Unlock Quality & Cost Savings with Cutting Board Custom (2025)
Introduction: Navigating the Global Market for cutting board custom
In today’s global marketplace, sourcing custom cutting boards presents a unique challenge for B2B buyers, especially those operating in diverse regions such as Africa, South America, the Middle East, and Europe. With varying standards and preferences across these markets, international buyers must navigate complexities related to quality, material selection, and supplier reliability. This guide aims to empower you with actionable insights into the world of custom cutting boards, detailing various types, applications, and essential factors to consider when selecting suppliers.
Understanding the different styles and materials available—ranging from wood and bamboo to plastic and composite options—will enable you to make informed choices that align with your business needs. Furthermore, we delve into the crucial aspect of vetting suppliers to ensure you partner with those who meet both regulatory standards and quality expectations. Cost analysis is another vital area covered, helping you to balance budget considerations with the need for high-quality products.
By the end of this guide, you will have a comprehensive toolkit for making confident purchasing decisions in the custom cutting board market. Whether you are based in Poland, the UK, or elsewhere, the insights provided will facilitate a smoother procurement process, reducing risk and enhancing your product offerings. Equip yourself with the knowledge needed to thrive in this competitive landscape, ensuring that your sourcing strategy is both effective and efficient.
Understanding cutting board custom Types and Variations
Type Name | Key Distinguishing Features | Primary B2B Applications | Brief Pros & Cons for Buyers |
---|---|---|---|
Wooden Cutting Boards | Made from hardwoods, often handcrafted; durable and aesthetic | Restaurants, catering services | Pros: Natural antibacterial properties, longevity. Cons: Requires maintenance, may warp if not cared for. |
Plastic Cutting Boards | Lightweight, dishwasher safe; available in various colors | Food processing, schools, hospitals | Pros: Easy to clean, affordable. Cons: Less durable, may retain odors. |
Bamboo Cutting Boards | Eco-friendly material, lightweight; often non-slip | Organic food markets, gourmet shops | Pros: Sustainable, attractive design. Cons: Can be prone to scratches, requires care. |
Glass Cutting Boards | Non-porous, hygienic surface; often used for presentation | High-end restaurants, catering events | Pros: Easy to clean, aesthetically pleasing. Cons: Can dull knives, prone to breakage. |
Composite Cutting Boards | Made from recycled materials; combines features of wood and plastic | Commercial kitchens, food service industries | Pros: Durable, resistant to knife marks. Cons: Heavier, can be more expensive. |
What Are the Key Characteristics of Wooden Cutting Boards?
Wooden cutting boards are typically crafted from hardwoods like maple or walnut, offering both durability and aesthetic appeal. These boards are favored in high-end restaurants and catering services due to their natural antibacterial properties and ability to withstand heavy use. When considering a wooden board, buyers should evaluate maintenance needs, as they require regular oiling to prevent warping and cracking.
How Do Plastic Cutting Boards Compare for B2B Use?
Plastic cutting boards are lightweight and available in a variety of colors, making them popular in food processing facilities, schools, and hospitals. They are dishwasher safe, ensuring ease of cleaning and sanitation. However, buyers should consider the potential downsides, such as a shorter lifespan and the possibility of retaining odors. Selecting high-density polyethylene (HDPE) can mitigate some durability issues.
Why Choose Bamboo Cutting Boards for Sustainability?
Bamboo cutting boards are a sustainable option that appeals to eco-conscious businesses, such as organic food markets and gourmet shops. They are lightweight and often feature a non-slip surface, making them user-friendly. While bamboo boards are attractive and environmentally friendly, buyers should keep in mind that they can be prone to scratches and require care to maintain their appearance.
What Are the Benefits of Using Glass Cutting Boards?
Glass cutting boards are non-porous and hygienic, making them ideal for high-end restaurants and catering events where presentation is key. Their easy-to-clean surface is a significant advantage, as they can be sanitized thoroughly. However, buyers must consider that glass boards can dull knives quickly and are more susceptible to breaking, which may not be ideal for all kitchen environments.
How Do Composite Cutting Boards Perform in Commercial Settings?
Composite cutting boards, made from recycled materials, combine the best features of wood and plastic. They are durable and resistant to knife marks, making them suitable for commercial kitchens and food service industries. While they may be heavier and more expensive than other options, their longevity and performance can justify the investment for businesses looking for reliable kitchen tools.
Related Video: Custom Edge Grain Cutting Board – Walnut and Maple
Key Industrial Applications of cutting board custom
Industry/Sector | Specific Application of cutting board custom | Value/Benefit for the Business | Key Sourcing Considerations for this Application |
---|---|---|---|
Food and Beverage | Custom cutting boards for commercial kitchens | Enhanced hygiene and durability; tailored sizes for efficiency | Material quality (bamboo, plastic, wood), compliance with food safety standards |
Healthcare and Pharmaceuticals | Antimicrobial cutting boards for hospitals and labs | Reduces cross-contamination risks, ensuring patient safety | Certifications (FDA, ISO), ease of cleaning, and resistance to chemicals |
Retail and Hospitality | Branded cutting boards for restaurants and food retailers | Strengthens brand identity and customer engagement | Customization options, lead times, and bulk purchasing discounts |
Manufacturing and Production | Heavy-duty cutting boards for industrial applications | Increased productivity and reduced wear on equipment | Thickness, material resilience, and suitability for specific machinery |
Agriculture and Farming | Custom cutting boards for food processing in farms | Streamlined food handling processes and compliance with regulations | Sourcing from local suppliers, sustainability certifications, and material safety |
How Are Custom Cutting Boards Used in the Food and Beverage Industry?
In commercial kitchens, custom cutting boards are essential for food preparation. Their tailored sizes and materials enhance hygiene and durability, allowing chefs to work efficiently while minimizing the risk of cross-contamination. International buyers should consider sourcing boards that meet local food safety standards and regulations, especially when importing to regions like Africa and South America, where compliance may vary.
