The Ultimate Guide to Cutting Machine China (2025)
Introduction: Navigating the Global Market for cutting machine china
Navigating the complexities of sourcing cutting machines from China can be a daunting task for international B2B buyers. With a myriad of options available, understanding the right equipment for your specific needs is crucial. Whether you are in Africa, South America, the Middle East, or Europe, the challenge lies not just in selecting a machine but also in ensuring quality, compliance, and cost-effectiveness. This comprehensive guide delves into the various types of cutting machines available in China, including laser, plasma, and waterjet cutters, and their diverse applications across industries such as manufacturing, textiles, and packaging.
In this guide, you will find actionable insights on how to effectively vet suppliers, assess pricing structures, and navigate the logistics of international shipping. We address key questions that often arise during the sourcing process, such as “How do I determine the best supplier for my cutting machine needs?” and “What are the hidden costs associated with importing machinery from China?” By equipping you with the knowledge to make informed purchasing decisions, this guide empowers B2B buyers to streamline their procurement processes and enhance operational efficiency.
Ultimately, understanding the dynamics of the Chinese market and the specific requirements of your region can lead to successful partnerships and sustainable growth. With the right information at your fingertips, you can confidently navigate the global market for cutting machines and make choices that align with your business objectives.
Understanding cutting machine china Types and Variations
Type Name | Key Distinguishing Features | Primary B2B Applications | Brief Pros & Cons for Buyers |
---|---|---|---|
CNC Cutting Machines | Computer-controlled for high precision | Aerospace, automotive, and metal fabrication | Pros: High accuracy; Cons: Higher initial cost |
Laser Cutting Machines | Uses laser technology for intricate cuts | Textiles, electronics, and signage | Pros: Versatile; Cons: Limited thickness capability |
Plasma Cutting Machines | High-speed cutting with plasma arc technology | Heavy metal fabrication and construction | Pros: Fast for thick materials; Cons: More energy consumption |
Water Jet Cutting Machines | Uses high-pressure water for cutting | Stone, glass, and metal industries | Pros: No heat-affected zone; Cons: Slower than other methods |
Die Cutting Machines | Utilizes dies to cut specific shapes | Packaging and label manufacturing | Pros: Cost-effective for large volumes; Cons: Limited to specific shapes |
What Are CNC Cutting Machines and How Do They Benefit B2B Buyers?
CNC (Computer Numerical Control) cutting machines are known for their precision and automation. They utilize computer programming to control the cutting tools, allowing for complex designs to be executed with high accuracy. These machines are particularly suitable for industries such as aerospace and automotive, where precision is critical. When considering a CNC machine, buyers should evaluate the software compatibility, ease of use, and after-sales support from the manufacturer to ensure a smooth integration into their production lines.
How Do Laser Cutting Machines Stand Out in the Market?
Laser cutting machines employ focused laser beams to cut through materials, making them ideal for intricate designs and fine details. They are widely used in textiles, electronics, and signage industries. When purchasing a laser cutting machine, it is essential to consider the thickness of materials it can handle, the speed of operation, and the maintenance requirements. This type of machine offers versatility, but buyers should be aware of its limitations regarding material thickness.
What Are the Advantages of Plasma Cutting Machines for Heavy Industries?
Plasma cutting machines are designed for high-speed cutting, particularly effective on thicker materials. They generate a plasma arc to melt and cut through metals, making them suitable for heavy metal fabrication and construction applications. Buyers should assess the power requirements and operational costs, as plasma cutting can consume more energy compared to other cutting methods. However, the speed and efficiency of plasma cutting can lead to significant time savings in production.
Why Choose Water Jet Cutting Machines for Sensitive Materials?
Water jet cutting machines utilize high-pressure water jets to cut through materials without generating heat. This method is particularly beneficial for cutting sensitive materials like stone, glass, and certain metals, as it avoids the heat-affected zone that can alter material properties. For B2B buyers, considerations should include the machine’s cutting speed, maintenance requirements, and the types of abrasive materials used. While water jet cutting is slower than other methods, its precision and versatility make it a valuable option.
How Do Die Cutting Machines Support Packaging and Label Manufacturing?
Die cutting machines are specialized equipment that uses dies to cut specific shapes out of materials, making them essential for packaging and label manufacturing. They are cost-effective for large production runs and can handle various materials, including paper, cardboard, and plastics. Buyers should consider the types of dies available, the machine’s speed, and the setup time required for different projects. While die cutting is efficient for mass production, it may be limited to specific shapes and designs.
Related Video: China Linear ATC CNC Wood Router with Saw Cutting Operational video
Key Industrial Applications of cutting machine china
Industry/Sector | Specific Application of Cutting Machine China | Value/Benefit for the Business | Key Sourcing Considerations for this Application |
---|---|---|---|
Textile Manufacturing | Fabric Cutting for Apparel Production | Enhanced precision and efficiency in fabric cutting processes | Machine durability, cutting speed, and after-sales support |
Packaging | Die Cutting for Custom Packaging Solutions | Customization and reduced material waste in packaging | Material compatibility, machine versatility, and lead time |
Automotive | Component Cutting for Vehicle Parts | Improved accuracy in component fabrication, leading to better fit | Compliance with safety standards, sourcing of spare parts |
Electronics | PCB Cutting for Electronic Devices | High precision in circuit board production, reducing defects | Precision requirements, machine calibration, and service availability |
Construction | Material Cutting for Structural Elements | Efficient processing of construction materials, reducing labor costs | Machine size, portability, and energy consumption |
How is ‘Cutting Machine China’ Used in Textile Manufacturing?
In the textile manufacturing sector, cutting machines from China are essential for fabric cutting in apparel production. These machines enhance precision, allowing manufacturers to cut multiple layers of fabric simultaneously, which significantly boosts efficiency. For international buyers, particularly those from Africa and South America, sourcing machines that offer durability and reliable after-sales support is crucial. Additionally, understanding the machine’s cutting speed can lead to better production timelines and reduced operational costs.
What Role Does ‘Cutting Machine China’ Play in Packaging?
