The Ultimate Guide to Sandwich Panel Supplier (2025)
Introduction: Navigating the Global Market for sandwich panel supplier
Navigating the global market for sandwich panel suppliers can be a daunting task for international B2B buyers, especially when considering the diverse needs and standards across regions such as Africa, South America, the Middle East, and Europe. As these buyers seek to source high-quality sandwich panels for various applications—from cold storage facilities to modern architectural projects—they often face challenges in identifying reliable suppliers who meet their specific requirements. This guide aims to simplify the sourcing process by providing comprehensive insights into the types of sandwich panels available, their applications, and key considerations for supplier vetting.
Throughout this guide, readers will gain a deeper understanding of different sandwich panel materials, including polyurethane and polystyrene options, and their respective thermal and structural properties. We will also explore the critical aspects of supplier evaluation, such as certifications, production capabilities, and pricing structures, ensuring that buyers can make informed decisions that align with their project goals and budgets.
By addressing common pain points and offering actionable strategies, this resource empowers B2B buyers to confidently navigate the complexities of the sandwich panel market. Whether you are in Turkey looking for insulation solutions or in South Africa seeking durable wall panels, this guide will equip you with the knowledge necessary to optimize your purchasing decisions and enhance your project outcomes.
Understanding sandwich panel supplier Types and Variations
Type Name | Key Distinguishing Features | Primary B2B Applications | Brief Pros & Cons for Buyers |
---|---|---|---|
Polyurethane Panels | High thermal insulation, lightweight, and moisture resistant | Cold storage, industrial buildings, warehouses | Pros: Excellent insulation, energy-efficient; Cons: Higher initial cost compared to others. |
Polystyrene Panels | Cost-effective, good insulation properties, and versatile design | Residential buildings, temporary structures | Pros: Affordable, easy to install; Cons: Lower thermal resistance than polyurethane. |
Mineral Wool Panels | Fire-resistant, soundproof, and eco-friendly | Fire-rated applications, commercial buildings | Pros: Superior fire resistance; Cons: Heavier, may require specialized installation. |
Steel Composite Panels | Durable, robust, and customizable finishes | Industrial facades, storage facilities | Pros: Long lifespan, high strength; Cons: Higher weight can increase structural costs. |
EPS Panels | Lightweight, economical, and good thermal performance | Agricultural buildings, cold storage, and warehouses | Pros: Cost-effective and easy to handle; Cons: Limited fire resistance compared to mineral wool. |
What are the characteristics and suitability of Polyurethane Panels for B2B buyers?
Polyurethane panels are renowned for their exceptional thermal insulation properties, making them ideal for applications requiring temperature control, such as cold storage facilities and industrial buildings. Their lightweight nature simplifies transportation and installation, which is a significant advantage for large-scale projects. Buyers should consider the initial investment, as these panels typically come at a higher price point, but the long-term energy savings can offset this cost.
How do Polystyrene Panels compare in terms of applications and cost-effectiveness?
Polystyrene panels are a popular choice for B2B buyers seeking cost-effective insulation solutions. They offer good thermal performance and are often used in residential buildings and temporary structures. Their affordability and ease of installation make them attractive for projects with tight budgets. However, it’s essential for buyers to note that while they are cheaper, they may not provide the same level of thermal resistance as polyurethane panels, which could impact energy efficiency in the long run.
Why choose Mineral Wool Panels for fire-rated applications?
Mineral wool panels are particularly valued in environments where fire safety is paramount. Their inherent fire-resistant properties make them suitable for commercial buildings and applications that require fire ratings. Additionally, these panels offer excellent soundproofing benefits, which can enhance occupant comfort in office spaces. Buyers should be aware that while mineral wool panels provide significant safety advantages, their heavier weight may necessitate specialized installation, potentially increasing labor costs.
What advantages do Steel Composite Panels offer for industrial applications?
Steel composite panels are characterized by their durability and strength, making them an excellent choice for industrial facades and storage facilities. These panels can be customized with various finishes to meet aesthetic and functional requirements. While they boast a long lifespan and robustness, buyers must account for their weight, which may increase structural support costs. Overall, steel composite panels are ideal for projects requiring resilience and customization.
How do EPS Panels serve the needs of agricultural and cold storage facilities?
EPS (Expanded Polystyrene) panels are lightweight and economical, making them a suitable choice for agricultural buildings and cold storage facilities. Their good thermal performance helps maintain stable temperatures, essential for preserving perishable goods. The ease of handling and installation further enhances their appeal for large projects. However, buyers should consider that EPS panels may have limited fire resistance compared to alternatives like mineral wool, which could be a critical factor depending on the application.
Related Video: 1 minute to learn Installation of Sandwich Panel
Key Industrial Applications of sandwich panel supplier
Industry/Sector | Specific Application of Sandwich Panel Supplier | Value/Benefit for the Business | Key Sourcing Considerations for this Application |
---|---|---|---|
Construction | Prefabricated walls and roofs for commercial buildings | Quick installation and reduced labor costs | Compliance with local building codes and insulation standards |
Cold Storage | Insulated panels for cold storage facilities | Energy efficiency and temperature control | Material durability and thermal performance ratings |
Food Processing | Cleanroom environments using insulated panels | Enhanced hygiene and compliance with health regulations | Certification for food-safe materials and ease of cleaning |
Agriculture | Agricultural storage and processing facilities | Improved product preservation and reduced spoilage | Resistance to moisture and pests, as well as thermal insulation |
Transportation | Modular units for mobile offices and shelters | Flexibility and mobility in operations | Lightweight materials and ease of assembly |
What Are the Key Industrial Applications of Sandwich Panels?