What Are the Benefits of Antimicrobial Cutting Boards in Healthcare?
In healthcare settings, antimicrobial cutting boards are crucial for preventing cross-contamination. These boards are designed to withstand rigorous cleaning and sterilization processes, ensuring patient safety in hospitals and laboratories. Buyers in the Middle East and Europe should prioritize certifications such as FDA and ISO to ensure the boards meet stringent health regulations.
Why Do Retail and Hospitality Sectors Prefer Branded Cutting Boards?
In the retail and hospitality industries, custom cutting boards serve not only functional purposes but also branding opportunities. Restaurants and food retailers can use these boards to enhance their brand identity and engage customers. B2B buyers should focus on customization options and consider lead times for bulk orders to align with promotional strategies.
How Do Heavy-Duty Cutting Boards Impact Manufacturing Efficiency?
Manufacturers often require heavy-duty cutting boards to withstand the demands of industrial applications. These boards contribute to increased productivity by providing durable surfaces that minimize wear and tear on machinery. Buyers should assess the thickness and material resilience to ensure compatibility with their specific manufacturing processes, especially in Europe, where machinery standards are high.
What Role Do Custom Cutting Boards Play in Agriculture?
In agriculture, custom cutting boards are vital for food processing, helping streamline handling and preparation. They ensure compliance with health regulations, essential for maintaining quality in food supply chains. Buyers in Africa and South America should focus on sourcing boards from local suppliers who prioritize sustainability and material safety to enhance their operational efficiency.
Related Video: Making a 3D end grain cutting board #3
3 Common User Pain Points for ‘cutting board custom’ & Their Solutions
Scenario 1: Navigating Quality Control Challenges in Custom Cutting Boards
The Problem: B2B buyers often encounter significant quality control issues when ordering custom cutting boards. These challenges can arise from inconsistent materials, varying production standards, and lack of clear communication with suppliers. Buyers may receive boards that do not meet their specifications, leading to dissatisfaction from their end customers and potential financial losses.
The Solution: To mitigate these quality control challenges, buyers should establish a detailed specification document that outlines the exact requirements for the custom cutting boards. This document should include material type, thickness, dimensions, finish, and any branding elements. Additionally, conduct thorough research to identify reputable suppliers with a track record of delivering high-quality products. Request samples before placing bulk orders to assess the quality firsthand. Implementing regular quality audits and establishing a feedback loop with suppliers can ensure that the products consistently meet the required standards. Engaging in open communication throughout the production process will also help address any issues proactively.
Scenario 2: Overcoming Lead Time Delays in Custom Orders
The Problem: Lead time delays are a common pain point for B2B buyers looking to purchase custom cutting boards. Suppliers may struggle with production schedules, resulting in longer-than-expected wait times for delivery. This situation can disrupt inventory management and create challenges for businesses that rely on timely stock replenishment, ultimately affecting customer satisfaction.
The Solution: To avoid lead time delays, buyers should select suppliers who offer transparent timelines and can demonstrate their capacity to meet deadlines. It is beneficial to engage in discussions about lead times during the initial negotiations and to incorporate penalties for late deliveries in the contract. Buyers can also consider placing orders well in advance of peak demand periods to buffer against unforeseen delays. Establishing a reliable relationship with a few key suppliers can help in negotiating faster turnaround times and ensure that there is a backup plan in case of delays. Using project management tools to track the order status and maintaining regular check-ins with the supplier can further enhance efficiency.
Scenario 3: Addressing Customization Limitations with Suppliers
The Problem: Many B2B buyers face limitations regarding the customization options offered by suppliers of cutting boards. This can include restrictions on size, shape, engraving options, or material choices. When suppliers cannot meet specific branding or functional requirements, it can lead to frustration and hinder a business’s ability to differentiate its products in the market.
The Solution: To overcome customization limitations, buyers should conduct thorough research on potential suppliers to identify those that specialize in custom solutions. Before engaging with a supplier, it is crucial to clearly outline the desired custom features and understand their capabilities. Buyers should inquire about the design process and request information on any minimum order quantities associated with custom options. Collaborating closely with the supplier during the design phase can also yield innovative solutions that meet the buyer’s needs. Additionally, exploring multiple suppliers or even local artisans who may offer unique customization options can help businesses find the perfect fit for their branding and functional requirements.
Strategic Material Selection Guide for cutting board custom
When selecting materials for custom cutting boards, international B2B buyers must consider several factors that influence product performance, durability, and compliance with regional standards. Below is an analysis of four common materials used in cutting board manufacturing, focusing on their properties, advantages, disadvantages, and specific considerations for buyers from Africa, South America, the Middle East, and Europe.
What Are the Key Properties of Wood for Custom Cutting Boards?
Wood is a traditional material for cutting boards, often chosen for its aesthetic appeal and natural antimicrobial properties. Common types of wood used include maple, walnut, and bamboo.
-
Key Properties: Wood has a moderate temperature resistance and can withstand typical kitchen pressures. It is not prone to corrosion but can absorb moisture if not properly treated.
-
Pros & Cons: Wood cutting boards are durable and can last for years with proper care. They are generally easy to maintain but can be more expensive than synthetic options. However, they may require regular oiling to prevent cracking and warping.
-
Impact on Application: Wood is compatible with a variety of food media, making it suitable for both meats and vegetables. However, it can retain odors and stains if not cleaned properly.
-
Considerations for International Buyers: Buyers should ensure compliance with local food safety standards, such as those outlined by the European Food Safety Authority (EFSA) or the U.S. Food and Drug Administration (FDA). Additionally, sourcing sustainably harvested wood is becoming increasingly important in many markets.
How Does Plastic Compare as a Material for Custom Cutting Boards?
Plastic cutting boards, often made from polyethylene or polypropylene, offer a different set of benefits and drawbacks.
-
Key Properties: Plastic boards are resistant to staining and odors and can withstand high temperatures. They are also non-porous, which helps in preventing bacterial growth.
