Transform Your Business: The Ultimate Tshirt Custom Guide (2025)
Introduction: Navigating the Global Market for tshirt custom
In today’s competitive landscape, sourcing high-quality custom t-shirts that align with brand identity and market demand poses a significant challenge for international B2B buyers. The global market is flooded with options, making it increasingly difficult to identify reliable suppliers, understand pricing structures, and gauge product quality. This comprehensive guide aims to demystify the complexities of the custom t-shirt market by exploring various types, applications, and essential criteria for supplier vetting.
International buyers from regions such as Africa, South America, the Middle East, and Europe (including the UAE and Indonesia) will find valuable insights on how to navigate the intricacies of sourcing custom apparel. From understanding the differences in fabric types and printing techniques to evaluating supplier reliability and cost-effectiveness, this guide empowers businesses to make informed purchasing decisions.
By addressing common pain points such as quality assurance, lead times, and compliance with local regulations, we equip B2B buyers with the knowledge needed to streamline their sourcing process. Whether you are looking to order bulk quantities for promotional events or seeking unique designs for niche markets, our guide serves as a vital resource to enhance your procurement strategy and maximize your return on investment in the custom t-shirt sector.
Understanding tshirt custom Types and Variations
Type Name | Key Distinguishing Features | Primary B2B Applications | Brief Pros & Cons for Buyers |
---|---|---|---|
Screen Printed T-Shirts | High-quality graphics, vibrant colors, cost-effective for large orders | Promotional events, corporate branding | Pros: Economical for bulk, high durability. Cons: Limited color options for complex designs. |
Direct-to-Garment (DTG) | Detailed designs, suitable for small batches, no color limitations | Custom orders, niche markets | Pros: High detail, unlimited colors. Cons: Higher cost per unit, slower production speed. |
Embroidered T-Shirts | Durable stitching, professional appearance, often used for logos | Corporate uniforms, team apparel | Pros: Long-lasting, upscale look. Cons: More expensive, limited design complexity. |
Dye Sublimation T-Shirts | Full-color designs that are embedded into the fabric, great for all-over prints | Fashion lines, sportswear | Pros: Exceptional color vibrancy, soft feel. Cons: Requires polyester fabric, less effective on cotton. |
Vintage/Retro Style T-Shirts | Distressed look, often pre-washed for softness, trendy designs | Fashion retailers, promotional giveaways | Pros: Popular aesthetic, appealing to younger demographics. Cons: May not suit all branding strategies. |
What Are Screen Printed T-Shirts and Their B2B Relevance?
Screen printed T-shirts are characterized by their vibrant graphics and durability, making them a popular choice for bulk orders. This method is ideal for promotional events and corporate branding, allowing businesses to effectively market themselves through visually appealing apparel. When considering screen printing, B2B buyers should evaluate their design complexity and order quantity, as this method is most cost-effective for larger batches.
How Does Direct-to-Garment (DTG) Printing Work for Custom T-Shirts?
Direct-to-Garment (DTG) printing allows for intricate designs and a wide range of colors, making it suitable for small batch customizations. This method is often used for niche markets where unique designs are essential. B2B buyers should consider the higher cost per unit and slower production speed when opting for DTG, as it may not be the best choice for bulk orders.
Why Choose Embroidered T-Shirts for Your Business?
Embroidered T-shirts offer a professional appearance with durable stitching, making them ideal for corporate uniforms and team apparel. The upscale look of embroidery can enhance brand perception, but buyers must weigh the cost implications and design limitations. Companies looking for longevity in their apparel branding may find embroidered options particularly appealing.
What Benefits Does Dye Sublimation Offer for Custom T-Shirts?
Dye sublimation is a unique printing method that embeds ink into the fabric, allowing for full-color designs and all-over prints. This technique is commonly used in fashion lines and sportswear, where vibrant colors are crucial. However, B2B buyers should note that dye sublimation works best with polyester fabrics and may not be as effective on cotton, influencing material choices.
How Do Vintage/Retro Style T-Shirts Fit into B2B Customization?
Vintage or retro style T-shirts are crafted to provide a distressed look and often come pre-washed for added softness, appealing primarily to younger demographics. These shirts are popular among fashion retailers and for promotional giveaways, offering a trendy aesthetic. However, B2B buyers should ensure that this style aligns with their branding strategy, as it may not resonate with all target audiences.
Related Video: DIY Custom T-Shirt Printing Tutorial – Made Easy!
Key Industrial Applications of tshirt custom
Industry/Sector | Specific Application of tshirt custom | Value/Benefit for the Business | Key Sourcing Considerations for this Application |
---|---|---|---|
Education | Custom t-shirts for school events and clubs | Enhances school spirit and unity among students | Quality of materials, customization options, bulk pricing |
Corporate Branding | Branded t-shirts for employee uniforms | Promotes brand visibility and employee cohesion | Fabric durability, design flexibility, order lead time |
Sports and Recreation | Custom jerseys for local teams and events | Fosters team identity and engagement with fans | Size variety, moisture-wicking fabrics, production speed |
Nonprofit Organizations | Fundraising t-shirts for awareness campaigns | Raises funds and awareness for social causes | Ethical sourcing, graphic design services, cost-effectiveness |
Retail and E-commerce | Personalized t-shirts for promotional sales | Increases customer loyalty and brand recognition | Inventory management, print quality, shipping options |
How is Custom T-Shirt Printing Used in Education?
In the education sector, custom t-shirts are widely used for school events, clubs, and sports teams. Schools often order shirts that showcase their logos and colors to foster a sense of community and pride among students. This application not only enhances school spirit but also serves as a marketing tool for attracting new students. For international buyers, sourcing considerations include the quality of materials used, the range of customization options available, and pricing for bulk orders, especially when catering to larger student populations.