In the packaging industry, cutting machines are used for die-cutting custom packaging solutions, enabling businesses to create tailored designs that minimize material waste. This is particularly important for companies in Europe looking to enhance sustainability practices. Buyers should consider the compatibility of the cutting machine with various materials, as well as its versatility to handle different packaging types. Lead time for delivery can also be a critical factor, especially for businesses needing quick turnaround.
How Does ‘Cutting Machine China’ Benefit the Automotive Sector?
The automotive industry relies on cutting machines for precise component cutting for vehicle parts. These machines contribute to improved accuracy, ensuring that parts fit together perfectly, which is essential for safety and performance. International buyers from the Middle East should prioritize machines that comply with stringent safety standards and consider the availability of spare parts to minimize downtime. This focus on compliance and support can enhance operational efficiency and product reliability.
Why is ‘Cutting Machine China’ Important for Electronics?
In electronics, cutting machines are vital for PCB (Printed Circuit Board) cutting, where high precision is necessary to reduce defects in electronic devices. For B2B buyers in regions like Europe, sourcing machines that meet specific precision requirements is imperative. Additionally, buyers should inquire about machine calibration processes and the availability of service support to ensure ongoing operational efficiency and product quality.
What are the Benefits of ‘Cutting Machine China’ in Construction?
In the construction sector, cutting machines are used for processing various structural materials, allowing for efficient cutting of wood, metal, and other materials. This efficiency leads to reduced labor costs and faster project completion times. Buyers should consider the size and portability of the machines, especially when working on-site, as well as energy consumption, to align with budget constraints and sustainability goals.
3 Common User Pain Points for ‘cutting machine china’ & Their Solutions
Scenario 1: Inconsistent Quality of Cutting Machines from China
The Problem:
International B2B buyers often encounter issues with the quality of cutting machines sourced from China. Variability in manufacturing standards can lead to machines that do not perform consistently, resulting in production delays and increased operational costs. For businesses in Africa and South America, where reliable machinery is critical for maintaining production timelines, inconsistent quality can severely impact profitability and customer satisfaction.
The Solution:
To mitigate quality issues, buyers should conduct thorough due diligence before finalizing a purchase. This includes vetting suppliers through platforms like Alibaba or Global Sources, checking their production certifications (such as ISO 9001), and requesting samples or demonstrations. Additionally, establishing a quality assurance protocol that includes third-party inspections can help ensure the machines meet the required standards. Engaging with suppliers who have a proven track record of quality and reliability can also significantly reduce risks associated with inconsistent product quality.
Scenario 2: Lack of Technical Support and Spare Parts Availability
The Problem:
Another common pain point for B2B buyers is the lack of adequate technical support and the availability of spare parts for cutting machines purchased from China. Many suppliers may not provide sufficient after-sales support, leaving businesses stranded when issues arise. In regions like the Middle East and Europe, where timely maintenance is crucial, the inability to obtain parts or support can lead to extended downtimes and financial losses.
The Solution:
Before purchasing a cutting machine, buyers should ensure that the supplier has a robust after-sales support system. This includes verifying the availability of spare parts and the responsiveness of their technical support team. Buyers can request a list of commonly needed spare parts along with their lead times and assess the supplier’s logistics capabilities. Additionally, forming partnerships with local distributors or service providers can enhance access to support and parts, ensuring that any operational disruptions are addressed swiftly.
Scenario 3: Misalignment of Machine Specifications with Production Needs
The Problem:
B2B buyers often struggle with aligning the specifications of cutting machines with their specific production requirements. For instance, a company in Italy may need a machine that cuts intricate designs in various materials, but the sourced machine might only be suited for basic cuts. This misalignment can lead to wasted resources, including time and materials, as well as dissatisfaction among end-users.
The Solution:
To avoid such misalignments, it is essential for buyers to engage in comprehensive needs assessment before sourcing a cutting machine. This involves detailing the specific materials, thicknesses, and types of cuts required in their production process. Buyers should also involve technical experts in the decision-making process to ensure that the selected machine can handle their production demands. When approaching suppliers, sharing these detailed specifications will help in selecting the right machine. Furthermore, exploring customization options with manufacturers can provide tailored solutions that precisely fit operational needs, ensuring maximum efficiency and satisfaction.
By addressing these common pain points with actionable solutions, B2B buyers can enhance their sourcing strategy for cutting machines from China, ensuring better operational efficiency and higher satisfaction in their production processes.
Strategic Material Selection Guide for cutting machine china
When selecting materials for cutting machines manufactured in China, international B2B buyers must consider various factors that influence performance, durability, and cost-effectiveness. Below is an analysis of four common materials used in cutting machines, focusing on their properties, advantages, disadvantages, and specific considerations for buyers from Africa, South America, the Middle East, and Europe.
What Are the Key Properties of Steel in Cutting Machines?
Steel is a widely used material in cutting machines due to its strength and versatility. It typically has high tensile strength and excellent wear resistance, making it suitable for high-pressure cutting applications. Steel can withstand high temperatures, which is crucial for processes involving heat generation.
Pros: Steel is durable and can be easily machined into precise components. It is also relatively cost-effective compared to other materials.
Cons: Steel can be susceptible to corrosion if not properly treated, which may limit its lifespan in humid or corrosive environments.
Impact on Application: Steel is compatible with various cutting media, including metals and plastics, making it a versatile choice for different industries.
Considerations for International Buyers: Buyers should ensure compliance with international standards such as ASTM and DIN for quality assurance. Additionally, they should consider the availability of corrosion-resistant coatings to enhance durability in specific climates.
How Does Aluminum Compare as a Material for Cutting Machines?
Aluminum is another popular material, particularly for components that require lightweight properties without sacrificing strength. It has excellent corrosion resistance and good thermal conductivity, which can be beneficial in heat-sensitive applications.
Pros: The lightweight nature of aluminum reduces the overall weight of cutting machines, making them easier to transport and operate. It also offers good machinability and can be anodized for additional surface protection.
