Discover Top Dining Chair Manufacturers: Your Ultimate Guide (2025)
Introduction: Navigating the Global Market for dining chair manufacturer
In today’s competitive landscape, sourcing high-quality dining chairs presents a considerable challenge for international B2B buyers, especially those from Africa, South America, the Middle East, and Europe. As businesses strive to enhance their dining environments—whether in restaurants, hotels, or corporate settings—understanding the nuances of various dining chair manufacturers becomes imperative. This guide is designed to navigate the complexities of the global market, providing insights into different types of dining chairs, their applications, and the importance of selecting the right suppliers.
Buyers will gain a comprehensive understanding of essential factors such as material quality, ergonomic design, and aesthetic appeal, all of which are crucial for creating inviting dining spaces. Additionally, the guide will cover supplier vetting processes, cost considerations, and best practices for negotiating favorable terms. By empowering buyers with actionable insights, this resource aims to simplify the purchasing journey and facilitate informed decisions that align with specific business needs and budget constraints.
Whether you are a hotelier in Poland seeking to refurbish your dining area or a restaurateur in Saudi Arabia looking for unique styles, this guide will equip you with the knowledge necessary to source the ideal dining chairs that enhance customer experience and operational efficiency.
Understanding dining chair manufacturer Types and Variations
Type Name | Key Distinguishing Features | Primary B2B Applications | Brief Pros & Cons for Buyers |
---|---|---|---|
Solid Wood Dining Chairs | Made from durable hardwood, offers classic aesthetics | Restaurants, hotels, homes | Pros: Durable, timeless design; Cons: Heavier, often more expensive. |
Upholstered Dining Chairs | Features fabric or leather covering for comfort | Upscale dining, event venues | Pros: Comfortable, customizable; Cons: Requires more maintenance, can stain easily. |
Metal Dining Chairs | Constructed from steel or aluminum, often lightweight | Cafes, outdoor dining, modern spaces | Pros: Lightweight, modern look; Cons: Less comfortable without cushions. |
Plastic Dining Chairs | Made from durable plastic, often stackable | Casual dining, outdoor events | Pros: Lightweight, easy to clean; Cons: Less durable than wood or metal. |
Vintage/Antique Chairs | Unique designs, often restored or repurposed | Specialty restaurants, boutiques | Pros: Unique aesthetic, storytelling potential; Cons: May require restoration, can be costly. |
What Are the Key Features of Solid Wood Dining Chairs?
Solid wood dining chairs are characterized by their use of high-quality hardwoods such as oak, maple, or walnut. These chairs provide a classic and timeless aesthetic, making them a popular choice for traditional dining settings, restaurants, and upscale homes. When purchasing, B2B buyers should consider factors such as wood type, finish, and construction quality to ensure longevity and durability in high-traffic environments.
How Do Upholstered Dining Chairs Enhance Comfort?
Upholstered dining chairs are designed with a soft fabric or leather covering, providing enhanced comfort for diners. These chairs are ideal for upscale dining establishments and event venues where guest comfort is paramount. Buyers should evaluate the quality of the upholstery, the type of padding used, and the ease of cleaning when selecting upholstered chairs, as these factors directly influence the product’s longevity and maintenance needs.
Why Choose Metal Dining Chairs for Modern Spaces?
Metal dining chairs are a popular choice for contemporary settings due to their sleek, minimalist designs and lightweight nature. Often made from steel or aluminum, these chairs are suitable for cafes, outdoor dining areas, and modern interiors. Buyers should consider the chair’s weight capacity, rust resistance, and whether cushions are needed for added comfort, as metal chairs can sometimes lack the coziness of upholstered options.
What Are the Benefits of Plastic Dining Chairs?
Plastic dining chairs are known for their affordability and practicality, often being lightweight and stackable for easy storage. They are commonly used in casual dining environments and outdoor events due to their resistance to weather elements. B2B buyers should assess the chair’s durability and UV resistance, as well as its color options, to ensure it meets the aesthetic and functional needs of their space.
How Do Vintage/Antique Chairs Stand Out in the Market?
Vintage and antique dining chairs offer unique designs and historical significance, making them attractive for specialty restaurants and boutique settings. These chairs can be restored or repurposed, adding character to any dining area. Buyers should be prepared for potential restoration costs and should verify the authenticity and condition of each piece to ensure they are making a worthwhile investment that aligns with their brand identity.
Related Video: Building a Set of Dining Chairs
Key Industrial Applications of dining chair manufacturer
Industry/Sector | Specific Application of dining chair manufacturer | Value/Benefit for the Business | Key Sourcing Considerations for this Application |
---|---|---|---|
Hospitality | Custom dining chairs for hotels and restaurants | Enhances guest experience and brand image | Quality, durability, design options, and compliance with local regulations |
Education | Dining chairs for cafeterias in schools and universities | Supports student comfort and engagement during meals | Ergonomics, safety standards, and bulk purchasing discounts |
Healthcare | Dining chairs for hospitals and nursing homes | Provides comfort and accessibility for patients and visitors | Hygiene standards, material durability, and ease of cleaning |
Corporate Offices | Dining chairs for employee lounges and cafeterias | Fosters a collaborative environment and enhances employee satisfaction | Aesthetic appeal, ergonomics, and adaptability to space |
Event Management | Rental dining chairs for events and banquets | Offers flexibility and variety for different event themes | Cost-effectiveness, transportability, and style options |
How Are Dining Chairs Used in the Hospitality Sector?
In the hospitality industry, dining chairs play a critical role in shaping the guest experience. Hotels and restaurants often require custom-designed chairs that align with their brand aesthetics while ensuring comfort. International B2B buyers from regions like Africa and the Middle East should prioritize sourcing durable materials that withstand heavy use and comply with local safety regulations. Additionally, considerations such as the ease of maintenance and the ability to customize designs can significantly enhance the dining experience for guests.