How Are Sandwich Panels Used in the Construction Industry?
Sandwich panels are increasingly utilized in the construction sector for prefabricated walls and roofs, particularly for commercial buildings. They offer a streamlined installation process, significantly reducing labor costs and construction timelines. International buyers, especially from regions like Africa and South America, should ensure that the panels meet local building codes and insulation standards to ensure safety and efficiency.
What Role Do Sandwich Panels Play in Cold Storage Facilities?
In cold storage applications, insulated sandwich panels are critical for maintaining temperature control and energy efficiency. These panels are designed to minimize thermal bridging, ensuring that the internal environment remains stable, which is essential for preserving perishable goods. Buyers must prioritize sourcing materials with high durability and excellent thermal performance ratings to maximize energy savings and compliance with industry standards.
Why Are Sandwich Panels Important for Food Processing Environments?
In food processing, sandwich panels create cleanroom environments that enhance hygiene and comply with stringent health regulations. These panels help prevent contamination and maintain strict cleanliness standards. B2B buyers in this sector should focus on sourcing panels made from certified food-safe materials, ensuring that they are easy to clean and maintain, which is crucial for operational efficiency.
How Are Sandwich Panels Beneficial in Agriculture?
Agricultural facilities, including storage and processing units, benefit from sandwich panels by improving product preservation and reducing spoilage rates. Their insulating properties help maintain optimal conditions for stored goods, while their resistance to moisture and pests adds an extra layer of protection. International buyers should consider the specific climate conditions of their region when sourcing these materials to ensure longevity and performance.
What Advantages Do Sandwich Panels Offer in the Transportation Sector?
In the transportation industry, sandwich panels are often used in modular units for mobile offices and shelters. Their lightweight design allows for easy transport and quick assembly, making them ideal for temporary or mobile applications. Buyers should look for panels that combine durability with ease of assembly, ensuring that they can withstand the rigors of transportation while providing adequate insulation and protection from the elements.
Related Video: Sandwich Panel Machine
3 Common User Pain Points for ‘sandwich panel supplier’ & Their Solutions
Scenario 1: Difficulty in Ensuring Quality and Compliance of Sandwich Panels
The Problem: One of the most significant challenges faced by B2B buyers in the sandwich panel industry is ensuring that the products meet quality standards and regulatory compliance. Many suppliers may not provide sufficient documentation regarding the materials used or the manufacturing processes, leading to uncertainty. This situation is particularly critical in regions like South Africa and Turkey, where construction regulations are stringent, and failure to comply can result in hefty fines or project delays. Buyers often find themselves navigating a complex landscape of certifications, performance metrics, and quality assurances that vary significantly from one supplier to another.
The Solution: To address this pain point, buyers should establish a clear set of quality criteria before engaging with suppliers. This includes requesting detailed documentation on material specifications, compliance with international standards (such as ASTM or EN), and certifications for fire resistance and insulation properties. It’s advisable to conduct supplier audits or site visits whenever possible to verify manufacturing practices. Additionally, leveraging third-party testing services can provide an unbiased assessment of the panels’ quality. Building a long-term relationship with reputable suppliers who can provide consistent quality and transparency will also mitigate risks associated with non-compliance and product failures.
Scenario 2: Navigating Supply Chain Disruptions for Timely Deliveries
The Problem: Supply chain disruptions can severely impact the timely delivery of sandwich panels, causing project delays and increased costs. This issue has been exacerbated by global events such as the COVID-19 pandemic, geopolitical tensions, and environmental factors that affect transportation routes. For B2B buyers in regions like the Middle East and South America, where logistical challenges are already prevalent, unexpected delays can lead to significant financial losses and reputational damage.
The Solution: To effectively manage this risk, buyers should diversify their supplier base to include multiple vendors across different regions. This strategy reduces dependence on a single source and provides alternative options in case of disruptions. Implementing a robust inventory management system can also help in forecasting demand and maintaining buffer stock for critical projects. Additionally, establishing clear communication channels with suppliers regarding potential risks and delivery timelines can foster transparency and allow for better contingency planning. Incorporating flexible contracts that account for possible delays can provide additional protection against supply chain volatility.
Scenario 3: Lack of Customization Options for Specific Projects
The Problem: Many B2B buyers find that standard sandwich panel offerings do not meet the specific requirements of their projects, particularly in specialized applications such as cold storage or unique architectural designs. This lack of customization can lead to compromises on performance or aesthetics, impacting the overall success of a project. For buyers in Europe or Africa, where climate conditions vary greatly, the need for tailored solutions is even more pronounced.
The Solution: To overcome this challenge, buyers should engage suppliers who offer a range of customization options. This includes specifying panel thickness, core materials, and surface finishes that align with project requirements. It’s crucial to communicate project specifications early in the procurement process and request prototypes or samples to evaluate performance. Collaborating with suppliers who have a strong engineering team can also facilitate the development of bespoke solutions that cater to specific needs. Additionally, utilizing advanced design software can help visualize how customized panels will integrate into the overall project, ensuring that the final product meets both functional and aesthetic criteria.
