Discover Top Tips to Choose an Alloy Manufacturer (2025)
Introduction: Navigating the Global Market for alloy manufacturer
Navigating the complexities of the global market for alloy manufacturers can be daunting for international B2B buyers, especially when trying to source high-quality materials that meet specific industry standards. With the increasing demand for customized alloys across various sectors—from automotive to aerospace—the ability to identify reliable suppliers and make informed purchasing decisions is crucial. This guide serves as a comprehensive resource, covering essential aspects such as types of alloys, their applications, effective supplier vetting processes, and cost considerations.
International buyers, particularly from regions like Africa, South America, the Middle East, and Europe—including key markets such as Italy and Indonesia—face unique challenges in sourcing alloys that align with their operational needs and compliance requirements. By providing actionable insights and best practices, this guide empowers you to streamline your procurement process, mitigate risks, and enhance the quality of your supply chain.
Whether you are looking to understand the nuances of different alloy compositions or seeking strategies for negotiating favorable terms with manufacturers, this guide will equip you with the knowledge and tools necessary to navigate the global landscape effectively. Embrace the opportunity to make informed choices that drive your business forward in the competitive alloy market.
Understanding alloy manufacturer Types and Variations
Type Name | Key Distinguishing Features | Primary B2B Applications | Brief Pros & Cons for Buyers |
---|---|---|---|
Ferrous Alloy Manufacturers | Focus on iron-based alloys; common in construction and automotive | Structural components, machinery, automotive | Pros: High strength, cost-effective. Cons: Susceptible to corrosion. |
Non-Ferrous Alloy Manufacturers | Specialize in non-iron metals like aluminum, copper, and titanium | Aerospace, electronics, automotive parts | Pros: Lightweight, corrosion-resistant. Cons: Generally more expensive. |
Specialty Alloy Manufacturers | Produce custom alloys for specific applications; often high-performance | Aerospace, medical devices, specialized machinery | Pros: Tailored solutions, high performance. Cons: Higher costs, longer lead times. |
Superalloy Manufacturers | Focus on high-temperature and corrosion-resistant alloys | Aerospace, energy, chemical processing | Pros: Exceptional durability, performance under extreme conditions. Cons: Very high cost, specialized sourcing. |
Tool Steel Manufacturers | Produce alloys specifically designed for tools and dies | Tooling, manufacturing, construction | Pros: High hardness, wear resistance. Cons: Brittle, can be expensive. |
What Are the Key Characteristics of Ferrous Alloy Manufacturers?
Ferrous alloy manufacturers primarily focus on iron-based alloys, which include steel and cast iron. These materials are widely used in construction and automotive industries due to their strength and durability. When purchasing from ferrous alloy manufacturers, B2B buyers should consider factors such as corrosion resistance, especially for applications in harsh environments. Additionally, understanding the specific grades and compositions available can help ensure suitability for particular projects.
How Do Non-Ferrous Alloy Manufacturers Differ?
Non-ferrous alloy manufacturers specialize in alloys that do not contain iron, such as aluminum, copper, and titanium. These materials are essential in industries like aerospace and electronics, where lightweight and corrosion-resistant properties are crucial. Buyers should evaluate the specific applications for which these alloys are intended, as well as their mechanical properties, to ensure compatibility with their needs. Cost considerations also play a significant role, as non-ferrous alloys tend to be more expensive than their ferrous counterparts.
What Sets Specialty Alloy Manufacturers Apart?
Specialty alloy manufacturers create custom alloys tailored to meet specific performance requirements, making them invaluable in high-stakes industries such as aerospace and medical devices. When engaging with these manufacturers, B2B buyers should assess the manufacturer’s ability to meet unique specifications and their expertise in developing high-performance materials. While these custom solutions often come at a premium, the investment can yield significant benefits in terms of performance and reliability.
Why Choose Superalloy Manufacturers?
Superalloy manufacturers focus on producing alloys that can withstand extreme temperatures and corrosive environments, making them ideal for aerospace and energy sectors. Buyers should consider the specific thermal and chemical resistance properties of the alloys offered. Although superalloys are typically more expensive due to their specialized nature, their exceptional durability can lead to lower maintenance costs and longer service life in critical applications.
What Are the Benefits of Tool Steel Manufacturers?
Tool steel manufacturers provide high-performance alloys specifically designed for tooling and manufacturing applications. These steels are known for their hardness and wear resistance, making them suitable for cutting tools and dies. B2B buyers should consider the specific grades of tool steel available and their suitability for the intended application. While tool steels can be more brittle and costly, their performance in demanding environments often justifies the investment.
Related Video: Steel & Its Types | Alloy Steel, Carbon Steel, Mild Steel & Stainless Steel
Key Industrial Applications of alloy manufacturer
Industry/Sector | Specific Application of Alloy Manufacturer | Value/Benefit for the Business | Key Sourcing Considerations for this Application |
---|---|---|---|
Aerospace | Production of lightweight, high-strength components | Improved fuel efficiency and performance | Certifications (e.g., AS9100), sourcing from compliant suppliers |
Automotive | Manufacturing of engine and transmission parts | Enhanced durability and reduced weight | Quality assurance, compliance with international standards |
Construction | Creation of structural components and reinforcement materials | Increased safety and longevity of structures | Local regulations, availability of materials in required grades |
Electronics | Production of heat sinks and conductive materials | Better thermal management and energy efficiency | Precision in specifications, reliability of supply chain |
Oil & Gas | Fabrication of pipelines and drilling equipment | Resistance to corrosion and extreme conditions | Material certifications, compatibility with local environmental standards |
How Are Alloys Used in Aerospace Applications?
