Improve Efficiency: Your Guide to Garage Equipment Suppliers (2025)
Introduction: Navigating the Global Market for garage equipment supplier
Navigating the complex landscape of sourcing garage equipment suppliers can be a daunting challenge for international B2B buyers, especially those operating in diverse markets such as Africa, South America, the Middle East, and Europe. Identifying reliable suppliers who offer high-quality products at competitive prices while ensuring compliance with local regulations is critical for businesses seeking to enhance their automotive service capabilities. This comprehensive guide to garage equipment suppliers aims to streamline your sourcing process by providing in-depth insights into various types of garage equipment, their applications, and the best practices for supplier vetting.
In this guide, you will explore the essential aspects of purchasing garage equipment, including key types of equipment, such as lifts, diagnostic tools, and repair stations, alongside their specific applications in different automotive contexts. Additionally, we will delve into the nuances of evaluating suppliers based on quality, service reputation, and cost-effectiveness. By equipping you with actionable insights and industry-specific knowledge, this guide empowers you to make informed purchasing decisions that align with your business needs.
Whether you are based in the bustling markets of Johannesburg, São Paulo, Dubai, or London, understanding the global market dynamics will enhance your competitive edge and ensure that you invest wisely in the equipment that drives your business forward.
Understanding garage equipment supplier Types and Variations
Type Name | Key Distinguishing Features | Primary B2B Applications | Brief Pros & Cons for Buyers |
---|---|---|---|
General Garage Equipment Suppliers | Offer a wide range of tools and equipment for various garage needs. | Automotive repair, maintenance shops | Pros: Comprehensive selection; Cons: May lack specialized products. |
Specialized Equipment Suppliers | Focus on niche products like tire changers or alignment machines. | Tire shops, specialized auto repair | Pros: High-quality, tailored solutions; Cons: Limited range of other equipment. |
OEM Suppliers | Provide original equipment manufacturer parts and tools. | Dealerships, authorized service centers | Pros: Guaranteed compatibility; Cons: Higher price point. |
Used Equipment Dealers | Sell pre-owned tools and machinery, often at a lower cost. | Budget-conscious repair shops | Pros: Cost-effective; Cons: Uncertain warranty and condition. |
Online Marketplace Suppliers | Platforms that aggregate various suppliers and products. | Diverse automotive businesses | Pros: Competitive pricing, wide selection; Cons: Quality assurance may vary. |
What Are General Garage Equipment Suppliers?
General garage equipment suppliers are essential for automotive repair and maintenance businesses. They provide a comprehensive selection of tools and machinery necessary for various tasks, from basic repairs to complex diagnostics. B2B buyers benefit from these suppliers due to their extensive inventory, which often includes everything from lifts to hand tools. However, while they offer variety, they may not provide specialized products tailored to specific needs, which can be a drawback for niche operations.
How Do Specialized Equipment Suppliers Operate?
Specialized equipment suppliers focus on particular types of tools, such as tire changers, wheel alignment machines, or diagnostic equipment. These suppliers cater to businesses that require high-quality, tailored solutions to meet their specific operational demands. B2B buyers should consider these suppliers when looking for equipment that requires specialized knowledge or technical support. The downside is that while they excel in their niche, their overall product range may be limited.
Why Choose OEM Suppliers for Garage Equipment?
OEM suppliers provide equipment and parts that are made by the original manufacturer of the vehicle or its components. This ensures compatibility and reliability, which is crucial for dealerships and authorized service centers. B2B buyers often prefer OEM suppliers for their assurance of quality and performance. However, the higher price point associated with OEM products can be a significant consideration for budget-conscious businesses.
What Are the Advantages of Used Equipment Dealers?
Used equipment dealers offer pre-owned tools and machinery, making them an attractive option for budget-conscious repair shops. These suppliers can provide significant savings compared to new equipment, allowing businesses to expand their capabilities without a large capital investment. However, buyers should be cautious about the condition and warranty of used products, as these factors can vary widely.
How Do Online Marketplace Suppliers Benefit B2B Buyers?
Online marketplace suppliers aggregate offerings from various manufacturers and distributors, providing B2B buyers with a vast selection of garage equipment. This model promotes competitive pricing and accessibility, allowing buyers to compare products easily. However, the quality assurance of products can vary greatly, so buyers should conduct thorough research and vet suppliers to ensure they are purchasing reliable equipment.
Related Video: Small business ideas 2024. Garage business machines. Mini manufacturing business ideas
Key Industrial Applications of garage equipment supplier
Industry/Sector | Specific Application of Garage Equipment Supplier | Value/Benefit for the Business | Key Sourcing Considerations for this Application |
---|---|---|---|
Automotive Repair | Vehicle Lifts and Hoists | Increased efficiency in vehicle servicing and repair times | Ensure compatibility with various vehicle types and weights. |
Fleet Management | Diagnostic and Repair Tools | Enhanced fleet reliability and reduced downtime | Look for equipment that offers multi-vehicle diagnostics. |
Manufacturing | Tire Changing Equipment | Improved safety and faster tire service for machinery | Evaluate durability and ease of use for high-frequency tasks. |
Construction | Portable Garage Equipment | Flexibility in job sites and quick setup for repair tasks | Consider weight, transportability, and power source options. |
Logistics and Shipping | Wheel Alignment Systems | Ensures optimal vehicle performance and fuel efficiency | Verify calibration capabilities and international compliance. |
How Are Garage Equipment Suppliers Used in the Automotive Repair Industry?
In the automotive repair sector, garage equipment suppliers provide essential tools such as vehicle lifts and hoists that facilitate efficient servicing and repairs. These tools allow mechanics to easily access the undercarriage of vehicles, which is crucial for tasks such as oil changes, brake replacements, and exhaust repairs. For international B2B buyers, particularly those in Africa and South America, it’s vital to source equipment that can handle various vehicle types and weights, ensuring compatibility with local automotive standards.