-
Pros & Cons: These boards are generally less expensive than wood and are dishwasher safe, making them easy to clean. However, they can scratch easily, which may harbor bacteria over time, and they are less durable compared to wood.
-
Impact on Application: Plastic cutting boards are particularly suitable for raw meat and fish, as they can be sanitized easily. However, they may not provide the same aesthetic appeal as wood.
-
Considerations for International Buyers: Buyers should check for compliance with relevant plastic safety standards, such as those from the American National Standards Institute (ANSI) or the British Standards Institution (BSI). Additionally, the environmental impact of plastic waste is a growing concern.
What Are the Benefits of Bamboo as a Cutting Board Material?
Bamboo has gained popularity as an eco-friendly alternative to traditional wood and plastic cutting boards.
-
Key Properties: Bamboo is lightweight, strong, and has natural antibacterial properties. It is resistant to moisture, making it less prone to warping.
-
Pros & Cons: Bamboo cutting boards are generally more affordable than hardwood options and are considered sustainable. However, they can be more prone to cracking if not properly maintained and may dull knives more quickly than other materials.
-
Impact on Application: Bamboo is suitable for various food types but may not be ideal for heavy-duty use due to its potential for cracking.
-
Considerations for International Buyers: Buyers should verify that bamboo products are sourced from sustainable forests and comply with international standards like the Forest Stewardship Council (FSC) certification.
How Does Composite Material Perform for Custom Cutting Boards?
Composite cutting boards, made from a blend of wood fibers and resins, offer a unique alternative.
-
Key Properties: These boards are highly durable, resistant to scratches, and can withstand high temperatures. They are also non-porous, which helps in preventing bacterial growth.
-
Pros & Cons: Composite boards are easy to clean and maintain, and they offer a balance between the aesthetic appeal of wood and the practicality of plastic. However, they can be heavier and more expensive than traditional plastic boards.
-
Impact on Application: Composite materials are versatile and can be used for various food types, providing a good balance of performance and hygiene.
-
Considerations for International Buyers: Buyers should ensure that composite boards meet safety standards such as ASTM or DIN and consider the environmental impact of the resins used in manufacturing.
Summary Table of Material Selection for Custom Cutting Boards
Material | Typical Use Case for cutting board custom | Key Advantage | Key Disadvantage/Limitation | Relative Cost (Low/Med/High) |
---|---|---|---|---|
Wood | General kitchen use | Aesthetic appeal and durability | Requires maintenance | High |
Plastic | Raw meat and fish preparation | Easy to clean and sanitize | Scratches easily | Low |
Bamboo | General kitchen use | Eco-friendly and lightweight | Prone to cracking | Medium |
Composite | Versatile kitchen use | Durable and non-porous | Heavier and costlier | Medium to High |
This analysis provides a comprehensive overview of the materials available for custom cutting boards, helping international B2B buyers make informed decisions based on their specific needs and compliance requirements.
In-depth Look: Manufacturing Processes and Quality Assurance for cutting board custom
What Are the Key Stages in the Manufacturing Process of Custom Cutting Boards?
The manufacturing process for custom cutting boards involves several critical stages, each ensuring that the final product meets quality standards and customer specifications.
1. Material Preparation
The first step in the manufacturing process is selecting the right materials. Common choices include hardwoods like maple, walnut, and cherry, or more affordable options like bamboo and plastic. The selected wood is typically kiln-dried to reduce moisture content, preventing warping and cracking. Suppliers should provide detailed information about the wood origin, sustainability practices, and treatment processes to ensure the material is of high quality.
2. Forming
Once the materials are prepared, the next stage is forming. This involves cutting the wood into the desired sizes and shapes using precision saws or CNC machines. CNC technology allows for intricate designs and patterns, which can be customized according to client specifications. During this stage, manufacturers should focus on minimizing waste and optimizing material usage, which is particularly important for cost-effective production.
3. Assembly
After forming, the pieces are assembled. For multi-piece boards, this involves gluing and clamping the pieces together. The glue used should be food-safe and compliant with international standards to ensure safety for end-users. Proper assembly techniques are crucial to ensure durability and functionality, especially for cutting boards that will be subjected to heavy use.
4. Finishing
The finishing stage involves sanding the surface to achieve a smooth texture and applying finishes that enhance the wood’s appearance while providing protection. Common finishes include mineral oil, beeswax, or specialty food-safe oils. The choice of finish can influence the board’s usability and longevity, making it essential for buyers to specify their preferences.
How Does Quality Assurance Impact the Custom Cutting Board Manufacturing Process?
Quality assurance (QA) is critical in the manufacturing of custom cutting boards, ensuring that products meet both industry standards and customer expectations.
Relevant International Standards for Custom Cutting Boards
International standards like ISO 9001 provide a framework for quality management systems, helping manufacturers ensure consistency in production. For cutting boards, compliance with food safety standards is paramount, especially in regions like Europe, where regulations such as CE marking may apply. Suppliers should be able to demonstrate compliance with these standards through proper certifications.
What Are the Key Quality Control Checkpoints?
Quality control (QC) checkpoints are integrated throughout the manufacturing process. Key checkpoints include:
-
Incoming Quality Control (IQC): This involves inspecting raw materials upon arrival to ensure they meet specified standards.
-
In-Process Quality Control (IPQC): During production, random samples are taken to verify that the manufacturing process adheres to quality standards. This may include checking dimensions, finish quality, and adhesion strength.
-
Final Quality Control (FQC): Before shipment, finished products are inspected for any defects, ensuring they meet the agreed-upon specifications.
What Common Testing Methods Are Used for Custom Cutting Boards?
Several testing methods are employed to ensure the quality and safety of custom cutting boards:
-
Visual Inspection: A thorough visual examination checks for surface defects, color consistency, and proper assembly.
-
Moisture Content Testing: This tests the moisture levels in the wood, ensuring they fall within acceptable limits to prevent warping.