Strategic Material Selection Guide for sandwich panel supplier
When selecting materials for sandwich panels, international B2B buyers must consider various factors that influence product performance, cost, and suitability for specific applications. Here, we analyze four common materials used in sandwich panels: Polyurethane (PUR), Polystyrene (EPS), Mineral Wool, and Polyisocyanurate (PIR). Each material has distinct properties, advantages, and limitations that can impact the decision-making process for buyers from diverse regions such as Africa, South America, the Middle East, and Europe.
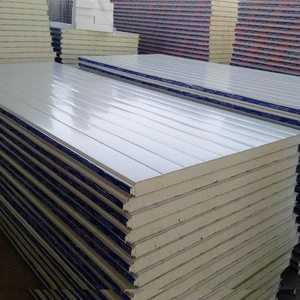
A stock image related to sandwich panel supplier.
What Are the Key Properties of Polyurethane (PUR) in Sandwich Panels?
Polyurethane (PUR) is known for its excellent thermal insulation properties, making it a popular choice for sandwich panels. It typically offers a thermal conductivity of around 0.020-0.025 W/mK, which is superior to many alternatives. PUR panels can withstand temperatures ranging from -50°C to 120°C, providing versatility in various climates.
Pros and Cons of Polyurethane (PUR)
– Pros: High thermal efficiency, lightweight, and good mechanical strength. PUR is also resistant to moisture and chemicals, enhancing its longevity.
– Cons: Higher cost compared to EPS and potential environmental concerns due to the use of isocyanates in production. Additionally, PUR panels may require specific fire ratings depending on local regulations.
Impact on Application
PUR is ideal for applications requiring high thermal performance, such as cold storage facilities and refrigerated transport. However, buyers must ensure compliance with local fire safety standards, such as ASTM E84 in the U.S. or EN 13501-1 in Europe.
How Does Polystyrene (EPS) Compare as a Sandwich Panel Material?
Expanded Polystyrene (EPS) is a cost-effective option that provides decent thermal insulation, with thermal conductivity values around 0.030-0.040 W/mK. EPS panels are lightweight and easy to handle, making them suitable for various construction applications.
Pros and Cons of Polystyrene (EPS)
– Pros: Low cost, good insulation properties, and ease of installation. EPS is also resistant to moisture, making it suitable for humid environments.
– Cons: Lower compressive strength compared to PUR and PIR, and it may not provide adequate fire resistance without additional treatments.
Impact on Application
EPS is commonly used in building facades, roofs, and floors. Buyers in regions with stringent fire safety regulations should consider additional fire retardants or coatings to meet compliance standards.
What Are the Benefits of Using Mineral Wool in Sandwich Panels?
Mineral wool is recognized for its excellent fire resistance and sound insulation properties. It typically withstands temperatures up to 1000°C, making it suitable for applications where fire safety is paramount.
Pros and Cons of Mineral Wool
– Pros: Outstanding fire resistance, good thermal performance, and sound absorption capabilities. Mineral wool is also environmentally friendly as it is made from natural or recycled materials.
– Cons: Heavier than other materials, which may increase transportation costs, and it can absorb moisture if not properly sealed.
Impact on Application
Mineral wool is ideal for industrial and commercial buildings where fire safety is critical. Buyers should ensure that the panels comply with local fire safety codes, such as EN 13501-1 in Europe.
Why Choose Polyisocyanurate (PIR) for Sandwich Panels?
Polyisocyanurate (PIR) offers a higher thermal resistance than PUR, with thermal conductivity values around 0.020-0.025 W/mK. PIR panels can also withstand higher temperatures, making them suitable for various applications.
Pros and Cons of Polyisocyanurate (PIR)
– Pros: Excellent thermal performance, good fire resistance, and lower environmental impact compared to PUR.
– Cons: Higher manufacturing complexity and cost compared to EPS and mineral wool.
Impact on Application
PIR is commonly used in roofing systems and energy-efficient buildings. Buyers should verify compliance with relevant standards, such as ASTM C518 for thermal resistance.
Summary Table of Sandwich Panel Materials
Material | Typical Use Case for sandwich panel supplier | Key Advantage | Key Disadvantage/Limitation | Relative Cost (Low/Med/High) |
---|---|---|---|---|
Polyurethane (PUR) | Cold storage, refrigerated transport | High thermal efficiency | Higher cost, environmental concerns | High |
Polystyrene (EPS) | Building facades, roofs, floors | Low cost, easy installation | Lower compressive strength | Low |
Mineral Wool | Industrial/commercial buildings | Outstanding fire resistance | Heavier, moisture absorption risk | Medium |
Polyisocyanurate (PIR) | Energy-efficient buildings, roofing systems | Excellent thermal performance | Higher manufacturing complexity | Medium to High |
This strategic material selection guide provides international B2B buyers with a comprehensive overview of key materials used in sandwich panels, enabling informed decisions based on specific application needs and regional compliance requirements.
In-depth Look: Manufacturing Processes and Quality Assurance for sandwich panel supplier
What Are the Main Stages of Manufacturing Sandwich Panels?