What Role Do Custom T-Shirts Play in Corporate Branding?
Corporate branding leverages custom t-shirts as a means of promoting brand visibility and unity among employees. Companies often provide branded apparel for staff uniforms, which helps in creating a professional image while reinforcing brand identity. For businesses in Africa, South America, the Middle East, and Europe, key considerations include the durability of fabrics, flexibility in design options, and the lead time required for production. Ensuring that the t-shirts are suitable for various climates and work environments is also critical.
Why Are Custom Jerseys Important in Sports and Recreation?
In the realm of sports and recreation, custom t-shirts and jerseys are essential for local teams and events. They help to create a sense of belonging and identity among players and fans alike. Custom jerseys can be used for everything from community leagues to professional teams, providing a way for supporters to engage with their favorite sports. For B2B buyers, considerations include the variety of sizes available, the use of moisture-wicking fabrics for performance, and the speed of production to meet event timelines.
How Do Nonprofits Benefit from Custom T-Shirts?
Nonprofit organizations utilize custom t-shirts as a powerful tool for fundraising and raising awareness about their causes. These shirts often feature compelling graphics and messages that resonate with supporters, encouraging them to wear their commitment proudly. When sourcing t-shirts, nonprofits should consider ethical sourcing practices, the availability of graphic design services, and cost-effectiveness to maximize their fundraising efforts, particularly in diverse markets across Africa, South America, the Middle East, and Europe.
What Advantages Do Retailers Gain from Personalized T-Shirts?
In the retail and e-commerce sector, personalized t-shirts are used to drive promotional sales and enhance customer loyalty. Retailers often offer customizable options that allow customers to express their individuality, thereby increasing brand recognition and repeat business. Key sourcing considerations for retailers include effective inventory management, ensuring high print quality, and exploring shipping options that can accommodate international buyers, particularly in regions like the UAE and Indonesia where demand for unique apparel is growing.
3 Common User Pain Points for ‘tshirt custom’ & Their Solutions
Scenario 1: Quality Assurance in Custom T-Shirt Orders
The Problem: One of the most significant challenges faced by B2B buyers in the custom t-shirt market is ensuring the quality of the product. Buyers often encounter discrepancies in the fabric quality, print durability, and overall craftsmanship when comparing samples to the final order. This inconsistency can lead to dissatisfaction among end customers, damage to brand reputation, and ultimately financial losses. For international buyers, particularly those from regions like Africa or South America, the challenge is exacerbated by varying manufacturing standards and limited ability to inspect products before shipment.
The Solution: To mitigate quality assurance issues, B2B buyers should establish a robust vendor evaluation process. Start by sourcing suppliers with verified quality certifications, such as ISO or Oeko-Tex, which indicate adherence to international standards. Request detailed product specifications and samples before placing bulk orders, allowing for side-by-side comparisons of fabric and print quality. Additionally, consider leveraging third-party inspection services, especially for large orders, to verify quality before shipment. Investing in a quality assurance checklist tailored to your specifications can further help in maintaining consistent product standards.
Scenario 2: Navigating Cultural Preferences in Custom Designs
The Problem: Another common pain point for B2B buyers is understanding and catering to cultural preferences and trends in custom t-shirt designs. Buyers from diverse regions, such as the Middle East or Europe, may face challenges in selecting designs that resonate with their target audience. Misalignment in cultural aesthetics can lead to poor sales and wasted inventory, making it crucial for buyers to understand local tastes and preferences.
The Solution: Conducting thorough market research is essential in addressing this challenge. B2B buyers should engage in focus groups or surveys to gather insights on design preferences, color schemes, and cultural symbols that appeal to their target demographic. Collaborating with local designers or cultural consultants can also provide valuable perspectives that align your product offerings with regional expectations. Furthermore, consider implementing a test marketing phase by producing limited quantities of selected designs and monitoring sales performance before committing to larger production runs.
Scenario 3: Managing Lead Times and Inventory Challenges
The Problem: Managing lead times and inventory for custom t-shirts can be particularly challenging, especially for B2B buyers who are accustomed to just-in-time inventory systems. Delays in production or shipping can result in missed deadlines for promotional events or seasonal sales, leading to lost revenue opportunities. Buyers must also contend with the uncertainty of overstocking or understocking inventory, which complicates financial forecasting and cash flow management.
The Solution: To address lead time challenges, establish clear communication channels with suppliers to set realistic production timelines. Utilize project management tools to track order progress and proactively address potential delays. Additionally, implementing a demand forecasting system can help predict inventory needs based on historical sales data and market trends. Consider diversifying your supplier base to include local manufacturers who can offer faster turnaround times for urgent orders. Lastly, maintaining a safety stock of high-demand items can serve as a buffer against unexpected demand spikes or supply chain disruptions.
Strategic Material Selection Guide for tshirt custom
When selecting materials for custom t-shirts, international B2B buyers must consider various factors that impact product performance, cost, and market suitability. Below, we analyze four common materials used in custom t-shirt production, highlighting their properties, advantages, disadvantages, and specific considerations for buyers from Africa, South America, the Middle East, and Europe.
What are the Key Properties of Cotton for Custom T-Shirts?
Cotton is one of the most widely used materials in the apparel industry, particularly for t-shirts. It is known for its breathability, softness, and comfort, making it ideal for casual wear.

A stock image related to tshirt custom.