In the aerospace industry, alloy manufacturers produce lightweight and high-strength components crucial for aircraft and spacecraft. These alloys, often made from aluminum, titanium, and nickel, help reduce overall weight, leading to improved fuel efficiency and performance. International B2B buyers should prioritize suppliers with certifications like AS9100, ensuring adherence to stringent quality and safety standards. Additionally, sourcing from manufacturers experienced in aerospace applications can mitigate risks associated with compliance and performance.
What Role Do Alloys Play in Automotive Manufacturing?
The automotive sector relies heavily on alloy manufacturers for the production of engine and transmission parts. Alloys such as aluminum and magnesium are favored for their durability and reduced weight, contributing to better fuel economy and vehicle performance. Buyers from regions like Africa and South America should consider suppliers who offer robust quality assurance processes and comply with international automotive standards. This ensures that the components not only meet performance expectations but also enhance vehicle safety.
How Are Alloys Utilized in Construction?
In construction, alloy manufacturers provide essential materials for structural components and reinforcement materials. Alloys like steel and aluminum are used for beams, columns, and other structural elements, ensuring safety and longevity. For international buyers, particularly in developing regions, it’s vital to understand local regulations and standards for construction materials. Suppliers should demonstrate a proven track record of reliability and the ability to deliver materials in the required grades to meet project specifications.
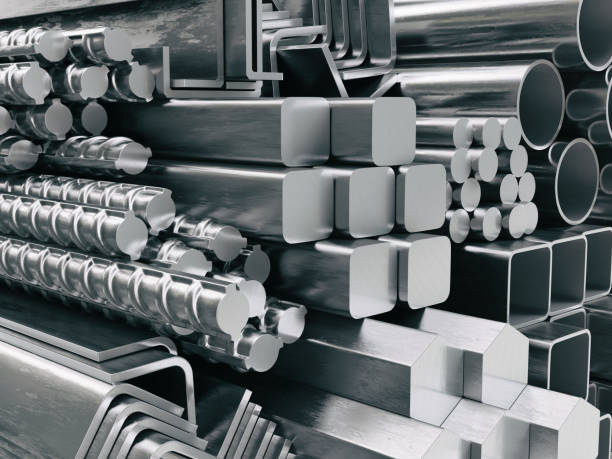
A stock image related to alloy manufacturer.
Why Are Alloys Important in Electronics?
Alloy manufacturers play a significant role in the electronics industry by producing heat sinks and conductive materials that enhance thermal management and energy efficiency. Alloys such as copper and aluminum are essential for effective heat dissipation in electronic devices. Buyers, especially from Europe and the Middle East, must ensure that their suppliers can meet precise specifications and maintain a reliable supply chain. This guarantees that the materials used will perform optimally in high-tech applications.
How Do Alloys Benefit the Oil & Gas Industry?
In the oil and gas sector, alloy manufacturers fabricate pipelines and drilling equipment using materials designed to withstand extreme conditions and resist corrosion. Alloys like stainless steel and high-strength low-alloy steel are commonly utilized for their durability. For international buyers, especially in regions with harsh environments, sourcing from manufacturers that provide material certifications and demonstrate compatibility with local environmental standards is crucial. This ensures that the equipment remains operational under challenging conditions, minimizing downtime and maintenance costs.
Related Video: Types of steel, Steel types, Carbon steel, Alloy steel, Tool steel
3 Common User Pain Points for ‘alloy manufacturer’ & Their Solutions
Scenario 1: Difficulty in Finding Reliable Alloy Manufacturers
The Problem:
B2B buyers often struggle to find trustworthy alloy manufacturers who can deliver consistent quality. This challenge is exacerbated for buyers in regions like Africa and South America, where local suppliers may lack the necessary certifications or quality standards. Buyers may have experienced delays in delivery, subpar materials, or even outright fraud from less reputable manufacturers, leading to project setbacks and financial losses.
The Solution:
To effectively source reliable alloy manufacturers, buyers should start by conducting thorough research online and leveraging platforms such as industry directories and trade associations. Look for manufacturers with ISO certifications or other quality assurance standards, as these are indicators of reliability. Additionally, consider visiting the manufacturer’s facilities if possible, or arrange for third-party inspections before placing a large order. Establishing clear communication regarding specifications, delivery timelines, and quality expectations at the outset can significantly mitigate risks.
Scenario 2: Inadequate Technical Support and Guidance
The Problem:
Many B2B buyers face challenges when it comes to understanding the technical specifications of alloys, which can lead to improper usage in their applications. For instance, a manufacturer in the Middle East may require specific alloy compositions for high-temperature applications but may not receive the necessary guidance from their supplier. This lack of technical support can result in product failures, increased costs, and wasted time.
The Solution:
Buyers should prioritize working with alloy manufacturers who offer comprehensive technical support and consultation services. When engaging with potential suppliers, inquire about their engineering and technical teams, and ask for case studies or examples where they have provided successful solutions to similar challenges. Additionally, request detailed documentation on alloy compositions, mechanical properties, and application guidelines. A collaborative approach, where the buyer shares their application needs and the supplier provides tailored recommendations, can lead to successful outcomes and enhanced product performance.