-
Adhesive Bond Strength Testing: This assesses the strength of the glue used, critical for multi-piece boards.
-
Chemical Safety Testing: For compliance with food safety regulations, testing for harmful substances in finishes and materials is essential.
How Can B2B Buyers Verify Supplier Quality Control Measures?
For international B2B buyers, especially those from Africa, South America, the Middle East, and Europe, verifying a supplier’s quality control measures is crucial. Here are actionable steps:
1. Conduct Supplier Audits
Buyers should perform audits of potential suppliers to assess their manufacturing processes, quality control systems, and compliance with international standards. This can be done through on-site visits or third-party audit services.
2. Request Documentation
Ask suppliers for documentation of their quality assurance processes, including reports from IQC, IPQC, and FQC stages. Certifications such as ISO 9001 and CE marking should also be provided.
3. Utilize Third-Party Inspection Services
Engaging third-party inspection services can provide an unbiased assessment of the supplier’s quality control measures. These services can conduct tests and inspections at various stages of production, offering buyers peace of mind.
What Are the Quality Control and Certification Nuances for International Buyers?
International buyers must be aware of specific nuances in quality control and certification that can vary by region. For example, European buyers may require CE marking, while buyers in the Middle East might focus on local compliance standards. It’s essential to communicate these requirements clearly with suppliers to avoid any compliance issues.
Furthermore, understanding the implications of various certifications on product quality and safety can help buyers make informed decisions. For instance, a supplier with ISO certification may demonstrate a higher commitment to quality management compared to one without such credentials.
Conclusion
The manufacturing processes and quality assurance measures for custom cutting boards are multifaceted and critical for B2B buyers. By understanding these processes, setting clear expectations, and implementing robust verification methods, international buyers can ensure they receive high-quality products that meet their needs and regulatory requirements.
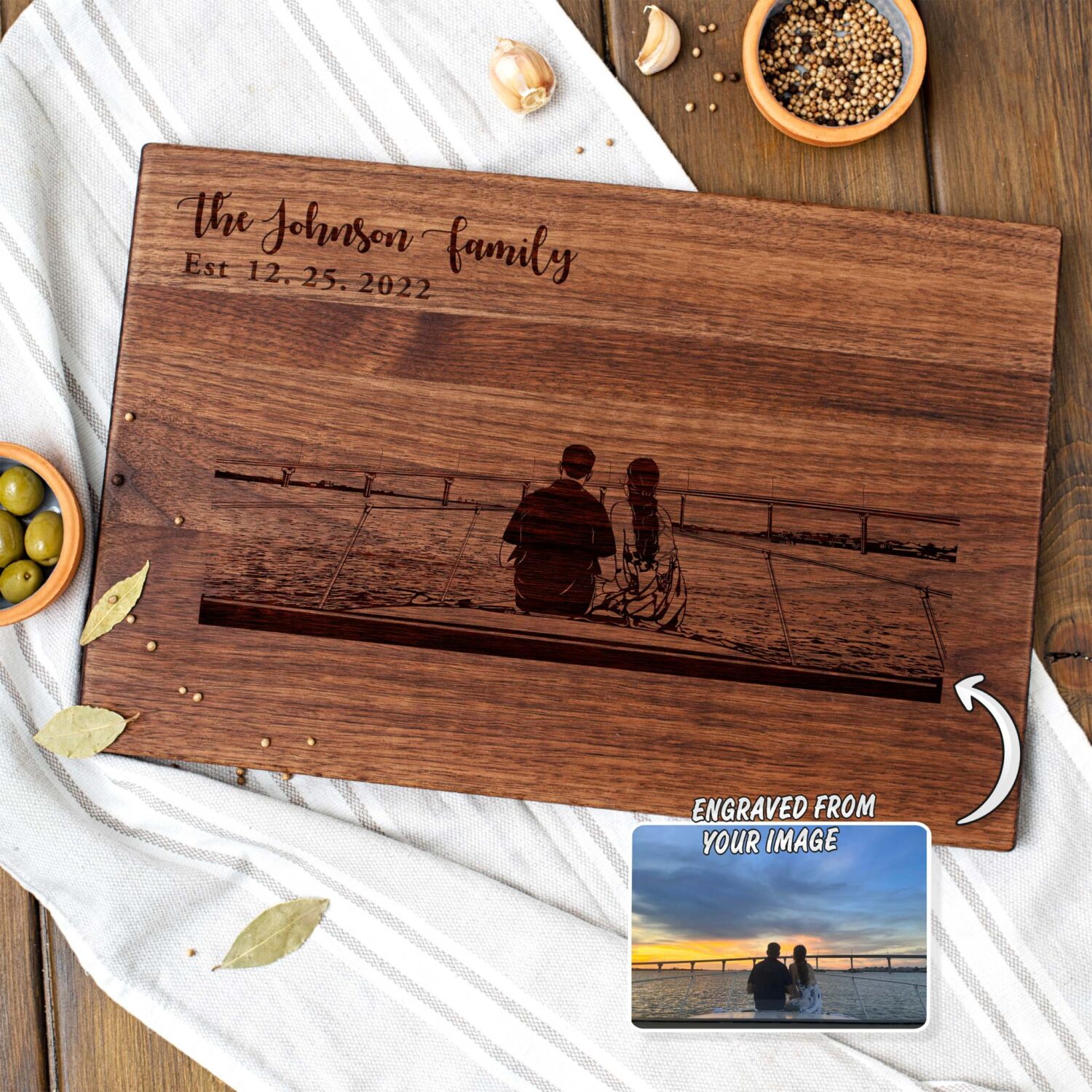
A stock image related to cutting board custom.
Practical Sourcing Guide: A Step-by-Step Checklist for ‘cutting board custom’
To successfully procure custom cutting boards, international B2B buyers must follow a structured approach. This guide offers a practical checklist designed to streamline the sourcing process, ensuring that buyers can identify the best suppliers while meeting their specific requirements.