The manufacturing process for sandwich panels involves several critical stages to ensure high-quality end products that meet the diverse needs of international B2B buyers. The primary stages include:
-
Material Preparation: This initial phase involves selecting and preparing raw materials, typically consisting of two outer layers (often metal or polymer) and a core material (commonly polyurethane, polystyrene, or mineral wool). The materials must be sourced from reliable suppliers to ensure compliance with international quality standards. Proper storage and handling of these materials are crucial to prevent contamination and degradation.
-
Forming: In this stage, the outer layers are shaped and configured to create the desired profile of the sandwich panel. Techniques such as roll forming or extrusion are commonly employed. Roll forming is particularly advantageous as it allows for continuous production and consistent profile accuracy, which is essential for ensuring proper insulation and structural integrity.
-
Assembly: Once the layers are formed, they are assembled together. This involves applying adhesive or mechanical fasteners to bond the core material with the outer layers. The assembly process is critical as it directly affects the thermal and structural performance of the panels. It is essential that this stage is executed with precision to avoid issues such as delamination.
-
Finishing: The final stage includes surface treatments and coatings to enhance durability, aesthetics, and resistance to environmental factors. Finishing techniques may involve painting, laminating, or applying protective films. This stage not only improves the product’s visual appeal but also extends its lifespan, making it more suitable for various applications.
How Is Quality Assurance Managed in Sandwich Panel Manufacturing?
Quality assurance (QA) is a vital aspect of the manufacturing process for sandwich panels, ensuring that products meet specified standards and customer expectations. The following are key components of an effective QA process:
-
International Standards: Adherence to recognized international standards such as ISO 9001 is essential for ensuring quality management systems are in place. Additionally, specific industry standards like CE marking in Europe or API certifications for industrial applications may also apply. These standards help to assure buyers that the products are manufactured in compliance with safety and performance criteria.
-
Quality Control Checkpoints: Quality control (QC) is typically structured around several checkpoints:
– Incoming Quality Control (IQC): This involves inspecting raw materials upon arrival to ensure they meet predefined specifications.
– In-Process Quality Control (IPQC): This stage includes continuous monitoring during the manufacturing process to identify and rectify defects early.
– Final Quality Control (FQC): After assembly and finishing, the final products undergo rigorous testing to verify compliance with performance standards. -
Common Testing Methods: Various testing methods are employed to assess the quality of sandwich panels. These may include:
– Thermal Insulation Testing: Evaluating the thermal performance of the panels to ensure they meet insulation requirements.
– Mechanical Strength Testing: Assessing the load-bearing capacity and structural integrity of the panels.
– Fire Resistance Testing: Ensuring compliance with fire safety regulations, which is particularly crucial for construction applications.
How Can B2B Buyers Verify Supplier Quality Control?
For B2B buyers, especially those in Africa, South America, the Middle East, and Europe, verifying the quality control measures of sandwich panel suppliers is crucial for minimizing risks. Here are effective strategies to ensure the reliability of suppliers:
-
Supplier Audits: Conducting on-site audits can provide insights into a supplier’s manufacturing processes and quality control systems. Buyers should look for evidence of compliance with international standards and assess the effectiveness of the QA measures in place.
-
Quality Assurance Reports: Requesting detailed QA reports from suppliers can help buyers understand the testing methodologies, results, and any corrective actions taken. These reports should include documentation of previous quality checks and certifications.
-
Third-Party Inspections: Engaging independent third-party inspectors can provide an unbiased assessment of the supplier’s quality control processes. This is particularly beneficial for buyers unfamiliar with the local market or those who want an additional layer of assurance.
What Are the Quality Control Nuances for International B2B Buyers?
International B2B buyers must navigate various nuances when it comes to quality control in sandwich panel manufacturing. Here are some considerations:
-
Cultural and Regulatory Differences: Understanding the local regulations and cultural practices in the supplier’s country is essential. For instance, compliance requirements may vary significantly between regions, impacting the manufacturing process and quality assurance practices.
-
Documentation and Certifications: Buyers should ensure that suppliers can provide the necessary documentation, including certificates of compliance with international standards. This is particularly important for projects that require specific certifications for regulatory approval.
-
Communication and Language Barriers: Effective communication is crucial for ensuring that quality expectations are clearly understood and met. Buyers should consider suppliers with multilingual capabilities or those that have experience dealing with international clients to mitigate potential misunderstandings.
-
Post-Purchase Support: Establishing a relationship with suppliers that includes post-purchase support can help address any quality issues that may arise after delivery. Buyers should inquire about warranty terms and the supplier’s approach to handling complaints or product failures.
By carefully evaluating the manufacturing processes and quality assurance practices of sandwich panel suppliers, B2B buyers can make informed decisions that align with their project requirements and quality expectations.
Practical Sourcing Guide: A Step-by-Step Checklist for ‘sandwich panel supplier’
Introduction
Sourcing sandwich panels for construction or industrial applications requires careful consideration and due diligence. This checklist serves as a practical guide for B2B buyers, particularly from Africa, South America, the Middle East, and Europe, ensuring that you make informed decisions when selecting a supplier. By following these steps, you can optimize your procurement process and mitigate risks associated with quality and compliance.
Step 1: Define Your Technical Specifications
Before you begin your search for a sandwich panel supplier, it’s crucial to establish clear technical specifications. This includes the desired thickness, insulation type, and fire rating of the panels. Having a detailed specification allows you to communicate effectively with potential suppliers and ensures that the products meet your project’s requirements.
- Consider factors such as thermal efficiency, acoustic insulation, and structural integrity.