What Role Do Garage Equipment Suppliers Play in Fleet Management?
In fleet management, diagnostic and repair tools supplied by garage equipment vendors are critical for maintaining the reliability of vehicles. These tools enable fleet operators to quickly identify and resolve issues, minimizing downtime and maximizing operational efficiency. For buyers in the Middle East and Europe, selecting equipment that supports multi-vehicle diagnostics is essential, as it allows for streamlined operations across diverse vehicle models within their fleets.
Why Is Tire Changing Equipment Important in Manufacturing?
Manufacturing industries often rely on tire-changing equipment to ensure machinery operates safely and effectively. This equipment speeds up the tire service process, reducing the risk of workplace accidents and ensuring that machines remain operational. Buyers should focus on sourcing durable equipment that can withstand high-frequency usage, particularly in regions with demanding industrial environments like Africa and South America.
How Does Portable Garage Equipment Benefit the Construction Sector?
Portable garage equipment is invaluable in the construction sector, allowing for quick setup and repairs on various job sites. This flexibility enables construction teams to address vehicle maintenance needs without significant downtime, enhancing overall project efficiency. Buyers should prioritize equipment that is lightweight and easy to transport, which is particularly beneficial for companies operating in remote areas or those with fluctuating job locations.
What Are the Benefits of Wheel Alignment Systems in Logistics and Shipping?
Wheel alignment systems supplied by garage equipment vendors play a crucial role in ensuring optimal vehicle performance and fuel efficiency in logistics and shipping. Proper alignment reduces tire wear and improves handling, which is vital for maintaining a reliable fleet. International buyers must ensure that the systems they procure are compliant with local standards and capable of precise calibration to meet the specific needs of their operations.
Related Video: Industrial Control Panel Basics
3 Common User Pain Points for ‘garage equipment supplier’ & Their Solutions
Scenario 1: Ensuring Equipment Compliance with Local Regulations
The Problem: International B2B buyers often face challenges related to compliance with local regulations when sourcing garage equipment. This issue is particularly acute for businesses operating in multiple regions, as regulations can vary significantly between countries. For example, equipment that meets safety standards in Europe may not be compliant with regulations in South America or Africa. This can lead to costly delays, fines, or the need to modify or replace equipment.
The Solution: To navigate these compliance challenges, buyers should engage in thorough research and establish strong communication with their garage equipment suppliers. This includes asking suppliers for detailed documentation regarding compliance with local standards, such as CE marking in Europe or ISO certifications. Additionally, buyers should consult local industry associations or regulatory bodies to stay updated on the latest requirements. A proactive approach involves developing a checklist of compliance standards relevant to each market and ensuring that suppliers can provide proof of adherence before finalizing any purchase. Regular training sessions for staff on compliance can also help mitigate risks associated with equipment usage.
Scenario 2: Managing Equipment Downtime and Maintenance
The Problem: Equipment downtime can significantly impact productivity and profitability for businesses that rely on garage equipment. For instance, a breakdown of a vehicle lift or diagnostic machine can halt operations, leading to lost revenue and dissatisfied customers. B2B buyers often struggle to find suppliers who provide not only the equipment but also reliable maintenance and support services.
The Solution: To address this pain point, buyers should prioritize suppliers that offer comprehensive maintenance packages and robust customer support. When evaluating potential suppliers, it’s crucial to inquire about their service level agreements (SLAs) and response times for repairs. Buyers can also consider suppliers that have a track record of providing timely maintenance services and training on equipment usage. Establishing a routine maintenance schedule based on manufacturer recommendations can minimize unexpected breakdowns. Additionally, leveraging technology such as equipment monitoring systems can help anticipate issues before they lead to downtime, enabling businesses to schedule repairs during non-peak hours.
Scenario 3: Difficulty in Sourcing Specialized Equipment
The Problem: Sourcing specialized garage equipment that meets specific operational needs can be a daunting task for B2B buyers. Many suppliers may offer standard equipment but lack the capability to provide customized solutions, which can lead to inefficiencies and hinder business operations. This is especially true for businesses in niche markets, such as electric vehicle servicing or heavy-duty truck maintenance.
The Solution: To overcome this sourcing challenge, buyers should identify and collaborate with suppliers who specialize in their specific industry segment. Conducting a market analysis to locate suppliers that offer customized solutions is essential. Buyers can also attend industry trade shows and conferences to network with suppliers and gain insights into the latest technologies and equipment innovations. When discussing requirements with potential suppliers, it’s important to provide detailed specifications and operational needs to ensure they can deliver the right solutions. Creating a pilot project for new equipment can also help assess its effectiveness before making a larger investment. Engaging with suppliers early in the product development process can foster innovation and lead to tailored solutions that better fit the business’s unique requirements.
Strategic Material Selection Guide for garage equipment supplier
What Are the Key Materials Used in Garage Equipment and Their Properties?
When selecting materials for garage equipment, international B2B buyers must consider various factors, including performance, durability, cost, and compliance with regional standards. Below are analyses of four common materials used in garage equipment, focusing on their properties, pros and cons, and specific considerations for buyers from Africa, South America, the Middle East, and Europe.
How Does Steel Perform in Garage Equipment Applications?
Steel is one of the most widely used materials in garage equipment due to its excellent strength-to-weight ratio and versatility.
- Key Properties: Steel typically exhibits high tensile strength, good temperature resistance, and can withstand considerable pressure. It is also available in various grades, allowing for tailored performance characteristics.
- Pros & Cons: The durability of steel makes it suitable for heavy-duty applications, but it can be prone to corrosion if not properly treated. While the manufacturing process can be complex, the cost remains relatively low compared to other materials.
- Impact on Application: Steel is compatible with various media, making it suitable for hydraulic systems and lifting equipment.
- Considerations for Buyers: Buyers should ensure compliance with international standards such as ASTM A36 or EN 10025. Corrosion-resistant coatings may be necessary in humid climates, particularly in regions like South America and Africa.