What Are the Applications of Dining Chairs in Education?
Dining chairs in educational institutions, such as schools and universities, are essential for cafeterias where students gather for meals. These chairs must be ergonomic to support long periods of sitting and facilitate ease of movement for students. Buyers in South America and Europe should focus on chairs that meet safety standards and are constructed from materials that can endure high usage. Furthermore, bulk purchasing agreements can provide significant cost savings for educational institutions looking to furnish dining areas efficiently.
How Are Dining Chairs Utilized in Healthcare Settings?
In healthcare environments like hospitals and nursing homes, dining chairs must prioritize patient comfort and accessibility. These chairs often need to accommodate individuals with varying mobility levels and should be easy to clean and maintain. Buyers from regions such as Europe and the Middle East should ensure that the chairs comply with hygiene standards and are made from materials resistant to wear and tear. This focus on durability and hygiene is vital for enhancing the overall patient experience.
What Role Do Dining Chairs Play in Corporate Offices?
Corporate offices utilize dining chairs in employee lounges and cafeterias to create a welcoming environment that promotes social interaction. The design and ergonomics of these chairs can significantly influence employee satisfaction and productivity. International buyers, particularly from Europe, should consider aesthetic appeal and adaptability to different office layouts when sourcing dining chairs. Investing in quality seating can foster a collaborative atmosphere and contribute positively to workplace culture.
How Are Dining Chairs Essential in Event Management?
In the event management sector, dining chairs are often rented for various occasions, from weddings to corporate gatherings. The flexibility and variety in styles offered by dining chair manufacturers allow event planners to create tailored experiences for their clients. Buyers, especially in Africa and South America, should consider cost-effectiveness and transportability when sourcing rental chairs. Additionally, ensuring that the chairs complement the overall theme of the event can enhance the visual appeal and guest experience.
Related Video: Sci6 Q3 – Characteristics and Uses of Simple Machines
3 Common User Pain Points for ‘dining chair manufacturer’ & Their Solutions
Scenario 1: Sourcing Quality Materials for Dining Chairs
The Problem: One of the most significant challenges faced by B2B buyers when sourcing dining chairs is the inconsistency in the quality of materials used by manufacturers. Buyers often receive samples that meet their expectations, only to find that the final products delivered vary significantly in quality. This inconsistency can lead to dissatisfaction among customers, increased return rates, and damage to the buyer’s reputation in their respective market, particularly in regions like Europe and the Middle East where quality standards are stringent.
The Solution: To mitigate this issue, B2B buyers should establish clear material specifications and quality standards before engaging with a manufacturer. This includes requesting detailed documentation of the materials used and certifications that attest to their quality. Additionally, buyers should conduct factory visits or request third-party inspections of the manufacturing process. By fostering a close relationship with the manufacturer and maintaining open lines of communication, buyers can ensure that the materials used meet their expectations and are consistent across production batches. Investing in a reliable quality assurance program can also help identify potential issues before products are shipped.
Scenario 2: Managing Lead Times and Delivery Schedules
The Problem: Many international B2B buyers experience significant delays in lead times and delivery schedules when ordering dining chairs. These delays can disrupt business operations, especially for those in the hospitality and retail sectors that rely on timely deliveries to meet customer demand. For example, a buyer in South America may place an order for dining chairs for a new restaurant opening, only to face delays that push back the opening date and result in lost revenue.
The Solution: To address lead time challenges, buyers should work closely with manufacturers to establish realistic timelines and include penalty clauses for missed deadlines in contracts. It is also advisable to build a buffer into the order schedule to account for potential delays. Additionally, buyers can explore local or regional manufacturers to reduce shipping times and costs. Leveraging technology, such as supply chain management software, can enhance visibility into order status and help in proactive planning. Regular check-ins with the manufacturer during the production phase can also help identify any potential delays early on.
Scenario 3: Customization and Design Limitations
The Problem: Many B2B buyers seek unique dining chair designs that cater to specific market trends or brand identities. However, they often find that manufacturers have limited customization options, which can restrict their ability to differentiate their products in a competitive market. This is particularly relevant for buyers in Africa and Europe, where consumer preferences can vary significantly, requiring tailored solutions that reflect local tastes.
The Solution: Buyers should engage with manufacturers that offer flexible customization options and have a strong design team capable of translating unique concepts into production-ready designs. Before finalizing a partnership, buyers should discuss their vision and request a portfolio of past custom projects to assess the manufacturer’s capabilities. Establishing a collaborative approach during the design phase can lead to innovative solutions that meet the buyer’s needs. Additionally, exploring manufacturers that utilize advanced technologies, such as 3D printing, can provide greater flexibility in design and quicker turnaround times for prototypes. This proactive approach not only enhances product differentiation but also strengthens the buyer-manufacturer relationship.
Strategic Material Selection Guide for dining chair manufacturer
When selecting materials for dining chairs, manufacturers must consider various factors that influence performance, durability, and cost. This section analyzes four common materials used in dining chair production: wood, metal, plastic, and upholstery fabrics. Each material has its unique properties, advantages, and limitations, which are essential for international B2B buyers, especially those from Africa, South America, the Middle East, and Europe.
What Are the Key Properties of Wood in Dining Chair Manufacturing?
Wood is a traditional material favored for its aesthetic appeal and durability. Different types of wood, such as oak, maple, and teak, offer varying strength and resistance to wear. Key properties include:
- Temperature/Pressure Rating: Wood can withstand moderate pressure but may warp or crack under extreme temperature fluctuations.