Pros & Cons:
– Advantages: Cotton is highly absorbent, allowing it to wick moisture away from the skin, which is essential in hot climates. It is also biodegradable, aligning with sustainability trends.
– Disadvantages: Cotton can shrink and wrinkle easily, and its durability is lower compared to synthetic materials. Additionally, it may require more complex manufacturing processes to achieve certain designs.
Impact on Application:
Cotton t-shirts are suitable for screen printing and direct-to-garment (DTG) printing, making them versatile for custom designs.
Considerations for International Buyers:
Buyers should be aware of cotton quality standards, such as the Global Organic Textile Standard (GOTS) for organic cotton. Compliance with local regulations regarding sustainable practices is also crucial.
How Does Polyester Enhance Performance in Custom T-Shirts?
Polyester is a synthetic material known for its durability and resistance to shrinking and stretching. It is often blended with cotton to enhance performance.
Pros & Cons:
– Advantages: Polyester is quick-drying and retains its shape well, making it suitable for athletic wear. It is also resistant to wrinkles and fading.
– Disadvantages: The fabric can be less breathable than cotton, which may lead to discomfort in hot conditions. Additionally, polyester is not biodegradable, raising environmental concerns.
Impact on Application:
Polyester t-shirts are ideal for sublimation printing, allowing for vibrant, long-lasting designs.
Considerations for International Buyers:
Buyers must consider the environmental impact of polyester and look for suppliers that adhere to recycling standards, such as the Recycled Polyester certification.
What Role Does Rayon Play in Custom T-Shirt Fabrication?
Rayon is a semi-synthetic fiber derived from natural sources, primarily wood pulp. It offers a luxurious feel and drapes well.
Pros & Cons:
– Advantages: Rayon is soft, breathable, and has a silky appearance, making it popular for fashion-forward designs.
– Disadvantages: It is less durable than cotton and polyester and can be prone to wrinkling. Additionally, rayon requires careful washing to maintain its appearance.
Impact on Application:
Rayon t-shirts are suitable for fashion lines where aesthetics are prioritized over durability.
Considerations for International Buyers:
Buyers should verify the sourcing of rayon to ensure it meets environmental and ethical standards, such as the Forest Stewardship Council (FSC) certification.
Why is Blended Fabric Important for Custom T-Shirt Production?
Blended fabrics, such as cotton-polyester blends, combine the best properties of both materials.
Pros & Cons:
– Advantages: Blends offer improved durability, comfort, and moisture-wicking properties. They are versatile for various printing methods and styles.
– Disadvantages: The performance can vary widely depending on the blend ratio, and some blends may not be as sustainable as pure materials.
Impact on Application:
Blended fabrics are suitable for a wide range of applications, from casual wear to promotional items.
Considerations for International Buyers:
Buyers should inquire about the specific blend ratios and the sustainability practices of manufacturers to ensure compliance with local regulations.
Summary Table of Material Selection for Custom T-Shirts
Material | Typical Use Case for tshirt custom | Key Advantage | Key Disadvantage/Limitation | Relative Cost (Low/Med/High) |
---|---|---|---|---|
Cotton | Casual wear, promotional items | Breathable and comfortable | Prone to shrinking and wrinkling | Medium |
Polyester | Athletic wear, sublimation printing | Quick-drying and durable | Less breathable | Low |
Rayon | Fashion-forward designs | Luxurious feel and drape | Less durable, prone to wrinkling | Medium |
Blended | Versatile applications | Combines benefits of multiple materials | Performance varies by blend ratio | Medium |
This strategic guide aims to assist international B2B buyers in making informed decisions when selecting materials for custom t-shirts, ensuring alignment with market demands and sustainability practices.
In-depth Look: Manufacturing Processes and Quality Assurance for tshirt custom
What Are the Key Stages in the Manufacturing Process for Custom T-Shirts?
The manufacturing process for custom t-shirts involves several critical stages, each requiring careful execution to ensure high quality and efficiency. Understanding these stages is essential for international B2B buyers looking to source quality products.
Material Preparation: How Is Fabric Selected and Processed?
The first stage of t-shirt manufacturing begins with the selection of raw materials. Fabrics such as cotton, polyester, or blends are commonly used, depending on the desired characteristics like softness, durability, and moisture-wicking properties.
Once the fabric is selected, it undergoes pre-treatment processes including washing and dyeing. This step is crucial to remove impurities and prepare the fabric for printing or other embellishment techniques. Buyers should inquire about the origin of the materials and any certifications (e.g., organic cotton, recycled polyester) to ensure compliance with ethical sourcing standards.
Forming: What Techniques Are Used to Cut and Sew T-Shirts?
After the material is prepared, the next stage is forming, which includes cutting and sewing the fabric. Advanced cutting techniques such as laser cutting or computer-aided design (CAD) are often employed to ensure precision and minimize waste.