Step 1: Define Your Technical Specifications
Clearly outlining your technical specifications is vital for ensuring that the final product meets your needs. Consider the materials (e.g., bamboo, plastic, wood), dimensions, thickness, and any specific features like handles or grooves. This clarity will help suppliers provide accurate quotes and reduce the likelihood of misunderstandings later in the process.
Step 2: Research Potential Suppliers
Conduct thorough research to identify potential suppliers who specialize in custom cutting boards. Utilize online platforms, trade shows, and industry directories to compile a list of candidates. Pay attention to their experience in producing similar products and their geographical location, as this can impact shipping costs and lead times.
Step 3: Evaluate Supplier Certifications
It’s essential to verify that your chosen suppliers comply with industry standards and regulations. Check for certifications such as ISO 9001 for quality management and any relevant food safety certifications, like FDA approval for food-contact materials. These credentials indicate a commitment to quality and safety, which is crucial for food-related products.
Step 4: Request Samples Before Committing
Before finalizing your order, request samples of the cutting boards to assess quality firsthand. This step allows you to evaluate the materials, craftsmanship, and overall design. Ensure that the samples align with your specifications and meet your quality standards, as this will help prevent costly errors in larger orders.
Step 5: Negotiate Pricing and Terms
Once you have selected potential suppliers, initiate discussions to negotiate pricing and payment terms. Consider factors such as minimum order quantities, payment schedules, and delivery timelines. A clear understanding of these terms is essential to avoid any unexpected costs or delays during the procurement process.
Step 6: Establish Clear Communication Channels
Maintaining open lines of communication with your suppliers is crucial for a smooth sourcing experience. Determine the preferred methods of communication (email, phone, or messaging apps) and establish regular check-ins to monitor progress. This proactive approach helps to address any issues promptly and ensures that both parties remain aligned throughout the production process.
Step 7: Plan for Logistics and Shipping
Finally, plan your logistics and shipping strategy well in advance. Consider factors such as shipping methods, customs regulations, and potential tariffs, particularly if you are sourcing from overseas. Collaborating with a logistics partner can simplify this process and ensure that your custom cutting boards arrive on time and in good condition.
By following this checklist, B2B buyers can navigate the complexities of sourcing custom cutting boards effectively. Each step is designed to minimize risks and enhance the overall procurement experience, leading to successful partnerships and high-quality products.
Comprehensive Cost and Pricing Analysis for cutting board custom Sourcing
What Are the Key Cost Components in Cutting Board Custom Sourcing?
When sourcing custom cutting boards, understanding the cost structure is crucial for effective budgeting and negotiation. The main cost components include:
-
Materials: The type of wood or composite material significantly influences the price. High-quality hardwoods like maple or walnut will incur higher costs than softer woods or synthetic materials.
-
Labor: Skilled labor is necessary for precision cutting, finishing, and customization. Labor costs can vary based on the geographic location of the manufacturer and the complexity of the designs.
-
Manufacturing Overhead: This includes utilities, rent, and equipment maintenance. It is typically a percentage of total costs and varies by manufacturer.
-
Tooling: Initial tooling costs can be substantial, especially for custom designs. This includes molds, dies, and other equipment needed to create unique cutting boards.
-
Quality Control (QC): Ensuring that each product meets quality standards requires investment in QC processes. This is particularly important in B2B transactions where the buyer expects a consistent product.
-
Logistics: Shipping costs can vary greatly depending on the destination, weight, and volume of the order. International buyers need to factor in customs duties and taxes.
-
Margin: Suppliers will typically add a profit margin to cover their costs and risks. This margin can fluctuate based on market demand and competition.
How Do Price Influencers Affect Cutting Board Custom Sourcing?
Several factors can influence the pricing of custom cutting boards:
-
Volume/MOQ (Minimum Order Quantity): Larger orders often lead to lower per-unit costs due to economies of scale. Discussing volume discounts upfront can yield significant savings.
-
Specifications and Customization: The more complex the design and specifications (e.g., laser engraving, unique shapes), the higher the cost. Clear communication about specifications is essential to avoid unexpected costs.
-
Materials and Quality Certifications: Boards made from sustainably sourced materials or those that meet specific food safety certifications will generally have a higher price point.
-
Supplier Factors: The reputation and reliability of the supplier can impact pricing. Established suppliers may charge more but offer better quality assurance and delivery timelines.
-
Incoterms: Understanding the terms of shipment (FOB, CIF, etc.) is crucial. These terms dictate who bears the shipping costs and risks, which can affect the final price.
What Are the Best Negotiation Tips for International B2B Buyers?
International B2B buyers from regions such as Africa, South America, the Middle East, and Europe should consider the following negotiation strategies:
-
Conduct Thorough Market Research: Understand the average market prices for cutting boards in your region. This knowledge will empower you during negotiations.
-
Discuss Total Cost of Ownership (TCO): Focus on the overall cost implications, including maintenance, durability, and replacement costs, rather than just the purchase price.
-
Be Transparent About Your Needs: Clearly communicate your requirements and expectations to suppliers. This can help in getting accurate quotes and avoiding hidden costs.
-
Explore Multiple Suppliers: Engaging with several suppliers can foster competition and lead to better pricing and terms.
-
Understand Pricing Nuances for Your Region: Be aware of the economic conditions and buyer expectations in your area. For instance, European buyers may prioritize sustainability and certifications more than others.
Are There Any Pricing Nuances That International Buyers Should Be Aware Of?
International buyers should be mindful of several pricing nuances when sourcing custom cutting boards:
-
Currency Fluctuations: Exchange rates can impact costs, especially for larger orders. Ensure you understand the currency used in quotes and any potential risks involved.
-
Import Tariffs and Duties: Different countries have varying import taxes that can significantly affect the final cost. It’s advisable to research these before making a purchasing decision.
-
Local Regulations: Be aware of any local laws regarding food safety and product certifications, as these can affect compliance costs and pricing.