- Corrosion Resistance: Naturally resistant to corrosion, but susceptible to moisture and pests unless treated.
Pros & Cons: Wood is known for its durability and timeless elegance. However, it can be costly, especially for high-quality hardwoods, and requires careful maintenance to prevent damage.
Impact on Application: Wood is compatible with various finishes and can be tailored to specific design requirements. However, international buyers should ensure compliance with local regulations regarding sustainable sourcing and treatment.
How Does Metal Perform in Dining Chair Applications?
Metal, particularly steel and aluminum, is increasingly popular for its modern look and strength.
- Key Properties: Metals are highly durable, with excellent pressure ratings. They are resistant to corrosion when treated with appropriate coatings.
- Temperature/Pressure Rating: Metals can handle high loads and are less affected by temperature changes compared to wood.
Pros & Cons: Metal chairs are often more affordable and easier to manufacture in bulk. However, they can be heavier and less comfortable without additional cushioning.
Impact on Application: Metal chairs are suitable for both indoor and outdoor use, making them versatile. Buyers should consider compliance with international standards for safety and material quality.
What Are the Advantages of Plastic in Dining Chair Manufacturing?
Plastic is a lightweight and versatile option that has gained popularity in modern dining chair designs.
- Key Properties: Plastics are resistant to moisture and easy to clean, making them ideal for high-traffic areas.
- Temperature/Pressure Rating: Generally, plastics can withstand moderate pressure but may deform under extreme heat.
Pros & Cons: The main advantages of plastic include low cost and ease of production. However, they may lack the durability and aesthetic appeal of wood or metal.
Impact on Application: Plastic chairs are often used in casual dining settings and can be compliant with various safety standards. Buyers should check for certifications regarding chemical safety, especially for food service applications.
How Do Upholstery Fabrics Affect Dining Chair Design?
Upholstery fabrics, including leather, vinyl, and synthetic materials, are crucial for comfort and style in dining chairs.
- Key Properties: Fabrics vary widely in durability, with some being stain-resistant and others requiring special care.
- Temperature/Pressure Rating: Generally, upholstery materials are not rated for temperature or pressure but should be selected based on intended use.
Pros & Cons: Upholstered chairs provide comfort and aesthetic flexibility. However, they can be more expensive and may require more maintenance than hard materials.
Impact on Application: Upholstered chairs are often preferred in formal dining settings. Buyers should consider fabric durability ratings and cleaning requirements, ensuring compliance with international textile standards.
Summary Table of Material Selection for Dining Chair Manufacturing
Material | Typical Use Case for dining chair manufacturer | Key Advantage | Key Disadvantage/Limitation | Relative Cost (Low/Med/High) |
---|---|---|---|---|
Wood | High-end residential and commercial dining chairs | Aesthetic appeal and durability | Requires maintenance and can be costly | High |
Metal | Modern dining settings, both indoor and outdoor | Strength and modern design | Heavier and less comfortable without cushioning | Medium |
Plastic | Casual dining and outdoor settings | Lightweight and easy to clean | Less durable and aesthetic appeal | Low |
Upholstery | Formal dining chairs requiring comfort and style | Comfort and design flexibility | Higher maintenance and cost | Medium to High |
This strategic material selection guide provides a comprehensive overview for international B2B buyers, enabling informed decisions that align with their specific market needs and compliance requirements.
In-depth Look: Manufacturing Processes and Quality Assurance for dining chair manufacturer
What Are the Typical Manufacturing Processes for Dining Chair Production?
The manufacturing of dining chairs involves several critical stages that ensure the final product meets quality standards and customer expectations. Understanding these processes is essential for B2B buyers looking to source dining chairs from international manufacturers.
Material Preparation: What Materials Are Used in Dining Chair Manufacturing?
The first stage in the manufacturing process is material preparation. Dining chairs can be constructed from various materials, including solid wood, engineered wood, metal, and upholstered fabrics. The choice of material significantly influences the chair’s durability, comfort, and aesthetic appeal.
-
Wood Selection: For wooden chairs, the selection process involves sourcing high-quality hardwoods such as oak, walnut, or cherry. Each type of wood has unique characteristics, and buyers should consider factors such as grain, color, and resistance to wear and tear.
-
Metal Components: For chairs that incorporate metal, such as steel or aluminum frames, the material must be treated to prevent rust and corrosion. Metal parts are often cut, shaped, and coated for added durability.
-
Upholstery Fabrics: When upholstery is involved, manufacturers often choose from a range of fabrics, including leather, synthetic fibers, and natural textiles. The fabric’s durability, stain resistance, and maintenance requirements are crucial considerations for long-lasting products.
How Are Dining Chairs Formed in the Manufacturing Process?
Once materials are prepared, the next stage is forming. This involves shaping the components into the desired design.
-
Cutting: Materials are cut into specific dimensions using precision tools and machinery. Advanced techniques such as CNC (Computer Numerical Control) cutting are often employed for accuracy.
-
Shaping: For wooden chairs, shaping may involve techniques like steam bending or carving to create ergonomic designs. Metal chairs might require welding or laser cutting to achieve intricate shapes.
-
Joining: Different components of the chair, such as legs, seats, and backs, are joined using various methods, including dowels, screws, or adhesives. The choice of joining technique can affect the chair’s structural integrity and ease of assembly.
What Are the Assembly Techniques Used in Dining Chair Manufacturing?
The assembly stage is where all the components come together to form the final product. This stage is crucial for ensuring that the chair is sturdy and functional.
-
Assembly Line Production: Many manufacturers employ an assembly line process to increase efficiency. Each worker may be responsible for a specific part of the assembly, reducing production time.
