alternator technology, particularly with the need for more efficient, lightweight, and powerful components. Additionally, the rise in renewable energy sources has led to an uptick in the requirement for alternators in solar and wind energy systems, creating new opportunities for manufacturers.
Emerging B2B technology trends include the adoption of Industry 4.0 practices, which leverage IoT (Internet of Things) devices for real-time monitoring and predictive maintenance of alternators. This integration not only enhances operational efficiency but also improves the supply chain management process. International buyers, especially from Africa, South America, the Middle East, and Europe, should focus on suppliers that utilize these advanced technologies to ensure reliable product performance and reduced downtime.
Market dynamics are also being shaped by geopolitical factors and trade policies. Buyers should be aware of tariffs and import restrictions that may impact pricing and availability. Understanding these dynamics can aid international buyers in making informed sourcing decisions, ensuring they partner with manufacturers capable of navigating these complexities effectively.
How Does Sustainability Impact Sourcing for Alternator Manufacturers?
Environmental concerns are becoming increasingly pivotal in the alternator manufacturing industry. As global awareness of climate change grows, B2B buyers are prioritizing suppliers that demonstrate a commitment to sustainable practices. This includes utilizing renewable materials, reducing waste in production, and implementing energy-efficient manufacturing processes.
Ethical sourcing is equally important. Buyers should seek manufacturers who maintain transparent supply chains and adhere to ethical labor practices. This not only mitigates risks associated with reputational damage but also aligns with the growing consumer preference for environmentally responsible products.
Certification plays a crucial role in this landscape. Certifications such as ISO 14001 for environmental management and other ‘green’ labels can guide buyers in identifying manufacturers who prioritize sustainability. Opting for suppliers that have these certifications can enhance a company’s brand image and appeal to eco-conscious customers.
How Has the Alternator Manufacturing Industry Evolved Over Time?
The alternator manufacturing sector has undergone significant evolution over the decades, transitioning from simple mechanical devices to complex electronic systems. Initially designed to provide basic electrical power for vehicles, modern alternators are now equipped with advanced features, including built-in voltage regulators and smart technology that optimizes performance based on real-time data.
As the automotive industry shifts towards electrification, manufacturers are increasingly focusing on developing alternators that can support hybrid and electric vehicles. This evolution reflects broader trends in the automotive sector, where efficiency and sustainability are paramount. For international B2B buyers, recognizing this historical context can help them understand current product offerings and anticipate future innovations in alternator technology.
In summary, the alternator manufacturing sector is poised for growth driven by technological advancements and sustainability imperatives. International buyers must stay informed about market dynamics and supplier capabilities to make strategic sourcing decisions that align with their business goals.
Frequently Asked Questions (FAQs) for B2B Buyers of alternator manufacturer
-
How do I identify a reliable alternator manufacturer for international sourcing?
To identify a reliable alternator manufacturer, start by researching their reputation in the industry. Look for customer reviews, ratings, and testimonials, particularly from other B2B buyers in your region. Verify their certifications and quality assurance processes, as these can indicate adherence to international standards. Engaging with industry forums or trade associations can provide insights into manufacturers’ reliability. Additionally, consider requesting samples or conducting factory visits to assess their production capabilities and quality control measures. -
What are the key factors to consider when selecting an alternator for my specific application?
When selecting an alternator, consider factors such as power output, size, weight, and compatibility with your equipment or vehicle. Evaluate the alternator’s efficiency ratings, as higher efficiency translates to better performance and longer lifespan. Additionally, think about the environmental conditions in which the alternator will operate; for instance, extreme temperatures or humidity may require specialized designs. Customization options from manufacturers can also play a crucial role in meeting your specific application needs. -
What minimum order quantities (MOQs) should I expect when sourcing alternators from manufacturers?
Minimum order quantities (MOQs) can vary significantly among manufacturers, typically ranging from 50 to 500 units. It’s essential to discuss MOQs upfront during your negotiations, as some manufacturers may be flexible, especially for first-time orders. If your order volume is lower than the MOQ, consider partnering with other buyers to consolidate orders or seek manufacturers that specialize in smaller batch productions. Understanding MOQs can help you manage inventory and cash flow effectively. -
What payment terms are commonly offered by alternator manufacturers in international trade?
