Discover Cost-Saving Benefits of Custom Machined Parts China (2025)
Introduction: Navigating the Global Market for custom machined parts china
In today’s competitive landscape, sourcing custom machined parts from China presents both opportunities and challenges for international B2B buyers. With the rapid globalization of supply chains, businesses in regions such as Africa, South America, the Middle East, and Europe—like Indonesia and Kenya—are increasingly turning to Chinese manufacturers for high-quality components. However, the complexities of navigating this market can be daunting, as buyers must contend with varying quality standards, supplier reliability, and fluctuating costs.
This guide aims to demystify the process of acquiring custom machined parts from China by providing an in-depth analysis of key considerations. We will explore the different types of machined parts available, their diverse applications across industries, and essential strategies for supplier vetting. Additionally, we will delve into cost factors, including shipping, tariffs, and negotiation tactics, equipping you with the knowledge needed to make informed purchasing decisions.
By understanding the intricacies of the Chinese market, B2B buyers can streamline their sourcing process, mitigate risks, and ultimately enhance their competitive edge. This comprehensive resource empowers businesses to navigate the complexities of international procurement, ensuring that you not only find the right parts but also secure the best value for your investment.
Understanding custom machined parts china Types and Variations
Type Name | Key Distinguishing Features | Primary B2B Applications | Brief Pros & Cons for Buyers |
---|---|---|---|
CNC Machined Parts | High precision, automated processes | Aerospace, automotive, electronics | Pros: High accuracy, repeatability. Cons: Initial setup costs can be high. |
Die Casting Parts | Metal casting using molds for complex shapes | Consumer goods, machinery components | Pros: Cost-effective for large volumes. Cons: Limited design flexibility. |
Sheet Metal Fabrication | Forming metal sheets into desired shapes | HVAC, automotive, construction | Pros: Versatile, can be customized easily. Cons: May require additional finishing. |
Injection Molding Parts | Plastic parts created by injecting material into molds | Electronics, automotive, medical | Pros: High production rates, complex geometries. Cons: High initial tooling costs. |
3D Printed Components | Additive manufacturing for rapid prototyping | Prototyping, specialized parts | Pros: Fast turnaround, design freedom. Cons: Material limitations, not suitable for mass production. |
What Are CNC Machined Parts and Their B2B Relevance?
CNC (Computer Numerical Control) machined parts are manufactured using highly automated equipment that allows for intricate designs and high precision. These parts are ideal for industries such as aerospace and automotive, where accuracy is paramount. B2B buyers should consider CNC machining for projects requiring tight tolerances and repeatability. However, the initial investment in CNC technology can be substantial, which may impact the overall cost for smaller orders.
How Do Die Casting Parts Benefit B2B Buyers?
Die casting involves pouring molten metal into molds to create parts with complex geometries. This method is particularly beneficial for producing large volumes of consistent and durable components, making it suitable for consumer goods and machinery applications. B2B buyers should weigh the advantages of cost-effectiveness against the limitations in design flexibility. While die casting can reduce per-unit costs significantly, intricate designs may necessitate a different manufacturing approach.
Why Choose Sheet Metal Fabrication for Your Business Needs?
Sheet metal fabrication is a versatile manufacturing process that allows for the creation of various shapes and sizes from metal sheets. This method is widely used in HVAC systems, automotive parts, and construction applications. B2B buyers find sheet metal fabrication advantageous due to its adaptability to custom specifications. However, additional finishing processes may be required to achieve the desired surface quality, which could affect project timelines and costs.
What Are the Advantages of Injection Molding Parts for B2B Applications?
Injection molding is a process where plastic is injected into molds to create parts, making it ideal for high-volume production. This method is highly suitable for industries like electronics and automotive, where complex geometries are often required. While the production rates are high and the design capabilities are extensive, B2B buyers must consider the significant upfront costs associated with tooling. This factor is crucial for businesses planning to scale their production.
How Can 3D Printed Components Transform Your B2B Purchasing Strategy?
3D printing, or additive manufacturing, enables the rapid production of components directly from digital models. This technology is beneficial for prototyping and creating specialized parts, offering unmatched design freedom. B2B buyers should consider 3D printing for projects that require quick iterations and custom designs. However, material limitations and the unsuitability for mass production may restrict its application in larger-scale operations.
Related Video: Transforming METAL into MACHINED Parts! | Manual Machining, Turning & Threading
Key Industrial Applications of custom machined parts china
Industry/Sector | Specific Application of custom machined parts china | Value/Benefit for the Business | Key Sourcing Considerations for this Application |
---|---|---|---|
Automotive | Precision engine components | Enhanced performance and reliability | Quality certifications, lead times, and material specifications |
Aerospace | Structural components for aircraft | Improved safety and compliance with regulations | Understanding of aerospace standards, traceability of materials |
Oil & Gas | Custom valves and fittings | Increased efficiency in resource extraction | Supplier reliability, technical support, and material certifications |
Electronics | Heat sinks and housings for electronic devices | Better thermal management and device longevity | Expertise in thermal properties and design capabilities |
Medical Devices | Surgical instruments and implants | High precision and biocompatibility | Compliance with medical regulations, quality control processes |
How Are Custom Machined Parts Used in the Automotive Industry?
In the automotive sector, custom machined parts from China are crucial for producing precision engine components, such as pistons and crankshafts. These components need to meet stringent tolerances to ensure optimal engine performance and durability. International buyers, especially from regions like Africa and South America, must prioritize suppliers that offer quality certifications and can demonstrate their capabilities in meeting specific material and design requirements. This focus not only enhances vehicle reliability but also drives down long-term maintenance costs.