Cons: Aluminum is generally more expensive than steel and may not be suitable for high-stress applications due to its lower tensile strength.
Impact on Application: Aluminum is ideal for cutting softer materials such as plastics and wood, but may struggle with harder metals.
Considerations for International Buyers: Buyers should verify that aluminum components meet local regulations regarding material safety and environmental impact. Understanding the specific grades of aluminum used in cutting machines is also essential.
What Are the Advantages of Using Composite Materials?
Composite materials, which typically combine fibers with a resin matrix, are increasingly used in cutting machines for their unique properties. They offer excellent strength-to-weight ratios and can be engineered for specific applications.
Pros: Composites are lightweight, resistant to corrosion, and can be tailored for specific performance characteristics. They also tend to have lower thermal expansion rates.
Cons: The manufacturing process for composites can be more complex and costly, which may increase the overall price of the cutting machine.
Impact on Application: Composites are particularly effective in applications requiring high precision and minimal thermal distortion, making them suitable for advanced manufacturing processes.
Considerations for International Buyers: Buyers should ensure that composite materials comply with relevant international standards and certifications. Understanding the specific properties of the composite used can help in assessing its suitability for particular applications.
What Role Does Tool Steel Play in Cutting Machine Performance?
Tool steel is specifically designed for manufacturing cutting tools and components. It has high hardness, wear resistance, and the ability to maintain a sharp edge under high temperatures.
Pros: Tool steel is highly durable and can withstand the rigors of cutting operations, making it ideal for high-performance applications.
Cons: The cost of tool steel is generally higher than standard steel, and it may require specialized processing techniques.
Impact on Application: Tool steel is particularly suited for cutting hard materials, including metals and alloys, making it a preferred choice in heavy-duty applications.
Considerations for International Buyers: Buyers should be aware of the specific grades of tool steel and their compliance with international standards. Additionally, they should consider the availability of tool steel in their region to avoid supply chain issues.
Summary Table of Material Selection for Cutting Machines
Material | Typical Use Case for cutting machine china | Key Advantage | Key Disadvantage/Limitation | Relative Cost (Low/Med/High) |
---|---|---|---|---|
Steel | General cutting applications | High strength and durability | Susceptible to corrosion | Medium |
Aluminum | Lightweight cutting tasks | Lightweight and corrosion-resistant | Lower tensile strength than steel | High |
Composite | Precision cutting applications | Excellent strength-to-weight ratio | Complex and costly manufacturing process | High |
Tool Steel | Heavy-duty cutting operations | Maintains sharp edge under high temperatures | Higher cost and specialized processing needed | High |
This strategic material selection guide provides a comprehensive overview for international B2B buyers to make informed decisions when sourcing cutting machines from China, ensuring compatibility with specific applications and compliance with relevant standards.
In-depth Look: Manufacturing Processes and Quality Assurance for cutting machine china
What Are the Main Stages in the Manufacturing Process of Cutting Machines from China?
The manufacturing process for cutting machines involves several critical stages that ensure the final product meets quality standards and performance expectations.
-
Material Preparation: This initial stage involves selecting high-quality raw materials, typically steel or aluminum, which are essential for durability and performance. Suppliers should provide certifications for these materials, verifying their composition and quality.
-
Forming: In this phase, raw materials are shaped into the desired components using techniques like CNC machining, laser cutting, or stamping. CNC (Computer Numerical Control) machining is particularly favored for its precision, allowing for complex geometries that enhance the machine’s functionality.
-
Assembly: After forming, the components are assembled. This stage may include both manual and automated processes, ensuring that each part fits perfectly. Quality checks are often integrated into this process to catch any defects early.
-
Finishing: The final stage involves surface treatment, painting, or coating to enhance durability and aesthetics. Processes like powder coating or anodizing are common, providing protection against corrosion and wear.
By understanding these stages, B2B buyers can better assess the capabilities of their suppliers and ensure that they are producing cutting machines that meet international standards.
Which Key Techniques Are Used in the Manufacturing of Cutting Machines?
Cutting machine manufacturers in China utilize various advanced techniques that impact the quality and efficiency of the production process:
-
CNC Machining: This technique allows for high precision and repeatability, crucial for components that require tight tolerances. Buyers should inquire about the specific CNC capabilities of their suppliers, such as the types of machines used and their operational capacities.
-
Laser Cutting: This method is employed for intricate designs and can handle various materials with minimal waste. It is essential to verify that the supplier uses high-quality laser cutting technology to ensure clean cuts and reduce rework.
-
Hydraulic Pressing: Commonly used for forming, hydraulic presses can create complex shapes quickly and efficiently. Understanding the press’s tonnage and capabilities can give buyers insight into the supplier’s production capacity.
-
Quality Control Techniques: Techniques like Statistical Process Control (SPC) can be beneficial in maintaining manufacturing quality. Suppliers should be able to demonstrate their use of SPC to monitor processes and ensure consistent quality.
How Do International Standards Influence Quality Assurance in Cutting Machine Manufacturing?
Quality assurance in cutting machine manufacturing is heavily influenced by international standards. For B2B buyers, understanding these standards is crucial for ensuring compliance and product reliability.
-
ISO 9001: This standard focuses on quality management systems and is a benchmark for manufacturers globally. Buyers should request ISO 9001 certification documents from suppliers to ensure they adhere to stringent quality control processes.
-
CE Marking: For products sold within the European Economic Area, CE marking is essential, indicating conformity with health, safety, and environmental protection standards. Buyers in Europe should ensure that their suppliers provide CE certification to avoid regulatory issues.
-
API Standards: For cutting machines used in oil and gas industries, API (American Petroleum Institute) standards may apply. B2B buyers should verify that their suppliers meet relevant API specifications, ensuring the machines are suitable for industry-specific applications.
What Are the Key Quality Control Checkpoints in Cutting Machine Manufacturing?
Quality control (QC) is a vital part of the manufacturing process for cutting machines. Several checkpoints should be implemented throughout production:
-
Incoming Quality Control (IQC): This initial checkpoint involves inspecting raw materials upon arrival. Buyers should ensure suppliers perform rigorous IQC to verify that materials meet specified standards before production begins.