-
Quality Checks During Assembly: Quality control is integrated into the assembly process, with checkpoints to ensure that each component meets specifications before moving on to the next stage.
How Is the Finishing Process Completed for Dining Chairs?
The finishing stage is vital for enhancing the appearance and durability of dining chairs. This includes applying stains, paints, or protective coatings.
-
Surface Treatment: After assembly, chairs may undergo sanding to smooth out surfaces, followed by applying finishes that protect against scratches and moisture. This is particularly important for wooden chairs, which are often treated with varnish or lacquer.
-
Final Inspection: Before packaging, each chair undergoes a final inspection to ensure it meets quality standards and customer specifications.
What International Quality Assurance Standards Are Relevant for Dining Chair Manufacturers?
Quality assurance (QA) is a critical aspect of the dining chair manufacturing process, particularly for B2B buyers who need to ensure compliance with international standards.
Understanding ISO 9001 and Other Relevant Standards
ISO 9001 is a widely recognized quality management standard that outlines criteria for a quality management system. Compliance with ISO 9001 indicates that a manufacturer consistently meets customer and regulatory requirements. Additionally, industry-specific standards such as CE marking in Europe or ANSI/BIFMA in the U.S. may be relevant, depending on the market.
-
ISO 9001 Certification: B2B buyers should verify that their suppliers are ISO 9001 certified, which can significantly reduce the risk of defects and improve overall product quality.
-
Other Certifications: Depending on the material used, certifications related to environmental standards (like FSC for wood) can also be crucial for buyers focused on sustainability.
What Are the Key Quality Control Checkpoints in Dining Chair Manufacturing?
Quality control (QC) plays a vital role in ensuring that dining chairs meet the required standards throughout the manufacturing process. Key checkpoints include:
-
Incoming Quality Control (IQC): This is the first checkpoint where raw materials are inspected upon arrival. This ensures that only materials that meet the specified quality standards are used in production.
-
In-Process Quality Control (IPQC): During the manufacturing process, various inspections are conducted to monitor the quality of the work being done. This includes checking dimensions, assembly accuracy, and adherence to design specifications.
-
Final Quality Control (FQC): After the chairs are finished, a comprehensive inspection is performed to verify that the final product meets all quality standards before packaging and shipment.
How Can B2B Buyers Verify Supplier Quality Control Processes?
International B2B buyers need to ensure that their suppliers maintain robust quality control processes. Here are actionable steps to verify QC:
-
Conduct Supplier Audits: Regularly auditing suppliers can help buyers assess the effectiveness of their quality management systems. This can include reviewing documentation, inspecting production facilities, and observing manufacturing processes.
-
Request Quality Reports: Suppliers should provide detailed quality reports, including test results and compliance certificates. This documentation can help buyers understand the manufacturer’s commitment to quality.
-
Engage Third-Party Inspectors: Utilizing third-party inspection services can provide an unbiased evaluation of the manufacturing processes and the final products. This is particularly important for buyers from regions like Africa and South America, where local resources may be limited.
What Are the Quality Control and Certification Nuances for International Buyers?
For international B2B buyers, understanding the nuances of quality control and certification can be complex.
-
Cultural and Regulatory Differences: Quality standards may vary significantly between regions. Buyers from Europe might prioritize certifications that ensure compliance with EU regulations, while buyers from the Middle East may focus on local standards.
-
Language Barriers: Documentation provided by suppliers may be in different languages. Buyers should ensure they have access to translations or local representatives to facilitate communication and understanding.
-
Market-Specific Requirements: Certain markets may have unique requirements regarding materials and safety. For instance, fire-retardant materials may be mandated in specific regions, and buyers must ensure their suppliers are compliant.
Conclusion: Making Informed Decisions in Dining Chair Procurement
Understanding the manufacturing processes and quality assurance standards is crucial for B2B buyers looking to source dining chairs from international suppliers. By focusing on material preparation, forming, assembly, finishing, and rigorous quality control measures, buyers can ensure they procure high-quality products that meet their needs and standards. Engaging in due diligence through audits, quality reports, and third-party inspections will further safeguard their investments in the competitive dining chair market.
Practical Sourcing Guide: A Step-by-Step Checklist for ‘dining chair manufacturer’
To successfully procure dining chairs from manufacturers, international B2B buyers must follow a systematic approach. This checklist serves as a practical guide to help you navigate the complexities of sourcing dining chair manufacturers, ensuring you make informed decisions that align with your business needs.
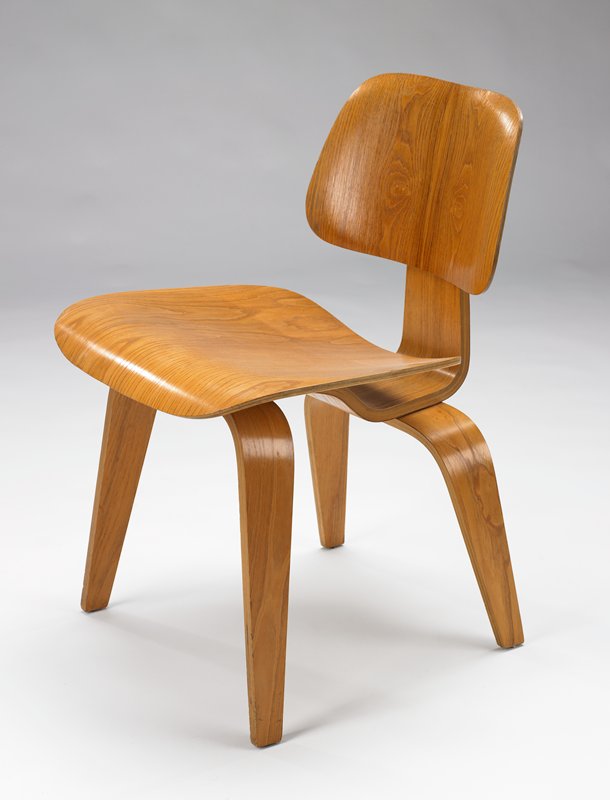
A stock image related to dining chair manufacturer.