What Role Do Custom Machined Parts Play in Aerospace Applications?
Custom machined parts are integral to the aerospace industry, where structural components must comply with rigorous safety standards. Parts such as brackets and fittings are often produced to exact specifications, ensuring that they can withstand extreme conditions. For buyers from the Middle East and Europe, it’s essential to partner with manufacturers familiar with aerospace regulations and who can provide documentation for material traceability. This adherence to standards is vital for maintaining safety and regulatory compliance in all aircraft operations.
How Are Custom Machined Parts Utilized in the Oil & Gas Sector?
In the oil and gas industry, custom machined parts such as valves and fittings are essential for ensuring efficient resource extraction and processing. These components must be tailored to handle high-pressure environments and corrosive substances. Buyers from regions like Africa must consider the reliability of their suppliers, ensuring they have the technical support needed for installation and maintenance. Additionally, sourcing from manufacturers who adhere to international standards can significantly enhance operational efficiency and reduce downtime.
Why Are Custom Machined Parts Important for Electronics Manufacturing?
The electronics industry relies heavily on custom machined parts for heat sinks and housings that improve thermal management in devices. As electronic components generate heat, effective heat dissipation is crucial for device longevity and performance. For international buyers, particularly in emerging markets, it is important to select suppliers with expertise in thermal properties and design capabilities. This ensures that the machined parts not only fit perfectly but also enhance the overall efficiency of electronic devices.
How Do Custom Machined Parts Benefit the Medical Device Sector?
In the medical device industry, custom machined parts are used to create surgical instruments and implants that require high precision and biocompatibility. These components are often subject to strict regulatory standards, making it essential for buyers to work with manufacturers who have robust quality control processes. International buyers, particularly from Europe and the Middle East, should prioritize suppliers that demonstrate compliance with medical regulations, ensuring that the products meet safety and efficacy requirements for patient care.
Related Video: Incredible Machining: Parts Made In Seconds Using 8 Spindles
3 Common User Pain Points for ‘custom machined parts china’ & Their Solutions
Scenario 1: Quality Assurance Challenges in Sourcing Custom Machined Parts from China
The Problem: One of the primary concerns for B2B buyers when sourcing custom machined parts from China is ensuring consistent quality. Many buyers have experienced scenarios where the delivered parts do not meet the specified tolerances or finish. This can lead to production delays, increased costs for rework, and damage to the buyer’s reputation if products fail to perform as expected. Furthermore, language barriers and time zone differences can complicate effective communication regarding quality expectations.
The Solution: To mitigate quality issues, it is crucial to establish clear specifications and standards upfront. Buyers should create detailed technical drawings and specifications that include tolerances, materials, and surface finishes. Engaging a reliable third-party quality inspection service in China can provide an additional layer of assurance. These services can conduct inspections at various stages of production, ensuring that parts meet the required standards before shipment. Additionally, fostering a strong relationship with your supplier through regular communication and feedback can help align expectations and maintain quality.
Scenario 2: Navigating Lead Time and Delivery Delays for Custom Machined Parts
The Problem: Timely delivery of custom machined parts is essential for maintaining production schedules. However, B2B buyers often face unpredictable lead times due to various factors such as customs delays, manufacturing bottlenecks, or even political instability. This unpredictability can severely disrupt operations, leading to lost sales and strained supplier relationships.
The Solution: To better manage lead times, buyers should incorporate buffer periods into their project timelines. A proactive approach involves conducting thorough research on potential suppliers to understand their production capabilities and typical lead times. Establishing clear communication regarding deadlines and incorporating contractual penalties for late deliveries can incentivize suppliers to prioritize your orders. Utilizing a vendor management system can also help track orders and monitor supplier performance, allowing buyers to identify and address potential delays before they impact production.
Scenario 3: Understanding Intellectual Property Risks with Custom Machined Parts
The Problem: Intellectual property (IP) theft is a significant concern for international B2B buyers sourcing custom machined parts from China. There have been numerous instances where proprietary designs or technology have been misappropriated, leading to financial losses and competitive disadvantages. Buyers often feel vulnerable, especially when sharing sensitive designs with foreign manufacturers.
The Solution: To protect intellectual property, buyers should take several precautionary steps. First, conducting thorough due diligence on potential suppliers is essential; check their reputation, past collaborations, and adherence to IP laws. Buyers should utilize Non-Disclosure Agreements (NDAs) to legally bind suppliers to confidentiality regarding proprietary designs. Additionally, consider using design patents or trademarks where applicable. Limiting the amount of sensitive information shared and employing a phased approach to sharing designs can further minimize risk. Finally, engaging legal counsel familiar with international trade laws can provide additional guidance on safeguarding your intellectual property when working with overseas suppliers.
Strategic Material Selection Guide for custom machined parts china
When selecting materials for custom machined parts in China, international B2B buyers must consider various factors that can significantly impact the performance, cost, and suitability of the final product. Here, we analyze four common materials used in custom machining, focusing on their properties, advantages, disadvantages, and specific considerations for buyers from regions such as Africa, South America, the Middle East, and Europe.
What Are the Key Properties of Aluminum in Custom Machined Parts?
Aluminum is a lightweight metal known for its excellent corrosion resistance and good thermal conductivity. It typically performs well in applications where weight reduction is crucial, such as in aerospace and automotive industries. Aluminum can withstand moderate temperatures and pressures, making it suitable for various environments.