Scenario 3: Supply Chain Disruptions and Unpredictable Lead Times
The Problem:
Supply chain issues are a significant concern for B2B buyers, particularly in today’s global marketplace. Buyers from Europe and other regions may find that unexpected disruptions, such as geopolitical tensions or natural disasters, can lead to unpredictable lead times for alloy deliveries. This unpredictability can cause project delays and financial repercussions, making it crucial for buyers to have a reliable supply chain.
The Solution:
To mitigate supply chain risks, buyers should diversify their supplier base by establishing relationships with multiple alloy manufacturers across different regions. This strategy not only provides alternatives in case one supplier faces disruptions but also fosters competitive pricing and better negotiation power. Additionally, implementing a robust inventory management system can help track lead times and manage stock levels effectively. Regular communication with suppliers regarding inventory and demand forecasts can also enhance responsiveness to changing market conditions, ensuring that projects remain on schedule.
Strategic Material Selection Guide for alloy manufacturer
What Are the Key Materials Used in Alloy Manufacturing?
When selecting materials for alloy manufacturing, international B2B buyers must consider various factors that affect product performance, cost, and application suitability. Below are analyses of four common materials used in alloy manufacturing, focusing on their properties, advantages, disadvantages, and specific considerations for buyers from Africa, South America, the Middle East, and Europe.
How Do Aluminum Alloys Perform in Various Applications?
Key Properties: Aluminum alloys are known for their lightweight nature, excellent corrosion resistance, and good thermal and electrical conductivity. They typically have a temperature rating of up to 600°F (316°C) and can withstand moderate pressure.
Pros & Cons: The primary advantage of aluminum alloys is their high strength-to-weight ratio, making them ideal for aerospace and automotive applications. However, they can be more expensive than other materials and may require specialized manufacturing techniques, which can complicate production processes.
Impact on Application: Aluminum alloys are compatible with various media, including water and certain chemicals, but they may not perform well in highly acidic or alkaline environments.
Considerations for International Buyers: Buyers should ensure compliance with international standards such as ASTM and EN specifications. In regions like Africa and South America, where infrastructure varies, sourcing aluminum alloys that meet local regulations is crucial.
What Are the Benefits of Copper Alloys in Manufacturing?
Key Properties: Copper alloys exhibit excellent electrical and thermal conductivity, with a temperature rating of around 400°F (204°C). They also demonstrate good corrosion resistance, particularly in marine environments.
Pros & Cons: The key advantage of copper alloys is their superior conductivity, making them ideal for electrical applications. However, they are generally heavier than aluminum alloys and can be more expensive, which may limit their use in cost-sensitive projects.
Impact on Application: Copper alloys are particularly suited for applications involving electrical components, plumbing, and heat exchangers. Their compatibility with various media, including water and gases, enhances their versatility.
Considerations for International Buyers: Buyers should be aware of the varying standards for copper alloys across regions. Compliance with standards like ASTM B271 and ISO 9001 is essential, especially in Europe, where quality assurance is stringent.
How Do Stainless Steel Alloys Compare in Terms of Durability?
Key Properties: Stainless steel alloys are renowned for their exceptional strength and corrosion resistance, with temperature ratings exceeding 1500°F (815°C). They are suitable for high-pressure applications.
Pros & Cons: The durability of stainless steel alloys makes them ideal for harsh environments, including chemical processing and oil and gas applications. However, they can be more challenging to machine and weld, increasing manufacturing complexity and cost.
Impact on Application: Stainless steel alloys are compatible with a wide range of media, including corrosive substances, making them suitable for food and pharmaceutical industries.
Considerations for International Buyers: Compliance with international standards such as ASTM A240 and EN 10088 is vital. Buyers from the Middle East and Europe should also consider the specific grades required for their applications, as local preferences may vary.
What Role Do Titanium Alloys Play in High-Performance Applications?
Key Properties: Titanium alloys offer an impressive strength-to-weight ratio and excellent corrosion resistance, with temperature ratings up to 1200°F (649°C). They are also biocompatible, making them suitable for medical applications.
Pros & Cons: The primary advantage of titanium alloys is their ability to perform under extreme conditions while maintaining low weight. However, they are among the most expensive materials and can be difficult to machine, which may deter some manufacturers.
Impact on Application: Titanium alloys are ideal for aerospace, military, and medical applications due to their strength and corrosion resistance. They are compatible with various media, including seawater and aggressive chemicals.
Considerations for International Buyers: Buyers should ensure compliance with ASTM B265 and ISO 5832 for titanium alloys. In regions like Africa and South America, understanding local market dynamics and availability is crucial for procurement.
Summary Table of Common Materials for Alloy Manufacturing
Material | Typical Use Case for alloy manufacturer | Key Advantage | Key Disadvantage/Limitation | Relative Cost (Low/Med/High) |
---|---|---|---|---|
Aluminum Alloys | Aerospace and automotive components | High strength-to-weight ratio | Higher cost and manufacturing complexity | Medium |
Copper Alloys | Electrical components and plumbing | Superior electrical conductivity | Heavier and potentially more expensive | Medium |
Stainless Steel | Chemical processing and oil & gas | Exceptional strength and corrosion resistance | Difficult to machine and weld | High |
Titanium Alloys | Aerospace and medical applications | Performs well under extreme conditions | Very high cost and machining difficulty | High |
This strategic material selection guide aims to equip international B2B buyers with the necessary insights to make informed decisions regarding alloy materials, ensuring compliance and suitability for their specific applications.