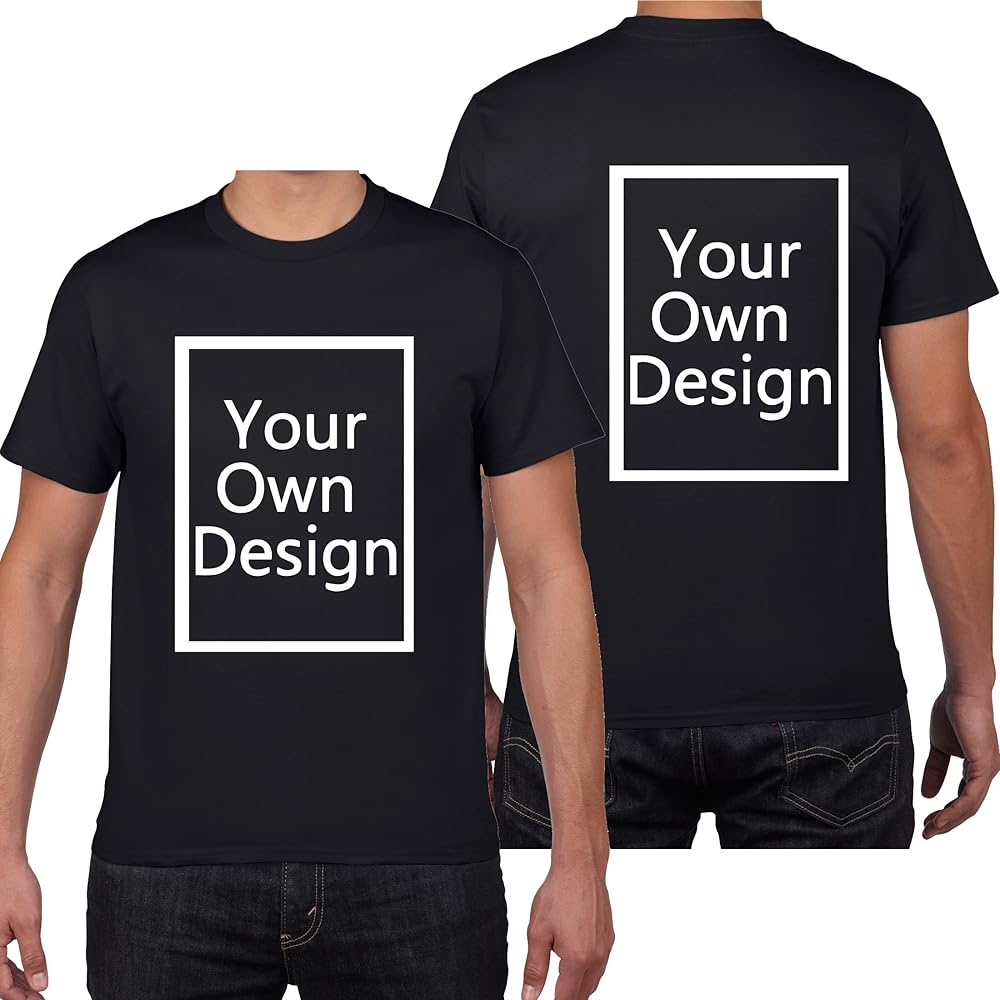
A stock image related to tshirt custom.
Sewing is typically done using industrial sewing machines that can handle various types of stitches, depending on the design and fabric type. It’s advisable for buyers to request samples to assess the stitching quality and seam integrity, as these aspects significantly impact the garment’s durability.
Assembly: How Are Custom Designs Incorporated?
The assembly stage involves adding custom designs, which may include screen printing, embroidery, or heat transfer methods. Each technique has its advantages: screen printing is cost-effective for large runs, while embroidery adds a premium feel to smaller batches.
B2B buyers should ensure that manufacturers have the capacity to handle specific design requirements, including color matching and complexity of artwork. Additionally, discussing lead times and production capabilities is essential to meet market demands.
Finishing: What Final Touches Enhance Quality?
The final stage in the manufacturing process is finishing, where t-shirts are cleaned, pressed, and packaged. Quality checks are performed to ensure that the final product meets the specifications agreed upon during the order process. This includes checking for defects, color consistency, and proper sizing.
Buyers should inquire about the finishing processes used, as these can influence the overall appearance and feel of the t-shirts. A well-finished product not only enhances customer satisfaction but also reflects positively on the brand.
What Quality Assurance Standards Should B2B Buyers Consider?
Quality assurance (QA) is crucial in the custom t-shirt manufacturing process, ensuring that products meet both international and industry-specific standards. Buyers should be familiar with relevant certifications and quality checkpoints.
Which International Standards Are Relevant for Custom T-Shirt Manufacturing?
International standards like ISO 9001 are essential for ensuring a consistent quality management system. This certification indicates that the manufacturer follows established processes to meet customer and regulatory requirements.
Moreover, certifications specific to the textile industry, such as OEKO-TEX® and GOTS (Global Organic Textile Standard), are increasingly important for buyers concerned about sustainability and safety. These certifications guarantee that textiles are free from harmful substances and produced in environmentally friendly processes.
What Are the Key Quality Checkpoints in the Production Process?
Quality control checkpoints are strategically placed throughout the manufacturing process. Key checkpoints include:
- Incoming Quality Control (IQC): This involves inspecting raw materials upon arrival to ensure they meet predefined standards.
- In-Process Quality Control (IPQC): Ongoing inspections during production help identify defects early, reducing waste and rework.
- Final Quality Control (FQC): A thorough inspection of finished products before packaging ensures they meet quality standards.
Buyers should inquire about the frequency of these inspections and the criteria used to evaluate quality at each stage.
How Can B2B Buyers Verify Supplier Quality Control?
Verifying the quality control measures of potential suppliers is crucial for B2B buyers, especially when sourcing internationally. Here are some effective strategies:
What Steps Can Buyers Take for Supplier Audits?
Conducting supplier audits is one of the most effective ways to assess a manufacturer’s quality control processes. These audits can be done by the buyers themselves or through third-party inspection services. During an audit, buyers should evaluate the manufacturing facility, quality management systems, and adherence to safety and environmental regulations.
How Can Buyers Utilize Reports and Third-Party Inspections?
Requesting detailed quality reports from suppliers can provide insights into their quality control practices and previous audits. These reports should outline any quality issues encountered and how they were resolved.