Pros and Cons of Using Aluminum
The primary advantage of aluminum is its low density, which translates to reduced shipping costs and easier handling. However, it may not be as durable as other metals, particularly in high-stress applications. Additionally, the manufacturing complexity can increase due to the need for specialized machining techniques.
Impact on Application
Aluminum is compatible with a wide range of media, including air and water, but may not be suitable for aggressive chemicals. Buyers should ensure that the specific application does not expose aluminum to conditions that could lead to rapid degradation.
How Does Stainless Steel Compare as a Material for Custom Machined Parts?
Stainless steel is renowned for its exceptional strength and corrosion resistance. It can withstand high temperatures and pressures, making it ideal for applications in the oil and gas, food processing, and medical industries.
Pros and Cons of Using Stainless Steel
The key advantage of stainless steel is its durability and longevity, which can lead to lower lifecycle costs. However, it is generally more expensive than aluminum and may require more complex machining processes, potentially increasing lead times.
Impact on Application
Stainless steel is compatible with a wide variety of media, including corrosive substances, making it a versatile choice for many applications. Buyers should be aware of the specific grade of stainless steel required for their application, as different grades offer varying levels of corrosion resistance.
What Are the Benefits and Limitations of Using Brass in Custom Machined Parts?
Brass is an alloy primarily composed of copper and zinc, known for its excellent machinability and good corrosion resistance. It is often used in applications such as plumbing fittings and electrical components.
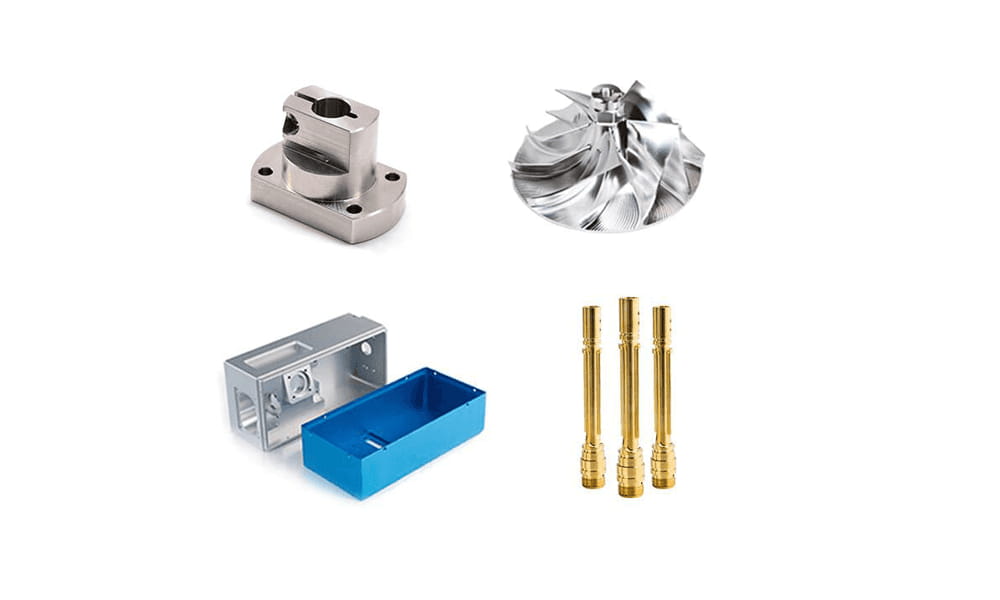
A stock image related to custom machined parts china.
Pros and Cons of Using Brass
Brass offers excellent thermal and electrical conductivity, making it ideal for electrical applications. However, it is less durable than stainless steel and can be more expensive than aluminum, depending on the alloy used.
Impact on Application
Brass is compatible with water and various gases but may not perform well in highly corrosive environments. Buyers should consider the specific conditions their parts will face, especially in outdoor or marine applications.
Why Is Plastic a Viable Option for Custom Machined Parts?
Plastics, such as polycarbonate and nylon, are increasingly being used in custom machined parts due to their lightweight nature and versatility. They can be molded into complex shapes, which can reduce manufacturing complexity.
Pros and Cons of Using Plastic
The primary advantage of plastic is its cost-effectiveness and ease of machining. However, plastics generally have lower strength and temperature resistance compared to metals, which may limit their use in high-stress applications.
Impact on Application
Plastics are suitable for applications where corrosion resistance is essential, such as in chemical processing. However, buyers must ensure that the selected plastic can withstand the specific media and environmental conditions of their application.
Summary Table of Material Selection for Custom Machined Parts
Material | Typical Use Case for custom machined parts china | Key Advantage | Key Disadvantage/Limitation | Relative Cost (Low/Med/High) |
---|---|---|---|---|
Aluminum | Aerospace components, automotive parts | Lightweight and corrosion-resistant | Lower durability in high-stress applications | Medium |
Stainless Steel | Oil and gas, food processing, medical devices | Exceptional strength and durability | Higher cost and complex machining | High |
Brass | Plumbing fittings, electrical components | Excellent machinability and conductivity | Less durable than stainless steel | Medium |
Plastic | Chemical processing, lightweight applications | Cost-effective and easy to machine | Lower strength and temperature resistance | Low |
This strategic material selection guide provides essential insights for international B2B buyers, enabling them to make informed decisions when sourcing custom machined parts from China. Understanding the properties, advantages, and limitations of each material will help ensure that the chosen components meet the specific requirements of their applications.