What Advantages Does Aluminum Offer in Garage Equipment?
Aluminum is increasingly popular in garage equipment due to its lightweight nature and resistance to corrosion.
- Key Properties: Aluminum has a lower density than steel, making it easier to handle and transport. It also exhibits good thermal and electrical conductivity.
- Pros & Cons: The main advantage of aluminum is its corrosion resistance, which is vital for equipment exposed to the elements. However, it is generally less durable than steel and can be more expensive, particularly for high-strength alloys.
- Impact on Application: Aluminum is ideal for applications requiring lightweight components, such as portable lifts and tools.
- Considerations for Buyers: Compliance with standards like ASTM B221 is crucial. Buyers in Europe may prefer aluminum due to its recyclability and lower environmental impact.
Why Is Plastic Used in Garage Equipment?
Plastic materials, particularly high-density polyethylene (HDPE) and polypropylene, are commonly used for various components in garage equipment.
- Key Properties: Plastics are lightweight, resistant to chemicals, and can withstand a range of temperatures. They also have good impact resistance.
- Pros & Cons: The primary advantage of plastic is its resistance to corrosion and chemicals, making it suitable for storage tanks and containers. However, plastics may not withstand high temperatures or heavy loads as well as metals, which can limit their applications.
- Impact on Application: Plastics are often used in non-structural components, such as storage bins and tool organizers.
- Considerations for Buyers: Buyers should check for compliance with standards such as ASTM D638 for tensile strength. In regions with high UV exposure, UV-stabilized plastics may be necessary.
How Does Composite Material Enhance Garage Equipment?
Composite materials, which combine two or more constituent materials, are gaining traction in garage equipment for their unique properties.
- Key Properties: Composites can be engineered to provide high strength while remaining lightweight. They often exhibit excellent fatigue resistance and can be tailored for specific applications.
- Pros & Cons: The main advantage of composites is their versatility and ability to resist corrosion and wear. However, they can be more expensive and complex to manufacture, which may deter some buyers.
- Impact on Application: Composites are suitable for specialized applications, such as high-performance automotive parts and tools.
- Considerations for Buyers: Buyers should ensure that composites meet relevant industry standards, such as ASTM D3039 for tensile properties. Additionally, understanding the specific environmental conditions in regions like the Middle East is crucial for selecting the right composite material.
Summary Table of Material Selection for Garage Equipment
Material | Typical Use Case for Garage Equipment Supplier | Key Advantage | Key Disadvantage/Limitation | Relative Cost (Low/Med/High) |
---|---|---|---|---|
Steel | Hydraulic lifts, structural components | High strength and durability | Prone to corrosion | Low |
Aluminum | Portable tools, lifting equipment | Lightweight and corrosion-resistant | Less durable than steel | Med |
Plastic | Storage bins, non-structural components | Chemical resistance and lightweight | Limited high-temperature performance | Low |
Composite | High-performance automotive parts | Tailored strength and lightweight | Higher manufacturing complexity | High |
This strategic material selection guide provides international B2B buyers with essential insights into the properties, advantages, and limitations of materials commonly used in garage equipment, helping them make informed purchasing decisions.
In-depth Look: Manufacturing Processes and Quality Assurance for garage equipment supplier
What Are the Main Stages of Manufacturing Garage Equipment?
The manufacturing of garage equipment encompasses several critical stages, each designed to ensure that the final products meet both quality and functionality standards. Understanding these stages can help international B2B buyers make informed decisions when selecting suppliers.
Material Preparation: How Are Raw Materials Selected and Processed?
The first stage in manufacturing garage equipment involves the careful selection and preparation of raw materials, which typically include metals like steel and aluminum, plastics, and composites. Suppliers must ensure that the materials meet specific industry standards for durability and safety. This often involves sourcing materials from certified suppliers and conducting preliminary quality checks.
Once selected, raw materials undergo processes such as cutting, shaping, and treating to prepare them for the next stages of production. Techniques like laser cutting or CNC machining are commonly used to achieve precision and minimize waste, which is crucial for maintaining cost-effectiveness in manufacturing.