In-depth Look: Manufacturing Processes and Quality Assurance for alloy manufacturer
What Are the Key Stages of Manufacturing Processes for Alloy Manufacturers?
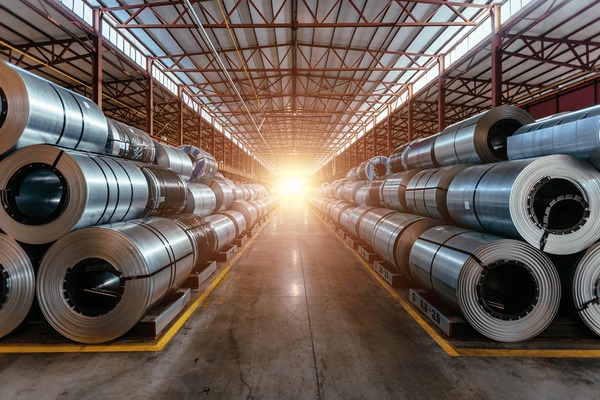
A stock image related to alloy manufacturer.
The manufacturing process of alloys involves several critical stages, each contributing to the final product’s quality and performance. Understanding these stages can help international B2B buyers assess potential suppliers effectively.
1. Material Preparation
The first step in alloy manufacturing is the preparation of raw materials, which often includes metals such as aluminum, copper, nickel, and others. This stage involves:
- Material Selection: Choosing the right type of metal based on the desired properties of the final alloy. For example, aluminum alloys might be selected for lightweight applications, while steel alloys could be chosen for strength.
- Pre-treatment: Raw materials may undergo cleaning or pre-treatment processes to remove impurities and ensure optimal bonding during the alloying process.
2. Forming Techniques
Once the materials are prepared, the next step is forming, where raw metals are shaped into the desired forms. Key techniques include:
- Casting: Molten metal is poured into molds to create specific shapes. This technique is widely used for complex geometries and large components.
- Forging: This involves shaping metal using compressive forces, often resulting in stronger materials due to grain refinement.
- Extrusion: Metal is forced through a die to produce long shapes with uniform cross-sections, commonly used for profiles and tubes.
3. Assembly Processes
For alloys that require multiple components, the assembly process becomes crucial. Techniques include:
- Welding: Joining metal parts using heat to melt the edges together, ensuring a strong bond.
- Machining: Precision cutting or shaping of metal components to meet specific dimensions and tolerances.
4. Finishing Techniques
Finishing processes enhance the alloy’s appearance and performance. Common methods include:
- Surface Treatment: Techniques such as anodizing or galvanizing can improve corrosion resistance and aesthetic appeal.
- Heat Treatment: Controlled heating and cooling processes can alter the physical properties of the alloy, enhancing strength or ductility.
How Do Quality Assurance Practices Impact Alloy Manufacturing?
Quality assurance (QA) is integral to the alloy manufacturing process, ensuring that the final products meet international standards and customer specifications.
Relevant International Standards for Alloy Manufacturers
To maintain high-quality output, alloy manufacturers often adhere to various international standards, including:
- ISO 9001: This standard focuses on quality management systems, emphasizing customer satisfaction and continuous improvement.
- CE Marking: Particularly relevant for European markets, CE marking indicates compliance with health, safety, and environmental protection standards.
- API Standards: For manufacturers supplying the oil and gas sector, adherence to API (American Petroleum Institute) standards is critical for safety and reliability.
What Are the Key Quality Control Checkpoints in Alloy Manufacturing?
Quality control (QC) involves systematic checks at different stages of production to ensure compliance with standards. Key checkpoints include:
- Incoming Quality Control (IQC): This initial stage involves inspecting raw materials for defects before production begins. Buyers should ensure that suppliers have rigorous IQC processes to avoid issues later in the manufacturing cycle.
- In-Process Quality Control (IPQC): Continuous monitoring during production helps detect issues early. This could include real-time testing of material properties and dimensions.
- Final Quality Control (FQC): This stage involves a thorough inspection of the finished product against specifications. Common tests performed during FQC include tensile strength testing, chemical composition analysis, and surface finish evaluation.
How Can B2B Buyers Verify Quality Control Practices of Alloy Manufacturers?
International B2B buyers need to ensure that their suppliers maintain high-quality standards. Here are actionable insights for verifying QC practices:
Conducting Supplier Audits
Regular audits of suppliers can provide a clear picture of their manufacturing and quality assurance processes. During an audit, buyers should check for:
- Compliance with ISO and other relevant standards.
- Documentation of QC processes and results.
- Evidence of ongoing training and certification of staff involved in quality assurance.
Requesting Quality Reports and Certificates
Buyers should request detailed quality reports from suppliers, including results from IQC, IPQC, and FQC checkpoints. Certificates of compliance with international standards (like ISO 9001 or CE) should also be requested to confirm adherence to quality practices.
Engaging Third-Party Inspection Services
For additional assurance, B2B buyers can engage third-party inspection services to conduct independent evaluations of the supplier’s manufacturing and QC processes. These inspections can provide unbiased insights into the supplier’s capabilities and adherence to quality standards.
What Are the QC and Certification Nuances for International B2B Buyers?