In-depth Look: Manufacturing Processes and Quality Assurance for custom machined parts china
What Are the Main Stages of Manufacturing Custom Machined Parts in China?
Manufacturing custom machined parts in China involves several key stages that are critical to achieving high-quality outputs. Understanding these processes can help international B2B buyers make informed decisions when sourcing from Chinese suppliers.
1. Material Preparation
The initial stage of manufacturing begins with material selection and preparation. Common materials used include aluminum, steel, titanium, and plastics. Suppliers typically source raw materials that meet specific industry standards. It’s essential for buyers to inquire about the material certifications to ensure compliance with international standards.
Key Actions for Buyers:
– Request material certificates and compliance documents.
– Confirm the source of raw materials to ensure quality and sustainability.
2. Forming Techniques Used in Machining
Once the materials are prepared, the next phase involves various forming techniques. Common techniques include CNC machining, turning, milling, and electrical discharge machining (EDM). Each technique has its own advantages depending on the complexity and precision required for the parts.
Key Actions for Buyers:
– Discuss the specific machining techniques that will be employed for your parts.
– Understand the capabilities of the machinery used, as this affects precision and lead times.
3. Assembly and Integration
After individual components are machined, they may require assembly, especially if the custom part consists of multiple pieces. This stage often involves fitting, welding, or fastening parts together. Effective assembly processes are critical for the functionality of the final product.
Key Actions for Buyers:
– Verify if the supplier has in-house assembly capabilities or if they subcontract this work.
– Ask for details on assembly quality checks to ensure proper integration.
4. Finishing Processes for Enhanced Quality
Finishing processes such as polishing, anodizing, or coating are crucial for achieving the desired surface quality and protection against corrosion. These processes not only enhance the aesthetic appeal but also improve durability and functionality.
Key Actions for Buyers:
– Clarify the finishing processes that will be applied and their implications on lead time and cost.
– Request samples of finished products to evaluate quality before placing bulk orders.
How Is Quality Assurance Implemented in Chinese Manufacturing?
Quality assurance (QA) is a cornerstone of the manufacturing process in China, particularly for custom machined parts. Understanding how QA is structured can help international buyers ensure they receive products that meet their specifications.
What International Standards Are Relevant for Quality Assurance?
To maintain high-quality outputs, many Chinese manufacturers adhere to international standards such as ISO 9001, which focuses on quality management systems. Additionally, industry-specific certifications like CE (Conformité Européenne) for safety and compliance and API (American Petroleum Institute) standards for oil and gas components may also be relevant.
Key Actions for Buyers:
– Verify the certifications held by the manufacturer.
– Ensure that the supplier’s quality management system aligns with your industry requirements.
What Are the Key Quality Control Checkpoints?
Quality control (QC) in the manufacturing process typically involves several critical checkpoints:
- Incoming Quality Control (IQC): This stage inspects raw materials before they are used in production.
- In-Process Quality Control (IPQC): Ongoing checks during the manufacturing process to ensure adherence to specifications.
- Final Quality Control (FQC): A comprehensive inspection of the finished product before delivery.
Key Actions for Buyers:
– Request detailed QC reports for each stage of production.
– Understand the frequency and methodology of inspections conducted at each checkpoint.
What Common Testing Methods Are Used for Custom Machined Parts?
Testing methods can vary based on the type of part and its intended use. Common methods include:
- Dimensional Inspection: Verifying that parts meet specified dimensions using tools such as calipers and gauges.
- Material Testing: Assessing the mechanical properties of materials, including tensile strength and hardness.
- Functional Testing: Ensuring the part performs as intended in real-world applications.
Key Actions for Buyers:
– Inquire about the specific testing methods used and the qualifications of personnel conducting these tests.
– Consider third-party inspection services for unbiased evaluations.
How Can B2B Buyers Verify Supplier Quality Control?
International buyers should take proactive steps to verify the quality control measures of their suppliers in China.
What Auditing Practices Should Be Considered?
Regular audits can provide insight into a supplier’s adherence to quality standards. Buyers may conduct their own audits or hire third-party services to assess the supplier’s facilities and processes.
Key Actions for Buyers:
– Schedule periodic audits to evaluate the supplier’s quality control systems.
– Review audit reports to identify areas of improvement or potential risks.
How Can Buyers Access Quality Reports and Documentation?
Suppliers should be willing to provide comprehensive quality reports that detail the results of inspections and tests conducted throughout the manufacturing process. This documentation is crucial for transparency and accountability.
Key Actions for Buyers:
– Request access to quality control documentation before finalizing contracts.
– Establish clear communication regarding expectations for quality reporting.
What Are the QC and Certification Nuances for International B2B Buyers?
Navigating the complexities of quality control and certifications can be particularly challenging for international buyers from regions like Africa, South America, the Middle East, and Europe.
How Do Cultural Differences Impact Quality Expectations?
Cultural perceptions of quality can vary significantly across regions. Buyers should be aware of these differences and communicate their expectations clearly to avoid misunderstandings.
Key Actions for Buyers:
– Provide detailed specifications and quality benchmarks in writing.
– Engage in regular communication to align expectations throughout the production process.
What Should Buyers Know About Import Regulations and Compliance?
Compliance with local import regulations in the buyer’s country is crucial. Understanding these regulations can help avoid delays and additional costs.
Key Actions for Buyers:
– Research the import regulations that apply to custom machined parts in your region.
– Ensure that the supplier can provide necessary documentation to facilitate smooth customs clearance.