- Understand the compliance standards relevant to your region, such as ASTM or DIN certifications.
Step 2: Research Potential Suppliers
Conduct thorough research to identify potential suppliers that specialize in sandwich panels. Utilize online directories, industry forums, and trade shows to compile a list of candidates. A well-researched shortlist can save you time and effort later in the procurement process.
- Look for suppliers with a proven track record and positive customer reviews.
- Consider geographical proximity to reduce shipping costs and time.
Step 3: Verify Supplier Certifications
Once you’ve narrowed down your list, verify that each supplier holds relevant certifications. This is critical for ensuring product quality and compliance with local regulations. Suppliers should be able to provide documentation for certifications such as ISO, CE, or specific industry standards.
- Request copies of certifications and verify their validity.
- Ensure that the certifications match the specifications of the products you require.
Step 4: Request Product Samples
Requesting product samples is a vital step in the sourcing process. Samples allow you to evaluate the quality, durability, and appearance of the sandwich panels before making a bulk order. This step helps mitigate risks associated with product performance once installed.
- Assess the samples for insulation properties, finish quality, and overall aesthetics.
- Test the samples under conditions similar to your intended application.
Step 5: Evaluate Pricing and Payment Terms
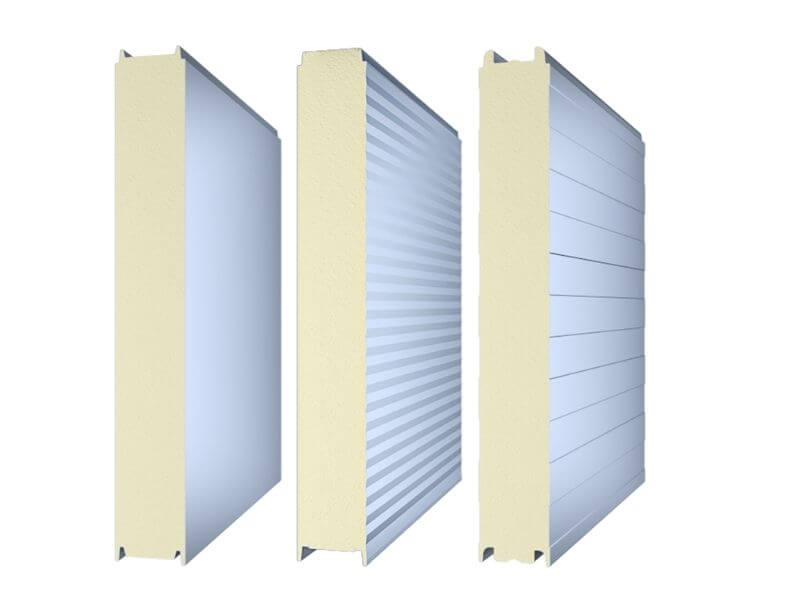
A stock image related to sandwich panel supplier.
Compare pricing among your shortlisted suppliers, but remember that the cheapest option may not always be the best. Look for transparency in pricing and inquire about payment terms. Understanding the total cost of ownership, including shipping and potential import duties, is essential for accurate budgeting.
- Ask for detailed quotations that break down all costs.
- Consider negotiating payment terms that align with your cash flow needs.
Step 6: Review Supplier Reliability and Support
Assess the reliability of potential suppliers by checking their delivery timelines, customer service, and support capabilities. A reliable supplier can significantly impact your project timeline and success. Look for testimonials or case studies that demonstrate their ability to meet deadlines and provide ongoing support.
- Ensure that the supplier has a responsive customer service team.
- Check for their ability to provide after-sales support, including warranties and returns.
Step 7: Finalize the Contract
Before proceeding with an order, finalize a contract that outlines all agreed-upon terms. This should include product specifications, pricing, delivery schedules, and warranty details. A well-structured contract protects both parties and helps prevent misunderstandings.
- Consult with legal advisors if necessary to ensure the contract is enforceable.
- Include clauses for quality assurance and dispute resolution.
By following this step-by-step checklist, international B2B buyers can streamline the process of sourcing sandwich panels and establish strong partnerships with reliable suppliers.
Comprehensive Cost and Pricing Analysis for sandwich panel supplier Sourcing
What Are the Key Cost Components in Sandwich Panel Production?
When sourcing sandwich panels, understanding the cost structure is essential for B2B buyers. The primary cost components include:
-
Materials: This is often the largest expense, including the core insulation material (e.g., polyurethane, polystyrene) and the outer metal sheets. Quality certifications, such as ASTM compliance, can significantly impact costs.
-
Labor: Skilled labor is required for the manufacturing process, which includes cutting, assembling, and finishing panels. Labor costs can vary based on location and the complexity of the product.
-
Manufacturing Overhead: This encompasses indirect costs associated with production, such as utilities, equipment maintenance, and administrative expenses. Efficient manufacturing processes can help reduce these costs.
-
Tooling: Initial setup costs for molds and machinery can be substantial, especially for customized or specialized panels. These costs are typically amortized over the production volume.
-
Quality Control (QC): Ensuring that panels meet specified standards requires investment in QC processes. This may include testing for thermal insulation properties and structural integrity.
-
Logistics: Transportation costs can vary significantly based on distance and mode of transport. Buyers should consider local suppliers to minimize logistics expenses.