When sourcing alloys internationally, particularly from diverse regions like Africa, South America, the Middle East, and Europe, buyers must navigate various certification nuances:
- Regional Standards: Different regions may have specific standards and certifications that must be met. For instance, European buyers might prioritize CE marking, while those in the Middle East may focus on local certifications.
- Cultural and Regulatory Differences: Understanding the regulatory landscape in different countries can impact the selection process. Buyers should familiarize themselves with local laws and practices to avoid compliance issues.
Conclusion
International B2B buyers seeking alloy manufacturers must understand the intricacies of manufacturing processes and quality assurance practices. By focusing on material preparation, forming techniques, and robust quality control measures, buyers can select suppliers that meet their specific needs and standards. Engaging in thorough audits, requesting quality documentation, and understanding regional certification nuances will further empower buyers to make informed sourcing decisions.
Practical Sourcing Guide: A Step-by-Step Checklist for ‘alloy manufacturer’
In today’s competitive landscape, sourcing from an alloy manufacturer requires a strategic approach. This guide provides a comprehensive checklist to help international B2B buyers, particularly from Africa, South America, the Middle East, and Europe, navigate the complexities of procurement effectively.
Step 1: Define Your Technical Specifications
Clearly outline the specific alloy types, compositions, and properties you require for your projects. This clarity will aid in communicating your needs effectively to potential suppliers. Make sure to include:
– Mechanical properties (e.g., tensile strength, corrosion resistance)
– Alloy grades that meet industry standards relevant to your sector
Step 2: Research Potential Suppliers
Conduct thorough research to identify potential alloy manufacturers that align with your requirements. Utilize industry directories, trade shows, and online platforms to gather a list of candidates. Pay attention to:
– Supplier reputation and reviews from other businesses
– Geographical location to assess logistics and shipping costs
Step 3: Evaluate Supplier Certifications
Before moving forward, verify that suppliers have the necessary certifications and quality assurance processes in place. Certifications such as ISO 9001 or specific industry-related standards indicate a commitment to quality. Look for:
– Quality management systems that ensure consistent production
– Environmental and safety certifications to align with your sustainability goals
Step 4: Request Samples for Testing
Once you have shortlisted potential suppliers, request samples of the alloys you intend to purchase. Testing these samples will allow you to assess whether they meet your technical specifications and quality expectations. Consider:
– Conducting rigorous testing to confirm performance characteristics
– Comparing samples from multiple suppliers for quality assurance
Step 5: Negotiate Terms and Pricing
Engage in negotiations to establish favorable terms that reflect your purchasing power and the market conditions. Ensure you discuss not only pricing but also:
– Payment terms and conditions
– Delivery timelines and logistics arrangements
Step 6: Assess Supply Chain Reliability
Evaluate the potential supplier’s supply chain capabilities to ensure they can meet your demand consistently. Factors to consider include:
– Production capacity to handle your order volumes
– Flexibility in scaling production during peak times
Step 7: Establish a Communication Plan
Once you select a supplier, establish a clear communication plan to facilitate ongoing dialogue. Regular updates and feedback loops can help in resolving any issues promptly. Key elements include:
– Designating points of contact for both parties
– Setting regular check-in meetings to discuss progress and any concerns
This step-by-step checklist is designed to streamline your sourcing process and ensure that you partner with an alloy manufacturer that meets your specific needs, ultimately contributing to your business’s success.
Comprehensive Cost and Pricing Analysis for alloy manufacturer Sourcing
What Are the Key Cost Components in Alloy Manufacturing?
When sourcing from alloy manufacturers, understanding the breakdown of costs is crucial for effective budgeting and negotiation. The primary cost components include:
-
Materials: The price of raw materials, such as metals and alloys, significantly influences the overall cost. Fluctuations in global commodity prices can affect your sourcing budget, making it essential to stay updated on market trends.
-
Labor: Labor costs, which encompass wages, benefits, and training, vary by region. For instance, sourcing from countries with lower labor costs may yield savings, but it’s essential to assess the skill level and productivity of the workforce.
-
Manufacturing Overhead: This includes indirect costs such as utilities, facility maintenance, and administrative expenses. Efficient production processes can help minimize these costs, impacting the final pricing.
-
Tooling: The cost of tooling can be substantial, especially for custom parts. This expense can vary based on the complexity of the tooling required and whether the manufacturer already has the necessary equipment.
-
Quality Control (QC): Implementing strict quality control measures ensures that products meet industry standards. While this adds to the cost, it can prevent costly recalls and reputational damage.
-
Logistics: Shipping and handling costs, including freight, insurance, and customs duties, must be factored into your total cost. These costs can vary significantly based on the distance from the manufacturer and the shipping method chosen.
-
Margin: Manufacturers typically include a profit margin in their pricing, which can vary based on market demand and competition. Understanding this margin can help you gauge the overall pricing strategy.
How Do Pricing Influencers Affect Alloy Manufacturing Costs?
Several factors can influence the pricing of alloys, particularly for international buyers:
-
Volume and Minimum Order Quantity (MOQ): Larger orders often attract discounts, so understanding the MOQ can help in negotiating better prices.
-
Specifications and Customization: Unique specifications or custom alloys may incur additional costs. Discussing these requirements upfront can prevent unexpected charges later.