By understanding the manufacturing processes and quality assurance measures in place for custom machined parts in China, international B2B buyers can make more informed decisions and foster successful partnerships with their suppliers.
Practical Sourcing Guide: A Step-by-Step Checklist for ‘custom machined parts china’
The purpose of this guide is to provide a comprehensive checklist for international B2B buyers looking to source custom machined parts from China. By following these steps, you can ensure a smoother procurement process, minimize risks, and establish fruitful partnerships with reliable suppliers.
Step 1: Define Your Technical Specifications
Before initiating the sourcing process, clearly outline your technical requirements for the custom machined parts. This includes dimensions, material types, tolerances, and any specific industry standards that must be adhered to. Having a detailed specification document will help potential suppliers understand your needs better and provide accurate quotes.
- Consider creating a technical drawing to illustrate your specifications visually.
- Include tolerances and surface finishes that are critical for your application.
Step 2: Research Potential Suppliers Thoroughly
Conduct thorough research to identify potential suppliers in China. Utilize platforms like Alibaba, Made-in-China, and Global Sources to compile a list of manufacturers specializing in custom machining.
- Check supplier ratings and reviews to gauge their reliability and quality of service.
- Look for suppliers with industry certifications such as ISO 9001, which indicates a commitment to quality management.
Step 3: Evaluate Supplier Capabilities
Once you have shortlisted potential suppliers, evaluate their manufacturing capabilities. This includes assessing their machinery, production capacity, and technological expertise.
- Request information on their machinery and production processes to ensure they can meet your specifications.
- Ask for case studies or examples of previous work to verify their experience with similar projects.
Step 4: Request and Analyze Quotes
Reach out to your selected suppliers and request detailed quotes. Ensure that the quotes include pricing, lead times, payment terms, and any additional costs such as shipping or taxes.
- Compare quotes based on total cost rather than just unit price to get a complete picture.
- Inquire about bulk discounts or payment terms that could affect your budget.
Step 5: Verify Supplier Certifications and Compliance
Before finalizing a supplier, verify their certifications and compliance with international standards. This step is crucial in ensuring that the parts produced meet your quality and regulatory requirements.
- Request copies of relevant certifications and check their validity.
- Consider third-party audits for additional assurance of compliance.
Step 6: Establish Clear Communication Channels
Effective communication is essential throughout the sourcing process. Set up clear communication channels and protocols with your chosen supplier to avoid misunderstandings.
- Utilize tools like video calls or collaborative platforms for regular updates and discussions.
- Clarify language preferences to ensure that both parties fully understand each other.
Step 7: Conduct a Trial Order
Before committing to larger orders, place a trial order to assess the supplier’s performance. This will help you evaluate product quality, lead times, and overall service.
- Use this order to test the entire process, from manufacturing to shipping.
- Gather feedback from your team regarding the quality and usability of the parts received.
By following this step-by-step checklist, international B2B buyers can effectively navigate the complexities of sourcing custom machined parts from China, ensuring quality and reliability in their procurement process.
Comprehensive Cost and Pricing Analysis for custom machined parts china Sourcing
What Are the Key Cost Components for Custom Machined Parts Sourcing from China?
When sourcing custom machined parts from China, understanding the comprehensive cost structure is crucial. The primary cost components include:
-
Materials: The choice of materials significantly impacts the total cost. Common materials like aluminum, stainless steel, and plastics vary in price based on market demand and availability. Buyers should consider sourcing materials locally when possible to minimize costs.
-
Labor: Labor costs in China are generally lower compared to Western countries. However, the level of skill required for specific machining processes can affect this cost. More complex operations may require skilled labor, which can drive up expenses.
-
Manufacturing Overhead: This includes utilities, rent, and equipment maintenance. Efficient factories that leverage automation may offer lower overhead costs, which can translate into better pricing for buyers.
-
Tooling: The cost of tooling can be substantial, especially for custom designs. It’s essential to factor in these upfront costs, as they can be amortized over large production runs.
-
Quality Control (QC): Implementing quality assurance processes adds to the overall cost but is vital for ensuring product reliability. Investing in QC upfront can prevent costly defects and rework later.
-
Logistics: Shipping costs can vary widely based on the size and weight of the parts, as well as the chosen transportation method. Understanding Incoterms is essential for clarifying responsibilities and costs associated with shipping.
-
Margin: Suppliers will include their profit margin in the final pricing. This margin can vary based on the supplier’s position in the market and their perceived value proposition.
How Do Price Influencers Affect Custom Machined Parts Pricing?
Several factors influence the pricing of custom machined parts sourced from China:
-
Volume/MOQ (Minimum Order Quantity): Generally, higher order volumes lead to lower per-unit costs. Suppliers may offer tiered pricing based on the quantity ordered, making it advantageous for buyers to consolidate orders.
-
Specifications and Customization: Unique designs or specifications can increase costs due to the complexity involved in production. Buyers should clearly define their requirements to avoid unexpected expenses.
-
Materials: The choice of material not only affects the cost but also the performance and durability of the parts. Opting for standard materials may help in reducing costs.
-
Quality Certifications: Parts that require specific quality certifications (ISO, CE, etc.) may incur higher costs. Buyers should assess whether these certifications are necessary for their application.
-
Supplier Factors: The supplier’s reputation, experience, and operational efficiencies can significantly influence pricing. Conducting thorough research and vetting suppliers can lead to better pricing and quality assurance.