Additionally, utilizing third-party inspection services can offer an unbiased assessment of the products before shipment. These inspectors can check for compliance with specifications, quality standards, and overall product integrity.
What Are the Nuances of Quality Control for International Buyers?
For international B2B buyers, particularly those from diverse regions such as Africa, South America, the Middle East, and Europe, understanding local regulations and market expectations is essential.
How Do Cultural and Regulatory Differences Affect Quality Assurance?
Cultural differences can influence perceptions of quality and acceptable standards. Buyers should be aware of regional preferences and standards when sourcing custom t-shirts. Additionally, understanding the regulatory landscape in the supplier’s country can help buyers ensure compliance with import/export laws and product safety standards.
What Should Buyers Know About Shipping and Handling Risks?
Finally, buyers should consider the risks associated with shipping and handling. Quality can be compromised during transport, so it’s vital to discuss packaging methods and protective measures with suppliers. Buyers should also confirm that insurance is in place to cover potential damages during shipping.
By taking these steps, international B2B buyers can ensure they source high-quality custom t-shirts that meet their specifications and customer expectations.
Practical Sourcing Guide: A Step-by-Step Checklist for ‘tshirt custom’
In the fast-paced world of B2B procurement, sourcing custom t-shirts requires a strategic approach to ensure quality, cost-effectiveness, and timely delivery. This checklist will guide international buyers, particularly from Africa, South America, the Middle East, and Europe, through the essential steps to procure custom t-shirts effectively.
Step 1: Define Your Technical Specifications
Before reaching out to suppliers, clearly outline your technical specifications. This includes the desired fabric type, weight, color options, sizes, and printing methods.
– Why it matters: Precise specifications help suppliers provide accurate quotes and ensure the final product meets your expectations.
– Tip: Create a detailed document that can be shared with potential suppliers to streamline communication.
Step 2: Research and Identify Potential Suppliers
Conduct thorough research to identify potential suppliers that specialize in custom t-shirts. Use online platforms, trade shows, and industry directories to compile a list.
– Why it matters: A diverse supplier base increases your chances of finding a partner that aligns with your quality and budget requirements.
– Tip: Look for suppliers with experience in your target market, as they will better understand local regulations and consumer preferences.
Step 3: Evaluate Potential Suppliers
Before committing, it’s crucial to vet suppliers thoroughly. Request company profiles, case studies, and references from buyers in a similar industry or region.
– Why it matters: Understanding a supplier’s reliability and past performance can prevent costly mistakes.
– Tip: Ask for samples of previous work to assess quality firsthand.
Step 4: Verify Supplier Certifications
Ensure that potential suppliers hold relevant certifications and adhere to quality standards. Common certifications include ISO 9001 for quality management and OEKO-TEX for sustainable materials.
– Why it matters: Certifications indicate that a supplier meets specific industry standards, which can be essential for maintaining your brand’s reputation.
– Tip: Request copies of certifications and check their validity through the issuing bodies.
Step 5: Request Quotes and Compare Pricing
After narrowing down your list, request detailed quotes from your selected suppliers. Compare pricing, minimum order quantities, and payment terms.
– Why it matters: Understanding the total cost, including shipping and customs duties, is crucial for budgeting.
– Tip: Don’t just focus on the lowest price; consider the value offered, including quality and service.
Step 6: Negotiate Terms and Conditions
Once you receive quotes, engage in negotiations to finalize terms and conditions. Discuss lead times, payment schedules, and warranty policies.
– Why it matters: Clear agreements help avoid misunderstandings and ensure both parties are aligned on expectations.
– Tip: Document all agreed-upon terms in a formal contract to protect your interests.
Step 7: Place a Trial Order
Before committing to a large order, consider placing a trial order to assess the supplier’s capabilities and product quality.
– Why it matters: A trial order allows you to evaluate the supplier’s service and product before making a significant investment.
– Tip: Use the trial order to test the quality of the t-shirts, printing accuracy, and delivery timelines.
By following this checklist, B2B buyers can navigate the complexities of sourcing custom t-shirts effectively, ensuring a smooth procurement process that meets their business needs.
Comprehensive Cost and Pricing Analysis for tshirt custom Sourcing
Understanding the cost structure and pricing dynamics involved in custom t-shirt sourcing is crucial for international B2B buyers, particularly those operating in diverse markets like Africa, South America, the Middle East, and Europe. Below is a comprehensive analysis of the various cost components, price influencers, and actionable tips for buyers.
What Are the Key Cost Components in Custom T-Shirt Sourcing?
-
Materials: The choice of fabric significantly impacts cost. Cotton, polyester, and blended fabrics each have different price points. Sustainable materials, while often more expensive, can appeal to environmentally conscious consumers and command a premium price.
-
Labor: Labor costs vary by region, influenced by local wage standards and availability of skilled workers. Countries with lower labor costs, such as some in Southeast Asia, may offer competitive pricing for bulk orders.
-
Manufacturing Overhead: This includes expenses such as utilities, rent, and administrative costs associated with running the production facility. Efficient operations can help minimize these overheads, leading to better pricing for buyers.
-
Tooling: Custom designs may require specific tools or machinery, adding to upfront costs. This is particularly relevant for specialized printing techniques or unique garment constructions.
-
Quality Control (QC): Ensuring product quality can incur additional costs, especially if third-party inspections are required. However, investing in QC can prevent costly returns and maintain brand reputation.
-
Logistics: Shipping costs can vary significantly depending on the distance, volume, and shipping method. Buyers should consider both freight costs and any import duties that may apply.
-
Margin: Suppliers typically add a profit margin on top of their costs. Understanding the average margins within your supplier’s region can aid in negotiating better prices.