-
In-Process Quality Control (IPQC): Conducted during the manufacturing process, IPQC checks components and assemblies at various stages. This real-time monitoring helps catch defects early, reducing waste and rework.
-
Final Quality Control (FQC): After assembly, a comprehensive inspection is conducted to assess the entire machine’s functionality and quality. Buyers should request detailed FQC reports, including test results and any adjustments made.
What Common Testing Methods Are Used to Ensure Quality in Cutting Machines?
Testing methods play a crucial role in ensuring the quality and performance of cutting machines. Here are some common techniques:
-
Functional Testing: This assesses whether the machine operates according to specifications. Buyers should inquire about the specific tests performed, such as cutting accuracy and speed.
-
Load Testing: This method evaluates the machine’s performance under various operational loads, ensuring it can handle real-world usage. It’s vital for buyers to understand the load testing procedures and results.
-
Durability Testing: Conducted to assess the machine’s longevity under continuous use, durability testing helps predict maintenance needs and overall lifespan.
-
Dimensional Inspection: Utilizing tools like calipers and micrometers, suppliers can verify that critical dimensions meet design specifications. Buyers should ask for dimensional inspection reports to confirm compliance.
How Can B2B Buyers Verify Supplier Quality Control?
For international B2B buyers, verifying the quality control processes of suppliers is essential for ensuring product reliability. Here are actionable steps to consider:
-
Conduct Audits: Regular audits of suppliers’ manufacturing facilities can provide insights into their quality control systems. Buyers should establish a schedule for audits and use checklists to ensure all critical areas are covered.
-
Request Documentation: Suppliers should provide detailed documentation of their quality control processes, including IQC, IPQC, and FQC reports. This transparency builds trust and allows buyers to assess compliance with international standards.
-
Engage Third-Party Inspectors: Utilizing independent inspection services can provide an unbiased assessment of the supplier’s quality control practices. This is especially valuable for buyers unfamiliar with local manufacturing standards.
-
Understand Certification Nuances: Buyers should be aware that certifications may differ based on regional regulations. It’s important to clarify the certifications relevant to their specific market and ensure the supplier possesses them.
By following these guidelines, B2B buyers from regions such as Africa, South America, the Middle East, and Europe can make informed decisions when sourcing cutting machines from China, ensuring quality and compliance with international standards.
Practical Sourcing Guide: A Step-by-Step Checklist for ‘cutting machine china’
To successfully procure cutting machines from China, international B2B buyers must navigate a complex landscape of suppliers, specifications, and regulations. This practical sourcing guide provides a step-by-step checklist designed to streamline your purchasing process, ensuring that you select the best equipment for your business needs.
Step 1: Define Your Technical Specifications
Before engaging with suppliers, it’s essential to clearly define the technical specifications of the cutting machines you need. Consider factors such as cutting capacity, material compatibility, and automation features. Documenting these details helps suppliers provide accurate quotes and ensures that the machines meet your operational requirements.
- Key Specifications to Consider:
- Cutting type (laser, waterjet, plasma)
- Material thickness and dimensions
- Automation level (manual vs. fully automated)
Step 2: Research Potential Suppliers
Conduct thorough research to identify reputable suppliers in China. Look for companies that specialize in manufacturing cutting machines and have a solid track record in the industry. Utilize platforms like Alibaba, Made-in-China, and Global Sources to find potential partners.
- What to Look For:
- Supplier ratings and reviews
- Years of experience and production capacity
- Relevant industry certifications (ISO, CE)
Step 3: Evaluate Supplier Certifications
Certifications are a crucial aspect of supplier credibility. Verify that potential suppliers hold relevant certifications, which can indicate compliance with international quality standards and safety regulations. This step is vital to avoid subpar equipment that could impact your production line.
- Important Certifications:
- ISO 9001 for quality management
- CE marking for European market compliance
- Specific industry certifications relevant to your region
Step 4: Request Samples and Demonstrations
Once you shortlist potential suppliers, request samples or demonstrations of the cutting machines. This allows you to assess the machine’s performance and suitability for your specific applications. Observing a live demonstration can also provide insights into the machine’s ease of use and maintenance.
- What to Ask For:
- Sample cuts on your specific materials
- Access to previous buyer case studies
Step 5: Negotiate Terms and Conditions
Negotiation is a critical phase in the sourcing process. Discuss pricing, payment terms, delivery schedules, and warranty conditions with your chosen supplier. Ensure that both parties clearly understand the terms to prevent future misunderstandings.
- Key Negotiation Points:
- Price per unit and bulk order discounts
- Payment methods (LC, TT, PayPal)
- Warranty duration and service agreements
Step 6: Conduct a Factory Audit
Before finalizing the purchase, consider conducting a factory audit to verify the supplier’s production capabilities and quality control processes. This step helps ensure that the supplier can meet your order requirements consistently and deliver high-quality machines.
- Audit Focus Areas:
- Manufacturing processes and equipment
- Quality control measures in place
- Worker training and safety practices
Step 7: Plan for Logistics and Import Regulations
Finally, plan for the logistics of shipping your cutting machines from China to your location. Familiarize yourself with import regulations, tariffs, and customs procedures in your country. Partnering with a reliable logistics provider can help facilitate a smooth import process.
- Logistics Considerations:
- Shipping methods (sea freight, air freight)
- Customs clearance requirements
- Import duties and taxes applicable in your region
By following this checklist, you can make informed decisions that lead to successful procurement of cutting machines from China, ultimately enhancing your operational efficiency and productivity.
Comprehensive Cost and Pricing Analysis for cutting machine china Sourcing
What Are the Key Cost Components in Sourcing Cutting Machines from China?
When sourcing cutting machines from China, understanding the cost structure is essential for international B2B buyers. The primary cost components include:
-
Materials: The type of materials used in manufacturing cutting machines significantly affects the overall cost. High-quality steel, specialized blades, and electronic components can vary in price, impacting the final product’s cost.