Step 1: Define Your Technical Specifications
Establishing clear technical specifications is crucial before engaging with suppliers. This includes materials (wood, metal, upholstery), dimensions, weight capacity, and design features. Having detailed specifications helps you communicate your requirements effectively and ensures that manufacturers understand your needs.
- Material Considerations: Assess the durability and aesthetic appeal of materials.
- Design Requirements: Specify whether you need modern, traditional, or custom designs.
Step 2: Conduct Market Research
Understanding the market landscape is vital for identifying potential suppliers. Research manufacturers in different regions, especially those with a strong reputation for quality and reliability. Consider attending trade shows or industry events to network with potential suppliers and observe their products firsthand.
- Regional Focus: Look for manufacturers in regions known for furniture production, such as Europe and Southeast Asia.
- Competitor Analysis: Examine what similar businesses are using to inform your choices.
Step 3: Evaluate Potential Suppliers
Before committing, it’s crucial to vet suppliers thoroughly. Request company profiles, case studies, and references from buyers in a similar industry or region. Don’t just rely on their website; seek transparency in their operations and capabilities.
- Quality Assurance: Inquire about quality control processes and certifications (e.g., ISO).
- Production Capacity: Ensure the supplier can meet your order volume and timeline.
Step 4: Verify Supplier Certifications
Confirm that the manufacturers comply with industry standards and regulations. Certifications such as ISO 9001 for quality management systems or eco-friendly certifications can indicate a commitment to quality and sustainability.
- Sustainability Practices: Look for manufacturers who prioritize environmentally friendly materials and processes.
- Compliance with Local Standards: Ensure they meet the regulations of your target market.
Step 5: Request Samples
Always request samples before finalizing an order. Samples allow you to evaluate the craftsmanship, materials, and overall quality of the dining chairs. This step is critical in ensuring that the final products meet your expectations.
- Test Durability: Assess the sturdiness and comfort of the chairs.
- Design Validation: Ensure the samples align with your specifications and aesthetic preferences.
Step 6: Negotiate Terms and Pricing
Once you identify a suitable supplier, engage in negotiations to establish favorable terms. Discuss pricing, payment terms, delivery schedules, and any warranties or after-sales support. Clear agreements can prevent misunderstandings later on.
- Bulk Discounts: Inquire about price reductions for larger orders.
- Payment Flexibility: Explore options that align with your financial planning.
Step 7: Establish a Communication Plan
Effective communication is key to a successful partnership. Set up a communication plan outlining how often you will check in, preferred communication methods, and points of contact on both sides. This ensures that both parties remain aligned throughout the sourcing process.
- Regular Updates: Schedule regular meetings to discuss progress and address any issues.
- Crisis Management: Establish protocols for handling unexpected challenges or delays.
By following these steps, international B2B buyers can confidently navigate the complexities of sourcing dining chairs from manufacturers, ensuring that they select the best partners for their business needs.
Comprehensive Cost and Pricing Analysis for dining chair manufacturer Sourcing
What Are the Key Cost Components in Dining Chair Manufacturing?
When sourcing dining chairs, understanding the cost structure is essential for making informed purchasing decisions. The primary components of the cost structure include:
-
Materials: The choice of materials significantly impacts the cost. Common materials include wood, metal, plastic, and upholstery fabrics. High-quality materials generally lead to a higher price but can enhance durability and aesthetics.
-
Labor: Labor costs vary by region and skill level. For instance, manufacturers in regions with lower labor costs, such as parts of South America and Africa, may offer more competitive pricing. However, skilled labor is necessary for craftsmanship, particularly in custom or high-end chairs.
-
Manufacturing Overhead: This includes indirect costs associated with production, such as utilities, rent, and administrative expenses. Efficient manufacturers will have lower overhead costs, which can translate to better pricing for buyers.
-
Tooling: Initial setup costs for molds and machinery can be significant, particularly for custom designs. Buyers should consider whether these costs are factored into the quoted price.
-
Quality Control (QC): Implementing rigorous QC processes ensures product reliability, which is vital for B2B buyers. However, these processes add to the overall cost.
-
Logistics: Shipping costs can vary dramatically based on the distance, volume, and mode of transport. International buyers should factor in customs duties and tariffs, which can significantly affect total costs.
-
Margin: Manufacturers typically include a profit margin in their pricing. Understanding the average margin in the industry can help buyers gauge whether a price is fair.
How Do Price Influencers Affect Dining Chair Sourcing?
Several factors can influence the pricing of dining chairs, including:
-
Volume/MOQ (Minimum Order Quantity): Higher order volumes often lead to reduced per-unit costs. Buyers looking to purchase in bulk should negotiate for better pricing based on volume.
-
Specifications and Customization: Custom designs or specific material requests may increase costs. Buyers should weigh the benefits of customization against potential price hikes.
-
Material Quality and Certifications: Chairs made from certified sustainable materials or those that meet specific quality standards often carry a premium. Ensure that the materials align with your brand values and target market expectations.
-
Supplier Factors: The reputation and reliability of the supplier can influence pricing. Established suppliers may charge more but can offer better quality assurance and service.
-
Incoterms: Understanding shipping terms (e.g., FOB, CIF) is crucial for calculating total costs. Incoterms define responsibilities for shipping, insurance, and tariffs, which can affect the overall price.