Payment terms vary by manufacturer and can include options like advance payment, partial payment before shipment, or net 30-90 days after delivery. Letters of credit (LC) are also popular for international transactions, providing security for both parties. It’s advisable to negotiate terms that align with your cash flow needs while ensuring that the manufacturer feels secure in the transaction. Always document agreed-upon payment terms in your contract to avoid misunderstandings. -
How do I ensure quality assurance when sourcing alternators from overseas manufacturers?
To ensure quality assurance, request detailed documentation of the manufacturer’s quality control processes, including certifications like ISO 9001. Conducting pre-shipment inspections can help verify product quality before shipment. It’s also beneficial to establish clear specifications and standards in your purchase agreement. Consider working with third-party inspection services to provide unbiased evaluations. Building a strong relationship with your manufacturer can also foster better communication regarding quality expectations. -
What logistics considerations should I keep in mind when importing alternators?
When importing alternators, consider shipping methods, costs, and transit times, as these can significantly affect your supply chain. Choose between air freight for speed or sea freight for cost-effectiveness, depending on your urgency and budget. Additionally, be aware of customs regulations, tariffs, and import duties that may apply in your country. Collaborating with a logistics provider experienced in international shipping can help streamline the process and ensure compliance with local laws. -
How can I customize alternators to meet specific requirements for my business?
Many alternator manufacturers offer customization options, including adjustments to voltage output, size, and connection types. When discussing customization, provide detailed specifications and requirements to the manufacturer. Some manufacturers may also offer design services to create alternators tailored to your needs. Be sure to inquire about lead times and costs associated with custom orders, as these can vary significantly based on the complexity of the modifications. -
What are the common signs of a failing alternator that I should monitor in my equipment?
Common signs of a failing alternator include dimming headlights, electrical malfunctions, unusual noises, or a warning light on the dashboard. If you notice that your equipment is not starting as reliably, or if batteries are losing charge quickly, these may indicate alternator issues. Regular maintenance and monitoring can help identify these symptoms early, allowing for proactive replacements and minimizing downtime. Ensure your maintenance team is trained to recognize these signs for timely interventions.
Important Disclaimer & Terms of Use
⚠️ Important Disclaimer
The information provided in this guide, including content regarding manufacturers, technical specifications, and market analysis, is for informational and educational purposes only. It does not constitute professional procurement advice, financial advice, or legal advice.
While we have made every effort to ensure the accuracy and timeliness of the information, we are not responsible for any errors, omissions, or outdated information. Market conditions, company details, and technical standards are subject to change.
B2B buyers must conduct their own independent and thorough due diligence before making any purchasing decisions. This includes contacting suppliers directly, verifying certifications, requesting samples, and seeking professional consultation. The risk of relying on any information in this guide is borne solely by the reader.
Strategic Sourcing Conclusion and Outlook for alternator manufacturer
In today’s competitive landscape, effective strategic sourcing in the alternator manufacturing sector is vital for international B2B buyers, particularly from Africa, South America, the Middle East, and Europe. By leveraging a thorough understanding of supply chains, evaluating supplier capabilities, and prioritizing quality, buyers can significantly reduce costs while enhancing operational efficiency.
A focus on strategic sourcing not only allows businesses to secure reliable alternator suppliers but also fosters long-term partnerships that can drive innovation and responsiveness to market demands. As the automotive sector increasingly embraces advancements in technology and sustainability, aligning sourcing strategies with these trends will be crucial.
Looking ahead, B2B buyers should actively engage with manufacturers who demonstrate a commitment to quality, sustainability, and technological innovation. This proactive approach will not only ensure the reliability of alternators but also position your business favorably in a rapidly evolving marketplace. Embrace the opportunity to collaborate with leading manufacturers and take the next step in optimizing your supply chain for greater success.