-
Labor: Labor costs in China are generally lower compared to Western countries, but they can vary based on the region and the skill level required for manufacturing specific cutting machines. Skilled labor may demand higher wages, which should be factored into pricing.
-
Manufacturing Overhead: This encompasses factory expenses such as utilities, maintenance, and administrative costs. Efficient factories may have lower overheads, which can translate into competitive pricing for buyers.
-
Tooling: Custom tooling for specific machine designs can be a significant upfront cost. Buyers should assess whether the tooling costs are included in the quoted price or if they will be an additional expense.
-
Quality Control (QC): Implementing stringent quality control measures is vital for ensuring that the machines meet international standards. While this can increase costs, it is a necessary investment to avoid future complications.
-
Logistics: Shipping costs, including tariffs and freight fees, must be considered. The choice of Incoterms (International Commercial Terms) will influence who bears these costs and can significantly impact the total price.
-
Margin: Suppliers will typically add a profit margin to their costs, which can vary based on their market positioning and competition.
How Do Price Influencers Affect the Sourcing of Cutting Machines?
Several factors influence the pricing of cutting machines sourced from China:
-
Volume/MOQ (Minimum Order Quantity): Purchasing in bulk can lead to significant discounts. Suppliers often offer lower unit prices for larger orders, making it crucial for buyers to assess their needs carefully.
-
Specifications and Customization: Custom features can increase the price. Buyers should clearly communicate their specifications to avoid unexpected costs.
-
Materials and Quality Certifications: Machines made from higher-grade materials or those with specific quality certifications (like ISO) will generally cost more. Buyers should weigh the benefits of these certifications against their budget constraints.
-
Supplier Factors: The reputation and reliability of the supplier can influence pricing. Established suppliers with a track record of quality may charge more but can provide peace of mind.
-
Incoterms: The choice of Incoterms affects the distribution of shipping costs and risks. Understanding these terms is crucial for budgeting and negotiating the final price.
What Are the Best Negotiation Tips for B2B Buyers in Cutting Machine Sourcing?
To maximize cost-efficiency when sourcing cutting machines from China, consider the following tips:
-
Conduct Thorough Research: Understand the market rates for cutting machines and the typical costs associated with materials and production. This knowledge will empower you during negotiations.
-
Leverage Volume Discounts: If possible, consolidate orders to meet the MOQ for discounts. Suppliers are more likely to negotiate on price with larger orders.
-
Request Detailed Quotations: Ensure that you receive a breakdown of all costs involved, including materials, labor, logistics, and any additional fees. This transparency will help you identify potential areas for negotiation.
-
Consider Total Cost of Ownership (TCO): Evaluate not just the purchase price but also long-term costs, including maintenance, operational efficiency, and potential downtime. A lower initial price may not be the best value if the machine incurs higher operational costs.
-
Build Relationships with Suppliers: Establishing a good rapport can lead to better pricing and terms over time. Suppliers are more likely to offer favorable conditions to reliable partners.
What Should International Buyers Keep in Mind Regarding Pricing Nuances?
International buyers, especially those from Africa, South America, the Middle East, and Europe, should be aware of specific pricing nuances:
-
Currency Fluctuations: Exchange rate variations can impact the final cost significantly. Consider locking in prices or using hedging strategies to mitigate this risk.
-
Import Duties and Tariffs: Be informed about any applicable import duties or tariffs that may increase the overall cost of the machines.
-
Cultural Differences in Negotiation: Understand that negotiation styles vary by region. Building trust and showing respect for the supplier’s culture can facilitate smoother negotiations.
Disclaimer on Indicative Prices
Please note that prices for cutting machines sourced from China can fluctuate based on the factors outlined above. It is advisable to request updated quotes directly from suppliers to ensure you are working with the most accurate pricing information.
Alternatives Analysis: Comparing cutting machine china With Other Solutions
The landscape of cutting technologies presents various solutions for businesses looking to enhance their production capabilities. This section will analyze ‘Cutting Machine China’ against two viable alternatives: Laser Cutting Technology and Waterjet Cutting Systems. Each solution has unique attributes that can influence a buyer’s decision based on their specific needs and operational contexts.
Comparison Aspect | Cutting Machine China | Laser Cutting Technology | Waterjet Cutting Systems |
---|---|---|---|
Performance | High precision for various materials. | Exceptional precision, especially for thin materials. | Effective for thick materials with minimal heat-affected zones. |
Cost | Generally lower initial investment. | Higher upfront costs but lower operational costs. | Moderate initial investment, variable operational costs depending on material. |
Ease of Implementation | Requires moderate training for operators. | Requires skilled technicians for setup and operation. | User-friendly but needs space for water recycling systems. |
Maintenance | Regular maintenance required for optimal performance. | Low maintenance but requires occasional lens replacement. | High maintenance due to water filtration and pump upkeep. |
Best Use Case | Ideal for mass production of simple shapes. | Best suited for intricate designs in metals and plastics. | Perfect for cutting thick materials like stone and metal without thermal distortion. |
What are the Advantages and Disadvantages of Laser Cutting Technology?
Laser cutting technology is revered for its precision and speed, making it an excellent choice for detailed work in industries such as automotive and aerospace. The major advantage of laser cutting is its ability to produce intricate designs with a high degree of accuracy, minimizing waste material. However, the initial investment can be significantly higher than that of cutting machines sourced from China, which may deter budget-conscious buyers. Additionally, the technology requires skilled technicians to operate and maintain, which can complicate implementation for companies with limited resources.