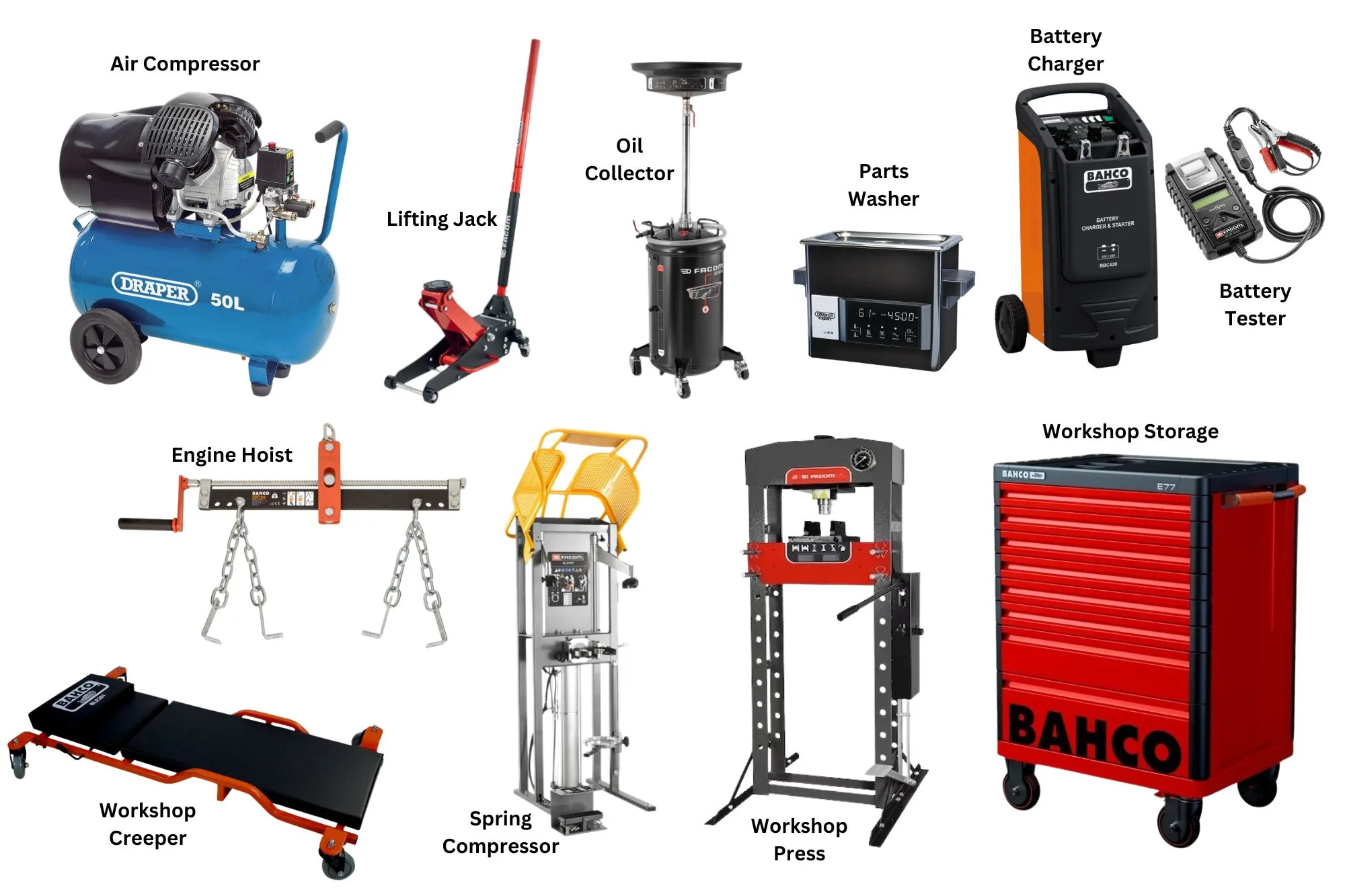
A stock image related to garage equipment supplier.
Forming: What Techniques Are Used to Shape Garage Equipment Components?
The forming stage involves shaping the prepared materials into the desired components. This can include processes like stamping, bending, and welding. Techniques such as hydroforming and deep drawing are also utilized, especially for complex shapes.
In this stage, it is essential for manufacturers to adhere to strict tolerances to ensure that parts fit together correctly during assembly. B2B buyers should inquire about the specific forming techniques used by suppliers and whether they have the necessary equipment to produce high-quality components consistently.
Assembly: How Is Garage Equipment Assembled for Optimal Performance?
Once the components are formed, they move to the assembly stage. This involves fitting together various parts, such as frames, hydraulic systems, and electronic controls. Assembly can be manual or automated, depending on the scale of production and the complexity of the equipment.
Quality assurance during assembly is critical. Manufacturers often implement standardized assembly procedures, which include the use of jigs and fixtures to ensure consistency. B2B buyers should request information about the assembly process and whether it includes checks to verify component compatibility and functionality.
Finishing: What Processes Enhance the Durability and Aesthetics of Garage Equipment?
The finishing stage aims to enhance both the durability and appearance of garage equipment. This may involve processes such as painting, powder coating, galvanizing, or anodizing. These techniques not only improve aesthetics but also provide protection against corrosion and wear, which is vital for equipment used in various environments.
International B2B buyers should be aware of the finishing techniques employed by suppliers and their compliance with environmental regulations regarding hazardous materials. Understanding the finishing processes can also provide insights into the expected lifespan and maintenance requirements of the equipment.
What Are the Key Quality Assurance Standards for Garage Equipment?
Quality assurance (QA) is a vital aspect of the manufacturing process for garage equipment, ensuring that products meet specific standards and regulations. Buyers from regions like Africa, South America, the Middle East, and Europe should familiarize themselves with relevant QA standards and practices.
Which International Standards Should B2B Buyers Be Aware Of?
The most recognized international standard for quality management is ISO 9001. This standard outlines the criteria for a quality management system and is based on principles such as customer focus, leadership, and continuous improvement. Manufacturers adhering to ISO 9001 demonstrate a commitment to quality and customer satisfaction.
In addition to ISO 9001, industry-specific standards such as CE marking in Europe and API (American Petroleum Institute) certifications are critical. CE marking indicates that products meet European safety, health, and environmental protection requirements, while API standards are essential for equipment used in the oil and gas sector.
What Are the Key Quality Control Checkpoints in Garage Equipment Manufacturing?
Quality control (QC) involves systematic checks at various points in the manufacturing process. Key QC checkpoints include:
- Incoming Quality Control (IQC): This involves inspecting raw materials upon arrival to ensure they meet specified standards.
- In-Process Quality Control (IPQC): Conducted during the manufacturing process, this step ensures that operations adhere to set parameters and that any deviations are addressed immediately.
- Final Quality Control (FQC): This final inspection checks the completed product against quality standards before shipping.
B2B buyers should ask suppliers about their QC protocols and how often these checkpoints are performed.
How Can B2B Buyers Verify Supplier Quality Control Processes?
Verifying a supplier’s quality control processes is crucial for international B2B buyers, particularly in ensuring that products meet regional and international standards.
What Methods Can Buyers Use to Assess Supplier Quality Control?
-
Supplier Audits: Conducting on-site audits allows buyers to assess the manufacturing environment, equipment, and QA practices firsthand. This is particularly important for buyers from Africa and South America, where local regulations may differ significantly from international standards.
-
Quality Assurance Reports: Requesting recent QA reports can provide insights into a supplier’s performance over time. These reports should include data on defect rates, customer complaints, and corrective actions taken.