What Are the Best Negotiation Tips for International B2B Buyers?
To maximize cost efficiency when sourcing dining chairs, international buyers should consider the following tips:
-
Conduct Market Research: Understanding the market rates for dining chairs in different regions can empower you during negotiations. Use this knowledge to justify your price expectations.
-
Emphasize Total Cost of Ownership (TCO): Rather than focusing solely on the purchase price, consider factors such as durability, maintenance, and potential resale value. A higher upfront cost may lead to lower long-term expenses.
-
Be Transparent About Your Needs: Clearly communicate your specifications and budget constraints to suppliers. This transparency can foster trust and lead to better pricing options.
-
Request Multiple Quotes: Engaging with several manufacturers can provide a clearer picture of the market and help identify the best deals.
-
Establish Long-Term Relationships: Building a rapport with suppliers can lead to better pricing and terms in future transactions. Consider negotiating contracts that facilitate long-term partnerships.
Conclusion
In summary, the cost and pricing analysis for dining chair manufacturers involves a multi-faceted approach that takes into account various cost components and price influencers. By understanding these elements and employing strategic negotiation tactics, international B2B buyers can secure favorable deals that align with their operational needs. Keep in mind that prices can vary widely based on numerous factors; thus, always seek indicative pricing tailored to your specific requirements.
Alternatives Analysis: Comparing dining chair manufacturer With Other Solutions
Understanding Alternatives in Dining Chair Solutions
In the competitive landscape of dining furniture, B2B buyers often seek alternatives to traditional dining chair manufacturers. This section provides a comparative analysis of ‘dining chair manufacturers’ against alternative solutions, highlighting key aspects that inform decision-making for international buyers from regions such as Africa, South America, the Middle East, and Europe.
Comparison Table of Dining Chair Solutions
Comparison Aspect | Dining Chair Manufacturer | Modular Furniture Solutions | Custom Upholstery Services |
---|---|---|---|
Performance | High durability and style tailored for restaurants and hotels | Versatile configurations, suitable for varied spaces | Personalized comfort and aesthetics tailored to client needs |
Cost | Moderate to high, based on material and design complexity | Typically lower initial costs, but may increase with customization | Higher costs due to bespoke designs and materials |
Ease of Implementation | Requires lead time for production and delivery | Quick setup; often pre-assembled or easy to assemble | Longer lead times due to design and production processes |
Maintenance | Regular cleaning and occasional refinishing needed | Generally low maintenance, depending on materials used | Maintenance varies; requires care to preserve upholstery |
Best Use Case | Ideal for upscale dining establishments and long-term investments | Suitable for adaptable spaces, such as cafes and co-working areas | Perfect for luxury venues requiring unique designs |
Evaluating Modular Furniture Solutions
Modular furniture solutions offer a flexible approach to dining seating. They allow for easy reconfiguration to meet changing needs, making them particularly advantageous for businesses that require adaptability. The cost is generally lower compared to traditional dining chairs, but additional expenses can arise if customization is desired. While maintenance is minimal, the performance might not match the durability of dedicated dining chair manufacturers. These solutions are best suited for casual dining environments, such as cafes or shared workspaces, where style and adaptability are crucial.
Analyzing Custom Upholstery Services
Custom upholstery services provide a highly personalized option for dining furniture, allowing buyers to select specific fabrics, colors, and styles. This can enhance the aesthetic appeal of a venue significantly. However, this option tends to be more expensive due to the bespoke nature of the service, and the lead times for delivery can be lengthy. Maintenance can also be a concern, as fabrics may require special care to maintain their appearance. Custom upholstery is ideal for high-end restaurants or boutique hotels seeking to create a distinctive atmosphere that reflects their brand identity.
Conclusion: How to Choose the Right Dining Chair Solution
When selecting the right dining chair solution, B2B buyers should carefully consider their specific needs, including budget, design requirements, and operational flexibility. If durability and long-term investment are priorities, traditional dining chair manufacturers may be the best choice. Conversely, if adaptability and lower initial costs are more critical, modular furniture solutions could be advantageous. For businesses focused on creating a unique ambiance, custom upholstery services might provide the desired aesthetic appeal, albeit at a higher cost. Ultimately, understanding these alternatives allows buyers to make informed decisions that align with their operational goals and customer expectations.
Essential Technical Properties and Trade Terminology for dining chair manufacturer
What Are the Key Technical Properties of Dining Chairs for Manufacturers?
When sourcing dining chairs, understanding the technical specifications is essential for ensuring quality and durability. Here are some critical properties to consider:
-
Material Grade
The choice of materials (wood, metal, upholstery) directly impacts the chair’s durability and aesthetic appeal. For instance, solid hardwoods like oak or beech are preferred for their strength and longevity compared to softer woods like pine. In contrast, metal frames provide a modern look and enhanced stability. Buyers should inquire about the grade of materials used, as this will affect the chair’s performance and maintenance requirements. -
Weight Capacity
Each dining chair should have a specified weight limit, typically ranging from 250 to 500 pounds. This specification is crucial for ensuring that the chairs can accommodate a diverse clientele without risk of damage or injury. Manufacturers should provide this information clearly to help buyers select appropriate seating for their target market. -
Tolerance Levels
Tolerance levels refer to the permissible limits of variation in dimensions and weight. For instance, dining chairs should maintain precise measurements for height, width, and depth to ensure comfort and compatibility with standard dining tables. Tighter tolerances often indicate higher quality manufacturing processes, which can enhance the buyer’s brand reputation. -
Finish and Coating
The finish applied to a dining chair can affect its resistance to wear, moisture, and UV light. Common finishes include varnishes, lacquers, and paints. Buyers should look for finishes that are durable and easy to clean, especially in high-traffic areas such as restaurants or cafes. -
Ergonomics
Ergonomic design is vital for comfort, particularly in settings where people may sit for extended periods. Features such as lumbar support, seat height, and armrest design should be evaluated. Manufacturers should provide data on how their designs promote good posture and user comfort.