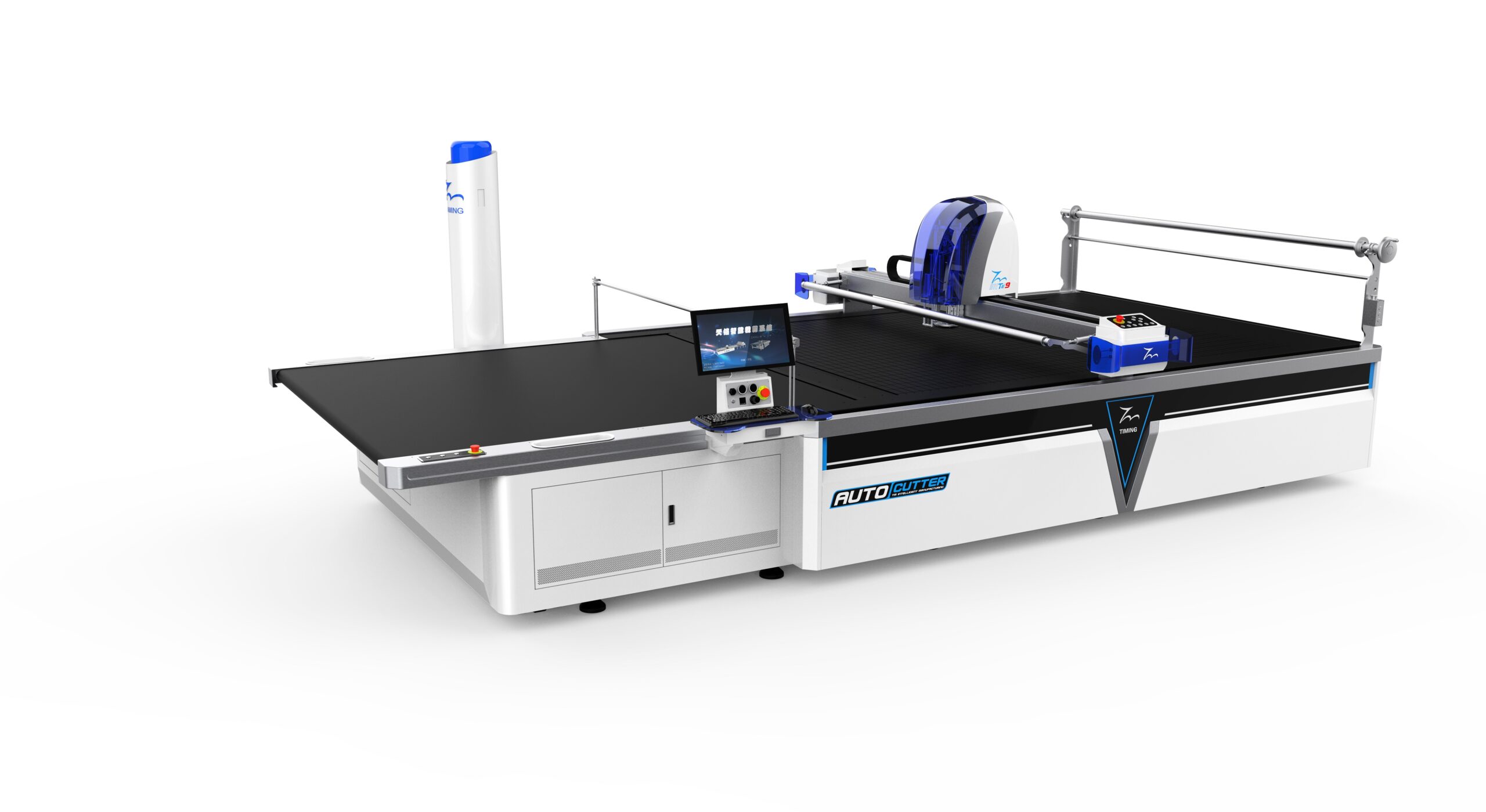
A stock image related to cutting machine china.
What Makes Waterjet Cutting Systems a Viable Alternative?
Waterjet cutting systems offer a unique advantage in their ability to cut through a wide range of materials, including metals, glass, and even food products, without introducing thermal stress. This makes them ideal for applications where material integrity is crucial. The moderate initial investment is balanced by the versatility of the system, which can adapt to various cutting tasks. However, maintenance can be intensive due to the need for water filtration and pump care, which might lead to higher operational costs over time. Additionally, while the setup is relatively user-friendly, it requires ample space for water recycling systems, which could be a consideration for businesses with space constraints.
How Can B2B Buyers Choose the Right Cutting Solution?
When selecting the right cutting solution, B2B buyers should consider their specific production needs, budget constraints, and the types of materials they work with. For businesses focused on high-volume production with simpler designs, a ‘Cutting Machine China’ may offer the best value. Conversely, if precision and intricate designs are critical, investing in laser cutting technology could yield better long-term results. Waterjet cutting systems are best for those requiring versatility across various materials but are prepared for the associated maintenance costs. By carefully evaluating these factors, buyers can make an informed decision that aligns with their operational goals and financial parameters.
Essential Technical Properties and Trade Terminology for cutting machine china
What Are the Essential Technical Properties of Cutting Machines from China?
When sourcing cutting machines from China, understanding key technical properties is crucial for making informed purchasing decisions. Here are some critical specifications to consider:
1. Material Grade
The material used in manufacturing cutting machines affects durability and performance. Common materials include high-carbon steel for blades and aluminum for frames. Higher-grade materials typically provide better cutting precision and longevity, which is vital for businesses looking to maximize their investment.
2. Cutting Tolerance
Tolerance refers to the allowable deviation from a specified dimension. For cutting machines, tighter tolerances (e.g., ±0.01 mm) are essential for industries like aerospace or automotive, where precision is non-negotiable. Understanding the tolerance levels can help buyers ensure that the machine meets their production quality standards.
3. Power Consumption
Power consumption is an important property that affects operational costs. Machines with higher wattage may offer more robust cutting capabilities but can lead to increased electricity expenses. B2B buyers should assess their energy requirements and consider machines that balance power and efficiency.
4. Cutting Speed
Cutting speed is measured in meters per minute (m/min) and indicates how quickly a machine can perform cuts. Higher speeds can lead to increased productivity, which is vital for businesses with tight production schedules. However, it’s important to ensure that increased speed does not compromise cutting quality.