-
Margin: Suppliers will include a profit margin based on their operational costs and market positioning. Understanding the supplier’s pricing strategy can provide leverage during negotiations.
How Do Price Influencers Affect Sandwich Panel Costs?
Several factors influence the pricing of sandwich panels, which international buyers should be aware of:
-
Volume/MOQ (Minimum Order Quantity): Larger orders typically result in lower per-unit costs due to economies of scale. Buyers should negotiate for bulk purchasing to maximize savings.
-
Specifications and Customization: Custom specifications can increase costs significantly. Buyers should evaluate whether standard panels meet their needs before opting for custom solutions.
-
Material Quality and Certifications: Higher-quality materials and additional certifications for fire resistance or environmental compliance can raise costs. However, investing in quality may reduce long-term maintenance expenses.
-
Supplier Factors: The supplier’s reputation, reliability, and location can affect pricing. Established suppliers may charge more but offer better quality assurance and service.
-
Incoterms: Understanding the terms of delivery (e.g., FOB, CIF) is crucial as they dictate who bears the shipping costs and risks. This can influence the total landed cost of panels.
What Are Effective Buyer Tips for Negotiating Sandwich Panel Prices?
International buyers, particularly from Africa, South America, the Middle East, and Europe, can adopt several strategies to optimize costs:
-
Negotiation Strategies: Engage suppliers in discussions about pricing, especially when placing large orders. Highlighting long-term relationships can lead to better pricing agreements.
-
Focus on Total Cost of Ownership (TCO): Consider the entire lifecycle costs, including installation, maintenance, and energy efficiency. Sometimes a higher upfront cost can result in lower overall expenses.
-
Understand Pricing Nuances: Be aware of currency fluctuations, tariffs, and import duties that may affect pricing. Having a financial strategy to mitigate these risks can lead to better budgeting.
-
Research Market Trends: Keep abreast of market conditions and competitor pricing. This knowledge can be instrumental in negotiations and ensuring you are getting competitive rates.
-
Request Multiple Quotes: Solicit quotes from various suppliers to compare pricing and terms. This not only gives leverage in negotiations but also helps identify the best value.
Disclaimer on Indicative Prices
Pricing for sandwich panels can fluctuate based on market conditions, material availability, and supplier policies. Buyers should treat any indicative prices as a starting point for negotiations and confirm current pricing with suppliers directly.
Alternatives Analysis: Comparing sandwich panel supplier With Other Solutions
When selecting building materials, B2B buyers must consider a variety of solutions that meet their specific needs. Sandwich panels have gained popularity for their insulation properties and structural efficiency; however, there are viable alternatives that may also suit different applications. This section will compare sandwich panel suppliers with two alternative solutions: traditional brick and mortar construction and prefabricated metal buildings.
Comparison Table of Sandwich Panel Suppliers and Alternatives
Comparison Aspect | Sandwich Panel Supplier | Traditional Brick and Mortar Construction | Prefabricated Metal Buildings |
---|---|---|---|
Performance | High thermal insulation, lightweight | Excellent durability, lower insulation | Good insulation, rapid assembly |
Cost | Moderate initial cost, cost-effective over time | High initial investment, ongoing costs | Competitive pricing, lower labor costs |
Ease of Implementation | Quick installation, less labor required | Time-consuming, requires skilled labor | Fast installation, minimal site work |
Maintenance | Low maintenance, weather-resistant | Moderate maintenance, susceptible to weather | Low maintenance, rust-resistant coatings |
Best Use Case | Cold storage, industrial, commercial | Residential, heritage buildings | Warehouses, factories, temporary structures |
What Are the Benefits and Drawbacks of Traditional Brick and Mortar Construction?
Traditional brick and mortar construction is known for its durability and aesthetic appeal. It provides excellent thermal mass, which can help regulate indoor temperatures. However, the initial cost is significantly higher, and the construction process is lengthy, requiring skilled labor. This method is best suited for residential buildings or those requiring a classic look but may not be ideal for projects with tight timelines or budget constraints.
How Do Prefabricated Metal Buildings Compare to Sandwich Panels?
Prefabricated metal buildings offer a robust alternative to sandwich panels. They are designed for quick assembly and can be customized for various applications. The cost is competitive, and labor costs are generally lower due to simplified construction. However, while they provide good insulation, they may not match the thermal efficiency of high-quality sandwich panels. These buildings are particularly advantageous for warehouses and factories where speed of construction is critical.
Conclusion: How Can B2B Buyers Choose the Right Solution?
When selecting the right building solution, B2B buyers must evaluate their specific project requirements, including budget, timeline, and intended use. Sandwich panels offer excellent thermal performance and quick installation, making them ideal for cold storage or industrial applications. In contrast, traditional brick and mortar construction is better for aesthetic-driven projects but comes with higher costs and longer timelines. Meanwhile, prefabricated metal buildings provide a balance of cost-effectiveness and rapid assembly, suitable for various commercial uses. By carefully analyzing these factors, buyers can make informed decisions that align with their operational goals and project specifications.
Essential Technical Properties and Trade Terminology for sandwich panel supplier
What Are the Key Technical Properties of Sandwich Panels for B2B Buyers?