What Are Common Trade Terms Used in the Dining Chair Manufacturing Industry?
Understanding industry jargon is essential for effective communication and negotiation. Here are some key terms frequently used in the dining chair manufacturing sector:
-
OEM (Original Equipment Manufacturer)
This term refers to companies that produce parts or equipment that may be marketed by another manufacturer. For dining chair buyers, working with an OEM can facilitate customization and ensure that the products meet specific design and quality standards. -
MOQ (Minimum Order Quantity)
MOQ indicates the smallest quantity of a product that a supplier is willing to sell. Understanding MOQ is critical for B2B buyers to manage inventory effectively and negotiate favorable terms with suppliers, especially when testing new products. -
RFQ (Request for Quotation)
An RFQ is a document sent to suppliers to request pricing, terms, and details about specific products. It helps buyers gather comparative quotes from multiple manufacturers, making it easier to assess costs and negotiate better deals. -
Incoterms (International Commercial Terms)
These are a series of predefined commercial terms published by the International Chamber of Commerce (ICC) relating to international commercial law. They define the responsibilities of buyers and sellers for shipping, insurance, and tariffs. Familiarity with Incoterms is essential for ensuring smooth transactions and avoiding misunderstandings in international trade. -
Lead Time
Lead time refers to the duration from when an order is placed until it is delivered. This term is crucial for buyers who need to align inventory levels with sales expectations. Understanding lead times helps in planning for seasonal demands or promotional events. -
BOM (Bill of Materials)
A BOM is a comprehensive list of raw materials, components, and assemblies required to manufacture a dining chair. It is essential for cost estimation and inventory management, allowing buyers to better understand the materials involved in production.
By familiarizing themselves with these technical properties and trade terms, international B2B buyers can make informed decisions that enhance their procurement processes and ultimately improve customer satisfaction.
Navigating Market Dynamics and Sourcing Trends in the dining chair manufacturer Sector
What Are the Current Market Dynamics in the Dining Chair Manufacturing Sector?
The dining chair manufacturing sector is experiencing a dynamic shift driven by several global factors. The increase in disposable income in emerging markets, particularly in Africa and South America, is spurring demand for high-quality dining furniture that combines style with functionality. Simultaneously, urbanization in the Middle East and Europe has led to smaller living spaces, making multi-functional furniture a key trend. International B2B buyers should also be aware of the growing influence of e-commerce platforms that facilitate direct sourcing, allowing for greater price transparency and access to a wider range of manufacturers.
Technological advancements are reshaping sourcing trends in this sector. The integration of augmented reality (AR) in online shopping enables buyers to visualize how dining chairs will fit into their spaces before making a purchase. Additionally, the adoption of smart manufacturing technologies, such as automation and AI, is enhancing production efficiency, reducing lead times, and enabling custom designs. B2B buyers should prioritize suppliers who leverage these technologies to stay competitive and meet evolving consumer preferences.
How Is Sustainability Shaping Sourcing Strategies in Dining Chair Manufacturing?
The importance of sustainability in the dining chair manufacturing sector cannot be overstated. As global awareness of environmental issues rises, B2B buyers are increasingly seeking manufacturers committed to ethical sourcing and sustainable practices. This includes using eco-friendly materials, such as reclaimed wood, bamboo, and recycled plastics, which not only reduce environmental impact but also appeal to a growing segment of eco-conscious consumers.
Ethical supply chains are crucial for international buyers. Manufacturers with certifications such as FSC (Forest Stewardship Council) and GOTS (Global Organic Textile Standard) demonstrate their commitment to sustainable practices. Moreover, these certifications can enhance a brand’s reputation and customer loyalty, particularly in markets like Europe and North America, where consumers are more inclined to support brands with transparent, ethical practices. By prioritizing suppliers with strong sustainability credentials, B2B buyers can align their purchasing decisions with broader corporate social responsibility goals.
What Is the Historical Context of the Dining Chair Manufacturing Industry?
The dining chair manufacturing industry has evolved significantly over the decades. Originating from simple, utilitarian designs, the sector has seen a transformation influenced by changing consumer tastes, technological advancements, and a focus on design aesthetics. In the mid-20th century, the rise of modernism introduced minimalist designs that emphasized functionality without sacrificing style. This shift paved the way for a diverse range of styles, from classic to contemporary, catering to varied consumer preferences globally.
Today, the industry is marked by a fusion of traditional craftsmanship and modern technology, allowing for innovative designs that meet contemporary demands. As international B2B buyers navigate this landscape, understanding the historical evolution of dining chair manufacturing can provide insights into current trends and future directions, enabling more informed sourcing decisions.
Frequently Asked Questions (FAQs) for B2B Buyers of dining chair manufacturer
-
How do I ensure quality when sourcing dining chairs from manufacturers?
To ensure quality when sourcing dining chairs, start by conducting thorough research on potential manufacturers. Look for verified reviews, industry certifications, and examples of their previous work. Request samples before placing bulk orders to assess materials and craftsmanship. Additionally, consider visiting the manufacturing facility if feasible, or hiring a third-party inspection service to evaluate the production process and final products. Establish clear quality standards in your contracts to safeguard your interests. -
What customization options are available for dining chairs from manufacturers?