-
Material Quality and Certifications: Higher quality materials or those that meet specific certifications (like ISO) can lead to increased prices. However, investing in quality can reduce the Total Cost of Ownership (TCO) by minimizing failures and replacements.
-
Supplier Factors: The reliability and reputation of the supplier can influence pricing. Established manufacturers may charge a premium for their expertise and quality assurance.
-
Incoterms: The shipping terms agreed upon can significantly impact costs. Understanding terms like FOB (Free on Board) or CIF (Cost, Insurance, and Freight) can help in calculating total expenses accurately.
What Are Effective Buyer Tips for Negotiating Alloy Prices?
For international B2B buyers, particularly from Africa, South America, the Middle East, and Europe, effective negotiation strategies can lead to significant savings:
-
Research and Benchmarking: Conduct market research to understand prevailing prices and terms. Comparing multiple suppliers can provide leverage in negotiations.
-
Focus on Total Cost of Ownership (TCO): Evaluate the long-term costs associated with the alloy, including maintenance and potential downtime. This broader perspective can justify higher upfront costs for superior quality.
-
Negotiate Terms: Don’t hesitate to negotiate payment terms, delivery schedules, and bulk purchase discounts. Flexibility in these areas can lead to more favorable pricing.
-
Build Relationships: Establishing a good relationship with suppliers can lead to better pricing and service. Frequent communication and prompt payments can enhance trust and cooperation.
-
Stay Informed on Market Trends: Keeping an eye on the global market for raw materials and alloy prices can help you time your purchases strategically, potentially capitalizing on lower prices.
Conclusion and Disclaimer
Understanding the cost structure and pricing dynamics of alloy manufacturing is essential for international buyers. While indicative prices can guide initial budgeting, always seek detailed quotes and terms from suppliers to ensure accurate financial planning. Prices may vary based on numerous factors, including market conditions and specific requirements, so thorough due diligence is advisable.
Alternatives Analysis: Comparing alloy manufacturer With Other Solutions
Understanding Alternatives to Alloy Manufacturing Solutions
In the realm of materials engineering, alloy manufacturers play a crucial role by producing specialized metal mixtures that enhance performance and durability for various applications. However, B2B buyers often seek alternative solutions that may offer similar benefits while addressing specific business needs such as cost-effectiveness, ease of implementation, and maintenance. This section analyzes several alternatives to traditional alloy manufacturing, providing insight into their respective advantages and drawbacks.
Comparison of Alloy Manufacturer with Alternative Solutions
Comparison Aspect | Alloy Manufacturer | 3D Metal Printing | Metal Injection Molding |
---|---|---|---|
Performance | High strength and durability | Customizable properties | High precision and detail |
Cost | Moderate to high | High initial investment | Lower volume, high setup cost |
Ease of Implementation | Requires specialized equipment | Requires technical expertise | Established process but needs tooling |
Maintenance | Low maintenance | Medium maintenance | Low maintenance |
Best Use Case | Aerospace, automotive | Prototyping, complex geometries | Mass production of small parts |
Analyzing Alternative Solutions: 3D Metal Printing
Pros:
3D metal printing offers unparalleled customization, allowing manufacturers to create complex geometries that are difficult or impossible to achieve with traditional alloy manufacturing. This technology is particularly beneficial for rapid prototyping, enabling quicker iterations and design adjustments without the need for extensive tooling changes.
Cons:
The primary drawback of 3D metal printing is its high initial investment in equipment and materials, which may not be feasible for all businesses, especially those with limited budgets. Furthermore, the speed of production can be slower than traditional methods for high-volume orders, making it less suitable for mass production.
Evaluating Metal Injection Molding
Pros:
Metal injection molding (MIM) is an efficient manufacturing process for producing small, complex parts in large volumes. It combines the flexibility of plastic injection molding with the strength of metals, resulting in high precision and detail. MIM is ideal for applications where tight tolerances and intricate designs are necessary.
Cons:
While MIM can be cost-effective for large production runs, the initial setup costs for tooling and molds can be significant. Additionally, it may not be suitable for low-volume production or rapid design changes, as adjustments to molds can be time-consuming and expensive.
Choosing the Right Solution for Your Business Needs
When selecting between alloy manufacturing and its alternatives, international B2B buyers should carefully assess their specific requirements. Consider factors such as production volume, complexity of design, and budget constraints. For instance, businesses focused on high customization and rapid prototyping might find 3D metal printing advantageous. In contrast, those requiring mass production of small parts with high precision may lean towards metal injection molding. Ultimately, the best choice will depend on aligning the manufacturing process with the strategic goals of the organization.
By understanding the strengths and limitations of each solution, buyers can make informed decisions that optimize both performance and cost-effectiveness in their supply chain.
Essential Technical Properties and Trade Terminology for alloy manufacturer
What Are the Essential Technical Properties of Alloys for B2B Buyers?
Understanding the technical properties of alloys is vital for B2B buyers in making informed purchasing decisions. Here are some critical specifications to consider:
1. Material Grade
Material grade refers to the classification of an alloy based on its chemical composition and mechanical properties. Different industries require specific grades to ensure performance under various conditions. For instance, aerospace applications often demand high-strength aluminum alloys, while automotive applications may prioritize lightweight steel alloys. Choosing the correct material grade can significantly impact the durability and safety of the final product.