Disclaimer on Indicative Prices
Prices for custom cutting boards can vary widely based on the factors mentioned above. It is recommended to obtain multiple quotes and conduct thorough due diligence to ensure you are making an informed purchasing decision.
Alternatives Analysis: Comparing cutting board custom With Other Solutions
When considering options for cutting solutions in a B2B environment, understanding the available alternatives to custom cutting boards is essential. Various solutions can meet different operational needs, budgets, and user preferences. This analysis provides a comparative overview of custom cutting boards against other viable options, helping international B2B buyers make informed decisions.
Comparison Aspect | Cutting Board Custom | Bamboo Cutting Boards | Plastic Cutting Boards |
---|---|---|---|
Performance | Highly durable, tailored for specific tasks | Eco-friendly, good for knife preservation | Lightweight, easy to clean |
Cost | Higher initial investment due to customization | Moderate cost, sustainable option | Low-cost, budget-friendly |
Ease of Implementation | Requires design specifications and longer lead time | Ready-to-use, limited customization | Easily available, minimal setup |
Maintenance | Requires proper care to maintain quality | Requires oiling for longevity | Dishwasher safe, minimal upkeep |
Best Use Case | Specialty kitchens needing specific dimensions | Culinary environments focusing on sustainability | General food prep in high-volume operations |
What Are the Advantages and Disadvantages of Bamboo Cutting Boards?
Bamboo cutting boards serve as a popular alternative due to their eco-friendly properties and durability. They are less porous than traditional wood, making them resistant to bacteria and easy to clean. However, they may not have the same level of customization as cutting board custom solutions, which can be a significant drawback for businesses that require specific dimensions or features. Bamboo boards can also require oiling to maintain their quality over time, adding a layer of maintenance that some buyers may wish to avoid.
How Do Plastic Cutting Boards Compare to Custom Options?
Plastic cutting boards are a cost-effective and practical solution for many food service operations. They are lightweight, easily available, and often dishwasher safe, making them convenient for high-volume environments. However, they may not provide the same durability or aesthetic appeal as custom wood or bamboo options. Additionally, plastic boards can develop scratches over time, which may harbor bacteria if not properly maintained. Thus, while they are budget-friendly, they may not be suitable for specialty kitchens that prioritize quality and performance.
Conclusion: How to Choose the Right Cutting Solution for Your Business
Selecting the right cutting solution depends on several factors, including budget, intended use, and maintenance preferences. Custom cutting boards offer tailored solutions ideal for specialized culinary tasks, while bamboo and plastic boards provide more general options. B2B buyers should assess their operational needs, considering performance, cost, and ease of maintenance to make a well-informed choice. By evaluating these alternatives, businesses can optimize their food preparation processes while aligning with their sustainability and performance goals.
Essential Technical Properties and Trade Terminology for cutting board custom
What Are the Essential Technical Properties of Custom Cutting Boards?
When sourcing custom cutting boards, understanding the technical properties is crucial for ensuring product quality and suitability for your specific needs. Here are some key specifications to consider:
1. Material Grade: Which Material is Best for Cutting Boards?
The material used in cutting boards significantly impacts durability, safety, and maintenance. Common materials include hardwood (like maple and walnut), bamboo, plastic, and composite materials. Each has its pros and cons. For example, hardwood is known for its durability and aesthetic appeal but requires more maintenance than plastic. B2B buyers should select material based on the intended use, such as food safety standards and ease of cleaning.
2. Tolerance: Why Is Precision Important in Cutting Board Manufacturing?
Tolerance refers to the allowable variation in the dimensions of the cutting board. High-quality custom cutting boards should adhere to strict tolerances to ensure uniformity and functionality. For instance, if a cutting board is intended for professional kitchen use, it must fit perfectly on countertops and in storage areas. Poor tolerances can lead to issues like warping or instability during use, which can affect food preparation efficiency.
3. Thickness: How Does Board Thickness Affect Performance?
The thickness of a cutting board can influence its durability and usability. Thicker boards tend to be more robust and can withstand heavier chopping without warping or cracking. For commercial kitchens where heavy use is expected, a thickness of at least 1.5 inches is often recommended. Buyers should consider their specific needs and the type of food preparation that will take place.
4. Finish: What Type of Finish Is Ideal for Custom Cutting Boards?
The finish applied to cutting boards can affect both appearance and hygiene. Common finishes include food-grade mineral oil, beeswax, and polyurethane. A food-safe finish is essential for maintaining hygiene, as it helps prevent bacteria from penetrating the wood. B2B buyers should inquire about finishes to ensure they meet health regulations and are suitable for their culinary applications.
5. Weight: How Does Weight Influence Usability?
The weight of a cutting board impacts its stability during use. Heavier boards tend to stay in place better, making them safer and easier to use for chopping. However, portability is also a consideration. For buyers, understanding the balance between weight and functionality is key, especially if the cutting board will be moved frequently.
What Are Common Trade Terminologies Used in the Custom Cutting Board Industry?
Familiarity with industry jargon can streamline communication and negotiations in the B2B market. Here are several critical terms:
1. OEM (Original Equipment Manufacturer): What Does OEM Mean for Custom Cutting Boards?
OEM refers to companies that manufacture products based on another company’s specifications and branding. In the cutting board industry, this means that a buyer can have cutting boards produced under their brand name, ensuring that the product meets their quality standards.
2. MOQ (Minimum Order Quantity): Why Is MOQ Important for Buyers?
MOQ is the smallest quantity of a product that a supplier is willing to sell. Understanding MOQ is essential for B2B buyers to ensure they can meet the supplier’s minimum requirements while managing their inventory effectively. Lower MOQs are often more favorable for small businesses or startups.
3. RFQ (Request for Quotation): How Can an RFQ Streamline Your Purchasing Process?
An RFQ is a document used to invite suppliers to bid on providing specific goods or services. For buyers, issuing an RFQ for custom cutting boards allows for comparison of prices, materials, and lead times, enabling informed purchasing decisions.