How Do Volume and Customization Affect Pricing?
Volume/MOQ (Minimum Order Quantity): Generally, larger orders lead to lower per-unit costs due to economies of scale. Suppliers often provide tiered pricing based on order size, incentivizing bulk purchases.
Specifications and Customization: More complex designs, additional colors, or unique features can increase costs. Buyers should weigh the benefits of customization against potential price increases.
Material Quality and Certifications: Higher-quality materials and certifications (e.g., organic or fair-trade certifications) can raise costs. Buyers should assess their target market’s willingness to pay for these premium attributes.
Supplier Factors: Established suppliers may offer better pricing due to their operational efficiencies or bulk purchasing power. Evaluating potential suppliers based on their history and reliability can lead to better pricing outcomes.
Incoterms: Understanding Incoterms is crucial for international buyers as they dictate the responsibilities for shipping, insurance, and tariffs. Choosing the right terms can significantly impact total costs.
What Tips Can Help International B2B Buyers Negotiate Better Prices?
-
Negotiate Terms: Always negotiate pricing and payment terms. Many suppliers are open to discussions, especially for larger orders or long-term partnerships.
-
Focus on Total Cost of Ownership (TCO): Consider not just the purchase price but also the long-term costs associated with the product, including logistics, storage, and potential returns.
-
Research Market Trends: Understanding local market trends can provide leverage during negotiations. For instance, if sustainable fashion is trending, suppliers might offer better deals on eco-friendly materials.
-
Leverage Technology: Utilize sourcing platforms that compare suppliers and pricing. This can provide insights into competitive pricing and supplier reliability.
-
Build Relationships: Establishing a good relationship with suppliers can lead to better pricing and terms over time. Suppliers are more likely to offer discounts to reliable, repeat customers.
Disclaimer on Indicative Prices
Prices in the custom t-shirt market can fluctuate based on various factors such as market demand, material availability, and geopolitical influences. Buyers are encouraged to conduct thorough market research and engage with multiple suppliers to obtain the most accurate pricing information for their specific needs.
Alternatives Analysis: Comparing tshirt custom With Other Solutions
When considering the best solutions for custom apparel, particularly t-shirts, it is essential for B2B buyers to explore various alternatives. Each option presents unique benefits and drawbacks, which can significantly influence a company’s branding, marketing, and operational efficiency. Here, we compare ‘Tshirt Custom’ with two viable alternatives: Direct-to-Garment (DTG) Printing and Bulk Purchasing from Wholesale Suppliers.
Comparison Aspect | Tshirt Custom | Direct-to-Garment (DTG) Printing | Bulk Purchasing from Wholesale Suppliers |
---|---|---|---|
Performance | High-quality customization with various designs | Excellent detail and color vibrancy | Limited customization, but consistent quality |
Cost | Moderate to high, depending on design complexity | Variable; can be cost-effective for small runs | Low cost per unit, but high initial investment |
Ease of Implementation | Requires design and setup time | Quick setup for designs but requires specialized printers | Simple ordering process with established suppliers |
Maintenance | Minimal; ongoing design updates needed | Requires maintenance of printing equipment | No maintenance; straightforward supply chain |
Best Use Case | Unique, one-off designs for events or promotions | Small to medium runs with intricate designs | Large volume orders for resale or branding |
What Are the Pros and Cons of Direct-to-Garment (DTG) Printing?
Direct-to-Garment (DTG) printing is an innovative technology that allows for high-quality prints directly onto fabric.
Pros:
– High Detail: DTG excels in producing intricate designs with vibrant colors, making it ideal for complex graphics and images.
– Low Minimum Orders: Businesses can order as few as one shirt, allowing for flexibility in inventory management and design experimentation.
Cons:
– Higher Costs for Larger Runs: While effective for small quantities, costs can escalate quickly with larger orders compared to bulk purchasing.
– Equipment Dependency: Requires investment in specialized printers, which may not be feasible for all businesses.
How Does Bulk Purchasing from Wholesale Suppliers Work?
Bulk purchasing involves buying t-shirts in large quantities from suppliers, typically at a reduced cost per unit.
Pros:
– Cost Efficiency: The more units ordered, the lower the cost per item, making it an economical choice for businesses looking to scale.
– Simplified Supply Chain: Established suppliers often have reliable delivery schedules and quality assurance processes.
Cons:
– Limited Customization: Customization options may be restricted to colors and sizes, which can hinder brand differentiation.
– Higher Initial Investment: Businesses must commit to large orders upfront, which may not align with fluctuating market demands.
How Should B2B Buyers Choose the Right Solution?
When selecting the appropriate solution for t-shirt customization, B2B buyers should assess their specific needs and operational capabilities. For instance, if the goal is to create unique, limited-edition designs for a marketing campaign, ‘Tshirt Custom’ or DTG printing would be advantageous. Conversely, if a business seeks to maintain a consistent inventory for resale, bulk purchasing from wholesale suppliers may be the most cost-effective strategy. Ultimately, understanding the trade-offs between customization, cost, and operational demands will guide buyers to make informed decisions that align with their business objectives.
Essential Technical Properties and Trade Terminology for tshirt custom
What Are the Key Technical Properties of Custom T-Shirts?