-
Third-Party Inspections: Engaging third-party inspection agencies can provide an unbiased evaluation of the supplier’s quality control processes. This is a common practice among buyers in Europe and the Middle East who require additional assurance before placing large orders.
What Are the Nuances of QC and Certifications for International Buyers?
International buyers should also be aware of the nuances related to certifications. For instance, while CE marking is essential for the European market, it may not hold the same weight in Africa or South America. Buyers should ensure that the certifications a supplier holds are relevant to their specific market requirements.
Understanding these nuances can aid in selecting suppliers who are not only compliant with international standards but also aligned with regional regulations and expectations. This knowledge is particularly valuable for B2B buyers navigating complex supply chains across diverse markets.
In conclusion, a comprehensive understanding of manufacturing processes and quality assurance can empower international B2B buyers to make informed purchasing decisions, ensuring they select suppliers capable of delivering high-quality garage equipment that meets their specific needs.
Practical Sourcing Guide: A Step-by-Step Checklist for ‘garage equipment supplier’
In the competitive landscape of garage equipment procurement, especially for international B2B buyers from regions like Africa, South America, the Middle East, and Europe, following a structured sourcing checklist can streamline the process and enhance decision-making. This guide outlines essential steps to ensure you select a reliable garage equipment supplier that meets your business needs.
Step 1: Define Your Technical Specifications
Understanding your technical requirements is crucial in the sourcing process. Clearly outline the types of garage equipment you need, such as lifts, diagnostic tools, or tire changers. This helps in narrowing down suppliers who specialize in those specific products, ensuring compatibility with your operations.
- Considerations: Identify the models, sizes, and capacities required based on your garage’s operations.
- Documentation: Create a detailed specifications document to share with potential suppliers.
Step 2: Research Potential Suppliers
Conduct thorough research to identify reputable garage equipment suppliers. Utilize online directories, industry forums, and trade shows to compile a list of potential partners. This step is vital as it lays the foundation for your supplier selection process.
- Sources: Leverage platforms like LinkedIn, Alibaba, and industry-specific forums.
- Network: Engage with industry contacts to gather recommendations and insights about supplier reliability.
Step 3: Evaluate Supplier Certifications
Verification of supplier certifications is essential to ensure compliance with international standards. Look for ISO certifications, safety standards, and industry-specific accreditations that guarantee quality and reliability in products.
- Documentation: Request copies of certifications and any relevant compliance documentation.
- Importance: Certifications not only reflect quality but also commitment to industry best practices.
Step 4: Request Quotes and Compare Pricing
Once you have a shortlist of suppliers, request detailed quotes for the equipment you need. Comparing pricing is not just about finding the lowest cost; consider the value offered, including warranty, after-sales support, and delivery times.
- Breakdown: Ensure quotes include a breakdown of costs, such as shipping, installation, and maintenance.
- Negotiation: Use quotes to negotiate better terms with suppliers.
Step 5: Assess After-Sales Support and Service
After-sales support is a critical factor in the longevity and performance of your garage equipment. Inquire about warranty terms, service agreements, and availability of spare parts. This ensures that you have support for maintenance and repairs, which can minimize downtime.
- Service Level Agreements (SLAs): Look for clear SLAs detailing response times and service commitments.
- Local Support: Check if the supplier offers local support or has partnerships with service providers in your region.
Step 6: Verify References and Past Performance
Before making a final decision, verify the supplier’s references and assess their past performance. Contact previous clients to understand their experiences, focusing on product quality, service reliability, and support responsiveness.
- Questions to Ask: Inquire about the supplier’s ability to meet deadlines and handle issues.
- Case Studies: Request case studies or testimonials that illustrate successful partnerships.
Step 7: Finalize the Contract and Terms
Once you have chosen a supplier, ensure that all terms and conditions are clearly defined in a formal contract. This should include payment terms, delivery schedules, and service obligations to avoid any misunderstandings.
- Legal Review: Consider having a legal professional review the contract to ensure it protects your interests.
- Flexibility: Ensure there are clauses for adjustments based on changing business needs or unforeseen circumstances.
By following this structured checklist, international B2B buyers can effectively navigate the complexities of sourcing garage equipment, ultimately leading to informed decisions that enhance operational efficiency and productivity.
Comprehensive Cost and Pricing Analysis for garage equipment supplier Sourcing
What Are the Key Cost Components for Garage Equipment Suppliers?
When sourcing garage equipment, understanding the comprehensive cost structure is crucial for international B2B buyers. The primary cost components include:
-
Materials: This is often the largest expense and varies significantly based on the type of equipment. For instance, high-grade steel or specialized alloys for automotive lifts will be costlier than standard materials used in simpler tools.
-
Labor: Skilled labor is required for manufacturing complex equipment, which can increase costs. Labor costs also differ by region; for example, sourcing from Europe may incur higher labor expenses compared to sourcing from South America or Africa.
-
Manufacturing Overhead: This encompasses expenses related to utilities, maintenance, and rent. Understanding the overhead costs of potential suppliers can provide insights into their pricing strategies.
-
Tooling: Investment in specific tools or molds necessary for production can add to initial costs, especially for customized or specialized equipment.
-
Quality Control (QC): Quality assurance processes, including testing and certifications, are essential to ensure product reliability and safety. These processes can add to the overall cost.
-
Logistics: Transportation and storage costs must be factored in, particularly for international shipments. Factors such as distance, mode of transport, and customs duties significantly influence logistics costs.
-
Margin: Finally, suppliers will add a profit margin to their pricing, which can vary based on their business model and market competition.
How Do Price Influencers Impact Garage Equipment Sourcing?
Several factors influence pricing that international buyers should consider:
-
Volume and Minimum Order Quantity (MOQ): Suppliers often provide discounts for bulk purchases. Understanding the MOQ can help buyers negotiate better terms and reduce per-unit costs.
-
Specifications and Customization: Custom equipment designed to meet specific requirements can lead to higher prices. Buyers should assess whether the customization is necessary or if off-the-shelf solutions suffice.