2. Tolerance
Tolerance indicates the allowable deviation in dimensions for manufactured parts. In the alloy manufacturing process, precise tolerances are crucial to ensure parts fit together correctly and function as intended. Tighter tolerances often lead to higher production costs but are essential in applications where precision is paramount, such as in medical devices or aerospace components.
3. Yield Strength
Yield strength is the maximum stress that an alloy can withstand without undergoing permanent deformation. This property is particularly important for industries that require materials to bear heavy loads or resist environmental stressors. A higher yield strength means a more robust and reliable product, which can be a decisive factor for buyers in construction or heavy machinery sectors.
4. Corrosion Resistance
Corrosion resistance is the ability of an alloy to withstand degradation due to environmental factors such as moisture, chemicals, and temperature variations. Alloys with high corrosion resistance are crucial for applications in marine environments or chemical processing. Buyers must assess the environmental conditions their products will face and select alloys that offer appropriate protection.
5. Thermal Conductivity
Thermal conductivity measures how well an alloy can conduct heat. This property is particularly relevant for industries involved in heat exchangers, electronic components, and automotive applications where heat dissipation is critical. Buyers should consider thermal conductivity when selecting materials to ensure optimal performance in temperature-sensitive environments.
What Are Common Trade Terms Used in the Alloy Manufacturing Industry?
Familiarizing yourself with industry jargon can facilitate smoother transactions and negotiations. Here are several key terms:
1. OEM (Original Equipment Manufacturer)
An OEM is a company that produces parts or equipment that may be marketed by another manufacturer. For alloy manufacturers, understanding OEM relationships is crucial for aligning production capabilities with client needs. Buyers should consider whether the supplier can meet OEM standards for quality and consistency.
2. MOQ (Minimum Order Quantity)
MOQ refers to the smallest quantity of a product that a supplier is willing to sell. This term is significant for B2B buyers as it can affect inventory management and cash flow. Understanding the MOQ can help buyers negotiate better terms and avoid excess inventory costs.
3. RFQ (Request for Quotation)
An RFQ is a formal document issued by a buyer to solicit price quotes from suppliers for specific products or services. This process allows buyers to compare prices, specifications, and delivery times, ensuring they make the best decision based on their project requirements.
4. Incoterms (International Commercial Terms)
Incoterms are a set of predefined commercial terms published by the International Chamber of Commerce (ICC) that define the responsibilities of buyers and sellers in international transactions. Familiarity with Incoterms is essential for B2B buyers to understand shipping responsibilities, risk management, and cost implications associated with their purchases.
5. Lead Time
Lead time refers to the amount of time it takes from placing an order to receiving the goods. For alloy manufacturers, understanding lead times is vital for planning production schedules and managing client expectations. Buyers should inquire about lead times to ensure they can meet their project deadlines.
By grasping these essential properties and trade terms, international B2B buyers can make more informed decisions when sourcing alloys, ultimately improving their supply chain efficiency and product quality.
Navigating Market Dynamics and Sourcing Trends in the alloy manufacturer Sector
What Are the Key Market Dynamics and Trends Influencing the Alloy Manufacturing Sector?
The alloy manufacturing sector is experiencing significant transformations driven by globalization, technological advancements, and changing buyer preferences. International B2B buyers from regions such as Africa, South America, the Middle East, and Europe are increasingly seeking diverse alloy solutions that meet specific performance criteria. The demand for lightweight and high-strength materials is rising, particularly in the automotive and aerospace industries, prompting manufacturers to innovate their alloy compositions and production processes.
Emerging technologies, including additive manufacturing and artificial intelligence, are reshaping sourcing strategies. Additive manufacturing allows for the production of complex alloy geometries, reducing waste and enhancing design flexibility. Meanwhile, AI-driven analytics can optimize supply chain logistics, enabling buyers to make informed decisions based on real-time data. Buyers should focus on suppliers who leverage these technologies to ensure they are receiving cutting-edge products that align with their operational needs.
Additionally, geopolitical factors and trade policies play a crucial role in shaping market dynamics. For instance, tariffs and trade agreements can impact alloy prices and availability. B2B buyers should stay informed about these developments to navigate potential disruptions and secure favorable sourcing arrangements.
How Can Sustainability and Ethical Sourcing Impact Your Alloy Supply Chain?
Sustainability has become a cornerstone of sourcing strategies in the alloy manufacturing sector. The environmental impact of alloy production, including resource extraction and energy consumption, is under scrutiny. International buyers are increasingly prioritizing suppliers who demonstrate commitment to sustainable practices, such as reducing carbon footprints and utilizing renewable energy sources in their manufacturing processes.
Ethical sourcing is equally important, particularly in regions where labor practices may vary. Buyers should seek out manufacturers who maintain transparency in their supply chains, ensuring fair labor conditions and responsible sourcing of raw materials. Certifications like ISO 14001 for environmental management and SA8000 for social accountability can serve as indicators of a supplier’s commitment to ethical practices.
Moreover, the use of recycled materials in alloy production is gaining traction. Recycled alloys not only reduce waste but also lower the overall environmental impact of manufacturing. Buyers should inquire about suppliers’ recycling policies and the percentage of recycled content in their products to align with sustainability goals.
What Is the Historical Context Behind Alloy Manufacturing?
The evolution of alloy manufacturing dates back thousands of years, with the earliest alloys being bronze and brass, which revolutionized tool-making and construction. The Industrial Revolution marked a significant turning point, as advancements in metallurgy and production techniques led to the widespread use of alloys in various applications, from machinery to transportation.