When engaging in the custom t-shirt business, understanding the technical properties of the products is crucial for making informed purchasing decisions. Here are some essential specifications that international B2B buyers should consider:
-
Material Grade
The fabric’s material grade determines its quality, durability, and comfort. Common materials include cotton, polyester, and blends. For instance, 100% cotton is soft and breathable, making it ideal for casual wear, while polyester is more durable and moisture-wicking, suitable for activewear. Selecting the right material is vital for aligning with your target market’s preferences and ensuring customer satisfaction. -
Weight
T-shirt weight is measured in grams per square meter (GSM). A lighter weight (around 140-160 GSM) is often preferred for summer wear, while heavier weights (200 GSM and above) are seen as more durable and suitable for colder climates. Understanding weight is essential for positioning your products appropriately in the market and meeting customer expectations. -
Color Fastness
This property refers to how well a fabric retains its color after washing and exposure to light. High color fastness is crucial for maintaining the visual appeal of custom designs over time. Buyers should request samples to test color fastness, as this can impact the longevity of your brand’s image. -
Shrinkage Rate
The shrinkage rate indicates how much a fabric might shrink after washing. Fabrics with high shrinkage rates can lead to customer dissatisfaction if the final product does not fit as expected. Buyers should inquire about the pre-treatment processes that suppliers use to minimize shrinkage. -
Tolerance
Tolerance refers to the acceptable range of variation in product dimensions. For instance, a t-shirt’s size might have a tolerance of ±1 inch. Understanding tolerance is important for ensuring consistency in production, which is critical for bulk orders. -
Print Compatibility
Not all fabrics are suitable for all types of printing methods (e.g., screen printing, digital printing, heat transfer). Buyers need to confirm that the chosen material is compatible with the desired printing technique to ensure high-quality results.
What Are Common Trade Terms in the Custom T-Shirt Industry?
Navigating the custom t-shirt market involves familiarizing oneself with key trade terminology. Here are several important terms that every B2B buyer should know:
-
OEM (Original Equipment Manufacturer)
This term refers to a company that produces parts or products that are then sold under another company’s brand name. In the context of custom t-shirts, buyers may work with OEMs to create unique designs that fit their branding needs. -
MOQ (Minimum Order Quantity)
MOQ represents the smallest quantity of product that a supplier is willing to sell. Understanding MOQ is vital for budgeting and inventory management, especially for businesses that may be testing new designs or markets. -
RFQ (Request for Quotation)
An RFQ is a document that a buyer sends to suppliers to request pricing and terms for specific products. It is a crucial step in the sourcing process, allowing buyers to compare offers and make informed purchasing decisions. -
Incoterms (International Commercial Terms)
These are standardized terms used in international trade to clarify the responsibilities of buyers and sellers regarding shipping, insurance, and tariffs. Familiarity with Incoterms helps buyers understand their obligations and risks in the shipping process. -
Lead Time
Lead time refers to the time it takes from placing an order to receiving the products. Knowing the lead time is essential for effective planning and ensuring that products are available when needed, especially for seasonal sales. -
Customs Duties and Taxes
These are fees imposed by governments on imported goods. Understanding the customs duties applicable to custom t-shirts can significantly impact overall costs and pricing strategies for international buyers.
By grasping these technical properties and trade terms, B2B buyers can make more strategic decisions in their custom t-shirt procurement, ultimately enhancing their business operations and market competitiveness.
Navigating Market Dynamics and Sourcing Trends in the tshirt custom Sector
What Are the Key Trends Shaping the Custom T-Shirt Market?
The global custom t-shirt market is experiencing significant growth, driven by factors such as increased consumer demand for personalized apparel and the rise of e-commerce platforms. For international B2B buyers, particularly in regions like Africa, South America, the Middle East, and Europe, understanding these dynamics is crucial. The proliferation of digital printing technologies, including Direct-to-Garment (DTG) and dye-sublimation, has made it easier for businesses to offer customized designs at scale.
Additionally, social media’s influence cannot be overstated; platforms like Instagram and TikTok have become vital marketing tools for brands, pushing them to create unique, eye-catching designs that resonate with their audience. This trend is particularly prominent among younger demographics who prioritize individuality in fashion choices. Furthermore, the demand for quick turnaround times and low minimum order quantities is reshaping sourcing strategies, compelling suppliers to adopt agile production methods to meet customer expectations.
How Is Sustainability Influencing B2B Sourcing Decisions in the Custom T-Shirt Sector?
Sustainability and ethical sourcing are becoming non-negotiable factors for B2B buyers in the custom t-shirt sector. The environmental impact of the apparel industry is significant, contributing to pollution and waste. As a response, businesses are increasingly seeking suppliers who prioritize sustainable practices, such as using organic cotton, recycled materials, and non-toxic dyes. Certifications like GOTS (Global Organic Textile Standard) and OEKO-TEX® provide assurance of a product’s environmental credentials and ethical production processes.
Moreover, consumers are becoming more conscious of the brands they support, often favoring companies that align with their values. This shift is particularly relevant in Europe and North America, where eco-friendly products are gaining traction. By sourcing from suppliers with robust sustainability practices, B2B buyers can not only enhance their brand reputation but also comply with emerging regulations aimed at reducing environmental impact.
How Has the Custom T-Shirt Market Evolved Over Time?
The custom t-shirt market has undergone a remarkable transformation over the past few decades. Initially dominated by screen printing techniques, the industry has evolved with advancements in technology, allowing for greater customization and efficiency. The introduction of digital printing methods has enabled businesses to produce smaller batches of customized shirts without sacrificing quality or incurring high setup costs.
In addition, the rise of online platforms has democratized access to custom apparel, allowing even small businesses and individual entrepreneurs to enter the market. This evolution reflects a broader trend in consumer behavior, where personalization and unique offerings are increasingly valued. As a result, the custom t-shirt sector is not only thriving but is also becoming an integral part of many brands’ marketing strategies, aligning with the growing demand for tailored, impactful products.