-
Incoterms: Understanding Incoterms is critical for international transactions. They define the responsibilities of buyers and sellers regarding shipping, insurance, and tariffs, all of which affect the total landed cost.
What Are Effective Buyer Tips for Cost-Efficiency in Sourcing?
For international B2B buyers, particularly from Africa, South America, the Middle East, and Europe, here are actionable tips for achieving cost-efficiency:
-
Negotiate Effectively: Leverage the competitive landscape in China by negotiating terms and pricing. Building a good relationship with suppliers can lead to better deals and flexibility in pricing.
-
Consider Total Cost of Ownership (TCO): Instead of focusing solely on the purchase price, evaluate the TCO, which includes shipping, duties, and potential rework costs. This approach provides a clearer picture of the overall investment.
-
Understand Pricing Nuances: Be aware of seasonal fluctuations in material prices and labor costs in China. Timing your orders can lead to significant savings.
-
Request Detailed Quotations: Always ask for itemized quotations that break down costs. This transparency helps in understanding the pricing structure and facilitates better negotiation.
-
Engage Local Agents: In regions like Africa and South America, working with local agents who understand both the market and cultural nuances can bridge communication gaps and streamline the sourcing process.
Disclaimer
The prices discussed in this analysis are indicative and can vary based on market conditions, supplier capabilities, and specific project requirements. Always conduct thorough due diligence and obtain multiple quotes before making purchasing decisions.
Alternatives Analysis: Comparing custom machined parts china With Other Solutions
When considering the procurement of custom machined parts, international B2B buyers often find themselves weighing the benefits of sourcing from China against other viable alternatives. Understanding these alternatives can significantly impact cost, efficiency, and overall project success. Below, we compare custom machined parts from China with two notable alternatives: domestic machining services and additive manufacturing (3D printing).
Comparison Aspect | Custom Machined Parts China | Domestic Machining Services | Additive Manufacturing (3D Printing) |
---|---|---|---|
Performance | High precision and quality | Generally high, but may vary by provider | Variable; often limited in material strength |
Cost | Competitive pricing due to lower labor costs | Typically higher due to labor and overhead | Cost-effective for low-volume production, expensive for large runs |
Ease of Implementation | Established supply chains, but potential language barriers | Familiarity with local regulations and standards | Requires specialized knowledge and software |
Maintenance | Minimal; depends on supplier | Ongoing support and repair services often available | Limited maintenance, but design iterations can be complex |
Best Use Case | High-volume production, complex geometries | Custom, low to medium volume, short lead times | Prototyping, complex geometries with fewer parts |
What Are the Advantages and Disadvantages of Domestic Machining Services?
Domestic machining services offer the advantage of proximity, which can enhance communication and reduce lead times. B2B buyers from regions like Europe and the Middle East often prefer this option due to familiarity with local regulations and standards. However, the cost is typically higher than sourcing from China, primarily due to labor and operational expenses. Additionally, the availability of specialized machinery may limit some capabilities compared to what is offered overseas.
How Does Additive Manufacturing Compare to Custom Machined Parts from China?
Additive manufacturing, or 3D printing, has gained traction as a viable alternative for producing custom parts, especially for prototypes and low-volume production. It allows for intricate designs that may be difficult to achieve through traditional machining. However, the material strength can be a concern, and the process can become cost-prohibitive for larger production runs. Moreover, 3D printing requires a certain level of expertise in design and operation, which can complicate implementation for some businesses.
How Can B2B Buyers Choose the Right Solution for Their Needs?
Choosing the right solution for custom machined parts requires a clear understanding of your project requirements, including volume, budget, and design complexity. If high precision and cost-effectiveness are paramount, custom machined parts from China may be the best choice. However, if you prioritize local support and compliance with regional standards, domestic machining services could be more suitable. For projects needing rapid prototyping and complex geometries, additive manufacturing may offer unique advantages, despite its limitations in material strength and scalability.
In summary, by evaluating the performance, costs, and implementation challenges of each alternative, B2B buyers can make informed decisions that align with their specific operational needs and strategic goals.
Essential Technical Properties and Trade Terminology for custom machined parts china
What Are the Key Technical Properties of Custom Machined Parts from China?
When sourcing custom machined parts from China, understanding the critical technical specifications is vital for ensuring product quality and compatibility with your operations. Here are some essential properties to consider:
-
Material Grade
– The material grade indicates the specific type of raw material used in the manufacturing of the parts, such as aluminum, stainless steel, or plastic composites. Different grades have varying properties, including strength, corrosion resistance, and machinability. Selecting the appropriate material grade is crucial for meeting the performance requirements of your application. -
Tolerance
– Tolerance refers to the permissible limit or limits of variation in a physical dimension. It is essential to specify tolerances accurately as they affect the fit and function of the parts in the final assembly. Tight tolerances may be necessary for precision engineering applications, while looser tolerances might suffice for less critical components. Understanding tolerances helps in evaluating the manufacturing capabilities of suppliers. -
Surface Finish
– The surface finish is the texture and quality of the part’s surface. Common finishes include anodized, polished, or powder-coated. The choice of surface finish can impact not only aesthetics but also functionality, such as resistance to wear and corrosion. Specify the desired finish to ensure it meets both visual and operational standards. -
Heat Treatment
– Heat treatment processes, such as annealing or hardening, alter the properties of the material to improve strength, ductility, or hardness. Understanding whether heat treatment is necessary for your parts can significantly affect their performance and longevity, especially in high-stress environments. -
Dimensional Accuracy
– Dimensional accuracy refers to how closely the manufactured part matches the intended design specifications. It encompasses several factors, including geometry and measurements. Ensuring high dimensional accuracy is essential for parts that must fit together precisely within assemblies, impacting overall system performance.