When evaluating sandwich panels for construction or industrial applications, understanding their technical properties is crucial for making informed purchasing decisions. Here are the essential specifications to consider:
1. Material Grade
Sandwich panels are typically made from a variety of materials, including steel, aluminum, or composite materials. The material grade impacts the panel’s durability, insulation properties, and resistance to environmental factors. Higher-grade materials often translate to longer lifespan and better performance, making them a vital consideration for B2B buyers focused on quality and longevity.
2. Thermal Conductivity
This property measures how well a material conducts heat. Sandwich panels with lower thermal conductivity values provide better insulation, which is particularly important in regions with extreme climates. For B2B buyers, understanding thermal conductivity helps in assessing energy efficiency and potential cost savings in heating or cooling.
3. Fire Resistance Rating
Given the importance of safety in construction, the fire resistance rating indicates how well a panel can withstand fire exposure. Panels are often classified according to standards such as ASTM E84. For international buyers, this is not just a regulatory compliance issue but also a significant factor in minimizing risk and liability.
4. Weight and Load-Bearing Capacity
Weight is a critical factor, especially for transport and installation logistics. Lightweight panels facilitate easier handling and lower shipping costs. Concurrently, understanding the load-bearing capacity is essential for ensuring that the panels can support the intended structures without risk of failure. Buyers should carefully assess these metrics to align with their project requirements.
5. Tolerance Levels
Tolerance refers to the acceptable limits of variation in the dimensions and properties of the panels. High tolerance levels ensure better fit and finish during installation. For B2B buyers, knowing the tolerance levels helps in minimizing material waste and ensuring seamless integration into construction projects.
What Trade Terms Should International Buyers Understand in the Sandwich Panel Industry?
In addition to the technical properties, familiarity with industry jargon is essential for effective communication and negotiation. Here are some common terms:
1. OEM (Original Equipment Manufacturer)
This term refers to companies that produce components that are used in another company’s end product. For sandwich panel suppliers, understanding OEM relationships can help buyers identify reliable sources for customized panels that meet specific project needs.
2. MOQ (Minimum Order Quantity)
MOQ defines the smallest number of units a supplier is willing to sell. This is particularly relevant for international buyers looking to manage inventory costs effectively. Understanding MOQs can help in budgeting and ensuring sufficient supply for larger projects.
3. RFQ (Request for Quotation)
An RFQ is a standard business process where a buyer solicits price quotes from suppliers. For B2B buyers, issuing an RFQ helps in comparing prices, terms, and quality among different suppliers, leading to more strategic purchasing decisions.
4. Incoterms (International Commercial Terms)
These are a series of pre-defined commercial terms published by the International Chamber of Commerce (ICC) relating to international commercial law. Familiarity with Incoterms helps buyers understand their responsibilities regarding shipping, insurance, and tariffs, which is crucial for budgeting and logistics management.
5. Lead Time
Lead time refers to the amount of time from placing an order to its delivery. Knowing the lead time is vital for project planning and ensures that materials arrive on schedule to avoid delays in construction timelines.
By grasping these essential technical properties and trade terminologies, international B2B buyers can enhance their procurement strategies, minimize risks, and achieve successful project outcomes.
Navigating Market Dynamics and Sourcing Trends in the sandwich panel supplier Sector
What Are the Current Market Dynamics and Key Trends in the Sandwich Panel Supplier Sector?
The global sandwich panel market is experiencing substantial growth, driven by the rising demand for energy-efficient and sustainable building materials. Key markets in Africa, South America, the Middle East, and Europe are witnessing an upsurge in construction activities, particularly in industrial and commercial sectors. The adoption of advanced manufacturing technologies, such as automated production lines and computer-aided design (CAD), is enhancing the efficiency and quality of sandwich panels, making them an attractive option for builders and architects.
Emerging trends include a growing preference for lightweight and modular construction solutions. International B2B buyers are increasingly looking for suppliers who offer customizable products that can be easily transported and installed. Additionally, the integration of smart technologies in panel production, such as IoT-enabled monitoring systems, is gaining traction. These innovations facilitate better quality control and supply chain management, ensuring that buyers receive products that meet their specific requirements.
Furthermore, the influence of regional regulations is shaping market dynamics. For instance, in Europe, strict building codes related to thermal performance and fire safety are pushing suppliers to develop panels that comply with these standards. Buyers from Turkey and South Africa are encouraged to stay informed about local regulations that may impact sourcing decisions, ensuring compliance while optimizing costs.
How Is Sustainability and Ethical Sourcing Impacting the Sandwich Panel Sector?
Sustainability has become a pivotal concern in the sandwich panel industry, significantly affecting sourcing decisions for international B2B buyers. The environmental impact of construction materials is under scrutiny, prompting buyers to seek suppliers who prioritize eco-friendly practices. For instance, panels made from recycled materials or those that incorporate renewable resources are increasingly in demand.
Ethical sourcing is equally crucial, as buyers recognize the importance of responsible supply chains. Ensuring that suppliers adhere to ethical labor practices and environmental regulations not only enhances brand reputation but also mitigates risks associated with potential supply chain disruptions.
Buyers should look for suppliers that possess certifications such as ISO 14001 (Environmental Management) or LEED (Leadership in Energy and Environmental Design) accreditation. These certifications signify a commitment to sustainability and ethical practices, providing buyers with the assurance they need to make informed purchasing decisions.
What Is the Brief Evolution of the Sandwich Panel Supplier Sector?