4. Incoterms: What Are Incoterms and Why Do They Matter?
Incoterms (International Commercial Terms) are a set of rules that define the responsibilities of buyers and sellers in international transactions. Understanding these terms is vital for B2B buyers to clarify shipping, insurance, and delivery responsibilities, thereby avoiding potential disputes.
By grasping these technical properties and trade terminologies, international B2B buyers can make informed decisions that align with their operational needs and enhance their supply chain management in sourcing custom cutting boards.
Navigating Market Dynamics and Sourcing Trends in the cutting board custom Sector
What Are the Key Market Dynamics and Sourcing Trends in the Custom Cutting Board Sector?
The custom cutting board market has witnessed a significant evolution driven by various global factors. The rise in health-conscious consumerism, particularly in regions such as Africa, South America, the Middle East, and Europe, is propelling demand for high-quality kitchen products. Buyers are increasingly seeking cutting boards that not only serve a functional purpose but also align with lifestyle trends. The integration of technology in sourcing, such as online platforms and B2B marketplaces, is making it easier for international buyers to connect with manufacturers, evaluate products, and negotiate pricing.
Emerging trends indicate a shift towards personalization and customization. B2B buyers are looking for unique designs that cater to their specific market needs, whether it’s engraved logos for branding or specific materials that resonate with local preferences. Additionally, the advent of smart technology in kitchenware, including cutting boards that track food preparation, is gaining traction, especially in developed markets in Europe and the UK. This trend presents opportunities for suppliers to innovate and offer advanced features that appeal to tech-savvy consumers.
How Does Sustainability Influence Sourcing Decisions in the Custom Cutting Board Industry?
Sustainability and ethical sourcing are becoming paramount in the custom cutting board sector. Environmental concerns related to deforestation and plastic waste have prompted buyers to seek products made from responsibly sourced materials. For instance, bamboo and reclaimed wood are gaining popularity due to their renewable nature and lower environmental impact. B2B buyers from Africa and South America, where natural resources are abundant, are particularly inclined towards sourcing sustainable materials that support local economies.
Moreover, the importance of ethical supply chains cannot be overstated. Buyers are increasingly demanding transparency in sourcing practices, ensuring that the materials used in cutting boards are not only sustainable but also ethically produced. Certifications such as FSC (Forest Stewardship Council) and organic certifications provide assurance to buyers regarding the environmental impact of their purchases. By prioritizing suppliers who adhere to these standards, B2B buyers can enhance their brand reputation and appeal to a growing demographic that values sustainability.
What Is the Historical Context of the Custom Cutting Board Market?
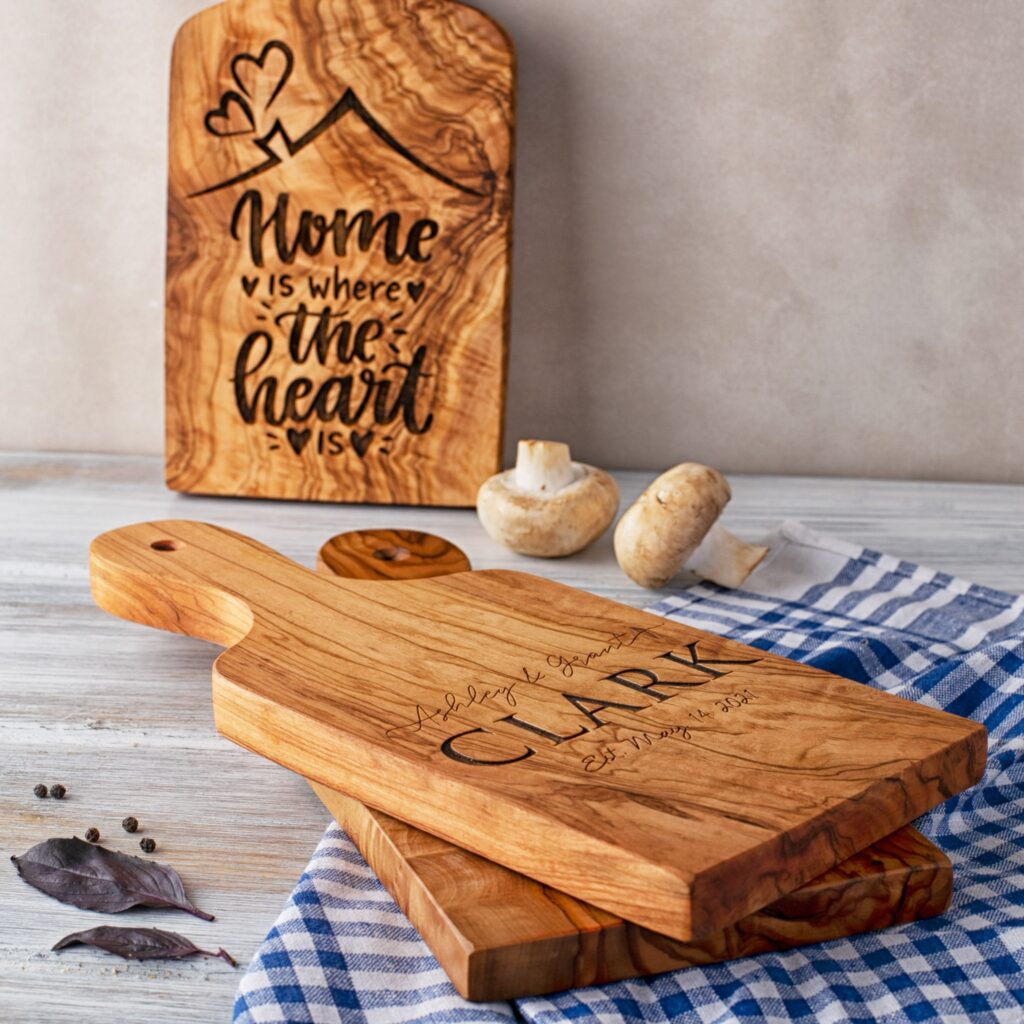
A stock image related to cutting board custom.