5. Control System
Modern cutting machines often feature advanced control systems, including CNC (Computer Numerical Control) technology. This allows for automated and precise cutting operations. Buyers should evaluate the control system for ease of use and compatibility with existing workflows.
What Trade Terminology Should B2B Buyers Know for Cutting Machines?
Familiarity with trade terminology is equally important for international B2B buyers. Here are some common terms related to cutting machines:
1. OEM (Original Equipment Manufacturer)
OEM refers to companies that manufacture products that are then sold under another company’s brand name. For buyers, sourcing from reputable OEMs can ensure product quality and reliability, as these manufacturers often adhere to stringent quality standards.
2. MOQ (Minimum Order Quantity)
MOQ is the minimum number of units a supplier is willing to sell. Understanding MOQ is crucial for budgeting and inventory management. Buyers should negotiate MOQs that align with their operational needs, especially when dealing with high-value machinery.
3. RFQ (Request for Quotation)
An RFQ is a document used by buyers to request price quotes from suppliers. It’s important to include detailed specifications and quantities to receive accurate pricing. This process helps buyers compare costs effectively and ensures they are getting the best value for their investment.
4. Incoterms (International Commercial Terms)
Incoterms define the responsibilities of buyers and sellers in international shipping. Terms such as FOB (Free on Board) and CIF (Cost, Insurance, and Freight) dictate who is responsible for shipping costs, insurance, and risk during transit. Understanding these terms helps in negotiating contracts and managing shipping logistics.
5. Lead Time
Lead time is the time taken from placing an order to receiving the goods. This is a critical factor for businesses that rely on timely deliveries to meet production schedules. Buyers should always inquire about lead times to ensure their operations run smoothly.
How Can These Properties and Terms Impact Your Buying Decision?
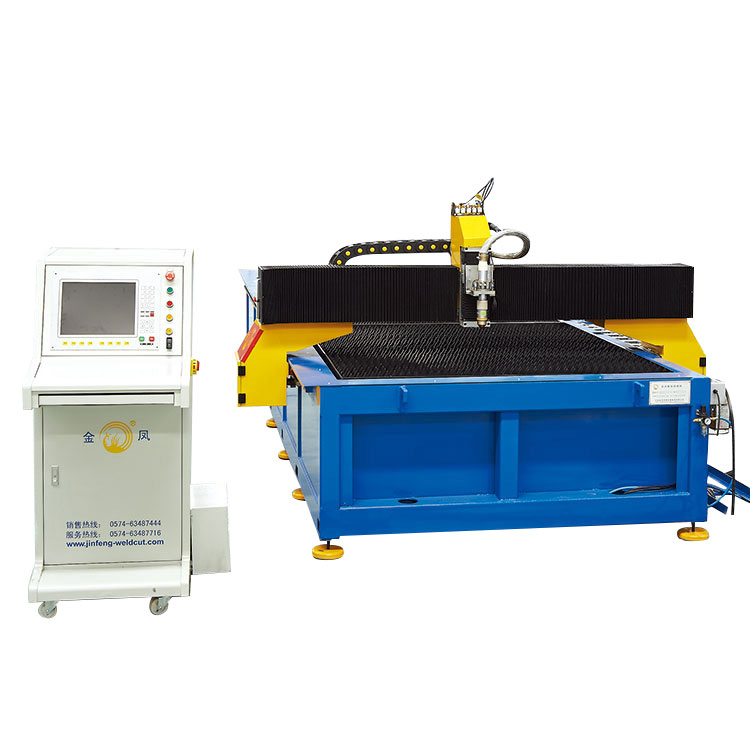
A stock image related to cutting machine china.
Understanding the technical properties and trade terminology related to cutting machines from China enables B2B buyers to make informed decisions. By considering specifications such as material grade, cutting tolerance, and control systems, along with familiarizing themselves with terms like OEM and MOQ, businesses can enhance their procurement strategies, reduce risks, and ultimately drive profitability.
Navigating Market Dynamics and Sourcing Trends in the cutting machine china Sector
What Are the Current Market Dynamics and Key Trends in the Cutting Machine Sector from China?
The cutting machine sector in China has witnessed significant transformations driven by advancements in technology, shifts in global demand, and evolving buyer expectations. One of the key drivers is the rising demand for precision and efficiency in manufacturing processes across various industries, including textiles, automotive, and electronics. International B2B buyers, particularly from Africa, South America, the Middle East, and Europe, are increasingly seeking cutting machines that offer automation capabilities, enabling them to enhance production speed while reducing labor costs.
Emerging trends include the adoption of Industry 4.0 principles, where manufacturers leverage IoT (Internet of Things) and AI (Artificial Intelligence) for predictive maintenance and real-time monitoring of equipment. This trend is particularly appealing to B2B buyers looking to optimize their supply chains and minimize downtime. Furthermore, the emphasis on customized solutions has grown, with suppliers offering machines tailored to specific industry needs, which is crucial for sectors like automotive and aerospace that require specialized cutting techniques.
Moreover, as global supply chains become more interconnected, international buyers are focusing on suppliers with robust logistics capabilities and shorter lead times. This trend is essential for maintaining competitiveness in fast-paced markets. Buyers should also be aware of the geopolitical factors influencing trade, as tariffs and regulations can impact sourcing decisions, especially when dealing with suppliers from China.
How Important Is Sustainability and Ethical Sourcing in the Cutting Machine Industry?
Sustainability is becoming a core consideration for B2B buyers in the cutting machine sector. The environmental impact of manufacturing processes is under scrutiny, and companies are increasingly held accountable for their carbon footprint. Buyers are encouraged to seek suppliers who prioritize eco-friendly practices, such as using energy-efficient machinery and sourcing materials responsibly. This not only aligns with global sustainability goals but also enhances brand reputation.
Moreover, ethical sourcing has gained prominence, with buyers now demanding transparency in supply chains. This includes ensuring that raw materials are sourced from suppliers who adhere to fair labor practices and environmental regulations. Certifications such as ISO 14001 for environmental management and SA8000 for social accountability are becoming crucial benchmarks for evaluating potential suppliers.