Most dining chair manufacturers offer a range of customization options, including materials, colors, sizes, and designs. When discussing your needs, be specific about the style and functionality you require, such as ergonomic features or stackability. Request catalogues or digital mock-ups to visualize the finished product. Some manufacturers may also accommodate bespoke designs, so it’s beneficial to inquire about their flexibility and past projects to gauge their capabilities. -
What is the minimum order quantity (MOQ) for dining chairs?
The minimum order quantity (MOQ) for dining chairs varies by manufacturer and can depend on the materials and complexity of the design. Generally, MOQs can range from 50 to 500 units. If you are a smaller business or just starting, communicate your needs with manufacturers who may offer lower MOQs or tiered pricing structures for larger orders. Negotiating terms upfront can lead to better pricing and flexibility in your supply chain. -
What payment terms should I expect when ordering dining chairs internationally?
Payment terms for international orders typically involve an initial deposit, often ranging from 30% to 50%, with the balance due prior to shipment. Some manufacturers may offer net terms, allowing payment within a specified period post-delivery. It’s crucial to discuss and agree on payment methods, such as wire transfers or letters of credit, to ensure security. Establishing clear payment terms in your contract can help avoid misunderstandings and ensure a smooth transaction. -
How can I vet a dining chair manufacturer before placing an order?
To vet a dining chair manufacturer, start by checking their business credentials, including registration and industry certifications. Look for reviews and testimonials from previous clients to assess their reputation. Request references and follow up with past customers to understand their experiences. Additionally, consider the manufacturer’s production capacity, lead times, and responsiveness to inquiries, which can indicate their reliability and professionalism. -
What are the common logistics challenges when importing dining chairs?
Common logistics challenges when importing dining chairs include customs clearance, shipping delays, and damage during transit. To mitigate these risks, work with experienced freight forwarders who can navigate customs regulations and ensure proper documentation. Ensure that your dining chairs are well-packaged to minimize damage and consider purchasing insurance for high-value shipments. Establishing clear communication with your suppliers about shipping timelines can also help manage expectations.
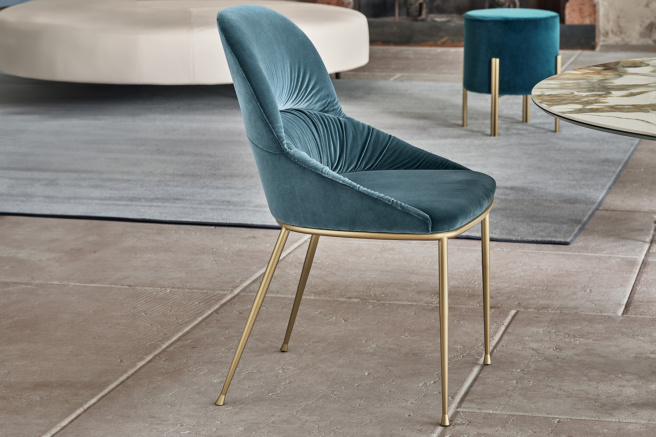
A stock image related to dining chair manufacturer.
-
What quality assurance (QA) practices should I require from manufacturers?
When sourcing dining chairs, require manufacturers to have established quality assurance (QA) practices. This includes regular inspections during production, testing of materials for durability and safety, and adherence to international quality standards. Ask for documentation of QA processes, such as inspection reports or certificates of compliance. Regular communication about QA measures and potential issues can foster a collaborative approach to maintaining product quality. -
How can I find reputable dining chair manufacturers in Africa, South America, the Middle East, and Europe?
To find reputable dining chair manufacturers in these regions, utilize online B2B platforms like Alibaba, Global Sources, or industry-specific directories. Attend trade shows and exhibitions to network with manufacturers and view their products firsthand. Leverage local business associations or trade missions that can provide leads on reliable manufacturers. Additionally, consider seeking recommendations from industry peers or using social media platforms to connect with potential suppliers.
Important Disclaimer & Terms of Use
⚠️ Important Disclaimer
The information provided in this guide, including content regarding manufacturers, technical specifications, and market analysis, is for informational and educational purposes only. It does not constitute professional procurement advice, financial advice, or legal advice.
While we have made every effort to ensure the accuracy and timeliness of the information, we are not responsible for any errors, omissions, or outdated information. Market conditions, company details, and technical standards are subject to change.
B2B buyers must conduct their own independent and thorough due diligence before making any purchasing decisions. This includes contacting suppliers directly, verifying certifications, requesting samples, and seeking professional consultation. The risk of relying on any information in this guide is borne solely by the reader.
Strategic Sourcing Conclusion and Outlook for dining chair manufacturer
What Are the Key Takeaways for International B2B Buyers in the Dining Chair Market?
Strategic sourcing is pivotal for international B2B buyers, especially in the dining chair manufacturing sector. By understanding market trends and supplier capabilities, businesses can optimize their procurement processes, ensuring that they receive high-quality products that meet their specifications. Buyers from Africa, South America, the Middle East, and Europe should prioritize suppliers who demonstrate sustainability, innovation, and adaptability to regional preferences and compliance standards.
How Can Strategic Sourcing Enhance Supply Chain Efficiency?
Investing in strategic sourcing not only reduces costs but also enhances supply chain resilience. By diversifying supplier bases and leveraging technology for better inventory management, buyers can navigate potential disruptions more effectively. This approach is particularly beneficial for markets experiencing rapid growth and demand fluctuations, as seen in many regions today.
What Should International Buyers Do Next?
As you look to the future, consider collaborating with manufacturers who are committed to quality and sustainability. Engaging in long-term partnerships will provide stability and foster innovation in product development. Now is the time to act—evaluate your sourcing strategies, align them with market demands, and connect with reputable dining chair manufacturers to ensure your business stands out in a competitive landscape. Embrace this opportunity to enhance your offerings and meet the evolving needs of your customers.