The custom cutting board market has evolved significantly over the decades, transitioning from basic, utilitarian designs to highly personalized and sophisticated products. Initially, cutting boards were primarily made from wood, reflecting the artisanal craftsmanship of local woodworkers. However, with the advent of mass production techniques and global trade, manufacturers began to explore a variety of materials, including plastics and composite materials, which offered durability and ease of maintenance.
As consumer preferences shifted towards aesthetics and functionality, the market adapted by introducing customizable options. Today, international B2B buyers can choose from an array of designs, materials, and finishes that cater to diverse culinary cultures and consumer preferences. This evolution signifies the growing importance of innovation and adaptability in the custom cutting board sector, making it essential for buyers to stay informed about market trends and emerging technologies.
Frequently Asked Questions (FAQs) for B2B Buyers of cutting board custom
-
How do I choose the right supplier for custom cutting boards?
Choosing the right supplier involves thorough research and vetting. Start by assessing their experience in the industry and their production capabilities. Request samples to evaluate the quality of their cutting boards, and check for certifications that ensure compliance with international safety standards. Additionally, consider their communication responsiveness, lead times, and ability to meet your specific customization needs. Engaging in direct conversations can also provide insights into their reliability and business ethics. -
What are the typical minimum order quantities (MOQ) for custom cutting boards?
Minimum order quantities can vary significantly based on the supplier and the complexity of the customization. Generally, MOQs for custom cutting boards range from 100 to 500 units, but some suppliers may accommodate smaller orders, especially for new clients. Discuss your needs with potential suppliers to find flexibility in their MOQs, particularly if you’re testing a new product line or entering a new market. -
What customization options are available for cutting boards?
Customization options typically include material selection (e.g., bamboo, hardwood, plastic), size dimensions, engraving or branding, and surface treatments for durability. Some suppliers may also offer unique shapes or thicknesses based on your requirements. When discussing customization, be clear about your brand’s aesthetic and functional needs to ensure the final product aligns with your expectations. -
What payment terms should I expect when sourcing custom cutting boards?
Payment terms can vary by supplier and region, but common practices include a deposit (usually 30-50%) upfront, with the balance due upon shipment or delivery. Some suppliers may offer credit terms for established businesses. It’s crucial to negotiate payment terms that align with your cash flow needs while ensuring security for both parties. Always confirm the currency and method of payment to avoid unexpected fees. -
How can I ensure quality assurance for my custom cutting boards?
To ensure quality, request a detailed quality assurance (QA) plan from your supplier, which should outline inspection processes and standards. Arrange for pre-shipment inspections, where a third-party service can verify that products meet your specifications. Establishing a clear communication channel for feedback during production can also help address any quality concerns before the final product is shipped. -
What logistics considerations should I keep in mind when importing cutting boards?
Logistics considerations include understanding shipping methods, customs regulations, and potential tariffs applicable to your region. Decide whether you’ll handle shipping logistics yourself or utilize the supplier’s services. Ensure you have all necessary documentation for customs clearance, and consider potential delays that may arise during transit. Partnering with a reliable freight forwarder can streamline the import process and help navigate international shipping complexities. -
Are there specific regulations for importing cutting boards into my country?
Import regulations vary by country and may include compliance with health and safety standards, especially for food-related items. Research your country’s import laws regarding materials used in cutting boards, labeling requirements, and any necessary certifications. Consulting with a customs broker can help ensure that you meet all regulatory requirements and avoid costly fines or shipment delays. -
How can I effectively communicate my needs to international suppliers?
Effective communication with international suppliers involves being clear and detailed about your requirements. Use precise language and provide visual aids, such as sketches or photos, to convey your expectations. Establish a regular communication schedule, and consider time zone differences. Utilizing platforms like email, video calls, and project management tools can facilitate better collaboration and ensure that all parties are aligned throughout the sourcing process.
Important Disclaimer & Terms of Use
⚠️ Important Disclaimer
The information provided in this guide, including content regarding manufacturers, technical specifications, and market analysis, is for informational and educational purposes only. It does not constitute professional procurement advice, financial advice, or legal advice.
While we have made every effort to ensure the accuracy and timeliness of the information, we are not responsible for any errors, omissions, or outdated information. Market conditions, company details, and technical standards are subject to change.
B2B buyers must conduct their own independent and thorough due diligence before making any purchasing decisions. This includes contacting suppliers directly, verifying certifications, requesting samples, and seeking professional consultation. The risk of relying on any information in this guide is borne solely by the reader.
Strategic Sourcing Conclusion and Outlook for cutting board custom
What Are the Key Takeaways for Strategic Sourcing in Cutting Board Customization?
In conclusion, strategic sourcing is essential for international B2B buyers looking to optimize their procurement of custom cutting boards. By leveraging data analytics and supplier relationships, businesses can enhance product quality, reduce costs, and improve delivery timelines. The importance of understanding local market trends cannot be overstated, especially for buyers in Africa, South America, the Middle East, and Europe. Engaging with suppliers who are aware of regional preferences and compliance standards can significantly impact the success of your sourcing strategy.
How Can International Buyers Prepare for Future Trends in Cutting Board Customization?
Looking ahead, international B2B buyers should remain agile and open to innovation in the cutting board market. Sustainability practices and the demand for eco-friendly materials are rising trends that cannot be ignored. By proactively adapting to these changes, businesses can not only meet customer expectations but also differentiate themselves in a competitive landscape.
What Steps Should Buyers Take Next?
As you navigate the complexities of sourcing custom cutting boards, consider establishing long-term partnerships with reliable suppliers and investing in technology that facilitates seamless communication and tracking. By prioritizing these strategies, you will be well-equipped to thrive in the evolving market landscape. Embrace the opportunity to enhance your product offerings and supply chain efficiency—your future success depends on it.