In the latter half of the 20th century, the introduction of high-performance alloys, such as titanium and nickel-based superalloys, began to dominate industries that required enhanced material properties. This shift was driven by the aerospace and automotive sectors, which demanded lightweight yet durable materials for improved efficiency and performance.
Today, the alloy manufacturing sector continues to evolve, fueled by ongoing research and development efforts. Innovations in alloy compositions and manufacturing techniques are enabling new applications and expanding market opportunities for international B2B buyers. Understanding this historical context can provide valuable insights into current sourcing trends and technological advancements shaping the industry.
Frequently Asked Questions (FAQs) for B2B Buyers of alloy manufacturer
- How do I choose the right alloy manufacturer for my business needs?
Selecting the appropriate alloy manufacturer involves assessing their specialization in the type of alloys you require, such as aluminum, titanium, or specialty alloys. Research their manufacturing capabilities, certifications, and past client reviews to gauge their reliability. It’s also beneficial to inquire about their experience with international shipping and compliance with regional regulations, especially if you’re sourcing from Africa, South America, the Middle East, or Europe.
-
What are the most important factors to consider when vetting an alloy supplier?
Key factors include the supplier’s production capacity, quality assurance processes, and compliance with international standards. Request samples to evaluate their product quality and ask about their certifications, such as ISO 9001. Additionally, assess their financial stability and history in international trade to ensure they can meet your order demands consistently and reliably. -
What customization options are available when sourcing alloys?
Many alloy manufacturers offer customization options to meet specific requirements, such as varying compositions, dimensions, and finishes. It’s essential to communicate your specifications clearly and ask about their capabilities to produce tailored alloys. Consider discussing lead times for custom orders, as these can vary significantly based on the complexity of your requirements. -
What is the minimum order quantity (MOQ) for alloy products?
MOQs can vary widely among alloy manufacturers depending on the type of alloy and production processes. Some manufacturers may have a low MOQ for standard products, while custom alloys may require larger quantities to justify production costs. Always clarify MOQ during negotiations to ensure it aligns with your purchasing strategy. -
What payment terms should I expect when dealing with international alloy suppliers?
Payment terms typically range from upfront payments to net 30 or net 60 days, depending on the supplier’s policy and your business relationship. It’s advisable to negotiate terms that protect both parties, such as letter of credit (LC) arrangements or escrow services for larger transactions. Always clarify payment methods accepted, including wire transfers or credit terms. -
How do I ensure quality assurance in alloy manufacturing?
To ensure quality assurance, request information on the manufacturer’s quality control processes, including testing methods and certifications. Look for suppliers that conduct third-party inspections and provide material test reports. Establishing a quality agreement that outlines standards and expectations can also help mitigate risks related to product quality. -
What logistics considerations should I keep in mind when importing alloys?
Logistics for importing alloys involve understanding shipping methods, customs clearance, and potential tariffs. Work closely with your supplier to ensure they provide necessary documentation for customs and consider using freight forwarders experienced in handling metal products. Be aware of lead times and any potential delays due to regulatory inspections in your country. -
How can I build a long-term relationship with my alloy supplier?
Building a long-term relationship involves consistent communication and mutual trust. Regularly provide feedback on product quality and delivery performance, and be open to discussing potential improvements. Consider entering into long-term contracts or partnership agreements that benefit both parties, fostering loyalty and reliability in your supply chain.
Important Disclaimer & Terms of Use
⚠️ Important Disclaimer
The information provided in this guide, including content regarding manufacturers, technical specifications, and market analysis, is for informational and educational purposes only. It does not constitute professional procurement advice, financial advice, or legal advice.
While we have made every effort to ensure the accuracy and timeliness of the information, we are not responsible for any errors, omissions, or outdated information. Market conditions, company details, and technical standards are subject to change.
B2B buyers must conduct their own independent and thorough due diligence before making any purchasing decisions. This includes contacting suppliers directly, verifying certifications, requesting samples, and seeking professional consultation. The risk of relying on any information in this guide is borne solely by the reader.
Strategic Sourcing Conclusion and Outlook for alloy manufacturer
What Are the Key Takeaways for B2B Buyers in Alloy Manufacturing?
Strategic sourcing is pivotal in enhancing the efficiency and competitiveness of alloy manufacturers. As international B2B buyers, particularly from regions like Africa, South America, the Middle East, and Europe, understanding the nuances of sourcing can significantly impact your supply chain and cost management. Prioritizing quality, compliance with international standards, and sustainability can lead to long-term partnerships with alloy manufacturers that align with your business goals.
How Can You Leverage Strategic Sourcing for Competitive Advantage?
By engaging in strategic sourcing, buyers can not only secure better pricing but also foster innovation through collaboration with suppliers. This approach enables access to cutting-edge technologies and materials that are essential in today’s fast-paced market. Additionally, focusing on suppliers who demonstrate ethical practices and sustainability can enhance your brand reputation and appeal to environmentally conscious consumers.
What Should Your Next Steps Be?
As you navigate the complex landscape of alloy manufacturing, consider establishing strong relationships with reliable suppliers. Evaluate potential partners based on their capabilities, certifications, and commitment to quality. By doing so, you can position your business for success and resilience in an increasingly competitive global market. Embrace the opportunity to innovate and grow—your strategic sourcing journey begins now.