What Are Common Trade Terms in the Custom Machined Parts Industry?
Familiarizing yourself with industry jargon can facilitate smoother communication with suppliers and enhance negotiations. Here are some commonly used trade terms:
-
OEM (Original Equipment Manufacturer)
– OEM refers to a company that produces parts or equipment that may be marketed by another manufacturer. Understanding whether your supplier operates as an OEM can clarify their role in the supply chain and their ability to meet specific design requirements. -
MOQ (Minimum Order Quantity)
– MOQ is the smallest quantity of a product that a supplier is willing to sell. This term is critical for budgeting and planning your procurement strategy. Knowing the MOQ helps you assess whether a supplier can accommodate your needs without overcommitting resources. -
RFQ (Request for Quotation)
– An RFQ is a document sent to suppliers to request pricing and terms for specific products or services. Crafting a detailed RFQ is essential for receiving accurate quotes and ensures that suppliers understand your requirements. This process helps in comparing offers effectively. -
Incoterms (International Commercial Terms)
– Incoterms are a set of predefined commercial terms published by the International Chamber of Commerce. They define the responsibilities of buyers and sellers in international transactions, including shipping and insurance obligations. Familiarity with Incoterms is crucial for understanding the logistics and risks associated with your purchases. -
Lead Time
– Lead time refers to the time it takes from placing an order until the goods are delivered. It includes production and shipping time. Knowing the lead time is essential for planning your inventory and ensuring that your projects stay on schedule. -
CNC (Computer Numerical Control)
– CNC refers to the automated control of machining tools using computer programming. Understanding CNC processes is important as they influence the precision and complexity of the machined parts. It also helps in evaluating the technological capabilities of potential suppliers.
By grasping these technical properties and trade terms, international B2B buyers can enhance their procurement strategies, ensuring that they source custom machined parts that meet their operational needs while navigating the complexities of international trade effectively.
Navigating Market Dynamics and Sourcing Trends in the custom machined parts china Sector
What Are the Key Market Dynamics and Trends Influencing Custom Machined Parts from China?
The custom machined parts sector in China is witnessing transformative changes driven by various global factors. Increasing demand for precision-engineered components across industries such as automotive, aerospace, and electronics is propelling the market. International B2B buyers, particularly from regions like Africa, South America, the Middle East, and Europe, are increasingly looking to China not just for cost efficiency but also for quality and technological advancements.
Emerging trends such as Industry 4.0, which emphasizes automation and data exchange in manufacturing technologies, are reshaping the sourcing landscape. Buyers are encouraged to leverage smart manufacturing technologies that enhance production efficiency and reduce lead times. Additionally, the rise of digital platforms is facilitating more straightforward communication and transaction processes, allowing buyers to connect with suppliers seamlessly.
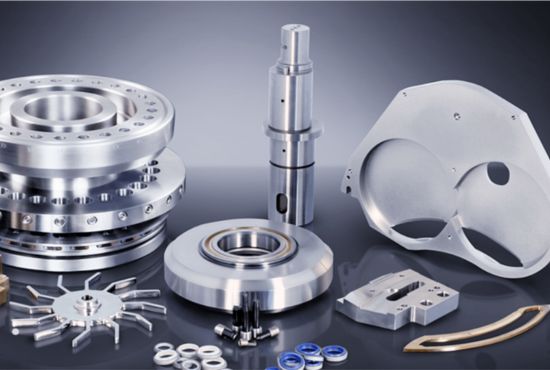
A stock image related to custom machined parts china.
Moreover, geopolitical factors and trade policies are influencing sourcing strategies. For instance, the ongoing trade tensions between China and Western nations are prompting buyers to evaluate their supply chains critically and consider alternatives. However, China remains a dominant player due to its vast manufacturing capabilities and supply chain infrastructure. As a result, international buyers must stay informed about these dynamics to navigate challenges effectively while capitalizing on opportunities within the market.
How Can Sustainability and Ethical Sourcing Impact Your B2B Operations?
Sustainability has become a focal point for international B2B buyers sourcing custom machined parts from China. The environmental impact of manufacturing processes is under scrutiny, with companies increasingly being held accountable for their carbon footprint and resource consumption. Buyers are encouraged to seek out suppliers who prioritize sustainable practices, such as using renewable energy sources and minimizing waste.
Ethical sourcing is equally important, as global supply chains face pressure to ensure fair labor practices and responsible sourcing of raw materials. Certifications such as ISO 14001 for environmental management and ISO 45001 for occupational health and safety can serve as valuable indicators of a supplier’s commitment to ethical practices.
Buyers should also consider materials that are recycled or sustainably sourced. For instance, using aluminum or steel that adheres to ‘green’ standards can significantly reduce the environmental impact of custom machined parts. By prioritizing sustainability and ethical sourcing, B2B buyers not only contribute to global environmental goals but also enhance their brand reputation and meet the growing consumer demand for responsible business practices.
What Is the Historical Context of Custom Machined Parts Manufacturing in China?
The evolution of the custom machined parts sector in China can be traced back to the late 20th century when the country began to open its markets to foreign investments. This transition marked the onset of an industrial boom, driven by low labor costs and an abundance of raw materials. Over the years, China’s manufacturing capabilities have significantly advanced, integrating advanced technologies that enhance precision and efficiency.