The sandwich panel sector has evolved significantly over the past few decades. Initially developed in the mid-20th century for industrial applications, sandwich panels gained popularity due to their lightweight structure and excellent insulation properties. As construction methodologies advanced, the technology behind these panels also improved, incorporating better insulation materials and production techniques.
By the 1990s, the demand for energy-efficient solutions propelled the growth of the sandwich panel market into the commercial and residential sectors. Today, with increasing emphasis on sustainability and smart building technologies, the industry is poised for further innovation. This evolution highlights the adaptability of sandwich panel suppliers in meeting the changing needs of international B2B buyers, making them a vital component of modern construction projects.
Frequently Asked Questions (FAQs) for B2B Buyers of sandwich panel supplier
-
How do I select the right sandwich panel supplier for my project?
When choosing a sandwich panel supplier, start by evaluating their industry experience and product range. Look for suppliers with a proven track record in your region, particularly those familiar with local building codes and climate conditions. Additionally, request samples to assess the quality and insulation properties of their panels. Finally, ensure that the supplier offers customization options to meet your specific project requirements. -
What are the key specifications to consider when sourcing sandwich panels?
Key specifications include thermal insulation performance, fire resistance ratings, panel thickness, and structural integrity. It’s essential to verify compliance with relevant international standards, such as ASTM or DIN. Also, consider the aesthetic finishes available, as they can affect the overall look of your project. Lastly, check the warranty and after-sales support offered by the supplier. -
What is the typical minimum order quantity (MOQ) for sandwich panels?
The MOQ for sandwich panels can vary significantly between suppliers, typically ranging from 100 to 1,000 square meters. Suppliers may offer lower MOQs for custom or specialized orders, but it’s essential to confirm this before placing an order. Understanding your project’s scale will help you negotiate better terms and possibly lower your costs per unit. -
What payment terms should I expect when dealing with international suppliers?
Payment terms for international transactions often include options such as upfront deposits (usually 30-50%) with the balance due before shipment. Some suppliers may offer letters of credit or escrow services to ensure both parties are protected. Always clarify payment methods accepted (e.g., wire transfer, credit card) and consider the impact of currency exchange rates on your total costs. -
How do I ensure quality assurance when sourcing sandwich panels?
To ensure quality assurance, request documentation of the supplier’s quality management certifications, such as ISO 9001. It is also advisable to conduct factory audits or hire third-party inspection services to verify compliance with specifications. Additionally, consider establishing a clear agreement regarding quality standards, inspection protocols, and penalties for non-compliance before finalizing the contract. -
What logistics considerations should I keep in mind when importing sandwich panels?
Logistics for importing sandwich panels involve understanding shipping methods, lead times, and customs regulations. Assess whether the supplier offers shipping options or if you need to arrange your own freight forwarder. Be aware of potential duties and taxes applicable to your shipments, and ensure that the supplier provides necessary documentation for customs clearance. -
How can I customize sandwich panels to meet specific project requirements?
Most reputable sandwich panel suppliers offer customization options, including panel size, thickness, and insulation material. Discuss your project’s specific needs with the supplier to explore available options. Additionally, inquire about custom finishes or colors, as these can significantly impact the final appearance of your project. Ensure that any customizations are documented in your purchase agreement. -
What are the common applications of sandwich panels in construction?
Sandwich panels are commonly used in various applications, including industrial buildings, cold storage facilities, commercial warehouses, and residential constructions. Their lightweight yet durable nature makes them ideal for roofing, wall cladding, and partitioning. Furthermore, due to their excellent insulation properties, they are increasingly favored for energy-efficient buildings across diverse climates in Africa, South America, the Middle East, and Europe.
Important Disclaimer & Terms of Use
⚠️ Important Disclaimer
The information provided in this guide, including content regarding manufacturers, technical specifications, and market analysis, is for informational and educational purposes only. It does not constitute professional procurement advice, financial advice, or legal advice.
While we have made every effort to ensure the accuracy and timeliness of the information, we are not responsible for any errors, omissions, or outdated information. Market conditions, company details, and technical standards are subject to change.
B2B buyers must conduct their own independent and thorough due diligence before making any purchasing decisions. This includes contacting suppliers directly, verifying certifications, requesting samples, and seeking professional consultation. The risk of relying on any information in this guide is borne solely by the reader.
Strategic Sourcing Conclusion and Outlook for sandwich panel supplier
In the evolving landscape of sandwich panel sourcing, strategic partnerships are crucial for international B2B buyers seeking quality and efficiency. Understanding the specific needs of your projects—be it thermal insulation, structural integrity, or aesthetic appeal—can significantly enhance your procurement process. Prioritizing suppliers that adhere to international standards, such as ASTM and DIN, ensures that you receive products that meet your operational requirements.
Moreover, the strategic sourcing process allows you to leverage global market trends, particularly as suppliers from regions like Africa, South America, the Middle East, and Europe are increasingly competitive. Engaging with reputable manufacturers and suppliers not only fosters reliability but also opens avenues for innovation in design and application.
As you navigate the complexities of sourcing sandwich panels, consider establishing long-term relationships with suppliers who demonstrate commitment to quality and customer service. This approach will not only secure better pricing and terms but also enhance your project’s overall success. Moving forward, remain proactive in evaluating supplier performance and market changes to stay ahead in this dynamic industry. Your next step? Reach out to potential suppliers today and explore how they can meet your specific needs for future projects.