Investing in ‘green’ certifications and materials not only helps companies meet regulatory requirements but also opens new market opportunities. For instance, many European buyers are increasingly favoring suppliers who can demonstrate a commitment to sustainability through certified practices. By prioritizing ethical sourcing, businesses can differentiate themselves in a competitive market and appeal to environmentally conscious customers.
What Is the Evolution of the Cutting Machine Sector in China?
The cutting machine sector in China has a rich history that traces back to the early 20th century when manual cutting tools dominated the market. As industrialization progressed, the introduction of electric cutting machines revolutionized manufacturing processes, significantly increasing productivity. The late 20th century saw the advent of computerized cutting technologies, which allowed for higher precision and efficiency.
In recent years, the sector has embraced advanced technologies such as laser cutting and CNC (Computer Numerical Control) machines. These innovations have transformed the capabilities of cutting machines, allowing for complex designs and materials that were previously difficult to work with. The evolution of the cutting machine sector reflects China’s broader industrial strategy, emphasizing technological advancement and global competitiveness. As a result, international B2B buyers now have access to a wide range of cutting-edge machines that cater to various industry needs, reinforcing China’s position as a leading supplier in the global market.
Frequently Asked Questions (FAQs) for B2B Buyers of cutting machine china
-
How do I choose the right cutting machine for my business needs?
Selecting the right cutting machine involves assessing your specific production requirements, including the types of materials you work with and the desired cutting precision. Consider factors such as machine speed, blade types, and the maximum thickness of materials. Additionally, evaluate the machine’s compatibility with your existing workflow and production capacity. Consulting with suppliers for demonstrations or sample cuts can also provide valuable insights into the machine’s capabilities. -
What are the advantages of sourcing cutting machines from China?
Sourcing cutting machines from China offers competitive pricing due to lower manufacturing costs. Additionally, Chinese manufacturers often provide a wide range of options and customization capabilities, allowing buyers to tailor machines to their specific needs. The robust supply chain and availability of advanced technologies in China also mean that buyers can access innovative features that enhance productivity and efficiency in their operations. -
What should I know about minimum order quantities (MOQ) when purchasing cutting machines?
Minimum order quantities (MOQ) vary by manufacturer and can significantly impact your purchasing strategy. Some suppliers may require a higher MOQ, especially for customized machines, while others might be more flexible. It’s essential to communicate your needs clearly and negotiate MOQs that align with your budget and production requirements. Keep in mind that smaller orders may incur higher unit costs, so plan your inventory accordingly.
-
How can I ensure the quality of cutting machines from Chinese suppliers?
To ensure quality, conduct thorough research on potential suppliers. Look for certifications such as ISO9001, which indicate adherence to quality management standards. Request samples or arrange factory visits to assess the manufacturing process. Additionally, consider using third-party quality assurance services to inspect machines before shipment, ensuring they meet your specifications and industry standards. -
What payment terms should I expect when dealing with Chinese manufacturers?
Payment terms can vary widely among suppliers. Common practices include a deposit (usually 30-50%) upfront with the balance due upon shipment or delivery. Some manufacturers may offer letters of credit or payment through platforms like Alibaba. Always clarify payment terms upfront and ensure they are included in the contract to avoid misunderstandings later. -
How do I handle logistics and shipping when importing cutting machines from China?
When importing cutting machines, work with logistics providers familiar with international shipping regulations and customs procedures. Determine whether you will use FOB (Free On Board) or CIF (Cost, Insurance, and Freight) terms, as this will affect shipping costs and responsibilities. Ensure that all documentation, including invoices, packing lists, and certificates of origin, is accurate to facilitate smooth customs clearance. -
What customization options are typically available for cutting machines?
Customization options for cutting machines can include adjustments in blade types, sizes, and cutting speeds to suit specific materials or applications. Many manufacturers also offer software integration for automated cutting processes and enhancements for precision. Discuss your specific needs with suppliers early in the process to explore available options and the feasibility of modifications. -
How can I build a long-term relationship with my cutting machine supplier in China?
Building a long-term relationship with your supplier involves consistent communication and transparency. Establish clear expectations regarding quality, delivery times, and service support. Regularly provide feedback and engage in discussions about future needs or potential upgrades. Consider visiting the supplier’s facility to strengthen ties and foster trust, leading to better terms and support in future transactions.
Important Disclaimer & Terms of Use
⚠️ Important Disclaimer
The information provided in this guide, including content regarding manufacturers, technical specifications, and market analysis, is for informational and educational purposes only. It does not constitute professional procurement advice, financial advice, or legal advice.
While we have made every effort to ensure the accuracy and timeliness of the information, we are not responsible for any errors, omissions, or outdated information. Market conditions, company details, and technical standards are subject to change.
B2B buyers must conduct their own independent and thorough due diligence before making any purchasing decisions. This includes contacting suppliers directly, verifying certifications, requesting samples, and seeking professional consultation. The risk of relying on any information in this guide is borne solely by the reader.
Strategic Sourcing Conclusion and Outlook for cutting machine china
In the rapidly evolving landscape of manufacturing, strategic sourcing of cutting machines from China presents a wealth of opportunities for international B2B buyers, particularly those from Africa, South America, the Middle East, and Europe. By leveraging China’s extensive production capabilities and competitive pricing, buyers can enhance their operational efficiency and reduce costs. Key takeaways include the importance of thorough supplier vetting, understanding local regulations, and aligning with manufacturers that prioritize quality and innovation.
How can international buyers maximize their investment in cutting machines from China? Prioritize long-term partnerships with reliable suppliers who offer robust after-sales support and maintenance services. This approach not only ensures the longevity of your machinery but also fosters a collaborative environment that can lead to future innovations tailored to your specific needs.
As we look ahead, the demand for advanced cutting machines will continue to grow, driven by technological advancements and the need for sustainable production practices. International buyers are encouraged to stay informed about emerging trends and to proactively engage with suppliers that are committed to innovation and quality. Embrace the future of manufacturing—strategically source your cutting machines today to secure a competitive edge in your market.