-
Materials and Quality Certifications: The choice of materials affects both performance and price. Additionally, equipment with recognized quality certifications may command higher prices due to the assurance of durability and safety.
-
Supplier Factors: Established suppliers may have higher prices due to brand reputation and reliability. However, lesser-known suppliers might offer competitive pricing but with potential risks regarding quality and service.
-
Incoterms: The terms of sale (Incoterms) dictate who is responsible for shipping, insurance, and tariffs. Understanding these terms is essential as they can significantly affect the total landed cost of equipment.
What Are Effective Buyer Tips for Cost-Efficiency?
To maximize value in garage equipment sourcing, buyers should consider the following strategies:
-
Negotiate Pricing: Always engage in negotiations. Suppliers may have flexibility in pricing, especially if you are ordering in bulk or establishing a long-term relationship.
-
Evaluate Total Cost of Ownership (TCO): Beyond initial purchase price, consider long-term costs including maintenance, operational efficiency, and potential downtime. Equipment that costs more upfront might save money in the long run through reduced maintenance needs.
-
Understand Pricing Nuances: International buyers should be aware of currency fluctuations, import taxes, and additional fees that can affect the final price. Engaging local experts can provide insights into regional pricing trends.
-
Research Supplier Reputation: Before making a decision, research potential suppliers thoroughly. Check reviews, request references, and verify their compliance with international quality standards.
Disclaimer on Indicative Prices
Prices for garage equipment can vary widely based on the aforementioned factors. The cost analysis presented here is indicative and should be supplemented with quotes from multiple suppliers to ensure competitive pricing. Always conduct thorough due diligence when finalizing your sourcing decisions to align with your business objectives.
Alternatives Analysis: Comparing garage equipment supplier With Other Solutions
Understanding Alternative Solutions to Garage Equipment Suppliers
When evaluating options for garage equipment, international B2B buyers must consider various alternatives to traditional garage equipment suppliers. These alternatives can offer unique benefits tailored to specific business needs, whether in terms of performance, cost-efficiency, or ease of implementation. In this analysis, we will compare the conventional garage equipment supplier model with two viable alternatives: DIY Equipment Solutions and Automated Garage Management Systems. This comparison aims to help buyers make informed decisions based on their operational requirements and budget constraints.
Comparison Aspect | Garage Equipment Supplier | DIY Equipment Solutions | Automated Garage Management Systems |
---|---|---|---|
Performance | High-quality, reliable gear | Variable quality, depending on sourcing | Advanced tech integration for efficiency |
Cost | Higher upfront investment | Lower initial costs, but potential for higher long-term expenses | Moderate to high costs, depending on tech used |
Ease of Implementation | Straightforward, guided setup | Requires expertise for assembly | Requires training but offers seamless integration |
Maintenance | Professional support available | Self-maintained, may require more effort | Automated updates and remote support |
Best Use Case | Established garages needing comprehensive solutions | Small-scale operations or hobbyists | Large-scale garages seeking efficiency and data tracking |
What Are the Pros and Cons of DIY Equipment Solutions?
DIY Equipment Solutions can be an attractive option for businesses looking to save on upfront costs. Buyers can source components individually, allowing for customization and potential savings. However, the quality of these components can vary significantly, leading to inconsistent performance. Additionally, assembly and maintenance require a certain level of expertise, which may not be feasible for all businesses. This option is best suited for small-scale operations or hobbyists who have the time and skill to manage equipment themselves.
How Do Automated Garage Management Systems Compare?
Automated Garage Management Systems represent a technological evolution in garage operations. These systems integrate advanced technology for inventory management, scheduling, and even customer relationship management. While they can offer significant efficiency gains and data-driven insights, the initial investment and training can be substantial. Moreover, businesses must be prepared for ongoing costs related to system updates and maintenance. This solution is particularly beneficial for large-scale operations aiming to streamline processes and enhance productivity.
Conclusion: Choosing the Right Solution for Your Garage Equipment Needs
Selecting the most suitable solution for garage equipment depends on a variety of factors, including your operational scale, budget, and specific needs. For businesses with established operations requiring reliable equipment and professional support, traditional garage equipment suppliers may be the best choice. Conversely, DIY solutions may appeal to smaller operations or those with technical expertise, while automated systems can greatly benefit larger enterprises aiming for efficiency and data optimization. By carefully evaluating these alternatives, B2B buyers can make informed decisions that align with their business goals and operational capabilities.
Essential Technical Properties and Trade Terminology for garage equipment supplier
What are the Essential Technical Properties of Garage Equipment?
When sourcing garage equipment, international B2B buyers must understand several critical technical specifications that impact performance, safety, and compliance. Here are key properties to consider:
-
Material Grade
– The material grade refers to the quality and type of materials used in manufacturing garage equipment, such as steel, aluminum, or composite materials. Higher-grade materials typically offer better durability, resistance to corrosion, and overall performance. For buyers, selecting equipment made from appropriate material grades ensures longevity and reduced maintenance costs. -
Load Capacity
– This specification indicates the maximum weight that a piece of equipment can safely handle. Understanding load capacity is crucial for ensuring operational safety and efficiency in any garage setting. Buyers should assess their operational needs to select equipment that meets or exceeds their required load specifications. -
Tolerance Levels
– Tolerance refers to the allowable deviation from a specified dimension or measurement. In garage equipment, tighter tolerances can lead to better performance and safety. For B2B buyers, recognizing the importance of tolerance levels helps in selecting equipment that minimizes wear and tear and enhances precision in operations. -
Power Rating
– The power rating, often measured in horsepower (HP) or kilowatts (kW), indicates the energy output of equipment like lifts and compressors. A higher power rating typically correlates with better performance and faster operation. Buyers must align power ratings with their operational demands to ensure efficiency and productivity. -
Safety Features
– This encompasses various built-in protections, such as emergency stops, overload sensors, and automatic shut-off mechanisms. Safety features are essential for protecting workers and preventing equipment damage. B2B buyers should prioritize equipment with robust safety features to comply with regulations and safeguard personnel.