By the early 2000s, China’s reputation as a global manufacturing hub was firmly established, attracting international B2B buyers seeking cost-effective solutions for their component needs. The focus has since shifted from merely low-cost production to quality and innovation, with many manufacturers investing in state-of-the-art machinery and skilled labor to meet the increasing demands of global markets. As a result, today’s landscape is characterized by a combination of competitive pricing and high-quality manufacturing, positioning China as a critical player for international buyers in the custom machined parts sector.
Frequently Asked Questions (FAQs) for B2B Buyers of custom machined parts china
-
How do I solve sourcing challenges for custom machined parts in China?
Sourcing custom machined parts from China can be challenging due to language barriers, cultural differences, and varying quality standards. To mitigate these issues, establish clear communication with potential suppliers by using detailed specifications and visual aids. Consider partnering with a local sourcing agent who understands the market and can help navigate the complexities. Additionally, visiting suppliers in person or utilizing third-party quality control services can ensure the parts meet your requirements. -
What is the best way to vet suppliers for custom machined parts in China?
To effectively vet suppliers, start by researching their business credentials, such as registration details and certifications like ISO 9001. Request references from previous clients, particularly those in your industry, to assess their reliability. Conduct audits, if possible, to evaluate their production facilities and processes. Engaging a third-party inspection service can also provide an objective assessment of the supplier’s capabilities and quality standards. -
What should I consider regarding customization options for machined parts?
When seeking customization for machined parts, clearly define your specifications, including dimensions, materials, tolerances, and finishes. Discuss the design and engineering capabilities of potential suppliers, ensuring they have experience with your specific requirements. It’s also important to understand their prototyping process; a good supplier should be able to produce samples before full production, allowing for adjustments and ensuring the final product meets your expectations. -
What is the typical minimum order quantity (MOQ) for custom machined parts in China?
Minimum order quantities can vary significantly based on the supplier and the complexity of the parts. Generally, MOQs for custom machined parts range from 100 to 1,000 units. However, some suppliers may offer lower MOQs for prototyping or pilot runs. It’s essential to discuss your specific needs with suppliers and negotiate terms that align with your production plans and budget. -
What payment terms are common when sourcing from Chinese suppliers?
Payment terms can vary, but common practices include a 30% deposit upfront and the remaining 70% before shipment. Some suppliers may offer flexible payment methods, such as PayPal or letters of credit, which provide added security. It’s crucial to establish clear payment terms in your contract to avoid misunderstandings and ensure a smooth transaction process. -
How can I ensure quality assurance when sourcing custom machined parts from China?
Implementing a robust quality assurance strategy is essential. Start by defining quality standards and inspection criteria in your contract. Request regular updates and conduct in-process inspections if possible. Engaging a third-party quality control firm can help monitor production quality and provide final inspections before shipping. Establishing a clear return policy for defective parts will also protect your interests. -
What logistics considerations should I keep in mind when importing machined parts from China?
Logistics is crucial in the importation process. Consider factors such as shipping methods (air vs. sea), costs, lead times, and customs regulations in your country. Work with a reliable freight forwarder who can help navigate the complexities of international shipping and ensure compliance with local import laws. It’s also wise to factor in potential delays and plan your inventory accordingly. -
How do I handle communication and cultural differences when working with Chinese suppliers?
Effective communication is key to successful collaboration with Chinese suppliers. Utilize simple, clear language and avoid jargon to minimize misunderstandings. Establish regular check-ins via video calls or messaging platforms to build rapport. Being aware of cultural nuances—such as the importance of building relationships—can also facilitate smoother interactions. Consider time zone differences when scheduling meetings to ensure both parties are available.
Important Disclaimer & Terms of Use
⚠️ Important Disclaimer
The information provided in this guide, including content regarding manufacturers, technical specifications, and market analysis, is for informational and educational purposes only. It does not constitute professional procurement advice, financial advice, or legal advice.
While we have made every effort to ensure the accuracy and timeliness of the information, we are not responsible for any errors, omissions, or outdated information. Market conditions, company details, and technical standards are subject to change.
B2B buyers must conduct their own independent and thorough due diligence before making any purchasing decisions. This includes contacting suppliers directly, verifying certifications, requesting samples, and seeking professional consultation. The risk of relying on any information in this guide is borne solely by the reader.
Strategic Sourcing Conclusion and Outlook for custom machined parts china
In today’s competitive landscape, strategic sourcing of custom machined parts from China offers significant advantages for international B2B buyers, particularly those from Africa, South America, the Middle East, and Europe. By leveraging China’s robust manufacturing capabilities, buyers can access high-quality components at competitive prices, driving down overall production costs and enhancing product value.
Establishing strong supplier relationships is essential; it fosters trust and ensures consistent quality and timely delivery. As buyers navigate this complex sourcing environment, understanding local regulations, cultural nuances, and market trends is crucial for successful partnerships. Utilizing comprehensive due diligence processes and seeking suppliers with proven track records can mitigate risks and enhance supply chain resilience.
Looking ahead, the demand for custom machined parts is expected to grow, driven by advancements in technology and shifts in global manufacturing dynamics. Buyers must remain agile, embracing innovations in manufacturing and logistics to optimize their sourcing strategies. By taking proactive steps now, international B2B buyers can position themselves for success in a rapidly evolving market.
Engage with reliable suppliers, invest in relationship-building, and stay informed on industry trends to maximize your sourcing potential in China. The future is bright for those who strategically navigate this landscape.