Conclusion
For international B2B buyers navigating the custom t-shirt market, staying informed about emerging trends, sustainability practices, and the historical evolution of the industry is essential. By embracing these insights, buyers can make informed sourcing decisions that resonate with their target audience and align with contemporary market demands.
Frequently Asked Questions (FAQs) for B2B Buyers of tshirt custom
-
How do I choose the right supplier for custom t-shirts?
Choosing the right supplier for custom t-shirts involves evaluating several factors, including the supplier’s reputation, production capabilities, and quality control measures. Look for suppliers with positive reviews and a proven track record in the B2B space. Request samples to assess fabric quality and printing techniques. Additionally, ensure they have experience with international shipping and compliance with your country’s import regulations. A supplier that communicates effectively and is responsive to your needs can enhance the overall purchasing experience. -
What are the minimum order quantities (MOQs) for custom t-shirts?
Minimum order quantities (MOQs) can vary significantly among suppliers, typically ranging from 50 to several hundred units. Many suppliers may offer flexible MOQs for first-time buyers or bulk orders. It’s essential to confirm the MOQ before proceeding to avoid unexpected costs. Consider negotiating MOQs based on your budget and anticipated sales volume, especially if you are a new business. Understanding the supplier’s production capacity can help you make informed decisions. -
What customization options are available for custom t-shirts?
Customization options for t-shirts can include screen printing, embroidery, heat transfer, and direct-to-garment (DTG) printing. Additionally, buyers can choose from a variety of fabrics, colors, and styles, such as crew necks, v-necks, and long sleeves. Many suppliers also offer design services to help create unique graphics or logos. It’s advisable to discuss your specific requirements upfront to ensure the supplier can meet your customization needs effectively. -
What payment terms should I expect when ordering custom t-shirts?
Payment terms for custom t-shirt orders can vary widely among suppliers. Common arrangements include full payment upfront, a deposit followed by the balance upon completion, or payment upon delivery. International buyers should inquire about currency options, wire transfer fees, and potential escrow services for added security. Understanding the supplier’s payment terms will help you manage cash flow and mitigate risks associated with international transactions. -
How do I ensure quality assurance for custom t-shirts?
To ensure quality assurance for your custom t-shirts, establish clear specifications for materials, dimensions, and printing techniques before placing an order. Request pre-production samples to verify quality and accuracy. Many reputable suppliers implement quality control processes, such as inspections at various production stages. Additionally, consider third-party quality assurance services, especially for larger orders, to minimize risks related to defects or discrepancies. -
What logistics considerations should I keep in mind when sourcing custom t-shirts internationally?
When sourcing custom t-shirts internationally, consider shipping options, delivery timelines, and customs regulations. Evaluate freight costs and choose between air freight for faster delivery or sea freight for cost savings. Ensure your supplier provides accurate shipping documents to facilitate customs clearance. Familiarize yourself with your country’s import duties and taxes, as these can significantly impact your overall costs. -
How can I effectively communicate my design ideas to the supplier?
Effectively communicating your design ideas to the supplier can be achieved by providing detailed artwork files, including color specifications and dimensions. Utilize design software to create mock-ups or sketches that clearly illustrate your vision. Additionally, consider using reference images and providing written descriptions to ensure alignment. Regular communication throughout the design process will help address any questions or concerns, ultimately leading to a successful outcome. -
What are the common challenges faced by international buyers in custom t-shirt procurement?
International buyers often face challenges such as language barriers, varying quality standards, and complex shipping logistics. Additionally, cultural differences can affect negotiation styles and expectations. To mitigate these challenges, conduct thorough research on potential suppliers and establish clear lines of communication. Building a relationship with your supplier can also foster trust and facilitate smoother transactions, reducing the likelihood of misunderstandings.
Important Disclaimer & Terms of Use
⚠️ Important Disclaimer
The information provided in this guide, including content regarding manufacturers, technical specifications, and market analysis, is for informational and educational purposes only. It does not constitute professional procurement advice, financial advice, or legal advice.
While we have made every effort to ensure the accuracy and timeliness of the information, we are not responsible for any errors, omissions, or outdated information. Market conditions, company details, and technical standards are subject to change.
B2B buyers must conduct their own independent and thorough due diligence before making any purchasing decisions. This includes contacting suppliers directly, verifying certifications, requesting samples, and seeking professional consultation. The risk of relying on any information in this guide is borne solely by the reader.
Strategic Sourcing Conclusion and Outlook for tshirt custom
The journey of strategic sourcing in the custom t-shirt industry reveals significant opportunities for international B2B buyers across diverse markets, particularly in Africa, South America, the Middle East, and Europe. By leveraging strategic sourcing practices, businesses can unlock cost savings, enhance product quality, and foster sustainable partnerships with manufacturers. Understanding the nuances of local markets and consumer preferences is crucial for tailoring offerings that resonate with target audiences, ensuring greater market penetration and customer loyalty.
What are the key takeaways for B2B buyers in custom t-shirts? First, prioritize suppliers who demonstrate sustainability and ethical production practices. Second, invest in technology that streamlines the ordering and customization process, enhancing efficiency and customer experience. Lastly, build long-term relationships with reliable suppliers who can adapt to changing market demands and trends.
Looking ahead, the global demand for custom apparel is set to rise. As you navigate this evolving landscape, consider the potential of innovative designs and materials to differentiate your offerings. Embrace the opportunities that strategic sourcing presents to position your business at the forefront of the custom t-shirt market. Now is the time to take action—explore new partnerships and elevate your sourcing strategy to achieve sustainable growth and success.