What Trade Terminology Should B2B Buyers Know in the Garage Equipment Sector?
Understanding industry jargon is critical for effective communication and negotiation in the garage equipment sector. Here are common terms buyers should familiarize themselves with:
-
OEM (Original Equipment Manufacturer)
– OEM refers to companies that produce parts or equipment that may be marketed by another manufacturer. In the garage equipment industry, working with OEMs can ensure high-quality components and compatibility with existing systems. Buyers should consider OEM products for reliability and warranty support. -
MOQ (Minimum Order Quantity)
– MOQ is the smallest quantity of a product that a supplier is willing to sell. Understanding MOQ is vital for B2B buyers as it impacts purchasing decisions and inventory management. Buyers should negotiate MOQs that align with their demand to avoid excess inventory costs. -
RFQ (Request for Quotation)
– An RFQ is a formal document sent to suppliers to request pricing, terms, and conditions for specific products. It is a critical step in the procurement process, allowing buyers to compare offers and make informed decisions. B2B buyers should prepare detailed RFQs to receive accurate and competitive quotations. -
Incoterms (International Commercial Terms)
– Incoterms are a set of predefined commercial terms published by the International Chamber of Commerce (ICC) that define the responsibilities of buyers and sellers in international transactions. Familiarity with Incoterms helps B2B buyers understand shipping costs, insurance responsibilities, and risk management during the procurement process. -
Lead Time
– Lead time refers to the time taken from placing an order to receiving the product. Understanding lead times is essential for planning and inventory management. Buyers should inquire about lead times during negotiations to ensure timely delivery of equipment.
By grasping these technical properties and trade terms, B2B buyers can make more informed decisions when sourcing garage equipment, ultimately leading to better operational efficiency and cost management.
Navigating Market Dynamics and Sourcing Trends in the garage equipment supplier Sector
What Are the Key Market Dynamics and Sourcing Trends in the Garage Equipment Supplier Sector?
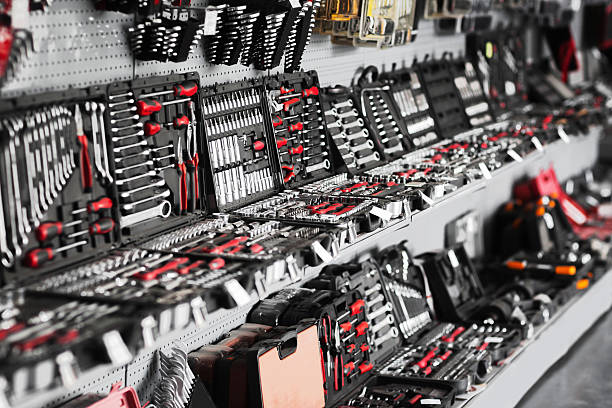
A stock image related to garage equipment supplier.
The garage equipment supplier sector is witnessing transformative changes driven by technological advancements and evolving customer expectations. Globally, the rise of electric vehicles (EVs) and autonomous vehicles is reshaping the market landscape. Suppliers are increasingly focusing on specialized equipment that caters to the unique maintenance and repair needs of these vehicles. In regions such as Africa, South America, the Middle East, and Europe, international B2B buyers must adapt to this shift by sourcing innovative tools and equipment that align with the latest automotive technologies.
Emerging trends such as the integration of IoT (Internet of Things) technology in garage equipment are enhancing operational efficiency and service delivery. Smart tools that can communicate with vehicle systems for diagnostics and repair are becoming essential. Additionally, the demand for automation in garages is on the rise, prompting suppliers to offer robotic solutions for tasks like tire changes and vehicle inspections. This trend is particularly relevant in Europe, where labor shortages and increased productivity demands are pushing businesses to adopt automated solutions.
Buyers should also pay attention to supply chain resilience amid global disruptions. Sourcing from diverse suppliers and regions can mitigate risks associated with geopolitical tensions, trade barriers, and environmental challenges. Establishing partnerships with suppliers who can provide flexible, scalable solutions will be crucial for maintaining competitive advantages.
How Is Sustainability Impacting Sourcing Decisions in the Garage Equipment Supplier Sector?
Sustainability is increasingly becoming a pivotal consideration for international B2B buyers in the garage equipment supplier sector. The environmental impact of manufacturing processes and the lifecycle of garage equipment is under scrutiny, leading buyers to seek suppliers who prioritize eco-friendly practices. This includes using sustainable materials, reducing waste, and optimizing energy consumption in production.
The importance of ethical sourcing cannot be overstated. Buyers are now looking for suppliers who adhere to strict ethical standards, ensuring fair labor practices and responsible sourcing of raw materials. Certifications such as ISO 14001 for environmental management and LEED for sustainable building practices are becoming important indicators of a supplier’s commitment to sustainability.
Moreover, the demand for “green” certifications and materials is growing. For example, garage equipment made from recycled or sustainably sourced materials is gaining traction, as buyers aim to reduce their carbon footprint. Suppliers that can demonstrate their commitment to sustainability through transparent reporting and eco-friendly product lines will be better positioned to meet the needs of conscientious B2B buyers.
What Is the Historical Context of the Garage Equipment Supplier Sector?
The garage equipment supplier sector has evolved significantly over the past few decades. Initially dominated by manual tools and equipment, the industry has transitioned towards more sophisticated, technology-driven solutions. The introduction of computer-based diagnostic tools in the 1980s marked a turning point, allowing mechanics to access vehicle data and troubleshoot issues more efficiently.
As vehicles became more complex, so did the tools required for their maintenance and repair. The late 1990s and early 2000s saw a surge in the development of specialized equipment for various vehicle types, including heavy-duty trucks and EVs. This evolution continues today, with suppliers innovating to meet the demands of a rapidly changing automotive landscape.
Understanding this historical context is vital for B2B buyers, as it highlights the continuous need for adaptation and forward-thinking strategies in sourcing garage equipment. By recognizing past trends, buyers can better anticipate future shifts and align their purchasing strategies accordingly.
Frequently Asked Questions (FAQs) for B2B Buyers of garage equipment supplier
-
How can I identify a reliable garage equipment supplier?
To identify a reliable garage equipment supplier, start by researching their reputation in the industry. Look for reviews and testimonials from other B2B buyers, and check their track record of delivering quality products on time. Attend trade shows and industry events to meet suppliers in person and assess their offerings. Additionally, request references from previous clients to gauge their reliability and customer service. Consider suppliers who comply with international quality standards, as this often reflects their commitment to excellence. -
What types of garage equipment should I consider for my business?
The best garage equipment for your business depends on the services you plan to offer. Common types include vehicle lifts, tire changers, wheel balancers, and diagnostic tools. Evaluate your target market’s needs and tailor your equipment selection accordingly. For instance, if you specialize in high-performance vehicles, invest in advanced diagnostic tools and lifts that accommodate larger vehicles. Consulting with industry experts can also provide insights into the most valuable equipment for your specific niche. -
What are the typical minimum order quantities (MOQs) from garage equipment suppliers?
Minimum order quantities (MOQs) can vary significantly between garage equipment suppliers. Generally, MOQs for large machinery may range from one to five units, while smaller items could have MOQs as low as ten or twenty. It’s essential to discuss your specific needs with suppliers, as some may be flexible with MOQs for first-time buyers or larger orders. Understanding MOQs can help you manage your inventory and cash flow effectively, especially in emerging markets like Africa and South America.
-
What payment terms should I expect when sourcing garage equipment?
Payment terms can vary widely among garage equipment suppliers, but common options include net 30, net 60, or upfront payments. For international transactions, it’s advisable to use secure payment methods like letters of credit or escrow services to protect your investment. Discussing payment terms in advance can help establish a clear understanding and build trust with your supplier. Ensure that you also clarify any additional fees for shipping and customs duties to avoid unexpected costs. -
How can I ensure quality assurance when sourcing garage equipment?
To ensure quality assurance, request detailed specifications and certifications for the equipment you plan to purchase. Look for suppliers who have implemented quality control processes and are compliant with international standards, such as ISO certification. Conducting factory visits or third-party inspections can provide further assurance of product quality. Additionally, consider negotiating trial periods for new equipment to assess its performance before committing to larger orders. -
What logistics considerations should I be aware of when importing garage equipment?
Logistics is critical when importing garage equipment. Familiarize yourself with the shipping options available, including air freight for speed and sea freight for cost-effectiveness. Understand the customs regulations in your country, as tariffs and import duties can significantly impact your total costs. Collaborating with a reliable freight forwarder can streamline the shipping process and help navigate any potential challenges. Additionally, factor in lead times for production and shipping to ensure timely delivery of your equipment. -
How can I customize garage equipment to meet my specific needs?
Many suppliers offer customization options for garage equipment. Start by discussing your specific requirements during initial consultations with potential suppliers. Customizations may include modifications to the size, features, or branding of the equipment. Be prepared to provide detailed specifications and examples of what you envision. Some suppliers may require a minimum order quantity for customized products, so ensure to clarify this aspect early in the negotiation process.
- What are the key factors to consider when negotiating with garage equipment suppliers?
When negotiating with suppliers, consider factors such as price, payment terms, delivery schedules, and warranty conditions. Research comparable products and pricing in the market to strengthen your negotiating position. Building a relationship with your supplier can also be beneficial, as trust often leads to better terms. Additionally, be clear about your expectations regarding quality and service, and ensure that these elements are included in the contract to prevent misunderstandings later on.
Important Disclaimer & Terms of Use
⚠️ Important Disclaimer
The information provided in this guide, including content regarding manufacturers, technical specifications, and market analysis, is for informational and educational purposes only. It does not constitute professional procurement advice, financial advice, or legal advice.
While we have made every effort to ensure the accuracy and timeliness of the information, we are not responsible for any errors, omissions, or outdated information. Market conditions, company details, and technical standards are subject to change.
B2B buyers must conduct their own independent and thorough due diligence before making any purchasing decisions. This includes contacting suppliers directly, verifying certifications, requesting samples, and seeking professional consultation. The risk of relying on any information in this guide is borne solely by the reader.
Strategic Sourcing Conclusion and Outlook for garage equipment supplier
What Are the Key Takeaways for Strategic Sourcing in Garage Equipment?
In today’s competitive landscape, strategic sourcing remains a cornerstone for international B2B buyers seeking garage equipment. Understanding market dynamics, supplier capabilities, and regional compliance is crucial for informed decision-making. Buyers from Africa, South America, the Middle East, and Europe should leverage data-driven insights to evaluate suppliers, ensuring they align with operational needs and financial goals. The adoption of technology in sourcing processes can streamline procurement and enhance supplier relationships, driving long-term value.
How Can B2B Buyers Prepare for Future Sourcing Opportunities?
Looking ahead, the garage equipment sector is poised for growth, driven by advancements in technology and shifts in consumer behavior. International buyers are encouraged to stay informed about emerging trends, such as eco-friendly equipment and automation. By prioritizing sustainable practices and investing in innovative solutions, businesses can not only meet regulatory demands but also enhance their market position.
What Actions Should Buyers Take Today?
Now is the time for international B2B buyers to evaluate their sourcing strategies critically. Engage with diverse suppliers, explore collaborative partnerships, and remain agile in adapting to market changes. By doing so, you will not only secure a competitive edge but also contribute to a more resilient and sustainable garage equipment supply chain. Take action today to ensure your sourcing strategy is aligned with future opportunities in this evolving industry.